Конвертер вертикальный




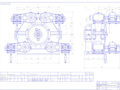
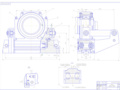
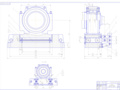
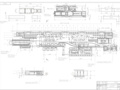
- Добавлен: 25.10.2022
- Размер: 5 MB
- Закачек: 1
Описание
Состав проекта
![]() |
![]() |
![]() ![]() ![]() ![]() |
![]() ![]() ![]() ![]() |
![]() ![]() ![]() ![]() |
![]() ![]() ![]() ![]() |
![]() ![]() ![]() ![]() |
![]() ![]() ![]() ![]() |
![]() ![]() ![]() ![]() |
![]() ![]() ![]() ![]() |
![]() ![]() ![]() ![]() |
![]() ![]() ![]() ![]() |
![]() ![]() ![]() ![]() |
![]() ![]() ![]() |
![]() ![]() ![]() |
![]() ![]() ![]() |
![]() |
![]() ![]() |
![]() ![]() |
![]() ![]() |
![]() ![]() |
![]() ![]() |
![]() ![]() |
![]() ![]() |
![]() ![]() |
![]() ![]() |
![]() ![]() |
![]() ![]() |
![]() ![]() ![]() |
Дополнительная информация
План цеха.dwg

Аккумуляторная установка
Главный пост управления
Спецификация на конвертер.dwg

Гидравлический амортизатор
Привод наклона конвертера
Комплект электрооборудования
Спецификация на подшипниковую опору(мод).dwg

Спецификация на конвертер(мод).dwg

Конвертер вертикальный
Гидравлический амортизатор
Привод наклона конвертера
Комплект электрооборудования
Опора подшипника(мод).dwg

Спецификация на подшипниковую опору.dwg

Спецификация на привод.dwg

Конвертер(мод).dwg

Техническая характеристика
Вме.стимость конвертера
Рабочий объем конвертера
Удельный объем конвертера
Скорость поворота конвертера обмим
Количество электродвигателей
Технические требования
*Размеры для справок.
Прокладки установить на монтаже при необходимости. После
установки пакеты прокладок прихватить
электродуговой сваркой между собой.
Сварной шов выполнить ручной электродуговой свркой. Сварку
производить электродами типа Э46А ГОСТ 9467-75.
на монтаже у заказчика футеровать со стороны
конвертера огнеупорным кирпичом.
Монтаж оборудования конвертера производить согласно
инструкции по монтажу и эксплуатации.
Ось подшипника фиксированного
Ось подшипника плавающего
Опора подшипника.dwg

разогретого конвертера
холодного" конвертера
Ось основания подшипника
Привод поворота.dwg

кгсм №ступени А m Z1 Z2
iст iред Смазка редуктора А m Z1 Z2 iред Смазка редуктора iобщ
Редуктор специальный
Конвертер.dwg

Техническая характеристика
Вме.стимость конвертера
Рабочий объем конвертера
Удельный объем конвертера
Скорость поворота конвертера обмим
Количество электродвигателей
Технические требования
*Размеры для справок.
Прокладки установить на монтаже при необходимости. После
установки пакеты прокладок прихватить
электродуговой сваркой между собой.
Сварной шов выполнить ручной электродуговой свркой. Сварку
производить электродами типа Э46А ГОСТ 9467-75.
на монтаже у заказчика футеровать со стороны
конвертера огнеупорным кирпичом.
Монтаж оборудования конвертера производить согласно
инструкции по монтажу и эксплуатации.
Ось подшипника фиксированного
Ось подшипника плавающего
СОДЕРЖАНИЕ.doc
СПЕЦИАЛЬНАЯ ЧАСТЬ 15
1Назначение и область применения кислородного конвертера ..15
2Техническая характеристика кислородного конвертера 15
3Описание конструкции кислородного конвертера .16
4Анализ недостатков в работе кислородного конвертера 20
5Литературно-патентный обзор .20
6Предложения по модернизации 24
7Описание конструкции модернизированной подшипниковой опоры..24
8Расчеты по модернизации .25
8.1Расчеты нагрузок действующих на машину и определение исходных данных для расчета ..25
8.2Силовой и кинематический анализ механизма 28
8.3Расчет мощности привода машины ..30
8.4Выбор элементов кинематической схемы механизма 30
8.5Прочностные расчеты модернизированных узлов .31
1Разработка конфигурации фундамента для монтажа конвертера .36
2Геодезическое обоснование монтажа конвертера 36
3Способы доставки конвертера к месту монтажа .38
4Технологическая карта монтажа конвертера 39
ЭКСПЛУАТАЦИЯ КОНВЕРТЕРА 41
1Условия работы кислородного конвертера ..41
2Характер износа наиболее ответственных деталей кислородного конвертера в процессе эксплуатации 41
3Анализ мероприятий по техническому обслуживанию кислородного конвертера в целях поддержания его работоспособности .41
4Предложения по совершенствованию организационного и технологического характера направленного на поддержание исправного состояния кислородного конвертера 44
РЕМОНТ КОНВЕРТЕРА .46
1Выбор формы и метода проведения ремонтов конвертера 46
2Разработка перспективного графика планово-предупредительных ремонтов конвертера на год ..44
3Описание методов восстановления футеровки кислородного конвертера 47
4Смазка кислородного конвертера 48
ОРГАНИЗАЦИОННАЯ ЧАСТЬ 52
2Характеристика ремонтного хозяйства конвертерного цеха 55
3Планирование ремонтов оборудования ..56
4Организация выполнения ремонтных работ ..57
5Расчет годового фонда заработной платы ремонтных рабочих участка 58
ЭКОНОМИЧЕСКАЯ ЧАСТЬ 60
1Анализ затрат на текущий ремонт и содержание основных средств 60
2Экономическая эффективность от внедрения проекта ..61
1Характеристика строительной площадки 65
1.1Бытовые и вспомогательные помещения ККЦ-2 66
2Основные вредные и опасные факторы производственного процесса в кислородно-конвертерном цехе № 2 67
3Мероприятия по уменьшению вредных и опасных факторов в кислородно-конвертерном цехе № 2 68
3.1Расчет искусственного освещения в цехе ..70
4Средства индивидуальной защиты ..71
5Пожарная безопасность в конвертерном цехе № 2 72
ОХРАНА ОКРУЖАЮЩЕЙ СРЕДЫ ..74
ВВЕДЕНИЕ.doc
В сталеплавильном производстве за последнее время произошли коренные качественные изменения в связи с заменой мартеновского способа плавки кислородно-конверторным созданием крупных конвертерных агрегатов разработкой и широким применением машин непрерывного литья заготовок.
