Предприятие по ремонту машин




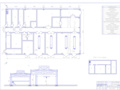
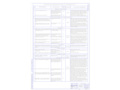
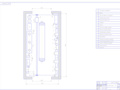
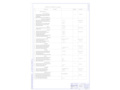
- Добавлен: 25.10.2022
- Размер: 3 MB
- Закачек: 0
Описание
Состав проекта
![]() |
![]() ![]() ![]() ![]() |
![]() ![]() ![]() |
![]() ![]() ![]() ![]() |
![]() ![]() ![]() ![]() |
![]() ![]() |
![]() ![]() ![]() |
![]() ![]() ![]() ![]() |
![]() ![]() |
![]() ![]() |
![]() ![]() |
Дополнительная информация
korpus.dwg

Агрегатно-технический участок
Электротехнический участок
Топливно-аппаратурный
Шиномонтажный и вулканизационный
Кузнечно-рессорный и сборочный
Склад запчастей и инструментов
Участок мойки узлов и деталей
Административое помещение
Туалеты и умывальники
Четра Т11-00.00.000 ТХ
Производственный корпус
rrrrrrr.doc
Реализация новых технологий предусматривает использование зарубежной и отечественной техники рациональная эксплуатация которой определяется выбором топливосмазочных материалов и технических жидкостей. Их взаимосвязь строго регламентируется основой (минеральной синтетической) и присадками по номенклатуре и количеству.
При производстве строительных работ многие операции могут выполняться разными типоразмерами машин. Современный подход к оценке эффективности применения конкретных машин и (или) комплексов определяется с учетом таких технико-экономических показателей как производительность количество рабочего времени себестоимость машино-часа себестоимость механизированных работ себестоимость единицы продукции прибыль и рациональная область использования отдельных машин комплектов и комплексов.
Строительные дорожные и подъемно-транспортные машины и оборудование составляют основу комплексной механизации автоматизации и роботизации строительного производства. Эффективность контроля во многом определяется правильной технической эксплуатацией. Затраты на поддержание сохранение и восстановление работоспособности строительно-дорожных машин составляет (СДМ) 25 % себестоимости машиночаса эксплуатации а за срок службы они в 6 – 10 раз превосходят стоимость новой при трудоемкости изготовления до 5 и до 95 % на поддержание и восстановление их работоспособности.
Основная задача технической эксплуатации СДПТМиО – реализация потенциальных возможностей конструкции при наименьших затратах на поддержание работоспособности и минимальных вредных воздействиях на окружающую среду. Для ее решения необходимо изучать закономерности изменения технического состояния СДПТМиО под воздействием различных факторов в процессе их эксплуатации что позволяет управлять работоспособностью машин на научной основе. Правила технической эксплуатации должны предусматривать при этом снижение загрязнения окружающей среды выхлопными газами и топливосмазочными материалами (ТСМ) при испарении и попадании их в грунт.
В процессе технической эксплуатации важны вопросы управления работоспособностью машин. Управление техническим состоянием машины предусматривает организацию технических обслуживаний (ТО) и ремонтов и ее связь с диагностированием машин; применение ТСМ и запасных частей при научно обоснованном нормировании; совершенствование технологических процессов ТО и ремонтов включая проектирование предприятий по их технической эксплуатации; информацию об эксплуатационной надежности машин; организацию хранения подготовку к работе и транспортировку машин на объект и на предприятия по ТО и ремонту.
Использование машин в настоящее время требует более строгой оценки экологических последствий и ожидаемого экономического эффекта. Машины с двигателем внутреннего сгорания (ДВС) являются источником загрязнения атмосферы вредными веществами. За 1 ч работы ДВС может выделить такое количество только оксида углерода которого достаточно для загрязнения около 10 млн м3. Для снижения концентрации вредных составляющих в отработавших газах необходимо эксплуатировать технику в исправном состоянии.
Строительство или восстановление автомобильной дороги является сложными высокомеханизированным организационно-технологическим процессом с большим количеством единиц техники. Отказ одной машины (особенно ведущей) приводит к снижению эффективности строительного производства.
Для оценки работоспособности машины и обеспечения ее безотказной работы на объекте особое внимание уделяется вопросам диагностирования.
Все инженерные решения по внедрению новых технологий машин и материалов обосновываются с учетом технико-экономических показателей.
Знание теоретических положений и практические навыки по эксплуатации СДПТМ обеспечивают будущим молодым специалистам возможность проектировать и эффективно использовать машины в строительном производстве.
Анализ и выбор технологий строительства и ремонта автомобильной дороги
На сегодняшний день применяются следующие технологии для строительства и ремонта автомобильных дорог:
Армирующие и разделительные прослойки из геосинтетических материалов в конструкциях нежестких дорожных одежд.
Описание технологии и область применения
Армирующие и разделительные прослойки из геосеток (георешеток) применяют на границе контакта «несущее основание из неукрепленного зернистого материала – песчаный подстилающий слой» на дорогах I-III технических категорий с интенсивностью движения накопленных осей за срок службы от 375 000 и выше для снижения толщины щебеночного основания и для препятствия взаимопроникновению материалов смежных слоев. Разделительные прослойки из геотекстильных полотен предназначены для препятствия вза- имопроникновению материалов смежных слоев а также для предотвращения заиливания дрени- рующих слоев земляного полотна. Могут применяться как на границе контакта основания из щеб- ня или щебеночно-гравийно-песчаной смеси и песчаного подстилающего слоя так и на границе контакта дренирующего слоя из песка и грунта земляного полотна.
Технико-экономический эффект преимущество над аналогами
Армирование щебеночного основания позволяет исключить взаимопроникновение щебня и песка (особенно при вибрационном уплотнении) повысить несущую способность всей конструк- ции дорожной одежды в целом не увеличивая ее материалоемкость или уменьшить толщину слоя из фракционированного щебня обеспечивая при этом требуемые параметры по прочности кон- струкции. Применение разделительной прослойки из нетканого геотекстильного полотна предотвра- щает взаимопроникновение материала щебеночного основания и песка подстилающего слоя обеспечивает дренаж воды попадающей на прослойку через материал обочины и дорожную одежду или грунтовой воды попадающей в зону прослойки за счет капиллярного поднятия или 3 отжатия ее из грунта земляного полотна при его оттаивании под действием транспорта исключает загрязнение каменного материала основания или песка дренирующего слоя тонкодисперсными грунтовыми частицами перемещающимися под действием движения грунтовых вод. Применение армирующей или разделительной прослойки под щебеночным основанием поз- воляет отказаться от устройства технологического слоя.
Автомобильные дороги: М-4 Минск – Могилев км 640 - км 740 км 16810 - км 18005; Р-28 Минск – Молодечно – Нарочь км 195 - км 198; Р-110 Глубокое – Поставы – Лынтупы – гр. Литовской Республики км 704 – км 718; пр. Победителей в г. Минске (участок от ул. 4-е Кольцо до МКАД).
Наличие нормативного документа
ДМД 02191.2.045-2011 «Рекомендации по применению геосинтетических материалов в нижних слоях нежестких дорожных одежд».
Технология устройства тонкослойного фрикционного износостойкого защитного покрытия «Тонфриз-Слой»
Рекомендуется к использованию на дорожных покрытиях обладающих достаточной несущей способностью но при этом характеризующихся наличием: прогрессирующей сетки трещин отдельных редких и частых трещин; шелушения поверхности покрытия; незначительной относительно стабилизировавшейся колейности; ранее отремонтированных выбоин (заплат) ухудшающих ровность дороги и комфортность проезда. Также используется на тех покрытиях где параметры шероховатости не обеспечивают требуемые сцепные качества. Принцип технологии устройства тонкого фрикционного слоя износа состоит в обеспечении высокоскоростной (10 ммин) укладки слоя горячей асфальтобетонной смеси подобранного гранулометрического состава поверх тонкого связующего слоя из модифицированной эмульсии (или битума) распределенных непосредственно перед укладкой. Обе операции производятся за один проход специального асфальтоукладчика марки Vge - повышенным содержанием крупного наполнителя (до 70 % щебня). Кроме того в технологии реализовывается эффект поднятия (с заполнением пор на 23 толщины слоя) полимербитумного вяжущего распределяемого непосредственно перед укладкой смеси (с дальнейшей его работой как составляющего в образуемом слое износа). При этом обеспечивается когезия и прочная связь укладываемого слоя с существующим основанием.
Покрытие очень гомогенно и благодаря характерной текстуре а также достигаемой ровности обладает следующими преимуществами: повышаются сцепные качества покрытия вследствие чего снижается уровень шума от проезжающих автомобилей; в слякотную погоду уменьшается разбрызгивание колесами автомобиля воды и грязи что способствует улучшению видимости для водителей автомобилей; влияние обледенения и гололедицы на сцепные качества покрытия «ТОНФРИЗ-СЛОЙ» проявляется значительно позже в сравнении с другими типами покрытий. При этом в силу высокого содержания щебня данная технология с успехом может применяться на грузонапряженных магистралях а расчетный срок службы покрытия «ТОНФРИЗ-СЛОЙ» для магистралей – до 8 лет. Движение можно открывать непосредственно после окончания уплотнения (при температуре уложенного слоя не выше 85 °С).
Применяется с 2007 года на автомобильной дороге М-1Е30 Брест – Минск – граница Россий- ской Федерации.
ДМД 02191.2.024-2009 «Рекомендации по устройству тонких фрикционных износостойких защитных слоев из горячих асфальтобетонных смесей с применением модифицированных вяжущих».
Покрытие из асфальтобетонной смеси с резиновой крошкой
Технологический процесс приготовления резиноасфальтобетонной смеси аналогичен технологии приготовления асфальтобетонной щебеночно-мастичной смеси. Резиновую крошку в смеситель подают по линии подачи целлюлозного волокна одновременно с минеральными материала- ми. Температура смеси на выходе из смесителя должна составлять 190 0 С-200 0 С при укладке - 60 0 С-180 0 С. Содержание резиновой крошки фракции от 03 до 05 мм составляет 2 % от массы сме-си. Технология применяется для устройства покрытий автомобильных дорог общего пользования и гидроизоляционных покрытий искусственных сооружений.
Применение в составе асфальтобетонной смеси резиновой крошки способствует повышению водонепроницаемости деформативности и трещиностойкости асфальтобетонного покрытия. Экономический эффект от использования покрытий из резиноасфальтобетона достигается за счет увеличения срока службы покрытия.
Мост через р. Воложинку на автомобильной дороге М-6 Минск – Гродно – граница Республики Польша км 9166; автомобильная дорога М-10 граница Российской Федерации – Гомель – Кобрин км 423 – км 427; мостовой переход через р. Нача на автомобильной дороге Р-14 Полоцк – Миоры – Браслав км 20598; автомобильная дорога Р-71 Могилев – Славгород км 1155 – км 172; мост через р. Оку на автомобильной дороге М-5 «Урал» (Москва - Челябинск).
