Привод галтовочного барабана




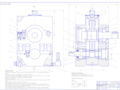
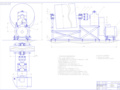
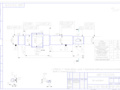
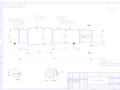
- Добавлен: 25.10.2022
- Размер: 2 MB
- Закачек: 1
Описание
Состав проекта
![]() |
![]() |
![]() ![]() ![]() ![]() |
![]() ![]() ![]() ![]() |
![]() ![]() ![]() ![]() |
![]() ![]() ![]() ![]() |
![]() ![]() ![]() ![]() |
![]() |
![]() ![]() |
![]() ![]() |
![]() ![]() |
![]() ![]() |
![]() ![]() |
![]() ![]() |
![]() ![]() |
![]() ![]() |
![]() ![]() |
![]() ![]() |
![]() |
![]() ![]() ![]() |
![]() ![]() ![]() |
![]() ![]() ![]() |
Дополнительная информация
Редуктор. Детали машин.dwg

Техничечкая характеристика.
Передаточное число редуктора U=4
Вращающий момент на тихоходном валу Т2=
Частота вращения быстроходного вала n1=
Техничечкие условия.
Размеры для справок.
Все детали поступившие на сборку промыть в уайт-спирте ГОСТ 3134-52 и насухо протереть безворсными
Редуктор залить маслом : индустриальное И-Г-А-68 ГОСТ 17479.4-87.
Допускается эксплуотировать редуктор с отклонением от горизон-тального положентя на угол до 5
должен быть обеспечен
достаточный для смазки зацепления.
Посадку на валу подшипника производить после нагрева в масляной
ваннедо температуры 80
Герметичность сопряжения основания корпуса с крышкой обеспечить нанесением на поверхность перед монтажом
Подшипниковые узлы набить смазкой УТ-1 ГОСТ 1957-73.
Все резьбовые соединения должны быть надёжно затянуты и законтрены.
Редуктор обкатать с нагрузкой моментом 278 Нм в течении 6 часов.Во время обкатки контролируется шум.
После обкатки провести внешний осмотр редуктора
проверяютсятечи в разъмах
которая не должна превышать 70
После приемки редуктора
отработавшее масло слить
редукторпромыть уайт-спиртом и заполнить маслом.
Все несопряженные поверхности грунтовать грунтом ХГС-26 ГОСТ 7313-55 и эмилью ХВ-124 ГОСТ 10144-62.
Характеристика Зацепления.
Редуктор вид сверху.dwg

Быстроходный вал.dwg

Направление линии зуба
Коэффициент смещения
Обозначение чертежа сопряженного зубчато
220НВ min. 2.* Размер обеспеч. инстр. 3. Неуказанные предельные отклонения размеров:
Чертеж. Привод.dwg

Электродвигатель 4АМ
У3. Мощность- 3 кВт.
Частота вращения - 9
Общее передаточное число U=
Передаточное число редуктора U=4
Передаточное число поликлиновой ременной
Окружная сила на барабане F=0.7 кН.
Окружная скорость барабана V=3
Допускаемое откланение скорости барабана
Вращающий момент на тихоходном валу - 277
Частота вращения быстроходного вала -
Технические требования
*Размеры для справок
Размеры уточнить при сборке
Техническая характеристика.
Тихоходный вал.dwg

* Размер обеспеч. инстр.
Неуказанные пре-дельные отклонения
Спецификация 2.doc
Крышка подшипниковая
Муфта упругая втулочно-пальцевая
Двигатель 4АМ112МА6У3
Подшипник 36206 ГОСТ832-78
Болт М12 ГОСТ2239-80
Ремень клиноременный
Шайба пружинная 12 ГОСТ 6402-70
Шайба пружинная 14 ГОСТ 6402-70
Гайка М12-6Н.5.029 ГОСТ 5915-70
Гайка М14-6Н.5.029 ГОСТ 5915-70
Винт М8-6gх20.68.029
Пояснительная записка.doc
1 Кинематическая схема привода2
2 Определение срока службы приводного устройства2
Кинематические расчеты привода. Выбор двигателя3
1.Определение номинальной мощности и номинальной частоты вращения двигателя3
Выбор материала зубчатых передач. Определение допускаемых напряжений.8
1. Выбор твердости термообработки и материала колес.8
2.Определение допускаемых контактных напряжений [s]Н8
3.Определение допускаемых напряжений изгиба []F9
Расчет закрытой цилиндрической зубчатой передачи.10
1.Определяем главный параметр – межосевое расстояние aw.10
2. Определяем модуль зацепления m11
3. Определяем угол наклона зубьев 11
4. Определение суммарного числа зубьев шестерни и колеса11
5. Уточняем действительную величину угла наклона зубьев11
6. Определяем число зубьев шестерни:12
7. Определяем число зубьев колеса:12
8. Определяем фактическое передаточное число uф и проверяем его отклонение Du от заданного u12
9. Определяем фактическое межосевое расстояние12
10. Определяем фактические основные геометрические параметры передачи12
11. Проверяем межосевое расстояние13
12. Проверяем пригодность заготовок колес. Условие пригодности заготовки колес13
13. Проверяем контактные напряжения Н13
14. Проверяем напряжения изгиба зубьев шестерни F1 и колеса F214
Расчет клиноременной передачи16
1. Выбираем сечение ремня16
2. Определяем минимально допустимый диаметр ведущего шкива d1min16
3. Задаемся расчетным диаметром ведущего шкива16
4. Определяем диаметр ведомого шкива d216
5.Определяем фактическое передаточное число uф и проверяем его отклонение u от заданного u16
6. Определяем ориентировочное межосевое расстояние a16
