Бульдозер ДЗ-110А на базе трактора Т-170




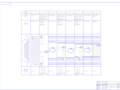
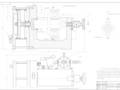
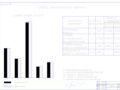
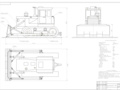
- Добавлен: 25.10.2022
- Размер: 13 MB
- Закачек: 1
Описание
Состав проекта
![]() |
![]() |
![]() |
![]() |
![]() ![]() ![]() ![]() |
![]() |
![]() ![]() ![]() ![]() |
![]() |
![]() ![]() ![]() ![]() |
![]() |
![]() |
![]() ![]() ![]() ![]() |
![]() |
![]() ![]() ![]() ![]() |
![]() |
![]() ![]() ![]() ![]() |
![]() |
![]() ![]() ![]() ![]() |
![]() |
![]() ![]() ![]() ![]() |
![]() ![]() ![]() ![]() |
![]() ![]() ![]() ![]() |
![]() ![]() |
![]() ![]() |
![]() ![]() |
![]() |
![]() ![]() |
![]() ![]() |
![]() ![]() |
![]() ![]() |
![]() ![]() |
![]() ![]() |
![]() ![]() |
![]() ![]() |
![]() ![]() |
![]() ![]() |
![]() ![]() |
![]() ![]() |
![]() ![]() |
![]() ![]() |
![]() ![]() |
![]() ![]() |
![]() ![]() |
![]() ![]() ![]() |
![]() |
![]() ![]() ![]() |
![]() ![]() ![]() |
![]() ![]() ![]() |
![]() ![]() ![]() |
![]() ![]() ![]() |
Дополнительная информация
List N 1.dwg

Базовый трактор Т-170
Тип отвала неповоротный
наибольшее заглубление
скорость подъема и опуска-
управление гидравлическое
Наибольшая скорость движения:
Технические требования:
Гидробак заполнять маслом МГ-30 - летом
соответствии с сезоном;
При ТО и ремонте предохранять внутренние полости от
Необходимо промывать сапун гидробака через 60 ч;
Систему охлаждения дизеля заполнять чистой водой в холодное
время года - антифризом.
List N 2.dwg

Сварка ручная электродуговая ГОСТ 5264-80
При сборке все пальцы и отверстия под них по-
дмазать солидолом "С" .Масленки прошприцевать
Выступание швов не допускается
Технические требования
List N7.dwg

верхнего слоя грунта
Возведение земляного
List N 10.dwg

List N 9.dwg

эффект за год работы
- амортизационные отисления
- фонд оплаты труда оператора бульдозера
- затраты на энергоносители
- затраты на смазочные материалы
- затраты на выполнение ТО и ремонтов
Годовой экономический
Годовой экономический эффект
ГОДОВЫЕ ТЕКУЩИЕ ЗАТРАТЫ
Лист N8.dwg

от дальности транспортирования грунта
Зависимость энергоёмкости единицы продукции
Зависимость трудоёмкости единицы продукции
Зависимость металлоёмкости единицы продукции
Технико-экономические
Технико-экономические показатели
List N5.dwg

Цементировать поверхность зубьев на глубину h 0
63 ядро 27 35 HRC. Предохранять шлицевое отверстие от
Допускается заточка одного из зубьев для проверки
твердости сердцевины и глубины цементационного слоя. Длина
заточки от торца зубчатого венца не более 5 мм;
Неуказанные предельные отклонения h14
Данные для контроля по нормам точности по ГОСТ 1643-81.
Сталь 20Х ГОСТ 4543-81
List N6.dwg

Отклонение от соосности осей отверстия опра-
вки 6 и отверстия оправки 8 не более 0
Отклонение от перпендикулярности поверхности
А относительно оси втулки 7 не более 0
Приспособление красить серой эмалью ПФ-115 по
На виде сверху базовая деталь условно не показана
Обабатываемое колесо условно не показано
фрезерования зубчатого колеса
Технические требования
List N 4.dwg

Анализ существующих конструкций отвалов
List N 3.dwg

изводить электродом Уоний 1345
Покрытие грунтовка Г.Ф-021
Технические требования
Пояснительная записка.doc
к дипломному проекту
«Эксплуатация модернизированного бульдозера ДЗ-110А при строительстве земляного полотна»
ВВЕДЕНИЕ .. .. . . 6
ОБЛАСТЬ ПРИМЕНЕНЕНИЯ БУЛЬДОЗЕРА НА БАЗЕ
ТРАКТОРА Т-170 . . 7
ТЕХНИЧЕСКАЯ ХАРАКТЕРИСТИКА .. .. .. .. .10
ОБОСНОВАНИЕ ДИПЛОМНОГО ПРОЕКТА И ОПИСАНИЕ
1 Патентный поиск 12
2 Описание предлагаемой конструкции .. .25
КОНСТРУКТОРСКИЙ РАЗДЕЛ . .29
1 Тяговый расчет . . ..29
2 Определение нагрузок на отвал и расчет на прочность навесного
бульдозерного оборудования .. 32
2.1 Первое расчетное положение . .32
2.2 Второе расчетное положение 42
2.3 Третье расчетное положение .. . . . .46
2.4 Четвертое расчетное положение .. 57
3 Выбор гидроцилиндра подъема отвала ..59
4 Расчет производительности бульдозера .. ..62
4.1 Расчет производительности бульдозера с модернизированным
4.2 Расчет производительности бульдозера с обычным отвалам .64
5 Выбор пружин для модернизированного отвала ..64
ТЕХНОЛОГИЯ ВОССТАНОВЛЕНИЯ ЗУБЧАТОГО КОЛЕСА .. 66
1 Расчет маршрута восстановления детали ..66
2 Расчет режимов выполняемых операций 67
2.1 Назначение припусков на механическую обработку 67
2.2 Расчет режимов наплавки 69
2.3 Расчет режимов резания и нормирование операций
токарной обработки .. 73
2.4 Расчет режимов фрезерования и нормирование фрезерной
2.5 Расчет режимов шлифования и нормирование операции
2.6 Приспособление для изготовления детали . 84
ВОЗВЕДЕНИЕ ЗЕМЛЯНОГО ПОЛОТНА . .88
1 Исходные данные . 88
2 Определение общего темпа работ . 90
3 Определение темпов работ для каждой машины входящей в СКМ..91
4 Определение состава машин входящих в СКМ-1 и СКМ-2
и определение их эксплуатационной производительности . ..93
5 Определение количества машиносмен . 95
6 Определение количества машин входящих в СКМ-1 и СКМ-2. 97
7 Уточнение темпа работ для ведущей машины 99
8 Определение себестоимости машиносмен машин входящих в
состав СКМ-1 и СКМ-2 100
9 Определение технико-экономических показателей . 104
9.1 Определение трудоёмкости единицы продукции 104
9.2 Определение стоимости единицы продукции ..105
9.3 Определение энергоёмкости единицы продукции 106
9.4 Определение металлоёмкости единицы продукции 107
9.5 Экономическая эффективность работы СКМ-1 и СКМ-2 ..108
ТЕХНИКО-ЭКОНОМИЧЕСКИЕ ПОКАЗАТЕЛИ 112
1 Определение годовой эксплуатационной производительности 112
2 Определение годовых текущих издержек потребителя .118
3 Определение хозрасчетного экономического эффекта . .124
БЕЗОПАСНОСТЬ ЖИЗНЕДЕЯТЕЛЬНОСТИ ..126
1 Анализ вредных факторов ..127
2 Расчет устойчивости бульдозера Т-170 .136
3 Экологическая безопасность ..138
СПИСОК ИСПОЛЬЗОВАННЫХ ИСТОЧНИКОВ 142
В условиях все более интенсивного развития нефте-газодобычи в стране и в Омской области в частности возникает необходимость применения современных механизмов и оборудования. Одним из главных производственных процессов является расчистка и профилирование участков для строительства. Так при строительстве Крапивинского месторождения находящегося на севере нашей области куда доставка техники и оборудования затруднена и осуществляется только по зимнику весьма выгодно на мой взгляд было бы применение разработки данного дипломного проекта. Экономически выгодным и целесообразным было бы применение бульдозера с подпружиненными ножами при строительстве Тевризского газо-конденсатного месторождения а также при осуществлении губернаторской программы «Газификация Омской области».
Бульдозеры как навесное оборудование на тракторе тягачи и другие базовые машины широко распространены что объясняется простотой их конструкции высокой производительностью возможностью их использования в самых разнообразных грунтовых и климатических условиях и относительно низкой стоимостью выполненных работ. Применяются они в дорожном железнодорожном горнорудном мелиоративном и ирригационном строительстве. Бульдозеры приспособлены для прокладки дорог чистки снега сгребания торфа и выполнения землеройно-планировочных работ. В данном дипломном проекте производится модернизация бульдозера путем установки на него подпружиненных ножей отвала. Таким образом в связи с введением в конструкцию предлагаемого отвала подпружиненных секционных ножей за счет уменьшения потерь грунта при транспортировке и увеличения удельного напорного усилия резания увеличивается производительность бульдозерных работ. Все это дает возможность снизить затраты на проведение подготовительно-заключительных работ при строительстве.
ОБЛАСТЬ ПРИМЕНЕНИЯ БУЛЬДОЗЕРА НА БАЗЕ
Рисунок 1.1 - Бульдозер ДЗ - 110А на базе трактора Т – 170
Состоит бульдозер из базового трактора или тягача впереди навешен рабочий орган – отвал. Бульдозер – машина циклического действия. Рабочий цикл состоит из следующих операций: отвал бульдозера опускают ниже опорной поверхности на 50 200 мм в зависимости от категории грунта. При движении вперед заглубленный отвал режет стружку определенной толщины. После образования перед отвалом призмы грунта его транспортируют при переднем ходе на расстояние и одновременно подрезают материал. Подрезанием компенсируют потери грунта высыпающегося из призмы в боковые валики. Во время подхода к месту отсыпки грунта отвал поднимают при одновременном движении машины. Призма грунта ссыпается образуя штабель. После этого бульдозер с поднятым отвалом задним ходом откатывается в исходное положение для повторного резания.
Особое внимание при создании СДМ придают улучшению условий и облегчению труда машинистов что снижает их утомляемость и повышает производительность туда. С этой целью введен электростартерный запуск или управление пусковым двигателем дизеля из кабины оператора; снижены усилия на органах управления; применены удобные подрессоренные сиденья регулируемые по высоте и массе машинистов остекленные кабины с круговой обзорностью; существенно снижены шум и вибрация на рабочем месте; установлена вентиляция отопительные приборы кондиционеры аптечки термос. Комплекс приборов позволяет контролировать работу агрегатов и заправку топливом с рабочего места машиниста.
Облегчению условий работы машинистов способствует внедрение гидромеханических и электрических трансмиссий на базовых тракторах и тягачах применение автоматизированных систем при планировке которые сводят к минимуму затраты энергии для управления машиной и утомляемость машинистов.
Повышение надежности и срока службы машин обусловлено применение более высококачественных и высокопрочных конструкционных сталей и материалов повышением качества изготовления механизмов и деталей своевременным диагностированием и техническим обслуживанием СДМ соблюдением сроков проведения профилактических работ инструкцией по эксплуатации. Строгое выполнение правил эксплуатации сокращает количество неисправностей машины и повышает готовность ее к выполнению рабочих операций.
Эффективное использование техники требует высокой квалификации от машиниста знания устройства машины правил технического обслуживания и ремонта безопасной эксплуатации постоянного повышения знаний и профессионального мастерства овладения передовыми методами управления и эксплуатации.
Бульдозерами можно выполнять расчистку полосы отвода с удалением кустарника деревьев крупных камней растительного слоя снега и т. п.; планировку различных строительных площадок включая объекты дорожного строительства разравнивание грунтов в насыпях отсыпаемых другими машинами; перемещение и разравнивание экскаваторных и скреперных отвалов в кавальеры; разработку профильных выемок в кавальеры а там где возможно и в насыпи; возведение насыпей при перемещении грунтов из боковых резервов; засыпку ям и оврагов; устройство временных дорог и проездов; разработку песчаных и гравийных карьеров; перемещение и погрузку сыпучих материалов (песка гравия щебня и др.) в карьерах и на складах.
Бульдозеры – маневренные и высокоэффективные машины обладающие высокой проходимостью. На долю бульдозеров в дорожном строительстве приходится не меньше 50 % общего объема земляных работ.
Бульдозеры используют для выполнения основных видов землеройно-транспортных и вспомогательных работ на различных грунтах и в климатических условиях умеренной зоны с температурой окружающей среды от –400 до +400 холодного климата с температурой воздуха –600 а также в условиях тропиков с температурой до +500.
