Проектирование ленточного конвейера для железной руды с производительностью 360 т/ч.




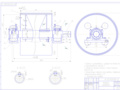
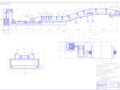
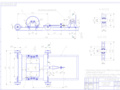
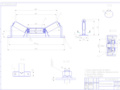
- Добавлен: 25.10.2022
- Размер: 2 MB
- Закачек: 1
Описание
Состав проекта
![]() |
![]() ![]() |
![]() ![]() |
![]() |
![]() |
![]() |
![]() ![]() |
![]() ![]() ![]() ![]() |
![]() ![]() ![]() ![]() |
![]() ![]() |
![]() ![]() ![]() ![]() |
![]() ![]() ![]() ![]() |
![]() ![]() |
![]() ![]() ![]() ![]() |
![]() ![]() |
![]() ![]() ![]() ![]() |
![]() ![]() |
![]() ![]() |
![]() ![]() |
![]() ![]() ![]() ![]() |
![]() ![]() ![]() ![]() |
![]() ![]() ![]() ![]() |
![]() ![]() ![]() ![]() |
![]() ![]() |
![]() ![]() ![]() ![]() |
![]() ![]() |
![]() ![]() |
![]() ![]() ![]() ![]() |
![]() ![]() ![]() |
![]() |
![]() |
![]() |
Дополнительная информация
Приводной барабан, Св.dwg

Приводной барабан спе, Св.dwg

нат устр спец, Св.dwg

Стандартные изделия
Гайка М16-6H.5 (S24)
Гайка М12-6H.5 (S28)
Конвейер ленточный.dwg

Рама натяжного устройства
Устройство разгрузочное
Роликоопора холостой ветви
Барабан отклоняющийся
Устройство загрузочное
Электродвигатель 4А100L4У3
нат устр спец2, Св.dwg

Роликоопора СПЕЦ, СВ.dwg

Болт М16 ГОСТ 7808-82
Гайка М16 ГОСТ 5915-82
Шайба 16 ГОСТ 6402-82
Подшипник 1000812 ГОСТ 8338-82
Шайба 16 ГОСТ 11371-82
Приводной барабан2 спец, Св.dwg

ВАЛ, Св.dwg

Острые кромки притупить
Неуказанные предельные отклоненияН14;IT2
Неуказанные скругления R=2мм
Сталь 45 ГОСТ 1050-88
НАТЯЖНОЕ УСТРОЙСТВО, Св.dwg

Допустимый прекос осей отверстий корпусов
подшипников не более 3
В узлы подшипников заложить смазку-литол-24
Усилие затяжки болтов не более 25 Нм
Лист 1, Св12.dwg

Транспортируемый груз руда железная
Тип ленты резино-тканевая
Скорость транспортирования
Угол наклона конвейера
Длина горизонтального участка
электродвигатель 4А160М6У3
редуктор 2Ц3-200Н 63
муфта МУВП №1 Нм 500
БАРАБАН2, Св.dwg

и законтрогаить гайкой 5
Зазор по ширине шпонки и паза ступицы
Допустимый перекос осей рабочих поверхностей
подшипников не более 2-3
*размеры для справок
РОЛИКООПОРА, Св.dwg

После сборки проверить вращение ролика
на отсутствие заеданий
*Размеры для справок
МОЕ МНТэшко!!! (Восстановлен).docx
Ленточные конвейеры обычно составляют из отдельных секций. Трасса конвейера в горизонтальной плоскости прямолинейная а в вертикальной может быть наклонной или иметь более сложную конфигурацию. Тяговый и грузонесущий орган — лента которая движется по стационарным роликоопорам огибая приводной натяжной а иногда и отклоняющие барабаны. Груз перемещается на ленте вместе с ней. В зависимости от типа роликоопор лента имеет плоскую или желобчатую форму. Конвейер ленточный с плоской лентой используется преимущественно для перемещения штучных грузов. Необходимое натяжение ленты обеспечивает натяжная станция обычно грузовая а в передвижных конвейерах — винтовая. Привод (приводная станция) состоит из электродвигателя редуктора барабана и соединительных муфт. Загрузку сыпучего груза на ленту производят через направляющий лоток или воронку а разгрузку — через концевой барабан или при помощи плужкового или барабанного сбрасывателя.
