Мостовой кран грузоподъемностью 30/5 тонн




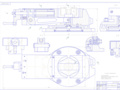
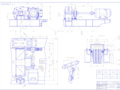
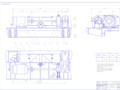
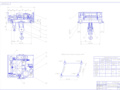
- Добавлен: 25.10.2022
- Размер: 7 MB
- Закачек: 0
Описание
Состав проекта
![]() |
![]() ![]() ![]() |
![]() ![]() |
![]() ![]() |
![]() ![]() |
![]() |
![]() ![]() ![]() ![]() |
![]() ![]() ![]() ![]() |
![]() ![]() ![]() ![]() |
![]() ![]() ![]() ![]() |
![]() ![]() ![]() ![]() |
![]() ![]() ![]() ![]() |
![]() ![]() ![]() ![]() |
![]() ![]() ![]() ![]() |
![]() ![]() ![]() ![]() |
![]() ![]() ![]() ![]() |
![]() ![]() ![]() ![]() |
![]() ![]() ![]() ![]() |
![]() ![]() ![]() ![]() |
![]() ![]() ![]() ![]() |
![]() ![]() ![]() ![]() |
![]() ![]() ![]() ![]() |
![]() ![]() ![]() ![]() |
![]() ![]() ![]() ![]() |
![]() ![]() ![]() ![]() |
![]() ![]() |
![]() ![]() |
![]() ![]() ![]() |
![]() ![]() ![]() |
![]() ![]() |
![]() ![]() |
![]() ![]() |
![]() ![]() |
![]() ![]() |
![]() ![]() ![]() |
![]() ![]() |
![]() ![]() |
![]() ![]() ![]() |
![]() ![]() ![]() |
![]() ![]() ![]() |
![]() ![]() |
![]() ![]() |
![]() ![]() |
![]() ![]() |
![]() ![]() ![]() |
![]() ![]() |
![]() ![]() |
![]() ![]() ![]() |
![]() ![]() |
![]() ![]() |
![]() ![]() |
![]() ![]() |
![]() ![]() |
![]() ![]() |
![]() ![]() ![]() |
![]() |
![]() ![]() |
![]() ![]() |
![]() ![]() |
![]() ![]() |
![]() ![]() |
![]() ![]() |
![]() ![]() |
![]() ![]() |
![]() ![]() |
![]() ![]() |
![]() ![]() |
![]() ![]() |
![]() ![]() |
![]() ![]() |
![]() ![]() |
![]() ![]() |
![]() ![]() |
![]() ![]() |
![]() ![]() ![]() |
![]() ![]() ![]() |
![]() ![]() |
![]() ![]() ![]() |
![]() ![]() ![]() |
![]() ![]() ![]() |
![]() ![]() |
![]() ![]() |
![]() ![]() |
![]() ![]() |
![]() ![]() |
![]() ![]() ![]() |
![]() ![]() ![]() |
![]() ![]() |
![]() ![]() |
![]() ![]() |
Дополнительная информация
9(2) Шлифовальная.dwg

Закрепление в быстрорежущей оправке
КФ МГТУ им. Н.Э. Баумана
12 Исследовательская часть1.dwg

- после сварки; 2 - после высокого отпуска; 3 - после нагрузки 270 МПа при N=10;
КФ МГТУ им. Н.Э. Баумана
Исследовательская часть 1
4 механизм передвижения крана.dwg

Смещение на каждой стороне крана должно быть в одну сторону.
Механизм передвижения
КФ МГТУ им. Н.Э. Баумана
7 крюковая.dwg

КФ МГТУ им. Н.Э. Баумана
3 механизм вспомогательного подъема.dwg

параллельны верхним опорным поверхностям
отклонение более 1 мм на 1000 мм
Радиальное биение рабочей поверхности
тормозного шкива после его установки
допускаетя не более 0
Механизм вспомогательного
КФ МГТУ им. Н.Э. Баумана
10 приспособление готов.dwg

Рабочий ход поршня 30 мм
Тиски пневматические
КФ МГТУ им. Н.Э. Баумана
Технические характеристики
9(3) Токарная.dwg

11 схема электрическая V9.dwg

AS2 - правая колонка пульта упр.
Стыки подтележных рельс электрически соединить. Каждый
рельс заземлить с двух концов. Металлоконструкцию
крана заземлить через подкрановые рельсы.
Вентилятор М 10 при установке изолировать от металлокон-
Электромагниты реле F
настроить на ток срабатывания
номинального тока фазы двигателя.
мостового крана гп 305 т.
КФ МГТУ им. Н.Э. Баумана
Механизм передвижения моста
Механизм передвижения тележки
2 механизм главного подъема.dwg

0 Цех №1 5.1100.dwg

Места складирования
Место сборки секций
и примерка трубопроводов
Участок для хранения
- трубогибочный станок
- стенд для пневмоиспытаний труб
- стеллаж для хранения прямых труб
- стелажи для хранения гнутых труб
- место для отрезки труб
- трубогибочный станок БМК-51
- стол для снятия фасок и заусенцев
- стол для хранения заготовок
- сверлильный станок
- токарно-винтроезный станок 1М63
- токарный станок 1К625
- фрезерный станок 6Р13
- фрезерный станок 6Т82-1
- фрезерный станок 6Т13-29
- управление прессом
- листогибочный станок
- сверлильный станок Gebr.Reinhold
- сверлильный станок 2А135
- сверлильный станок 2Н135
- станок сверлильный 2М57
- сверлильный станок 2М55
- сверлильный станок
- контейнеры для стружки
- стол для резки кромок
- подставки передвижные
- аппарат сварочный ВДМ-1201
- аппарат сварочный ВДУ-506С
- стапель для сборки СБ18
- стапель для сборки СБ17
- стапель для сборки СБ24
- станок для наматывания проволоки
- станок для вязания стальных троссов
- стеллаж для хранения строп
- рабочее место мастера
- стенд для мойки трубных досок
- емкость для жидкости
КФ МГТУ им. Н.Э. Баумана
26.dwg

Участок сборки кабин
Какие виды сварки присутствуют?
9(4) Сверлильная.dwg

Сверлильная операция
КФ МГТУ им. Н.Э. Баумана
Сверление через кондукторную плиту
8 установка барабана.dwg

13 Исследовательская часть2.dwg

- после высокого отпуска; 3
- после предварительной
=400 МПа для ВСт3сп5 и 470 МПа для стали 16Г2АФ).
Исследовательская часть 2
КФ МГТУ им. Н.Э. Баумана
Квазистатическое разрушение
Усталостное разрушение
1 Кран мостовой.общий вид.dwg

Запрещается применение кранов для работы во взрывоопасной
а также для транспортировки людей.
КФ МГТУ им. Н.Э. Баумана
Технические требования
Техническая характеристика крана
5 механизм передвижения тележки.dwg

ходовых колес к плоскости
проходящей через поверхность
рельсов или биение этой торцевой плоскости не должно
быть более 1 мм на 1000 мм.
Отклонение геометрических осей ходовых колес от общей
геометрической плоскости не более 3 мм.
мм сверлить прт установке редуктора.
Механизм передвижения
9(1) Шкив тормозной.dwg

6 тележка крановая.dwg

КФ МГТУ им. Н.Э.Баумана
Давление колес тележки на рельсы моста
Характеристика тележки
Механизм передвижения
0 Цех №26.dwg

