Проектирование участка по выпуску гидроцилиндров НК4040




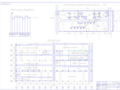
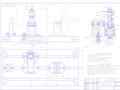
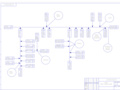
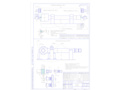
- Добавлен: 25.10.2022
- Размер: 6 MB
- Закачек: 0
Описание
Состав проекта
![]() |
![]() ![]() ![]() |
![]() |
![]() |
![]() |
![]() |
![]() |
![]() |
![]() |
![]() |
![]() ![]() |
![]() |
![]() |
![]() |
![]() |
![]() |
![]() |
![]() |
![]() |
![]() |
![]() |
![]() ![]() |
![]() ![]() ![]() ![]() |
![]() ![]() ![]() ![]() |
![]() ![]() |
![]() ![]() ![]() ![]() |
![]() ![]() ![]() ![]() |
![]() ![]() |
![]() ![]() |
![]() ![]() |
![]() ![]() |
![]() ![]() |
![]() ![]() ![]() ![]() |
![]() ![]() |
![]() ![]() |
![]() ![]() ![]() ![]() |
![]() ![]() ![]() ![]() |
![]() |
![]() ![]() ![]() ![]() |
![]() ![]() ![]() ![]() |
![]() |
![]() ![]() ![]() |
![]() ![]() ![]() |
![]() ![]() ![]() |
![]() ![]() |
![]() ![]() ![]() |
Дополнительная информация
Доклад диплом.docx
Объектом проектирования является шток гидроцилиндра. Шток является основным узлом гидроцилиндра Деталь – шток входит в состав силовой системы механизма затвора (Р=157кН).
Шток тело вращение длиной l=588 мм с максимальным диаметром 100мм. Деталь изготовлена из стали 40Х ГОСТ4543-71. Шток весит 84 кг максимальный перепад диаметров 60мм на 355 мм
В данном курсовом проекте была разработана схема сборки. Схема сборки определяет последовательность и содержание сборочных операций. Базовой деталью является корпус установленный при сборки на свою конструкторскую базу.
Организация схемы сборки – узловая с разделением операций.
- снижение цикла сборки;
- снижение требований в квалификационных кадрах (узкая специализация рабочих);
- снижение трудоемкости и стоимости сборки при повышении уровня механизации и технологической подготовке и производства;
- применение специализированного оборудования для типовых операций сборки деталей;
- снижение нагрузки и производственных площадей сборочного участка.
Метод достижения точности сборки – метод неполной взаимозаменяемости.
Деталь представитель – «Шток»
Шток обеспечивает перемещение оси путем преобразования собственного поступательного движения в поступательное сопрягаемой оси. Шток является подвижным звеном механизма перемещения оси исполнительного механизма перемещения оси исполнительного механизма комбайна
Конструкции штока предусматривает 2 посадочных места под подшипник скольжения 50f9 Ra063мкм. Поверхность подвергается покрытию хромом – гальваника (что позволяет достигнуть износостойкости рабочей поверхности) а так же 40h8 Ra25 мкм под установку поршня. Для выхода шлифовального круга и при нарезке резьбы М36х2 предусмотрены 2 канавки. Расточенное отверстие 67Н7 в шестиграннике позволяет осуществить передачу поступательного движения оси (внутри шестигранника выполнена посадочная место под наружное кольцо подшипника скольжения и стопорные кольца).
Твердость штока в пределах 241 285 НВ (определяется механическими свойствами материала). Деталь выполнена из стали 40Х ГОСТ 4543-71.
. Заготовку можно получить штамповкой на ГКМ. Штамповкой на ГКМ получают заготовки массой 01 200 кг диаметром до 315 мм с Rz от 320 до 160 мкм. В Качестве исходного материала для штамповки на ГКМ можно использовать сортовой прокат но так как производство мелкосерийное а производительность штамповки на ГКМ целесообразно для крупносерийного и массового производства (иначе не окупается высокая стоимость заготовки) эффективность данного способа следует доказать
На основании анализа вариантов принимаем заготовку поковку штампованную на КГШП. Штамповочное оборудование – кривошипный горячештамповочный пресс; нагрев заготовок – индукционный. Стоимость заготовки получаемой на КГШП ниже 318 грн чем 362 грн ГКМ.
Определили серийность производства. Серийность производства определена по коэффициенту закрепления операций . Для детали шток производство мелкосерийное.
В данном дипломном проекте были рассчитаны припуска разработан технологический процесс механообработки.
В базовый тех. процесс были внесены следующие изменения:
- исключена разметочная и токарные операции как операции по подготовки черновых баз торцы обрабатываются на фрезерно-центровальном полуавтомате МР71-М;
- получистовая и чистовая обработка детали выполняется на токарно-винторезном с ЧПУ FCL-15TTY.
Для детали выполнены точностные расчеты разработана схема базирования определена схема базирования по основным операциям.
Для переходов программной обработки штока выполненных на токарно-винторезном станке с ЧПУ FCL-15TTY разработаны РТК. Особенностью операции является то что произходит обработка многопереходного тоцения контурная обрабортка точение канавок и нарезание резьбы. Для переходов обработки точением применен современный режущий инструмент. Режимы резания на эти переходы рассчитаны на ЭВМ.
Были рассчитаны режимы резания и нормы времени. В результате принятых новых решений достигнуто снижения трудоемкости на 40-45.
Конструкторская часть проекта
Для расточной операции детали «шток» на было спроектировано приспособление гидроприхват.
Разработанное приспособление конструировалось для серийного производства и позволяет выполнять простую и надёжную установку детали с обеспечением её легкой установки базированя.а так же закрепления детали Шток.
Разработана схема базирования выполнен её анализ. Для приспособления выполнены следующие расчеты:
) Силовой расчет. Цель – определения требуемого усилия закрепления расчет привода обеспечение неподвижности заготовки под действием сил резания.
)Точностной расчет. расчет допускаемой точности приспособления при обработки самого точного размера на данной операции.
) Прочностной расчет. На прочность рассчитана резьба штока так как было определено наименьший диаметр являющийся опасным сечением.
Для точного контроля детали «шток» было разработано переносное перенастроечное приспособление для контроля торцевого биения.
Анализ использования современного инструмента в условиях производства «ГМЗ»
Было проанализированы расходы на инструмент оборудование инструментальную оснастку что дало повод для сравнительных расчетов на затраты напайного инструмента и современного сборного. Расчеты показали что для мелкосерийного производства выгода составила 10% а для серийного или крупносерийного преимущество сборного инструмента возрастает достаточно. Если учитывать режимную часть то напайной инструмент проигрывает тем самым преимущество сборного современного инструмента возрастает и по времени обработки.
Вывод: Современный инструмент выгодно использовать в сочетании со станками с ЧПУ в мелкосерийном производстве но большую эффективность инструмент получает с возрастанием серийности.
За счет этого: уменьшаются затраты на инструмент использование специального оборудования для перезаточки повышатся эффективность обработки и возрастает качество.
- снижение трудоемкости сборки на 15-20;
- снижение трудоемкости механообработки в 05;
- применено новое оборудование оснастка.
Сборка.dwg

Гидроцилиндр в сборе
Кольцо 090-100-58-25
Спецификация изм.dwg

Индикатор часового типа
Заготовка.dwg

степень сложности-С1
исходный индекс-14) ГОСТ 7505-89
Нагрев заготовки - индукционный
Удаление облоя - механическое
Очистка - пескоструйная
Остальные ТТ - по ГОСТ 8479-70
Маркировать шривтом 6 - ПРЗ ГОСТ 26020-80
РТК.dwg

Резец для угловых канавок 25х25 Т15К6 ТУ2035-558-77
Резец канавочный в=5 Т15К6 К01-4112
Резец резьбовой 25х25 Т15К6 В=60
0 Токарно-винторезная с ЧПУ
Приспособление.dwg

Диаметры закрепления деталей 40 60 мм.
Давление в полости гидроцилиндра 10 МПа.
Усилие закрепления Qф=12586 Н.
Погрешность приспособления Епр=0
Перед началом работы испытать в течении 30 мин гидросистему
Т=20 мин. Утечек масла не допускать.
Регулировка упора посредством болтов 12
стопорение гайкой 17.
Обеспечить главный ход всех рабочих поверхностей.
Смазать все трущиеся элементы густой смазкой
Переодичность контрольных праверок - 1раз в месяц
Цех испр.dwg

Участок складирования
Компановочно-планировочное
Участок обработки корпусных деталей
Специализированный участок механообработки
Участок обработки тел вращения
Термическое отделение
Заготовительное отделение
Инструментальная кладовая
Компановачно-плпнировочное решение участка 1:200
График загрузки оборудования
Спецчасть.dwg

Фрезерный инструмент
Инструментальная оснастка
Спецификация установ.dwg

Карты наладок.dwg

Расточить предварительно
Расточить окончательно
Режущий и вспомогательный инструмент
Сверло центровое В4 Р6М5 ГОСТ 14952-75
Режущий и вспомогательный инструмент
резец канавочный в=1
резец фасочный Т5К10 ГОСТ 9798-84
5 Фрезерно-центровальная
0 Горизонтально-расточная
Отверстие центровое В4 ГОСТ 14034-74
Призмы самоцентрирующие
ЗАПИСКА.docx
Цель работы – Сформировать навыки самостоятельного проектирования технологических процессов сборки и механообработки изделий технологической оснастки средств механизации и автоматизации направленные на закрепление полученных ранее знаний.
Технологическая часть состоит из пунктов в которых рассмотрены процессы сборки гидроцилиндра и механообработки штока. Произведен анализ на технологичность выполнен анализ имеющегося базового технологического процесса. Выполнены расчеты режимов резания произведено нормирование операций технико-экономическое обоснование выбранного проектного варианта операции механической обработки и заготовки для детали-представителя.
В конструкторско-технологической части спроектировано станочное приспособление для горизонтально-расточной операции и контрольное приспособление для контроля радиального и торцевого биения посадочных шеек штока.
В специальной части проекта были проанализировано использование современного инструмента в условиях производства.
ШТОК ПРИПУСК РЕЖИМЫ РЕЗАНИЯ МАШИННОЕ ВРЕМЯ ШТУЧНО-КАЛЬКУЛЯЦИОННОЕ ВРЕМЯ ПРИСПОСОБЛЕНИЕ РАСЧЁТНО-ТЕХНОЛОГИЧЕСКАЯ КАРТА ЭКОНОМИЧЕСКИЙ ЭФФЕКТ СЕБЕСТОИМОСТЬ
ТЕХНОЛОГИЧЕСКАЯ ЧАСТЬ . .10
1 Разработка технологического процесса сборки узла .10
1.1 Техническое описание и служебное назначение узла 12
1.2 Отработка узла на технологичность .. 14
1.3 Определение метода достижения точности замыкающего звена при сборке 15
1.4 Выбор организационной формы сборки 24
1.5 Разработка последовательности и содержание сборочных операций. 25
1.6 Выбор оборудования и технологической оснастки . 28
2. Разработка процесса изготовления штока
2.1 Анализ служебного назначения и технического описания детали шток 33
2.2 Анализ детали шток на технологичность . 35
2.3 Выбор типа и организационной формы производства.. ..41
2.4 Анализ технологического процесса изготовления детали шток . .47
2.5 Выбор и обоснование вида и способа получения заготовки . .55
2.6 Определение припусков расчетно-аналитическим методом . .56
2.7 Разработка маршрутной технологии механической обработки 56
2.8 Точностные расчеты при механообработки детали шток 61
2.9 Расчет режимов резания 66
2.10 Техническое нормирование операций 66
2.11 Технико-экономическое обоснование проектного варианта технологического процесса . 66
КОНСТРУКТОРСКО-ТЕХНОЛОГИЧЕСКАЯ ЧАСТЬ 66
1 Разработка схемы базирования детали . ..68
2 Силовой расчет приспособления 70
3 Выбор привода и расчет основных характеристик ..75
4 Точностной расчет приспособления 81
5 Прочностной расчет приспособления . 81
6 Техническое описание приспособления . 82
7 Разработка контрольного приспособления ..84
СПЕЦИАЛЬНАЯ ЧАСТЬ .. .86
1 Эффективность применения инструмента со сменными пластинами (СМП) 87
2 Дорогой инструмент — целесообразно ли это? 90
3 Экономическая эффективность применения высокотехнологичного инструмента. .91
ТЕХНОЛОГИЧЕСКОЕ ПРОЕКТИРОВАНИЕ ЦЕХА ..75
ОРГАНИЗАЦИОННО-ЭКОНОМИЧЕСКАЯ ЧАСТЬ 81
1 Расчёт капитальных расходов 81
2 Расчёт текущих затрат 82
3 Расчёт калькуляции себестоимости продукции ..84
4 Расчёт эффективности проекта .86
ОХРАНА ТРУДА И ТЕХНИКА БЕЗОПАСНОСТИ 88
ПЕРЕЧЕНЬ ССЫЛОК .98
Приложение А. Анализ базового технологического процесс 101
Приложение Б. Маршрутные и операционные карты 109
Приложение В. Карты эскизов .126
Приложение Г. Спецификации .130
Развитее машиностроения должно осуществляться за счет комплексной механизации и автоматизации использования прогрессивной технологии направленной на сокращение рабочих мест автоматизации проектно-конструкторских и технологических разработок. В целях постоянного ускорения и снижения затрат механообработки предусматривается развивать его в основном за счет использования станков с ЧПУ агрегатных станков обрабатывающих центров автоматических линий и т.д. Вторичным направлением ускорения развития машиностроения является повышение научно-технологического уровня сборочного производства обладающего самыми крупными потенциалами резервами для повышения эффективности производства. Основной эффект от использования станков с ЧПУ состоит в значительном снижении вспомогательного времени и увеличении доли машинного временив составе штучного времени. Но одновременно это оборудование в комплексе с автоматическими системами управления от ЭВМ является сложным и дорогостоящим. Поэтому необходимым условием его эффективности является технологичность производимых деталей использование наиболее прогрессивных техпроцессов методов обработки и т.д.