Существенным преимуществом ленточных конвейеров является значительная производительность которая при больших скоростях движения (6 8 мс) и ширине ленты может быть доведена до 20 000 и даже до 30 000 тч что во много раз превышает производительность других конвейеров. Ленточные конвейеры могут иметь сложные трассы с горизонтальными и наклонными участками а также с изгибами в горизонтальной плоскости. Длина горизонтальных конвейеров может составлять 3 5 км для одной машины (става) а в отдельных случаях достигает 14 км. Благодаря простоте конструкции и эксплуатации удобству контроля за работой и автоматизации управления ленточные конвейеры имеют высокую надежность даже при работе в тяжелых условиях 70 % всех ленточных конвейеров представляют собой установки с приводом мощностью до 400 кВт и длиной до 500 м. У конвейеров большой длины и высокой производительности общая мощность приводных двигателей достигает 10 000 кВт. К недостаткам ленточных конвейеров относится высокая стоимость ленты и роликов составляющая соответственно около 50 и 30 % общей стоимости конвейера. Следует отметить что использование этих конвейеров затруднено при транспортировании пылевидных горячих и тяжелых штучных грузов а также при углах наклона трассы превышающих 18 20°. Затраты на перемещение грузов ленточными конвейерами на расстояние 5 30 км невелики несущественно меньше чем затраты на перемещение грузов автомобильным транспортом. Во многокилометровых линиях представляющих собой последовательно установленные друг за другом ленточные конвейеры большое значение имеет сокращение их числа.
Как показывают экономические расчеты замена четырех одинаковых конвейеров длиной по 500 м на один длиной 2000 м заметно снижает удельные затраты на транспортирование 1 т груза на расстояние в 1 км.
Рис. 1. Схемы трасс ленточных конвейеров: а — горизонтальный; б — наклонного с уклонам вверх; в— наклонного с уклоном вниз ; г — горизонтально-наклонного; д — наклонно-горизонтального; е— горизонтально – наклонно - горизонтального; ж — сложного с несколькими разноименными перегибами.
Ленточные конвейеры классифицируют по следующим признакам:
по области применения — на конвейеры общего назначения специальные (для погрузочных машин транспортирования людей передвижные катучие) и подземные; по форме трассы — на простые с одним прямолинейным участков (рис. 1 а—в) и сложные с ломаной трассой состоящие из горизонтальных и наклонных участков (рис. 1 г—ж) соединенных перегибами а также криволинейные изгибающиеся в плоскости ленты (пространственные);
по направлению движения груза — на подъемные с уклоном вверх (рис. 1б) и спускные с уклоном вниз (бремсберговые; рис.1 в);
по форме ленты н размещению груза на ней — на конвейеры с плоской и желобчатой лентой с верхней (основной тип) н нижней или с обеими несущими ветвями; по типу тягового элемента — на конвейеры с резинотканевой резинотросовой стальной и проволочной лентами;
по углу наклона трассы — на горизонтальные полого наклонные крутонаклонные (более 22°) и вертикальные;
по разделению тяговой и несущей функций между элементами — на канатно-ленточные и ленточно-цепные.
Несущим и тяговым элементом ленточного конвейера общего назначения (рис. 1) является бесконечная гибкая лента 9 опирающаяся верхней (рабочей) и нижней (холостой) ветвями на роликовые опоры 6 17 и огибающая на концах конвейера приводной 10 и натяжной 2 барабаны. У коротких конвейеров часто используемых для перемещения штучных грузов рабочая ветвь ленты может скользить по деревянному или металлическому настилу. Движение передается ленте фрикционным способом от приводного барабана. Необходимое первоначальное натяжение сбегающей ветви ленты создается натяжным барабаном при мощи натяжного устройства 1 грузового или винтового типа. Сыпучий груз подается на ленту через загрузочную воронку 3 устанавливаемую обычно в начале конвейера у концевого барабана 2. Разгрузка ленты может быть концевой или промежуточной для чего используют передвижную разгрузочную тележку 7 или стационарные плужковые сбрасыватели. Направление потока сбрасываемого с барабана груза обеспечивается разгрузочной коробкой 8 имеющей одну или две воронки.
Для очистки рабочей стороны ленты от оставшихся частиц устанавливают вращающиеся щетки 11 (капроновые резиновые) или неподвижный скребок. Для многих видов грузов установка очистного устройства совершенно необходима так как прилипшие частицы образуют на роликах трудноудаляемую неровную корку и могут привести к неравномерному их вращению вызывающему ускоренное изнашивание ленты. Хорошо очищает ленту вращающийся барабан с резиновыми спиральными скребками.
Рис. 1. Наклонно-горизонтальный ленточный конвейер
Для сбрасывания случайно попавших на внутреннюю поверхность нижней ветви ленты частиц перед натяжным барабаном рекомендуется устанавливать дополнительный сбрасывающий скребок 16. Очистка ленты после приводного барабана необходима еще и потому что прилипшие частицы осыпаясь от встряхивания на каждой опоре нижней ветви могут образовывать завалы из мелких частиц усложняющие эксплуатацию конвейера.
Для центрирования хода обеих ветвей ленты и исключения ее чрезмерного поперечного смещения применяют различные центрирующие роликовые опоры 5.
Привод ленточного конвейера состоит из барабана электродвигателя 14 редуктора 13 и соединительных муфт 12. На поворотных участках ветвей трассы устанавливают роликовые батареи создающие плавный перегиб ленты или отклоняющие барабаны 4.
