Организация технического обслуживания и ремонта парка машин с разработкой передвижного диагностического поста на базе «Газель»




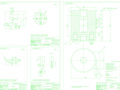
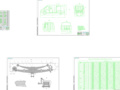
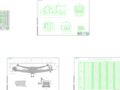

- Добавлен: 25.10.2022
- Размер: 7 MB
- Закачек: 2
Описание
Состав проекта
![]() |
![]() ![]() |
![]() |
![]() ![]() ![]() ![]() |
![]() |
![]() ![]() |
![]() ![]() |
![]() ![]() ![]() |
![]() ![]() |
![]() ![]() ![]() |
![]() ![]() ![]() ![]() |
![]() |
![]() |
![]() ![]() ![]() ![]() |
![]() ![]() ![]() ![]() |
![]() ![]() |
![]() ![]() |
![]() |
![]() ![]() |
![]() ![]() |
![]() ![]() |
![]() ![]() ![]() |
![]() ![]() |
![]() ![]() ![]() ![]() |
![]() |
![]() |
![]() ![]() |
![]() ![]() |
![]() ![]() ![]() |
![]() |
![]() ![]() ![]() ![]() |
![]() ![]() ![]() ![]() |
![]() ![]() ![]() |
![]() ![]() |
![]() |
![]() |
![]() ![]() ![]() ![]() |
![]() ![]() ![]() ![]() |
![]() |
![]() |
![]() ![]() ![]() ![]() |
![]() |
![]() ![]() ![]() ![]() |
![]() ![]() |
![]() ![]() ![]() ![]() |
![]() ![]() ![]() |
Дополнительная информация
3,4,5 лист_recover001.dwg

подьемника автомобильного
ПЗ.01.00.Сб Рессора 1
ПЗ.02.00.Сб Дополнительная рессора 1
ПЗ.03.00.Сб Продольная балка 1
ПЗ.04.00.Сб Балка моста 1
ПЗ.00.01.Сб Стремянка 3
ПЗ.00.02.Сб Хомутики 6
ПЗ.00.03.Сб Кронштейн 4
ПЗ.00.04.Сб Масленка 1
ПЗ.00.05.Сб Ушко рессоры 1
ПЗ.00.06.Сб Накладка 3
ПЗ.00.07.Сб Опорный сухарь 1
ПЗ.00.08.Сб Фиксаторная подушка 1
Числа месяца и виды ТО и ремонта
МЕСЯЧНЫЙ ПЛАН-ГРАФИК ТЕХНИЧЕСКОГО ОБСЛУЖИВНИЯ И РЕМОНТА СТРОИТЕЛЬНО-ДОРОЖНЫХ МАШИН НА МАРТ МЕСЯЦ 2014г.
Диагностическая машина (Вид общий)
Техническая характеристика:
Базовая машина "Газель
Скорость передвижения-45 кмч
Обслуживающий персонал-2 чел.
Количество обслуживаемых машин
000000000000000000000О
190605-ДП-14-3453-01-00-00СБ Рессора 1
190605-ДП-14-3453-02-00-00СБ Дополнительная рессора 1
190605-ДП-14-3453-03-00-00СБ Продольная балка 1
190605-ДП-14-3453-04-00-00СБ Балка моста 1
190605-ДП-14-3453-01-01-00 Стремянка 3
190605-ДП-14-3453-01-02-00 Хомутики 6
190605-ДП-14-3453-01-03-00 Кронштейн 4
190605-ДП-14-3453-01-04-00 Масленка 1
190605-ДП-14-3453-01-05-00 Ушко рессоры 1
190605-ДП-14-3453-01-06-00 Накладка 3
190605-ДП-14-3453-01-07-00 Опорный сухарь 1
190605-ДП-14-3453-01-02-00 Фиксаторная подушка 1
0605-ДП-14-3453-00-00-00ПЗ Пояснительная записка 1
0605-ДП-14-3453-01-00-00СБ Задняя подвеска 1
Месячный план-график
ДОКЛАД11.doc
государственной экзаменационной комиссии
вашему вниманию предлагается дипломный проект на тему:
«Организация технического обслуживания и ремонта парка машин на базе Спецстрой России ФГУП «ГУССТ №4 УПП №422» с разработкой передвижного диагностического поста»
Под эксплуатацией строительно-дорожных машин и оборудования (СДМ и О) принято понимать комплексную систему инженерно-технических и организационных мероприятий обеспечивающих наиболее эффективное использование возможностей машин высокую их эксплуатационную надёжность а также минимальные простои при техническом обслуживании (ТО) и ремонте с минимальными затратами.
Система планово-предупредительных работ долгое время не подвергалась существенным изменениям. По мере усложнения конструкций машин увеличения их количества а также необходимости повышения затрат на эксплуатацию все очевиднее становятся их недостатки. Так в связи со значительным рассеиванием фактических значений показателей надежности машин принятая в настоящее время система ППР не обеспечивает заданного срока работы изделий и не может обеспечить полного использования их ресурса.
Поэтому в настоящее время наметилась тенденция замены принятой системы ППР системой технического обслуживания и ремонта по техническому состоянию.
В ее основу положен плановый контроль состояния машины с помощью диагностических средств и проведение ТО и ремонта в зависимости от этого состояния.
В проекте рассчитан производственный корпус подобранно оборудование.
На основании парка машин составлен годовой план ТО и Р. Для составления плана исходными данными являются фактическая наработка машин и их планируемая наработка за год.
Эффективность технического обеспечения машин на строительных объектах зависит как от характера распределения работ между различными типами мастерских так и оснащения передвижных средств технического обслуживания и ремонта.
Для проведения диагностирования машин непосредственно на месте их эксплуатации в настоящее время применяется разработанная в ГОСНИТИ мобильная установка (станция) КИ-4270 (рисунок 3.1) предназначенная для диагностирования технического состояния гусеничных машин при проведении технического обслуживания. Она базируется на машине Газель.
В кузове Газели смонтированы стеллаж верстак стол отсеки контейнеры с приборами приспособлениями и инструментом компрессор и электрооборудование.
В комплект машины для технического диагностирования на базе УАЗ-452 входят:
- измеритель натяжения гусениц КИ -13903;
- индикатор расхода газов КИ - 4887-11;
- вакуум-анализатор КИ - 5315;
- устройство для измерения зазоров кривошипно-шатунном механизме КИ -11140;
- устройство для проверки прецизионных пар топливных насосов КИ -4802;
- устройство для проверки давления в системе топливоподачи КИ -4801;
- топливомер КИ – 4818;
- динамометр ДПУ – 002-2;
- люфтометр тракторный КИ - 4813;
- приспособление для проверки зазоров в подшипниках КИ – 4850;
- устройство для определения износа гусеничной цепи КИ - 4943;
-линейка для проверки схождения колес КИ – 650;
- устройство для определения технического состояния гидросистемы -
- прибор для проверки схождения колес КИ - 650;
- прибор для проверки автотракторного оборудования КИ - 1093;
- прибор для проверки контрольно-измерительных приборов Э – 204;
- компрессорно-вакуумная установка КИ - 4942;
- прибор для измерения втулочно-роликовых цепей КИ - 1854;
- нефтеденсиметр Б-2 и Б-3;
При диагностировании в полевых условиях хорошие результаты может показать смонтированный в чемодане и имеющий массу в 195 кг комплект диагностирующей аппаратуры КИ – 13901.
Так же в дипломном проекте рассчитано приспособление для разборки и сборки рессор.
Предназначено для зажима рессор при разборки рессор. Состоит из рукоять червяка гайки корпуса зажим опорной пластины отверстий под крепежные болты.
При разборке сборке предварительно снятую рессору зажимают в приспособлении и ослабляют хомутики не вынимая рессоры из приспособления. Снимают стремянки и болт держащие съемное ушко.
Далее разжимаем приспособление и снимаем по очереди листы рессор и выполняем проверку изогнутости.
Задание Сердюков-П.docx
Государственное автономное профессиональное образовательное учреждение Краснодарского края
«Новороссийский колледж строительства и экономики»
Специальность: 190631 «Техническое обслуживание и ремонт автомобильного транспорта»
Зам. директора по УР
Тема дипломного проекта: «Организация технического обслуживания и ремонта парка машин на базе СТО Першерон с разработкой передвижного диагностического поста»
Студенту Сердюкову Ивану Александровичу гр. АМ-41 Курс 4
Рассмотрено на заседании цикловой комиссии
автомеханических дисциплин
1 Диагностика как дополнение планово-предупредительных работ
2 Организационные приемы диагностики
Расчетно-технологическая часть
1 Годовой план технического обслуживания и ремонта
2 Выбор технологического оборудования
Расчетно-проектировочная часть
3 Оснащение постов диагностирования
4 Оснащение передвижных средств диагностирования
5 Машина технического диагностирования
Техника безопасности и охрана окружающей среды
1 Основные меры безопасности проектируемого предприятия
2 Общая характеристика опасных и вредных производственных факторов
3 Электробезопасность
1 Расчет капитальных вложений.
2 Смета затрат на производство ТО и Р эксплуатируемой техники
Лист 1Объект проектирования формат А1
Лист 2 Чертеж общий формат А1
РЕКОМЕНДУЕМАЯ ЛИТЕРАТУРА
В.И. Карагодин Н.Н Митрохин - Ремонт автомобилей и двигателей.- 9-е изд. стер.-- М.:Издательский центр «Академия» 2013.-496 с.
В.М. Виноградов – Технологические процессы ремонта автомобилей: - 5-е изд. стер.- М.:Издательский центр «Академия» 2012.-432 с.
Б.Д.Колубаев И.С. Туревский – Дипломное проектирование станций технического обслуживания автомобилей: учеб. пособие – М.: ИД «ФОРУМ»: ИНФРА – М 2008. –
И.С. Туревский – Дипломное проектирование автотранспортных предприятий: учеб. пособие – М.: ИД «ФОРУМ»: ИНФРА – М 2007. –246 с.
И.С Туревский - Техническое обслуживание автомобилей. Книга 2. Организация хранения технического обслуживания и ремонта автомобильного транспорта: учебное пособие. – М.: ИД «ФОРУМ»: ИНФРА – М 2008. –256 с.
Справочник специалиста по ремонту автомобилей В.Д Александров Л.И. Арзамасцев Б.С. Васильев и др.; под ред. В.М.Приходько. – М.: ИКЦ «Академкнига» 2007. – 439 с.: ил.
Круглов С.М. Справочник автослесаря по техническому обслуживанию и ремонту легковых автомобилей: Справочное пособие. – 2-е изд. – М.: Высшая школа 2005-391с
1 Корпус производственный.dwg

ДПДМ2012.001.00.00.00 ДО
ДПДМ2012.001.00.00.00 ПК
ДПДМ2012.ХХХ.00.00.00ПК
8 Стенд.dwg

Стенд диагностический
НФ БГТУ им. В.Г. Шухова
Условные обозначения
Предохранительный клапан
ДПДМ2012.001.00.00.00ПК
Номинальная производитель-
Техническая характеристика
Примечание: гибкий трубопровод
показаны по конструктивным
6 Тензодатчик.dwg

ДПДМ2012.001.02.01.03
Неуказанные предельные отклонения размеров:
ДПДМ2012.001.02.01.02
ДПДМ2012.001.02.01.01
НФ БГТУ им. В.Г. Шухова
ДПДМ2012.001.02.01.02
Примечание: сварку проводить электродо типа
Э 50 А марки УОНИ 1355
Техническая характеристика
Максимальная нагрузка
Основная погрешность
Относительная чуствительность 2 10
чувствительности датчиков
Рабочие климатические условия
Относительная влажность
ПЗ.doc
Под эксплуатацией строительно-дорожных машин и оборудования (СДМ и О) принято понимать комплексную систему инженерно-технических и организационных мероприятий обеспечивающих наиболее эффективное использование возможностей машин высокую их эксплуатационную надёжность а также минимальные простои при техническом обслуживании (ТО) и ремонте с минимальными затратами. Поэтому как только машина введена в эксплуатацию возникает ряд вопросов: как спланировать и организовать ТО и ремонт какие формы наиболее целесообразны для данного типа машин и конкретных условий эксплуатации что когда как и зачем необходимо проверить и отрегулировать.
Цель теории состоит в том чтобы дать необходимые теоретические знания и практические навыки в области эксплуатации машин и оборудования и научиться управлять использованием и техническим состоянием машин с применением современных средств и методов технической диагностики руководствуясь принципом минимизации эксплуатационных затрат.
Основной задачей инженера-механика занимающегося эксплуатацией машин является поддержание машин в технически исправном состоянии что получило название технической эксплуатации. С точки зрения теории надежности техническая эксплуатация - это обеспечение надежности машин и оборудования в условиях эксплуатации. Отсюда возникает вторая задача — инженера-механика увязывать разработки теории надежности с практическими задачами возникающими при эксплуатации машин. Эта задача заключается в умении раскрывать закономерности изменения технического состояния машин и потери ими работоспособности в процессе эксплуатации в изучении методов и средств направленных на поддержание машин в технически исправном состоянии.
С точки зрения современной теории управления техническая эксплуатация как и всякая теория управления имеет обратную связь в виде поступления информации об эксплуатационной надежности машин что немыслимо без современных средств и методов технической диагностики. Поэтому увязка технологии и организации диагностирования машин с существующей системой планово-предупредительного ремонта (ППР) является третьей важной задачей - инженера-механика.
По своему характеру техническое диагностирование разделяется на функциональное и тестовое. Функциональное техническое диагностирование осуществляется во время функционирования объекта диагностирования на который поступают только рабочие воздействия. Тестовое техническое диагностирование предполагает наведение на объект диагностирования специальных тестовых воздействий.
По обхвату техническое диагностирование разделяется на общее и локальное. Общей системой технического диагностирования устанавливается техническое состояние всего объекта в целом тогда как локальной системой - только техническое состояние отдельных составных частей объекта диагностирования.
1.Наименование парка строительно-дорожной техники
Таблица 1.1 – Номенклатура парка строительно-дорожной техники
Наработка на начало года
Продолжение таблицы 1.1
2 Расчет годового режимов рабочих машин и составления годового плана ТО и ремонта машин
Для разработки годового плана ТО и Р машин следует получить возможное количество часов их работы за год (дефективные нормы).
Действительный годовой фонд времени или дефективная норма Тд определяется:
где ТН - номинальное число часов работы машины за год час;
КВ = 085-095 - коэффициент использования рабочего времени машин в течении года;
Номинальное число рабочих часов машины в год равно:
ТН = (ДК - (ДВ + ДП)) . tCM . ПСМ час;
здесь ДК - количество календарных дней в году (365 д.);
ДВ - количество воскресных и субботних дней в году (105 д.);
Дп - количество праздничных дней в году (7 д.);
tсм - длительность рабочей смены (8 час);
Псм - число смен работы машин в сутки (1).
Тн = (365 - (105 + 7)) . 8 . 1 = 2024
Тд.эк. = 2024 .085 = 17204;
Тд.б. = 2024 . 075 = 1518ч;
Tд.ав. = 2024 . 082 =16597 ч;
Тд.погр. = 2024 . 085 = 17204 ч;
Тд.кр. = 2024 . 092 = 1862ч;
Тд..тр.= 2024 .08 = 16192 ч;
Число технических обслуживании и ремонтов каждого вида NTO Р которые должны быть проведены в планируемом году для соответствующей машины рассчитывают по формуле:
где Тф - величина фактической наработки на начало планируемого года со времени проведения последнего аналогичному расчетному вида технического обслуживания ремонта или с начала эксплуатации час;
Тп.л.- планируемая наработка или директивная норма на расчетный год час;
Тп - доремонтный или межремонтный ресурс соответствующего вида технического обслуживания или ремонта по которому ведется расчет час;
Nп - число всех видов технических обслуживании и ремонтов с периодичностью большей периодичности того вида по которому ведется расчет (при расчете капитального ремонта Nп - 0).
Таблица 1.2 - Число ТО и Р для каждого вида машин в планируемом году
Продолжение таблицы 1.2
Экскаватор ЭО-2621 инвентарный номер 101
К.: NTOP=((16716+17204)5760)-0=0
Т.: NTOP=((7116+17204)960)-0=2
TO-2: NТОР=((2316+17204)240)-2=6
TO-1: NТОР=((516+17204)60)-8=21
Экскаватор ЭО-2621 инвентарный номер 102
К.: NTOP=((42003+17204)5760)-0=1
Т.: NTOP=((3603+17204)960)-1=1
TO-2: NТОР=((1203+17204)240)-2=5
TO-1: NТОР=((03+17204)60)-7=21
Экскаватор ЭО-2621 инвентарный номер 103
К.: NTOP=((6476+17204)5760)-0=0
Т.: NTOP=((6476+17204)960)-0=2
TO-2: NТОР=((1676+17204)240)-2=5
TO-1: NТОР=((476+17204)60)-7=22
Экскаватор ЭО-4321Б инвентарный номер 104
К.: NTOP=((55446+17204)7680)-0=0
Т.: NTOP=((7446+17204)960)-0=2
TO-2: NТОР=((246+17204)240)-2=5
TO-1: NТОР=((246+17204)60)-7=22
Экскаватор ЭО-4121 инвентарный номер 105
К.: NTOP=((6461+17204)7680)-0=0
Т.: NTOP=((6461+17204)960)-0=2
TO-2: NТОР=((1661+17204)240)-2=5
TO-1: NТОР=((461+17204)60)-7=22
Экскаватор ЭО-5126 инвентарный номер 106
К.: NTOP=((36223+17204)9600)-0=0
Т.: NTOP=((6223+17204)1000)-0=2
TO-2: NТОР=((1223+17204)500)-2=1
TO-1: NТОР=((223+17204)100)-7=14
Экскаватор ЭО-5126 инвентарный номер 107
К.: NTOP=((47853+17204)9600)-0=0
Т.: NTOP=((7853+17204)1000)-0=2
TO-2: NТОР=((2853+17204)500)-2=2
TO-1: NТОР=((853+17204)100)-4=14
Экскаватор ЭО-5124 инвентарный номер 108
TO-1: NТОР=((223+17204)100)-3=14
Экскаватор ЭО-5124 инвентарный номер 109
Экскаватор ЭО-5122 инвентарный номер 110
К.: NTOP=((58668+17204)9600)-0=0
Т.: NTOP=((8668+17204)1000)-0=2
TO-2: NТОР=((3668+17204)500)-2=2
TO-1: NТОР=((668+17204)100)-4=13
Экскаватор ЭО-5122 инвентарный номер 111
К.: NTOP=((30149+17204)9600)-0=0
Т.: NTOP=((149+17204)1000)-0=1
TO-2: NТОР=((149+17204)500)-1=2
TO-1: NТОР=((149+17204)100)-3=14
Бульдозер Д532 Т170 инвентарный номер 212
К.: NTOP=((30149+1518)7680)-0=0
Т.: NTOP=((1349+1518)960)-0=1
TO-2: NТОР=((1349+1518)240)-1=5
TO-1: NТОР=((149+1518)60)-6=19
Бульдозер Д532 Т170 инвентарный номер 213
К.: NTOP=((48853+1518)7680)-0=0
Т.: NTOP=((853+1518)960)-0=1
TO-2: NТОР=((853+1518)240)-1=5
TO-1: NТОР=((253+1518)60)-6=19
Бульдозер Д532 Т170 инвентарный номер 214
К.: NTOP=((49334+1518)7680)-0=0
Т.: NTOP=((1334+1518)960)-0=1
TO-2: NТОР=((1334+1518)240)-1=5
TO-1: NТОР=((134+1518)60)-6=19
Бульдозер Д532 Т170 инвентарный номер 215
К.: NTOP=((3557+1518)7680)-0=0
Т.: NTOP=((6757+1518)960)-0=2
TO-2: NТОР=((1957+1518)240)-2=5
TO-1: NТОР=((157+1518)60)-7=18
Бульдозер ДЗ 170 инвентарный номер 216
К.: NTOP=((60389+1518)7680)-0=0
Т.: NTOP=((2789+1518)960)-0=1
TO-2: NТОР=((389+1518)240)-1=5
TO-1: NТОР=((389+1518)60)-6=19
Бульдозер ДЗ 170 инвентарный номер 217
К.: NTOP=((22446+1518)7680)-0=0
Т.: NTOP=((3246+1518)960)-0=1
TO-2: NТОР=((846+1518)240)-1=5
TO-1: NТОР=((246+1518)60)-6=19
Бульдозер ДЗ 170 инвентарный номер 218
К.: NTOP=((56004+1518)7680)-0=0
Т.: NTOP=((8004+1518)960)-0=2
TO-2: NТОР=((804+1518)240)-2=4
TO-1: NТОР=((204+1518)60)-6=19
Бульдозер ДЗ 170 инвентарный номер 219
К.: NTOP=((51252+1518)7680)-0=0
Т.: NTOP=((3252+1518)960)-0=1
TO-2: NТОР=((852+1518)240)-1=5
TO-1: NТОР=((252+1518)60)-6=19
Бульдозер ДЗ 170 инвентарный номер 220
К.: NTOP=((32148+1518)7680)-0=0
Т.: NTOP=((3348+1518)960)-0=1
TO-2: NТОР=((948+1518)240)-1=5
TO-1: NТОР=((348+1518)60)-6=19
Бульдозер ДЗ-122 инвентарный номер 321
К.: NTOP=((38661+16597)5760)-0=0
Т.: NTOP=((261+16597)960)-0=1
TO-2: NТОР=((261+16597)240)-1=6
TO-1: NТОР=((261+16597)60)-7=21
Автогрейдер ДЗ 98 1 инвентарный номер 322
К.: NTOP=((20403+16597)5760)-0=0
Т.: NTOP=((1203+16597)960)-0=1
TO-2: NТОР=((1203+16597)240)-1=6
TO-1: NТОР=((03+16597)60)-7=20
Автогрейдер ДЗ 98 1 инвентарный номер 323
К.: NTOP=((57038+16597)5760)-0=0
Т.: NTOP=((9038+16597)960)-1=1
TO-2: NТОР=((1838+16597)240)-2=5
Автогрейдер ДЗ 143 инвентарный номер 324
К.: NTOP=((7957+16597)5760)-0=0
Т.: NTOP=((7957+16597)960)-0=2
TO-2: NТОР=((757+16597)240)-2=5
TO-1: NТОР=((157+16597)60)-7=20
Автогрейдер ДЗ 122А инвентарный номер 325
К.: NTOP=((5053+16597)5760)-0=0
Т.: NTOP=((5053+16597)960)-0=2
TO-2: NТОР=((253+16597)240)-2=5
TO-1: NТОР=((253+16597)60)-7=21
Каток ДУ 48Б инвентарный номер 426 427
К.: NTOP=((5053+12144)5760)-0=0
Т.: NTOP=((5053+12144)960)-0=1
TO-2: NТОР=((253+12144)240)-2=5
TO-1: NТОР=((253+12144)60)-7=21
Каток ДУ 47Б инвентарный номер 428
К.: NTOP=((52483+12144)5760)-0=1
Т.: NTOP=((4483+12144)960)-1=0
TO-2: NТОР=((2083+12144)240)-1=4
TO-1: NТОР=((283+12144)60)-5=15
Каток ДУ 37Б инвентарный номер 429
К.: NTOP=((1458+12144)5760)-0=0
Т.: NTOP=((498+12144)960)-0=1
TO-2: NТОР=((18+12144)240)-1=4
TO-1: NТОР=((18+12144)60)-5=15
Каток ДУ 65 инвентарный номер 430
К.: NTOP=((43739+12144)5760)-0=0
Т.: NTOP=((5339+12144)960)-0=1
TO-2: NТОР=((539+12144)240)-1=4
TO-1: NТОР=((539+12144)60)-5=16
Автокран КС-4561 инвентарный номер 531
К.: NTOP=((7572+1862)11520)-0=0
Т.: NTOP=((1812+1862)1920)-0=1
TO-2: NТОР=((132+1862)240)-1=7
TO-1: NТОР=((12+1862)60)-8=23
Автокран КС-4561 инвентарный номер 532
К.: NTOP=((6931+1862) 11520)-0=0
Т.: NTOP=((1171+1862)1920)-0=1
TO-2: NТОР=((211+1862)240)-1=7
TO-1: NТОР=((31+1862)60)-8=23
Погрузчик ТО-6 инвентарный номер 433
К.: NTOP=((33365+17204)5760)-0=0
Т.: NTOP=((4565+17204)960)-0=2
TO-2: NТОР=((2165+17204)240)-2=6
TO-1: NТОР=((365+17204)60)-8=21
Трейлер ЧМЗАП инвентарный номер 434
К.: NTOP=((17202+16192)5760)-0=0
Т.: NTOP=((7602+16192)960)-0=2
TO-2: NТОР=((402+16192)240)-2=4
TO-1: NТОР=((402+16192)60)-6=21
Трейлер ЧМЗАП инвентарный номер 435
К.: NTOP=((53036+16192)5760)-0=1
Т.: NTOP=((5036+16192)960)-1=1
TO-2: NТОР=((236+16192)240)-2=4
TO-1: NТОР=((236+16192)60)-6=21
Так как каток используется только в течении сезона то рассчитаем сезонный коэффициент:
Nмес.- число месяцев в сезоне
Порядковый номер месяца Км в котором должен проводиться капитальный ремонт машин (если при расчете Км окажется больше 12 КР машин в планируемом году не производится и переносятся на следующий год) рассчитывают по формуле:
где Тп- доремонтный или межремонтный ресурс капитального ремонта.
