Ленточный дозатора муки




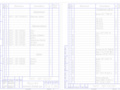
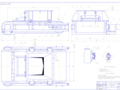
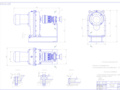
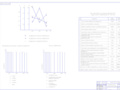
- Добавлен: 25.10.2022
- Размер: 3 MB
- Закачек: 3
Описание
Состав проекта
![]() |
![]() ![]() ![]() |
![]() ![]() ![]() ![]() |
![]() ![]() |
![]() ![]() ![]() ![]() |
![]() |
![]() |
![]() ![]() ![]() |
![]() ![]() |
![]() ![]() ![]() ![]() |
![]() ![]() ![]() ![]() |
![]() ![]() ![]() ![]() |
![]() |
![]() ![]() ![]() ![]() |
![]() ![]() |
![]() ![]() ![]() |
![]() ![]() |
![]() ![]() ![]() ![]() |
![]() ![]() ![]() |
![]() ![]() |
![]() ![]() ![]() ![]() |
![]() ![]() ![]() ![]() |
![]() ![]() ![]() ![]() |
![]() ![]() ![]() ![]() |
![]() ![]() ![]() ![]() |
![]() ![]() |
![]() ![]() ![]() |
![]() ![]() ![]() ![]() |
![]() ![]() ![]() ![]() |
![]() ![]() |
![]() ![]() ![]() ![]() |
![]() ![]() ![]() ![]() |
![]() ![]() |
![]() ![]() |
![]() ![]() |
![]() ![]() |
![]() |
![]() ![]() |
![]() ![]() |
![]() ![]() ![]() ![]() |
![]() ![]() ![]() |
![]() |
![]() ![]() ![]() |
![]() ![]() ![]() ![]() |
![]() ![]() |
![]() ![]() |
![]() ![]() |
![]() ![]() |
![]() ![]() |
Дополнительная информация
Содержание.docx
1 Анализ производительности ленточного дозатора муки 28
2 Расчет производительности ленточного дозатора и мощности .42
3 Расчет конструкции на прочность 43
Технологическая часть .59
Экономическая часть 71
Безопасность и экологичность проекта ..76
Список использованной литературы .104
8_2_Петля.dwg

1_Общий вид ленточного дозатора муки.dwg

Щели между петлями поз.20 более 1 мм не допускаются
Полости подшипников заполнить солидолом "С" ГОСТ 4366-76
Покрытие - эмаль ПФ 115 ГОСТ 6465 -76
Техническая характеристика:
Технические требования:
БЖД.docx
1. Основные опасные и вредные производственные факторы
На предприятиях хлебопекарной промышленности возникает опасность травмирования обслуживающего персонала при нарушении правил техники безопасности в процессе эксплуатации машин и механизмов.
При использовании электрических установок (электродвигателей пультов управления оборудованием и т.д.) возникает опасность поражения электрическим током; превышение давления в сосудах работающих под давлением (паровые котлы баллоны теплообменники) грозит взрывом и т.д.
Перемещение основного сырья – муки сопровождается значительным выделением пыли. Превышение ее ПДК указанной в СН 245-71 и правилах по технике безопасности и производственной санитарии для соответствующих отраслей промышленности (2 - 6 мгм3) может привести к профессиональным заболеваниям повышение концентрации пыли более 10-15 гм3 при наличии источника искрения – к взрыву.
В хлебопекарной промышленности многие технологические процессы связанные с брожением сопровождаются выделением в окружающую среду диоксида углерода (емкостей бункерных тестомесильных агрегатов чаны для брожения теста при ведении технологического процесса на жидкой фазе и др.). ПДК диоксида углерода в воздухе составляет 05%. Превышение этой концентрации неблагоприятно отражается на здоровье работающих. В некоторых случаях при значительном превышении ПДК (выше 6 - 7%) может привести к летальному исходу.
Неудовлетворительными могут оказаться условия труда при недостаточной освещенности при недостаточной степени механизации на ряде участков например при передвижении деж при эксплуатации тестомесильных машин периодического действия и др.
Анализ опасных факторов. Целью данного проекта является модернизация ленточного дозатора муки.
Таблица Анализ возможных опасных и вредных производственных факторов (ГОСТ 12.1.005-74 ССБТ).
Производственный фактор
Производственное оборудование
Движущиеся машины и механизмы
Движущиеся механизмы в оборудовании
Повышенная напряженность электрического поля
Электродвигатель электрическая цепь
Повышенный шум и вибрация
Электродвигатель и движущиеся части дозатора
Тестоприготовительное отделение
Психофизиологические.
Нервнопсихологические перегрузки монотонность труда
2. Требования охраны труда к ведению технологических процессов
Особенности технологических процессов на предприятиях хлебопекарной промышленности диктуют необходимость при проектировании предусматривать меры безопасности и создание комфортных и безопасных условий труда. В соответствии с санитарной характеристикой производственных процессов предприятия относятся по СНиП 11-92-76 «Вспомогательные здания и помещения промышленных предприятий» к следующим категориям:
а)основные производственные процессы –IVа;
б)производственные процессы ремонтно-механических мастерских столярных мастерских – 1б;
в)производственные процессы топочных отделений хлебопекарных печей при работе на твердом топливе – IIб.
Цехи предприятий хлебопекарной макаронной и кондитерскойпромышленности согласно СНИП II-М.2-72 относятся к категории взрыво- и пожароопасности в зависимости от технологических процессов (от Б до Д). Например склад бестарного хранения муки – к категории Б топочное отделение – к категории Г и т.д.
Замес теста. На хлебопекарных предприятиях после просеивания мука поступает для замеса в тестомесильное отделение где замешивание производится на периодически действующих тестомесильных машинах с подкатными дежами различной емкости (330 270 л и т.д.) и агрегатах непрерывного замешивания теста (ХТР И8-ХАГ-6 Р3-ХТН и др.). На макаронных предприятиях мука после просеивания поступает для замеса в шнековые прессы на кондитерских – на тестомесильные агрегаты.
При обслуживании тестомесильных машин периодического действия дложны быть установлены ограждения и предусмотрена блокировка их с электродвигателем. Блокировка обеспечивает отключение электродвигателя при снятии ограждения снятии крышки колпака (щитка).
Тестомесильные машины с подкатными дежами должны иметь приспособления надежно запирающие во время замеса дежу на фундаментной плите машины. Дежеопрокидыватели (с подъемом и без подъема дежи) должны подвергаться термическому испытания не реже одного раза в год. При установлении опрокидывателей с подъемом дежи (ХОД ХОУ ПО-1 ПО-2) следует обеспечить безопасность их эксплуатации снабдив ограждениями как передаточные устройства так и места подъема дежи.
Тестоспуски должны быть снабжены съемными предохранительными решетками.
Очистка тестопусков и бункеров должна производится скребками на длинной рукоятке. При необходимости спуска рабочего в бункера для брожения теста и в тестоспуски должны соблюдаться порядок указанных на с. 248.
При ведении технологического процесса с применением метода тестоведения на жидкой фазе и применением в связи с этим емкостей для рожения необходимо обеспечить удаление углекислого газа получаемого в процессе брожения и при необходимости зачистки емкостей соблюдать меры безопасности принятые для работы в емкостях.
Для уменьшения шума необходимо своевременно заменять износившиеся детали (особенно зубчатых передач) обеспечить заземление электродвигателя производить окраску оборудования в светлые тона а стены облицовывать глазурованными плитками.
Высота помещения тестомесильного отделения предусматривается в зависимости от устанавливаемого оборудования но не менее 48 м. При установке тестомесильных агрегатов непрерывного действия (И8-ХАГ-6 и др.) следует оставлять высоту от вера оборудования до верхнего перекрытия не менее 18 м для удобства ремонта проходы между устанавливаемыми агрегатами – не менее 1 м.
В тестомесильном отделении хлебопекарных преприятий должны быть обеспечены освещение (естественное и искусственное) и кратность обмена воздуха в соответствии со СНиП а также отраслевыми правилами техники безопасности и производственной санитарии для хлебопекарной промышленности. В соответствии с этими правилами освещенность в тестомесильных цехах должна составлять 200 лк. Воздухообмен должен обеспечить комфортные условия труда. Кратность воздухообмена рассчитывается в зависимости от условий на рабочих местах и может колебаться в пределах от 2 до 4.
Паропровод и трубопровод горячей воды (все тепловыделяющие поверхности печей сушилок и др.) должны быть теплоизолированы с температурой на поверхности не более 45оС.
Площадки для обслуживания прессов макаронного производства и тестомесильных агрегатов непрерывного действия должны быть обеспечены удобными лестницами (в случае их установки над уровнем пола) и перилами высотой в 1м.
Разделка теста. В тесторазделочном отделении хлебопекарных предприятий используются такие виды оборудования как тестоделительные округлительные и закаточные машины расстойные шкафы или пруфера для предварителной и окончательной расстойки тестовых заготовок.
Для мелкоштучных изделий используются розанчиковые и рожковые машины.
В бараночном производстве применяются агрегаты по прессованию и формовке бараночных изделий. Помещение тестоделительного отделения хлебозаводов должно быть просторным хорош освещенным (естественным и искусственным светом).
Особенность технологического процесса требует поддержания температуры и влажности воздуха в расстойных шкафах и пруферах по заданной величине для чего применяются кондиционеры воздуха.
В тесторазделочном отделении у рабочих мест должно быть обеспечено хорошее освещение в соответствии со СНиП-4-79 (200 лк). Все электродвигатели должны быть заземлены а ограждения движущихся частей оборудования сблокированы с электродвигателями.
Блокировка ограждения должна обеспечить отключение электродвигателя при снятии (или отсутствии) ограждения. В помещении тесторазделочного отделения должна быть приточно-вытяжная вентилция обеспечивающая кратность обмена воздуха в соответствии с условиями работы и правилами техники безопасности.
Расстояние перед фронтом тупиковых печей (ФТЛ-2 ДСД ХПК ПХС ПХК БН и др.) при расстойке теста на вагонетках должно быть не менее 5 м для удобства обслуживания.
Эксплуатация хлебопекарных печей. Устройство рабочего места у хлебопекарных печей зависит в первую очередь от типа и конструкции печей количества выделяемых тепла и влаги состояния и вида ограждающих конструкций пекарной камеры их изоляции и т.д.
Широкое внедрение механической посадки тестозаготовок на под печи и механической выгрузки применяемых на ковейерных печах значительно улучшают условия труда обслуживающего персонала так как рабочее место в этом случае отделяется от очага теплоизлучения.
Однако действующие конвейерные печи а также печи со стационарным подом где имеют место значительные выделения тепла в окружающую среду и в первую очередь теплоизлучение в зоне нахождения обслуживающего персонала требует принятия мер по оздоровлению условий труда.
Прежде всего необходимо обеспечить местное душирование путем установки вентиляторов с направлением воздуха для обдувания в месте нахождения рабочих работающих у печей.
В пекарном зале в связи со значительным выделением тепла в окружающую среду особое внимание необходим уделить работе вентиляции. В этом помещении кратность воздухообмена наиболее значительна (в пределах до 10 – 12 при температуре 18оС).
В помещении пекарного зала где производится посадка и выгрузка изделии выпекаемых в формах и на листах в дополнение к неблагоприятным температурным условиям имеет место также и загазованность от пригорания масла которым смазываются листы и формы а также шум во время выгрузки изделий.
В связи с этим необходим в каждом отдельном случае решать вопрос о смягчении ударов путем применения резиновых подкладок у места выбойки форм а также отсасывания и удаления газов из помещений пекарного зала. Все приводы печей необходимо ограждать и следить за своевременной смазкой трущихся частей с целью уменьшения шума.
Освещенность в пекарном зале должна быть не менее 75 -100 лк при использовании ламп накаливания и 150 – 200 лк при люминесцентном освещении.
В случае ремонта внутри пекарной камеры соблюдают правила техники безопасности при работе внутри емкостей обеспечивают соответствующей спецодеждой переносными лампами пониженного напряжения (12 В) и т.д.
В каждом отдельном случае в зависимости от типа эксплуатируемых печей разрабатываются инструкция по технике безопасности с учетом конструктивных особенностей этих печей – система пода и обогрева применение трубок Перкинаса сжигание газа внутри камеры электрообогрев и т.д.
При этом должно быть учтено какой вид топлива сжигается – твердое жидкое газообразное.
Так например при эксплуатации печей со стационарным подом и канальным обогревом (типа ХР) а также конвейерных печей и с канальным обогревом (ФТЛ-2) при сжигании твердых видов топлива (уголь торф и т.д.) следует уделить особое внимание маарам безопасности при чистке каналов так как могут произойти случаи ожогов. Во избежание травм от ожогов необходимо обеспечить работающих по чистке каналов рукавицами защитными очками соответствующим удобным инструментом а также переносными ламами низкого напряжения – 12В.
При сжигании твердого топлива необходимо обеспечить систематическую очистку концов трубок выступающих в топочную часть печи от налета золы соблюдая при этом меры безопасности обеспечив рабочих занятых на очистке трубок соответствующим приспособлением: не допуская ударов о выступающие концы.
При эксплуатации конвейерных печей (ХВЛ АЦХ и др.) обогреваемых трубками Перкинса могут быть случаи взрывов трубок работающих под большим избыточным давлением (10 – 20 МПа или 100 – 200 кгсм2) в связи с чем необходим систематически проверять состояние концов трубок выступающих в топочную часть и при обнаружении их перегрева принимать меры к немедленной замене.
При использовании хлебопекарных печей с электрообогревом необходим соблюдать правила по электробезопасности – заземление систематическая проверка состояния изоляции проводов и т.д.
Особое внимание следует уделить безопасным условиям труда при газовом обогреве обеспечив герметичность подводки газа во избежание выделения газа в окружающую среду как с точки зрения взрывоопасности так и в целях профилактики случаев отравления газом.
При сжигании газа в топках хлебопекарных печей необходимо следить чтобы факел правильно располагался в топочном цилиндре печи: симметрично относительно как оси цилиндра (топки) так и оси газовой горелки. Кроме того нужно следить за полнотой сгорания топлива и наличием нормального коэффициента расхода (избытка) воздуха который подается в топку печи для сгорания в ней топлива.
Проскок и отрыв пламени являются неблагоприятными явлениями. При проскоке пламени в инжекционную горелку констурции Царикова которая при работе заполнена газовоздушной смесью может произойти хлопок смеси а в некоторых случаях взрыв и разрушение горелки.
Отрыв пламени от горелки опасен тем что угасание факела и продолжающееся поступление газа в топочное пространство могут привести к загазовыванию каналов и газоходов печного агрегата и взрыву при разжигании горелки.
Поэтому во всех случаях при розжиге необходимо провентилировать каналы и газоходы а во время сжигания газа следить за приборами указывающими давление газа в сети(манометром) и состоянием горения топлива и при появлении признаков неправильного горения прекратить подачу газа.
После устранения обнаруженных недостатков можно приступить к дальнейшей эксплуатации топочных устройств.
3. Электробезопасность
Помещение цеха относиться к категории с повышенной опасностью поражения электрическим током так как в цехе токопроводящие полы. В целях предохранения от поражения электрическим током проводятся следующие мероприятия согласно действующих правил ПУЭ: периодическая проверка знаний персонала по правилам техники безопасности один раз в год.
Панели распорядительных устройств окрашены в белый цвет и имеют четкие надписи указывающие назначение отдельных цепей для обеспечения безопасности людей от поражения электрическим током заземляющие устройство к которому подключены металлические части и корпуса электрооборудования которые в следствии нарушения изоляции могут оказаться под напряжением. Сопротивление корпуса защитного заземления не превышает 4 Ом. Оно необходимо для того чтобы снизить напряжение прикосновения до безопасной величины. В работе машины принимаем электродвигатель. Подвод электричества осуществляется через провода в заземленных трубах или рукавах.
В тестоприготовительном отделении все процессы автоматизированы движущиеся части механизма закрыты кожухом. Что приводит к низкому травматизму.
Защитное заземление представляет собой систему вертикальных электродов-заземлителей вкопанных в грунт и соединенных стальными трубами уголками полосами и другими металлическими соединителями. Заземление бывают контурным или выносным.
Заземлители располагаются по периметру цеха или площадке где размещено электрическое оборудование. При пробое изоляции корпус такой установки при защитном заземлении будет находится под малым относительно земли напряжением безопасным для жизни человека при прикосновении.
Сопротивление растеканию электрического тока при замыкании на землю одного электрода круглого сечения определяется по формуле:
Rэл = S*[l*n(21d)+ 0.5*l*n((4t+1)(4t-))] Ом (1)
р – удельное электрическое сопротивление грунта в который помещены электроды–заземлители Ом*м;
d – диаметр электрода м;
t = h+12; h – глубина заложения электрода в грунт (расстояние от верхнего конца электрода до поверхности земли) м.
Необходимое количество заземляющих электродов определяется по соотношению:
Кс – коэффициент сезонности;
Vэл – коэффициент использования электродов;
Rз – максимальное допустимое сопротивление заземляющего устройства.
При оценках принимается равным 4 Ом т.е. это наибольшее допустимое сопротивление заземляющего устройства.
Из условия безопасности организму человека протекающий через тело его ток не должен превышать 004 а это установлено медицинским экспериментами.
L = (n-1)*a+0.14 м (4)
Если обозначить ширину полосы символом b то электрическое сопротивление ее определяется выражением:
Rпол = Sn*Ln[(2*L**2)(b*h)] Ом (5) где Sn= p(2**L)
Тогда электрическое сопротивление защитного заземления состоящего из n электродов и полосы шириной b и длиной L равно
Результирующие сопротивления Rрез защитного заземления по нормативам не должно превышать 4 Ом.
Таким образом задача ставиться так: при заданных:
- грунт в котором устанавливается защитное заземление;
- температура в январе месяце;
- ширина соединительной полосы.
Подобрать такое заземление т.е. рассчитать диаметр электродов длину электрода их количество глубину закладки в грунт расстояние между электродами и длину соединительной полосы которое не превышает заданное максимальное значение 4 Ом.
Название грунта - Чернозем
Тип заземления - Выносное
Ширина соединительной полосы м - 004
Температура воздуха t оС - 18.00
Таблица Десять лучших решений по сопротивлению
Таблица Приняты обозначения
d - диаметр электрода м
l - длина электрода м
h - глубина заложения м
a – расстояние между электродами м
r - сопротивление заземления Ом
n – число закладываемых электродов шт
lb – длина соединительной полосы м
Pc – затраты на заземление.
5. Мероприятия по гигиене труда и промышленной санитарии
Воздушная среда рабочей зоны и производственный микроклимат.
Таблица Предельно – допустимые концентрации вредных веществ в воздухе рабочей зоны (ГОСТ 12.1.005 – 88).
Агрегатное состояние
Технический процесс в тестоприготовительном отделении характеризуется выделением в среду двуокиси углерода при брожении теста. ПДК двуокиси углерода составляет 05% к объему помещения.
Необходимая кратность объема воздуха в производственном помещении с умеренным выделением двуокиси углерода равна 6.
В процессе дозирования муки в воздухе выделяется мучная пыль. Её ПДК из таблицы составляет 6 мгм3.
Для предотвращения распыла муки в конструкциях машин предусматривают уплотнение крышек месильных емкостей.
Таблица Оптимальные и допустимые параметры микроклимата в рабочей зоне производственных помещений (ГОСТ 12.1.005-88)
Производственное помещение
вительное отделение
Для обеспечения условий микроклимата в тестоприготовительном отделении предусмотрено:
В холодный период года обогрев с помощью центрального водяного отопления.
Вентиляция (естественная и приточно – вытяжная ).
Система вентиляции в помещении хлебозавода в соответствии с нормами технологического проектирования ОИТП – 86.
Основные вредные выделения
Тепло влага двуокись углерода летучая пыль.
Механическая обменная из верхней зоны
Механическая рассредоточенная с подачей в верхнюю зону
Источником вибрации и шума являются части дозатора а также электродвигатель машины. Общие требования безопасности уровень шума не должен превышать установленных норм. Установленная норма 80 Дб.
Для снижения уровня шума на корпус питателя дозатора наносится шумоизолирующая мастика ВД 17-58. Мука непрерывно поступает через питатель и бункер на короткий ленточный транспортер. Поэтому и наноситься шумоизолирующая мастика. Действие мастики основано на ослаблении вибрации путем перехода части колебательной энергии в тепловую при деформации покрытий.
Таблица Уровень звукового давления в Дб в октавных полосах со средним геометрическими частотами в предельном спектре Сан.ПиН 2.2.12.1.8-562
Таблица Гигиенические нормы общей вибрации СН 2.2.42.1.8.566-96. Среднеквадратические уровни виброскорости (мс) в октавных полосах со среднегеометрическими частотами (Гц) на постоянных рабочих местах.
7. Взрывопожаробезопасность
Цех по производству хлебо–булочных изделий относиться к Г категории так как источником пожаробезопасности являются используемые для смазки горючесмазочные вещества мучная пыль деревянные ложки.
На предприятии ответственность за пожарную безопасность возложена на администрацию. Все цеха и участки завода имеют индивидуальные средства пожаротушения. На заводе имеется пожарная сигнализация местная телефонная связь. Вода для пожаротушения поступает из городской водопроводной сети через два ввода.
Наружное пожаротушение производится при помощи пожарных гидрантов расположенных под углом здания на расстоянии 5 метров. На внутренней водопроводной сети у входов устанавливается пожарные краны на высоте 135 м. и пожарные рукава с бронсбойтом. Расстояние между пожарным кранами такова что обеспечивает сопротивление струй воды от двух стволов в наиболее высокой и удаленной части здания.
Таблица Классификация помещений по взрывоопасности.
Характеристика помещений
Класс по взрывоопасности
Помещения в которых выделяется приходящие во взвешенное состояние горючие пыли или волокна в таком количестве что способны образовывать с воздухом взрывоопасные при нормальных режимах работы.
Тестомесильное отделение
Таблица Категории производств по взрывной взрывопожарной и пожарной опасности в соответствии со СНиП 21.01-97
Характеристика производства
Материалы участвующие в технологическом процессе не горючие раскаленные расплавленные.
Тестомесительное отделение
8. Промышленная экология
Предприятия удалено от жилых массивов строится с учетом рельефа местности и "розы ветров". Соблюдается санитарная зона (50 м.). Участки территории между здания свободны от использования в производственных целях а также санитарно–защитная зона отделена. Территория поддерживается в чистоте.
Для очистки воздуха от пыли в приточных вентиляционных камерах установлены фильтры. Для нашего помещения предусмотрены инерционные фильтры и установлены циклоны. Смесь происходит последовательную и тщательную фильтрацию. Очищается и поступает в окружающую среду.
Так как источником среды загрязнения окружающей среды является технологическая вода. Предусмотрен спуск технической воды в горячую канализацию с последующей очисткой.
БЖД.dwg