Целью работы является закрепление и углубление полученных в академии знаний пополнение их основными сведениями приобретение практических навыков самостоятельного проектирования технологических процессов сборки и механообработки изделий технологической оснастки средств механизации и автоматизации информационного обеспечения технологических и других работ.
Для этого используется базовый технологический процесс который анализируется и корректируется в соответствии с передовыми процессами обработки. Завод ограничен в своих возможностях в то время как имеется возможность использовать самые новейшие разработки в отрасли машиностроения.
Данная работа ориентирована на решения реальных технологических конструктивных и научно-исследовательских задач в области разработки ресурсосберегающих технологий автоматизации проектирования и производства повышение качества продукции организации производства и улучшения его технико-экономических показателей.
ТЕХНОЛОГИЧЕСКАЯ ЧАСТЬ
1Разработка технологического процесса сборки узла
1.1 Техническое описание и служебное назначение узла
Объектом проектирования является гидроцилиндр НК4040 проходческого комбайна который является машиной применяют в горнодобывающей промышленности. Функцией проходческого комбайна как технологической машины является обеспечение добычи и дальнейший транспортировки каменного угля. Гидроцилиндр входящий в состав комбайна как любой другой гидроцилиндр обеспечивает создание осевого усилия на выходном (исполнительном) звене механизма под воздействием создания давления в поршневой полости. Таким образом фактически гидроцилиндр является осевым усилием.
Техническая характеристика изделия:
- рабочая жидкость – масло гидравлическое ВННИНП-403
- рабочий ход поршня – 277 мм;
- рабочее давление – 20Мпа;
- рабочие площади полостей:
а) поршневой 785 см2;
- рабочие объемы полостей:
а) поршневой 217445 см2;
б) штоковой 16315 см2;
- усилие при рабочем давлении:
а) толкающее – 157кН;
Гидроцилиндр подвергается испытаниям согласно соответствующей б таблице.
Основными узлами гидроцилиндра являются гидрозамок 4 поршень 2 крышка 1 корпус 6 а также детали шток 15 фланец 12 гайка 10 подшипник 28.
Базовой деталью узла является корпус 6 сборочный узел скомпонованный и собранный посредством сварки из деталей – полуфабрикатов корпус 1 крышка 5 заглушка 10. В корпусе 6 посредством крышки 1 установлен шток 15 с поршнем 2. Фиксация поршня 2 на штоке 15 при помощи гайки 10 и шплинта 24. Герметичность штоковой и поршневой полостей обеспечивается наличием защитного кольца 11 кольца 20 поршневого уплотнения 30 31. Фиксация крышки 1 на корпусе 6 – при помощи наружного кольца 13. На корпусе 6 приварен гидрозамок 4.
1.2 Обработка узла на технологичность.
Сборочная единица «гидроцилиндр» разделяется на рациональное число сборочных единиц существующих индивидуально собираемых независимо и взаимозаменяемых в процессе сборки и ремонта устройства.
Компоновка узла выполняется из взаимозаменяемых узлов и деталей. Большое количество деталей изготовлено по ГОСТУ (стандартные изделия) или имеют отраслевую стандартизацию.
Сборка изделия не требует применения сложного технологического оборудования и оснащения имеет место частичная механизация проведения сборочных работ.
В узле имеется небольшое количество соединений установленных по резьбе кроме того есть соединения гладкие с натягом (установка пружинных колец). Все соединения удобны при сборке.
Габаритные размеры и форма изделий позволяет транспортировать и монтировать составляющие узла без создания дополнительных технологических трудностей.
Базовая составная часть (сборочная единица) корпус 6 является основой для установки прочих узлов и деталей. Конструктивные особенности узла позволяют производить общую сборку изделия без промежуточной разборки; удобный доступ к местам контроля регулировка и регламентным работам. Легкосъемность элементов составляющих узел обеспечена.
1.3 Выбор и обоснование метода достижения требуемой точности сборки
Собираемое изделие – гидравлический механизм усилие высокого давления. Служебное назначение гидроцилиндра предусматривает высокую точность сопряжений элементов:
- корпус и поршень (100 H9f9)
- шток и поршень (40 Н9n8)
- шток и крышка (50 H9f9)
- корпус и крышка (100 Н9f9 и 105 H9f9)
Герметичность соединений обеспечивается установкой колец и уплотнений. Предохраняет полости от попадания в них пыли скребок 29.
Выполнение сопрягаемых диаметральных поверхностей в пределах величин допусков в процессе механообработки позволит собирать изделие по методу полной и неполной взаимозаменяемости (с минимальной вероятностью возникновения брака).
Метод неполной взаимозаменяемости обеспечивает достаточно высокий выход годных деталей (порядка 97-99%) со значительно меньшими затратами времени на механообработку по сравнению с методом полной взаимозаменяемости. Сборка при этом осуществляется без выбора подбора регулировки или подгонки изделий входящих в узел.
Точность сборки линейных размеров деталей входящих в узел «гидроцилиндра» не регламентируется.
1.4 Выбор организационной формы сборки
В основном выбор организационной формы сборки узла определяет тип производства.
Предварительно тип производства – мелкосерийное. Данный тип характеризуется довольно частой сменой объектов производства при небольших производственных партиях. Рекомендуемый принцип сборки – непоточная стационарная сборка характеризуется последовательной подачей сборочных узлов и деталей к месту сборки. Все сборочные узлы и детали подаются на отдельных рабочих местах. Таким образом технологический процесс сборки составляется из отдельных операций расчлененных между собой.
Характер сборки полностью отражается в разработанном маршрутном техпроцессе сборки.
1.5 Разработка последовательности и содержания сборочных операций
Для узла гидроцилиндр разработана схема сборки приведенная на листе 1 ДП.
Маршрут сборки состоит из следующих операций сборочной технологии.
Комплектовать изделия согласно спецификациям.
Промыть и протереть детали. Расконсервировать покупные узлы и изделия.
Выборочный входной контроль
0 Слесарно-сборочная (узловая)
Установить и закрепить поршень 2. Минеральным маслом смазать поршневое уплотнение 30 установить.
5 Слесарно-сборочная (узловая)
Установить шток 15 закрепить. Смазать минеральным маслом кольца 1120. Установить. Запрессовать поршень в сборке 2. Стопорить гайкой 10 и шплинтом 24. Охладить подшипник 28. Установить кольцо 23 подшипник 28 подшипник 28 кольцо 23.
Установить крышку 1 закрепить. Смазать маслом детали поз. 21223129 установить.
5 Слесарно-сборочная (общая)
Корпус 6 установить закрепить. Охладить подшипник 28. Установить детали в последовательности: 23-28-23. Установить поршень со штоком в сборе крышку 1 кольцо 13. Фиксация фланцем 12 болтами 19 проволокой 35. Установить гидрозамок 4 по средством сварки.
Согласно схеме испытаний предупреждается и выполняется.
1.6 Выбор оборудования и технологической оснастки.
Для установки и закреплении деталей цилиндрической формы используется призмы прихваты планки упоры.
Для установки и закрепления деталей типа пустотелые втулки используются втулки опорные тиски с призматическими губками.
Для прочих деталей используется также элементы приспособлений так же призмы опоры планки шайбы гайки струбцины механические элементы УСП регулируемые и др.
Типовой контроль элементов осуществляется с использованием специализированного инструмента и приспособлений контроля с операцией механообработки.
В комплект слесарно-сборочных инструментов входят молотки слесарные втулки и направляющие плоскогубцы напильники и др.
Частичная механизация слесарно-сборочных работ достигается за счет применения пневмо- гидро- электроинструмент и приспособлений: гидропрессы ручные электродрели шлифовальные машинки гайковерты электроотвертки.
2Разработка технологического процесса изготовление штока
2.1 Анализ служебного назначения и технического описания детали шток
Деталь – шток входит в состав силовой системы механизма затвора (Р=157кН).
Шток тело вращение длиной l=588 мм с максимальным диаметром 100мм. Деталь изготовлена из стали 40Х ГОСТ4543-71. Шток весит 84 кг максимальный перепад диаметров 60мм на 355 мм.
Шток обеспечивает перемещение оси путем преобразования собственного поступательного движения в поступательное сопрягаемой оси. Шток является подвижным звеном механизма перемещения оси исполнительного механизма перемещения оси исполнительного механизма комбайна.
Конструкции штока предусматривает 2 посадочных места под подшипник скольжения 50f9 Ra063мкм. Поверхность подвергается покрытию хромом – гальваника (что позволяет достигнуть износостойкости рабочей поверхности) а так же 40h8 Ra25 мкм под установку поршня. Для выхода шлифовального круга и при нарезке резьбы М36х2 предусмотрены 2 канавки. Расточенное отверстие 67Н7 в шестиграннике позволяет осуществить передачу поступательного движения оси (внутри шестигранника выполнена посадочная место под наружное кольцо подшипника скольжения и стопорные кольца).
Твердость штока в пределах 241 285 НВ (определяется механическими свойствами материала). Деталь выполнена из стали 40Х ГОСТ 4543-71. Данная сталь относится к легированным сталям. Область применения детали работающей на износ покрытые хромом поверхности позволяет сделать вывод что деталь работает в условиях трения скольжения и испытывает на себя нагрузки приводящие к износу рабочих поверхностей.
Химические и механические свойства приведена в таблице 1 и 2
Таблица 1 – Химический состав стали 40Х (ГОСТ 4543-71)%
Таблица 2 –Механические свойства стали 40Х
2.2 Анализ детали шток на технологичность
Деталь является технологичной она может быть изготовлена на стандартном оборудовании с использованием стандартного режущего и измерительного инструментов.
Параметр точности и размерные связи поверхностей детали шток представляет собой тело вращения с пятью ступенями: 2 из которых 40h8 длиной 20 и 40 мм третья М36х2 резьба на L=43 мм четвертая 50f9 L=355 мм с Ra063 мкм рабочая зона трения-скольжения пятая ступень представляет собой шестигранник с внутренним отверстием 62Н7 посадочным местом подшипника скольжения. Для обеспечения точности обработки детали в ее торцах имеются центровочные отверстия.
Чертежом обусловлена сквозная обработка всех поверхностей детали.
Количественную оценку технологичности детали проведем по следующим показателям:
- По точности обработки;
Для повышения использования материала стремится к тому что значения коэффициента характеризующих каждый показатель стремилось к единице. Уровень технологичности по точности обработки определим по формуле:
где Тср – средний квалитет точности обработки деталей.
где Ті – квалитет точности отдельной поверхности;
ni –число размеров соответствующего квалитета точности.
Таблица 3 – Данные анализа технологичности детали
По точности изготовления изменение производить не целесообразно так как может повлечь непригодность корпуса подшипника к работе или усложнит процесс его сборки тогда
Коэффициент точности обработки будет равен:
Коэффициент точности шероховатости детали равен
где Шср – средняя шероховатость поверхностей
Для анализа технологичности по этому показателю составим таблицу 4
Таблица 4 – Данные анализа технологичности детали
Средняя шероховатость обработанных поверхностей будет равна.
Коэффициент шероховатости будет равен:
Технологичность по показателю использования материала Ким определяем при обоснованным экономически целесообразного варианта получения заготовки по базовому варианту:
По совокупности проведенного анализа по качественным характеристикам деталь «Шток» следует считать технологичной.
2.3 Выбор типа и организационной формы производства
Приведенная годовая программа
где m – число узлов в изделии
α – процент деталей идущих в запчасти и на неизбежные потери.