Рассчитываю порядковый номер месяца для ЭО-2621 инвентарный №102:
Рассчитываю порядковый номер месяца для ДЗ-98 инвентарный №323:
Рассчитываю порядковый номер месяца для ДУ-47Б инвентарный №428:
Рассчитываю порядковый номер месяца для ЧМЗАП инвентарный №735:
3 Разработка месячного плана-графика технического обслуживания и ремонта СДМ
Месячный план-график ТО и ремонта машин устанавливает дату постановки каждой машины на ТО и ремонт и продолжительность ее простоя в днях. Его составляют на основании годового плана технического обслуживания и ремонта машин.
При выполнении дипломного проекта месячный план-график составляется на август месяц. Порядковый номер рабочего дня месяца Дтор в который начинается проведение технического обслуживания и ремонта машин определяется по формуле:
где Драб.- число рабочих дней в планируемом месяце определяемое по календарю с учетом установленного в данной организации режима работы;
Тп- межремонтный ресурс соответствующего вида ТО;
Тф- величина фактической наработки на начало планируемого месяца со времени проведения последнего аналогично расчетному вида ТО и ремонта или с начала эксплуатации;
Тпл- планируемая наработка на расчетный месяц.
Если при расчете ДТОР окажется больше чем число рабочих дней в месяце то соответствующий вид ТО и ремонта в этом месяце не проводят.
Принятое в системе ППР планирование профилактических воздействий носит условный характер поскольку машины работают в различных режимах при различном качестве технических воздействий и квалификаций эксплуатационного персонала. При этом необходимо учитывать план-график производства работ выполняемых организацией. Поэтому все профилактические воздействия планируют по срокам и объемам условно а их фактическое выполнение производят по потребности но в пределах установленных ограничений.
В зависимости от условий эксплуатации машин согласно ГОСТ 25646-83 допускается корректировать запланированную периодичность ТО в пределах 10% текущих ремонтов 8-5% за исключением случаев когда отклонение периодичности не допускается по условиям безопасности.
Согласно исследованию отклонение сроков проведения ТО от расчетных на 2-3 дня в ту или другую сторону вполне допустимо и экономически оправдано.
Фактическая наработка маш.час
С начала эксплуатации
Со времени проведения
Таким образом правильно разработанный месячный план-график должен быть увязан с графиком загрузки машин на объектах а также со сроками проведения сезонных технических осмотров служб государственных инспекций и со сроками выполнения планируемых капитальных ремонтов.
Экскаватор ЭО-2621 инв. №101
Экскаватор ЭО-2621 инв. №102
Экскаватор ЭО-2621 инв. №103
Экскаватор ЭО-4321Б инв. №104
Экскаватор ЭО-4121 инв. №105
Экскаватор ЭО-5126 инв. №106
Экскаватор ЭО-5126 инв. №107
Экскаватор ЭО-5124 инв. №108
Экскаватор ЭО-5124 инв. №109
Экскаватор ЭО-5122 инв. №110
Экскаватор ЭО-5122 инв. №111
Бульдозер Д532 Т170 инв. №212
Бульдозер Д532 Т170 инв. №213
Бульдозер Д532 Т170 инв. №214
Бульдозер Д532 Т170 инв. №215
Бульдозер ДЗ 170 инв. №216
Бульдозер ДЗ 170 инв. №217
Бульдозер ДЗ 170 инв. №218
Бульдозер ДЗ 170 инв. №219
Бульдозер ДЗ 170 инв. №220
Автогрейдер ДЗ 122 инв. №321
Автогрейдер ДЗ 981 инв. №322
Автогрейдер ДЗ 98 инв. №323
Автогрейдер ДЗ 143 инв. №324
Автогрейдер ДЗ 122А инв. №325
Каток ДУ 48Б инв. №426427
Каток ДУ 47Б инв. №428
Каток ДУ 37Б инв. №429
Каток ДУ 37Б инв. №430
Автокран КС-4561 инв. №531
Автокран КС-4561 инв. №532
Погрузчик ТО-6 инв. №633
Трейлер ЧМЗАП инв. №734
Трейлер ЧМЗАП инв. №735
4. Расчет параметров базы строительно-дорожных машин
Трудоемкость выполнения текущих ремонтов (Тртi) сезонных (Трсi) и технических (Тртоi) обслуживаний на каждую группу машин подсчитывается по формулам:
где Тртi Трсi Тртоi – соответственно трудоемкости проведения текущего ремонта технического и сезонного обслуживания для каждой группы машин.
Расчетные трудоемкости проведения текущих ремонтов (Тт) технических обслуживаний (Тто) и сезонных обслуживаний (Тс) подсчитываются по формулам:
Тт = Tртi Тто = Tртоi Тс = Tрсi
Таблица 1.4 - Трудоемкость ТО-1 ТО-2 СО и ТР.
Трудоемкость проведения ТР: Ттр= 3496 чел.-ч.
Трудоемкость проведения СО: Тсо=758 чел.-ч.
Трудоемкость проведения ТО-2: ТТО-2 =1427 чел.-ч.
Трудоемкость проведения ТО-1: ТТО-2 =2173 чел.-ч.
Для гусеничных машин ТО1 и ТО2 проводятся с помощью передвижных средств диагностики ТО и ремонта:
ТТО2(гус.) =988 чел.-ч.
ТТО1(гус.) =1364 чел.-ч.
Тогда для отдельного парка строительно-дорожной техники:
ТТО1 = 2173-1364 =809 чел.-ч.
Общая трудоемкость проведения текущих ремонтов технических и сезонных обслуживаний:
ТО=( ТТ+ ТТО2+ ТТО2+ ТС) К1
где К1-коэффициент учитывающий нужды производства.
ТО=( 3496+2173 + 1427+ 758) 145=113883 чел.-час.
Трудоемкость по профессиям(ТПi) подсчитывается по формуле :
где К2-коэффициент учитывающий нужды производства.
ТО принимаем отдельно по каждой группе машин (автогрейдеры экскаваторы катки погрузчики поливочно-моечные машины краны гудронаторы асфальтоукладчики).
Примечание «*» означает что трудоемкость проведения ТО2; ТО1 за исключением диагностических работ суммируется для всех остальных видов
Таблица 1.5. - Количество строительно-дорожных машин по их специализации
обслуживание гидросистемы
обслуживание системы питания
По данным таблицы 1.5 суммарная трудоемкость по отделениям рассчитывается по формуле:
Тпiотдел. = Тпiмашин
где Тпiотдел берется из таблицы 1.5.
Данные расчета сводим в таблицу 1.6.
Таблица 1.6 - Суммарная трудоемкость по отделениям.
Зона ТО1(колесная техника: крепежные
Регулировочные смазочные работы)
Ремонта гидрооборудования
Слесарно-механическое
Ремонта систем питания
Зона ТР (гусеничная техника колесная техника)
Количество рабочих (НРi) по каждой профессии подсчитывается по формуле:
где ТПГi – годовой фонд рабочего времени рабочего данной профессии равный:
для маляров и гальванизаторов- 1610 ч.
сварщиков кузнецов аккумуляторщиков медников - 1853 ч.
термистов вулканизаторщиков мойщиков электриков -1893 ч.
прочих профессий-1909 ч.
Диагностика:Нрдиагн.=1490641909=0781
Зона ТО1:Нрто1=2516161909=137
Агрегатное отделение:Нрагр.= 9671909=0607
Ремонт гидрооборудования:Нргидр.= 72951909=068
Слесарное отделение: Нрслес.= 3821909=0605
Аккумуляторное отделение:Нракк.= 1101853=0249
Тепловое отделение:Нртеп.= 5061853=0765
Электротехническое отделение:Нрэлтех=2141893=0513
Ремонт систем питания:Нрпит.= 4971909=056
Малярное отделение:Нрмаляр.= 1641610=0324
Шиномонтажное отделение:Нршин.= 721893=0241
Зона ТО2:Нр(тр кол.)= 22531909=127
Зона ТР: Нр(тр)= 20501909=155
Мойка:Нрмойки=38151893=0430
Исходя из подсчетов можно сделать вывод что один рабочий может обслуживать несколько отделений. Например при существующем объеме работ производственного цеха в шиномонтажном малярном и моечном отделениях все необходимые работысможет выполнять один человек.
Таблица 1.7 - Распределение рабочих по отделениям
Отделение проведения ТО1
Отделение проведения ТО2
Отделение проведения ТР
Отделение диагностики
Отделение системы питания
Отделение ремонта и гидроаппаратуры
НPi=14 человек – в производственном цехе будет задействовано 14 человек.
Расчетные площади (ФРi) производственных помещений подсчитываются по формуле:
ФРi=( НРi или НСi)К4 м2
где К4-удельная площадь приходящаяся на работников данной группы.
Полученные данные сводим в таблицу 1.8.
Таблица 1.8 - Площади производственных помещений
Производственное помещение
Площадь помещения м2
Отделение ТР и ремонта агрегатов
Продолжение таблицы 2.8
Отделение по ремонту гидроаппаратуры
Электротехническое отделение
Аккумуляторное отделение
Тепловое отделение(кузнечное сварочное
Слесарно-механическое отделение
Шиномонтажное отделение
Отделение по ремонту систем питания
Таблица 1.9 - Перечень основного технологического оборудования
Перечень оборудования
Машина для наружной мойки
Моторный тестер КИ-4897 ГОСНИТИ
Прибор для определения технического состояния фар К-303
Прибор для диагностики электроприборов (реле стартеров генераторов) КИ-968 ГОСНИТИ
Переносной диагностический прибор К-484
Переносной газоанализатор Э-311
Расходомер топлива КИ-8910А
Компрессорная установка
Линейка универсальная для проверки схождения передних колес
Солидолонагнитатель 3154 9 (передвижной)
Аппарат для промывки маслосистем СДМ 1147 (передвижной)
Устройство для сборки масла УСОМ
Продолжение таблицы 1.9
Пост смазчика-заправщика С-201
Пост слесаря П-506 (передвижной)
Набор ключей стандартный
Гидравлический подъемник ГАРО 410
Установка по очистки гидравлического масла
Зона текущего ремонта
Шкаф инструментальный
Стенд с гайковертом для сборки ходовых тележек
Стенд для сборки разборки регулировки сцепления
Стенд для сборки бортовых фрикционов
Стенд для сборки коробок передач
Стенд для разборки сервомеханизма
Стенд для сборки механизма натяжения гусениц
Пресс гидравлический для выпресовки пальцев гусениц
Стенд для ремонтов гидроцилиндров
Стенд для испытания гидроагрегатов
Ларь для обтирочных материалов
Стенд для ремонта гидрораспределителей
Стенд для разборки топливной аппаратуры
Ванна для мойки деталей
Настольно-токарный станок
Сушильный шкаф для якорей
Ванна для пропитки якорей меллаком
Станок для намотки якорей
Настольно-сверлильный станок
Установка УБР-3 (передвижная) для нанесения краски при температуре =3100сС
Силеновый выпрямитель
Стенд для проверки зарядки аккумуляторов
Верстак для ремонта аккумуляторов
Шкаф для зарядки аккумуляторов
Ванна для слива и приготовления электролита
Приспособление для разлива кислоты
Ножницы рычажные ручные
Обдирочно-шлифовальный станок
Сварочный трансформатор
Молоток выкалотлчный
Верстак для жестянщика
Установка для отчистки радиаторов от накипи
Стенд для ремонта радиаторов
Ванна для промывки топливных баков
Станок для прогонки резьбы
Вертикально-сверлильный станок
Токарно-винторезный станок
Станок точильный двухсторонний
Агрегатное отделение
Стол для сборки крупногабаритных узлов
Стенд для сборки коробки передач
Радиально-сверлильный станок
Ванна для проверки камер
Стеллаж для покрышек
Ларь для резиновых отходов
Ручной пневматический борторасширитель
Электровулканизационный аппарат для ремонта камер
Настенная вешалка для камер
Число постов для проведения технического обслуживания и текущего ремонта определяется по формуле:
где Тр – годовой объем работ чел.-час
Дp – число рабочих дней в году
TCM - длительность смены
m – количество рабочих одновременно работающих на посту (2-4 чел).
n - коэффициент использованного рабочего времени поста (08-09)
– коэффициент учитывающий неравномерность поступления машин на пост.
Зона ТР для колесных и
Расчет числа подвижных диагностических средств и средств технического обслуживания
Количество передвижных средств для диагностического обслуживания определяется по формуле:
где ТПС - трудоемкость работ планируемых для передвижных средств чел.-ч
Тфс - годовой фонд рабочего времени передвижных средств (час)
m - число рабочих обслуживающих передвижное средство.
Кис - коэффициент использования передвижного средства Кис = 04.
Принимаем одну единицу – установку КИ-4270 на базе автомобиля Газель.
Количество передвижных средств технического обслуживания и ремонта определяем по формуле:
Кис - коэффициент использования передвижного средства КИС = 06.
Принимаем одну единицу – установку А-701 на базе автомобиля ЗИЛ-130.
Стационарные и передвижные средства технической диагностики и ремонта
1 Диагностика как дополнение планово-предупредительных работ
Система планово-предупредительных работ долгое время не подвергалась существенным изменениям. По мере усложнения конструкций машин увеличения их количества а также необходимости повышения затрат на эксплуатацию все очевиднее становятся их недостатки. Так в связи со значительным рассеиванием фактических значений показателей надежности машин принятая в настоящее время система ППР не обеспечивает заданного срока работы изделий и не может обеспечить полного использования их ресурса.
Как правило этот ресурс оказывается или выбранным (в этом случае на ремонт становится машина которая еще не может работать) или перерасходованным когда машина оказывается в зоне аварийного износа что значительно удорожает стоимость ее ремонта. При этом разработанные системы оптимизации периодичности ТО и ремонтов не нашли широкого применения в силу своей сложности.
Поэтому в настоящее время наметилась тенденция замены принятой системы ППР системой технического обслуживания и ремонта по техническому состоянию.
В ее основу положен плановый контроль состояния машины с помощью диагностических средств и проведение ТО и ремонта в зависимости от этого состояния. Такая система обеспечивает почти полное использование технического ресурса составных частей и машины в целом а также предотвращение отказов машин и тем самым обусловливает высокую безотказность и долговечность их в процессе эксплуатации.
2 Организационные приемы диагностики
Эффективность диагностирования зависит от места диагностирования в технологическом процессе технического обслуживания и ремонт строительно-дорожных машин. Наиболее распространены совмещенная и специализированная формы диагностирования. Совмещенное диагностирование не требует какого-либо организационного процесса. Специализированное диагностирование осуществляет функцию управления технологическим процессом. Технологические потоки проходят через участок диагностирования.
Процесс диагностирования состоит из трех этапов: подготовленного основного и заключительного.
На подготовительном этапе проводят мойку чистку и внешний осмотр машины. Результаты осмотра заносят в диагностическую карту. Устанавливают диагностические приборы и датчики.
Таблица 2.1 - Перечень основных параметров определяемых при общем (Д-1) и углубленном (Д-2) диагностировании
Наименование сборочных единиц систем механизмов
Диагностические параметры и признаки
Общее состояние двигателя
Частота вращения вала
Удельный расход топлива
Кривошипно-шатунный механизм
Цилиндропоршневая группа
Компрессия в отдельных цилиндрах
Количество газов прорвавшихся в кратер
Продолжение таблицы 2.1
Частота вращения центрифуги
Продолжительность вращения центрифуги
Механизм газораспределения
Плотность прилегания клапанов
Зазоры между элементами механизма
Угол начала открытия впускных клапанов
Система охлаждения двигателя
Натяжение ремня вентилятора
Система очистки и подачи воздуха
Степень загрязнения воздухоочистителя
Герметичность впускного воздушного тракта
Система питания двигателя
Пропускная способность фильтрующих элементов грубой и тонкой очистки
Давление впрыска и качества распыла топлива форсунками
Производительность топливного насоса
Степень неравномерности подачи топлива элементами топливного насоса
Угол опережения впрыска топлива
Частота вращения кулачкового вала топливного насоса
Степень разреженности аккумуляторных батарей
Напряжение на фазах генератора
Напряжение поддерживаемое реле генератора
Величина тока регулируемая ограничителем тока
Величина тока отключения реле обратного тока
Величина тока потребляемого стартером
Состояние контрольно-измерительных приборов
Степень натяжения ремня генератора
Скорость подъема и опускания рабочего оборудования
Давление в гидросистеме
Температура рабочей жидкости
Загрязнение рабочей жидкости
Расход рабочей жидкости
Степень натяжения ремня компрессора
Герметичность пневмосистемы
Давление воздуха в системе
Натяжение гусеничной цепи
Износ гусеничных звеньев
Износ ведущей звездочки
Зазор направляющих колес опорных и поддерживающих катков
Схождение передних колес
Трансмиссия и система управления
Свободный ход рулевого колеса и усилия на ободе
Усилие и ход рычагов управления
Суммарный зазор в механизмах силовой передачи
Осевой и радиальный зазор в сопряжениях силовой передачи зазор в подшипниках
Степень износа канатов
Люфты в крюковой обойме
Размеры и число повреждений
Уровни срабатывания приборов безопасности
На основном этапе определяют техническое состояние машины и выполняют часть регулировочных работ.
На заключительном этапе проводят анализ результатов диагностики при этом уточняют характер и объем работ по техническому воздействию на машину и прогнозируют остаточный ресурс сборочных единиц. Снимают приборы и датчики с машины и проверенную машину направляют в зону соответствующих работ по техническому обслуживанию и ремонту.
Диагностирование проводят в сроки установленные для соответствующих технических воздействий и объема работ. Объем работ уточняют как в результате опроса оператора машины так и по показаниям приборов выявляющих мощностные характеристики машин и работоспособность сборочных единиц обеспечивающих безопасность производства работ. В обязательном порядке выполняют работы по общему диагностированию и по его результатам уточняют объем углубленного диагностирования. Перечень основных параметров при общем (Д-1) и углубленном (Д-2) диагностированиях приведен в таблице 2.1.
Причем ряд таких параметров углубленного диагностирования (Д-2) таких как загрязненность рабочей жидкости плотность электролита загрязненность воздухоочистителя давление масла в системе смазки определяют в обязательном порядке независимо от результатов общего диагностирования.
С учетом необходимости проверки основных диагностических параметров комплектуют оборудованием посты и участки технического обслуживания и ремонта.
При комплектовании диагностическим оборудованием учитывают объем производимых работ.
При специализированной форме диагностирования и. следовательно большом объеме диагностических работ используют средства позволяющие быстро и точно определить максимальное число параметров. В стационарных условиях применяют стенды позволяющие до минимума сократить время диагностирования на всех этапах (за счет установки датчиков уменьшении числа проверок стабилизации условий проверок и т.д.) В передвижных установках необходимое уменьшение времени на диагностирование достигают оснащением средств легкосъемными соединительными элементами уменьшением числа переносных средств.
Последовательность определения диагностических параметров устанавливают для каждого параметра на работоспособность машины. Обычно сначала проверяют параметры обеспечивающие безопасность производства работ затем общие после чего диагностируют основные сборочные единицы начиная с двигателя. В принятой последовательности производят специализацию диагностических постов а на универсальных постах – размещение оборудования.
Все посты оснащают документацией на диагностирование. На постах должна храниться документация по проверке диагностических средств.
С диагностическими средствами работает специально обученный персонал. По результатам диагностирования определяют исходя из общей трудоемкости диагностирования и с учетом возможности применения наиболее эффективного оборудования с полной загрузкой. При специализированном диагностировании возможно создание постов комплексного диагностирования так и специализированных постов.
С учетом технологической схемы участка диагностирования оборудование обычно размещают с соответствующим подводом электроэнергии воздуха и воды отоплением и системой вывода выхлопных газов.
3.Технология диагностирования
Технология диагностирования машин предусматривает последовательность выполнения операций место подсоединения диагностических средств дополнительное оборудование и инструмент квалификацию обслуживающего персонала. Основное содержание технологии определяется целью и задачами диагностирования.
При разборке технологии необходимо учитывать что на трудоемкость и стоимость диагностирования значительное влияние оказывает последовательность выполнения работ. При этом работы группируют по однотипности диагностических параметров по необходимости выполнения одноименных работ при подготовительно-заключительных операциях. Все операции диагностирования группируют таким образом чтобы обеспечить максимальную и равномерную загрузку всех участков диагностирования машины и сократить время нахождения ее в процессе диагностирования до минимума при заданной вероятности возникновения отказов механизмов и систем.
Каждому виду технического обслуживания соответствует определенный вид диагностирования и следовательно определенный перечень и последовательность операций.
При составлении комплексной схемы маршрутной технологии диагностирования устанавливают перечень обязательных диагностических операций и последовательность проверки систем при выходе за допустимые пределы показателей общего технического состояния.
Упрощенная схема маршрутной технологии диагностирования машины с выявлением неисправностей различных систем представлена на схеме 2.1.
Маршрутная технология диагностирования систем отражает все многообразие возможных состояний отдельных элементов и должна позволять при минимальных затратах труда отыскивать неисправности систем и механизмов. При составлении технологии диагностирования отдельных систем саму систему (или механизм) расчленяют на сборочные единицы устанавливают предельные значения структурных и диагностических параметров сборочных единиц выявляют минимальный перечень диагностических параметров и в результате составляют маршрутную схему проверки системы или механизма.
При составлении технологии диагностирования систем и механизмов разделение их на сборочные единицы производят с учетом самостоятельного функционирования каждой части. При этом учитывают возможность быстрого восстановления трудоспособности и замену неправильно функционирующей части механизма или системы.
Схема 2.1 - Упрощенная схема маршрутной технологии диагностирования машины (12 п – обязательные диагностические операции;
абв – диагностические операции по потребности).
4 Оснащение постов диагностирования
Создание специальных зон диагностирования строительно-дорожных машин на ремонтно-эксплуатационной базе зависит от производственной программы технического обслуживания строительно-дорожных машин выполняемой в стационарных условиях базы. Объем диагностических работ зависит от состава парка. Строительно-дорожные машины на базе автомобилей проходят все виды технического обслуживания на эксплуатационной базе. К этим машинам относят автомобильные краны автогудронаторы автовышки буровые установки и другие машины. Для большинства строительных машин (как с гусеничным ходом так и с пневмоколесным) техническое обслуживание с периодичностью 60 и 240 часов выполняют на строительных объектах и только работы по ремонту сезонному обслуживанию с периодичностью 970 часов выполняют на ремонтно-строительной базе. При определении программ ремонтно-эксплуатационнных баз учитывают что 40 50% текущего ремонта и 60 70% технического обслуживания машин выполняют на строительных объектах.
Число технических воздействий зависит от назначения каждого типа машины от интенсивности ее годового использования от числа строительно-дорожных машин и автотранспорта периодичности и продолжительности соответствующих технических воздействий. В результате уточняют необходимое число технических воздействий в течение года в период наиболее интенсивного использования машины и ежедневную программу и наиболее загруженный период работы базы.
5. Оснащение передвижных средств диагностирования
На строительных объектах при помощи передвижных средств выполняют работы по плановым техническим обслуживаниям. Крупные ремонты машин и сборочных
Единиц выполняют только в стационарных условиях (в том числе во временных стационарных мастерских).
Эффективность технического обеспечения машин на строительных объектах зависит как от характера распределения работ между различными типами мастерских так и оснащения передвижных средств технического обслуживания и ремонта. Причем большое влияние на производительность оказывают внешние условия работы ремонтного персонала а именно: оснащенность рабочего места температура окружающей Среды подготовленность площадки к проведению технических воздействий защищенность площадки от осадков. Особенностью передвижных средств технического обслуживания является то что наряду с технологическим оборудованием для обеспечения условий труда ремонтных рабочих под открытым небом.
Все необходимое технологическое и вспомогательное оборудование должно располагаться на транспортном средстве при этом учитывают время на приведение технологического оборудования в рабочее положение возможность выполнения некоторых работ в кузове транспортного средства и удобство размещения оборудования в транспортном положении. Укомплектование передвижных средств
Полным комплектом технологического оборудования во многих случаях нерационально так как значительно увеличивает простои оборудования не только из-за времени перемещения передвижного средства к объекту технического воздействия но и из-за необходимости развертывания оборудования перед выполнением операций технического воздействия и свертывания после проведенной операции.
В настоящее время получили распространение передвижные технические средства как для выполнения всего комплекса работ по техническому обслуживанию и частичному ремонту в основном агрегатно-узловым методом так и средства специализированные для выполнения отдельных видов работ и определенных типов строительных машин с гидро- и электроприводом.
