Проектирование участка изготовления корпуса редуктора




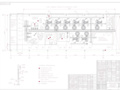
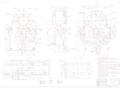
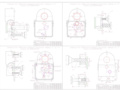
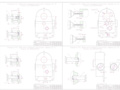
- Добавлен: 25.10.2022
- Размер: 1 MB
- Закачек: 0
Описание
Состав проекта
![]() |
![]() |
![]() ![]() ![]() |
![]() ![]() ![]() |
![]() ![]() ![]() |
![]() ![]() ![]() |
![]() ![]() ![]() |
![]() |
![]() ![]() ![]() |
![]() ![]() ![]() |
![]() ![]() ![]() |
![]() |
![]() ![]() ![]() ![]() |
![]() ![]() ![]() ![]() |
![]() |
![]() ![]() ![]() ![]() |
![]() ![]() ![]() ![]() |
![]() ![]() ![]() ![]() |
![]() ![]() ![]() ![]() |
![]() ![]() ![]() ![]() |
![]() ![]() ![]() ![]() |
![]() ![]() ![]() ![]() |
![]() ![]() ![]() ![]() |
![]() ![]() ![]() ![]() |
![]() ![]() ![]() ![]() |
![]() ![]() ![]() ![]() |
![]() ![]() ![]() ![]() |
![]() ![]() ![]() ![]() |
![]() ![]() ![]() ![]() |
Дополнительная информация
Глава1.doc
В этих условиях на первый план выходят такие технологии которые снижают себестоимость изделия способствуют созданию эффективной конкурентоспособной техники при этом не требующие непомерно больших капиталовложений.
Широкие перспективы повышения эффективности производства открылись в связи с внедрением в машиностроение станков с ЧПУ и гибких производственных систем.
Основными преимуществами станков с ЧПУ по сравнению с универсальными станками с ручным управлением являются: повышение точности обработки сокращение или полная ликвидация разметочных работ; концентрация переходов обработки на одном станке что приводит к сокращению затрат времени на установку заготовки а также уменьшения парка станков.
Гибкие автоматизированные участки и гибкие автоматические линии на их базе а также системы машин также получили наибольшее распространение в крупно – серийном и массовом производствах. Эти производства характеризуются постоянным увеличением выпуска продукции повышенными требованиями к ее качеству и высокими требованиями к экономической эффективности производства. Поэтому основными задачами совершенствования автоматических линий являются:
повышение технологичности деталей сборочных единиц и изделий;
дальнейшее повышение точности и качества заготовок обеспечение стабильности припуска под механическую обработку совершенствование методов получения заготовки снижающих ее себестоимость и расход материала;
создание автоматических линий и систем машин для комплексного изготовления деталей с включением всех необходимых операций технологического процесса;
дальнейшее повышение степени концентрации операций технологического процесса и связанное с этим усложнение структур технологических систем машин;
развитие прогрессивных технологических процессов – основы эффективной автоматизации производства создание новых методов обработки деталей выбор наиболее эффективной структуры процессов и структурно - компоновочных схем оборудования разработка новых типов и конструкций режущих инструментов обеспечивающих высокую производительность и качество обработки;
повышение степени непрерывности технологических процессов;
дальнейшее развитие идеи агрегатирования и модульного принципа создание средств автоматизации;
широкое использование ЭВМ;
разработка и применение САПР ТП САПР ТСО и др.;
совершенствование эксплуатационной технологии;
сокращение производственных циклов;
внедрение наукоемких технологий.
По сравнению с не автоматизированным производством эффективность применения автоматических линий станков с ЧПУ агрегатных станков достигается за счет существенного роста производительности снижения себестоимости изготовления деталей резкого уменьшения трудоемкости обработки и численности производственного персонала повышения качества продукции и ритмичности ее выпуска уменьшения производственной площади.
Тема дипломного проекта посвящена созданию производственного процесса изготовления корпуса редуктора. Объем выпуска – 20000 штук в год.
При дипломном проектировании поставлены следующие задачи:
выбрать способ получения заготовки и маршрут обработки; рассчитать припуски и режимы резания на механическую обработку; выбрать необходимое оборудование и инструменты; рассчитать участок по изготовлению корпуса редуктора; спроектировать расточную оправку и приспособление-спутник; предложить компоновку гибкого автоматического участка; обосновать экономически необходимость создания ГАУ.
При дипломном проектировании выполнен следующий объем работ:
на основании анализа назначения и характеристик детали выбран способ получения заготовки и маршрут ее обработки для условий массового производства;
сформированы операции технологического процесса выбрано оборудование режущий инструмент и оснастка;
рассчитаны припуски и режимы резания для обработки основных поверхностей корпуса при механической обработке;
сконструирована расточная оправка для растачивания внутренних отверстий заготовки и приспособление для сверления и расточки отверстий;
выполнен расчет производственного участка и разработаны основные принципы организации труда;
разработан раздел охраны труда и экологии;
выполнена экономическая часть.
Расчеты показали целесообразность создания ГАУ для крупносерийного производства корпуса редуктора при программе выпуска 20000в год.
Глава 1. ТЕХНОЛОГИЧЕСКАЯ ЧАСТЬ
Исходными данными для создания технологического процесса является чертеж детали с техническими требованиями.
Объем годового выпуска – 20000 штук в год работа производится в две смены.
2. Анализ исходных данных
Корпус редуктора входит в электромеханизм предназначенный для изменения угла установки оси облучателя в составе антенно-поворотного устройства системы тропосферной радиосвязи. Условия работы характеризуются большими нагрузками на места посадки подшипников.
Вторая ступень редуктора имеет комбинированную коническую шестерню управляющую через промежуточный вал прибором контроля угла поворота облучателя.
Электромеханизм проверяется на герметичность взаимозаменяемость по электрическим и геометрическим параметрам устойчивость к климатическим воздействиям; а для проверки работоспособности должен быть подвергнут технологической приработке в течении 10 минут от сети переменного трехфазного тока напряжением 220 В с частотой 50 Гц.
Максимальный внутренний обрабатываемый диаметр:.
Минимальный внутренний обрабатываемый диаметр с резьбой: .
Габаритные размеры корпуса: .
Поверхности посадки подшипников имеют диаметры: (размеры высокой точности).
С одной стороны имеется фигурный паз под уплотнитель: .
Условия работы корпуса определяют наличие допусков на соосность отверстий относительно друг друга – 002 мм.
Посадочные поверхности имеют шероховатости Ra=08 мкм резьба имеет шероховатость Ra = 125 мкм остальные поверхности имеют шероховатости Ra=10 мкм Ra=32 мкм Ra=16 мкм согласно базовому чертежу.
3. Оценка технологичности детали
Конструкция детали должна удовлетворять двум основным условиям:
- выполнение служебного назначения;
- обеспечение возможности применения высокопроизводительных методов обработки детали а следовательно обеспечение минимальной себестоимости изделия.
Рассмотрим соответствие данного корпуса этим требованиям.
Корпус редуктора представляет собой отливку коробчатой формы из сплава алюминия марки АЛ9. Отливка II-той группы сложности требует применения стержневой формовки для образования внутренних поверхностей.
Корпус имеет достаточно надежный комплект технологических баз обеспечивающий требуемую ориентацию и надежное крепление заготовки на станке при возможности ее обработки с нескольких сторон без переустановки детали тем самым позволяет снизить погрешность базирования.
Основные отверстия: выполняется высокой точности сквозными находящиеся на одной оси что позволяет выполнять обработку на проход меньшим числом инструментов (рис. 1).
Рис. 1. Пример нахождения отверстий
Диаметральные размеры отверстий уменьшаются в одном направлении (см. рис. 1.).
Обрабатываемые поверхности заготовки расположены в доступных для обработки плоскостях которые могут быть обращены к шпинделю при последовательном повороте стола. Назначены оптимальные требования к точности и качеству поверхностей; рационально проставлены размеры.
Отверстие является не достаточно технологичным т.к. выполнено глухим что затрудняет обработку (рис. 2.)
Рис. 2. Пример нетехнологичного отверстия
Рис. 3. Пример нетехнологичного выступа
Недостаточная жесткость выступа так же отрицательно сказывается на технологичности детали (рис. 3.).
Остальные обрабатываемые поверхности с точки зрения точности и чистоты не представляют значительных технологических трудностей. В целом анализ исходных данных показал что деталь – корпус редуктора из сплава АЛ9 с условием изготовления ее на автоматической линии можно считать технологичной.
4. Определение типа производства
В зависимости от широты номенклатуры регулярности выпуска стабильности и объема выпуска продукции различают три типа производства: единичное серийное и массовое (ГОСТ 14.004-83).
Основным критерием при определении типа производства является коэффициент закрепления операций который определяется по формуле:
где – число операций выполняемых в течение месяца;
– число рабочих мест.
Однако на первом этапе трудно определить число рабочих мест и число операций выполняемых в течение месяца. Поэтому ориентировочно будем судить о типе производства по коэффициенту серийности:
где – действительный годовой фонд рабочего времени
– годовая программа выпуска
– среднее штучное время обработки.
Данное значение соответствует крупносерийному производству.
Для крупносерийного производства характерно:
- ограниченная номенклатура изделий;
- изготовление повторяющимися партиями;
- большой объем выпуска;
- изготовление всей серии целиком при обработке деталей и сборке;
- расположение оборудования по технологическому циклу;
- процесс изготовления деталей построен по принципу дифференциации операций;
- использование специального и нормализованного инструмента;
- низкая квалификация работающих (при высокой квалификации наладчиков).
Материал заготовки – алюминиевый сплав марки АЛ9 ГОСТ 2685-75 ; сплав на основе системы алюминий – кремний кремния – 6-8% - обладает хорошими технологическими свойствами (жидкотекучестью).
Служебное назначение особенности и материал детали программа выпуска предопределяют метод получения заготовки – литье.
Предложено получать заготовку литьем в кокиль т.к. это дает много преимуществ:
)низкая себестоимость по сравнению с другими методами получения заготовки;
)снижение затрат труда на обработку.
Определим коэффициент использования металла (КИМ):
Сравним два метода литья: литье в песчанно-глинистые формы и литье в кокиль. Оценивать способы получения заготовки будем по себестоимости т.к. она дает наиболее полную картину взаимосвязанных затрат на производство заготовки и ее последующей механической обработки.
Базовая стоимость одного килограмма литья будет складываться из оптовой цены 1 кг материала 36% - вспомогательный материал (от оптовой цены) 10% - транспортно-заготовительные расходы (от оптовой цены).
Литье в песчанно-глинистые формы – 27 руб.кг литье в кокиль – 20 руб.кг (по ценам базового предприятия).
Отсюда найдем базовую стоимость по двум вариантам.
Литье в песчанно-глинистые формы:
Себестоимость сопоставляемых заготовок найдем по формуле:
где - базовая себестоимость 1кг заготовок руб.;
- коэффициенты зависящие от класса точности группы сложности массы марки материала объема производства ;
- масса готовой детали ;
- цена 1 кг отходов
Себестоимость заготовки полученной литьем в кокиль:
Себестоимость заготовки полученной литьем в песчанно-глинистые формы:
Из произведенного расчета видно что метод получения заготовки – литье в кокиль дешевле чем литье в песчанно-глинистые формы.
Таким образом заготовку корпуса редуктора предложено получать литьем в кокиль.
6. Анализ существующего технологического процесса
Деталь-аналог изготавливается на участке где оборудование расставлено по группам станков (токарные фрезерные сверлильные резьбонарезные станки). Детали передают от станка к станку в таре. Установка и снятие деталей на всех рабочих местах осуществляется с помощью рабочих. Контроль производится на рабочих местах. Все станки на участке не имеют ЧПУ и обработка всех поверхностей идет поочередно
Технологический маршрут механической обработки состоит из следующих операций:
Существующий технологический процесс выполняется на 8 рабочих местах (при объеме выпуска 1000в год) следовательно для реализации заданной программы выпуска выполнение технологического процесса потребует большего количества оборудования и рабочих а так же дополнительные производственные площади.
7. Обоснование выбора технологических баз
Выбор технологических баз основывается на выявлении и анализе функционального назначения поверхностей детали и установлении соответствующих размерных связей определяющих точность положения одних поверхностей относительно других.
Следует различать выбор технологических баз для обработки большинства поверхностей заготовки и выбор технологических баз на первой операции.
Анализ функционального назначения различных поверхностей детали и размерных связей между ними позволяет определить поверхности относительно которых задано положение большинства других поверхностей и выявить поверхности к которым предъявляют наиболее жесткие технические требования.