Все элементы конвейера монтируют на металлоконструкции 15 прикрепляемой к фундаменту или к опорным частям здания. Металлоконструкцию с приводом и разгрузочной коробкой называют приводной станцией. Часть конструкции с натяжным устройством и загрузочной воронкой составляет натяжную станцию. Между обеими станциями расположена средняя часть конвейера которая выполнена из одинаковых линейных секции. Линейные секции переходные участки приводная и натяжная станции соединены болтами. Как правило для сыпучих грузом применяют многороликовые опоры формирующие желобчатую ленту. Такая форма ленты при одинаковых ширине и скорости позволяет получить более чем двукратное увеличение производительности при исключении просыпи груза.
Двухбарабанные сбрасывающие тележки предназначены для промежуточной разгрузки только сыпучих грузов в стороны от ленты по одному из отводящих патрубков. Стационарные плужковые сбрасыватели можно использовать как для сыпучих так и для штучных грузов. Известны конструкции плужковых сбрасывателей на передвижных тележках.
Широкая конвейеризация составляет одну из характерных черт развитого промышленного производства. Это объясняется тем что внедрение загрузочных и разгрузочных дозировочных счетных и взвешивающих автоматов автоматических очищающих и смазывающих устройств разнообразной контрольной защитной и блокировочной аппаратуры средства автоматического управления невозможно без применения конвейеров как одной из основных машин комплектующих систему автоматизированного производства.
Высокая производительность простота конструкции и сравнительно невысокая стоимость возможность выполнения на конвейерами различных технологических операций невысокая трудоёмкость работ обеспечение безопасности труда улучшение его условий — всё это обусловило широкое применение конвейеров во всех областях народного хозяйства: в чёрной и цветной металлургии машиностроении горной химической пищевой и др. отраслях промышленности. В промышленном производстве конвейера являются неотъемлемой составной частью технологического процесса. Конвейера позволяют устанавливать и регулировать темп производства обеспечивать его ритмичность. Являясь основным средством комплексной механизации и автоматизации транспортных и погрузо-разгрузочных процессов и поточных технологических операций конвейеры вместе с тем освобождают рабочих от тяжелых и трудоемких транспортных и погрузочно-разгрузочных работ делают их труд более производительным.
Эффективность использования конвейера в технологическом процессе любого производства зависит от того насколько тип и параметры выбранного конвейера соответствуют свойствам груза и условиям в которых протекает технологический процесс. К таким условиям относятся: производительность длина транспортирования форма трассы и направление перемещения (горизонтальное наклонное вертикальное комбинированное); условия загрузки и разгрузки конвейера.; размеры груза его форма удельная плотность абразивность кусковатость влажность температура и пр.; ритм и интенсивность подачи а также различные местные факторы.
Поэтому главной задачей данного курсового проекта является: спроектировать оптимальную конструкцию и отдельные узлы конвейера для наиболее эффективной транспортировки заданного груза.
Техническое предложение.
Рис. 1 Общий вид конвейера
Предлагаемый ленточный конвейер предназначен для транспортирования легких насыпных грузов (пшеница). Для повышения эффективности и производительности была проработана оптимальная конструкция конвейера и его основных узлов.
Выбираем резинотканевую конвейерную ленту с тяговым каркасом из тканевых прокладок. Ее достоинством является универсальность выполнения стыкового соединения повышенная стойкость к продольным порывам высокая амортизирующая способность. Т.к. производительность а следовательно и скорость тарнспортирования груза невысоки то выбираем одноприводную схему с одним двигателем. Для увеличения тягового усилия увеличим угол обхвата приводного барабана с помощью установки отклоняющего барабана.
Рис. 2 Кинематическая схема привода
Насыпные грузы загружаются на ленту конвейера из бункера или с технологических транспортных и погрузочных машин поэтому для направления струи на ленту груза установим загрузочный лоток.
Для данного ленточного конвейера целесообразно применение грузового натяжного устройства тележечного типа с непосредственным воздействием груза на натяжную тележку или через полиспаст а также разгрузочного устройства в виде концевого барабана.
Конструкции опорных элементов ленточного конвейера могут быть выполнены жесткими (жесткие ставы) или с применением гибкого органа (канатные ставы) а также комбинированные – жесткие и канатные.
Жесткие ставы состоящие из стального проката (уголки швеллеры и др.) или труб изготавливают отдельными секциями длиной 2 5 м кратной шагу роликовых опор. В зависимости от условий эксплуатации конвейеров секции жестких ставов могут быть оснащены съемными кронштейнами позволяющими устанавливать роликовые опоры различной длины.
Рис. 3 Линейная секция ленточного конвейера с жестким ставом
Транспортируемый груз – руда железная.
Плотность – р=32 тм.
Производительность – 360 тч.
Длины участков: L1=25 м.; L2=18 м.; L3=80м.
Условный угол обхвата барабана α=2100
Условия работы – тяжелые.