7. Определяем расчетную длину ремня l16
8. Уточняем значение межосевого расстояния по стандартной длине:16
9. Определяем угол обхвата ремнем ведущего шкива α116
11. Определяем частоту пробегов ремня U17
12. Определяем допускаемую мощность передаваемую одним клиновым ремнем17
13. Определяем количество клиновых ремней Z17
14. Определяем силу предварительного натяжения F017
15. Определяем окружную силу передаваемую комплектом клиновых ремней Ft17
16.Определяем силы натяжения ведущей F1 и ведомой F2 ветвей17
17. Определяем силу давления ремней на вал Fоп17
18. Проверяем прочность одного клинового ремня по максимальным напряжениям в сечении ведущей ветви 18
19. Параметры клиноременной передачи18
Нагрузки валов редуктора19
1. Определение сил в зацеплении закрытых передач19
2. Определение консольных сил19
Разработка чертежа общего вида редуктора20
1. Выбор материала валов20
2. Выбор допускаемых напряжений на кручение20
3. Определение геометрических параметров ступеней вала:20
4. Предварительный выбор подшипников качения20
Расчетная схемы валов редуктора21
Проверочный расчет подшипников21
1. Проверочный расчет подшипников быстроходного вала22
2. Проверочный расчет подшипников тихоходного вала24
3 Основные размеры и эксплуатационные характеристики подшипников25
Конструктивная компоновка привода26
2. Конструирование валов26
3. Выбор соединений28
4.Конструирование подшипниковых узлов.30
5.Конструирование корпуса редуктора.32
6.Конструирование элементов открытых передач.36
8.Смазывание. Смазочные устройства.37
Проверочные расчеты39
2. Проверочный расчет стяжных винтов подшипниковых узлов.39
3. Проверочный расчет валов40
4. Тепловой расчет редуктора46
Расчет технического уровня редуктора47
1 Определение массы редуктора.47
2 Определение критерия технического уровня редуктора.47
3. Технический уровень редуктора.47
Список использованной литературы49
Разработка чертежа кинематической схемы привода
1 Кинематическая схема привода
Графическая часть задачи выполнена на чертежной бумаге формата А4. Работа содержит: кинематическую схему привода галтовочного барабана ; перечень элементов схемы; исходные данные для проектирования.
2 Определение срока службы приводного устройства
Устанавливаем барабан на машиностроительном заводе для снятия заусенцев.
2.1. Определение ресурса привода:
где Lr- нормативный срок службы привода Lr=6лет;
Lc- число смен работы Lc=2;
t- число часов работы в смену t=8 ч.
2.2. Служба привода с учетом простоев равных 15% рабочего времени:
2.3. Расчетный рабочий ресурс привода принимаем:
Таблица 1.2.3.1. Сводная таблица
Место установки привода
Машиностроительный завод
С малыми колебаниями
Кинематические расчеты привода. Выбор двигателя
Двигатель является одним из основных элементов. От типа двигателя зависят конструктивные и эксплуатационные характеристики рабочей машины и ее привода.
1.Определение номинальной мощности и номинальной частоты вращения двигателя
1.1. Определяем требуемую мощность:
1.2. Определение КПД привода:
1.3. Находим требуемую мощность двигателя:
1.4. Выбираем двигатель серии 4А с номинальной мощностью применив для расчета четыре варианта типа двигателя:
Номинальная мощность кВт
Частота вращения обмин
при номинальном режиме
1.5. Определение частоты вращения барабана:
1.6. Находим передаточное число привода u для каждого варианта:
1.7. Производим разбивку передаточного числа привода u принимая для всех вариантов передаточное число редуктора постоянным 5:
Цилиндрического редуктора
1.8. Анализируя полученные значения передаточных чисел приходим к выводу:
а) четвертый вариант затрудняет реализацию принятой схемы из-за большого передаточного числа u всего привода;
б) первый вариант не рекомендуется для приводов общего назначения ввиду большой металлоемкости.
в) в третьем варианте получилось большое значение передаточного числа ременной передачи(2 3)
г) из рассмотренных четырех вариантов предпочтительнее второй.
1.9. Определение максимально допустимого отклонения частоты вращения приводного вала конвейера:
1.10. Определение допускаемой частоты вращения приводного вала приняв =+105обмин:
отсюда фактическое передаточное число привода
передаточное число открытой передачи
Таким образом выбираем двигатель4АМ112МА6У3 ( =955 обмин); передаточные числа: привода u=114 редуктора ременной передачи =24
Определение силовых и кинематических параметров привода
Последовательность соединения элементов привода по кинематической схеме
Частота вращения n обмин
Силовые и кинематические параметры привода
Тип двигателя 4АМ112МА6У3
Приводной рабочей машины
Расчетная мощность Р кВт
Выбор материала зубчатых передач. Определение допускаемых напряжений.
1. Выбор твердости термообработки и материала колес.