Диагностическими приборами оснащают большинство видов передвижных средств при этом комплекты диагностических приборов различны. Наиболее полно оснащены специальные диагностические установки предназначенные для проведения работ по выявлению технического состояния строительных машин перед выполнением операций технического обслуживания. Передвижные средства в основном комплектуют переносными приборами и частично стендами для проверки гидравлического оборудования электрооборудования и двигателя устанавливаемые в кузове машины и имеющие выводы для подключения к соответствующим точкам диагностируемой машины. В основном диагностические приборы подбирают с целью установления необходимости проведения регулировочных и ремонтных работ выявления неисправных сборочных единиц в различных системах строительно-дорожных машин и контроля качества проведенных технических воздействий.
Число соответствующих технических воздействий при которых выполняются диагностические работы определяются таким же образом как и для стационарных постов. Обязательно учитываются не только время на обслуживание tоб но и время на продвижение на развертывание и свертывание технологического оборудования а именно:
tсм = 2tпер +tраз +tсв+ntоб час (2.1)
где tсм – сменное время работы машины;
tпер – время передвижения мастерской от ремонтно-эксплуатационной базы до района эксплуатации техники;
tсв tсв – соответственно время на развертывание и свертывание технологического оборудования передвижных средств;
tоб – время технического обслуживания (диагностирования) одной обслуживаемой машины;
n - число обслуживаний в течение смены (в основном в районе одного развертывания).
Время передвижения зависит от расстояния до машины требующей технического воздействия от условий движения состояния транспортной сети и следовательно от возможной скорости передвижения мобильных средств обслуживания. Время развертывания оборудования и время на выполнение единичного технического обслуживания величины постоянные для каждого вида передвижного средства. Время передвижения зависит от степени концентрации работы и передвижного состава.
При определении необходимого числа передвижных средств понимают что от всего времени обслуживания машин до 50% времени работы приходится на передвижение и не более 10% - на развертывание и свертывание (не более 5% - при проведении нескольких технических воздействий на одной стоянке).
С учетом трудоемкости работ по техническому обслуживанию и ремонту выполняемых на строительных объектах (ТО) можно определить среднее число передвижных средств по формуле:
где Тr- годовой фонд времени передвижного средства (исключая время необходимое на техническое обслуживание базового автомобиля и на проверку диагностического оборудования);
Хn - число передвижных средств.
В настоящее время расчет передвижных средств осуществляется с учетом нагрузки передвижных постов и простоев машин в ожидании технического воздействия используя положения теории массового обслуживания. Выявляют минимум затрат связанных с простоем передвижного средства в ожидании работ и простоем машин в очереди. Число передвижных средств определяют по формулам применяемым для расчета стационарных постов но при этом учитывая снижение производительности в связи с необходимостью перебазировки и свертыванием технологического оборудования.
Для каждого вида технического воздействия соответственно рассчитывают оптимальное количество передвижных средств в том числе для диагностических работ. Если количество передвижных средств менее оптимального для определенного парка машин затраты увеличиваются в связи с увеличением времени простоя машин в ожидании технического воздействия а при повышении количества передвижных средств по сравнению с оптимальными – резко возрастают затраты из-за их неполной загрузки.
6 Машина для технического диагностирования
Для проведения диагностирования машин непосредственно на месте их эксплуатации в настоящее время применяется разработанная в ГОСНИТИ мобильная установка (станция) КИ-4270 (рисунок 3.1) предназначенная для диагностирования технического состояния гусеничных машин при проведении технического обслуживания. Она базируется на машине Газель.
В кузове Газели смонтированы стеллаж верстак стол отсеки контейнеры с приборами приспособлениями и инструментом компрессор и электрооборудование.
Продолжительность диагностирования основных узлов без регулировки - 2 ч. с регулировкой - 6 ч. Установку обслуживают два человека. Питается она от сети переменного тока 220 В. Количество машин обслуживаемых установкой в год - 150-200. Наибольшее число определяемых основных параметров - 60. Наибольшая скорость передвижения по грунтовым дорогам – 50 кмч. Одна диагностическая установка подобного типа может обслужить в течение года 100 машин.
В комплект машины для технического диагностирования на базе УАЗ-452 входят:
- измеритель натяжения гусениц КИ -13903;
- индикатор расхода газов КИ - 4887-11;
- вакуум-анализатор КИ - 5315;
- устройство для измерения зазоров кривошипно-шатунном механизме КИ -11140;
- устройство для проверки прецизионных пар топливных насосов КИ -4802;
- устройство для проверки давления в системе топливоподачи КИ -4801;
- топливомер КИ – 4818;
- динамометр ДПУ – 002-2;
- люфтометр тракторный КИ - 4813;
- приспособление для проверки зазоров в подшипниках КИ – 4850;
- устройство для определения износа гусеничной цепи КИ - 4943;
-линейка для проверки схождения колес КИ – 650;
- устройство для определения технического состояния гидросистемы -
- прибор для проверки схождения колес КИ - 650;
- прибор для проверки автотракторного оборудования КИ - 1093;
- прибор для проверки контрольно-измерительных приборов Э – 204;
- компрессорно-вакуумная установка КИ - 4942;
- прибор для измерения втулочно-роликовых цепей КИ - 1854;
- нефтеденсиметр Б-2 и Б-3;
При диагностировании в полевых условиях хорошие результаты может показать смонтированный в чемодане и имеющий массу в 195 кг комплект диагностирующей аппаратуры КИ – 13901. Комплект КИ - 13901 предназначен для определения технического состояния машин всех марок без их разработки при техническом обслуживании как в полевых условиях так и на пунктах технического обслуживания. Переносной комплект 34 включает более 20 наименований контрольно-диагностических приборов приспособлений и инструмента размещенных в одном чемодане. Техническое состояние машин определяется в соответствие с принятой технологией диагностирования машин. Переносной комплект приборов целесообразно использовать в хозяйстве с парком 10 машин и более.
Кроме контрольно-диагностического оборудования передвижные диагностические мастерские укомплектованы компрессорно-вакуумной установкой верстаком со слесарным инструментом рабочим столом и комплектом электрооборудования для подключения к внешней сети и питанием соответствующих диагностических средств.
Целесообразно добавить к стандартному комплекту диагностического оборудования КИ -4270 стенд включающий в себя смазки типа НО 818 (с дополнениями) и силоизмерительный электротензометрический датчик.
Станция смазки типа НО 818 предназначена для централизованной смазки узлов.
При относительно небольших габаритах (355х250х495) и массе (40 килограмм) станция смазки позволяет за короткий промежуток времени большое количество смазочных точек и тем самым заменить такие ручные приспособления как солидолонагнетатели шприцы и т.п. ЕЕ номинальная производительность составляет 33 литра в минуту при давлении нагнетания в системе 1 Мпа. Подача смазки – 04 - 06 см3 за цикл.
Станция смазки типа НО 818 состоит из гидробака емкостью 10 дм3 насосной установки (насос типа БГ 12-41Б и электродвигатель 4АА63В4У603 мощностью 037 кВт) предохранительного клапана.
Силоизмерительные датчики являются приборами электротензометрических устройств общего назначения. Они предназначены для измерения и дозирования веса а также измерения и регулирования статических или изменяющихся усилий.
Различают силоизмерительные датчики следующих типов и модификаций:
- У – универсальные ( на сжатие и растяжение) с кабелем;
- С – на сжатие с кабелем;
- Р – на растяжение с кабелем;
- УА – универсальные с разъемом;
- СА – на сжатие с разъемом;
- РА – на растяжение с разъемом.
На стенде дополняющем диагностическую установку используем датчик У-10. Его характеристики: габаритные размеры -196х160х209 вес – 16 килограммов. Технические данные: основная погрешность – 10% от предельной нагрузки (10тс) относительная чувствительность от номинальной – в 02 тс- 2*103 отклонение относительной чувствительности от номинальной – в пределах основной погрешности допустимой разброс чувствительности – 05%.
Датчик У-10 удобен при измерении усилия на рабочем органе машины без его разборки а также более мелких узлов – штоков гидроцилиндров автогрейдеров бульдозеров экскаваторов и т.п. Сборочный чертеж стенда изображен в графической части дипломного проекта.
Устройство приспособления для разборки и сборки рессор
Предназначен для зажима рессор при разборки рессор. Состоит из рукоять червяка гайки корпуса зажим опорной пластины отверстий под крепежные болты.
При разборке сборке предварительно снятую рессору зажимают в приспособлении и ослабляют хомутики не вынимая рессоры из приспособления. Снимают стремянки и болт держащие съемное ушко.
Далее разжимаем приспособление и снимаем по очереди листы рессор и выполняем проверку изогнутости.
Техническая характеристика приспособления для разборки сборки рессор
При установке рессоры на приспособление рессора затягивается на ручную силу так чтобы рессора не выворачивалась этому помогает опорная пластина которая не дает рессоре вывернутся.
Опорная или предохранительная пластина регулируется по высоте рессоры. Имеется зажимное устройство которое имеет форму двутавра что помогает обеспечить твердое зажатие рессоры в приспособлении.
Основные виды разрушения резьб: крепежных – срез витков. В соответствии с этим основными критериями работоспособности и расчета для резьб является прочность связанная с напряжениями среза (рис 2.1).
Определить напряжении среза в резьбе.
Используя таблицы стандартов находим необходимые для расчетов размеры (таб. 2.2)
Внутренний диаметр d1
Условие прочности резьбы по напряжениям среза:
= F·d1·H·K·Km=[] [1]
где H-высота гайки или глубина завинчивания винта в деталь H=29 мм
d1- внутренний диаметр резьбыd1=31670 мм
K- коэффициент полноты резьбыK087
Km- коэффициент неравномерности нагрузки по виткам резьбыKm=07
[]- допускаемое напряжение среза[]=06T
=980314·31670·29·087·07=65МПа
=[] т.е. 65МПа =2352МПа условие выполняется.
Технологическая часть
Описание работы детали
Вал-шестерня установлена в главной передаче пневмоколёсного крана смазывается рабочей жидкостью. Опасные сечения и напряжения: шлицевое соединение зубья.
Исходя из условий работы выбираем материал – сталь 45 (вал-шестерня работает без ударных нагрузок вид нагрузки – переменная).
Планирование операций по изготовлению вала-шестерни
Заготовительная операция.
Термическая обработка.
Шлифовальная операция.
Контрольная операция.
1 Заготовительная операция
) Отрезать заготовку d=98 мм и длиной l=276 мм.
Расчёт длины рабочего хода Lр.х. мм фрезерования
где Lрез=98 мм – длина резания.
y= 5мм – величина подвода врезания и перебега инструмента. (прил.1)
Lдоп=0 мм – дополнительная длина хода.
Lр.х.=98+5+0=103 мм.
) Определение рекомендуемой подачи на зуб фрезы по нормативам Sz ммзуб (см. карту Ф-2).
Глубина резания t=98 мм (>5 мм)
Подача на зуб Sz=012 ммзуб
Т.к. обрабатываемый металл Сталь 45 его твёрдость НБ=217-241;
Тип фрезы – дисковая;
Инструментальный материал – быстрорежущая сталь.
) Определение периода стойкости инструмента по нормативам Т мин. резания (см. карту Ф-3).
Период стойкости каждого инструмента Т в минутах резания равен:
где Тм1 Тм2 и т.д. – периоды стойкости первого второго и т.д. инструментов наладки;
λ – коэффициент времени резания каждого инструмента равный отношению длины резания Lрез этого инструмента к длине рабочего хода стола Lр.х..
λ=LрезLр.х.=98307=03
KФ=1 т.к. один инструмент в наладке.
Тм – период стойкости фрез в минутах машинной работы=250 мин.
) Расчёт скорости резания V ммин числа оборотов шпинделя n обмин минутной подачи Sм мммин.
а) определение рекомендуемой нормативами скорости резания (карта Ф-4) Скорость резания:
где Vтабл=35 ммин – скорость резания по таблице К1 К2 К3 – поправочные коэффициенты.
V=35·11·08·1=308 ммин
б) расчёт числа оборотов шпинделя соответствующего рекомендуемой скорости резания и уточнение его по паспорту станка (карта Ф-1 лист 2)
в) определение скорости резания по принятым оборотам шпинделя (карта Ф-1 лист 2)
г) расчёт минутной подачи по принятому значению числа оборотов шпинделя (карта Ф-1 лист 2)
где Sz – подача на зуб=012 ммзуб;
Zu – число зубьев фрезы=20;
n – число оборотов шпинделя=4904 обмин.
Sм=012·20·4904=117 мммин
) Расчёт основного машинного времени обработки tм мин на комплект (комплект включает все детали установленные на столе станка).
) Выявление подачи на зуб фрезы Sz ммзуб по принятым режимам резания (карта Ф-1 лист 2)
) Проверочные расчёты по мощности резания (карта Ф-1 лист 3)
а) определение по нормативам потребной мощности Nрез кВт (карта Ф5)
где Е – величина определяемая по таблице.
V – скорость резания.
t – глубина резания.
Zu – число зубьев фрезы.
К1 и К2 – поправочные коэффициенты
Устанавливаем и снимаем заготовку. Отрезаем заготовку 98 в размер
L=276 мм на фрезерно-центровальном станке МР73М. Из инструментов используем фрезу и центровочное сверло для сверления центров.
А. Установим заготовку в патроне и шариковых центрах.
Черновая обработка. Проточить с 98 до 48 на длину 232.
Глубина резания t=5 мм. Припуск на данном участке снимаем за 5 проходов (i=5).
) Расчёт длины рабочего хода суппорта Lр.х. мм
где Lрез=232 мм – длина резания.
y=10 мм – величина подвода врезания и перебега инструмента. (прил.1)
Lр.х.=232+10+0=242 мм.
) Назначение подачи суппорта на оборот шпинделя S0 ммоб:
а) определение рекомендуемой подачи по нормативам (карта Т-2 лист 2); Подачу принимаем S0=02 ммоб.
) Определение периода стойкости инструмента по нормативам Т мин. резания (карта Т-3):
Период стойкости Т в минутах времени резания каждого из инструментов наладки по которому ведётся расчёт скорости резания равен:
где Тм – период стойкости в минутах машинной работы станка. Для многоинструментных работ Тм относится к лимитирующим по стойкости инструментам наладки.
λ – коэффициент времени резания.
Количество оборотов шпинделя за время резания:
Количество оборотов шпинделя за время рабочего хода суппорта:
Отсюда λ = nш.nш0.= 11601210=096.
Примечание. 1. В случаях когда очевидно что λ>07 можно его не рассчитывать и принять ТТм.
Значения периодов стойкости Т для обработки стальных деталей твёрдосплавными инструментами принимать не более 200 мин ТТм50 мин
) Расчёт скорости резания V ммин и числа оборотов шпинделя n обмин:
а) определение рекомендуемой скорости резания по нормативам (карта Т-4)
где Vтабл – скорость резания по таблице;
K1 K2 и K3 – поправочные коэффициенты.
б) расчёт рекомендуемого числа оборотов шпиндельного станка
) Расчёт основного машинного времени обработки tм мин (при работе с различными подачами машинное время суммируется по участкам)
Чистовая обработка. Проточить с 48 до 455 на длину 232.
Глубина резания t=0625 мм. Припуск на данном участке снимаем за 2 прохода (i=2).
y= 1 мм – величина подвода врезания и перебега инструмента. (прил.1)
Lр.х.=232+1+0=233 мм.
а) определение рекомендуемой подачи по нормативам (карта Т-2 лист 2); Подачу принимаем S0=012 ммоб.
Период стойкости Т в минутах времени резания каждого из инструментов
наладки по которому ведётся расчёт скорости резания равен:
Значения периодов стойкости Т для обработки стальных деталей твёрдосплавными инструментами принимать не более 200 мин несмотря на результаты расчёта по приведённой формуле: ТТм50 мин
Черновая обработка. Проточить с 455 до 415 на длину 44 контролируя длину 146.
Глубина резания t=2 мм. Припуск на данном участке снимаем за 1 проход (i=1).
где Lрез=44 мм – длина резания.
y= 4 мм – величина подвода врезания и перебега инструмента. (прил.1)
а)определение рекомендуемой подачи по нормативам (карта Т-2 лист 2); Подачу принимаем S0=02 ммоб.
Отсюда λ = nш.nш0.= 220240=092.
Чистовая обработка. Проточить с 415 до 40 на длину 44 контролируя длину 146.
Глубина резания t=0375 мм. Припуск на данном участке снимаем за 2 прохода (i=2).
y= 2 мм – величина подвода врезания и перебега инструмента. (прил.1)
а)определение рекомендуемой подачи по нормативам (карта Т-2 лист 2); Подачу принимаем S0=012 ммоб.
Отсюда λ = nш.nш0.= 367383=096.
Снять 2 фаски 2×45° с 455 до 41.
Глубина резания t=14 мм.
где Lрез3 мм – длина резания.
Отсюда λ = nш.nш0.=25412=0 6.
а) определение рекомендуемой скорости резания по нормативам
Черновая обработка. Проточить с 455 до 375 на длину 38.
Глубина резания t=2 мм. Припуск на данном участке снимаем за 2 прохода (i=2).
где Lрез=38 мм – длина резания.
Отсюда λ = nш.nш0.= 190200=095.
Чистовая обработка. Проточить с 375 до 36 на длину 38.
Отсюда λ = nш.nш0.= 317333=095.
Прорезаем канавку с 36 до 32 на ширину 4мм контролируя размер 34мм.
где Lрез=4 мм – длина резания.
) Определение периода стойкости инструмента по нормативам Т мин. Резания.
Период стойкости Т в минутах времени резания каждого из инструментовналадки по которому ведётся расчёт скорости резания равен:
Т=Тм·λ =5005=25 мин.
Отсюда λ = nш.nш0.=2040=05.
Снять фаску 2×45° с 36 до 32.
Б. Переставить и закрепить заготовку.
Проточить поверхность 4 с 98 до 50 на ширину 4мм.(черновая).
Глубина резания t=4 мм. Припуск на данном участке снимаем за 6 проходов (i=6).
Проточить поверхность 4 с 50 до 48 на ширину 4мм.(чистовая).
Глубина резания t=1 мм. Припуск на данном участке снимаем за 1 проход (i=1).
Отсюда λ = nш.nш0.=3367=05.
Снять фаску 35×30° с 98 до 85.
Глубина резания t=25 мм.
где Lрез7 мм – длина резания.
Отсюда λ = nш.nш0.=5875=077.
Переставляем и закрепляем заготовку при этом смещаем заднюю бабку станка таким образом чтобы угол между осью вращения заготовки и горизонталью составлял 30°. Это необходимо для обработки конической поверхности.
Обрабатываем коническую поверхность на толщину 20 мм.
а) черновая обработка. ( снимаем стружку толщиной 18 мм)
Глубина резания t=45 мм. Припуск на данном участке снимаем за 2 прохода (i=2).
где Lрез=40 мм – длина резания.
y= 8 мм – величина подвода врезания и перебега инструмента. (прил.1)
Отсюда λ = nш.nш0.=200240=083.
б) чистовая обработка. ( снимаем стружку толщиной 2 мм)
Глубина резания t = 05 мм. Припуск на данном участке снимаем за 2 прохода (i=2).
Отсюда λ = nш.nш0.=333400=083.
Устанавливаем и обрабатываем заготовку на токарно-винторезном станке
Б05П. Из инструментов используем широкий и отрезной резцы.
3 Фрезерная операция
Установить и закрепить заготовку.
А.Нарезание шлицев l=60 мм высотой t=4 мм шириной b=5 мм контролируя длину l=108 мм.
) Расчёт длины рабочего хода Lр.х (карта Ф-1 лист 1):
где Lрез – длина резания равная длине обработки измеренной в направлении резания;
y – величина подвода врезания и перебега инструмента (см. приложение 1);
Lдоп – дополнительная длина хода вызванная в ряде случаев особенностями наладки и конфигурации детали.
y=yподв+yврез+yп=21 мм (при высоте зуба h=4 мм диаметр фрезы D=90 мм. См. приложение 1 для шлицевых червячных фрез при нарезании шлицев).
) Определение рекомендуемой подачи по нормативам (Карта З-3. Режимы резания при нарезании шлицев червячными фрезами.).
Подачу принимаем S0=26 ммоб
) Определение периода стойкости инструмента Т мин резания
где Кф – коэффициент учитывающий количество инструментов в наладке Кф=1;
Тм – период стойкости инструмента наладки Тм=240 мин
λ – коэффициент времени резания каждого инструмента равный
) Определение рекомендуемой нормативами скорости резания
по карте З-3: V=35 ммин.
) Расчёт числа оборотов шпинделя соответствующего рекомендуемой скорости резания (карта Ф-1 лист 2):
) Определение скорости резания по принятым оборотам шпинделя (карта Ф-1 лист 2):
Нарезать таким образом 14 шлицев после каждого раза поворачивая заготовку на 257°.
Б. Нарезание резьбы на резьбонарезных станках (Карта Р-2).
). Скорость резания:
Kv – поправочный коэффициент.
Диаметр нарезаемой резьбы d=36 мм.
Шаг резьбы S =15 мм.
При нарезании резьбы 1 класса точности скорость резания надо уменьшить на 20%.
Мкр=Мкр(табл)·Км кгс·м
где Мкр(табл) – крутящий момент по таблице=450 кгс·м
Км – поправочный коэффициент=12
Мкр=450·12=540 кгс·м
) Расчёт машинного времени:
где Lр.х – длина рабочего хода (прил. 1):
Lр.х=Lрез+y+Lдоп= 34+37+0=71 мм.
y – величина подвода врезания и перебега инструмента
Рекомендуемые смазочно-охлаждающие жидкости для резьбонарезных головок и метчиков сульфофрезол и эмульсия. Чистота резьбы улучшается при добавлении к сульфофрезолу жидкого мыла и к эмульсии – льняного масла.
В. Фрезерование резьбы (Карта Р-3).
) Подача на зуб фрезы:
При нарезании резьбы 1 класса точности табличные значения подач умножать на 075.
Sz=0034·075=0026 ммзуб.
) Период стойкости фрез Т в минутах резания.
При диаметре фрезы D=80 мм Т=180 мин.
где Vтабл – скорость резания по таблице Vтабл=45 ммин;
К1 в зависимости от обрабатываемого металла и твёрдости НБ К1=07;
К2 в зависимости от периода стойкости инструмента К2=1.
Д. Нарезание зубьев конического зубчатого колеса.
Нарезаем зубья на глубину t = 8 мм дисковой модульной фрезой диаметром D = 90 мм количеством зубьев Z = 24.
а) предварительное фрезерование зубьев.
) Расчёт длины рабочего хода Lр.х. мм
где Lрез=42 мм – длина резания.
y= 29 мм – величина подвода врезания и перебега инструмента. (прил.1)
Lр.х.=42+29+0=71 мм.
) Назначение подачи рекомендуемой подачи на зуб фрезы Sz ммоб по нормативам (карта З-7); Подачу принимаем Sz=011 ммоб.
) Расчёт скорости резания V ммин и числа оборотов фрезы n обмин:
а) определение рекомендуемой скорости резания по нормативам (карта З-7)
б) расчёт рекомендуемого числа оборотов фрезы:
) Определение минутной подачи Sм мммин
S = Sz Zu n = 011 20 110 = 242 мммин
где Sz – подача на зуб фрезы;
Zu – число зубьев фрезы;
n – число оборотов фрезы.
) Расчёт основного машинного времени обработки tм мин.
б) окончательное фрезерование зубьев.
) Расчёт длины рабочего хода резцов Lр.х. мм
где lb=42 мм – длина зуба.
) Расчёт скорости резания V ммин и числа двойных ходов резцов nд.х. дв. ходмин:
Скорость резания V=23 ммин.( Карта З-8)
б) расчёт числа двойных ходов резцов в минуту:
) Назначение времени обработки одного зуба tz секзуб.
) Расчёт основного машинного времени tм мин.
4 Термическая операция
Закалка с нагревом ТВЧ с глубиной закалённого слоя 18-22 мм.
Для достижения высокой поверхностной твёрдости и повышенной изностойкости места под посадку подшипников и шлицевых соединений необходимо закалить с нагревом ТВЧ.
Нагреть посадочные поверхности вала до t=8500С индуктором и охладить в воде.
Нагреть деталь до t=180–2000С выдержать при этой температуре 05–1 час и охладить в индукторе.
5 Шлифовальная операция
А. Установить и закрепить заготовку
а) Шлифование посадочного места под подшипник длиной 42 мм (Карта Ш-1 лист 1).
) Расчёт скорости шлифовального круга
где D – диаметр круга;
nкр – число оборотов круга по станку.
) Выбор характеристики шлифовального круга (Карта Ш-1 лист 2).
Характер обработки – шлифование гладких шеек.
Точность обработки мм точнее 003 =002.
Обрабатываемый металл – сталь закалённая.
Шлифовальный круг Э46-60 С2-СТ1К.
) Расчёт скорости V ммин и числа оборотов n обмин детали:
а) Определение рекомендуемой нормативами скорости вращения детали (лист 2 карта Ш-1):
б) Расчёт числа оборотов шпинделя соответствующего рекомендуемой скорости и уточнение его по паспорту станка:
где d – диаметр детали.