Анализ состояния травматизма за прошедший год
Повысить качество проведения инструктажей
Руководители участков
Организовать учебные занятия со специалистами и
руководителями работ
Осуществлять контроль за соблюдением техники безопасности
Отремонтировать бытовые помещения
Проверить сопротивление изоляции и сопротивление заземления
Улучшить освещение мастерской
Отремонтировать вентиляцию мастерской
Провести освидетельствование грузоподъемных машин
Аттестовать газоэлектросварщиков по газоэлектробезопасности
Проверить состояние пожарной безопасности и средств
Установить дополнительные гидранты и доукомплектовать
имеющиеся пожарными руковами
Устранить недостатки
указанные в предписание инженера по ТБ
для руководителей подразделений
Руководители подразделений
Проверить состояние защитных устройств и ограждений
Разработать и укомплектовать рабочие места в мастерской
На рабочих местах в ремонтной мастерской улучшить освещение и
Заведущий мастерской
Утеплить окна и двери в производственных и ремонтных помещениях
Провести собрание с рабочими на тему "Охрана труда в хозяйстве
- несоответствие условий труда
требованиям безопасности
- нарушение трудовой
электрооборудования
и экологичность проекта
Коэффициент тяжести травматизма
Коэффициент частоты травматизма
Коэффициент нетрудоспособности
Распределение несчастных случаев по профессиям
8_4_2_Шпилька.dwg

4_Общий вид рамы.dwg

Сварные швы по ГОСТ 14771-76 по контуру прилегания деталей
Неуказанные размеры - по месту
* Размеры длоя справок
Технология_12.dwg

Токарно-карусельный станок
Резец проходной Т5К10 ГОСТ 18877-73
Поворот заготовки 180
МАПП - ПДП 11.12.000
Резец проходной Т5К10
Технология.docx
1. Технология изготовления вала ролика
Назначение и описание вала ролика
Части машин и механизмов могут вращаться двигаться поступательно или колебаться передавая свое движение и усилия другим деталям. Наиболее распространенным движением является вращательное при котором осуществляется вращение различных деталей на валах и осях.
Вал представляет собой тело вращения цилиндрической конической и другой формы опирающееся на две или несколько опор. На валу закрепляются шкивы зубчатые колеса маховики и т. п. Некоторые из этих деталей называемые ведущими получают вращательное движение от постороннего источника энергии (двигателя). К другим деталям вращение передается валом. Они называются ведомыми. Таким образом вал при своем движении.
Момент обязательно передает усилие (вращающий момент) а поэтому испытывает деформации кручения и изгиба.
Валы по форме разделяются на прямые или изогнутые (коленчатые) целые или составные (собранные из нескольких частей) сплошные или полые (пустотелые).
При проектировании дипломного проекта рассматривается ступенчатый вал. Ролик на валу будет крепиться в двух местах по средствам натяга.
Конструктивно-технологический анализ детали
Вал ролика являются ответственной деталью. Поэтому наряду с правильным определением форм и размеров валов первостепенное значение в обеспечении их прочности и работоспособности имеет способ изготовления — выбор заготовок и методов их получения изыскание и осуществление рациональных вариантов технологических процессов обработки.
Заготовку данного вала осуществляется резанием прутка дисковой пилой. Заготовкой вала является именно пруток так как диаметр вала намного меньше его длины. Материал вала – сталь20Х13. Эта сталь характеризуется хорошим сочетанием свойств позволяющим применять её в виде листового и сортового проката поковок и штамповок а также в отливках для аппаратуры работающей под давлением. Она хорошо деформируется в горячем и холодном состояниях обрабатывается резанием и сваривается всеми видами сварки.
Выбор указанной стали обусловлен главным образом тем что по механическим свойствам она вполне удовлетворяет требованиям предъявляемым к деталям затворов и вместе с тем используются для изготовления корпусов и крышек сосудов что имеет немаловажное значение в производстве. Не исключается применение и сталей других марок отвечающих требованиям правил Госгортехнадзора и ОСТ 26-291—71.
Однако при этом следует иметь в виду не только механические свойства выбранных материалов но и возможность получения качественных заготовок из них склонность к образованию некоторых характерных дефектов в процессе той или другой обработки и возможность их исправления без снижения качества. Также данная сталь должна иметь высокую антикоррозионную стойкость. Это одна из важнейших характеристик выбора материалов в пищевом машино и аппаратостроении.
Для количественной оценки технологичности детали используются показатели технологичности: коэффициенты использования материала точности обработки шероховатости поверхности .
Проанализируем рабочий чертеж детали.
Результаты анализа рабочего чертежа
Количество поверхностей
Коэффициент использования материала:
Коэффициент точности обработки :
средний квалитет точности обработки детали по всем поверхностям;
Коэффициент шероховатости поверхности :
среднее числовое значение параметра шероховатости всех поверхностей детали;
Сравнивая полученные результаты с нормативными можно сказать что деталь по показателям шероховатости поверхности и коэффициенту точности технологична:; .
Основными видами заготовок в пищевом машиностроении являются отливки из черных и цветных металлов поковки и штамповки заготовки из листового металла проката сварные заготовки заготовки из неметаллических материалов
В моем случае для изготовления вала перемешивающего устройства возьмем пруток так как эта заготовка обеспечивает заданное качество готовой детали при ее минимальной себестоимости.
Выбор припусков и допусков
Вследствие незначительных деформаций валов припуски на механическую обработку могут быть уменьшены примерно в 2 раза против величин принимаемых для значительных деформаций.
Несмотря на большую разницу в размерах для всех валов приняты минимальные и одинаковые припуски по диаметрам — 5 мм на сторону по торцам — 25 мм.
Выбор средств технологического оснащения
Токарная обработка - это один из самых используемых методов механической обработки деталей резанием. С применением токарных работ наиболее часто проводится механообработка следующих деталей: различных шестерней валов и пружин а также любых изделий требующих соблюдения идеальной цилиндрической конической сферической и др. форм.
Токарный станок представляет собой в большинстве случаев установку для вращения заготовки и различный инструмент: резцы сверла развертки зенкеры и т.д. для ее обработки. Токарные станки бывают различных размеров и позволяют с высокой точностью обрабатывать как небольшие детали размер которых измеряется долями миллиметра так и очень крупные длиной до нескольких метров.
Различают следующие станки для токарных работ: токарно-винторезный станок чаще всего применяемый для механообработки мягких металлов в особенности в мелкосерийном производстве. Позволяет выполнять разнообразные работы от обточки до нарезания резьб. Токарно-карусельный станок отличается вертикально направленной осью вращения и используется для мехобработки крупных деталей - колец валов дисков и так далее. Также на нём можно прорезать канавки и протачивать отверстия по центральной оси. Лоботокарный станок используется для обработки труб валов и других подобных деталей. Токарно-револьверный станок позволяет проводить сложные серийные токарные работы из штучных заготовок. Автомат продольного точения и многошпиндельный токарный автомат предназначены для механообработки серийных изделий с высокой скоростью обработки и высокой точностью (то есть минимизацией допусков). В обоих аппаратах чаще всего используются различные прутки или специальные заготовки.
Токарно-карусельные станки бывают одностоечные (стол с диаметром до 1500 мм) и двухстоечные. В первом случае на вертикальной стойке имеются направляющие по которым может перемещаться траверса 1 (рис. 139). На траверсе 1 имеются направляющие по которым в горизонтальном направлении перемещается поворотный суппорт 2 (револьверная головка) несущий режущие инструменты которые периодически можно вводить в действие путем поворота головки вокруг ее горизонтальной оси. Перемещение траверсы по стойке и суппорта по траверсе производят вручную вращением маховиков 3 и 4 или механически при включении механизмов подач. Сбоку стола размещен поперечный суппорт 5 с четырехгранным поворотным резцедержателем.
Обработка может производиться одновременно инструментами помещенными в верхнем и боковом суппортах.
Фрезерные станки - группа металлорежущих станков в классификации по виду обработки. Фрезерные станки предназначены для обработки с помощью фрезы плоских и фасонных поверхностей тел вращения зубчатых колёс и т. п. металлических и других заготовок. При этом фреза вместе со шпинделем фрезерного станка совершает вращательное (главное) движение а заготовка закреплённая на столе совершает движение подачи прямолинейное или криволинейное. Управление может быть ручным автоматизированным или осуществляться с помощью системы ЧПУ (CNC).
Металлорежущий инструмент фрезерной группы станков. Концевые фрезы.
Во фрезерных станках главным движением является вращение фрезы а движение подачи — относительное перемещение заготовки и фрезы.
Вспомогательные движения необходимы в станке для подготовки процесса резания. К вспомогательным движениям относятся движения связанные с настройкой и наладкой станка его управлением закреплением и освобождением детали и инструмента подводом инструмента к обрабатываемым поверхностям и его отводом; движения приборов для автоматического контроля размеров и т. д. Вспомогательные движения можно выполнять на станках как автоматически так и вручную. На станках-автоматах все вспомогательные движения в определенной последовательности выполняются автоматически.
Шлифованием называют процесс обработки заготовок резанием с помощью абразивных кругов. Абразивные зерна расположены в круге беспорядочно и удерживаются связующим материалом. При вращательном движении круга в зоне его контакта с заготовкой часть зерен срезает материал в виде очень большого числа тонких стружек (до 100000000 в минуту). Шлифовальные круги срезают стружки на очень больших скоростях — от 30 мс и выше. Процесс резания каждым зерном осуществляется почти мгновенно. Обработанная поверхность представляет собой совокупность микроследов абразивных зерен и имеет малую шероховатость. Часть зерен ориентирована так что резать не может. Такие зерна производят работу трения по поверхности резания.
Абразивные зерна могут также оказывать на заготовку существенное силовое воздействие. Происходит поверхностное пластическое деформирование материала искажение его кристаллической решетки. Деформирующая сила вызывает сдвиги одного слоя атомов относительно другого. Вследствие упругопластического деформирования материала обработанная поверхность упрочняется. Но этот эффект оказывается менее ощутимым чем при обработке металлическим инструментом.
Тепловое и силовое воздействие на обработанную поверхность приводит к структурным превращениям изменениям физико-механических свойств поверхностных слоев обрабатываемого материала. Так образуется дефектный поверхностный слой детали. Для уменьшения теплового воздействия процесс шлифования производят при обильной подаче смазочно-охлаждающих жидкостей.
Шлифование применяют для чистовой и отделочной обработки деталей с высокой точностью. Для заготовок из закаленных сталей шлифование является одним из наиболее распространенных методов формообразования. С развитием малоотходной технологии доля обработки металлическим инструментом будет уменьшаться а абразивным — увеличиваться.
Расчет режимов резанья и норм времени
Основными элементами режимов резания являются: скорость резания подача и глубина резания. Установление рациональных режимов резания для любого вида механической обработки заключается в выборе оптимального сочетания глубины резания подачи и скорости резания обеспечивающих наибольшую производительность при соблюдении всех требований предъявляемых к обрабатываемой детали. При назначении элементов режимов резания учитывают характер обработки тип и размеры инструмента материал его режущей части материал и состояние заготовки тип и состояние оборудования. Элементы режима резания обычно устанавливаются в порядке указанном ниже.
Рассмотрим для определения режимов и норм времени одну операцию – вертикально-фрезерная (смотри технологический процесс операция 20).
Глубина резания t: при черновой (предварительной) обработке назначают по возможности максимальную t равную всему припуску на обработку или большей части его; при чистовой (окончательной) обработке – в зависимости от требований точности размеров и шероховатости обработанной поверхности.
Примем глубину резания t = 1 мм.
Подача S: при черновой обработке выбирают максимально возможную подачу исходя из жесткости и прочности системы СПИЗ мощности привода станка прочности твердосплавной пластинки и других ограничивающих факторов; при чистовой обработке – в зависимости от требуемой степени точности и шероховатости обработанной поверхности.
табличное (матричное) значение подачи ;
коэффициент учитывающий состояние обрабатываемой поверхности;
коэффициент учитывающий материал инструмента;
коэффициент учитывающий форму обрабатываемой поверхности;
коэффициент учитывающий влияние закалки;
коэффициент учитывающий жесткость технологической системы;
коэффициент учитывающий материал обрабатываемой детали.
табличное (матричное) значение скорости резания ;
коэффициент учитывающий свойства обрабатываемости материала;
коэффициент учитывающий влияние угла в плане;
коэффициент обрабатываемости материала;
коэффициент учитывающий влияние СОЖ;
коэффициент учитывающий вид обработки.
Исходным документом при нормировании операции технологического процесса является операционная технологическая карта. Норма времени на любую станочную работу определяется по формуле:
штучно-калькуляционное время на обработку одной единицы изделия;
основное время – время непосредственно затрачиваемое на изменение формы и размеров изделия;
время обслуживания рабочего места (смена затупившегося инструмента сметание стружки смазка чистка станка и т. п.);
вспомогательное время – время затрачиваемое на выполнение приемов помогающих произвести на станке изменение формы и размеров изделия;
время на отдых и личные надобности;
норма подготовительно-заключительного времени на партию деталей в N штук;
N – число деталей в партии.
Норма основного времени:
– величина врезания и перебега инструмента;
– число проходов инструмента необходимое для снятия припуска;
подача за одну минуту (минутная подача).
Величина врезания и перебега инструмента равна 3 мм для удаления припуска необходимо два прохода инструмента следовательно
Норма вспомогательного времени состоит из времени на установку и закрепление детали в приспособлении времени связанного с переходом (включение и выключение подачи подвод и отвод инструмента и т.п.) и времени на контрольные измерения .
Примем измерение размеров 10 мин.
Основное и вспомогательное время в сумме дают оперативное время:
Нормативы времени на обслуживание рабочего места и отдых приведены в процентах от оперативного:
Определение подготовительно-заключительного времени.
Подготовительно-заключительное времянормируется на партию деталей и часть его приходящаяся на одну деталь включается в норму штучно-калькуляционного времени. Подготовительно-заключительное время включает в себя: ознакомление с работой; настройку оборудования на выполнение данной работы; пробную обработку детали; получение задания; получение режущего инструмента приспособлений; сдачу продукции; сдачу инструмента приспособлений. Подготовительно-заключительное время в зависимости от используемого оборудования определяется из таблиц а при обработке деталей на сверлильных станках в кондукторах составляет приблизительно 11 мин.
Технология_11.dwg