Проанализируем выбор баз для корпуса. На первой операции обрабатываем плоскость с наибольшими габаритами так как она будет являться основной базой на последующих операциях. Для обработки следующих поверхностей деталь базируем таким образом чтобы обработанная поверхность стала установочной базой что обеспечит снятие равномерного припуска с обрабатываемых поверхностей.
Рис. 4. Расположение баз
Таким образом плоскость А - является установочной базой; плоскость Б - направляющей т.к. имеет наибольшую протяженность (см. рис. 4.).
Обработка большинства поверхностей заготовки с использованием одних и тех же технологических баз позволяет получить требуемую точность размеров детали.
8. Разработка технологического процесса механической обработки
8.1. Установление последовательности обработки основных поверхностей и обоснование необходимого количества переходов
При механической обработке нельзя избежать искажения ранее обработанных поверхностей вследствие действия остаточных напряжений и повреждений при закреплении температурных деформаций системы и наследственных признаков заготовки. Для достижения заданных параметров готовых поверхностей маршрут механической обработки необходимо разделить на черновые чистовые и отделочные операции.
К черновым операциям относятся: черновое обтачивание черновое фрезерование сверление фрезерование и зенкерование где механическая обработка сопровождается большим съемом металла.
Чистовые операции: чистовое и тонкое обтачивание шлифование предварительное и окончательное развертывание которые не вызывают сильного изменения макронапряжений и обеспечивают заданную точность обработки.
На выбор способов средств и количества переходов оказывают влияние следующие основные факторы: качество готовой детали точность исходной заготовки и детали; технологические возможности станка. Для этого руководствуемся среднестатистическими данными по точности различных методов и видов обработки [2]. Для каждого перехода определяем расчетное уточнение [3].
Под расчетным уточнением понимается отношение допуска на рассматриваемую характеристику заготовки к допуску на рассматриваемую характеристику детали:
Для получения годной детали необходимо чтобы:
где - уточнение которое необходимо получить при обработке заготовки для достижения требуемой точности детали;
- уточнение получаемое на каждом переходе;
т - количество переходов.
Определим расчетные уточнения для нескольких поверхностей:
Обработка поверхности 1 Ra=16 мкм
Рис. 5. Схема расположения поверхности 1
Полученная величина расчетного уточнения не может быть принята за критерий т.к. она реализуется за один переход а требуемая шероховатость поверхности Ra=16 предполагает как минимум два перехода.
Определим расчетную величину уточнения по шероховатости:
черновое фрезерование:
чистовое фрезерование:
Обработка поверхности 2 Ra=08 мкм
Рис. 6. Схема расположения поверхности 2
черновое растачивание:
чистовое растачивание:
тонкое растачивание:
Обработка поверхности 3 Ra=10 мкм
Рис. 7. Схема расположения поверхности 3
Обработка поверхности 4 Ra=10 мкм
Рис. 8. Схема расположения поверхности 4
точность достигнута.
8.2. Разработка маршрута и формирование операций
Разработаем маршрут обработки корпуса редуктора. Ранее нами определен тип производства как крупносерийный поэтому предлагается обработку корпуса производить на гибком производственном участке с применением принципов концентрации и дифференциации.
Принцип концентрации предполагает объединение и выполнение всех операций технологического процесса на автоматической линии а дифференциация – разбиение операций на переходы с равным тактом выпуска.
Для удобства разработки маршрута обрабатываемые поверхности обозначим следующим образом:
– базовая площадка ;
– отверстие в двух стенках 58+003;
– внутренний торец 66+003;
– отверстие 30+0021;
– отверстие 34+0025;
– отверстие 38+0039;
– внутренний торец 80+003;
– внутренний уступ 26+052;
- отверстие 30±0023;
Заготовка – отливка коробчатой формы II группы. На первом этапе механической обработки необходимо выбрать черновые технологические базы выбрать и изготовить чистовые базы а также устранить дефекты размеров и поверхностного слоя. Для этого проводим черновое и чистовое фрезерование базовых поверхностей 1 и 2 а также черновое фрезерование поверхности 3 и уступа 4. Здесь же фрезеруем контурный паз 5.
За черновые технологические базы на этом этапе примем поверхности будущих баз. Поверхности 1 2 будут основными технологическими базами. Снимем заусенцы после фрезерования.
Остальные операции будут производиться с другой системой базирования.
Далее проведем черновое и чистовое фрезерование боковых торцев 6 7.
Затем производим черновую и получистовую обработку отверстий под подшипники и внутренних торцев под крышки 10 11 12 13 14 17 18 20 21.
Потом проведем получистовую обработку этих же поверхностей.
Произведем сверление отверстий и отверстий под резьбы: как с одной так и с другой стороны.
На последних переходах будем производить чистовую обработку отверстий под подшипники и торцев под крышки 10 11 12 13 14 17 18 20 21.
После чего нарежем резьбу и снимем фаски.
Далее на последней операции просверлим отверстия и нарежем резьбу в них ранее не доступных поверхностях.
На промежуточных и окончательных операциях деталь подвергают мойке сушке контролю.
По выбранному плану обработки можно составить последовательность операций и выбрать их количество. При помощи концентрации переходов определяем количество операций – 3.
Третья: сверлильно-фрезерно-расточная
Четвертая: сверлильно-фрезерно-расточная
На базе разработанного плана обработки основных поверхностей разработан маршрутный технологический процесс.
8.3. Расчет припусков на механическую обработку
Припуски на обработку всех поверхностей устанавливаем с использованием опытно статистического метода [6 табл. 63]. При этом методе припуски назначаем без учета конкретных условий построения технологического процесса. По таблице принимаем припуски на механическую обработку деталей из цветных металлов и сплавов для плоскостей равные 2 мм а для литых отверстий припуск на диаметр при его номинальном размере до 50 мм равный 3 мм свыше 50 мм - 35 мм.
Для двух поверхностей (плоской и цилиндрической) промежуточные припуски определяем расчетно-аналитическим методом разработанным профессором В.М. Кованом [2 с. 174-196] и учитывающим конкретные условия выполнения технологического процесса.
Минимальный припуск при последовательной обработке противолежащих поверхностей (односторонний припуск) определим из выражения:
а минимальный припуск при обработке внутренней поверхности (двухсторонний припуск) найдем по формуле:
где - высота неровностей профиля на предшествующем переходе;
- глубина дефектного поверхностного слоя на предшествующем переходе;
- суммарные отклонения расположения поверхности на предшествующем переходе;
- погрешность установки заготовки на выполняемом переходе.
Определим припуск на обработку и промежуточные предельные размеры для поверхности 1.
Суммарное значение Rz и h характеризующие качество поверхности деталей получаемых литьем в кокиль [2 с. 182] принимаем:
Заготовка представляет собой отливку II-го класса точности массой 478 кг. Технологический маршрут обработки поверхности 1 состоит из двух переходов: чернового и чистового фрезерования выполняемых при одной установке обрабатываемой детали.
Рис. 9. Расположение поверхности 1
Суммарное значение пространственных отклонений для заготовки данного типа определяем по формуле [6 с. 178]:
где - отклонение плоской поверхности отливки от плоскостности (коробление);
- смещение стержня в горизонтальной или вертикальной плоскости.
Коробление находим как произведение коробление на один мм и наибольшего размера заготовки L:
Величину для отливок находим по таблице [2 с.183] =08 а наибольший размер заготовки L=272 мм таким образом получаем:
Смещение стержня образующего отверстие следует принимать равным зазору между знаком формы и стержнем [2 с.184] принимаем:
Подставим найденные значения в формулу :
Величина остаточного отклонения расположения после чернового фрезерования равна:
где - коэффициент уточнения находим из таблицы 29 [2]:
Итак величина равна:
Погрешность установки при черновом фрезеровании определяем из выражения:
где - погрешность базирования;
- погрешность закрепления.
Так как в нашем случае двойная центрирующая база совпадает с измерительной базой то погрешность базирования равна нулю.
Согласно таблице 14 [2] принимаем:
Остаточная погрешность установки при чистовом фрезеровании равна:
Подставим найденные значения в формулу получим минимальный припуск под черновое фрезерование:
Минимальный припуск под чистовое фрезерование:
Результаты расчетов представим в виде таблицы:
Расчет припусков на обработку и предельных размеров по технологическим переходам поверхности 1
Технологические переходы обработки поверхности 1;
Элементы припуска мкм
Расчетный припуск мкм
Расчетный минимальный размер мм
Допуск на изготовление Тd мкм
Предельные размеры мм
Предельные припуски мкм
Значения допусков каждого перехода принимаются по таблице в соответствии с классом точности [2 табл. 31].
Графу таблицы "расчетный минимальный размер" заполняем начиная с конечного размера последовательным прибавлением расчетного минимального припуска каждого технологического перехода.
Для чернового фрезерования:
В графе "предельные размеры" наименьшие значения получаются округлением расчетных размеров а наибольшие прибавлением допуска к округляемому наименьшему размеру.
Предельные значения припусков находим как разность наибольших предельных размеров:
Минимальные значения получаем как разность наименьших предельных размеров предшествующего и выполняемого перехода:
Общие припуски и определяем суммируя промежуточные припуски на обработку:
Проверим правильность произведенных расчетов по формуле:
следовательно расчет проведен верно.
Рассчитаем припуск на обработку и промежуточные предельные размеры для отверстия 58+003 мм.
Рис. 10. Схема расположения отверстия
Технологический маршрут обработки отверстия состоит из трех переходов: чернового чистового и тонкого растачивания выполняемых при одной установке обрабатываемой детали.
Для отливок в кокиль указано суммарное значение:
Суммарное значение пространственных отклонений для заготовки данного типа определим по формуле (3); величину коробления по формуле (4):
Величину остаточного отклонения расположения после чернового растачивания определим из выражения (1.5) принимаем равным 006:
При последующей обработке величиной пространственного отклонения из-за малого значения пренебрегаем.
Погрешность установки при черновом растачивании найдем по формуле.
По таблице 14 [2] принимаем следовательно:
Остаточная погрешность установки при чистовом растачивании равна:
Под третий переход погрешность установки принимаем равной только погрешности индексации:
Подставив найденные значения в формулу получим минимальные межоперационные припуски под растачивание:
Результаты расчетов представим в виде таблицы 2.
Расчет припусков на обработку и предельных размеров по технологическим переходам отверстия 58
Технологические переходы обработки отверстия 58
Растачивание черновое
Растачивание чистовое
Значения допусков каждого перехода принимаем по таблице в соответствии с классом точности [2 с.192].
Графу таблицы "расчетный минимальный размер" заполняем начиная с конечного размера последовательным вычитанием из него следующего за ним смежного перехода расчетного припуска.
Для тонкого растачивания:
Для чистового растачивания:
Для чернового растачивания:
В графе "предельные размеры" наибольшие предельные размеры получаем округлением расчетных размеров а наименьшие - вычитанием допуска из округленного наибольшего предельного размера.
Предельные значения припусков найдем как разность наименьших предельных размеров и как разность наибольших предельных размеров выполняемого и предшествующего перехода т.е.:
Условие выполняется следовательно расчет проведен верно.
8.4. Расчет режимов резания
Режимы резания для всех технологических переходов были рассчитаны с помощью программы САПР ТП на персональной ЭВМ.
Приведем примеры расчета режимов резания по эмпирическим зависимостям для нескольких переходов.
Операция 010. Черновое фрезерование поверхности 1
Операция выполняется на гибком производственном участке на вертикально фрезерном станке 6Р13РФ3.
Определяем глубину резания при черновом фрезеровании .
Рассчитаем режимы резания на фрезерование поверхности 1
Инструмент – торцевая фреза со вставными ножами оснащенными пластинами из твердого сплава (ГОСТ 24359-80).
Исходной величиной подачи при черновом фрезеровании является величина подачи на один зуб . Выбираем эту величину по таблице 33 [2]:
Скорость резания определяем по формуле [2 с.282]:
где - диаметр фрезы ;
- период стойкости выбираем по таблице 40 [2] ;
- число зубьев фрезы .
Значения коэффициента и показателей степеней выбираем по таблице 39 [2]:
- общий поправочный коэффициент:
где - коэффициент учитывающий качество обрабатываемого материала по таблица 4 [2];
- коэффициент учитывающий состояние поверхности заготовки по таблица 5 [2];
- коэффициент учитывающий материал инструмента по таблице 6 [2].
Определим частоту вращения шпинделя :
Подставив значения получим:
Рассчитаем максимальную силу резания при фрезеровании поверхности 1 по формуле:
Значения коэффициента и показателей степени находим по таблице 41 [2]:
Поправочный коэффициент принимаем из таблицы 10 [2]:
Подставив значения в формулу получим:
Мощность резания равна:
Операция 035. Черновое растачивание отверстия 8 в двух стенках с подрезкой торца 9