Наличие нормативного документа
ДМД 02191.2.022-2009 «Рекомендации по повышению водонепроницаемости одежды ездового полотна мостовых сооружений».
Данную технологию будем применять в курсовом проекте для строительства дороги 3 категории.
Эмульсионно минеральная смесь
Описание технологии и область применения
ЭМС представляет собой смесь состоящую из минеральной части в которой используются доступные каменные материалы и пески специальной катионной битумной эмульсии и воды по- добранных в оптимальном соотношении. В отдельных случаях в смесь вводят стабилизатор скорости распада и минеральный порошок (при недостатке мелких фракций). ЭМС производятся с использованием мобильной установки «Дельта 100» белорусского производства. В зависимости от типа битумной эмульсии ЭМС может приготавливаться либо складируемой либо немедленной укладки. Складируемая гравийно-эмульсионная смесь может храниться в шта- белях или в таре (в мешках емкостях). ЭМС применяется на дорогах III-V категорий. На автомобильных дорогах III категории ЭМС применяются для устройства верхнего несущего слоя основания и нижнего слоя покрытия. На автомобильных дорогах IV и V категорий ЭМС применяются для устройства верхнего несущего слоя основания нижнего и верхнего слоев покрытий. Шерохова- тость и плотность поверхности покрытий из этих смесей обеспечиваются устройством поверхностной обработки.
Технология устройства покрытий из ЭМС для дорог местного значения по сравнению с традиционной имеет следующие преимущества: снижение общей стоимости работ на 20% за счет уменьшения технологических энергозатрат и удешевления конструкции дорожной одежды; повышение экологической безопасности в зоне приготовления и укладки смеси; снижение зависимости от погодноклиматических факторов при проведении дорожных работ.
Наличие нормативного документа ТКП 306-2011 «Автомобильные дороги. Правила устройства покрытий и оснований из эмульсионно-минеральных смесей».
Технология холодного ресайклинга
В основе технологии холодного ресайклинга лежит повторное использование старого фрезерованного асфальтобетонного покрытия. Она может применяться как для восстановления так и для повышения несущей способности дорожных одежд. Холодные регенерированные асфальто- бетонные смеси представляют собой смесь асфальтового гранулята (фрезерованного асфальтобетонного покрытия) специальной катионной битумной эмульсии цемента воды взятых в определенных соотношениях. Холодные регенерированные асфальтобетонные смеси приготавливаются в стационарных или мобильных установках специальных смесителях-укладчиках и укладываются в конструктивные слои дорожной одежды в хо- лодном состоянии. Такие смеси могут приго- тавливаться и укладываться с помощью специальных машин-ресайклеров которые измельчают конструктивные слои существующей дорожной одежды перемешивают измельченный материал с вяжущим и водой и укладывают полученную смесь для дальнейшей планировки и уплотнения в новый конструктивный слой. В зависимости от категории автомобильной дороги вышеуказанные смеси могут укладываться в верхние слои основания (I-III категории) в нижний (III категория) или верхний слои покрытия (IV-V категории). В зависимости от состава холодные регенерированные смеси могут приготавливаться либо складируемыми либо немедленной укладки.
Технико-экономический эффект
Экономическая эффективность использования такой смеси достигается за счет повторного использования минерального материала (до 100 %) а также за счет снижения энергозатрат на 25-50 % по сравнению с энергозатратами на приготовление традиционного асфальтобетона.
Холодная регенерация асфальтобетонного покрытия с помощью ресайклера WIRTGEN 2200CR при научно-техническом сопровождении государственного предприятия «БелдорНИИ» выполнена в 2007 году на автомобильной дороге Р-67 Борисов – Березино – Бобруйск; в 2008 году – на участке автомобильной дороги Р-110 Глубокое – Поставы – Лынтупы – граница Литовской Республики км 408 – км 502; в 2009 году - на участке автомобильной дороги Р-110 Глубокое – Поставы – Лынтупы – граница Литовской Республики км 680 – км 724.
РД 0219.1.09-99 «Дорожные технологии на основе катионных битумных эмульсий» ДМД 02191.2.017-2008 «Рекомендации по применению технологии холодного ресайклинга при усилении нежестких дорожных одежд».
Мембранная технология ремонта жестких покрытий автомобильных дорог
Технология предназначена для устройства защитных и защитно-гидроизоляционных слоев покрытий при ремонте дорог и ездового полотна искусственных сооружений. Для устройства таких слоев применяется специальный состав асфальтобетонной смеси с использованием модифицированного битума укладываемой на предварительно распределенный модифицированный битум или битумополимерную эмульсию (мембрану). Таким образом обеспечивается насыщение нижней части защитного покрытия вяжущим в момент уплотнения укладываемой смеси на 23 его толщины материал защитного слоя приобретает повышенные деформативные свойства обеспечивается его высокая трещиностойкость а также способность воспринимать температурные и динамические нагрузки без преждевременно- го разрушения покрытия.
Технико-экономический эффект преимущество над аналогами
Покрытие устроенное по мембранной технологии обладает высокой трещиностойкостью и водонепроницаемостью. Межремонтный срок службы таких покрытий увеличивается в 2-25 раза. Экономический эффект от внедрения данной технологии составляет: - при ремонте цементобетонных покрытий - 015-02 USD на 1 м 2 ; - при ремонте покрытий мостового полотна – 15-18 USD на 1 м 2 .
По данной технологии устроены защитно-гидроизоляционные покрытия на мостах через реки: Сож (г. Ветка); Березина (г. Борисов); Неман (пос. Лунно); Неман (г. Гродно); Припять (г. Мозырь); Ока (г. Подольск РФ) а также на 10 путепроводах. Кроме этого отремонтировано около 30 км дорог с цементобетонным покрытием.
ТКП 203-2009 «Автомобильные дороги. Правила устройства покрытий и защитных слоев покрытий по мембранной технологии» СТБ 2036-2010 «Смеси асфальтобетонные литые холодные для устройства защитных слоев. Технические условия».
Технология холодной регенирации
Технология полной разборки слоев существующей одежды включает следующие операции.
В целях частичной разборки верхнего слоя широко применяют машины для холодного фрезерования покрытия. Основным рабочим органом такой машины является фреза - барабан снабженная высокопрочными режущими зубьями . В процессе вращения фрезы - барабана - срезается слой покрытия на заданную толщину срезанный фрезой материал с помощью транспортера грузят в транспортное средство или отсыпают в отвал .
Для охлаждения рабочего органа машины его в процессе работы опрыскивают водой. Поверхность остающаяся после фрезерования является основанием для нового слоя покрытия. Эта поверхность должна быть параллельна поверхности укладываемого на нее слоя. Машина для холодного фрезерования должна обеспечивать :
· необходимую глубину фрезерования
· требуемый поперечный уклон;
· заданный продольный уклон;
· чистоту кромки фрезерования.
Существует значительное количество типоразмеров машин для холодного фрезерования покрытий шириной от 13 до 42 м при максимальной глубине фрезерования от 150 до 300 мм.
Выбор типоразмера холодной фрезы зависит от объема работ и необходимой глубины фрезерования с учетом технико-экономических соображений.
При оценке возможности и целесообразности использования материалов полученных при разборке существующих дорожных одежд выполняют следующее :
· визуальную оценку состояния материалов и предварительное определение вида сооружения в котором они могут быть использованы ( слои вновь строящейся дорожной одежды укрепление обочин строительство временного объезда и др.);
· определение вида работ необходимых для приведения материалов в состояние пригодное для их использования в том или ином сооружении ( дробление крупных кусков или фракций материалов поливка введение добавок );
· разработку технологии строительства из данных материалов намеченных сооружений включая способы обработки вяжущим регенерацию старого асфальтобетона или продуктов фрезерования асфальтобетонного покрытия на заводе;
· технико-экономическую оценку применения продуктов разборки старой дорожной одежды в тех или иных сооружениях в сравнении с использованием новых материалов.
После установления вида сооружения где может быть использован данный материал производят в необходимых случаях испытание этого материала в лабораторных условиях для определения соответствия требованиям стандартов СНиП и других нормативных документов ( определение зернового состава щебеночных и гравийных смесей износа в полочном барабане морозостойкости каменного материала его марки по прочности коэффициента фильтрации песчано-гравийных смесей или песка до промывки и после промывки ).
Данную технологию будем применять в курсовом проекте для ремонта дороги 2-ой категории.
Исходные данные к проекту
База механизации проектируется для комплекта машин предназначенного для строительства дорожного полотна и ремонта дорожного покрытия. Исходные данные приведены в таблице 2.1-2.2. Характеристики дорог приведены в таблице 2.3.
Таблица 2.1 Условия эксплуатации при строительстве дорожного полотна
Километраж строящегося участка дороги
Относительная влажность
Коэффициент сопротивления перемещению
Дальность транспортировки песка и щебня
Дальность транспортировки битума
Дальность транспортировки асфальтобетона
Расстояние от участка до базы
Коэффициент сменности работы машины
Наработка первой машины
Шаг наработки остальных машин
Таблица 2.2- Условия эксплуатации при ремонте дорожного покрытия
Километраж ремонтируемого участка
Расстояние от участка до базы
Дальность транспортирования битума
Дальность транспортирования асфальтобетона
Таблица 2.3-Характиристики дорог
Параметр элементов дороги
Интенсивность движения автомобиля в сутки
Число полос движения
Ширина проезжей части м
Ширина разделительной полосы
Ширина земляного полотна м
Расчетная скорость кмч
Для устройства земляного полотна применяется песок или супесь. Толщина слоя до 15 м. (наименьшее возвышение 11 м). Коэффициент уплотнения 10 098.
Тело насыпи (с откосами). Разрешается использовать грунты и отходы промышленности (шлак).
Требования к материалам по СНиП 2.05.02-85.
Асфальтобетонное покрытие на щебеночном основании выполненное по традиционной технологии включает в себя:
- мелкозернистый асфальтобетон -10 см;
- крупнозернистый асфальтобетон -5 см;
- щебеночная смесь пропитанная битумом -8 см;
- песчано-гравийная смесь -15 см;
Таблица 2.4– Нормы расхода материалов на 1 км дороги
Определение годового объема выполняемых работ.
1 Расчет годовых объемов работ для строительства дороги
Расчет потребного количества материалов Q производится в зависимости от категории строящейся дороги kд и ее длины Lд производится на основании норм расхода материалов на 1 км дороги.
Количество песка необходимого для постройки участка дороги заданной длины:
где: kп - норма расхода песка на 1 км дороги таблица 2.4 (kп=225×103 м3).
Lд - длина строящегося участка дороги км.
Qп =60225103=1350103 м3
Количество щебня необходимого для постройки участка дороги заданной длины:
где: kщ- норма расхода щебня на 1 км дороги таблица 2.4 (173×103 м3).