а) Выбираем материал для зубчатой пары колес одинаковый для шестерни и колеса:
Материал – Сталь 40Х
б) Выбираем термообработку для зубьев шестерни и колеса:
Для шестерни –У+ТВЧ для колеса – У
в) Выбираем интервал твердости зубьев шестерни НВ и НВ:
Для шестерни НВ=450 500
Для колеса НВ=269 302
г) Определяем среднюю твердость зубьев шестерни НВ и колеса НВ:
д) Определяем механические характеристики сталей для шестерни и колеса sв s-1:
Для шестерни sв=900 Нмм2 s-1=410Нмм2
Для колеса sв=900 Нмм2 s-1=410 Нмм2
е) Выбираем предельные значения размеров заготовки шестерни(Dпред – диаметр) и колеса(Sпред – толщина обода или диска):
Dпред=125мм Sпред=80мм
2.Определение допускаемых контактных напряжений [s]Н Нмм2
а) Определяем коэффициент долговечности для зубьев шестерни KHL1 и колеса KHL2:
где NH0 – число циклов перемены напряжений соответствующее пределу выносливости; N – число циклов перемены напряжений за весь срок службы(наработка) N=573Lh. Здесь – угловая скорость соответствующего вала 1с; Lh – срок службы привода(ресурс)ч.
для шестерни N1=циклов
для колеса N2=циклов.
NH02=16.5 × 106 циклов
Т.к. N1>NH01 и N2>NH02 то KHL1 = KHL2=1
б) Определяем допускаемое контактное напряжение [s]H01 и []H02 соответствующее пределу контактной выносливости при числе циклов перемены напряжений NH01 и
для шестерни [s]H01=14НRC+ 170=Нмм2
для колеса []H02=18 НВср + 67= Нмм2
в) Определяем допускаемые контактные напряжения для зубьев шестерни [s]H1 и колеса []H2:
для шестерни [s]H1= KHL1[s]H01=1×877=877 Нмм2
для колеса []H2= KHL2[]H02=1×5809=5809Нмм2
[]=045([s]H1 +[]H2 )=656055 Нмм2
3.Определение допускаемых напряжений изгиба []F Нмм2
а) Определяем коэффициент долговечности для зубьев шестерни КFL1=KFL2=
где NF0=4×106 – число циклов перемены напряжений для всех сталей соответствующее пределу выносливости; N – число циклов перемены напряжений за весь срок службы(наработка)
Т.к. N1>NF0 и N2> NF0 то КFL1= KFL2=1
б) Определяем допускаемое напряжение изгиба []F01 и []F02 соответствующее пределу изгибной выносливости при числе циклов перемены напряжений NF0:
для шестерни []F01=103 НВ=370 Нмм2
для колеса []F02=103 НВ2ср=103×2855=294065 Нмм2
в) определяем допускаемые напряжения изгиба для зубьев шестерни []F1 и колеса []F2:
для шестерни []F1= КFL1[]F01=1×370=370 Нмм2
для колеса []F2= KFL2[]F02=1×294065=294065 Нмм2
цилиндрическая зубчатая передача рассчитывается по меньшему значению []F и из полученных для шестерни [s]F1и колеса []F2 т.е. по менее прочным зубьям
Расчет зубчатых передач редукторов.
Расчет закрытой цилиндрической зубчатой передачи.
1.Определяем главный параметр – межосевое расстояние aw мм.
а) Ka – вспомогательный коэффициент для косозубых передач Ka=43;
б) - коэффициент ширины венца колеса равный 028 036 – для шестерни расположенной симметрично относительно опор в проектируемых нестандартных одноступенчатых цилиндрических редукторах;
в) u – передаточное число редуктора или открытой передачи u=3;
г) Т2 – вращающий момент на тихоходном валу при расчете редуктораН×м;
д) [s]н – допускаемое контактное напряжение колеса с менее прочным зубом;
е) Кнb - коэффициент неравномерности нагрузки по длине зуба. Для прирабатывающихся зубьев
По ГОСТу 6636-69 «Нормальные линейные размеры» принимаем aw=125мм.
2. Определяем модуль зацепления m мм:
где а) Кm – вспомогательный коэффициент. Для косозубых передач Кm=5.8;
б) - делительный диаметр колеса мм;
в) - ширина венца колеса мм;
г) []F – допускаемое напряжение изгиба материала колеса с менее прочным зубом Нмм2;
Принимаем стандартное значение m = 15мм.
3. Определяем угол наклона зубьев :
4. Определение суммарного числа зубьев шестерни и колеса:
5. Уточняем действительную величину угла наклона зубьев:
6. Определяем число зубьев шестерни:
7. Определяем число зубьев колеса:
8. Определяем фактическое передаточное число uф и проверяем его отклонение Du от заданного u:
9. Определяем фактическое межосевое расстояние:
10. Определяем фактические основные геометрические параметры передачи мм:
11. Проверяем межосевое расстояние:
12. Проверяем пригодность заготовок колес. Условие пригодности заготовки колес:
Dзаг ≤ Dпред Sзаг ≤ Sпред.
Диаметр заготовки шестерни
Толщина диска заготовки колеса закрытой передачи
13. Проверяем контактные напряжения Н Нмм2:
а) K – вспомогательный коэффициент К=376;
б) - окружная сила в зацеплении Н;
в) КНa - коэффициент учитывающий распределение нагрузки между зубьями. КНa=116
г) КHv – коэффициент динамической нагрузки зависящий от окружной скорости колес и степени точности передачи. КHv=1.01
Допускаемая недогрузка т.к. 10% условие прочности выполняется.