Годовой фонд работы оборудования Fд=4015 ч;
Нормативный коэффициент загрузки Кн=08;
Тт – производства по ГОСТ 3.1108-74 характеризуется коэффициентом закрепления операции:
где – число операций;
Количество станков определяется по формуле:
где – штучное время обработки детали фактический коэфициент загрузки оборудования:
Количество операций выполненных на одном рабочем месте:
Расчет коэффициента закрепления операций приведен в таблице 5
Таблица 5 – Расчет коэффициента загрузки
Продолжение таблицы 5 – Расчет коэффициента загрузки
Вертикально-фрезерная
Горизонтально-расточная
Тшт производства – мелкосерийный.
2.4 Анализ базового технологического процесса изготовления детали-представителя
Анализ базового технологического процесса представлен в виде таблицы в приложении А данного дипломного проекта.
2.5 Определение способа получения заготовки определение припусков
При выборе заготовки главным является обеспечение заданного качества готовой детали при ее минимальной себестоимости. Себестоимость детали определяется суммирование себестоимости заготовки по калькуляции заготовительного цеха и себестоимости ее последующей обработки достижения заданных требований по чертежу. Заготовку можно получить штамповкой на ГКМ. Штамповкой на ГКМ получают заготовки массой 01 200 кг диаметром до 315 мм с Rz от 320 до 160 мкм. В Качестве исходного материала для штамповки на ГКМ можно использовать сортовой прокат но так как производство мелкосерийное а производительность штамповки на ГКМ целесообразно для крупносерийного и массового производства (иначе не окупается высокая стоимость заготовки) эффективность данного способа следует доказать.
Полученная заготовка на КГШП может быть выгодно если затраты на изготовление штампов и амортизационные расходы по использованию оборудования не будет превышать допустимой величины так как данный способ получение заготовок тоже не дешевле.
Но так как даже изготовление заготовки детали «шток» прокат использован не может быть так как большой перепад диаметровдетали с 100 до 40 мм.
Затраты на заготовку полученную на ГКМ можно оценить по формуле:
где С – цена 1 кг поковки;
q – масса готовой детали;
где Кр – коэффициент для определения ориентировочной расчетной массы поковки (ГОСТ 7505-89) табл. 20.
Для детали типа вал Кр=12 тогда
Коэффициент использование материала
Стоимость заготовки составляет по первому варианту:
Где S1 – Стоимость 1 кг заготовок изготовляют на ГКМ
К1 – коэффициент учитывающий сложность поковки К=15
К2 – коэффициент учитывающий массу заготовок К2=13 для поковок массой выше 1 кг.
К3 – коэффициент учитывающий программу выпуска заготовок К3=30
К4 – коэффициент выбираемый в зависимости от материала заготовки К4=12 (для стали 40Х).
Тогда стоимость заготовки по этому варианту составляет:
По второму варианту деталь изготавливается из поковки штампованной полученной на КГШП по ГОСТ 7505-89. Предлагается что припуск на обработку поверхностей равномерный и равен 5 мм на сторону что на диаметр составит 10 мм.
Масса штампованной поковки определяется по формуле:
где Кр – коэффициент для определения ориентировочной расчетной массы поковки (ГОСТ 7505-89) табл. 21.
Для детали типа вал Кр=15 тогда
Стоимость заготовки составляет по второму варианту:
Где S2 – Стоимость 1 кг заготовок изготовляют на ГКМ
На основании анализа вариантов принимаем заготовку поковку штампованную на КГШП. Штамповочное оборудование – кривошипный горячештамповочный пресс; нагрев заготовок – индукционный.
Класс точности – Т4.
Степень сложности – С1.
Конфигурация поверхности разъема штампа – П.
Исходный индекс – 14
Дополнительный припуск учитывающий отклонение от плоскости и прямолинейности – 12 мм; смещение по поверхности штампа – 05.
Штамповочный уклон по наружной поверхности не более 7º.
мм – для диаметра 50 мм (Ra 063)
мм – для диаметра 100 мм (Ra 10)
мм – для длины 588 мм (Ra 10)
мм – для длины 105 мм (Ra 10)
Расчет номинальных размеров заготовки:
0+20(25+05+12)=1084 мм
5+(2+05+35+05)=1115 мм
Рисунок 1 – Эскиз заготовки полученной штамповкой по ГОСТ 7505-89
Окончальные размеры заготовки определяются в пункте 1.2.6.
2.6 Определение припусков расчетно-аналитическим методом.
Припуск – слой металла удаляемый в процессе обработки. Назначение оптимальных припусков оказывает прямое влияние на трудоемкость и время обработки а также на точность обработки.
Завышение припусков приводит к увеличению трудоемкости а также к повышенному износу инструмента и оборудования. Занижение припусков приводит к браку в процессе обработки.
- заготовка штамповка Rz=160 =12;
- предварительное точение Rz=80 =074 (14 кв.);
- получистовое точение Rа=25 =019 (11 кв.);
- окончательное точение (обкатывание) Rz=125 =0062 (9 кв.);
- полировка Rz=125 =0062 (9 кв.)
Расчёт припусков приведён в таблице 7.
Таблица 7 – Расчёт припусков на обработку ø30k6
Припуск на обработку диаметральных размеров определяется по формуле:
Zmin=2(Rzi-1+Ti-1+)
где - погрешность базирования т.к. деталь устанавливается в центрах или патроне
з – погрешность закрепления мкм
- при предварительном точение з=200 мкм;
- при окончательном точение з=0 мкм;
- при отделке з=0 мкм;
пр-погрешность приспособления мкм;
- при предварительном точении пр=100 мкм;
- при окончательном точении пр=30 мкм;
- при отделке пр=10 мкм.
где ρкор – коробление заготовки мкм;
ρсм – суммарная погрешность штампов;
где ky – коэффициент ужесточения ку1=006; ку2=004; ку3=002; ку4=001.
dрi-1=dрi+2Zmin (10.4)
Dmin получаем путем округления dрi до количества знаков в припуске.
Zmax пр =dmaxi-1-dmaxi
Zmin пр = dmin-1-dmini
где Нd Нз – нижнее отклонение детали и заготовки мм;
Zном=418-0087+04=45 мм.
Дзаг=49975+45=54475 мм.
Принимаем из ряда нормальных размеров Дзаг=55
Рассчитаем припуск на длину L=588±0875мм
План обработки торца
Заготовка штамповка Rz=160; =48
Фрезерование предварительное Rz=100; Т=100; =28 (h15);
Фрезерование окончательное Rz=80; Т=80; =175 (h14).
Минимальный расчётный припуск (двухсторонняя одновременная обработка противоположных торцов)
Zmin=2(Rz-1+Ti-1+ρi-1+і) мкм
Расчет припусков приведен в таблице 8.
Таблица 8 – Расчёт припуска по L=588 мм
Где б=0 мкм; з=0 мкм; пр1=1=400 мкм; пр2=2=0 мкм.
Номинальный припуск:
Zном==3875+16-0875=46 мм;
Lзаг=Lд+2Zном=588875+46=593475 мм
Принимаем Lзаг=594 мм
Определим коэффициент ужесточения на припуски на обработку линейных размеров:
Куж диам=ZрZгост=575=067
Куж диам=ZрZгост=68=075
Таблица 9 - Ужесточение припусков на размеры
Ужесточённый припуск мм
Таким образом размеры заготовки определены с учётом реальных условий обработки чертёж заготовки приведён на листе А2 графической части данного дипломного проекта ДП.000.000.002.
2.7 Разработка маршрутной технологии механической обработки.
Операции подготовки баз осуществляется на фрезерно-центровальном станке. Особенность данного оборудования такова что процессы фрезерования и сверления осуществляются совместно то есть выполняется одновременно фрезерование торцов а затем зацентровка с двух сторон что приводит к сокращению основного времени обработки повышается точность обработки за счет исключения погрешности базирования исключается необходимость переустановки детали для обработки противоположного торца. В качестве станочного приспособления используется переналаживаемые призматические опоры с механизированным прихватом для закрепления заготовки. Режущий и мерительный стандартный.
Фреза торцевая 125 с пластинами Т5К10 и Т15К6; сверло центровочное из Р6М5 мерительный инструмент – универсальный штангенциркуль шаблон на центровочное отверстие.
Чернова и чистовая токарная обработка выполняется по принципу концентрации операций на токарно-винторезных станках универсальном с ЧПУ модели CW6180 и FCL-15TTY. Оборудование станка с ЧПУ дорогостоящее но здесь возможна экономия за счет сокращения основного и вспомогательного времени.
Установочно-зажимные приспособления в виде механизированных самоцентрирующих патронов центров люнетов и т.д.
В качестве режущего инструмента применяются напайные резцы с твердым сплавом для универсального оборудования и сборные контурные резцы для станков с ЧПУ оснащенные твердым сплавом – для контурного точения канавочные мерительный инструмент – универсальный (штангенциркуль образцы шероховатости).
Фрезерование шестигранника выполняется на станке вертикально-фрезерной группы модели FSS-400. В качестве приспособления используется переналаживаемое приспособление с призматическими опорами с механическими прихватами для закрепления заготовки. Базирование детали по опорным шейкам. Режущий инструмент – фреза концевая 40 Р6М5. Мерительный инструмент – стандартный.
Расточка отверстий 62Н7 и канавок 65Н12 выполняется на горизонтально-расточном станке модели ТРХ6111В2. В качестве приспособления используем призматические опоры с переналаживаемыми прихватами и упоры для закрепления заготовки. Режущий инструмент – оправка с механическим креплением резца что позволяет осуществлять быструю смену режущего инструмента резцы расточные Т5К10 Т15К6 резец расточной канавочный оснащен твердым сплавом пластиной Т5К10. Мерительный инструмент стандартный нутромер микрометрический НМ 0-65 ГОСТ 1678-80 шаблон канавочный в=19 штангенциркуль.
Операции шлифования производится на кругло-шлифовальном станке модель 3М151 универсально группы. Приспособление – поводковый патрон формообразующий. Инструмент круг шлифовальный ПП600х40х305 24А 50СМ1К6 35мс ГОСТ2424-83. Контроль качества поверхностей по образцам шероховатости индикаторные средства для контроля размеров.
2.8 Точностные расчеты при механообработке детали шток
Точностные расчеты направлены на выявление и оценку возможных погрешностей проявляющихся в процессе механообработки. В условиях серийного производства когда обработка деталей на большинстве операции производится на станках настроенных на размер особенную важность имеет погрешность базирования. Приблизительно можно также определить погрешность закрепления и приспособления.
Погрешность установки
где – погрешность базирования закрепления приспособления.
Выполняются расчеты на основе составленных схем базирования.
Рисунок 2 – Схема базирования детали на фрезерно-центровальном станке (установка в спаренные самоцентрирующие призмы)
Установка в центра или трехкулачковом патроне с приводом обеспечивает довольно точно центрирование детали (совмещается технологическая база с измерительной).
где – допуск на размер L1.
Рисунок 3 – Схема базирования детали на токарных универсальных и кругло-шлифовальной операции
Величина должна быть учтена при расчете припусков на механообработку.
– переменная и зависит от величины усилия закрепления а также ее направления.
Рисунок 4 – Схема базирования детали на станках фрезерно-сверлильной-расточной группы (установка детали в призмы по упору)
где α – угол призм; α=90º 120º.
– допуск на базовые диаметры.
Анализируя полученные формулы можно сделать вывод о возможном получении размеров требуемой точности так как показатели управляемые.
2.9 Расчет режимов резания
Токарно-винторезная (чистовая) с ЧПУ.
Исходные данные: деталь шток материал – сталь 40Х масса детали – 84 кг заготовка поковка штампованная обработанная на черновой токарной операции. Обрабатываем 40h8 с припуском под шлифование. Точить 2 канавки вид Г и Б точить фаски и R2.
Определим режимы резания.
Станок токарный с ЧПУ модель FCL-15TTY резец проходной контурный с механическим креплением Т15К6 ф=60º ГОСТ2685-80.
Резец канавочный в=76 с механическим креплением Т15К6 ГОСТ 26485-80 в=3 с механическим креплением Т15К6 ГОСТ 26475-80 глубина резания t=15 число проходов i=1 S=02 ммоб.
Определяем скорость резания по формуле:
где Сv=340; y=045; m=02 – коэффициент и показатели степени характеризующие условия резания;
T – стойкость пластинки резца Т=60 мин;
Kv – коэффициент учитывающий условия обработки.
Kmv – коэффициент зависящий от состояния поверхности заготовки Kпv=10
Kuv – коэффициент зависящий от материала режущего инструмента для Т15К6 Кuv=10
Kv=078·08·10·09·10·094=052
Скорость резания равна:
Частоту вращения шпинделя определим по формуле:
Принимаем nст=1000 мин-1.