Qщ =60173103=1038103 м3
Количество битума необходимого для постройки участка дороги заданной длины:
где: kб - норма расхода битума на 1 км дороги таблица 2.4 (kб =1763 т)
Количество крупнозернистого асфальтобетона необходимого для постройки участка дороги заданной длины:
где: kф.к - норма расхода крупнозернистого асфальтобетона на 1 км дороги таблица 2.4 (kф.к =128×103 т).
Qф.к =60128×103=768103 т
Количество мелкозернистого асфальтобетона необходимого для постройки участка дороги заданной длины:
где: kф.м - норма расхода мелкозернистого асфальтобетона на 1 км дороги таблица 2.4 (kф.м =087×103 т).
Qф.м=60087×103=522103 т
Годовая программа по уплотнению асфальтобетона определяется по длине ширине и длине ремонтируемой дороги:
Qуп= n×Lд×Вд м2(3.9)
где: Вд – ширина проезжей части таблица 2.3 (Вд = 75 м).
n – число проходов катка (общее количество проходов катков по одному следу после прохода асфальтоукладчика без включенного уплотняющего оборудования - 20-24 при работающем оборудовании - 10-14)
Qуп= 10×60000×75= 45×106 м2
Таблица 3.1 – Годовые объемы работ для строительства дороги
2 Расчет годовых объемов работ для ремонта дороги
Расчет потребного количества битума Qб крупнозернистого и мелкозернистого асфальтобетона Qак и Qам; в зависимости от категории строящейся дороги kд и ее длины Lд производится на основании норм расхода материалов на 1 км дороги приведенных в таблице 2.4.
Количество битума необходимого для ремонта участка дороги заданной длины:
где: qб–норма расхода битума на 1 км дороги;
Lд - длина ремонтируеиого участка дороги км.
Количество крупнозернистого асфальтобетона необходимого для ремонта участка дороги заданной длины:
где: qф.к–норма расхода крупнозернистого асфальтобетона на 1 км дороги;
Qф.к= 70098103 = 68600 т
Количество мелкозернистого асфальтобетона необходимого для ремонта участка дороги заданной длины:
где: qф.м–норма расхода мелкозернистого асфальтобетона на 1 км дороги;
Qф.м= 70049103 = 34300 т
где: Вд – ширина проезжей части таблица 2.3 (Вд = 70 м).
Qуп= 10×70000×7= 49×106 м2
Годовая программа по укладке асфальтобетона асфальтоукладчиком определяется по ширине и длине ремонтируемой дороги:
Qасф= n×Lд×Вд м2.(3.10)
Qасф= 1×70000×7 = 49×104 м2.
Годовая программа по фрезерованию верхнего слоя асфальтобетона холодной фрезой определяется по ширине и длине ремонтируемой дороги а также по глубине фрезерования:
QФасф= n×Lд×Вд hф м2.(3.11)
где: hф–глубина фрезерования м;
QФасф= 1×70000×7×01 = 49×104 м2.
Результаты расчетов заносим в таблицу 3.2.
Таблица 3.2 – Годовые объемы работ для ремонта дороги
Таблица 3.3 Суммарный объем работ для строительства дороги
Перевозка материалов
Уплотнение асфальтобетона
Смесь асфальтобетона
Распределение материала
Таблица 3.4 Суммарный обьем работ для ремонта дороги
Выбор технологий и ведущих машин для выполнения годового объема работ.
Выбор номенклатуры используемых машин осуществляется с учетом нынешнего экономического положения Республики Беларусь. Необходимо всячески снижать количество используемой техники и людских ресурсов при одновременном повышении качественного их использования.
При выполнении землеройно-транспортных работ определяющим фактором является дальность транспортировки грунта. Предельная дальность транспортировки бульдозерами - 01 км; прицепными скреперами - 05 км самоходным скрепером - 10 км. При большей дальности транспортировки землеройные работы выполняются экскаваторами или погрузчиками а транспортировка автомобилями-самосвалами.
Набор грунта самоходным скрепером производится с помощью толкача а при работе экскаваторов и самосвалов в комплект машин включается бульдозер.
Для снижения коэффициента сопротивления перемещению машин f при транспортировке используется автогрейдер планирующий дорогу.
При выборе комплекта машин необходимо учитывать следующие условия:
- производительность машин должна быть максимальной при полной их загрузке;
- экскаваторами без предварительного рыхления можно разрабатывать грунты до IV категории включительно (число ударов плотномера ДорНИИ С до 35);
- разработка грунта скреперами погрузчиками и автогрейдерами при значении С до 12;
- разработка грунта повышенной влажности и при величине С1 возможна только экскаваторами;
- вместимость кузова автосамосвала должна превышать вместимость ковша экскаватора в 4 5 раз а погрузчика в 2 3 раза;
- тяговые усилия толкача и скрепера в кН выбираются из условия превышения вместимости ковша скрепера в 25 30 раз;
- если по условиям эксплуатации возможно применение экскаватора и погрузчика предпочтение отдается погрузчику.
Выбираем следующие машины для строительства дороги которые приведены в таблице 4.1.
Таблица 4.1- Машины для строительства дороги
Техническая характеристика
автосамосвал МАЗ-MAN 652036
для уплотнения дорожного полотна
- легкий DD38HFДУ-86;
-средний Амкодор 6631 ДУ-96;
-тяжелый Амкадор 6622
для уплотнения асфальто-бетона
грузоподъем-ность 14 т
для планирова-ния дороги
погрузчик Амкодор-332С4
вместимость ковша 19 м3
для погрузки песка и щебня
автогудронатор АРБ-8
для транспор-тировки и разлива битума
асфальтоуклад-чик ABG P7820C
толщина укладки 300 мм
для укладки асфальта
для разработки песка
При ремонте дорожного покрытия комплект машин принимается в зависимости от технологии выполняемых работ и расстояния от участка до асфальтобетонного завода.
При ремонте дорожного покрытия методом укладки дополнительных слоев асфальтобетона комплект машин включает: автогудронаторы для транспортировки и разлива битума; автосамосвалы для транспортировки асфальтобетона; асфальтоукладчики; катки для уплотнения асфальтобетона.
При ремонте дорожного покрытия методом холодной регенерации твердого покрытия с добавлением минеральных материалов комплект машин включает: холодную фрезу автотранспорт с минеральными материалами рисайклер автотранспорт с цементом водой и эмульсией каток для окончательного уплотнения.
Использование метода холодного рисайлинга уменьшает применение новых материалов устраняет помехи дорожному движению оказывает минимальное воздействие на окружающую среду. Однако этот метод требует использование достаточно дорогостоящей техники.
Для ремонта дорожного покрытия методом укладки дополнительных слоев асфальтобетона выбираем следующие машины приведенные в таблице 4.2.
Таблица 4.2- Машины для ремонта дороги
глубина фрезерования-до 0-300 мм за один проход
для фрез-ия верхнего слоя асфальто-бетона
Для транспортировки не мобильных машин используем трейлер Трал Trailer грузоподъемностью 60 тонн (длинна рабочей площадки 12 м высота погрузочной площадки 1250 мм ширина-2500мм также имеются уширители выдвижные до 3000мм) автокран КС35715 для погрузки асфальтоукладчика на платформу трейлера. Для технического обслуживания и ремонта техники используем передвежную ремонтную мастерскую ПРМ 5820. Для доставки топлива к месту базирования машин и их дальнейшей заправки используем топливозаправщик АТЗ-17 на базовом шасси МАЗ-МAN 630268.
погрузки асфальтоукладчика
технического обслуживания
Формирование парка машин
1 Определение действительного количества часов работы машин в год.
Действительное количество часов работы машин в год определяется по формуле:
Тч=(Дк - Дп) ×Кт.и. ×Ксм×Тсм (5.1)
где: Дк – количество календарных дней в году;
Дп – количество дней перерывов в году при работе машин;
Кт.и.- коэффициент технического использования;
Ксм – коэффициент сменности Ксм=2;
Тсм –продолжительность смены ч.
Определим время работы погрузчика Амкадор 332С4 имеющего наработку на начало года 1700 моточасов. Режим работы техники задается продолжительностью смены 8 ч и коэффициентом сменности равным 2. Температурная зона для которой рассчитывается режим работы - г. Могилев. Среднее время на одну перебазировку составило 4 ч количество перебазировок в году 12.
Количество рабочих суток в году определяется исключением из календарного времени года числа суток перерывов и простоев машины по всем причинам:
Д = Дк – (Дв + Дпб + Дм + Дн + До )(5.2)
где: Дк – количество календарных дней в году (Дк = 365) или сезоне дни;
Дв – количество выходных и праздничных дней (Дв=112);
Дпб – количество дней на перебазирование монтаж и демонтаж ДСМ;
Дм – количество дней перерывов по неблагоприятным метеоусловиям;
Дн – количество дней непредвиденных перерывов в работе машин;
До – количество дней затраченное на ожидания ремонта доставку на ремонтное предприятие и обратно;
Д = 365 – (112+8+1265+8+0) = 22435 дней.
Количество дней затраченных на перебазировку машины:
Дп = (Дк – Дв) 005 (5.4)
Дп=(365-112) 005=1265 дней
Количество дней связанных с неблагоприятными метеоусловиями:
Дм = Дм.табл. 075 (5.5)
где: Дм.табл – табличное количество дней с неблагоприятными условиями (Дм.табл=11 сут.);
Дм = 11 075 = 8 дней
Количество дней непредвиденных перерывов в работе машины определяется:
Дн = (Дк – Дв) 003 (5.6)
Принимается продолжительность непредвиденных перерывов Дн в размере 3 % количества календарных суток за исключением праздничных и выходных дней.
Дн = (365 – 112) 003 = 8 суток.
Капитальный ремонт в данном году не предусматривается т.к. наработка до капитального ремонта составляет 6000 моточасов Вк=0.
Определение коэффициента технического использования в зависимости от наработки с начала эксплуатации или после капитального ремонта (Нф) определяется по формуле:
где: А1 и А2 – эмпирические коэффициенты для каждого типа машины.
Кти = 092 – 00000241 1700 = 0879.
Годовой режим работы ДСМ определяется:
Тч = 22435 2 8 0879 = 315525 мч
Результаты расчета сводим в таблицу 5.1
Таблица 5.1 - Количество часов работы машин в год при строительстве и
ремонте дороги для каждой первой машины.
Остальные значения Тч и Кти для каждой машины в Приложениях.
2. Расчет производительности машин
2.1 Расчет годовой эксплуатационной производительности погрузчика АМКОДОР 332С4 (34т.) для разработки щебня. Эксплуатационная производительность погрузчика:
где: Vк – вместимость ковша м3 принимаем 19 м3;
γ – плотность материала тм³;
kН - коэффициент наполнения (095 11 в среднем 105);
kР - коэффициент разрыхления материала кР =095;
kи – коэффициент использования погрузчика в течении смены с учётом подачи автосамосвалов подготовки площадки передачи смены и возможных простоев (07 08) принимаем kи = 06
При проведении расчетов для погрузчика принимаем tц = 20 с.
