Бетоносмесительный завод, с расчетом шнека питателя дозатора цемента


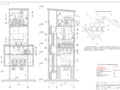
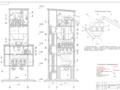
- Добавлен: 25.10.2022
- Размер: 4 MB
- Закачек: 3
Описание
Состав проекта
![]() |
![]() |
![]() ![]() ![]() ![]() |
![]() ![]() ![]() ![]() |
![]() |
![]() ![]() ![]() |
![]() |
![]() ![]() ![]() |
![]() |
![]() |
![]() |
![]() |
![]() ![]() ![]() |
Дополнительная информация
КП лист 1_.dwg

Канат (по ГОСТ 7667-69)
Тормозной момент в Н*м
Частота вращения обмин
Передвижения тележки
Продолжительность включения
Высота подъёма груза в м
Грузоподъёмность в т
Техническая характеристика
- ленточные конвейеры; 2 - распределительное устройство; 3 - расход- ные бункера песка
щебня и цемента; 4 - дозаторы сухих составляющих; 5 - дозатор воды; 6 - загрузочное устройство; 7 - растворосмесители
Тип установки Эксплуатационная производительность
м ч Режим работы Число ратворосмесителей
м технологического оборудования
- высотная - 45 - циклический - - 87 - 25
Технологическая схема
щебня и цемента; 4 - дозаторы сухих составляющих; 5 - дозатор воды; 6 - загрузочное устройство; 7 - растворосмеситель; 8 - шнековый питатель дозатор цемента
КП лист 1.dwg

Канат (по ГОСТ 7667-69)
Тормозной момент в Н*м
Частота вращения обмин
Передвижения тележки
Продолжительность включения
Высота подъёма груза в м
Грузоподъёмность в т
Техническая характеристика
- ленточные конвейеры; 2 - распределительное устройство; 3 - расход- ные бункера песка
щебня и цемента; 4 - дозаторы сухих составляющих; 5 - дозатор воды; 6 - загрузочное устройство; 7 - растворосмесители
Тип установки Эксплуатационная производительность
м ч Режим работы Число ратворосмесителей
м технологического оборудования
- высотная - 45 - циклический - - 87 - 25
Технологическая схема
щебня и цемента; 4 - дозаторы сухих составляющих; 5 - дозатор воды; 6 - загрузочное устройство; 7 - растворосмеситель; 8 - шнековый питатель дозатор цемента
Приложение 1.docx
КП СМИО 270113.00.000 ПЗ
Расчетно-пояснительная записка
КП СМИО 270113.01.000 ВО
Бункер накопительный
КП СМИО 270113.02.000 ВО
КП СМИО 270113.03.000 ВО
КП СМИО 270113.04.000 ВО
КП СМИО 270113.05.000 ВО
КП СМИО 270113.06.000 ВО
Шнековый питатель дозатор
КП СМИО 270113.07.000 ВО
КП СМИО 270113.08.000 ВО
КП СМИО 270113.09.000 ВО
КП СМИО 270113.10.000 ВО
КП СМИО 270113.11.000 ВО
КП СМИО 270113.12.000 ВО
КП СМИО 270113.13.000 ВО
КП СМИО 270113.14.000 ВО
КП СМИО 270113.06.000 СБ
КП СМИО 270113.06.010
КП СМИО 270113.06.012
КП СМИО 270113.06.002
КП СМИО 270113.06.001
КП СМИО 270113.06.003
КП СМИО 270113.06.004
КП СМИО 270113.06.005
КП СМИО 270113.06.006
КП СМИО 270113.06.007
КП СМИО 270113.06.008
КП СМИО 270113.06.009
КП СМИО 270113.06.013
КП СМИО 270113.02.001
Электродвигатель 4АМ71В6У3
КП СМИО 270113.02.013
Подшипник 215 ГОСТ 8338-75
КП СМИО 270113.02.014
Подшипник 110 ГОСТ 8338-75
КП СМИО 270113.02.015
КП СМИО 270113.02.016
КП СМИО 270113.02.019
Болт М24 ГОСТ 7808-70
КП СМИО 270113.02.020
Гайка 24 ГОСТ 2524-70
КП СМИО 270113.02.021
Шайба 24 ГОСТ 6402-70
КП СМИО 270113.02.022
Болт М20 ГОСТ 7808-70
КП СМИО 270113.02.023
Гайка 20 ГОСТ 2524-70
КП СМИО 270113.02.024
Шайба 20 ГОСТ 6402-70
КП лист 2-5.dwg
Частота вращения вала
Крутящий момент на валу
230 250 HB 2. Формовочные уклоны =1° 3. Неуказанные радиусы 2мм max 4. Неуказанные предельные отклонения размеров: охватываемых- h14
Технические требования 1. Электродвигатель крепить болтами М12х60 ГОСТ 7805-75 2. Редуктор крепить болтами М16-80 ГОСТ 7805-75 3. Сварка электродуговая ручная
Формовочные уклоны ~1*. 2. Неуказанные радиусы 2 мм мах. 3. Неуказанные предельные отклонения размеров поверхностей V: отверстий +t2
остальных +t22 поверхностей V:+t32 по ГОСТ 25670-83.
Т.т. на изготовление - по ГОСТ 21424-93. 2. Нерабочие поверхности полумуфты обезжирить
грунтовать слоем ЭПО-99 и покрасить эмалью ХВ-785 в два слоя.
