Производственная инфраструктура сервисного обслуживания автопарка и парка спецтехники




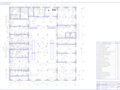
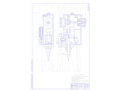
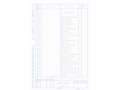
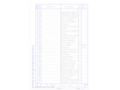
- Добавлен: 25.10.2022
- Размер: 4 MB
- Закачек: 2
Описание
Состав проекта
![]() |
![]() ![]() |
![]() ![]() |
![]() |
![]() ![]() |
![]() ![]() |
![]() ![]() |
![]() ![]() |
![]() ![]() |
![]() ![]() |
![]() ![]() |
![]() ![]() |
![]() ![]() ![]() |
![]() |
![]() ![]() ![]() ![]() |
![]() ![]() ![]() ![]() |
![]() |
![]() ![]() ![]() ![]() |
![]() ![]() ![]() ![]() |
![]() ![]() ![]() ![]() |
![]() ![]() ![]() ![]() |
![]() ![]() ![]() ![]() |
![]() ![]() ![]() ![]() |
![]() ![]() ![]() ![]() |
![]() ![]() ![]() ![]() |
![]() |
Дополнительная информация
Планировка мастерской.dwg

Приспособление для контроля диаметров.dwg

спецификация для планировки3.dwg

спецификация для планировки5.dwg

спецификация для планировки1.dwg

спецификация для планировки2.dwg

спецификация для приспособления2.dwg

спецификация для приспособления.dwg

спецификация для планировки4.dwg

спецификация для планировки6.dwg

Рекомендуемые чертежи
- 23.05.2021
- 02.05.2021
- 13.04.2023
- 03.07.2014