Технологический процесс изготовления и ремонта крышки




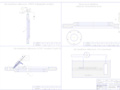
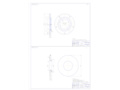
- Добавлен: 25.10.2022
- Размер: 347 KB
- Закачек: 0
Описание
Состав проекта
![]() |
![]() |
![]() ![]() ![]() ![]() |
![]() ![]() ![]() |
![]() ![]() ![]() |
![]() ![]() ![]() |
![]() ![]() ![]() ![]() |
![]() ![]() ![]() ![]() |
![]() |
![]() ![]() ![]() |
Дополнительная информация
лист 3.cdw

6h7 наплавкой в среде CO
Механическая обработка
отверстий под ремонтные болты
6H14 вибродуговой наплавкой
БРУ-34-16.02.03.00.000
Эскизы востановления
лист 2.bak.dwg
Сталь 40 Х ГОСТ 4543-71
Операция 010 Расточная
Операция 060 "Сверлильная
Операция 080 "Шлифовальная"
Лист-1.bak.dwg
Неуказанные штамповачные радиусы 2 2.5 мм
Неуказанные штамповочные уклоны 3 5
Остальные техн требования к штамповке по ГОСТ 26358-84
Остальные технические требования по СТБ 1014-95
БРУ-34-16.02.01.000 З
Сталь 40 Х ГОСТ 4543-71
лист 3.bak.dwg
наплавкой в среде CO
Механическая обработка
отверстий под ремонтные болты
вибродуговой наплавкой
БРУ-34-16.02.03.00.000
Эскизы востановления
Лист-1.frw

Неуказанные штамповачные радиусы 2 2.5 мм
Неуказанные штамповочные уклоны 3 5
Остальные техн требования к штамповке по ГОСТ 26358-84
Остальные технические требования по СТБ 1014-95
БРУ-34-16.02.01.000 З
Сталь 40 Х ГОСТ 4543-71
лист 2.cdw

Операция 010 Расточная
Операция 020 "Токарная гидрокопировальная
Операция 060 "Сверлильная
Операция 080 "Шлифовальная"
Записка.doc
1Анализ технологичности конструкции 5
2Выбор маршрута механической обработки .9
3Расчет припусков 10
4Выбор оборудования и оснастки 11
5Расчет режимов резания 12
Технология ремонта изделия 19
1 Анализ возможных дефектов 19
2 Маршрут обработки и режимы ремонта ..19
Список литературы 23
«Становой хребет» экономики любого развитого государства – это машиностроение и важное место при подготовке специалистов СДПТМиО имеет изучение технологии машиностроения.
Важная роль при изучении технологии производства и ремонта машин принадлежит курсовой работе где самостоятельно необходимо разработать технологические процессы изготовления и ремонта оригинальной детали. Поэтому целью курсовой работы является закрепление углубление и обобщение полученных знаний а так же приобретение практических навыков для разработки технологических процессов изготовления и ремонта деталей с использованием прогрессивных технологий.
Технологический процесс изготовления маховика
Рис.1 – главный фрикцион Т-34:
-шарикоподшипник; 2-нажимной диск; 3-ведущий барабан; 4-ведомый барабан; 5-пальцы с пружинами; 6-отжимной диск; 7-неподвижная чашка; 8-шарик; 9-подвижная чашка; 10-радиально-упорный подшипник; 1112-сальники; 13- ведущий вал коробки передач; 14-рычаг; 15- палец 16 – зубчатая муфта.
Годовая программа выпуска фрикционов N=100000 штук. В каждом оригинальном механизме устанавливают по 1 крышке (рис. 1 позиция 12). Значит годовая программа выпуска крышок фрикциона будет составлять N=1x100000=100000 штук. Поэтому можно сделать обоснованный вывод что используется массовый тип производства.
1Анализ технологичности конструкции.
На основе анализа рис. 2 можно сделать вывод что конструкторской базой данной делали является поверхность ø396 .
Вспомогательной установочной базой для крышки являются поверхности ø190 и ø396.
Так как установочная и конструкторская база у данной детали разные поверхности значит принцип совмещения баз невозможен.
Зубчатая муфта изготовлен из углеродистой качественной стали 40 Х по
ГОСТ 1050-88 химический состав которой: углерод С – 040 %; кремний S марганец Mn – 050-080 %; сера S – не более 0035 %; фосфор P – не более 0035 %; никель N хром Cr – около 08-110 %.
Выбор способа получения заготовки.