14. Проверяем напряжения изгиба зубьев шестерни F1 и колеса F2 Нмм2:
где а) КFa=1 – коэффициент учитывающий распределение нагрузки между зубьями;
б) КFv=1.04 – коэффициент динамической нагрузки зависящий от окружной скорости колес и степени точности передачи;
в) KF=1 – коэффициент неравномерности нагрузки по длине зуба;
г) Находим эквивалентные числа зубьев шестерни: и колеса ;
Затем находим коэффициенты формы зуба шестерни: и колеса
д) - коэффициент учитывающий наклон зуба;
е) []F2 - допускаемые напряжения изгиба шестерни и колеса.
[] что допустимо так как нагрузочная способность большинства зубчатых передач ограничевается контактной прочностью.
Межосевое расстояние aw
Угол наклона зубьев
Диаметр делительной окружности:
Ширина зубчатого венца:
Диаметр окружности вершин:
Диаметр окружности впадин:
Допускаемые значения
Контактные напряжения Н Нмм2
Напряжение изгиба Нмм2
Расчет клиноременной передачи
1. Выбираем сечение ремня
Выбор сечения ремня производим по номограмме в зависимости от мощности передаваемой ведущим шкивом Р1=3.0 кВт и его частоты вращения n1=955 обмин.
Таким образом выбираем сечение ремня А (нормальное).
2. Определяем минимально допустимый диаметр ведущего шкива d1min
В зависимости от вращающего момента на валу двигателя и сечения ремня:
3. Задаемся расчетным диаметром ведущего шкива
4. Определяем диаметр ведомого шкива d2 мм:
где u – передаточное число ременной передачи;
=0.01 0.02 - коэффициент скольжения
5.Определяем фактическое передаточное число uф и проверяем его отклонение u от заданного u:
6. Определяем ориентировочное межосевое расстояние a мм:
7. Определяем расчетную длину ремня l мм:
8. Уточняем значение межосевого расстояния по стандартной длине:
9. Определяем угол обхвата ремнем ведущего шкива α1 град.:
10. Определяем скорость ремня v мс:
11. Определяем частоту пробегов ремня U с-1:
12. Определяем допускаемую мощность передаваемую одним клиновым ремнем кВт:
где =071 - допускаемая приведенная мощность передаваемая одним клиновым ремнем кВт;
- коэффициент динамичности нагрузки и длительности работы;
9 – коэффициент угла обхвата α1 на меньшем шкиве;
=1 – коэффициент влияния отношения расчетной длины ремня к базовой;
=090 – коэффициент числа ремней в комплекте клиноременной передачи;
13. Определяем количество клиновых ремней Z;
14. Определяем силу предварительного натяжения F0 Н:
15. Определяем окружную силу передаваемую комплектом клиновых ремней Ft Н:
16.Определяем силы натяжения ведущей F1 и ведомой F2 ветвей Н:
17. Определяем силу давления ремней на вал Fоп Н:
18. Проверяем прочность одного клинового ремня по максимальным напряжениям в сечении ведущей ветви Нмм2:
Нмм2 – напряжение растяжения;
А=81мм2 – площадь поперечного сечения ремня;
Нмм2 – напряжение изгиба;
Е=80 100 Нмм2 – модуль продольной упругости при изгибе для прорезиненных ремней;
Нмм2 – напряжение от центробежных сил;
кгм3 – плотность материала ремня;
Нмм2 – допускаемое напряжение растяжения;
[] условие прочности выполняется
19. Параметры клиноременной передачи:
Частота пробегов ремня U 1с
Диаметр ведущего шкива d1
Диаметр ведомого шкива d2
Межосевое расстояние а
Максимальное напряжение Нмм2
Предварительное натяжение ремня F0 Н
Угол обхвата малого шкива α1 град
Сила давления ремня на вал Fоп Н
Нагрузки валов редуктора
1. Определение сил в зацеплении закрытых передач
Угол зацепления принят
Цилиндрическая косозубая
2. Определение консольных сил
Вид открытой передачи
Характер силы по направлению
На быстроходном валу
Разработка чертежа общего вида редуктора
1. Выбор материала валов
Выбираем термически обработанную среднеуглеродистую сталь 45 одинаковую для быстроходных и тихоходных валов: Нмм2 Нмм2 Нмм2.
2. Выбор допускаемых напряжений на кручение
Меньшее значение - для быстроходных валов большее - для тихоходных.
3. Определение геометрических параметров ступеней вала:
Ступень вала и ее размеры dl
-ая под элемент открытой передачи или полумуфту
мм где Mk=T – крутящий момент равный вращающему моменту на валу
-ая под уплотнение крышки с отверстием и подшипник
мм t – высота буртика
-я под шестерню колесо
мм где r – фаска подшипника
l3=78 – определяется графически
4. Предварительный выбор подшипников качения
Для тихоходного вала: Cредняя серия 309 D=100мм В=25мм r=25мм d=30мм Сr=527кН С0=30кН;
для быстроходного вала: Средняя серия 306 D=72мм В=19мм r=2мм d=30мм Сr=29.1кН С0=14.6кН
Расчетная схемы валов редуктора
Расчётная схема тихоходного и быстроходного валов редуктора даётся в приложении курсового проекта.