Рис.1 Трасса конвейера
1 Проработка задания:
Крупность частиц крупнокускового груза находится в пределах (1 т.1.2 с.8) угол естественного откоса в покое (1 т.1.1 с.6-8). Примем .Угол естественного откоса в движении принимаем равным (1 т.2.6 с.15).
У приводного и отклоняющего барабанов установлены отклоняющие барабаны увеличивающий угол обхвата ленты на перегибе нижней ветви ленты - поворотный барабан а на перегибе верхней ветви - роликовая батарея. На верхней ветви ленты применены трехроликовые опоры с углом наклона боковых роликов
Расчет ленточного конвейера.
1 Выбор типа ленты и определение её ширины.
коэффициент производительности при (1 т.2. с.12);
скорость движения ленты примем равной (1 т.2.1 с.11);
коэфициент уменьшения сечения сечения груза на наклонном конвейере примем равным (1 т.2.4 с.12).
Согласно ГОСТ 22644-77 (1 т.2.5 с.1) ширину ленты принимаем равной .
Проверим выбранную ширину ленты по гранулометрическому составу по формуле:
коэффициент Х примем равным Х=33 (1 с.10) тогда
Существенное увеличение ширины ленты требует пересчета скорости.
Примем в соответствии с ГОСТ 22644-77(1 т. 2.5 с.1) .
2 Выбор диаметра роликов и расстановка роли-
коопор по трассе конвейера.
Диаметр ролика примем равным (1 т.2.7 с.17)
Расстояние между роликоопорами на рабочей ветви конвейера примем с учетом размера типичных кусков: т.к. при транспортировании крупнокусковых грузов расстояние между роликоопорами принимают для amax500 мм - (4)
Расстояние между роликоопорами в зоне загрузки примем равным
На криволинейных участках рабочей ветви установим три роликоопоры с расстоянием 06м. На незагруженной ветви роликоопоры установим на расстоянии:
3 Расчет прочности ленты.
Установим приближенное значение общего сопротивления при установившемся движении ленты конвейера по формуле:
где обобщенный коэффициент местных сопротивлений примем равным (1 с.18).
- длины соответственно горизонтальной и вертикальной проекций расстояний между осями концевых барабанов конвейера
погонная масса насыпного груза по формуле:
погонная масса ленты по формуле:
=2(мм) – толщина внутренней обкладки;
=(мм) – толщина внешней обкладки.
погонная масса вращающихся частей роликоопор рабочей и холостой ветви соответственно(1 т. 2.10 с.18)
значения коэффициентов сопротивления рабочей и холостой ветвей соответственно равны (1 т. 2.11 с.20).
Определим приближенное значение максимального натяжения ленты по формуле:
где - коэффициент запаса сцепления ленты с барабаном (1 с.19);
значение тягового фактора примем равным (1т.2.12 с.21)
Определим требуемое число прокладок тягового каркаса в резинотканевой ленте по формуле:
- где запас прочности равен (1 с. 20)
Прочность прокладки примем (1 т. 2.5 с. 1)
Примем количество прокладок .
4 Определение размеров барабанов.
Определим диаметр барабана по формуле:
- где коэффициент учитывающий прочность прокладок (1 с.22);
- коэффициент зависящий от назначения барабана для приводного с однобарабанным приводом (1 с.22);
- для натяжного и отклоняющего барабанов установленных на трассе(1 с.22)
Для приводного барабана:
В соответствии с ГОСТ 22644-77 примем (1 т.2.5 с.1)
Для натяжного и отклоняющего барабанов:
Длину обечайки барабана назначаем (1 с.22).
Определим ориентировочно массу барабана по формуле:
Примем (1 с.2) тогда
5 Тяговый расчет конвейера.
Рис. 2.5 Схема трассы конвейера
Разобьем трассу конвейера на участки (см. рис.1)
Определим точку с наименьшим сопротивлением исходя из сравнения следующих величин:
- сила тяжести ленты
- сила сопротивления перемещению ленты.
Поскольку сила сопротивления перемещению ленты меньше силы тяжести ленты то наименьшее натяжение ленты будет в т.1.
Определим составляющие силы сопротивления передвижению ленты:
Сила сопротивления в пункте загрузки по формуле:
где - коэффициент трения груза о ленту (1 т. 1.1 с. 6-8);
- угол наклона загрузочного лотка;
- составляющая скорости груза в направлении транспортирования;
- коэффициент бокового давления груза на направляющие борта (1 с. 24);
- коэффициент трения груза о борта загрузочного латка.
Проведем тяговый расчет методом обхода по контуру начиная из точки 1 в которой лента имеет наименьшее натяжение.
Силу сопротивления на барабане:
- коэффициент сопротивления движению ленты на барабанах определим для приводного и натяжного барабанов (1 т. 2.13 с. 26);
- для отклоняющего барабана.
Силу сопротивления роликоопор на криволинейных выпуклых участках:
- коэффициент сопротивления на роликовых батареях.