) Выбор минутной поперечной подачи для шлифования шеек Sм мммин (Листы 2 и 3 карты Ш-1).
где Sм(табл) – минутная подача по таблице Sм(табл)=07 мммин;
К1К2К3 – поправочные коэффициенты.
) Определение времени выхаживания tвых мин (лист 3 карты Ш-1).
) Определение величины слоя снимаемого при выхаживании. авых мм (лист 3 карты Ш-1):
) Расчёт машинного времени tм мин:
где время врезания tвр=003÷004 мин;
а – припуск на сторону.
б) Шлифование посадочного места под подшипник длиной 32 мм (Карта Ш-1 лист 1).
где Sм(табл) – минутная подача по таблице Sм(табл)=082 мммин;
Шлифование шлицев на шлицешлифовальных станках (Карта Ш-5
) Расчёт скорости круга Vкр мсек:
где nкр – число оборотов круга по станку;
D – диаметр шлифовального круга.
) Выбор характеристики шлифовального круга (лист 2 карты Ш-5):
Метод шлифования шлицев – одновременное шлифование боковых сторон и дна.
Характеристика круга – Э46-60 С1-СТ1К.
) Определение продольной подачи (скорости) стола Sм ммин (лист 2 карты Ш–5):
Число шлифуемых шлицев zд=14.
Длина шлицев lш=60 мм.
Время полного оборота барабана tоб=01 мин для станка МСЗ-345-А.
) Определение подачи круга на двойной ход стола St ммдв. х (лист 2 карты Ш-5):
) Определение длины перебега yп мм (лист 2 карты Ш-5):
а) продольная подача стола Sм=60 ммин;
б) Время поворота барабана на один зуб мин.
) Определение числа проходов на выхаживание каждого шлица (лист 2 карты Ш-5):
uвых=2 при 7 классе чистоты поверхности.
) Определение слоя снимаемого при выхаживании авых мм (лист 2 карты Ш–5):
т.к. St=0032 ммдв.х и uвых=2.
) Расчёт числа проходов на шлифование каждого шлица u0:
yп=24 мм – длина перебега;
u0=5 – число проходов;
uвых=2 – число проходов на выхаживание;
Sм=60 ммин – продольная подача стола;
zд=14 – число шлицев.
Б. Установить и закрепить заготовку
Шлифование зубьев на зубошлифовальных станках (Карта Ш-5 лист 1).
Метод шлифования зубьев – одновременное шлифование боковых сторон и дна.
Число шлифуемых зубьев zд=24.
Длина зубьев lш=42 мм.
а) продольная подача стола Sм=90 ммин;
) Определение числа проходов на выхаживание каждого зуба (лист 2 карты Ш-5) uвых=2 при 7 классе чистоты поверхности.
) Определение слоя снимаемого при выхаживании авых мм (лист 2 карты Ш–5) авых=0025 мм т.к. St=0022 ммдв.х и uвых=2.
) Расчёт числа проходов на шлифование каждого зуба u0:
yп=27 мм – длина перебега;
u0=8 – число проходов;
Sм=90 ммин – продольная подача стола;
zд=24 – число зубьев.
Проверить размеры в соответствии с чертежом.
Применять для установки вала-шестерни чтобы определить биение.
Для измерения длины – штангенциркуль.
Для определения шероховатости поверхности применять образцы шероховатости.
Безопасность жизнедеятельности
1 Основные меры безопасности проектируемого предприятия
Основные требования безопасности к генеральным планам
Перед разработкой генерального плана уточняем перечень основных зданий и сооружений размещаемых на территорий предприятия площади для застройки и габаритные размеры в плане . Определяем потребные площади для хранения строительных машин складирования ремонтного фонда и других материалов хранение которых допускается вне помещений.
Здания и сооружения располагаем относительно преобладающего направления ветров с учетом обеспечения наиболее благоприятных условий естественного освещения проветривания и предотвращения снежных заносов. Здания и помещения с производственными процессами выделяющими в атмосферу газ дым пыль а так же взрывопожароопасные вещества располагаем по отношению к другим с подветренной стороны .Разрывы между зданиями и сооружениями принимаем минимально необходимыми для устройства дорог тротуаров прокладок инженерных сетей но не менее расстояний обуславливаемых санитарными и противопожарными требованиями.
Расстояния обусловленные противопожарными требованиями зависят от степени огнестойкости зданий и сооружений.
Для движения транспорта предусматриваем дороги. Проезды с двусторонним движением предусматриваются с шириной проезжей части -6 м с односторонним движением -3 м .Ширину тротуара принимаем кратной полосе движения шириной 075 м .но менее 10 м.
Минимальные расстояния от наружной степени здания до края проезжей части дороги при отсутствии въезда в здание и его длине более 20 м принимаем не менее 3 м ; при въезде в здание погрузчиков электротележек двухосных автомобилей – 8 м; трехосных – 12м .К зданиям и сооружениям по всей длине их должен быть обеспечен подъезд пожарных автомобилей: при ширине здания до 18 м – с одной стороны при ширине более 18 м – с двух сторон. при ширине более 100 м – со всех сторон.
Основные требования безопасности к производственным помещениям
При размещении производств различной категорий в одном зданий или помещений следует предусматривать мероприятия по предупреждению взрыва пожара ограничению или исключению воздействия вредных и опасных производственных факторов .
Помещение с производственным процессами категорий А (взрывоопасные): окрасочный участок краскоприготовительная склад лакокрасочных материалов (при применении органических растворителей или горючих жидкостей с температурой вспышки до 28 градусов Цельсия) зарядная аккумуляторного цеха; категорий Б (взрывоопасные) окрасочный участок краскоприготовительная склад смазочных материалов (при применении органических растворителей или горючих жидкостей с температурой вспышки выше 28 градусов Цельсия) цех ремонта топливной аппаратуры; категории В (пожароопасные ) посты ТО и ТР шиномонтажный обойный цеха склады шин смазочных материалов склад химикатов кислотная помещения для хранения техники; или сопровождающимися выделением вредных газов паров пыли тепла влаги искр пламени дыма шума и т.п. размещаем в отдельных помещениях у наружных стен и с подветренной стороны производственного корпуса. В случае размещения производств категории А Б В в отдельных помещениях их следует отделять от других помещений и коридоров противопожарными перегородками.
Помещения для хранения техники не должны сообщать с помещениями для ремонта и обслуживания. Такие помещения должны иметь выезд через ворота открывающимися наружу.
Для производства аккумуляторных работ необходимо предусматривать два помещения: одно – для ремонта другое – для зарядки аккумуляторов. Вход в аккумуляторное отделение должен быть оборудован тамбуром.
Для размещения окрасочных отделений должно предусматриваться два помещения: одно для подготовки краски другое для окраски.
Эвакуационными считаются выходы: из помещений первого этажа наружу непосредственно или через коридор; из помещений в соседнее помещение в том же этаже обеспеченные эвакуационными выходами. Как правило число эвакуационных выходов должно быть не менее двух. Допускается один выход если расстояние от наиболее удаленного рабочего места до выхода не более 25 м и число работающих в смене не более: 5 чел.- в помещение категории АБ; 25 чел.-В; 50 чел.-ГД.
Категория взрывопожароопасности производственного корпуса в данном проекте – Б.
2. Общая характеристика опасных и вредных производственных факторов
Таблица 4.1 - Общая характеристика опасных и вредных производственных факторов отделений диагностики
Опасные и вредные производственные факторы
источники места причины образования
нормативное значение
основные средства защиты от них
Движущиеся машины и механизмы
при заезде на пост и съезд с поста передвижные тележки гидравлический подъемник
Звуковая и световая сигнализация дистанционное управление
Острые кромки заусеницы шероховатость поверхностей
верстак стеллаж приборов
комбинированные рукавицы
Продолжение таблицы 4.1
Падающие приспособления и диагностируемые объекты
гидравлический подъемник
дистанционное управление предохранительные устройства
Повышенная или пониженная температура
на постах в холодное и жаркое время года
рукавицы обогрев и охлаждение поверхностей вентиляция
Электрический ток опасной величины
стационарные и передвижные диагностические стенды
изоляция зануление устройства автоматического отключения
Передвигающиеся стенды
диагностические передвижные стенды
устройства автоматического отключения световая и звуковая сигнализация
Падающий инструмент диагностические приборы
верстак стеллаж диагностических приспособлений
специальные стеллажи
Повышенная температура воздуха в рабочей зоне
Понижение температуры воздуха в рабочей зоне
Повышенная подвижность воздуха в рабочей зоне
наличие щелей неплотностей закрытия окон
ликвидировать щели удалить неплотности
Недостаток естественного света
удаление рабочих постов от световых проемов
искусственное освещение
Недостаточная освещенность рабочей зоны
В темное время суток
Искусственное освещение
Повышенный уровень шума и вибрации
При работающем двигателе или подъемнике
Звукоизолирующие и звукопоглощающие устройства виброгасящие устройства дистанционное управление
Наличие вредных веществ на рабочем месте
Баки для сбора отработавших масел
Повышенная загазованность воздуха
При работающем двигателе
Шланговая вытяжка выхлопных газов вентиляция
3. Освещение производственных помещений. Расчет естественного и искусственного освещения диагностического отделения
Естественное освещение должно быть предусмотрено во всех производственных помещениях. Помещения для хранения техники складские и санитарно – бытовые могут быть без естественного освещения. Вид освещения (боковое верхнее комбинированное) выбирается с учётом размеров помещения расположение рабочих мест характера выполняемых работ и нормируемой освещённости.
Диагностическое отделение имеет наружные стены и рядом с производственным корпусом нет стоящих зданий принимаем боковое освещение (через световые проёмы в наружных стенах).
При боковом освещении предварительный расчёт естественного освещения сводится к определению коэффициента естественной освещенности (Ке.о.) при известной площади световых проёмов.
Расчёт Ке.о. при боковом освещении для зданий с отдельными окнами при ширине окон равной ширине простенков высоте подоконника ре более 12 и надкованного пространства равного 03 – 05 м выполняется в следующей последовательности.
Нормированное значение КE.O.N определяется по формуле:
КЕ.О.N = KE.O.H · mN % (4.1)
где КE.O.H. – нормируемое значение коэффициента естественного освещение для третьего пояса светового климата %;
mN – коэффициент светового климата принимается равным mN = 085 – 090 таблица 6 [17];
КE.O.H = 08 таблица 5 [17]
КE.O.H = 08 · 09 = 072%
По принятому расстоянию В = 1 м от расчётной точки до стены с окнами высотой 1 = 45 м и высоте верха окна над условной рабочей поверхностью h1 = 43 м находим отношение 1h1.
По принятому типу окна материалу его заполнения - оконное стекло и отношению 1h1 определяется расчётное КЕ.О.расч.КЕ.О.расч. = 5% таблица 7[17].
Расчёт искусственного освещения
Принимаем комбинированную систему освещения. Для освещения выбираем источники освещения – люминесцентные лампы.
Выбираем тип светильников с учётом класса взрыво- пожароопасности помещения и характеристики окружающей среды – отделение диагностики строительно – дорожных машин. По таблице 10[17] выбираем категорию для помещения диагностики строительно – дорожных машин – а. По таблице 9[17] выбираем тип светильника с учётом категории помещения - ПВЛП ЛСПО4.
Определяем нормированное значение освещённости зависящее от характеристики зрительной работы фона и объекта различения вида освещённости и типа источника света по СНиП 114 – 79. Нормированные значения освещённости для основных производственных помещений согласно СНиП приведены в таблице 11[17]. Для отделения диагностики строительно – дорожных машин освещённость равна 400 лк.
Рассчитываем высоту подсева светильников по формуле:
Hn = H – (hc + hp) i (4.2)
где Н – высота помещения Н = 6 м;
hc – расстояние от светильника до точки подвеса равное (0.2 – 0.3 )· Но но не более 15;
Но – расстояние от точки подвеса до рабочей плоскости Но = 48 м;
hp – высота рабочей плоскости hp =12 м;
hc = 02 · 48 = 0 96 1 м
Нn = 6 – (1+12) = 38 м
Выбираем схему размещения светильников по помещению. Светильники с люминесцентными лампами размещаются по вершинам квадрата прямоугольника (с соотношением большей стороны к меньшей 15 : 1). Светильники располагаются рядами ориентированными параллельно стенам с окнами или продольным осям помещения.
Расстояние между рядами светильников L м принимают в зависимости от наивыгоднейшего отношения LHП таблица 15[17]. Для светильников ЛСП04 – 2х40 и ПВЛП – 2х40 отношение LHП =12 – 16
L = 38 · 1 6 = 608 6 м
Расстояние от стен до крайнего ряда светильников Lk.p. принимается: при наличии рабочих мест около стен – 03 L.
Пользуясь схемой размещения светильников подсчитываем количество ламп и определяем требуемый световой поток лампы по формуле:
FЛ = ЕН · Sn· K· Z n · лм (4.3)
где ЕН – нормированная освещенность ЕН = 300 лк;
Sn – площадь пола помещения Sn = 120 м2
к – коэффициент запаса равный для газоразрядных ламп – 15;
Z – коэффициент неравномерности освещения равный при освещении люминесцентными лампами – 11;
n – количества ламп в светильниках шт.;
– коэффициент использования светового потока определяемый в функции коэффициентов отражения внутренних поверхностей и индекса помещения в долях единицы определяемый по таблице 16[17].
Индекс помещения определяется по формуле:
i = A · B Hn (A+B) (4.4)
где А – длина помещения А = 10 м;
В – ширина помещения В = 12 м;
i = 10 · 12 38 · (10 + 12) = 158
тогда = 36 принимаем n = 12
Fn = 300 · 120 · 15 · 11 12· 0 36 = 13750 лм
Типовых люминесцентных светильников с таким световым потоком нет значит примем n = 62 шт.
Fn = 300 · 120 · 15 · 11 62· 0 36 = 2661 лм
По расчётному значению FЛ = 2661 лм таблица 20 [17] выбираем ближайшую стандартную лампу ЛБ40 – 4 световой поток который равен FЛ = 3000 лм (разница световых потоков должна быть не более 10 – 15 %) мощностью 40 Вт что соответствует выбранному светильнику ЛСП04 – 2х40.
4 Электробезопасность
Основными причинами поражения электрическим током являются непосредственный контакт человека с электроустановкой под напряжением; приближение на недопустимо близкое расстояние к высоковольтным установкам; с электроустановкой нормально не находящейся под напряжением но которая случайно может оказаться под напряжением; ошибочные действия персонала; появления шагового напряжения.
Технические способности и средства защиты обеспечения электробезопасности разделяются на две группы: обеспечивающие защиту от случайного прикосновения к токоведущим частям (изоляция ограждение блокировки электрозащитные средства); защищающие от поражения током при прикосновении к металлическим нетоковедущим частям которые могут оказаться под напряжением в результате повреждения изоляции или по иным причинам (защитное заземление зануление малое напряжение защитное отключение разделительный трансформатор выравнивание потенциалов двойная изоляция).
Расчёт зануления сводится к проверке его работоспособности. Рассчитаем для электродвигателя вентилятора в системе вентиляции.
Заданные параметры двигателя:
Мощность двигателя – 4 4 кВт
Мощность трансформатора – 250 кВА;
Напряжение сети – 380 В.
Рабочий ток электродвигателя определяемый по формуле:
Jp = 25 · Pн А (4.5)
где Pн - номинальная мощность электродвигателя кВт.
Определяем пусковой ток электродвигателя по формуле:
где k = 6 – кратность пускового тока.
Определяем номинальный ток плавкой ставки по формуле:
По расчетному току выбираем предохранитель с током плавкой ставки не менее расчетного. Для сети напряжением 380 В принимаем предохранитель НПИ60М с JH = 25 А.
По принятому типу четырёх жильного кабеля определяем сечения жил. Номинальному току плавкой вставки равному 25А соответствует сечение жилы 25 мм2.
Определяем активное сопротивление фазной и нулевой жилы кабеля по формуле:
R = p · L S Oм (4.8)
где p – удельное сопротивление материала для меди p = 00175 Ом мм2м;
L – длинна сети L = 18 м;
S – сечение жилы кабеля S = 25 мм 2
R = 00175 ·1825 = 0126 Ом.
Определяем активное сопротивление цепи фаза нуль по формуле:
ZП = √(RФ2 +RH2)Oм (4.9)
где RФ – активное сопротивление фазной жилы кабеля RФ = 0126 Ом;
RH - активное сопротивление нулевой жилы кабеля RH +0126 Ом.
ZП =√(0126 2+ 0126 2) = 0126 Ом
Определяем ток короткого замыкания по формуле:
IКЗ = UФ (ZTЗ + ZП) А (4.10)
где UФ – фазное напряжение сети UФ = 220 В;
ZТ З – расчетное сопротивление трансформатора при мощности трансформатора 250 кВт ZТ З = 0 104 Ом.
IКЗ = 220(0104 + 0126) =956 5 А
Производим проверку условия безопасности по формуле:
IКЗ ≥ k · Iном (4.11)
где k – Коэффициент кратности k = 3;
Iном – номинальный ток плавкой вставки Iном =25 А
65 ≥ 75 что соответствует условию безопасности.
5 Техника безопасности при диагностики строительно – дорожных машин
Организация и проведение работ по диагностированию
Организация и проведения работ по диагностированию должна осуществляться в строгом соответствии с правилами безопасности выполнения этих работ и противопожарной безопасности изложенными в эксплуатационной и ремонтной документации заводов – изготовителей машин а так же СНиП 111 – 4 – 80 “Техника безопасности в строительстве“.
К работе по диагностированию допускаются лица прошедшие специальную подготовку и получившие инструктаж по технике безопасности.
Площадка на которую устанавливают машину должна быть ровной сухой не загромождённой посторонними предметами и по возможности защищенной от ветра и пыли. При этом она не должна располагаться в близи стогов сена (соломы) складов нефтепродуктов и линий электропередач. Машины поставленные на диагностирование должны быть закреплены от самопроизвольного перемещения и опрокидывания а рабочее оборудование опущено на грунт или специальную подставку.
Диагностирование проводится при полностью остановленном двигателе за исключением тех случаев когда требуется прослушать его или другие механизмы.
Перед началом работы необходимо убедится в том что манжеты спецодежды застегнуты или завязаны концы завязок аккуратно убраны а волосы спрятаны под головной убор.
От пыли и грязи машину очищают с помощью специального инвентаря. Моют ее в рукавицах специальными растворами.
Диагностический инструмент должен быть надежно закреплен на рукоятках а его рабочие поверхности не должны иметь повреждений. На инструменте не должно быть трещин отслоений заусенец и забоин.
Объекты диагностирования следует осматривать пользуясь лампой напряжением не более 36 В. Лампа должна быть защищена проволочной сеткой. Применять для этих целей спички факелы и горелки запрещаются.
Правила безопасности при проведении работ по диагностированию
При проведении работ по диагностированию категорически запрещается;
- находиться под машиной поднятой домкратом;
- находиться под машиной при работающем двигателе;
- открывать крышу неохлажденного радиатора без рукавиц и наклонять лицо к заливной горловине радиатора;
- прикасаться к горячему компрессору во избежание ожогов ;
- наматывать на руку свободный конец шнура при запуске пускового двигателя вручную;
-снимать крышки заливных горловин баков передвижной мастерской если в них имеется избыточное давление или нагревать воду свыше 85 градусов Цельсия;
-создавать давление в баке с автотракторным маслом более 015Мпа в баке с трансмиссионным маслом – более 03Мпа и в ресивере – более 1Мпа;
- оставлять подвижную диагностическую мастерскую без присмотра в период заполнения баков топливозаправочным материалами;
-работать на подвижной диагностической мастерской с неисправными предохранительными клапанами и воздушными запорными устройствами топливозаправочной системы;
-загораживать проходы возле машин диагностическими приспособлениями и другими предметами;
-сливать масло и промывочное топливо из картера в грунт или водные бассейны и загрязнять окружающую территорию промасленной ветошью и другими отбросами.
При диагностировании составных частей связанным с частичной или полной разборкой их нужно соблюдать меры безопасности при разборочно-сборочных работах. Детали массой более 80 кг следует поднимать и перемещать только с применением грузоподъемных механизмов.
Инструкция по охране труда для слесаря –диагноста
Общие требования безопасности
1.К работе по диагностированию допускаются рабочие достигшие 18- летнего возраста прошедшие предварительное медицинское освидетельствование специальное обучение имеющие удостоверение на право проведения диагностических работ а также вводный инструктаж и первичный инструктаж по охране труда непосредственно на рабочем месте.
Повторный инструктаж проводиться не реже одного раза в три месяца а также внепланово при изменении условии и характера работы или при нарушении правил охраны труда.
2. Слесарь-диагност обязан:
- выполнять правила внутреннего трудового распорядка и повседневные указания мастера;
- пользоваться выданной спецодеждой спецобувью и предохранительными приспособлениями;
-помнить о личной ответственности за соблюдение правил техники безопасности и безопасности товарищей по работе;
- выполнять только ту работу по которой проинструктирован и допущен мастером;
-не выполнять распоряжение если они противоречат правилам безопасности;
- не допускать присутствие на рабочем месте посторонних лиц;
- оказывать первую помощь пострадавшим на производстве принимать меры по устранению нарушении правил по технике безопасности .О нарушениях и случаях травматизма немедленно сообщить мастеру;
- соблюдать установленные меры пожарной безопасности.
3.Слесарь-диагност должен содержать в порядке рабочего место в течение всего рабочего времени . Запрещается производить работы в неосвещенных или затемненных местах.
4. Слесарь-диагност допускается к работе при наличии следующих средств индивидуальной защиты: комбинезон обувь на резиновой подошве перчатки головной убор.
а) Слесарь-диагност получает и использует индивидуальные средства защиты (пользоваться ими разрешается только после прохождения специального инструктажа):
- для защиты от шума – противошумные наушники;
- для защиты от пыли – очки
- для защиты от выхлопных газов – респиратор.
5. Слесарь-диагност должен знать:
- устройства диагностируемых и диагностических машин механизмов и узлов установленных на их рабочем месте;
- правила технической эксплуатации каждого вида обслуживаемых машин и механизмов;
- простейшие мероприятия по устранению неисправностей и дефектов оборудования и безопасные способы их наладки или ремонта;
- безопасные способы выполнения вспомогательных работ (чистка механизмов уборка рабочего места);
- безопасные методы работы при диагностировании.
6. Деревянные рукоятки применяемых инструментов приспособлений должны быть гладко обработаны подогнаны и надежно закреплены.
7. Запрещается применять ручной инструмент имеющий выбоины сколы рабочих концов заусеницы и острые ребра в местах зажима рукой трещины и сколы на затылочной части.
8. Инструмент следует использовать только по прямому назначению.
9. Слесарь-диагност должен иметь квалификационную группу по электробезопасности.
10. За нарушение требований инструкции слесарь-диагност может быть привлечен к ответственности в установленном законом порядке.
Требования безопасности перед началом работы
1. Перед началом работы слесарь-диагност обязан:
- ознакомится с записями предыдущего диагностирования соответствующей машины в журнале приема - сдаче;
- осмотреть рабочее место убрать ненужные предметы и материалы освободить проходы;
- проверить исправность диагностического оборудования отсутствие повреждении его узлов и частей;
- проверить наличие заземления.
2. При обнаружении неисправностей сообщить мастеру.
Требования безопасности во время работы
1. При подключении (присоединении) диагностического оборудования к диагностируемой машине необходимо проверить:
- правильность подключения(присоединении);
- надежность подключения;
- отсутствие посторонних предметов на вращающихся и прочих механизмах;
- состояние всех защитных приспособлений и ограждений;
- наличие безприпятственного подхода (отхода) к диагностируемому механизму.
2. Включать диагностического оборудование после его полного подключения к диагностируемому механизму.
3. О начале работы слесарь-диагност должен дать предупредительный сигнал убедившись предварительно в отсутствии посторонних лиц у диагностируемого механизма и диагностического оборудования.
4. Во время работы диагностического оборудования слесарь-диагност должен строго соблюдать последовательность рабочих операции для определенного диагностического оборудования.
5. При проведении работ по диагностированию запрещается:
- покидать рабочее место;
- передавать управление диагностическим оборудованием другим лицам;
-прикасаться к нагретым механизмам во избежание ожогов;
- открывать крышку неохлажденного радиатора без перчаток;
- загораживать проходы возле машин диагностическим оборудованием и другими предметами.
Требования безопасности в аварийных ситуациях
1. При поломке диагностического оборудования слесарь-диагност должен остановить работу всех механизмов и оборудования и не приступать к работе до устранения неисправностей .
2. При аварии или несчастном случае слесарь-диагност должен:
- уметь оказать первую медицинскую помощь;
- самому или через рабочих вызвать скорую помощь;
- сохранить до приезда комиссии положение и обстановку несчастного случая
( если это не угрожает жизни людей);
- сообщить о случившемся ответственному лицу.
Требования безопасности по окончании работы
1. По окончании работы диагностическое оборудование необходимо выключить.