ТЕХНИЧЕСКАЯ ХАРАКТЕРИСТИКА
Таблица 2.1 - Техническая характеристика
С неповоротным отвалом
Тяговый класс базового трактора
Эксплуатационная мощность двигателя кВт
Скорость минимальная вперед кмч
Скорость максимальная назад кмч
Тип управления рабочим органом
Скорость подъема отвала мс
Основной угол резания
Минимальный диапазон изменения угла резания
Задний угол отвала не менее
Рабочее давление в гидросистеме МПа
Масса бульдозерного оборудования т
ОБОСНОВАНИЕ ДИПЛОМНОГО ПРОЕКТА И ОПИСАНИЕ
Интенсификация земляных работ осуществляется главным образом на базе создания и внедрения в производство принципиально новой технологии материалов создания машин большой единичной мощности и производительности и агрегатов работающих на основе использования новых технологических эффектов. Реализация этих положений основывается на повышении эффективности исследований и сокращения сроков внедрения достижений науки и техники в производство и модульного принципа создания систем машин. Оснащение строительства надежными высококачественными машинами ускоренная замена устаревшей техники новыми высокопроизводительными машинами выпуск машин с многофункциональными рабочими органами – манипуляторами и строительных роботов один из важных рычагов повышения эффективности работ в строительстве.
Создание высокопроизводительных землеройных машин осуществляется по двум направлениям: совершенствование рабочих органов и машин традиционного типа находящихся в настоящее время в эксплуатации и производство принципиально новых рабочих органов и машин на базе использования достижений фундаментальных наук.
Наряду с современными средствами автоматизации и механизации на оснащении дорожных организаций находятся машины устаревших конструкций но пригодные для эксплуатации. Списывать такую технику не всегда экономически целесообразно. Модернизация и восстановления путем агрегатного метода обеспечивает возможность её дальнейшей эксплуатации.
Вопросы эффективного использования новой а также имеющийся в дорожных организациях техники имеют большое значение. Важное условие повышения эффективности использования дорожных машин – правильная их эксплуатация которая зависит от технической подготовки персонала обслуживающего машины.
Под эффективным использованием строительно-дорожных машин в первую очередь понимается достижения максимальной производительности при высоких экономических показателях и высоком качестве работ. Достижение показателей может быть обеспечено организационными и техническими мероприятиями: целесообразным подбором машин для выполнения конкретных работ выбором рациональных схем работы машины применением вспомогательных устройств и приспособлений высоким мастерством машинистов.
Патентный поиск показал что существуют девять основных авторских свидетельств целью которых является расширение технологических возможностей бульдозерного оборудования. Принцип этих изобретений заключается в том на типовой отвал навешиваются дополнительные рабочие органы которые как раз и позволяют расширить технологические возможности рабочего оборудования.
АС 76 72 93 Е 02 F 3 76
Автор изобретения: А.В. Матвеев
Бульдозерное оборудование
Бульдозерное оборудование имеет отвал 1 установленный на толкающих брусьях 2 с помощью проушин 3 и распорок 4 (гидроцилиндры управления отвалом не показаны). На толкающих брусьях 2 приварены направляющие 5 в которых перемещаются катки 6 продольных штанг 7. Управляются продольные штанги с закрепленным на с помощью них днищем рычагов 8 которые закреплены в проушинах 9 на боковых стенках отвала 1 тяг 10 закрепленных в проушинах 11 продольных штанг и соединенных шарнирно с рычагами 8 и гидроцилиндров 12 которые с одной стороны установлены в проушинах 13 на толкающих брусьях 2 а с другой стороны в проушинах 14 закрепленных в средней части рычагов 8. Резание грунта осуществляется ножом 15 который расположен на продольных штангах 7.
Рисунок 3.1 –Эскиз бульдозерного оборудования
Цель изобретения – повышение производительности бульдозера путем обеспечения полной разгрузки. Указанная цель достигается тем что отвал выполнен составным из верхней части и нижней которая связана с толкающими брусьями посредством продольных штанг установленных на брусьях с возможностью возвратно-поступательного перемещения и с верхней частью отвала посредством шарнирных двузвенников причем днище закреплено на продольных штангах а гидроцилиндры разгрузки соединены с двузвенниками.
Недостатком указанного бульдозерного оборудования является значительные сопротивления возникающие при перемещении призмы волочения и большие потери грунта в боковые валики.
Бульдозерное оборудование работает следующим образом. В начале копания грунта бульдозером осуществляется выдвижение штоков гидроцилиндров 12 которые с помощью рычагов 8 и тяг 10 выдвигают продольные штанги с закрепленным днищем. После этого происходит опускание рабочего органа и заглубления ножа 15 днища в грунт обычным способом. Набранный грунт в призме волочения перемещается при этом не по грунту а на откатном днище что уменьшает сопротивление на перемещение бульдозера. Откатное днище позволяет к тому же набрать больший объем грунта в призму волочения.
АС 99 46 38 Е 02 F 376
Автор изобретения: А.В. Матвеев Д.Н. Сергеева Ф.И. Гутырчик А.П. Тесленок.
Бульдозер включает базовую машину 1отвал 2толкающие брусья 3 подвижный средний нож 4 который перемещается на катках 5 в направляющих отвала 2 с помощью шарнирных тяг 6 которые имеют на других концах продольные пазы взаимодействующие с пальцами 7 проушин 8 укрепленных на базовой машины 1 шарнирно установлены подпружиненные пружиной 9 двуплечие рычаги 10 и жестко закрепленные упоры 11.
Рисунок 3.2 – Эскиз бульдозерного оборудования
Целью изобретения является повышение производительности за счет исключения потерь грунта. Указанная цель достигается тем что в бульдозере концевые поверхности шарнирных тяг в месте их соединения с базовой машиной выполнены ступенчатыми а базовая машина имеет подпружиненные двуплечие рычаги смонтированные с возможностью взаимодействия одних из плеч с концевыми поверхностями шарнирных тяг и упоры закрепленные с возможностью взаимодействия с другими плечами двуплечих рычагов.
Введение в конструкцию бульдозера тяг со ступенчатыми концевыми поверхностями и подпружиненных двуплечих рычагов с упорами позволяет обеспечить повышение производительности за счет исключения потерь грунта под средним подвижным ножом.
Бульдозер работает следующим образом. При копании разработку грунта осуществляют в основном боковые ножи а средний нож в это время скользит по грунту или срезает стружку грунта малой толщины. Это обеспечивается тем что при опускании отвала 2 шарнирные тяги 6удерживают нож 4 и происходит относительное перемещение его вдоль направляющих отвала 2 вверх. При этом шарнирные тяги 6 верхними краями своих пазов взаимодействуют с пальцами 7 проушин 8.
АС 16 55 52 Е 02 F 376
Авторы: В.М. Лебедев А.А. Неверов Л.А.Бляхер
Бульдозерное оборудование.
Бульдозерное оборудование состоит из отвала выполненного из двух секций верхней 1 и нижней 2 соединенных между собой горизонтальным шарниром 3 и гидроцилиндров 4 управления наклоном секций. Нижняя 2 секция соединена шарнирно с толкающими брусьями 5 и 6 и механизмом 7 компенсации перекоса. Верхняя секция 1 опирается на нижнюю 2 через шарнир 3 а также на толкающие брусья 5 и 6 через подкос 8 и гидравлический подкос 9.
Таким образом конструкция выполнена так что верхняя 1 и нижняя 2 секции при запертом положении гидроцилиндров 4 управления наклоном секций представляет собой единый жесткий рабочий орган – отвал лобовая поверхность которого выполнена по заданному профилю .Отвал закреплен на толкающих брусьях 5 и 6 посредством подкоса 8 гидравлического подкоса 9 и механизма 7 компенсации перекоса. Для внедрения рабочего органа в грунт служат гидроцилиндры установленные на тракторе (не показаны).
Рисунок 3.3 – Эскиз бульдозерного оборудования
Бульдозерное оборудование включающее отвал выполненный из расположенных одна над другой шарнирно сочлененных секций подкосы гидроцилиндры управления наклоном секций связанные с верхними концами одной из секций отличающееся тем что с целью расширения технологических возможностей бульдозерного оборудования путем обеспечения поперечного перекоса отвала один из подкосов выполнен гидравлическим а гидроцилиндры управления наклоном секций нижними концами связаны с другой секцией отвала.
Бульдозерное оборудование работает следующим образом. После отвала в грунт и начала набора грунта водитель воздействуя на гидроподкос 9 может по необходимости изменить угол поперечного перекоса отвала что позволяет обеспечить разработку грунта повышенной прочности за счет работы углом отвала.
Недостатком этого оборудования является невозможность изменения угла поперечного перекоса и криволинейного профиля отвала .
АС 108 92 02 E 02 F 376
Авторы: Ю.А. Шевнин А.С.Абдурахманов П.Н.Шевнина Р.А.Тойчиев
Бульдозерное оборудование включает отвал 1 к которому посредством кронштейнов 2 и 3 по его торцам и в середине крепятся свободно вращающиеся диски 4 диаметром равные высоте отвала. Между дисками соосно установлены шнеки 5 и 6. Шнеки скреплены с дисками своими концами. Наружный диаметр шнеков уменьшается к центру отвала. Направление спирали шнеков таково что при рабочем движении бульдозера они стремятся перемещать грунт к центру отвала.
Бульдозерное оборудование отличающееся тем что с целью увеличения производительности путем обеспечения перемещения грунта к центру отвала снабжено установленными соосно между дисками и прикрепленным к ним своими концами шнеками винтовая поверхность каждого из которых выполнена убывающей к центру отвала.
Рисунок 3.4 – Эскиз бульдозерного оборудования
Бульдозерное оборудование работает следующим образом. При опускании отвала диски вместе с ножом отвала врезаются в грунт. В результате работе движения бульдозера вперед все диски начинают вращаться одновременно в сторону движения бульдозера. Набираемый грунт скользит по отвалу получая вращение которое усиливается в результате вращения установленных дисков. Когда перед отвалом набирается более половины объема призмы грунт получает дополнительную силу вращения вследствие вращения шнеков которые вращаются синхронно с дискамии. В результате вращения шнеков значительно сокращаются потери грунта в боковые валики в связи с перемещением грунта от краев отвала к центру. Поскольку витки шнеков имеют больший диаметр по их внешним краям захватывается больше грунта чем обеспечивается рациональное формование призмы грунта.
Недостатком оборудования является увеличение сопротивления перемещению и следовательно уменьшение производительности при работе на сухих и песчаных грунтах по причине малого сцепления между собой частиц этих грунтов вследствие чего грунт получает вращение только в непосредственной близости от дисков. При этом также происходят потери грунта в боковые валики.
АС 109 90 12 E 02 F 376
Авторы: В.А. Кацин В.П. Попов Н.В. Сакулин В.М. Куринский Г.Л. Батин
Бульдозерное оборудование включает толкающие брусья 1 шарнирно установленные на базовой машине 2 прямолинейные направляющие 3 шарнирно установленные на толкающих брусьях и соединенные между собой поперечной балкой 4 отвал 5 с режущими ножами 6.
На тыльной стороне отвала 5 жестко закреплены ребра 7 жесткости на которых в свою очередь жестко закреплены ползуны 8 установленные в направляющих 3 с приводом их перемещения в направляющих в виде гидроцилиндра 9 установленного на поперечной балке 4. На толкающих брусьях 1 шарнирно установлены гидроцилиндры 10 шарнирно соединенные своими штоками с прямолинейными направляющими 3. Поверхности 11 и 12 трения направляющих 3 и ползунов 8 выполнены из антифрикционного материала например второпласта с наполнителями такими как диазльфид молибдена бронза и другие.
Оборудование отличается тем что направляющие установлены на толкающих брусьях с возможностью поворота.
Бульдозерное оборудование работает следующим образом. В начале копания грунта направляющие 3 устанавливаются гидроцилиндром 10 в исходное положение. После этого осуществляют выдвижение штока гидроцилиндра 9 отвал 5 с ползунами 8 перемещается вниз по направляющим 3 и происходит заглубление отвала 5 с ножами 6 в разрабатываемый грунт.
Недостаток этого оборудования заключается в том что при внедрении отвала в грунт и при выглублении его из грунта возникают дополнительные сопротивления связанные с тем что при выполнении указанных операций отвал движется не по прямой а по радиусу центром которого является шарнир крепления толкающих брусьев к базовой машине. Особенно эти нагрузки сказываются при выглублении отвала из массы грунта при котором одновременно поднимается часть грунта находящегося в призме волочения. Указанные недостатки приводят к снижению эффективности разработки грунта .
Рисунок 3.5 – Эскиз бульдозерного оборудования
АС 82 77 00 E 02F 376
Авторы: В.И. Баловнев В.В. Мелашич С.А. Макаров В.Г. Попов
Бульдозерное оборудование состоит из отвального листа 1 боковых стенок 2 ножей 3 козырька 4 толкающих брусьев 5 гидроцилиндров 6. Отвальный лист 1 с боковыми стенками 2 соединен с помощью шарниров 7 а в верхней части с тыльной стороны к отвалу 1 прикреплены рычаги 8 с которыми шарнирно соединены штоки гидроцилиндров 9 корпуса которых установлены на козырьке 4.
С тыльной стороны козырька 4 установлена криволинейная пластина 10.
Рисунок 3.6 – Эскиз бульдозерного оборудования
Целью настоящего изобретения является повышение производительности.
Указанная цель достигается тем что бульдозерное оборудование снабжено соединительным козырьком гидроцилиндрами поворота отвальной части и прикрепленной к тыльной стороне козырька дугообразной пластиной с центром кривизны на оси поворота отвальной части причем последняя шарнирно соединена с ножом а козырек жестко соединен с боковыми стенками.
