Трубоукладчик гусеничный ТГ-124 на базе трактора Т-170




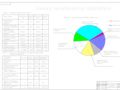
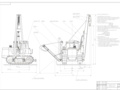
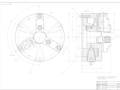
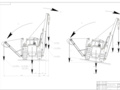
- Добавлен: 25.10.2022
- Размер: 4 MB
- Закачек: 1
Описание
Состав проекта
![]() |
![]() |
![]() ![]() |
![]() |
![]() ![]() |
![]() |
![]() ![]() ![]() ![]() |
![]() |
![]() ![]() ![]() ![]() |
![]() |
![]() ![]() ![]() ![]() |
![]() ![]() ![]() ![]() |
![]() ![]() ![]() ![]() |
![]() ![]() ![]() ![]() |
![]() |
![]() ![]() ![]() ![]() |
![]() |
![]() ![]() ![]() ![]() |
![]() ![]() ![]() ![]() |
![]() |
![]() |
![]() |
![]() |
![]() |
![]() ![]() ![]() ![]() |
![]() ![]() ![]() ![]() |
![]() ![]() ![]() ![]() |
![]() |
![]() ![]() |
![]() |
![]() ![]() |
![]() ![]() |
![]() |
![]() |
![]() |
![]() ![]() |
![]() ![]() |
![]() ![]() |
![]() |
![]() ![]() |
![]() ![]() |
![]() |
![]() ![]() |
![]() |
![]() ![]() |
![]() ![]() ![]() |
![]() |
![]() |
![]() |
![]() ![]() |
![]() ![]() |
Дополнительная информация
(5)стрела сбор..dwg

(11)технология.dwg

(12)Трёхкулачковый патрон.dwg

(6)стрела, прочность.dwg

(1)общий вид.dwg

(9)ГИДРАВЛИКА.dwg

(3)Рама противовеса расчет на прочность.dwg

(4)Система запираеия грузов противовеса.dwg

(2)Противовес.dwg

(10)Экономика.dwg

(8)расчетная схема.dwg

(7)ось прочность.dwg