Фактическая скорость резания:
Силу резания определим по формуле:
Pz=10·Cp·tx·Sy·Vn·Kp
гдеCp=300; y=075; n=-015 – коэффициент и показатели степени характеризующие условия резания;
Kp – поправочный коэффициент на силу резания
Kmp – коэффициент учитывающий влияние обрабатываемого материала:
Kφ – коэффициент зависящий от заточки режущего инструмента Kφ=09;
Kr – коэффициент зависящий о радиуса скругления режущей кромки Kr=094. Тогда:
Тогда величина силы резания будет равна:
Pz=10·300·0510·02075·1275-015·101=6599 Н
Мощность резания определим по формуле:
Эффективная мощность на шпинделе станка равна:
Nэф=Nст·=10·085=85 кВт.
Т.к. мощность необходимая для резания меньше эффективной мощности станка (136 кВт 85 кВт) то резание с принятыми режимами возможно.
Основное время на токарную операцию равно:
гдеLр.х – длина рабочего хода режущего инструмента
lд – длина обрабатываемого участка lд=67 мм.
i – количество проходов i=1 тогда
=0692 мин – суммарное время операции.
Подрезка торцов и снятие фасок .
Формирование канавок
Основное время операции
Фрезерно-центровальная
Фрезерование торцов в размер l=588 мм и сверление центровых отверстий 4.
Станок фрезерно-центровальный МР73-М
Режущий инструмент: сверло центровочное 4 Фреза торцевая с пластинами Т5К10 160 z=10.
где Сv=332; q=02; y=04; u=02; p=0; m=02 – коэффициент и показатели степени характеризующие условия резания;
T – стойкость фрезы Т=180 мин;
Kmv – коэффициент зависящий от обработки материала Kmv =078
Kпv – коэффициент зависящий от состояния поверхности заготовки для поковки штампованной Kпv =08
Kuv – коэффициент зависящий от материала режущего инструмента для Т5К10 Кuv=065
Частоту вращения шпинделя фрезы определим по формуле:
Принимаем nст=125 мин-1.
Определим расчетное значение минутной подачи: Sмин=Sz*z*nст=013*10*125=1625 мммин.
Определим действительное значение подачи на зуб фрезы:
Определим величину окружной силы:
Pz=98·Cp·tx·Sz gy·Bпр·z·KpDфq·ncтw
гдеCp=825; y=075; n=11; q=13; w=02 – коэффициент и показатели степени характеризующие условия резания;
Kp – поправочный коэффициент на силу резания Kp=078
Pz=98·825·310·013075·10011·10·07816013·12502=11233 Н
Nэф=Nст·=7·075=525 кВт.
Т.к. мощность необходимая для резания меньше эффективной мощности станка (115 кВт 525 кВт) то резание с принятыми режимами возможно.
где Lр.х – длина рабочего хода режущего инструмента
l – длина перемещения фрезы l=106 мм.
=096 мин – фрезерование торцов с двух сторон
Сверление центровочными сверлами с двух сторон. Сверло центровочное ВЧ Р6М5.
Глубина t=Dсв2=42=2 мм.
Подача на оборот S=0125 ммоб.
где Сv=70; q=04; y=07; m=02 – коэффициент и показатели степени характеризующие условия резания;
T – стойкость фрезы Т=25 мин;
Kпv – коэффициент зависящий от состояния поверхности заготовки для поковки штампованной Kпv =03
Kuv – коэффициент зависящий от материала режущего инструмента для Т5К10 Кuv=10
Принимаем nст=950 мин-1.
Определим крутящий момент при сверлении:
гдеCМ=00345; y=08; n=11; q=20; – коэффициент и показатели степени характеризующие условия резания;
M=98·00345·42·012508·078=08 Нм
Т.к. мощность необходимая для резания меньше эффективной мощности станка (008 кВт 525 кВт) то резание с принятыми режимами возможно.
Основное время на фрезерную операцию равно:
l – длина перемещения l=94 мм.
Суммарное время обработки на фрезерно-центровальном станке определяется суммой: Т0+Т0Σ=096+006=102 мин
Станок – горизонтально расточной модель TPX6111B2
Резец расточной 16х16 Т5К10 φ=45º;
Резец расточной 16х16 Т5К10 φ=60º;
Резец расточной канавочный 16х16 Т5К10;
Сверло 50 (кольцевое) Т5К10.
tсв=Dсв2=502=25 мм – предварительное сверление отверстия под расточку. S=016 ммоб V=40 мммин – принимаем по нормативу.
Принимаем nст=200 мин-1.
Основное время сверлильную операцию равно:
l – длина перемещения l=40 мм.
Растачивание отверстий 62Н7 на l=40 мм. S0=01 ммоб t=15 мм – глубина резания.
где Сv=420; y=02; m=02 – коэффициент и показатели степени характеризующие условия резания;
Принимаем nст=700 мин-1.
гдеCp=700; y=075; n=-015 – коэффициент и показатели степени характеризующие условия резания;
Kφ – коэффициент зависящий от заточки режущего инструмента Kφ=10;
Kr – коэффициент зависящий о радиуса скругления режущей кромки Kr=10. Тогда:
Pz=10·700·1510·01075·1363-015·119=4556 Н
Т.к. мощность необходимая для резания меньше эффективной мощности станка (101 кВт 85 кВт) то резание с принятыми режимами возможно.
lд – длина обрабатываемого участка lд=40 мм.
i – количество проходов i=3 тогда
=195 мин – суммарное время операции.
Растачивание канавки в=19 мм до 65Н12
t=25 мм – глубина канавок. S0=007 ммоб V=196 мммин – скорость резания.
Тогда частота вращения шпинделя:
Принимаем nст=90 мин-1.
Основное время операции [8 9 11].
2.10 Техническое нормирование операций
Под техническим нормированием понимают установление норм времени на выполнения отдельной работы.
Для среднесерийного производства штучно – калькуляционное время (Тшт.к) определяется как:
Тшт.к=Т0+Тв+Тобсл+Тот+Тп.зn=(Т0+Тв)·(1+x100)+Тп.зn
гдеТ0 – основное время мин;
Тв – вспомогательное время мин;
Тобсл – время на обслуживание мин;
n – число деталей в партии шт.
Основное и вспомогательное время составляют Топ – оперативное время.
Токарно-винторезная операция с ЧПУ.
tус=22 мин (установка в трёх-кулачковом самоцентрирующем патроне с поджатием центром задней бабки с учётом переустановки);
tпер=15 мин (время связанное с переходом);
tизм1=3·07=21 мин (контроль диаметральных размеров универсальным штангенциркулем по 2 раза каждый диаметр);
tизм2=2·08=16 мин (контроль линейных размеров штангенциркулем по 2 раза каждый размер);
tизм3=06 мин (контроль фасок шаблонами и шероховатости профилометром);
Тв=95 мин – суммарное вспомогательное время.
Тшт.к=(Т0+Тв)·(1+x100)+Тп.зn=(153+95)·(1+10100)+203=188019 мин – штучно-калькуляционное время для токарно-винторезной операции с ЧПУ.
Горизонтально-расточная операция
tус=5 мин (транспортировка установка в центрах и поводковом патроне с закреплением и выверкой);
tпер=09 мин (время связанное с переходом);
tизм1=12 мин (контроль размерной точности параметров зубчатого венца);
tизм2=09 мин (контроль качества поверхностей);
Тв=87 мин – суммарное вспомогательное время.
Тшт.к=(Т0+Тв)·(1+x100)+Тп.зn=(51+87)·(1+10100)+253=235124 мин – штучно-калькуляционное время для расточной операции.
tус=2 мин (транспортировка установка в центрах и поводковом патроне с закреплением и выверкой);
tпер=1 мин (время связанное с переходом);
tизм1=2 мин (контроль размерной точности параметров зубчатого венца);
Тв=5 мин – суммарное вспомогательное время.
Тшт.к=(Т0+Тв)·(1+x100)+Тп.зn=(12+5)·(1+10100)+163=11912 мин – штучно-калькуляционное время для расточной операции.
Коэффициенты ужесточения операций:
Куж=Тшт.к.прТшт.к.баз
гдеТшт.к.прТшт.к.баз – проектное и базовое штучно-калькуляционное время операции.
Куж1==063; Куж2==080; Куж3==060.
Средний коэффициент ужесточения норм времени Куж.ср=077. Штучно-калькуляционное время на обработку представлено в виде таблицы 10.
Таблица 10 – Штучно-калькуляционное время обработки детали шток
Радиально сверлильная
Горизонтально-расточ.
Таким образом за счёт совершенствования технологий изготовления детали шток была достигнута экономия штучно-калькуляционного времени в 90 мин на единицу времени что составляет 22%.
2.11 Разработка технологических карт наладок на технологические операции
Разработка РТК на технологические операции (токарную с ЧПУ) выполнялась в CAD системе Компас V12 фирмы АСКОН. Они представлены на листе А1 ДР.000.000.003
2.12 Технико-экономическое обоснование проектного варианта технологического процесса
Технологическая себестоимость операции:
См=Сз+Со+Сосн+Сзд+Спр
где Сз – затрата рабочих;
Со Сосн – затраты на эксплуатацию оборудования приходящихся на изделие при выполнении данной работы;
Сзд – затраты на содержание производственного здания;
Спр – прочие цеховые расходы.
Заработная плата рабочих
С=Сз.ч.с*Кв*Кд.з.*Кн*t*B
где Сз.ч.с – средняя часовая заработная плата рабочих;
Кв – коэффициент перевыполнения норм Кв=12;
Кд.з. – коэффициент учитывающий дополнительную зарплату Кд.з.=108;
t – норма времени на операцию;
B – количество рабочих занятых на данной операции.
Затраты на эксплуатацию оборудования
где Са – затраты на амортизацию оборудования приходящие на данную операцию;
Сэ – затраты на электроэнергию.
Затраты на амортизацию оборудования
где К0 – балансовая стоимость оборудования;
О – количество оборудования занятого при выполнении данной операции;
Мо – коэффициент занятости технологического оборудования;
а – норма амортизационных отчислений;
Nг – годовая программа выпуска
Балансовая стоимость оборудования
где Ц – оптовая цена оборудования;
т – коэффициент транспортно-заготовительных расходов т=005;
с – коэффициент затрат на строительство в том числе и на фундамент для оборудование с=006 008;
м – коэффициент затрат на монтаж и освоение м=01 015.
Коэффициент занятости технологического оборудования данной операции для выполнения заданной годовой программы выпуска изделий в серийном производстве определяется по формуле:
где Fд – действительный годовой фонд времени.
Годовое количество запускаемых в производство заготовок:
где Кф – коэффициент брака Кбр=104.
Затраты на электроэнергию:
Сэ=[Ny*Kx*(tшт- tмаш)+ Ny*KN* tмаш]*Кед*Vэ
где Кед – стоимость единицы режущего инструмента;
Затраты на содержание помещений. Эти затраты охватывают амортизацию помещений ремонт отопление освещение и уборку в расчете на площадь которая занята рабочим местом при выполнении операции.
Расчет затрат ведется по формуле:
где Sо – площадь помещения необходимая для выполнения данной операции;
Сзд.г – годовые расходы на содержание помещения.
Площадь необходимая для выполнения данной операции:
где Sед – площадь занимаемая отдельной единицей оборудования;
Kf – коэффициент добавочной площади
Расчет прочих цеховых расходов.
К ним относятся расходы которые не могут быть рассчитаны прямыми методами а именно: заработная плата НТР счетно-конторского персонала и др.
Прочие цеховые расходы определяются по формуле:
где Кп.ч – коэффициент учитывающий прочие цеховые расходы Кп.ч=15.
Расчет снижение трудоемкости и роста производительности.
Процент снижения трудоемкости и роста производительности. Процент снижения трудоемкости:
Б=( tшт1- tшт2 tшт1)*100
Рост производительности труда:
Расчет показателей приведен в таблице 11.
Таблица 11 – Технико-экономическое обоснование выбора операций
Часовая тарифная ставка
Коэффициент перевыполнения норм
Коэффициент учитывающий дополнительную заработную плату
Коэффициент учитывающий отчисления в соцстрах
Итого заработная плата рабочих
Действительный годовой фонд времени
Коэффициент занятости оборудования
Балансовая стоимость
Норма амортизационных отчислений
Мощность оборудования
Коэффициент учитывающий холостую работу привода
Коэффициент одновременной работы двигателей
Тариф на электроэнергию
Коэффициент учитывающий отношение всей мощности
Затраты на электроэнергию
Затраты на амортизацию
Эксплуатационные затраты по оборудованию
Стоимость единицы оснастки
Норма амортизационных отчислений на оснастку
Продолжение таблицы 11 – Технико-экономическое обоснование выбора операций
Стоимость инструмента
Количество переточек
Стоимость одной переточки
Затраты на инструмент
Затраты на содержание помещения на кв.м
Затраты на прочие цеховые расходы
Итого технологическая себестоимость операции
Процент снижения трудоемкости
Рост производительности труда
Срок окупаемости вложений
В разделе выполнен анализ служебного назначения и конструкции деталей-представителей анализ деталей на технологичность выполнение анализ базовых технологических процессов рассчитан коэффициент закрепления операции и определен тип производства рассчитанные припуски режимы резания и нормы времени на операции механической обработки разработаны новые технологические процессы механической обработки детали: «Шток».