В век научно-технического прогресса особо важную роль играет производство высококачественных сталей обладающих большой удельной прочностью. Повышение энергосиловых параметров машин и оборудования уменьшение их металлоемкости требуют выпуска специальных и особо чистых сталей.
В увеличении объема производства и улучшении качества стали исключительно важная роль принадлежит кислородно-конверторному производству имеющему высокую производительность при меньших капитальных затратах(по сравнению с мартеновским способом) а также имеет более благоприятные условия для автоматизации. Производительность одного 400-т конвертера превышает производительность целого мартеновского цеха с 8-10 печами вместимостью 600 т каждая.
Изложены основные расчеты используемые при расчете поворотного механизма конвертера определения энергосиловых параметров и прочностных характеристик. Приведен анализ их качеств указаны преимущества внедряемого оборудования и технологий.
Диплом.doc
Технологическая схема предприятия показана на рисунке 1.1.
В целом же структура комбината состоит из следующих подразделений:
-Горно-обогатительный комплекс;
-Коксохимическое производство;
-Аглодоменное производство;
-Сталеплавильное производство;
-Прокатное производство.
Шахтоуправление представлено:
-шахтой им. Артема №1 с годовой производственной мощностью 17 млн. тонн.
Горно-обогатительный комплекс который способен обеспечить металлургическое производство концентратом в объеме 7 млн. тонн агломератом – 65 млн. тонн представлен:
-дробильными фабриками;
-обогатительными фабриками.
Коксохимическое производство способно произвести более 3 млн. тонн валового кокса 6 % влажности для нужд доменного производства;
Аглодоменное производство с возможностями производства более 6 млн. тонн чугуна и 3 млн. тонн агломерата представлено:
-агломерационным цехом;
-доменным цехом № 1;
-доменным цехом № 2;
-шлакоперерабатывающим цехом.
Агломерационный цех.
Исходным сырьем для производства агломерата служит концентрат ГОКа аглоруда шахтоуправления и основная часть - утилизированные отходы производства: шламы шлаки отсевы колошниковая и известковая пыль и др. Полученный агломерат поступает в доменный цех № 1 комбината.
В состав цеха входят 5 доменных печей № 1 5 6. 7 8 с суммарным полезным объемом 10419 м3 а также бункерная эстакада отделение приготовления огнеупорных масс и смесей участок десульфурации чугуна.
Сырьем для производства чугуна служит: агломерат агломерационного цеха и ГОКа окатыши СевГОКа и ЦГОКа железная руда шахтоуправления скрап. В качестве топлива используется кокс коксохимического производства природный газ и антрацит.
В составе цеха - крупнейшая в Украине доменная печь № 9 объемом 5000 м3.
Шлакоперерабатывающий цех основные задачи которого - переработка огненно-жидкого шлака доменного цеха № 1 и обеспечение этого цеха составами шлаковозов а также извлечение скрапа из шлаков текущего производства. В цехе производится:
-шлаковая вата и пемза;
-песчано-щебеночная смесь.
Сталеплавильное производство комбината - это шесть самостоятельных цехов основная деятельность которых направлена на выпуск стали. В состав производства входят:
-кислородно-конвертерный цех;
-цех подготовки составов:
-огнеупорно-известковый цех:
-цех ремонта металлургических печей.
Кислородно-конвертерный цех.
Оснащен шестью конвертерами емкостью 160 тонн. Продувка металла в конвертере кислородом осуществляется сверху.
В составе цеха двухванный сталеплавильный агрегат № 6 и мартеновская печь № 4.
Цех подготовки составов.
В цехе два отделения подготовки составов которые обслуживают мартеновский и конвертерный цехи. Отделения производят наборку составов под разливку стали сверху и сифонным способом а два отделения по раздеванию слитков обеспечивают обжимные цехи стальными слитками с высокой температурой прибытия.
Предназначен для разделки стального негабаритного и чугунного скрапа и лома. Цех расположен на двух участках: на 1-м размещены шлаковые отделения отделение огневой резки и копровое отделение № 1; на 2-м - копровое отделение № 2.
Огнеупорно-известковый цех состоит из отделений:
-по производству извести;
-по производству огнеупоров и торкретмассы.
Производимой известью цех обеспечивает сталеплавильные цехи и аглофабрику.
Цех ремонта металлургических печей
Основная функция цеха - ремонт мартеновских печей конвертеров миксеров методических печей прокатных станов кольцевой и вращающихся печей ОИЦ.
Прокатное производство.
Для производства высококачественного проката комбинат располагает мощными современными автоматизированными станами специальными агрегатами и оборудованием для термической обработки и осуществления отделочных операций В состав прокатного производства входят:
Сортопрокатный цех № 1.
Сортопрокатный цех № 2.
В цехе установлены рекуперативные нагревательные колодцы стан "1250" и непрерывно-заготовочный стан "730500". Цех прокатывает слитки массой 85 т в квадратную заготовку сечением 125x125 мм и 80x80 мм которая затем передается для дальнейшего переката на мелкосортные и проволочные станы и отгружается товарной продукцией.
Нагрев слитков осуществляется в рекуперативных нагревательных колодцах а прокатка на обжимном стане «1300» и непрерывно-заготовочном стане «900700500». Цех прокатывает слитки массой 85 т в квадратную заготовку сечением 80x80 мм и 150x150 мм которая отгружается товарной продукцией и передается для переката на станы сортопрокатных цехов.
В составе сортопрокатного цеха № 1 три мелкосортных и один проволочный стан.
В его составе два мелкосортных стана и проволочный стан. Мелкосортные станы "250-4.5" выпускают круглую и арматурную сталь диаметром 14-32 мм квадратную сталь со стороной 16-22 мм шестигранную сталь 17-27 мм круглую сталь 14-28 мм. катанку диаметром 65 и 8 мм круглую арматурную сталь диаметром 6 и 8 мм.
В состав цеха входит мелкосортно-проволочный стан 250150 производящий сортовой прокат диаметром 14-32 мм и катанку диаметром 5.5-18 мм.
Цех оснащен современными станками для калибровки прокатных валков ремонта подшипников жидкостного трения. В цехе производится ремонт прокатных валков методом микроплазменного напыления.
В состав предприятия входят собственные ремонтные базы энергетические и транспортные хозяйства а также другие подразделения необходимые для обеспечения производственного процесса. Схема их взаимодействия представлена на рис. 1.2.
Рисунок 1.2 Схема взаимодействия основных и вспомогательных цехов комбината.
класса А240С (бывший А-1) (Ф8-32)
ДСТУ 3760-98 ГОСТ 56694
СТЗПС допускается СТЗКП
Ф8; 10-12 14-16; 18-24 2532
Прокат арматурный для жб конструкций класса А400С
(бывший А-3) класса А500Сн (№8-32)
ДСТУ 3760-98 ГОСТ 5669-4
№8-16 СтЗПС; 25Г2С; №18-22 СтЗГПС; №25-32 Ст32Г2Рпс.