Неуказанные предельные отклонения размеров: Н7
±IT142. 4. Острые кромки притупить R=0
ПЗ СМиО.doc
Технологическая часть
1.Технология приготовления бетонных и растворных смесей
Технология процессов на бетонорастворных заводах. Производство бетонных и растворных смесей на современных заводах состоит из ряда транспортно-складских и технологических процессов в том числе:
- транспортно-складских операций с составляющими материалами которые включают в себя разгрузку переработку и хранение сырьевых компонентов и топлива;
- тепловых операций – подогрева зимой воды и заполнителей на складах и в бункерах подогрева (расходных бункерах);
- технологических операций приготовления в их числе: дозирование цемента воды заполнителей добавок и загрузки ими смесителей; перемешивание составляющих материалов в соответствии с заданной длительностью во времени; выгрузка готовой смеси в накопительный бункер; погрузки готовой смеси на транспортные средства;
- вспомогательных операций в том числе: учет расходования сырьевых компонентов и объема производства смеси; обеспечение производственных процессов электроэнергией сжатым воздухом холодной и горячей водой; приготовление хранение и транспортирование добавок; гидрообеспыливание аспирация и вентиляция; выдача заполнителей и цемента другим потребителям.
Технология перемешивания смеси. Из перечисленных выше процессов центральное место занимает перемешивание составляющих материалов. Приготовление бетонной смеси согласно СНиП должно производиться с соблюдением следующих требований:
- продолжительность перемешивания как правило должна определяться строительной лабораторией опытным путем для применяемых материалов и составной бетонной смеси;
- при отсутствии данных опытной проверки наименьшая продолжительность перемешивания в смесителях цикличного действия ( считая с момента окончания загрузки всех материалов до начала выгрузки смеси из него) должна приниматься по Таблице 1.
Таблица 1- Наименьшая продолжительность смешивания бетонной смеси на плотных заполнителях с
Объем готового замеса бетонной смеси л
В гравитационных смесителях при подвижности бетонной смеси см
В смесителях принудительного действия
Проверять подвижность бетонной смеси и раствора у места их приготовления следует не реже двух раз в смену в условиях установившейся погоды и влажности заполнителей.
Строительные растворы в свежеприготовленном состоянии должны обладать подвижностью и водоудерживающей способностью обеспечивающих возможность получения ровного и плотного шва в кладке и при монтаже крупноблочных стен.
При перемешивании смеси требуется обеспечить сплошное обволакивание цементным тестом поверхности частиц заполнителя и равномерное распределение этих частиц в массе раствора. Для получения однородной смеси необходимо чтобы частицы составляющие смесь материалов при перемешивании совершали многократные перемешивания по сложным и пересекающимся между собой траекториям.
В зависимости от крупности зерен содержания воды и вяжущего материала требуются различные усилия для качественного перемешивания смеси. Смеси из крупных зерен перемешиваются легче чем мелкозернистые поскольку последние при увлажнении образуют трудно перемешиваемые комки.
Процесс перемешивания неразрывно связан с явлением адсорбции вяжущего в частицы заполнителя. При этом от глубины адсорбции во многом зависит качество бетонной смеси и соответственно бетонной конструкции. Установлено что при условии непрерывной смены адсорбированной пленки на поверхности частиц заполнителя происходит наиболее глубокая адсорбция вяжущего в заполнитель. Создать эти условия можно только при наличии турбулентного движения смеси при перемешивании.
С этой точки зрения наиболее прогрессивными являются принудительное перемешивание виброперемешивание и струйная технология приготовления смеси когда смена пленки и превращение золя цемента в гель происходит одновременно с явлением тиксотропии (разжижение) обеспечивающим равномерное размещение всех компонентов в смеси. Выбор способа перемешивания зависит от требований предъявляемых к режиму перемешивания и вида смеси. Различают следующие виды перемешивания:
Перемешивание со свободным падением материалов осуществляется во вращающихся смесительных барабанах на внутренних поверхностях которых по винтовой линии укреплены лопасти. При вращении смесителя лопасти захватывают порции смеси и поднимают их до верхнего крайнего положения откуда сбрасывают вниз.
Перемешивание с принудительным смешиванием материалов может осуществляться тремя способами: с помощью вращающихся лопастей при воздействии на смесь вибрационных импульсов и струйным перемешиванием.
Вращающиеся лопасти лопатки или кулачки насаженные на приводные горизонтальные или вертикальные валы перемешивают компоненты бетонной смеси по более сложным траекториям а также способствуют непрерывной смене адсорбированной пленки вяжущего материала на частицах заполнителя что в свою очередь повышает однородность смеси и прочность бетонных конструкций и позволяет экономить цемент. К преимуществам этого способа следует отнести также возможность приготовления смесей любой подвижности и жесткости меньшую продолжительность смешивания и следовательно большую производительность смесителей. К числу недостатков способа относится: высокая энергоемкость недолговечность рабочих органов и как следствие высокая стоимость приготовления смеси ограничения по крупности применяемого заполнителя.
Виброперемешивание происходит в результате воздействия на смесь вибрационных импульсов определенной силы и частоты. В процессе вибрации силы трения и сцепления между частицами бетонной смеси нарушаются а сила тяжести частиц уравновешивается давлением возбуждения в смеси вследствие чего смесь приобретает подвижность и переходит во взвешенное состояние. При этом усиливается явление тиксотропии способствующее равномерному распределению всех компонентов в смеси.
Струйное перемешивание смеси отличается тем что составляющие материалы перемешиваются встречными закрученными струями сжатого воздуха вытекающими из сопел с большими скоростями. По сравнению с другими способами в процессе струйного перемешивания создаются наиболее благоприятные условия для глубокого взаимопроникновения образующих смесь материалов и максимального проявления заложенного в них химической активности [6].
2.Описание и технологическая схема работы бетоносмесительного завода
На стационарных заводах приготовляют бетонную смесь в течение всего года. Технологическое оборудование монтируют по вертикальной схеме т. е. с однократным подъемом исходных сырьевых материалов.
Стационарный бетоносмесительный завод состоит по высоте из пяти отделений: надбункерного бункерного дозаторного смесительного и отделения выдачи готовой смеси.