Бульдозерное оборудование работает следующим образом. В процессе копания отвал 1 с помощью гидроцилиндров 9 удерживается в крайнем левом положении. Грунт вырезается ножами 3 и скользит по отвалу 1 образуя призму волочения. В процессе транспортировки когда впереди отвала образовалась значительная призма волочения отвал 1 под воздействием усилий развиваемый гидроцилиндрами 9 поворачивается на шарнирах 7 по часовой стрелке на определенный угол. Кроме того с помощью гидроцилиндров 6 отвал 1 вместе с боковыми стенками 2 ножами 3 дополнительно поворачивается посредством гидроцилиндров 6.
Боковые стенки 2 и криволинейная пластина 10 служат для предотвращения потерь грунта при транспортировке.
Недостатком указанного бульдозерного оборудования является то что при транспортировке грунта возникают значительные сопротивления от сил трения грунта по грунту что в конечном счете отрицательно сказывается на производительности.
АС 84 46 98 E 02 F 376
Рабочий орган имеет отвал 1 и боковые открылки 2. За ножом 3 установливается стружкоколом 4 с отверстиями 5 для пропуска воздуха из ресивера 6. Отвал при помощи толкающих брусьев 7 крепится к базовой машине. Для изменения положения отвала установлены пневмоцилиндры 8 выполняющие роль раскосов.
Рисунок 3.7 – Эскиз бульдозерного оборудования
Целью настоящего изобретения является повышение производительности работы оборудования путем снижения сопротивления грунта копанию.
Работает указанный рабочий орган следующим способом. Отвал 1 опускается грунт и при движении базовой машины заглубляется в него. Грунт подрезается ножом 3 и стружка при своем движении встречает на своем пути стружколом 4 изгибается и направляется вверх. При изгибе стружки грунт в ней нарушает свое структурное состояние и разрушается. Через отверстия 5 подается воздух из ресивера 6 и своим потоком захватывает частицы разрушенного грунта и транспортирует их в вертикальной плоскости через толщу грунта призмы волочения.
При помощи пневмоцилиндров 8 изменяется положение отвала относительно плоскости резания грунта.
Недостатком данного оборудования состоит в том что снижается маневренность машины и поступающий воздух на поверхность отвала только снижает трение грунта по металлу отвала но не сокращает путь его движения(грунт преодолевает путь от ножа до козырька отвала т.е. высшей его точки как и у традиционного отвала что в целом отрицательно сказывается на производительности машины).
АС 96 82 09 E 02 F376
Авторы: А.Ф. Кичигин В.П. Степаненко А.И. Эбин Ю.Н. Надемский Г.С. Фурто В.М. Бандуров А.В. Рыбко А.А. Гарцбейн В.Н. Шевченко
Отвал 1 бульдозера 2 включает режущие ножи 3 с зубьями 4 и 5 имеющими одинаковую длину. Боковые кромки 6 смежных зубьев 4 и 5 расположены в одной вертикальной плоскости а режущие кромки 7 смещены по высоте и направлению резания.
Целью изобретения является снижение энергоемкости процесса резания грунта.
Поставленная цель достигается тем что боковые кромки смежных зубьев расположены в одной вертикальной плоскости а режущие кромки – со смещением по высоте и направлению резания при этом расстояние между режущими кромками смежных зубьев по направлению резания равно 02-04 длины зуба а ширина зуба -06-12 длины зуба. Величины смещений режущих кромок S определяют аналитически или графически. При постоянном угле резания зубьев 5 =60°.
Рисунок 3.8 – Эскиз бульдозерного оборудования
Отвал работает следующим образом. При движении бульдозера отвал заглубляет в грунт и зубья входят в контакт с грунтом. Резание грунта осуществляется в послойном решении благодаря смещению зубьев ножа. При этом снижение энергоемкости процесса резания грунта обеспечивается за счет создания суммарного критического напряженного состояния массива грунта между участками приложения нагрузок взаимно смещенными зубьями.
2 Описание предлагаемой конструкции
Наибольший инетерес на мой взгляд представляет АС 115 71 74 E 02 F 376
Авторы: А.М. Щемелев
Отвал бульдозера включает лобовой лист 1 который в нижней части разделен на секции таким образом что одна часть отдельной поверхности состоящая из секций 2 выступает вперед а другая часть отвала состоящая из секций 3 смещена назад. К секциям 2 крепятся при помощи болтов ножи 4. У секций 3 ножи 5 выполнены подвижными в вертикальной плоскости и могут перемещаться по лицевой стороне лобового листа секций 3 между ребрами 6 коробки жесткости отвала. К тыльной стороне ножей 5 прикреплены ребра 7 и 8 на которые установлены пальцы 9 с пружинами 10. К тыльной стороне 11 лобового листа 1 крепятся кронштейны 12 через которые проходят пальцы 9. Установка ножей 5 и регулирование жесткости пружин производится при помощи гаек 13. Для возможности вертикального перемещения ножей 5 в лобовом листе секции 3 выполнены окна 14. ри выполнении планировочных работ кромки ножей 4 и 5 должны быть выставлены на одном уровне поэтому для ограничения хода ножа 5 устанавливаются стопорные планки 15.
Рисунок 3.9 – Эскиз бульдозерного оборудования
Рисунок 3.10 – Эскиз бульдозерного оборудования
Бульдозерное оборудование отличающееся тем что с целью повышения производительности ножи расположенные на задних секциях нижней части лобового листа смонтированы с возможностью перемещения в вертикальной плоскости и подпружинены с возможностью регулирования их жесткости.
Работа отвалом производится следующим образом. При заглублении отвала подпружиненные ножи 5 сжимают пружины 10 и перемещаются вверх. Перемещение ножей вверх происходит до тех пор пока усилие сжатия пружин 10 достигнет величины удельной несущей способности грунта. До этого момента заглубление ножей 5 происходить не будет. Усилие заглубления (удельное вертикальное напорное давление) будет сосредоточено вначале на ножах 4 что позволяет отвал на более прочных грунтах. При транспортировании грунта перед отвалом с одновременным резанием прочного грунта подпружиненные ножи 5 скользят по поверхности грунта и потерь грунта под ножами 5 не будет. При копании грунта скол грунта происходит периодически перед секциями 2 или 3. За счет этого уменьшается динамика рабочего процесса бульдозера.
Таким образом в связи с введением в конструкцию предлагаемого отвала подпружиненных секционных ножей за счет уменьшения потерь грунта при транспортировке и увеличения удельного напорного усилия резания увеличивается производительность бульдозерных работ.
КОНСТРУКТОРСКИЙ РАЗДЕЛ
Задача расчета состоит в том чтобы определить возникающие при копании и транспортировании грунта отвалом бульдозера по горизонтальной площадке сопротивления и усилия.
Таблица 4.1 - Исходные данные к расчету
Удельное сопротивление резанию нм²
Коэффициент разрыхления
Угол естественного откоса °
Объемная масса грунта тм³
Коэффициент потерь грунта
Рассмотрим вопросы тягового расчета применительно к наиболее распространенному способу работы лобовому толканию грунта при бестраншейном способе работ.
Объем призмы волочения Vпр зависит от геометрических размеров отвала и свойств грунта 1.
где L - ширина отвала м;
H – высота отвала c учетом козырька м;
kп – коэффициент зависящий от характера грунта (связности коэффициента разрыхленности грунта) и отношения НL 1 kп=09.
При транспортировании грунта отвалом бульдозера по горизонтальной площадке возникают следующие сопротивления
Wр – сопротивление резанию кН;
Wпр – сопротивление перемещению призмы грунта перед отвалом кН;
Wс – сопротивление перемещению грунта вверх по отвалу кН;
Wт – сопротивление перемещению бульдозера кН;
Wтр – сопротивление трению ножа бульдозера о грунт кН.
Сопротивление резанию определяется по формуле 1
где k – удельное сопротивление лобовому резанию 1 k=110 кНм²;
В – ширина отвала В=32 м;
- глубина резания во время перемещения грунта м.
где kп – коэффициент потерь грунта в боковые валики на 1 м пути ;
Vп – объем призмы волочения Vпр=3 м³;
В – ширина отвала В=32 м.
Потери грунта в боковые валики на 1 м равны 1
где Vв – объем грунта в плотном теле на 1 м пути Vв=0045 м³;
Vпр – объем призмы волочения м³.
Сопротивление перемещению призмы грунта перед отвалом 1.
где Vпр – объем призмы волочения м³ ;
- объемный вес грунта в плотном теле;
- коэффициент трения грунта по грунту =05;
- вес призмы волочения.
Сопротивление перемещению грунта вверх по отвалу 1
где- вес призмы волочения =4704 кН ;
d - угол резания d=55°;
- коэффициент трения грунта по металлу =05.
Сопротивление перемещению бульдозера 1
где G – вес трактора и бульдозера кН;
f – коэффициент сопротивления перемещению движителей бульдозера f=011.
Сопротивлением трения ножа бульдозера о грунт пренебрежем.
Итак сопротивление копанию грунта бульдозером равно
Wк=Wр+Wпр+Wв+Wт (4.8)
Wк =493+235+774+182=544 кН.
Имея ввиду что сопротивление грунта копанию преодолевается силой тяги базового тягача можно отметить
где Тн – сила тяги бульдозера кН .
где j - коэффициент сцепления движителя с грунтом j = 09.
Тн =165×09 = 1485 кН;
Из проведенных выше расчетов следует что выбранный базовый трактор и тяговый класс позволяет работать бульдозеру в заданных режимах.
2 Определение нагрузок на отвале и расчет на прочность навесного оборудования бульдозера
2.1 Первое расчетное положение
Внезапный упор в препятствие крайней точкой отвала;
Рисунок 4.1 – Схема для определения действующих сил
Бульдозер двигается по горизонтальной поверхности вперед; цилиндры находятся в запертом положении.
Сила Р1 определяется тяговыми возможностями трактора и действием динамических сил при упоре отвала в препятствие. Максимальная сила Р1 рассматриваться как сумма статической силы Р1с соответствующей условию буксования движителей а динамической силы Р1д зависящей от инерции движущихся масс и жесткостей препятствия и элементов конструкции.
Р1max= Р1с+ Р1д. (4.10)
Рисунок 4.2 – Схема действия сил на кромку ножа
Максимальная сила Р1с согласно 1 определяется из уравнения
Р1с =Тmax =Gсц×j max (4.11)
где Gсц – сцепной вес бульдозера кН ;
Р1с = 168×9.8×0.85 = 140 кН.
Динамическая составляющая Р1д определяется рассматриванием машины и препятствия как упругой системы с одной степенью свободы. Принимаем массу препятствия бесконечно большой а начальную скорость буксования равной номинальной скорости машины на первой передаче.
где - скорость движения бульдозера в момент встречи с препятствием = 3 кмч = 833 смс=083 мс ;
- сила тяжести бульдозера вместе с навесным оборудованием =165 кН ;
- суммарная жесткость препятствия ;
g - ускорение свободного падения g= 981 .
где - коэффициент жесткости навесного оборудования ;
- коэффициент жесткости препятствия .
где коэффициент жесткости навесного оборудования трактора ;
GГ – вес трактора GГ =138 кН .
где коэффициент жесткости препятствия на 1см длины отвала
B - длина отвала см .
Динамическая составляющая горизонтального усилия
Максимальная составляющая горизонтального усилия
Р1maх =140+2491 = 3891 кН.
Определение максимальной вертикальной составляющей реакции препятствия на грунт
где - максимальная вертикальная составляющая реакции препятствия на грунт кН ;
d - угол резания отвала d = 55°;
j1 – угол внутреннего трения j1 = 28° .
Определение расчетной силы подъема отвала
где Sр – расчетная сила подъемная сила отвала кН ;
Sу – сила подъема отвала кН ;
k д – коэффициент динамичности k д = 25 .
Рисунок 4.3 – Схема к определению сил
Для нахождения силы подъема отвала Sу определим сумму моментов сил относительно точки С
Рисунок 4.4 – Расчетная схема толкающего бруса
Sр = 2.5·2255=5638 кН.
Определение реакций в шарнире.
Из условий равновесия рабочего оборудования находим находим силы в шарнире С1
Сила в подкосе и реакции в шарнире А1 определяется из условий равновесия толкающего бруса
где - плечо силы м ;
Найденное значение силы в подкосе соответствует случаю одинакового нагружения правого и левого подкоса . Учитывая возможность неравномерного распределения нагрузок между подкосами допускаем что работает лишь один из них и за расчетное значение силы в подкосе принимаем удвоенное значение силы :
Проектируем силы на оси и складывая проекции получим
В опасном сечении бруса aa действует изгибающий момент в плоскости
Также в опасном сечении действует изгибающий момент в плоскости
Помимо изгибающих моментов в сечении действует сжимающая сила
Проверка прочности бруса в сечении производится по уравнению согласно 1
где -момент сопротивления относительно оси Y ;
момент сопротивления относительно оси Z ;
FБ – площадь поперечного сечения бруса ;
- коэффициент уменьшения допускаемых напряжений для сжатых стержней=085 .
- максимально-допустимое напряжение = па .
где а – сторона квадрата а=017 м .
Проверка на прочность сошлась.
Определение усилий действующих на отвал
Рисунок 4.5 – Схема приложения усилий на отвал
Рисунок 4.6 – Схема сил действующих на бульдозер
Определение вертикального усилия РZ согласно 22
где - вес трактора кН ;
- расстояние от силы тяжести трактора до точки А =125 м ;
- расстояние от силы тяжести трактора до точки В =09 м ;
Определение бокового усилия согласно 22
где GБ- вес бульдозера Кн ;
B – ширина отвала м;
- максимальный коэффициент сцепления гусеничного движителя с грунтом =095 .