2. Если необходимо очистить сложить и убрать диагностическое оборудование на стационарное место.
3. Обо всех замечаниях неполадок во время работы сообщить мастеру.
4. Спецодежду спецобувь и другие индивидуальные средства защиты очистить . Если спецодежда промокла ее необходимо высушить. Хранить в специально отведенных местах.
1 Расчет капитальных вложений
Объем капитальных вложений складывается из суммы затрат на основные производственные фонды и всех затрат на строительство проектируемого объекта.
Расчет основных производственных фондов.
Основные производственные фонды включают стоимость зданий и сооружений производственного и вспомогательного оборудования инструмента приспособлений и стоимости инвентаря.
В стоимость зданий и сооружений включают все затраты на их строительство в том числе затраты на подготовку площадки санитарно-технические устройства фундаменты для установки оборудования.
При укрупненных расчетах стоимость зданий определяем по удельному показателю затрат на 1 м² здания принимаем на основании нормативов.
где Сзд - общая сумма на строительство здания;
Fзд - площадь здания Fзд = 870 м²;
Суд - стоимость 1 м² общего строительства по данным предприятия стоимость 1 м² здания принимаем Суд = 21`861 руб. за 1м².
Сзд = 870·21`861 = 19`019`070 руб.
Расчет стоимости оборудования включает стоимость всех видов производственного и вспомогательного оборудования: металлорежущего ремонтно-технологического энергетического подъемного транспортного а так же инструмента приспособлений и инвентаря. Кроме того в стоимость оборудования входят затраты на его транспортирование и монтаж. При укрупненных расчетах стоимость оборудования принимаем по установленному проектному отношению для предприятия она составляет 50% от общей стоимости здания:
Соб = 19`019`070·05 = 9`509`535 руб.
Данные по капитальным вложениям на строительство проектируемого объекта по ТО и ремонту сводим в таблицу
Наименование сооружений и зданий
Стоимость основных фондов
Производственный корпус
Итого: 28.528.605 руб.
2 Смета затрат на производство ТО и Р эксплуатируемой техники
Смета затрат один из главных показателей планируемого предприятия.
Смета затрат включает в себя всю сумму затрат или издержки производства (запасные части или материал заработная плата производственных рабочих накладные и другие расходы).
Расчет заработной платы основных производственных и вспомогательных рабочих.
Для расчета заработной платы основных производственных рабочих необходимо распределить рабочих по разрядам.
Производственные рабочие
Вспомогательные рабочие
Часовая тарифная ставка по данным существующего предприятия для рабочих по ТО и ремонту:
l-ый разряд - 1777 руб. 4-ый разряд – 2455руб.
-ой разряд - 2052 руб. 5-ый разряд – 2544 руб.
-ий разряд – 2368 руб. 6-ой разряд – 3536 руб.
Средняя часовая тарифная ставка будет ровна:
Расчет основной заработной платы на год:
Зосн. =12· Тст · t · m
где Тст. - часовая тарифная ставка
m - количество человек
t - количество рабочих часов в месяц
Зосн.= 12 · 253 · 166 · 17 = 856`759 руб.
Расчет дополнительной заработной платы
Дополнительная заработная плата принята 30% от основной
Здоп.=856759·03=257`028 руб.
Расчет районного и северного коэфициента
Зрк.ск. = (Зосн. + З доп.) · 05
Зрк.ск. = (856`759 + 257`028) · 05 = 556`894 руб.
Расчет премии Премиальная надбавка принята 50%
Зпр. = (Зосн. + З доп.) · 05
Зпр. = (856`759 + 257`028) · 05 = 556`894 руб.
Отчисления в социальные фонды
Зс.ф.=0271·(Зосн. + Здоп. + Зрк.ск. + Зпр.)
Зс.ф.=0271·(856`759 + 257`028 + 556`894 + 556`894) = 603`673 руб.
Общий фонд заработной платы рабочих за год:
Фз.п.=Зосн. + Здоп. + Зрк.ск. + Зпр. + Зс.ф.
Фз.п.=856`759 + 257`028 + 556`894 + 556`894 + 603`673=2`831`248
Затраты на материалы и запасные части при ТО и ремонте.
Затраты на материалы и запасные части определяем по формуле:
где Нм – Стоимость материалов и запасных частей на 1 час работы принимаем по данным предприятия;
Тпл - плановая наработка машины;
Ас - списочное количество машин.
Стоимость материалов и зч. на один машино-час руб.
Для автогрейдера ДЗ-122 М = 4778 · 1464 · 2 = 139`900 руб.
Для автогрейдера ДЗ-98 М = 4383 · 1464 · 2 = 128`334 руб.
Для автогрейдера ДЗ-143 М = 4778 · 1464 · 1 = 69`950 руб.
Для бульдозера Т-170 М = 5213 · 1660 · 9 = 778`822 руб.
Для экскаватора ЭО-4121 М = 534 · 1660 · 1 = 88`644 руб.
Для экскаватора ЭО-4321 М = 534 · 1660 · 1 = 88`644 руб.
Для экскаватора ЭО-2621 М = 3634 · 1660 · 3 = 180`973 руб.
Для экскаватора ЭО-5124 М = 5572 · 1660 · 6 = 554`971 руб
ЭО – 5122 ЭО - 5126
Для погрузчика М = 4135 · 1660 · 1 = 68`641 руб.
Для катка ДУ – 48 ДУ-47ДУ-37 М = 3486 · 1366 · 3 =428`569 руб.
Для катка ДУ – 65 М = 3845 · 1366 · 1 =95`238 руб.
Для автокрана КС – 3571 М = 4675 · 1757 · 1 = 82`140 руб.
Для автокрана КС – 4561 М = 5082 · 1757 · 1 = 89`291 руб.
Для ЧМЗАП М = 289 · 1757 · 2 = 101`555 руб.
Итого: Затраты на материалы и запасные части Σ = 2`895`672
Определение накладных расходов.
Накладные расходы включают в себя расходы связанные с организацией производственной деятельности т.е. такие которые не могут быть отнесены к расходам на ремонтные нужды. Определение фонда заработной платы ИТР и СКП. Данные по окладам и премиальные принимаем по данному предприятию.
Годовой фонд заработной платы ИТР и СКП определяется по формуле:
Фзп = (Мокл ·В+Мокл ·Nпр) · В
где Мокл - месячный оклад ИТР СКП
В - районный коэффициент
Nпр. - премиальный коэффициент
В - кол-во месяцев в году (В=12)
Фзп. = (11000 · 15 + 11000 ·05) · 12 = 264`000 руб.
Фзп. = (10000 · 15 + 10000 ·05) · 12 = 240`000 руб.
Фзп. = (7000 · 15 + 7000 ·05) · 12 = 168`000 руб.
Отчисления в социальный фонд принимаем 271%
Зсф = 840`000 · 0271 = 218`400 руб.
Расходы на содержание и ремонт оборудования.
Принимаем по данным предприятия 8% от стоимости оборудования.
Роб = 9`509`535 · 008 = 760`763 руб.
Расходы на содержание и текущий ремонт производственных помещений.
Принимаем по данным предприятия 3% от общей стоимости здания.
Общая стоимость здания по данным предприятия Сзд.об. = 19`019`070 руб.
Р пл. = 19`019`070 · 003 = 570`572 руб.
Амортизация оборудования.
Принимаем 18% от общей суммы стоимости оборудования.
Рам.об = 9`509`535 · 018 = 1`711`716 руб.
Принимаем 35% от общей стоимости здания.
Рам.зд. = 19`019`070 · 0035 = 665`668 руб.
Износ и содержание малоценного инвентаря.
Износ и содержание малоценного инвентаря принимаем 150 руб. на одного производственного рабочего.
Ринв. = 150 · 17 = 2550 руб.
Расходы на охрану труда принимаем по данным предприятия 3% от годового фонда заработной платы основных производственных рабочих.
Рот. = 2`831`248·003 = 84`937 руб.
Затраты на рационализаторскую и изобретательскую деятельность.
Принимаем по данным предприятия 100 руб. на одного производственного рабочего.
Ррац. = 100·17 = 1700 руб.
Расходы на электроэнергию.
Расходы на электроэнергию при укрупненных расходах принимаем 4000 кВт на одного производственного рабочего. Стоимость 1 кВт=045 руб.
Рэл. = 4000 · 17 · 045 = 30600 руб.
Прочие расходы принимаем 3% от суммы затрат по перечисленным выше статьям.
Рпр. = (840`000 + 218`400 + 760`763 + 570`572 + 1`711`716 + 665`668 + 2550 + 84`937 + 1700 + 30`600) · 003 = 146`607 руб.
Таблица 5.5 - Смета цеховых расходов
Заработная плата ИТР СКП
Отчисления в социальный фонд
Расходы на содержание и ремонт оборудования
Расходы на содержание и ремонт производственных помещений
Расходы на амортизацию оборудования
Расходы на амортизацию здания
Расходы на износ и содержание малоценного инвентаря
Отчисления на охрану труда
Затраты на рационализаторскуюдеятельность
Затраты на электроэнергию
Таблица 5.5 - Расходы на ТО и ремонт.
Затраты на материалы и зап. части
Фонд заработной платы
Определение себестоимости одного часа работ на проведение ТО и ремонта.
где ΣР - Расходы на ТО и ремонт.
Σ Т - Суммарная трудоемкость на проведение ТО и Р Σ Тт = 11389ччас
Sед.= 10`760`43311389 = 945 руб.час.
Определение цены одного часа работ на проведение ТО и ремонта.
Прибыль на один час проведения работ по ТО и ремонту.
ΔS = 1182 – 945=237 рубчас.
Прибыль предприятия на проведение ТО и ремонта в год.
S = 237 · 11389 = 2`699`193 руб.
Окупаемость затрат на ТО и ремонт.
Токуп.= 19`019`070 2`669`193= 66 года.
Таблица 5.6 - Технико-экономические показатели
Капитальные вложения
Список используемой литературы
Анурьев В.И. справочник конструктора машиностроения: Т.1. – М.: Машиностроение 1982. – 729 с.
Башта Т.М. Руднев С.С. Некрасов Б.Б. Гидравлика гидромашины и
гидропровода. – М.: Машиностроения 1982. – 424 с.
Башта Т.М. Гидропровод и гидропневмоавтоматика. – М.: Машиностроение 1972. – 320 с.
Безопасность жизнедеятельности в условиях производства: Методические указания к дипломному проектированию Сост. Ю.В. Шешуков. – Иркутск 1992. – 36 с.
Беспалов Н.А. Дорожно-строительные машины и оборудования: Справочник. – К.: Будивельник 1980. – 177 с.
Гурвич И.С. Эксплуатация и ремонт дорожно-строительных машин. – М.: Транспорт 1989. – 236 с.
Дунаев П.Ф. Конструирование узлов и деталей машин. – М.: Высшая школа. 1985. – 416 с.
Зеленков Г.И. Технология ремонта дорожных машин и основы роектирования ремонтных предприятий. – М.: Высшая школа 1972. – 495 с.
Иванов М.И. Детали машин. – М.: Высшая школа 1991. – 496 с.
Кламанн Д. Смазки и родственные продукты. – М.: Химия 1988. – 488 с.
Косилова А.Г. Справочник технолога машиностроителя: Т.2. – М.: Высшая школа 1985. – 495 с.
Лукьяненко В.М. Таранец А.В. Промышленные центрифуги. – М.: Химия 1974. – 376 с.
Планирование годового режима работы парка машины: Методическое указание по выполнению практической работы Сост. А.И. Нижегородов О.Н. Спивак. – Иркутск 19995. – 6 с.
Чернавский А.С. Курсовое проектирование деталей машин. – М.: Машиностроение 1988. – 415 с.
9,10 техкарта.dwg

Сталь 45 ГОСТ1050-74
ДПДМ2012.001.00.00.00 ТК
Средний делительный диаметр
Коэф. смещения исходного контура
Направление линии зуба
Угол делительного конуса
Острые кромки притупить
радиусы скруглений 2мм
Неуказанные предельные отклонения размеров:
*Размеры для справок.
Заготовительная Установить
снять заготовку. Отрезать заготовку ø98 в размер L=276. Сверлить центровочные отверстия ø5 с обоих сторон.
Фрезерно- центровальный станок МР-37М.
Дисковая отрезная фреза. Сверло центр. ø 5
Токарно-винторезный станок 16Б05П
Резец широкий отогнутый из быстрорежущей стали ГОСТ 18874-73 Резец торезной из быстрорежущей стали по ГОСТ 18874-73
Трехкулачковый спиральнореечный патрон повышенной точности по ГОСТ 2675-80
Зубофрезерный станок 53А30П
Трехкулач ковый патрон
Шлифовальная Установить деталь Шлифовать поверхность 1 с ф45
до ф45k6 на длину 42. Шлифовать поверхность 2 с ф45
до ф45k6 на длину 32.
Зубошлифовальная Установить деталь Шлифовать зубья конического колеса.
Круглошлифовальный станок 3М153
Круг шлифовальный Э-46-60 С2-СТ1К
Зубошлифовальный станок МСЗ-345-А
Круг шлифовальный Э-46-60 С1-СТ1К
Контрольная Установить деталь Проверить размеры в соответствии с чертежом
Шлицешлифовальный станок МСЗ-345-А
Шлицешлифовальная Установить деталь Шлифовать шлицы длиной l=60 мм
Трехкулач ковый патрон
Токарная Установить заготовку Проточить пов. 1 с ф98 до ф48 на длину 232(черновая обработка) Проточить пов. 1 с ф48 до ф45
на длину 232(чистовая обработка) Проточить пов. 2 с ф45
контролируя длину 146(черновая обработка) Проточить пов. 2 с ф41
контролируя длину 146мм(чистовая обработка) Снять 2 фаски 2х45 с ф45
до ф41. Проточить пов. 3 с ф45
на длину 38. Проточить пов. 3 с ф37
до ф36 на длину 38. Прорезать канавку с ф36 до ф32 на ширину 4
контролируя размер 34. Снять фаску 2х45 с ф36 до ф32.
Переставить и закрепить заготовку. Проточить пов.4 с ф98 до ф50 на ширину 4(черновая). Проточить пов.4 с ф50 до ф48 на ширину 4(чистовая). Снять фаску 3
х35 с ф98 до ф85. Обрабатываем коническую пов. на проход(черновая обработка). Обрабатываем коническую пов. на проход(чистовая обработка).
Фрезерная Установить деталь Нарезать шлицы длиной 60мм
Нарезать резьбу М36х1
Нарезать зубья конического колеса длиной 42мм глубиной 8 мм
количество зубьев-24.
Термическая Произвести закалку ТВЧ с нагревом до t=850 C. Произвести отпуск: нагреть деталь до t=180-200 C и выдержать 0
-1 ч. Охладить на воздухе.
ТЕХНИКО-ЭКОНОМИЧЕСКОЕ ОБОСНОВАНИЕ
Технико-экономические
ДПДМ2012.001.00.00.00 ПЭ
НФ БГТУ им. В.Г. Шухова
Затраты на материалы и запасные части 2 895 672
Фонд заработной платы 2 831 248
Цеховые расходы 5 033 513
Стоимость на одинмашино
Затраты на материалы и запасные части при ТО и Р
Статьи расходов Сумма
Общая трудоемкость челчас 11 389
Дополнительные капит. вложения тыс. руб. 19 019 070
Капитальные вложения на ТО и Р тыс. руб. 10 760 433
Себестоимость рубчас 945
Прибыль предприятия тыс. руб. 2 966 193
Период окупаемости год 6.6
Наименование Единица измерения Проект
Технико-экономические показатели
содерж 1.doc
1 Диагностика как дополнение планово-предупредительных работ
2 Организационные приемы диагностики
Расчетно-технологическая часть
1 Годовой план технического обслуживания и ремонта .
2 Выбор технологического оборудования .
Расчётно – проектировочная часть ..
1 Оснащение постов диагностирования .
2 Оснащение передвижных средств диагностирования
3 Машина для технического диагностирования
Безопасность жизнедеятельности .
1 Основные меры безопасности проектируемого предприятия
2 Общая характеристика опасных и вредных производственных факторов в зоне ТО
3 Электробезопасность
4 Техника безопасности при диагностировании строительно- дорожных машин
Экономическая часть
1 Расчет капитальных вложений .
2 Смета затрат на производство техническое ТО и Р эксплуатируемой техники
Список используемой литературы .
0605-ДП-14-3453-00-00-00 ПЗ
«Организация технического обслуживания и ремонта парка машин на базе Спецстрой России ФГУП «ГУССТ №4 УПП №422» с разработкой передвижного диагностического поста»
7 лист техн рессор_.dwg

Технологическая карта
расборки сборки рессор заднего
моста подъемника автомобильного ПАРТ-24
расборки сборки рессор заднего моста
подъемника автомобильного ПАРТ-24
Отвернуть гайки стремянки
крепления съемного ушка и
Отвернуть гайку крепления
ушка к листам рессор и
Отвернуть гайки крепления
Вынуть болты с распорыми
Смазать листы графитной
Установить и закрепить
Поставить рессору на
расборки сборки рессор заднего моста
Собрать листы рессоры
Разъединить листы рессоры
Выпресовать втулки из ушка
расборки сборки рессор
Отверстия под крепежные болты 2
Поставить рессору на
Смазать листы графитной
Отвернуть гайки крепления
ушка к листам рессор и
Отвернуть гайку крепления
крепления съемного ушка и
Отвернуть гайки стремянки
7 лист техн рессор.dwg

Технологическая карта
расборки сборки рессор заднего
моста подъемника автомобильного ПАРТ-24
расборки сборки рессор заднего моста
подъемника автомобильного ПАРТ-24
Отвернуть гайки стремянки
крепления съемного ушка и
Отвернуть гайку крепления
ушка к листам рессор и
Отвернуть гайки крепления
Вынуть болты с распорыми
Смазать листы графитной
Установить и закрепить
Поставить рессору на
расборки сборки рессор заднего моста
Собрать листы рессоры
Разъединить листы рессоры
Выпресовать втулки из ушка
расборки сборки рессор
0605-ДП-14-3453-00-00-00ТК
Отверстия под крепежные болты 2
Поставить рессору на
Смазать листы графитной
Отвернуть гайки крепления
ушка к листам рессор и
Отвернуть гайку крепления
крепления съемного ушка и
Отвернуть гайки стремянки
Приложения.doc
Диагностическая машина
Стенд диагностический
Прибор для испытания и
Корпус тензометричес-
Пробка сливная МК 20×15
ТЗ-250-120 ГОСТ 1663-57
Блок распределительный
Предохранительный клапан
Корпус тензометрического
Электроды типа Э 50 А
Корпус производственный
Отделение диагностики ГТ
Агрегатное отделение
Жестяночное отделение
Слесарно-механическое
Отделение по ремонту
Помещения для пригото-
Отделение диагностики КТ
Шиномонтажное отдел.
Электротехническое отдел.
Аккумуляторное отдел.
Шкаф с диагностическим
Устройство для слива
Реостат регулировочный
Установка для диагностики
топливной аппаратуры
Бак настенный топливный
Стенд для регулировки
Прибор для диагностики
Компрессорная установка
3,4,5 лист_recover000.dwg

подьемника автомобильного
ПЗ.01.00.Сб Рессора 1
ПЗ.02.00.Сб Дополнительная рессора 1
ПЗ.03.00.Сб Продольная балка 1
ПЗ.04.00.Сб Балка моста 1
ПЗ.00.01.Сб Стремянка 3
ПЗ.00.02.Сб Хомутики 6
ПЗ.00.03.Сб Кронштейн 4
ПЗ.00.04.Сб Масленка 1
ПЗ.00.05.Сб Ушко рессоры 1
ПЗ.00.06.Сб Накладка 3
ПЗ.00.07.Сб Опорный сухарь 1
ПЗ.00.08.Сб Фиксаторная подушка 1
Числа месяца и виды ТО и ремонта
МЕСЯЧНЫЙ ПЛАН-ГРАФИК ТЕХНИЧЕСКОГО ОБСЛУЖИВНИЯ И РЕМОНТА СТРОИТЕЛЬНО-ДОРОЖНЫХ МАШИН НА МАРТ МЕСЯЦ 2014г.
Диагностическая машина (Вид общий)
Техническая характеристика:
Базовая машина "Газель
Скорость передвижения-45 кмч
Обслуживающий персонал-2 чел.
Количество обслуживаемых машин
000000000000000000000О
190605-ДП-14-3453-01-00-00СБ Рессора 1
190605-ДП-14-3453-02-00-00СБ Дополнительная рессора 1
190605-ДП-14-3453-03-00-00СБ Продольная балка 1
190605-ДП-14-3453-04-00-00СБ Балка моста 1
190605-ДП-14-3453-01-01-00 Стремянка 3
190605-ДП-14-3453-01-02-00 Хомутики 6
190605-ДП-14-3453-01-03-00 Кронштейн 4
190605-ДП-14-3453-01-04-00 Масленка 1
190605-ДП-14-3453-01-05-00 Ушко рессоры 1
190605-ДП-14-3453-01-06-00 Накладка 3
190605-ДП-14-3453-01-07-00 Опорный сухарь 1
190605-ДП-14-3453-01-02-00 Фиксаторная подушка 1
0605-ДП-14-3453-00-00-00ПЗ Пояснительная записка 1
0605-ДП-14-3453-01-00-00СБ Задняя подвеска 1
Месячный план-график
3,4,5 лист_recover.dwg

подьемника автомобильного
ПЗ.01.00.Сб Рессора 1
ПЗ.02.00.Сб Дополнительная рессора 1
ПЗ.03.00.Сб Продольная балка 1
ПЗ.04.00.Сб Балка моста 1
ПЗ.00.01.Сб Стремянка 3
ПЗ.00.02.Сб Хомутики 6
ПЗ.00.03.Сб Кронштейн 4
ПЗ.00.04.Сб Масленка 1
ПЗ.00.05.Сб Ушко рессоры 1
ПЗ.00.06.Сб Накладка 3
ПЗ.00.07.Сб Опорный сухарь 1
ПЗ.00.08.Сб Фиксаторная подушка 1
Числа месяца и виды ТО и ремонта
МЕСЯЧНЫЙ ПЛАН-ГРАФИК ТЕХНИЧЕСКОГО ОБСЛУЖИВНИЯ И РЕМОНТА СТРОИТЕЛЬНО-ДОРОЖНЫХ МАШИН НА МАРТ МЕСЯЦ 2014г.
Диагностическая машина (Вид общий)
Техническая характеристика:
Базовая машина "Газель
Скорость передвижения-45 кмч
Обслуживающий персонал-2 чел.
Количество обслуживаемых машин
000000000000000000000О
190605-ДП-14-3453-01-00-00СБ Рессора 1
190605-ДП-14-3453-02-00-00СБ Дополнительная рессора 1
190605-ДП-14-3453-03-00-00СБ Продольная балка 1
190605-ДП-14-3453-04-00-00СБ Балка моста 1
190605-ДП-14-3453-01-01-00 Стремянка 3
190605-ДП-14-3453-01-02-00 Хомутики 6
190605-ДП-14-3453-01-03-00 Кронштейн 4
190605-ДП-14-3453-01-04-00 Масленка 1
190605-ДП-14-3453-01-05-00 Ушко рессоры 1
190605-ДП-14-3453-01-06-00 Накладка 3
190605-ДП-14-3453-01-07-00 Опорный сухарь 1
190605-ДП-14-3453-01-02-00 Фиксаторная подушка 1
0605-ДП-14-3453-00-00-00ПЗ Пояснительная записка 1
0605-ДП-14-3453-01-00-00СБ Задняя подвеска 1
Месячный план-график
2 Годовой план.dwg

ДПДМ2012.001.00.00.00 ПГ
НФ БГТУ им. В.Г. Шухова
Планируемое время работы на год
Виды ТО и ремонта в планируемом году
Технических обслуживаний
3,4,5 лист.dwg

подьемника автомобильного
ПЗ.01.00.Сб Рессора 1
ПЗ.02.00.Сб Дополнительная рессора 1
ПЗ.03.00.Сб Продольная балка 1
ПЗ.04.00.Сб Балка моста 1
ПЗ.00.01.Сб Стремянка 3
ПЗ.00.02.Сб Хомутики 6
ПЗ.00.03.Сб Кронштейн 4
ПЗ.00.04.Сб Масленка 1
ПЗ.00.05.Сб Ушко рессоры 1
ПЗ.00.06.Сб Накладка 3
ПЗ.00.07.Сб Опорный сухарь 1
ПЗ.00.08.Сб Фиксаторная подушка 1
Числа месяца и виды ТО и ремонта
МЕСЯЧНЫЙ ПЛАН-ГРАФИК ТЕХНИЧЕСКОГО ОБСЛУЖИВНИЯ И РЕМОНТА СТРОИТЕЛЬНО-ДОРОЖНЫХ МАШИН НА МАРТ МЕСЯЦ 2014г.
Диагностическая машина (Вид общий)
Техническая характеристика:
Базовая машина "Газель
Скорость передвижения-45 кмч
Обслуживающий персонал-2 чел.