Токарная копировальная.
Точить начерно заготовку
Вертикально-фрезерная.
Фрезеровать с другой стороны.
Слесарно-опиловочная.
Шлифовать деталь выдерживая
технические требования.
Полировать деталь вручную
Токарный многорезцовый копировальный
полуавтомат модели1В625М.
Приспособление: патрон поводковый
Вертикально-фрезерный станок
Приспособление специальное:
Круглошлифовальный станок
Приспособление:для полирования.
Фрезерно-центровальный автомат
Приспособление специальное:
МАПП - ПДП 11.11.000
Технологический процесс изготовления вала ролика
ЛДМ.doc
Хлеб – гениальное изобретение человечества. В мире мало ценностей которые как хлеб ни на день ни на час не теряли бы своего значения. Когда хочется есть вспоминаешь прежде всего хлеб. И кто из нас усомнится в том что запах горячего хлеба один из самых лучших на свете. Его не спутаешь ни с каким другим. Ведь хлеб пахнет хлебом. Прекрасные слова о хлебе написал Антуан Отюст Перментье живший в XVIII веке. «Хлеб - писал Перментье - является великодушным подарком природы такой пищей которую нельзя заменить ничем другим. Заболев мы вкус к хлебу теряем в последнюю очередь; и как только он появляется вновь это служит признаком выздоровления. Хлеб можно потреблять в любое время пищеварения. С чем бы его ни ели с мясом или любым другим блюдом он не теряет своей привлекательности. Он настолько нужен человеку что едва родившись на свет мы уже без него не можем обойтись и до смертного часа он нам не надоедает».
Хлебные изделия являются одними из основных продуктов питания человека. Суточное потребления хлеба в разных странах составляет от 150 до 500 г на душу населения.
В России его потребляют традиционного много – в среднем до 330 г в сутки. В периоды экономической нестабильности потребления хлеба неизбежно возрастает так как хлеб относится к наиболее дешевым продуктам питания.
В хлебе содержатся многие важнейшие пищевые вещества необходимые человеку; среди них белки углеводы витамины минеральные вещества пищевые волокна.
За счет потребления хлеба человек почти наполовину удовлетворяет свою потребность в углеводах на треть – в белках более чем наполовину – витаминах группы В солях фосфора и железа. Хлеб из пшеничной обойной или ржаной муки почти полностью удовлетворяет потребность в пищевых волокнах.
Усвояемость хлеба в значительной мере связана с его органолептическими показателями в первую очередь такими как вкус аромат разрыхленность мякиша которые формируют понятие качества хлеба. Качество хлеба обусловлено составом и свойствами компонентов входящих в его состав а также процессами протекающими в тесте при его созревании и выпечке тестовых заготовок.
Современное хлебопекарное производство характеризуется высоким уровнем механизации и автоматизации технологических процессов производства хлеба внедрением новых технологий и постоянным расширением ассортимента хлебобулочных изделий а также широким внедрением предприятий малой мощности различных форм собственности. Все это требует от работников отрасли высокой профессиональной подготовки знания технологий и умения выполнять технологические операции по приготовлению пшеничного и ржаного теста по разделке и выпечке различных видов изделий.
История развития хлебопечения
Самая древняя еда человека – дикие злаки. Это были прародители пшеницы ячменя овса ржи проса. Первоначально пятнадцать тысяч лет назад люди употребляли в пищу сырые злаки. Позже люди научились растирать их с помощью двух специально обработанных камней и получать крупу а затем и муку которую смешивали с водой и в виде жидкой каши поедали сырой. Таким образом жидкая зерновая каша и является первым хлебом которые был изобретен человеком.
Прошло несколько тысячелетий и человек научился возделывать и культивировать пшеницу ячмень просо и другие злаки. Было это примерно восемь тысяч лет назад. Именно в это время у древних вавилонцев ассирийцев египтян евреев персов этрусков и других народов появляются различные приспособления позволяющие измельчать зерна злаков. Это ступки ручные мельницы.
С открытием огня люди убедились что подогретое зерно сваренная похлебка из муки вкуснее. Это было второе рождения хлеба.
Затем люди научились выпекать пресные лепешки из зерновой каши – плотные подгорелые куски бурой массы мало напоминающие хлеб наших дней. Но именно с появлением этих лепешек выпекавшихся на горячих камнях и началась на земле история хлебопечения.
Прошли тысячелетия и было сделано еще одно гениальное открытие хлеба. Древние египтяне научились разрыхлять тесто используя чудодейственную силу микроорганизмов. Так в Древнем Египте пять-шесть тысяч лет назад стали производить хлеб очень похожий на современный. Это открытие сделанное безвестными египетскими мастерами коренным образом изменило облик хлеба. Из пресной тяжелой лепешки он превратился в нежный разрыхленный хлеб с приятным вкусом и ароматом.
Начало производства печеного хлеба совпадает с развитием культуры каждого народа на Земле. А поскольку хлеб к этому времени стал основной частью питания человека от этого он начал совершенствовать технику переработки зерна.
Пять тысяч лет назад в Древнем Египте зерно дробили в каменных ступках или растирали на специальных каменных досках. Получаемая таким способом мука была грубой с большим количеством отрубянистых частиц которые затем частично отсевали. Затем в Египте изобретают жернова с помощью которых стали получать муку тонкого помола. Эта мука уже мало чем отличалась от обычной муки наших дней. Египтяне соединили в один процесс три великих открытия древности: выращивание пшеницы хорошего качества применения жерновов для помола муки и использование дрожжей при производстве хлеба.
В Древнем Египте большую часть пищи составляли пшеница и ячмень из которых египтяне умели изготавливать до 30 видов хлеба лепешек и пряников.
Искусство выпекать разрыхленный пшеничный хлеб от древних египтян перешло в Грецию. Древние греки выпекали хлеб в специальных горшках которые назывались «клебанос» - вероятно отсюда и произошло слов «хлеб». Пшеничный хлеб в Греции считался большим лакомством. Аристократы ели его как самостоятельную пищу. Существовало много разновидностей хлеба – от самого простого из муки грубого помола с большим количеством отрубей до изысканных сдобных хлебов.
Вслед за Грецией новую египетскую технологию производства разрыхленного хлеба перенимают римляне. Вначале хлебопечение у них носило домашний характер а уже на рубеже новой эры в столице Римской империи работали сотни пекарен в которых производили помимо хлеба сдобные изделия с различными специями пирожки. В пекарнях были организованы отдельные помещения в которых готовили дрожжевые закваски.
С момента изобретения хлеб почитался очень высоко и ценился всеми. В принятой в Древнем Египте скорописи солнце золото и хлеб обозначались одинаково – кружком с точкой посередине. Люди умевшие выпекать хлеб имели в те времена большой авторитет. В Древней Греции булочник мог занять очень высокий пост. В Риме раб умеющий печь хлеб стоил в десять раз дороже самого искусного гладиатора. А по старым германским законам преступник убивший пекаря наказывался втрое строже чем за убийство любого другого человека. В Византии хлебопеки не подвергались никаким государственным повинностям но если они выпекали и продавали хлеб низкого качества их могли подвергать наказаниям – выпороть остричь наголо привязать к позорному столбу отправить в изгнание.
Две тысячи лет назад в Риме воздвигнут памятник Марку Вергилию Эврисаку потомственному пекарю обеспечивавшему хлебом почти всех жителей города. Символом средневековых мастеров-пекарей во многих странах был большой крендель изготовленный из металла или дерева покрытый позолотой. Такие крендели висели у входа в пекарни и хлебные лавки.
На Руси с древних времен хлебом называли не только хлеб но и зерно. Рожь пшеница ячмень овес упоминаются в самых старых летописях. При археологических раскопках памятников трипольской культуры на Украине 94-2 тыс. лет до н.э.) и поселений славян на Восточно-Европейской равнине относящихся к V-VI вв. н.э. были обнаружены хлебные зерна и лепешки.
Во времена развития феодальных отношений хлеб на Руси пекли в домашних условиях а с развитием ремесел появились и ремесленники-пекари. В одной из пекарен того времени обнаружен инвентарь с помощью которого приготавливали хлеб - квашни корытца лопаты для хлеба противни.
С ростом городов и разделением труда развивались торговля и в первую очередь печеным хлебом. В XVII в. на московских рынках хлеб продавали в специальных хлебных рядах. По переписи 1638 г. в Москве было 2367 ремесленников из них 52 выпекали хлеб 43 пряники 7 блины 14 сырники 5 крупеники 12 ситники 50 просвирники т.е. 263 человека или каждый девятый ремесленник занимался хлебным промыслом.
В конце XIX в. появились первые хлебопекарные предприятия которые начали вытеснять кустарные. В Москве например славился булочник Филиппов. На его предприятии вырабатывался широкий ассортимент хлебобулочных изделий многие из которых производится и сегодня. К 1905 г. в фирме Филипповых в одной только Москве было 16 булочных и пекарен а также филиалы в еще шести городах. Основное предприятие находилось на Тверской д.10 и включало и сухарное бараночное кондитерское отделения два отделения немецкого хлеба рижского петербургского столового расстегайного черного белого и шведского хлеба жареных пирогов калачей.
К началу первой мировой войны (1914 г.) в России имелось только несколько крупных хлебопекарных предприятий в Москве Петербурге Кронштадте. Преобладали мелкие кустарные пекарни. Начало создания современной отечественной хлебопекарной промышленности способной высвободить большой объем ручного труда и обеспечить население качественным хлебом было положено в конце 20 – начале 30 годов строительством крупных высокомеханизированных хлебозаводов. Хлебное дело обретало индустриальные черты хлебозаводы оснащались современной техникой. За годы предвоенных пятилеток в строй действующих в стране вошло 280 хлебозаводов. В 1940 г. на хлебозаводах вырабатывалось более 55% всей продукции.
Хлебопекарная промышленность России и перспективы ее развития
Хлебопекарная промышленность России относится к ведущим пищевым отраслям АПК. Производственная база хлебопекарной промышленности Российской Федерации включает в себя более 1500 хлебозаводов и более 5000 предприятий малой мощности и обеспечивает ежегодную выработку около 20 млн. тонн продукции в том числе около 125 млн. тонн вырабатывался на крупных хлебозаводах.
Современный хлебозавод является высокомеханизированным предприятием. В настоящее время практически решены проблем механизации производственных процессов начиная от приемки сырья и кончая погрузкой хлеба в автомашины.
На многих хлебозаводах смонтированы установки для бестарного приема и хранения муки жира дрожжевого молока соли сахарного сиропа молочной сыворотки. Дальнейшее внедрение прогрессивных способов транспортирования и хранения основного и дополнительного сырья на хлебозаводах является актуальной задачей.
Большое значение имеет внедрение более совершенных способов приготовления теста. Особенностью таких способов является уменьшение продолжительности брожения теста что позволяет снизить затраты сухих веществ муки сократить потребность в емкостях для брожения снизит энергоемкость оборудования. Интенсификация процесса брожения теста достигается за счет увеличения дозировки прессованных дрожжей применения инстантных дрожжей повышения интенсивности механической обработки теста при замесе применения различных улучшителей форсирующих созревание теста.
На хлебозаводах начинает внедряться технология приготовления пшеничного теста с интенсификацией его брожения в процессе расстойки.
Широко используются традиционные способы приготовления пшеничного и ржаного теста на больших густых опарах и заквасках на жидких опарах и заквасках. Использование усиленной механической обработки при замесе позволяет сократит продолжительности брожения теста приготовленного этими способами. Имеется соответствующее аппаратурное оформление этих технологий обеспечивающих комплексную механизацию производства полную механизацию трудоемкого процесса приготовления теста.
В настоящее время в России примерно 60% всего хлеба вырабатывается на комплексно-механизированных линиях. Это линии для производства формового хлеба круглого хлеба батонов а также булочных и сдобных изделий. Важную роль в механизации процессов на поточных линиях играют манипуляторы: делительно-посадочные автоматы ленточные и другие посадочные устройства. Одну комплексно-механизированную линию может обслуживать один человек. На передовых предприятиях один человек обслуживает 2-3 линии. В основном производстве уровень механизации труда составляет примерно 80% производительность труда 655 т. на человека.
Однако на многих хлебозаводах еще используется ручной труд при разделке теста при посадке тестовых заготовок в расстойный шкаф пересадке расстоявшихся заготовок на под печи укладке хлеба в лотки и ранспортировании вагонеток и контейнеров с хлебом. Поэтому важной задачей является техническое перевооружение таких предприятий.
Для отечественной хлебопекарной промышленности характерна высокая концентрация производства при которое возникают трудности сохранения свежести хлеба и оперативной доставки его в торговую сеть.
В последние году условия работы хлебопекарной отрасли изменились и прежде всего организационно. Почте все хлебозаводы и пекарни стали приватизированными акционерными предприятиями. На хлебозаводах складываются рыночные отношения начинают действовать законы конкуренции.
Уровень среднедушевого потребления хлеба в России составляет 120-125 кг в год (325-345 г в сутки) в том числе для городского населения 98-100 кг в год (245-278 г в сутки) для сельского 195-205 кг в год (490-540 г в сутки). Эти нормы зависят от возраста пола степени физической и умственной нагрузки климатических особенностей мест проживания.
Вместе с тем анализ показывает что с 1991 г. наметилось снижение выработки хлеба годовое потребление хлеба на человека к 1995 г. упало до 70 кг. Потребление хлеба уже существенно ниже рациональной нормы питания что несомненно отразится на здоровье населения.
Такое положение вызывает необратимые процессы в хлебопекарной промышленности: хлебозаводы вынуждены консервировать технологические линии сокращать рабочие места увеличивать затраты на производство и реализацию продукции прекращать инвестиции.
В новых условиях работы хлебопекарной промышленности требуются новые подходы к разработке ассортимента изделий роль которого в организации потребления должна существенно возрасти. Если раньше ассортимент обуславливался главным образом условиями производства и диктатом механизированных линий теперь условия производства и состав оборудования определяются ассортиментом и спросом. При этом следует больше чем ранее учитывать спрос и потребности разных групп населения.
Задача повышения объемов потребления хлеба требует особого внимания и изучения проблем повышения его качества.
В новых экономических условиях имеются предпосылки для внедрения пекарен вырабатывающих широкий ассортимент хлебобулочных и мучных кондитерских изделий. В настоящее время основан выпуск отечественного оборудования для пекарен производительностью 02-50 т. в сутки. Эти предприятия позволяют вырабатывать широкий ассортимент хлебобулочных изделий и продавать их в свежем виде непосредственно в магазинах при этих пекарнях. Для обеспечения этого производства оборудованием разработаны новые машины которые вошли в комплекты оборудования А2-ХПО Л4-ХПМ-500 и другие для пекарен малой мощности.
Одно из важнейших направлений повышения эффективности производства и улучшения качества продукции хлебопекарной промышленности – создание рациональной структуры предприятий отрасли механизация и автоматизация производственных процессов на базе новейших технологий.
Решение основных задач научно-технического прогресса в хлебопекарной отрасли тесно связано с разработкой современных технологий упаковки и автоматизированных приборов для контроля свойств сырья полуфабрикатов и качества готовых изделий.
Согласно современным тенденциям науки о питании ассортимент хлебопекарной продукции должен быть расширен выпуском изделий повышенного качества и пищевой ценности профилактического и лечебного назначения.
Объем выработки диетических изделий незначителен потребность в них удовлетворяется лишь на 10-20%. Низок уровень производства изделий профилактического назначения для населения в зонах экологического неблагополучия хлеба длительного хранения (от 3 до 30 суток) для людей проживающих в труднодоступных и отдаленных районах в условиях техногенных катастроф аварийных ситуаций спецконтигентов и др.
Решение проблемы сбалансированного питания населения имеющее государственное значение возможно лишь при условии разработки и внедрения в производство технологий с помощью которых буду реализованы:
обеспечение безопасности сельскохозяйственного и продовольственного сырья пищевой продукции;
снижение уровня заболеваемости детей из-за неполноценного питания и загрязнения окружающей среды;
уменьшения продовольственной и сырьевой зависимости России от зарубежных стран;
экологически чистые продукты питания нового поколения массового и диетического назначения с учетом современных гигиенических требований;
принципиально новые технологии основанные на использовании нетрадиционных методов способствующих ускорению процесса;
научные основы создания технологических процессов производства продуктов детского питания нового поколения.
Создание ассортимента хлебных изделий группы «здоровье ведется по двум направлениям:
моделирование рационального ассортимента хлебной продукции для отдельных регионов с учетом их климатических демографических и др. особенностей;
разработка разнообразного ассортимента изделий для профилактического и лечебного питания.
Для выработки таких изделий используют специальные композитные мучные смеси с отрубями зародышевой муки дробленным и плющенным зерном витаминно-минеральными компонентами и др.; осуществляют производство этих смесей.
В новых условия большое значение и развитие приобретает упаковка хлеба. Упаковка хлеба предохраняет его от преждевременного высыхания сохраняет его потребительскую свежесть повышает санитарно-гигиенические условия его хранения и увеличивает сроки реализации. На хлебопекарных предприятиях применяют следующие упаковочные машины зарубежного и отечественного производства: HARTMANN IBONHART RSE FINPAK TAYRAC «Терминал» «Лаура» и др.
Основным направлением механического процесса в пищевой промышленности является внедрение поточных механизированных линий агрегатов и аппаратов.
Благодаря механизации производственных процессов резко повышается производительность труда ликвидируются трудоемкие операции сокращается потребность в производственных площадях и потерь сырья улучшение условий труда и повышение общей культуры производства.
Чтобы увеличить производство хлебобулочных изделий нужно увеличить выпуск технологического оборудования в 13-14 раза.
Сделав упор на комплексное высокопроизводительное оборудование значительно повысив технический уровень и надежность.
Комплексной механизации уделяется большое внимание для обеспечения хорошего качества готовых изделий необходим постоянный контроль технических процессов и качества полуфабрикатов на всех стадиях производства. Это становится непримиримым условием при создании автоматизированных участков цехов.
Разработка новых ресурсосберегающих технологий уменьшающих расход энергии металла труда материальные и социальные проблемы приводит к созданию принципиально нового оборудования для полностью автоматизированных производств. Решение этой задачи возможно лишь на основе глубокого знания закономерностей технологических процессов действующего и конструктивного оборудования.
В настоящие время хлебопекарная промышленность выпускает широкий ассортимент хлебобулочных изделий но порой качество их не отвечает вкусовым потребностям.
Задача хлебопеков состоит в том чтобы хлеб был качественным. Задача хлебопекарного производства заключается в следующем:
выпекать хлеб с повышенными вкусовыми качествами;
выпускать мелкоштучные изделия с повышенной пищевой ценностью;
реагировать на спрос населения;
качественно оформить вид продукции;
выпускать хлеб длительного хранения.
Для выполнения этих требований надо:
совершенствовать технологический процесс;
строго соблюдать параметр выпечки;
повышать точность дозирования;
качественно проводить ППР.
Дозирование является одной из важнейших технологических операций в процессе приготовления теста.
Основное назначение дозирующих устройств – отмеривание заданного количества материала по массе с определенной точностью.
Требования предъявляемые к дозаторам – определенная точность дозирования высокая производительность надежность работы.
По структуре рабочего цикла дозирование подразделяется на непрерывное и порционное (дискретное). По способу дозирования – объемное или весовое.
Объемный способ дозирования обладает меньшей точностью дозирования однако эти дозаторы наиболее просты конструктивно а следовательно - наиболее надежны.
Весовое дозирование – обеспечивает наибольшую точность дозирования и как правило применяется для основного сырья.
При непрерывном тестоприготовительном процессе применяется дозатор непрерывного действия работающего по объемному действию.
Дозаторы для муки бывают ленточные шнековые барабанные тарельчатые и вибрационные.
Рисунок 1. Схемы дозаторов:
а - Барабанный дозатор; б – Тарельчатый дозатор;
в – Шнековый дозатор; г – Ленточный дозатор;
д – Вибрационный дозатор.
Ленточный дозатор (рисунок 1 г) состоит из ленточного транспортера и вертикального бункера с заслонкой устройством которого можно регулировать толщину слоя муки уносимой из бункера.
Для обеспечения точности дозирования высота столба над лентой транспортера поддерживается в определенных пределах при помощи поворотных валиков со щитком который по мере заполнения емкости под щитком и над ним под действием тяжести муки опускается. При этом размыкаются контакты конечного выключателя и подача муки прекращается. Когда мука расходуется опускается щиток под действием груза возвращается в исходное положение и выключает привод транспортера подающего в бункер муку.
Производительность регулируется скоростью ленты. Точность дозировки 15 %.
Достоинство дозатора:
- простота конструкции;
- широкий придел регулирования;
- возможность использовать и весовой принцип дозирования.
- распыл муки при большой производительности то есть снижения точности дозировки.