Прокат арматурный для жб конструкций класса А500С
ГОСТ 7566-94 ГОСТ 380-94 ДСТУ 3760-98
№18-22 стЗГПС; №25-32 ст20ГС
Сталь арматурная термо-механически упрочненная
для жб конструкций А600
А800А600С №10-18 А1000 А1000н №10-18
Марки согласно ГОСТу
Катанка из углеродистой стали обыкновенного качества
УО1-65 В: УО2-55;60;70;80
СТОМ Ст 1КПДС.СП Ст 2КПЛС.СП СТ3КП ПС
Продолжение таблицы 1.1
Катанка стальная канатная (65)класс зя Ш1точн.пр.в
Катанка из низкоуглеро-дистой и легированной стали для изготовления сварочной проволоки (65)
ТУ 14-15-345-94; ТУ 14-15-346-94
Прокат из стали качественной конструкционной углеродистой и легированной для холодного выдавливания и высадки
Прокат сортовой из углеродистой качественной конструкционной стали (10-30)
горячекатаные равнополочные
х25х4;32х32х4;35х35х4;
СТО СТЗКП ПС СТ4КП. ПС СТ5ПС СП СТ6ПС.СП
Полоса стальная гарячекатанная 40х4-6; 50х4-10;
СТЗКП ПС СТ4КП. ПС СТ5ПС СП СТ6ПС.СП
Прокат стальной горячекатаными круглый(10-30)
СТО СТ3КП ПС СТ5ПС.СП
Прокат передельный сортовой и фасонный хозяйственного назначения
Передельный марок ПЛ1ПЛ6
2 Характеристика кислородно-конвертерного цеха. Применяемое оборудование и его характеристика
Конвертерный цех введен в эксплуатацию в 1965 году. В результате проведенной в 1978 году реконструкции в состав цеха входят следующие отделения: миксерное конвертерное разливочное шихтовое шлаковое. Производительность цеха за 2004г составила -3585000 тонн стали. В цехе производится кипящая полуспокойная спокойная сварочная и легированная сталь различных марок согласно ТИ 228 Ст. КК - 01- 98 ТИ 228 Ст. КК - 02- 98 . ТИ 228-КК-30-2000 и ТИ 228-КК-33-2001 на соответствующие требованиям ГОСТ 30136-95 ДСТУ 3683-98 ТУ14-15-345-94 ТУ 14-15-346-94 АSТМ А51OМ и АSТМ А36.
Техническое и механическое оборудование цеха используется согласно требованиям «Правил технической эксплуатации оборудования» с учетом «Системы технического обслуживания оборудования».
На всех участках технологического процесса производства стали осуществлять контроль нормируемых параметров.
Структурная схема конвертерного цеха показана на рис.1.2.
Рисунок 1.3 Структурная схема конвертерного цеха
Металлолом подают железнодорожным транспортом в отделение магнитных материалов I и загружают в приемные бункера. Совки объемом 40м3 заполняют металлоломом с помощью магнитного крана 1. Груженые совки взвешивают и устанавливают на скраповоз 2 подающий их на рабочую площадку или в загрузочный пролет. Завалку металлолома в конвертер 3 емкостью 160т осуществляют загрузочной машиной 4 грузоподъемностью 2х130т.
Чугун доставляют в ковшах чугуновозов 5 грузоподъемностью 185т из доменного цеха в миксерное отделение II и краном сливают в стационарный миксер 6 емкостью 1300т. При необходимости чугун выдают из миксера в ковши самоходных чугуновозов 7 транспортирующих его в загрузочный пролет к конвертерам. Чугун заливают заливочным краном 8 грузоподъемностью 18050т.
Сыпучие материалы доставляют в шихтовое отделение III немагнитных материалов железнодорожным или автомобильным транспортом. Шихтовое отделение предназначено для приема погрузки и подачи в конвертерное отделение металлолома и шлакообразующих материалов.
Материалы из полувагонов 9 разгружают в приемные бункера 10 с последующей выдачей электровибрационными питателями. Подачу материалов в расходные бункера 11 конвертерного корпуса IV осуществляют наклонным конвейерным трактом 12 и реверсивными передвижными конвейерами 13. Система 14 весового дозирования и подачи состоящая из вибропитателей весовых дозаторов конвейеров промежуточных бункеров и течек обеспечивает загрузку определенных порций шлакообразующих материалов в конвертер в процессе плавки.
Технически чистый кислород в конвертер подают машиной 15 через фурму. Он поступает по магистрали из кислородного цеха. Интенсивность продувки плавки кислородом- 400÷450 м3мин.
Доставку ферросплавов в главный корпус цеха осуществляют автомобильным или железнодорожным транспортом в контейнерах или используют конвейерный тракт подачи сыпучих материалов. Контейнеры с ферросплавами разгружают краном в расходные бункера 16. Взвешенные порции ферросплавов нагревают в камерных печах 17 и по течке 18 подают в сталеразливочный ковш.
В конвертерных цехах применяют способ разливки стали в изложницы установленные на тележках. Сталь сливают из конвертера в сталеразливочный ковш установленный на сталевозе 19.
Ковш со сталью передают сталевозом в разливочное отделение V или в разливочные пролеты примыкающие к главному корпусу. Изложницы заполняют металлом из ковша перемещаемого разливочным краном 20 над составом 21 с изложницами. После затвердевания и полной кристаллизации слитков составы с изложницами подают локомотивом в стрипперное отделение VI для снятия прибыльных надставок и подрыва слитков с уширением кверху. Изложницы с уширением книзу снимают с тележек и направляют на подготовку к следующему наливу. Все операции выполняют стрипперным краном 22. Затем состав отправляют в нагревательное отделение обжимного стана VII в котором слитки устанавливают в нагревательные колодцы а состав с изложницами направляют на душирующую установку. После охлаждения изложницы поступают в отделение чистки и смазки IX а затем в отделение подготовки составов X где осуществляют уборку и установку на тележки поддонов центровых» прибыльных надставок и т. д. Подготовленные составы вновь подают в разливочное отделение. Таким образом изложницы совершают замкнутый цикл работы и подготовки.
Шлак из конвертера сливают в ковш самоходного шлаковоза 23 и передают сначала в шлаковый пролет главного корпуса для перестановки чаши на уборочный шлаковоз 24 а затем направляют в шлаковое отделение XI для охлаждения и последующего дробления ударами бабы поднимаемой краном 25. Переработанный шлак отгружают в отвал думпкарами 26.
