Редуктор одноступенчатый косозубый цилиндрический курсовой проект


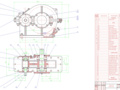
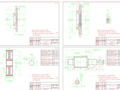
- Добавлен: 25.10.2022
- Размер: 415 KB
- Закачек: 5
Узнать, как скачать этот материал
Подписаться на ежедневные обновления каталога:
Описание
Редуктор одноступенчатый косозубый цилиндрический курсовой проект
Состав проекта
![]() |
![]() ![]() ![]() |
![]() ![]() ![]() ![]() |
![]() ![]() ![]() ![]() |
Дополнительная информация
Контент чертежей
4 рамки.dwg

Готов!!!.dwg

Рекомендуемые чертежи
- 24.01.2023
Свободное скачивание на сегодня
Обновление через: 13 часов 12 минут