Годовую эксплуатационную производительность погрузчика определим по формуле:
Пг = ПтТч м3год (5.9)
где: Тг - годовой фонд времени с учетом коэффициента сменности.
ПГ =35694·27082=104095 м³год.
2.2 Расчет годовой эксплуатационной производительности бульдозера Четра Т11
где: - объем призмы волочения:
где: - ширина отвала ;
- коэффициент разрыхления .
- коэффициент наполнения отвала (с открылками)
- коэффициент использования машины во времени
- коэффициент потерь грунта
- коэффициент учитывающий уклон или подъем
- число циклов за час работы:
где: - скорость бульдозера при зарезании отвала принимаем;
- скорость бульдозера при перемещении грунта принимаем ;
- скорость обратного хода бульдозера принимаем
- дальность перемещения грунта принимаем ;
- время на переключение скорости опускание отвала принимаем ;
- время на разгрузку отвала при отсыпке принимаем ;
Годовая эксплуатационная производительность определяется по формуле 5.9:
Пг = 170·249569 = 424667 тгод = 6794672 м3год
2.3 Расчет годовой эксплуатационной производитель-
ности асфальтоукладчика ABG P7820C
Часовая эксплуатационная производительность определяется:
Пэ=60*H*В*V**kВтчас
где: В – ширина (В = 375 м);
V – рабочая скорость(10 ммин);
H – толщина слоя (015 м для асфальтобетона)
- плотность ( 17 тм3 );
kВ – коэффициент использования по времени (kВ = 043 ).
Часовая эксплуатационная производительность асфальтоукладчика
Пэ = 60 * 015 * 375 * 10 * 17 * 043 = 243423тчас.
Годовая эксплуатационная производительность асфальтоукладчика равна:
Пг =24342316151 = 393152 тгод.
Таблица 5.2.3- Производительность асфальтоукладчика
для строительства дороги
2.4 Расчет годовой эксплуатационной производительности автогудронатора АРБ-8
Эксплуатационная производительность автогудронатора вычисляется по формуле:
Пэ=60·Q·kвt лмин (5.13)
где: Q- вместимость цистерны л;
Т- продолжительность смены час;
kв- коэффициент использования сменного времени kв=07;
t- время затрачиваемое на один рейс мин;
t = tн+ tт+ tр+ tм+ tп мин (5.14)
где: tн-время набора битума в цистерну(примем tн=6мин);
tт- время транспортировки битума к месту размеса;
tт = 60·LбVгр мин (5.15)
tт = 60·55237= 759 мин;
где: Lб- расстояние до места км;
Vгр- скорость груженой машины кмчас;
Vгр = 26-62·f1+034·f1-1 кмч (5.16)
Vгр = 26-62·002+034·002-1=237 кмч;
tн- время набора битума в цистерну (можно принимать 5 10 мин)=10
tр- время разлива битума мин;
где: Q- вместимость цистерны (для гудронатора АРБ-8 Q=7000л);
q - производительность битумного насоса (для гудронатора АРБ-8 q=1000лмин);
tм- время маневрирования на базе и на дороге примем 3 мин;
tп- время порожнего пробега;
tп = 60·LбVпор мин(5.18)
tп = 60·5560 = 55 мин;
t = 6+75.9+7+3+55= 126.9мин;
Пэ = 60·7000·07126.9 = 231678 лчас;
Годовая эксплуатационная производительность автогудронатора определяется по формуле 5.9:
Пг = 231678·202137 = 46830794 лгод = 46830794 м3 год
Таблица 5.2.4- Расчет автогудронатора
Автогудронатор АРБ-8 для строительства дороги
Автогудронатор АРБ-8 для ремонта дороги
2.5 Расчет годовой эксплуатационной производительности самоходных катков
Эксплуатационная производительность статического катка Амкодор 6631 рассчитывается по формуле:
где: В - ширина укатываемой полосы м (16 м);
а - перекрытие предыдущего прохода (05 м);
Vср - средняя скорость катка (5 кмч);
n - необходимое число проходов (принимается при уплотнении 18щебеночных и гравийных слоев 20 40; при уплотнении аб 15 20).
Пэ =1000·(16-05)·5·05520= 2142 м2час.
Годовая производительность определяется по формуле 6.3:
Пг =2142·17165 = 3676743 м2год
Остальной расчет катков сводим в таблицу 5.2.5
Таблица 5.2.5-Расчет катков
6 Расчет годовой эксплуатационной производительности фрезы Wirtgen W100.
Эксплуатационная производительность фрезы находится по формуле:
Пфр=60BV Нр kвγ тчас (5.20)
где: В- рабочая ширина (В=1м);
V- рабочая скорость W
Нр- глубина резания фрезы Нр=03м;
Кв- коэффициент использования сменного времени kв=05;
γ- плотность покрытия 24 тм3 ;
Пфр=6015 03 0524=108тчас
Годовая эксплуатационная производительность фрезы определяется по формуле 5.9:
Пг = 108·164548 = 177660 м3год.
2.7 Расчет годовой эксплуатационной производительности самосвала для транспортировки песка и щебня для постройки дороги. Эксплуатационная производительность автосамосвала находится по формуле:
где: qт - грузоподъемность самосвала т (225 т);
tп - время мин. необходимое на загрузку самосвала (45 мин);
L - расстояние транспортировки песка км (3 км);
V1 - скорость движения груженого самосвала кмчас(40 кмч);
V2 - скорость движения порожнего самосвала кмчас(85 кмч)
tр - время маневрирования и разгрузки самосвала мин (2 4 мин).
Пг1 = 827·1385 = 1145395 тгод.
Для транспортировки асфальтобетона
Пг1 = 141·158595 =22361 тгод.
Пг1 = 332·1385 = 460665 тгод.
Пг1 = 215·158595 =34098 тгод.
2.9 Расчет годовой эксплуатационной производительности грунтового катка
Эксплуатационная производительность дорожных катков в м2час:
где: B - ширина укатываемой полосы принимаем B = 213 м;
a - перекрытие предыдущего прохода (025м);
Vср - средняя скорость катка принимаем Vср = 6 кмч;
kв - коэффициент использования рабочего времени (055).
n - необходимое число проходов (принимается при уплотнении песчаных слоев (15 20 ) для проведения расчетов принимаем n = 20 .
Часовая эксплуатационная производительность равна:
Годовая эксплуатационная производительность грунтового катка определяется по формуле 6.3:
Пг =3102 ×2661 =8254422 м2год.
Таблица 5.2 – Годовая эксплуатационная и часовая эксплуатационная производительность машин.
для транспортировки песка и щебня
для транспортировки асфальтобетона
- средний Амкодор 6631
- тяжелый Амкадор 6622
автогудронатор АРБ-8 для строительства дороги
автогудронатор АРБ-8 для ремонта дороги
асфальтоукладчик ABG P7820C для строительства дороги
асфальтоукладчик ABG P7820C для ремонта дороги
3 Расчет потребного количества машин
Определив годовую эксплуатационную производительность машин каждого типа Пэг и объемы работ выполняемых в течение года Qг производится предварительный расчет необходимого количества машин каждого типа:
Предварительно определяем необходимое количество машин каждого типа для строительства дороги:
Количество погрузчиков Амкадор 332С4:
Nк. = 2238000 1050619= 21 принимаем Nк = 3 шт;
Остальные расчеты сводим в таблицу 5.3
Таблица 5.3-Необходимое количество маши каждого типа
Для строительства дорожного полотна
- средний Амкодор 6631
асфальтоукладчик ABG P7820C
Для ремонта дорожного полотна
автосамосвал МАЗ-MAN 652036 для транспортирования отфрезерованного слоя асфальтобетона
автосамосвал МАЗ-MAN 652036 для подвоза асфальтобетона
Погрузчик Амкадо 332С4
Планирование объемов работ по поддержанию и восстановлению работоспособности машин парка
1 Разработка годового плана ТО и ремонтов машин
В эксплуатационных организациях система ТО и ремонтов реализуется через годовые планы и месячные план графики ТО и ремонтов для всего парка машин. Годовым планом определяется число планируемых ТО и ремонтов каждой машины. Исходными данными для разработки годового плана являются: фактическая наработка с начала эксплуатации и планируемая наработка на расчетный год в часах для каждой машины а также регламентированная периодичность выполнения ТО и ремонтов.
В годовом плане определяется месяц постановки в капитальный ремонт машин выработавших плановый ресурс.
В месячных планах-графиках указываются даты выполнения ТО а также продолжительность пребывания в текущем или капитальном ремонте по дням для каждой машины.
Количество ТО и ремонтов каждого вида на планируемый год для каждой машины определяется по формуле:
где:Нф - фактическая наработка машины на начало планируемого года со времени проведения последнего аналогичного ТО или ремонта (определяется как разность между наработкой машины с начала эксплуатации или после капитального ремонта на начало планируемого года и ее наработкой на день последнего аналогичного ТО или ремонта предшествующего года);
Нпл - наработка на планируемый год определяемая по количеству часов рабочего времени машины в течение года и коэффициенту kп перехода от сменного времени к часам наработки;
Tтор - периодичность выполнения соответствующего ТО или ремонта (в часах) по которому производится расчет;
kвп - количество ТО и ремонтов более высокого порядка (для капитального ремонта kвп = 0).
Определим количество ТО и ремонтов для погрузчика Амкадор 332 С4.
Принимаем следующую периодичность проведения ТО и ремонтов: КР-6000 ч ТР-1000 ч ТО-2-500 ч ТО-1-100 ч.
Наработка с начала эксплуатации Н1 = 1700 маш-час.
Планируемая годовая наработка определяется по формуле:
где kп - коэффициентов перехода сменного рабочего времени к часам наработки (моточас) строительных дорожных и подъемно-транспортных машин и оборудования.
Определяем планируемую годовую наработку по формуле (6.2):
Нпл = 3156 074 = 1894 моточас
Капитальный ремонт погрузчика в планируемом году не производится так как сумма наработки с начала эксплуатации на начало года и планируемой наработки на расчетный год меньше периодичности его проведения:
Ккр = (1700+1894) 6000 - 0 = 0
Наработка после последнего ТР:
Нф.тр = H1-Ттр = 1700-2000=0ч
Количество ТР определим по формуле (6.1):
Ктр = (0+1894 1000 – 0 = 2
Наработка после последнего ТО-2:
Количество ТО-2 определим по формуле (6.1):
Кто2 = (0+1894)500 – 3 = 166=2.
Наработка после последнего ТО-1:
Нф.то1 = 200-300 = 100 ч
Количество ТО-1 определим по формуле (6.1):
Кто1 = (100+1894)100 – (3+2) = 1934=20
Аналогично производим расчет для всего парка машин учитывая шаг
наработки каждой последующей машины.
По результатам расчета строим годовой план-график для всего парка машин (приложение А).
В годовом плане ТО и ремонтов месяц проведения капитального ремонта машины определять не будем т.к. в планируемым году КР не выполняются. План-график ТО и ремонтов СДМ будем строить на январь.