Подставляем полученные значения и :
Приняв значение коэффициента запаса по сцеплению равным получим:
Определим натяжение ленты во всех рассмотренных точках:
6 Проверка минимального натяжения ленты.
Определим минимально допустимое натяжение ленты из обеспечения допустимой стрелы провеса ленты на грузовой ветви:
Сравним полученное значения минимального натяжения ленты с полученным в тяговом расчете:
- условие выполняется.
Определим минимально допустимое натяжение ленты из обеспечения допустимой стрелы провеса ленты на холостой ветви:
Поскольку минимальная сила натяжения ленты больше минимально допустимой то силу натяжения ленты следует считать достаточной.
Определим давление ленты на поверхность приводного барабана:
где - допустимая величина давления
7 Выбор двигателя и кинематический расчет привода.
Определим расчетное тяговое усилие ленты по формуле:
(2)- тяговое усилие на барабане;
- коэффициент запаса мощности (1 с. 29)
Примем схему привода однодвигательную.
Рис. 2.7. Кинематическая схема привода
-общий КПД привода с учетом потерь в приводных барабанах
В соответствии с полученной мощностью выбираем двигатель 4А160М6У3 со следующими техническими характеристиками:
с частотой вращения
момент инерции ротора (1 т. 4.2.1 с. 6-65)
Для соединения вала двигателя и быстроходного вала редуктора выберем муфту МУВП №1 с тормозным шкивом способную передавать крутящий момент в 500Нм и имеющую момент инерции а для соединения тихоходного вала редуктора и вала барабана выбираем муфту МЗ-5
По ГОСТ 5006-75 способную передавать крутящий момент 8000 Нм и имеющую момент инерции
Частоту вращения вала приводного барабана определим по формуле:
Необходимое передаточное отношение привода определим по формуле:
Исходя из необходимого передаточного отношения и мощности привода выберем редуктор 2Ц3-200Н с передаточным отношением которое отличается от требуемого значения на 3% что является допустимым.
Уточняем скорость ленты:
Фактическую производительность конвейера определим по формуле:
где - коэффициент производительности (1 т. 2. с. 12);
- коэффициент уменьшения производительности с увеличением угла наклона конвейера (1 т. 2.4 с. 12).
8 Расчет конвейера на пуск.
Расчетный коэффициент сопротивления движению ленты при пуске конвейера
где- коэффициент увеличения сопротивления
Статическое сопротивление при пуске:
Для рабочей ветви определим по формуле:
Для холостой ветви сопротивление определим по формуле:
Общее статическое сопротивление при пуске определим по формуле:
Статический пусковой момент конвейера приведенный к валу двигателя определим по формуле:
где - общий КПД привода.
Время пуска ленточного конвейера определим по формуле:
(44) – приведенный момент инерции поступательно и вращательных движущихся масс груза конвейера и привода;
где - коэффициент учитывающий инерцию вращающихся масс роликов и барабанов конвейера. (1 с. 2)
- коэффициент учитывающий массы деталей привода вращающихся медленнее чем вал двигателя . (1 с. 2)
- момент инерции зубчатой муфты
- соответственно суммарные моменты инерции роторов электродвигателей и соединяющих их с редуктором муфт.
(45) - номинальная угловая скорость двигателя;
(46) – средний пусковой момент двигателя;
(47) – максимальный пусковой момент двигателя;
(48) – номинальный пусковой момент двигателя;
- коэффициент учитывающий упругое удлинение ленты (1с.2).
Определим минимально допустимое время пуска конвейера по формуле:
где -допустимое ускорение при пуске (1 с.33 )
9 Проверка прочности ленты.
Максимальное натяжение ленты которое может создать двигатель в период пуска определим по формуле:
Значение фактического запаса прочности ленты определим по формуле:
Значение допустимого запаса прочности определим по формуле:
где - номинальный запас прочности (1 стр. 4);
- коэффициент неравномерности работы прокладок для ленты с четырьмя прокладками (1 стр.4);
- коэффициент учитывающий способ стыка концов ленты для вулканизированного соединения (1 стр.4);
- коэффициент учитывающий конфигурацию трассы для наклонного конвейера со сложным профилем равен (1 с. 4);
- коэффициент режима работы для среднего режима работы равен (1 с. 4).
Что меньше полученного значения фактического запаса прочности.
10 Расчет тормозного момента.
Статический тормозной момент на валу двигателя препятствующий обратному движению ленты под действием сил тяжести груза при выключении тока определим по формуле:
где - значение коэффициента возможного уменьшения сопротивлений конвейера примем равным (1 с. 5).
Знак минус показывает что лента под действием силы тяжести не начнет двигаться в обратном направлении и поэтому специального останова не требуется.
Статический тормозной момент на валу двигателя для ограничения выбега ленты конвейера после выключения электродвигателя определим по формуле:
(55)- время торможения
где - допустимую величину выбега (1 с. 5)
То есть выбега после выключения электродвигателя ленты не будет вследствие сопротивления перемещению ленты.