Техническая характеристика некоторого механического оборудования цеха:
Таблица 1.2 - Техническая характеристика конверторов
Внутренний объем конвертора м3
Удельный объем конвертора м3т
Внутренние размеры по футеровке мм
Габаритные размеры мм
Масса конвертора без футеровки т
Частота вращения конвертора обмин
количество и мощность кВт
Частота вращения обмин
быстроходного редуктора
тихоходного редуктора
Таблица 1.3 - Техническая характеристика сталеразливочных ковшей
Масса порожнего ковша т
Масса груженного ковша т
Наружный диаметр ковша мм
Таблица 1.4 - Техническая характеристика самоходных ковшевозов
Скорость передвижения кмч
Механизм передвижения:
мощность электродвигателя кВт
частота вращения обмин
передаточное число редуктора
1 Назначение и область применения кислородного конвертера
Основным агрегатом кислородно-конвертерного цеха является конвертер. К основному механическому оборудованию конвертера относится механизм его поворота.
Конвертер предназначен для производства стали методом продувки жидкого чугуна технически чистым кислородом. Конвертер устанавливается в конвертерном цехе металлургического предприятия.
2 Техническая характеристика кислородного конвертера
Общая характеристика
Емкость конвертора т 160
Внутренний объём конвертора м3 135
Удельный объём конвертора м3т 084
Габаритные размеры мм:
Масса конвертора без футеровки т 926
Масса футеровки т 477
Частота вращения обмин:
Электродвигатель Д-818
Частота вращения обмин 470
Режим работы ПВ% 25
- быстроходный трехступенчатый
- тихоходный одноступенчатый Передаточные числа:
- быстроходного редуктора 597
- тихоходного редуктора 775
Крутящий момент на выходном валу привода кНм:
3 Описание конструкции кислородного конвертера
Конвертер представляет собой сосуд цилиндрической формы с нижней суженной частью изготовленный из листовой стали с огнеупорной футеровкой внутри [1]. Корпус конвертера сварен из нескольких обечаек изготовленных гибкой штамповкой из листового металла - конических в верхней части цилиндрических в средней и сферической в нижней. Горловина конвертера усилена литой конической обечайкой к которой болтами крепят массивный шлем 1 (рис. 2.1). Цилиндрическая часть корпуса усилена приваренным несущим поясом 8 состоящим из кронштейнов подвесок опоры и упора связанных двумя рядами верхних и нижних дугообразных ребер жесткости. Также цилиндрическая часть кожуха конвертера охвачена массивным стальным кольцом 3 с двумя диаметрально расположенными цапфами 4 которыми конвертер опирается на подшипники на стойках. В сферическую обечайку вварено литое стальное кольцо служащее для крепления вставного днища клиньями. Последнее отсоединяют от корпуса при проведении ремонта для облегчения ломки и удаления выгоревшей футеровки а также для ускорения охлаждения корпуса конвертера воздухом подающимся вентиляторами. Внутри конвертер футерован монолитной кладкой из смоломагнезитовых блоков.
Несмотря на меры предосторожности кожух в процессе работы деформируется в нем появляются трещины устраняемые при ремонте. Наиболее интенсивно кожух изнашивается в области горловины где выходящие из горловины газы непосредственно воздействуют на стальной лист в результате чего последний окисляется и сгорает. Эту часть можно защитить массивными стальными накладками которые болтами крепятся к кожуху в области футеровки горловины. Такие накладки изготавливают в виде трех четырех сегментов по периметру горловины заменяемых в случае необходимости.
Опорное кольцо коробчатого сечения является составным – цапфовые плиты соединены со сварными секторами цилиндрическими шарнирами. В процессе работы оно нагревается до температуры 150 - 250°С что обуславливает возникновение деформаций. Для уменьшения воздействия на опорное кольцо выбросов металла и шлака его защищают экраном из стального листа приваренного к кожуху и нависающего над опорным кольцом. Для увеличении прочности опорного кольца на внутренней его поверхности в районе цапф приваривают ребра жесткости. Для создания водяного охлаждения внутри опорного кольца на его стенке обращенной к корпусу укладывают трубы по которым циркулирует вода.
Цапфы опираются на подшипники качения – сферические двухрядные роликоподшипники. Подшипники опираются на стальные литые станины. Фундамент опоры не связан с фундаментом здания. Стальную опору футеруют шамотным кирпичом для защиты от попадающего на нее металла и шлака при продувке и выпуске шлака.
Опоры конвертера помимо восприятия больших вертикальных и осевых сил должны компенсировать перекосы и значительные перемещения цапф вызванные тепловыми деформациями опорного кольца и погрешностями при монтаже и изготовлении. Они смонтированы на сварных рамах и
Рисунок 2.1 Корпус конвертера
закреплены в фундаментах. Одна опора фиксированная другая – плавающая подвижная в осевом направлении. Опоры смонтированы на конических роликоподшипниках (рис. 2.2). Каждая опора кольца 4 корпуса конвертера состоит из обоймы 2 смонтированной на цапфе 3. Обойма опирается на две колонны 9 со сферическими подшипниками. Верхние подшипники смонтированы на цапфах 7 нижние - на цапфах 10 станины. В нижней части обоймы установлен штырь 6 на котором находится сферическая втулка. На фиксированной опоре втулка помещена в цилиндрическое гнездо 8 станины на плавающей опоре – в гнездо 1 с пазом в направлении параллельном оси цапф конвертера. Перекосы корпуса конвертера компенсируются шарнирно закрепленными обоймами в стойках и стоек на станине а осевые перемещения от термических деформаций опорного кольца – поворотом шарнирно закрепленных на корпусе стоек и осевым перемещением обоймы плавающей опоры вместе со сферической втулкой в продольном пазе.
Привод поворота конвертера (рис. 2.3) состоит из одноступенчатого тихоходного редуктора 1 четырех трехступенчатых быстроходных редукторов 4 навесного типа четырех электродвигателей 5 со встроенными тормозами и систем фиксирования тихоходного и быстроходного редукторов с пружинными демпферами [2].
Рисунок 2.2 Кинематическая схема опор конвертера
Тихоходный редуктор с четырьмя приводными валами шестернями 6 втулкой колеса 7 посажен на коническую шейку 2 цапфы опорного кольца 9. Корпус редуктора соединен с качающейся рамой 16 которая через гидравлический демпфер 17 связана с основанием. Такая конструкция предупреждает поворот корпуса под действием реактивного опрокидывающего момента и гасит динамические нагрузки возникающие в системе. Сферические шарниры в узлах крепления демпфера обеспечивают его самоустановление при перекосах.
Быстроходные редукторы втулками 3 колес последних передач посажены на конические хвостовики валов-шестерен тихоходного редуктора. Фиксирование редукторов выполнено пружинными демпферами 15 с винтовыми стяжками связывающими корпусы редукторов с качающейся рамой или корпусом тихоходного редуктора.