План-график ТО и ремонтов для погрузчика Амкадор 332С4 строится по следующей методике:
Определим общее количество рабочих дней за год:
где: Дк=365-количество дней в году;
Дп=140-число дней перерывов в году;
Количество рабочих месяцев в год:
где: КД – среднее количество дней работы погрузчика в месяц принимаем КД=22;
Средняя продолжительность работы погрузчика в месяц:
Средняя продолжительность работы погрузчика в день:
Определим фактическую наработку на начала января с начала эксплуатации:
где: К – количество рабочих дней до января К=0;
Определим порядковый номер дня проведения текущего ремонта:
где: k – количество рабочих дней в месяце;
Следовательно ТР проводиться не будет.
Определим порядковый номер дня проведения ТО-2:
Следовательно ТО-2 проводиться не будет.
Определим порядковый номер дня проведения ТО-1:
Следовательно на 16 рабочий день января запланирован ТО-1.
Так как в январе 22 рабочих дня следовательно в январе ТО-1 больше проводиться не будет.
По результатам расчета строим план-график на месяц для машин парка (приложение Б).
Организация ТО и ремонта машин.
Место и способ выполнения технических обслуживаний и ремонтов зависит от вида и сложности технического воздействия и от удаленности места работы машин от базы. В зависимости от состава парка машин его количества и условий эксплуатации ТО и ремонты могут выполняться индивидуальным групповым участковым или агрегатно-участковым методами. Ремонт выполняемый в полевых или стационарных условиях агрегатно-узловым методом значительно сокращает время простоя машины в ремонте.
Исходя из опыта эксплуатации СДМ при курсовом проектировании можно считать что примерно 30 40% ТО; 60%ТР и до 25%КР выполняются в ремонтных мастерских базы а 60 70% ТО и 40% ТР выполняются в полевых условиях ПРМ.
1. Определение годовой трудоёмкости ТО и ремонтов
Годовая трудоёмкость ТО-1 ТО-2 ТР КР определяется по формуле:
Для погрузчика Амкадор 332С4:
Остальные значения сводим в таблицу в приложениях.
2 Проектирование ПРМ
Целесообразность использования ПРМ зависит от удаленности места работ от базы.
По рекомендациям С.К. Полянского предельное расстояние для обслуживания машин с помощью ПРМ определяется зависимостью:
где: tсм - продолжительность смены для рабочих ПРМ tсм = 8 ч;
tпод - время подготовки к работе (tпод = 1 2 часа) принимаем tпод =1 ч;
V - скорость передвижения мастерских кмч
V=26-62f+034f-1=26-62004+034004-1 = 429 кмч.
Необходимое количество ПРМ определяется по формуле:
где: kмто – коэффициент учитывающий долю работ по ТО выполняемых
ПРМ принимаем kмто = 07 ;
kмтр – коэффициент учитывающий долю работ по ТР выполняемых
ПРМ принимаем kмтр = 04;
Tгто - годовая трудоемкость ТО для машин возращающихся на базу Tгто = 19622497 ч;
Tгтр - годовая трудоемкость ТР для машин возращающихся на базу Tгтр = 1582991 ч
Фгм - номинальный годовой фонд времени мастерской;
Рм - число рабочих в ПРМ (обычно 2 3 чел.);
kв коэффициент учитывающий потери времени на перемещение
ПРМ (kв = 05 06) принимаем kв =055 .
Годовой фонд времени мастерской с учетом коэффициента сменности определяется по формуле:
где: Dк - число календарных дней в году Dк =365;
Dв - число выходных дней в году Dв =104;
Dп - число праздничных дней в году Dп =8;
tсм - продолжительность смены в часах tсм =8 ч;
kсм - коэффициент сменности kсм =2;
kти - коэффициент технического использования Кти = 08.
Годовой фонд времени работы мастерской равен:
Необходимое количество ПРМ равно:
Применяем ПРМ марки: МПР-3901 на автомобиле
МАЗ-5551320 ; агрегаты техобслуживания: АТО-9966 А .
Проектирование предприятий по поддержанию и востановлению работоспособности машин
1 Проектирование РММ.
Годовая трудоемкость этих работ включает в себя работы по ТО и ремонтам основных машин выполняемые РРМ и работы по самообслуживанию мастерских и по ТО и ремонту вспомогательных машин:
где: kто - коэффициент учитывающий долю работ по ТО машин
возвращающихся на базу выполняемых в РРМ Кто = 03;
kтр - коэффициент учитывающий долю работ по текущему ремонту
машин возвращающихся на базу выполняемых в РРМ Ктр = 06;
kкр - то же по капитальному ремонту (для проведения расчетов
принимаем Ккр = 075).
Tгто; Tгтр; Tгкр - годовая трудоемкость ТО текущих и капитальных
ремонтов для всех марок машин соответственно для проведения
расчетов принимаем Tгто = 12894 ч Tгтр = 41065 ч Tгкр = 15104ч. (Расчёт проведён в п. 7.1.)
kсам - коэффициент учитывающий трудозатраты на ремонт технологи-
ческого оборудования и ТО и ремонт вспомогательных машин (в
проекте принимаем kсам = 13).
Тогда годовая трудоемкость работ РРМ равна:
1.1. Определение фондов времени и численности основных производственных рабочих
Номинальный годовой фонд времени рабочего определяется по формуле:
где Dк; Dв; Dпр; Dпп - количество календарных выходных праздничных и предпраздничных дней соответственно Dк = 365 Dв = 104 Dпр = 8; Dпп = 6.
t’см - продолжительность смены в предпраздничные дни в час t’см = 7 ч.
Номинальный годовой фонд времени рабочего равен:
Действительный годовой фонд времени рабочего определяется по формуле:
где Dот - количество дней отпуска;
t’’см - продолжительность смены при шестидневной рабочей неделе
(в дни отпуска входят и субботы) t’’см = 7 ч.
hр - коэффициент учитывающий потери времени по уважительным
причинам (hр = 096);
Номинальный годовой фонд времени используется при расчете явочного количества рабочих:
Действительный годовой фонд времени используется при расчете списочного количества рабочих:
Годовой фонд времени рабочего места:
где: КСМ– количество смен.
ФРМ = 201818 = 36324ч
Годовой фонд времени рабочего поста:
ФРП = ФНР КСМ Рп hв (8.7)
где: Рп – количество рабочих на посту (для ТО-1 Рп = 2 для ТО-2
hв – коэф. загрузки поста (при ТО-1 hв = 1 при ТО-2 hв = 09).
ФРП ТО-1 =20181821 = 8072ч
ФРП ТО-2 = =201818309 = 108972ч
Годовой фонд времени оборудования:
ФОБ = ФНР КСМ hив (8.8)
где hив = 085 – коэф. использования оборудования.
ФОБ = 201818085=34306ч
1.2 Распределение трудоемкости ТО и текущего ремонта по видам работ.
Определяем трудоемкость ТО и ТР выполняемых в РРМ для каждого типа машин.
Трудоемкость капитального ремонта рассчитывается по формуле:
Tткр = 025*Ткр (8.9)
Tткр = 025*4608 = 1152 чел-ч
Трудоемкость текущего ремонта рассчитывается по формуле:
Тттр = 07*Ттр (8.10)
Тттр = 07*12528 = 87696 чел-ч
Трудоемкость ТО рассчитывается по формуле:
Ттор = 03*Тто (8.11)
Ттор = 03*39744 = 119232 чел-ч
Отальные данные сводим в таблицу 8.1.2
Таблица 8.1.2.-Трудоемкость ТО и ремонтов
- средний Амкодор 6631 - тяжелый Амкадор 6622
В соответствии с методическими указаниями распределяем трудоемкость по видам работ для каждого типа машин и определяем явочную и списочную численность рабочих для каждого вида работ округляя количество рабочих до целых значений. При необходимости объединяем родственные виды работ. Результаты расчетов заносим в таблицы 8.3.2 8.3.3.
Таблица 8.3.2 – Распределение трудоемкости ТО по видам работ
пневмогидроаппаратура
Таблица 8.3.3-Распределение ТР по видам работ
Ремонт системы питания
Ремонт пневмогидроап
1.3 Расчет штатов базы механизации
Определив общую трудоемкость ТО и ремонтов выполняемых в РРМ производят распределение ее по видам работ и определяют численность рабочих
Штат базы механизации включает в себя:
- машинистов дорожных машин - 86 ;
- водителей самосвалов - 48;
- основных производственных рабочих РММ - 16 ;
- рабочих ПРМ включая водителей - 12 ;
- вспомогательных рабочих РММ (принимается в пределах 8 10% от числа основных) и равно - 2 ;
- ИТР (принимается 15 20% от численности основных рабочих) и равно- 3;
- служащих (принимается 8 10% от численности основных рабочих и равно - 3;
- МОП (принимается 1 2% от численности рабочих) и равно - 2.
Всего рабочих – 95 чел.
1.4 Расчет количества рабочих постов ТО и ТР
Число универсальных или специализированных постов ТО и ремонта определяется по формуле
где:Tготд - годовая трудоемкость работ выполняемых в отделении (зоне) на постах;
kн - коэффициент неравномерности поступления машин (принимается 14);
Pп - количество рабочих одновременно работающих на посту - 2;
hп - коэффициент использования поста (принимается 09 ).
Проводим расчет количества постов для зоны ТО и ТР.
Хп = 7170414 ( 2018 2 18 09) = 153Принимаем Хп= 2 шт.
Хп = 1273114 (2018 21809) = 027Принимаем Хп= 1 шт.
Хп = 8313514 (2018 21809) = 178Принимаем Хп= 2 шт.
Для зоны диагностики:
Хп=(71704+12731+83135)*025*14(2018*2*18*09)=055шт. Принимаем Хп = 1 шт.
3.5 Расчет производственных площадей
Площади производственных участков РММ определяются по удельной площади приходящейся на одного производственного рабочего из числа одновременно работающих на участке по формуле
гдеf1 - удельная площадь на первого рабочего;
fА- удельная площадь на каждого следующего рабочего;
P - число рабочих на участке в наибольшей смене.
Определяем площади помещений для зон ТО и ремонта результаты расчетов заносим в таблицу 8.3.5
Таблица 8.3.5 - Расчет площадей отделений и участков
Наименование отделения
Удельная площадь для 1-ого
Удельная площадь для послед.
Переходный коэффициент
Трудоемкость работ на данном участке
Расчетное число рабочих на участках
Принятое число рабочих на участках
Слесарно-механическое
Производственные площади для зон ТО-1 ТО-2 и зон текущего ремонта машин определяются по формуле:
где: Xпi – число универсальных постов ТО или ремонта
FMi – площадь занимаемая машиной принимаем площадь 10300х3200.
Kп – переходный коэффициент учитывающий рабочие зоны проходы и проезды.
FТО = 2(10332) 4 =26368 м2;
FТР = 1(10332) 4 = 13184 м2;
FКР = 2(10332) 4 = 26368 м2;
FД = 1(10332) 4 =13184 м2;
Fпр = 26368 + 13184 + 26368+ 13184 = 791м2.