Определение горизонтального усилия согласно 22
где - скорость движения бульдозера в момент встречи с препятствием =3 кмч = 833 смс=083 мс;
2.2 Второе расчетное положение
Копание углом отвала с реализацией максимальной тяги и выглублением отвала.
Бульдозер движется по горизонтальной поверхности вперед гидроцилиндры развивают усилие достаточное для опрокидывания трактора относительно точки В (расчетная схема N 6).
Горизонтальное усилие на отвале P’y принимается равным максимальной силе тяги по сцеплению т.к. она обеспечивается свободной мощностью двигателя.
где φ – коэффициент сцепления максимальный φ=095;
Gт – вес бульдозера Кн .
P1 = 095·168 = 1596 кН.
Рисунок 4.7 – Схема приложения сил
Вертикальное усилие на отвале определяется из условия вывешивания машины относительно точки В.
Рисунок 4.8 – Схема приложения сил
Усилие в гидроцилиндре определяется из условия равновесия бульдозерного оборудования относительно оси упряжных шарниров (точки С) без учета P1.
Работает штоковая полость гидроцилиндра. Площадь сечения штоковой полости определяется по формуле
где d – диаметр штока гидроцилиндра d=006 м;
D – диаметр гидроцилиндра D=0122 м .
Давление в штоковой полости определяется из условия вывешивания
Одновременно с выглублением возможно движение машины с использованием максимальной по сцеплению силы тяги. Для данного случая определим максимально возможное вертикальное усилие на отвале при давлении в цилиндре 16 мПа.
Усилие в гидроцилиндре
Определение максимального усилия
Рисунок 4.9 - Схема приложения усилий на отвал
Определение вертикального усилия (см.рис.4.8)
Определение бокового усилия
Определение горизонтального усилия
2.3 Третье расчетное положение
Внезапный упор в препятствие средней точкой отвала.
Бульдозер движется по горизонтальной поверхности вперед гидроцилиндры находятся в запертом положении.
Определение горизонтальной составляющей Р1С согласно 1
где GT – вес трактора кН ;
G – вес навесного бульдозерного оборудования кН ;
- максимальный коэффициент сцепления гусеничного движителя с грунтом =085 ;
- угол резания =55° ;
- угол внутреннего трения =28° .
Определение максимальной составляющей силы Р2
Определение расчетной силы подъема отвала
В данном расчетном положении производится расчет на прочность отвала бульдозера. На отвал кроме сил Р1 Р2 и Sр действует сила тяжести отвала Gо и реакции в шарнирах и в подкосах РВ1 и РВ2 .
Рисунок 4.10 – Схема сил действующих на отвал
Рассматриваем отвал как балку шарнирно закрепленную в точках А1 и А2 пренебрегая при этом моментами в горизонтальной плоскости действующими на отвал со стороны толкающих брусьев при изгибе системы что ведет к незначительному увеличению запаса прочности.
Рисунок 4.11- Расчетная схема отвала
Допускаем что размеры и формы сечения отвала постоянны по его длине и соответствуют опасному сечению.
Рисунок 4.12 – Схема для определения усилий и напряжений в опасном сечении
Определив положение центра тяжести сечения О и направление главных осей инерции сечения X и Z приводим силы Р1 Р2 и Sр к точке О и раскладываем их на составляющие по осям X и Z .В сумме эти составляющие образуют силы Qx и Qz .
Силу тяжести отвала рассматриваем как равномерно распределенную нагрузку
Под действием внешних сил в сечении аа возникают изгибающие моменты в плоскости xOy и в плоскости yOz и крутящий момент
Изгибающие моменты и определяют по формулам согласно 1
Крутящий момент определяется как половина суммы моментов сил Р1 Р2 Sр и Go относительно центра жесткости(центра изгиба сечения) .
Координаты центра жесткости приближенно определяют по формулам
где -модуль упругости материалов элементов сечения мПа ;
-моменты инерции элементарных фигур составляющих профиль сечения ;
-координаты центров тяжести элементарных фигур .
Рисунок 4.13 – Схема отвала
Определение момента инерции профиля ABCD
Рисунок 4.14 – Схема для определения момента инерции сектора
где -момент инерции профиля ABCD относительно оси
r 1– радиус профиля до внутренней стенки r 1 = 128 м ;
r - радиус профиля r =1268 м ;
а – угол кругового сектора а=160° .
где -момент инерции профиля ABCD относительно оси z .
Xabcd = 013 м Zabcd =032 м.
Определение момента инерции профиля NKLD
Профиль NKLD представляет собой швеллер стальной горячекатанный по ГОСТ 8240-72
= 0000004 согласно 6
XNKLD =008 м ZNKLD =016 м
Определение момента инерции профиля EG
Профиль EG представляет собой швеллер стальной горячекатанный по
= 0000003 согласно 6
=00000003 согласно 6
XEG =00024 м ZEG =006 м
Определение координат центра жесткости отвала
[0130;0321]-координаты центра жесткости отвала
В сечении аа действуют нормальные напряжения от изгибающих моментов и касательные напряжения от крутящего момента Мк .
Нормальные напряжения находятся по уравнению согласно 1
где - главные моменты инерции ;
-координаты точки сечения наиболее удаленной от нейтральной линии.
=0039+00000079+0000003=00391
=0029+0000004+00000003=0029 .
Тангенс угла наклона нейтральной линии к оси x определяется по формуле
Xo =016 м ;Zo = 0156 м
Определение касательных напряжений
Определение касательных напряжений действующих в опасном сечении отвала аа связано со значительными трудностями ввиду сложной формы сечения. Отвал представляет собой тонкостенный пустотелый стержень подвергающийся кручению совместно с изгибом. В этом случае возникает стесненное кручение. Для упрощения задачи расчет касательных напряжений производим применительно к случаю свободного кручения. Такое допущение не приведет к значительной погрешности поскольку профиль сечения включает в себя замкнутый контур со значительной крутильной жесткостью и напряжения стесненного кручения для такого профиля имеет второстепенную роль.
Определение крутящего момента приходящегося на каждую часть сечения
где -момент инерции кручения для всего сечения ;
-момент инерции для профиля DNKL ;
крутящий момент инерции для сечения AMKL кН·м .
где -момент инерции для профиля AB ;
крутящий момент инерции для сечения AB кН·м .
где -момент инерции для профиля EG ;
крутящий момент инерции для сечения EG кН·м .
Моменты инерции для замкнутых контуров определяются согласно 1
где F0 –площадь заключенная внутри средней линии контура ;
толщина стенки элементов контура м ;
-длина средней линии элементов контура м .
Моменты инерции для незамкнутого контура имеющего форму кольца
где S – длина средней линии всего контура м .
Полный момент инерции при кручении определяется по уравнению
Касательные напряжения для замкнутых профилей AMKL и EG определяются по формуле
Касательные напряжения для незамкнутого профиля MB
Суммарное касательное напряжение определяется по формуле
Проверку на прочность сечения производим по уравнению
где -максимально допустимое напряжение =520 мПа .
Рисунок 4.15 – Схема усилий действующих на отвал
где GСЦ – сцепной вес бульдозера кН .
2.4 Четвертое расчетное положение
Копание центром отвала с реализацией максимальной тяги и одновременным выглублением отвала.
Бульдозер движется по горизонтальной поверхности вперед; гидроцилиндры развивают усилие достаточное для опрокидывания трактора относительно точки В (см. рис.4.7)
Рисунок 4.16 – Схема усилий действующих на отвал
Определение вертикального усилия РZ
3 Выбор гидроцилиндра подъема отвала
Рассмотрим бульдозер с гидроприводом движущийся по горизонтальной поверхности происходит заглубление отвала в грунт и одновременно упор в препятствие или в более плотный грунт. При этом бульдозер начинает опрокидываться вокруг задней точки В.
Рисунок 4.17 – Схема опрокидывания бульдозера относительно точки В
Р1 =Тmax =Gсц×j max (4.67)
Р1 = 168×9.8×0.85=1399 кН.
Рисунок 4.18 – Схема сил действующих на навесное оборудование
Отбросим трактор и найдем усилие в цилиндре SЦ
Определение диаметра гидроцилиндра
где DЦ – диаметр гидроцилиндра м ;
pН – нормальное давление жидкости в гидроцилиндре Па .
Рассмотрим работу бульдозера когда отвал зацепился за препятствие машина практически остановилась и оператор пытается отвал при этом происходит опрокидывание трактора вокруг передней точки А.
Рисунок 4.19 – Схема сил действующих на бульдозер
Отбросим трактор и найдем усилие SЦ2
Определение диаметра цилиндра
где рMAX – максимальное значение давление Па ;
dЦ – диаметр штока гидроцилиндра dЦ =006 м
рMAX =рНОМ ·(11-12) (4.80)
Выбираем гидроцилиндр 1.16.ОУ-122×60×1300
4 Расчет производительности бульдозера
Производительность бульдозера при резании и перемещении грунта определяется согласно 1
где КВ – коэффициент использования бульдозера по времени КВ =085 ;
КУКЛ – коэффициент учитывающий влияние уклона на производительность бульдозера КУКЛ =1 ;
ТЦ – длительность цикла с ;
VФ – объем грунта (в плотном теле) перед отвалом
Длительность цикла определяется выражением согласно 1
где -длина пути перемещения грунта =70 м ;
-длина пути резания =10 м ;
- скорость движения бульдозера при копании грунта =045 м.с ;
-скорость движения бульдозера при перемещении грунта =095 мс ;
- скорость обратного холостого движения трактора =115 мс ;
- время на опускание отвала =15 с ;
- время на переключение передач =45 с ;
-время необходимое на разворот =10 с .
Рисунок 4.20 – Схема модернизированного отвала
где B – ширина отвала м ;
H – высота отвала м ;
КПР – коэффициент зависящий от характера грунта КПР = 09 ;
КР – коэффициент разрыхления грунта КР =12 .
4.2 Расчет производительности бульдозера с обычным отвалом
Рисунок 4.21 – Схема обычного отвала
Итак после данного расчета можно сделать вывод что производительность у модернизированного отвала выше чем у обыкновенного.
5 Выбор пружин для модернизированного отвала
Пружины для модернизированного отвала выбираются исходя из следующих данных 6 :
Сила Р1 действующая со стороны грунта на отвал; площадь S кромки ножа давление на грунт р. Исходя из этих данных выбираем 4 пружины сжатия со следующими параметрами:
Расчетные данные по пружине сжатия N289 ГОСТ 13766 - 86
ПАРАМЕТР ОБОЗНАЧЕНИЕ ВЕЛИЧИНА
Наружный диаметр: D1 (мм) 7.000
Внутренний диаметр: D2 (мм) 4.800
Диаметр проволоки: d (мм) 1.100
Рабочий ход: h (мм) 10.020
Усилие предварительной деформации: F1 (H)20.000
Рабочее усилие: F2 (H) 40.000
Усилие максимальной деформации: F3 (H) 50.000
Число рабочих витков: n 35.000
Полное число витков: n1 36.500
Критическая скорость сжатия пружины: Vk(мс) 4.063
Длина пружины в свободном состоянии: L0 (мм) 64.650
Длина пружины при предварительной деформации:L1 (мм) 54.630
Длина пружины при рабочей деформации: L2 (мм) 44.610
Длина пружины при максимальной деформации: L3 (мм) 39.600
Максимальное касательное напряжение пружины: TAU3 (МПа) 861.494
Жесткость одного витка: C1 (Hмм) 69.860
Наибольший прогиб одного витка: s1 (мм) 0.715
Жесткость пружины: C (Hмм) 1.996
ТЕХНОЛОГИЯ ВОССТАНОВЛЕНИЯ ЗУБЧАТОГО КОЛЕСА
В данном подразделе производим описание технологии восстановления зубьев приводной шестерни механизма газораспределения.
Рисунок 5.1 – Эскиз шестерни
Как конструктивный элемент приводная шестерня является деталью блок – картера. Она предназначена для передачи крутящего момента от коленчатого вала двигателя к промежуточной шестерни механизма газораспределения. При этом зубья шестерни испытывают высокие контактные напряжения и поэтому подвергаются значительному износу они изменяют свои геометрические размеры появляется люфт в передаче. В данной части рассмотрен процесс восстановления зубчатого колеса.
1 Расчет маршрута восстановления детали
-износ зубьев зубчатого колеса коленчатого вала.
Способ восстановления:
) наплавить изношенную поверхность вибродуговой наплавкой;
) произвести токарную обработку детали;
) выполнить фрезерование зубьев;
) выполнить химико-термическую обработку зубьев;
) произвести шлифование зубьев.
2 Расчет режимов выполняемых операций
2.1 Назначение припусков на механическую обработку
Задачей расчета является определение размеров наплавленной детали с учетом припусков на механическую обработку.
Исходные данные для расчета: геометрические размеры приводной шестерни в соответствии с рисунком:
Рисунок 5.2 – Расчетная схема для определения припусков на механическую
Расчетный наименьший предельный диаметр детали определяем по формуле
где - наименьший предельный диаметр шестерни по чертежу ;
- расчетный минимальный общий припуск на обработку по диаметру мм.
Общий припуск определяем по формуле
- допуск на величину припуска мм.