На литых корпусе и крышке быстроходного редуктора предусмотрены приливы для крепления кронштейна электродвигателя и пружинного демпфера. Электродвигатель соединен с ведущим валом редуктора зубчатой муфтой. Подшипниковые узлы валов снабжена коническими роликоподшипниками с централизованной подачей смазки. Колесо последней зубчатой передачи закреплено шпонкой на втулке установленной в корпусе редуктора на подшипниках качения.
Быстроходный редуктор насаживают на конический хвостовик вала шестерни тихоходного редуктора и снимают и снимают с него с помощью гидрошайбы представляющей собой гидродомкрат с шестью гидроцилиндрами расположенными в корпусе по окружности. Для соединения с гидрошайбой на выступающей части втулки редуктора нарезана наружная резьба.
Тихоходный редуктор разъемной конструкции изготовлен с литым корпусом и крышкой в которых по окружности расположены шесть гнезд под подшипниковые узлы приводных валов-шестерен. К корпусу прилиты лапы для его соединения с качающейся рамой. Зубчатое колесо посажено на шпонках на массивную втулку установленную в центральном гнезде корпуса на двух роликоподшипниках. Внутри втулка расточена на конус кольца для посадки редуктора на коническую шейку цапфы опорного кольца. Тихоходный редуктор напрессовывают на цапфу и снимают с помощью гидрошайбы навинчиваемой на хвостовик втулки.
Рисунок 2.3 Кинематическая схема привода конвертера
Принцип работы кислородного конвертера заключается в следующем: при наклонном или горизонтальном положении конвертера в него загружают стальной лом и часть извести заливают чугун; затем переводят конвертер в вертикальное положение опускают фурму и продувают ванну [3]. Остальную известь вводят порциями через горловину по ходу продувки. В результате этого окисленность шлака в начальной стадии продувки кратковременно повышается обеспечивая быстрое растворение в нем извести и дефосфорации металла без передува т.е. при [C] > 0.1%. В случае недостаточно отработанного автоматического контроля технологии попадания в заданный анализ достигается тем что при [C] немного превышающим заданное (на 0.1 – 0.2 %) поднимают фурму выключают дутье переводят конвертер в горизонтальное положение отбирают пробы металла и шлака и замеряют температуру ванны с помощью термопары погружения (т.е. проводят промежуточную повалку конвертера). Ожидая анализ несколько поворачивают конвертер при этом сталевыпускное отверстие поднимается выше уровня ванны затем его разделывают. Получив анализ металла производят продувку длительность которой определяется отношением избытка углерода [C] к известной по данным предыдущих плавок скорости выгорания углерода. При хорошо налаженной технологии плавок и наличии автоматического контроля с помощью ЭВМ большинство плавок ведут без додувок.
После окончания продувки и отбора проб сталь сливают через отверстие в ковш а шлак – в чашу. Раскисляют и легируют металл в конвертере или в ковше.
При высоком содержании фосфора в чугуне в середине плавки сливают промежуточный шлак и наводят второй иногда используют промежуточный шлак часть которого оставляют в конвертере после слива предыдущей плавки. Длительность всего цикла плавки колеблется в пределах 30 – 45 мин.
4 Анализ недостатков в работе кислородного конвертера
Практика эксплуатации конвертеров показала что температура корпуса достигает 300°С. Термические напряжения возникающие в средней части корпуса вызывают значительную несоосность и перекосы осей до 1-2° которые приводят к быстрому разрушению цилиндрических роликовых подшипников.
Конвертер работает в тяжелых условиях механизм поворота и опорные узлы подвержены действию больших статических и динамических нагрузок корпус и опорное кольцо подвержены высокой и неравномерной температуре нагрева возникают большие температурные напряжения в элементах металлоконструкций привода [2].
Также отмечена недостаточная надежность плавающей подшипниковой опоры конвертера из-за проскальзывания роликов линейных подшипников сложности конструкции и неудобству обслуживания.
Не достаточная надежность работы навесных редукторов из-за частой поломки средних зубчатых колес вследствие больших нагрузок.
Большие остаточные напряжения возникающие в процессе сварки опорного кольца что ведет к снижению надежности и долговечности.
5 Литературно-патентный обзор
Существуют конвертеры разной вместимости : 100 150 160 250 300 350 400 450 т [1]. Отличаются они друг от друга массой габаритами и различной конструкцией механизма поворота. В настоящее время применяют стационарные и навесные механизмы поворота конвертера с электродвигателями ранее применяли гидравлический привод поворота но так как у такого привода довольно низкая надежность по сравнению с механизмом поворота с электродвигателями его сняли с эксплуатации.
Стационарные и навесные приводы бывают двух типов : двухсторонние и односторонние. Односторонние приводы применяют на конвертерах небольших габаритов (100 160) так как на конвертерах больших габаритов и массы они не обеспечивают необходимую надежность сталеплавильного агрегата. Стационарные приводы требуют специального массивного фундамента. Преимущества двухстороннего привода над односторонним – уменьшение в два раза крутящих моментов подводимых к цапфе и опорному кольцу.
Навесные многодвигательные приводы значительно повышают надежность работы механизма поворота конвертера так как выход со строя части электродвигателей не приводит к отказу в работе; устранение длинных валопроводов применение демпферов в системах фиксирования тихоходного и быстроходного редукторов способствует резкому снижению динамических нагрузок в приводе; многопоточное разветвление мощности в тихоходном редукторе позволило уменьшить нагрузки на зубья передачи принять меньшую величину модуля и свести к минимуму габариты редуктора.
Конвертеры могут быть с дутьем сверху снизу и комбинированным дутьем [2]. В рассматриваемой в работе конструкции кислородного конвертера применяется дутье сверху через фурмы. Фурма через горловину конвертера вводится в ванну жидкого металла и производится его продувка. При дутье снизу фурма расположена в днище конвертера. Недостатком этого метода является быстрое изнашивание футеровки днища конвертера вследствие воздействия на нее газов подающихся через фурму. Комбинированный метод – одновременное дутье сверху и снизу что повышает производительность агрегата и качество выплавляемой стали но является достаточно дорогим.
Например в работе В.П. Горбенка и В.Д. Добряка [4] предлагается изменение конструкции удерживающего устройства навесного привода конвертера отличающееся тем что оно снабжено дополнительным гибким элементом и шарнирами тяги одним концом закреплены в шарнирах и установлены на станине а на другом конце тяг закреплены блоки с перекинутыми через них гибкими элементами. При этом гибкие элементы навиты в противоположных направлениях на корпус привода а их концы закреплены на тягах и упругодеформируемых элементах. Такая конструкция должна повысить надежность привода так как на подшипники навесного привода не оказывает действия сила тяжести что позволяет также применить подшипники более легкой серии.