- трубогибочный станок
- стенд для пневмоиспытаний труб
- стеллаж для хранения прямых труб
- стелажи для хранения гнутых труб
- место для отрезки труб
- трубогибочный станок БМК-51
- стол для снятия фасок и заусенцев
- стол для хранения заготовок
- сверлильный станок
- токарно-винтроезный станок 1М63
- токарный станок 1К625
- фрезерный станок 6Р13
- фрезерный станок 6Т82-1
- фрезерный станок 6Т13-29
- управление прессом
- листогибочный станок
- сверлильный станок Gebr.Reinhold
- сверлильный станок 2А135
- сверлильный станок 2Н135
- станок сверлильный 2М57
- сверлильный станок 2М55
- сверлильный станок
- контейнеры для стружки
- стол для резки кромок
- подставки передвижные
- аппарат сварочный ВДМ-1201
- аппарат сварочный ВДУ-506С
- стапель для сборки СБ18
- стапель для сборки СБ17
- стапель для сборки СБ24
- станок для наматывания проволоки
- станок для вязания стальных троссов
- стеллаж для хранения строп
- рабочее место мастера
- стенд для мойки трубных досок
- емкость для жидкости
Участок для хранения
КФ МГТУ им. Н.Э. Баумана
Участок сборки кабин
Какие виды сварки присутствуют?
Механизм главного подъема.DOC
Болт М 20*50-010 ГОСТ 7796-62
Шайба 24Н65Г ГОСТ 7796-62
Гайка М24-010 ГОСТ 5915-62
Болт М 20*50-010 ГОСТ 7796-62
Шайба 24Н65Г ГОСТ 6402-61
Сталь 65Г ГОСТ 1050-60
Гайка М 24-010 ГОСТ 5915-62
Металлоконструкция тележки
Болт М20*50-010 ГОСТ 7796-62
Болт М16-60-010 ГОСТ 7796-62
Шайба 24 Н65Г ГОСТ 6402-61
Элементы крепл. уравн. блока
Элементы крепл. уравн. блока
Механизм главного подъема
КФ МГТУ им. Н.Э. Баумана
Механизмы передвижения крана.DOC
Подставка под тормоз
Шайба 24Н65Г ГОСТ 6402-61
Гайка М16-010 ГОСТ 5915-62
Платик подошвы под тормоз
Сталь 40 ГОСТ 907-65
Механизм передвижения крана
КФ МГТУ им. Н.Э. Баумана
Кран мостовой.DOC
Кран мостовой 305 т.
КФ МГТУ им. Н.Э. Баумана
Установка барабана ф615.DOC
Cu 15-32 ГОСТ 1412-54
Сталь 45 ГОСТ 1050-60
Ст 6 Л 3 ГОСТ 977-65
Сталь 63 ГОСТ 1050-60
Выключатель универсальный
Сталь 65Г ГОСТ 1050-60
Ст 3 кп ГОСТ 501-58
Сталь 65Г ГОСТ 1050-60
Установка барабана ф615
КФ МГТУ им. Н.Э. Баумана
Тележка крановая.DOC
Площадка для установки приборов безопасности
Механизм вспомогательного подъёма
Крюковая подвеска основного подъёма
Болт М12*3558 ГОСТ 7796-70
Шайба 1265Г ГОСТ 6402-71
Сталь 65Г ГОСТ 1050-74
Гайка М125 ГОСТ 5915-70
Ст. 3 кп ГОСТ 16523-70
Барабан вспомогательного
Барабан главного подъёма
Двигатель передвижения тележки
Металлоконструкция тележки
КФ МГТУ им. Н.Э. Баумана
Механизм вспомогательного подъема.DOC
Регулировочный платик
Подставка под редуктор
Регулировочный платик
Болт М20*50-010 ГОСТ 7796-62
Шайба 16Н65Г ГОСТ 6402-61
Сталь 65Г ГОСТ 1050-60
Гайка М 16-010 ГОСТ 5915-62
Барабан вспомогательный
Уравнительный блок в сборе
Механизм вспомогательного подъема
КФ МГТУ им. Н.Э. Баумана
За1писка.doc
В связи с интенсификацией технологических процессов доля времени на подъемно-транспортные операции значительно возросла. Резкое повышение производительности труда которое крайне необходимо во время перехода экономики на новые условия развития и управления может быть достигнуто прежде всего путем механизации и автоматизации подъемно-транспортных операций которые менее автоматизированы чем технологические.
Подъемно-транспортные машины (ПТМ) весьма металлоемки разрушение элементов этих машин или другие неисправности могут привести к травмам. Поэтому необходимо создавать менее металлоемкие совершенные надежные и рациональные конструкции.
В связи со специфическими задачами механизации производственных процессов проектированием подбором и установкой ПТМ занято много инженерно-технических работников не только в специализированных организациях и предприятиях но и в самых различных отраслях промышленности.
Подъемно-транспортное оборудование является неотъемлемой частью практически любой схемы механизации любого производственного процесса в каждой отрасли экономики. Поэтому подъемно-транспортные машины представляют исключительный методический интерес как объекты проектирования при подготовке инженеров-машиностроителей широкого профиля.
Конечной целью проектирования разработки внедрения и применения подъемно-транспортных машин является ликвидация ручных погрузочно-разгрузочных работ и исключение тяжелого труда при выполнении основных и вспомогательных операций.
РАСЧЕТ МЕХАНИЗМА ГЛАВНОГО ПОДЪЕМА.
Кинематическая схема привода представлена на рис. 1. Электродвигатель 1 передает крутящий момент через предохранительную муфту 5 на быстроходный вал редуктора 2 на другом конце которого установлен тормоз 6. От тихоходного вала редуктора момент передается на барабан 3 через компенсирующую муфту 4.
Рис.1.Кинематическая схема привода механизма главного подъема.
Для выбора оптимального варианта привода для расчета главного механизма подъема будет рассмотрен многовариантный счет канатов диаметров барабанов и редукторов.
Высоты подъемаH = 12м
Скорость подъема груза
Режим нагруженияL2 (умеренный)
Продолжительность включенияПВ = 40%
Класс использования механизмовМ5.
Предварительный выбор электродвигателя.
Статическая мощность двигателя механизма подъема груза:
= - масса груза и крюковой подвески;
Масса крюковой подвески прототипа составляет 550 кг.
=20000+550=20550 кг.
- предварительный КПД механизма.
= 096 – КПД редуктора;
= 098 – КПД зубчатой муфты;
= 096 – КПД барабана.
Значение КПД взяты (2).
Исходя из режима нагрузки L2 и полученного значения мощности (>15кВт) из (6) стр. 77 выбираем электродвигатель модельного ряда двигателей с короткозамкнутым ротором. Выбираем двигатель 4МТKH225L8 со следующими характеристиками:
Температура окружающей средыне более 50С;
КПД выбранных полиспастов:
= 098 – КПД блоков входящих в полиспаст (4):
Усилие в канате набегающем на барабан:
g – ускорение свободного падения;
z – число полиспастов в системе;
а – кратность полиспастов;
- КПД полиспаста и обводных блоков.
Согласно ПУБЭГК (стр.27) допускается изменение коэффициента выбора диаметра барабана h не более чем на два шага (в обе стороны) по группе классификации с соответствующей компенсацией по средствам величины zр по таблице на тоже число шагов (в меньшую или большую сторону) (см. таблицу).
Группа классификации
Введем ряд шагов = -2; -1; 0; 1; 2 по zр.
Расчет на разрывное усилие каната:
Для мостового крана работающего в закрытом помещении выбирают канаты по ГОСТ 2688-80 канат двойной свивки типа ЛК-РО. Канат устойчив к перегибам однако чувствителен к образивному износу. Конструкция 6х36(1+7+77+14)+1о.с. Маркировочная группа проволок 1770 Мпа. Для рассматриваемых вариантов выбираем канаты:
d[] – диаметр каната из каталога (5);
- группа прочности (МПа);
[F] – разрывное усилие каната также из каталога.
Длина барабана при двусторонней нарезке:
определяется по формуле:
с – коэффициент ненарезанной части зависит от кратности полиспаста.
Для а = 4 – коэффициент с = 04; для а = 5 и с = 05.
- расчетный диаметр барабана;
Для выбранных вариантов расчетный диаметр барабана равен:
Далее округляем полученный диаметр до ближайшего большего из ряда R20. Диаметр менее 160 мм можно отбросить так как зубчатый венец редуктора не войдет внутрь барабана.
Полученные округленные значения:
Из полученных результатов отметим варианты по равенству диаметров каната и барабана:
Варианты длины барабана:
Исходя из соотношения (4):
что обеспечивает устойчивость на изгиб стенки барабана отбросим не удовлетворяющие условию варианты:
Таким образом после отброса расчет продолжаем по оставшимся вариантам (404-14-2).
Угловая скорость барабана:
Оставшиеся варианты имеют одинаковый диаметр барабана и следовательно одинаковые угловые скорости:
Передаточное число редуктора:
Для привода механизма подъема выбирается цилиндрический двухступенчатый горизонтальный специальный крановый редуктор типа Ц2.
Ближайшее к полученному передаточное число UС = 25. Условие что разница не должна превышать 10% выполняется:
Проверка редуктора по радиальной и консольной нагрузке:
Ближайший редуктор который для ПВ=40% имеет допустимую радиальную консольную нагрузку Fr=25-104 Н – это редуктор Ц2-500 что удовлетворяет условиям проверки.
Проверка редуктора по грузовому моменту:
Эквивалентный момент на тихоходном валу:
- расчетный момент на тихоходном валу редуктора;
- коэффициент долговечности.
- коэффициент переменности нагружения;
= 125*106 – базовое число циклов контактных напряжений;
- суммарное число циклов.
= 395 – передаточное число тихоходной ступени редуктора;
- число циклов нагружения на тихоходном валу редуктора.
- частота вращения тихоходного вала редуктора;
- машинное время работы механизма;
Статический момент на входном валу редуктора при торможении.
Момент статического сопротивления на валу при торможении:
- передаточное отношение между валом барабана и тормозным шкивом.
- КПД привода от вала барабана до тормозного шкива.
Тормозной момент создаваемый тормозом:
- коэффициент запаса по торможению. Согласно ПУБГЭК стр.32 для механизмов класса М5 =15.
Выбираем тормоз колодочный с электрогидравлическим толкателем ТКГ-300М с тормозным моментом 800 Нм. Диаметр тормозного шкива 300 мм. При монтаже тормоза необходимо отрегулировать на тормозной момент 402 Нм.тормоза составляет 55 кг.
Расчет соединительных муфт.
Ввиду того что у выбранного редуктора тихоходный вал зубчатый то зубчатую полумуфту изготавливаем по тихоходному зубчатому валу редуктора без дополнительных проверочных расчетов.
Расчетный момент муфты между электродвигателем и редуктором:
=13 – коэффициент учитывающий степень ответственности механизма М5 (Анурьев);
- коэффициент учитывающий режим работы L2 механизма (Анурьев).
Из конструктивных соображений устанавливаем нестандартную муфту типа МУВП используя пальцы и упругие втулки стандартной МУВП с Тк = 1000(Нм).
Компоновка механизма.
Размер соседства А1 между навивной частью барабана и корпусом электродвигателя не должен превышать 20 мм. Если А10 то вводится промежуточный вал либо принимается редуктор с большим межосевым расстоянием что однако бывает экономически невыгодно либо сильно увеличивает массу привода.
Размер соседства А2 между фланцем барабана и предохранительной муфтой рассчитывается по формуле:
- межосевое расстояние редуктора;
Z – число зубьев по каталогу;
– радиус вместе с толщиной фланца.
А2 = 500-06*8*46-05*372 = 348
Проверочный расчет привода механизма главного подъема.
Фактический КПД Механизма:
= 099 – КПД упругой муфты;
= 096 – КПД учитывающий потери в опорах вала барабана и потери вызываемые вескостью каната;
= 097 – КПД полиспаста блоков и подвески.
Фактическая скорость подъема груза:
= 0315 м – диаметр барабана по оси каната;
а = 4 – кратность полиспаста.
Проверка выбранного двигателя.
Поскольку график действительных нагрузок механизма не задан пользуемся усредненным графиком использования механизмов по грузоподъемности [4] построенным на основе опыта эксплуатации кранов.
Согласно графику и расчетам за время цикла (подъем и опускание груза) механизм будет работать:
С номинальным грузом =20550 кг – 2 раза - =20550 кг;
С грузом 05*=10275 кг – 4 раза - =13275 кг;
С грузом 02*=4110 кг – 2 раза - =8110 кг;
С грузом 05*=10275 кг – 2 раза - =11275 кг.
По известным зависимостям (6) определяем моменты развиваемые двигателем время пуска при подъеме и опускании груза в различные периоды работы механизма и сводим результаты в таблицу.
Масса поднимаемого груза 103кг
Момент при подъеме груза
Время пуска при подъеме груза
Момент при опускании груза
Время пуска при опускании груза
Время установившегося движения
Сумма времени пуска при подъеме и опускании груза за цикл работы механизма:
Общее время включения за цикл:
Среднеквадратичный момент:
- среднепусковой момент электродвигателя.
Среднеквадратичная мощность электродвигателя:
Следовательно выполняется условие:
Проверка ускорения и замедления механизма подъема груза.
Ускорение при пуске механизма:
= 128с – время пуска.
что соответствует рекомендуемым значениям (6).
Время торможения при опускании груза:
-коэффициент учета инерции вращающихся масс расположенных на втором третьем и последних валах механизма;
- момент инерции вращающихся масс ротора и муфт;
n – номинальные обороты электродвигателя.
Определяем путь торможения механизма:
S = по таблице 1.22 (6).
Определяем время торможения:
Замедление при торможении:
что соответствует рекомендуемым значениям (5).
РАСЧЕТ МЕХАНИЗМА ВСПОМОГАТЕЛЬНОГО ПОДЪЕМА.
Кинематическая схема механизма вспомогательного подъёма аналогична схеме механизма главного подъёма приведённой ранее.
Высоты подъемаH = 14м
Продолжительность включенияПВ = 25%
Определим мощность электродвигателя:
= - сила тяжести поднимаемого груза;
=5000*981=4901*103 Н
Gгр=1800 H -сила тяжести крюковой подвески и полиспаста;
V = 033 мс - скорость подъема;
В каталоге данные на электродвигатели даны на ПВ=40% поэтому произведем пересчет на ПВ=25%:
Из (6) выбираем для Р=149 кВт и ПВ=25% электродвигатель с короткозамкнутым ротором серии 4MTKF со следующими характеристиками:
Тип двигателя 4MTKF160LB6
Пусковой монентМ = 460 В;
Температура окружающей средыне более 40С;
Статическое усиление в канате:
а=2 - кратность полиспаста;
т=1 - число полиспастов (креплений на барабане); КПД полиспаста:
= 098 – КПД блоков входящих в полиспаст;
k = 1 – число обводных блоков.
Определим разрывное усилие:
по правилам ГГТН для режима 6К см. (5) коэффициент использования каната n=6 таким образом
Для мостового крана работающего в закрытом помещении выбираются канаты по ГОСТ 2688-80 канат двойной свивки типа ЛК-РО. Канат устойчив к перегибам однако чувствителен к образивному износу. Конструкция 6x36(1 + 7 + 77 + 14) + lo.c. ГОСТ 7668-80. Маркировочная группа проволок 1770 МПа. Для полученного разрывного усилия выбираем канат диаметром:
h = 18 - коэффициент диаметра барабана по правилам ПУБГК стр.27;
Далее округляем полученный диаметр до ближайшего большего из ряда R20.
Угловая скорость вала барабана:
- шаг винтовой нарезки барабана;
Передаточное отношение редуктора:
Ближайшее к полученному передаточное число UС = 20. Условие что разница не должна превышать 10% выполняется:
Редуктор Ц2-300 - ближайший для ПВ=40% имеет допустимую радиальную консольную нагрузку Fr=14-104 Н что удовлетворяет условиям проверки.
Эквивалентный момент на тихоходном валу редуктора не превышает допускаемый крутящий момент редуктора Ц2-400 равный =825-103 Нм. Следовательно выбранный редуктор проходит по расчетному крутящему моменту.
Таким образом редуктор Ц2-400-20-11МУ1 ТУ 24-9-488-88 подходит по всем параметрам для данного привода.редуктора 315 кг.
Требуемый тормозной момент:
Грузовой момент на валу тормозного шкива:
требуемый тормозной момент:
kтор = 15 – коэффициент запаса торможения по ПУБГК стр.32;
Тт = 16736 * 15 = 25104 Нм.
Выбираем тормоз колодочный с электрогидравлическим толкателем ТКГ - 200М с тормозным моментом 300 Нм. Диаметр тормозного шкива 200 мм. При монтаже тормоз необходимо отрегулировать на тормозной момент 25104 Нм.тормоза не более 30 кг.
Расчет механизма подъема (проверочный).
Фактический КПД механизма:
= 025 м – диаметр барабана по оси каната;
a = 2 – кратность полиспаста.
Натяжение ветви каната набегающей на барабан:
Gsp=1800 H - сила тяжести грузоподъемника
т = 2 - число полиспастов.
Qгр = 49010 Н - сила тяжести груза
Статический крутящий момент на валу барабана при подъеме:
С = 2 - число ветвей каната закрепленных на барабане
Статический момент на подъем приведенных к валу двигателей:
к = 15 - коэффициент запаса торможения;
М =15-22031-096 = 31724 Нм.
Динамический момент на валу двигателя при подъеме груза:
- коэффициент динамичности;
- ускорение (замедление) обеспечиваемое системой управления двигателем.
Динамический момент на тихоходном валу редуктора:
Проверка прочности грузового каната:
Запас прочности каната:где Рр= 1015 кН - разрывное усилие каната в целом.
Канат двойной свивки типа ЛК-06х19 проволок с одним органическим сердечником ГОСТ 3077-80
S= 165815 Н - напряжение ветви каната набегающей на барабан.
По правилам ГГТН коэффициент запаса прочности каната для среднего режима работы группа - М5 по ГОСТ 25546-82: Кдоп=6
Расчет блоков полиспаста и обводных блоков механизма подъема:
Наименьший допускаемый диаметр блока по дну канавки выбирают в зависимости от диаметра каната:
l=20 - коэффициент зависящий от типа подъемного устройства и режима его работы ( )
D6 =135-(20-1) = 2565 мм
Диаметр блока полиспаста конструктивный выбирается из ряда стандартных значений: D6n=260 мм.
РАСЧЕТ МЕХАНИЗМА ПЕРЕДВИЖЕНИЯ ТЕЛЕЖКИ.
Схема привода механизма передвижения тележки представлена на рис. 1. Фланцевый электродвигатель 2 со встроенным тормозом закреплённый на раме тележки 1 соединен с навесным редуктором 3 который передаёт крутящий момент промежуточному валу 4 через зубчатую муфту 5. На промежуточном валу 4 жестко закреплено колесо 6. Тележка передвигается по крановым рельсам моста 7.
Грузоподъемность механизма главного подъёмаmг=3 0000кг;
Грузоподъемность вспомогательного механизмаmв=5000 кг;
Скорость передвижения тележкиV=067 мс (40ммин);
Режим нагруженияL2(умеренный);
Продолжительность включенияПВ=40%;
Выбор ходовых колес:
Определение массы тележки:
На основании справочных данных (1) с. 32 т.2 масса тележки вычисляется как:
где 03 - коэффициент массы тележки;
Вес тележки без груза:
Вес тележки с грузом:
Масса тележки с грузом:
Давление на ходовое колесо:
z = 4 – количество ходовых колес.
согласно (1) т.2 с.319 примем ходовое колесо со следующими характеристиками (небольшой запас по давлению нужен на тот случай если центр тяжести окжется не по центру тележки после проведения компоновки):
Характеристика ходового колеса.
Давление на ходовое колесо
Внешний диаметр Dxkmm
Посадочный диаметр dmm
Плечо трения качения
Диаметр реборды Dmaxmm
Выбор электродвигателя.
Расчет сопротивления передвижению тележки с грузом:
Сопротивление трения:
кр - коэффициент сопротивления реборды для троллейного токоподвода
кр = 25 из (1 )с.422
Сопротивление от уклонов крановых путей:
а =0001 - предполагаемый уклон пути;
Полное статическое сопротивление передвижению крана с грузом:
С учетом предварительного КПД:
- КПД редуктора муфты подшипника.
Для классов использования не выше М6 (4М по обозначению 1992г) возможно использование общепромышленных двигателей с повышенным скольжением и со встроенным тормозом серии 4АСЕ для избежания проскальзывания колес. Из (6) стр.85 выбираем двигатель со следующими характеристиками:
Тэд - номинальный момент электродвигателя;
Угловая скорость ходового колеса:
Ближайшее к полученному передаточное число равно U =25. Условие что разница не должна превышать 10% выполняется:
Фактическая скорость тележки тогда составит:
Эквивалентный момент редуктора на тихоходном валу:
кд - коэффициент долговечности;
- расчетный момент на тихоходном валу редуктора.
ко - коэффициент переменности нагружения;
zp - суммарное число циклов;
z0 =125-106 - базовое число циклов контактных напряжений.
zt - число циклов нагружения на тихоходном валу редуктора;
U т = 31 - передаточное число тихоходной ступени редуктора.
- частота вращения тихоходного вала редуктора.
машинное время работы механизма: t =12500 ч
Эквивалентный момент на тихоходном валу редуктора не превышает допускаемый крутящий момент редуктора ЩЗУвкф-125 равный Тд=500 Нм. Следовательно выбранный редуктор проходит по расчетному крутящему моменту.редуктора равна 73 кг.
Проверка двигателя по пусковому моменту.
Динамический момент сопротивления вращению электродвигателя во время пуска:
где J1 - момент инерции частей вращающихся на первом валу.
где Jмуф = 0002 кг*м2 – момент инерции муфты.
tn=Va - время пуска (торможения). Согласно (1) т.2 стр.324 для грузоподъёмности 20000 кг и условий работы крана.
Пусковой момент двигателя равен М =63 Нм следовательно условие пуска выполняется.
Коэффициент запаса сцепления:
Коэффициент запаса сцепления приводных колес с рельсом расчитываете: по следующей формуле:
[к]сц - допускаемый коэффициент сцепления.
Для помещений (без ветровых нагрузок) из (3) т.1 стр. 94 [к]сц =11.
Fcц - сила сцепления приводных ходовых колес с рельсом
Ft=735-104H - вертикальная сила без груза;
ксц=02 коэффициент трения для кранов в помещении по сухим рельсам из (8) стр.12;
zпр=2 - количество приводных колес;
z=4 -общее количество колес.
Fcm - сила статического сопротивления перемещения тележки без груза и без трения в подшипниках приводных колёс
Таким образом коэффициент сцепления равен:
кр = 2 - коэффициент реборды.
Fдин - сила динамического сопротивления передвижения без груза
Расчет соединительной муфты:
Расчетный момент муфты стоящей на промежуточном валу между колесом и редуктором:
к1 = 13 - коэффициент учитывающий степень ответственности механизма
к2 = 12 - коэффициент учитывающий режим работы L2 механизма (7).
Расчет тормозного момента:
Тормозной момент рассчитывается по следующей формуле:
Тин - момент инерции на валу электродвигателя
Тс - статический момент на валу электродвигателя
Таким образом тормозной момент равен:
В электродвигателе 4АС112МАЕ6 тормоз может быть отрегулирован до 40 Нм следовательно он обеспечивает требуемый тормозной момент.
Определение наибольшего изгибающего момента балки от действия ходовых колес тележки.
Из расчета механизма передвижения тележки известно что вес тележки с грузом равен:
Однако из ходя из компоновки механизма видно что вес распределен неравномерно между колесами тележки. Из измерений определим расстояния от центра тяжести тележки до опорных колес: а1 =17 м а 2=14 м.
Определим как следует расположить тележку что бы получить наибольший изгибающий момент (рис. 1).
Левая опорная реакция будет равна:
а изгибающий момент под первым колесом равен:
Для определения координаты х соответствующую максимальному значению изгибающего момента производную от этого момента по х необходимо приравнять к нулю:
а наибольший изгибающий момент:
Подставив численное значение пролета l = 225 получим:
x1= 104 м и М1mах = 13*106 Нм.
Выражение для момента представляет собой уравнение параболы нулевые точки которой
х0 = 0 и х0 = l – a1 = 208 м.
Аналогично для второго колеса тележки рассмотрим положение при котором оно располагается на расстоянии х от правой опоры В. Опорная реакция изгибающий момент будут равны:
После дифференцирования получим:
Таким образом после подстановки численных значений получим:
Нулевые точки параболы х0 = 0 и х0 =1-а2 =211 м. Сравнивая значения выбираем наибольший изгибающий момент:
Определение вертикального момента сопротивления сечения балки моста.
Исходя из условия прочности при работе на изгиб для одной балки:
m - коэффициент условий работы (4) стр. 336.
m1 =075 - коэффициент учитывающий степень ответственности элемента и возможные последствия при его разрушении;
т2 = 08 - коэффициент учитывающий возможные повреждения элементов при транспортировке и монтаже;
т3 = 09 - коэффициент учитывающий несовершенство расчёта.
Определение предварительных параметров сечения.
Высоту балки коробчатого сечения принимают в пределах (4) стр. 356:
Примем предварительно h=14 м.
Ширину горизонтального листа балки из условий обеспечения горизонтальной жесткости принимают в пределах:
Предварительно примем ширину B=055 м.
Предварительно ширина листа s для полого прямоугольного сечения определяется по формуле (рис. 2):