Общая себестоимость и качество детали складываются из себестоимости и качества заготовки и себестоимости и качества ее обработки. Поэтому всегда следует комплексно оценивать процесс получения изделия включая производство заготовки и ее обработку. Расчет себестоимости для конкретных способов получения заготовок предполагая что чистовая механическая обработка для всех вариантов одинакова можно осуществлять по следующим зависимостям:
где mш - масса перед штамповкой кг (на 2 8 % больше массы готовой детали);
Cш.р - стоимость штамповочных работ (Cш.р = 0005 mш );
qш - накладные расходы штамповочного цеха (50 100 %);
Cшт - стоимость штампа (Cшт = 10 mш );
nшт - количество заготовок изготавливаемых одним штампом (до 10 тыс.);
В-минитная заработная плата рабочих В=002 004;
Тшк-штучно-калькуляционное время;
Рисунок 3 – Эскиз заготовки из штамповки
(1 + qкуз 100 ) + (1 + q100 )
где - масса прутка перед ковкой кг :
= 13 × где - масса готовой детали (40 кг);
- цена 1 кг проката (02 долл.);
- стоимость кузнечных работ = 001 =001× 52= 0.52
qкуз – накладные расходы кузнечного цеха; принимаем qкуз = 100%
В – минутная зарплата рабочих производящих черновую механическую обработку заготовок принимаем В = 003 долл.мин;
- штучно-калькуляционное время черновой обработки детали мин:
где - длина обработки мм ;
- количество проходов инструмента .
Принимая глубину резания для одного прохода равной 1 3 мм имеем следующее: = 1; = 89+ 5 + 5 = 99 мм = 0.99 мин;
q - накладные расходы механического цеха в процентах к основной зарплате q = 100 – 200 % ( принимаем = 100 % ).
= 52 × 02 + 0.52( 1 + 150100 ) + 003 × 27 (1 + 150100) =
Поэтому целесообразнее использовать заготовку из штамповки.
2 Назначение технологического маршрута обработки.
Разработаем маршрут изготовления детали.
Таблица 1. – Маршрут обработки
Наименование операции
Расточить поверхность под ø190 L=40
Токарно- винторезный станок 16К20
Токарная гидрокопировальная
Обтачивание черновое 28 до 26 мм на L=204
Обтачивание черновое ø400 до ø396 L=26
Обтачивание черновое 40 до 38 L=34
Расточная гидрокопировальная
Обтачивание черновое ø190 до ø276 на L=12
Обтачивание черновое ø190 до ø240 L=2
Обтачивание черновое ø190 до ø214 на L=8
Печь ТВЧ для закалки; ёмкость с расплавом соли или воздушная электрическая печь для отпуска
Просверлить отверстия ø18 L=26 5шт
Радиально сверлильный станок 2Р53
Шлифовать поверхность ø190 L=22
Шлифовать поверхность ø276 L=12
3 Расчет и назначение припусков
На основании выбранного технологического маршрута обработки крышке и способа получения заготовки производим расчет минимальных припусков и допусков на механическую обработку.
Технологический маршрут обработки поверхности 190H9 состоит из чернового обтачивания и тонкого шлифования.
При обработке поверхности минимальный припуск для каждого i-го перехода можно оценить
ei - погрешность установки заготовки на данной операции мкм.
Минимальный припуск под растачивание:
Минимальный припуск под шлифование
На остальные обрабатываемые поверхности припуски и допуски выбираем по таблицам (ГОСТ 1855-55).
4 Выбор оборудования и оснастки
4.1 Для операций 010020030040050 выбираем Токарно-винторезный станок 16К20. Державка резца 25×25. Частота вращения мин-1: 12.5; 16; 20; 25; 31.5; 40; 50; 63; 80; 100-1600. Продольная подача на один оборот шпинделя ммоб: 005; 006; 0075; 009; 01; 0125; 015; 0175; 02; 025; 03; 035; 04; 05; 06 и т.д.; Поперечная подача на один оборот шпинделя ммоб: 0025; 003; 00375; 0045; 005; 00625-14. Привод: 2-х кулачковый патрон. Способ установки: закрепить по поверхности 400 и 190. Режущий инструмент: резец токарный отрезной с твердосплавной пластиной Т15К6 ГОСТ 18884-73 D 35-50 мм L=5мм; Мерительный инструмент: скоба (для контроля длины L=84мм). Способ установки: закрепить в призмах.
4.2 Для операции 060 выбираем радиально сверлильный станок 2Р53
Требующиеся диаметры сверла 18мм. Частота вращения сверла мин-1 :
0-2000. Рабочая подача сверлильной головки 20 300 мммин. Способ установки: закрепить в поверхности ø396 .
4.5 Для операции 080 выбираем станок универсальный круглошлифовальный ЗУ10В.
5 Расчёт режимов резания
Исходными данными для этого являются принятый маршрут механической обработки детали и назначенные припуски для каждого перехода что соответствует глубинам резания ti .