В работе В.А. Набокова [5] предлагается изменение конструкции опорного кольца конвертера в котором фланцы цапф 3 выполнены в виде многоугольника а стенки цапфовых узлов выполнены из элементов 6-13 ограниченных прямолинейными гранями и жестко соединенных по этим граням. При этом крайние из элементов соединены соответственно с гранями фланцев цапф и стенками цапфовых узлов. Применение такой конструкции позволяет упростить конструкцию и снизить остаточные напряжения возникающие в процессе сварки что повышает надежность и долговечность опорного кольца (рис.2.4).
В работе В.В. Филатова [6] предлагается установка дополнительно стопорного устройства на привод поворота (рис.2.5) которое имеет независимый гидравлический привод с пневмоаккумулятором. Данное стопорное устройство применяется в аварийных режимах когда необходимо зафиксировать корпус конвертера в определенном положении (например при аварийном отключении электроэнергии).
В работе В.Д. Клименко [7] предлагается изменение конструкции подшипниковой опоры (рис 2.6) которая отличается тем что снабжена тягами 23 и 24 верхними и нижними кронштейнами 25 и 22. При этом верхние кронштейны 25 закреплены на корпусе 1 и шарнирно соединены с ограничителем 21 посредством тяг 23 и 24. Нижние кронштейны 22 закреплены на основании и шарнирно соединены с ограничителем а сепараторы подшипников – с ограничителем через тяги. Причем оси
Рисунок 2.4 Опорное кольцо коробчатого сечения
Рисунок 2.5 Опорное кольцо конвертера
Рисунок 2.6 Стопорное устройство привода наклона конвертера
- конвертер; 2- опора; 3- цапфа; 4- зубчатое колесо; 5- корпус редуктора; 6- навесной привод; 7- гасители колебаний; 8- эксцентриковый захват; 9- вал; 10-кривошип; 11- гидроцилиндр.
Рисунок 2.7 Подшипниковая опора
верхних и нижних шарниров на ограничителе симметричны оси шарниров тяг сепаратора. Предлагаемая подшипниковая опора с ограничителем обеспечивает повышение надежности работы за счет простоты конструкции способствующей удобству обслуживания исключения возможности поворота конвертера вокруг вертикальной оси и исключения проскальзывания роликов линейных подшипников.
6 Предложения по модернизации
Анализ и синтез недостатков в работе конвертера а также существующих предложений по модернизации конвертера показал что наиболее целесообразным является модернизация подшипниковой опоры конвертера которая позволит устранить проскальзывание роликов линейного подшипника повысит простоту эксплуатации подшипниковой опоры а также предотвратит поворот конвертера вокруг вертикальной оси.
7 Описание конструкции модернизированной подшипниковой опоры
Плавающая подшипниковая опора конвертера рис. 2.8 включает корпус 1 крышку 2 торцевые крышки 3 с уплотнениями 4 самоустанавливающийся подшипник 5 закрепленный на цапфе 6 конвертера помощью распорных втулок 7 и 8 зафиксированных полукольцами 8 с накидным бандажом 9. Корпус 1 подшипниковой опоры посредством расположенных симметрично оси двух цилиндрических вкладышей и двух линейных подшипников опирается на пару цилиндрических и пару плоских вкладышей основания . Цилиндрические вкладыши подстраиваются из-за неточности изготовления и деформаций корпуса 1 на плоский вкладыш. Из-за термических расширений конвертера корпус 1 перемещается на роликах 10 установленных в сепараторе 11 на осях 12. При этом ограничитель 13 шарнирно связанный с основанием посредством нижнего кронштейна 14 и с сепараторами подшипников шарнирными тягами 15 а также с верхним кронштейном 16 корпуса шарнирными тягами обеспечивает принудительное перемещение линейных подшипников без проскальзывания роликов.
Ограничитель 13 устанавливается вертикально. Нижние 14 и верхние 16 кронштейны жестко закреплены соответственно к корпусу 1 и основанию 17.
Плавающая опора работает следующим образом. В процессе эксплуатации перекос цапфы 6 компенсируется самоустанавливающимся подшипником 5 подшипниковой опоры.
Компенсация термических расширений конвертера производится за счет перемещения корпуса 1 опоры вдоль оси цапф конвертера на роликах 12 линейных подшипников.
Благодаря кинематической связи тягам 15 и 18 обеспечивается условие принудительного перемещения линейных подшипников без проскальзывания роликов 10 что особенно важно для конвертеров испытывающих значительные вибрации в процессе работы.
Ограничитель самопроизвольных перемещений одновременно исключает возможность поворота корпуса 1 вокруг вертикальной оси подшипниковой опоры.
Рисунок 2.8 Подшипниковая опора
8 Расчеты по модернизации
8.1 Расчеты нагрузок действующих на конвертер и определение исходных данных для расчета
Техническая характеристика конвертера:
Масса конвертора т 1403
Координаты центра тяжести порожнего конвертера
(из чертежа): хn = 40 мм; yn =165 мм
При повороте электродвигатель преодолевает опрокидывающие моменты от порожнего конвертера Мп от массы жидкого металла Мм и сил трения Мтр [2].
Моп = Мп + Мм + Мтр (2.1)
Общий вес конвертера Gп = 1403 т = 14030000 Н = 14030 кН (из технической характеристики).
Расстояние от центра тяжести до оси вращения конвертера (рис. 2.9):
Угол между радиусом-вектором r0 и вертикальной осью:
α = = arctg= α = 140 (2.3)
Опрокидывающий момент сопротивления порожнего конвертера Мn:
Мп = Gп r0 sin(φ + α) = 14030 · 0170 · sin(42 + 14) = 2003 кНм (2.4)
Расчет опрокидывающего момента от жидкого металла производится графоаналитическим способом по методу проф. П.Н. Аксенова [8] согласно которой опрокидывающий момент жидкого металла при повороте конвертера зависит от угла поворота φ и веса металла нем. Предварительно вычисляется полный угол поворота конвертера при котором окончится слив:
φ = 9° + аrсtg = 9° + аrсtg = 42° (2.5)
где R1 R2 H1 – размеры верхней части конвертера (рис 2.5).
Момент сопротивления повороту жидкого металла весом См и порожнего конвертера весом Gп
Мтр = (Gn + Gм) f = (14030 +1600)015= 9964 кНм (2.6)
где Gn = 1403 т = 14030 кН – масса порожнего конвертора;
Gм = 160 т = 1600 кН – масса жидкого металла;
f = 015 коэффициент трения в опорах цапфы [4 т.1];
dц = 850 мм – диаметром цапфы (из чертежа).