Операция выполняется на гибком производственном участке на горизонтально-обрабатывающем центре ИР500ПМ1Ф4.
Инструмент – оправка расточная 2190-2197 специальная.
Так как растачивание отверстия было совмещено с подрезкой торца вследствие совмещения и концентрации переходов то режимы резания для этого перехода будем выбирать максимальные.
Максимальные режимы резания будут при растачивании отверстия 8.
Произведем расчет режимов резания на растачивание отверстия 544+12 до 574+019.
Подача при черновом растачивании принимается максимально допустимой по мощности оборудования жесткости технологической системы прочности режущей пластины и прочности державки.
По таблице 12 [2] принимаем
Скорость резания при растачивании:
где - коэффициент из таблицы 17 [2];
– показатели степени из таблицы 17 [2];
- поправочный коэффициент.
где - коэффициент на обрабатываемый материал из таблицы 1-4 [2 с.261-263];
- коэффициент учитывающий состояние поверхности таблица 5 [2 с.264];
- коэффициент учитывающий материал инструмента таблица 6 [2 с.264].
Рассчитаем скорость резания при растачиквании:
Определим частоту вращения шпинделя – :
Частота вращения шпинделя станка по паспорту совпадает с расчетной.
Рассчитаем максимальную силу резания при чистовом точении при глубине резания по формуле:
где – коэффициенты взятые из таблицы 22 [2 с.271].
Поправочный коэффициент представляет собой произведение ряда коэффициентов:
из таблицы 9 10 23 [2 с.268-272]:
Определим необходимую мощность электродвигателя станка N кВт:
Для остальных операций и позиций механической обработки корпуса редуктора выполнены расчеты режимов резания и сведены в таблицу 3.
Режимы резания механических операций.
Операция 010. Фрезерная
Операция 035. Сверлильно-фрезерно-расточная
Операция 045. Сверлильно-фрезерно-расточная
8.5. Техническое нормирование
Нормы времени на каждый переход и на операцию были рассчитаны как и режимы резания в программе САПР ТП на ПЭВМ.
Далее приведем расчет нескольких переходов и операций.
Штучное время затрачиваемое на операцию механической обработки определяем расчетно-аналитическим методом [2]:
где - основное технологическое (машинное) время на операцию;
- вспомогательное время (время затраченное: на поворот стола на перемещение шпинделя и т.д.) на операцию;
- время обслуживания рабочего места составляет 16% от оперативного времени .
- время перерывов на отдых т.к. в проектируемом процессе используем АЛ а она работает в автоматическом режиме то время перерывов принимаем .
Основное время затраченное на операцию будет складываться из основного времени каждого перехода этой операции [2].
Вспомогательное время на операцию находится точно также как и основное время [2].
Штучно-калькуляционное время равно:
где - подготовительно заключительное время на операцию берем в пределах 12 15 мин;
- число деталей в партии.
где - годовой объем выпуска деталей;
0 – число запусков АЛ в год.
Приведем пример расчета штучного штучно-калькуляционного основного и вспомогательного времени на операцию.
Переход 1: фрезеровать поверхность 1 предварительно
Основное время для фрезерования найдем по формуле:
где - расчетная длинна рабочего хода в нашем случае ;
где - подача на зуб фрезы ;
- частота вращения шпинделя ;
- число зубьев фрезы
При обработке на станках с ЧПУ включает время на поворот шпиндельного блока отвод и подвод суппорта. Время на поворот шпиндельного блока равно 025 мин; скорость быстрых перемещений суппорта около 6000 мммин.
Переход 2: фрезеровать поверхность 1 окончательно
Основное время для фрезерования:
Вспомогательное время на обработку:
На последующие переходы основное и вспомогательное время находим в той же последовательности.
Переход 3: фрезеровать поверхность 2 предварительно
Переход 4: фрезеровать поверхность 3 предварительно
Переход 5: фрезеровать поверхность 2 окончательно
Переход 6: фрезеровать поверхность 3 окончательно
Переход 7: фрезеровать уступ 4
Переход 8: фрезеровать фигурный паз 5
Основное время на операцию будет равно:
Вспомогательное время на операцию:
Рассчитаем оперативное время на операцию:
Время обслуживания рабочего места составляет 16% от оперативного времени:
Зная все значения можно рассчитать норму штучного времени на операцию:
Далее рассчитаем штучно-калькуляционное время на операцию:
Расчет норм времени по остальным операциям ведется аналогично значения их можно свести в таблицу 4.
Нормы времени на операции
8.6. Выбор и расчет оборудования
Для компоновки ГПУ были выбраны стандартные станки: ИР500ПМ1Ф4 – горизонтально-обрабатывающий центр и вертикально-фрезерный 6Р13РФ3. На фрезерном станке производится черновая обработка базовых поверхностей и фрезерование паза а на обрабатывающем центре черновое получистовое и чистовое фрезерование растачивание сверление и нарезание резьб. Также было выбрано оборудование для моечной и контрольной операции использованы приемные и передаточные столы и другие элементы а также транспортные системы специальные и специализированные автоматы.
Рассчитаем потребное количество станков на механические операции по формуле:
где - суммарное нормировочное время необходимое для обработки на станках данного типа годового количества деталей;
- действительный годовой фонд времени работы станков (работы в 2 смены);
- количество смен 2 смены.
где - штучно-калькуляционное время на операцию мин;
- количество одноименных деталей .
Так как действительный годовой фонд времени у нас дан в две смены то знаменатель m мы не учитываем. Значит можно упростить эти формулы и свести их в одну:
Зная все значения рассчитаем количество станков на механические операции. Для первой операции:
Сразу можно найти коэффициент загрузки (должен быть около 1) станка на данной операции по формуле:
Для первой операции он будет равен:
Для третьей операции:
принимаем станка тогда
Для четвертой операции:
принимаем станка тогда .
По результатам расчетов видно что для выполнения всех операций нам потребуется 9 станков. Два фрезерных и 7 горизонтально-обрабатывающих центров.
По результатам выполнения анализа существующего процесса изготовления корпуса редуктора можно сделать следующие выводы:
предложенный выбор технологических баз является наиболее правильным для изготовления корпуса его конфигурация технологична для крупносерийного производства выбран способ получения заготовки – литье в кокиль который обоснован с экономической точки зрения.
предложен новый технологический процесс изготовления корпуса.
выполнен расчет припусков для основных поверхностей.
выполнены расчеты режимов резания и основного технологического времени для операций технологического процесса.
выбрано оборудование для ГПУ
Глава3и4.doc
В состав цеха машиностроительного завода входят производственные и вспомогательные отделения (участки) а также бытовые и служебные помещения. Производственные отделения и участки предназначены для непосредственного осуществления технологических процессов обработки деталей отделки испытания и упаковки сборочных единиц и изделий. Вспомогательные отделения участки и мастерские используются для следующих целей: ремонта оборудования и технологической оснастки (инструментов приспособлений штампов) и заточки инструментов; обслуживания основного производства (приготовления и раздачи СОЖ сбора переработки и удаления отходов) и т.д.
В зависимости от принятой схемы организации производства и величины цеха некоторые вспомогательные отделения могут быть объединены или вовсе исключены.
Кроме производственной программы в состав исходных для проектирования цеха данных в общем случае входят следующие материалы:
рабочие чертежи и спецификации изготавливаемых изделий;
технические условия на обработку деталей на отделочные виды испытаний и упаковку;
сводные нормы расхода материалов на все изготавливаемые в цехе изделия;
технологические процессы с нормами времени а также средний процент выполнения норм по видам работ;
план расположения оборудования и рабочих мест а также ведомость уже установленного технологического и подъёмно-транспортного оборудования с указанием степени его износа при реконструкции цехов;
ведомость оборудования подлежащего модернизации имеющегося на складе и заказанного промышленности паспортные данные на имеющиеся на заводе уникальные и специальные станки;
ведомости деталей и узлов поставляемых со стороны.
2. Оборудование рабочие места и инвентарь
Оборудование цеха подразделяется на производственное вспомогательное подъемно - транспортное и энергетическое.
К производственному оборудованию относятся металлорежущие станки прессы моечные машины печи специальные стенды и установки на которых выполняются все основные технологические операции по обработке сборке окраске испытанию и упаковке деталей узлов и изделий выпускаемых участком.
К вспомогательному относится оборудование на котором выполняется например: ремонт и заточка инструментов ремонт приспособлений производственного оборудования изготовления запасных частей к нему а также лабораторное оборудование.
К энергетическому оборудованию относится отдельно стоящие источники преобразования тока насосы трансформаторы генераторы обеспечивающие работу всех других видов оборудования.
Рабочее место - это отдельный производственный участок закрепленный за рабочим или бригадой рабочих предназначенный для выполнения определенных технологических операций. При многостаночном обслуживании когда несколько станков обслуживается одним рабочим каждый из этих станков считается одним рабочим местом поэтому автоматизированную линию можно считать одним рабочим местом.
Инвентарь цеха подразделяется на производственный и хозяйственный.
3. Компоновка и планировка участка
Компоновка - это схематический план здания (корпуса) с изображением на нем цехов отделений участков вспомогательных и служебно-бытовых помещений. Назначение компоновочного плана - взаимная увязка входящих в состав цехов отделений и участков выбор оптимального направления производственного процесса внутрицехового транспорта грузовых и людских потоков а также рациональное размещение вспомогательных и служебно-бытовых помещений.
Планировка цеха - это план расположения производственного подъёмно-транспортного и другого оборудования инженерных сетей рабочих мест проездов и проходов. При разработке планировки были учтены следующие основные требования:
оборудование в цехе размещается в соответствии с принятой организационной формой технологических процессов. Оборудования размещено в порядке последовательности выполнения технологических операций обработки контроля и сдачи деталей или изделий;
расположение оборудования проходов и проездов выполнено с учетом действующих норм и гарантирует удобство и безопасность работы; возможность монтажа демонтажа и ремонта оборудования; удобство подачи заготовок и инструментов; удобство уборки отходов;
планировка размещения оборудования согласована с применяемыми подъёмно - транспортными средствами. Планировкой предусмотрены кратчайшие пути перемещения заготовок деталей узлов в процессе производства исключающие возвратные движения. Грузопотоки не пересекаются между собой а также не пересекаются и не перекрываются основные проезды и проходы предназначенные для движения людей.
Планировка предусматривает возможность перестановки оборудования при изменении технологического процесса.
План расположения оборудования составлен для определения площади занимаемой участком и взаимной увязки размещения станков. На чертеже показано технологическое контрольно-измерительное и вспомогательное оборудование (электрошкафы инструментальные шкафы и т.д.).
Исходными данными для планировки являются структурная схема и эскизы станков выполненные с учетом выбранных в соответствии с технологическим процессом их типов и габаритов.
При разработке плана расположения оборудования расстояние между станками определено в зависимости от необходимости выполнения проходов между станками и доступа к станкам.
Количество станков необходимых для обработки деталей по заданной производственной программе в гибкой автоматизированной линии определяется технологическим процессом и рассчитанными нормами времени на выполнение каждого перехода основных операций. Рассчитаем такт выпуска:
Следовательно такт выпуска при двухсменной работе ГАУ составляет 1257 мин.
4. Определение размера площади участка
Площадь механического цеха по своему назначению делится на производственную вспомогательную и служебную (служебно-бытовых помещений). К производственной площади относится площадь занятая автоматической линией станками верстаками проходами и проездами между рядами станков складами заготовок и другими вспомогательными службами а также магистральными проездами обслуживающими разные цехи. К площади служебно-бытовых помещений относятся площади занятые раздевалками душевыми санитарными узлами а также площадь занимаемая администрацией цеха и другими техническими и конторскими службами по обслуживанию производства.
Площадь участка в плане:
где - длина участка м;
где - высота участка м;
Объем участка будет составлять: 14826 м3
Общее количество участвующих в работе участка по обработке корпуса составляют: производственные и вспомогательные рабочие МОП и служащие.
Расчет необходимого количества производственных рабочих (операторов) для обслуживания автоматической линии производится по нормам: с автоматизированной передачей заготовок с линии на следующую операцию - 1 оператор.
Для наладки оборудования предусматривается 5 наладчиков по 2 наладчика в смену. Количество ИТР счетно-конторского и младшего обслуживающего персонала задано ориентировочно 5% от общего их количества в цехе.