Следовательно тормоз не нужен.
Проектирование узлов ленточного конвейера.
1 Определение основных параметров натяжного устройства.
Для обеспечения необходимого прижатия ленты к приводному барабану компенсации вытяжки и исключения недопустимого провисания ленты все конвейеры снабжаются натяжным устройством.
Усилие натяжения ленты создаваемое натяжным устройством при установившемся движении
где - усилие в ленте в точке набегания на натяжной барабан (определенное методом обхода по контуру);
- усилие в ленте в точке сбегания с натяжного барабана (определенное методом обхода по контуру).
Ход натяжного барабана выберем с учетом материала прокладок каркаса ленты (резинотканевая лента):
В зависимости от типа ленты (резинотканевая) усилия натяжения (нормальное для данного типа конвейеров и ленты) схемы трассы (не сложная и не очень длинная) и хода натяжного барабана (достаточно короткий) выбираем тележечное грузовое натяжное устройство.
Определим усилие необходимое для перемещения тележки натяжного устройства с барабаном:
где - сопротивление перемещению тележки в направляющих
- масса тележки с барабаном;
- коэффициент сопротивления движению тележки на подшипниках качения.
Масса натяжного груза:
где - общий КПД полиспаста и обводных блоков.
- КПД полиспаста примем;
- КПД обводных блоков примем;
- кратность полиспаста.
2 Определение размеров загрузочного лотка.
Насыпные грузы загружаются на ленту конвейера из бункера или с технологических транспортных и погрузочных машин. При загрузке груз должен ложиться равномерно по длине и ширине ленты. Равномерную подачу из бункера обеспечивают питатели а для формирования и направления струи на ленту груза применим лоток.
Длина бортов направляющего лотка определяется:
где - вектор скорости поступления груза в воронку (т. к. угол равен 900);
Максимальную высоту направляющих бортов лотка определим исходя из производительности и размеров выпускного отверстия лотка:
- ширина направляющих бортов.
Примем основные размеры загрузочного лотка (1 т. 2.14 с.44):
Расстояние между бортами – 530 мм;
Длина бортов – 2000 мм.
Эти значения не противоречат ранее полученным.
3 Выбор типа и определение основных параметров разгрузочного устройства.
Разгрузка конвейера может производиться с концевого барабана или при помощи промежуточных пунктов при помощи различных разгрузочных устройств установленных по длине трассы конвейера. Для разгрузки конвейера с концевого барабана или перегрузки груза с одного конвейера на другой необходимо определить место установки экрана воспринимающего удары части падающего груза; для этого производится построение траектории свободного полета насыпного груза.
Для построения траектории движения частицы груза с разгрузочного барабана необходимо определить положение точки А – начало координат после которой начинается свободный полет частицы груза. Для этого определим полюсное расстояние:
- радиус движения частицы на барабане;
- скорость движения частицы на барабане.
Т.к. то точка А находится в первом квадрате.
Расположение точки А от вертикальной оси определим по формуле:
Построение нахождения точки А:
Радиусом проведем окружность от вертикальной оси отложим угол и получим т. А – начало координат. Траекторию строим в косоугольных координатах для чего проводим ось Х (касательная к поверхности барабана проведенная через полюс А) и вертикальную ось Y.
Рис. 3.3. Построение траектории полета частиц груза
Задаваясь определенным интервалом времени t=01 с построим траекторию полета частиц груза (см. рис.6). Частица груза движется по параболе очертание которой определяется координатами:
. Для построения траектории всей массы груза сходящего с барабана необходимо провести совмещенное построение траектории движение частиц находящихся в верхнем и нижнем слое груза на ленте. Скорость частицы находящейся в нижнем слое груза равна скорости ленты а радиус движения – радиусу барабана. Скорость частицы в верхнем слое определяется:
- скорость ленты мс;
- радиус барабана м;
- высота слоя груза на ленте м.
В соответствии с траекториями движения частиц груза проектируется очертание разгрузочного кожуха. Конфигурация кожуха должна способствовать тому чтобы исключить удары о стенки кожуха излишнее крошение и пыление.
При установке разгрузочной воронки предусмотрены защитные средства от быстрого износа стенки воронки воспринимающие удары падающих частиц груза (покрытие стенок воронки листами износостойкой резины).
Разгрузка на трассе конвейера производится при помощи барабанных разгружателей.
Опорный стол служит для выпрямления ленты в месте установки разгружателя и выполняется в виде подъемных и поворотных роликов обеспечивающих желобчатый профиль ленты после подъема разгружателя. Подъем разгружателя для его перевода в нерабочее положение угловой. Подъемный механизм имеет электрический привод с дистанционным управлением.
4 Выбор типа и определение основных параметров устройства для очистки ленты.
На каждом конвейере транспортирующем насыпные грузы устанавливаются очистные устройства для очистки рабочей и внутренней поверхности ленты и барабанов. В соответствии с (1 т. 2.16 с. 52) выбираем в качестве очистного устройства одинарный скребок. Для очистки рабочей поверхности ленты установим его после разгрузочного барабана а для очистки внутренней поверхности ленты – перед задним концевым барабаном на расстоянии 1 м. от оси барабана.