Расчет складских площадей Fск производится по укрупненным нормам по удельной площади fуд на одну машину:
где: N - общее количество машин всех типов в парке N=58;
– переходной коэффициент.
Результаты расчетов заносим в таблицу 9.3.6
Таблица 8.3.6 – Площади складов.
Наименование складов
Смазочных материалов
Лесных и стройматериалов
Площади стоянок машин
Хранение строительных и дорожных машин в основном на открытых площадках. Машины сезонного использования хранят под навесом. Подвижный состав автотранспорта в зимнее время хранят на открытых стоянках с подогревом.
Площади стоянок определяются по формуле:
гдеfм - площадь занимаемая машиной;
n - число машин 1-го типа хранящихся на стоянке;
kпр - коэффициент учитывающий проезды kпр=25.
Площади стоянок для машин сезонного использования:
Fст = (287*3 + 235*1+3109*1+1976*5+3212*1)*25 = 680м2.
Площади стоянок для машин подвижного состава:
Fст = (1785*11+1728*3 )*25 = 620 м2.
Площади бытовых и административных помещений
Площади административных и бытовых помещений базы при укрупненных расчетах принимают в % от площади производственных помещений.
Площади административных помещений принимают равными 6% а бытовых - 15%.
3.6 Расчет бытовых и административных помещений
Гардеробы с индивидуальными шкафчиками для каждого рабочего принимаются из расчета 075 08 м2 на человека и составляют -95 м2. Остальные бытовые помещения рассчитываются по количеству работающих в наибольшей смене.
Площадь умывальных комнат принимается из расчета 01 015 м2 на человека (один кран на 10 человек).
Площадь душевых принимается равной 04 05 м2 на человека (одна кабина площадью 20 25 м2 на 5 человек).
Площадь туалетов 05 м2 на человека (один унитаз при площади 30 м2 на 15 человек).
Fад = 1500*006 = 90 м2;
Компоновка участка с подбором современного оборудования
Участок диагностики предназначен для выявления неполадок у машин.
При организации участка диагностики все технические и инженерные решения принимались с учетом номенклатуры машин базы механизации т.е. учитывались их габаритные размеры общая масса машин и масса отдельных углов и агрегатов.
Для выполнения диагностики необходим доступ к машине со всех сторон при этом машины имеют различные габариты. Для обеспечения рациональной позы рабочего высокого качества и безопасности работ применяются подъемное оборудование осмотровые канавы эстакады опрокидыватели. Осмотровые канавы обеспечивают возможность одновременно выполнять работы со всех сторон. Наиболее распространенные в практике организации ТО получили узкие межколейные канавы шириной 09-11 м и глубиной 12-13 м.
Для оснащения нашего участка принимаем смотровую яму глубиной 13 м и шириной 11 исходя из предпосылок что колея строительно – дорожных машин выбранных в проекте достаточно велика а работать удобнее в более широкой и глубокой яме.
Для повышения удобства осмотровые канавы оборудуют канавным подъемным устройством что позволяет работнику при обслуживании стоять в полный рост что снижает усталость и способствует увеличению производительности труда.
При разработке участка диагностики внедрены следующие решения
- предусмотрены перекидные мостки через смотровую яму что обеспечивает доступ к узлам машины расположенным над ямой и недоступным из нее по высоте основная причина их использования различная длина машин принятых в проекте а длина смотровой ямы превышает длину некоторых машин;
- участок оснащен как внешними подъемниками так и канавным подъемником что позволяет вывешивать отдельные агрегаты машины из ямы например бывает необходимо вывесить двигатель для замены выхлопной системы для снятия масляного картера ремонте подвески демонтажа мостов и коробок передач и других сходных операциях;
- предусмотрен отдельный въезд на участок оснащенный ленточным занавесом для уменьшения потерь тепловой энергии при проезде машин пластиковые ленты легко отклоняются машиной а потом по собственным весом закрывают проезд.
Участок диагностики оснащен следующим оборудованием в соответствии с назначением участка и особенностями обслуживаемых машин и применяемого оборудования и инструмента (пневматический):
- навесной передвижной канавный подъемник ПНК-1. Предназначен для вывешивания над смотровой канавой или подъемником передних или задних мостов строительных машин устанавливается на канаву на внутренние поверхности швеллеров подъемник выбран по грузоподъемности (10 т) исходя из максимально нагрузки на ось обслуживаемых машин.
Система диагностирования представляет собой совокупность средств технической диагностики машин объекта диагностирования и исполнителей. Средства технической диагностики – это средства позволяющие оценивать техническое состояние проверяемого объекта. Они включают: программные средства и компьютерную технику для их реализации; эксплуатационную документацию включающую технологическую пооперационную карту диагностирования диагностическую карту структурно-следственные схемы поиска неисправности диагностические матрицы локализации неисправностей схемы и пооперационные карты восстановления работоспособности и другие информационные материалы; технические средства диагностирования (ТСД) представляющей собой приборы стенды или устройства для определения состояния объекта диагностирования (ОД).
К основным средствам (оборудованию) применяемом для оперативной оценки гидросистемы машины относят:
Для определения обьемного КПД Hydak HMG-3000
Для определения давления в гидросистеме Манометр ТУ 25.02943-84
Для определения расхода рабочей жидкости Расходомер ТУ25.02943-84
Для проверки состояния гидромоторов Стенд-СГНМ
Рисунок 9 - Участок диагностики
Разработка технологических карт
Диагностирование – процесс определения технического состояния и перспектив дальнейшей эксплуатации машины и её сборочных единиц без их разборки. Техническое состояние машины и её сборочных единиц оценивается параметрами по признакам характеризующим эти параметры.
В соответствии с ГОСТ 20911-89 диагностический параметр – параметр объекта используемый при его диагностировании. Для каждого объекта можно указать множество параметров характеризующих его техническое состояние. Их выбирают в зависимости от метода диагностирования уровня информативности и точности трудоёмкости поддержания и восстановления работоспособности объекта различных организационно-экономических факторов.
Гидросистема машины состоит из четырех контуров:
погрузочного оборудования;
управления гидрораспределителем;
рулевого управления;
аварийного рулевого управления.
Питание всех контуров рабочей жидкостью осуществляется из гидробака Б. Гидробак оборудован сливным ниппелем ВН сливным фильтром Ф1 с переливным клапаном и сигнализатором РД засорения фильтра горловиной заправочной РДБ которая имеет встроенный
фильтр-сапун регулятор давления в гидробаке и заливной сетчатый фильтр. Контур погрузочного оборудования состоит из насоса Н1 2-секционного гидрораспределителя Р1 с прямым гидравлическим управлением гидроцилиндра ковша Ц3 двух гидроцилиндров Ц4 и Ц5 стрелы.
Насос Н1 подает рабочую жидкость из гидробака Б к гидрораспределителю Р1. На входе в гидрораспределитель установлен предохранительный клапан ограничивающий давление в контуре и отрегулированный на давление 20 МПа (200 кгссм2). Питание золотников гидрораспределителя Р1 осуществляется по параллельной схеме.
Первый золотник гидрораспределителя Р1 имеет три положения: «Удержание ковша» (нейтральное положение) «Запрокидывание ковша» «Разгрузка ковша» и управляет гидроцилиндром ковша Ц3. Для защиты штоковой полости гидроцилиндра ковша от перегрузки в гидрораспределителе установлен предохранительный клапан с давлением настройки 15 МПа (150 кгссм2) и обратный клапан. Для защиты поршневой полости гидроцилиндра ковша установлен предохра-
нительный клапан с давлением настройки 25 МПа (250 кгссм2) и обратный клапан. Обратные клапаны служат для предотвращения образования вакуума в полостях гидроцилиндра ковша Ц3.Второй золотник гидрораспределителя Р1 управляет гидроцилиндрами стрелы Ц4 Ц5 и
имеет четыре положения: «Удержание стрелы» (нейтральное положение) «Подъем стрелы» «Опускание стрелы» и «Плавающее стрелы». Положение «Плавающее стрелы» является фиксированным. Фиксация происходит за счет встроенного в блок управления БУ механического фиксатора. Для предотвращения образования вакуума в полостях гидроцилиндров Ц4 и Ц5 на этой рабочей секции установлены два обратных клапана.Для ограничения скорости опускания стрелы и недопущения кавитации дроссель ДР с обратным клапаном установлен в линии гидрораспределителя Р1 - поршневая полость гидроцилиндров стрелы Ц4 и Ц5. Контур управления гидрораспределителем Р1 состоит из блока клапанов с пневмогидроаккумулятором БК и одного блока управления БУ. Питание блока клапанов с пневмогидроаккумулятором БК осуществляется от контуров погрузочного оборудования и рулевого управления. Через клапан «ИЛИ» и редукционный клапан настроенный на давление 3.0 - 3.5 МПа (30 - 35 кгссм2) производится зарядка пневмогидроаккумулятора. От пневмогидроаккумулятора рабочая жидкость под давлением подается к блоку управления БУ.В аварийной ситуации когда заглох дизель а погрузочное оборудование находится в поднятом положении запаса рабочей жидкости в пневмогидроаккумуляторе блока клапанов БК достаточно для трех-четырех включений золотника что позволяет опустить погрузочное оборудование.
Параметры диагностирования
Гидросистема в целом:
- Внешние утечки рабочей жидкости в руковах и патрубках;
- Уровень масла в гидробаке;
- Давление масла в гидросистеме;
-Подача при номинальном давлении;
- Коэффициент подачи;
- Крутящий момент при номинальном давлении;
- Температура нагрева корпуса;
- Виброакустические параметры;
- Перетечки рабочей жидкости по зазорам золотника;
- Внешние утечки рабочей жидкости;
- перепад давления на гидрораспределитель;
- Время срабатывания;
- Сопративления перемещению золотника;
- Внутренние перетечки рабочей жидкости;
- Плавность хода штока;
- Состояние поверхности штока;
- Пропускная способность;
- Наличие металлической стружки;
-Температура рабочей жидкости в баке;
-Кинематическая вязкость жидкости;
-Концентрация механических примесей;
Организация заправки выбор ТСМ перебазирование машин.
1 Организация заправки и выбор ТСМ
Средний часовой расход топлива двигателем с учетом степени его загруженности можно определить по формуле
Gч = 103×Gном×[kдв×(kдм×kN - kх)+kх] (11.1)
где:коэффициент 103 учитывает расход топлива в период запуска и регулировки;
Gном - часовой расход топлива на номинальном режиме работы двигателя;
kдв- коэффициент использования двигателя по времени (принимается 06 08);
kдм- то же по мощности (принимается 04 09);
kN- коэффициент учитывающий изменение расхода топлива в зависимости от степени использования двигателя по мощности (принимается 10 125);
kх- коэффициент учитывающий расход топлива при работе двигателя на холостом ходу (принимается 025).