Рисунок 2.9 Схема расчета момента сопротивления
повороту жидкого металла
Расстояние центра тяжести от оси цапф r = 02К
определяет угол поворота = аrсtg . Плечо жидкого металла (расстояние от его центра тяжести до точки поворота):
rм = r sin(φ – ) (2.7)
Для определения опрокидывающего момента от веса жидкого металла необходимо знать плечо действия силы для каждого угла наклона относительно оси вращения конвертера:
Согласно опыта эксплуатации конвертеров емкостью 160 т наибольший момент от веса жидкого металла возникает в начальной стадии процесса слива металла из горловины конвертера при объеме жидкого металла в конвертере – Gм = 140 т = 14000 Н и угле поворота = 150 [8].
Тогда согласно формулы 2.11 и 2.12:
rм = 1100 sin(42 – 15) = 500 мм
Мм = 1400 · 05 = 700 кНм
Общий момент поворота конвертера согласно ф-лы 2.1:
Мобщ = 2003 + 9964 + 700 = 3700 кНм
8.2 Силовой и кинематический анализ механизма поворота конвертера
Механизм поворота конвертера емкостью 160 т (рис. 2.10) – это односторонний навесной механизм. На цапфе жестко закреплено ведомое зубчатое колесо 1 закрытое корпусом. Этот корпус опирается на цапфу через подшипники и от проворачивания его удерживает противовес 6. Таким образом при вращении зубчатого колеса 1 с цапфой корпус 5 остается неподвижным. Зубчатое колесо вращают четыре электродвигателя с редукторами 2 выходные вал-шестерни 3 которых входят в зацепление с колесом. Эти вал-шестерни через подшипники крепятся в отверстиях стенки корпуса 5. Электродвигатели с редукторами держатся (навешены) на валах-шестернях 3 при этом вращая валы сами электродвигатели остаются неподвижными т. к. удерживаются от проворачивания демпферами 6.
На рисунке 2.11 показана кинематическая схема одностороннего навесного привода. В ней выделяют электродвигатели 5 (4 шт.) с тормозами быстроходные трехступенчатые редукторы 4 тихоходный редуктор 1 (зубчатое колесо 7 вал-шестерня 6). В каждом из четырех приводов электродвигатель через быстроходный редуктор вращает вал-шестерню и тем самым зубчатое колесо и цапфу 2 с опорным кольцом 9. Цапфы установлены в подшипниковых опорах: опора 10 – фиксированная опора 8 – плавающая.
Из технической характеристики:
- передаточное число быстроходного редуктора –
- передаточное число тихоходного редуктора– iт.р.=775.
Согласно кинематической схемы общее передаточное отношение привода:
i = iб.р · iт.р = 597 · 775 = 462675 (2.9)
Рисунок 2.10 Силовая схема привода
- зубчатое колесо; 2- электродвигатель с редуктором;
- выходной вал-шестерня; 5- корпус; 6-демпфер;
Рисунок 2.11 Кинематическая схема навесного привода конвертера
- тихоходный редуктор; 2- цапфа; 3- выходной вал-шестерня;
- быстроходный трехступенчатый редуктор; 5- электродвигатель
с тормозом; 6- вал-шестерня; 7- зубчатое колесо; 8- опора плавающая;
- опорное кольцо; 10- опора фиксированная
8.3 Расчет мощности привода поворота конвертера
Согласно принятой кинематической схемы привода наклона конвертера общий момент на валах каждого из четырех валов эл. двигателей определяется из следующего выражения:
Мдв. общ.= 4 · Мдв (2.10)
где Мдв – момент на валу одного эл. двигателя; кВт.
Зная величину момента поворота конвертера мы можем определить расчетное значение момента на валу каждого из четырех электродвигателей по формуле:
Мдв = Мобщ 4 · i. · (2.11)
где = 096 к.п.д. привода (из паспорта);
Мдв = 3700·103 4 · 462675 · 096 = 2085 Нм
Статическая мощность одного двигателя кВт:
N = Мдв ·nдв 9550 (2.12)
где nдв – частота вращения выходного вала эл.двигателя обмин;
Предварительно принимаем значение nдв = 470 обмин.
N = 2085 ·470 9550 = 103 кВт.
2.4 Выбор элементов кинематической схемы механизма поворота конвертера
Согласно рассчитанной статической мощности одного эл. двигателя произведем его выбор по справочникам [8] соблюдая следующие условия:
Этим условиям удовлетворяет металлургический тихоходный электродвигатель постоянного тока Д-818 который имеет следующие технические характеристики:
- частота вращения выходного вала обмин 470
Трехступенчатый редуктор одноступенчатый редуктор и приводную шестерню принимает такими же как и в базовом варианте привода т.е.:
- трехступенчатый редуктор с передаточным отношением
- одноступенчатый редуктор с передаточным отношением i = 775.
2.5 Прочностные расчеты модернизированных узлов
Определим нагрузку приходящуюся на подшипниковую опору составив расчетную схему (см. рис. 2.12). Для расчета принимаем вес конвертера с металлом.
Согласно расчетной схемы на одну подшипниковую опору приходится нагрузка равная половине веса конвертера с металлом:
Р = = = 7815 т = 7815 кН(2.13)
где Qк – вес конвертера с футеровкой;
Qм – вес металла в конвертере при полной загрузке.
Корпус подшипника опирается на два цилиндрических ролика которые в свою очередь опираются на основание. Следовательно рассчитанная нагрузка Р передается на основание подшипника через пару роликов диаметр которых принимаем аналогично существующим – 320 мм. Следовательно величина нагрузки приходящаяся на один ролик:
Р1 = Р2 = Р 2 = 7815 2 = 39075 кН(2.14)
Ролик изготовлен из стали для которой предел текучести равен
Допускаемое напряжение на сжатие одного ролика:
[сж] = 03 · т = 03 · 800 = 240 МПа(2.15)
где 03 – коэффициент безопасности.
Расчетная площадь поперечного сечения ролика:
Ар = ) = 0785 ·(3202 – 362) = 7936664 мм2 (2.16)
где d – наружный диаметр ролика;
d1 –диаметр отверстия под установку шпильки.
Рисунок 2.12 Расчетная схема к определению нагрузки на подшипниковые опоры
Напряжение сжатия в ролике:
сж = = = 4923 МПа ≤ [сж] = 240 МПа (2.17)
Условие прочности выполняется следовательно диаметр роликов принимаем диаметру существующей конструкции. Но как видно из расчетов напряжение сжатия в ролике значительно меньше допустимого напряжения на сжатие т.е. мы имеем большой запас прочности что может позволить применить ролики меньшего диаметра или из более дешевого материала.