Выбираем материал лезвия инструмента: твёрдосплавная пластина Т15К6 период стойкости которой равен Т=120 мин.
Далее назначается подача инструмента s в зависимости от вида обработки.
Затем в зависимости от вида обработки (инструмент Т15К6) определим скорость резания v ммин по формуле:
где Cv - коэффициент скорости резания;
T - период стойкости инструмента мин;
t - глубина резания мм;
s - подача инструмента ммоб;
m x y - показатели степеней.
После определения скорости резанья частота вращения шпинделя станка n обмин. оценивается по следующей формуле:
где D – диаметр обрабатываемой детали или диаметр фрезы м.
При шлифовании скорость резания принимается = 10 120 мс.
После оценки v произведем вычисление проекций силы резания по координатным осям:
t - глубина резания мм (при отрезке – ширина лезвия резца);
v - скорость резания ммин;
xi yi ni - показатели степеней.
После вычисления силы резания оценивается крутящий момент при резании Мк Нм по формуле:
где D – диаметр обрабатываемой поверхности при точении или диаметр инструмента при сверлении и фрезеровании м.
Затем оценивается мощность при резании NкВт по формуле:
где n – частота вращения шпинделя станка мин-1.
Для шлифовальных операций силы резания не оцениваются из-за их малости а сразу определяют мощность N кВт. Так при шлифовании с продольной подачей т. е. когда шлифуемая поверхность больше ширины шлифовального круга
где CN- коэффициент мощности резания CN =01 52;
-окружная скорость заготовки 3=10 150ммин;
t- глубина шлифования (припуск) мм;
s- продольная подача s=12 10 ммин;
D-шлифуемый диаметр мм;
В заключении расчетов режимов резания определяется основное время обработки Tо мин. и штучно-калькуляционное Тшк мин. для каждой операции. Общая зависимость для основного времени:
k- количество проходов инструмента;
n- частота вращения шпинделя станка или число двойных ходов в минуту для станков с прямолинейным главным движением мин-1:
Штучно-калькуляционное время для операции вычисляется как сумма:
Tшк = Tо + Tв + Tоб + Tф мин
где Tв - вспомогательное время связанное с установкой заготовки и её закреплением управлением станка текущими измерениями детали ТВ=(001 02)Т0;
Tоб - время обслуживания станка т.е. на его уборку смазку и приведение в рабочее состояние которое составляет 1-6% от Т0 ;
Tф - время на физические надобности рабочего примерно равное 4-8% от суммы Т0 и ТВ.
Следует иметь в виду что при массовом производстве ТВ Тоб и Тф минимальны и часто перекрываются основным временем.
Определяем параметры резания для каждой операции:
Операция 010 «Расточная»
Растачивание черновое поверхности 1865мм до 190h14 на
L = 40 мм за 1 проход t = 171 мм.
При черновом точении поверхности 190:
Cv=240; Т=120 мин; t=171мм; s=05 ммоб ;m=02; y=02
Частота вращения шпинделя станка:
Принимаем по паспорту станка n=160мин
Основное время определяется по формуле:
Штучно-калькуляционное время для операции:
Tв = (001 02) Tо = 008 мин
Tоб = (1-6) % Tо= 005 мин
Tф = (4-8) %( Tо + Tв) = 00545мин
Операция 060 «Сверлильная»
Сверлить отверстия 18 мм на L =26 мм.
Определим скорость сверления:
Cv=100; Т=120 мин; t =1 мм; s =10ммоб ; m=02; y=05.
Частота вращения сверла:
Принимаем n=650 мин-1
Tшк2 = Tо + Tв + Tоб + Tф мин
Tв = (001 02) Tо = 00008 мин
Tоб = (1-6) % Tо= 0008 мин
Tф = (4-8) %( Tо + Tв) = 00009мин
Операция 080 «Шлифование»
Шлифовать с 276h14 до 276() на L = 12 мм
Скорость шлифовального круга:
где dкр - диаметр шлифовального круга мм;
nкр - частота вращения шлифовального круга мин -1;
Рекомендуемая частота вращения детали по нормативам:
где V = 35 ммин - рекомендуемая скорость вращения детали.
Принимаем частоту вращения детали n = 40 мин
Продольная подача за один оборот детали принимается в долях ширины круга = 20 мм :
Поперечную подачу принимаем =001мм.
где - длина хода стола мм;
где -длина шлифуемой поверхности мм;
-коэффициент учитывающий точность шлифования к=15;
где h - припуск на шлифовку на сторону h=02282 = 0114 мм;
Tв = (001 02) Tо = 001 х 08 = 0033 мин
Tоб = (1-6) % Tо= 003 х 08 = 00033мин
Tф = (4-8) %( Tо + Tв) = 0078 мин
Остальные режимы резания занесены в таблицу 2.