Заполнители по наклонной галерее ленточным конвейером подаются в поворотную воронку с пневмоприводом которая в зависимости от вида заполнителей направляет их в соответствующий бункер. Из бункеров заполнители по переходным патрубкам поступают в дозаторы откуда по течкам поступают в приемную воронку с перекидным клапаном а оттуда по течке в бетоносмеситель. Цемент из силосов пневмотическим транспортом подается наверх в циклон и фильтры. Образовавшаяся при этом цементная пыль возвращается в расходные бункера. Далее цемент винтовым реверсивным конвейером распределятся по отсекам бункеров из которых по переходным патрубкам подается в дозатор а оттуда по двухрукавной течке – в бетоносмеситель.
Рисунок 1.1 - Технологическая схема БСЗ
- ленточные конвейеры; 2 - распределительное устройство; 3 - расход-
ные бункера песка щебня и цемента; 4 - дозаторы сухих составляющих; 5 - дозатор воды; 6 - загрузочное устройство; 7 - растворосмеситель; 8 - шнековый питатель-дозатор цемента
Для предупреждения образования сводов в бункере песка устанавливаеся сводообрушитель вибрационного типа а в бункере цемента – сводообрушитель аэрационного типа. Готовая бетонная смесь выгружается в бункера выдачи а оттуда поступает в транспортные средства. При использовании гравитационных смесителей эти бункера располагаются по краям смесительного отделения.
Всеми механизмами односекционного завода управляют с двух пультов: надбункерного где расположен пульт управления механизмами данного отделения; дозировочного и смесительного отделений. [6]
Расчет и подбор потребного количества технологического оборудования
1.Расчет потребного количества исходного сырья для приготовления бетонов
Согласно методике предложенной в (4) произведем следующие расчеты.
Необходимо спроектировать бетонный узел по выпуску твердого бетона составом Ц:П:Щ=1:3:5 при ВЦ=055 и производительности Пэ.ч.=45 м3ч.
В соответствии с заданным соотношением можно определить расход составляющих компонентов на 1м3 бетона.
где y- объемный вес цемента кгм3 ; Кв- коэффициент выхода бетонной смеси Кв=05 07.
Расход песка на 1м3 бетона:
Расход щебня на 1 м3 бетона:
При известной производительности Пэ.ч=45м3ч можно рассчитать часовой расход материалов:
Произведем расчет ёмкостей расходных бункеров с учетом 2 3 часовых норм запасов.
2.Расчет потребного количества смесительных машин
где Vо – потребный объем смесителей по загрузке л; Пэ.ч – заданная часовая производительностьм3ч; z – число замесов а час; Кв – коэффициент выхода; Кэ=075 085 – коэффициент работы машины по времени.
Число замесов в час определяется как
где tц – время цикла с; tз=15 18 с – время загрузки смесителя; tв=10 15 с – время выгрузки смеси; tп – время смешения tп=40 90 с – для растворосмесителей и tп=90 180 для бетоносмесителей.
Используя технические данные по объему загрузки современных бетоносмесителей можно определить их число. Для смесителя с q=4500 л число смесительных машин будет равняться:
где q – объем смесителя л
Таким образом для обеспечения заданной производительности необходимы два бетоносмесителя марки БП-2Г-4500 принудительного действия.
Рисунок 2.1 - Бетоносмеситель БП-2Г-4500
– неподвижный сварной корпус 2 – два горизонтально расположенных вала 3 – лопатки 4 – скребковые лопасти 5 – электродвигатель 6 – защитных кожух 7 – затвор с ручным приводом 8 – ковш 9 – механизм подъёма 10 – электродвигатель 11 – шаровой кран 12 – водомер 13 – шкаф управления 14 – пылеуловитель 15 – смотровой люк 16 – червячный редуктор
Состав двухвального бетоносмесителя БП-2Г-4500 Двухвальный бетоносмеситель состоит из неподвижного сварного корпуса внутри которого размещен смешивающий механизм состоящий из двух горизонтально расположенных валов закреплённых на них лопатками и скребковыми лопастями. Валы соединены между собой двумя синхронизирующими шестернями. Привод осуществляется от электродвигателя через ременную передачу оснащенную кожухом и двухступенчатую зубчатую передачу заключённую в сварном корпусе объединённом с корпусом смесителя.
Рисунок 2.2 - Бетоносмеситель БП-2Г-4500
Таблица 2.1 - Техническая характеристика смесителя с горизонтальными смесительными валами принудительного действия марки БП-2Г-4500
Производительность м3ч
Число пар лопастей на каждом валу шт
Частота вращения лопастных валов с-1
Наибольшая крупность заполнителей мм
Мощность электродвигателей кВт
Габаритные размеры мм
Выбираем ближайший электродвигатель марки 4А200L8У3 мощностью 55кВт
Рисунок 2.3 - Электродвигатель марки 4А200L8У3
Таблица 2.2 - Техническая характеристика электродвигателя марки 4А200L8У3
Мощность на валу кВт
Частота вращения вала мин-1
3.Предварительный выбор дозатора цемента
По часовому расходу цемента (11 м3ч) подбираем шнековый питатель-дозатор цемента СПШ-2000
Рисунок 2.4 – Принципиальная схема шнекового питателя дозатора
– двигатель; 2 – муфта; 3 – редуктор; 4 – подшипник упорный головной; 5 – вал с винтом; 6 – опора промежуточная; 7 – загрузочный патрубок; 8 – задний подшипник; 9 – разгрузочное устройство
Таблица 2.3 - Технические характеристики
Производительность м3в час
Диаметр рабочего органа мм
Рисунок 2.5 – Шнековый питатель дозатор цемента СПШ-2000
4.Выбор дозатора заполнителей
По часовому расходу песка (36 тч) подбираем весовые дозаторы заполнителя. Весовой дозатор циклического действия ВДЭ-2400. Предназначен для последовательного взвешивания песка подаваемого в бункер дозатора электровибрационными питателями. Сигнал на опорожнение весового бункера и отключение питателя подается датчиком тонкого взвешивания. При дозировании компонентов в один этап датчики устанавливают в положение соответствующее требуемой дозе песка. После опорожнения бункера воды система автоматически подготовлена к очередному дозированию.