Проверка устойчивости для полого прямоугольного сечения балки.
Гибкость определяется по формуле:
- коэффициент опоры (для одного жестко заделанного конца);
- коэффициент формы (при постоянном моменте инерции).
- радиус инерции для полого прямоугольного сечения.
Итак гибкость равна:
Для стали Ст.3 (9) стр. 410 следовательно и формула Эйлера применима:
осевой момент инерции сечения.
расчетная сжимающая сила рассчитывается по формуле:
q=15 кНм - распределённая нагрузка по металлоконструкции крана;
n = 11 - коэффициент учитывающий вес рельса.
Таким образом данным сечением устойчивость обеспечена.
Проверка на совместное действие сжатия и изгиба:
Расчет сечения главной балки моста на горизонтальные нагрузки.
За основную систему сил примем две полу рамы в месте разреза прикладывается лишнее неизвестное х1 (рис. 3):
Неизвестные x1 являющиеся изгибающими моментами определяются из уравнения:
Для определения перемещений по способу Верещагина строим эпюры М от сосредоточенной нагрузки от колёс тележки (ускорение крана 02 мс2):
Неизвестные изгибающие моменты равны:
- отношение пролета главной балки к осевому расстоянию между ходовыми колесами концевой балки. Таким образом получим:
Наибольшие изгибающие моменты (рис. 3):
По середине главных балок:
На концах главных балок
Исходя из полученных значений подбираются параметры сечений концевых балок концов главной балки.
Произведем проверку сечения середины главной балки на горизонтальные нагрузки. Горизонтальный момент сопротивления сечения равен:
Требуемый момент сопротивления при действии горизонтального изгибающего момента:
Таким образом условие выполнено.
Нормальные напряжения в главной несущей балке.
Для верхних волокон:
= 11 – динамический коэффициент учитывающий скорость крана (для 60-120 ммин) (10) стр.105.
= 12 – динамический коэффициент учитывающий режим эксплуатации (для среднего).
Динамические прогибы и нагрузки.
В качестве динамической схемы принимаем схему груз - упругая связь – мост.
Коэффициент динамичности:
t0 - время нарастания нагрузки на металлоконструкции моста
Т - период колебаний металлоконструкции моста.
тк=311-105 Н - приведенная масса крана ;
тг = 2 *105Н - приведенная масса груза;
- жесткость конструкции моста.
Время нарастания нагрузки на мост:
v0=015 мс - скорость подъема груза;
- статическое удлинение каната;
z =8 - число ветвей полиспаста;
Fk = 10461*10--6 м2 - площадь сечения проволок каната;
Ек = 21*105 МПа - модуль упругости каната.
РАСЧЕТ МЕХАНИЗМА ПЕРЕДВИЖЕНИЯ КРАНА.
Кинематическая схема механизма состоит из электродвигателя 1 передающего через шкив тормоза 3 крутящий момент на быстроходный вал редуктора 2; тихоходный вал редуктора соединен через компенсирующую муфту 5 с промежуточным валом 4 и ходовым колесом 6.
Рис.1 Кинематическая схема привода механизма передвижения крана.
Определение предполагаемой массы крана :
На основании данных (4) с. 357 масса половины кранового моста для данной грузоподъёмности и пролёта равна 12 т следовательно полный вес моста равен 24 т. Вес двух концевых балок рекомендуется принимать 025 от веса моста. Вес механизмов (два механизма подъёма и два механизма передвижения) составит (табл.1)
Массы элементов привода крана кг.
Таким образом полная предполагаемая масса крана без груза составит:
тк = 12*2 + 025*12*2 + 21 = 321 т.
Масса крана с грузом:
ткг = тк + тг = 321*103+20*103==521*103кг.
Fкг = mкг*g = 521*103*98 = 511*105H
z = 4 - количество ходовых колес.
согласно (1) т.2 с.319 примем ходовое колесо со следующими характеристиками (табл. 2):
Выбор электродвигателя:
Расчет сопротивления передвижению крана с грузом:
кр - коэффициентсопротивления реборды для троллейного токоподвода
к =25 из (1) с. 422;
- КПД редуктора муфты подшипников колеса.
В кранах с пролётом более 10 м рекомендуется (4) использовать раздельный привод для механизма передвижения. Однако вводится коэффициент неравномерности нагружения для различных положений тележки.
Для классов использования не выше М6 (4М по обозначению 1992г) возможно использование общепромышленных двигателей с повышенным скольжением для избежания проскальзывания колес АИРС. Из технического каталога Владимирского электромоторного завода выбираем двигатель со следующими характеристиками:
к = 13 - коэффициент учитывающий степень ответственности механизма
к2 = 12 - коэффициент учитывающий режим работы L2 механизма
Из (7) т.2 выбираем муфту с номинальным моментом 125 Нм по ГОСТ 21424-75.
Ближайшее к полученному передаточное число равно Uc = 25. Условия что разница не должна превышать 10% выполняется:
- коэффициент долговечности;
к0 - коэффициент переменности нагружения;
- суммарное число циклов;
- 125*106 – базовое число циклов контактных напряжений.
Uт = 42 - передаточное число тихоходной ступени редуктора.
частота вращения тихоходного вала редуктора:
машинное время работы механизма: t=12500 ч
Ближайший подходящий редуктор Ц2-300 имеет допустимый крутящий момент равный для передаточного числа 40 и частоты вращения входного вала до 1500 обмин Tо=23 кНм. Следовательно выбранный редуктор проходит по расчетному крутящему моменту. Полное обозначение редуктора Ц2-300- 40-12М.
Проверка двигателя по пусковому моменту:
J1 – момент инерции частей вращающихся на первом валу.
Jмуф=0002 кг*м2 - момент инерции муфты.
J1 =0067+0002=0069 кг * м2;
tn=Va- время пуска (торможения). Согласно (1) т.2 стр.324 для грузоподъёмности 20000 кг и условий работы крана.
Пусковой момент двигателя равен Тп = Т 35 =261 Нм следовательно условие пуска выполняется.
Коэффициент запаса сцепления приводных колес с рельсом расчитывается по следующей формуле:
Fсц - сила сцепления приводных ходовых колес с рельсом.
ксц= 02 коэффициент трения для кранов в помещении по сухим рельсам из
zпр =2 - количество приводных колес;
z = 4 -общее количество колес.
Fсm – сила статического сопротивления перемещения тележки без груза и без трения в подшипниках приводных колес.
Определим момент на который следует отрегулировать тормоз. Согласно ПУБЭГК стр. 32 при двух и более тормозах коэффициент запаса торможения принимают:
Выбираем тормоз ТКГ- 160 с расчетным тормозным моментом 100 Нм и демпфирующим узлом . Тормоз отрегулировать на момент 2784 Нм.
Описание схемы механизации.
На листе представлена схема механизации механосборочного цеха завода металлоконструкций.
В цехе осуществляется сварка и сборка различных узлов металлоконструкций в том числе модуля ВЗП-4-1700 для газовой промышленности. Его полная масса в собранном виде составляет 24600 кг. он в свою очередь состоит из четырех основных узлов:
) Модуль нижний (13 т.)
) Модуль верхний (12 т.)
) Блок катковый (500 кг.)
Она осуществляется в следующем порядке. Сборка металлоконструкций осуществляется из комплектующих которые поступают из других цехов и заводов или изготавливаются на месте. Комплектующие и металл поступают в цех как железнодорожным так и безрельсовым транспортом. Непосредственно на этом участке осуществляется разгрузка комплектующих и металла краном гп 5т. Для окончательного перемещения и погрузки узлов необходимо использовать механизм главного подъема грузоподъемностью 30 т.
Из металла осуществляется сварка на стапелях. После чего происходит предварительный контроль качества продукции непосредственно на месте изготовления продукции.
После окончания сборки и проверки металлоконструкции покидают цех на специальных машинах.
ТЕХНОЛОГИЧЕСКАЯ ЧАСТЬ.
Тормозной шкив предназначен для передачи тормозного момента на валы механизма. Конструктивно тормозной шкив состоит из цилиндрического обода ступицы и диска. При торможении к цилиндрическому ободу прижимаются колодки а возникающие силы трения способствуют появлению тормозного момента. Диаметры тормозных шкивов 200 300 400 500 600 и 800 мм. Диск по окружности имеет отверстия для крепления с полумуфтами. Размеры отверстий зависят от диаметров соединения пальцев. Ступица имеет отверстие и шпоночный паз для передачи крутящего момента на вал.
Тормозной шкив устанавливается на входных валах редукторов вследствие того что для входных валов характерен минимальный крутящий момент при максимальной частоте вращения .
Анализ технологичности конструкции.
Для установки на валу шкив имеет цилиндрическое посадочное отверстие со шпоночным пазом. Тормозные шкивы присоединяют к зубчатым муфтам для чего в торцовых поверхностях предусмотрены выточки и несколько отверстий расположенных по окружности.
Наружную поверхность тормозного шкива для повышения срока службы подвергают поверхностной закалке на глубину 3-5 мм до твердости: HRC 38 -52 и шлифуют с обеспечением шероховатости 10 мкм. Посадочное отверстие выполняют по квалитету при чистоте поверхности 6-го класса. Должна быть соблюдена соосность наружной поверхности с посадочным отверстием ( радиальное биение не более 005 мм ) торцовое биение шкива не более 002 мм на 100 мм радиуса.
Способ получения заготовки.
Тормозные шкивы изготовляют преимущественно из стали 55 ЛЦ литьем в песчанную форму без отверстия. Вся отливка размещается в нижней опоке вниз полостью которая образуется одним кольцевым стержнем . Плоскость разъема формы совпадает с торцевой плоскостью шкива.
Маршрут обработки детали.
При составлении маршрута обработки пользуемся следующим правилом : сначала обрабатывают поверхности принятые за чистовые технологические базы затем обрабатываются поверхности в последовательности обратной их степени точности. Наиболее ответственные поверхности обрабатывают на заключительном этапе процесса. На основе этого составляется маршрут который представлен в таблице:
Карта эскизов приведена в приложении.
Расчет операционных припусков и межоперационных размеров.
Проведем расчетно-аналитический метод определения припуска на обработку поверхности обода тормозного шкива 300 ( -029 ). Обработка состоит из: получения заготовки черновом и чистовом обтачивании.
Таблица расчетных данных:
Элементная поверхность детали и маршрут ее обработки
Элементы припуска мкм
Допуск на изготовления ТД
Принятые размеры по переходам мм
Высота неровностей профиля Rz
Глубина дифектн. поверхностного слоя h
Суммарное отклонение расположений поверхностей
Погрешность установки заготовок
Припуск на черновое точение
Припуск на чистовое точение
Zmin = 2*[(250+240)++20] = 1440мкм
Припуск на шлифование
Zmin = 2*[(25+25)+] =120мкм
Zmin = 8460+185+29 = 8674мкм
Принимаем 2 Zном = 9000мкм
Расчет режимов резанья.
Операция 015 - токарная черновая обработка:
Рассчитывается по эмпирической формуле
- период стойкости инструмента;
t – глубина резания;
- поправочный коэффициент;
m x y – показатели степени.
Назначим глубину резания t = 22мм (по припуску на черновую обработку) подачу выберем из таблицы №11 стр.266 [7] S = 08 (ммоб). Коэффициент показатели степени берем из таблицы №17 стр.269 [7].
= 350; y = 035; m = 020
Поправочный коэффициент:
- коэффициент учитывающий качество обрабатываемого материала см. табл. № 1 - 4 стр.261 - 263[1];
- коэффициент отражающий состояние поверхности заготовки см. табл. № 5 стр.263[1];
- коэффициент учитывающий качество материала инструмента
см. табл. № 6 стр.263[1].
- коэффициент характеризующий группу стали по обрабатываемости и показатель степени см. в таблице № 2 стр. 262 [7].
Учитывая что мы растачиваем внутреннюю поверхность вводим поправочный коэффициент 09 см. таблицу № 17 стр. 270 [7].
Частота вращения заготовки:
Ср – постоянная см. табл. №22 стр.273 [7];
Кр – поправочный коэффициент;
Рz:Cp = 300x = 1y = 075n = -015
Рy:Cp = 243x = 09y = 06n = -03
Рx:Cp = 339x = 1y = 05n = -04.
- значения коэффициентов см. табл. № 9 10 и 23 стр. 264-275 [7].
Рz = 10*300*221*05075*109-015*1335=2593(H)
Рy = 10*243*2209*0506*109-03*1543=1232(H)
Рz = 10*339*221*0505*109-04*2713=2191(H).
По рассчитанной мощности и частоте вращения шпиделя выбираем станок токарный 16К20.
Операция 020 – Сверление:
D = 32 мм см. таблицу № 23 стр.271 [7].
t = 05*D = 05*32 = 16 мм
S = 03 мм см. таблицу № 25 стр.277 [7].
C = 98;q = 04;y = 05m = 02.
T = 70 см. таблицу № 30 стр. 283 [7].
K = 17*11*085 = 1445
= 00345;q = 2;y = 08 см. таблицу № 32 стр. 285 [7].
Из вышеизложенного известно что:
D = 32 мм см. таблицу № 23 стр.271 [7];
S = 03 мм см. таблицу № 25 стр.277 [7];
На основании рассчитанного резанья выбираем станок вертикально сверлильный 2Н125Л2.
Операция 035– Протягивание:
Sz = 01 мм см. таблицу № 64 стр. 173 [7].
Vтаб = 10ммин = 017 мс см. таблицу № 52 стр. 299 [7].
Сила резанья приходящаяся :
Р = 325 (Н) см. таблицу № 54 стр.300 [7].
- наибольшая суммарная длина лезвий всех одновременно режущих зубьев.
Определим периметр резанья:
В – периметр резанья мм;
zc – число зубьев в секции протяжки;
z1 – наибольшее число одновременно режущих зубьев.
t – шаг зубьев протяжки.
z1 = 8210 = 82 округляем до 9.
Рz = 325*180=58500 (Н).
На основании рассчитанной силы резанья выбираем станок горизонтально протяжной 7Б55.
Операция 040 – Сверление:
Операция 045 –Зенковка
На данной операции происходит снятие фасок
Операция 050 – Токарная чистовая обработка:
Назначим глубину резания t = 05мм подачу выберем из таблицы №14 стр.266 [7] S = 025 (ммоб). Коэффициент показатели степени берем из таблицы №17 стр.269 [7].
= 340; y = 020; m = 020
Рz = 10*300*03*025*3622*074 = 973(H)
Рy = 10*243*05*025*3622*0365=353(H)
Рz = 10*339*05*025*3622*0151=122(H).
Операция 055 – Шлифование:
Выбираем белый электрокорунд марки 15А зернистость 50-40 с твердостью С на керамической связке типа ПП.
Dкр=350 Bкр=100 d=203
Шлифование с продольной подачей на каждый ход.
Описание конструкции и принципа работы поворотных
пневматических тисков.
При вращении рукоятки вращается винт подвижной губки осуществляя предварительный зажим обрабатываемой заготовки.
При дальнейшем вращении рукоятки подпружиненный плунжер воздействуя на золотник открывает доступ сжатого воздуха на верхнюю полость пневмоцилиндра. При этом шток поршня через рычаг обеспечивает окончательный зажим заготовки подвижной губкой.
Технические характеристики станочного приспособления
Наибольшее расстояние между губками мм 240
Усилие зажима при давлении воздуха 04 МПа Н 6000
Диаметр цилиндра мм 320
Рис. 9 Тиски поворотные пневматические
9.2. Расчет усилия зажима детали в приспособлении
Рис. 10 Расчетная схема усилия зажима
Заготовка установлена горизонтальной и боковой поверхностями. Сила резания стремится повернуть заготовку вокруг т. О чему препятствует сила трения (рис. 10).
Если Рз не совпадает с центром тяжести опорного треугольника:
uде abc - коэффициенты которые в сумме равны единице их находят из уравнения статистики.
Выбранное станочное приспособление удовлетворяет для силы закрепления = 3370 Н так как для тисков поворотных пневматических по техническим характеристикам усилие зажима при давлении воздуха 04 МПа=6000 Н
Рис. 11 Схема рычажных зажимных механизмов для поворотных пневматических тисков
Из данной расчетной (кинематической) схемы (рис. 11) получаем уравнение для расчета силы на приводе.
Зная что получим требуемое Р при полученном R.
Получаем что Р давление сжатого воздуха 01 МПа. А так как подается давление воздуха 04 МПа то устанавливаем понижающий редуктор перед тисками.
Таким образом делаем вывод что тиски пневматические поворотные подходят для применения в качестве станочного приспособления при сверлильной операции.
ПРОМЫШЛЕННАЯ ЭКОЛОГИЯ
Обеспечение безопасности труда при эксплуатации грузоподъемных машин.
Одной из основных задач при эксплуатации ПТМ является контроль технического состояния обеспечивающего безопасную их работу. Для решения этой задачи организуется государственный и местный технический надзор.
Государственный надзор осуществляется инспекторами соответствующих инспекций а местный — ИТР закрепленными приказом по предприятию.
Правилами безопасной эксплуатации подконтрольных ПТМ предусматривается персональная ответственность за содержание ПТМ и оборудование в исправном состоянии; за организацию безопасного производства работ; за управление машиной и ее обслуживание; за осуществление технического надзора.
Лицо отвечающее за техническое состояние ПТМ организует периодические осмотры технические обслуживания и ремонты обученным и аттестованным персоналом; контролирует ведение журнала осмотров и устранения неисправностей; периодическую проверку знаний обслуживающего персонала с регистрацией в журнале; подготовку машин к техническому освидетельствованию; хранение паспортов и технической документации на машины.
Ответственный за безопасное производство работ контролирует использование грузозахватных приспособлений и тары; выдает указания крановщикам и стропальщикам о месте порядке и габаритных размерах грузов; привлекает к работе обученный и аттестованный персонал проводит инструктаж по безопасному выполнению работ; запрещает работу в особо опасных условиях без наряда-допуска.
Лица осуществляющие управление машинами и их обслуживание (крановщики слесари электромонтеры стропальщики сигнальщики) допускаются к работе приказом по предприятию (цеху) после профессиональной подготовки аттестации с соответствием по возрасту и состоянию здоровья. При переходе на другой вид машины или при перерывах в работе проводится переподготовка и повторная проверка знаний.
Инженерно-технический работник по надзору осуществляет контроль за техническим состоянием и безопасной эксплуатацией ПТМ; проводит освидетельствование машин грузозахватных приспособлений и тары; выдает разрешение на ввод в эксплуатацию; ведет учет и освидетельствование машин не подлежащих регистрации; выдает предписание и осуществляет контроль их выполнения а также предписаний органов технадзора; контролирует выполнение графиков технических обслуживании и ремонтов наличие инструкций у обслуживающего персонала соблюдение порядка допуска к управлению и обслуживанию машин; участвует в комиссии по аттестации и периодической проверке знаний персонала; принимает меры по устранению неисправностей и нарушений инструкций (вплоть до остановки машин).
К основным мероприятиям по техническому надзору относят: регистрацию получение разрешения на допуск к работе периодическое техническое освидетельствование контроль за техническим состоянием и организацией управления ПТМ а также методами производства работ.
Регистрацию в органах технадзора проводят на всех подконтрольных ПТМ. Не регистрируют краны всех типов с ручным приводом управляемые с пола мостовые электрические и поворотные консольные краны грузоподъемностью до 10 т простейшие стреловые краны ручные и электрические тали лебедки и др. Все они подлежат местному техническому надзору. Регистрацию проводят на основании заявления руководства предприятия паспорта машины и акта на выполнение монтажных работ. После реконструкции ремонта передачи грузоподъемной машины другому владельцу и перестановки на новое место проводят ее перерегистрацию.
Разрешение на допуск к работе грузоподъемных машин подлежащих регистрации в органах технадзора получают: вновь зарегистрированные машины; после монтажа на новом месте; после реконструкции (модернизации) или ремонта металлоконструкции машины. На машины с местным техническим надзором это разрешение выдается ответственным за эксплуатацию ИТР на основании документации завода-изготовителя и результатов технического освидетельствования.
Техническое освидетельствование грузоподъемных машин приспособлений и тары производится с регламентированной периодичностью и величиной ”* испытательной нагрузки для обеспечения работоспособности и безопасности производства работ.
При эксплуатации ПТМ обеспечивается высокий уровень безотказной работы. Однако при их эксплуатации случаются аварии и несчастные случаи которые делят на следующие виды: аварии без травмирования людей; аварии с травмированием людей; несчастные случаи связанные с авариями. Все они расследуются в установленном порядке с анализом причин и разработкой рекомендаций по их предотвращению.
Для предупреждения аварий и несчастных случаев на ПТМ устанавливают приборы безопасности и блокировочные устройства. Так грузоподъемные краны оборудуются концевыми выключателями ограничителями подъема стрелы ограничителями и указателями грузоподъемности ограничителями поворота (для башенных кранов) креномерами (для самоходных и прицепных стреловых кранов) сигнализаторами опасного напряжения анемометрами (приборы для автоматического включения сирен и противоугонных устройств при достижении предельной скорости ветра) ограничителями перекоса (для мостовых и козловых кранов) противоугонными устройствами (для кранов на рельсовом пути).
Содержание приборов и устройств обеспечивающих безопасную работу машин в работоспособном состоянии и строгое выполнение установленных правил эксплуатации ПТМ позволяет практически исключить аварийные ситуации и травмирование обслуживающего персонала.
Техника безопасности при работе на мостовых кранах
В процессе трудовой деятельности человека в производственных условиях не исключены несчастные случаи. Несчастным случаем называется происшествие при котором в результате внешнего внезапного воздействия на человека (механического теплового электрического химического) произошло повреждение организма или нарушилось его нормальное функционирование. Повреждения организма называемые травмами могут быть в виде ушибов и ранений тепловых и химических ожогов поражений электрическим током обморожения и т. п.
По силе поражения человека различают микротравмы когда в результате повреждения организма человек не теряет трудоспособности; травмы с временной нетрудоспособностью; тяжелые травмы приводящие к частичной или полной потере трудоспособности т. е. к инвалидности; травмы со смертельным исходом.
Профессиональным заболеванием называется постепенное ухудшение здоровья человека в результате неблагоприятных производственных условий например шума вибрации пыли дыма. Чтобы предупредить несчастные случаи на производстве необходимо знать причины производственного травматизма и способы их устранения.
Различают технические организационные и санитарно-гигиенические причины. К техническим причинам относятся:
а) конструктивные недостатки электрооборудования механизмов и транспортных устройств;
б) несовершенство технологического процесса;
в) несовершенство или отсутствие ограждений предохранительных устройств и блокировок. К организационным причинам относятся:
а) нарушение производственных инструкций и технологического процесса;
б) неправильная организация труда и рабочих мест;
в) применение несоответствующего инструмента приспособлений и оборудования;
г) отсутствие правильного руководства со стороны технического персонала.
К санитарно-гигиеническим причинам относятся:
а) нарушение окружающей среды в производственном помещении — очень низкая или очень высокая температура высокая влажность ветер сквозняки;
б) несоответствующее искусственное освещение — слишком сильное или недостаточное например применение люминесцентных ламп для освещения кранов о чем сказано выше;
в) недопустимая загрязненность воздуха пылью газами или парами;
г) наличие вредных радиоактивных или электромагнитных излучений;
д) недопустимый шум или недопустимая вибрация;
е) нарушение рабочими правил личной гигиены антисанитарное состояние производственного помещения;