Количество обслуживаемых машин
0605-ДП-14-3453-00-00-00ВО
190605-ДП-14-3453-01-00-00СБ Рессора 1
190605-ДП-14-3453-02-00-00СБ Дополнительная рессора 1
190605-ДП-14-3453-03-00-00СБ Продольная балка 1
190605-ДП-14-3453-04-00-00СБ Балка моста 1
190605-ДП-14-3453-01-01-00 Стремянка 3
190605-ДП-14-3453-01-02-00 Хомутики 6
190605-ДП-14-3453-01-03-00 Кронштейн 4
190605-ДП-14-3453-01-04-00 Масленка 1
190605-ДП-14-3453-01-05-00 Ушко рессоры 1
190605-ДП-14-3453-01-06-00 Накладка 3
190605-ДП-14-3453-01-07-00 Опорный сухарь 1
190605-ДП-14-3453-01-02-00 Фиксаторная подушка 1
0605-ДП-14-3453-00-00-00ПЗ Пояснительная записка 1
0605-ДП-14-3453-01-00-00СБ Задняя подвеска 1
0605-ДП-14-3453-00-00-00ПМ
Месячный план-график
0605-ДП-14-3453-00-00-00Пл
3 диагностическая машина.dwg

Диагностическая машина
ДПДМ2012.001.00.00.00 ВО
Техническая характеристика:
Базовая машина "Газель
Скорость передвижения-45 кмч
Обслуживающий персонал-2 чел.
Количество обслуживаемых машин
ДПДМ2012.001.00.00.00 ВО
ПЗ 2014.doc
Под эксплуатацией строительно-дорожных машин и оборудования (СДМ и О) принято понимать комплексную систему инженерно-технических и организационных мероприятий обеспечивающих наиболее эффективное использование возможностей машин высокую их эксплуатационную надёжность а также минимальные простои при техническом обслуживании (ТО) и ремонте с минимальными затратами. Поэтому как только машина введена в эксплуатацию возникает ряд вопросов: как спланировать и организовать ТО и ремонт какие формы наиболее целесообразны для данного типа машин и конкретных условий эксплуатации что когда как и зачем необходимо проверить и отрегулировать.
Цель теории состоит в том чтобы дать необходимые теоретические знания и практические навыки в области эксплуатации машин и оборудования и научиться управлять использованием и техническим состоянием машин с применением современных средств и методов технической диагностики руководствуясь принципом минимизации эксплуатационных затрат.
Основной задачей инженера-механика занимающегося эксплуатацией машин является поддержание машин в технически исправном состоянии что получило название технической эксплуатации. С точки зрения теории надежности техническая эксплуатация - это обеспечение надежности машин и оборудования в условиях эксплуатации. Отсюда возникает вторая задача — инженера-механика увязывать разработки теории надежности с практическими задачами возникающими при эксплуатации машин. Эта задача заключается в умении раскрывать закономерности изменения технического состояния машин и потери ими работоспособности в процессе эксплуатации в изучении методов и средств направленных на поддержание машин в технически исправном состоянии.
С точки зрения современной теории управления техническая эксплуатация как и всякая теория управления имеет обратную связь в виде поступления информации об эксплуатационной надежности машин что немыслимо без современных средств и методов технической диагностики. Поэтому увязка технологии и организации диагностирования машин с существующей системой планово-предупредительного ремонта (ППР) является третьей важной задачей - инженера-механика.
По своему характеру техническое диагностирование разделяется на функциональное и тестовое. Функциональное техническое диагностирование осуществляется во время функционирования объекта диагностирования на который поступают только рабочие воздействия. Тестовое техническое диагностирование предполагает наведение на объект диагностирования специальных тестовых воздействий.
По обхвату техническое диагностирование разделяется на общее и локальное. Общей системой технического диагностирования устанавливается техническое состояние всего объекта в целом тогда как локальной системой - только техническое состояние отдельных составных частей объекта диагностирования.
1 Диагностика как дополнение планово-предупредительных работ
Система планово-предупредительных работ долгое время не подвергалась существенным изменениям. По мере усложнения конструкций машин увеличения их количества а также необходимости повышения затрат на эксплуатацию все очевиднее становятся их недостатки. Так в связи со значительным рассеиванием фактических значений показателей надежности машин принятая в настоящее время система ППР не обеспечивает заданного срока работы изделий и не может обеспечить полного использования их ресурса.
Как правило этот ресурс оказывается или выбранным (в этом случае на ремонт становится машина которая еще не может работать) или перерасходованным когда машина оказывается в зоне аварийного износа что значительно удорожает стоимость ее ремонта. При этом разработанные системы оптимизации периодичности ТО и ремонтов не нашли широкого применения в силу своей сложности.
Поэтому в настоящее время наметилась тенденция замены принятой системы ППР системой технического обслуживания и ремонта по техническому состоянию.
В ее основу положен плановый контроль состояния машины с помощью диагностических средств и проведение ТО и ремонта в зависимости от этого состояния. Такая система обеспечивает почти полное использование технического ресурса составных частей и машины в целом а также предотвращение отказов машин и тем самым обусловливает высокую безотказность и долговечность их в процессе эксплуатации.
2 Организационные приемы диагностики
Эффективность диагностирования зависит от места диагностирования в технологическом процессе технического обслуживания и ремонт строительно-дорожных машин. Наиболее распространены совмещенная и специализированная формы диагностирования. Совмещенное диагностирование не требует какого-либо организационного процесса. Специализированное диагностирование осуществляет функцию управления технологическим процессом. Технологические потоки проходят через участок диагностирования.
Процесс диагностирования состоит из трех этапов: подготовленного основного и заключительного.
На подготовительном этапе проводят мойку чистку и внешний осмотр машины. Результаты осмотра заносят в диагностическую карту. Устанавливают диагностические приборы и датчики.
Таблица 1.1 - Перечень основных параметров определяемых при общем (Д-1) и углубленном (Д-2) диагностировании
Наименование сборочных единиц систем механизмов
Диагностические параметры и признаки
Общее состояние двигателя
Частота вращения вала
Удельный расход топлива
Кривошипно-шатунный механизм
Цилиндропоршневая группа
Компрессия в отдельных цилиндрах
Количество газов прорвавшихся в кратер
Частота вращения центрифуги
Продолжительность вращения центрифуги
Механизм газораспределения
Плотность прилегания клапанов
Зазоры между элементами механизма
Угол начала открытия впускных клапанов
Система охлаждения двигателя
Натяжение ремня вентилятора
Система очистки и подачи воздуха
Степень загрязнения воздухоочистителя
Герметичность впускного воздушного тракта
Продолжение таблицы 1.1
Система питания двигателя
Пропускная способность фильтрующих элементов грубой и тонкой очистки
Давление впрыска и качества распыла топлива форсунками
Производительность топливного насоса
Степень неравномерности подачи топлива элементами топливного насоса
Угол опережения впрыска топлива
Частота вращения кулачкового вала топливного насоса
Степень разреженности аккумуляторных батарей
Напряжение на фазах генератора
Напряжение поддерживаемое реле генератора
Величина тока регулируемая ограничителем тока
Величина тока отключения реле обратного тока
Величина тока потребляемого стартером
Состояние контрольно-измерительных приборов
Степень натяжения ремня генератора
Скорость подъема и опускания рабочего оборудования
Давление в гидросистеме
Температура рабочей жидкости
Загрязнение рабочей жидкости
Расход рабочей жидкости
Степень натяжения ремня компрессора
Герметичность пневмосистемы
Давление воздуха в системе
Натяжение гусеничной цепи
Износ гусеничных звеньев
Износ ведущей звездочки
Зазор направляющих колес опорных и поддерживающих катков
Схождение передних колес
Трансмиссия и система управления
Свободный ход рулевого колеса и усилия на ободе
Усилие и ход рычагов управления
Суммарный зазор в механизмах силовой передачи
Осевой и радиальный зазор в сопряжениях силовой передачи зазор в подшипниках
Степень износа канатов
Люфты в крюковой обойме
Размеры и число повреждений
Уровни срабатывания приборов безопасности
На основном этапе определяют техническое состояние машины и выполняют часть регулировочных работ.
На заключительном этапе проводят анализ результатов диагностики при этом уточняют характер и объем работ по техническому воздействию на машину и прогнозируют остаточный ресурс сборочных единиц. Снимают приборы и датчики с машины и проверенную машину направляют в зону соответствующих работ по техническому обслуживанию и ремонту.
Диагностирование проводят в сроки установленные для соответствующих технических воздействий и объема работ. Объем работ уточняют как в результате опроса оператора машины так и по показаниям приборов выявляющих мощностные характеристики машин и работоспособность сборочных единиц обеспечивающих безопасность производства работ. В обязательном порядке выполняют работы по общему диагностированию и по его результатам уточняют объем углубленного диагностирования. Перечень основных параметров при общем (Д-1) и углубленном (Д-2) диагностированиях приведен в таблице 1.1.
Причем ряд таких параметров углубленного диагностирования (Д-2) таких как загрязненность рабочей жидкости плотность электролита загрязненность воздухоочистителя давление масла в системе смазки определяют в обязательном порядке независимо от результатов общего диагностирования.
С учетом необходимости проверки основных диагностических параметров комплектуют оборудованием посты и участки технического обслуживания и ремонта.
При комплектовании диагностическим оборудованием учитывают объем производимых работ.
При специализированной форме диагностирования и. следовательно большом объеме диагностических работ используют средства позволяющие быстро и точно определить максимальное число параметров. В стационарных условиях применяют стенды позволяющие до минимума сократить время диагностирования на всех этапах (за счет установки датчиков уменьшении числа проверок стабилизации условий проверок и т.д.) В передвижных установках необходимое уменьшение времени на диагностирование достигают оснащением средств легкосъемными соединительными элементами уменьшением числа переносных средств.
Последовательность определения диагностических параметров устанавливают для каждого параметра на работоспособность машины. Обычно сначала проверяют параметры обеспечивающие безопасность производства работ затем общие после чего диагностируют основные сборочные единицы начиная с двигателя. В принятой последовательности производят специализацию диагностических постов а на универсальных постах – размещение оборудования.
Все посты оснащают документацией на диагностирование. На постах должна храниться документация по проверке диагностических средств.
С диагностическими средствами работает специально обученный персонал. По результатам диагностирования определяют исходя из общей трудоемкости диагностирования и с учетом возможности применения наиболее эффективного оборудования с полной загрузкой. При специализированном диагностировании возможно создание постов комплексного диагностирования так и специализированных постов.
С учетом технологической схемы участка диагностирования оборудование обычно размещают с соответствующим подводом электроэнергии воздуха и воды отоплением и системой вывода выхлопных газов.
Расчетно-технологическая часть
Наименование парка строительно-дорожной техники.
Таблица 2.1 – Номенклатура парка строительно-дорожной техники
Наработка на начало года
Продолжение таблицы 2.1
1 Годовой план технического обслуживания и ремонта
Для разработки годового плана ТО и Р машин следует получить возможное количество часов их работы за год (дефективные нормы).
Действительный годовой фонд времени или дефективная норма Тд определяется:
где ТН - номинальное число часов работы машины за год час;
КВ = 085-095 - коэффициент использования рабочего времени машин в течении года;
Номинальное число рабочих часов машины в год равно:
ТН = (ДК - (ДВ + ДП)) . tCM . ПСМ час;
здесь ДК - количество календарных дней в году (365 д.);
ДВ - количество воскресных и субботних дней в году (105 д.);
Дп - количество праздничных дней в году (7 д.);
tсм - длительность рабочей смены (8 час);
Псм - число смен работы машин в сутки (1).
Тн = (365 - (105 + 7)) . 8 . 1 = 2024
Тд.эк. = 2024 .085 = 17204;
Тд.б. = 2024 . 075 = 1518ч;
Tд.ав. = 2024 . 082 =16597 ч;
Тд.погр. = 2024 . 085 = 17204 ч;
Тд.кр. = 2024 . 092 = 1862ч;
Тд..тр.= 2024 .08 = 16192 ч;
Число технических обслуживании и ремонтов каждого вида NTO Р которые должны быть проведены в планируемом году для соответствующей машины рассчитывают по формуле:
где Тф - величина фактической наработки на начало планируемого года со времени проведения последнего аналогичному расчетному вида технического обслуживания ремонта или с начала эксплуатации час;
Тп.л.- планируемая наработка или директивная норма на расчетный год час;
Тп - доремонтный или межремонтный ресурс соответствующего вида технического обслуживания или ремонта по которому ведется расчет час;
Nп - число всех видов технических обслуживании и ремонтов с периодичностью большей периодичности того вида по которому ведется расчет (при расчете капитального ремонта Nп - 0).
Таблица 2.2 - Число ТО и Р для каждого вида машин в планируемом году
Продолжение таблицы 2.2
Экскаватор ЭО-2621 инвентарный номер 101
К.: NTOP=((16716+17204)5760)-0=0
Т.: NTOP=((7116+17204)960)-0=2
TO-2: NТОР=((2316+17204)240)-2=6
TO-1: NТОР=((516+17204)60)-8=21
Экскаватор ЭО-2621 инвентарный номер 102
К.: NTOP=((42003+17204)5760)-0=1
Т.: NTOP=((3603+17204)960)-1=1
TO-2: NТОР=((1203+17204)240)-2=5
TO-1: NТОР=((03+17204)60)-7=21
Экскаватор ЭО-2621 инвентарный номер 103
К.: NTOP=((6476+17204)5760)-0=0
Т.: NTOP=((6476+17204)960)-0=2
TO-2: NТОР=((1676+17204)240)-2=5
TO-1: NТОР=((476+17204)60)-7=22
Экскаватор ЭО-4321Б инвентарный номер 104
К.: NTOP=((55446+17204)7680)-0=0
Т.: NTOP=((7446+17204)960)-0=2
TO-2: NТОР=((246+17204)240)-2=5
TO-1: NТОР=((246+17204)60)-7=22
Экскаватор ЭО-4121 инвентарный номер 105
К.: NTOP=((6461+17204)7680)-0=0
Т.: NTOP=((6461+17204)960)-0=2
TO-2: NТОР=((1661+17204)240)-2=5
TO-1: NТОР=((461+17204)60)-7=22
Экскаватор ЭО-5126 инвентарный номер 106
К.: NTOP=((36223+17204)9600)-0=0
Т.: NTOP=((6223+17204)1000)-0=2
TO-2: NТОР=((1223+17204)500)-2=1
TO-1: NТОР=((223+17204)100)-7=14
Экскаватор ЭО-5126 инвентарный номер 107
К.: NTOP=((47853+17204)9600)-0=0
Т.: NTOP=((7853+17204)1000)-0=2
TO-2: NТОР=((2853+17204)500)-2=2
TO-1: NТОР=((853+17204)100)-4=14
Экскаватор ЭО-5124 инвентарный номер 108
TO-1: NТОР=((223+17204)100)-3=14
Экскаватор ЭО-5124 инвентарный номер 109
Экскаватор ЭО-5122 инвентарный номер 110
К.: NTOP=((58668+17204)9600)-0=0
Т.: NTOP=((8668+17204)1000)-0=2
TO-2: NТОР=((3668+17204)500)-2=2
TO-1: NТОР=((668+17204)100)-4=13
Экскаватор ЭО-5122 инвентарный номер 111
К.: NTOP=((30149+17204)9600)-0=0
Т.: NTOP=((149+17204)1000)-0=1
TO-2: NТОР=((149+17204)500)-1=2
TO-1: NТОР=((149+17204)100)-3=14
Бульдозер Д532 Т170 инвентарный номер 212
К.: NTOP=((30149+1518)7680)-0=0
Т.: NTOP=((1349+1518)960)-0=1
TO-2: NТОР=((1349+1518)240)-1=5
TO-1: NТОР=((149+1518)60)-6=19
Бульдозер Д532 Т170 инвентарный номер 213
К.: NTOP=((48853+1518)7680)-0=0
Т.: NTOP=((853+1518)960)-0=1
TO-2: NТОР=((853+1518)240)-1=5
TO-1: NТОР=((253+1518)60)-6=19
Бульдозер Д532 Т170 инвентарный номер 214
К.: NTOP=((49334+1518)7680)-0=0
Т.: NTOP=((1334+1518)960)-0=1
TO-2: NТОР=((1334+1518)240)-1=5
TO-1: NТОР=((134+1518)60)-6=19
Бульдозер Д532 Т170 инвентарный номер 215
К.: NTOP=((3557+1518)7680)-0=0
Т.: NTOP=((6757+1518)960)-0=2
TO-2: NТОР=((1957+1518)240)-2=5
TO-1: NТОР=((157+1518)60)-7=18
Бульдозер ДЗ 170 инвентарный номер 216
К.: NTOP=((60389+1518)7680)-0=0
Т.: NTOP=((2789+1518)960)-0=1
TO-2: NТОР=((389+1518)240)-1=5
TO-1: NТОР=((389+1518)60)-6=19
Бульдозер ДЗ 170 инвентарный номер 217
К.: NTOP=((22446+1518)7680)-0=0
Т.: NTOP=((3246+1518)960)-0=1
TO-2: NТОР=((846+1518)240)-1=5
TO-1: NТОР=((246+1518)60)-6=19
Бульдозер ДЗ 170 инвентарный номер 218
К.: NTOP=((56004+1518)7680)-0=0
Т.: NTOP=((8004+1518)960)-0=2
TO-2: NТОР=((804+1518)240)-2=4
TO-1: NТОР=((204+1518)60)-6=19
Бульдозер ДЗ 170 инвентарный номер 219
К.: NTOP=((51252+1518)7680)-0=0
Т.: NTOP=((3252+1518)960)-0=1
TO-2: NТОР=((852+1518)240)-1=5
TO-1: NТОР=((252+1518)60)-6=19
Бульдозер ДЗ 170 инвентарный номер 220
К.: NTOP=((32148+1518)7680)-0=0
Т.: NTOP=((3348+1518)960)-0=1
TO-2: NТОР=((948+1518)240)-1=5
TO-1: NТОР=((348+1518)60)-6=19
Бульдозер ДЗ-122 инвентарный номер 321
К.: NTOP=((38661+16597)5760)-0=0
Т.: NTOP=((261+16597)960)-0=1
TO-2: NТОР=((261+16597)240)-1=6
TO-1: NТОР=((261+16597)60)-7=21
Автогрейдер ДЗ 98 1 инвентарный номер 322
К.: NTOP=((20403+16597)5760)-0=0
Т.: NTOP=((1203+16597)960)-0=1
TO-2: NТОР=((1203+16597)240)-1=6
TO-1: NТОР=((03+16597)60)-7=20
Автогрейдер ДЗ 98 1 инвентарный номер 323
К.: NTOP=((57038+16597)5760)-0=0
Т.: NTOP=((9038+16597)960)-1=1
TO-2: NТОР=((1838+16597)240)-2=5
Автогрейдер ДЗ 143 инвентарный номер 324
К.: NTOP=((7957+16597)5760)-0=0
Т.: NTOP=((7957+16597)960)-0=2
TO-2: NТОР=((757+16597)240)-2=5
TO-1: NТОР=((157+16597)60)-7=20
Автогрейдер ДЗ 122А инвентарный номер 325
К.: NTOP=((5053+16597)5760)-0=0
Т.: NTOP=((5053+16597)960)-0=2
TO-2: NТОР=((253+16597)240)-2=5
TO-1: NТОР=((253+16597)60)-7=21
Каток ДУ 48Б инвентарный номер 426 427
К.: NTOP=((5053+12144)5760)-0=0
Т.: NTOP=((5053+12144)960)-0=1
TO-2: NТОР=((253+12144)240)-2=5
TO-1: NТОР=((253+12144)60)-7=21
Каток ДУ 47Б инвентарный номер 428
К.: NTOP=((52483+12144)5760)-0=1
Т.: NTOP=((4483+12144)960)-1=0
TO-2: NТОР=((2083+12144)240)-1=4
TO-1: NТОР=((283+12144)60)-5=15
Каток ДУ 37Б инвентарный номер 429
К.: NTOP=((1458+12144)5760)-0=0
Т.: NTOP=((498+12144)960)-0=1
TO-2: NТОР=((18+12144)240)-1=4
TO-1: NТОР=((18+12144)60)-5=15
Каток ДУ 65 инвентарный номер 430
К.: NTOP=((43739+12144)5760)-0=0
Т.: NTOP=((5339+12144)960)-0=1
TO-2: NТОР=((539+12144)240)-1=4
TO-1: NТОР=((539+12144)60)-5=16
Автокран КС-4561 инвентарный номер 531
К.: NTOP=((7572+1862)11520)-0=0
Т.: NTOP=((1812+1862)1920)-0=1
TO-2: NТОР=((132+1862)240)-1=7
TO-1: NТОР=((12+1862)60)-8=23
Автокран КС-4561 инвентарный номер 532
К.: NTOP=((6931+1862) 11520)-0=0
Т.: NTOP=((1171+1862)1920)-0=1
TO-2: NТОР=((211+1862)240)-1=7
TO-1: NТОР=((31+1862)60)-8=23
Погрузчик ТО-6 инвентарный номер 433
К.: NTOP=((33365+17204)5760)-0=0
Т.: NTOP=((4565+17204)960)-0=2
TO-2: NТОР=((2165+17204)240)-2=6
TO-1: NТОР=((365+17204)60)-8=21
Трейлер ЧМЗАП инвентарный номер 434
К.: NTOP=((17202+16192)5760)-0=0
Т.: NTOP=((7602+16192)960)-0=2
TO-2: NТОР=((402+16192)240)-2=4
TO-1: NТОР=((402+16192)60)-6=21
Трейлер ЧМЗАП инвентарный номер 435
К.: NTOP=((53036+16192)5760)-0=1
Т.: NTOP=((5036+16192)960)-1=1
TO-2: NТОР=((236+16192)240)-2=4
TO-1: NТОР=((236+16192)60)-6=21
Так как каток используется только в течении сезона то рассчитаем сезонный коэффициент:
Nмес.- число месяцев в сезоне
Порядковый номер месяца Км в котором должен проводиться капитальный ремонт машин (если при расчете Км окажется больше 12 КР машин в планируемом году не производится и переносятся на следующий год) рассчитывают по формуле:
где Тп- доремонтный или межремонтный ресурс капитального ремонта.
Рассчитываю порядковый номер месяца для ЭО-2621 инвентарный №102:
Рассчитываю порядковый номер месяца для ДЗ-98 инвентарный №323:
Рассчитываю порядковый номер месяца для ДУ-47Б инвентарный №428:
Рассчитываю порядковый номер месяца для ЧМЗАП инвентарный №735:
Разработка месячного плана-графика технического обслуживания и ремонта СДМ.
Месячный план-график ТО и ремонта машин устанавливает дату постановки каждой машины на ТО и ремонт и продолжительность ее простоя в днях. Его составляют на основании годового плана технического обслуживания и ремонта машин.
При выполнении дипломного проекта месячный план-график составляется на август месяц. Порядковый номер рабочего дня месяца Дтор в который начинается проведение технического обслуживания и ремонта машин определяется по формуле:
где Драб.- число рабочих дней в планируемом месяце определяемое по календарю с учетом установленного в данной организации режима работы;
Тп- межремонтный ресурс соответствующего вида ТО;
Тф- величина фактической наработки на начало планируемого месяца со времени проведения последнего аналогично расчетному вида ТО и ремонта или с начала эксплуатации;
Тпл- планируемая наработка на расчетный месяц.
Если при расчете ДТОР окажется больше чем число рабочих дней в месяце то соответствующий вид ТО и ремонта в этом месяце не проводят.
Принятое в системе ППР планирование профилактических воздействий носит условный характер поскольку машины работают в различных режимах при различном качестве технических воздействий и квалификаций эксплуатационного персонала. При этом необходимо учитывать план-график производства работ выполняемых организацией. Поэтому все профилактические воздействия планируют по срокам и объемам условно а их фактическое выполнение производят по потребности но в пределах установленных ограничений.
В зависимости от условий эксплуатации машин согласно ГОСТ 25646-83 допускается корректировать запланированную периодичность ТО в пределах 10% текущих ремонтов 8-5% за исключением случаев когда отклонение периодичности не допускается по условиям безопасности.
Согласно исследованию отклонение сроков проведения ТО от расчетных на 2-3 дня в ту или другую сторону вполне допустимо и экономически оправдано.
Таблица 2.3 – Проведение ТО
Фактическая наработка маш.час
С начала эксплуатации
Со времени проведения
Продолжение таблицы 2.3
Таким образом правильно разработанный месячный план-график должен быть увязан с графиком загрузки машин на объектах а также со сроками проведения сезонных технических осмотров служб государственных инспекций и со сроками выполнения планируемых капитальных ремонтов.