Допуск на величину припуска определяем по формуле
Таким образом для определения общего припуска на механическую обработку по диаметру необходимо назначить величины промежуточных припусков. Согласно рекомендации на обработку заготовки по поверхности А (см. рисунок 5.2) назначаем следующие величины промежуточных припусков:
на черновое точение Z1=2 мм;
на чистовое точение Z2=05 мм.
Определяем допуск на величину припуска по формуле
Определяем общий припуск по формуле
Далее рассчитываем наименьший предельный диаметр заготовки
Полученное значение диаметра детали должно получиться после операции наплавки.
2.2 Расчет режимов наплавки
В качестве электродов применяется высокоуглеродистая проволока Нп 80 диаметром 35 мм рекомендуемая для восстановления коленчатых валов крестовин деталей ходовой части.
-токарный станок с наплавляющей головкой ОКС-6569 с механическим вибратором.
Величина силы сварочного тока определяется по формуле
где - диаметр электродной проволоки .
Скорость подачи электродной проволоки может быть подсчитана по формуле
где – скорость подачи проволоки мч; I – сила тока А; U – напряжение U =14 – 20 В; – диаметр электродной проволоки мм.
Процесс вибродуговой наплавки в среде углекислого газа будет состоять из двух этапов:
)наплавка впадин зубчатого колеса (вдоль оси колеса);
)наплавка внешней поверхности колеса (по ходу вращения колеса).
Расчеты этих этапов будет различаться.
Скорость наплавки рассчитывается по формуле
где – скорость наплавки мч; – коэффициент перехода электродного материала в наплавленный металл принимают равным 09; h – заданная толщина наплавленного слоя (без механической обработки) мм; h=33мм ; S –шаг наплавки ммоб; ; a – коэффициент учитывающий отклонения фактической площади сечения наплавленного слоя от площади четырехугольника с высотой h a = 08.
Частота вращения детали при наплавке цилиндрических поверхностей определяется только для второго этапа по формуле
где -диаметр наплавляемой детали мм; .
Амплитуда колебаний определяется
Норма времени на выполнение наплавочных работ складывается из следующих элементов затрат времени
где – основное время определяется по следующей формуле
где - длина наплавляемой поверхности м;
- скорость наплавки .
Длина наплавляемой поверхности определяется произведением количества витков проволоки необходимых для заполнения впадин колеса (определяется графически) на ширину зубчатого венца и на число наплавляемых зубьев
- вспомогательное время наплавки ;
- дополнительное время определяется по формуле
где К=14 % – коэффициент учитывающий долю дополнительного времени от основного и вспомогательного.
– время подготовительно-заключительное .
Тогда норма времени на выполнение первого этапа наплавки равно
Основное время определяется по формуле
-диаметр наплавляемой детали мм; .
- дополнительное время определяется по формуле (5.12)
2.3 Расчет режимов резания и нормирование операций токарной
Задачей расчета является определение режимов резания и норм времени на проведение операций.
Токарная обработка включает в себя следующие операции:
установка детали в станке;
проточить поверхность в размер «1» начерно;
проточить поверхность в размер «1» начисто;
снять деталь со станка.
Рисунок 5.3 – Токарная обработка детали
В качестве оборудования для данной операции выбираем токарный станок 16К20 резец проходной из твердого сплава Т15К6.
Назначаем режим резания для чернового точения:
глубина резания t = 2 мм;
по диаметру обрабатываемой поверхности и в зависимости от материала детали выбираем величину подачи S = 1 ммоб.
Скорость резания V ммин определяем по формуле
где Сv – табличный коэффициент Сv = 340;
Т – период стойкости инструмента Т = 40 мин;
kv – поправочный коэффициент.
где kмv – коэффициент учитывающий влияние физико-механических свойств обрабатываемого материала на скорость резания;
где kг – коэффициент характеризующий группу стали по обрабатываемости
nv – показатель степени nv = 10;
- предел прочности материала на растяжение = 720 МПа;
kпv-коэффициент отражающий состояние поверхности заготовки kпv=09;
kиv-коэффициент учитывающий качество материала инструмента kиv=10.
Подставляем найденное значение в формулу и находим скорость резания при черновом точении
Определим частоту вращения шпинделя станка n мин-1 по формуле
где d – диаметр обрабатываемой поверхности d = 20338 мм.
Норму времени на черновое точение определяем в соответствии с рекомендацией.
Штучно-калькуляционное время Тшт.к мин определяем по формуле
где То – основное время мин;
Тв – вспомогательное время мин;
Тд – дополнительное время мин;
Тп.з – подготовительно-заключительное время мин;
- количество деталей в партии
Основное время определяем по формуле
где L – расчетная длина обрабатываемой поверхности L = 54 мм.
Вспомогательное время Тв на установку детали определяем в зависимости от её массы и способа установки согласно рекомендации Тв = 15 мин.
Дополнительное время Тд мин определяем по формуле
где Топ – оперативное время мин;
Топ = 025 + 150 = 175 мин;
k – отношение дополнительного времени к оперативному при токарной
Подготовительно-заключительное время Тп.з мин выбираем в зависимости от сложности работы и размеров станка согласно рекомендации Тп.з= 10 мин.
Тшт.к= 025 + 15 + 014 + 101 = 1189 мин.
Назначаем режимы резания для чистового точения:
глубина резания t = 05 мм;
количество проходов
подача S = 035 ммоб.
Скорость резания V ммин для чистового точения определяем по формуле с учетом изменения входящих в формулу коэффициентов:
Сv – табличный коэффициент Сv = 350;
kмv – коэффициент учитывающий влияние физико-механических свойств
обрабатываемого материала kмv = 104;
kпv –коэффициент отражающий состояние поверхности заготовки kпv=1.
Тогда поправочный коэффициент будет равен
Частоту вращения шпинделя станка n мин-1 определяем по формуле (5.16)
Основное время определяем по формуле (5.18)
Вспомогательное время на чистовую обработку детали равно вспомогательному времени на черновую обработку детали: Тв = 15 мин.
Дополнительное время определяем по формуле (5.19)
Подготовительно-заключительное время для чистового точения как и при черновом точении равно Тп.з= 10 мин.
Штучно-калькуляционное время для чистового точения Тшт.к мин определяем по формуле (5.17)
В результате расчетов были определены следующие режимы токарной обработки детали:
1 подача S = 2 ммоб;
2 скорость резания V = 143 ммин;
3 штучно-калькуляционное время Тшт.к = 1189 мин;
1 подача S = 035 ммоб;
2 скорость резания V = 279 ммин;
3 штучно-калькуляционное время Тшт.к = 12 мин.
2.4 Расчет режимов фрезерования и нормирование фрезерной операции
Задачей расчета является определение режимов резания и норм времени на проведение операции фрезерования зубьев ведущей шестерни.
Исходные данные для расчета:
модуль зубьев m = 363;
число зубьев z = 54;
материал детали – сталь 20Х.
Операция зубофрезерования включает в себя:
установить деталь в приспособление;
фрезеровать зубья с припуском под шлифование;
В качестве оборудования для операции фрезерования принимаем горизонтально-фрезерный станок 6Р82Ш инструмент – дисковая модульная фреза.
Основные параметры фрезы:
модуль фрезы m = 3 375;
диаметр фрезы О = 80 мм;
число зубьев фрезы z0 = 12;
ширина фрезы В = 14 мм.
Назначаем режимы резания для фрезерования зубьев в соответствии с рекомендацией:
глубина резания t = 5 мм;
подача на один зуб фрезы (в зависимости от мощности станка и материала детали) Sz = 018 мм.
Рисунок 5.4 – Операция фрезерования зубьев ведущей шестерни.
Подачу на один оборот фрезы S0 ммоб определяем по формуле
где Сv – табличный коэффициент Сv = 685;
q m m = 0.2; y = 0.2;
Т – период стойкости инструмента Т = 120 мин.
Частоту вращения фрезы n мин-1 определяем по формуле
где D – диаметр фрезы D = 80 мм.
Штучно-калькуляционное время Тшт.к мин определяем по формуле (5.17) приведенной выше.
Основное время Т0 мин определяем по формуле
где L – длина фрезеруемой поверхности с учетом врезания и перебега мм;
l2 – длина перебега l2 = 3 мм.
- число зубьев шестерни
Вспомогательное время на установку детали Тв мин выбираем в соответствии с рекомендацией Тв = 09 мин.
Оперативное время Топ мин определяем по формуле
где k – отношение дополнительного времени к оперативному при
Подготовительно-заключительное время Тп.з мин принимаем в соответствии с рекомендацией Тп.з = 19 мин.
В результате расчета получили следующие режимы для операции фрезерования:
подача на один оборот фрезы S0 = 2.16 ммоб;
скорость резания V = 43 ммин;
норма времени Тшт.к = 329 мин.
Задачей расчета является определение режимов шлифования и норм времени на проведение данной технологической операции.
модуль зубьев шестерни m = 3.63;
число зубьев шестерни = 54;
диаметр шестерни D = 197 мм.
Процесс шлифования зубьев включает в себя следующие операции:
шлифовать зубья шестерни;
В качестве оборудования для данной операции принимаем зубошлифовальный станок марки 5851 и шлифовальный круг общего применения типа 2П.
Характеристика шлифовального круга:
диаметр шлифовального круга Dк = 80 мм;
высота шлифовального круга Н = 10 мм;
шлифовальный материал – 2А.
Окружная скорость шлифовального круга V мс согласно рекомендации равна V = 30 мс.
Число проходов i определяем по формуле
где z0 – операционный припуск z0 = 005 мм;
Sв – вертикальная подача Sв = 005 ммоб.
Частоту вращения шлифовального круга определяем по формуле
где V – окружная скорость шлифовального круга ммин;
D – диаметр шлифовального круга мм.
Рисунок 5.5 – Операция шлифования зубьев шестерни
Основное время на шлифование определяем по формуле
где L – длина шлифуемой поверхности с учетом врезания и перебега мм;
определяем с учетом изменения длины врезания
Вспомогательное время выбираем из рекомендации в зависимости от веса детали и характера её установки – Тв = 27 мин.
Оперативное время определяем по формуле (5.17)
Подготовительно – заключительное время согласно рекомендации при шлифовании равно Тп.з. = 9 мин.
Штучно – калькуляционное время Тшт.к. мин определяем по формуле
В результате расчета были определены следующие режимы шлифования зубьев шестерни:
вертикальная подача Sв = 005 ммоб;
скорость вращения шлифовального круга V = 1800 ммин;
норма времени Тшт.к. = 249 мин.
2.6 Приспособление для изготовления детали
Для выполнения операции зубонарезания необходимо быстрое и надежное крепление. Так как для фрезерования используется горизонтальный фрезерный станок 6Р82Ш необходима фиксация колеса в горизонтальной плоскости.
Целью данного подраздела является разработка приспособления и описание принципа его работы. Кроме этого будет произведен расчет зажимающего усилия и сравнение его с усилием действующим на деталь в процессе операции.
Приспособление работает следующим образом. Зубчатое колесо насаживается на ось упираясь с одной стороны буртиком а с другой затягивается гайкой. Ось устанавливается одним концом в оправку 6 а с другой стороны предварительно зацентровывается вращением рукояти 2 винта 8. Далее происходит подача сжатого воздуха в пневмоцилиндр и поршень 1 начинает перемещаться в сторону оси одновременно зажимая ее. Таким образом происходит закрепление зубчатого колеса. После этого происходит поочередная смена обрабатываемого зуба.
Определение величины толкающей силы поршня
Толкающая сила определяется по формуле
где D –диаметр поршня пневмоцилиндра D = 192 мм ;
p – давление сжатого воздуха p=05 мПа ;
-коэффициент полезного действия привода =09 .
Расчет составляющих силы резания при фрезеровании
Рис. 5.6 Схемы сил резания при фрезеровании: а – упрощенная; б – полная; – окружная составляющая силы резания; – радиальная составляющая силы резания; – вертикальная составляющая силы резания; – осевая составляющая силы резания; – горизонтальная составляющая силы резания
Окружная сила действующая на обрабатываемый материал определяется по формуле
где z – число зубьев фрезы; z=12;
n – частота вращения фрезы обмин; n=171 обмин;
B – ширина фрезерования мм; B=14мм;
D – диаметр фрезы мм; D=80мм;
t – глубина фрезерования мм; t=5мм;
Sz – подача на зуб фрезы мм; Sz=018 мм;
Окружная сила возникающая при фрезеровании зубчатого колеса намного меньше силы толкающей силы поршня (прижимающей нагрузки).
ВОЗВЕДЕНИЕ ЗЕМЛЯНОГО ПОЛОТНА
Современное дорожное строительство характеризуется выполнением ряда сложных взаимно независимых технологических процессов с применением значительного количества машин и оборудования различного специального назначения а также переработкой больших объёмов материалов.
Важное место среди факторов оказывающих влияние на темпы строительства стоимость производства работ затраты труда и времени занимает механизация производства. Проектирование механизации связано с определением типов машин и их количества которые впоследствии объединяются в комплекты и комплексы. Без знания технических возможностей дорожно-строительных машин и организации их совместной работы нельзя достичь высокой эффективности их использования. Надёжность работы парков машин определяется их структурой и количественным составом и является важным условием ритмичности производства работ. Оптимальным будет тот парк машин использование которого обеспечит выполнение заданных объёмов работ в заданные сроки с минимальными трудовыми энергетическими денежными и др. затратами. Известно что один и тот же технологический процесс может быть выполнен различными машинами отличающимися друг от друга как принципом работы так и техническими параметрами.