ж) неудовлетворительный медицинский контроль за состоянием здоровья рабочих.
Рабочим местом считается место постоянного или периодического пребывания работающего для осуществления производственного процесса. Рабочим местом машиниста мостового крана является кабина. Организация рабочего места заключается в выборе рабочей позы и в размещении органов управления краном. При правильно выбранной рабочей позе например сидя или стоя которая зависит от характера движений крановщик выполняет работу с минимальной затратой энергии совершая безопасные движения с наименьшей утомляемостью и неослабным вниманием. Рабочая поза должна быть устойчивой чтобы рабочий не прилагал чрезмерных мышечных усилий.
Очень важно в организации рабочего места чтобы органы управления краном были правильно расположены в рабочей зоне крановщика. Органы управления надо располагать так чтобы по возможности свести рабочие движения при управлении краном к движению предплечья и кистей рук допуская движение плечевого сустава только в виде исключения. Особенно важно обеспечить персонал необходимым инструментом приспособлениями и защитными средствами при наличии которых работа будет протекать уверенно безопасно и с высокой производительностью.
Повышение производительности труда крановщика которая в конечном счете определяет производительность крана достигается улучшением условий его работы — комфортом и состоянием окружающей среды: климатом уровнем звука и вибрации запыленностью освещенностью и видимостью.
Понятие «климат» определяется температурой влажностью степенью излучений и скоростью движения воздуха. Для нормальной жизнедеятельности человека необходимо чтобы температура его тела была постоянной — около 37 °С а тепловой баланс тела выравнивался за определенный промежуток времени т. е. восприятие тепла должно быть таким как и отдача его в окружающую среду. На теплообмен влияет климат который является благоприятным тогда когда для обеспечения теплового баланса не требуется применения специальных регулирующих устройств и неблагоприятным когда без применения таких устройств не может наступить равновесия между восприятием и отдачей тепла. Тепловые излучения — это излучения энергия которых распространяется невидимыми глазом человека инфракрасными лучами. Источниками тепловых излучений являются все нагретые тела: расплавленные и нагретые металлы работающие электродвигатели крановые резисторы осветительные лампы (95 % энергии ламп накаливания тратится на нагрев и только не более 5 % — на световое излучение).
Лучистая тепловая энергия воздухом почти не поглощается а передается от более нагретых тел к поверхности менее нагретых повышая их температуру. Воздух производственных помещений должен иметь не слишком высокую температуру и влажность и определенную подвижность. Санитарными нормами установлены предельно допустимые пределы температур в зависимости от характеристики производственных помещений в отношении избытка тепла и категории работы в различные периоды года. При температуре 18—20 °С в организме человека наилучшим образом осуществляется терморегуляция т. е. поддержание постоянной температуры тела на уровне около 37 °С. Такой климат вполне возможен в механических цехах машиностроительных заводов и ремонтных цехах вообще.
В литейных кузнечных термических и прокатных цехах климат всегда будет более неблагоприятный вследствие большого выделения теплоты дыма сернистого газа. Относительная влажность определяемая как отношение содержания водяных паров воздуха к их максимально возможному содержанию в процентах характеризует влажность воздуха при определенной температуре. Влажность воздуха в значительной мере влияет на теплообмен организма человека на отдачу тепла испарением.
Подвижность воздуха определяемая скоростью его движения влияет на охлаждение человека при температуре воздуха до 35—36 °С т. е. более низкой чем температура тела. При более высокой температуре воздуха (до 40 °С) и большей его подвижности вместо охлаждения происходит внешний подогрев тела а для охлаждения его требуется дополнительное выделение пота следовательно потеря влаги. Если вблизи человека находятся источники тепла то такое излучение может вызвать перегрев кожи и общий перегрев тела.
При значительном перегреве организма возникает опасное заболевание связанное с нарушением работы сердечно-сосудистой системы называемое тепловым ударом который в тяжелых случаях может быть смертельным.
В зависимости от наличия в помещении источников тепла и опасности перегрева для поддержания нормального микроклимата применяется вентиляция или более совершенное средство — кондиционирование воздуха — подача в помещение например кабину крана очищенного от пыли и примесей воздуха с определенной температурой и влажностью.
Вентиляция и кондиционирование воздуха не защищают организм от тепловых лучей. Защиты кабины от теплового излучения осуществляется экранами из таких материалов как асбест асбестоцемент или шифер. Защита кабины от шума производится соответствующими материалами слабо проводящими звук. Крановщику нет необходимости слышать грохот кузнечного или литейного цеха — сигналы ему подают руками. В его распоряжении звуковой сигнал для работающих внизу сам крановщик не обязательно должен его слышать.
Обеспечение акустической безопасности при эксплуатации мостового крана.
Звуковым давлением называется то дополнительное давление воздуха которое возникает при прохождении через него звуковых волн. Единицей звукового давления служит ньютон на квадратный метр (Нм2). Силой звука называется количество звуковой энергии проходящей в 1 с через площадь в 1 м2 расположенную перпендикулярно к распространению звуковой волны. Единицей силы звука служит ватт на квадратный метр (Втм2). Сила звука по физиологическим восприятиям уха оценивается как громкость. Ухо человека обладает чувствительностью не к силе звука а звуковому давлению которое зависит от силы звука. Слышимость определяется звуковым давлением и частотой звуковых волн и зависит от индивидуальных особенностей человека. Минимальное значение силы звука — это величина силы звука которая вызывает едва заметное ощущение в ушах. Для звуковых частот от 1 до 4 кГц органы слуха наиболее чувствительны. При этих частотах имеет место так называемый порог слышимости.
Максимальное значение — это такое значение силы звука которое вызывает болевое ощущение в ушах — болевой порог. При частоте 1 кГц сила звука на пороге слышимости равна 10~12 Втм2 а при болевом пороге — 1012 Втм2.
Вредное физиологическое действие шума на организм человека состоит в том что помимо повреждения слухового аппарата в виде развивающейся глухоты страдает и нервная система ухудшается деятельность органов дыхания нарушается работа сердечно-сосудистых органов. Из-за чрезмерного шума ослабляется внимание и поэтому возможны несчастные случаи и снижение производительности труда
Обеспечение вибрационной безопасности при эксплуатации мостового крана.
Механические колебания тел с частотой меньше 20 Гц воспринимаются только как вибрации. Часто вибрации сопровождаются и шумом. Особенно опасны вибрации непосредственного действия когда источник колебаний находится вблизи человека. При этом возможно заболевание сосудов и нервной системы сопровождаемое головными болями головокружением онемением кистей рук повышенной утомляемостью.
Одной из основных мер борьбы с шумами и вибрациями является снижение уровня звука и уменьшение амплитуды вибраций путем конструктивного усовершенствования производственных установок (применение виброгасителей) и совершенствования технологии. Шум и вибрации также можно ослабить применением звукоизоляции оборудования а также путем индивидуальной защиты людей подверженных вредному действию шумов и вибраций.
Снижение шума от вращающихся частей машин достигается созданием более гладких их поверхностей большой точностью балансировки применением высококачественных подшипников. Большое значение имеет также правильный уход за оборудованием надлежащая смазка и устранение биения в соединительных муфтах и редукторах. Для индивидуальной защиты рабочих от шума применяют вкладыши из ваты или пробки из губчатой резины закладываемые в отверстие уха а также специальные наушники или шлемы плотно закрывающие ухо. Для защиты от вибраций машинистов мостовых кранов можно применять коврики из губчатой резины или поролона. На сиденье стула можно укрепить поролоновые прокладки.
Обеспечение механической безопасности при эксплуатации мостового крана.
Движущиеся машины и механизмы незащищённые подвижные элементы механизмов:
вращающийся барабан;
представляют собой опасный производственный фактор. Для исключения контакта человека с опасной зоной применяются оградительные средства защиты: кожухи щиты решётки сетки на жёстком каркасе корпуса гидромоторов и редукторов а также предупреждающие и указывающие плакаты. Все механизмы закрыты защитными кожухами или приспособлениями предусмотренными в конструкции самого крана и соответствующие Правилам Госгортехнадзора. С целью безопасного доступа к механизмам на кране предусмотрены различные площадки и лестницы.
Также при работе крана возникает возможность обрыва каната при подъеме груза вес которого превышает номинальную грузоподъемность более чем на 10%. Падение груза может привести к травмам людей попавших в зону работы крана. Для того чтобы это не возникало в конструкции крана предусмотрен ограничитель грузоподъемности автоматически отключающий механизм подъема при превышении номинальной грузоподъемности. Подъём и перемещение мелкоштучных грузов должны производиться в специально предназначенной для этого таре при этом должна исключаться возможность выпадения отдельных грузов.
Также при увеличении нагрузки на грузовые канаты выше допустимой для исключения натяга и обрыва каната при подъеме груза на недопустимую высоту предусмотрен ограничитель высоты подъема. При подъеме груза должны применяться стропы соответствующие весу поднимаемого груза. С учётом числа ветвей и угла наклона строп их следует подбирать так чтобы угол между их ветвями не превышал 90 градусов.
Для предупреждения обслуживающего персонала находящегося в непосредственной близости от рабочей зоны крана в конструкции предусмотрен автоматический звуковой сигнал. Для того чтобы избежать риска нанесения травмы людям находящимся в зоне работы крана имеется ряд правил которые должен выполнять крановщик:
подъём и перемещение груза не должны производиться если под грузом находятся люди.
не разрешается опускать груз в автомашины при нахождении в её кузове людей.
запрещается подъём и перемещение груза с находящимися на нем людьми.
Острые кромки заусенцы и шероховатость поверхностей изделий и оборудования представляют собой опасность повреждения для крановщика и обслуживающего персонала следовательно они применяют средства для исключения физического контакта с ними (применяются ломы строповка производится строповщиком в рукавицах). Не допускается расположение рабочего места на значительной высоте относительно земли.
Для защиты посторонних людей территория на которой работает кран должна быть ограждена из-за возможности нанесения им вреда перемещаемыми грузами и разрушающимися конструкциями.
Обеспечение пожаробезопасности при эксплуатации мостового крана.
На объектах где эксплуатируются мостовые краны существует высокая степень возникновения пожароопасной ситуации. При возникновении пожара на людей в основном воздействуют: открытый огонь искры повышенная температура окружающей среды предметов токсичные продукты горения дым пониженная концентрация кислорода попадающие части строительных конструкций и т.д.
Для предотвращения такой ситуации на этих объектах должны соблюдаться все правила техники безопасности. Для своевременного устранения уже возникшего непредвиденного возгорания на объектах должны быть предусмотрены средства борьбы с огнём. К таким средствам относятся огнетушители и рукава с водяным питанием. Также для борьбы с огнём может использоваться огнетушитель входящий в комплект необходимых принадлежностей мостового крана. Он также используется для тушения электропроводки и электрооборудования крана.
Требования по обеспечению пожаробезопасности и соответствующие мероприятия по ее обеспечению излагаются в ГОСТ 12.1.004- 91 «ССБТ. Пожарная безопасность. Общие требования».
Для обеспечения пожаробезопасности вся аппаратура управления размещена в герметизированном контейнере электродвигатели всех механизмов имеют степень защиты от внешней среды
Обеспечение нормальных условий зрительной работы крановщика при эксплуатации мостового крана.
Недостаточное освещение рабочего места затрудняет длительную работу вызывает повышенное утомление и способствует развитию близорукости. Слишком низкие уровни освещенности вызывают апатию и сонливость.
Излишне яркий свет слепит снижает зрительные функции приводит к перевозбуждению нервной системы уменьшает работоспособность. При недостаточности естественного освещения применяются источники искусственного света: лампы прожектора специальные осветительные установки. По ГОСТ 24378-80Е «Освещённость на погрузочно-разгрузочных площадках в зоне работы крана и на грузозахватном устройстве на любом уровне его подъёма и перемещения в горизонтальной плоскости» должна быть не менее от наружной осветительной установки. По типу источника света освещение бывает естественное искусственное и совмещенное.
Для расчета общего равномерного освещения используем метод коэффициента использования светового потока.
Размеры кабины: 13 х 145 м2 при высоте 185 м. Высота подвеса светильника общего освещения – 18 м.
Световой поток лампы Фл (лм) одного светильника находится по формуле:
где ЕН - минимальная нормированная освещенность лк;
ЕН = 300 (лк) (по СНиП 23-05-95)
КЗ - коэффициент запаса принимается в зависимости от загрязненности воздуха в помещении. КЗ = 14 (СНиП 23-05-95)
S - площадь помещения: S = 13 145 = 19 (м2)
z – коэффициент минимальной освещенности z = 115.
N - число светильников N = 2.
- коэффициент использования светового потока ламп (%) зависящий от типа светильника коэффициента отражения потолка Roп и стен Roc и индекса i формы помещения.
где A и B - ширина и длина помещения; h - высота подвеса светильников над рабочей поверхностью. Для нашего случая:
для помещения Roп = 50% (светлый потолок) Roc = 30% находим коэффициент использования светового потока для светильника типа «Астра»: = 21%
Находим световой поток одного светильника:
Выбираем лампы накаливания Г-125–135–150 со световым потоком 2280 лм. Отклонение рассчитанного светового потока от выбранного составляет +4% что является допустимым.
Для полноценной работы крановщика в комфортных условиях необходимо наличие в кабине управления ламп накаливания со световым потоком не менее 2280 л
Очистка сточных вод от нефтепродуктов (масел СОЖ).
Очистка сточных вод – обработка сточных вод с целью разрушения или удаления из них вредных веществ. Освобождение сточных вод от загрязнения – сложное производство. В нем как и в любом другом производстве имеется сырье (сточные воды) оборудование (очистные сооружения) а также готовая продукция (очищенная вода).
Методы очистки сточных вод можно разделить на механические химические физико-химические и биологические когда же они применяются вместе то метод очистки и обезвреживания сточных вод называется комбинированным. Применение того или иного метода в каждом конкретном случае определяется характером загрязнения степенью вредности примесей объемами производства предприятия стоимостью метода. В данном дипломном проекте рассматривается механический метод очистки сточных вод металлообрабатывающего цеха.
Механическая очистка является обязательной ступенью очистки в любом очистном комплексе.
Сущность механического метода состоит в том что из сточных вод путем отстаивания и фильтрации удаляются крупные механические примеси. Грубодисперсные частицы в зависимости от размеров улавливаются решетками ситами песколовками септиками навозоуловителями различных конструкций а поверхностные загрязнения – нефтеловушками бензомаслоуловителями отстойниками и др. Механическая очистка позволяет выделять из бытовых сточных вод до 60 - 75% нерастворимых примесей а из промышленных до 95% многие из которых как ценные примеси используются в производстве.
На предприятиях очистка сточных вод осуществляется нефтеловушками горизонтальными отстойниками.
Для расчета нефтеловушек необходимо знать скорость всплывания нефтепродуктов: [1]
- средний диаметр частиц (капель) нефтепродукта мкм;
- плотность сточных вод и нефтепродуктов;
- динамическая вязкость сточных вод.
Таким образом после подстановки получим:
Выбираем горизонтальную составляющую скорости течения сточной воды:
Геометрические характеристики нефтеловушки:
Площадь поперечного сечения ловушки: [1]
Ширина нефтеловушки В=6м.
Высота нефтеловушки:
Наименьшая длина нефтеловушки: [1]
Время отстаивания сточной воды в нефтеловушки: [1]
Выводы: при эксплуатации мостовых кранов следует соблюдать все правила техники безопасности характерные для данного вида работ (механо-сборочные погрузочно-разгрузочные и прочие работы). Обслуживающему кран персоналу следует соблюдать соответствующие инструкции при работе а также иметь средства индивидуальной защиты от основных типов воздействия. Также должны быть предусмотрены возможности быстрого устранения аварий возникших при работе с краном (пожаров утечки нефтепродуктов и т.д.). Предложенные меры позволяют обеспечить безопасный труд персонала и защиту окружающей среды.
Мероприятия по охране окружающей среды обеспечивают содержание вредных веществ в пределах ПДК.
ЭКОНОМИЧЕСКАЯ ЧАСТЬ.
Мостовой кран общего назначения грузоподъемности 5 тонн устанавливается на участке сборочного цеха предназначенного для сборки и подъема ВЗП. Установка данного крана и введение его в работу совместно с действующим ранее на данном участке мостовым краном грузоподъемности 50 тонн позволит уменьшить потери рабочего времени рабочих занятых на сборке машин и сократить срок изготовления ВЗП с 4-х месяцев до 3-х месяцев за счет дополнительного изготовления 025 деталей для ВЗП. Это даст значительный экономический эффект и принесет заводу определенную прибыль.
Техническая характеристика мостового крана общего назначения грузоподъемностью 5 тонн.
Грузоподъемность – 5 тонн;
Годовой фонд времени работы – 2800 ч;
Срок службы с учетом износа – 10 лет;
Высота подъема – 16 м;
Масса крана – 12.74 т.
Передвижения крана – 134 мс;
Передвижения тележки – 067 мс;
Подъема груза – 017 мс.
Расчет капитальных затрат.
Капитальные затраты на внедрение новой техники – это единовременные затраты связанные с осуществлением технологического решения.
Формула для определения капитальных затрат по подъемно-транспортным машинам в общем случае имеет вид:
Км- затраты на монтаж определяются по прейскуранту на монтаж ПТМ.
Ктр- затраты на перевозку ПТМ определяются по тарифам действующим на автомобильном и железнодорожном транспорте;
Кзч- затраты на запчасти;
m – количество типоразмеров машин.
Для определения себестоимости крана пользуемся методом калькулирования по статьям затрат.
Основная зарплата рабочих:
СЧАС – часовая тарифная ставка = 120 руб
SОСН=120*5692=683040 руб.
Дополнительная зарплата рабочих:
SДОП=012*683040=81964 руб.
Отчисления в фонд социального страхования в пенсионный фонд и др. составляют 26% от основной зарплаты.
SОТ=026*683040=273216 руб.
Расход на содержание и эксплуатацию оборудования:
SОСН.М. – затраты на основные материалы.
Общецеховые расходы:
Общезаводские расходы:
Внепроизводственные расходы составляют 2% от заводской себестоимости.
Наименование статей затрат
Комплектующие изделия
Транспортно-заготовительные расходы
Дополнительная зп рабочих (12%)
Отчисления на соц.страхование и в пенсионный фонд (26%)
Расходы на содержание и эксплуатацию оборудования
Общезаводские расходы
Внепроизводственные расходы
Полная себестоимость составляет 885840 руб.
Оптовая цена определяется по формуле:
Транспортно-заготовительные расходы составят 1820 рублей за 1 тонну веса крана.
КТР=1820*m; где m=12740 т.
КТР=1820*1274= 23186 руб.
КТР=1820*1396=25407 руб.
Затраты на монтаж крана КМК состоит из затрат на монтаж электрической и механической частей крана. Они составляют:
Проектируемого крана – КМ=36 %; КЭМ=12%.
Базового крана – КМ=71%; КЭМ=17%.
КМ=36*1122360100=40405 руб.
КМ=71*1035000100=73485 руб.
КЭМ=12*1122360100=134832 руб.
КЭМ=17*103500100=175950 руб.
Затраты на запчасти составляют 3% цены для проектируемого крана и 5% для базового крана.
КЗЧ=0003*1122360=33670 руб.
КЗЧ=005*10350000=51750 руб.
К сопутствующим затратам КСОП относится стоимость подкрановых путей стоимость производственных помещений и др. по данным завода.
Результат расчета капитальных затрат см. табл.
Затраты на электромонтаж
Транспортные расходы
Сопутствующие затраты
Расчет эксплуатационных затрат.
Под технологической себестоимостью понимают совокупность затрат применяющихся в зависимости от варианта технологического решения:
СЗ – зарплата рабочих;
СЭЛ – затраты на электроэнергию;
СРЕМ – затраты на текущий ремонт;
СА – амартизационные отчисления.
Затраты на зарплату рабочих:
КДЗ = 13 - коэф-т учитывающий дополнительную зарплату;
КСС = 1079 - коэф-т учитывающий отчисления на соц. страхование;
FЭФ = 1987 - годовой фонд времени;
IТАР = 14 – часовая тарифная ставка;
NСП = 2 – численность рабочих.
Расходы на электроэнергию:
ЦЭ – тариф на 1 кВТ час электроэнергии;
NД – суммарная мощность двигателей;
WД – коэф-т использования двигателей;
WМ – коэф-т использования по мощности;
F – годовой фонд времени.
Затраты на ремонт оборудования:
АРЕМ – доля затрат на ремонт;
К=12 – коэф-т учитывающий дополнительный ремонт.
СРЕМ=0036*12*1122360 = 48485 руб.
СРЕМ=006*12*1035000 = 74520 руб.
Амортизационные отчисления:
НО = 29% норма амортизационных отчислений по основным фондам.
В результате расчетов получим
Затраты на эл. энергию
Затраты на текущий ремонт
Амортизационные отчисления
Расчет экономического эффекта.
ЗПР = 178493+015*153976650 = 409458 руб.
ЗБ = 207049+015*153350200 = 437074 руб.
ЭГ = 437074 – 409458 = 27615 руб.
Определение интегрального эффекта:
СБ СП – эксплуатациооные затраты базового и проектируемого кранов;
КП КБ – капитальные затраты нового и базового кранов;
КРП КРБ – затраты на кап. ремонт кранов.
ЭИ = (207049-178493)*10 - (1539766 - 1533502) – (89551 - 81220)*2 = 262627 руб.
Экономический эффект за весь период службы проектируемого крана по сравнению с базовым вариантом составит 262627 рублей. Следовательно проектируемый вариант мостового крана грузоподъемностью 5 тонн экономически целесообразен.
ЭЛЕКТРИЧЕСКАЯ ЧАСТЬ.
Требования к элктрооборудованию со стороны главных механизмов.
Электрическое оборудование кранов его монтаж заземление и токопровод должны соответствовать Правилам устройства электроустановок (ПУЭ).
Рабочее напряжение сети питающей краны не должно превышать 500 В. в соответствии с этим на кранах применяется электрооборудование на 220 380 и 500 В переменного тока а также 220 и 440 В постоянного тока.
Для защиты проводов и электродвигателей от коротких замыканий и значительных перегрузок свыше 2-25 % на кране должна быть максимальная защита.