Рисунок 2.6 - Дозатор ВДЭ-2400
- указатель; 2 - рама; 37- рычаги; 4 17 - тяги; 513- серьги; 6 18 - стойки; 8 - груз; 9 - корпус; 10 - упор; 11 - винт; 12 - штырь; 14 - гаситель колебаний; 15 -платформа; 16-гайка.
Таблица 2.4 - Технические характеристики дозатора ВДЭ-2400
Наименование параметра
Допускаемая погрешность
Число заранее задаваемых составов
5.Выбор и расчет ленточного конвейера для щебня
Рисунок 2.7 - Расчетная схема конвейера
Согласно методике предложенной в [5] произведем следующие расчеты.
Ширина ленты конвейера:
где Пк=55 - производительность конвейера тч; С=09 - коэффициент снижения производительности в зависимости от угла наклона (при =200); V=10-скорость движения ленты при транспортировке щебня мс; ρ=17- плотность щебня тм3.
Ширина ленты должна быть проверена по крупности транспортируемого материала:
где dmax=004- максимальная крупность заполнителя (щебня) м
Принимаем ближайшее стандартное значение ширины ленты конвейера равное В0=04 м.
Необходимая мощность привода конвейера:
где W – необходимое тяговое усилие на приводном барабане конвейера Н;
=075 08 – КПД привода барабана.
Тяговое усилие на барабане конвейера:
W=1264.59-493.98=770.61 H
Мощность электродвигателя:
где k3=11 115 – коэффициент запаса.
Принимаем ближайший серийный электродвигатель марки МТК-012-6 с мощностью Nдв=60 кВт частотой вращения вала 870 мин-1 и массой m=53 кг.
Выбираем конвейер для щебня марки ЛК-500
Рисунок 2.8 - Конвейеры ленточные (ленточный транспортер) с желобчатыми роликоопорами ЛК-500
Состоит из следующих элементов: рамы-носителя (1) конвейерной ленты (2) грузовых (3) и возвратных (4) роликоопор направляющих роликов (5) возвратного (6) и приводного (7) барабанов подшипниковых опор (8) мотор-редуктора (9) устройства натяжения конвейерной ленты (10).
Таблица 2.5 - Основные конструктивные и рабочие параметры конвейера для щебня марки ЛК-500
Расчетная ширина ленты м
Стандартная ширина м
Размеры барабанов мм
- диаметр приводного барабана
- диаметр натяжного барабана
Электродвигатель МТК-012-6:
- частота оборотов мин-1
Редуктор марки Ц2-200:
- передаточное число
- мощность на ведущем валу
- частота оборотов ведущего вала мин-1
Конструктивный расчет шнекового питателя-дозатора цемента
Шнековые дозаторы применяются для подачи на переработку сыпучих материалов (порошкообразных или зернистых) в виде потоков с заданным расходом (при непрерывном способе производства) и определенных парциальных потоков (при периодическом способе). В противоположность весовому дозированию осуществляемому с помощью весов используется объемное дозирование при котором материал или соответствующий удельный (в единицу времени) поток не взвешивается а дозируется «косвенным» методом т. е. измерением объема соответствующего определенной массе.
Одношнековый дозатор представляет собой простейшую форму исполнения этого типа машин. Дозируемый материал забирается шнеком из воронки транспортируется и выводится в виде равномерного материального потока. Шнеки и корпуса шнеков изготавливают обычно сварной конструкции из листовой стали. С целью точной центровки шнек с обоих концов вала устанавливается как правило в радиально-упорные конические роликовые подшипники. Для удобства монтажа шнеков имеющих различный шаг и глубину нарезки и тщательной очистки при перемене типа или цвета материала современные конструкции выполняются таким образом что шнек можно легко извлекать из корпуса со стороны узла выгрузки отвернув несколько болтов. Привод должен обеспечивать плавное (бесступенчатое) регулирование частоты вращения вала шнека.
Рисунок 3.1 - Принципиальная схема шнекового питателя-дозатора
2.Расчет основных параметров винтового конвейера
Производительность шнека рассчитывается по формуле:
где D – диаметр винта м;
п – частота вращения винта обмин;
ρ – плотность транспортируемого материала тм3;
С – поправочный коэффициент зависящий от угла наклона конвейера
при = 0º принимаем С = 1;
– коэффициент наполнения поперечного сечения винта для
абразивных материалов = 0125 [1 стр. 57].
В нормальных условиях работы рекомендуется шаг винта t принимать равным диаметру винта D [1 стр. 55]. Плотность цемента выбираем таблицы 24 [3 стр. 300] ρ = 1400 кгм3. Рекомендуемое число оборотов винта выбираем по ГОСТ 2037-65 п = 50 обмин.
Из формулы (1) получим формулу для расчета диаметра винта:
Полученное значение округляем до ближайшего стандартного D = 320 мм.