Поэтому в таких условиях очень важно установить рациональные составы специализированных машинно-дорожных отрядов которые определяют технико-экономические показатели всего строительства.
Вид работ: возведение земляного полотна.
Место строительства: Омская область.
Протяженность участка – 20 км.
Категория грунта – II.
высота земляного полотна – 09 м.
Ведущая машина: бульдозер ДЗ-110А.
Дальность транспортирования грунта: 30 40 50 60 м.
При возведении земляного полотна рабочие процессы имеют следующую последовательность:
Снятие растительного слоя (используется бульдозер ДЗ-35С).
Разработка грунта и перемещение грунта в нижний слой земляного полотна (используется бульдозер ДЗ-110А).
Разравнивание нижнего слоя земляного полотна (используется автогрейдер ДЗ-31-1).
Уплотнение нижнего слоя земляного полотна (используется самоходный пневмоколёсный каток ДУ-29).
Разработка грунта и перемещение грунта в средний слой земляного полотна (используется бульдозер ДЗ-110А).
Разравнивание среднего слоя земляного полотна (автогрейдер ДЗ-31-1).
Уплотнение среднего слоя земляного полотна (каток ДУ-29).
Разработка грунта и перемещение грунта в верхний слой земляного полотна (используется бульдозер ДЗ-110А).
Разравнивание верхнего слоя земляного полотна (автогрейдер ДЗ-31-1).
Уплотнение верхнего слоя земляного полотна (каток ДУ-29).
Профилировка верхнего слоя земляного полотна (автогрейдер ДЗ-31-1).
2 Определение общего темпа работ
Рисунок 6.1 - Поперечное сечение земляного полотна
Объем работ определяется по формуле
где - площадь поперечного сечения земляного полотна м2;
- протяжённость участка дороги =20000 м.
Поперечное сечение земляного полотна представляет собой трапецию (рисунок 1). Площадь можно определить по формуле
где - нижнее основание трапеции поперечного сечения земляного полотна = 12 м;
- верхнее основание трапеции м;
- высота земляного полотна = 09 м.
Длину верхнего основания трапеции выразим через длину нижнего основания и уклон
- находим из отношения .
Общий темп строительства можно определить по формуле
где - количество рабочих дней;
- коэффициент сменности;
где - продолжительность смены = 8 ч.;
- время в течение которого работает машина за сутки = 8;
Количество рабочих дней определяется
где - количество календарных рабочих дней в данном регионе
- количество выходных дней = 44;
- количество праздничных дней = 2;
- количество нерабочих дней по погодным условиям = 5.
Тогда общий темп строительства равен
3 Определение темпов работ для каждой машины входящей в СКМ
Темп работы бульдозера снимающего растительный слой определяется по формуле
где - площадь грунта на которой снимается растительный слой м2;
- коэффициент сменности ;
- количество рабочих дней .
Темп работы автогрейдера разравнивающего каждый слой и профилирующего верх земляного полотна равен
где - сумма площадей земляного полотна на которых работает автогрейдер м2;
Темп работы катка уплотняющего каждый слой равен
где - объём грунта уплотняемого катком м3;
Темп работы бульдозера разрабатывающего и транспортирующего грунт определяется
- суммарный объём грунта в земляном полотне ;
4 Определение состава машин входящих в СКМ-1 и СКМ-2 и
определение их эксплуатационной производительности
Эксплуатационная сменная производительность бульдозера ДЗ-35С снимающего растительный слой определяется по формуле
где - время рабочей смены = 8 ч;
- норма времени для бульдозера =13 .
Эксплуатационная сменная производительность автогрейдера ДЗ-31-1 разравнивающего грунт определяется
Эксплуатационная сменная производительность самоходного катка ДУ-29 который занят на уплотнении грунта определяется
Эксплуатационная сменная производительность базового бульдозера ДЗ-110А разрабатывающего и перемещающего грунт определяется
- норма времени для бульдозера (определяем аппроксимированием для данной модели базового трактора).
В разделе 5.5 были определены значения производительностей базового и модернизированного бульдозера и по полученным значениям можно сделать вывод что отношение производительностей .
Тогда по формуле (6.12) эксплуатационная сменная производительность равна
модернизированный бульдозер ;
модернизированный бульдозер .
5 Определение количества машиносмен
Количество машиносмен бульдозеров снимающих растительный слой определяется по формуле
-эксплуатационная сменная производительность машины.
Количество машиносмен автогрейдеров определяется по формуле
Количество машиносмен катков определяется по формуле
Количество машиносмен бульдозеров разрабатывающих и перемещающих грунт определяется по формуле
-эксплуатационная сменная производительность бульдозера ДЗ-110А(базового и модернизированного).
для базового бульдозера
для модернизированного бульдозера
6 Определение количества машин входящих в СКМ-1 и СКМ-2
Количество бульдозеров снимающих растительный слой определяется по формуле
Количество автогрейдеров определяется по формуле
Количество катков определяется по формуле
Количество бульдозеров разрабатывающих и перемещающих грунт определяется по формуле
-эксплуатационная сменная производительность бульдозеров (базового и модернизированного) которая меняется в зависимости от дальности транспортирования грунта.
7 Уточнение темпа работ для ведущей машины
Уточняем эксплуатационную сменную производительность ведущей машины (бульдозера ДЗ-110А) в СКМ-1 СКМ-2.
Темп работ для бульдозера определяется
где - требуемое количество машин.
В зависимости от дальности транспортирования грунта
По полученным значениям темпов будем вести расчёт технико-экономических показателей.
состав СКМ-1 и СКМ-2
Себестоимость машиносмен определяется по формуле
где - единовременные затраты (монтаж демонтаж) руб;
- затраты на амортизационные отчисления руб;
- эксплуатационные затраты руб;
- единовременные затраты заработная плата в рублях руб;
- единовременные затраты перевозка на строительную площадку руб;
- эксплуатационные затраты заработная плата в рублях руб;
- эксплуатационные затраты ТО и ТР руб;
- эксплуатационные затраты заработная плата руб;
- эксплуатационные затраты затраты на дизельное топливо руб;
- эксплуатационные затраты затраты на смазочные материалы руб;
- районный коэффициент .
Для приведения стоимости машиносмен к существующим в настоящее время необходимо определить поправочный коэффициент
где - норма амортизации для бульдозера ДЗ-110А от общей стоимости машины.
Определим затраты на амортизационные отчисления в настоящее время руб.
- стоимость бульдозера ДЗ-110А в настоящее время ;
- годовой фонд рабочего времени машины час;
- количество выходных дней в году дня;
- количество праздничных дней в году дней;
Тогда поправочный коэффициент равен
Единовременные затраты приведённые к настоящему времени определяются:
Затраты на амортизационные отчисления приведённые к настоящему времени определяются:
Эксплуатационные затраты приведённые к настоящему времени определяются:
Себестоимость машиносмен определим по формуле (6.22)
автогрейдер ДЗ - 31-1
9 Определение технико-экономических показателей
9.1 Определение трудоёмкости единицы продукции
Трудоёмкость единицы продукции чел.-чм3 - это затраты физического труда операторов в чел.-ч. на изготовление единицы продукции.
где - число обслуживающего персонала по машине
- потребное количество машин
- темп работы ведущей машины.
При дальности перемещения 30 м:
при дальности перемещения 40 м:
при дальности перемещения 50 м:
при дальности перемещения 60 м:
9.2 Определение стоимости единицы продукции
Стоимость механизированных работ затрачиваемых на производство единицы продукции определяется
где - стоимость машиносмен машин руб.
9.3 Определение энергоёмкости единицы продукции
Энергоёмкость продукции показывает расход мощности средств механизации на производство единицы продукции и определяется
где - суммарная мощность силовых установок машины i - го типа машины.
При дальности перемещения 40 м:
При дальности перемещения 50 м:
При дальности перемещения 60 м:
9.4 Определение металлоёмкости единицы продукции
Металлоёмкость показывает какая часть массы машин приходится на единицу продукции и определяется
где - масса машины i - го типа.
При дальности перемещения 30 м:
9.5 Экономическая эффективность работы СКМ-1 и СКМ-2
Определяется по формуле
где - коэффициент дисконтирования;
- финансовые результаты от работы на объекте руб;
где - тариф за единицу продукции .
- затраты на выполнение работы СКМ включая стоимость материала;
где - затраты на строительные материалы так как в данном случае строительным материалом является грунт добываемый из придорожных карьеров;
- расходы на специализированный комплект машин;
где - стоимость единицы продукции при различной дальности перемещения грунта.
- норма дисконта = 015 (приведение затрат по времени);
gor - горизонт расчёта (сроки строительства в годах) .
Экономическая эффективность работы СКМ при дальности перемещения 30 м по формуле (6.32)
Тщательно анализируя показатели можно легко выяснить что комплект СКМ-2 с модернизированным бульдозером использовать гораздо эффективнее нежели комплект СКМ-1 с базовым бульдозером.
Можно с уверенностью сказать что модернизация бульдозера значительно уменьшает себестоимость металлоемкость трудоемкость и удельные приведенные затраты единицы продукции СКМ а также значительно уменьшает энергоемкость процесса возведения земляного полотна.
ТЕХНИКО-ЭКОНОМИЧЕСКИЕ ПОКАЗАТЕЛИ
1 Определение годовой эксплуатационной производительности
Годовая эксплуатационная производительность B определяется по формуле
где – эксплуатационная среднечасовая производительность техники ед. прод. маш.-ч;
– количество машино-часов работы техники в году маш.-чгод.
Исходя из условия выполнения работ бульдозером 50% времени и автогрейдером 50% тогда согласно
где - объем выполненных работ м² =1000 м².
- норма времени на производство данного объема работ ч
- число проходов бульдозера принимаем для базовой машины
Эксплуатационная среднечасовая производительность для новой техники определяется по формуле
где где – коэффициент учитывающий изменение показателей
входящих в формулу технической производительности;
– коэффициент учитывающий изменение использования техники во времени в смену.
где - объем призмы волочения для новой техники =2504 ;
- объем призмы волочения базовой техники =142 .
Количество машино-часов работы бульдозера в году определяется по формуле
где - годовой фонд рабочего времени техники =247 дней;
- продолжительность сезонного обслуживания =2 дня;
- простои во всех видах ремонтов и технических обслуживаний днимаш.-ч.;
- продолжительность одной перебазировки дни;
- время работы на объекте маш.-ч. =200 маш.-ч. ;
- коэффициент сменности =14 ;
- продолжительность смены =8 ч. .
Простои во всех видах ремонтов и ТО согласно :
- продолжительность пребывания техники в
- продолжительность ожидания ремонта дни;
- средний ресурс до капитального ремонта мото-ч. мото-ч.;
- среднее время на устранение отказа маш.-ч. =10 маш.-ч.;
- наработка на отказ мото-ч. =126 мото-ч. =190 мото-ч.;
- коэффициент перевода мото-ч. в маш.-ч. =044.
Необходимые данные связанные с ремонтом и ТО находим из и сводим в таблицу.
Таблица 7.1 - Количество ремонтов и время пребывания в i –м ремонте и ТО
Продолжительность одной перебазировки бульдозера при перевозке на большегрузном прицепе тяжеловозе определяется по формуле согласно
где - среднее расстояние перебазировки =100 км;
- средняя скорость переезда =15 кмч.;
- средняя продолжительность погрузки перевозимой техники на автотранспорт и ее разгрузки маш.-ч. =4 маш.-ч;
Количество машино-часов работы бульдозера в году равно
Годовая эксплуатационная производительность бульдозера равна
Определяем затраты на переоборудование машины .
где – затраты на материалы для переоборудования руб ;
– заработная плата рабочих-сварщиков с начислением 356% руб ;
– амортизационные отчисления на сварочный аппаратруб ;
– затраты на электроэнергию руб ;
– сумма накладных расходов руб .
где – стоимость единицы материала по действующим биржевым ценам =633 рубкг;
– масса материала требующегося на переоборудование кг.
объем i-го материала для переоборудования .
Масса материала требуемого для переоборудования отвала бульдозера складывается из массы подпружиненного ножа 5 массы ребер 7 и 8 массы кронштейна 12 массы пальца 9 с гайкой 13 и массы пружины 10
Затраты на материал для переоборудования
где – часовая тарифная ставка сварщика по данным сибирского регионального центра ценообразования =23 рубчас;
– длина шва сварного соединения =3.28 м;
– норма времени на сварочные работы по данным УМ-1 ТСМ-2
С начислениями 36.5% окончательно получаем =1252 руб.
где – цена сварочного аппарата по действующим биржевым ценам принимаем =12000 руб.
где – мощность сварочного аппарата согласно принимаем =1 кВт;
–время требующееся для сварки конструкции =LшHсв=32812= 273 часа ;
– стоимость единицы электроэнергии по действующим тарифам
Сумму накладных расходов определяем по формуле
С=2697+1255+1200+328 =15982 руб
Общая сумма затрат на переоборудование
Сп = 15982+3356 = 19338 руб
Затраты на переоборудование сведем в таблицу.