Наряду с обязательными требованиями вытекающими из правил Госгортехнадзора и ПУЭ приводятся следующие требования:
При выключенном электродвигатели подъема (на нулевом положении) должен существовать контур динамического торможения обеспечивающий в случае выхода из строя механического тормоза медленное опускание груза;
На первых положениях подъема двигатель должен развивать такой пусковой момент чтобы исключалась возможность спуска номинального груза при напряжении питающей сети 90 % и в тоже время желательная минимальная скорость составила при наименьшей нагрузки не более 30 % номинального значения;
При перемещении рукоятки командоконтролера в направлении снижения в направлении снижения скорости последняя не должна повышаться даже кратковременно;
Система электрического торможения должна иметь необходимый запас обеспечивающий надежное замедление груза равного 125 % номинального при напряжении питающей сети 90 % номинального;
Скорость перемещения грузов для электроприводов переменного тока рекомендуется иметь на 30 % выше чем для привода постоянного тока при одинаковых условиях использования механизмов;
Движение груза должно происходить только в направлении установленном командоконтролером даже при неисправной схеме. В последнем случае груз может остаться неподвижным и т.д.
Основные стандарты используемые для кранового электрооборудования.
Электрооборудование. Основные понятия – ГОСТ 18311-80. ряд номинальных мощностей электрических машин – ГОСТ 12139-74. стандарты на характеристики режимов работы механизмов – ГОСТ 25835-83.
Кран должен быть снабжен конечными выключателями для автоматической остановки механизмов при подходе их к крайним положениям. На механизмах подъема обязательной является установка одного выключателя ограничивающего движение вверх.
Все механизмы кранов должны быть обеспечены механическими тормозами. На механизмах подъема и передвижения должны устанавливаться тормоза замкнутого типа автоматически размыкающиеся при включении электродвигателей и замыкающихся при их отключении.
Система управления в свою очередь должна обеспечивать необходимую последовательность переключений для реализации желаемых скоростных параметров предотвращать при этом не допустимые перегрузки и обеспечивать необходимую защиту.
Параметры регулирования систем управления неразрывно связаны с регулировочными свойствами приводного электродвигателя.
В данном случае рассматривается электрооборудование механизма подъема мостового крана общего назначения
грузоподъемностью - 5 т.
среднего режима работы с числом включений в час n = 60
скоростью подъема (опускания) груза – 017 мс.
скоростью подъема (опускания) порожнего крюка – 0147 мс.
Электрооборудование крана предназначена для управления механизмами крана освещения и сигнализации. Электрооборудования крана в зависимости от грузоподъёмности и режима работы имеет некоторые отличия по способу управления.
Пуск остановка торможение и регулировка скорости электродвигателей кранов тяжелого режима работы имеет силовое или смешанное управление(силовое и контакторное).
На мосту крана размещается пускорегулировочные сопротивления магнитные контроллеры реверсы преобразователи шкафы управления конечные выключатели ограничения передвижения крана и его тележки.
В кабине крановщика устанавливаются кулачковые контроллеры командо-контроллеры защитная панель рубильник трансформатор и автоматические выключатели освещения крана. Кабина закрытого типа оснащена отопительными приборами.
Электрическая связь между тележкой и мостом осуществляется гибким кабелем перемещающимся вдоль моста на кабельных каретках.
Защитная панель в кабине крановщика предназначена для максимальной мгновенной защиты электродвигателей а также для нулевой и конечной защиты механизмов. Защитная панель представляет собой металлический шкаф в котором установлены вводной рубильник вводной контактор многополюсные максимальны реле предохранители цепей управления и клемный блок. На стене панели размещена кнопка предназначенная для включения защитной панели. Защитная панель оборудована блок-замком с электрическим контактором.
Максимальная защита осуществляется электромагнитным реле представляющими собой максимальное токовое реле без блок-контакторов. Несколько таких реле воздействующих на один блок-контакт представляют многополюсное реле. Электромагниты реле в зависимости от соотношения мощностей защищаемых электродвигателей могут быть соединены в различные схемы. Для защиты электродвигателей от перегрузок достаточно иметь электромагнитное реле в одной фазе каждого электродвигателя. В остальные фазы электродвигателей электромагнит реле устанавливается для защиты проводов поэтому одноименные фазы нескольких электродвигателей необходимо объединить под общие электромагниты реле.
Защитная панель предназначенная для работы с магнитными контроллерами снабжена пакетными переключателями на два положения. В положения «Проверка» осуществляется проверка последовательности аппаратов магнитных контроллеров без силовой цепи подачей напряжения во всей цепи управления. В положение «Работа» пакетный переключатель устанавливается для нормальной работы крана.
Выбор привода и принципиальное решение по системе управления.
Повышение требований к крановым приводам массового применения ставит задачи значительного улучшения их технико – экономических показателей без существенного увеличения стоимости и усложнения эксплуатации. Основным направлением решения указанной задачи является применение средств полупроводниковой техники в традиционных системах в целях повышения коммутационной устойчивости контакторно – контрольной аппаратуры и реализации более рациональных режимов регулирования торможения и самовозбуждения в которых применен не управляемый диодный мост.
Для данного механизма подъема выбран электропривод с ПЧ серии АИТ.
Описание работы схемы с частотно-управляемым регулированием .
Силовая часть ПЧ включает управляемый выпрямитель UZ1 автономный инвертор UZ2 с узлом коммуникации условно показанный в виде блока U5 ведомый инвертор UZ3 ограничения обратного напряжения сглаживающий реактор L-M2 в цепи постоянного тока ПЧ с АИТ и токоограничивающий реактор L-M1. Система управления ПЧ с АИТ состоит из блока управления напряжением AV и частотой AU блока задания U1 блока обратной связи по частоте вращения двигателя U2 с входным сигналом от датчика скорости BR блока обратной связи по току U3 с входным сигналом от датчика тока UA САР электропривода представленной блоком U4 и блока токовой отсчетки UF связанного с трансформатором тока ТА.
Электропривод имеет двухзонное регулирование скорости однако максимальная скорость в системах с инверторами напряжения обычно не превышает 1.5 номинальной. Это вызвано перенапряжениями при коммутациях тока. Для ограничения перенапряжений в систему вводится нерегулируемый ведомый инвертор UZ3.
В системе регулирование до номинальной скорости осуществляется изменением выходной частоты в диапазоне 3-50 Гц и соответственно напряжения ПЧ а в верхней зоне – изменением частоты от 50 до 100 Гц при номинальном напряжении. В нижней зоне регулирования САР обеспечивает реализацию закона частотного управления с компенсацией падения напряжения на сопротивлениях статора двигателя. Переход на повышенные частоты происходит на последнем положении комадоконтроллера при малых нагрузках по сигналу от блока U3.
Плавность пуска и торможения обеспечивается датчиком темпа изменения частоты и напряжения входящих в состав САР. Тормозной электромагнит YA или двигатель гидротолкателя тормоза подключается к выводам двигателя поскольку соотношение между частотой и напряжением ПЧ обеспечивает достаточный для растормаживания тормоза ток YA. При реверсе САР выполняет сначала частотное торможение электропривода с заданным темпом а затем пуск в обратную сторону. Защита электропривода – конечная (выключатели SQ1 и SQ2) и нулевая – вынесены на реле KT1 включающее линейный контактор KMM. Для выполнения этих защит командоконтроллер имеет три контактных элемента SM1-SM3. В цепь реле KT1 введен также контакт реле максимальной скорости KV контролирующего правильную работу ПЧ. Защита от короткого замыкания в главной цепи осуществляется автоматическим выключателем QF1 а в цепях управления – выключателем QF2. Аварийное отключение в схеме производится выключателем SA1.
Современные тенденции и достоинства частотного регулирования.
Программно-аппаратный комплекс для управления сложными механизмами имеет в своем составе силовые модули (инверторы) и программируемый логический контроллер с возможностью подключения дисплея. Основа эффективной системы управления асинхронными электродвигателями - частотные преобразователи.Частотные преобразователи объединяются в сеть для обмена с программируемым логическим контроллером и устанавливаются в шкафах управления которые могут размещаться на мостовых кранах с асинхронными электродвигателями. Шкафы управления имеют стандартную степень защиты IP54 и встроенную систему термостабилизации.При необходимости система управления комплектуется кресло-пультом и кабиной оператора.Частотные преобразователи установленные на подъемные краны позволяют плавно управлять механизмами главного и вспомогательного подъёма подъёма и передвижения передвижения моста и тележки изменения вылета и поворота.
Главные достоинства системы:
снижение энергопотребления по сравнению с контакторными решениями;
большая плавность работы механизмов;
возможность достижения высокой точности позиционирования механизмов;
увеличенный диапазон регулирования скорости;
удобство в управлении;
высокая ремонтопригодность;
минимальная потребность в обслуживании;
высокая надежность;
совместимость с большинством приборов безопасности;
возможность самодиагностики;
легкость монтажа и пусконаладки.
Записка.doc
В связи с интенсификацией технологических процессов доля времени на подъемно-транспортные операции значительно возросла. Резкое повышение производительности труда которое крайне необходимо во время перехода экономики на новые условия развития и управления может быть достигнуто прежде всего путем механизации и автоматизации подъемно-транспортных операций которые менее автоматизированы чем технологические.
Подъемно-транспортные машины (ПТМ) весьма металлоемки разрушение элементов этих машин или другие неисправности могут привести к травмам. Поэтому необходимо создавать менее металлоемкие совершенные надежные и рациональные конструкции.
В связи со специфическими задачами механизации производственных процессов проектированием подбором и установкой ПТМ занято много инженерно-технических работников не только в специализированных организациях и предприятиях но и в самых различных отраслях промышленности.
Подъемно-транспортное оборудование является неотъемлемой частью практически любой схемы механизации любого производственного процесса в каждой отрасли экономики. Поэтому подъемно-транспортные машины представляют исключительный методический интерес как объекты проектирования при подготовке инженеров-машиностроителей широкого профиля.
Конечной целью проектирования разработки внедрения и применения подъемно-транспортных машин является ликвидация ручных погрузочно-разгрузочных работ и исключение тяжелого труда при выполнении основных и вспомогательных операций.
РАСЧЕТ МЕХАНИЗМА ГЛАВНОГО ПОДЪЕМА.
Кинематическая схема привода представлена на рис. 1. Электродвигатель 1 передает крутящий момент через предохранительную муфту 5 на быстроходный вал редуктора 2 на другом конце которого установлен тормоз 6. От тихоходного вала редуктора момент передается на барабан 3 через компенсирующую муфту 4.
Рис.1.Кинематическая схема привода механизма главного подъема.
Для выбора оптимального варианта привода для расчета главного механизма подъема будет рассмотрен многовариантный счет канатов диаметров барабанов и редукторов.
Высоты подъемаH = 12м
Скорость подъема груза
Режим нагруженияL2 (умеренный)
Продолжительность включенияПВ = 40%
Класс использования механизмовМ5.
Предварительный выбор электродвигателя.
Статическая мощность двигателя механизма подъема груза:
= - масса груза и крюковой подвески;
Масса крюковой подвески прототипа составляет 550 кг.
=20000+550=20550 кг.
- предварительный КПД механизма.
= 096 – КПД редуктора;
= 098 – КПД зубчатой муфты;
= 096 – КПД барабана.
Значение КПД взяты (2).
Исходя из режима нагрузки L2 и полученного значения мощности (>15кВт) из (6) стр. 77 выбираем электродвигатель модельного ряда двигателей с короткозамкнутым ротором. Выбираем двигатель 4МТKH225L8 со следующими характеристиками:
Температура окружающей средыне более 50С;
КПД выбранных полиспастов:
= 098 – КПД блоков входящих в полиспаст (4):
Усилие в канате набегающем на барабан:
g – ускорение свободного падения;
z – число полиспастов в системе;
а – кратность полиспастов;
- КПД полиспаста и обводных блоков.
Согласно ПУБЭГК (стр.27) допускается изменение коэффициента выбора диаметра барабана h не более чем на два шага (в обе стороны) по группе классификации с соответствующей компенсацией по средствам величины zр по таблице на тоже число шагов (в меньшую или большую сторону) (см. таблицу).
Группа классификации
Введем ряд шагов = -2; -1; 0; 1; 2 по zр.
Расчет на разрывное усилие каната:
Для мостового крана работающего в закрытом помещении выбирают канаты по ГОСТ 2688-80 канат двойной свивки типа ЛК-РО. Канат устойчив к перегибам однако чувствителен к образивному износу. Конструкция 6х36(1+7+77+14)+1о.с. Маркировочная группа проволок 1770 Мпа. Для рассматриваемых вариантов выбираем канаты:
d[] – диаметр каната из каталога (5);
- группа прочности (МПа);
[F] – разрывное усилие каната также из каталога.
Длина барабана при двусторонней нарезке:
определяется по формуле:
с – коэффициент ненарезанной части зависит от кратности полиспаста.
Для а = 4 – коэффициент с = 04; для а = 5 и с = 05.
- расчетный диаметр барабана;
Для выбранных вариантов расчетный диаметр барабана равен:
Далее округляем полученный диаметр до ближайшего большего из ряда R20. Диаметр менее 160 мм можно отбросить так как зубчатый венец редуктора не войдет внутрь барабана.
Полученные округленные значения:
Из полученных результатов отметим варианты по равенству диаметров каната и барабана:
Варианты длины барабана:
Исходя из соотношения (4):
что обеспечивает устойчивость на изгиб стенки барабана отбросим не удовлетворяющие условию варианты:
Таким образом после отброса расчет продолжаем по оставшимся вариантам (404-14-2).
Угловая скорость барабана:
Оставшиеся варианты имеют одинаковый диаметр барабана и следовательно одинаковые угловые скорости:
Передаточное число редуктора:
Для привода механизма подъема выбирается цилиндрический двухступенчатый горизонтальный специальный крановый редуктор типа Ц2.
Ближайшее к полученному передаточное число UС = 25. Условие что разница не должна превышать 10% выполняется:
Проверка редуктора по радиальной и консольной нагрузке:
Ближайший редуктор который для ПВ=40% имеет допустимую радиальную консольную нагрузку Fr=25-104 Н – это редуктор Ц2-500 что удовлетворяет условиям проверки.
Проверка редуктора по грузовому моменту:
Эквивалентный момент на тихоходном валу:
- расчетный момент на тихоходном валу редуктора;
- коэффициент долговечности.
- коэффициент переменности нагружения;
= 125*106 – базовое число циклов контактных напряжений;
- суммарное число циклов.
= 395 – передаточное число тихоходной ступени редуктора;
- число циклов нагружения на тихоходном валу редуктора.
- частота вращения тихоходного вала редуктора;
- машинное время работы механизма;
Статический момент на входном валу редуктора при торможении.
Момент статического сопротивления на валу при торможении:
- передаточное отношение между валом барабана и тормозным шкивом.
- КПД привода от вала барабана до тормозного шкива.
Тормозной момент создаваемый тормозом:
- коэффициент запаса по торможению. Согласно ПУБГЭК стр.32 для механизмов класса М5 =15.
Выбираем тормоз колодочный с электрогидравлическим толкателем ТКГ-300М с тормозным моментом 800 Нм. Диаметр тормозного шкива 300 мм. При монтаже тормоза необходимо отрегулировать на тормозной момент 402 Нм.тормоза составляет 55 кг.
Расчет соединительных муфт.
Ввиду того что у выбранного редуктора тихоходный вал зубчатый то зубчатую полумуфту изготавливаем по тихоходному зубчатому валу редуктора без дополнительных проверочных расчетов.
Расчетный момент муфты между электродвигателем и редуктором:
=13 – коэффициент учитывающий степень ответственности механизма М5 (Анурьев);
- коэффициент учитывающий режим работы L2 механизма (Анурьев).
Из конструктивных соображений устанавливаем нестандартную муфту типа МУВП используя пальцы и упругие втулки стандартной МУВП с Тк = 1000(Нм).
Компоновка механизма.
Размер соседства А1 между навивной частью барабана и корпусом электродвигателя не должен превышать 20 мм. Если А10 то вводится промежуточный вал либо принимается редуктор с большим межосевым расстоянием что однако бывает экономически невыгодно либо сильно увеличивает массу привода.
Размер соседства А2 между фланцем барабана и предохранительной муфтой рассчитывается по формуле:
- межосевое расстояние редуктора;
Z – число зубьев по каталогу;
– радиус вместе с толщиной фланца.
А2 = 500-06*8*46-05*372 = 348
Проверочный расчет привода механизма главного подъема.
Фактический КПД Механизма:
= 099 – КПД упругой муфты;
= 096 – КПД учитывающий потери в опорах вала барабана и потери вызываемые вескостью каната;
= 097 – КПД полиспаста блоков и подвески.
Фактическая скорость подъема груза:
= 0315 м – диаметр барабана по оси каната;
а = 4 – кратность полиспаста.
Проверка выбранного двигателя.
Поскольку график действительных нагрузок механизма не задан пользуемся усредненным графиком использования механизмов по грузоподъемности [4] построенным на основе опыта эксплуатации кранов.
Согласно графику и расчетам за время цикла (подъем и опускание груза) механизм будет работать:
С номинальным грузом =20550 кг – 2 раза - =20550 кг;
С грузом 05*=10275 кг – 4 раза - =13275 кг;
С грузом 02*=4110 кг – 2 раза - =8110 кг;
С грузом 05*=10275 кг – 2 раза - =11275 кг.
По известным зависимостям (6) определяем моменты развиваемые двигателем время пуска при подъеме и опускании груза в различные периоды работы механизма и сводим результаты в таблицу.
Масса поднимаемого груза 103кг
Момент при подъеме груза
Время пуска при подъеме груза
Момент при опускании груза
Время пуска при опускании груза
Время установившегося движения
Сумма времени пуска при подъеме и опускании груза за цикл работы механизма:
Общее время включения за цикл:
Среднеквадратичный момент:
- среднепусковой момент электродвигателя.
Среднеквадратичная мощность электродвигателя:
Следовательно выполняется условие:
Проверка ускорения и замедления механизма подъема груза.
Ускорение при пуске механизма:
= 128с – время пуска.
что соответствует рекомендуемым значениям (6).
Время торможения при опускании груза:
-коэффициент учета инерции вращающихся масс расположенных на втором третьем и последних валах механизма;
- момент инерции вращающихся масс ротора и муфт;
n – номинальные обороты электродвигателя.
Определяем путь торможения механизма:
S = по таблице 1.22 (6).
Определяем время торможения:
Замедление при торможении:
что соответствует рекомендуемым значениям (5).
РАСЧЕТ МЕХАНИЗМА ВСПОМОГАТЕЛЬНОГО ПОДЪЕМА.
Кинематическая схема механизма вспомогательного подъёма аналогична схеме механизма главного подъёма приведённой ранее.
Высоты подъемаH = 14м
Продолжительность включенияПВ = 25%
Определим мощность электродвигателя:
= - сила тяжести поднимаемого груза;
=5000*981=4901*103 Н
Gгр=1800 H -сила тяжести крюковой подвески и полиспаста;
V = 033 мс - скорость подъема;
В каталоге данные на электродвигатели даны на ПВ=40% поэтому произведем пересчет на ПВ=25%:
Из (6) выбираем для Р=149 кВт и ПВ=25% электродвигатель с короткозамкнутым ротором серии 4MTKF со следующими характеристиками:
Тип двигателя 4MTKF160LB6
Пусковой монентМ = 460 В;
Температура окружающей средыне более 40С;
Статическое усиление в канате:
а=2 - кратность полиспаста;
т=1 - число полиспастов (креплений на барабане); КПД полиспаста:
= 098 – КПД блоков входящих в полиспаст;
k = 1 – число обводных блоков.
Определим разрывное усилие:
по правилам ГГТН для режима 6К см. (5) коэффициент использования каната n=6 таким образом
Для мостового крана работающего в закрытом помещении выбираются канаты по ГОСТ 2688-80 канат двойной свивки типа ЛК-РО. Канат устойчив к перегибам однако чувствителен к образивному износу. Конструкция 6x36(1 + 7 + 77 + 14) + lo.c. ГОСТ 7668-80. Маркировочная группа проволок 1770 МПа. Для полученного разрывного усилия выбираем канат диаметром:
h = 18 - коэффициент диаметра барабана по правилам ПУБГК стр.27;
Далее округляем полученный диаметр до ближайшего большего из ряда R20.
Угловая скорость вала барабана:
- шаг винтовой нарезки барабана;
Передаточное отношение редуктора:
Ближайшее к полученному передаточное число UС = 20. Условие что разница не должна превышать 10% выполняется:
Редуктор Ц2-300 - ближайший для ПВ=40% имеет допустимую радиальную консольную нагрузку Fr=14-104 Н что удовлетворяет условиям проверки.
Эквивалентный момент на тихоходном валу редуктора не превышает допускаемый крутящий момент редуктора Ц2-400 равный =825-103 Нм. Следовательно выбранный редуктор проходит по расчетному крутящему моменту.
Таким образом редуктор Ц2-400-20-11МУ1 ТУ 24-9-488-88 подходит по всем параметрам для данного привода.редуктора 315 кг.
Требуемый тормозной момент:
Грузовой момент на валу тормозного шкива:
требуемый тормозной момент:
kтор = 15 – коэффициент запаса торможения по ПУБГК стр.32;
Тт = 16736 * 15 = 25104 Нм.
Выбираем тормоз колодочный с электрогидравлическим толкателем ТКГ - 200М с тормозным моментом 300 Нм. Диаметр тормозного шкива 200 мм. При монтаже тормоз необходимо отрегулировать на тормозной момент 25104 Нм.тормоза не более 30 кг.
Расчет механизма подъема (проверочный).
Фактический КПД механизма:
= 025 м – диаметр барабана по оси каната;
a = 2 – кратность полиспаста.
Натяжение ветви каната набегающей на барабан:
Gsp=1800 H - сила тяжести грузоподъемника
т = 2 - число полиспастов.
Qгр = 49010 Н - сила тяжести груза
Статический крутящий момент на валу барабана при подъеме:
С = 2 - число ветвей каната закрепленных на барабане
Статический момент на подъем приведенных к валу двигателей:
к = 15 - коэффициент запаса торможения;
М =15-22031-096 = 31724 Нм.
Динамический момент на валу двигателя при подъеме груза:
- коэффициент динамичности;
- ускорение (замедление) обеспечиваемое системой управления двигателем.
Динамический момент на тихоходном валу редуктора:
Проверка прочности грузового каната:
Запас прочности каната:где Рр= 1015 кН - разрывное усилие каната в целом.
Канат двойной свивки типа ЛК-06х19 проволок с одним органическим сердечником ГОСТ 3077-80
S= 165815 Н - напряжение ветви каната набегающей на барабан.
По правилам ГГТН коэффициент запаса прочности каната для среднего режима работы группа - М5 по ГОСТ 25546-82: Кдоп=6
Расчет блоков полиспаста и обводных блоков механизма подъема:
Наименьший допускаемый диаметр блока по дну канавки выбирают в зависимости от диаметра каната:
l=20 - коэффициент зависящий от типа подъемного устройства и режима его работы ( )
D6 =135-(20-1) = 2565 мм
Диаметр блока полиспаста конструктивный выбирается из ряда стандартных значений: D6n=260 мм.
РАСЧЕТ МЕХАНИЗМА ПЕРЕДВИЖЕНИЯ ТЕЛЕЖКИ.
Схема привода механизма передвижения тележки представлена на рис. 1. Фланцевый электродвигатель 2 со встроенным тормозом закреплённый на раме тележки 1 соединен с навесным редуктором 3 который передаёт крутящий момент промежуточному валу 4 через зубчатую муфту 5. На промежуточном валу 4 жестко закреплено колесо 6. Тележка передвигается по крановым рельсам моста 7.
Грузоподъемность механизма главного подъёмаmг=3 0000кг;
Грузоподъемность вспомогательного механизмаmв=5000 кг;
Скорость передвижения тележкиV=067 мс (40ммин);
Режим нагруженияL2(умеренный);
Продолжительность включенияПВ=40%;
Выбор ходовых колес:
Определение массы тележки:
На основании справочных данных (1) с. 32 т.2 масса тележки вычисляется как:
где 03 - коэффициент массы тележки;
Вес тележки без груза:
Вес тележки с грузом:
Масса тележки с грузом:
Давление на ходовое колесо:
z = 4 – количество ходовых колес.
согласно (1) т.2 с.319 примем ходовое колесо со следующими характеристиками (небольшой запас по давлению нужен на тот случай если центр тяжести окжется не по центру тележки после проведения компоновки):
Характеристика ходового колеса.
Давление на ходовое колесо
Внешний диаметр Dxkmm
Посадочный диаметр dmm
Плечо трения качения
Диаметр реборды Dmaxmm
Выбор электродвигателя.
Расчет сопротивления передвижению тележки с грузом:
Сопротивление трения:
кр - коэффициент сопротивления реборды для троллейного токоподвода
кр = 25 из (1 )с.422
Сопротивление от уклонов крановых путей:
а =0001 - предполагаемый уклон пути;
Полное статическое сопротивление передвижению крана с грузом:
С учетом предварительного КПД:
- КПД редуктора муфты подшипника.
Для классов использования не выше М6 (4М по обозначению 1992г) возможно использование общепромышленных двигателей с повышенным скольжением и со встроенным тормозом серии 4АСЕ для избежания проскальзывания колес. Из (6) стр.85 выбираем двигатель со следующими характеристиками:
Тэд - номинальный момент электродвигателя;
Угловая скорость ходового колеса:
Ближайшее к полученному передаточное число равно U =25. Условие что разница не должна превышать 10% выполняется:
Фактическая скорость тележки тогда составит:
Эквивалентный момент редуктора на тихоходном валу:
кд - коэффициент долговечности;
- расчетный момент на тихоходном валу редуктора.
ко - коэффициент переменности нагружения;
zp - суммарное число циклов;
z0 =125-106 - базовое число циклов контактных напряжений.
zt - число циклов нагружения на тихоходном валу редуктора;
U т = 31 - передаточное число тихоходной ступени редуктора.
- частота вращения тихоходного вала редуктора.
машинное время работы механизма: t =12500 ч
Эквивалентный момент на тихоходном валу редуктора не превышает допускаемый крутящий момент редуктора ЩЗУвкф-125 равный Тд=500 Нм. Следовательно выбранный редуктор проходит по расчетному крутящему моменту.редуктора равна 73 кг.
Проверка двигателя по пусковому моменту.
Динамический момент сопротивления вращению электродвигателя во время пуска:
где J1 - момент инерции частей вращающихся на первом валу.
где Jмуф = 0002 кг*м2 – момент инерции муфты.
tn=Va - время пуска (торможения). Согласно (1) т.2 стр.324 для грузоподъёмности 20000 кг и условий работы крана.
Пусковой момент двигателя равен М =63 Нм следовательно условие пуска выполняется.
Коэффициент запаса сцепления:
Коэффициент запаса сцепления приводных колес с рельсом расчитываете: по следующей формуле:
[к]сц - допускаемый коэффициент сцепления.
Для помещений (без ветровых нагрузок) из (3) т.1 стр. 94 [к]сц =11.
Fcц - сила сцепления приводных ходовых колес с рельсом
Ft=735-104H - вертикальная сила без груза;
ксц=02 коэффициент трения для кранов в помещении по сухим рельсам из (8) стр.12;
zпр=2 - количество приводных колес;
z=4 -общее количество колес.
Fcm - сила статического сопротивления перемещения тележки без груза и без трения в подшипниках приводных колёс
Таким образом коэффициент сцепления равен:
кр = 2 - коэффициент реборды.
Fдин - сила динамического сопротивления передвижения без груза
Расчет соединительной муфты:
Расчетный момент муфты стоящей на промежуточном валу между колесом и редуктором:
к1 = 13 - коэффициент учитывающий степень ответственности механизма
к2 = 12 - коэффициент учитывающий режим работы L2 механизма (7).
Расчет тормозного момента:
Тормозной момент рассчитывается по следующей формуле:
Тин - момент инерции на валу электродвигателя
Тс - статический момент на валу электродвигателя
Таким образом тормозной момент равен:
В электродвигателе 4АС112МАЕ6 тормоз может быть отрегулирован до 40 Нм следовательно он обеспечивает требуемый тормозной момент.
Определение наибольшего изгибающего момента балки от действия ходовых колес тележки.
Из расчета механизма передвижения тележки известно что вес тележки с грузом равен:
Однако из ходя из компоновки механизма видно что вес распределен неравномерно между колесами тележки. Из измерений определим расстояния от центра тяжести тележки до опорных колес: а1 =17 м а 2=14 м.
Определим как следует расположить тележку что бы получить наибольший изгибающий момент (рис. 1).
Левая опорная реакция будет равна:
а изгибающий момент под первым колесом равен:
Для определения координаты х соответствующую максимальному значению изгибающего момента производную от этого момента по х необходимо приравнять к нулю:
а наибольший изгибающий момент:
Подставив численное значение пролета l = 225 получим:
x1= 104 м и М1mах = 13*106 Нм.
Выражение для момента представляет собой уравнение параболы нулевые точки которой
х0 = 0 и х0 = l – a1 = 208 м.
Аналогично для второго колеса тележки рассмотрим положение при котором оно располагается на расстоянии х от правой опоры В. Опорная реакция изгибающий момент будут равны:
После дифференцирования получим:
Таким образом после подстановки численных значений получим:
Нулевые точки параболы х0 = 0 и х0 =1-а2 =211 м. Сравнивая значения выбираем наибольший изгибающий момент:
Определение вертикального момента сопротивления сечения балки моста.
Исходя из условия прочности при работе на изгиб для одной балки:
m - коэффициент условий работы (4) стр. 336.
m1 =075 - коэффициент учитывающий степень ответственности элемента и возможные последствия при его разрушении;
т2 = 08 - коэффициент учитывающий возможные повреждения элементов при транспортировке и монтаже;
т3 = 09 - коэффициент учитывающий несовершенство расчёта.
Определение предварительных параметров сечения.
Высоту балки коробчатого сечения принимают в пределах (4) стр. 356:
Примем предварительно h=14 м.
Ширину горизонтального листа балки из условий обеспечения горизонтальной жесткости принимают в пределах:
Предварительно примем ширину B=055 м.
Предварительно ширина листа s для полого прямоугольного сечения определяется по формуле (рис. 2):
Проверка устойчивости для полого прямоугольного сечения балки.
Гибкость определяется по формуле:
- коэффициент опоры (для одного жестко заделанного конца);
- коэффициент формы (при постоянном моменте инерции).
- радиус инерции для полого прямоугольного сечения.
Итак гибкость равна:
Для стали Ст.3 (9) стр. 410 следовательно и формула Эйлера применима:
осевой момент инерции сечения.
расчетная сжимающая сила рассчитывается по формуле:
q=15 кНм - распределённая нагрузка по металлоконструкции крана;
n = 11 - коэффициент учитывающий вес рельса.
Таким образом данным сечением устойчивость обеспечена.
Проверка на совместное действие сжатия и изгиба:
Расчет сечения главной балки моста на горизонтальные нагрузки.
За основную систему сил примем две полу рамы в месте разреза прикладывается лишнее неизвестное х1 (рис. 3):
Неизвестные x1 являющиеся изгибающими моментами определяются из уравнения:
Для определения перемещений по способу Верещагина строим эпюры М от сосредоточенной нагрузки от колёс тележки (ускорение крана 02 мс2):
Неизвестные изгибающие моменты равны:
- отношение пролета главной балки к осевому расстоянию между ходовыми колесами концевой балки. Таким образом получим:
Наибольшие изгибающие моменты (рис. 3):
По середине главных балок:
На концах главных балок
Исходя из полученных значений подбираются параметры сечений концевых балок концов главной балки.
Произведем проверку сечения середины главной балки на горизонтальные нагрузки. Горизонтальный момент сопротивления сечения равен:
Требуемый момент сопротивления при действии горизонтального изгибающего момента:
Таким образом условие выполнено.
Нормальные напряжения в главной несущей балке.
Для верхних волокон:
= 11 – динамический коэффициент учитывающий скорость крана (для 60-120 ммин) (10) стр.105.
= 12 – динамический коэффициент учитывающий режим эксплуатации (для среднего).
Динамические прогибы и нагрузки.
В качестве динамической схемы принимаем схему груз - упругая связь – мост.
Коэффициент динамичности:
t0 - время нарастания нагрузки на металлоконструкции моста
Т - период колебаний металлоконструкции моста.
тк=311-105 Н - приведенная масса крана ;
тг = 2 *105Н - приведенная масса груза;
- жесткость конструкции моста.
Время нарастания нагрузки на мост:
v0=015 мс - скорость подъема груза;
- статическое удлинение каната;
z =8 - число ветвей полиспаста;
Fk = 10461*10--6 м2 - площадь сечения проволок каната;
Ек = 21*105 МПа - модуль упругости каната.
РАСЧЕТ МЕХАНИЗМА ПЕРЕДВИЖЕНИЯ КРАНА.
Кинематическая схема механизма состоит из электродвигателя 1 передающего через шкив тормоза 3 крутящий момент на быстроходный вал редуктора 2; тихоходный вал редуктора соединен через компенсирующую муфту 5 с промежуточным валом 4 и ходовым колесом 6.
Рис.1 Кинематическая схема привода механизма передвижения крана.
Определение предполагаемой массы крана :
На основании данных (4) с. 357 масса половины кранового моста для данной грузоподъёмности и пролёта равна 12 т следовательно полный вес моста равен 24 т. Вес двух концевых балок рекомендуется принимать 025 от веса моста. Вес механизмов (два механизма подъёма и два механизма передвижения) составит (табл.1)
Массы элементов привода крана кг.
Таким образом полная предполагаемая масса крана без груза составит:
тк = 12*2 + 025*12*2 + 21 = 321 т.
Масса крана с грузом:
ткг = тк + тг = 321*103+20*103==521*103кг.
Fкг = mкг*g = 521*103*98 = 511*105H
z = 4 - количество ходовых колес.
согласно (1) т.2 с.319 примем ходовое колесо со следующими характеристиками (табл. 2):
Выбор электродвигателя:
Расчет сопротивления передвижению крана с грузом:
кр - коэффициентсопротивления реборды для троллейного токоподвода
к =25 из (1) с. 422;
- КПД редуктора муфты подшипников колеса.
В кранах с пролётом более 10 м рекомендуется (4) использовать раздельный привод для механизма передвижения. Однако вводится коэффициент неравномерности нагружения для различных положений тележки.
Для классов использования не выше М6 (4М по обозначению 1992г) возможно использование общепромышленных двигателей с повышенным скольжением для избежания проскальзывания колес АИРС. Из технического каталога Владимирского электромоторного завода выбираем двигатель со следующими характеристиками:
к = 13 - коэффициент учитывающий степень ответственности механизма
к2 = 12 - коэффициент учитывающий режим работы L2 механизма
Из (7) т.2 выбираем муфту с номинальным моментом 125 Нм по ГОСТ 21424-75.
Ближайшее к полученному передаточное число равно Uc = 25. Условия что разница не должна превышать 10% выполняется:
- коэффициент долговечности;
к0 - коэффициент переменности нагружения;
- суммарное число циклов;
- 125*106 – базовое число циклов контактных напряжений.
Uт = 42 - передаточное число тихоходной ступени редуктора.
частота вращения тихоходного вала редуктора:
машинное время работы механизма: t=12500 ч
Ближайший подходящий редуктор Ц2-300 имеет допустимый крутящий момент равный для передаточного числа 40 и частоты вращения входного вала до 1500 обмин Tо=23 кНм. Следовательно выбранный редуктор проходит по расчетному крутящему моменту. Полное обозначение редуктора Ц2-300- 40-12М.
Проверка двигателя по пусковому моменту:
J1 – момент инерции частей вращающихся на первом валу.
Jмуф=0002 кг*м2 - момент инерции муфты.
J1 =0067+0002=0069 кг * м2;
tn=Va- время пуска (торможения). Согласно (1) т.2 стр.324 для грузоподъёмности 20000 кг и условий работы крана.
Пусковой момент двигателя равен Тп = Т 35 =261 Нм следовательно условие пуска выполняется.
Коэффициент запаса сцепления приводных колес с рельсом расчитывается по следующей формуле:
Fсц - сила сцепления приводных ходовых колес с рельсом.
ксц= 02 коэффициент трения для кранов в помещении по сухим рельсам из
zпр =2 - количество приводных колес;
z = 4 -общее количество колес.
Fсm – сила статического сопротивления перемещения тележки без груза и без трения в подшипниках приводных колес.
Определим момент на который следует отрегулировать тормоз. Согласно ПУБЭГК стр. 32 при двух и более тормозах коэффициент запаса торможения принимают:
Выбираем тормоз ТКГ- 160 с расчетным тормозным моментом 100 Нм и демпфирующим узлом . Тормоз отрегулировать на момент 2784 Нм.
Описание схемы механизации.
На листе представлена схема механизации механосборочного цеха завода металлоконструкций.
В цехе осуществляется сварка и сборка различных узлов металлоконструкций в том числе модуля ВЗП-4-1700 для газовой промышленности. Его полная масса в собранном виде составляет 24600 кг. он в свою очередь состоит из четырех основных узлов:
) Модуль нижний (13 т.)
) Модуль верхний (12 т.)
) Блок катковый (500 кг.)
Она осуществляется в следующем порядке. Сборка металлоконструкций осуществляется из комплектующих которые поступают из других цехов и заводов или изготавливаются на месте. Комплектующие и металл поступают в цех как железнодорожным так и безрельсовым транспортом. Непосредственно на этом участке осуществляется разгрузка комплектующих и металла краном гп 5т. Для окончательного перемещения и погрузки узлов необходимо использовать механизм главного подъема грузоподъемностью 30 т.
Из металла осуществляется сварка на стапелях. После чего происходит предварительный контроль качества продукции непосредственно на месте изготовления продукции.
После окончания сборки и проверки металлоконструкции покидают цех на специальных машинах.
ТЕХНОЛОГИЧЕСКАЯ ЧАСТЬ.
Тормозной шкив предназначен для передачи тормозного момента на валы механизма. Конструктивно тормозной шкив состоит из цилиндрического обода ступицы и диска. При торможении к цилиндрическому ободу прижимаются колодки а возникающие силы трения способствуют появлению тормозного момента. Диаметры тормозных шкивов 200 300 400 500 600 и 800 мм. Диск по окружности имеет отверстия для крепления с полумуфтами. Размеры отверстий зависят от диаметров соединения пальцев. Ступица имеет отверстие и шпоночный паз для передачи крутящего момента на вал.
Тормозной шкив устанавливается на входных валах редукторов вследствие того что для входных валов характерен минимальный крутящий момент при максимальной частоте вращения .
Анализ технологичности конструкции.
Для установки на валу шкив имеет цилиндрическое посадочное отверстие со шпоночным пазом. Тормозные шкивы присоединяют к зубчатым муфтам для чего в торцовых поверхностях предусмотрены выточки и несколько отверстий расположенных по окружности.
Наружную поверхность тормозного шкива для повышения срока службы подвергают поверхностной закалке на глубину 3-5 мм до твердости: HRC 38 -52 и шлифуют с обеспечением шероховатости 10 мкм. Посадочное отверстие выполняют по квалитету при чистоте поверхности 6-го класса. Должна быть соблюдена соосность наружной поверхности с посадочным отверстием ( радиальное биение не более 005 мм ) торцовое биение шкива не более 002 мм на 100 мм радиуса.
Способ получения заготовки.
Тормозные шкивы изготовляют преимущественно из стали 55 ЛЦ литьем в песчанную форму без отверстия. Вся отливка размещается в нижней опоке вниз полостью которая образуется одним кольцевым стержнем . Плоскость разъема формы совпадает с торцевой плоскостью шкива.
Маршрут обработки детали.
При составлении маршрута обработки пользуемся следующим правилом : сначала обрабатывают поверхности принятые за чистовые технологические базы затем обрабатываются поверхности в последовательности обратной их степени точности. Наиболее ответственные поверхности обрабатывают на заключительном этапе процесса. На основе этого составляется маршрут который представлен в таблице:
Карта эскизов приведена в приложении.
Расчет операционных припусков и межоперационных размеров.
Проведем расчетно-аналитический метод определения припуска на обработку поверхности обода тормозного шкива 300 ( -029 ). Обработка состоит из: получения заготовки черновом и чистовом обтачивании.
Таблица расчетных данных:
Элементная поверхность детали и маршрут ее обработки
Элементы припуска мкм
Допуск на изготовления ТД
Принятые размеры по переходам мм
Высота неровностей профиля Rz
Глубина дифектн. поверхностного слоя h
Суммарное отклонение расположений поверхностей
Погрешность установки заготовок
Припуск на черновое точение
Припуск на чистовое точение
Zmin = 2*[(250+240)++20] = 1440мкм
Припуск на шлифование
Zmin = 2*[(25+25)+] =120мкм
Zmin = 8460+185+29 = 8674мкм
Принимаем 2 Zном = 9000мкм
Расчет режимов резанья.
Операция 015 - токарная черновая обработка:
Рассчитывается по эмпирической формуле
- период стойкости инструмента;
t – глубина резания;
- поправочный коэффициент;
m x y – показатели степени.
Назначим глубину резания t = 22мм (по припуску на черновую обработку) подачу выберем из таблицы №11 стр.266 [7] S = 08 (ммоб). Коэффициент показатели степени берем из таблицы №17 стр.269 [7].
= 350; y = 035; m = 020
Поправочный коэффициент:
- коэффициент учитывающий качество обрабатываемого материала см. табл. № 1 - 4 стр.261 - 263[1];
- коэффициент отражающий состояние поверхности заготовки см. табл. № 5 стр.263[1];
- коэффициент учитывающий качество материала инструмента
см. табл. № 6 стр.263[1].
- коэффициент характеризующий группу стали по обрабатываемости и показатель степени см. в таблице № 2 стр. 262 [7].
Учитывая что мы растачиваем внутреннюю поверхность вводим поправочный коэффициент 09 см. таблицу № 17 стр. 270 [7].
Частота вращения заготовки:
Ср – постоянная см. табл. №22 стр.273 [7];
Кр – поправочный коэффициент;
Рz:Cp = 300x = 1y = 075n = -015
Рy:Cp = 243x = 09y = 06n = -03
Рx:Cp = 339x = 1y = 05n = -04.
- значения коэффициентов см. табл. № 9 10 и 23 стр. 264-275 [7].
Рz = 10*300*221*05075*109-015*1335=2593(H)
Рy = 10*243*2209*0506*109-03*1543=1232(H)
Рz = 10*339*221*0505*109-04*2713=2191(H).
По рассчитанной мощности и частоте вращения шпиделя выбираем станок токарный 16К20.
Операция 020 – Сверление:
D = 32 мм см. таблицу № 23 стр.271 [7].
t = 05*D = 05*32 = 16 мм
S = 03 мм см. таблицу № 25 стр.277 [7].
C = 98;q = 04;y = 05m = 02.
T = 70 см. таблицу № 30 стр. 283 [7].
K = 17*11*085 = 1445
= 00345;q = 2;y = 08 см. таблицу № 32 стр. 285 [7].
Из вышеизложенного известно что:
D = 32 мм см. таблицу № 23 стр.271 [7];
S = 03 мм см. таблицу № 25 стр.277 [7];
На основании рассчитанного резанья выбираем станок вертикально сверлильный 2Н125Л2.
Операция 035– Протягивание:
Sz = 01 мм см. таблицу № 64 стр. 173 [7].
Vтаб = 10ммин = 017 мс см. таблицу № 52 стр. 299 [7].
Сила резанья приходящаяся :
Р = 325 (Н) см. таблицу № 54 стр.300 [7].
- наибольшая суммарная длина лезвий всех одновременно режущих зубьев.
Определим периметр резанья:
В – периметр резанья мм;
zc – число зубьев в секции протяжки;
z1 – наибольшее число одновременно режущих зубьев.
t – шаг зубьев протяжки.
z1 = 8210 = 82 округляем до 9.
Рz = 325*180=58500 (Н).
На основании рассчитанной силы резанья выбираем станок горизонтально протяжной 7Б55.
Операция 040 – Сверление:
Операция 045 –Зенковка
На данной операции происходит снятие фасок
Операция 050 – Токарная чистовая обработка:
Назначим глубину резания t = 05мм подачу выберем из таблицы №14 стр.266 [7] S = 025 (ммоб). Коэффициент показатели степени берем из таблицы №17 стр.269 [7].
= 340; y = 020; m = 020
Рz = 10*300*03*025*3622*074 = 973(H)
Рy = 10*243*05*025*3622*0365=353(H)
Рz = 10*339*05*025*3622*0151=122(H).
Операция 055 – Шлифование:
Выбираем белый электрокорунд марки 15А зернистость 50-40 с твердостью С на керамической связке типа ПП.
Dкр=350 Bкр=100 d=203
Шлифование с продольной подачей на каждый ход.
Описание конструкции и принципа работы поворотных
пневматических тисков.
При вращении рукоятки вращается винт подвижной губки осуществляя предварительный зажим обрабатываемой заготовки.
При дальнейшем вращении рукоятки подпружиненный плунжер воздействуя на золотник открывает доступ сжатого воздуха на верхнюю полость пневмоцилиндра. При этом шток поршня через рычаг обеспечивает окончательный зажим заготовки подвижной губкой.
Технические характеристики станочного приспособления
Наибольшее расстояние между губками мм 240
Усилие зажима при давлении воздуха 04 МПа Н 6000
Диаметр цилиндра мм 320
Рис. 9 Тиски поворотные пневматические
9.2. Расчет усилия зажима детали в приспособлении
Рис. 10 Расчетная схема усилия зажима
Заготовка установлена горизонтальной и боковой поверхностями. Сила резания стремится повернуть заготовку вокруг т. О чему препятствует сила трения (рис. 10).
Если Рз не совпадает с центром тяжести опорного треугольника:
uде abc - коэффициенты которые в сумме равны единице их находят из уравнения статистики.
Выбранное станочное приспособление удовлетворяет для силы закрепления = 3370 Н так как для тисков поворотных пневматических по техническим характеристикам усилие зажима при давлении воздуха 04 МПа=6000 Н
Рис. 11 Схема рычажных зажимных механизмов для поворотных пневматических тисков
Из данной расчетной (кинематической) схемы (рис. 11) получаем уравнение для расчета силы на приводе.
Зная что получим требуемое Р при полученном R.
Получаем что Р давление сжатого воздуха 01 МПа. А так как подается давление воздуха 04 МПа то устанавливаем понижающий редуктор перед тисками.
Таким образом делаем вывод что тиски пневматические поворотные подходят для применения в качестве станочного приспособления при сверлильной операции.
ПРОМЫШЛЕННАЯ ЭКОЛОГИЯ
Обеспечение безопасности труда при эксплуатации грузоподъемных машин.
Одной из основных задач при эксплуатации ПТМ является контроль технического состояния обеспечивающего безопасную их работу. Для решения этой задачи организуется государственный и местный технический надзор.
Государственный надзор осуществляется инспекторами соответствующих инспекций а местный — ИТР закрепленными приказом по предприятию.
Правилами безопасной эксплуатации подконтрольных ПТМ предусматривается персональная ответственность за содержание ПТМ и оборудование в исправном состоянии; за организацию безопасного производства работ; за управление машиной и ее обслуживание; за осуществление технического надзора.