КОНСТРУКТОРСКО-ТЕХНОЛОГИЧЕСКАЯ ЧАСТЬ
Разработка технологического оснащения для обработки деталей – представителей гидроцилиндра.
1 Разработка схемы базирования детали.
Разрабатывается приспособление для горизонтально-расточного станка на котором производится обработка отверстий в головке штока 62Н7 и сопутствующих поверхностей.
В условиях мелкосерийного производства имеет смысл применять механизированное с удобным расположением установочных и силовых элементов. Реализация приспособление в деле должно обеспечить автоматическое получение обрабатываемых размеров (станок настроенный на размер).
Д – базовая поверхность
Точки 1–4 – двойная направляющая база
Точки 5 – опорная база
Рисунок 5 – Схема базирования детали
Погрешность базирования L=0 (совмещается установочная и измерительная база – точка 5).
Погрешность базирования
Где α=120° - угол призмы;
Д2 – допуск на базовую шейку 50f9 (=0062 мм).
Погрешность положения оси отверстия 62Н7 по вертикали:
Так как (0005 мм0062 мм) то выбранная реализация базирования допустима.
Погрешность закрепления при действии механизированного прихвата сверху на деталь устанавливаемую обработанной поверхностью в призмы
Среднестатистическая величина погрешности приспособления для чистовой обработки
Анализируя значения можно сделать вывод о достаточно низкой погрешности. Это дает возможность при обработке получить требуемую точность обработки.
2 Силовой расчет приспособления
Максимальное усилие наблюдается при обработке растачиванием на черновых проходах.
При этом при V=80 ммин; S0=05 ммоб; t=40мм Pz=2150Н (Pх=1720Н Pу=1290Н).
На основе схемы действия сил требуется определить усилие закрепления Q.
где Q1 – усилие закрепления;
f1 – коэффициент трения;
Рисунок 6 – Схема действия сил
Суммарная сила закрепления с учетом коэффициента запаса Кзап=30
Где Kn=K0·K1·K2·K3·K4·K5=15·1·16·1·1·12=30
3 Выбор привода и определение основных характеристик
Так как QΣ>10000 Н то целесообразно применить гидропривод учитывая так же то что горизонтально – расточной станок имеет собственную гидросистему от которой будет осуществляться запитка гидросистемы приспособления.
Принимаем гидропривод двустороннего действия. Усилие на штоке расчетное из зависимостей на рисунке.
Рисунок 7 – Схема механизма закрепления
Рабочий ход при подаче масла в штоковую полость. При этом
Усилие на штоке согласно схемы:
где 105 – коэффициент учитывающий потери на трение.
Принимаем Dст=50мм dст=25 мм.
Так как Wф>W то усилие закрепления обеспечивается.
Усилие закрепления по факту:
4. Точностной расчет приспособления
Допустимая погрешность приспособления:
к=06 (соотв. 7-му квалитету);
=0015 мм – погрешность базирования;
з=0020 мм – погрешность закрепления.
Условие выполняется.
5 Прочностной расчет приспособления
Наиболее слабым элементом приспособления является соединение М167H7g стыкующее поршень привода и ось прихвата.
Рисунок 8 – Схема элементов приспособления
Резьбовая поверхность должна выдерживать осевое усилие Wф. Таким образом на прочность рассчитывается минимальный диаметр резьбы dmin.
Условие обеспечения прочности:
где – допустимое напряжение МПа; =.
dmin – минимальный диаметр резьбы.
– условие обеспечено
6 Техническое описание приспособления
Разработанное приспособление предназначено для установки и закрепления деталей типа вал или стержень на горизонтально-расточном станке. Рекомендуется для эксплуатации в условиях мелкосерийного и серийного производства.
Представляет собой компоновку элементов обеспечивающих базирование и закрепление деталей. На плите 10 крепятся по т – образным пазам с центрированием по шпонкам корпуса 5 7 с призмами 4 6 (α=120º) на призмы осуществляется установка детали. Осевое перемещение детали ограничивает упор уголок 9 перемещение которого регулируется болтами в т-образных пазах. Также при помощи болтов к плите 10 крепится гидроцилиндр 1 шток которого посредством оси 11 связан с прихватом 2. Наличие радиального паза в оси и винта входящего направляющей частью в этот паз обеспечивает одновременный поворот оси и прихвата на 90º в процессе их поднятия и опускания. Данная схема носит название бойонетной.
Схема закрепления детали такова. Первоначально прихват находится в крайнем верхнем положении (благодаря действию гидравлики подача масла в поршневую полость) и он повернут на 90º от его положения при закрепленной детали [59-61].
Деталь устанавливается в призмы по упору в штоковую полость подается масло заставляющее перемещаться поршень вниз; при этом ось поворачивается на 90º закрепляется деталь с разворотом прихвата 90º. Производится обработка. По окончании обработки давление масла (его подача) прекращаются масло подается в поршневую полость заставляя ось с прихватом двигаться вверх с поворотом на 90º. Доступ к обрабатываемой детали обеспечен. производится снятие детали. Чертеж приспособления на листе ДП 000.000.05 СБ.
7 Разработка контрольного приспособления
Для контроля радиального и торцевого биения шеек и ступеней детали проектируется индикаторное переналаживаемое приспособление обеспечивающее минимальное время контроля детали надежную установку и достаточную точность.
Наиболее грубая величина – 005 мм. При цене деления индикатора 001 мм требуемая величина измерения контролируется.
Проектируемое приспособление относится к индикаторным контрольным приспособлениям рычажного типа.
Рисунок 9 – Схема контроля биений
Разработанное приспособление состоит из призмы 2 α=90º на которой при помощи направляющей расположен корпус 3 с индикатором часового типа 1. Наконечник индикатора контактирует с рычагом 6 который касается измерительной поверхности детали при помощи упругих пластин 4. Индикатор располагается во втулке 5. Обеспечив контакт подпружиненного рычага 6 с контактирующей поверхностно закрепив на базовой шейке совершается полный оборот детали. При этом замечаются отклонения по шкалам прибора. Разница является биением.
Погрешность приспособления:
гдеt=0005 мм – погрешность изменения температуры;
n=0005 мм – погрешность индикатора;
уn=0005 мм – погрешность поверхности
Схема контроля типична процесс измерения занимает короткий промежуток времени. Чертеж приспособления приведен на листе ДП 000.000.06 СБ
1 Эффективность применения инструмента со сменными пластинами (СМП)
В настоящее время наблюдается стремительное развитие технологии машиностроительного производства.
Отличительной особенностью современного машиностроения является ужесточение требований к качеству выпускаемых машин и их себестоимости. В условия рыночных отношений необходимо быстро реагировать на требования потребителя. Побеждает в конкурентной борьбе тот кто способен быстрее реализовывать принятые конструктивные и технологические решения.
Реализовать такие решения возможно применив комплексную автоматизацию производства.
Режущий инструмент является составной частью комплексной автоматизированной системы станка с ЧПУ. Тщательному выбору и подготовке инструмента для станков с ЧПУ должно уделяться особое внимание. Это связано с высокой стоимостью этого оборудования и необходимостью достижения максимальной производительности и более высокой точности обработки. Для обеспечения автоматического цикла работы этих станков требуется более высокая степень надежности работы инструмента.
Режущий инструмент для станков с ЧПУ должен удовлетворять следующим требованиям: обеспечению высоких и стабильных режущих характеристик; удовлетворительному формированию и отводу стружки; обеспечению заданных условий по точности обработки; универсальности применения для типовых обрабатываемых поверхностей различных деталей на разных моделях станков; быстро сменности при переналадке на другую обрабатываемую деталь или замене затупившегося инструмента.
Применение сборного инструмента со сменными многогранными пластинами (СМП) позволяет повысить эксплуатационные качества инструмента обеспечивает значительную экономию дефицитных режущих материалов. Вместе с тем создаются благоприятные условия для широкого применения более износо- и теплостойких режущих материалов.
Сборный инструмент с СМП нашел широкое применение выпуск его постоянно увеличивается как по объему так по номенклатуре. Удельный вес такого инструмента сегодня составляет 35-40 % общего объема выпуска режущего инструмента.
Поиск путей снижения себестоимости изготовления инструмента и повышения гибкости инструментального производства привел к унификации конструкции за счет широкого применения резцовых вставок кассет и головок в которых устанавливаются СМП. Взаимозаменяемость вставок кассет и головок для различных типов режущих инструментов позволяет создавать их гаммы по видам и размерам и объединять большие группы инструмента в так называемые системы. В совокупности с набором удлинителей стандартных стандартных и специальных хвостовиков такие системы являются удобным средством удовлетворения потребностей в специализированном инструменте и сведения до минимума доли индивидуальных заказов.
Задача обеспечения надежности режущих инструментов решается созданием новых инструментальных материалов с повышенным износо- и теплостойкостью прочностью и твердостью.
В качестве материалов для изготовления лезвийного инструмента для станков с ЧПУ используют: твердые сплавы керамику сверхтвердые синтетические материалы и быстрорежущие стали. [22-29]
Производством инструмента с СМП занимаются фирмы как отечественные так и зарубежные: Победит Росмарк Элемаш Widia Hertel SandvikKORLOYISCAR и др.
Рисунок 10 – Резцы со сменными пластинами.
Твердые сплавы подразделяются на четыре группы: вольфрамовые титано-вольфрамовые титанотанталовольфрамовые и без вольфрамовые. Они различаются по химическому составу физико-механическим и эксплуатационным свойствам.
Крепление СМП должно обеспечивать: надежность (не допускать микро смещений пластины в процессе резания); плотный контакт опорной поверхности пластины с опорной поверхностью паза в державочной части; точность позиционирования и взаимозаменяемость режущих кромок при повороте и смене пластин; стабильность геометрии дробление завивание и надежный отвод стружки; минимальное время для смены лезвий и кроме того оно должно быть компактным и технологичным.
Наибольшее распространение в последнее время получают СМП с центральным отверстием и способы их крепления на резцах и фрезах с использованием этого центрального отверстия. СМП без отверстия с плоскими опорной и передней поверхностями в основном используются лишь для резцов с положительными передними углами.
Рисунок 11 – Типы крепления пластин.
В семействе СМП с центральным отверстием широко применяют пластины с тороидальной формой отверстия. Такие пластины имеют задний угол 7° устанавливаются на корпусах резцов с нулевым углом врезки обеспечивая тем самым главный и вспомогательный задние углы 7° и угол наклона режущей кромки равный нулю. Коническое отверстие в пластине позволяет применить наиболее простой способ крепления СМП на резце - с помощью винта имеющего коническую головку. Такой винт подтягивает СМП к базовым сторонам гнезда в корпусе и ко дну этого гнезда. Крепление отличается не только простотой но и
компактностью что позволяет создавать резцы с сечениями державок 10Ч10 мм.
Совершенствование методов точного прессования дает возможность изготовлять пластины с большими положительными передними углами (одно- и двухсторонними) с установкой в державках предназначенных для негативных пластин. При этом сохраняется положительный передний угол благодаря чему снижаются (до 30 %) силы резания затрачиваемая мощность станка нагрузка на пластину и обрабатываемую деталь уменьшается опасность появления вибраций. [30-39]
Пластины такого типа называют негативно-позитивными имея в виду то что они устанавливаются в державке подобно негативным пластинам но сохраняют при этом положительный передний угол в процессе резания.
Стандартами ISO предусмотрено четыре типа механического крепления перечисленных СМП (Рисунок 12).
Для улучшения эксплуатационных характеристик используют нанопокрытия. Анализируя существующие нанопокрытия можно выделить три основные группы:
- Нано структурные покрытия в отличие от традиционных совмещают в себе повышенную микро твердость и достаточную пластичность. Поведение нано кристаллических материалов с размерами зерен 10 нм и менее определяется главным образом процессами в пограничных областях поскольку количество атомов в зернах сравнимо или меньше чем в их границах. Это обстоятельство существенно изменяет характер взаимодействия между соседними зернами например тормозит генерацию дислокаций препятствует распространению трещин из-за упрочнения границ зерен. При этих условиях дислокации в нанозернах отсутствуют (рис. 12 а).
Рисунок 12 – Типы нано покрытий
Нано композитные покрытия состоят из основной нано кристаллической твердой фазы на границах зёрен которой располагается тонкий слой второй нано кристаллической или нано аморфной фазы. Таким образом твёрдые зёрна упрочняющей фазы разделены между собой тонкими прослойками атомов другой фазы. Такие покрытия обладают сверхвысокой твёрдостью большими коэффициентами упругого возврата высокой термостойкостью (рис. 12 б).
