Редуктор червячный




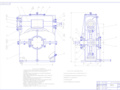
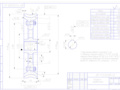
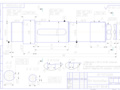
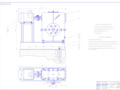
- Добавлен: 25.10.2022
- Размер: 2 MB
- Закачек: 0
Описание
Состав проекта
![]() |
![]() |
![]() ![]() ![]() ![]() |
![]() ![]() ![]() ![]() |
![]() ![]() ![]() ![]() |
![]() ![]() ![]() ![]() |
![]() ![]() ![]() ![]() |
![]() ![]() ![]() ![]() |
![]() ![]() ![]() ![]() |
![]() ![]() ![]() ![]() |
![]() ![]() ![]() ![]() |
![]() ![]() ![]() ![]() |
![]() ![]() ![]() ![]() |
![]() |
![]() ![]() |
![]() ![]() |
![]() ![]() |
![]() ![]() |
![]() ![]() |
![]() ![]() |
![]() ![]() |
![]() ![]() |
![]() ![]() |
![]() ![]() |
![]() |
![]() ![]() |
![]() ![]() |
![]() ![]() |
![]() ![]() |
![]() ![]() |
![]() ![]() |
![]() ![]() ![]() |
Дополнительная информация
Спецификация для редуктора_лист1.dwg

Спецификация для общего вида привода_лист 2.dwg

Спецификация для общего вида привода_лист 1.dwg

Спецификация для редуктора_лист3.dwg

Спецификация для червячного колеса.dwg

Чертеж червячного колеса (сборочный).dwg

Чертеж корпуса червячного редуктора.dwg

Сборочный чертеж червячного редуктора.dwg

Спецификация для редуктора_лист2.dwg

Чертеж общего вида привода.dwg

Чертеж тихоходного вала.dwg

Рекомендуемые чертежи
Свободное скачивание на сегодня
- 22.08.2014
- 29.08.2014