Таблица 7.2 – Калькуляция затрат на переоборудование
Затраты на материал
Фонд оплаты труда сварщиков
Амортизационные отчисления на сварочный аппарат
Затраты на электроэнергию
Общая сумма затрат на переоборудование
2 Определение годовых текущих издержек потребителя
Годовые текущие издержки потребителя при использовании рассчитывают по формуле согласно :
где - амортизационные отчисления на реновацию руб;
- затраты на выполнение текущих неплановых ремонтов и ТО руб;
- фонд оплаты труда рабочих управляющих техникой руб;
- затраты энергоносителей руб;
- затраты на смазочные материалы руб;
- затраты на перебазировки руб;
- норма накладных расходов связанных с эксплуатацией строительных и дорожных машин.
Амортизационные отчисления на реновацию
где - норма амортизационных отчислений на реновацию =12% .
-капитальные вложения потребителя связанные с приобретением бульдозера его первоначальной доставкой и монтажом.
где - цена техники =1025 тыс. руб ;
- коэффициент перехода от цены к балансовой стоимости =109 .
тыс. руб = 1117300 руб
Затраты на выполнение ТО текущих и плановых ремонтов
где - средняя тарифная ставка работы по ремонту машин руб.чел.·ч.
=20 руб.чел.·ч. (по данным УМ-7 на 01.05.2006 г.);
- средний коэффициент к тарифной ставке =115 ;
- коэффициент учитывающий премии ремонтным рабочим
- количество рабочих занятым устранением отказа =2 чел. ;
- расход запасных частей на год работы техники руб.год
Кесн – коэффициент на единый социальный налог Кесн=1356.
тыс.руб. = 70455 руб .
Фонд оплаты труда рабочих управляющих техникой
где - часовая тарифная ставка рабочего
- коэффициент учитывающий доплаты за 2-ю и 3-ю смены
Отчисления на социальные нужды равны 356 % от фонда оплаты
Фонд оплаты труда с отчислениями
=76147+271083=1032553 руб
Определение затрат энергоносителей
Затраты на топливо согласно
где - цена топлива =17 руб.л = 17084 = 2024 рубкг (на 1 мая 2006 года).
- часовой расход топлива кгмаш.-ч.
где - номинальная мощность двигателя =132 кВт;
- удельный расход топлива при номинальной мощности
- коэффициент учитывающий изменение расхода топлива в зависимости от степени использования ДВС по мощности =1 ;
- коэффициент использования двигателя по времени =088;
- коэффициент использования двигателя по мощности =053
Затраты на смазочные материалы согласно
где - коэффициент перехода от годовых затрат на топливо к затратам на смазочные материалы =02 .
Затраты на гидравлическую жидкость определяются по формуле
где Vг – ёмкость гидросистемы Vг=120 дм3;
Ом – объёмная масса гидравлической жидкости Ом=0365 кгдм3;
Цмг– оптовая цена гидравлической жидкости Цмг = 82 рубл = 82085 = 9647 рубкг;
Кд – коэффициент доливок Кд=15;
Тм – периодичность замены гидравлической жидкости Тм=1000 маш-ч;
Затраты на перебазировку при перевозке техники на большегрузном прицепе-тяжеловозе определяется по формуле согласно
где - заработная плата экипажа перевозимой машины руб.;
- заработная плата такелажников руб.;
- затраты на эксплуатацию автомобиля руб.;
Заработная плата экипажа перевозимого бульдозера
где - часовая тарифная ставка =20 руб.маш.-ч.;
Заработная плата такелажников
где - часовая тарифная ставка такелажников =20 руб.маш.-ч.;
Затраты на эксплуатацию автопоезда
где - цена одного автомобиле-часа в зависимости от грузоподъемности автомобиля =200 руб.ч. (данные по УМ-7);
- плата за 1 км. пробега руб.км.
Окончательно общая сумма годовых текущих издержек при использовании бульдозера рассчитывается и оформляется в виде таблицы.
Условное обозначение
Значение показателей руб.
Затраты на выполнение ТО и ремонтов
Фонд оплаты труда рабочих управляющих техникой
Затраты на смазочные материалы
Затраты на гидравлическую жидкость
Затраты на перебазировки
Общая сумма годовых текущих издержек
Таблица 7.3 - Калькуляция годовых текущих издержек.
3 Определение хозрасчетного экономического эффекта
Хозрасчетный экономический эффект в расчете на одну машину за год
где - годовая эксплуатационная производительность базовой машины ;
- годовая эксплуатационная производительность новой машины ;
- себестоимость эксплуатации базовой машины ;
- себестоимость эксплуатации новой машины .
Таблица 7.4 - Экономическая эффективность использования нового бульдозера
Наименование показателей
Значения показателей
Годовая эксплуатационная
Годовые текущие издержки потребителя
Экономический эффект на технику за год работы
БЕЗОПАСНОСТЬ ЖИЗНЕДЕЯТЕЛЬНОСТИ
Производственные процессы выполняемые бульдозерами сложны и разнообразны. При ручном управлении бульдозером оператор наблюдая за ходом рабочего процесса вручную переключает рычаги управления стремясь обеспечить наивыгоднейшие режимы работы заданные траектории рабочего органа требуемую последовательность операций. Одновременно он должен учитывать большое количество разнородных и быстро меняющихся факторов (неровности поверхности по которой перемещается бульдозер механические и физические свойства грунта). Все это делает режим работы оператора чрезвычайно напряженным. На некоторых машинах число переключений рычагов управления достигает до тысячи в час. Зачастую оператор может оценить изменение внешних условий и результаты работы только глазомером или ориентировочно.
Поэтому выбираемые им режимы работы далеки от оптимальных а количество работ часто не удовлетворяет техническим условиям. Все возрастающие требования к качеству земляных работ и улучшению условий труда оператора неизбежно приводят к необходимости введения автоматического управления машин.
В данном дипломном проекте модернизируется бульдозер путем установки подпружиненных ножей расположенных на задних секциях нижней части лобового листа что улучшает условия труда оператора и качество выполняемых земляных работ.
Основной целью безопасности жизнедеятельности являются защита человека в техносфере от негативных воздействий и достижения комфортных условий жизнедеятельности. Бульдозер является источником повышенной опасности не только для человека но и для окружающей среды. Оператор подвергается воздействию шума вибрации вредных веществ существует опасность травмирования. Все это приводит к возникновению профессиональных заболеваний.
Таких как нарушение обмена веществ сердечно-сосудистые заболевания ухудшение зрения боли в суставах бессонница. Значительное антропогенное загрязнение атмосферного воздуха создают строительно-дорожные машины. При работе бульдозера происходит загрязнение атмосферы выхлопными газами. Самыми распространенными токсичными веществами загрязняющими атмосферу являются: оксиды азота углеводороды и пыль. Задачей безопасности жизнедеятельности является защита оператора и окружающей среды от возникающих опасностей и негативных воздействий или снижение их до допустимых значений путем создания и установки на бульдозер различных приборов и механизмов. Таких как кондиционер для очистки воздуха механизмы гашения вибраций кабины и сидения оператора установка катализатора на выхлопную трубу для снижения вредных выбросов в атмосферу.
1 Анализ вредных факторов
В системе ЧМС человек оказывает влияние на машину и окружающую среду машина оказывает влияние на человека и окружающую среду окружающая среда оказывает влияние на человека и машину.
Рисунок 8.1 - Схематическое изображение системы ЧМС
При работе бульдозера на базе трактора Т-170 возникает множество отрицательных явлений в той или иной степени влияющих на оператора бульдозера.
Рисунок 8.2 - Схема возникновения вредных факторов
Шум. Источниками шума является двигатель (взаимодействие поршня с цилиндром вибрации в подшипниках коленчатого вала вибрации головки блока цилиндров стуки клапанного механизма вибрации стенок гильз цилиндров взаимодействие распределительных шестерен действие элементов топливного и масляного насосов всасывание воздуха выпуск отработавших газов вращение крыльчатки вентилятора шум сгорания в цилиндрах )шум рабочего органа шум гидравлических систем (гидромоторы гидромуфты гидронасосы трубопроводы)шум трансмиссии.
Уровень шума в кабине достигает 85 Дб. 19. В зависимости от уровня шума его характеристики и продолжительности а также индивидуальных особенностей человека шум может повлечь за собой различные вредные явления и расстройства здоровья. Такие как: понижение производительности труда головные боли раздражительность слабость бессонница. Согласно требованиям СН-2.2.У2.1.8.562-96 и ГОСТ 12.2.120-88 допустимый уровень шума 80 Дб в кабине оператора.
В данном случае для нормальных условий работы оператора предусмотрено следующее: с целью понижения шумовых эффектов кабина бульдозериста оббивается шумопонижающим материалом. Шумопонижающая оболочка представляет собой материал на основе картона со слоем звукопоглощающего материала (например: ваты минеральной и стеклянной виброзола) а также стальных листов и органического стекла. Шумопонижающий материал располагается между металлическим сварным каркасом и фанерой.
Также снижение структурного шума достигается за счет применения звукоизолирующего капота и резино-металлической гусеницы. Проведенные мероприятия снижают уровень шума до 70 дБ.
Вибрация. На оператора бульдозера воздействует разнообразная вибрация вызываемая передвижением и работой этих машин. Общая вибрация передается через пол и сиденье на тело оператора а локальная на его руки через рычаги управления. Вибрация вызывает снижение работоспособности нарушение функций центральной нервной системы нарушение функций опорно-двигательного аппарата смещение органов.
Длительное воздействие вибраций ведет к развитию профессиональной вибрационной болезни. Вибрация рабочих мест операторов транспортных средств и оборудования носит преимущественно низкочастотный характер с высокими уровнями в октавах 1 8 Гц. Параметры вибрации зависят от технологической операции скорости передвижения типа сидения виброзащиты степени изношенности машины. Для защиты от вибраций проводят следующие мероприятия: устанавливают виброгасители сидения и кабины устанавливают двигатель на резиновые подушки площадь основания кабины покрывают войлоком. В качестве виброизоляторов также используют металлические пружины пробку и другие упругие материалы.
Для санитарного нормирования и контроля вибраций используются среднеквадратичные значения виброускорения и виброскорости а также их логарифмические уровни в децибелах (СН-2.2.У2.1.8.562-96 ГОСТ 12.2.120-88).
Модернизированный отвал с подпружиненными ножами также является источником шума и вибрации абсолютно также как и обыкновенный отвал. Так например при работе бульдозера отвал может наткнуться на препятствие что вызовет вибрацию и шум а также при заглублении отвала при перемещении подпружиненных ножей. Нагрузка сглаживается что снижает амплитуду вибрационного воздействия на оператора и кроме этого улучшает условия обзора.
Вредные вещества. Классификация и предельные содержания вредных веществ в воздухе рабочей зоны изложены в ГОСТ 12.1.007-88 «Вредные вещества» и составляют 1мгм³. Наиболее распространенными являются оксиды азота летучие углеводороды угарный газ и пыль. В организм химические вещества могут проникать через органы дыхания желудочно-кишечный тракт и неповрежденную кожу. Однако основным путем поступления являются легкие.
Помимо острых и хронических профессиональных интоксикаций промышленные яды могут быть причиной понижения устойчивости организма и повышенной общей заболеваемости. Оператор может быть подвержен таким заболеваниям как расстройство нервной системы судороги нарушение структуры ферментов отек легких. Развитие общетоксического действия аэрозолей в значительной степени связано с размером частиц пыли так как пыль с частицами до 5 мкм. Проникает в глубокие дыхательные пути в амвеолы растворяется в лимфе и поступает в кровь вызывает интоксикацию.
Для уменьшения попадания вредных веществ и пыли в кабину установлены уплотнения из резинотканевых изделий. Вентиляция рабочего места оператора осуществляется вентилятором или кондиционером.
Для предотвращения попадания пыли и газов в кабину через неплотности пола в области рычагов управления педалей предусмотрены специальные кожухи.
ГОСТ 12.1.005-88 «Общие санитарно-гигиенические требования к воздуху рабочей зоны».
Источниками вредных веществ в основном являются отработанные картерные газы а также испарение вредных веществ с поверхности горюче-смазочных материалов. Источниками пыли выступают материалы с которыми работает бульдозер (например песок щебень любой грунт). Нормирование по ГОСТ 12.2.120-88 в кабине содержание СО≤20 мгм3 содержание пыли в зависимости от содержания SiO2 (при SiO2=100% ПДК = 1 мгм3.
Микроклимат. На рисунке рассмотрим схему негативных факторов окружающей среды.
Рисунок 8.3 - Схема негативных факторов окружающей среды
Данный бульдозер предусматривает работу в диапазоне температур от -40 °С до +40 °С. Метеорологические условия как и шум заметно снижают производительность труда и оказывают негативное влияние на здоровье оператора. Работы оператора бульдозера относятся к работам второй категории тяжести с затратой энергии 175 232 Вт. В соответствии с ГОСТом 12.2.120 – 88 температура в кабине оператора должна быть зимой не ниже +16 °С а летом не выше +28 °С.
Для поддержания этого режима температур предусмотрено следующее оборудование.
В зимнее время производится обогрев кабины с помощью отопителей электропечи ПЭТ-4УЗ а также трубчатых подогревателей ЭТ-100. В летнее время оператор может воспользоваться кондиционером который обеспечивает заданные параметры среды. Данные приборы рекомендованы ГОСТ 12.1.005 – 88 который предусматривает устройство естественной и принудительной вентиляции а также использование отопителей и кондиционеров. Избыточное давление в кабине не менее 10 МПа.