Часовой расход топлива кгчас на номинальном режиме определяется по формуле:
где:Ne - эффективная мощность двигателя в кВт;
- удельный расход топлива (для карбюраторных двигателей 300 340 гркВт×час для дизельных 225 240 гркВт×час).
Величина коэффициента kдв для различных СДМ принимается равной:для автогрейдера 065 07; автосамосвала 06 08; бульдозера 08; катков пневмошинных 06 07; экскаваторов 07 08; асфальтоукладчика 07 08; катков самоходных статического действия 05 06; погрузчиков 08.
Расход топлива для пусковых двигателей принимается в пределах 3% от расхода основных двигателей СДМ.
Проводим расчет количества топлива результаты заносим в таблицу 11.1
Таблица 11.1 – Расчет расхода топлива
погрузчик Амкодор-332
Бульдозер Четра ТК-11
Для автосамосвалов расход топлива определяется на основании пробега:
где Gн- норма расхода на 100 км;
L-дальность транспортирования;
m-число рейсов в час.
Определив среднечасовой расход топлива для машин всех типов и учитывая продолжительность их работы в течение года в часах определяют годовую потребность в топливе для машин парка.
Годовая потребность ДТ:
Годовая потребность в бензине:
Необходимое количество топливозаправщиков зависит от их вместимости и от расстояния от нефтебазы до участков выполнения работ.
Производительность топливозаправщика определяется по формуле:
гдеqт - грузоподъемность заправщика АТЗ-4-52;
t3 - время заправки на нефтебазе (05 08 часа);
V1 и V2 - средняя скорость движения заправщика с топливом и порожнего (принимается V1 =40 50 кмч; V2 =60 70 кмч);
t2 - время заправки СДМ на участке (в зависимости от количества машин 1 2 часа).
Пз = 607500(40 + 609045 + 609065 + 90) = 2004 кгч
Определяем количество топливозаправщиков:
Расход смазочных материалов определяется в % от расхода топлива:
моторное масло для карбюраторных двигателей – 2 35%; дизельное масло – 5 55%; трансмиссионные масла – 07 14%; пластичные смазки – 02 03%.
Результаты расчета количества масел заносим в таблицу 11.2
Таблица 11.2 – Количество масел.
Потребное количество в год тгод
Трансмиссионное масло
Расход в килограммах рабочих жидкостей для гидросистем СДМ планируется на 1 час работы машины в следующих пределах: автогрейдеры бульдозеры погрузчики 001 004 кгчас; экскаваторы одноковшовые 007 009 кгчас; асфальтоукладчики 010 014 кгчас.
где R – расход в килограммах рабочих жидкостей для гидросистем СДМ;
n – количество машин одного типа;
Т – количество часов работы машины в год.
2 Перебазирование машин
При транспортировке СДМ с базы на участки строительства дороги или с участков в РРМ для ТО или ремонта колесные машины перемешаются своим ходом. На буксире или на прицепе-тяжеловозе с тягачом. Гусеничные машины транспортируются только на прицепе тяжеловозе.
Для транспортировки СДМ принимаем трейлер Трал Trailer грузоподъемностью 60 тонн (длинна рабочей площадки 12 м высота погрузочной площадки 1250 мм ширина-2500мм также имеются уширители выдвижные до 3000мм)
Для перевозки обслуживающего персонала СДМ (водителей) принимаем автомобиль-фургон УАЗ-451Б.
Технико-экономическое обоснование инженерных решений
В зависимости от задач решаемых при оценке поддержании и восстановлении работоспособности машин можно используют: контроль работоспособности поиск неисправностей прогнозирование технического состояния а также их сочетания.
При проектировании производственного корпуса было принято решение об использовании электрокаров для подвозки агрегатов с участков по ТО и ремонту в агрегатный и прочие специализированные участки и обратно.
Были приняты следующие решения:
- агрегатный участок и зона ремонта размещены рядом для сокращения путей транспортировки;
- применено техническое решение в конструкции крана которое позволяет управлять им как из кабины расположенной на кране так и с помощью проводного пульта с пола цеха.
- для передачи грузов с кран-балки на агрегатно механический участок использована рельсовая тележка;
- при необходимости транспортирования узлов и деталей с участка на участок предлагаю использовать электрокары и малогабаритные вилочные погрузчики с электрическим приводом либо с газовым ДВС;
- все ворота на производственные участки оснастить ленточными завесами предохраняющими от потери тепла и не препятствующими прохождению транспорта и людей а так же при необходимости оснастить проходы и проезды выходящие на улицу тепловыми завесами;
- для газоотводной установки предлагается вывести воздушную магистраль не сразу на крышу а пустить ее частично по помещению участков ТО и диагностирования с целью дополнительного обогрева в зимний период;
Предполагаемый экономический эффект может быть достигнут за счет:
- экономии затрат на покупку и эксплуатацию дополнительных средств перемещения агрегатов с одного участка на другой;
- снижения затрат на оплату дополнительным рабочим;
- использование одного крана в пределах всей зоны ремонта.
- снижение затрат на эксплуатацию дополнительного оборудования.
- возможности использования существующих участков для капитального ремонта за счет дооснащения дополнительным оборудованием.
Для предупреждения травматизма и профессиональных заболеваний в производственных вспомогательных и административно-бытовых помещениях организация рабочих мест выполнена в соответствии с общими требованиями безопасности труда предусмотренными ГОСТ 12.3.002 – 75.
Для профилактики и борьбы с пожарами в каждом помещении предусмотрены огнетушители ящики с песком.
Цена ремона— цена включающая себестоимость и прибыль от ремонта.
Фактическая реализация товаров (услуг) поценам изготовителя(цена производителя заводская цена) возможна преимущественно в том случае когда в структуре цен нет косвенных налогов. В современной хозяйственной практике перечень таких товаров (услуг) ограничен. Как правило в структуре цены в качестве непосредственных ценообразующих элементов присутствуют косвенные налоги. В цены абсолютного
большинства товаров (услуг) включенналог на добавленную стоимость(НДС).
В структуре цен на ряд товаров присутствуетакциз. Данный косвенный налог включается в цену товаров для которых характерен неэластичный спрос т. е. повышение уровня цены в результате включения в нее акциза не ведет к снижению объема покупок данного товара. Тем самым реализуется фискальная налоговая функция — обеспечение доходов бюджета. Вместе с тем подакцизные товары не должны быть товарами первой необходимости: введение акциза в этом случае противоречило бы требованиям социальной политики. В связи с этим и в отечественной и в международной практике подакцизными являются в первую очередь алкогольная продукция и табачные изделия. Такие товары как сахар и спички характеризующиеся самой высокой степенью неэластичности спроса подакцизными не являются поскольку входят в перечень товаров первой необходимости.
Примемуровень цены изготовления —
у.е. за одно изделие. Ставка налога на добавленную стоимость равна 20%. Тогда уровень отпускной цены т. е. цены превышающей цену ремонта на величину НДС составит:
Цотп = Цизг *НДС:100 = 95 у.е · 20% : 100% = 114у.е
В результате проведения расчетов выбраны типы машин необходимые для выполнения дорожно-строительных работ в соответствии с вариантом указанном в задании.
Для каждого типа машин определена эксплуатационная часовая и годовая производительность. В соответствии с определенной производительностью рассчитано количество машин необходимое для выполнения данного вида работ.
Для выбранного комплекта машин определено количество технических обслуживаний и ремонтов в соответствии с характеристиками машин и начальными условиями. По результатам расчета количества ТО и ремонтов спроектирована база механизации.
Зоны и участки базы механизации предназначены для выполнения на них технических обслуживаний и ремонтов выбранного комплекта машин. При проектировании базы механизации учтено что часть технических обслуживаний и ремонтов проводится на участках проведения работ для чего проведен расчет количества передвижных авторемонтных мастерских.
Для обеспечения выбранного комплекта машин топливом и смазочными материалами проведены расчеты и определено необходимое количество топлива смазочных материалов и гидравлической жидкости. Для подвоза ТСМ от нефтебазы до базы механизации и развоза ТСМ по дорожным участкам проведен расчет и определено количество топливозаправщиков.
Список использованных источников
Максименко А.Н. Эксплуатация строительных и дорожных машин: Учебник. – Мн.: УП «Технопринт» 2004. – 400 с.; ил..
Новые технологии и машины при строительстве содержании и ремонте автомобильных дорог Под ред. А.Н. Максименко. – Мн.: Дизайн ПРО 2000. – 224 с.
Дорожно-строительные машины и комплексы: Учебник для вузов по дисциплине «Дорожные машины» Под общ. ред. В.И. Баловнева. – 2-е изд. доп. и перераб. – М. – Омск. Изд-во СибАДИ 2001. – 528 с.
Дорожно-строительные машины: Учебник Под общ. ред.
А.М. Щемелева. – Мн.: УП «Технопринт» 2000. – 515 с.
Эксплуатация дорожных машин: Учебник для вузов А.М. Шейнин Б.И. Филиппов В.А. Зорин и др.; Под общ. ред. А.М. Шейнина. – М.: Транспорт 1992. – 328 с.
Головин С.Ф. Проектирование предприятий по эксплуатации дорожных машин: Учеб. пособ. для вузов. С.Ф Головин. В.А Зорин– М.: Транспорт 1991. – 215 с.
Максименко А.Н. Эксплуатация строительных и дорожных машин: Учеб. пособ.. – Мн.: Выш. шк. 1994. – 221 с.
Ивашков И.И. Монтаж эксплуатация и ремонт подъемно-транспортных машин: Учебник для студентов вузов по специальности
Рекомендации по определению себестоимости машиночаса эксплуатации строительных и дорожных машин с учетом процесса их старения: методические указания по курсу «Эксплуатация строительных и дорожных машин» для студентов специальности 1-36 11 01 Сост. А. Н. Максименко. – Могилев: Белорус. - Рос. ун-т 2009. – 39 с.
Тайц В. Г. Безопасная эксплуатация грузоподъемных машин: учеб. пособие В. Г. Тайц. – М.: Академкнига 2005. – 383 с. : ил.
Эксплуатация дорожных машин: учебник А. М. Шейнин [и др.]; под общ. ред. А. М. Шейнина. – М.: Транспорт 1992. – 328 с. : ил.
Эксплуатация строительных и дорожных машин: учебно-методическое пособие к курсовому проектированию по дисциплине для студентов специальности 1–36 11 01 «Подъемно–транспортные строительные дорожные машины и оборудование» Сост. А. В. Вавилов [и др.]. – Минск: БНТУ 2003. – 95 с.
Приложения к методическим указаниям по дисциплине «Эксплуатация СДМ» [Электрон. ресурс] Ред. А. Н. Максименко. – Режим доступа : е : Базы программ и чертежи Дисциплины ПДМ Специализации Специальные Эксплуатация СДМ Эксплуатация СДПТМ.doc.