Проверочный расчет подшипников
Пригодность подшипников определяется сопоставлением расчетной динамической грузоподъемности Н с базовой Н или базовой долговечности ч ( млн. оборотов) с требуемой ч по условиям:
Расчетная динамическая грузоподъемность Н и базовая долговечность ч определяются по формулам:
где эквивалентная динамическая нагрузка Н;
m – показатель степени: m=3 – для шариковых подшипников m=333 – для роликовых подшипников;
коэффициент надежности при безотказной работе подшипников ;
коэффициент учитывающий влияние качества подшипника и качества его эксплуатации; при обычных условиях работы подшипника для шариковых подшипников; для роликовых конических подшипников;
n – частота вращения внутреннего кольца подшипника соответствующего вала обмин.
1. Проверочный расчет подшипников быстроходного вала
Проверить пригодность радиального шарикового однорядного подшипника 306 быстроходного вала цилиндрического редуктора работающего с умеренными толчками и вибрацией. Осевая сила в зацеплении Н. Реакции в подшипниках 196823Н 137147 Н. Характеристика подшипников: C=29100 Н C=14600 Н Х=056 V=1 . Требуемая долговечность ч. Подшипники установлены по схеме 3 (враспор).
Определяем коэффициент влияния осевого напряжения:
Так как () то интерполированием находим e=022 Y=199.
По соотношению выбираем соответствующие формулы для определения :
По значению эквивалентной нагрузки определяем динамическую грузоподъемность Н:
Определяем долговечность подшипника ч:
Подшипник не пригоден возьмем другой.
Проверить пригодность радиального шарикового однорядного подшипника 406 быстроходного вала цилиндрического редуктора работающего с умеренными толчками и вибрацией. Осевая сила в зацеплении Н. Реакции в подшипниках 196823Н 137147 Н. Характеристика подшипников: C=47000 Н C=26700 Н Х=056 V=1 . Требуемая долговечность ч. Подшипники установлены по схеме 3 (враспор).
Так как () то интерполированием находим e=019 Y=230.
Подшипник пригоден т.к.
2. Проверочный расчет подшипников тихоходного вала
Проверить пригодность радиального шарикового однорядного подшипника 309 быстроходного вала цилиндрического редуктора работающего с умеренными толчками и вибрацией. Осевая сила в зацеплении Н. Реакции в подшипниках 352035Н 8326 Н. Характеристика подшипников: C=52700 Н C=30000 Н Х=056 V=1 . Требуемая долговечность ч. Подшипники установлены по схеме 3 (враспор).
3 Основные размеры и эксплуатационные характеристики подшипников
Составить табличный ответ к задаче 9 (табл. 9.1).
Таблица 9.1 Основные размеры и эксплуатационные характеристики подшипников
Принят предварительно
Конструктивная компоновка привода
1. Конструирование зубчатых колес.
а) конструирование зубчатых колес цилиндрического редуктора.
Принимаем параметры колеса по таблице 10.1.
Таблица 10.1. Параметры колеса.
Диаметр внутренний мм
Радиусы закруглений и уклон мм
На торцах зубьев выполняем фаски размером . Принимаем . Угол фаски .
2. Конструирование валов
Диаметры и длины ступеней валов определены при предварительном проектном расчете в задаче 7. Конструируя валы уточняем размеры посадочных поверхностей в зависимости от конструкции и размеров деталей установленных на вал с учетом их расположения относительно опор.
2.1. Быстроходный вал.
Принимаем выходной конец вала цилиндрическим. По табл.10.8 принимаем d=25 мм l=30 мм r=16 мм c=1 мм.
Диаметр второй и четвертой ступени определяем по внутреннему диаметру окончательно выбранного для вала подшипника 309: мм.
Диаметр третьей ступени .
2.2. Тихоходный вал.
Принимаем выходной конец вала цилиндрическим. По табл.10.8 принимаем d=40 l=40 r=20 c=16.
Диаметр ступени принимаем равным диаметру внутреннего кольца подшипника 406 окончательно выбранного в задаче 9. Длина ступени зависит от осевых размеров деталей входящих в конструкцию подшипникового узла и окончательно будет принята при выборе этих деталей.
Длину третьей ступени принимаем исходя из условия . Принимаем мм.
Для соединения быстроходного вала с элементом открытой передачи а также тихоходного вала с муфтой используем шпоночное соединение а для соединения колеса редуктора с 3-й ступенью тихоходного вала используем соединение с натягом.
Используем призматические шпонки изготовленные из стали 45. Длину шпонки выбираем из стандартного ряда Ra40 исходя из длину ступицы насаживаемой детали. Сечение шпонки выбираем в зависимости от диаметра соответствующей ступени по табл.К42.
Принимаем для шпоночного соединения тихоходного вала с муфтой – шпонку длиной мм мм; для шпоночного соединения быстроходного вала с элементом открытой передачи – шпонку длиной мм мм.
Соединение с натягом. Эти соединения имеют упрощенную технологию изготовления за счет отсутствия шпонки и двух пазов в сопрягаемых деталях; они нечувствительны к реверсивным нагрузкам хорошо воспринимают динамические нагрузки. Исключают ослабление вала шпоночным пазом. Недостаток этих соединений трудоемкость сборки сложность контроля качества соединения.
Расчет (подбор) посадки с натягом для цилиндрического колеса с 3-й ступенью тихоходного вала проводится в следующем порядке.