Рисунок 3.2 - Эскиз сплошного винта
3.Определение мощности на валу винта
Мощность на валу винта определяют по формуле [1 стр. 59]:
где LГ – горизонтальная проекция длины конвейера м;
W – опытный коэффициент сопротивления при движении груза по желобу [1 стр. 59 табл. 7] W = 4;
k – коэффициент учитывающий характер перемещения винта k = 02;
qК – погонная масса вращающихся частей конвейера кгм;
u – осевая скорость движения груза мс;
wВ – коэффициент сопротивления движению вращающихся частей конвейера при подшипниках качения wВ = 008. [1]
4.Определение максимальной частоты вращения вала
Максимальную частоту вращения винта можно определить по формуле:
где К– расчетный коэффициент для абразивного материала
К = 30 [5 табл. 13.3 стр.221]
Номинальную частоту вращения винта при заданной производительности и выбранном диаметре винта определяем по формуле:
5.Определение мощности и выбор электродвигателя
Мощность двигателя определяется с учетом КПД механизма:
где h – механический КПД привода [8 табл. 5.1.];
где hм – кпд муфт hм.=098;
hред – кпд двухступенчатого редуктора hред.= 096.
По ГОСТ 19523-81 выбираем асинхронный электродвигатель типа: 4АМ71В6У3 с номинальной мощностью 055 кВт и асинхронной частотой вращения nдв.ном.= 1000 мин-1.
Рисунок 3.3 - Кинематическая схема привода винтового конвейера
6.Кинематический расчет привода
Определим общее передаточное число привода по формуле:
Принимаем Uобщ.= 198. По табл.7 [5 стр. 318] выбираем цилиндрический двухступенчатый редуктор типа ГОСТ 20373-94: Ц2У-250 и передаточным отношением Uобщ.= 198; Мощность по быстроходному валу Nв.быст=14 кВт (при среднем режиме эксплуатации); КПД =097 .
Определим фактическую частоту вращения винта.
Определим фактическую производительность винтового конвейера по формуле (1).
т.е. отличается в допустимых пределах.
7.Определение силовых параметров на валу винта
Момент на валу винта определяем по формуле:
где h – механический КПД привода.
Определим наибольшую действующую продольную силу:
где j – угол трения материала о поверхность винта;
a – угол подъема винтовой линии;
k – коэффициент учитывающий радиус действия силы (k=07 08).
Угол трения материала о поверхность винта:
где f1 – коэффициент трения частиц груза о поверхность винта для цемента
выбираем по таблице 24 [5 табл. 4.1 стр. 105] f1 = 08.
Определим массу груза передвигающегося по конвейеру:
где u – скорость груза мс.
Определим силу действующую на один виток:
где q' – вес передвигающийся по конвейеру Нм.
Поперечная нагрузка на участок винта между опорами:
где l=2 м – расстояние между опорами винт.
Поперечная сила приложена к винту на расстоянии среднего радиуса винта.
Расчет вала винта на прочность
1.Предварительный расчет вала
Вал изготавливают полым. Его внешний диаметр равен:
Внутренний диаметр вала найдем из соотношения:
где с – коэффициент отношения внутреннего диаметра вала к внешнему
Преобразуя формулу получим:
Определим число промежуточных опор:
где L – длина конвейера м;
l – длина секций между опорами принимаем конструктивно l = 1 м.
то есть промежуточных опор нет
2. Рассмотрим секцию вала
Вал винта рассчитывается на сложное сопротивление от эксцентрично приложенной на радиусе r осевой силы Рос и Рпопер.
Рисунок 4.1 - Расчетная схема вала винта Эпюры изгибающего и крутящего моментов
Определим реакции RA и RB:
Построение эпюры изгибающих моментов:
3.Проверочный расчет вала винта
Вал винта будет изготовлен из стали марки Ст 45 с пределом прочности sв = 700 Нмм2.
Определим для опасного сечения запас прочности и сравним его с допускаемым [3] [S]=125 25.
4.Определение напряжения в опасном сечении вала
Нормальные напряжения изменяются по симметричному циклу при котором амплитуда напряжений sа равна расчетным напряжениям изгиба sи:
где Мизг – изгибающий момент в рассматриваемом сечении Нм;
Wнетто – осевой момент сопротивления сечения вала мм3.
Для круглого полого сечения вала:
Касательные напряжения изменяются по нулевому циклу при котором амплитуда цикла tа равна половине расчетных напряжений кручения tк:
где Мкр – крутящий момент Нм;
Wrнетто – полярный момент инерции сопротивления сечения вала мм3.
Полярный момент инерции для круглого полого сечения вала определим по формуле:
5. Определение коэффициента концентрации нормальных и касательных напряжений для расчетного сечения вала
где Кs – эффективный коэффициент концентрации нормального напряжения таблица 11.2 [4 стр. 257] для опасного сечения вала Кs=22;
Кt - эффективный коэффициент концентрации касательного напряжения таблица 11.2 [4 стр. 257] для опасного сечения вала Кt=16;
Кd – коэффициент влияния абсолютных размеров поперечного сечения таблица 11.3 [4 стр. 258] Кd =081;
КF – коэффициент влияния шероховатости таблица 11.4 [4 стр.258] КF = 10;
Ку – коэффициент влияния поверхностного упрочнения таблица 11.5 [4 стр. 258] Ку = 15.
6.Определение пределов выносливости в расчетном сечении вала
где s-1 – предел выносливости при симметричном цикле изгиба Нмм2;
t-1 – пределы выносливости при симметричном цикле кручения Нмм2.
7. Определение коэффициента запаса прочности по нормальным и касательным напряжениям
8. Определение общих коэффициентов запаса прочности
Условие (41) выполняется. Запас прочности вала винта обеспечен.
9. Подбор подшипников для опор вала винта
В качестве опор вала применяются подшипники качения.
Каждая секция вала установлена в роликовые конические двурядные подшипники враспор.
Рисунок 4.2 – Роликовые конические подшипники
Пригодность подшипников определяется сопоставлением расчетной динамической грузоподъемности Сrр Н с базовой Сr или базовой долговечности L10h ч с требуемой Lh ч по условиям:
Сrр ≤ Сr или L10h ³ Lh
где RЕ – эквивалентная динамическая нагрузка Н
w - угловая скорость соответствующего вала
m = 333 – для роликовых.