Лицо отвечающее за техническое состояние ПТМ организует периодические осмотры технические обслуживания и ремонты обученным и аттестованным персоналом; контролирует ведение журнала осмотров и устранения неисправностей; периодическую проверку знаний обслуживающего персонала с регистрацией в журнале; подготовку машин к техническому освидетельствованию; хранение паспортов и технической документации на машины.
Ответственный за безопасное производство работ контролирует использование грузозахватных приспособлений и тары; выдает указания крановщикам и стропальщикам о месте порядке и габаритных размерах грузов; привлекает к работе обученный и аттестованный персонал проводит инструктаж по безопасному выполнению работ; запрещает работу в особо опасных условиях без наряда-допуска.
Лица осуществляющие управление машинами и их обслуживание (крановщики слесари электромонтеры стропальщики сигнальщики) допускаются к работе приказом по предприятию (цеху) после профессиональной подготовки аттестации с соответствием по возрасту и состоянию здоровья. При переходе на другой вид машины или при перерывах в работе проводится переподготовка и повторная проверка знаний.
Инженерно-технический работник по надзору осуществляет контроль за техническим состоянием и безопасной эксплуатацией ПТМ; проводит освидетельствование машин грузозахватных приспособлений и тары; выдает разрешение на ввод в эксплуатацию; ведет учет и освидетельствование машин не подлежащих регистрации; выдает предписание и осуществляет контроль их выполнения а также предписаний органов технадзора; контролирует выполнение графиков технических обслуживании и ремонтов наличие инструкций у обслуживающего персонала соблюдение порядка допуска к управлению и обслуживанию машин; участвует в комиссии по аттестации и периодической проверке знаний персонала; принимает меры по устранению неисправностей и нарушений инструкций (вплоть до остановки машин).
К основным мероприятиям по техническому надзору относят: регистрацию получение разрешения на допуск к работе периодическое техническое освидетельствование контроль за техническим состоянием и организацией управления ПТМ а также методами производства работ.
Регистрацию в органах технадзора проводят на всех подконтрольных ПТМ. Не регистрируют краны всех типов с ручным приводом управляемые с пола мостовые электрические и поворотные консольные краны грузоподъемностью до 10 т простейшие стреловые краны ручные и электрические тали лебедки и др. Все они подлежат местному техническому надзору. Регистрацию проводят на основании заявления руководства предприятия паспорта машины и акта на выполнение монтажных работ. После реконструкции ремонта передачи грузоподъемной машины другому владельцу и перестановки на новое место проводят ее перерегистрацию.
Разрешение на допуск к работе грузоподъемных машин подлежащих регистрации в органах технадзора получают: вновь зарегистрированные машины; после монтажа на новом месте; после реконструкции (модернизации) или ремонта металлоконструкции машины. На машины с местным техническим надзором это разрешение выдается ответственным за эксплуатацию ИТР на основании документации завода-изготовителя и результатов технического освидетельствования.
Техническое освидетельствование грузоподъемных машин приспособлений и тары производится с регламентированной периодичностью и величиной ”* испытательной нагрузки для обеспечения работоспособности и безопасности производства работ.
При эксплуатации ПТМ обеспечивается высокий уровень безотказной работы. Однако при их эксплуатации случаются аварии и несчастные случаи которые делят на следующие виды: аварии без травмирования людей; аварии с травмированием людей; несчастные случаи связанные с авариями. Все они расследуются в установленном порядке с анализом причин и разработкой рекомендаций по их предотвращению.
Для предупреждения аварий и несчастных случаев на ПТМ устанавливают приборы безопасности и блокировочные устройства. Так грузоподъемные краны оборудуются концевыми выключателями ограничителями подъема стрелы ограничителями и указателями грузоподъемности ограничителями поворота (для башенных кранов) креномерами (для самоходных и прицепных стреловых кранов) сигнализаторами опасного напряжения анемометрами (приборы для автоматического включения сирен и противоугонных устройств при достижении предельной скорости ветра) ограничителями перекоса (для мостовых и козловых кранов) противоугонными устройствами (для кранов на рельсовом пути).
Содержание приборов и устройств обеспечивающих безопасную работу машин в работоспособном состоянии и строгое выполнение установленных правил эксплуатации ПТМ позволяет практически исключить аварийные ситуации и травмирование обслуживающего персонала.
Техника безопасности при работе на мостовых кранах
В процессе трудовой деятельности человека в производственных условиях не исключены несчастные случаи. Несчастным случаем называется происшествие при котором в результате внешнего внезапного воздействия на человека (механического теплового электрического химического) произошло повреждение организма или нарушилось его нормальное функционирование. Повреждения организма называемые травмами могут быть в виде ушибов и ранений тепловых и химических ожогов поражений электрическим током обморожения и т. п.
По силе поражения человека различают микротравмы когда в результате повреждения организма человек не теряет трудоспособности; травмы с временной нетрудоспособностью; тяжелые травмы приводящие к частичной или полной потере трудоспособности т. е. к инвалидности; травмы со смертельным исходом.
Профессиональным заболеванием называется постепенное ухудшение здоровья человека в результате неблагоприятных производственных условий например шума вибрации пыли дыма. Чтобы предупредить несчастные случаи на производстве необходимо знать причины производственного травматизма и способы их устранения.
Различают технические организационные и санитарно-гигиенические причины. К техническим причинам относятся:
а) конструктивные недостатки электрооборудования механизмов и транспортных устройств;
б) несовершенство технологического процесса;
в) несовершенство или отсутствие ограждений предохранительных устройств и блокировок. К организационным причинам относятся:
а) нарушение производственных инструкций и технологического процесса;
б) неправильная организация труда и рабочих мест;
в) применение несоответствующего инструмента приспособлений и оборудования;
г) отсутствие правильного руководства со стороны технического персонала.
К санитарно-гигиеническим причинам относятся:
а) нарушение окружающей среды в производственном помещении — очень низкая или очень высокая температура высокая влажность ветер сквозняки;
б) несоответствующее искусственное освещение — слишком сильное или недостаточное например применение люминесцентных ламп для освещения кранов о чем сказано выше;
в) недопустимая загрязненность воздуха пылью газами или парами;
г) наличие вредных радиоактивных или электромагнитных излучений;
д) недопустимый шум или недопустимая вибрация;
е) нарушение рабочими правил личной гигиены антисанитарное состояние производственного помещения;
ж) неудовлетворительный медицинский контроль за состоянием здоровья рабочих.
Рабочим местом считается место постоянного или периодического пребывания работающего для осуществления производственного процесса. Рабочим местом машиниста мостового крана является кабина. Организация рабочего места заключается в выборе рабочей позы и в размещении органов управления краном. При правильно выбранной рабочей позе например сидя или стоя которая зависит от характера движений крановщик выполняет работу с минимальной затратой энергии совершая безопасные движения с наименьшей утомляемостью и неослабным вниманием. Рабочая поза должна быть устойчивой чтобы рабочий не прилагал чрезмерных мышечных усилий.
Очень важно в организации рабочего места чтобы органы управления краном были правильно расположены в рабочей зоне крановщика. Органы управления надо располагать так чтобы по возможности свести рабочие движения при управлении краном к движению предплечья и кистей рук допуская движение плечевого сустава только в виде исключения. Особенно важно обеспечить персонал необходимым инструментом приспособлениями и защитными средствами при наличии которых работа будет протекать уверенно безопасно и с высокой производительностью.
Повышение производительности труда крановщика которая в конечном счете определяет производительность крана достигается улучшением условий его работы — комфортом и состоянием окружающей среды: климатом уровнем звука и вибрации запыленностью освещенностью и видимостью.
Понятие «климат» определяется температурой влажностью степенью излучений и скоростью движения воздуха. Для нормальной жизнедеятельности человека необходимо чтобы температура его тела была постоянной — около 37 °С а тепловой баланс тела выравнивался за определенный промежуток времени т. е. восприятие тепла должно быть таким как и отдача его в окружающую среду. На теплообмен влияет климат который является благоприятным тогда когда для обеспечения теплового баланса не требуется применения специальных регулирующих устройств и неблагоприятным когда без применения таких устройств не может наступить равновесия между восприятием и отдачей тепла. Тепловые излучения — это излучения энергия которых распространяется невидимыми глазом человека инфракрасными лучами. Источниками тепловых излучений являются все нагретые тела: расплавленные и нагретые металлы работающие электродвигатели крановые резисторы осветительные лампы (95 % энергии ламп накаливания тратится на нагрев и только не более 5 % — на световое излучение).
Лучистая тепловая энергия воздухом почти не поглощается а передается от более нагретых тел к поверхности менее нагретых повышая их температуру. Воздух производственных помещений должен иметь не слишком высокую температуру и влажность и определенную подвижность. Санитарными нормами установлены предельно допустимые пределы температур в зависимости от характеристики производственных помещений в отношении избытка тепла и категории работы в различные периоды года. При температуре 18—20 °С в организме человека наилучшим образом осуществляется терморегуляция т. е. поддержание постоянной температуры тела на уровне около 37 °С. Такой климат вполне возможен в механических цехах машиностроительных заводов и ремонтных цехах вообще.
В литейных кузнечных термических и прокатных цехах климат всегда будет более неблагоприятный вследствие большого выделения теплоты дыма сернистого газа. Относительная влажность определяемая как отношение содержания водяных паров воздуха к их максимально возможному содержанию в процентах характеризует влажность воздуха при определенной температуре. Влажность воздуха в значительной мере влияет на теплообмен организма человека на отдачу тепла испарением.
Подвижность воздуха определяемая скоростью его движения влияет на охлаждение человека при температуре воздуха до 35—36 °С т. е. более низкой чем температура тела. При более высокой температуре воздуха (до 40 °С) и большей его подвижности вместо охлаждения происходит внешний подогрев тела а для охлаждения его требуется дополнительное выделение пота следовательно потеря влаги. Если вблизи человека находятся источники тепла то такое излучение может вызвать перегрев кожи и общий перегрев тела.
При значительном перегреве организма возникает опасное заболевание связанное с нарушением работы сердечно-сосудистой системы называемое тепловым ударом который в тяжелых случаях может быть смертельным.
В зависимости от наличия в помещении источников тепла и опасности перегрева для поддержания нормального микроклимата применяется вентиляция или более совершенное средство — кондиционирование воздуха — подача в помещение например кабину крана очищенного от пыли и примесей воздуха с определенной температурой и влажностью.
Вентиляция и кондиционирование воздуха не защищают организм от тепловых лучей. Защиты кабины от теплового излучения осуществляется экранами из таких материалов как асбест асбестоцемент или шифер. Защита кабины от шума производится соответствующими материалами слабо проводящими звук. Крановщику нет необходимости слышать грохот кузнечного или литейного цеха — сигналы ему подают руками. В его распоряжении звуковой сигнал для работающих внизу сам крановщик не обязательно должен его слышать.
Обеспечение акустической безопасности при эксплуатации мостового крана.
Звуковым давлением называется то дополнительное давление воздуха которое возникает при прохождении через него звуковых волн. Единицей звукового давления служит ньютон на квадратный метр (Нм2). Силой звука называется количество звуковой энергии проходящей в 1 с через площадь в 1 м2 расположенную перпендикулярно к распространению звуковой волны. Единицей силы звука служит ватт на квадратный метр (Втм2). Сила звука по физиологическим восприятиям уха оценивается как громкость. Ухо человека обладает чувствительностью не к силе звука а звуковому давлению которое зависит от силы звука. Слышимость определяется звуковым давлением и частотой звуковых волн и зависит от индивидуальных особенностей человека. Минимальное значение силы звука — это величина силы звука которая вызывает едва заметное ощущение в ушах. Для звуковых частот от 1 до 4 кГц органы слуха наиболее чувствительны. При этих частотах имеет место так называемый порог слышимости.
Максимальное значение — это такое значение силы звука которое вызывает болевое ощущение в ушах — болевой порог. При частоте 1 кГц сила звука на пороге слышимости равна 10~12 Втм2 а при болевом пороге — 1012 Втм2.
Вредное физиологическое действие шума на организм человека состоит в том что помимо повреждения слухового аппарата в виде развивающейся глухоты страдает и нервная система ухудшается деятельность органов дыхания нарушается работа сердечно-сосудистых органов. Из-за чрезмерного шума ослабляется внимание и поэтому возможны несчастные случаи и снижение производительности труда
Обеспечение вибрационной безопасности при эксплуатации мостового крана.
Механические колебания тел с частотой меньше 20 Гц воспринимаются только как вибрации. Часто вибрации сопровождаются и шумом. Особенно опасны вибрации непосредственного действия когда источник колебаний находится вблизи человека. При этом возможно заболевание сосудов и нервной системы сопровождаемое головными болями головокружением онемением кистей рук повышенной утомляемостью.
Одной из основных мер борьбы с шумами и вибрациями является снижение уровня звука и уменьшение амплитуды вибраций путем конструктивного усовершенствования производственных установок (применение виброгасителей) и совершенствования технологии. Шум и вибрации также можно ослабить применением звукоизоляции оборудования а также путем индивидуальной защиты людей подверженных вредному действию шумов и вибраций.
Снижение шума от вращающихся частей машин достигается созданием более гладких их поверхностей большой точностью балансировки применением высококачественных подшипников. Большое значение имеет также правильный уход за оборудованием надлежащая смазка и устранение биения в соединительных муфтах и редукторах. Для индивидуальной защиты рабочих от шума применяют вкладыши из ваты или пробки из губчатой резины закладываемые в отверстие уха а также специальные наушники или шлемы плотно закрывающие ухо. Для защиты от вибраций машинистов мостовых кранов можно применять коврики из губчатой резины или поролона. На сиденье стула можно укрепить поролоновые прокладки.
Обеспечение механической безопасности при эксплуатации мостового крана.
Движущиеся машины и механизмы незащищённые подвижные элементы механизмов:
вращающийся барабан;
представляют собой опасный производственный фактор. Для исключения контакта человека с опасной зоной применяются оградительные средства защиты: кожухи щиты решётки сетки на жёстком каркасе корпуса гидромоторов и редукторов а также предупреждающие и указывающие плакаты. Все механизмы закрыты защитными кожухами или приспособлениями предусмотренными в конструкции самого крана и соответствующие Правилам Госгортехнадзора. С целью безопасного доступа к механизмам на кране предусмотрены различные площадки и лестницы.
Также при работе крана возникает возможность обрыва каната при подъеме груза вес которого превышает номинальную грузоподъемность более чем на 10%. Падение груза может привести к травмам людей попавших в зону работы крана. Для того чтобы это не возникало в конструкции крана предусмотрен ограничитель грузоподъемности автоматически отключающий механизм подъема при превышении номинальной грузоподъемности. Подъём и перемещение мелкоштучных грузов должны производиться в специально предназначенной для этого таре при этом должна исключаться возможность выпадения отдельных грузов.
Также при увеличении нагрузки на грузовые канаты выше допустимой для исключения натяга и обрыва каната при подъеме груза на недопустимую высоту предусмотрен ограничитель высоты подъема. При подъеме груза должны применяться стропы соответствующие весу поднимаемого груза. С учётом числа ветвей и угла наклона строп их следует подбирать так чтобы угол между их ветвями не превышал 90 градусов.
Для предупреждения обслуживающего персонала находящегося в непосредственной близости от рабочей зоны крана в конструкции предусмотрен автоматический звуковой сигнал. Для того чтобы избежать риска нанесения травмы людям находящимся в зоне работы крана имеется ряд правил которые должен выполнять крановщик:
подъём и перемещение груза не должны производиться если под грузом находятся люди.
не разрешается опускать груз в автомашины при нахождении в её кузове людей.
запрещается подъём и перемещение груза с находящимися на нем людьми.
Острые кромки заусенцы и шероховатость поверхностей изделий и оборудования представляют собой опасность повреждения для крановщика и обслуживающего персонала следовательно они применяют средства для исключения физического контакта с ними (применяются ломы строповка производится строповщиком в рукавицах). Не допускается расположение рабочего места на значительной высоте относительно земли.
Для защиты посторонних людей территория на которой работает кран должна быть ограждена из-за возможности нанесения им вреда перемещаемыми грузами и разрушающимися конструкциями.
Обеспечение пожаробезопасности при эксплуатации мостового крана.
На объектах где эксплуатируются мостовые краны существует высокая степень возникновения пожароопасной ситуации. При возникновении пожара на людей в основном воздействуют: открытый огонь искры повышенная температура окружающей среды предметов токсичные продукты горения дым пониженная концентрация кислорода попадающие части строительных конструкций и т.д.
Для предотвращения такой ситуации на этих объектах должны соблюдаться все правила техники безопасности. Для своевременного устранения уже возникшего непредвиденного возгорания на объектах должны быть предусмотрены средства борьбы с огнём. К таким средствам относятся огнетушители и рукава с водяным питанием. Также для борьбы с огнём может использоваться огнетушитель входящий в комплект необходимых принадлежностей мостового крана. Он также используется для тушения электропроводки и электрооборудования крана.
Требования по обеспечению пожаробезопасности и соответствующие мероприятия по ее обеспечению излагаются в ГОСТ 12.1.004- 91 «ССБТ. Пожарная безопасность. Общие требования».
Для обеспечения пожаробезопасности вся аппаратура управления размещена в герметизированном контейнере электродвигатели всех механизмов имеют степень защиты от внешней среды
Обеспечение нормальных условий зрительной работы крановщика при эксплуатации мостового крана.
Недостаточное освещение рабочего места затрудняет длительную работу вызывает повышенное утомление и способствует развитию близорукости. Слишком низкие уровни освещенности вызывают апатию и сонливость.
Излишне яркий свет слепит снижает зрительные функции приводит к перевозбуждению нервной системы уменьшает работоспособность. При недостаточности естественного освещения применяются источники искусственного света: лампы прожектора специальные осветительные установки. По ГОСТ 24378-80Е «Освещённость на погрузочно-разгрузочных площадках в зоне работы крана и на грузозахватном устройстве на любом уровне его подъёма и перемещения в горизонтальной плоскости» должна быть не менее от наружной осветительной установки. По типу источника света освещение бывает естественное искусственное и совмещенное.
Для расчета общего равномерного освещения используем метод коэффициента использования светового потока.
Размеры кабины: 13 х 145 м2 при высоте 185 м. Высота подвеса светильника общего освещения – 18 м.
Световой поток лампы Фл (лм) одного светильника находится по формуле:
где ЕН - минимальная нормированная освещенность лк;
ЕН = 300 (лк) (по СНиП 23-05-95)
КЗ - коэффициент запаса принимается в зависимости от загрязненности воздуха в помещении. КЗ = 14 (СНиП 23-05-95)
S - площадь помещения: S = 13 145 = 19 (м2)
z – коэффициент минимальной освещенности z = 115.
N - число светильников N = 2.
- коэффициент использования светового потока ламп (%) зависящий от типа светильника коэффициента отражения потолка Roп и стен Roc и индекса i формы помещения.
где A и B - ширина и длина помещения; h - высота подвеса светильников над рабочей поверхностью. Для нашего случая:
для помещения Roп = 50% (светлый потолок) Roc = 30% находим коэффициент использования светового потока для светильника типа «Астра»: = 21%
Находим световой поток одного светильника:
Выбираем лампы накаливания Г-125–135–150 со световым потоком 2280 лм. Отклонение рассчитанного светового потока от выбранного составляет +4% что является допустимым.
Для полноценной работы крановщика в комфортных условиях необходимо наличие в кабине управления ламп накаливания со световым потоком не менее 2280 л
Очистка сточных вод от нефтепродуктов (масел СОЖ).
Очистка сточных вод – обработка сточных вод с целью разрушения или удаления из них вредных веществ. Освобождение сточных вод от загрязнения – сложное производство. В нем как и в любом другом производстве имеется сырье (сточные воды) оборудование (очистные сооружения) а также готовая продукция (очищенная вода).
Методы очистки сточных вод можно разделить на механические химические физико-химические и биологические когда же они применяются вместе то метод очистки и обезвреживания сточных вод называется комбинированным. Применение того или иного метода в каждом конкретном случае определяется характером загрязнения степенью вредности примесей объемами производства предприятия стоимостью метода. В данном дипломном проекте рассматривается механический метод очистки сточных вод металлообрабатывающего цеха.
Механическая очистка является обязательной ступенью очистки в любом очистном комплексе.
Сущность механического метода состоит в том что из сточных вод путем отстаивания и фильтрации удаляются крупные механические примеси. Грубодисперсные частицы в зависимости от размеров улавливаются решетками ситами песколовками септиками навозоуловителями различных конструкций а поверхностные загрязнения – нефтеловушками бензомаслоуловителями отстойниками и др. Механическая очистка позволяет выделять из бытовых сточных вод до 60 - 75% нерастворимых примесей а из промышленных до 95% многие из которых как ценные примеси используются в производстве.