6. Организация рабочих мест
Заготовки поставляют в контейнерах из литейного цеха. После чернового фрезерования слесарь-наладчик осматривает заготовки на отсутствие дефектов в соответствии с требованиями чертежа и устанавливает в приспособление. На рабочем месте установлен стол для входного контроля и инструментальный шкаф.
На рабочем месте автоматизированной линии установлены: пульт управления инструментальный шкаф для цеховых наладчиков содержащий набор инструментов и приспособлений для выполнения наладочных работ. Здесь же установлен верстак для выполнения небольших текущих ремонтов.
Для замены инструментов на ГАЛ предусмотрена транспортная система замены инструментальных блоков (на станках ОЦ) и передачи их на участок подготовки инструмента. Также около фрезерных станков установлен инструментальный шкаф и шкаф для вспомогательных материалов. B инструментальном шкафу хранится резервный набор инструментов. Режущий инструмент распределен на группы по времени стойкости и проходят централизованную заточку и настройку. В случае задержки инструмента используется резервный комплект инструментов.
7. Управление гибким автоматизированным участком
Спроектированный ГАУ по обработке корпуса редуктора входит в состав цеха механической обработки. Цех работает в две смены.
Участком руководит мастер. Вопросы эксплуатации решает заместитель начальника цеха. ТО и ТР проводится комплексной бригадой состоящей из наладчиков слесарей-ремонтников инструментальщиков и др. Автоматизированную линию обслуживают наладчики прошедшие специальную подготовку и имеющие квалификацию 5-го и 6-го разряда.
В обязанности мастера входит:
обеспечение выполнения сменных заданий участком соблюдение установленной технологии производства изделий m
организация своевременной подготовки производства его полную загрузку и бесперебойную работу оборудования;
осуществление оперативного контроля за обеспечением материальными и энергетическими ресурсами технически правильной эксплуатацией оборудования и других основных средств экономным расходованием сырья топлива материалов;
выявление предотвращение и устранение причин нарушения хода производства;
проведение работы по изысканию организации использования дополнительных производственных резервов повышения производительности труда снижению трудоемкости и себестоимости продукции;
участие в работе по оперативному планированию производства улучшению нормирования аттестации и рационализации рабочих мест распространение передовых приемов и методов снижению затрат труда;
анализ результатов производственной деятельности участка за смену и причин вызывающих простои оборудования и снижение качества продукции;
участие в разработке и внедрении мероприятий по устранению выявленных недостатков;
организация оперативного учета движения продукции на автоматической линии и складах-штабелерах и выполнения производственных заданий;
контроль соблюдения работниками технологической производственной и трудовой дисциплины правил и норм охраны труда техники безопасности производственной санитарии и противопожарной защиты;
представление предложений о наложении дисциплинарных взысканий на нарушителей трудовой и производственной дисциплины.
Старший оператор должен контролировать работу ГАЛ а также своевременную замену режущего инструмента смену эмульсии масла очистку фильтров должен вести журнал простоев и ремонтов.
Для стабильной работы станков необходимо периодически проводить профилактические осмотры и ремонт оборудования.
К основным правилам профилактики относится следующее:
регулярная смазка и поддержание уровня масла применение масел в соответствии с инструкциями;
регулярный контроль степени нагрева подшипников;
своевременная замена режущего инструмента и быстро изнашиваемых частей;
постоянное наблюдение за работой концевых выключателей блокирующих устройств пневмо- и гидро-клапанов регуляторов электроконтактов и дросселей;
своевременная замена СОЖ;
регулярная проверка надежности зажима обрабатываемой детали и закрепление инструмента;
поддержание в рабочем состоянии стружкоотводящих и загрузочно-разгрузочных устройств;
тщательная уборка рабочих мест и защита от коррозии.
Ремонт следует производить агрегатным методом. При замене использовать групповую систему.
Условия для нормальной работы:
колебание напряжения: ±5% Vн;
давление сжатого воздуха не менее 4 кгссм;
сжатый воздух должен подаваться сухим и чистым;
давление масла в гидросистеме - 10 МПа;
температура СОЖ 16° - 18° С;
заготовки должны соответствовать ТУ;
режущий инструмент должен соответствовать рассчитанной стойкости.
8. Организация технического контроля
Периодический входной контроль осуществляется на рабочем месте оператором после обработки на каждой позиции. Периодический операционный контроль осуществляет контролер ОТК.
Контролер ОТК производит окончательный контроль качества изготовления детали перед отправкой в сборочный цех. Контрольные автоматы установлены после основных ответственных чистовых операции.
Глава 4. РАСЧЕТНО-ЭКОНОМИЧЕСКАЯ ЧАСТЬ
В экономической части дипломного проекта определяем единовременные и текущие затраты необходимые для осуществления проекта обеспечения автоматизированной линией продукции требуемого качества и количества; технико-экономические показатели проектируемого участка; условия и сроки окупаемости затрат. На этой основе необходимо сделать окончательные выводы о целесообразности разработки проекта и его эффективности.
В качестве единовременных затрат рассчитываем предпроизводственные затраты капитальные вложения и основные фонды а также затраты на создание необходимого запаса оборотных средств.
1. Расчет величины капитальных вложений
Для определения эффективности вложения средств объемы капитальных вложений рассчитываем вне зависимости от источников финансирования.
В нашем случае в состав капитальных вложений включаются:
)затраты на научно-исследовательские проектно-изыскательские опытно – конструкторские работы включая испытание и доработку опытных образцов – Книокр;
)затраты на технологическую подготовку и освоение производства - Ктпп;
)затраты на приобретение стандартного и нестандартного оборудования транспортных средств дорогостоящего инвентаря их установку монтаж наладку демонтаж - Коб;
)стоимость производственных зданий сооружений передаточных устройств и других непосредственно связанных с производством - Кзд.
)затраты на формирования оборотных средств связанные с необходимостью организации по новому проекту цеха.
Таким образом в общем случае величина капитальных вложений по проектируемому варианту будет равна:
К=Книокр + Ктпп + Коб + Кзд +Кос
При расчете отдельных составляющих этой формулы можно воспользоваться рекомендациями изложенными в [9 10].
Капитальные вложения в здания и сооружения производственного и вспомогательного назначения рассчитываем исходя из стоимости 1 м3. Общий объем здания рассчитан исходя из предложенной планировки участка.
Он определен по формуле:
где F - площадь здания м2;
h - высота пролетов м.
Из [14 с.174] высота пролетов при наличии крана - 125 м. Т.к. линия занимает 1 пролет по 24 м длиной и 72 м шириной то
Стоимость 1 м3 при укрупненных расчетах берем 67 руб.
Капитальные вложения во вспомогательные сооружения рассчитаем исходя из необходимости нормального жизнеобеспечения рабочих.
Из [15 с.40] на одного работающего приходится 7 м2 при высоте помещения 28 м. Затраты на 1 м3 бытовых сооружений 204 руб. Тогда затраты на сооружение бытовых помещений составят:
Но в связи с тем что на базовом заводе простаивают цеха производств то вышеуказанные затраты на строительство новых цехов целесообразно не учитывать.
Капитальные вложения в оборудование рассчитываются по формуле:
Коб= Кот + Коэ + Копт +Коу
где Кот – капитальные вложения в технологическое оборудование руб.;
Коэ – капитальные вложения в энергетическое оборудование руб.;
Коу – капитальные вложения в средства контроля и управления руб.;
Копт – капитальные вложения в подъемно – транспортное оборудование руб.
Капитальные вложения в технологическое оборудование определяются по формуле:
где Цот – оптовая (рыночная) цена оборудования руб.ед.
Ктз – коэффициент транспортно-заготовительных расходов Ктз=01;
Кс – коэффициент учитывающий затраты на строительные работы в том числе устройство фундамента (в нашем случае не учитывается);
Км – коэффициент учитывающий затраты на монтаж и освоение оборудования Км= 015.
Капитальные вложения в энергетическое оборудование определяют из уравнения:
Капитальные вложения в подъемно – транспортное оборудование укрупнено принимаются равными:
Капитальные вложения в средства контроля и управления технологическим процессом не рассчитываются так как эти средства входят в состав технологического оборудования Коу=0.
Таким образом капитальные вложения в оборудование:
Капитальные вложения в здания и сооружения производственного и вспомогательного назначения не учитываем.
Капитальные вложения в оснастку в нашем случае складываются из стоимости режущего инструмента и приспособлений за основу взяты данные по аналогичной оснастки базового предприятия.
Капиталовложения на НИР будущих периодов примем укрупнено 2% от Коб.
Таким образом общая сумма капитальных вложений:
2. Расчет себестоимости продукции
2.1 Расчет прямых затрат на производство
Под прямыми затратами понимаются расходы которые могут быть непосредственно отнесены на единицу продукции. В состав прямых затрат на производство входят:
Материальные затраты в том числе:
а) стоимость основных материалов (за вычетом возвратных отходов) а также стоимость вспомогательных материалов которые используются для обеспечения нормального технологического процесса;
б) стоимость изделий общепромышленного назначения (арматура метизы и др.).
Покупные комплектующие изделия полуфабрикаты услуги кооперативных предприятий;
Топливо и энергия на технологические цели;
Основная заработная плата производственных рабочих;
Дополнительная заработная плата производственных рабочих;
Отчисления на социальные нужды из заработной платы производственных рабочих;
Расходы на подготовку и освоение производства;
Износ инструментов и приспособлений целевого назначения и прочие специальные расходы.
Затраты на основные материалы рассчитываем по формуле:
где Цм – действительная оптовая цена весовой единицы материала руб.кг Цм=57;
N – годовой выпуск деталей шт.год N=20000;
qм – норма расхода материала на одно изделие кг qм=478;
Ктз – коэффициент транспортно – заготовительных расходов ориентировочно Ктз=104;
qо – реализуемые отходы данного материала на изделие кг qо=106;
Цо – цена весовой единицы отходов руб.кг Цо=2672
Стоимость вспомогательных материалов которые используются для обеспечения нормального технологического процесса устанавливаются по нормам расхода действующим на базовом предприятии.
Затраты на топливо и энергию для технологических целей включают стоимость всех видов топлива и энергии непосредственно расходуемых в процессе производства продукции (как получаемых со стороны так и вырабатываемых самим предприятиям). К таким расходам в частности относятся расходы на:
а) топливо и энергию расходуемые на проведение испытаний изделий;
б) пар горячую и холодную воду расходуемые цехом для технологических нужд.
Затраты на эти статьи определяются умножением тарифа по каждому виду энергоресурсов на его норму расхода на единицу продукции и годовую программу выпуска.
Затраты на топливо и энергию для отопления и освещения помещений и хозяйственных различных нужд отражаются в таких косвенных комплексных статьях расходов а затраты на эл. энергию для привода в действии рабочих машин и оборудования – в расходах по содержанию и эксплуатации оборудования.
Затраты на вспомогательные материалы.
Из вспомогательных материалов на технические нужды используется сода кальцинированная и вода для мойки изделий.
На одну деталь расходуется 06кг соды и 94л воды.
Стоимость 1кг соды по данным базового предприятия 7 руб.кг техническая вода 228 руб. за 1000 м3 т.е. 1л=10-3 м3.
Тарифы на топливо эл. энергию сжатый воздух воду взяты на предприятии в бухгалтерии цеха.
эл. энергия – 025 руб. за 1кВтчас;
сж. воздух низкого давления – 38 руб. за 1000 м3;
вода техническая – 228 руб. за 1000 м3;
вода сточная – 2219 руб. за 1000 м3;
пар – 7054 руб. за 1000 м3;
Зная эти значения заполним таблицу 5 (по форме 4.1.)
Форма 4.1. Ведомость затрат на основные и вспомогательные материалы используемые для технологических целей
Наименование и марка материального ресурса
Действующая оптовая (рыночная) цена за единицу руб.
Расход по норме в натуральных единицах
Затраты по действующим оптовым ценам руб.
На программу выпуска
Отливка из сплава АЛ9
Основная заработная плата выплачивается производственным рабочим за работу выполняемую непосредственно по изготовлению продукции а также и ИТР когда в современных условиях производства они непосредственно (на рабочих местах) участвуют в изготовлении продукции.
Основная заработная плата производственных рабочих включает все виды оплаты труда и доплаты за фактически проработанное время.
Основная заработанная плата по данным предприятия
Основные рабочие на повременной оплате (тариф):
оператор ЧПУ (5-й разряд) – 149 руб.час – 5 чел.;
оператор ЭВМ (5-й разряд) – 149 руб.час – 1 чел.;
слесарь (3-й разряд) – 094 руб.час – 2 чел.
Вспомогательные рабочие:
электрик (5-й разряд) – 149 руб.час – 1 чел.;
наладчик (4-й разряд) – 125 руб.час. – 1 чел.