По диаметру вала из каталога выбираем роликовый подшипник:
Условное обозначение: 7309
10.Схема нагружения подшипников
Определим нагрузки в подшипниках.
Для роликоподшипников характерны следующие соотношения:
где е – поправочный коэффициент.
Rr1 = RА= 43809; Rr2 = RВ= 31104 Н; Fa = Рос
Ra2 = 10544 + 93604 = 1042 Н
Рисунок 4.3 - Схема нагружения подшипников вала
Определение эквивалентной динамической нагрузки подшипников
Эквивалентная динамическая нагрузка Н:
где Кб – коэффициент безопасности находим по таблице 9.4 [4 стр. 133] Кб=11;
КТ – температурный коэффициент при рабочей температуре до 100° С находим по таблице 9.5 [4 стр. 135] КТ = 10;
Х – коэффициент радиальной нагрузки находим по таблице 9.1 [4 стр.129] Х = 04.
Определим для каждого подшипника соотношение и сравним полученное значение с е.
V – коэффициент вращения для подшипников с вращающемся внутренним кольцом V = 1.
Найдем эквивалентную динамическую нагрузку.
Определение расчетной динамической грузоподъемности
Определение базовой долговечности
Определение пригодности подшипников
Условие Сrр ≤ Сr и L10h ³ Lh выполняется следовательно выбранные подшипники пригодны для конструирования подшипниковых узлов.
11.Подбор муфт для привода вала
11.1.Подбор муфты для соединения вала электродвигателя и быстроходного вала редуктора
Для данного соединения используем муфту втулочно – пальцевую. Параметры муфты выбираются по справочнику в зависимости от крутящего момента на валу. [3]
Определим крутящий момент в этом соединении:
где Кр – коэффициент режима нагрузки таблице 10.26 [5 стр. 237] Кр= 15;
Мкр – вращающий момент на соответствующем валу редуктора Нм.
По ГОСТ 21424-93 выбираем упругую втулочно-пальцевую муфту с внутренними диаметрами полумуфт 22 мм и максимальном крутящим моментом 63 Нм. Диаметр пальца dп = 10 мм диаметр упругой втулки dв = 19 мм.
Рисунок 4.4 – Муфта упругая втулочно – пальцевая
Упругие элементы муфты проверяются по напряжениям смятия по формуле:
Пальцы муфта изготовлены из стали 45 ( МПа) рассчитывают на изгиб
С = 4 мм – зазор между полумуфтами
Данная муфта удовлетворяет всем условиям следовательно оставляем подобранную муфту.
11.2.Подбор муфты для соединения выходного вала редуктора и вала винта
Типоразмер муфты выбираем по диаметру валов и по величине расчетного крутящего момента:
Рисунок 4.5 – Муфта упругая втулочно – пальцевая
По ГОСТ 21424-75 выбираем упругую втулочно-пальцевую муфту с внутренними диаметрами полумуфт 50 и 56 мм и максимальном крутящим моментом 1000 Нм. Диаметр пальца dп = 18 мм диаметр упругой втулки dв = 35 мм.
В ходе выполнения курсового проекта был спроектирован шнековый питатель дозатор со следующими параметрами:
- диаметр винта 320 мм;
- мощность на валу винта 0287 кВт;
- номинальная частота вращения винта 4813 обмин;
- диаметр вала винта внешний 50 мм;
- диаметр вала винта внутренний 38 мм;
- число промежуточных опор вала 0;
Двигатель 4АМ71В6У3: Р = 055 кВт n = 1000 обмин;
Редуктор типоразмера Ц2У-250: U =198 n = 1000 обмин;
Быстроходный вал - муфта 63-22-I.1-32-II.2-У3 ГОСТ 21424-75;
Тихоходный вал - муфта 1000-50-I.1-45-II.2-У3 ГОСТ 21424-75.
Модернизация конструкции шнека питателя дозатора
ШНЕКОВЫЙ ПИТАТЕЛЬ содержащий цилиндрический корпус с загрузочным бункером и разгрузочным патрубком размещенный в корпусе приводной шнек вал и лопасть которого выполнены полыми и их полости сообщены между собой и соответственно с источником сжатого воздуха и полостью корпуса отличающийся тем что с целью снижения энергоемкости и увеличения срока эксплуатации внутренняя поверхность корпуса выполнена с расположенными равномерно кольцевыми выступами прерывистыми в продольном направлении и в нем размещена с возможностью опирания на указанные выступы концентричная втулка выполненная из пористого материала кольцевая полость между втулкой и корпусом сообщена с источником сжатого воздуха при этом лопасть шнека состоит из двух частей одна из которых выполнена с расположенными равномерно в продольном направлении выступами а другая — из пористого материала причем расстояние между выступами корпуса равно расстоянию между выступами лопасти шнека и его отношение к толщине пористого материала не более десяти.
Рисунок 5.1 – Модернизированная конструкции шнека питателя дозатора
Изобретение относится к устройствам предназначенным для перемещения сыпучих материалов с помощью вращающегося шнека (винта) а именно к пневмовинтовым питателям.
Известен шнековый питатель содержащий цилиндрический корпус с загрузочным бункером и разгрузочным патрубком- размещенный в корпусе приводной шнек вал и лопасть которого выполнены полыми и их полости сообщены между собой и соответственно с источником сжатого воздуха и полостью корпуса [1].
Недостаток известного устройства — повышенная энергоемкость и интенсивный износ что ведет к сокращению срока эксплуатации.
Цель изобретения — снижение энергоемкости и увеличение срока эксплуатации.