Экскаватор ЭО-2621 инв. №101
Экскаватор ЭО-2621 инв. №102
Экскаватор ЭО-2621 инв. №103
Экскаватор ЭО-4321Б инв. №104
Экскаватор ЭО-4121 инв. №105
Экскаватор ЭО-5126 инв. №106
Экскаватор ЭО-5126 инв. №107
Экскаватор ЭО-5124 инв. №108
Экскаватор ЭО-5124 инв. №109
Экскаватор ЭО-5122 инв. №110
Экскаватор ЭО-5122 инв. №111
Бульдозер Д532 Т170 инв. №212
Бульдозер Д532 Т170 инв. №213
Бульдозер Д532 Т170 инв. №214
Бульдозер Д532 Т170 инв. №215
Бульдозер ДЗ 170 инв. №216
Бульдозер ДЗ 170 инв. №217
Бульдозер ДЗ 170 инв. №218
Бульдозер ДЗ 170 инв. №219
Бульдозер ДЗ 170 инв. №220
Автогрейдер ДЗ 122 инв. №321
Автогрейдер ДЗ 981 инв. №322
Автогрейдер ДЗ 98 инв. №323
Автогрейдер ДЗ 143 инв. №324
Автогрейдер ДЗ 122А инв. №325
Каток ДУ 48Б инв. №426427
Каток ДУ 47Б инв. №428
Каток ДУ 37Б инв. №429
Каток ДУ 37Б инв. №430
Автокран КС-4561 инв. №531
Автокран КС-4561 инв. №532
Погрузчик ТО-6 инв. №633
Трейлер ЧМЗАП инв. №734
Трейлер ЧМЗАП инв. №735
2 Выбор технологического оборудования
Трудоемкость выполнения текущих ремонтов (Тртi) сезонных (Трсi) и технических (Тртоi) обслуживаний на каждую группу машин подсчитывается по формулам:
где Тртi Трсi Тртоi – соответственно трудоемкости проведения текущего ремонта технического и сезонного обслуживания для каждой группы машин.
Расчетные трудоемкости проведения текущих ремонтов (Тт) технических обслуживаний (Тто) и сезонных обслуживаний (Тс) подсчитываются по формулам:
Тт = Tртi Тто = Tртоi Тс = Tрсi
Таблица 2.4 - Трудоемкость ТО-1 ТО-2 СО и ТР
Продолжение таблицы 2.4
Трудоемкость проведения ТР: Ттр= 3496 чел.-ч.
Трудоемкость проведения СО: Тсо=758 чел.-ч.
Трудоемкость проведения ТО-2: ТТО-2 =1427 чел.-ч.
Трудоемкость проведения ТО-1: ТТО-2 =2173 чел.-ч.
Для гусеничных машин ТО1 и ТО2 проводятся с помощью передвижных средств диагностики ТО и ремонта:
ТТО2(гус.) =988 чел.-ч.
ТТО1(гус.) =1364 чел.-ч.
Тогда для отдельного парка строительно-дорожной техники:
ТТО1 = 2173-1364 =809 чел.-ч.
Общая трудоемкость проведения текущих ремонтов технических и сезонных обслуживаний:
ТО=( ТТ+ ТТО2+ ТТО2+ ТС) К1
где К1-коэффициент учитывающий нужды производства.
ТО=( 3496+2173 + 1427+ 758) 145=113883 чел.-час.
Трудоемкость по профессиям(ТПi) подсчитывается по формуле :
где К2-коэффициент учитывающий нужды производства.
ТО принимаем отдельно по каждой группе машин (автогрейдеры экскаваторы катки погрузчики поливочно-моечные машины краны гудронаторы асфальтоукладчики).
Примечание «*» означает что трудоемкость проведения ТО2; ТО1 за исключением диагностических работ суммируется для всех остальных видов
Таблица 2.5 - Количество строительно-дорожных машин по их специализации
обслуживание гидросистемы
Продолжение таблицы 2.5
обслуживание системы питания
По данным таблицы 5.5 суммарная трудоемкость по отделениям рассчитывается по формуле:
Тпiотдел. = Тпiмашин
где Тпiотдел берется из таблицы 2.5.
Данные расчета сводим в таблицу 2.6.
Таблица 2.6 - Суммарная трудоемкость по отделениям
Зона ТО1(колесная техника: крепежные
Регулировочные смазочные работы)
Ремонта гидрооборудования
Слесарно-механическое
Ремонта систем питания
Зона ТР (гусеничная техника колесная техника)
Количество рабочих (НРi) по каждой профессии подсчитывается по формуле:
где ТПГi – годовой фонд рабочего времени рабочего данной профессии равный:
для маляров и гальванизаторов- 1610 ч.
сварщиков кузнецов аккумуляторщиков медников - 1853 ч.
термистов вулканизаторщиков мойщиков электриков -1893 ч.
прочих профессий-1909 ч.
Диагностика:Нрдиагн.=1490641909=0781
Зона ТО1:Нрто1=2516161909=137
Агрегатное отделение:Нрагр.= 9671909=0607
Ремонт гидрооборудования:Нргидр.= 72951909=068
Слесарное отделение: Нрслес.= 3821909=0605
Аккумуляторное отделение:Нракк.= 1101853=0249
Тепловое отделение:Нртеп.= 5061853=0765
Электротехническое отделение:Нрэлтех=2141893=0513
Ремонт систем питания:Нрпит.= 4971909=056
Малярное отделение:Нрмаляр.= 1641610=0324
Шиномонтажное отделение:Нршин.= 721893=0241
Зона ТО2:Нр(тр кол.)= 22531909=127
Зона ТР: Нр(тр)= 20501909=155
Мойка:Нрмойки=38151893=0430
Исходя из подсчетов можно сделать вывод что один рабочий может обслуживать несколько отделений. Например при существующем объеме работ производственного цеха в шиномонтажном малярном и моечном отделениях все необходимые работы сможет выполнять один человек.
Таблица 2.7 - Распределение рабочих по отделениям
Отделение проведения ТО1
Отделение проведения ТО2
Отделение проведения ТР
Отделение диагностики
Отделение системы питания
Отделение ремонта и гидроаппаратуры
НPi=14 человек – в производственном цехе будет задействовано 14 человек.
Расчетные площади (ФРi) производственных помещений подсчитываются по формуле:
ФРi=( НРi или НСi)К4 м2
где К4-удельная площадь приходящаяся на работников данной группы.
Полученные данные сводим в таблицу 2.8.
Таблица 2.8 - Площади производственных помещений
Производственное помещение
Площадь помещения м2
Отделение ТР и ремонта агрегатов
Отделение по ремонту гидроаппаратуры
Электротехническое отделение
Аккумуляторное отделение
Тепловое отделение(кузнечное сварочное
Слесарно-механическое отделение
Шиномонтажное отделение
Отделение по ремонту систем питания
Таблица 2.9 - Перечень основного технологического оборудования
Перечень оборудования
Машина для наружной мойки
Моторный тестер КИ-4897 ГОСНИТИ
Прибор для определения технического состояния фар К-303
Прибор для диагностики электроприборов (реле стартеров генераторов) КИ-968 ГОСНИТИ
Переносной диагностический прибор К-484
Переносной газоанализатор Э-311
Расходомер топлива КИ-8910А
Компрессорная установка
Линейка универсальная для проверки схождения передних колес
Солидолонагнитатель 3154 9 (передвижной)
Аппарат для промывки маслосистем СДМ 1147 (передвижной)
Устройство для сборки масла УСОМ
Пост смазчика-заправщика С-201
Пост слесаря П-506 (передвижной)
Набор ключей стандартный
Гидравлический подъемник ГАРО 410
Установка по очистки гидравлического масла
Продолжение таблицы 2.9
Зона текущего ремонта
Шкаф инструментальный
Стенд с гайковертом для сборки ходовых тележек
Стенд для сборки разборки регулировки сцепления
Стенд для сборки бортовых фрикционов
Стенд для сборки коробок передач
Стенд для разборки сервомеханизма
Стенд для сборки механизма натяжения гусениц
Пресс гидравлический для выпресовки пальцев гусениц
Стенд для ремонтов гидроцилиндров
Стенд для испытания гидроагрегатов
Ларь для обтирочных материалов
Стенд для ремонта гидрораспределителей
Стенд для разборки топливной аппаратуры
Ванна для мойки деталей
Настольно-токарный станок
Сушильный шкаф для якорей
Ванна для пропитки якорей меллаком
Станок для намотки якорей
Настольно-сверлильный станок
Установка УБР-3 (передвижная) для нанесения краски при температуре =3100сС
Силеновый выпрямитель
Стенд для проверки зарядки аккумуляторов
Верстак для ремонта аккумуляторов
Шкаф для зарядки аккумуляторов
Ванна для слива и приготовления электролита
Приспособление для разлива кислоты
Ножницы рычажные ручные
Обдирочно-шлифовальный станок
Сварочный трансформатор
Молоток выкалотлчный
Верстак для жестянщика
Установка для отчистки радиаторов от накипи
Стенд для ремонта радиаторов
Ванна для промывки топливных баков
Станок для прогонки резьбы
Вертикально-сверлильный станок
Токарно-винторезный станок
Станок точильный двухсторонний
Агрегатное отделение
Стол для сборки крупногабаритных узлов
Стенд для сборки коробки передач
Радиально-сверлильный станок
Ванна для проверки камер
Стеллаж для покрышек
Ларь для резиновых отходов
Ручной пневматический борторасширитель
Электровулканизационный аппарат для ремонта камер
Настенная вешалка для камер
Расчет числа постов.
Число постов для проведения технического обслуживания и текущего ремонта определяется по формуле:
где Тр – годовой объем работ чел.-час
Дp – число рабочих дней в году
TCM - длительность смены
m – количество рабочих одновременно работающих на посту (2-4 чел).
n - коэффициент использованного рабочего времени поста (08-09)
– коэффициент учитывающий неравномерность поступления машин на пост.
Зона ТР для колесных и
Расчет числа подвижных диагностических средств и средств технического обслуживания
Количество передвижных средств для диагностического обслуживания определяется по формуле:
где ТПС - трудоемкость работ планируемых для передвижных средств чел.-ч
Тфс - годовой фонд рабочего времени передвижных средств (час)
m - число рабочих обслуживающих передвижное средство.
Кис - коэффициент использования передвижного средства Кис = 04.
Принимаем одну единицу – установку КИ-4270 на базе автомобиля Газель.
Количество передвижных средств технического обслуживания и ремонта определяем по формуле:
Кис - коэффициент использования передвижного средства КИС = 06.
Принимаем одну единицу – установку А-701 на базе автомобиля ЗИЛ-130.
Расчетно-проектировочная часть
Технология диагностирования.
Технология диагностирования машин предусматривает последовательность выполнения операций место подсоединения диагностических средств дополнительное оборудование и инструмент квалификацию обслуживающего персонала. Основное содержание технологии определяется целью и задачами диагностирования.
При разборке технологии необходимо учитывать что на трудоемкость и стоимость диагностирования значительное влияние оказывает последовательность выполнения работ. При этом работы группируют по однотипности диагностических параметров по необходимости выполнения одноименных работ при подготовительно-заключительных операциях. Все операции диагностирования группируют таким образом чтобы обеспечить максимальную и равномерную загрузку всех участков диагностирования машины и сократить время нахождения ее в процессе диагностирования до минимума при заданной вероятности возникновения отказов механизмов и систем.
Каждому виду технического обслуживания соответствует определенный вид диагностирования и следовательно определенный перечень и последовательность операций.
При составлении комплексной схемы маршрутной технологии диагностирования устанавливают перечень обязательных диагностических операций и последовательность проверки систем при выходе за допустимые пределы показателей общего технического состояния.
Упрощенная схема маршрутной технологии диагностирования машины с выявлением неисправностей различных систем представлена на рисунке 3.1.
Маршрутная технология диагностирования систем отражает все многообразие возможных состояний отдельных элементов и должна позволять при минимальных затратах труда отыскивать неисправности систем и механизмов. При составлении технологии диагностирования отдельных систем саму систему (или механизм) расчленяют на сборочные единицы устанавливают предельные значения структурных и диагностических параметров сборочных единиц выявляют минимальный перечень диагностических параметров и в результате составляют маршрутную схему проверки системы или механизма.
При составлении технологии диагностирования систем и механизмов разделение их на сборочные единицы производят с учетом самостоятельного функционирования каждой части. При этом учитывают возможность быстрого восстановления трудоспособности и замену неправильно функционирующей части механизма или системы.
Рисунок 3.1 - Упрощенная схема маршрутной технологии диагностирования машины (12 п – обязательные диагностические операции;
абв – диагностические операции по потребности)
1 Оснащение постов диагностирования
Создание специальных зон диагностирования строительно-дорожных машин на ремонтно-эксплуатационной базе зависит от производственной программы технического обслуживания строительно-дорожных машин выполняемой в стационарных условиях базы. Объем диагностических работ зависит от состава парка. Строительно-дорожные машины на базе автомобилей проходят все виды технического обслуживания на эксплуатационной базе. К этим машинам относят автомобильные краны автогудронаторы автовышки буровые установки и другие машины. Для большинства строительных машин (как с гусеничным ходом так и с пневмоколесным) техническое обслуживание с периодичностью 60 и 240 часов выполняют на строительных объектах и только работы по ремонту сезонному обслуживанию с периодичностью 970 часов выполняют на ремонтно-строительной базе. При определении программ ремонтно-эксплуатационнных баз учитывают что 40 50% текущего ремонта и 60 70% технического обслуживания машин выполняют на строительных объектах.
Число технических воздействий зависит от назначения каждого типа машины от интенсивности ее годового использования от числа строительно-дорожных машин и автотранспорта периодичности и продолжительности соответствующих технических воздействий. В результате уточняют необходимое число технических воздействий в течение года в период наиболее интенсивного использования машины и ежедневную программу и наиболее загруженный период работы базы.
2 Оснащение передвижных средств диагностирования
На строительных объектах при помощи передвижных средств выполняют работы по плановым техническим обслуживаниям. Крупные ремонты машин и сборочных
Единиц выполняют только в стационарных условиях (в том числе во временных стационарных мастерских).
Эффективность технического обеспечения машин на строительных объектах зависит как от характера распределения работ между различными типами мастерских так и оснащения передвижных средств технического обслуживания и ремонта. Причем большое влияние на производительность оказывают внешние условия работы ремонтного персонала а именно: оснащенность рабочего места температура окружающей Среды подготовленность площадки к проведению технических воздействий защищенность площадки от осадков. Особенностью передвижных средств технического обслуживания является то что наряду с технологическим оборудованием для обеспечения условий труда ремонтных рабочих под открытым небом.
Все необходимое технологическое и вспомогательное оборудование должно располагаться на транспортном средстве при этом учитывают время на приведение технологического оборудования в рабочее положение возможность выполнения некоторых работ в кузове транспортного средства и удобство размещения оборудования в транспортном положении. Укомплектование передвижных средств
Полным комплектом технологического оборудования во многих случаях нерационально так как значительно увеличивает простои оборудования не только из-за времени перемещения передвижного средства к объекту технического воздействия но и из-за необходимости развертывания оборудования перед выполнением операций технического воздействия и свертывания после проведенной операции.
В настоящее время получили распространение передвижные технические средства как для выполнения всего комплекса работ по техническому обслуживанию и частичному ремонту в основном агрегатно-узловым методом так и средства специализированные для выполнения отдельных видов работ и определенных типов строительных машин с гидро- и электроприводом.
Диагностическими приборами оснащают большинство видов передвижных средств при этом комплекты диагностических приборов различны. Наиболее полно оснащены специальные диагностические установки предназначенные для проведения работ по выявлению технического состояния строительных машин перед выполнением операций технического обслуживания. Передвижные средства в основном комплектуют переносными приборами и частично стендами для проверки гидравлического оборудования электрооборудования и двигателя устанавливаемые в кузове машины и имеющие выводы для подключения к соответствующим точкам диагностируемой машины. В основном диагностические приборы подбирают с целью установления необходимости проведения регулировочных и ремонтных работ выявления неисправных сборочных единиц в различных системах строительно-дорожных машин и контроля качества проведенных технических воздействий.
Число соответствующих технических воздействий при которых выполняются диагностические работы определяются таким же образом как и для стационарных постов. Обязательно учитываются не только время на обслуживание tоб но и время на продвижение на развертывание и свертывание технологического оборудования а именно:
tсм = 2tпер +tраз +tсв+ntоб час (2.1)
где tсм – сменное время работы машины;
tпер – время передвижения мастерской от ремонтно-эксплуатационной базы до района эксплуатации техники;
tсв tсв – соответственно время на развертывание и свертывание технологического оборудования передвижных средств;
tоб – время технического обслуживания (диагностирования) одной обслуживаемой машины;
n - число обслуживаний в течение смены (в основном в районе одного развертывания).
Время передвижения зависит от расстояния до машины требующей технического воздействия от условий движения состояния транспортной сети и следовательно от возможной скорости передвижения мобильных средств обслуживания. Время развертывания оборудования и время на выполнение единичного технического обслуживания величины постоянные для каждого вида передвижного средства. Время передвижения зависит от степени концентрации работы и передвижного состава.
При определении необходимого числа передвижных средств понимают что от всего времени обслуживания машин до 50% времени работы приходится на передвижение и не более 10% - на развертывание и свертывание (не более 5% - при проведении нескольких технических воздействий на одной стоянке).
С учетом трудоемкости работ по техническому обслуживанию и ремонту выполняемых на строительных объектах (ТО) можно определить среднее число передвижных средств по формуле:
где Тr- годовой фонд времени передвижного средства (исключая время необходимое на техническое обслуживание базового автомобиля и на проверку диагностического оборудования);
Хn - число передвижных средств.
В настоящее время расчет передвижных средств осуществляется с учетом нагрузки передвижных постов и простоев машин в ожидании технического воздействия используя положения теории массового обслуживания. Выявляют минимум затрат связанных с простоем передвижного средства в ожидании работ и простоем машин в очереди. Число передвижных средств определяют по формулам применяемым для расчета стационарных постов но при этом учитывая снижение производительности в связи с необходимостью перебазировки и свертыванием технологического оборудования.
Для каждого вида технического воздействия соответственно рассчитывают оптимальное количество передвижных средств в том числе для диагностических работ. Если количество передвижных средств менее оптимального для определенного парка машин затраты увеличиваются в связи с увеличением времени простоя машин в ожидании технического воздействия а при повышении количества передвижных средств по сравнению с оптимальными – резко возрастают затраты из-за их неполной загрузки.
3 Машина для технического диагностирования
Для проведения диагностирования машин непосредственно на месте их эксплуатации в настоящее время применяется разработанная в ГОСНИТИ мобильная установка (станция) КИ-4270 (рисунок 3.1) предназначенная для диагностирования технического состояния гусеничных машин при проведении технического обслуживания. Она базируется на машине Газель.
В кузове Газели смонтированы стеллаж верстак стол отсеки контейнеры с приборами приспособлениями и инструментом компрессор и электрооборудование.
Продолжительность диагностирования основных узлов без регулировки - 2 ч. с регулировкой - 6 ч. Установку обслуживают два человека. Питается она от сети переменного тока 220 В. Количество машин обслуживаемых установкой в год - 150-200. Наибольшее число определяемых основных параметров - 60. Наибольшая скорость передвижения по грунтовым дорогам – 50 кмч. Одна диагностическая установка подобного типа может обслужить в течение года 100 машин.
В комплект машины для технического диагностирования на базе УАЗ-452 входят:
- измеритель натяжения гусениц КИ -13903;
- индикатор расхода газов КИ - 4887-11;
- вакуум-анализатор КИ - 5315;
- устройство для измерения зазоров кривошипно-шатунном механизме КИ -11140;
- устройство для проверки прецизионных пар топливных насосов КИ -4802;
- устройство для проверки давления в системе топливоподачи КИ -4801;
- топливомер КИ – 4818;
- динамометр ДПУ – 002-2;
- люфтометр тракторный КИ - 4813;
- приспособление для проверки зазоров в подшипниках КИ – 4850;
- устройство для определения износа гусеничной цепи КИ - 4943;
-линейка для проверки схождения колес КИ – 650;
- устройство для определения технического состояния гидросистемы -
- прибор для проверки схождения колес КИ - 650;
- прибор для проверки автотракторного оборудования КИ - 1093;
- прибор для проверки контрольно-измерительных приборов Э – 204;
- компрессорно-вакуумная установка КИ - 4942;
- прибор для измерения втулочно-роликовых цепей КИ - 1854;
- нефтеденсиметр Б-2 и Б-3;
При диагностировании в полевых условиях хорошие результаты может показать смонтированный в чемодане и имеющий массу в 195 кг комплект диагностирующей аппаратуры КИ – 13901. Комплект КИ - 13901 предназначен для определения технического состояния машин всех марок без их разработки при техническом обслуживании как в полевых условиях так и на пунктах технического обслуживания. Переносной комплект 34 включает более 20 наименований контрольно-диагностических приборов приспособлений и инструмента размещенных в одном чемодане. Техническое состояние машин определяется в соответствие с принятой технологией диагностирования машин. Переносной комплект приборов целесообразно использовать в хозяйстве с парком 10 машин и более.
Кроме контрольно-диагностического оборудования передвижные диагностические мастерские укомплектованы компрессорно-вакуумной установкой верстаком со слесарным инструментом рабочим столом и комплектом электрооборудования для подключения к внешней сети и питанием соответствующих диагностических средств.
Целесообразно добавить к стандартному комплекту диагностического оборудования КИ -4270 стенд включающий в себя смазки типа НО 818 (с дополнениями) и силоизмерительный электротензометрический датчик.
Станция смазки типа НО 818 предназначена для централизованной смазки узлов.
При относительно небольших габаритах (355х250х495) и массе (40 килограмм) станция смазки позволяет за короткий промежуток времени большое количество смазочных точек и тем самым заменить такие ручные приспособления как солидолонагнетатели шприцы и т.п. ЕЕ номинальная производительность составляет 33 литра в минуту при давлении нагнетания в системе 1 Мпа. Подача смазки – 04 - 06 см3 за цикл.
Станция смазки типа НО 818 состоит из гидробака емкостью 10 дм3 насосной установки (насос типа БГ 12-41Б и электродвигатель 4АА63В4У603 мощностью 037 кВт) предохранительного клапана.
Силоизмерительные датчики являются приборами электротензометрических устройств общего назначения. Они предназначены для измерения и дозирования веса а также измерения и регулирования статических или изменяющихся усилий.
Различают силоизмерительные датчики следующих типов и модификаций:
- У – универсальные ( на сжатие и растяжение) с кабелем;
- С – на сжатие с кабелем;
- Р – на растяжение с кабелем;
- УА – универсальные с разъемом;
- СА – на сжатие с разъемом;
- РА – на растяжение с разъемом.
На стенде дополняющем диагностическую установку используем датчик У-10. Его характеристики: габаритные размеры -196х160х209 вес – 16 килограммов. Технические данные: основная погрешность – 10% от предельной нагрузки (10тс) относительная чувствительность от номинальной – в 02 тс- 2*103 отклонение относительной чувствительности от номинальной – в пределах основной погрешности допустимой разброс чувствительности – 05%.
Датчик У-10 удобен при измерении усилия на рабочем органе машины без его разборки а также более мелких узлов – штоков гидроцилиндров автогрейдеров бульдозеров экскаваторов и т.п. Сборочный чертеж стенда изображен в графической части дипломного проекта.
Устройство приспособления для разборки и сборки рессор
Предназначен для зажима рессор при разборки рессор. Состоит из рукоять червяка гайки корпуса зажим опорной пластины отверстий под крепежные болты.
При разборке сборке предварительно снятую рессору зажимают в приспособлении и ослабляют хомутики не вынимая рессоры из приспособления. Снимают стремянки и болт держащие съемное ушко.
Далее разжимаем приспособление и снимаем по очереди листы рессор и выполняем проверку изогнутости.
Техническая характеристика приспособления для разборки сборки рессор
При установке рессоры на приспособление рессора затягивается на ручную силу так чтобы рессора не выворачивалась этому помогает опорная пластина которая не дает рессоре вывернутся.
Опорная или предохранительная пластина регулируется по высоте рессоры. Имеется зажимное устройство которое имеет форму двутавра что помогает обеспечить твердое зажатие рессоры в приспособлении.
Основные виды разрушения резьб: крепежных – срез витков. В соответствии с этим основными критериями работоспособности и расчета для резьб является прочность связанная с напряжениями среза (рис 2.1).
Определить напряжении среза в резьбе.
Используя таблицы стандартов находим необходимые для расчетов размеры (таб. 2.2)
Внутренний диаметр d1
Условие прочности резьбы по напряжениям среза:
= F·d1·H·K·Km=[] [1]
где H-высота гайки или глубина завинчивания винта в деталь H=29 мм
d1- внутренний диаметр резьбыd1=31670 мм
K- коэффициент полноты резьбыK087
Km- коэффициент неравномерности нагрузки по виткам резьбыKm=07
[]- допускаемое напряжение среза[]=06T
=980314·31670·29·087·07=65МПа
=[] т.е. 65МПа =2352МПа условие выполняется.
Безопасность жизнедеятельности
1 Основные меры безопасности проектируемого предприятия
Основные требования безопасности к генеральным планам.
Перед разработкой генерального плана уточняем перечень основных зданий и сооружений размещаемых на территорий предприятия площади для застройки и габаритные размеры в плане . Определяем потребные площади для хранения строительных машин складирования ремонтного фонда и других материалов хранение которых допускается вне помещений.