Шнековый дозатор (рисунок 1 в) для муки состоит из бункера питателя и расположенного по ним шнекового дозатора . Бункер питатель предназначен для равномерной подачи муки из производственного силоса подается в бункер-питатель. В бункере установлен вертикальный вал к которому прикреплены ворошитель к нижней части вала прикреплена лопасть для подачи муки в шнек дозатора.
В боковом шнеке бункера имеются смотровые отверстия для наблюдения уровнем муки.
Бункер снабжен ограничителями для поддержания уровня.
Ограничители выполнены в виде поворотных пластин на осях которых закреплены кулачки действующие как контакты микропереключателей.
При повышении уровня муки до верхней пластины контакт микропереключателя срабатывает и выключает электродвигатель питающего шнека.
Когда мука опускается до нижнего уровня ограничитель поворачивается и выключает электродвигатель питающего шнека.
Если мука не поступает в бункер ограничитель поворачивается вниз на большой угол при этом срабатывает контакт микропереключателя выключая тестоприготовительный агрегат.
Шнековый дозатор состоит из шнека храпового механизма и регулирующего стержня на одном конце которого прикреплена клинообразная пластина другой конец стержня имеет резьбу с градуируемой резьбой регулирующей степень перемещается вдоль своей оси при повороте гайки. Храповый механизм приводится в действие цепной передачей которая вращает втулку к торцевой поверхности втулка шарнирно прикреплена рычагом имеющим на одном конце собачку а на другом пружину.
При накатывании ролика на пластину собачка выключается из зацепления с храповиком. Храповое кольцо закреплено в ободе пустотелого вала приводящего во вращение шнек. Поворот шнека происходит в тот момент когда ролик рычага катится по поверхности регулирующего стержня и шнек останавливается когда ролик накатывается на клинообразную пластину количество муки за один поворот шнека изменяется от 10 до 100 г. в зависимости от положения шнека.
Для более точного дозирования установлена решетка чтобы не было осыпания муки.
- возможность работать на разных сортах муки (по влажности);
- достаточная точность дозировки.
- сложность шнека привода;
- большая занимаемая площадь;
- требуется обязательно бункер-питатель.
Барабанный дозатор (рисунок 1 а) муки состоит из приемного бункера автономного поворотного бункера секторного барабана и приводного механизма.
Мука подается в дозатор из силоса шнеком через патрубок на лоток до тех пор пока вес не превысит противовеса лотка; последний состоит из рычажного механизма и цилиндра внутри которого находится перекатывающий шар. При опрокидывании размыкается пружинный контакт электродвигателя резко прекращая подачу муки в лоток. Мука с лотка ссыпается в нижнею часть бункера м при воздействии ворошителя поступает в секторный барабан до тех пор пока барабан не заберет всю муку. После этого лоток под действием груза возвращается в первоначальное положение шар перекатывается в лево пружинный контакт замыкается и снова мука подается на лоток.
Электронно-сигнализирующие устройство может выключать исполнительные механизмы в частности привод питающего шнека. Сигнализатор работает по принципу изменения электрической емкости системы: электрод датчика - измеримая среда.
Удаление среды от стержня датчика вызывает изменение электрической емкости которая воздействует на генератор электронного блока. При емкости 5 ЛКФ происходит срыв высокочастотного колебания при этом резко возникает катодный ток лампы и реле включенное в цепь катодной лампы срабатывает.
Секторный барабан забирающий муку ссыпающуюся с лотка приводится в периодическое вращение посредством кривошипа свободно сидящего на валу барабана. На кривошипе шарнирно закреплена клиновидная собачка прижимаемая пружиной к желобчатому колесу закрепленному на валу барабана на шпонке. Кривошип получает колебательное движение по средствам шарнира от кривошипного диска снабженного механизмом для изменения радиуса кривошипа. Кривошипный диск закреплен на валу тестоприготовительного агрегата. При вращении кривошипа собачка заклинивает в желобе колеса поворачиваются затем возвращаются в исходное положение. Вторая собачка прижимается к желобу колеса пружиной препятствуют обратному вращению колеса.
Угол поворота секторного барабана регулируется путем измерения радиуса кривошипа вследствие чего изменяется производительность дозатора. Дозатор при влажной муке не обеспечивает точность дозировки.
В связи с этим ВНИИХП реконструировал дозатор следующим образом: мука из приемного бункера по средствам качающего кривошипа подается на двух дисковых вращателях и направляется ими в желобчатый барабан вращающийся с постоянной скоростью.
Барабан имеет 12 неглубоких желобков хорошо заполняемых мукой. При вращении мука высыпается ее остатки счищаются скребком укрепленным на качающимся рычаге.
Производительность регулируется перемещением стержней благодаря штурвалу.
- довольно высокая точность+-1%;
- работает с точностью +-1% и на влажной муке.
- не совсем точная регулировка производительности.
Тарельчатый дозатор (рисунок 1 б). Принцип действия заключается в сбрасывании скребком продукта с горизонтально вращающего диска расположенного под выпускным отверстием бункера.
Тарельчатый дозатор представляет собой вращающийся на вертикальной оси диск-тарелку; над ней повешен цилиндрический патрубок который можно передвигать по горловине бункера с помощью винта.
Продукт высыпающийся из бункера располагается на тарелке виде корпуса. Продукт высыпающийся из бункера снимается скребком кроме того производительность можно регулировать патрубком.
- не большие габариты.
- невысокая точность дозирования;
- плохо компонуется с другими дозаторами.
Вибрационный дозатор
Вибрационный дозатор (рисунок 1 д) выполнен виде бункера с двумя наклонными стенками. Внутри бункера на передней наклонной стене свободно лежит наклонный лист из тестолита связанный шарнирной тягой с вибрирующей задней стенкой закрепленной на петлях.совершает колебательные движения.
Вибрация задней стенки осуществляется при помощи ролика по которому ударяет кулачек.
Возвращение задней стенки: прижатие ее к подвижному упору осуществляется двумя пружинами установленными на стакане питателя на специальных стаканах в кранштейне таким образом задняя стенка непрерывно вибрирует и сообщает возвратно-поступательное движение передней стенки предотвращая образование свода муки в бункере и забивание входной щели. Кулочек приводящий в движение заднюю стенку имеет три выступа на кулочковом валике. Кулочковый валик вращается через цепную передачу от вала тестоприготовительной машины. Делает 450 встряхиваний в минуту поворотом рукоятки эксцентрикового вала можно изменять величину колебаний вибрирующей стенки от 0 до 8 мм. Из дозатора в тестомеситель мука высыпается через щель образуемую через подвижную стенку шибером и нижней частью вибрирующей стенки бункера. Количество подаваемой муки можно регулировать в широких пределах за счет изменения величины питающей цели и амплитуды колебаний. Это обеспечивает точность дозировки.
- Надежность в работе;
- Неудобство в обслуживании.
- Быстрый износ стенки.
Результат анализа сведен в сравнительную таблицу вариантов (таблица №1).
Таблица №1. Сравнительная таблица типов дозаторов
Наименование оборудования
Простота конструкции и надежность небольшие габариты.
Невысокая точность дозирования при максимальной производительности.
Точность дозировки +-10 %.
Сложность привода. Большие габариты.
Простота конструкции. Надежность.
Узкие диапазоны регулирования.
Простота конструкции.
Низкая точность плохо компонирует с другим оборудованием.
Хорошая точность дозировки.
Неудобство эксплуатации.
Таким образом наиболее приемлемым является ленточный дозатор сыпучих компонентов. Как наиболее надежный в работе имеющий небольшие габаритные размеры и простату конструкции.
Мука — важнейший продукт переработки зерна. Ее получают путем помола зерна и классифицируют по виду типу и сорту.
Вид муки определяется той хлебной культурой из которой она получена. Различают муку пшеничную ржаную ячменную овсяную рисовую гороховую гречневую соевую. Муку можно получать из одной культуры и из смеси пшеницы и ржи (пшенично-ржаная и ржано-пшеничная).
Тип муки определяется ее целевым назначением. Например мука пшеничная может вырабатываться хлебопекарной и макаронной. Хлебопекарная мука вырабатывается в основном из мягкой пшеницы макаронная — из твердой высоко-стекловидной. Ржаная мука вырабатывается только хлебопекарной.
Сорт муки является основным качественным показателем всех ее видов и типов. Сорт муки связан с ее выходом т. е. количеством муки получаемой из 100 кг зерна. Выход муки выражают в процентах. Чем больше выход муки тем ниже ее сорт.
Для выработки хлеба и хлебобулочных изделий на хлебопекарных предприятиях применяют в основном пшеничную и ржаную муку. Пшеничную муку вырабатывают пяти сортов по ГОСТ 26574 «Мука пшеничная хлебопекарная»: крупчатка высшего первого второго сортов и обойная или четырех сортов по ТУ 8 РФ 11-95—91 «Мука пшеничная» высшего первого второго сортов и обойная. Кроме того вырабатывают муку пшеничную подольскую по ТУ 8 РСФСР 11-42—88 и муку пшеничную хлебопекарную «Особая» по ТУ 9293-003-00932169-96 высшего и первого сортов.
Мука ржаная хлебопекарная вырабатывается по ГОСТ 7045 трех сортов — сеяная обдирная и обойная. Кроме того вырабатывается мука ржаная хлебопекарная «Особая» по ТУ РФ 11-115—92.
Муку полученную из зерновых и крупяных культур используют в составе композитных смесей. Это следующие виды и сорта муки: мука ячменная сортовая (ТУ 9293-008-00932169-96) мука пшенная сортовая (ТУ 9293-007-00932169-96) мука кукурузная сортовая (крупная и мелкая) (ТУ 9293-009-00932169-96) мука рисовая 1 сорта (ТУ 9293-010-00932169-96) мука гороховая сортовая (ТУ 9293-011-00932169—96) мука пшеничная с высоким содержанием отрубянистых частиц (ТУ 9293-003-00932169-96) мука пшеничная обогащенная пищевыми волокнами (докторская) (ТУ 9293-004-00932169-96).
В настоящее время стали создаваться композитные мучные смеси для хлебобулочных изделий. Композитные мучные смеси для хлеба включают три компонента: муку пшеничную хлебопекарную 1 сорта (65%) муку ржаную обдирную (15%) и крупяную (ячменную сортовую пшенную сортовую или гречневую 1 сорта) (20%). Смеси для хлебцев состоят из двух компонентов — муки пшеничной хлебопекарной высшего сорта (89%) и крупяной муки (11%). Композитные смеси для кондитерских изделий включают муку пшеничную хлебопекарную высшего сорта (80%) и крупяную муку (20%). Композитные мучные смеси предназначены для расширения ассортимента изделий с улучшенным аминокислотным составом повышенным количеством макро- и микроэлементов и витаминов.
Основные показатели качества всех основных сортов муки используемых для производства хлебобулочных изделий представлены в таблице 2.
Таблица №2. Показатели качества муки
Содержание сырой клейковины % не менее
Установлены документами
остаток на сите % не более
Пшеничная хлебопекарная:
Пшеничная хлебопекарная подольская
Пшеничная хлебопекарная особая:
ТУ 9293-003-00932169-96
Ржаная хлебопекарная особая
Конструкторская часть
1 Анализ конструкций ленточного дозатора муки
Ленточные дозаторы ДВ-50
Предназначены для автоматического непрерывного дозирования легкосыпучих материалов. Применяются на предприятиях пищевой химической металлургической и других отраслей промышленности.
Рисунок 2. Ленточный дозатор ДВ-50:
- paмa; 2 - двигатель; 3 12 - барабаны; 4 - стойка; 5 - впускная воронка; 6 - заслонка; 7 - передвижная гиря; 8 - ролик; 9 - лента;
- коромысло; 11 - счетчик; 13 -выпускная воронка; 14 - опорный ролик.
Дозатор стационарный состоит: из приемной воронки короткого ленточного транспортера с приводом и весового рычажного механизма с грузоприемным роликом расположенным под весовым участком ленты. По заданной погонной нагрузке на ленту и ее скорости устанавливается поток материала обеспечивающий заданную производительность дозатора.
На раме дозатора ДВ-50 установлен ленточный транспортер. Ведущий барабан приводится в движение от электродвигателя. Над лентой дозатора на стойках устанавливается впускная воронка. Дозируемый материал из воронки поступает непосредственно на ленту дозатора. При работе дозатора лента получая движение захватывает материал вытягивая его из воронки.
Весовой механизм дозатора представляет собой рычаг с весовым роликом на одном плече. На ролик действует вес ленты с находящимся материалом на ее участке от оси последнего опорного ролика и до оси ведомого барабана. Этот участок ленты является «весовой платформой» дозатора. Другое плечо рычага тягой соединяется с коромыслом на котором имеется передвижная гиря. Передвижением гири по коромыслу определяется количество материала обеспечивающее заданную производительность дозатора.
Если материал поступает равномерным потоком то коромысло будет находиться в равновесии и будет обеспечиваться подача материала в заданном количестве. Как только вес материала изменится изменится и давление на ролик. Если например количество материала на ленте увеличится ролик будет опускаться одновременно другой конец рычага через тягу будет поднимать правое плечо коромысла. Вследствие этого левое плечо коромысла опустится связанная с ним автоматическая заслонка также опустится и уменьшится выпускное отверстие приемной воронки. В результате выход материала на ленту будет уменьшаться до тех пор пока не восстановитсязаданная производительность.
При уменьшении веса материала находящегося на весовой платформе произойдет обратное: весовой ролик поднимается вверх и коромысло поднимает заслонку вследствие чего увеличится отверстие для подачи материала.
Ленточные дозаторы типа ДВЛ
Ленточные весовые дозаторы ДВЛ используются для непрерывного динамического взвешивания и дозирования сыпучих материалов в технологических потоках металлургической промышленности а также на предприятиях цементной горнорудной угольной строительных материалов пищевой и других отраслей промышленности. Дозатор является комплектным оборудованием в системах управления технологическими процессами но может иметь и самостоятельное автономное применение. Дозатор ДВЛ – система состоящая из весового конвейера электропривода микроконтроллера функционирующая на основе принципа непрерывного взвешивания и дозирования.
В дозаторе используется контроллер СД-01 или Simatic С7-633 ("Siemens" Германия). Сигналы весовых нагрузок на ленту и скорости ее движения обрабатываются системой измерения управления и регулирования. Постоянное сравнение фактического значения массового расхода с заданным значением позволяет определить отклонения.
По величине отклонений рассчитывается управляющий сигнала для регулирования скорости движения конвейерной ленты что обеспечивает поддержание требуемого расхода материала. Контроллер обеспечивает:
автоматическую настройку диапазона взвешивания; задание производительности; измерение скорости транспортерной ленты с учетом "проскальзывания" по сигналам датчиков вращения ведомоговедущего валов
транспортера; вычисление значения текущей производительности; вычисление и суммирование количества массы материала за заданный интервал времени; индикацию параметров на ЖКИ (4 × 20 символов); выдачу
информации на устройство термопечати; обработку входных сигналов и управление электроприводом транспортера; преобразование входных сигналов ДСТ в значения веса материала; контроль блокировок аварийных ситуаций. Управление электроприводом транспортера осуществляется с помощью преобразователя частоты MICROMASTER Vector производства фирмы Siemens.
Рисунок 3. Ленточный дозатор типа ДВЛ.
Рисунок 4. Общий вид ленточного дозатора типа ДВЛ:
- рама конвейера; 2 - приводной барабан с мотор-редуктором; 3 - несущие и поддерживающие ролики; 4 - грузоприемное устройство; 5 - датчик схода ленты; 6 - датчик оборота ленты; 7 - оборотный барабан с устройством натяжения ленты; 8 - очиститель верхней ветви ленты; 9 - очиститель нижней ветви ленты; 10 - формирующая воронка с регулируемым шибером; 11 - борта с аспирационным кожухом; 12 - защитный кожух; 13 - пост местного управления; 14 -датчики скорости и проскальзывания.
Автоматические дозаторы непрерывного действия типа ЛДА
Предназначены для непрерывного дозирования различных кусковых материалов с заданной производительностью. Применяются для подачи угля руды известняка доломита агломерационной шихты и колошниковой пыли на предприятиях металлургической промышленности в пищевой промышленности – при дозировании муки могут быть использованы и для других аналогичных материалов.
Рисунок 5. Автоматический дозатор непрерывного действия типа ЛДА.
Дозатор состоит из электровибрационного питателя 4 с вибродвига-телем 7 и весового транспортера с бесконечной лентой 3 приводимой в движение электродвигателем через редуктор.
Вибрационный питатель подвешивается на амортизаторах 6 к горловине расходного бункера 5 рама 2 весовой части устанавливается на специальной опорной металлоконструкции над сборным конвейером 1. Блок управления дозатором помещается в отдельном шкафу который можно устанавливать на расстоянии до 1000 лот дозатора.
При работе дозатора требуемая производительность задается по шкале электронного прибора ЭПИД. Производительность можно регулировать вращением ручки задания без остановки дозатора.
Подача дозируемого материала на ленту 2 осуществляется электро-вибрационным питателем 10. Лента приводится в движение электродвигателем 12 установленным на основании 1. Нагрузку размещенную на ленте 2 воспринимает рычажная система 8 и передает ее на уравновешивающую пружину 4 механизма 5.
Деформация пружины вызывает соответствующее перемещение плунжера индукционного датчика 3 вследствие чего нарушается равновесие индукционного моста электронного дифференциально-трансформаторного прибора 6 и стрелка 7 прибора отклоняется на величину пропорциональную изменению нагрузки на ленту. При этом контактное устройство включает исполнительный механизм 9 потенциал-регулятора. Последний изменяет напряжение постоянного тока на катушках электровибродвигателя 11 что соответственно увеличивает или уменьшает амплитуду вибраций лотка питателя а следовательно и производительность вибропитателя. Изменение производительности происходит до тех пор пока вес дозируемого материала на ленте конвейера не достигнет заданной величины.
Дозатор для кусковых материалов ДН-4
Предназначен для непрерывного дозирования кусковых материалов с объемной массой 08-16 тм3.
Рисунок 6. Дозатор для кусковых материалов ДН-4.
Принцип работы дозатора основан на изменении скорости ленты транспортера в зависимости от веса дозируемого материала находящегося на ней. При уменьшении веса материала находящегося на ленте скорость ее движения повышается при увеличении веса материала наоборот скорость ленты снижается. Таким образом все время подается заданное количество материала. Регулировка скорости ленты осуществляется электроприводом с магнитным усилителем. Регулятор скорости двигателя управляемый прибором ЭПИД-О5 при изменении веса дозируемого материала на ленте изменяет ее скорость до величины обеспечивающей заданную на приборе производительность.
Ленточный дозатор Р3-ХДА
Относится к дозаторам весового типа и состоит из приемного бункера 3 снабженного сигнализатором уровня муки ленточного транспортера-питателя 7 с приводом 2 весового ленточного транспортера 10 с приводом 20. Лента каждого транспортера прикреплена к цепям которые приводятся в движение от приводных звездочек 1 и 19. Весовой транспортер 17 установлен на раму которая представляет собой рычаг первого рода. Призмой 8 рама опирается на подушку стойки 18. На первом плече рычага укреплены основная шкала 11 дозатора с передвижной гирей 9 и вспомогательная 15 с гирей 16 регулировочный баланс 14 и указатель равновесия 12. На левом плече рычага укреплен металлический флажок 23. На станине дозатора установлен указатель 13 с ограничителями колебаний весового транспортера. На противоположной стороне станины установлен блок из двух бесконтактных сигнализаторов 21 и 22.
Регулирование подачи муки осуществляется с помощью трех заслонок: одной основной 26 укрепленной на винтовом стержне 4 с червячной парой 5 и рукояткой 6 и двух электромагнитных заслонок 24 и 25.
Рисунок 7. Ленточный дозатор муки Р3-ХДА.
Работа дозатора осуществляется следующим образом. Гири 9 и 16 на основной и вспомогательной шкалах устанавливают на заданное значение подаваемой муки (кгмин). Затем при включенном дозаторе вращением рукоятки 6 настраивают дозатор до совмещения указателей равновесия 12 и 13. При отклонении массы дозируемой муки от заданного значения флажок 23 производит включение бесконтактного датчика 21 или 22 в результате чего включаются электромагнитные заслонки 24 или 25 которые перемещаясь в вертикальном направлении увеличивают или уменьшают массу подаваемой муки.
Ленточный дозатор ШД-1М
Предназначен для объемного дозирования муки сахара-песка и др.
Дозатор (рисунок 9 а) состоит из вертикальной шахты 10 горизонтального корпуса 18 со встроенным в него ленточным конвейером и привода.
Шахта 10 снабжена электронными сигнализаторами уровня продукта 11 и 12 и электрическим пультом управления 13. Внутри шахты расположен ворошитель приводимый в движение рычагами 9. На боковой стенке шахты расположено отверстие закрываемое заслонкой 5. Положение заслонки регулируется вращением маховика 3. Через коническую передачу 7 вращение передается горизонтальному валу 6 и реечному зацеплению 8 которое перемещает заслонку 5 в вертикальной плоскости.
Ленточный конвейер и ворошитель приводятся в движение от электродвигателя постоянного тока через ременную передачу закрытую ограждением 15 и редуктор 17. Ременная передача приводит в движение тахогенератор 16 электрический сигнал от которого подается на пульт управления где установлен показывающий прибор (вольтметр) шкала которого отградуирована в оборотах в единицу времени вала электродвигателя 14. Дозируемый продукт высыпается через гибкий рукав 2 нижний конец которого соединен с фланцем 1 устанавливаемым на машине куда осуществляется дозирование. Окно 4 предназначено для контроля работы ленточного конвейера.
Рисунок 8. Ленточный дозатор ШД-1М.
Технологический процесс дозирования происходит следующим образом. Продукт поступает в вертикальную шахту 7 (рисунок 9 б). Стабильное дозирование достигается лишь в том случае если уровень продукта в шахте будет относительно постоянным. Постоянство уровня контролируется сигнализатором уровня: сигнализатор 9 верхнего уровня посылает импульс о необходимости прекращения подачи продукта а сигнализатор 8 нижнего уровня – о необходимости наполнения шахты новой порцией. Ворошитель 6 совершая колебательное движение препятствует сводообразованию. Дном шахты служит лента конвейера 5 уносящая из шахты слой продукта толщина которого а следовательно и производительность дозатора регулируется подъемом или опусканием вертикальной заслонки 10. Регулировать производительность при постоянном положении заслонки можно также путем изменения частоты вращения вала электродвигателя постоянного тока увеличивая или уменьшая при этом скорость ленты конвейера 5.