Ультрадисперсные материалы с увеличенной площадью межзеренных границ имеют более сбалансированное соотношение между твердостью оказывающей определяющее положительное влияние на износостойкость и прочностными характеристиками материала в том числе и в условиях действия циклических термомеханических напряжений.
- Нанослойные покрытия обладают повышенной трещиностойкостью. Предпосылки для их получения возникли еще 20 лет назад при разработке многослойных покрытий на основе TiNNbN TiNVN (TiAl)NCrN и др. с чередующимися слоями металлов или соединений. Нанослойные покрытия обладают различными внутренними напряжениями (модулями упругости) и близкими по величине коэффициентами термического расширения. Толщина отдельных слоёв должна быть настолько мала чтобы внутри них не появлялся источник дислокаций а дислокации которые под действием напряжений двигались бы к границе раздела из более мягкого слоя отталкивались бы силами создающимися упругими напряжениями в более твёрдом слое. Общее количество слоев покрытия выбирается в зависимости от решаемых технологических задач и в ряде случаев может достигать двухсот (рис. 12 в).
Таким образом создание покрытий для режущего инструмента нового поколения наиболее эффективно осуществлять при использовании инновационной концепции многослойно-композиционных архитектуры с нанометрической структурой и чередующимися слоями наноразмерной толщины различного композиционного состава и функционального назначения.
Покрытия CVD (Сhemical Vapor Deposition)
Первые износостойкие покрытия были получены путем химического процесса осаждения при высоких температурах 950–1050 °C из парогазовой среды. Данный процесс принято сокращенно называть CVD (Сhemical Vapor Deposition). Следует отметить что данная технология широко применяется не только для нанесения износостойких покрытий на режущем инструменте но и в других областях техники где требуется получение слоев покрытия и пленок из кристаллических материалов с высокой чистотой и заданной структурой. Первые износостойкие CVD покрытия были однослойными с толщиной порядка 4–7 мкм.
Наибольшие проблемы вызваны недостаточной адгезией СVD покрытий а также и негативным влиянием на механические свойства основы. Уровень этого влияния можно пояснить на простом примере. То есть простейшие СVD смещают область применения твердых сплавов в сторону высоких скоростей резания ухудшая их прочностные характеристики. Учитывая это можно было бы сделать вывод что такие сплавы наилучшим образом будут подходить для чистовой обработки но тут вступает в силу другое ограничение [40-45].
Эволюция CVD покрытий шла в трех направлениях. Первое – это снижение негативного влияния покрытия на прочность твердосплавной основы. Второе – улучшение адгезии. Третье – возможность наращивания толщины слоев покрытия для усиления защитных свойств желательно не в ущерб двум первым задачам.
Первые попытки поднять защитные свойства покрытий за счет наращивания толщины слоя TiC не дали большого эффекта. Больший эффект был достигнут от внедрения многослойных покрытий СVD где поверх слоя карбида титана TiC наносились слои оксида алюминия Al2O3 и нитрида титана TiN (рис. 13).
Рисунок 13 – Многослойное покрытие CVD
При этом первый слой покрытий служил основой для создания хорошей адгезии а последующие слои усиливали защитные функции от различных факторов износа. Оксид алюминия как очень простое химическое соединение с высокой химической инертностью и температурной стабильностью является идеальным компонентом покрытия для защиты твердого сплава от воздействия высокой температуры и химических видов износа [46-50].
Для первых покрытий СVD была характерна диффузия из компонентов основы в покрытие в процессе нанесения. В результате на границе твердого сплава и покрытия образовывался аморфный слой богатый свободным углеродом так называемая Эта-фаза снижающая адгезию и повышающая хрупкость основы. Увеличенное округление режущей кромки несколько снижало негативный эффект но не решало проблему. Практически полностью исключить образование Эта–фазы удалось только с внедрением модифицированного процесса СVD когда нанесение первого слоя покрытия начинается при пониженных до 700 °С температурах. При таких температурах не возникает условий для диффузии компонентов основы и покрытия а вырастающий слой карбида титана TiC получает структуру в виде узких вертикальных кристаллов хорошо сопротивляющихся сдвигу. Данный процесс получил название MT-CVD. Адгезия MT-CVD покрытий значительно выше. Для них не характерен такой вид износа как отслоение покрытия.
Покрытия PVD (Physical Vapor Deposition) или КИБ (конденсация с ионной бомбардировкой)
Тем не менее во всем мире признается первенство советских а впоследствии российских разработок в создании второго по объему рынка технологии нанесения покрытий на режущий инструмент а именно PVD (Phisical Vapor Deposition) или MEVVA (Metal Vapor Vacuum Arc) илиКИБ (конденсация с ионной бомбардировкой – термин применяющийся в русскоязычной литературе). Инструменты с покрытием PVD появились в начале 80-х годов прошлого столетия.
Популярность нового метода нанесения покрытий определилась в первую очередь тем фактом что PVD наиболее успешно улучшает свойства тех режущих инструментов где технология CVD неэффективна или бесполезна. Во-первых PVD реализуется при принципиально более низких температурах не превышающих 500 °С что позволяет покрывать как твердосплавные пластины так и инструменты из быстрорежущих сталей и даже просто детали машин работающие в условиях интенсивного трения. Во–вторых покрытие PVD может быть нанесено на острую кромку и вследствие равномерного характера осаждения не вызывает ее притупления. Таким образом данный тип покрытий может с успехом использоваться для мелкоразмерных концевых инструментов. В то же время тонкий слой покрытия PVD не может соперничать с более мощными покрытиями СVD суммарная толщина слоев которых может достигать 22–25 мкм поэтому по сей день уступает им долю рынка сменных неперетачиваемых пластин.
Они обладают хорошей адгезией не влияют на прочность основного инструментального материала и даже создают благоприятные сжимающие напряжения в поверхностном слое.
Простейшие однослойные PVD покрытия TiN сейчас применяются для метчиков и быстрорежущих фрез средней производительности используемых для обработки простых материалов на низких скоростях. Эти же покрытия можно увидеть на сверлах из быстро реза предлагаемых для домашнего использования.
В серьезных индустриальных применениях требуются более теплостойкие покрытия. Однослойное покрытие ТiCN продолжает использоваться для быстрорежущих и твердосплавных фрез общего назначения. Оно обладает высокой абразивной износостойкостью. Однако оно повсеместно вытесняется еще более производительным покрытием со структурой титан-алюминий нитрид TiNAl.
Рисунок 14 – Покрытия DLC (Diamond Like Coatings)
Принципиально отличными от вышеописанных но также относящихся к классу PVD являются покрытия DLC (Diamond Like Coatings). Получаемые при этом углеродные нанопленки близки по свойствам к алмазу. Такие покрытия обладают очень высокой превосходящей до 50 раз другие типы покрытий абразивной износостойкостью. К сожалению их температурная стабильность и стойкость к окислению ограничены величиной 300 °С что недостаточно для большинства случаев металлообработки за исключением резания алюминия и силумина. Но благодаря своей абразивной стойкости покрытия DLC показывают хорошие результаты при обработке резанием различных композиционных материалов на основе стекло- и угле- наполненных пластиков находящих все более широкое применение в технике [51-55]
В таблице 12 представлен технико-экономический эффект применения СМП.
Tенденции развития современного металлорежущего производства сопровождаются неуклонным ростом объема применения современного оборудования и инструментов. Желание потребителя минимизировать затраты при совершенствовании технологического процесса делает актуальным наличие механизма оценки эффективности производимых или планируемых затрат.
Для оценки экономической эффективности внедрения современных металлорежущих инструментов можно использовать методику разработанную компанией “Искар СНГ” которая успешно применяется в настоящее время на ряде промышленных предприятий.
Таблица 12 – Преимущества использования сменных многогранных пластин.
Особенности использования сменных многогранных пластин
Технико-экономический эффект
Многократное использование державки
Уменьшение стоимости инструмента. Повышение качества и надежности инструмента
Устранение переточек
Повышение качества пластин. Сокращение заточного оборудования площадей числа рабочих-заточников. Сокращение стоимости эксплуатации инструмента. Уменьшение расхода абразивных материалов
Повышение качества пластин. Уменьшение стоимости и трудоемкости изготовления инструмента. Сокращение расхода припоя
Сокращение времени смены инструмента
Снижение периода экономической стойкости. Интенсификация режимов резания и повышение производительности труда
Формирование передней грани на стадии изготовления пластины
Обеспечение устойчивого дробления стружки. Повышение качества инструмента. Сокращение стоимости эксплуатации
Возможность упрочнения пластин
Повышение качества пластин. Интенсификация режимов резания и повышение производительности труда
Программа расчета выполнена в Excel. Она позволяет оперативно вводить и изменять исходные данные получая на выходе количественную оценку реальных затрат на обработку.
Таблица 13. – Сравнение показателей при увеличении производительности
Сравниваемые показатели
При напайном инструменте
режимов инструментом
Производительность мммин.
Расходы на инструмент на 1 переход руб.
Общие затраты на 1 переход руб.
Экономия затрат на 1 переход руб.
Аргументированный вывод о целесообразности применения или отказе от применения предлагаемого инструмента взамен применяемого или другого сравниваемого инструмента можно сделать лишь на основании сравнительного экономического расчёта что и позволяет сделать предлагаемая методика.
Подводя итог вышеизложенного считаем что эффективность механической обработки определяется соотношением между расходами и доходами.
Расходы при металлообработке складывается из-за затрат связанных зарплатой оператора стоимостью оборудования оснастки заготовок инструментальный кладовой складируемого инструмента накладными расходами (рисунок 15).
Рисунок 15 – Расходы при металлообработке
Под производительностью металлообработки мы понимаем соотношение между выходом и готовой продукции и входными затратами производства.
На входе процесса затрачиваются определенные ресурсы необходимые для организации производства такие как: рабочая сила оборудование оснастка сырье инструментальные запасы административные расходы.
Выход – это продукция которую удается произвести в рамка имеющегося фонда рабочего времени.
Правильный выбор и применение современных металлорежущих инструментов на повышенных режимах резания является решающим фактором снижения затрат. [56]
По нашему мнению применение инструмента с СМП является наиболее эффективным при производстве деталей машин.
2 Дорогой инструмент — целесообразно ли это?
На сегодняшний день многие отечественные машиностроители столкнулись с негативным влиянием мирового финансового кризиса. В этих обстоятельствах каждый вынужден искать пути экономии и снижения себестоимости производимой продукции. Но следует при этом учитывать что не всегда сокращением затрат на современный высокотехнологичный инструмент можно добиться желаемого результата. Но тем не менее экономии на инструменте существует реальная альтернатива
Каким же образом у нас подходят к этому вопросу? Путем снижения всех затрат. И в первую очередь под «оптимизацию» попадают расходы на режущий инструмент. На примере одного из немецких автопроизводителей — фирмы Daimler AG — рассмотрим структуру себестоимости изделия.
Рисунок 16 – Структура себестоимости готовой детали
Как видно из приведенной выше диаграммы основную часть затрат (72%) составляют расходы на электроэнергию оплату труда оператора амортизацию станка и т.д. В то время как расходы на металлорежущий инструмент в себестоимости составляют 4%!
Вторым вариантом является увеличение стойкости режущей кромки инструмента. Но и в таком случае даже при увеличении стойкости инструмента вдвое (что само по себе является нетривиальной задачей) вы сможете сэкономить половину своих расходов на инструмент или же всего 2% от себестоимости обработки детали!
Повышение производительности
Так как же экономить? Несомненно наиболее экономичным вариантом будет технология с максимальной производительностью. Это позволит снизить затраты на электроэнергию оборудование и персонал. То есть экономить можно (и нужно) не только путем снижения затрат но путем повышения выхода готовых изделий в единицу времени.
Повышение производительности на современном оборудовании возможно лишь за счет использования современных высокопроизводительных металлорежущих инструментов которые позволяют работать с повышенными скоростями и подачами и могут «выжать максимум» из вашего оборудования.
Режимы резания: увеличение скорости резания на 22% Исходное время обработки - 100% Уменьшенное время обработки - 78%
Режимы резания: увеличение подачи на 40% Исходное время обработки - 100% Уменьшенное время обработки - 60%
Рисунок 17 – Влияние повышения производительности на себестоимость детали
Как мы видим из приведенных выше диаграмм сокращение времени обработки наиболее существенно влияет на основную часть расходов — на станочные расходы. При повышении скорости резания на 22% (Рис. 17 а) мы получаем сокращение расходов на 1672%. Аналогичное влияние оказывает и величина подачи (Рис. 17 б). При увеличении подачи на 40% экономия составляет до 30%! Кроме того сэкономленное станочное время позволяет существенно увеличить выпуск готовых деталей или высвободить оборудование для производства другой продукции. Рассмотрим примеры такой экономии у одного из заказчиков. Исходные данные — обработка тормозного диска из серого чугуна на токарном станке. Величина шероховатости ограничивает максимальную подачу при обработке.