а) Среднее контактное давление на посадочной поверхности:
где К—коэффициент запаса сцепления деталей (в зависимости от
ответственности соединений принимают К = 2 45). Для валов с
консольной нагрузкой принимают: К= 35— на конце тихоходного вала шестерня;
f=008 —коэффициент трения;
Т=1188 Нм—вращающий момент;
б) Коэффициенты С1и С2
где d=56мм—посадочный диаметр; d2—диаметр отверстия охватываемой детали (для сплошного вала d2=0); d2=86мм—диаметр охватывающей детали (наружный диаметр ступицы колеса);
—коэффициенты Пуассона охватываемой и охватывающей деталей.
в) Деформацию деталей Δ мкм:
где Е1 и E2—модули упругости материалов охватываемой (материал тихоходного вала – сталь) и охватывающей деталей (материал колеса – безоловянистая бронза)Нмм2.
г) Поправка на обмятие микронеровностей u мкм:
Предварительно принимается точность изготовления вала и отверстия соответствующая 8-му квалитету. Таким образом принимаем Ra1=16 и Ra2=16
где Ra1 и Ra2 - арифметические отклонения профиля микронеровностей
посадочных поверхностей отверстия и вала.
д) Определить минимальный требуемый натяг:
ж) Максимальное контактное давление допускаемое прочностью охватывающей детали:
где т -- предел текучести материала охватывающей детали (колесо)
е) Максимальная деформация соединения допускаемая прочностью охватывающей детали:
и) Максимальный допускаемый натяг соединения гарантирующий прочность охватывающей детали:
ж) По значениям [N]МАХ и [N]МIN выбирается стандартная посадка у которой
Выбрана посадка Н7t6
и) Давление от максимального натяга выбранной посадки :
к) Для выбранной посадки сила запрессовки детали составит:
где fп — коэффициент трения при прессовании;
Таким образом для сборки соединения требуется пресс развивающий силу 200 кН.
4.Конструирование подшипниковых узлов.
Типы подшипников подобраны в задаче 7 и их пригодность проверена в задаче 9.
Выбираем схему 3: осевое фиксирование вала в двух опорах – враспор. Рис 10.4.
Возможность регулировки подшипников.
Простота конструкции опор(отсутствие стаканов и других дополнительных деталей).
Вероятность защемления тел качения в опорах вследствие температурных деформаций.
Более жесткие допуски на осевые размеры вала и ширину корпуса.
Уплотнительные устройства применяют для предотвращения вытекания смазочного материала из подшипникового узла а также защиты от пыли грязи и влаги. Выбираем наружные манжетные уплотнения. Их используют при смазывании подшипников как густым так и жидким материалом при низких и средних скоростях так как они оказывают сопротивление вращению вала.(рис.10.5)
Подшипники качения могут быть собраны в узле с различными радиальными и осевыми зазорами. Под радиальным е или осевым а зазором понимают полную величину радиального или осевого перемещения в обоих направлениях одного кольца подшипника относительно другого под действием определенной силы или без нее.
Нерегулируемые типы подшипников (например радиальные шариковые) изготавливают с небольшими зазорами: после установки на вал и в корпус они могут работать без дополнительной регулировки (рис. 10.6.)
5.Конструирование корпуса редуктора.
рис.10.6.Корпус цилиндрического одноступенчатого редуктора.
Рис.10.7. Форма корпуса одноступенчатого горизонтального редуктора.
а)габаритные размеры корпуса одноступенчатого цилиндрического редуктора
б)Толщина стенок корпуса и ребер жесткости. В проектируемом редукторе толщина стенок крышки и основания корпуса принимаются одинаковыми :
в)Фланцевые соединения.
Диаметр d болтов фланцев:
Диаметр болта(винта) фланца.
Конструктивные элементы фланца: К—ширина; С —- координата оси отверстия под винт (болт); D0 и Ь0—диаметр и высота опорной поверхности под головку винта (болта); d0—диаметр отверстия под винт (болт).
а) Фундаментный фланец основания корпуса. Предназначен для крепления редуктора к фундаментной раме (плите). Опорная поверхность фланца выполняется в виде двух длинных параллельно расположенных или четырех небольших платиков. Места крепления располагают на возможно большем (но в пределах корпуса) расстоянии друг от друга L ширина ; высота . Проектируемые редукторы крепятся к раме (плите) четырьмя болтами (шпильками) расположенными в нишах корпуса.; высота ниш при креплении шпильками болтами. Форма ниши (угловая или боковая) определяется размерами формой корпуса и расположением мест крепления. По возможности корпус крепится к раме (плите) болтами снизу что исключает необходимость конструирования ниши.
б) Фланец подшипниковой бобышки крышки и основания корпуса. Предназначен для соединения крышки и основания разъемных корпусов. Фланец расположен в месте установки стяжных подшипниковых болтов (винтов) на продольных длинных сторонах корпуса: в крышке - наружу от ее стенки в основании — внутрь от стенки.
в) Соединительный фланец крышки и основания корпуса.
Разъемный корпус. Для соединения крышки корпуса с основанием по всему контуру разъема выполняют соединительный фланец. На коротких боковых сторонах крышки и основания корпуса не соединенных винтами фланец расположен внутрь корпуса и его ширина К3 определяется от наружной стенки; на продольных длинных сторонах соединенных винтами d3 фланец располагается: в крышке корпуса — наружу от стенки в основании — внутрь.