Поставленная цель достигается тем что в шнековом питателе содержащем цилиндрический корпус с загрузочным бункером и 20 разгрузочным патрубком размещенный в корпусе приводной шнек вал и лопасть которого выполнены полыми и их полости между собой и соответственно с. источником сжатого воздуха и полостью корпуса внутренняя поверхность 'корпуса выполнена с расположенными равномерно кольцевыми выступами прерывистыми в продольном направлении и в нем размещена с возможностью опирания на указанные выступы концентричная втулка выполненная из пористого материала кольцевая полость между втулкой и корпусом сообщена с источником сжатого воздуха прй этом лопасть шнека состоит из двух частей одна из которых выполнена с расположенными равномерно в продольном направлении выступами а дру-гая — из пористого материала причем расстояние между выступами корпуса равно расстоянию между выступами лопасти шнека и его отношение к толщине пористого материала не более десяти.
Рисунок 5.2 – Разрез А-А
Шнековый питатель состоит из шнека 1 лопасти 2 продольного прерывистого выступа 3 на лопасти 2. Часть 4 лопасти 2 выполнена из пористого материала сверление 5 сообщает полость лопасти 2 с полым валом 6 шнека 1. Устройство содержит так-же корпус 7 продольный прерывистый выступ 8 на внутренней поверхности корпуса 7 на которую не опирается втулка 9 из пористого материала штуцер 10 для подвода воздуха (жидкости) в полость между втулкой 9 и корпусом 7 уплотнение 11 между корпусом 7 и пористой втулкой 9.
Отношение расстояния h между соседними выступами 8 корпуса 7 равно расстоянию h между соседними выступами 3 лопасти 2 и его отношение к толщине 6 пористого материала выбрано не более десяти из условия предотвращения изгиба пористого материала.
Шнековый питатель работает следующим образом. Вал 6 приводится во вращение внешним приводом к полости вала подводят сжатый воздух (жидкость) с давлением 20 Pi к полости корпуса 7 через штуцер 10 подводят воздух с давлением Р2. Воздух (жидкость) проходит через поры стенок 4 лопасти 2 и втулки 9 и создает слой воз-душной (жидкостной) смазки в зоне их контакта с транспортируемым материалом 25 что существенно снижает коэффициент трения материала об эти поверхности снижает расход энергии и износ контактирующих элементов (лопасти и корпуса) транспортируемым материалом.
Выбор оптимального режима работы шнекового питателя для перемещения сыпучего материала с определенными свойствами осуществляется путем регулирования давления воздуха вначале Р^ из условия потребления питателем минимальной мощности при постоянной производительности затем изменяют давление воздуха Р2 добиваясь минимума потребления мощности при неизменной производительности.
Полученные значения P1 и Р2 оптимальны для режима транспортирования данного материала.
Технико-экономический эффект от применения шнекового питателя в различных отраслях народного хозяйства весьма значителен поскольку снижается энергоемкость и увеличивается срок эксплуатации.
2. Расчет основных показателей модернизированного узла
2.1.Определение мощности на валу винта
W – опытный коэффициент сопротивления при движении груза по желобу [1 стр. 59 табл. 7] W = 3;
k – коэффициент учитывающий характер перемещения винта k = 05;
wВ – коэффициент сопротивления движению вращающихся частей конвейера при подшипниках качения wВ = 005. [1]
2.2.Определение мощности и выбор электродвигателя
2.3.Определение силовых параметров на валу винта
По ГОСТ 19523-81 выбираем асинхронный электродвигатель типа: 4АМ71В6У3 с номинальной мощностью и асинхронной частотой вращения nдв.ном.= 1000 мин-1
Подведем итог: с учетом модернизации конструкции шнека питателя уменьшения сопротивления мы получили уменьшение мощности и крутящего момента на валу винта выигрыш в мощности электродвигателя а следовательно повышение экономичности и срока службы данного узла.
Охрана труда мероприятия по техническому обслуживанию и эксплуатации шнека питателя-дозатора
Общие требования безопасности
1. К самостоятельной работе машиниста питателя могут быть приняты лица не имеющие медицинских противопоказаний достигшие 18-летнего возраста и прошедшие:
инструктаж по пожарной безопасности;
первичный инструктаж на рабочем месте;
обучение безопасным методам и приемам труда не менее чем по 10 часовой программе (для работ к которым предъявляются повышенные требования безопасности по 20 часовой программе);
инструктаж по электробезопасности на рабочем месте и проверку усвоения его содержания. 1.2. Машинист питателя должен проходить:
повторный инструктаж по безопасности труда на рабочем месте не реже чем через каждые три месяца;
внеплановый инструктаж: при изменении технологического процесса или правил по охране труда замене или модернизации производственного оборудования приспособлений и инструмента изменении условий и организации труда при нарушениях инструкций по охране труда перерывах в работе более чем на 60 календарных дней (для работ к которым предъявляются повышенные требования безопасности - 30 календарных дней);
диспансерный медицинский осмотр согласно приказу МПС № 23 от 07.07.87 г
3. Машинист питателя обязан:
соблюдать правила внутреннего трудового распорядка установленные на предприятии;
соблюдать требования настоящей инструкции инструкции о мерах пожарной безопасности инструкции по электробезопасности;
соблюдать требования к эксплуатации оборудования;
использовать по назначению и бережно относиться к выданным средствам
индивидуальной защиты.
4. Машинист питателя должен:
уметь оказывать первую (доврачебную) помощь пострадавшему при несчастном случае;
знать местоположение средств оказания доврачебной помощи первичных средств пожаротушения главных и запасных выходов путей эвакуации в случае аварии или пожара;
выполнять только порученную работу и не передавать ее другим без разрешения мастера или начальника цеха;
во время работы быть внимательным не отвлекаться и не отвлекать других не допускать на рабочее место лиц не имеющих отношения к работе;
содержать рабочее место в чистоте и порядке
5. Машинист питателя должен знать и соблюдать правила личной гигиены. Принимать пищу курить отдыхать только в специально отведенных для этого помещениях и местах. Пить воду только из специально предназначенных для этого установок.