Для очистки внутренней поверхности ленты применим двухсторонний скребок плужкового типа с выводом очищаемых частиц вне ленты конвейера.
Расчет элементов конвейера на прочность.
1 Расчет вала приводного барабана.
1.1 Выбор материала валов.
Основными условиями которым должна отвечать конструкция вала конвейера являются достаточная прочность жесткость технологичность конструкции и экономия материала. Выбираем Сталь 45.
Характеристика данной стали:
Расчет вала выполняется в два этапа: ориентировочный расчет на кручение и сложное сопротивление; проверка запаса прочности по выносливости в наиболее опасных сечениях.
1.2 Предварительный расчет вала барабана.
Расчет вала на кручение. Диаметр вала в опасном сечении определим из условия прочности на кручение при пониженных допускаемых напряжениях.
где Т - крутящий момент ;
- допускаемые напряжения на кручение.
Применим двухопорный вал. Действующие на вал расчетные силы считаем сосредоточенными и расположенными посередине длины воспринимающих их элементов.
При установке вала на подшипниках скольжения расчетную точку опоры расположим на расстоянии 025 0 длины его подшипника от его конца со стороны пролета между опорами.
Суммарная нагрузка на вал:
где - векторы от натяжения соответственно в набегающей и сбегающей ветвях тягового элемента по результатам тягового расчета Н.
где z=2- число ступиц на валу
Крутящий момент на валу
Диаметр вала в опасном сечении из условия прочности на кручение:
Примем диаметр вала по ГОСТ .
Т.к. муфта зубчатая смонтированная на валу то примем что на вал действует изгибающий момент:
На основании третьей гипотезы прочности приведённый момент в опасном сечении:
Диаметр вала в опасном сечении:
где - допускаемые напряжения.
На основании предварительного расчёта разрабатываем конструкцию вала (рис 2.1): назначаем диаметры и длины отдельных участков расположение шпоночных канавок и т. д.
Ориентировочно длину барабана и вала для предварительного расчёта валов конвейера у которого тяговым элементом является лента можно пользоваться рекомендациями приведёнными в табл. 4.2. для типовых конструкций.
Расстояние между центрами опор l0 =1250 мм.
Общая длина вала l=1680 мм.
Направление силы или момента принимаем наиболее неблагоприятным для вала.
Рис. 4.1.2 Вал барабана и эпюры распределения нагрузок
1.3 Уточненный расчет вала на выносливость.
Проверим наиболее опасные сечения в которых имеется концентрация напряжений. При проверке определим фактический (расчетный) коэффициент запаса по усталостной прочности и согласовываем его с допустимым.
Коэффициент запаса прочности при симметричном цикле нагружений для нормальных напряжений:
для касательных напряжений:
При одновременном действии нормальных и касательных напряжений:
В приведенных формулах:
- предел выносливости гладкого образца при симметричном цикле напряжений изгиба;
- предел выносливости гладкого образца при симметричном цикле напряжений кручения;
-амплитуда номинальных напряжений соответственно изгиба и кручения при симметричном цикле нагружений;
и - суммарные коэффициенты учитывающие влияние всех факторов на сопротивление усталости соответственно при изгибе и кручении.
- допускаемое значение запаса выносливости.
Напряжения изгиба и кручения находим по известным формулам сопротивления материалов:
где Мизг Т – расчетный изгибающий и крутящий моменты;
Wo Wр – осевой и полярный моменты сопротивления сечения вала.
При определении напряжений осевой Wo и полярный Wp моменты сопротивления подсчитываем с учетом ослабления вала шпонками шлицами лысками и т.д.
Для вала сплошного сечения при диаметре:
Запас прочности обеспечен.
Рассчитаем вал в опасном сечение 2-2 на изгиб и кручение т.к. в этом сечение наибольшие крутящие моменты:
1.4 Расчёт шпоночных соединений
Основным для соединения является расчёт на смятие шпонок и пазов.
Рассчитаем шпонку на выходном конце вала.
Выберем шпонку 28x16x120 СТ СЭВ 189-75 с параметрами:
b=28 мм h=16 мм l=120 мм t1=10 мм. (2. табл. 4.15. стр.92)
Основным для соединения является расчёт на смятие шпонок и пазов
где - крутящий момент на валу;
d=105 мм - диаметр вала;
- для стальных ступиц;
Прочность шпоночного соединения обеспечена.
Рассчитаем шпонку под ступицей
По таблице для диаметра 113 мм выбираем шпонку с параметрами:
Выберем шпонку 32x18x180 СТ СЭВ 189-75
b=32 мм h=18 мм l=200мм (2 табл. 4.15. стр.92)
d=113 мм - диаметр вала;
1.4 Выбор и расчет подшипников качения для приводного барабана.