Таблица 2 Режимы резания
0 Токарная - гидрокопировальная
0 Расточная – гидрокопировальная
Технология ремонта изделия
Об исправной работе машины судят путем сравнения ее настоящих характеристик с нормативными завода-изготовителя. Отклонение характеристик от нормативных и наличие посторонних шумов вибрации и т.п. указывает на те или иные неисправности. Ненормальная работа машины может быть связана как с плохой регулировкой механизмов и систем так и с износом деталей. Все виды износов классифицируют на две группы:
) естественные то есть связанные с нормальной работой машины;
) аварийные которые являются результатом аварии при некачественном обслуживании или неправильном управлении.
1 Анализ возможных дефектов
Крышка фрикциона может иметь следующие дефекты:
-износ рабочих поверхностей;
2 Маршрут оборудование и режимы восстановления
2.1 Восстановление поверхности 276h7 наплавкой в среде СО2
Для восстановления поверхности зубьев используем наплавку в среде СО2.
Параметры и режимы восстановления:
-скорость подачи проволоки V=5ммин.
Операция 005 Наплавка
Операция 010 Расточная
Операция 015 Шлифовальная
2.2 Восстановление отверстий под ремонтные болты
Восстановление отверстий заключается в следующим:
Производит сверление отверстий сверлом диаметром большим первоначального диаметра.
2.3 Восстановление поверхности 396H14 вибродуговой наплавкой. Сущность процесса наплавки заключается в следующем. К наплавляемой поверхности вращающейся детали роликами из кассеты через вибрирующий мундштук подается электродная проволока. Вибрация мундштука осуществляется с помощью электромагнитного вибратора и пружины. Вследствие вибрации происходит замыкание и размыкание сварочной цепи между электродной проволокой и деталью и холостой ход.
В момент короткого замыкания сварочной цепи напряжение резко падает до нуля а сила тока возрастает до максимальной величины. При размыкании сварочной цепи напряжение между электродами быстро повышается до 24—30 В и происходит дуговой разряд в результате которого электродная проволока оплавляется и в виде капель переносится на поверхность детали.
Электрический ток от источника подводится к детали через скользящий контакт. Для повышения устойчивости и длительности дугового разряда в сварочную цепь включают индуктивное сопротивление. В зону наплавки металла через канал с по мощью насоса подается охлаждающая жидкость из фильтра отстойника в результате чего происходит закалка наплавленного металла. В качестве охлаждающей жидкости рекомендуется применять 4—6-процентный раствор кальцинированной соды или 10—20 %-ный водный раствор технического глицерина.
Для обеспечения высокой твердости (51—56 HRC) и износостойкости поверхностного слоя восстанавливаемой детали применяют проволоку типа Нп-80
При восстановлении деталей имеющих форму тел вращения применяется токарный станок с понижающим редуктором который обеспечивает частоту вращения детали до 8 мин-1.
-Частота вибрации Гц 50-100
-Материал . проволока Нп-80
-Оборудование: вибродуговая головка ВДГ-5М.
Операция 010 Точение
Операция 015 Шлифование
В результате проведенной работы разработан технологический процесс изготовления и ремонта крышки БРУ-34-16.02.016 фрикциона Т-34. При этом получены процессы которые предполагают наименьшую себестоимость изготовления и ремонта данной детали. Общая трудоёмкость изготовления составляет Тшк =3.3 мин.
В результате получены практические навыки выбора оптимального варианта процесса изготовления и ремонта что важно для дальнейшей работы на производстве.
Список использованных литературных источников
Горбацевич А.Ф. Шкред В.А. Курсовое проектирование по технологии машиностроения. – Мн.: Вышэйшая школа 1983г.
Дипломное проектирование по технологии машиностроения: Учебное пособие для вузов В.В. Бабук П.А. Горезко К.П. Забродин и др.Под общ. ред. В.В. Бабука. – Мн.: Выш. Школа 1979г.
Конспект лекций по ТПРМ 2007 г.
Справочник технолога-машиностроителя 1 том. – Под редакцией кандидатов технических наук А. Г. Косиловой и Р. К. Мещерякова Москва “Машиностроение”- 1986г.
Справочник технолога-машиностроителя 2 том. – Под редакцией кандидатов технических наук А. Г. Косиловой и Р. К. Мещерякова Москва “Машиностроение”- 1986г.
Рекомендуемые чертежи
- 24.01.2023
- 13.12.2022
- 24.05.2016
- 24.05.2016
Свободное скачивание на сегодня
Другие проекты
- 13.02.2024
- 20.08.2014