Слой продукта ссыпаясь с конвейера 5 проходит под постоянными магнитами 11 которые задерживают ферропримеси. По лотку 3 и гибкому рукаву 2 продукт поступает в приемный патрубок 1 машины в которую осуществляется дозирование. Окно 4 служит для очистки конвейера 5 от продукта.
Погрешность дозирования составляет ±15%. Производительность ленточного дозатора до 1100 кгч.
Рисунок 9. Ленточный дозатор ШД-1М непрерывного действия:
а – общий вид; б – схема работы.
Обзор литературы показал что наиболее эффективно использовать дозатор типа ДВЛ так как дозаторы ДН-4 ЛДА применяются для подачи кусковых материалов а питатель ДВ-50 имеет хотя и автоматическую но все же устарелую конструкцию. Дозатор ДВЛ более совершенен взвешивание материала и регулирование скорости транспортёрной ленты происходит без механического вмешательства автоматически что значительно позволяет облегчить труд технологического персонала и повысить качество сырья подаваемого в тестоприготовительное отделение. Кроме того он наиболее надежный в работе имеет небольшие габаритные размеры и простату конструкции.
Дозатор - управляемый электронным контроллером ленточный конвейер с регулируемым асинхронным приводом снабженный тензометрической весоизмерительной системой и датчиком скорости движения ленты. В процессе работы происходит непрерывное взвешивание материала проходящего над весоизмерительным устройством а также измерение скорости движения ленты. Управляющий контроллер рассчитывает текущую производительность дозатора и при необходимости формирует корректирующий сигнал на регулируемый частотный привод. Ленточный дозатор муки - механосборочная конструкция состоящая из станины приводного и натяжного барабанов транспортёрной ленты привода приёмного бункера и весоизмерителя.
Дозируемый продукт поступает через приёмный бункер на котором установлена подвижная формирующая заслонка позволяющая регулировать высоту слоя продукта на транспортёрной ленте. Наличие механического запорного устройства (шиберной или штыревой заслонки) перед приёмным бункером дозатора необходимо для обеспечения возможности тарировки и поверки дозатора без освобождения питающего бункера от продукта.
Транспортерная лента натянута между двумя барабанами – приводным и натяжным валы которых установлены в корпуса подшипников. Для смазки подшипников качения предусмотрены масленки. Степень натяжения ленты регулируется путем перемещения натяжного барабана в направляющих станины с помощью шпилек. При оптимальном натяжении транспортерной ленты ее нижняя ветвь располагается между рисками нанесенными на втулки уравнителя.
Вращение приводного барабана осуществляется приводом тихоходный вал которого соединён с валом барабана посредством муфты. Быстроходный вал привода соединён с датчиком скорости. Привод при помощи болтов крепится к опоре. Привод может быть установлен как с правой так и с левой стороны дозатора если смотреть по ходу движения транспортёрной ленты. В стандартном исполнении дозатора реализовано левостороннее расположение привода.
Поперечины определяют ширину и усиливают конструкцию дозатора. Роликоопоры установленные в фиксирующих пазах поперечин и опоре поддерживают верхнюю ветвь транспортёрной ленты. Роликоопора установленная на каркасе весоизмерителя и симметрично расположенные относительно неё роликовые опоры образуют весоизмерительную площадку.
Для исключения возможного просыпания продукта установлены борта закреплённые на боковых кожухах.
Все вращающиеся части дозатора закрыты защитными кожухами. Кожух передний служит для ограждения приводного барабана и направления продукта в выпускной патрубок. Через люк возможен доступ к выпускному патрубку. В стенке заднего кожуха имеются жалюзи для наблюдения за положением транспортёрной ленты. При работе с пылящими продуктами над лентой может устанавливаться аспирационный кожух.
Ленточный дозатор состоит из ленточного транспортера и вертикального бункера с заслонкой устройством которого можно регулировать толщину слоя муки уносимой из бункера.
Для обеспечения точности дозирования высота столба над лентой транспортера поддерживается в определенных пределах при помощи поворотных валиков с заслонкой которая по мере заполнения емкости под заслонкой и над ней под действием тяжести муки опускается. При этом размыкаются контакты конечного выключателя и подача муки прекращается. Когда мука расходуется опускается заслонка под действием груза возвращается в исходное положение и выключает привод транспортера подающего в бункер муку.
простота конструкции:
широкий придел регулирования:
возможность использовать и весовой принцип дозирования.
распыл муки при большой производительности то есть снижения точности дозировки.
2 Расчет производительности ленточного дозатора и мощности
Производительность дозатора:
где b– ширина ленты м;
h – толщина слоя муки на ленте м;
V – скорость ленты мс;
j – объемная масса муки кгм3.
П = b*h*V*j=08(м)*0005(м)*450(кгм3)*013(мс)=0234(кгс).
П=0234(кгс)*3600*241000=20(тсут).
Мощность электродвигателя ленточного дозатора:
где K3 – коэффициент запаса мощности (K3=12 13);
P – тяговое усилие ленты дозатора из литературы [1] P-12800 H;
– КПД привода (=05 08).
3 Расчет конструкции на прочность
3.1 Расчет открытой прямозубой передачи
Рисунок 10. Силы действующие в зацеплении.
Расчет проводим по литературе [2].
Режим работы привода средний;
t = 2*104 час – ресурс передачи;
Материал шестерни: сталь 45 улучшение HB1 = 269÷302 Gt1 = 750 МПа;
Материал колеса: сталь 45 улучшение HB2 = 255 Gt2 = 640 МПа.
Общее число циклов нагружения зубьев колес:
NΣ2 = 60* n3 * t*зац; (3)
NΣ2 = 60*50*2*104 *1= 60*106;
NΣ1 = NΣ2 * Uзуб; (4)
NΣ1 = 60*106 * 12 = 72*106
где зац = 1 – число зацеплений за один оборот.
Эквивалентное число нагружения:
NHE1 = kHE* NΣ1; (5)
NHE1 = 0.25*72*106 = 18*106;
NHE2 = kHE* NΣ2; (6)
NHE2 = 025* 60*106 = 15*106.
Расчетные значения твердости колес HB1 и HB2
шестерни: HB1 = (269+302)2 = 285; (7)
колеса: HB2 = (258+262)2 = 2585. (8)
Длительные пределы выносливости он:
он1 = 2*285+70= 640 МПа;
он2 = 2*2585+70= 587 МПа.
Допускается напряжение при неограниченном ресурсе работы:
где Sh = 11 – коэффициент безопасности по контактным напряжениям;
[он1 ] = 640 11 = 582 МПа;
[он2 ] = 587 11 = 524 МПа.
Базовое число циклов нагружения Noh :
Noh = 30* HB 2.4; (11)
Noh1 = 30* 285 2.4 = 23*106;
Noh1 = 30* 258.5 2.4 = 185*106.
Допускаемые напряжения на контактную выносливость[2]:
[н ] = 05*([ н1 ]+[н2]); (12)
[н ] = 05 *(645+620) = 632.5 МПа;
[н1 ] = [он1 ] * ; (13)
[н1 ] = 582*= 6325 МПа;
[н2 ] = 534*=620 МПа.
Межосевое расстояние:
Qw = (Uзуб + 1) * ; (14)
Qw = (12+1)*= 207 мм
где Uзуб – передаточное отношение передачи;
Т3 – вращающийся момент на колесе Нм;
а – коэффициент учитывающий относительную ширину зубчатых колес;
С – радиус кривизны зубьев для прямозубого зацепления;
[н ] – допустимое напряжение на контактную выносливость МПа;
KH – коэффициент нагрузки;
х – коэффициент приработки для среднего режима.
K = K0* (1-х)+х; (16)
K = 08*(1-05)+05=09;
K – коэффициент концентрации нагрузки по длине зуба;
K0 – коэффициент концентрации нагрузки до приработки колес;
b1d1 = 0.5(Uзуб+1)*a; (17)
b1d1 = 05(12+1)*03=042;
это значение подходит и K0=08 для прямозубых (симметричных) колес.
где V – скорость колеса косозубой передачи соответствует восьмой степени точности значит Kv = 1.1 коэффициент динамической нагрузки.
Найденное расчетное значение Qw = 207 мм округляется до стандартного значения Qw = 200 мм по ГОСТ 2186-76.
где b2 – ширина колеса.
где b1 – ширина шестерни.
Находим модуль передачи:
mn = (0.01÷0.02)* (21)
mn = (0.01÷0.02)*200=2÷4;
принимаем mn =30 мм по ГОСТ 9563-80.
Находим суммарное число зубьев:
Находим число зубьев:
Z3 = =62963 – шестерни;
Z4 = Z3 *Uзуб ; (24)
Z4 = 63*14=754 75 – колеса.
Находим диаметр делительных окружностей:
Диаметры окружностей впадины и вершин зубьев колес:
dа1 = 89+2*3=267 мм.;
dа2 = 225+2*3=675 мм.;
df1 =89-2.5*3=81.5 мм.;
df2 = 225-25*3=2175 мм.
Находим силы зацепления:
где Ft – окружная сила.
Fr = 4417*tg200 = 1716.642H;
Fr – радиальная сила;
Таблица №3. Исходные данные
Передаваемая мощность – N = 2800
Частота вращения шестерни – n1 = 60
Число зубьев шестерни – Z1 = 63
Ориентировочное передаточное отношение – U0 = 12
Твердость материалов – сталь 45 (нормализованная или улучшенная) – НВ = 350
Коэффициент ширины винца – К3 = 016
Коэффициент неравномерности нагрузки – К4 = 12
Коэффициент концентрации нагрузки – К6 = 12
Коэффициент динамичности – К7 = 11
Коэффициент формы зуба – К8 = 4
Таблица №4. Результаты расчета
Число зубьев колеса - Z2 = 75
Передаточное число - U = 1190476
Частота вращения колеса – n2 = 504
Крутящий момент на валах: M1 = 445667; M2 = 530556
Модуль зацепления - m =3
Начальные окружности колес: - D1=189; D2= 225;
Наружные диаметры колес: - DH1=195; DH2= 231
Диаметры ступицы шестерни - Ds= 7453263
Диаметры вала шестерни – Db3= 5623759
Диаметр вала колеса - Db4 = 5642005
Диаметры ступицы колеса – Ds1= 7398807
Ширина колес - B= 60
Межосевое расстояние – А= 207
Допускаемое контактное напряжение – S1= 9099999
Рабочее контактное напряжение – S=6077327
Допускаемое напряжение изгиба – S2= 6066666
Рабочее напряжение изгиба – S3=1383374
Окружная сила – Ft= 471605
Радиальная сила – Fr= 1716642
Нормальная сила – F0= 5018729
3.2 Расчет открытой цилиндрической передачи
ресурс работы t = 2*104 часа;
режим средний равновероятный;
материал шестерни – сталь 45;
улучшение НВ1 = 269÷302;
термообработка – улучшение;
материал колеса – сталь 45
NΣ2 = 60*n5*tΣ*зац; (30)
NΣ2 = 60*43*2*104*1=51*106;
NΣ1 = NΣ2 * Uкон; (31)
NΣ1 = 51*106*10= 510*106.
Эквивалентное число циклов нагружения:
Nhe1 = КНЕ * NΣ1; (32)
Nhe1 = 0.25*51.6*106=12.9*106;
Nhe2 = 025 * 516*106= 129*106.
Расчетные значения твердости колес НВ1 и НВ2 :
шестерни: НВ1 = (269+302)2 = 285;
колеса: НВ2 = (255+262)2 = 2585.
Делительные пределы выносливости он:
он1 = 2*285+70=640 МПа;
он2 =2*2585+70=587 МПа.
Допускаемые напряжения при неограниченном ресурсе работы:
где Sн – коэффициент безопасности по контактным напряжениям.
Базовое число циклов нагружения:
Nон = 30 НВ 24 ; (34)
Nон1 = 30 *285=23*106 ;
Nон2 = 30*285524= 185*106.
допускаемые напряжения для расчета на контактную выносливость:
[н] = ([н1]+[н2]); (35)
[н] = (588+556)= 572 МПа;
[н1] = [он1] *; (36)
[н1] =582* = 588 МПа;
[н2] = 534* = 556 МПа.
Внешний делительный параметр колеса (de2):
de2 = 1650* где (37)
Кн = Кr*Kv = 1*1=1 – коэффициент нагрузки;
de2 = 1650 * = 552424 мм.
bdm1 = 0166*= 029926 03;
полученное значение соответствует К = 1 – коэффициент концентрации нагрузки до приработки колес;
где К – коэффициент концентрации нагрузки по длине зуба;
При такой скорости принимаем седьмую степень точности изготовления передачи с Кv = 1 – коэффициент динамической нагрузки.
Принимаем число зубьев колеса Z6 = 17.
Внешний окружной модуль:
Тогда число зубьев шестерни:
Диаметр внешней делительной окружности шестерни:
внутренней делительной окружности:
dм1 = de1 *0857; (43)
dм1 = 51*0857=3367524 мм.
Угол делительных конусов шестерни:
Угол делительного конуса колеса:
= 90 - 45 03 28 = 45 03 32.
Внешние конусные расстояния:
Re = 05*3* = 36.06041 мм.
ширина зубчатых венцов:
b = b1 = b2 = Kbe* (47)
b = 0.285*36.06041 32 мм.
Силы в зацеплении конических прямозубых колес:
dm2 = de2 * 0.857; (49)
dm2 = 0.857*55.2424= 33.67524;
Fa2 = -Fr1= Ft*tg α *cos ; (50)
Fa2 = 1267.354*tg 20* 45 03 28 = 1025.188 H;
где Fr2 – радиальная сила;
cos 45 03 28 = 06947;
sin 45 03 28 = 0.7083.
Таблица №5. Исходные данные
Передаваемая мощность – N = 1350785
Частота вращения шестерни - n1 = 43
Ориентировочное передаточное отношение – U0 = 1
Межосевой угол – А = 90
Число зубьев шестерни – Z1 = 17
Материал – сталь 45 (нормализованная или улучшенная)
Твердостью – НВ = 400
Таблица №6. Результаты расчета
Крутящий момент на валу шестерни - М1 = 30
Крутящий момент на валу колеса – М2 = 30
Фактическое передаточное отношение – U = 1
Число зубьев колеса – Z2 =17
Частота врашения колеса – n2 =43
Торцовый модуль зацепления – m = 3
Начальные окружности колес: d1 = 51; d2=51
Конусное расстояние – L = 360641
Ширина зубчатого венца – В = 32
Внешняя высота зуба – h =66
Внешний диаметр вершин зубьев шестерни – DH1 = 552424
Внешний диаметр вершин зубьев колеса – DH2 = 552424
Угол начального конуса шестерни – а1= 4500328
Угол начального конуса колеса – а2 = 4500328
Диаметр вала шестерни - Db1= 232243
Диаметр ступицы шестерни – Ds1= 3367524
Диаметр вала колеса – Db2 = 23.2243
Диаметр ступицы колеса – Ds2 = 3251402
Допускаемое контактное напряжение – S = 800
Рабочее контактное напряжение – S1 = 7135311
Окружная сила – Ft =1267354
Осевая сила – F0 = 1025188
Радиальная сила – Fr = 02294735
Нормальная сила – Fо = 2141828
Находим диаметры вала:
где [] = 20 МПа – допускаемое напряжение на кручении для материала ст. 45.
Таблица №7. Выбираем шарикоподшипники радиальные однорядные легкой серии по ГОСТ 8338 – 75
Диаметр корпуса D мм.
Ширина подшипника В мм.
Радиус округления r мм.
Грузоподъемность к.Н
отношение = =0081; (52)
значение соответствует 0028;
отношение = = 0433≥028 (53)
следовательно х= 10; х= 0
тогда Рэкв= х*Pr4*Y*Kb*Kт. (54)
Рэкв= 1*129171*10*12= 1902 Н.
Расчетная долговечность подшипников:
L1 = = 396.761 млн. обор.
Таблица №8. Исходные данные
Крутящий момент на валу – М = 18000
Радиальная нагрузка на вал – Р = 951
Плечо приложения нагрузки – L = 50
Осевая нагрузка на вал – сталь 45 + термообработка – нормализация
Допускаемое напряжение на кручение - S = 2026583
Предел прочности материала S1 = 760
Коэффициенты параметров вала:
Коэффициент концентрации напряжения изгиба – К3 = 22
Коэффициент концентрации напряжений кручения – К4 = 14
Коэффициент шероховатости поверхностей – К5 = 095
Таблица №9. Результаты расчета
Диаметр вала в опасном сечении – D = 25
Запас прочности по нормальным напряжениям – С1 = 4068884
Запас прочности по касательным напряжениям – С2 = 1718512
Общий запас прочности вала – С3 = 3959417
Таблица №10. Расчет шариковых подшипников качения
Диаметр вала – Db =25
Тип – радиальный однорядный легкой серии
Частота вращения кольца подшипника – N = 31
Радиальная нагрузка – Fr = 0951
Осевая нагрузка – Fa = 0
Коэффициент условий работы Kb = 2
Рабочая температура подшипника – Tr = 40
Заданная долговечность подшипника – L = 5000
Таблица №11. Результаты расчета
Номер подшипника – N0 = 205
Внутренний диаметр – Db =25
Наружный диаметр – Dn = 52
Динамическая грузоподъемность – С = 14
Статическая грузоподъемность – С0 = 695
Коэффициент осевого нагружения – Е = 0
Коэффициент радиальной нагрузки – х = 1
Коэффициент осевой нагрузки y = 0
Эквивалентная нагрузка – Ре = 1902
Расчетная долговечность подшипника – Lh = 2144073
Технология изготовления вала ролика
1 Технология изготовления вала ролика
Назначение и описание вала ролика
Части машин и механизмов могут вращаться двигаться поступательно или колебаться передавая свое движение и усилия другим деталям. Наиболее распространенным движением является вращательное при котором осуществляется вращение различных деталей на валах и осях.
Вал представляет собой тело вращения цилиндрической конической и другой формы опирающееся на две или несколько опор. На валу закрепляются шкивы зубчатые колеса маховики и т. п. Некоторые из этих деталей называемые ведущими получают вращательное движение от постороннего источника энергии (двигателя). К другим деталям вращение передается валом. Они называются ведомыми. Таким образом вал при своем движении.
Момент обязательно передает усилие (вращающий момент) а поэтому испытывает деформации кручения и изгиба.
Валы по форме разделяются на прямые или изогнутые (коленчатые) целые или составные (собранные из нескольких частей) сплошные или полые (пустотелые).
При проектировании дипломного проекта рассматривается ступенчатый вал. Ролик на валу будет крепиться в двух местах по средствам натяга.
Конструктивно-технологический анализ детали
Вал ролика являются ответственной деталью. Поэтому наряду с правильным определением форм и размеров валов первостепенное значение в обеспечении их прочности и работоспособности имеет способ изготовления — выбор заготовок и методов их получения изыскание и осуществление рациональных вариантов технологических процессов обработки.
Заготовку данного вала осуществляется резанием прутка дисковой пилой. Заготовкой вала является именно пруток так как диаметр вала намного меньше его длины. Материал вала – сталь20Х13. Эта сталь характеризуется хорошим сочетанием свойств позволяющим применять её в виде листового и сортового проката поковок и штамповок а также в отливках для аппаратуры работающей под давлением. Она хорошо деформируется в горячем и холодном состояниях обрабатывается резанием и сваривается всеми видами сварки.
Выбор указанной стали обусловлен главным образом тем что по механическим свойствам она вполне удовлетворяет требованиям предъявляемым к деталям затворов и вместе с тем используются для изготовления корпусов и крышек сосудов что имеет немаловажное значение в производстве. Не исключается применение и сталей других марок отвечающих требованиям правил Госгортехнадзора и ОСТ 26-291—71.
Однако при этом следует иметь в виду не только механические свойства выбранных материалов но и возможность получения качественных заготовок из них склонность к образованию некоторых характерных дефектов в процессе той или другой обработки и возможность их исправления без снижения качества. Также данная сталь должна иметь высокую антикоррозионную стойкость. Это одна из важнейших характеристик выбора материалов в пищевом машино и аппаратостроении.
Для количественной оценки технологичности детали используются показатели технологичности: коэффициенты использования материала точности обработки шероховатости поверхности .
Проанализируем рабочий чертеж детали.
Таблица №12. Результаты анализа рабочего чертежа
Количество поверхностей
Коэффициент использования материала:
Коэффициент точности обработки :
средний квалитет точности обработки детали по всем поверхностям;
Коэффициент шероховатости поверхности :
среднее числовое значение параметра шероховатости всех поверхностей детали;
Сравнивая полученные результаты с нормативными можно сказать что деталь по показателям шероховатости поверхности и коэффициенту точности технологична:; .
Основными видами заготовок в пищевом машиностроении являются отливки из черных и цветных металлов поковки и штамповки заготовки из листового металла проката сварные заготовки заготовки из неметаллических материалов
В моем случае для изготовления вала перемешивающего устройства возьмем пруток так как эта заготовка обеспечивает заданное качество готовой детали при ее минимальной себестоимости.
Выбор припусков и допусков
Вследствие незначительных деформаций валов припуски на механическую обработку могут быть уменьшены примерно в 2 раза против величин принимаемых для значительных деформаций.
Несмотря на большую разницу в размерах для всех валов приняты минимальные и одинаковые припуски по диаметрам — 5 мм на сторону по торцам — 25 мм.
Выбор средств технологического оснащения
Токарная обработка - это один из самых используемых методов механической обработки деталей резанием. С применением токарных работ наиболее часто проводится механообработка следующих деталей: различных шестерней валов и пружин а также любых изделий требующих соблюдения идеальной цилиндрической конической сферической и др. форм.
Токарный станок представляет собой в большинстве случаев установку для вращения заготовки и различный инструмент: резцы сверла развертки зенкеры и т.д. для ее обработки. Токарные станки бывают различных размеров и позволяют с высокой точностью обрабатывать как небольшие детали размер которых измеряется долями миллиметра так и очень крупные длиной до нескольких метров.
Различают следующие станки для токарных работ: токарно-винторезный станок чаще всего применяемый для механообработки мягких металлов в особенности в мелкосерийном производстве. Позволяет выполнять разнообразные работы от обточки до нарезания резьб. Токарно-карусельный станок отличается вертикально направленной осью вращения и используется для мехобработки крупных деталей - колец валов дисков и так далее. Также на нём можно прорезать канавки и протачивать отверстия по центральной оси. Лоботокарный станок используется для обработки труб валов и других подобных деталей. Токарно-револьверный станок позволяет проводить сложные серийные токарные работы из штучных заготовок. Автомат продольного точения и многошпиндельный токарный автомат предназначены для механообработки серийных изделий с высокой скоростью обработки и высокой точностью (то есть минимизацией допусков). В обоих аппаратах чаще всего используются различные прутки или специальные заготовки.
Токарно-карусельные станки бывают одностоечные (стол с диаметром до 1500 мм) и двухстоечные. В первом случае на вертикальной стойке имеются направляющие по которым может перемещаться траверса 1 (рис. 139). На траверсе 1 имеются направляющие по которым в горизонтальном направлении перемещается поворотный суппорт 2 (револьверная головка) несущий режущие инструменты которые периодически можно вводить в действие путем поворота головки вокруг ее горизонтальной оси. Перемещение траверсы по стойке и суппорта по траверсе производят вручную вращением маховиков 3 и 4 или механически при включении механизмов подач. Сбоку стола размещен поперечный суппорт 5 с четырехгранным поворотным резцедержателем.
Обработка может производиться одновременно инструментами помещенными в верхнем и боковом суппортах.
Фрезерные станки - группа металлорежущих станков в классификации по виду обработки. Фрезерные станки предназначены для обработки с помощью фрезы плоских и фасонных поверхностей тел вращения зубчатых колёс и т. п. металлических и других заготовок. При этом фреза вместе со шпинделем фрезерного станка совершает вращательное (главное) движение а заготовка закреплённая на столе совершает движение подачи прямолинейное или криволинейное. Управление может быть ручным автоматизированным или осуществляться с помощью системы ЧПУ (CNC).
Металлорежущий инструмент фрезерной группы станков. Концевые фрезы.
Во фрезерных станках главным движением является вращение фрезы а движение подачи — относительное перемещение заготовки и фрезы.
Вспомогательные движения необходимы в станке для подготовки процесса резания. К вспомогательным движениям относятся движения связанные с настройкой и наладкой станка его управлением закреплением и освобождением детали и инструмента подводом инструмента к обрабатываемым поверхностям и его отводом; движения приборов для автоматического контроля размеров и т. д. Вспомогательные движения можно выполнять на станках как автоматически так и вручную. На станках-автоматах все вспомогательные движения в определенной последовательности выполняются автоматически.