На предприятиях очистка сточных вод осуществляется нефтеловушками горизонтальными отстойниками.
Для расчета нефтеловушек необходимо знать скорость всплывания нефтепродуктов: [1]
- средний диаметр частиц (капель) нефтепродукта мкм;
- плотность сточных вод и нефтепродуктов;
- динамическая вязкость сточных вод.
Таким образом после подстановки получим:
Выбираем горизонтальную составляющую скорости течения сточной воды:
Геометрические характеристики нефтеловушки:
Площадь поперечного сечения ловушки: [1]
Ширина нефтеловушки В=6м.
Высота нефтеловушки:
Наименьшая длина нефтеловушки: [1]
Время отстаивания сточной воды в нефтеловушки: [1]
Выводы: при эксплуатации мостовых кранов следует соблюдать все правила техники безопасности характерные для данного вида работ (механо-сборочные погрузочно-разгрузочные и прочие работы). Обслуживающему кран персоналу следует соблюдать соответствующие инструкции при работе а также иметь средства индивидуальной защиты от основных типов воздействия. Также должны быть предусмотрены возможности быстрого устранения аварий возникших при работе с краном (пожаров утечки нефтепродуктов и т.д.). Предложенные меры позволяют обеспечить безопасный труд персонала и защиту окружающей среды.
Мероприятия по охране окружающей среды обеспечивают содержание вредных веществ в пределах ПДК.
ЭКОНОМИЧЕСКАЯ ЧАСТЬ.
Мостовой кран общего назначения грузоподъемности 5 тонн устанавливается на участке сборочного цеха предназначенного для сборки и подъема ВЗП. Установка данного крана и введение его в работу совместно с действующим ранее на данном участке мостовым краном грузоподъемности 50 тонн позволит уменьшить потери рабочего времени рабочих занятых на сборке машин и сократить срок изготовления ВЗП с 4-х месяцев до 3-х месяцев за счет дополнительного изготовления 025 деталей для ВЗП. Это даст значительный экономический эффект и принесет заводу определенную прибыль.
Техническая характеристика мостового крана общего назначения грузоподъемностью 5 тонн.
Грузоподъемность – 5 тонн;
Годовой фонд времени работы – 2800 ч;
Срок службы с учетом износа – 10 лет;
Высота подъема – 16 м;
Масса крана – 12.74 т.
Передвижения крана – 134 мс;
Передвижения тележки – 067 мс;
Подъема груза – 017 мс.
Расчет капитальных затрат.
Капитальные затраты на внедрение новой техники – это единовременные затраты связанные с осуществлением технологического решения.
Формула для определения капитальных затрат по подъемно-транспортным машинам в общем случае имеет вид:
Км- затраты на монтаж определяются по прейскуранту на монтаж ПТМ.
Ктр- затраты на перевозку ПТМ определяются по тарифам действующим на автомобильном и железнодорожном транспорте;
Кзч- затраты на запчасти;
m – количество типоразмеров машин.
Для определения себестоимости крана пользуемся методом калькулирования по статьям затрат.
Основная зарплата рабочих:
СЧАС – часовая тарифная ставка = 120 руб
SОСН=120*5692=683040 руб.
Дополнительная зарплата рабочих:
SДОП=012*683040=81964 руб.
Отчисления в фонд социального страхования в пенсионный фонд и др. составляют 26% от основной зарплаты.
SОТ=026*683040=273216 руб.
Расход на содержание и эксплуатацию оборудования:
SОСН.М. – затраты на основные материалы.
Общецеховые расходы:
Общезаводские расходы:
Внепроизводственные расходы составляют 2% от заводской себестоимости.
Наименование статей затрат
Комплектующие изделия
Транспортно-заготовительные расходы
Дополнительная зп рабочих (12%)
Отчисления на соц.страхование и в пенсионный фонд (26%)
Расходы на содержание и эксплуатацию оборудования
Общезаводские расходы
Внепроизводственные расходы
Полная себестоимость составляет 885840 руб.
Оптовая цена определяется по формуле:
Транспортно-заготовительные расходы составят 1820 рублей за 1 тонну веса крана.
КТР=1820*m; где m=12740 т.
КТР=1820*1274= 23186 руб.
КТР=1820*1396=25407 руб.
Затраты на монтаж крана КМК состоит из затрат на монтаж электрической и механической частей крана. Они составляют:
Проектируемого крана – КМ=36 %; КЭМ=12%.
Базового крана – КМ=71%; КЭМ=17%.
КМ=36*1122360100=40405 руб.
КМ=71*1035000100=73485 руб.
КЭМ=12*1122360100=134832 руб.
КЭМ=17*103500100=175950 руб.
Затраты на запчасти составляют 3% цены для проектируемого крана и 5% для базового крана.
КЗЧ=0003*1122360=33670 руб.
КЗЧ=005*10350000=51750 руб.
К сопутствующим затратам КСОП относится стоимость подкрановых путей стоимость производственных помещений и др. по данным завода.
Результат расчета капитальных затрат см. табл.
Затраты на электромонтаж
Транспортные расходы
Сопутствующие затраты
Расчет эксплуатационных затрат.
Под технологической себестоимостью понимают совокупность затрат применяющихся в зависимости от варианта технологического решения:
СЗ – зарплата рабочих;
СЭЛ – затраты на электроэнергию;
СРЕМ – затраты на текущий ремонт;
СА – амартизационные отчисления.
Затраты на зарплату рабочих:
КДЗ = 13 - коэф-т учитывающий дополнительную зарплату;
КСС = 1079 - коэф-т учитывающий отчисления на соц. страхование;
FЭФ = 1987 - годовой фонд времени;
IТАР = 14 – часовая тарифная ставка;
NСП = 2 – численность рабочих.
Расходы на электроэнергию:
ЦЭ – тариф на 1 кВТ час электроэнергии;
NД – суммарная мощность двигателей;
WД – коэф-т использования двигателей;
WМ – коэф-т использования по мощности;
F – годовой фонд времени.
Затраты на ремонт оборудования:
АРЕМ – доля затрат на ремонт;
К=12 – коэф-т учитывающий дополнительный ремонт.
СРЕМ=0036*12*1122360 = 48485 руб.
СРЕМ=006*12*1035000 = 74520 руб.
Амортизационные отчисления:
НО = 29% норма амортизационных отчислений по основным фондам.
В результате расчетов получим
Затраты на эл. энергию
Затраты на текущий ремонт
Амортизационные отчисления
Расчет экономического эффекта.
ЗПР = 178493+015*153976650 = 409458 руб.
ЗБ = 207049+015*153350200 = 437074 руб.
ЭГ = 437074 – 409458 = 27615 руб.
Определение интегрального эффекта:
СБ СП – эксплуатациооные затраты базового и проектируемого кранов;
КП КБ – капитальные затраты нового и базового кранов;
КРП КРБ – затраты на кап. ремонт кранов.
ЭИ = (207049-178493)*10 - (1539766 - 1533502) – (89551 - 81220)*2 = 262627 руб.
Экономический эффект за весь период службы проектируемого крана по сравнению с базовым вариантом составит 262627 рублей. Следовательно проектируемый вариант мостового крана грузоподъемностью 5 тонн экономически целесообразен.
ЭЛЕКТРИЧЕСКАЯ ЧАСТЬ.
Требования к элктрооборудованию со стороны главных механизмов.
Электрическое оборудование кранов его монтаж заземление и токопровод должны соответствовать Правилам устройства электроустановок (ПУЭ).
Рабочее напряжение сети питающей краны не должно превышать 500 В. в соответствии с этим на кранах применяется электрооборудование на 220 380 и 500 В переменного тока а также 220 и 440 В постоянного тока.
Для защиты проводов и электродвигателей от коротких замыканий и значительных перегрузок свыше 2-25 % на кране должна быть максимальная защита.
Наряду с обязательными требованиями вытекающими из правил Госгортехнадзора и ПУЭ приводятся следующие требования:
При выключенном электродвигатели подъема (на нулевом положении) должен существовать контур динамического торможения обеспечивающий в случае выхода из строя механического тормоза медленное опускание груза;
На первых положениях подъема двигатель должен развивать такой пусковой момент чтобы исключалась возможность спуска номинального груза при напряжении питающей сети 90 % и в тоже время желательная минимальная скорость составила при наименьшей нагрузки не более 30 % номинального значения;
При перемещении рукоятки командоконтролера в направлении снижения в направлении снижения скорости последняя не должна повышаться даже кратковременно;
Система электрического торможения должна иметь необходимый запас обеспечивающий надежное замедление груза равного 125 % номинального при напряжении питающей сети 90 % номинального;
Скорость перемещения грузов для электроприводов переменного тока рекомендуется иметь на 30 % выше чем для привода постоянного тока при одинаковых условиях использования механизмов;
Движение груза должно происходить только в направлении установленном командоконтролером даже при неисправной схеме. В последнем случае груз может остаться неподвижным и т.д.
Основные стандарты используемые для кранового электрооборудования.
Электрооборудование. Основные понятия – ГОСТ 18311-80. ряд номинальных мощностей электрических машин – ГОСТ 12139-74. стандарты на характеристики режимов работы механизмов – ГОСТ 25835-83.
Кран должен быть снабжен конечными выключателями для автоматической остановки механизмов при подходе их к крайним положениям. На механизмах подъема обязательной является установка одного выключателя ограничивающего движение вверх.
Все механизмы кранов должны быть обеспечены механическими тормозами. На механизмах подъема и передвижения должны устанавливаться тормоза замкнутого типа автоматически размыкающиеся при включении электродвигателей и замыкающихся при их отключении.
Система управления в свою очередь должна обеспечивать необходимую последовательность переключений для реализации желаемых скоростных параметров предотвращать при этом не допустимые перегрузки и обеспечивать необходимую защиту.
Параметры регулирования систем управления неразрывно связаны с регулировочными свойствами приводного электродвигателя.
В данном случае рассматривается электрооборудование механизма подъема мостового крана общего назначения
грузоподъемностью - 5 т.
среднего режима работы с числом включений в час n = 60
скоростью подъема (опускания) груза – 017 мс.
скоростью подъема (опускания) порожнего крюка – 0147 мс.
Электрооборудование крана предназначена для управления механизмами крана освещения и сигнализации. Электрооборудования крана в зависимости от грузоподъёмности и режима работы имеет некоторые отличия по способу управления.
Пуск остановка торможение и регулировка скорости электродвигателей кранов тяжелого режима работы имеет силовое или смешанное управление(силовое и контакторное).
На мосту крана размещается пускорегулировочные сопротивления магнитные контроллеры реверсы преобразователи шкафы управления конечные выключатели ограничения передвижения крана и его тележки.
В кабине крановщика устанавливаются кулачковые контроллеры командо-контроллеры защитная панель рубильник трансформатор и автоматические выключатели освещения крана. Кабина закрытого типа оснащена отопительными приборами.
Электрическая связь между тележкой и мостом осуществляется гибким кабелем перемещающимся вдоль моста на кабельных каретках.
Защитная панель в кабине крановщика предназначена для максимальной мгновенной защиты электродвигателей а также для нулевой и конечной защиты механизмов. Защитная панель представляет собой металлический шкаф в котором установлены вводной рубильник вводной контактор многополюсные максимальны реле предохранители цепей управления и клемный блок. На стене панели размещена кнопка предназначенная для включения защитной панели. Защитная панель оборудована блок-замком с электрическим контактором.
Максимальная защита осуществляется электромагнитным реле представляющими собой максимальное токовое реле без блок-контакторов. Несколько таких реле воздействующих на один блок-контакт представляют многополюсное реле. Электромагниты реле в зависимости от соотношения мощностей защищаемых электродвигателей могут быть соединены в различные схемы. Для защиты электродвигателей от перегрузок достаточно иметь электромагнитное реле в одной фазе каждого электродвигателя. В остальные фазы электродвигателей электромагнит реле устанавливается для защиты проводов поэтому одноименные фазы нескольких электродвигателей необходимо объединить под общие электромагниты реле.
Защитная панель предназначенная для работы с магнитными контроллерами снабжена пакетными переключателями на два положения. В положения «Проверка» осуществляется проверка последовательности аппаратов магнитных контроллеров без силовой цепи подачей напряжения во всей цепи управления. В положение «Работа» пакетный переключатель устанавливается для нормальной работы крана.
Выбор привода и принципиальное решение по системе управления.
Повышение требований к крановым приводам массового применения ставит задачи значительного улучшения их технико – экономических показателей без существенного увеличения стоимости и усложнения эксплуатации. Основным направлением решения указанной задачи является применение средств полупроводниковой техники в традиционных системах в целях повышения коммутационной устойчивости контакторно – контрольной аппаратуры и реализации более рациональных режимов регулирования торможения и самовозбуждения в которых применен не управляемый диодный мост.
Для данного механизма подъема выбран электропривод с ПЧ серии АИТ.
Описание работы схемы с частотно-управляемым регулированием .
Силовая часть ПЧ включает управляемый выпрямитель UZ1 автономный инвертор UZ2 с узлом коммуникации условно показанный в виде блока U5 ведомый инвертор UZ3 ограничения обратного напряжения сглаживающий реактор L-M2 в цепи постоянного тока ПЧ с АИТ и токоограничивающий реактор L-M1. Система управления ПЧ с АИТ состоит из блока управления напряжением AV и частотой AU блока задания U1 блока обратной связи по частоте вращения двигателя U2 с входным сигналом от датчика скорости BR блока обратной связи по току U3 с входным сигналом от датчика тока UA САР электропривода представленной блоком U4 и блока токовой отсчетки UF связанного с трансформатором тока ТА.
Электропривод имеет двухзонное регулирование скорости однако максимальная скорость в системах с инверторами напряжения обычно не превышает 1.5 номинальной. Это вызвано перенапряжениями при коммутациях тока. Для ограничения перенапряжений в систему вводится нерегулируемый ведомый инвертор UZ3.
В системе регулирование до номинальной скорости осуществляется изменением выходной частоты в диапазоне 3-50 Гц и соответственно напряжения ПЧ а в верхней зоне – изменением частоты от 50 до 100 Гц при номинальном напряжении. В нижней зоне регулирования САР обеспечивает реализацию закона частотного управления с компенсацией падения напряжения на сопротивлениях статора двигателя. Переход на повышенные частоты происходит на последнем положении комадоконтроллера при малых нагрузках по сигналу от блока U3.
Плавность пуска и торможения обеспечивается датчиком темпа изменения частоты и напряжения входящих в состав САР. Тормозной электромагнит YA или двигатель гидротолкателя тормоза подключается к выводам двигателя поскольку соотношение между частотой и напряжением ПЧ обеспечивает достаточный для растормаживания тормоза ток YA. При реверсе САР выполняет сначала частотное торможение электропривода с заданным темпом а затем пуск в обратную сторону. Защита электропривода – конечная (выключатели SQ1 и SQ2) и нулевая – вынесены на реле KT1 включающее линейный контактор KMM. Для выполнения этих защит командоконтроллер имеет три контактных элемента SM1-SM3. В цепь реле KT1 введен также контакт реле максимальной скорости KV контролирующего правильную работу ПЧ. Защита от короткого замыкания в главной цепи осуществляется автоматическим выключателем QF1 а в цепях управления – выключателем QF2. Аварийное отключение в схеме производится выключателем SA1.
Современные тенденции и достоинства частотного регулирования.
Программно-аппаратный комплекс для управления сложными механизмами имеет в своем составе силовые модули (инверторы) и программируемый логический контроллер с возможностью подключения дисплея. Основа эффективной системы управления асинхронными электродвигателями - частотные преобразователи.Частотные преобразователи объединяются в сеть для обмена с программируемым логическим контроллером и устанавливаются в шкафах управления которые могут размещаться на мостовых кранах с асинхронными электродвигателями. Шкафы управления имеют стандартную степень защиты IP54 и встроенную систему термостабилизации.При необходимости система управления комплектуется кресло-пультом и кабиной оператора.Частотные преобразователи установленные на подъемные краны позволяют плавно управлять механизмами главного и вспомогательного подъёма подъёма и передвижения передвижения моста и тележки изменения вылета и поворота.
Главные достоинства системы:
снижение энергопотребления по сравнению с контакторными решениями;
большая плавность работы механизмов;
возможность достижения высокой точности позиционирования механизмов;
увеличенный диапазон регулирования скорости;
удобство в управлении;
высокая ремонтопригодность;
минимальная потребность в обслуживании;
высокая надежность;
совместимость с большинством приборов безопасности;
возможность самодиагностики;
легкость монтажа и пусконаладки.
ИССЛЕДОВАТЕЛЬСКАЯ ЧАСТЬ.
Вопросы надежности и повышения срока службы кранов.
Одной из причин обуславливающих необходимость прекращения эксплуатации кранов является возникновение остаточных прогибов мостов что наиболее часто наблюдается у кранов групп режима 6К и выше регулярно перемещающих предельные и близкие к предельным грузы. Причиной этого являются значительные технологические напряжения (до 100-150 мПа) в материале пролетных балок обусловленные приятным на большинстве краностроительных предприятий методом изготовления пролетных балок – с приваркой нижнего поясного листа после силового выгиба (растяжки) балки – заготовки с соединенными между собой верхними поясами стенкой.
При изготовлении пролетным балкам обычно придают строительный подъем равный 11000 пролета. При выработке строительного подъема прогиб от подвижной нагрузки может достичь 1500 – 1400 пролета что приводит к нарушению точности позиции грузовой тележки и даже к неуправляемым перемещениям.
Оценка надежности несущих конструкций.
По конструктивным особенностям условиям изготовления и нагружения металлические конструкции кранов мостового типа во многом схожи с несущими металлическими конструкциями строительных сооружений поэтому для оценки их надежности целесообразно использовать ряд положений разработанных применительно к строительным конструкциям.
В общем виде задачу обеспечения надежности крановых металлоконструкций можно представить следующим образом: существует многомерное пространство качества граничные точки которого по отдельным координатным осям определяются ранетами несущей способности базирующимися на нормативных характеристиках материала. Внешнее воздействие на сооружение определяет образуемое аналогичным образом пространство состояния. В процессе эксплуатации крана характеристики материала меняются изменениям подвергаются также и действующие на конструкцию воздействия поэтому во время всего срока службы конструкции оба пространства будут постоянно менять свой объем пульсировать.
Нормальная эксплуатация (сохранение надежности конструкции) будет длиться до тех пор пока пространство состояния во всех точках находится в пределах состояния качества.
Сокращение разницы объемов пространства будет приводить к экономии материалов при обеспечении заданных надежности и долговечности. Однако достоверное определение границ пространств затруднено тем что большое количество определяющих их факторов является случайными величинами процессами или функциями от ряда случайных параметров. Поэтому прогнозируемая надежность конструкции будет определяться вероятностью которую следует назначать в зависимости от класса ответственности крана. На практике расчетов и проектирования для оценки надежности конструкции используют решения выполняемые для отдельных координат осей пространств состояния и качества.
Принятая при расчете металлических конструкций кранов методика предельных состояний базируется на формуле ХУ где Х – параметр действительного состояния конструкции У – предельное значение параметра определяющее прогнозируемое качество конструкции. Вероятность достижения предельного состояния учитывается системой коэффициентов которые определяются методами теории вероятности или назначаются на основании эмпирических данных но с учетом вероятностных факторов.
Применительно к металлическим конструкциям грузоподъемных кранов возможности применения методов теории вероятности ограничены так как до настоящего времени для ряда показателей отсутствуют исходные статические данные. Использование эмпирических коэффициентов базирующихся в значительной мере на данных эксплуатации позволяет создавать конструкции обладающие определенными степенями надежности и экономичности. Однако их дальнейшее совершенствование особенно оптимизация затруднены из-за недостатка статистических данных. Их определение должно являться одним из основных направлений исследовательских работ в краностроении.
Диагностика состояния несущих конструкций.
При эксплуатации контроль состояния металлических конструкций кранов производится преимущественно методом внешнего осмотра что предусмотрено «Методическими указаниями по проведению обследований металлоконструкций кранов с целью определения возможности их дальнейшей эксплуатации» разработанными ВНИИПТМАем и согласованными с ГОСГОРТЕХНАДЗОРом. Многолетний опыт использования этой методики показал что она обеспечивает достаточно надежную оценку возможности безопасной эксплуатации кранов а также выявление подлежащих устранению дефектов. Тем не менее внешний осмотр не может полностью гарантировать выявление всех дефектов металлоконструкции в том числе зарождающихся трещин. В практику обследования кранов все шире начинают входить методы физического контроля состояния металлических конструкций особенно их сварных соединений. Методы не разрушающего контроля позволяют выявить уже возникшие повреждения. Прогнозирование их возникновения проводится расчетным путем.
Абрамович И.И. и др. Грузоподъемные краны промышленных предприятий: Справочник. – М.: Машиностроение 1989.
Грузоподъемные краны: В 2-х кн. Сокр. пер. с нем. Пер. М.М.Рунова В.Н. Федосеева; под ред. М.П. Александрова. – М.: Машиностроение 1981. – Кн. 1: 216 с.; Кн. 2: 287 с.
Справочник по кранам: В 2 т. Под общ. ред. М.М. Гохберга. – Л.: Машиностроение 1988. – Т.1: 536 с.; Т.2: 560 с.
Расчеты крановых механизмов и их деталей. ВНИИПТМАШ. – М.: Машиностроение 1971. – 496 с.
Шестопалов К.К. Подъемно-транспортные строительные и дорожные машины и оборудование: Учебное пособие. –М.: Издательский центр «Академия» 2005. – 320 с.
Тимошин А.А. Мачульский И.И. Голутвин В.А. Клейнерман А.Л. Капырина В.И. Комплексная механизация и автоматизация погрузочно-разгрузочных работ. – М.: Издательство учебно-методического центра по образованию на железнодорожном транспорте 2003.
Соколов С.А. Металлические конструкции подъемно-транспортных машин: Учебное пособие для вузов. – СПб: Политехника 2005.
Подъемно-транспортные машины. Атлас конструкций Под ред. М.П. Александрова и Д.Н. Решетова. 2-ое изд. перераб. и доп. – М.: Машиностроение 1987. – 122 с. ил.
Шабашов А.П. Мостовые краны общего назначения А.П. Шабашов А.Г. Лысяков. – М.: Машиностроение 1980. – 304 с.
Яуре А.Певзнер Е. Крановый электропривод.Справочник. М. Энергоатомиздат 1988г. 344 с.
Подвеска крюковая.DOC
КФ МГТУ им. Н.Э. Баумана
Рекомендуемые чертежи
- 25.10.2022