Таблица 14 – Исходные данные
Вертикальный токарный станок
Шероховатость поверхности*
Объем выпуска шт.год
На первом этапе была произведена замена использованной пластины на пластину из нового сплава марки WAK10 предназначенного для обработки чугуна. Без изменения режимов резания стойкость новой пластины была на 50% выше по сравнению со старой. За счет этого была достигнута экономия в размере 11200 Евро на годовую программу.
На следующем этапе была повышена скорость резания с 400 до 450 ммин при этом стойкость пластины была все равно выше первоначальной технологии. Годовая экономия инструмента — порядка 6000 Евро но за счет сокращения времени обработки удалось добиться снижения общих расходов более чем на 110000 Евро!
Таким образом с помощью повышения производительность нам удалось добиться увеличения экономии более чем в 10 раз по сравнению с просто снижением расходов на инструмент.
Но еще более впечатляющей экономии удалось добиться технологам фирмы Walter при внедрении новых канавочных инструментов.
Благодаря использованию новой марки твердого сплава им удалось существенно снизить производственные расходы.
И это экономия всего лишь на оптимизации технологии прорезания одной канавки!
Конечно необходимо отметить что такая экономия возможна при определенных условиях связанных с подготовкой технологов их информированностью о новых инструментах и технологиях.
Надеемся у читателей не осталось сомнений в эффективности применения современного высокопроизводительного инструмента который позволяет существенно снизить производственные расходы.
3 Экономическая эффективность применения высокотехнологичного инструмента.
Очень часто на производствах не имеющих опыта применения современного высокотехнологичного инструмента мы сталкиваемся с желанием увидеть экономический эффект от внедрения подобного инструмента. Это легко реализуемо в условиях крупносерийного производства где имеются большие партии деталей постоянной номенклатуры и известна реальная подробная калькуляция затрат со всеми составляющими себестоимости единицы продукции. В этом случае проводятся сравнительные испытания предлагаемого высокотехнологичного инструмента с составлением соответствующего «Акта сравнительных испытаний». По результатам испытаний производится расчёт экономической эффективности и принимается решение о внедрении.
Показать реальный экономический эффект в сегменте малого и среднего бизнеса при мелкосерийном а тем более - при единичном типе производства очень трудно.
Проблема заключается в отсутствии или неполноте калькуляции затрат т.е. в отсутствии информации о стоимости использованного основного и вспомогательного инструмента фактической трудоёмкости накладных расходов и т.д. в себестоимости изготовленной детали.
Часто даже невозможно найти партию деталей для проведения испытаний на которой можно было бы определить фактическую стойкость режущей грани сменной пластины
Как же в этом случае принимать решение?
Попробуем на простом примере определить целесообразность внедрения современного инструмента.
Стоимость отечественного токарного резца с напайной пластиной из твердого сплава (типа Т5К10 ВК8 Т15К6) в среднем составляет ~20-30 грн.шт.
Такой резец допускает порядка 3 5 переточек напайной режущей пластины.
Стоимость импортной державки токарного резца для наружного точения в среднем составляет ~1000 грн.
Правильно подобранная державка эксплуатируемая надлежащим образом позволит отработать 400-м сменным пластинам.
Сменные пластины нельзя перетачивать но они имеют несколько режущих граней (от 2-х до 12-ти).
Средняя стоимость сменной пластины группы ISO с длиной режущей грани 12 мм составляет 100 грн.
В то же время стойкость современных сменных пластин ведущих мировых производителей превышает стойкость отечественных сплавов надлежащего качества в 5-7 раз в пересчёте на одну режущую грань.
Встречались и запредельные цифры соотношения стойкостей до 30 раз на сложных операциях которые подтверждены Актами испытаний.
Что если предоставить работнику отдела снабжения два счёта в которых будут фигурировать десяток отечественных резцов (в одном счёте) и одна токарная державка + десяток сменных пластин (в другом счёте) то без знания действительной доли затрат на инструмент в единице продукции выбор скорее всего будет сделан в пользу отечественного напайного инструмента.
А теперь давайте немного посчитаем.
Реальную работу совершают сменные пластины (СМП) поэтому переведём стоимость державки в стоимость СМП:
грн. мы добавим к стоимости нашей пластины:
0 + 10 = 110[грншт].
Теперь вычислим стоимость одной режущей грани.
Возьмем для расчёта односторонние пластины с минимальным количеством режущих граней равным двум:
Мы видим что стоимость режущей грани СМП составляет 55 грн.
Продолжим наши расчёты.
Рассмотрим крайний случай такой как черновое точение где используются пластины с минимальным количеством режущих граней.
Так как отечественный резец можно переточить как правило не более трёх раз на подобных операциях то фактическая стоимость 1 режущей грани составит:
Но мы помним что стойкость у высокотехнологичного инструмента в 5-7 раз выше поэтому:
В итоге мы получили близкие результаты несмотря на большую разницу в цене традиционного и высокотехнологичного инструмента.
Но и тут еще не всё посчитано.
Нам так же необходимо учесть стоимости:
времени затрачиваемое высококвалифицированными станочниками на переточку;
времени затрачиваемое на под наладку оборудования («выставление резца и размера») после каждой переточки;
абразивного инструмента используемого для переточки напайных резцов;
эл. энергии затраченной на работу заточного оборудования и его вытяжной вентиляции.
Всё это является частями стоимости «Подготовительно-заключительного времени» вспомогательных материалов и некоторых накладных расходов.
Перевес уже явно на стороне инструмента с СМП.
При этом на общих операциях применяются как правило двухсторонние режущие пластины у которых количество режущих граней в два раза больше при равной стоимости пластин.
В приведенных выше расчётах не упоминалось о существенном повышении таких параметров обработки как «Скорость резания» «Глубина резания» и «Подача на оборот» при заявленной стойкости инструмента. У высокотехнологичного инструмента эти параметры превосходят возможности традиционного инструмента т.е. имеем дело со снижением «Машинного времени».
Снижение долей в сумме: «Машинного» «Подготовительно-заключительного времени» не меняя технологии изготовления продукции и без разработки дополнительных мероприятий ведёт к значительному увеличению производительности труда культуры производства и мотивационной составляющей привлекательности труда станочника – а это уже совсем другие экономические категории и возможности для реальной экономии!
Качество современных отечественных напайных пластин из твёрдого сплава имеет большую разницу [57].
Иллюстративная часть представлена на плакате ДП 000.000.07
ТЕХНОЛОГИЧЕСКОЕ ПРОЕКТИРОВАНИЕ УЧАСТКА
При проектировании механосборочного производства одновременно разрабатывают и решают технологические экономические и организационные задачи тесно связанные между собой.
В общем виде задача проектирования может быть сформулирована в следующем виде: спроектировать цех или участок обеспечивающий выпуск изделий определенной номенклатуры требуемого качества заданную программу выпуска при достижении минимально возможных приведенных затрат на изготовление и с учетом всех требований к охране труда [25].
Для решения технологических задач необходимо: проработать вопросы технологичности изделий спроектировать технологические процессы выявить трудоемкость и станко ёмкость операции установить тираж и количество оборудования состав и количество работающих нормы расхода материалов определить площади и размеры участков и цеха разработать компоновку цеха и планировку оборудования определить задание для строительного сантехнического и энергетического проектирования.
Для решения экономических затрат необходимо: рассчитать себестоимость и рентабельность выпуска изделий определить удельные приведенные затраты размеры основных и оборотных средств составить калькуляции решить вопросы финансирования.
Для решения организационных задач необходимо: выбрать принципы формирования производственных подразделений разработать структуру правления научную организацию труда документооборот организацию служб производства систему контроля над ходом производства.
В дипломном проекте необходимо разработать проект специализированого участка по ремонту гидроцилиндров. Проектируемая производственная единица должна быть предназначена для выпуска гидроцилиндров НК4040 выпускаемых предприятием.
Целью создания участка является создание эффективного экономически
целесообразного производственного участка обеспечивающего изготовление всех деталей узлов комбайна проходческого за исключением нормализованных и стандартных изделий.
Задача разработки решается следующим образом: на основе анализа структуры трудоемкости изготовления гидроцилиндра по базовому варианту определяется перечень оборудования и его часовая загрузка на механообработку детали узла-представителя.
При этом в общем перечне базового списка механообрабатывающего оборудования необходимо иметь те модели станков которые задействованы в проектируемых вариантах обработки деталей представителей.
Сводка нормированного времени обработки по группам станков базового варианта изготовления взята на базовом предприятии. Необходимо выполнить расчет количества станков участка предназначенного для выпуска гидроцилиндров НК4040. При этом предполагается сосредоточить механизмов данной конструкции на локальной производственной территории (участке). После определения станочного состава оборудования его количества общей удельной площади один из участков базового цеха будет освобожден от наличного оборудования а на месте вновь созданных фундаментов будут установлены станки для обработки деталей редуктора конического.
Демонтированное оборудование после его полного и всестороннего контроля и ремонта будет размещено на других участках цеха взамен физически и морально устаревшего.
Расчет количества станков i-го типоразмера:
где: N – годовая приведенная программа выпуска = 221 шт;
Fд – действительный годовой фонд времени работы станка при двухсменной работе;
где Тшт-кб – базовая трудоемкость;
Куж – коэффициент ужесточения норм времени.
Трудоемкость сборки гидроцилиндра НК4040 – 30ч.
Средняя загрузка станков участка – 08.
Потребное количество рабочих мест слесарей-сборщиков при условии стендовой стационарной сборки:
Где - трудоемкость сборки приведенной годовой программы;
=1880ч – номинальный фонд времени работы сборочного стенда с механизированными приспособлениями;
m=2 – количество смен в сутки.
Количество рабочих мест – 6.
Расчет количества рабочих-сборщиков:
где =6 – количество рабочих мест;
= 2040ч. – эффективный годовой фонд рабочего места рабочего-сборщика;
=08 – нормативный коэффициент загрузки рабочего места сборщика;
=1850ч. – эффективный фонд рабочего;
П=2 – плотность работ т.е. число рабочих сборщиков на одном рабочем
Принятое число рабочих сборщиков – 11 чел.
Коэффициент загрузки оборудования:
Степень загруженности станков отдельных типоразмеров характеризуется коэффициентом загрузки оборудования:
а загрузка в целом по участку или цеху – средним коэффициентом загрузки:
где Срі -расчетное количество всех станков;
Спі –принятое количество станков.
Средний коэффициент загрузки равен 077.
Площадь сборочного отделения для сборки букс приводных:
=20м2 – удельная площадь на 1-го рабочего-сборщика.
Расчет склада заготовок участка:
де Ки=05– коэффициент использования площади склада;
Q – черновой вес материала заготовки.
Масса гидроцилиндра –50 кг.
Средний коэффициент использования материала Кв=060.
Таблица 15 – Станочное оборудование участка обработки гидроцилиндров НК4040.
Фрезерно-центровальные
Вертикально-фрезерные
Радиально-сверлильные
Горизонтально- расточные
Черновой вес редуктора:
t=5дн. – количество дней для которых создается нормативный запас заготовок;
Ф=254дн. – количество рабочих дней в году;
q=05тм2 – допустимое нагружение на площадь пола.
Площадь склада деталей:
Выбор подъемно-транспортных средств участка:
Транспортировка деталей и заготовок на участке механической обработки осуществляется:
- цеховым мостовым краном грузоподъёмностью 1т предусмотренным общей компоновкой цеха;
- внутрицеховым рельсовым транспортом (подача заготовок на участок вывоз готовых деталей на сборку).
Вывод: В данной части дипломного проекта был спроектирован участок механической сборки . Было рассчитано необходимое количество оборудования исходя из трудоемкости изготовления узла «Шток». Были рассчитаны коэффициент загрузки оборудования производственные площади необходимые для расположения станочного оборудования склад заготовок склад готовой продукции. План и механосборочного участка проекта представлен на листе графической части дипломного проекта ДП.000.000.008.
Задача дипломного проекта – проект специализированного участка по выпуску гидроцилиндров НК 4040 в условиях мелкосерийного производства. С этой целью было применено современное оборудование уменьшено количество операций в сравнении с базовым технологическим процессом проведена оптимизация технологических операций путем обоснованного выбора оборудования станочных и контрольных приспособлений режущих и вспомогательных инструментов средств механизации и автоматизации; рассчитаны припуски под механическую обработку расчётно-аналитическим методом; спроектировано станочное приспособление для обработки штока контрольно-измерительное приспособление для контроля торцевого биения.