Шлифованием называют процесс обработки заготовок резанием с помощью абразивных кругов. Абразивные зерна расположены в круге беспорядочно и удерживаются связующим материалом. При вращательном движении круга в зоне его контакта с заготовкой часть зерен срезает материал в виде очень большого числа тонких стружек (до 100000000 в минуту). Шлифовальные круги срезают стружки на очень больших скоростях — от 30 мс и выше. Процесс резания каждым зерном осуществляется почти мгновенно. Обработанная поверхность представляет собой совокупность микроследов абразивных зерен и имеет малую шероховатость. Часть зерен ориентирована так что резать не может. Такие зерна производят работу трения по поверхности резания.
Абразивные зерна могут также оказывать на заготовку существенное силовое воздействие. Происходит поверхностное пластическое деформирование материала искажение его кристаллической решетки. Деформирующая сила вызывает сдвиги одного слоя атомов относительно другого. Вследствие упругопластического деформирования материала обработанная поверхность упрочняется. Но этот эффект оказывается менее ощутимым чем при обработке металлическим инструментом.
Тепловое и силовое воздействие на обработанную поверхность приводит к структурным превращениям изменениям физико-механических свойств поверхностных слоев обрабатываемого материала. Так образуется дефектный поверхностный слой детали. Для уменьшения теплового воздействия процесс шлифования производят при обильной подаче смазочно-охлаждающих жидкостей.
Шлифование применяют для чистовой и отделочной обработки деталей с высокой точностью. Для заготовок из закаленных сталей шлифование является одним из наиболее распространенных методов формообразования. С развитием малоотходной технологии доля обработки металлическим инструментом будет уменьшаться а абразивным — увеличиваться.
Расчет режимов резанья и норм времени
Основными элементами режимов резания являются: скорость резания подача и глубина резания. Установление рациональных режимов резания для любого вида механической обработки заключается в выборе оптимального сочетания глубины резания подачи и скорости резания обеспечивающих наибольшую производительность при соблюдении всех требований предъявляемых к обрабатываемой детали. При назначении элементов режимов резания учитывают характер обработки тип и размеры инструмента материал его режущей части материал и состояние заготовки тип и состояние оборудования. Элементы режима резания обычно устанавливаются в порядке указанном ниже.
Рассмотрим для определения режимов и норм времени одну операцию – вертикально-фрезерная (смотри технологический процесс операция 20).
Глубина резания t: при черновой (предварительной) обработке назначают по возможности максимальную t равную всему припуску на обработку или большей части его; при чистовой (окончательной) обработке – в зависимости от требований точности размеров и шероховатости обработанной поверхности.
Примем глубину резания t = 1 мм.
Подача S: при черновой обработке выбирают максимально возможную подачу исходя из жесткости и прочности системы СПИЗ мощности привода станка прочности твердосплавной пластинки и других ограничивающих факторов; при чистовой обработке – в зависимости от требуемой степени точности и шероховатости обработанной поверхности.
табличное (матричное) значение подачи ;
коэффициент учитывающий состояние обрабатываемой поверхности;
коэффициент учитывающий материал инструмента;
коэффициент учитывающий форму обрабатываемой поверхности;
коэффициент учитывающий влияние закалки;
коэффициент учитывающий жесткость технологической системы;
коэффициент учитывающий материал обрабатываемой детали.
табличное (матричное) значение скорости резания ;
коэффициент учитывающий свойства обрабатываемости материала;
коэффициент учитывающий влияние угла в плане;
коэффициент обрабатываемости материала;
коэффициент учитывающий влияние СОЖ;
коэффициент учитывающий вид обработки.
Исходным документом при нормировании операции технологического процесса является операционная технологическая карта. Норма времени на любую станочную работу определяется по формуле:
штучно-калькуляционное время на обработку одной единицы изделия;
основное время – время непосредственно затрачиваемое на изменение формы и размеров изделия;
время обслуживания рабочего места (смена затупившегося инструмента сметание стружки смазка чистка станка и т. п.);
вспомогательное время – время затрачиваемое на выполнение приемов помогающих произвести на станке изменение формы и размеров изделия;
время на отдых и личные надобности;
норма подготовительно-заключительного времени на партию деталей в N штук;
N – число деталей в партии.
Норма основного времени:
– величина врезания и перебега инструмента;
– число проходов инструмента необходимое для снятия припуска;
подача за одну минуту (минутная подача).
Величина врезания и перебега инструмента равна 3 мм для удаления припуска необходимо два прохода инструмента следовательно
Норма вспомогательного времени состоит из времени на установку и закрепление детали в приспособлении времени связанного с переходом (включение и выключение подачи подвод и отвод инструмента и т.п.) и времени на контрольные измерения .
Примем измерение размеров 10 мин.
Основное и вспомогательное время в сумме дают оперативное время:
Нормативы времени на обслуживание рабочего места и отдых приведены в процентах от оперативного:
Определение подготовительно-заключительного времени.
Подготовительно-заключительное времянормируется на партию деталей и часть его приходящаяся на одну деталь включается в норму штучно-калькуляционного времени. Подготовительно-заключительное время включает в себя: ознакомление с работой; настройку оборудования на выполнение данной работы; пробную обработку детали; получение задания; получение режущего инструмента приспособлений; сдачу продукции; сдачу инструмента приспособлений. Подготовительно-заключительное время в зависимости от используемого оборудования определяется из таблиц а при обработке деталей на сверлильных станках в кондукторах составляет приблизительно 11 мин.
1 Техническое обоснование
Растущий спрос на хлебобулочные изделия и в частности на мелкоштучные требует увеличение выпуска этой продукции и улучшение выпуска этой продукции и улучшения ее качества.
Оборудование для дозировки муки – ленточный дозатор муки – важнейшая часть паточной линии. Дозатор сыпучих компонентов служит для отмеривания определенных порций муки в соответствии с рецептурой.
Дозировка муки как основного сырья одна из важнейших операций технологического процесса приготовления теста. От точности дозирования муки зависит соблюдение установленной рецептуры а следовательно и качество изделий. Поэтому основным требованием к дозаторам муки является точность дозирования.
Производительность ленточного дозатора П = 20тсутки.
Масса дозатора – 240кг.
Точность дозирования – 15%.
На участке поточной линии где используется ленточный дозатор муки производятся следующие операции: загрузка муки в бункер дозатора выгрузка в определенных дозах (дозировка) муки из бункера дозатора на ленточный конвейер.
Проектируемый вариант
По способу выполнения
Для выгрузки муки из бункера дозатора на ленточный конвейер используется следующие типы дозаторов. Дозаторы непрерывного действия – барабанные тарельчатые шнековые ленточные вибрационные и дозатор периодического действия – бункерный. Из перечисленных дозаторов свой выбор останавливаем на бункерном так как это наиболее распространенный дозатор на пищевых предприятиях. Имеет небольшие размеры простоту конструкции надежность работы. Кроме этого изготовление монтаж дозатора можно осуществить своими силами непосредственно на предприятии. Тем самым поощряя у работников предприятия рационализаторские внедрения.
2 Экономическое обоснование
Капитальные затраты на установку и монтаж ленточного дозатора составляет 30 тыс.руб. которые по предполагаемым расчетам окупятся за короткий срок и позволяет снизить себестоимость готовой продукции на несколько пунктов.
3 Экономический расчет
Таблица №14. Данные для расчёта
Производительность дозатора:
до модернизации кгсут
после модернизации кгсут
Цена оборудования тыс.руб.
Норма амортизационных отчислений на оборудование %
Норма расхода на содержание и текущий ремонт оборудования %
Стоимость 1т. муки тыс.руб.
В расчете принимаем что расход электроэнергии не изменяется.
Определяем годовую выработку хлеба:
qг – среднегодовое потребление муки на душу населения равно 012 тоннгод;
Nчис – численность населенного пункта чел.
Определяем количество хлеба:
Пгв – годовая выработка хлеба тгод;
Км = *100%=1096875 (тгод).
Экономия по муке составит:
коэффициент 02 - уменьшение потери сырья %.
Определяем экономию средств в результате модернизации:
C2 = Эм * Цм где (71)
C2 = 2194(тгод)*7= 1536 (тыс.руб.год).
Изменение затрат на амортизацию оборудования:
И – цена на модернизацию тыс. руб.;
Ао – норма амортизационных отчислений на оборудование 15%.
Изменение затрат на содержание и текущий ремонт оборудования:
Но – норма расхода на содержание и текущий ремонт оборудования.
Гэ = С2 – Изо – Иро (74)
Гэ = 1536 – 45 – 18 = 1473 тыс.рубгод.
Расчет срока окупаемости:
Срок окупаемости оборудования:
И – инвестиции тыс.руб;
Гэ – годовая экономия тыс.руб.
Таблица №15. Показатели эффективности
Величина показателей
Выроботка продукции тгод
Годовая экономия тыс.руб.
Срок окупаемости оборудования год
Безопасность и экологичность проекта
1 Основные опасные и вредные производственные факторы
На предприятиях хлебопекарной промышленности возникает опасность травмирования обслуживающего персонала при нарушении правил техники безопасности в процессе эксплуатации машин и механизмов.
При использовании электрических установок (электродвигателей пультов управления оборудованием и т.д.) возникает опасность поражения электрическим током; превышение давления в сосудах работающих под давлением (паровые котлы баллоны теплообменники) грозит взрывом и т.д.
Перемещение основного сырья – муки сопровождается значительным выделением пыли. Превышение ее ПДК указанной в СН 245-71 и правилах по технике безопасности и производственной санитарии для соответствующих отраслей промышленности (2 - 6 мгм3) может привести к профессиональным заболеваниям повышение концентрации пыли более 10-15 гм3 при наличии источника искрения – к взрыву.
В хлебопекарной промышленности многие технологические процессы связанные с брожением сопровождаются выделением в окружающую среду диоксида углерода (емкостей бункерных тестомесильных агрегатов чаны для брожения теста при ведении технологического процесса на жидкой фазе и др.). ПДК диоксида углерода в воздухе составляет 05%. Превышение этой концентрации неблагоприятно отражается на здоровье работающих. В некоторых случаях при значительном превышении ПДК (выше 6 - 7%) может привести к летальному исходу.
Неудовлетворительными могут оказаться условия труда при недостаточной освещенности при недостаточной степени механизации на ряде участков например при передвижении деж при эксплуатации тестомесильных машин периодического действия и др.
Анализ опасных факторов
Целью данного проекта является модернизация ленточного дозатора муки.
Таблица №16. Анализ возможных опасных и вредных производственных факторов (ГОСТ 12.1.005-74 ССБТ)
Производственный фактор
Производственное оборудование
Движущиеся машины и механизмы
Движущиеся механизмы в оборудовании
Повышенная напряженность электрического поля
Электродвигатель электрическая цепь
Повышенный шум и вибрация
Электродвигатель и движущиеся части дозатора
Тестоприготовительное отделение
Психофизиологические.
Нервнопсихологические перегрузки монотонность труда
2 Требования охраны труда к ведению технологических процессов
Особенности технологических процессов на предприятиях хлебопекарной промышленности диктуют необходимость при проектировании предусматривать меры безопасности и создание комфортных и безопасных условий труда. В соответствии с санитарной характеристикой производственных процессов предприятия относятся по СНиП 11-92-76 «Вспомогательные здания и помещения промышленных предприятий» к следующим категориям:
а)основные производственные процессы –IVа;
б)производственные процессы ремонтно-механических мастерских столярных мастерских – 1б;
в)производственные процессы топочных отделений хлебопекарных печей при работе на твердом топливе – IIб.
Цехи предприятий хлебопекарной макаронной и кондитерскойпромышленности согласно СНИП II-М.2-72 относятся к категории взрыво- и пожароопасности в зависимости от технологических процессов (от Б до Д). Например склад бестарного хранения муки – к категории Б топочное отделение – к категории Г и т.д.
На хлебопекарных предприятиях после просеивания мука поступает для замеса в тестомесильное отделение где замешивание производится на периодически действующих тестомесильных машинах с подкатными дежами различной емкости (330 270 л и т.д.) и агрегатах непрерывного замешивания теста (ХТР И8-ХАГ-6 Р3-ХТН и др.). На макаронных предприятиях мука после просеивания поступает для замеса в шнековые прессы на кондитерских – на тестомесильные агрегаты.
При обслуживании тестомесильных машин периодического действия дложны быть установлены ограждения и предусмотрена блокировка их с электродвигателем. Блокировка обеспечивает отключение электродвигателя при снятии ограждения снятии крышки колпака (щитка).
Тестомесильные машины с подкатными дежами должны иметь приспособления надежно запирающие во время замеса дежу на фундаментной плите машины. Дежеопрокидыватели (с подъемом и без подъема дежи) должны подвергаться термическому испытания не реже одного раза в год. При установлении опрокидывателей с подъемом дежи (ХОД ХОУ ПО-1 ПО-2) следует обеспечить безопасность их эксплуатации снабдив ограждениями как передаточные устройства так и места подъема дежи.
Тестоспуски должны быть снабжены съемными предохранительными решетками.
Очистка тестопусков и бункеров должна производится скребками на длинной рукоятке. При необходимости спуска рабочего в бункера для брожения теста и в тестоспуски должны соблюдаться порядок. При ведении технологического процесса с применением метода тестоведения на жидкой фазе и применением в связи с этим емкостей для рожения необходимо обеспечить удаление углекислого газа получаемого в процессе брожения и при необходимости зачистки емкостей соблюдать меры безопасности принятые для работы в емкостях.
Для уменьшения шума необходимо своевременно заменять износившиеся детали (особенно зубчатых передач) обеспечить заземление электродвигателя производить окраску оборудования в светлые тона а стены облицовывать глазурованными плитками.
Высота помещения тестомесильного отделения предусматривается в зависимости от устанавливаемого оборудования но не менее 48 м. При установке тестомесильных агрегатов непрерывного действия (И8-ХАГ-6 и др.) следует оставлять высоту от вера оборудования до верхнего перекрытия не менее 18 м для удобства ремонта проходы между устанавливаемыми агрегатами – не менее 1 м.
В тестомесильном отделении хлебопекарных преприятий должны быть обеспечены освещение (естественное и искусственное) и кратность обмена воздуха в соответствии со СНиП а также отраслевыми правилами техники безопасности и производственной санитарии для хлебопекарной промышленности. В соответствии с этими правилами освещенность в тестомесильных цехах должна составлять 200 лк. Воздухообмен должен обеспечить комфортные условия труда. Кратность воздухообмена рассчитывается в зависимости от условий на рабочих местах и может колебаться в пределах от 2 до 4.
Паропровод и трубопровод горячей воды (все тепловыделяющие поверхности печей сушилок и др.) должны быть теплоизолированы с температурой на поверхности не более 45оС.
Площадки для обслуживания прессов макаронного производства и тестомесильных агрегатов непрерывного действия должны быть обеспечены удобными лестницами (в случае их установки над уровнем пола) и перилами высотой в 1м.
В тесторазделочном отделении хлебопекарных предприятий используются такие виды оборудования как тестоделительные округлительные и закаточные машины расстойные шкафы или пруфера для предварителной и окончательной расстойки тестовых заготовок.
Для мелкоштучных изделий используются розанчиковые и рожковые машины.
В бараночном производстве применяются агрегаты по прессованию и формовке бараночных изделий. Помещение тестоделительного отделения хлебозаводов должно быть просторным хорош освещенным (естественным и искусственным светом).
Особенность технологического процесса требует поддержания температуры и влажности воздуха в расстойных шкафах и пруферах по заданной величине для чего применяются кондиционеры воздуха.
В тесторазделочном отделении у рабочих мест должно быть обеспечено хорошее освещение в соответствии со СНиП-4-79 (200 лк). Все электродвигатели должны быть заземлены а ограждения движущихся частей оборудования сблокированы с электродвигателями.
Блокировка ограждения должна обеспечить отключение электродвигателя при снятии (или отсутствии) ограждения. В помещении тесторазделочного отделения должна быть приточно-вытяжная вентилция обеспечивающая кратность обмена воздуха в соответствии с условиями работы и правилами техники безопасности.
Расстояние перед фронтом тупиковых печей (ФТЛ-2 ДСД ХПК ПХС ПХК БН и др.) при расстойке теста на вагонетках должно быть не менее 5 м для удобства обслуживания.
Эксплуатация хлебопекарных печей
Устройство рабочего места у хлебопекарных печей зависит в первую очередь от типа и конструкции печей количества выделяемых тепла и влаги состояния и вида ограждающих конструкций пекарной камеры их изоляции и т.д.
Широкое внедрение механической посадки тестозаготовок на под печи и механической выгрузки применяемых на ковейерных печах значительно улучшают условия труда обслуживающего персонала так как рабочее место в этом случае отделяется от очага теплоизлучения.
Однако действующие конвейерные печи а также печи со стационарным подом где имеют место значительные выделения тепла в окружающую среду и в первую очередь теплоизлучение в зоне нахождения обслуживающего персонала требует принятия мер по оздоровлению условий труда.
Прежде всего необходимо обеспечить местное душирование путем установки вентиляторов с направлением воздуха для обдувания в месте нахождения рабочих работающих у печей.
В пекарном зале в связи со значительным выделением тепла в окружающую среду особое внимание необходим уделить работе вентиляции. В этом помещении кратность воздухообмена наиболее значительна (в пределах до 10 – 12 при температуре 18оС).
В помещении пекарного зала где производится посадка и выгрузка изделии выпекаемых в формах и на листах в дополнение к неблагоприятным температурным условиям имеет место также и загазованность от пригорания масла которым смазываются листы и формы а также шум во время выгрузки изделий.
В связи с этим необходим в каждом отдельном случае решать вопрос о смягчении ударов путем применения резиновых подкладок у места выбойки форм а также отсасывания и удаления газов из помещений пекарного зала. Все приводы печей необходимо ограждать и следить за своевременной смазкой трущихся частей с целью уменьшения шума.
Освещенность в пекарном зале должна быть не менее 75 -100 лк при использовании ламп накаливания и 150 – 200 лк при люминесцентном освещении.
В случае ремонта внутри пекарной камеры соблюдают правила техники безопасности при работе внутри емкостей обеспечивают соответствующей спецодеждой переносными лампами пониженного напряжения (12 В) и т.д.
В каждом отдельном случае в зависимости от типа эксплуатируемых печей разрабатываются инструкция по технике безопасности с учетом конструктивных особенностей этих печей – система пода и обогрева применение трубок Перкинаса сжигание газа внутри камеры электрообогрев и т.д.
При этом должно быть учтено какой вид топлива сжигается – твердое жидкое газообразное.
Так например при эксплуатации печей со стационарным подом и канальным обогревом (типа ХР) а также конвейерных печей и с канальным обогревом (ФТЛ-2) при сжигании твердых видов топлива (уголь торф и т.д.) следует уделить особое внимание маарам безопасности при чистке каналов так как могут произойти случаи ожогов. Во избежание травм от ожогов необходимо обеспечить работающих по чистке каналов рукавицами защитными очками соответствующим удобным инструментом а также переносными ламами низкого напряжения – 12В.
При сжигании твердого топлива необходимо обеспечить систематическую очистку концов трубок выступающих в топочную часть печи от налета золы соблюдая при этом меры безопасности обеспечив рабочих занятых на очистке трубок соответствующим приспособлением: не допуская ударов о выступающие концы.
При эксплуатации конвейерных печей (ХВЛ АЦХ и др.) обогреваемых трубками Перкинса могут быть случаи взрывов трубок работающих под большим избыточным давлением (10 – 20 МПа или 100 – 200 кгсм2) в связи с чем необходим систематически проверять состояние концов трубок выступающих в топочную часть и при обнаружении их перегрева принимать меры к немедленной замене.
При использовании хлебопекарных печей с электрообогревом необходим соблюдать правила по электробезопасности – заземление систематическая проверка состояния изоляции проводов и т.д.
Особое внимание следует уделить безопасным условиям труда при газовом обогреве обеспечив герметичность подводки газа во избежание выделения газа в окружающую среду как с точки зрения взрывоопасности так и в целях профилактики случаев отравления газом.
При сжигании газа в топках хлебопекарных печей необходимо следить чтобы факел правильно располагался в топочном цилиндре печи: симметрично относительно как оси цилиндра (топки) так и оси газовой горелки. Кроме того нужно следить за полнотой сгорания топлива и наличием нормального коэффициента расхода (избытка) воздуха который подается в топку печи для сгорания в ней топлива.
Проскок и отрыв пламени являются неблагоприятными явлениями. При проскоке пламени в инжекционную горелку констурции Царикова которая при работе заполнена газовоздушной смесью может произойти хлопок смеси а в некоторых случаях взрыв и разрушение горелки.
Отрыв пламени от горелки опасен тем что угасание факела и продолжающееся поступление газа в топочное пространство могут привести к загазовыванию каналов и газоходов печного агрегата и взрыву при разжигании горелки.
Поэтому во всех случаях при розжиге необходимо провентилировать каналы и газоходы а во время сжигания газа следить за приборами указывающими давление газа в сети(манометром) и состоянием горения топлива и при появлении признаков неправильного горения прекратить подачу газа.