6. При обнаружении неисправностей оборудования приспособлений инструментов и других недостатках или опасностях на рабочем месте немедленно сообщить мастеру или начальнику цеха. Приступить к работе можно только с их разрешения после устранения всех недостатков. 1.7. При обнаружении загорания или в случае пожара:
отключить оборудование;
сообщить в пожарную охрану и администрации;
приступить к тушению пожара имеющимися в цехе первичными средствами пожаротушения в соответствие с инструкцией по пожарной безопасности. При угрозе жизни - покинуть помещение.
8. При несчастном случае оказать пострадавшему первую (доврачебную) помощь немедленно сообщить о случившемся мастеру или начальнику цеха принять меры к
сохранению обстановки происшествия (состояние оборудования) если это не создает опасности для окружающих.
9. За невыполнение требований безопасности изложенных в настоящей инструкции
рабочий несет ответственность согласно действующему законодательству.
10. В соответствии с "Типовыми отраслевыми нормами бесплатной выдачи рабочим и служащим специальной одежды специальной обуви и других средств индивидуальной защиты" машинист компрессорной установки должен использовать следующие СИЗ:
-комбинезон хлопчатобумажный рукавицы комбинированные противогаз.
11. Основными опасными факторами при определенных обстоятельствах могут быть:
узлы конвейерных линий;
низкие температуры в зимний период;
повышенный шум и вибрация.
12. При нахождении на железнодорожных путях машинист должен соблюдать следующие требования безопасности:
-к месту работы и с работы проходить только специально установленными маршрутами обозначенными указателями «Служебный проход»;
-переходить железнодорожные пути только под прямым углом;
Требования безопасности перед началом работы
1. Осмотреть спецодежду и убедиться в ее исправности. Надеть спецодежду застегнуть ее
на все пуговицы волосы убрать под головной убор.
2. Проверить свое рабочее место. Убедиться что оно освещено и не загромождено
посторонними предметами.
3. Ознакомиться с записями в журнале приемки-сдачи смены со дня своей последней
4. . Проверить исправность обслуживаемого оборудования.
5 Убедиться что оборудование заземлено электрошкафы закрыты и заперты на
Проверить работу телефонной связи и аварийной сигнализации.
Требования безопасности во время работы
1. После включения (согласно производственной инструкции) питателя и всех конвейеров необходимо прослушать его работу.
При обнаружении постороннего шума или стука несвойственного нормальной работе оборудования остановить его для устранения неполадок.
2. Для безопасной работы питателя необходимо контролировать:
непрерывность поступления в питатель исходных материалов;.
отсутствие посторонних стуков и шумов
нормальную работу шнеков;
3. Производить регулярный наружный осмотр оборудования питателя.
4.. Ремонт электрооборудования электросети рубильников прочего электрооборудования разрешается производить только электротехническому персоналу.
Требования безопасности в аварийных ситуациях
1.Питатель должен быть немедленно остановлен в случаях если:
слышны стуки удары в питателе или двигателе или обнаружены их неисправности которые могут привести к аварии;
ощущается запах гари или дыма из электродвигателя;
заметно увеличение вибрации питателя или двигателя.
2. Машинист должен аварийно остановить питатель (нажать кнопку "стоп") и только
затем доложить руководству.
3. После аварийной остановки питателя пуск его может быть произведен с разрешения лица ответственного за безопасную эксплуатацию компрессорной установки.
4. В случае внезапного прекращения подачи электроэнергии машинист обязан немедленно перевести пусковые устройства электродвигателей и рычагов управления в положение "стоп".
Требования безопасности по окончании работы
1. Привести в порядок рабочее место.
Приспособления и инструмент убрать в специально отведенное для этого место. Промасленную ветошь во избежание самовозгорания убрать в металлическую тару с крышкой.
2 Остановить оборудование и обесточить электрооборудование
3. Обо всех имевших место недостатках сообщить мастеру..
4. Снять и убрать в специально отведенное место (шкаф) спецодежду.
5. Тщательно вымыть руки и лицо. По возможности принять душ.
В результате выполнения курсового проекта были получены теоретические знания по проектированию и расчету оборудования бетоносмесительного завода:
- по заданным техническим параметрам подобрано требуемое количество типы и марки вспомогательного оборудования;
-выполнен расчет шнека питателя дозатора цемента и описан принцип его работы;
-приведена техника безопасности и мероприятия по охране труда при работе по приготовлению бетонной смеси и строительного раствора и эксплуатация и обслуживание шнека питателя дозатора цемента;
-выполнен патентный поиск расчет и модернизация рассматриваемого оборудования.
СПИСОК ИСПОЛЬЗОВАННОЙ ЛИТЕРАТУРЫ
Машины непрерывного транспорта. Р.Л. Зенков И.И. Ивашков Л.Н. Колобов. – М.: Машиностроение 1987. – 347с.
Транспортирующие машины. А.О. Спиваковский В.К. Дьячков. – М.: Машиностроение 1983. – 568 с.
Курсовое проектирование по деталям машин. А.Е. Шейнблит. – М.: Высшая школа 1991. – 275 с.
Оборудование для обработки сыпучих материалов. В.Я. Борщев Ю.И. Гусев.: Учебное пособие. М.: Машиностроение 2006. – 421 с.
Справочник по расчетам подъемно-транспортных машин. Ф.Л. Марон А.В. Кузьмин. Минск: Высшая школа 1977. – 369 с.
Организация производства растворных и бетонных смесей. Балицкий В.С. - Киев: Будовелъник 1980.-184с.
Конструирование узлов и деталей машин: Учеб. пособие для студ. техн. спец. вузов П.Ф. Дунаев О.П. Леликов. – 8-е изд. пепераб. и доп. – М.: «Издательский центр академия» 2004. – 496 с.