мастер 275 руб.месяц – 1 чел.;
механик 320 руб.месяц – 1 чел.
Расчет основной заработной платы производится по часовым тарифным ставкам.
Дополнительная заработная плата основных рабочих составляет 492% от основной заработной платы (в состав дополнительной заработной платы входит оплата очередного учебного отпуска выслуга лет и др.)
Годовой фонд оплаты труда ИТР устанавливается на основе их расчетной численности и месячных окладов с учетом процента дополнительной заработной платы. Дополнительная заработная плата составляет 23% от основной заработной платы для ИТР.
Тарифный (нормативный) фонд оплаты труда производственных рабочих на повременной оплате труда руб.год:
Фд – действительный годовой фонд рабочего времени чгод;
Рпов – списочная численность основных и вспомогательных рабочих чел;
Кр – коэффициент учитывающий районную надбавку к заработной плате Кр=13.
Отчисления на соц. нужды установлены в размере 39% от основной и дополнительной заработной платы производственных рабочих (в т.ч. 54% - отчисление на социальное страхование; 28% - отчисления в пенсионный фонд; 31% - на медицинское страхование; 2% - в фонд занятости)
Результаты расчетов по зарплате оформим в виде таблицы 6 (по форме 4.2) и таблицы 7 (по форме 4.3).
Форма 4.1. Ведомость фондов заработанной платы рабочих
Тарифный фонд оплаты труда (с учетом районных надбавок) руб.год
Основная зплата руб.год
Доплата по премиальным системам 50% руб.год
Дополнительная ЗП руб.год
Общий фонд оплаты труда руб.год
Форма 4.2. Ведомость фондов оплаты труда ИТР
2.2. Расчет косвенных затрат
Для дальнейших расчетов необходимо составить сводную ведомость оборудования цеха.
Форма 4.3. Расчет стоимости оборудования для ГАУ
Наименование оборудования
Фрезерный с ЧПУ 6Р13РФ3
Косвенные затраты образуют комплексные статьи поэтому для их расчета составляются отдельные сметы в частности смета расходов на содержание и эксплуатацию оборудования и смета цеховых расходов.
Затраты на текущий ремонт оборудования дорогостоящего инструмента и транспортных средств принимаем 3% от стоимости оборудования.
Затраты на износ малоценных и быстроизнашивающихся инструментов и приспособлений принимаем по данным базового предприятия (примерно 4875 руб. в год на один производственный станок).
Затраты на прочие расходы принимаем по нормам действующим на предприятии (примерно 3 % от суммы затрат всех предыдущих статей).
Форма 4.4. Смета расходов на содержание и эксплуатацию оборудования
Амортизация оборудования и транспортных средств
Эксплуатация оборудования (кроме расходов на тек. ремонт)
Текущий ремонт оборудования дорогостоящего инструмента и транспортных средств
Износ малоценных и быстроизнашивающихся инструментов и приспособлений
В смете цеховых расходов статью: "Амортизация зданий сооружений инвентаря" берем с базового предприятия . Смета "Содержание зданий сооружений инвентаря" считается как 10% от 4-ой статьи.
Затраты по охране труда" также берем с базового предприятия.
Форма 4.5. Смета цеховых расходов
ЗП основная и дополнительная ИТР
Отчисления на социальные нужды
Амортизация зданий сооружений инвентаря
Текущий ремонт зданий сооружений инвентаря
Содержание зданий сооружений инвентаря
Затраты по охране труда
Итого цеховые расходы:
2.3. Калькуляция цеховой себестоимости продукции
Все текущие затраты на производство единицы продукции необходимо сгруппировать по калькуляционным статьям (форма 4.7.). В результате получаем возможность сопоставить проектные значения по себестоимости с аналогичными показателями действующих производств. Это позволить судить о преимуществах заложенных в проекте установить отклонения по отдельным статьям калькуляции и выявить дополнительные резервы.
При составлении калькуляции на отдельное изделие величина затрат по каждой статье калькуляции принимается на основании приведенных выше расчетов. Разница лишь в том что при калькулировании себестоимости расчет ведется не на годовую программу а единицу калькулируемой продукции.
Форма 4.7. Калькуляция цеховой себестоимости корпуса редуктора
Материалы (с учетом транспортно - заготовит. расходов)
Возвратные расходы (вычитаются)
Топливо и энергия на технологические нужды
Основная зарплата основных производственных рабочих
Дополнительная зарплата основных производственных рабочих
Возмещение износа инструментов и приспособлений
Расходы на содержание и эксплуатацию оборудования
Итого цеховая себестоимость:
В форме 4.7. статья " Дополнительная зарплата основных производственных рабочих" составляет 53% от статьи "Основная зарплата основных производственных рабочих" а статья "Отчисления на социальные нужды" составляет 30% от суммы этих двух статей (ст. 4 и 5)
Статья "Расходы на содержание и эксплуатацию оборудования" составляет 572% от статьи "Основная зарплата основных производственных рабочих" а статья "Цеховые расходы" – 963% от той же статьи.
Сметная калькуляция на изготовление корпуса
Цеховая себестоимость
Общезаводские расходы
Заводская себестоимость
2.4. Экономическая эффективность проектных решений
Следует рассчитать срок окупаемости капитальных вложений по следующей формуле:
где - сумма капитальных вложений руб.;
- планируемая прибыль.
Планируемая прибыль составляет 20-60% от полной себестоимости программы.
Себестоимость единицы продукции равна – 34270 руб.
Полная себестоимость программы будет равняться:
Планируемая прибыль (берем 40% от ):
Зная все значения можно рассчитать срок окупаемости капитальных вложений:
Срок окупаемости составит: 28 лет.
2.5. Технико-экономические показатели проектируемого цеха
По результатам выполненных расчетов необходимо заполнить форму 4.10. и провести комплексный анализ основных технико-экономических показателей цеха.
Значение показателей
Капитальные вложения
Стоимость основных материалов
Зарплата основным рабочим
Отчисления на соц. нужды
Срок окупаемости затрат
Глава 5. БЕЗОПАСНОСТЬ ПРОЕКТА
Обеспечение здоровых и безопасных условий труда возлагается на администрацию предприятия. Администрация обязана внедрять современные средства техники безопасности предупреждающие травматизм и обеспечивать санитарно-технические условия предотвращающие возникновение профзаболевания.
Производственные здания сооружения оборудование технологический процесс должны отвечать требованиям обеспечивающим здоровые и безопасные условия труда. Объем производственных помещении должен быть таким чтобы на каждого работающего приходилось не менее 15 м3 площади.
Одним из необходимых условий здорового и высокопроизводительного труда является обеспечение чистоты воздуха и нормальных метеорологических условий в рабочих помещениях. Данный технологический процесс механической обработки не сопровождается выбросами больших количеств ядовитых веществ. Имеют место лишь испарения охлаждающей жидкости и масел. Стружка и микро-пыль при резании полностью смываются охлаждающей жидкостью. Исходя из этих условий назначаем смешанную вентиляцию по месту действия: общеобменная по назначению - приточно-вытяжная. Приток воздуха производиться в рабочие зоны а вытяжка из верхней зоны помещения. Механическая вентиляция осуществляется по мере загрязнения.
При нормальном микроклимате и отсутствии вредных веществ или содержании их в пределах норм воздухообмен определяется по формуле:
Метеорологические условия:
температура в цехе – t =18° 20° С;
влажность воздуха в цехе j =30 60 %;
в зимнее время скорость движения воздуха не должна превышать 03-05 мс а летом 05-1 мс Рнорм = 760 мм рт. столба.
Организованная естественная вентиляция осуществляется с помощью дефлекторов (D=100 mm - диаметр дефлектора).
2. Расчет искусственного освещения
Создание благоприятных условий труда исключающих быстрое утомление зрения возникновение несчастных случаев и способствующих повышению производительности труда возможно только при рациональном освещении рабочих мест зон обработки и производственных помещений.
Освещение цеха комбинированное. Искусственное освещение производится от светильников с газоразрядными лампами. Площадь участка высота . Расположение светильников прямоугольное.
Определим расстояние от потолка до рабочей поверхности:
где – высота здания м;
– высота рабочей поверхности.
Определим расстояние от потолка до светильника:
Определим высоту подвеса светильников:
Зная оптимальное соотношение с точки зрения равномерности освещения при прямоугольном расположении светильников:
Определим расстояние между светильниками:
Определим необходимое количество светильников:
где - площадь цеха м2
Показатель помещения определяем по формуле:
где – длина участка;
Коэффициент отражения потолка:
Коэффициент отражения стен:
Зная определим коэффициент полезного действия:
Для расчета общего освещения применяем точечный метод:
где – минимальное нормированное освещение;
S = 1186 м2 – площадь помещения;
z = 1.1 – коэффициент минимального освещения;
K = 1.5 – коэффициент запаса;
N = 9 – число светильников;
h = 053 – коэффициент использования светового потока.
Для освещения используется лампа ЛБ80. Лампы располагаются в три ряда по 3 штуки. На территории участка обязателен источник питьевой воды с темппературой +8 +20 град С. Расход воды на хозяйственно-питевые нужды составляет 25 л на одного человека в смену.
3. Техника безопасности
Основными требованиями предъявленными с точки зрения охраны труда при проектировании машин и механизмов являются: безопасность для здоровья и жизни человека надежность удобство эксплуатации.
Внешние контуры защитных устройств должны вписываться в контуры основного оборудования. Защитные устройства должны решать несколько задач одновременно и конструктивно совмещаются с машинами и агрегатами являясь их составной частью. Корпуса машин должны обеспечивать не только ограждение опасных элементов но и должны способствовать снижению уровня шума и вибрации. Электроприводы должны иметь защитные кожухи. Рабочие зоны на позициях автоматической линии имеют защитные экраны. Все виды технологического оборудования должны быть удобны для осмотра смазки и управления. Необходимо обеспечить возможность быстрого считывания показателей контрольно-измерительных приборов и четкого восприятия сигналов.
Органы управления должны быть надежными и легкодоступными. Часть из них располагается на оборудовании. Используются сигнальные устройства которые предназначены для извещения о ходе ТП о наличии неисправностей и поломок как основного оборудования так и систем вентиляции и пожаробезопасности.
Основными мерами защиты от поражения током являются:
-обеспечение недоступности токоведущих частей находящихся под напряжением для случайного прикосновения;
-защитное разделение сети;
-устранение опасности поражения при появлении напряжения на корпусах кожухах и других частях электрооборудования что достигается применением малых напряжений применением двойной изоляции выравниванием потенциала защитным заземлением занулением защитным отключением применение специальных защитных средств.
Как и все машиностроительные цехи помещение для разрабатываемого участка относится к особо опасным участкам поэтому все вышеуказанные меры электробезопасности должны быть выполнены и проверены с особой тщательностью.
На заводе используется сеть 3-х проводная с заземленной нейтралью
V= 380220 В. Защитное заземление для таких цепей не используется для защиты применяется зануление. Область применения зануления 3-х фазные 4-х проводные сети напряжением до 1000 в. Назначение нулевого провода - создание для тока короткого замыкания цепи с малым сопротивлением чтобы этот ток был достаточным для быстрого срабатывания защиты.
Занулению подлежат корпуса и другие металлические части электрооборудования которые вследствие повреждения могут оказаться под напряжением. Необходимо также заземление нейтрали. В сети с заземленной нейтралью и занулением при случайном замыкании фазы на землю напряжение между зануленньм оборудованием и землей:
где - сопротивление замыкания фазы на землю;
- сопротивление заземления нейтрали;
Для уменьшения опасности при обрыве нулевого провода применяется повторное заземление нейтрали:
Необходимо использовать защитно-отключающие устройства реагирующие на напряжение корпуса относительно земли и на оперативный постоянный ток и защитное покрытие полов рабочих мест.
3.1. Техника безопасности при эксплуатации гибкой автоматизированной линии
Перед началом работы необходимо:
а) осмотреть оборудование и убедиться в визуальной исправности механизмов. Все механизмы должны находиться висходном положении.
б) привести в порядок рабочее место (осмотреть пульт пол решетку).
в) проверить исправность смазочных систем уровень масла и давление в гидросистемах.
г) осмотреть ограждающие устройства.
д) проверить состояние режущего инструмента.
е) проверить систему охлаждения.
ж) проверить систему уборки стружки.
з) произвести пробный пуск проверить автоблокировку и аварийное отключение.
При возникновении ненормального шума стука или рывков необходимо отключить станки и сообщить о неисправности мастеру.
Ремонт узлов систем должен производить слесарь-ремонтник. Во время ремонта системы должны быть отключены от электросети.
Исправление электрооборудования технологической линии должен производить только работник электрослужбы цеха. Не допускается во время работы станка производить какие-либо наладочные работы. Для наладки ГАЛ необходимо остановить.
Необходимо следить за тем чтобы выступающие части на зажимных приспособлениях были всегда в таком положении которое обеспечивало свободный проход приспособлений мимо инструментов закрепленных в головках.