После устранения обнаруженных недостатков можно приступить к дальнейшей эксплуатации топочных устройств.
3 Электробезопасность
использовать кабели и провода с изоляцией имеющей повреждения или утратившей в процессе эксплуатации защитные электроизоляционные свойства;
применять электропредохранители с некабеллированными плавкими вставками;
пользоваться электронагревательными приборами без огнестойких подставок а так же не оставлять их на длительное время без присмотра;
оставлять под напряжением электрические кабели и провода с неизолированными концами;
крепить электропровода гвоздями пускать их между створками дверей вешать на провода какие-либо предметы.
Техника безопасности
Перед началом работы рабочие должны надеть спецодежду халаты и др. Одежда должна быть опрятной не должно быть висячих концов – ремни пояса волосы – во избежание ее попадания в рабочие органы оборудования. Должны одеваться головные уборы – косынки беретки и др. Для этих же целей. Во избежание ранения рук применять перчатки и рукавицы. Несоблюдение установленных правил может привести к несчастным случаям.
Прежде чем начать работу рабочий должен проверить надежность закрепления заготовки на приспособлении отсутствие оголенных токоведущих кабелей заземление оборудования надежность закрепления инструмента. Для предотвращения повреждения глаз летящей стружкой необходимо использовать защитные очки устанавливать защитные щитки и экраны.
Во время работы станка нельзя оставлять на движущихся частях вспомогательные инструменты. Что может привести к несчастному случаю или выходу из строя оборудования. Во избежание порезов стружкой пользоваться специальным крючком или щеткой.
Подвесные транспортно-подъемные устройства не должны располагаться над рабочим местом. Эксплуатируемое оборудование должно быть в полной исправности. Работать на неисправном оборудовании запрещается. Оборудование должно быть установлено на фундаментах или основаниях.
Проходы между станками не должны загромождаться. Проходы и проезды на территории цехов должны быть прямолинейными а их ширина соответствовать интенсивности движения. Все передачи – ременные зубчатые цепные и др. Должны иметь специальные ограждения на высоте до 2 метров от уровня пола. Места движения людей и транспорта должны хорошо освещаться во избежание несчастных случаев.
Строгое соблюдение техники безопасности – залог безопасной и успешной работы и сохранения здоровья.
Помещение цеха относиться к категории с повышенной опасностью поражения электрическим током так как в цехе токопроводящие полы. В целях предохранения от поражения электрическим током проводятся следующие мероприятия согласно действующих правил ПУЭ: периодическая проверка знаний персонала по правилам техники безопасности один раз в год.
Панели распорядительных устройств окрашены в белый цвет и имеют четкие надписи указывающие назначение отдельных цепей для обеспечения безопасности людей от поражения электрическим током заземляющие устройство к которому подключены металлические части и корпуса электрооборудования которые вследствие нарушения изоляции могут оказаться под напряжением. Сопротивление корпуса защитного заземления не превышает 4 Ом. Оно необходимо для того чтобы снизить напряжение прикосновения до безопасной величины. В работе машины принимаем электродвигатель. Подвод электричества осуществляется через провода в заземленных трубах или рукавах.
В тестоприготовительном отделении все процессы автоматизированы движущиеся части механизма закрыты кожухом. Что приводит к низкому травматизму.
Защитное заземление представляет собой систему вертикальных электродов-заземлителей вкопанных в грунт и соединенных стальными трубами уголками полосами и другими металлическими соединителями. Заземление бывают контурным или выносным.
Заземлители располагаются по периметру цеха или площадке где размещено электрическое оборудование. При пробое изоляции корпус такой установки при защитном заземлении будет находится под малым относительно земли напряжением безопасным для жизни человека при прикосновении.
По литературе [10] cопротивление растеканию электрического тока при замыкании на землю одного электрода круглого сечения определяется по формуле:
р – удельное электрическое сопротивление грунта в который помещены электроды–заземлители Ом*м;
d – диаметр электрода м;
h – глубина заложения электрода в грунт (расстояние от верхнего конца электрода до поверхности земли) м.
Необходимое количество заземляющих электродов определяется по соотношению:
Кс – коэффициент сезонности;
Vэл – коэффициент использования электродов;
Rз – максимальное допустимое сопротивление заземляющего устройства.
При оценках принимается равным 4 Ом т.е. это наибольшее допустимое сопротивление заземляющего устройства.
Из условия безопасности организму человека протекающий через тело его ток не должен превышать 004 а это установлено медицинским экспериментами.
L = (n-1)*a+0.14 м. (80)
Если обозначить ширину полосы символом b то электрическое сопротивление ее определяется выражением:
Rпол = Sn*Ln[(2*L**2)(b*h)] Ом (5) где Sn= p(2**L). (81)
Тогда электрическое сопротивление защитного заземления состоящего из n электродов и полосы шириной b и длиной L равно
Результирующие сопротивления Rрез защитного заземления по нормативам не должно превышать 4 Ом.
Таким образом задача ставиться так: при заданных:
- грунт в котором устанавливается защитное заземление;
- температура в январе месяце;
- ширина соединительной полосы.
Подобрать такое заземление т.е. рассчитать диаметр электродов длину электрода их количество глубину закладки в грунт расстояние между электродами и длину соединительной полосы которое не превышает заданное максимальное значение 4 Ом.
Название грунта - Чернозем
Тип заземления - Выносное
Ширина соединительной полосы м 004
Температура воздуха t оС 18.00
Таблица №17. Десять лучших решений по сопротивлению
Таблица №18. Приняты обозначения
d - диаметр электрода м
l - длина электрода м
h - глубина заложения м
a – расстояние между электродами м
r - сопротивление заземления Ом
n – число закладываемых электродов шт
lb – длина соединительной полосы м
Pc – затраты на заземление.
5 Мероприятия по гигиене труда и промышленной санитарии
Освещение рабочего стола – важный фактор создания нормальных условий труда.
Хорошее освещение оказывает положительное психологическое воздействие на рабочего способствует повышению производительности труда.
В зависимости от источника световой энергии освещение делят на:
Естественное освещение какой-либо точки в помещении характеризуется коэффициентом естественной освещенности. Наименьшая расчетная освещенность при естественной освещенности определяется при наружной освещенности 5000 Лк. Для искусственного освещения применяют люминесцентные лампы с высокой световой отдачей и продолжительным сроком службы.
Применяются лампы ЛБ (белый свет) и ЛТБ (теплобелый свет) мощностью 20 40 и 80 ВТ. Лампы должны быть размещены параллельно светопроемам и равномерно по потолку.
Освещенность: комбинированная 1000 Лк общее 300 Лк для люминесцентных ламп. Общая освещенность на расстоянии от 08 м. от пола 200 Лк для вспомогательных помещений.
Искусственное освещение бывает общее и комбинированное.
Общее подразделяется на:
общее локализованное.
Искусственное освещение может быть двух видов: рабочее и аварийное.
Аварийное освещение подразделяется на освещение для продолжения работы и освещение для эвакуации людей.
Наименьшая освещенность при аварийном режиме должна составлять 5% освещенности нормируемой для рабочего освещения но не менее 2 Лк внутри зданий и не менее 1 Лк на площадках предприятий.
Вредные вещества находящиеся в производственных помещениях в воздухе через дыхательные пути пищевой тракт могут попасть в организм человека и при определенных условиях вызвать острые хронические отравления (заболевания).
При помощи вентиляции в помещениях создаются нормальные санитарно-гигиенические условия воздушной среды. Воздухообмен в помещениях осуществляется приточно-вытяжной вентиляцией.
Вентиляция может быть общеобменная когда смесь воздуха с выделяющимися вредностями доводится до допустимых пределов по всему объему помещения или местной когда вредности удаляются от мест их выделения через специальные укрытия (местные отсосы).
В помещениях с влаговыделениями устройство общеобменной механической вытяжки предусматривается в случаях когда невозможно предусмотреть естественную вытяжку. При возможных поступлениях больших количеств токсичных и взрывоопасных веществ предусматривается аварийная вытяжная вентиляция.
Вентиляция должна обеспечивать в помещении метеорологические условия в полном соответствии с требованиями санитарных норм (сн 245-71) и ГОСТ 12.1.005 – 76.
Воздушная среда рабочей зоны и производственный микроклимат.
Таблица №19. Предельно – допустимые концентрации вредных веществ в воздухе рабочей зоны (ГОСТ 12.1.005 – 88).
Агрегатное состояние
Технический процесс в тестоприготовительном отделении характеризуется выделением в среду двуокиси углерода при брожении теста. ПДК двуокиси углерода составляет 05% к объему помещения.
Необходимая кратность объема воздуха в производственном помещении с умеренным выделением двуокиси углерода равна 6.
В процессе дозирования муки в воздухе выделяется мучная пыль. Её ПДК из таблицы составляет 6 мгм3.
Для предотвращения распыла муки в конструкциях машин предусматривают уплотнение крышек месильных емкостей.
Таблица №20. Оптимальные и допустимые параметры микроклимата в рабочей зоне производственных помещений (ГОСТ 12.1.005-88)
Производственное помещение
вительное отделение
Для обеспечения условий микроклимата в тестоприготовительном отделении предусмотрено:
В холодный период года обогрев с помощью центрального водяного отопления.
Вентиляция (естественная и приточно – вытяжная ).
Система вентиляции в помещении хлебозавода в соответствии с нормами технологического проектирования ОИТП – 86.
Таблица № 21. Система вентиляции в помещении хлебозавода в соответствии с нормами технологического проектирования ОИТП – 86
Основные вредные выделения
Тепло влага двуокись углерода летучая пыль.
Механическая обменная из верхней зоны
Механическая рассредоточенная с подачей в верхнюю зону
На многих производствах чрезмерный шум в несколько раз превышающий санитарные нормы создает неблагоприятную производственную обстановку отрицательно влияет на состояние здоровья работников что ведет к снижению производительности труда.
Нормируемыми параметрами шума являются уровни в децибелах.
Основными физическими величинами характеризующими шум являются:
В соответствии с ГОСТом 121003-83 защита от шума создаваемого на рабочих местах осуществляется следующим образом.
уменьшение шума в самом источнике;
применение средств коллективной защиты;
размещение источника шума на возможно более удаленном расстоянии;
использование средств звукопоглощения при выполнении акустической обработки шумных помещений;
применение средств индивидуальной защиты (ГОСТ 12.4-051-87);
рациональная планировка помещений.
В качестве звукопоглащающих конструкций можно предложить маты из стекловаты или перфорированные плиты укрепленные на стене.
Для оценки звукопоглащающей способности ограждения введено понятие звукопоглащаемости численно равное отношению звуковой энергии прошедшей через ограждение и падающей на него.
В промышленности в связи новыми технологиями изготовления деталей ростом мощности оборудования и его быстроходности широкое применение получили машины и оборудования создающие вибрации неблагоприятно воздействующие на человека. В соответствии с ГОСТ 24346-80 вибрация может быть вызвана множеством причин: неуравновешенными силовыми воздействиями неоднородностью материала вращающегося тела несовпадением осей вращения с осью массы тела.
Основными параметрами вибраций происходящих по синусоидальному закону является амплитуда виброперемещений. Различают общую и локальные вибрации. Общая вибрация вызывает сотрясение всего организма местная вовлекает в колебательное движение отдельные части тела. В ряде случаев рабочий может подвергаться и общей и локальной вибрации одновременно.
Существует несколько способов борьбы с вибрацией:
отстройка от режимов резонанса путем рационального выбора массы или жесткости колеблющихся систем;
снижение вибрации в источнике – исключением резонансных режимов работы оборудования;
виброизоляция – дорогостоящий метод;
индивидуальные средства защиты (спец. рукавицы обувь и др.).
В нашем случае рабочий подвергается общей вибрации. По ГОСТ 12.4-024-76 следует применять спец.обувь.
Предельно допустимый уровень шума на рабочих местах в производственных помещениях обозначается ПС-80.
Источником вибрации и шума являются части дозатора а также электродвигатель машины. Общие требования безопасности уровень шума не должен превышать установленных норм. Установленная норма 80 Дб.
Для снижения уровня шума на корпус питателя дозатора наносится шумоизолирующая мастика ВД 17-58. Мука непрерывно поступает через питатель и бункер на короткий ленточный транспортер. Поэтому и наноситься шумоизолирующая мастика. Действие мастики основано на ослаблении вибрации путем перехода части колебательной энергии в тепловую при деформации покрытий.
Таблица №22. Уровень звукового давления в Дб в октавных полосах со средним геометрическими частотами в предельном спектре Сан.ПиН 2.2.12.1.8-562
Таблица №23. Гигиенические нормы общей вибрации СН 2.2.42.1.8.566-96. Среднеквадратические уровни виброскорости (мс) в октавных полосах со среднегеометрическими частотами (Гц) на постоянных рабочих местах
7 Взрывопожаробезопасность
Несмотря на широкое осуществление мер пожарной профилактики число загораний пожаров и взрывов на пищевых предприятиях остается сравнительно большим. Под пожарами понимается неконтролируемое горение вне специального очага наносящее (а под загоранием – непричинившее) материальный ущерб.
К опасным факторам пожара относятся сопровождающие его открытый огонь искры повышение температуры воздуха лучистая теплота выделение токсичных продуктов горения и дыма снижение концентрации кислорода в воздухе уменьшение видимости вследствие задымления обрушение и повреждение зданий сооружении и оборудования а также возникновение взрывов.
Для предупреждения пожаров и взрывов правильного планирования и осуществления противопожарных мероприятий на каждом предприятии необходимо контролировать все пожаро- и взрывоопасные места и работы учитывать основные причины пожаров и взрывов в производственных условиях.
Пожароопасными местами и работами являются такие на которые имеются или могут появиться горючие газы пары самовоспламеняющиеся и легковоспламеняющиеся жидкости или твердые материалы а при их наличии и появлении и соответствующих условий (высокой температуры открытого огня) может возникнуть пожар.
К взрывоопасным местам и работам относятся такие на которых в воздухе имеются или могут появиться взрывчатые газы (пары пыль) в концентрациях близких к нижнему пределу воспламеняемости и больше его.
Согласно требованиям на каждом предприятии должен быть составлен и утвержден главным инженером перечень всех пожаро- и взрывоопасных мест и работ технологического ремонтного и восстановительного характера с указанием степени их опасности. На основе этого перечня проводятся вся практическая работа по предотвращению пожаров и взрывов тушению пожаров ликвидации аварийных ситуаций и устранению последствий пожаров и взрывов. Эта работа планируется в соответствии с общими требованиями изложенными в ГОСТ 12.1.004-85 и 12.1.010-76 по пожаро- и взрывобезопасности.
Для хлебопекарных предприятий характерно большое число пожаро- и взрывоопасных мест и работ расположенных по всей технологической цепи от складов исходных продуктов и до складов готовой продукции. Это обусловлено тем что подавляющее количество исходного сырья веществ и материалов используемых в производстве полупродуктов и готовой продукции является твердыми или жидкими горючими материалами значительная часть которых может быть взрывоопасной. На бродильных производствах могут образовываться взрывоопасные концентрации паров спирта с воздухом. На многих из указанных предприятий применяются и взрывоопасные газы (аммиак ацетилен пропан и др.).
Кроме горючей среды для возникновения пожара и взрыва необходим источник или инициатор зажигания несущий достаточную энергию для ее воспламенения. Такими источниками на пищевых предприятиях являются открытый огонь технологического оборудования (топки) а также непогашенные окурки и спички; тепловые проявления электрического тока искры и дуги короткого замыкания; разряды статического и атмосферного электричества; перегрев подшипников из-за отсутствия или неправильного применения смазочного материала их неисправности износа или загрязнении; искры механического происхождения возникающие при соударении металлических частей оборудования (вентиляторы нории и т.п.) попадании металлических предметов в дробилки и другое технологическое оборудование а также при падении инструмента на металлическую поверхность оборудования или бетонный пол; небрежном обращении с растительными маслами промасленными обтирочными материалами кислородными баллонами.
Цех по производству хлебо–булочных изделий относиться к Г категории так как источником пожаробезопасности являются используемые для смазки горючесмазочные вещества мучная пыль деревянные ложки.
На предприятии ответственность за пожарную безопасность возложена на администрацию. Все цеха и участки завода имеют индивидуальные средства пожаротушения. На заводе имеется пожарная сигнализация местная телефонная связь. Вода для пожаротушения поступает из городской водопроводной сети через два ввода.
Наружное пожаротушение производится при помощи пожарных гидрантов расположенных под углом здания на расстоянии 5 метров. На внутренней водопроводной сети у входов устанавливается пожарные краны на высоте 135 м. и пожарные рукава с бронсбойтом. Расстояние между пожарным кранами такова что обеспечивает сопротивление струй воды от двух стволов в наиболее высокой и удаленной части здания.
Таблица №24. Классификация помещений по взрывоопасности
Характеристика помещений
Класс по взрывоопасности
Помещения в которых выделяется приходящие во взвешенное состояние горючие пыли или волокна в таком количестве что способны образовывать с воздухом взрывоопасные при нормальных режимах работы.
Тестомесильное отделение
Таблица № 25. Категории производств по взрывной взрывопожарной и пожарной опасности в соответствии со СНиП 21.01-97
Характеристика производства
Материалы участвующие в технологическом процессе не горючие раскаленные расплавленные.
Тестомесительное отделение
Огнетушащие вещества
Это вещества которые при введении в зону сгорания прекращают процесс горения.
Основными современными огнетушащими веществами применяемыми в практике пожаротушения являются: вода песок пены поверхностно-активные вещества порошки углекислота инертные газы и др. на основе этих веществ разработаны огнетушители типа: ОП ОХП и др.
Особое внимание стоит уделять мероприятиям режимного характера: курению в неустановленных местах производство сварочных работ.
Меры пожарной безопасности:
наличие необходимого количества выходов;
наличие в цеху ящиков с песком;
пожарная сигнализация.
8 Промышленная экология
Предприятия удалено от жилых массивов строится с учетом рельефа местности и "розы ветров". Соблюдается санитарная зона (50 м.). Участки территории между здания свободны от использования в производственных целях а также санитарно–защитная зона отделена. Территория поддерживается в чистоте.
Для очистки воздуха от пыли в приточных вентиляционных камерах установлены фильтры. Для нашего помещения предусмотрены инерционные фильтры и установлены циклоны. Смесь происходит последовательную и тщательную фильтрацию. Очищается и поступает в окружающую среду.
Так как источником среды загрязнения окружающей среды является технологическая вода. Предусмотрен спуск технической воды в горячую канализацию с последующей очисткой.
Темой дипломного проекта является ленточный дозатор муки установленный в тестоприготовительном отделении тестоприготовительного агрегата. В котором из – за недостаточной подачи муки и для уменьшения потерь муки на 02 % модернизируем за счет точности дозирования.
Учитывая недостаточную эффективность устройства для разрушения сводов муки мною в конструкции дозатора сыпучих компонентов были разработаны ленточные побудители которые разрыхляют муку перед дозированием.
Для исключения переполнения бункера и ликвидации больших колебаний уровня муки влияющих на точность дозировки на корпус питателя мною были установлены специальные блокировки управляющие работой питающих устройств.
Для повышения надежности узла регулировки производительности дозатора мною была переработана конструкция крепления заслонки.
Для удобства контроля расхода на переднюю панель дозатора вынесен специальный щит показывающий фактический расход компонента.
При капитальных затратах на модернизацию дозатора смета составляет 30000 руб. что дает экономический эффект на сумму 1443 тыс.руб. со сроком окупаемости 02 года и позволяет внедрить проектируемый дозатор на производстве.
Список использованной литературы
Ауэрман А.А "Технология хлебопекарного производства". Пищевая промышленность М.1984г.
Гатилин Н.Ф."Проектирование хлебозаводов". Пищепромиздат.М.1979г.
Головань Ю.А. Ильинский И.А. "Технологическое оборудование хлебопекарных предприятий". Пищевая промышленность .М.1971г.
Дукаев Л.Ф. Ликов О.П. "Детали машин. Курсовое проектирование". Высшая школа. М. 1967г.
Зайцев Н.В. "Технологическое оборудование хлебозаводов". Пищевая промышленность. М. 1967г.
Иванов М.Н. "Детали машин". Высшая школа. М. 1991г.
Калинина В.И. "Разработка и расчет инженерных решений по охране труда и окружающей среды в дипломных проектах студентов механических специальностей пищевых и зерноперерабатывающей промышленности". Учебное пособие" М. МГЗИПП.1997г.
Лукин О.Г. Вельтищев В.Н. Калаче М.В. Калошин Ю.А. "Курсовое и дипломное проектирование технологического оборудования пищевых производств". М. Агропромиздат 1990г.
Мачихин С.А. "Технологическое оборудование хлебопекарных и макаронных предприятий" М. Агропромиздат 1986г.
Теплов А.Ф. "Охрана труда в отрасли хлебопродуктов" Агропромиздат 1990г.
Хромеенков В.М. "Оборудование хлебопекарного производства" М. 2000г.
Шейнблинг А.Е. "Курсовое проектирование деталей машин" М. Высшая школа 1991г.
Чернилевский Д.В. "Детали машин. Проектирование приводов технологического оборудования" М. Машиностроение. 2000г.
Чернов М.Е. Хромеенков В.М. Калошин Ю.А. Либиян А.А. "Практикум по расчетам оборудования хлебопекарного и макаронного проиводств". М. Агропромиздат. 1991г.
8_3_1_Бортик.dwg