Суммарная трудоемкость
uchastokto.dwg

Наименование оборудования
Инструментальный шкаф
Противопожарный инвентарь
Смазочно заправочная установка
Система сбора отработанных масел
Установка для промывки фильтров
Подметально-уборочная машина
Колонка для продувки рукавов
Комплект мастера наладчика
Колонка для подкачки шин
karta_to-2.dwg

Проверить крепление фланцевого корданного вала.
Спустить конденсат из воздушных балонов пневмо-привода тормозов.
Заменить элементы фильтров тонкой и грубой очистки топлива .
СМАЗОЧНЫЕ И ОЧИСТИТЕЛЬНЫЕ РАБОТЫ
Смазоть узлы трения через прес-масленки и капельные масленки в соответствии с картой смазки.
Сменить масло в картере двигателя
очистить масленные фильтра тонкой очистки.
Проверить уровень масла в бачке насоса гидроусилителя
картерах рулевого механизма.
Проверить крепление стартера проверить присоединение клем.
Проверить крепление генератораи при необходимости подтянуть болты.
Проверить степень заряженности аккумулятора и уровень электролита.
ПЛОТФОРМА И ОПЕРЕНИЕ
Проверитькрепление балки запорного механизма кабины и балки задней опоры кабины с рамой.
Проверить крепление передних опор и стремянок платформы.
Проверить состояние рамы
кронштейнов ресор и вкладышей кранштейнов.
Проверить стремянки передних и задних ресор
пальцев и стремянок ушек ресор.
Проверить крепление буксирного прибора с поперечной рамы
затяжку и шплинтовку прорезной гайки.
Проверить работу компресора
герметичность соединений трубопроводов и приборов.
Проверить шплинтовку пальцев вилок штоков тормозных камер и деталей привода
Снять передние ступицы
проверить состояние тормозных колесных механизмов и фрикционов.
Проверить плотность и исправность шлангов гидроусилителя рулевого управления
Проверить осевой люфт вала рулевого колеса отнасительно рулевой колонки .
Проверить крепление насоса гидроусилителя рулевого управления.
Проверить состояние упорных подшипников и шплинтовку гаек шаровых пальцев.
Проверить крепление редуктора к картеру заднего моста.
Проверить состояние заднего моста и отсутствие подтеканий через сальники .
Проверить состояние втулок кронштейнов кабины.
Проверить состояние втулок амортизаторов.
Проверить люфт в шарнирах и шлицевых соединениях корданной передачи.
Проверить крепление картера механизма дистанционного переключения передач с верхней
крышкой коробки передач и промежуточного механизма коробки с рамой.
Проверить состояние и плотность соединений коробки передач.
Проверить и при необходимости закрепить кронштейн и крышку силового цилиндра
Проверить крепление кронштейна задней опоры двигателя к коробке передач
Проверить крепление опоры рычага переключения передач.
Проверить герметичность системы смазки и если нужно устранить неисправность
Проверить крепление труб глушителя
состояние и плотность соединений и при
Проверить действие стеклоочистителей
устройства для обмыва ветрового стекла
исправность механизмов дверей
запорного механизма кабины
Проверить герметичность системы охлождения
крепеление водяного насоса при необхо-
Проверить и подтянуть гайки крепления балки передней и задних опор двигателя
ВКЛЮЧАЯ СИСТЕМЫ ОХЛОЖДЕНИЯ И СМАЗКИ
Осмотреть бульдозер. Проверить состояние кабины
Обший осмотр бульдозера:
ПЕРЕЧЕНЬ РАБОТ ИНСТРУМЕНТЫ
ПОСТОВАЯ КАРТА ОПЕРАЦИЙ ТО-2 Бульдозера
пневмоусилителя сцепления.
Отрегулировать положение опоры коробки передач.
необходимости устранить неисправность
димости устранить неисправность.
запоров бортов платформы.
ВЫПОЛНИТЬ ОПЕРАЦИИ ТО-2
Проверить деформацию тормозных барабанов
Нагрузочная вилка ЛЭ-2
srrrsrrrrer.docx
Определение годового объема выполняемых работ15
1 Расчет годовых объемов работ для строительства дороги15
2 Расчет годовых объемов работ для ремонта дороги16
Выбор технологий и ведущих машин для выполнениягодового объема работ20
Формирование парка машин24
Планирование объемов работ по поддержанию и восстановлению работоспособности машин парка35
Организация ТО и ремонта машин38
1 Определение годовой трудоемкости ТО и ремонтов39
2 Проектирование ПРМ39
Проектирование предприятий по поддержанию и восстановлению работоспособности машин41
Компоновка участка с подбором современного оборудования50
Разработка технологических карт52
Организация запрвки выбор ТСМ перебазирование машин 55
Технико-экономическое обоснование инженерных решений59
Список использованных источников63
karta_to-1.dwg

прибор для проверки фар
новка для мойки двигателя
для наружной мойки машин
Установить бульдозер на ровную площадку
удалить грязь и грунт
регулировочного винта
поддерживающих и опорных катках
очистить и проверить защитную решет-
протереть и очистить кабину внутри
стекла кабины чистым обтирочным материалом.
Протереть стекла окон и дверей
очистки двигателя снять боковые щиты
Проверить путем внешнего осмотра комплектность и состо-
яние сборочныхедениц бульдозера
надежность сединений
убедиться в отсутствии течи маслатоплива
при необходимости устранить неисправ-
Ключи гаечные открытые 14
Проверить крепление и герметичность соединений трубопро-
водов и приборов систем охлаждения
при необходимости закрепить
Ключи гаечные открытые 10
Не допускается течи топлива после запуска
гайки болтов крепле-
ния насоса предпускового подогревателя должны быть затянуты.
герметичность и работоспособность
соединений трубопроводов подогревателей предпускового
отопителя кабины водителя
Перевести все органы управления в нейтральное положение
открыть боковые панели и крышки люков на
верхней панели капота
болты крепления приборов систем охлаж-
дения должны быть затянуты
соединительные шланги и трубо-
проводы систем охлаждения должны быть надежно соединены
печивать герметичность
Закрепить крышки головок цилиндров
проверить состояние про-
масло не должно подтекать
болты крепления масляного
поддона должны быть затянуты
на поверхности поддона не дол-
а из-под прокладки следов подтекания масла.
Ключ гаечный открытый 14
Проверить состояние лакокрасочного и антикоррозионного покры-
при наличии коррозии необходимо после ТО-1 отправить
бульдозер в малярный участок
двери не должны быть согнуты
стекла окон и дверей должны быть целыми
проверить замки дверей
боковых панелей и крышек люков капота
и устранить неисправности.
проверить состояние окраски
зеркал заднего вида и их крепление
Проверить герметичность крышек клапанных коробок
маслозаливной пробки
ключи гаечные открытые 12
Проверить состояние прокладки пробки маслозаливного отверстия
герметичность проверять при работающем двигателе
и прогары деталей не допускаются
гайки болтов крепления кол-
глушителя должны быть затянуты.
Проверить герметичность и крепление коллектора
теля системы выпуска отработавших газов
Ключ гаечный открытый 17 мм
ключ динамометрический
Гайки хомутов крепления патрубков
трубопроводов системы пи-
тания воздуха двигателя должны быть затянуты моментом от
Проверить герметичность разъема воздухоочистителя и
впускных воздухопроводов двигателя
ключ гаечный открытый 14
ключи гаечные кольцевые 17
На поверхности диска не должно быть трещин
диска должны быть затянуты моментом от 150 до 200 Нм.
Проверить состояние и крепление диска муфты эластичной
к маховику двигателя
при необходимости подтянуть болты
Гайки болтов крепления должны быть затянуты
Проверить степень натяжения гусеничной цепи
по провисанию звеньев верхней ветви
номинальное значение
провисания от 40 до 50 мм.
Для трактора Т-11 Проверить и отрегулировать
натяжение гусеничной цепи
Осмотреть и очистить аккумуляторную батарею от пыли
грязи и следов электролита
проверить крепление контактов
наконечников проводов с полюсными штырями
Лампа освещения кабины водителя должна быть исправной
быть исправными выключатель задних рабочих фар и центральный
дорожные и рабочие фары должны быть пра-
вильно отрегулированы и обеспечивать устойчивое освещение
редние и задние фонари внешней световой сигнализации
вращатели задние и боковые должны быть целыми
должен подавать гармонический звук без дребезжания
чаги стеклоочистителей не должны иметь повреждений
жны плотно прилегать к стеклу и перемещаться по поверхности
фары дальнего и ближне-
габаритные огни должны быть надежно закреплены
печивать устойчивое освещение без мигания
Проверить действие приборов освещения
Натяжение ремня считается нормальным
если при усилии 40 Н стре-
ла прогиба ремня вентилятора должна быть в пределах от 7 до 14
ремня генератора 20 мм. Натяжение ремня генератора осу-
ществлять поворотом генератора с упором в стальную крышку.
Пробуксовка ремня привода генератора не допускается.
Открыть крышку ящика аккумуляторных батарей и выключить
очистить и протереть наружную поверхность
аккумуляторных батарей
электролит вытереть чистым обти-
рочным материалом смоченным в растворе нашатырного спирта
стенах баков батарей и крышках трещины и подтекания электро-
наконечники проводов и плоские штыри сма-
зать техническим вазелином
гайки болтов крепления наконечни-
ков должны быть затянуты.
Убедиться в отсутствии выхода замыкающих пальцев гусеницы
осмотреть состояние сборочных единиц
ность болтовых и сварных соединений бульдозера
мости подтянуть крепления
обнаруженные трещины заварить
задиры не допускаются;течь рабочей жидкости
топлива не допускается.
Ключ гаечный открытый 14 мм
материал облицовочный
Трактор Т-11. Проверить крепление и герметичность ГМП
Ключи гаечные открытые 17 мм
метрический мод. МТ-1-120
ключ гаечный открытый
твором кальцинированной соды
при бор для проверки фар
прибор для измерения натяжения
ключи гаечные открытые 8
емкость с 10% раствором нашатырного
ключ гаечный открытый 12
Проверить уровень и плотность электролита в аккумуля-
торной батареи и степень заряженности под нагрузкой
Уровень измерять при помощи уровнемерной трубки
тить в заливную горловину до упора
закрыть сверху пальцем и
уровень электролита должен быть выше защитной решетки
пластин от 10 до 15 мм при необходимости долить дистиллирован-
при необходимости зарядить батарею.
Емкость 2 л с дистиллированной водой
ческого обслуживания аккумуляторных
технологическая карта ТО-1
Технологическая пооперационная карта ТО-1 бульдозера ДЗ-171
Технические требования
Уборочно-моечные работы
Очистка и мойка бульдозера снаружи и снизу
Уборка кабины машиниста
регулировочные и контрольные работы
Электротехнические работы
Убедиться в отсутствии течи масла.
Проверить состояние коробки передач
Проверить натяжение ремня вентилятора и генератора
Крепление должно быть надежным.
Трактор Т-11. Проверить крепление привода управления ГМП
Рекомендуемые чертежи
- 25.10.2022