Во время закрепления детали необходимо следить за тем чтобы руки не находились в зоне действия зажимного приспособления.
Ключ от электрошкафа должен находиться только у электрика обслуживающего станок. Электрошкаф всегда должен быть закрыт.
Во время профилактических осмотров и ремонтов вводный выключатель должен находится в положении "Выключено" а предохранители сняты.
Во время работы станков электроаппараты и приборы должны быть закрыты кожухами или крышками.
На рабочих местах предусматривается удаление стружки напором охлаждающей жидкости поэтому должно быть установлено специальное ограждение обеспечивающее безопасность работы. Рабочий должен работать только в защитных очках.
Предусмотренные кожухи ограждения должны находиться на станке и быть в таком положении которое обеспечивало бы безопасность работы на нем.
3.2. Противопожарная безопасность
Помещение для проектируемого участка относится к категории Д по СНиП-М. 2-72.
Эффективной мерой пожаробезопасности является повышение предела огнестойкости: оборудование покрывается специальной краской металлические конструкции облицовываются деревянные конструкции пропитываются антипиренами.
Системы вентиляции должны быть оборудованы огнепреградительными заслонками.
Участок должен быть оборудован системой пожарной сигнализации реагирующей на дым и повышение температуры автоматической системой пожаротушения (водяная) оборудуется пожарный гидрант.
Место отдыха оборудовано индивидуальными средствами пожаротушения.
Противопожарные мероприятия:
а) своевременно убирать рабочие места;
б) обтирочные материалы складывать в металлический ящик а легковоспламеняющиеся предметы хранить в местах предназначенных для этого;
в) после окончания работы выключать все оборудование кроме дежурного освещения;
г) местное противопожарное оборудование должно находиться в исправном состоянии на специальном месте и периодически проверять его состояние;
д) на участке на видном месте должен быть написан телефон пожарной охраны.
По результатам выполнения анализа конструкции корпуса редуктора существующего технологического процесса и масштаба выпуска а также разработок выполненных в дипломном проекте можно сделать следующие выводы:
предложенный для изготовления корпус редуктора технологичен для крупносерийного типа производства;
предложен новый технологический процесс изготовления корпуса редуктора на гибкой автоматизированной линии (ГАЛ) в составе гибкого автоматизированного участка (ГАУ);
выполнен расчет припусков расчеты режимов резания и основного технологического времени для изготовления основных поверхностей;
разработана планировка и описана гибкая автоматизированная линия;
для рабочих мест автоматизированной линии подобрано специальное оборудование;
выполнены основные расчеты ГАУ;
спроектирована специальная расточная оправка;
разработан раздел охраны труда проекта. Предложены мероприятия существенно улучшающие условия труда работающих и охраны окружающей среды;
в организационно-экономической части выполнен анализ себестоимости изготовления изделия по предложенному варианту. Окупаемость затрат на создание гибкого автоматизированного участка - 28 года.
Материалы дипломного проекта могут быть использованы при создании автоматизированного участка на базовом предприятии.
Глава2.doc
1. Описание компоновочной схемы гибкого производственного участка
На участок заготовки поступают в кассетах после чего их устанавливают на приемный стол и подают на автоматический склад-штабелер 1. Из склада заготовки краном штабелером укладываются на выдвижной стол и перемещаются на стол передаточный 11 затем роботом-манипулятором 4 переносятся и устанавливаются в пневматические тиски установленные на вертикально-фрезерном станке 16 где происходит черновая обработка поверхностей заготовки. Далее заготовка с помощью манипулятора 4 снимается со станка и переносится на стол приемный 2 откуда она при помощи крана штабелера переносится на другой передаточный стол находящийся на слесарном участке который совмещен с участком сборки приспособлений. Затем как заготовка поступила на передаточный стол 11 ее с помощью манипулятора 4 переносят на стенд сборки приспособлений оттуда заготовка перемещается на слесарный стол 6 где с помощью слесаря-наладчика происходит снятие заусенец после фрезерования очистка заготовки с помощью щетки и предварительный контроль. После завершения этих операций заготовка переносится на стенд сборки приспособлений. После установки в приспособление и на стол-спутник заготовка при помощи манипулятора 4 таким же образом поступает на станцию загрузки-разгрузки транспортной системы 15. Со станции деталь передается на транспортную рельсовую тележку на которой она также перемещается на стол-накопитель многоцелевого станка 8. После со стола-накопителя заготовка в приспособлении устанавливается в рабочую зону где и происходит основная двухсторонняя (при помощи поворота стола станка) обработка а именно: черновое и чистовое фрезерование поверхностей; черновая и получистовая обработка отверстий; сверление; зенкерование; фрезерование торцов; чистовая обработка посадочных отверстий; нарезание резьб. После завершения обработки деталь выводится из рабочей зоны на стол-накопитель откуда перемещается на транспортную тележку транспортной системы 15. Далее заготовка с помощью тележки поступает на приемный стол 2 участка мойки и сушки.
Двигаясь по U-образному конвейеру 19 происходит мойка в моечной машине 9 и сушка сушильная камера 10. С конвейера деталь поступает на стол передаточный 11 который предает деталь в приспособлении на транспортную тележку и по рельсовой дороге она перемещается на станцию загрузки-разгрузки. Далее с помощью манипулятора 4 происходит перенос детали на стенд сборки приспособлений на котором заменяется приспособление и деталь в том же порядке поступает на транспортную тележку а далее на стол-накопитель станка и в рабочую зону станка где происходит окончательная обработка: сверление отверстий и резьбонарезание в них ранее не доступных для обработки. После деталь выводится из зоны обработки и через стол-накопитель поступает на транспортную тележку с помощью которой перемещается на участок мойки и сушки. Движение по которому было описано выше. Далее деталь в приспособлении с помощью транспортной системы перемещается на участок контроля.
С транспортной тележки деталь поступает на станцию загрузки-разгрузки 3 откуда роботом-манипулятором 18 переносится на стол контрольно измерительной машины 12 где происходит окончательный контроль (при помощи щупов) всех поверхностей их размеров и расположения. После контроля деталь в обратом порядке с помощью манипулятора 18 переносится на станцию загрузки-разгрузки (участка контроля) и далее по транспортной системе 15 станции загрузки-разгрузки 3 и манипулятора 4 перемещается на стенд сборки приспособлений где деталь высвобождается из приспособления и манипулятором 4 переносится на передаточный стол 11 откуда по выдвижному столу (автоматизированного склада 1) а потом с помощью крана штабелера укладывается в ячейки склада.
ГАУ оснащен пультом управления 14 и тремя ЭВМ 13 к нему. У транспортной системы также имеется пульт управления 7 который соединен с пультом 14 для управления ГАУ с одного места. Уборка стружки осуществляется с помощью конвейера 21 расположенным с задней части станков и выводится по траншеям расположенным под станками. Отвод СОЖ осуществляется конвейерами расположенными также в траншеях под станками которые подают СОЖ к люкам через которые поступают в подвальное помещение. Замена инструментальных блоков в станках (для последующей заточки и настройки) осуществляется с помощью портального робота 22 (находящегося на высоте 3 м) который переносит их над станками и кладет на транспортную тележку 17 (находящуюся также на высоте 23 м). Транспортная тележка перемещает блок до другого портального робота 22 который снимает его с тележки и укладывает на передаточный стол 20 участка подготовки инструмента.
2. Расчет и проектирование специального приспособления для обработки детали на обрабатывающем центре
2.1. Техническое задание
Необходимо спроектировать приспособление к горизонтально-обрабатывающем центре для механической обработки корпуса.
Исходные данные: годовой объем выпуска деталей – 20000 шт.; габаритные размеры детали ; материал – алюминиевый сплав АЛ9.
В данном приспособлении производится фрезерование растачивание сверление.
Расчетами установлено что наибольшие силы резания будут действовать при фрезеровании отверстия 40 до 80+003 мм на глубину .
Принятый режим фрезерования данного отверстия: ; ; .
Приспособление должно обеспечивать необходимую точность обработки детали.
2.2. Выбор и обоснование схемы приспособления
Из анализа заготовки видно что для установки ее в приспособлении за базы следует принять поверхности А Б В.
Установочной базой будет являться поверхность А как наибольшая по площади.
В связи с тем что палета совершает сложное планетарное движение и круговое движение привод стационарного энергоносителя использовать невозможно; учитывая что заготовка обрабатывается на автоматической линии и конструкция приспособления не должна быть громоздкой а также должна быть легкой (т.к. перемещение ее происходит по транспортной системе на транспортной тележке) применяем ручное крепление заготовки.
В качестве зажимного устройства используем винтовые зажимы; они просты в использовании дешевы и надежны в работе.
Обрабатываемая заготовка устанавливается в корпус приспособления который представляет собой плиту с фигурным пазам что позволяет производить обработку заготовки с 2–х сторон без переустановки и закрепляется тремя прихватами (2 г-образных и специальный). Один из прихватов изготовлен вместе с центрирующей призмой которая центрирует заготовку относительно оси приспособления что также повышает точность обработки. Крепление к столу-спутнику производиться при помощи 4-х U – образных пазов а центрирование относительно стола происходит при помощи двух пальцев.
Рис. 11. Обозначение баз
2.3. Расчет параметров силового привода
Обрабатываемая деталь находится в равновесии вследствие действия как сил возникающих в процессе обработки так и сил зажима и реакции опор. Основными силами в процессе обработки являются силы резания.
Величина сил зажима рассчитывается исходя из условия равновесии всех перечисленных сил при полном сохранении контакта базовых поверхностей обрабатываемой детали с установочными элементами приспособления и невозможности сдвига в процессе обработки.
Приведем схему для вычисления сил закрепления при фрезеровании отверстия 40 до 80 на глубину .
Составляющая направлена навстречу силе зажима и стремится оторвать заготовку от опор а составляющая стремится сдвинуть заготовку в боковом направлении.
Рис. 12. Расчетная схема
Для данной схемы закрепления необходимая сила зажима таблица 1 [17] равна:
принимать большее из двух значений
где - составляющие силы резания: ; табл. 42 [2];
- коэффициенты трения в местах контакта заготовки с опорами и с зажимным механизмом табл. 3 [17];
- жесткости опор и зажимного механизма: табл. 1 [17];
- коэффициент запаса.
Коэффициент запаса определяется из произведения [17 с.382]:
где - гарантированный коэффициент запаса;
- коэффициент учитывающий увеличение сил резания из-за случайных неровностей;
- коэффициент учитывающий увеличение силы резания вследствие затупления инструмента;
- коэффициент учитывающий увеличение силы резания при прерывистом резании;
- коэффициент характеризующий постоянство силы зажима;
- коэффициент характеризующий эргономику зажимного механизма.
Подставив найденные значения в формулу получим:
Таким образом необходимая сила зажима равна 4890 Н.
Произведем расчет винтовых зажимов. Для этого определим номинальный диаметр резьбы винта по формуле [20]:
где - коэффициент для основной метрической резьбы ;
- потребная сила зажима Н;
- допустимое напряжение растяжения (сжатия) .
Момент закрепления для данного типа винтов находим по формуле [20]:
Зная все значения найдем:
Так как в нашем случае гайки приспособления после установки в его заготовки будем закручивать с помощью гайковерта (машина для закручивания гаек) то дальнейший расчет можно не проводить. Но в случае поломки гайковерта потребуется заворачивать гайки ключом а для этого определим длину рукоятки ключа.
Определим длину рукоятки ключа по заданной силе воздействия из условия равновесия винта:
где - при ручном зажиме.
2.4. Расчет приспособления на точность
Расчет заключается в определении точности изготовления приспособления по принятым параметрам.
На точность обработки влияет ряд технологических факторов вызывающих общую погрешность обработки которая не должна превышать допуск выполняемого размера при обработки заготовки т.е.:
Допустимая погрешность изготовления приспособления равна [21]:
где - допуск выполняемого размера;
- коэффициент учитывающий отклонение рассеяния значений составляющих величин от закона нормального распределения [21];
- коэффициент учитывающий уменьшение предельного значения [21];
- коэффициент учитывающий долю погрешности обработки в суммарной погрешности [21];
- погрешность базирования;
- погрешность закрепления;
- погрешность установки приспособления;
- погрешность износа установочных элементов;
- погрешность смещения инструмента;
- экономическая точность обработки.
Расчетный параметр – размер 58+003
т.к. установочная поверхность совпадает с исходной;
