Пластинчатый конвейер



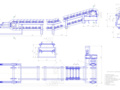

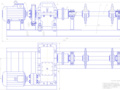
- Добавлен: 25.10.2022
- Размер: 1 MB
- Закачек: 1
Описание
Состав проекта
![]() |
![]() |
![]() ![]() ![]() ![]() |
![]() |
![]() ![]() |
![]() ![]() |
![]() ![]() ![]() |
![]() ![]() ![]() |
![]() ![]() ![]() |
![]() ![]() |
![]() ![]() ![]() ![]() |
![]() ![]() ![]() ![]() |
![]() ![]() ![]() ![]() |
![]() ![]() ![]() ![]() |
![]() ![]() ![]() ![]() |
![]() |
![]() ![]() ![]() |
Дополнительная информация
КП_МНТ_СПЕЦ_ОВ.cdw

КП_МНТ_СПЕЦ_ПРИВ_СТАН1.cdw

КП_МНТ_СПЕЦ_ПРИВ_БАРАБАН1.cdw

КП_МНТ_ПРИВ_СТ.cdw

КП_МНТ_ОВ1.cdw

КП_МНТ_ПРИВ_БАРАБАН.cdw