В дипломном проекте выполнены соответствующие силовые расчёты расчёты на точность спроектированных приспособлений; выполнено экономическое обоснование замены универсального оборудования на станки с ЧПУ и полуавтоматы; разработаны мероприятия по охране труда.
Эффективность внесённых изменений в базовые технологические процессы доказана экономическими расчётами в организационно экономической части дипломного проекта.
Горбацевич А.Ф. Курсовое проектирование по технологии машиностроения. - Минск: Вышейш. шк. 1983. - 256с.
Общемашиностроительные нормативы времени обработки на станках с ЧПУ и сборки машин (серийное производство). - М.: Машиностроение 1968. - 235 с
Маталин А.А. Технология машиностроения. - Л.: Машиностроение 1985-496 с.
Егоров М.Е. Дементьев В.И. Дмитриев В.Л. Технология машиностроения. - М.: Высшая школа 1986.-534 с.
Корсаков В.С. Основы технологии машиностроения-М.: Машиностроение 1977-416с.
Балакшин Б.С. Основы технологии машиностроения. М.: Машиностроение 19ф69-559 с.
Гжиров Р.И. Краткий справочник конструктора. - Л.: Машиностроение 1983.-464с.
Технология машиностроения: В 2 кн. Кн.1. Основы технологии Машиностроения: Под ред. С.Л. Мурашкина. – М.: Высш. шк. 2003. – 278с.
Технология машиностроения: В 2 кн. Кн.2. Производство деталей машин Под ред. С.Л. Мурашкина. – М.: Высш. шк. 2003. – 295с.
Технология машиностроения (специальная часть) А.А. Гусев Е.Р. Ковальчук И.М. Колесов и др. - М.:Машиностроение 1986.-480с.
Режимы резания металлов: Справочник. Под ред. Ю.В. Барановского. - М.:Машиностроение 1972.-407с.
Справочник технолога-машиностроителя: В 2т. Под ред. А.Г. Косиловой и Р.К. Мещерякова. - М.: Машиностроение 1985.-Т.1-656с.
Сафраган Р.Э. Технологическая подготовка производства для станков с ЧПУ Р.Э. Сафраган Ю.И. Кузнецов Б.А. Гончаренко. - Киев:
Оптимизация технологических процессов и методов обработки. Ч. 2. Оптимизация процессов резания. Учеб. пособие Ю. Н. Полянчиков А. Г. Схиртладзе А. Н. Воронцова. - ВолгГТУ Волгоград 2004. - 80. с
Егоров М. Е. «Основы проектирования машиностроительных заводов» М.: Машиностроение 1969.– 480 с
Проектирование автоматизированных участков и цехов. Под ред.Ю.М. Соломенцева Москва «Высшая школа» 2000г. 270 с
Киселев Е.С. Проектирование механосборочных и вспомогательных цехов машиностроительных предприятий: учебное пособие. Ульяновск: УлГТУ 1999. 118 с. ISBN 5-89146-000-0
Модульное оборудование для гибких производственных систем механической обработки: Справочник Р. Э. Сафроган Г. А. Кривов В. Н. Татаренко и др.; Под ред. канд. техн. наук Р. Э. Сафрагана. - К.: Техника 1989 - 175 с
Вохидов А. С. Нанотехнология сегодня и завтра: учеб. пособие. Спб. 2009.
Каталог SANDVIK. Coromant. 2012
Нанопокрытия для металлорежущего инструмента [электронный ресурc] – Режим доступа . –
Аваков А.А. Физические основы теорий стойкости режущих инструментов. М. Машгиз 1960.
Автоматизированное проектирование режущего инструмента Гречишников В.А. Кирсанов Г.Н. и др. М.: Мосстанкин 1984. 107 с.
Александров А .Я. Ахметзянов М.Х. Поляризационно-оптические методы механики деформируемого тела. М.: Наука 1973. - 576 с.
Андреев Г.С. Исследование напряжений в рабочей части резца на поляризационно-оптической установке с применением киносъемки Вестник машиностроения. 1958. - № 5.- с.54-57.
Бетанели А.И. Прочность и надежность режущего инструмента. -Тбилиси: Сабчота сакартвело 1973. 304 е.: ил.
Бобров В.Ф. О распределении удельных нормальных сил и сил трения на передней поверхности инструмента. -II Сб. "Обработка металлов резанием и давлением" М.: Машиностроение 1965.154
Бобров В.Ф. Определение напряжений в режущей части металлорежущих инструментов Высокопроизводительное резание в машиностроении. -М.: Наука 1966. с.228-233.
Бобров. В.Д. Основы теории резания металлов. М.: Машиностроение 1975. -344с.
Гжиров Р.И. Серебреницкий П.П. Программирование обработки на станках с ЧПУ: Справочник. — Д.: Машиностроение 1990. 588 с.
Гордон М.Б. Распределение контактных напряжений и коэффициента трения на передней поверхности резца Известия вузов Машиностроение. - 1966.-№9.-с. 126-131.
Грановский Г.И. Грановский В.Г. Резание металлов: учебник для машиностр. и приборостр. спец. вузов.- М.: Высшая школа 1985.-304 е.: ил.155
Гречишников В.А. Системы проектирования режущих инструментов. М.: ВНИИТЭМР. Сер. 9 1987 вып. 2. 52 с.
Драгун А.П. Режущий инструмент. Л.: Лениздат 1986. - 270с.
Ефимович И.А. Повышение эксплуатационной эффективности инструмента на основе исследования напряженно-деформированного состояния и прочности его режущей части при различных видах стружкообразова-ния: Дисс. . канд. техн. наук. Томск. - 1999. - 198 с.
Полетика М.Ф. Козлов В.Н. Контактные нагрузки и температуры на изношенном инструменте Прогрессивные технологические процессы в машиностроении: Сборник научных трудов. Томск: ТПУ 1997. - с. 18-21.
Прибылов Б.П. Основы расчета режущего инструмента на прочность. М. ВНИИ 1966.
Прочность режущего инструмента. Сборник статей под ред. Романова К.Ф.М. 1967.
Развитие науки о резании металлов Н.Н. Зорев Г.И. Грановский М.Н. Ларин Т.Н. Лоладзе И.П. Третьяков и др. М.: Машиностроение 1967.-416 е.: ил.
Режущий инструмент: Альбом Под ред. В.А. Гречишникова. ч. 1. -М.: «Станкин» 1996.
Резников А.Н. Резников Л.А. Тепловые процессы в технологических системах. М.: Машиностроение 1990. - 288 е.: ил.
Родин П.Р. Металлорежущие инструменты. Киев: «Вища школа» 1974-400 с.
Розенберг A.M. Еремин А.Н. Элементы теории процесса резания металлов. М.: Машгиз 1956. - 319 с. 14.161
Розенберг A.M. Розенберг О.А. Механика пластического деформирования в процессах резания и деформирующего протягивания АН УССР. Ин-т сверхтвердых материалов. Киев: Наук думка 1990. - 320
Утешев М.Х. Разработка научных основ расчета прочности режущей части инструмента по контактным напряжениям с целью повышения его работоспособности: Автореф. доктора техн. наук. Томск 1996. - 36 с.
Фадюшин И.Л. Музыкант Я.А. Мещеряков А.И. и др. Инструмент для станков с ЧПУ многоцелевых станков и ГПС. М.: Машиностроение 1990.-272 с.
Филлипов Г.В. Режущий инструмент. Л.: Машиностроение 1981. -393 с.
Хает Г.Л. Надежность режущего инструмента. Изд. Укр. НИИНТИ Киев 1968.164
Хает Г.Л. Сергеев Л.В. Миранцов Л.М. Расчет на прочность твердосплавного резца как составного тела Надежность режущего инструмента. Техника 1972. - с. 106-116.
Хает Г.Л. Прочность режущего инструмента. М.: Машиностроение 1975. - 166 с.
Хает Г.Л. Гах В.М. Громаков К.Г. и др. Сборный твердосплавный инструмент. М.: Машиностроение 1989. - 256 с.
Шарин Ю. С. Обработка деталей на станках с ЧПУ. М.: Машиностроение 1983. - 117 с.
Кузнецов Ю. И. Маслов А. Р. Бабайков А. Н. Оснастка для станков с ЧПУ: Справочник. - 2-е изд. перераб. и доп. - М.: Машиностроение 1990. - 512 л.: ил.
Станочные приспособления: Справочник: В 2т. Под ред. Б.Н. Вардашкина. - М.: Машиностроение 1984.-Т.1-592с.; Т.2-656с.
Карнаух С.Г. Детали машин: Конспект лекций. – Краматорск: ДГМА 2002. – 212 с.
Безопасность труда в промышленности: Справочник К.Н. Ткачук П.Я. Галушко Р.В. Сабарно и др. - К.: Техника 1982. – 231 с.
Охрана труда в автоматизированном производстве – Краматорск ДГМА 2007 – 300 с.
Дементий Л.В. Охрана труда в механических и сборочных цехах Л.В. Дементий С.А. Гончарова. – Краматорск: ДДМА 2005. – 312 с.
Анализ базового технологического процесса
Таблица А1 – Анализ технологического процесса изготовления детали шток
Режущий измерительный инструмент
Комплект разметочного инструмента
Проверить годность заготовки припуска. Разметить торцы нанести осевые линии
Патрон 4х кулачковый люнет центр вращающийся ГОСТ 8742-75
Применить фрезерно-центровальный станок для зацентровки и торцевания
Продолжение таблицы А1 – Анализ технологического процесса изготовления детали шток
Комплект слесарного инструмента
Патрон 4х кулачковый люнет центр ГОСТ 8742-75
Резец проходной 10х25 Т5К10 ГОСТ 18879-73 резец проходной 40х25 Т5К10 ГОСТ18869-73 штангенциркуль ШЦ 2 0-250-01
Линейка 1000 ГОСТ 475-80
Использовать механизированное зажимное приспособление с наладочным кулачком
Провести то закалку с высоким отпуском (241 285 НВ)
Очистить поверхность от окалины
Патрон 3х кулачковый центр ГОСТ 8742-75
Резец токарный проходной 25х25 ф=45 гр. Т5К10 ГОСТ 1879-73 резец подрезной 25х25 Т5К10 ГОСТ 18880-73 сверло центровое ВЧ Р6М5 ГОСТ 14952-75 ШЦ -250-01 ГОСТ166-80
Установ АБ (проверить центра начисто подрезать торцы) см. схему операция №10 (Установ БВ)
Установ А Б на фрезерно-центровальном станке установ В – выделить в обработку на операцию 20
Патрон 3х кулачковый центр упорный ГОСТ 13214-75 центр вращающийся ГОСТ 8742-75
Резец токарный проходной 25х25 ф=45 гр. Т5К10 ГОСТ 1879-73 резец Канавочный в=5 в=3 25х25 Т5К10 ГОСТ 18880-73 сверло центровое ВЧ Р6М5 ГОСТ 14952-75 ШЦ -250-01 ГОСТ166-80 резец канавочный специальный скоба шаблоны канавочные ШЦ 2 0-250-01
Применить токарно-винторезный станок с ЧПУ (16К20Ф3 резцы с механическим креплением пластин)
Снять заусенец кромки опилить нарезать резьбу М36х2
Исключить резьбу нарезать на предыдущей операции
Разметить под обработку лыску в=40 осевые отверстия 62 6
0 Вертикально-фрезерная
Призмы прихваты упор
Фреза торцевая 125 z=12 Т5К10 ГОСТ 24359-80 ШЦ 1 0-125 005 ГОСТ 166-80 скоба
Установить АБ (с поворотом детали на 180град.)
Применить переналаживаемые поворотное приспособление
Снять заусенец кромки опилить
0 Горизонтально расточная
Сверло спиральное 6 Р6М5 ГОСТ 10903-77 суппорт летучий оправка расточная резец расточной 10х10 ф=45 Т5К10 резец канавочный в=19 Р6М5 специальный нутромер калибр-пробка ШЦ 10-125 005 ГОСТ 166-80
Применить механизированное приспособление сверление выполнить на радиально-сверлильном станке
Патрон поводковый центр упорный ГОСТ 132214-75
Токарно-обкатное приспособление шлифовальная шкурка СМ 63А ГОСТ 27181-86 шлифовальный брусок резец токарный ГОСТ 18879-73 скоба
Применить средство активного контроля
Покрытие хром – Хтв 35 55
0 Кругло-шлифовальная 3М161
Центра упорные ГОСТ 13214-75 патрон поводковый
Круг шлифовальный ПП 600х40х305 24А 50 СМ1 к 67 35мс ГОСТ 2424-83 микрометр образцы шероховатости
Применить прибор активного контроля
Полировальное приспособление шкурка полировальная
Маршрутные о операционные карты
Рекомендуемые чертежи
- 13.04.2022
Свободное скачивание на сегодня
- 23.02.2023