- по табл. 75 [21] для закрепления в приспособлении с винтовыми зажимами на окончательно обработанную поверхность;
- т.к. обеспечен надежный контакт приспособления со столом станка;
- для чистового точения;
- т.к. отсутствуют направляющие элементы для инструмента.
Таким образом допустимое отклонение перпендикулярности установочной поверхности относительно опорной не более 002 мм
Полученная величина погрешности установки не превышает величины допустимого отклонения следовательно приспособление обеспечивает необходимую точность обработки.
3. Проектирование специального режущего инструмента
Операции обработки внутренних отверстий в двух стенках и подрезание торца находящегося на одной оси с отверстиями позволяют объединить их в одну если использовать специальную расточную оправку. Тем самым мы значительно уменьшаем количество инструмента и сокращаем время обработки и переустановки а также увеличиваем точность обработки.
Расточная оправка (смотри чертеж) состоит из корпуса в котором с помощью крепежных устройств установлены два расточных блока для одновременной обработки отверстий в двух стенках и подрезания торца заготовки. Вылет режущих пластин расточного блока регулируется в размер с помощью регулирующих кулачков. Расположение их с разных сторон (180°) позволяет уменьшить радиальное биение. Для растачивания глубоких отверстий или отверстий находящихся в глубине заготовки корпус оснащен удлинителем который может быть взаимозаменен в зависимости от глубины отверстия. Удлинитель крепится с одной стороны к унифицированному хвостовику при помощи цилиндрического наружного базирующего диаметра с базирующем торцом и резьбовым хвостовиком а с другой стороны – идентичным узлом с внутренним диаметром к корпусу. Конструкция корпуса расточной оправки обеспечивает необходимую прочность и точность закрепления резцов. Расточная оправка может применяться как для чистовой так и для получистовой обработки внутренних поверхностей.
Рассчитаем диметры крепежных болтов которыми расточные блоки крепятся к корпусу оправки:
– максимально допустимое напряжение сдвига.
Значит из номинального ряда принимает болты диаметром 5 мм.
Проверим стенки отверстий скрепленных болтом на смятие. Напряжение смятия в стенках отверстий будет:
где – толщина крепежной поверхности;
d - диаметр отверстия.
Значит толщина крепежной поверхности достаточна для надежного и точного закрепления блоков в корпусе оправки.
Содержание.doc
1. Исходные данные11
2. Анализ исходных данных11
3. Оценка технологичности детали12
4. Определение типа производства14
5. Выбор заготовки15
6. Анализ существующего технологического процесса17
7. Обоснование выбора технологических баз18
8. Разработка технологического процесса механической
8.1. Установление последовательности обработки основных
поверхностей и обоснование необходимого количества
8.2. Разработка маршрута и формирование операций24
8.3. Расчет припусков на механическую обработку26
8.4. Расчет режимов резания37
8.5. Техническое нормирование43
8.6. Выбор и расчет оборудования47
Глава 2. КОНСТРУКТОРСКАЯ ЧАСТЬ
1. Описание компоновочной схемы гибкого производственного участка50
2. Расчет и проектирование специального приспособления для
обработки детали на обрабатывающем центре52
2.1. Техническое задание52
2.2. Выбор и обоснование схемы приспособления52
2.3. Расчет параметров силового привода53
2.4. Расчет приспособления на точность56
3. Проектирование специального режущего инструмента58
Глава 3. ОРГАНИЗАЦИОННАЯ ЧАСТЬ
2. Оборудование рабочие места и инвентарь61
3. Компоновка и планировка участка61
4. Определение размера площади участка63
6. Организация рабочих мест64
7. Управление гибким производственным участком64
8. Организация технического контроля66
Глава 4. РАСЧЕТНО-ЭКОНОМИЧЕСКАЯ ЧАСТЬ
1. Расчет величины капитальных вложений67
2. Расчет себестоимости продукции70
2.1. Расчет прямых затрат на производство70
2.2. Расчет косвенных затрат75
2.3. Калькуляция цеховой себестоимости продукции77
2.4. Экономическая эффективность проектных решений78
2.5. Технико-экономические показатели проектируемого
Глава 5. БЕЗОПАСНОСТЬ ПРОЕКТА
2. Расчет искусственного освещения81
3. Техника безопасности83
3.1. Техника безопасности при эксплуатации гибкой
автоматизированной линии85
3.2. Противопожарная безопасность86
СПИСОК ИСПОЛЬЗОВАННОЙ ЛИТЕРАТУРЫ89
Технологический процесс на 56 листах
Спецификации на 3 листах
Литература.doc
Справочник технолога - машиностроителя. В 2-х т. Т. 1 Под ред. А.Г. Косиловой и Р.К. Мещерякова 4-е изд. перераб. и доп. - М.: Машиностроение 1985г. - 656с.
Справочник технолога - машиностроителя. В 2-х т. Т. 2 Под ред. А.Г. Косиловой и Р.К. Мещерякова 4-е изд. перераб. и доп. - М.: Машиностроение 1985. - 496с.
Балакшин Б.С. Основы технологии машиностроения. – М.: Машиностроение 1960. – 560с.
Мосталыгин Г.П. Толмачевский Н.Н. Технология машиностроения: Учебник для вузов по инженерно-экономическим специальностям - М.: Машиностроение 1990. - 288с.
Справочник технолога по автоматическим линиям А.Г. Косилова А.Г. Лыков О.В. Деев и др.; Под ред. А.Г. Косиловой. - М.: Машиностроение 1982. - 288с.
Косилова А.Г. Мещеряков Р.К. Калинин М.А. Точность обработки заготовки и припуски в машиностроении. М.: Машиностроение 1976. - 288с.
Общемашиностроительные нормативы режимов резания: Справочник: В 2-х т.: Т.1 А.Д. Локтев Ч.Ф. Гущин Б.Н. Балашов и др. - М.: Машиностроение 1991. - 304с.
Режимы резания металлов Под. ред. Ю.В. Барановского. - М.: Машиностроение 1972. - 407с.
Курсовое проектирование по технологии машиностроения: Учеб. пособие для машиностроительных вузов А.В. Худобин В.Ф. Гурьянихин В.Р. Берзин. - М.: Машиностроение 1989. - 288с.
Сборник задач и упражнений по технологии машиностроения: Учеб. пособие для машиностроит. вузов по спец. “Технология машиностроения” “Металлорежущие станки и инструменты” В.И. Аверченков О.А. Горленко В.Б. Ильицкий и др.; Под общ. ред. О.А. Горленко. - М.: Машиностроение 1988. - 192с.
Автоматические линии в машиностроении: Справочник. В 3-х т. Ред. совет: А.И. Дащенко и др. - М.: Машиностроение 1984. - Т.2. Станочные автоматические линии Под ред. А.И. Дащенко 1984. - 408с.
Экономика и организация производства в дипломных проектах: Учебное пособие для машиностроительных вузов. К.М. Великанов Э.Г. Васильева В.Ф. Власов и др.; Под общей редакцией К.М. Великанова. - 4-е изд. перераб. и доп. - Л.: Машиностроение. Ленингр. отделение 1986. - 285 с.
Проектирование механосборочного цеха. Методические пособие по выполнению организационно - экономических расчетов в дипломных проектах технологического характера Сост. А.К. Микоян Е.Л. Петрашова
Справочник инструментальщика И.А. Ординарцев и др. – Л.: Машиностроение. Ленингр. отд-ние 1987. – 846с.
Станочные приспособления: Справочник. В 2-х т. Ред. совет: Б.Н. Вардашкин и др. – М.: Машиностроение 1984 – Т. 2 Под ред. Б.Н. Вардашкина В.В. Данилевского. 1984. – 656с.
Егоров М.Е. Основы проектирования машиностроительных заводов. Изд. 6-е перераб. и доп. Учебник для машиностроит. вузов. М.: Высш. школа 1969. – 480с.
Роботизированные технологические комплексы и гибкие производственные системы в машиностроении: Альбом схем и чертежей: Учеб. пособие для вузов Ю.М. Соломенцев К.П. Жуков Ю.А. Павлов и др.; Под. общ. ред. Ю.М. Соломенцева. – М.: Машиностроение 1989. – 192с.
Горохов В.А. Проектирование и расчет приспособлений: Учеб. пособие – Мн.: Высш. школа 1986. – 283с.
Антонюк В.Е. Конструктору станочных приспособлений: Справочное пособие. – Мн: Беларусь 1991. – 400с.
Горбацевич А.Ф. Шкред В.А. Курсовое проектирование по технологии машиностроения. – Минск: Высш. школа 1983. – 298с.
Карта Т.Т. иТ.Б..doc
Обозначение документа
*Размеры для справок
Отливка II группы по ОСТ4ГО.021192
Предельные отклонения литейных размеров Л8 ОСТ4ГО.010.025
Неуказанные литейные радиусы 5мм
Неуказанные литейные уклоны по ГОСТ 3212-57
Предельные отклонения угла между базовыми отверстиями Е Ж З К Л и любыми другими ±25'
Предельные отклонения угла между базовыми отверстиями и любыми другими ±20'
Предельные отклонения размеров между базовыми отверстиями И М и любым другим ±008; Н и любым
Остальные технические требования по ОСТ4ГО.070.014
Карта безопасности.doc
Обозначение документа
При изготовлении детали соблюдать правила по технике безопасности
предусмотренными инструкциями:
По мойке и упаковке
По пожарной безопасности
Детали транспортировать в кассете хранение в штабелере
ТЕХ.ПРОЦЕСС.doc
на _механическую обработку корпуса__
Руководитель проекта .
Процесс внедрения в производство
Обработка деталей на металлорежущих станках
Отливка II гр. по ОСТ 4 ГО 021.192 сплав АЛ9 ГОСТ 2685-75
Код. Наименование операции
Обозначение документа
Код. Наименование оборудования
ХХХХ Транспортировочная
ХХХХХХ.ХХХХ Кран – штабелер СА-100 Манипулятор ПР-4
ХХХХХХ.ХХХХ Верстак слесарный СМ520
Наименование детали сборочной единицы или материала
ХХХХХХ.ХХХХ Щуп кл. 1-2
ХХХХХХ.ХХХХ Транспортная система ТС-500
ХХХХ Сверлильно-фрезерно-расточная 60046.ХХХХХ ИОТ ХХХ
0019.ХХХХ ИР500ПМ1Ф4
ХХХХ Транспортировочная 60004ХХХХХ ИОТ ХХХ
ХХХХХХ.ХХХХ Моечная машина ММ-5
ХХХХХХ.ХХХХ Сушильная камера КС-10
4300.ХХХХ Измерительная машина ИМС-850
Наименование операции
Сплав АЛ9 ГОСТ 2685-75
Обозначение программы
Фрезерный с ЧПУ 6Р13РФ3
6131.ХХХХ – тиски пневматические
Фрезеровать поверхность 1 предварительно
1830.ХХХХ – фреза торцевая 200 1830-1831 ГОСТ 24360-80
Фрезеровать поверхность 1 окончательно
Б Переустановить заготовку
Фрезеровать поверхность 2 предварительно
Фрезеровать поверхность 3 предварительно
Фрезеровать поверхность 2 окончательно
Фрезеровать поверхность 3 окончательно
1820.ХХХХ – фреза концевая 60 1820-1822 ГОСТ 17026-71
1820.ХХХХ – фреза концевая 5 1820-1822 ГОСТ 17026-71
2871.ХХХХ – тиски слесарные
Снять заусенцы после фрезерования
2900.ХХХХ – напильник плоский тупоносый 200 №1 ГОСТ 1465-80 ХХХХХХ.ХХХХ – шабер трехгранный R1H477 – 60
Б Снять заготовку уложить в тару
Проконтролировать размеры: 272-01; 19±06; 84-022; 110±04; 77-01; 10-036; 40±06; 5±03; 4±015; R12±20; 152+10; 166+16
3311.ХХХХ – ШЦ – 1 – 400 – 01 ГОСТ 166-80; 394300.ХХХХ – Набор щупов кл. 1-2 ГОСТ 882-75
Проконтролировать шероховатость: Ra=16; Ra=10
4230.ХХХХ – Индикатор И40-2 кл.1 ГОСТ 577-75
Сверлильно-фрезерно-расточная
6181.ХХХХ – приспособление специальное №2
Фрезеровать поверхность 6 предварительно
1820.ХХХХ – фреза концевая 30 1820-1822 ГОСТ 17026-71 392801.ХХХХ – втулка 191836-042
Фрезеровать поверхность 7 предварительно
Фрезеровать поверхность 6 окончательно
1820.ХХХХ – фреза концевая 30 1820-1822 ГОСТ 17026-71 392801.ХХХХ – оправка с конусом 7:24
Фрезеровать поверхность 7окончательно
Расточить отверстие 8 в двух стенках с подрезкой торца 9 предварительно
2190.ХХХХ – резец 2190-2197 ГОСТ 9795-84 392801.ХХХХ – оправка 191421-334
Расточить отверстие 10 11 с подрезкой торца 12 предварительно
ХХХХХХ.ХХХХ – оправка 2190-2198 специальная
Расточить отверстие 8 и 9 предварительно
ХХХХХХ.ХХХХ – оправка расточная 191421-354
Расточить отверстие 10 и 11 предварительно
Расточить отверстие 13 однократно
ХХХХХХ.ХХХХ – оправка 2190-2198 специальная 392801.ХХХХ – державка переходная
Сверлить отверстие 14
1290.ХХХХ – сверло 19 1290-1293 ГОСТ 10903-77 392801.ХХХХ – патрон 191111-019
Сверлить 3 отверстия 16+043
1290.ХХХХ – сверло 16 1290-1293 ГОСТ 10902-77 392801.ХХХХ – втулка переходная 191836-032
Сверлить 11 отверстий 67+017
1290.ХХХХ – сверло 67 1290-1293 ГОСТ 10902-77 392801.ХХХХ – втулка переходная 191836-032
Сверлить 4 отверстия 84+017
1290.ХХХХ – сверло 84 1290-1293 ГОСТ 10902-77 392801.ХХХХ – втулка переходная 191836-032
Фрезеровать торец 15
1820.ХХХХ – фреза концевая 16 1820-1822 ГОСТ 17026-71 392801.ХХХХ – втулка 191836-032
Сверлить отверстие 17
1290.ХХХХ – сверло 265 1290-1293 ГОСТ 10903-77 392801.ХХХХ – втулка переходная 191836-046
Зенкеровать отверстие 17 и 18
1690.ХХХХ – зенкер 27 1690-1691 ГОСТ 21581-76 392801.ХХХХ – втулка переходная 191836-046
Зенкеровать уступ 19
1690.ХХХХ – зенкер 26 1690-1691 ГОСТ 21581-76 392801.ХХХХ – втулка переходная 191836-046
Расточить отверстие 17 и 18 предварительно
Расточить отверстие 17 и 18 окончательно
Сверлить 8 отверстий 67+017
Сверлить 14 отверстий 25+006
1290.ХХХХ – сверло 25 1290-1293 ГОСТ 10902-77 392801.ХХХХ – втулка переходная 191836-032
Расточить отверстие 20 предварительно
Расточить отверстие 21 однократно
Расточить отверстие 20 окончательно
Снять фаску 03х45 в отверстиях 20 21 10 17
Расточить отверстие 8 с подрезкой торца 9 окончательно
ХХХХХХ.ХХХХ – оправка Т20.11.00.00.000РИ
Расточить отверстие 10 11 с подрезкой торца 12 окончательно
Снять фаску 03х45 в отверстиях 10 11 12
Снять фаску 03х45 в отверстии 15
1830.ХХХХ – фреза 94 1840-1842 специальная 392801.ХХХХ – оправка
Нарезать резьбу М10 в 4 отверстиях
1391ХХХХ – метчик М10-7Н 1390-1391 ГОСТ 3266-81 патрон 191221-130
Нарезать резьбу М8 в 11 отверстиях
1391ХХХХ – метчик М8-7Н 1390-1391 ГОСТ 3266-81 патрон 191221-130
Нарезать резьбу М3 в 4 отверстиях
1391ХХХХ – метчик М3-7Н 1390-1391 ГОСТ 3266-81 патрон 191221-130
Сверлить 6 отверстий 33+0075
1290.ХХХХ – сверло 33 1290-1293 ГОСТ 10903-77 392801.ХХХХ – втулка переходная 191836-032
Нарезать резьбу М4 в 6 отверстиях
1391ХХХХ – метчик М4-7Н 1390-1391 ГОСТ 3266-81 патрон 191221-130
Сверлить 10 отверстий 25+006
1290.ХХХХ – сверло 25 1290-1293 ГОСТ 10903-77 392801.ХХХХ – втулка переходная 191836-032
Нарезать резьбу М3 в 10 отверстиях
Провести полный контроль детали в соответствии с базовым чертежом
4300.ХХХХ – Набор щупов кл. 1-2 ГОСТ 882-75
ЗКОНОМИКА.dwg