Здания и сооружения располагаем относительно преобладающего направления ветров с учетом обеспечения наиболее благоприятных условий естественного освещения проветривания и предотвращения снежных заносов. Здания и помещения с производственными процессами выделяющими в атмосферу газ дым пыль а так же взрывопожароопасные вещества располагаем по отношению к другим с подветренной стороны .Разрывы между зданиями и сооружениями принимаем минимально необходимыми для устройства дорог тротуаров прокладок инженерных сетей но не менее расстояний обуславливаемых санитарными и противопожарными требованиями.
Расстояния обусловленные противопожарными требованиями зависят от степени огнестойкости зданий и сооружений.
Для движения транспорта предусматриваем дороги. Проезды с двусторонним движением предусматриваются с шириной проезжей части -6 м с односторонним движением -3 м .Ширину тротуара принимаем кратной полосе движения шириной 075 м .но менее 10 м.
Минимальные расстояния от наружной степени здания до края проезжей части дороги при отсутствии въезда в здание и его длине более 20 м принимаем не менее 3 м ; при въезде в здание погрузчиков электротележек двухосных автомобилей – 8 м; трехосных – 12м .К зданиям и сооружениям по всей длине их должен быть обеспечен подъезд пожарных автомобилей: при ширине здания до 18 м – с одной стороны при ширине более 18 м – с двух сторон. при ширине более 100 м – со всех сторон.
1 Общая характеристика опасных и вредных производственных факторов в зоне ТО
Таблица 4.1 – Общая характеристика опасных и вредных производственных факторов.
Опасные и вредные производственные факторы
Источники места причины возникновения
Основные средства защиты
Движущиеся машины и механизмы.
Минимальная скорость предупреждение людей.
Подающие машины механизмы инструмент.
Поднятая на подъемник машина. Снятые агрегаты и детали.
Установка опор под колеса установка козелков. Установка предупредительных знаков.
Инструмент хранить в специальных ящиках.
Электрический ток опасной величины.
Системное освещение оборудованное электроприводом.
Заземление. Изоляция. Напряжение для переносных ламп 12 - 36 В.
Повышенная загазованность и запыленность.
Самоходные строительные машины в зоне ТО.
Установка проточно-вытяжной вентиляции и местных отсосов.
Строительные машины в зоне ТО.
Индивидуальные средства зашиты органов слуха.
Недостаточное освещение рабочей зоны.
Оконные проемы только с одной стороны.
Верхний фонарь для естественного освящения. Переносные лампы.
Падение людей на поверхности.
Ребристость поверхностей решетки.
Разогретые части двигателя.
Выпускной коллектор глушитель
Недостаточное освещение
Искусственное освещение
Пониженная температура в рабочей зоне.
Холодное время года.
Отопление воздушно-тепловые завесы.
Повышенная температура в рабочей зоне.
3 Электробезопасность
ГОСТ 12.1.019 -79 ГОСТ 121030 - 81.
Производственный корпус современного предприятия имеет большую энерговооруженность поэтому выполнение правил электробезопасности находятся под постоянным контролем ИТР и общественных организаций.
Основными средствами обеспечивающими электробезопасность при прикосновении к токоведущим частям электроустановок которые могут оказаться под напряжением из - за повреждения изоляции являются защитное заземление и зануление выравнивание потенциалов защитное отключение применение малого напряжения ограждения блокировки изоляции токоведущих частей.
Большое значение в исходе поражения электрическим током человека имеет путь его прохождения и состояние человека и его организма. Поражение будет наиболее тяжелым если ток пройдет через сердце грудную клетку головной или спинной мозг. Наиболее опасными путями прохождения электрического напряжения через тело человека является рука и нога человека[37].
Для предупреждения работающих о безопасности поражения электрическим током Государственным стандартом системы безопасности труда (ГОСТ 12.4.027-79) установлен знак электрического напряжения (рисунок 5.3). Знак наносится на электрооборудование электрические изделия и устройства а также используется в качестве символа. Цвет знака должен быть красным или черным. Он должен наноситься или устанавливаться на контрастном фоне и находится в поле зрения работающих для которых он предназначен.
Для предохранения от поражения электрическим током при прикосновении к металлическим частям электроустановки которые не находятся под напряжением но могут оказаться под ним применяется заземление и зануление
Заземлению подлежат металлические части оборудования корпуса распределительных щитов и силовых шкафов пусковых аппаратов электродвигателей трансформаторов и другие металлические части которые могут оказаться под напряжением в результате повреждения изоляции.
Присоединение заземляющих проводников к заземлителям выполняется сваркой а к раме стенда - при помощи болтового соединения. Концы заземляющих гибких проводников применяемых для присоединения к рамам должны иметь наконечники.
Надежность заземления и зануления периодически проверяют. Для этого его осматривают проверяют наличие цепи между заземлителем и заземленными элементами установки измеряют сопротивление заземляющего устройства. Под один заземляющий болт разрешается присоединять только один проводник.
Профилактические испытания электроустановок являются одним из мероприятий обеспечивающих электробезопасность работающих а также надежность и бесперебойность работы смесителя. При профилактических испытаниях выявляют дефекты что позволяет предотвращать неисправность и несчастные случаи во время эксплуатации.
Электрооборудование осматривают электромонтажники электрослесари с квалифицированной группой не ниже третьей. Осмотры чистка смазка регулировка и ремонт электрооборудования выполняют при отключенном двигателе. При этом выполняют дополнительные меры препятствующие ошибочной подаче напряжения (запирают пусковые устройства вынимают предохранители применяют изолирующие накладки) или отсоединяют концы питающего кабеля на пункте его подключения. На пусковых устройствах при помощи которых может быть подано напряжение – вывешивают знак безопасности рисунок 5.3 с надписью «Не включать – работают люди».
При неисправностях электрооборудования заземления зануления защитных средств и питающего резинового кабеля или шлангового провода не разрешается. В случае внезапного исчезновения напряжения пусковые устройства (рубильник) выключают. Необходимо помнить что напряжение может быть подано вновь без предупреждения. Поэтому при исчезновении напряжения запрещается приступать к каким-либо работам по осмотру или ремонту касаться токоведущих частей не отключив машину от источника электропитания и не приняв дополнительных мер электробезопасности. Менять и чистить пусковую или защитную аппаратуру следует при обязательном отключении от источника электропитания. О всех замеченных неполадках в работе электрооборудования необходимо сообщить электромонтеру (электрослесарю механику).
Аварийное отключение производится при:
-несчастном случае (или угрозе его) когда требуется немедленная остановка электродвигателя;
-появление дыма или огня из электродвигателя или пускорегулирующей аппаратуры;
-вибрации и стуков сверх допустимых норм;
-поломке приводного механизма или машины;
-нагреве подшипников сверх допустимых температур;
-значительное снижение частоты вращения двигателя сопровождающееся быстрым нагревом.
Запрещается использовать для дополнительной подсветки обычных ламп без корпуса рукоятки выполненной из огнестойких и влагостойких изолирующих материалов и защитной металлической в виде сетки и неисправных светильников.
Расчет зануления стенда
Электрический ток при несоблюдении правил и мер предосторожности может оказывать на людей опасное и вредное воздействие проявляющееся в виде электротравм электроударов и професииональных заболеваний.
Опасность поражения электрическим током специфична поскольку наличие напряжения не может быть обнаружено на расстоянии без специальных приборов. Органы чувств человека позволяют обнаружить его только при контакте с электроустановкой находящейся под напряжением в момент поражения. Поэтому защите от поражения электрическим током следует уделять особое внимание[28].
При эксплуатации стенда по диагностики насосов существует опасность поражения электрическим током в следствии неисправности электродвигателя трансформатора систем управления неправильного подключения установки к сети неисправности электропроводки и неправильной эксплуатации неудовлетворительное ограждение токоведущих частей установки от случайного прикосновения выполнение работ под напряжением без соблюдения необходимых мер безопасности и без защитных средств неудовлетворительное зануление несоответствие использования оборудования кабелей и проводов условиям их эксплуатации.
Для защиты от поражения электрическим током при прикосновении к металлическим нетоковедущим частям которые могут оказаться под напряжением в результате повреждения изоляции пробоя на корпус применяем зунуление.
Рассчитаем зануление электродвигателя серии 4А200L4У3 мощностью 45 кВт номинальным напряжением 380 В частотой вращения 1500 обмин.
Расчет сводится к определению отключающей способности защиты[17].
Условие обеспечивающее отключающую способность зануления
где Iкз – ток короткого замыкания А;
Iнпл вст – номинальный ток плавкой вставки А;
UФ – фазное напряжение сети В; UФ = 380 В;
ZT – сопротивление трансформатора Ом; при трансформаторе мощностью 160 кВ×А – ZT = 0.162 Ом;
ZП – сопротивление петли фаза – нуль Ом.
Сопротивление петли фаза – нуль Ом
где RФ и RН – активные сопротивления соответствено проводников фазового и нулевого жил кабеля Ом.
Активные сопротивления фазового и нулевого жил кабеля Ом
где g – удельное сопротивление материала Ом×мм2м; для алюминиевого кабеля g = 0.028 Ом×мм2м;
s – сечение проводника мм2.
Для определения сечения жил проводников нужно расчитать номинальный ток вставки.
Номинальный ток электродвигателя А
где Р – номинальная мощность электродвигателя кВт; Р = 4 кВт;
UH – номинальное напряжение В; UН = 380 В;
cos a - коэффициент мощности; cos a = 0.89 [27 с.89].
Пусковой ток двигателя найдем из отношения отсюда
Номинальный ток плавкой вставки А
где z - коэффициент режима работы; z = 2 [27 с.89].
По расчетному току номинальной вставки выбираем предохранитель (с током плавкой вставки не менее расчетного) – тип НПН60М с Iнпл вст = 25 А следовательно сечение проводника s = 2.5 мм2 [27].
Далее определяем активные сопротивления фазового и нулевого жил кабеля Ом (4.3)
Сопротивление петли фаза – нуль Ом (4.2)
Проверим условие (4.1)
Условие выполнено поэтому при замыкании на корпус произойдет отключение электродвигателя (или поврежденную фазу).
4 Техника безопасности при диагностировании строительно- дорожных машин
Общие требования безопасности.
К эксплуатации и обслуживанию на стенде допускаются лица хорошо знающие устройство не моложе 18 лет прошедшие медицинский осмотр имеющие соответствующую квалификацию сдавшие экзамены по правилам безопасной эксплуатации и обслуживания стенда по технике безопасности и охране труда.
По поступлении на работу провести вводный инструктаж в ходе которого разъясняют:
- основные положения по охране труда;
- правила внутреннего трудового распорядка на предприятии правила поведения схемы движения пешеходов и транспортных средств на предприятии значение надписей знаков цветов сигналов безопасности;
- порядок пользования бытовыми помещениями и устройствами;
- особенности условий работы соответствующей установки и меры по предупреждению несчастных случаев;
- требования по соблюдению личной гигиены и производственной санитарии на предприятии;
- действие работающих при авариях и несчастных случаях;
- порядок содержания и пользования средствами защиты;
- требования электро и пожаробезопасности;
- правила оказания доврачебной медицинской помощи.
Проводить первичные повторные и внеплановые инструктажи по технике безопасности и пожарной безопасности на рабочем месте.
- в закрытом помещении с температурой воздуха не ниже 10 градусов при влажности 40 60% и достаточно освещенном. При работе в холодное время в помещении или на открытом воздухе предусмотреть помещения с температурой воздуха 21-22 градуса и на рабочем месте обеспечить местный обогрев;
- в помещении с высотой от пола рабочего места до потолка или перекрытия – не менее 2 метров;
- соблюдая расстояние не менее 1 метра между стендом и выступающими частями для обеспечения проходов ежедневного осмотра и проведения технического обслуживания.
Закрепить установку исключая возможность самопроизвольного перемещения при воздействиях сил тяжести и внешних нагрузок.
Требования безопасности до начала работы.
Ознакомиться с записями предыдущей смены в журнале приема и сдачи смены.
Навести чистоту и порядок на рабочем месте.
Перед осмотром чисткой смазкой и устранением неисправностей обесточить электродвигатель вынуть предохранители ящик пускового устройства закрыть на замок и вывесить запрещающий знак безопасности с надписью: «Не включать! Работают люди»
Проверить состояние устройств стенда их готовность к работе;
Проверить отсутствие посторонних предметов на узлах агрегатов;
Проверить состояние болтовых и сварных соединений.
Проверить состояние системы управления пускового устройства и зануления отсутствие повреждений изоляции.
Проверить состояние и правильность установки и крепление амортизирующих устройств.
Проверить зазоры между движущимися частями .
Проверить исправность наличие и надежность креплений оградительных устройств.
Требования безопасности в процессе работы
При эксплуатации испытательного стенда необходимо выполнять следующие требования:
)Работать со стендом могут только рабочие хорошо изучившие конструкцию принцип работы и правила эксплуатации
)При испытании гидроцилиндров не превышать допустимое давление стенда
)Стенд должен быть заземлен рабочее оборудование должно закрыть защитным кожухом
)Воздух к электродвигателю должен поступать свободно
)Испытываемый цилиндр должен быть закреплен хомутом пальцы крепления должны быть зафиксированы
)При испытании запрещается стоять непосредственно рядом с испытываемым цилиндром.
)При пробном пуске и работе гидропривода запрещается находиться возле трубопровода с высоким давлением
)Использовать посторонние предметы для крепления запрещено
)При посторонних звуках во время работы стенда немедленно отключить стенд
)Использовать только то масло которое предусмотрено инструкцией по эксплуатации.
1 Расчет капитальных вложений
Объем капитальных вложений складывается из суммы затрат на основные производственные фонды и всех затрат на строительство проектируемого объекта.
Расчет основных производственных фондов.
Основные производственные фонды включают стоимость зданий и сооружений производственного и вспомогательного оборудования инструмента приспособлений и стоимости инвентаря.
В стоимость зданий и сооружений включают все затраты на их строительство в том числе затраты на подготовку площадки санитарно-технические устройства фундаменты для установки оборудования.
При укрупненных расчетах стоимость зданий определяем по удельному показателю затрат на 1 м² здания принимаем на основании нормативов.
где Сзд - общая сумма на строительство здания;
Fзд - площадь здания Fзд = 870 м²;
Суд - стоимость 1 м² общего строительства по данным предприятия стоимость 1 м² здания принимаем Суд = 21`861 руб. за 1м².
Сзд = 870·21`861 = 19`019`070 руб.
Расчет стоимости оборудования включает стоимость всех видов производственного и вспомогательного оборудования: металлорежущего ремонтно-технологического энергетического подъемного транспортного а так же инструмента приспособлений и инвентаря. Кроме того в стоимость оборудования входят затраты на его транспортирование и монтаж. При укрупненных расчетах стоимость оборудования принимаем по установленному проектному отношению для предприятия она составляет 50% от общей стоимости здания:
Соб = 19`019`070·05 = 9`509`535 руб.
Данные по капитальным вложениям на строительство проектируемого объекта по ТО и ремонту сводим в таблицу
Наименование сооружений и зданий
Стоимость основных фондов
Производственный корпус
Итого: 28.528.605 руб.
2 Смета затрат на производство ТО и Р эксплуатируемой техники
Смета затрат один из главных показателей планируемого предприятия.
Смета затрат включает в себя всю сумму затрат или издержки производства (запасные части или материал заработная плата производственных рабочих накладные и другие расходы).
Расчет заработной платы основных производственных и вспомогательных рабочих.
Для расчета заработной платы основных производственных рабочих необходимо распределить рабочих по разрядам.
Производственные рабочие
Вспомогательные рабочие
Часовая тарифная ставка по данным существующего предприятия для рабочих по ТО и ремонту:
l-ый разряд - 1777 руб. 4-ый разряд – 2455руб.
-ой разряд - 2052 руб. 5-ый разряд – 2544 руб.
-ий разряд – 2368 руб. 6-ой разряд – 3536 руб.
Средняя часовая тарифная ставка будет ровна:
Расчет основной заработной платы на год:
Зосн. =12· Тст · t · m
где Тст. - часовая тарифная ставка
m - количество человек
t - количество рабочих часов в месяц
Зосн.= 12 · 253 · 166 · 17 = 856`759 руб.
Расчет дополнительной заработной платы
Дополнительная заработная плата принята 30% от основной
Здоп.=856759·03=257`028 руб.
Расчет районного и северного коэфициента
Зрк.ск. = (Зосн. + З доп.) · 05
Зрк.ск. = (856`759 + 257`028) · 05 = 556`894 руб.
Расчет премии Премиальная надбавка принята 50%
Зпр. = (Зосн. + З доп.) · 05
Зпр. = (856`759 + 257`028) · 05 = 556`894 руб.
Отчисления в социальные фонды
Зс.ф.=0271·(Зосн. + Здоп. + Зрк.ск. + Зпр.)
Зс.ф.=0271·(856`759 + 257`028 + 556`894 + 556`894) = 603`673 руб.
Общий фонд заработной платы рабочих за год:
Фз.п.=Зосн. + Здоп. + Зрк.ск. + Зпр. + Зс.ф.
Фз.п.=856`759 + 257`028 + 556`894 + 556`894 + 603`673=2`831`248
Затраты на материалы и запасные части при ТО и ремонте.
Затраты на материалы и запасные части определяем по формуле:
где Нм – Стоимость материалов и запасных частей на 1 час работы принимаем по данным предприятия;
Тпл - плановая наработка машины;
Ас - списочное количество машин.
Стоимость материалов и зч. на один машино-час руб.
Для автогрейдера ДЗ-122 М = 4778 · 1464 · 2 = 139`900 руб.
Для автогрейдера ДЗ-98 М = 4383 · 1464 · 2 = 128`334 руб.
Для автогрейдера ДЗ-143 М = 4778 · 1464 · 1 = 69`950 руб.
Для бульдозера Т-170 М = 5213 · 1660 · 9 = 778`822 руб.
Для экскаватора ЭО-4121 М = 534 · 1660 · 1 = 88`644 руб.
Для экскаватора ЭО-4321 М = 534 · 1660 · 1 = 88`644 руб.
Для экскаватора ЭО-2621 М = 3634 · 1660 · 3 = 180`973 руб.
Для экскаватора ЭО-5124 М = 5572 · 1660 · 6 = 554`971 руб
ЭО – 5122 ЭО - 5126
Для погрузчика М = 4135 · 1660 · 1 = 68`641 руб.
Для катка ДУ – 48 ДУ-47ДУ-37 М = 3486 · 1366 · 3 =428`569 руб.
Для катка ДУ – 65 М = 3845 · 1366 · 1 =95`238 руб.
Для автокрана КС – 3571 М = 4675 · 1757 · 1 = 82`140 руб.
Для автокрана КС – 4561 М = 5082 · 1757 · 1 = 89`291 руб.
Для ЧМЗАП М = 289 · 1757 · 2 = 101`555 руб.
Итого: Затраты на материалы и запасные части Σ = 2`895`672
Определение накладных расходов.
Накладные расходы включают в себя расходы связанные с организацией производственной деятельности т.е. такие которые не могут быть отнесены к расходам на ремонтные нужды. Определение фонда заработной платы ИТР и СКП. Данные по окладам и премиальные принимаем по данному предприятию.
Годовой фонд заработной платы ИТР и СКП определяется по формуле:
Фзп = (Мокл ·В+Мокл ·Nпр) · В
где Мокл - месячный оклад ИТР СКП
В - районный коэффициент
Nпр. - премиальный коэффициент
В - кол-во месяцев в году (В=12)
Фзп. = (11000 · 15 + 11000 ·05) · 12 = 264`000 руб.
Фзп. = (10000 · 15 + 10000 ·05) · 12 = 240`000 руб.
Фзп. = (7000 · 15 + 7000 ·05) · 12 = 168`000 руб.
Отчисления в социальный фонд принимаем 271%
Зсф = 840`000 · 0271 = 218`400 руб.
Расходы на содержание и ремонт оборудования.
Принимаем по данным предприятия 8% от стоимости оборудования.
Роб = 9`509`535 · 008 = 760`763 руб.
Расходы на содержание и текущий ремонт производственных помещений.
Принимаем по данным предприятия 3% от общей стоимости здания.
Общая стоимость здания по данным предприятия Сзд.об. = 19`019`070 руб.
Р пл. = 19`019`070 · 003 = 570`572 руб.
Амортизация оборудования.
Принимаем 18% от общей суммы стоимости оборудования.
Рам.об = 9`509`535 · 018 = 1`711`716 руб.
Принимаем 35% от общей стоимости здания.
Рам.зд. = 19`019`070 · 0035 = 665`668 руб.
Износ и содержание малоценного инвентаря.
Износ и содержание малоценного инвентаря принимаем 150 руб. на одного производственного рабочего.
Ринв. = 150 · 17 = 2550 руб.
Расходы на охрану труда принимаем по данным предприятия 3% от годового фонда заработной платы основных производственных рабочих.
Рот. = 2`831`248·003 = 84`937 руб.
Затраты на рационализаторскую и изобретательскую деятельность.
Принимаем по данным предприятия 100 руб. на одного производственного рабочего.
Ррац. = 100·17 = 1700 руб.
Расходы на электроэнергию.
Расходы на электроэнергию при укрупненных расходах принимаем 4000 кВт на одного производственного рабочего. Стоимость 1 кВт=045 руб.
Рэл. = 4000 · 17 · 045 = 30600 руб.
Прочие расходы принимаем 3% от суммы затрат по перечисленным выше статьям.
Рпр. = (840`000 + 218`400 + 760`763 + 570`572 + 1`711`716 + 665`668 + 2550 + 84`937 + 1700 + 30`600) · 003 = 146`607 руб.
Таблица 5.5 - Смета цеховых расходов
Заработная плата ИТР СКП
Отчисления в социальный фонд
Расходы на содержание и ремонт оборудования
Расходы на содержание и ремонт производственных помещений
Расходы на амортизацию оборудования
Расходы на амортизацию здания
Расходы на износ и содержание малоценного инвентаря
Отчисления на охрану труда
Затраты на рационализаторскуюдеятельность
Затраты на электроэнергию
Таблица 5.5 - Расходы на ТО и ремонт.
Затраты на материалы и зап. части
Фонд заработной платы
Определение себестоимости одного часа работ на проведение ТО и ремонта.
где ΣР - Расходы на ТО и ремонт.
Σ Т - Суммарная трудоемкость на проведение ТО и Р Σ Тт = 11389ччас
Sед.= 10`760`43311389 = 945 руб.час.
Определение цены одного часа работ на проведение ТО и ремонта.
Прибыль на один час проведения работ по ТО и ремонту.
ΔS = 1182 – 945=237 рубчас.
Прибыль предприятия на проведение ТО и ремонта в год.
S = 237 · 11389 = 2`699`193 руб.
Окупаемость затрат на ТО и ремонт.
Токуп.= 19`019`070 2`669`193= 66 года.
Таблица 5.6 - Технико-экономические показатели
Капитальные вложения
Список используемой литературы
Анурьев В.И. справочник конструктора машиностроения: Т.1. – М.: Машиностроение 1982. – 729 с.
Башта Т.М. Руднев С.С. Некрасов Б.Б. Гидравлика гидромашины и
гидропровода. – М.: Машиностроения 1982. – 424 с.
Башта Т.М. Гидропровод и гидропневмоавтоматика. – М.: Машиностроение 1972. – 320 с.
Безопасность жизнедеятельности в условиях производства: Методические указания к дипломному проектированию Сост. Ю.В. Шешуков. – Иркутск 1992. – 36 с.
Беспалов Н.А. Дорожно-строительные машины и оборудования: Справочник. – К.: Будивельник 1980. – 177 с.
Гурвич И.С. Эксплуатация и ремонт дорожно-строительных машин. – М.: Транспорт 1989. – 236 с.
Дунаев П.Ф. Конструирование узлов и деталей машин. – М.: Высшая школа. 1985. – 416 с.
Зеленков Г.И. Технология ремонта дорожных машин и основы роектирования ремонтных предприятий. – М.: Высшая школа 1972. – 495 с.
Иванов М.И. Детали машин. – М.: Высшая школа 1991. – 496 с.
Кламанн Д. Смазки и родственные продукты. – М.: Химия 1988. – 488 с.
Косилова А.Г. Справочник технолога машиностроителя: Т.2. – М.: Высшая школа 1985. – 495 с.
Лукьяненко В.М. Таранец А.В. Промышленные центрифуги. – М.: Химия 1974. – 376 с.
Планирование годового режима работы парка машины: Методическое указание по выполнению практической работы Сост. А.И. Нижегородов О.Н. Спивак. – Иркутск 19995. – 6 с.
Чернавский А.С. Курсовое проектирование деталей машин. – М.: Машиностроение 1988. – 415 с.
Рекомендуемые чертежи
- 23.05.2021
- 02.05.2021
- 28.03.2021
- 15.01.2020
- 25.01.2023
- 04.11.2022
- 14.11.2019
Свободное скачивание на сегодня
- 24.01.2023