Влажность воздуха оказывает значительное влияние на термоизоляцию организма человека. Высокая влажность при высокой температуре воздуха способствует перегреванию организма а при низкой ведет к переохлаждению. Низкая влажность вызывает пересыхание слизистых оболочек дыхательных путей оператора. Параметры влажности оговорены в ГОСТе 12.1.005 – 88.
Освещение. По СниП 23-04-95 производится выбор источника света там же можно найти нормы искусственного освещения. В темное время суток рабочая площадка должна быть освещена и освещенность составляет не менее 10 лк. Для этого предусмотрены тракторные фары соответствующего образца а также освещение самой площадки прожекторами ПЗС – 45 (1000 Вт; 220 В). Освещенность в кабине не должна превышать 50 лк для этого кабину оборудуют плафоном общего освещения ПК – 201. Освещенность приборов и указателей осуществляется заливающим светом. Площадь застекления обеспечивает достаточный обзор оператору.
В солнечную погоду лобовое стекло защищено солнцезащитным козырьком. В дождливую погоду используются стеклоочистители.
Электробезопасность.
Электронасыщенность современного производства формирует электрическую опасность источником которой могут быть электрические сети электрифицированный инструмент и оборудование вычислительная и организационная техника работающая на электричестве. Электротравматизм по сравнению с другими видами производства составляет небольшой процент однако по числу травм с тяжелым и особенно летальным исходом занимает одно из первых мест.
Электрический ток протекая через тело человека производит термическое электрическое биологическое механическое и световое воздействие. Термическое воздействие характеризуется нагревом кожи тканей вплоть до ожогов.
Электрическое воздействие заключается в электрическом разложении жидкостей в том числе и крови. Биологическое действие электрического тока проявляется в нарушении биологических процессов протекающих в организме человека и сопровождается разрушением и возбуждением тканей и судорожным сокращением мышц. Механическое действие приводит к разрыву тканей а световое к поражению тканей.
При проведении ремонтных работ необходимо использовать источники питания напряжением не более 36 В. При работе бульдозера удар молнией не возможен.
Перед началом планировочных работ необходимо убедиться в отсутствии силовых кабелей в рабочей зоне.
К защитным мерам от опасности от опасности прикосновения к токоведущим частям электроустановок относятся: изоляция ограждения блокировка кожухи пониженные напряжения электрозащитные средства и сигнализация. Надежная изоляция от земли и корпуса создает безопасные условия для обслуживающего персонала. Основная характеристика изоляции- сопротивление. Во время работы машины состояние электрической изоляции ухудшается вследствие нагрева механических повреждений влияния климатических условий и окружающей производственной среды. Сопротивление изоляции необходимо постоянно контролировать с помощью специальных приборов.
Электрооборудование бульдозера и устройства имеет напряжение 24В что согласно ГОСТ 12.1.038 – 82 не представляет собой опасности для оператора.
Пожаробезопасность. Возникновение горения чаще всего связано с нагреванием горючей системы тем или иным источником воспламенения. Причинами пожара являются: ненадежное соединение топливо и гидропроводов неисправности баков с горюче-смазочными материалами нахождение машины вблизи открытого огня несоблюдение техники безопасности. Для предотвращения пожароопасных ситуаций необходимо: поддерживать надежное соединение топливо и гидропроводов не допускать применение открытого огня при запуске двигателя в зимнее время на выхлопной трубе обязательна установка искрогасителя запрещается курение при заправке бульдозера топливом. ГОСТ 12.0.004 – 90
«Пожаробезопасность» предусматривает действия при возгорании горюче-смазочных материалов. На случай пожара в кабине имеется огнетушитель 046 – 7 (пенный).
Источником воспламенения выступает электрооборудование которое может явиться источником искры вызывающей возгорание; также топливопроводы ДВС.
Техника безопасности. Инструктаж по технике безопасности проводит мастер или механик. При выполнении работ по специальностям повышенной опасности проводятся повторные инструктажи через определенные промежутки времени (1 раз в 3 месяца) а так же при каждом нарушении правил ТБ. Для предупреждения производственного травматизма на каждом предприятии должны быть разработаны и утверждены и изучены всем производственным персоналом правила ТБ производственной санитарии и пожарной безопасности.
Соблюдение всех строительных норм правил эксплуатации бульдозера а так же инструкций по монтажу и эксплуатации рабочих органов – это пути к сохранению здоровья и окружающих.
Таблица 8.1 - Вредные факторы
головные боли бессонница
Шумоизоляция кабины установка резиновых уплотнений в местах подвижного соединения деталей кабины.
утомляемость нарушение функций нервной системы
Виброизоляция сидения и кабины оператора.
угарный газ пыль углеводороды
Установка катализатора на выхлопную трубу установка кондиционера.
перегревание и переохлаждение организма утомляемость раздражение дыхательных путей
Установка вентиляторов кондиционеров отопителей осветительных плафонов.
Соблюдение техники безопасности огнетушители
2 Расчет устойчивости бульдозера Т-170
По условиям работы бульдозеру необходимо преодолевать значительные продольные уклоны и двигаться по косогорам. Поэтому необходима проверка возможности их работы в этих условиях.
При продольных уклонах движение бульдозера может оказаться невозможным как вследствие его опрокидывания так и ввиду недостаточного сцепления его гусениц.
Рисунок 8.4 – Расчетная схема для определения максимального угла уклона по
условию опрокидывания
Максимальный угол уклона при котором начинается опрокидывание бульдозера определяется по формуле
где - абсцисса центра тяжести бульдозера ;
- ордината центра тяжести .
Возможность преодоления уклонов определяется условиями сцепления гусениц бульдозера с поверхность грунта. С увеличением угла уклона сцепление колес ухудшается что объясняется снижением нагрузки на гусеницы.
Рисунок 8.5 – Расчетная схема для определения максимального угла уклона по
Таким образом максимальный угол уклона (по сцеплению) определяется по формуле
где - коэффициент сцепления ;
- расстояние между осями ;
- коэффициент сопротивления движению ;
Остальные величины известны.
Рисунок 8.5 – Расчетная схема для проверки боковой устойчивости
Максимально допустимое значение угла косогора можно определить по формуле
где - колея бульдозера .
Таким образом расчетным путем были определены предельно допустимые значения продольных и поперечных уклонов при которых работа может быть безопасной. При превышении данных значений увеличивается вероятность опрокидывания бульдозера.
3 Экологическая безопасность
В последние годы роль и значение экологической безопасности Российской Федерации как одной из важных составляющих национальной безопасности существенно возросли. Обеспечение экологической безопасности определено одним из основных направлений обеспечения национальной безопасности что отражено в действующих правовых актах в том числе в Концепции национальной безопасности Российской Федерации (утверждена Указом Президента Российской Федерации от 10 января 2000г. № 24).
Конституция РФ: Ст42 "О праве каждого гражданина на благоприятную окружающую среду и на информацию о состоянии окружающей среды’’. Аналогична статья с конституции РБ – ст49 (сокрытие информации должностными лицами которая может представлять собой угрозу для жизни и здоровья влечет ответственность в соответствии с законом говорится о праве граждан на возмещение ущерба об обязанности граждан сохранять окружающую среду о поощрении деятельности по охране окружающей среды).
Федеральный закон от 30 марта 1999г. № 52-ФЗ «О санитарно-эпидемиологическом благополучии населения» (собрание законодательства 1999 № 14 ст. 1650).
Федеральный закон от 4 мая 1999г. № 96-ФЗ «Об охране атмосферного воздуха» (собрание законодательства 1999 № 18 ст. 2222).
Постановление Правительства Российской Федерации от 27 августа 1999г. № 972 «Об утверждении Положения о создании охранных зон стационарных пунктов наблюдений за состоянием окружающей среды ее загрязнением» (собрание законодательства 1999 № 36 ст. 4405).
Рекультивация земель производится в соответствии с постановлением Совета Министров РСФСР “О рекультивации земель. Сохранении и рациональном использовании плодородного слоя почвы при разработке месторождений полезных ископаемых и торфа при проведении геологоразведочных строительных и других работ”.
В период производства работ необходимо соблюдение следующих природоохранных мероприятий направленных на защиту атмосферного воздуха:
-при выполнении работ вблизи населённых пунктов использовать технику оптимальной производительности с минимальными выбросами работы выполнять в кротчайшие сроки;
-допускать к эксплуатации машины и механизмы в исправном состоянии особенно тщательно следить за состоянием технических средств способных вызвать возгорание естественной растительности;
-при неблагоприятных погодных условиях строительные работы вблизи населенных пунктов не выполнять;
-периодически осуществлять контроль за содержанием загрязняющих веществ в выхлопных газах.
При охране почв для снижения воздействия на поверхность земли в период производства работ предусмотрены следующие мероприятия:
-первоочередное строительство вдоль трассового проезда;
-проезд строительной техники разрешается только в пределах полосы отвода земли;
-своевременная уборка мусора и отходов;
-рекультивация нарушенных земель.
В данном дипломном проекте на основании обзора технической литературы и патентных исследований разработан модернизированный бульдозер Т-170.
Произведены расчеты подтверждающие работоспособность и надежность предложенной конструкции в частности расчет на прочность металлоконструкции рабочего оборудования бульдозера.
В технологическом разделе дипломного проекта разработана технология изготовления детали.
В разделе «Безопасность жизнедеятельности» проведен анализ опасных и вредных факторов сделан расчет устойчивости бульдозера и предложены меры по безопасности жизнедеятельности.
В экономическом разделе проекта определили годовой экономический эффекта от внедрения модернизированного бульдозера Т-170 который составил 883431 руб.
СПИСОК ИСПОЛЬЗОВАННЫХ ИСТОЧНИКОВ
Авторские свидетельства: АС 76 72 93 Е 02 F 3 76 АС 99 46 38 Е 02 F 376 АС 16 55 52 Е 02 F 376 АС 108 92 02 E 02 F 376 АС 109 90 12 E 02 F 376 АС 82 77 00 E 02F 376 АС 84 46 98 E 02 F 376 АС 115 71 74 E 02 F 376 АС 96 82 09 E 02 F376 .
Алексеева Т.В. Артемьев К.А. Дорожные машины. Часть 1 Машины для земляных работ (теория и расчёт): Учебное пособие. – М.: Машиностроение 1972. – 504 с.
Анурьев В. И. Справочник конструктора-машиностроителя: 123 том. –5-е издание перераб. и доп. – М.: Машиностроение 1980.
Баловнев В. И. Дорожно-строительные машины с рабочим органом интенсифицирующего действия: Учебное пособие. – М.: Машиностроение 1981. – 223 с.
Бородачев И.П. Справочник конструктора дорожных машин .М. “Машиностроение” 1973 –504 с.
Бромберг А.А. Машины для земляных работ. Атлас конструкций. М. “Машиностроение” 68. – 140 с.
Броневич Г.А. Курсовое и дипломное проектирование по специальности строительные машины и оборудование. М.”Стройиздат” 1973 –240 с.
Васильченко В.А. Гидравлическое оборудование мобильных машин: Справочник. – М.: Машиностроение 1983. – 302 с.
Ветров Ю.А. Расчёты сил резания и копания грунтов. Изд. Киевского университета 1965. – 412 с.
Власов А. Ф. Предупреждение производственного травматизма: Учебное пособие. - М.:Профиздат 1973. – 201 с.
Домбровский Н.Г. Гальперин М.И. Землеройно-транспортные машины. М.”Машиностроние” 1965 – 276 с.
Дунаев П.Ф. Леликов О.П. Конструирование узлов и деталей машин. М.”Высшая школа” 2001 – 447 с.
Е. С. Щербаков. Построение эпюр внутренних усилий: Методические указания для студентов механических специальностей. - Омск 1983. – 35 с.
Единые нормы и расценки на строительные монтажные и ремонтно-строительные работы. Сборник Е2. Земляные работы. Выпуск 1. Механизированные и ручные земляные работы. – М.: Издание официальное 1988. – 223 с.
Закон Российской Федерации Об охране окружающей природной среды. Ведомости Верховного Совета №10 1992 - с.82-87.
Зеленков Г.И. Проектирование предприятий по ремонту строительных и дорожных машин.
И. А. Биргер. Справочник. Расчет на прочность деталей машин. –М.: Машиностроение 1993. – 640 с.
Иванов Н. И. Борьба с шумом и вибрациями на путевых и строительных машинах. –2-е изд. перераб. и доп. – М.: Транспорт 1987. – 223 с.
Корсаков В.С. Основы технологии машиностроения . М. “Высшая школа” 1974 – 336 с.
Научно-технический прогресс и охрана труда ВЦНИИОТ ВЦСПС. Обзорная информация вып.7. М.:1980. – 57 с.
Справочник технолога-машиностроителя в 2-х томах под ред. А. Г. Косиловой – 4-е изд. перераб. и доп. –М.: Машиностроение 1985.
Строительные и дорожные машины. Издание периодическое. №31997 г.
Т. В. Алексеева Э. Б. Шерман. Отдельные разделы гидропривода мобильных машин: Методические указания. – Омск 1989. – 69 с.
Чекмарев А. А. Справочник по машиностроительному черчению. М.: “Машиностроение” 1985. – 468 с.
Строительные нормы и правила V - 3 - 82: Часть V сметные нормы и правила. Глава 3 правила определения сметной стоимости эксплуатации строительных машин. - М.: Стройиздат 1984. – 77 с.