Выбираем подшипники шариковые радиальные сферические двухрядные по диаметру посадочного места вала или оси 1320 ГОСТ 5720-75
Номинальная долговечность подшипника в миллионах оборотов:
где С=119кН – каталожная динамическая грузоподъемность выбранного
р=3- показатель степени для шариковых подшипников;
Эквивалентная нагрузка:
– радиальная нагрузка на подшипник;
V=12- коэффициент вращения при вращении наружного кольца;
=1- коэффициент безопасности для ленточных конвейеров;
Кт=1- температурный коэффициент при .
Расчетная долговечность подшипника:
где - частота вращения подшипника.
Рекомендуемый срок службы подшипников в конвейерах составляет не менее 8000 часов.
Срок службы подшипника больше рекомендуемого.
2 Расчет оси натяжного барабана
2.1 Предварительный расчет оси
Аналогично выбираем материал для оси барабана - Сталь 45
Для оси составляем её расчетную схему (рис. 5): расположение опор величину и направление действующих на ось нагрузки а так же точки их приложения.
Ориентировочно длину барабана и оси для предварительного расчёта осей конвейера у которого тяговым элементом является лента используем рекомендации приведённые для типовых конструкций.
Общая длинна вала l=1680 мм.
Суммарная нагрузка на ось:
где z=2- число ступиц на оси
Рис. 4.2.1 Вал барабана и эпюры распределения нагрузок
На основе составленной расчетной схемы вала определяем реакции опор и построим эпюры изгибающих и крутящих моментов.
Из условия прочности по напряжениям изгиба определяется диаметр оси под ступицей.
где - момент сопротивления расчетного сечения при изгибе;
- допускаемое напряжение в симметричном цикле.
где - диаметр оси под ступицей
где - предел выносливости .
- коэффициент учитывающий конструкцию детали (для осей);
- допустимый коэффициент запаса прочности
Диаметр оси в опасном сечении:
Принимаем диаметр средней части оси d=86мм диаметры посадочных поверхностей под подшипники d=80мм.
Определим диаметр оси в опасном сечении:
где М – изгибающий момент в опасном сечении;
S=14 – запас прочности при постоянных напряжениях
На основании предварительного расчёта разрабатываем конструкцию оси назначаем диаметры и длины отдельных участков расположение шпоночных канавок и т. д.
2.2 Уточненный расчет оси.
где - амплитуда номинальных напряжений соответственно изгиба и кручения при симметричном цикле нагружений;
- суммарные коэффициенты учитывающие влияние всех факторов на сопротивление усталости соответственно при изгибе и кручении.
Суммарные коэффициенты концентрации напряжений для детали при отсутствии технологического упрочнения:
где - эффективные коэффициенты концентрации напряжений для полированного образца;
- коэффициенты состояния поверхности;
=08 - коэффициенты влияния абсолютных размеров детали;
2.3 Выбор и расчет подшипников качения для оси натяжного барабана.
Выбираем подшипники шариковые радиальные сферические двухрядные по диаметру посадочного места вала или оси 1220 ГОСТ 5720-75
где С=111220Н – каталожная динамическая грузоподъемность выбранного
Определение основных параметров металлоконструкции конвейера.
Опорная конструкция ленточного конвейера представляет собой жесткие ставы состоящие из стального проката (швеллеры). Ставы изготовляют отдельными секциями длиной 5 м.
Для выбора параметров проката рассмотрим наиболее протяженный горизонтальный участок конвейера между двух опорных балок L=5 м. На данный участок действуют распределенные силы от веса металлоконструкции погонной массы движущихся частей конвейера и погонной массы груза. Условно примем что рассматриваемая металлоконструкция представляет собой балку на двух опорах расчетная схема представлена на рис. 6.
Рис. 5 Расчетная схема распределённых нагрузок действующих на металлоконструкцию конвейера.
Суммарная распределенная нагрузка определится:
где - погонная масса груза;
- погонная масса движущихся частей конвейера;
- погонная масса вращающихся частей роликоопор;
- погонная масса вращающихся частей роликоопор холостой ветви.
- погонная масса проката кгм.
Ориентировочно примем за расчетный прокат – швеллер № 12 изготовленный из горячекатаной углеродистой стали 2 [8 стр. 364].
Реакции опор определим:
Максимальный изгибающий момент:
Момент сопротивления для подобранного профиля:
где - допустимое напряжение изгиба для горячекатаной углеродистой стали 2 [9 стр.77];
Условие прочности для выбранного профиля соблюдается.
В результате выше произведенных расчетов был спроектирован ленточный конвейер имеющий следующие технические характеристики:
Производительность 360 тч
Скорость транспортирования груза 063 мс
Размер типичных кусков груза 180 мм
Также был спроектирован привод конвейера с техническими характеристиками:
Мощность двигателя 15 кВт
Передаточное число редуктора 63
Рекомендуемые чертежи
- 18.11.2018
- 25.01.2023