Капитальные вложения
Отчисления на социальные нужды
Зарплата основным рабочим
Стоимость основных материалов
Себестоимость продукции
Расходы на содержание и эксплуо-
Срок окупаемости затрат
К. Н.2.dwg

Фреза ø5 1820-1822 ГОСТ 17026-71
Оправка 2190-2198 специальная
Резец 2190-2197 ГОСТ 9795-84
Операция 010. Сверлильно-фрезерно-расточная
Станок ОЦ ИР500ПМ1Ф4
Станок фрезерный-консольный 6Р13РФ3
Операция 010. Фрезерная
К. Н.4.dwg

1290-1293 ГОСТ 10902-77
Операция 010. Сверлильно-фрезерно-расточная
Станок ОЦ ИР500ПМ1Ф4
Зенкер ø26 1690-1691 ГОСТ 21581-76
К. Н.3.dwg

Станок ОЦ ИР500ПМ1Ф4
Сверло ø19 1290-1293 ГОСТ 10903-77
Оправка 2190-2198 специальная
1290-1293 ГОСТ 10902-77
Сверло ø16 1290-1293 ГОСТ 10902-77
Фреза ø30 1820-1822 ГОСТ 17026-71
Фреза ø16 1820-1822 ГОСТ 17026-71
Зенкер ø27 1690-1691 ГОСТ 21581-76
1290-1293 ГОСТ 10903-77
ПР1.dwg

относительно установочных элементов
Обеспечить свободное перемещение деталей 3; 11
*Размеры для справок
Допуск перпендикулярности поверхности А отно-
План1.dwg

Условные обозначения:
План первого этажа на отметке 0.000
транспортной системы
Машина измерительная
Транспортная система
Тележка транспортная
Система стружкоуборки
К. Н.5.dwg

Оправка 2190-2198 специальная
Операция 010. Сверлильно-фрезерно-расточная
Станок ОЦ ИР500ПМ1Ф4
Оправка Т20.11.00.00.000РИ
Метчик М10-7Н 1390-1391 ГОСТ 3266-81
Метчик М8-7Н 1390-1391 ГОСТ 3266-81
К. Н.1.dwg

Операция 010. Фрезерная
Фреза ø200 1830-1831 ГОСТ 24360-80
Фреза ø60 1820-1822 ГОСТ 17026-71
Специф. РИ.dwg

КОРПУС.dwg

Предельные отклонения литейных рамеров Л8
М и любым другим ; Н и лю-
верстиями и любыми другими
Неуказанные литейные радиусы 5мм
Неуказанные литейные уклоны по ГОСТ 3212-57
Предельные отклонения угла между базовыми от-
Предельные отклонения размеров между базовыми
Покрытие: наружных поверхностей эмаль ХВ-518
Остальные технические требования по
кроме поверхностей П
верстий; внутренних - эмаль ПФ-115
*Размеры для справок
Отливка II группы по ОСТ4ГО.021.192
К. Н.6.dwg

Станок ОЦ ИР500ПМ1Ф4
Операция 015. Сверлильно-фрезерно-расточная
1290-1293 ГОСТ 10903-77
Метчик М8-7Н 1390-1391 ГОСТ 3266-81
Метчик М3-7Н 1390-1391 ГОСТ 3266-81
Метчик М4-7Н 1390-1391 ГОСТ 3266-81
Специф. ПР1.dwg

ЗАГОТОВКА1.dwg

Предельные отклонения литейных
размеров Л8 ОСТ4ГО.010.025
Неуказанные литейные радиусы 5мм
Неуказанные литейные уклоны по ГОСТ 3212-57
Сплав АЛ9 ГОСТ 2685-75
Неуказанные литейные уклоны по
ИНСТРУМ..dwg

Диапазон регулирования размеров
Погрешность настройки размеров по кольцу
Износ по задней грани режущей кромки не должен
Погрешность настройки размеров по кольцу не
Остальные Т.Т. по СТП 207-5.336-89
Специф.2 ПР1.dwg

Классификатор.dwg

Рекомендуемые чертежи
- 24.01.2023
- 24.01.2023
- 29.07.2014
Свободное скачивание на сегодня
Другие проекты
- 25.01.2023
- 09.06.2022