Количество соединительных винтов пг и расстояние между ними L3 принимают по конструктивным соображениям в зависимости от размеров продольной стороны редуктора и размещения подшипниковых стяжных винтов. При сравнительно небольшой длине продольной стороны можно принять d3 = d2 и h3 = h2 и поставить один-два соединительных винта. При длинных продольных сторонах принимают для болтов для винтов а количество винтов (болтов) п3 и расстояние между ними L3 определяют конструктивно . Соединительные винты (болты) можно разместить в боковых нишах.
г) Фланец для крышки подшипникового узла. Отверстие подшипникового узла неразъемной подшипниковой бобышки закрывается торцовой крышкой на винтах. В комплекте деталей подшипникового узла разъемных корпусов чаще применяется врезная крышка .
Винт d4 торцовой крышки и ширина расточки f под врезную крышку.
Диаметр наружного кольца подшипника.
д) Фланец для крышки смотрового окна. Размеры сторон фланца количество винтов n5 и расстояние между ними L5 устанавливают конструктивно в зависимости от места расположения окна и размеров крышки; высота фланца мм.
е) Опорные платики. Для прикрепления к корпусу сливных пробок отдушин маслоуказателеи на крышке и основании корпуса предусмотрены опорные платики (фланцы). Размеры сторон платиков должны быть на величину с = 3 5 мм больше размеров опорных поверхностей прикрепляемых деталей. Высота платика h=c.
Детали и элементы корпуса редуктора
а) Смотровой люк. Служит для контроля сборки и осмотра редуктора при эксплуатации. Для удобства осмотра его располагают на верхней крышке корпуса что позволяет также использовать люк для заливки масла. Смотровой люк делают прямоугольной или (реже) круглой формы максимально возможных размеров.
Люк закрывают крышкой. Для того чтобы внутрь корпуса извне не засасывалась пыль под крышку ставят уплотняющие прокладки из картона (толщиной 1 15 мм) или полосы из резины (толщиной 2 3 мм). Если с такой крышкой совмещена пробка-отдушина то ее приваривают к ней или прикрепляют развальцовкой. На рис.10.8. приведена крышка совмещенная с отдушиной.
Рис.10.8.Крышка люка редуктора.
Рис. 10. 9 Крышка люка редуктора с колпачковой отдушиной.
б) Установочные штифты.
Фиксирующие конические штифты располагают наклонно или вертикально в зависимости от конструкции фланца. Там где невозможно применение конических штифтов встык соединения ставят со стороны каждой стенки по одному (всего четыре) цилиндрическому штифту. Диаметр штифта диаметр соединительного винта.
Рис.10.10.Фиксирование крышки корпуса штифтами.
в) Отжимные винты. Уплотняющее покрытие плоскости разъема склеивает крышку и основание корпуса. Для того чтобы обеспечить их разъединение при разборке рекомендуют применять отжимные винты которые ставят в двух противоположных местах крышки корпуса.
г) Проушины. Для подъема и транспортировки крышки корпуса и собранного редуктора применяют проушины отливая их заодно с крышкой. Проушина выполнена в виде сквозного отверстия в корпусе.
6.Конструирование элементов открытых передач.
dе1 = 2 · t + dр1 =66 +180=1866
B = (z - 1) · р + 2 · f = 1·15+2·10=35
dст = 155 · d1 = 25·155=40
lст = 12 · d1 = 25·12=30
C = (12 13) = 12·10=12
Для соединения выходного конца тихоходного вала редуктора и приводного вала рабочей машины применена муфта упругая втулочно-пальцевая. Муфта проста по конструкции и обладает высокой податливостью что позволяет применять её при переменных ударных нагрузках а также при значительных кратковременных перегрузках.
Основной характеристикой для выбора муфты является номинальный вращающий момент Т Н·м. муфты выбираются по большому диаметру концов соединяемых валов и расчетному моменту Тр который должен быть в пределах номинального:
где Кр – коэффициент режима нагрузки
Т – номинальный момент Т = 500 Н·м
Материал полумуфты — сталь СтЗ (ГОСТ 380—88); материал упругой оболочки — резина с пределом прочности при разрыве не менее 10 Нмм2.
8.Смазывание. Смазочные устройства.
Смазывание зубчатых зацеплений и подшипников применяют в целях защиты от коррозии снижения коэффициента трения уменьшения износа отвода тепла и продуктов износа от трущихся поверхностей снижения шума и вибраций.
Смазывание зубчатого зацепления.
а)Способ смазывания. Для редукторов общего назначения применяют непрерывное смазывание жидким маслом картерным непроточным способом (окунание).
б)Выбор сорта масла. Зависит от значения расчетного контактного напряжения в зубьях н и фактической окружной скорости колес v.
Контактное напряжение н Нмм2
Окружная скорость v мс
в)Определение количества масла. Для одноступенчатых редукторов при смазывании окунанием объем масляной ванны определяется из расчета 04 08 л масла на 1кВт передаваемой мощности. Для данного редуктора мощностью 3 кВт – 12 л масла.
Уровень масла определяем по формуле
г) Контроль уровня масла.
Уровень масла находящегося в корпусе редуктора контролируют различными маслоуказателями. В проектируемом приводе устанавливается круглый маслоуказатель (рис.10.12). Круглые маслоуказатели удобны для корпусов расположенных достаточно высоко над уровнем пола. В них через нижнее отверстие в стенке корпуса масло проходит в полость маслоуказателя; через верхнее отверстие маслоуказатель сообщается с воздухом в корпусе редуктора.