8_3_2_Заслонка.dwg

3_Общий вид загрузочного бункера.dwg

МАПП - ПДП 11.03.000
Сварные швы по ГОСТ 14771-76
Неуказанные сварные швы сплошные по
контуру прилегания деталей.
* Размеры для справок
**Выполнить плавный переход к основному
8_4_1_Стяжка.dwg

Длина развертки - 583
*Размеры для справок
2_Общий вид ленточного дозатора муки.dwg

датчик проскальзывания ленты
датчик скорости ленты
Аннотация.docx
Дозатор стал более совершенен взвешивание материала и регулирование скорости транспортёрной ленты происходит без механического вмешательства автоматически что значительно позволяет облегчить труд технологического персонала и повысить качество сырья подаваемого в тестоприготовительное отделение. Кроме того он наиболее надежный в работе имеет небольшие габаритные размеры и простату конструкции.
Приведем ключевые слова:
- экономический эффект;
6_Барабан приводной.dwg

Сварные швы по ГОСТ 14771-76
*Размеры для справок
8_1_Ролик.dwg

При сборке ролика подшипник смазывать (набивать) смазкой
ЦИАТИМ -201 ГОСТ 6267-74
7_Барабан натяжной.dwg

Сварные швы по ГОСТ 14771-76
*Размеры для справок
Спецификация.dwg

ленточного дозатора муки
МАПП - ПДП 11.01.000 СБ
МАПП - ПДП 11.08.001
МАПП - ПДП 11.04.000
МАПП - ПДП 11.06.000
МАПП - ПДП 11.08.003
МАПП - ПДП 11.03.000
МАПП - ПДП 11.08.004
МАПП - ПДП 11.07.000
МАПП - ПДП 11.08.005
МАПП - ПДП 11.08.006
МАПП - ПДП 11.08.002
Заклепка 6х16 ГОСТ 10300-80
Кольцо СТ-74-57-6 ГОСТ 288-72
Подшипник 1210 ГОСТ 5720-75
Лента 2Л-800 3-ТК-200-2-5-3
5_Общий вид привода.dwg

барабана дозатора не более:
МАПП - ПДП 11.05.000
Технические требования:
Техническая характеристика:
Мощность электродвигателя 4 кВт
Частота вращения вала электродвигателя 124 обмин
Задание.docx
Обзор существующих конструкций
3 Барабанный дозатор
4 Тарельчатый дозатор
5 Вибрационный дозатор
Технико–экономическое обоснование
1 Техническое обоснование
2 Экономическое обоснование
Описание разрабатываемой машины
1 Назначение ленточного дозатора
2 Устройство ленточного дозатора
3 Техническая характеристика ленточного дозатора
1 Расчет потребной мощности ленточного дозатора
2 Кинематический расчет
3 Расчет муки по рецептуре
4 Недельный расчет расхода муки
Расчет на прочность с применением ЭВМ
1 Расчет открытой прямозубой передачи (из привода делительной головки)
2 Расчет открытой конической передачи
3 Расчет цепной передачи
4 Расчет второй цепной передачи
1 Анализ опасных факторов
2 Электробезопасность
4 Взрывопожаробезопасность
5 Промышленная экология
Экономический расчет
1 Данные для расчёта
2 Расчёт экономической эффективности
3 Расчет срока окупаемости
Задание на дипломный проект
A1 лист – Ленточный дозатор муки (сборочный чертеж);
А1 лист – Барабан натяжной;
А1 лист – Барабан приводной;
А1 лист – Бункер (горловина);
А1 лист – Деталировка;
А1 лист – Экономическая часть;
А1 лист – Безопасность жизнедеятельности;
А1 лист – Технологический лист;
А1 лист – Электрическая схема.
Экономика.docx
1. Техническое обоснование
Растущий спрос на хлебобулочные изделия и в частности на мелкоштучные требует увеличение выпуска этой продукции и улучшение выпуска этой продукции и улучшения ее качества.
Оборудование для дозировки муки – ленточный дозатор муки – важнейшая часть паточной линии. Дозатор сыпучих компонентов служит для отмеривания определенных порций муки в соответствии с рецептурой.
Дозировка муки как основного сырья одна из важнейших операций технологического процесса приготовления теста. От точности дозирования муки зависит соблюдение установленной рецептуры а следовательно и качество изделий. Поэтому основным требованием к дозаторам муки является точность дозирования.
Производительность ленточного дозатора П = 20тсутки.
Масса дозатора – 240кг.
Точность дозирования – 15%.
На участке поточной линии где используется ленточный дозатор муки производятся следующие операции: загрузка муки в бункер дозатора выгрузка в определенных дозах (дозировка) муки из бункера дозатора на ленточный конвейер.
Проектируемый вариант
По способу выполнения
Для выгрузки муки из бункера дозатора на ленточный конвейер используется следующие типы дозаторов. Дозаторы непрерывного действия – барабанные тарельчатые шнековые ленточные вибрационные и дозатор периодического действия – бункерный. Из перечисленных дозаторов свой выбор останавливаем на бункерном так как это наиболее распространенный дозатор на пищевых предприятиях. Имеет небольшие размеры простоту конструкции надежность работы. Кроме этого изготовление монтаж дозатора можно осуществить своими силами непосредственно на предприятии. Тем самым поощряя у работников предприятия рационализаторские внедрения.
2. Экономическое обоснование
Капитальные затраты на установку и монтаж ленточного дозатора составляет 30 тыс.руб. которые по предполагаемым расчетам окупятся за короткий срок и позволяет снизить себестоимость готовой продукции на несколько пунктов.
3. Экономический расчет
Таблица № Данные для расчёта
Производительность дозатора:
до модернизации кгсут
после модернизации кгсут
Цена оборудования тыс.руб.
Норма амортизационных отчислений на оборудование %
Норма расхода на содержание и текущий ремонт оборудования %
Стоимость 1т. муки тыс.руб.
В расчете принимаем что расход электроэнергии не изменяется.
Определяем годовую выработку хлеба:
где qг – среднегодовое потребление муки на душу населения равно 012 тоннгод;
Nчис – численность населенного пункта чел.
Определяем количество хлеба:
где Пгв – годовая выработка хлеба тгод;
Км = *100%=1096875 (тгод).
Экономия по муке составит:
где коэффициент 02 - уменьшение потери сырья %.
Определяем экономию средств в результате модернизации:
где Цм - цена 1т. муки;
C2 = 2194(тгод)*7= 1536 (тыс.руб.год).
Изменение затрат на амортизацию оборудования:
где И – цена на модернизацию тыс. руб.;
Ао – норма амортизационных отчислений на оборудование 15%.
Изменение затрат на содержание и текущий ремонт оборудования:
где Но – норма расхода на содержание и текущий ремонт оборудования.
Гэ = С2 – Изо – Иро (8.6)
Гэ = 1536 – 45 – 18 = 1473 тыс.рубгод.
Расчет срока окупаемости:
Срок окупаемости оборудования:
где И – инвестиции тыс.руб;
Гэ – годовая экономия тыс.руб.
Таблица Показатели эффективности
Величина показателей
Выроботка продукции тгод
Годовая экономия тыс.руб.
Срок окупаемости оборудования год
Экономика.dwg

Срок окупаемости оборудования
ехнико-экономические покзатели базового и модернизированного
ленточного дозатора муки
Технико-экономические
МАПП - ПДП 11.10.000 ТБ
Рекомендуемые чертежи
- 09.07.2014