Рис.10.12 Круглый маслоуказатель
При работе передач масло постепенно загрязняется продуктами износа деталей передач. С течением времени оно стареет свойства его ухудшаются. Поэтому масло налитое в корпус редуктора периодически меняют. Для этой цели в корпусе предусматривают сливное отверстие закрываемое пробкой с конической резьбой (рис.10.13).
Рис.10.13 Пробка с цилиндрической резьбой.
При длительной работе в связи с нагревом масла и воздуха повышается давление внутри корпуса. Это приводит к просачиванию масла через уплотнения и стыки. Чтобы избежать этого внутреннюю полость корпуса сообщают с внешней средой путем установки отдушины в его верхних точках. В проектируемом приводе конструируют пробку – отдушину (рис.15).
Рис.10. 14Пробка-отдушина.
1. Проверочный расчет шпонок.
Призматические шпонки в редукторе проверяют на смятие. Проверке подлежит шпонка на быстроходном валу – под элементом открытой передачи.
а)Определяем площадь смятия
б)Проверяем условие прочности
Шпонка удовлетворяет требованиям.
2. Проверочный расчет стяжных винтов подшипниковых узлов.
Проверить прочность стяжных винтов подшипниковых узлов тихоходного вала редуктора. Максимальная реакция в вертикальной плоскости опоры подшипника Н. Диаметр винта мм шаг резьбы крупный ; класс прочности 5.6 из стали 30 по ГОСТ 11738-84.
Определяем силу приходящуюся на один винт:
Принимаем (постоянная нагрузка); (соединение чугунных деталей без прокладок).
Определяем механические характеристики материала винтов: предел прочности Нмм2; предел текучести Нмм2; допускаемое напряжение Нмм2.
Определяем расчетную силу затяжки винтов
Определяем площадь опасного сечения винта
Определяем эквивалентные напряжения
Поскольку условие прочности болтов подшипниковых соединений выполняется.
3. Проверочный расчет валов
Проверочный расчет валов на прочность выполняется на совместное действие изгиба и кручения. При этом расчет отражает разновидности цикла напряжений изгиба и кручения усталостные характеристики материалов размеры форму и состояние поверхности валов. Цель расчета – определить коэффициенты запаса прочности в опасных сечениях вала и сравнить их с допускаемыми:
Для быстроходного вала.
Определить напряжения в опасных сечениях вала Нмм.
Нормальные напряжения изменяются по симметричному циклу при котором амплитуда напряжений равна расчетным напряжениям изгиба :
где М – суммарный изгибающий момент в рассматриваемом сечении
осевой момент сопротивления сечения вала мм.
Определить касательные напряжения которые изменяются по нулевому циклу при котором амплитуда цикла равна половине расчетных напряжений кручения :
где крутящий момент Нм;
полярный момент инерции сопротивления сечения вала мм.
Определить коэффициент концентрации нормальных и касательных напряжений для расчетного сечения вала:
где и эффективные коэффициенты концентрации напряжений;
коэффициент влияния абсолютных размеров поперечного сечения;
коэффициент влияния шероховатости;
коэффициент влияния поверхности упрочнения
Определить пределы выносливости в расчетном сечении вала Нмм:
где и пределы выносливости гладких образцов при симметричном цикле изгиба и кручения Нмм;
Определить коэффициенты запаса прочности по нормальным и касательным напряжениям:
Определить общий коэффициент запаса прочности в опасном сечении:
Условие выполняется .
Для тихоходного вала.
где М – суммарный изгибающий момент в рассматриваемом сечении Нм;
где крутящий момент Н·м;
Как показала практика проектирования валов одноступенчатых редукторов на чистое кручение проверочные расчеты на прочность повсеместно дают удовлетворительные результаты
4. Тепловой расчет редуктора
Определяем температуру масла в корпусе редуктора при непрерывной работе без искусственного охлаждения:
Вт(м2*град) – коэффициент теплопередачи;
м2 (принимаем по табл.11.6 в зависимости от мм).
Температура в проектируемом редукторе удовлетворяет требованиям так как не превышает допускаемой .
Расчет технического уровня редуктора
1 Определение массы редуктора.
где - коэффициент заполнения;
- условный объем редуктора мм3;
- плотность чугуна кгмм3;
По графику на рис.12.1 определяем для аw=125 мм .
2 Определение критерия технического уровня редуктора.
3. Технический уровень редуктора.
технический уровень редуктора низкий
Список использованной литературы
Шейнблит А.Е. Курсовое проектирование деталей машин. – Калининград: Янтарный сказ 2005 – 456 c.
Кудрявцев В.Н Курсовое проектирование деталей машин 1984г. -400с.
Проектирование рам и корпусных деталей приводов машин: метод. указ. к курс. и диплом. проектированию по деталям машин и основам проектирования ПГУПС Каф. "Теория механизмов и робототехнические системы"; сост.: Р. Д. Сухих [и др.]. - СПб. : ПГУПС 2005. - 45 с.
Спецификация 1.doc
Редуктор цилиндрический
Средняя часть корпуса
Подшипник ГОСТ8338-75
Винт А.М6-6g 12.48 ГОСТ 17473-84
Штифт 6 36 ГОСТ 9464-79
Штифт 6 18 ГОСТ3128-70
Шпонка 8 7 18 ГОСТ 23360-78
Шпонка 8 7 25 ГОСТ 23360-78
Рекомендуемые чертежи
- 17.03.2025
Свободное скачивание на сегодня
- 29.08.2014
- 24.01.2023