При работе из-за термических расширений корпус конвертера перемещается на плавающей опоре. Сепараторы соединяющие ролики передают нагрузку от движущегося конвертера на шарнирные тяги (см. рис. 2.13). Благодаря кинематической связи тяг сепаратора и тяг установленных на кронштейнах которые крепятся к корпусу и основанию подшипника обеспечивается принудительное перемещение линейных подшипников без проскальзывания роликов.
Рисунок 2.13 Схема к расчету крепления кронштейнов
При перемещении сепаратора нагрузка передается на кронштейн закрепленный на корпусе подшипника создавая разрывное усилие для болтов крепления кронштейна. Величину усилия на сепараторе определим из выражения:
Р1 = Р · = 7815 · 015 = 117225 кН(2.18)
где – коэффициент трения качения.
Тогда разрывное усилие для расчета диаметра болтов крепления кронштейна определим из уравнения равновесия системы относительно точки А:
МА = - Р1 · а + Р1б · 2а = 0(2.19)
Р1б = = Р1 2 = 117225 2 = 586125 кН(2.20)
Болт рассматриваем как стержень на который действует осевая растягивающая сила. Условие прочности такого соединения должно удовлетворять выглядит следующим образом:
= Р1б 4 · Аб = 4 · Fр 4 · · d2 [] (2.21)
где Р1б – растягивающая осевая сила;
– количество болтов в одном соединении (принимаем предварительно;
Аб – расчетная площадь сечения болта;
[] - допускаемое напряжение.
Для определения допускаемого напряжения необходимо знать допускаемый коэффициент запаса прочности [S] который в общем машиностроении принимается в пределах [S] = 15 – 3. Принимаем [S] = 2. Тогда допускаемое напряжение равно:
[] = = = 1225 МПа (2.22)
где т – предел текучести материала болта.
Принимаем к установке болты изготовленные из стали 20 ГОСТ1050 -80 для которой т = 240 МПа.
Тогда расчетный диаметр одного болта:
d = = = 00391 м = 391 мм (2.23)
Принимаем к установке болт М48 по ГОСТ7798-70 прочность которого согласно проведенным расчетам обеспечена.
Сепараторы передающие усилия от движущегося при расширении конвертера также испытывают напряжение сжатия которое определим из выражения:
сж = = = 6977 МПа (2.24)
где 2 - количество сепараторов;
Ат – площадь поперечного сечения одного сепаратора которую принимаем равной:
Ат = а · б = 60 · 280 = 16800 мм2
где а – ширина сечения сепаратора мм;
б – высота сечения сепаратора мм.
Условие прочности сечения сепаратора:
сж = 6977 МПа ≤ [сж] = 105 МПа
где [сж] = 03 · т = 03 · 350 = 105 МПа;
т - предел текучести материала сепаратора (сталь 45).
Условие прочности на сжатие выполняется следовательно принятые предварительные размеры поперечного сечения сепаратора принимаем окончательно. Как видно из расчетов напряжение сжатия в сепараторе значительно меньше допустимого напряжения на сжатие т.е. мы имеем большой запас прочности что может позволить выполнить сепараторы или из более дешевого материала.
1 Разработка конфигурации фундамента для монтажа конвертера
Требования предъявляемые к фундаменту:
В процессе приемки фундамента конвертера проверяют все размеры в плане и по высоте; расположение анкерных болтов и их размеры; состояние и правильность расположения плашек фиксирующих продольные и поперечные оси конвертера и реперов указывающих высотные отметки площадок фундамента на которые будет устанавливаться оборудование [9].
Перед установкой оборудования на фундамент прежде чем заливать цементную подливку необходимо поверхность фундамента смочить водой это предупреждает впитывание воды с бетона из цементной подливки.
Готовность фундамента конвертера к производству монтажных работ оформляется актом который подписывают представители строительной организации а также технадзора заказчика. К акту должны быть приложены составленные строительной организацией исполнительные схемы фундамента анкерных болтов в сопоставлении с основными и привязочными размерами их как в плане так и по высоте а также схематическое расположение геодезических знаков плашек и реперов.
2 Геодезическое обоснование монтажа конвертера
Установку и проверку оборудования конвертера производят совмещая оси машины с монтажными осями закрепленными на фундаментах под оборудование. При этом должны быть выдержаны заданные проектом размеры в вертикальной плоскости между уровнем движения обрабатываемого материала и уровнем чистого пола цеха.
Для этой цели на планах цехов наносят основные продольные и поперечные оси от машин и привязывают к продольным и поперечным осям колонн здания цеха. В процессе монтажа все высотные измерения проводят на основе специальных отметок называемых реперами. Все монтажные оси в плане и высотные реперы разделяют на контрольные и рабочие. Рабочие оси реперы в свою очередь делят на основные и вспомогательные. Все разбивки рабочих осей и высотных реперов на фундаментах выполняют от контрольных осей и реперов заложенных в цехе.
Контрольные оси совмещают с осями колонн здания цеха. Здание цеха привязывают к осям рабочей координатной сетки завода. Каждую контрольную ось фиксируют двумя плитками или скобами установленными на отдельных бетонных столбах вне фундаментов под оборудование на башмаках колонн.
Основанием для отметок высотных реперов служат абсолютные отметки полигонометрических знаков относительно уровня моря перенесенные на территорию завода. Эти абсолютные отметки пересчитанные относительно уровня пола цеха указывают на строительных чертежах. На технологических чертежах расположения оборудования отметку пола принимают за нуль считая ее абсолютной отметкой. Контрольные репера устанавливают на специальных железобетонных столбах сечением 500х500 мм и более возвышающихся над уровнем пола на 200 мм и расположенных вне фундаментов под оборудование [10].
Рисунок 3.1 Геодезическая привязка фундамента конвертера
Рисунок 3.2 Геодезическое привязка конвертера
3 Способы доставки конвертера к месту монтажа
Оборудование конвертера от завода изготовителя доставляется на железнодорожных платформах в разобранном виде. Оборудование отгружается заводом-изготовителем местами с соблюдением принципа поузловой поставки. Отдельные съемные детали некоторых узлов и аппаратуры поставляются групповыми местами включающими оборудование нескольких различных узлов изделия.
Оборудование приходит заказчику в законсервированном виде (окрашенным покрытым консервирующими смазками в местной упаковке) срок действия консервирующих покрытий 24 месяца со дня отгрузки.
Внутри завода разгрузка оборудования осуществляется кранами расположенными в конвертерном цехе.
4 Технологическая карта монтажа конвертера
Решающее влияние на дальнейшую работу оказывает качество монтажа. При монтаже осуществляется сборка установка и выверка оборудования конвертера на рабочем месте с последующей регулировкой наладкой испытанием и сдачей в эксплуатацию.
Для проведения монтажных и ремонтных работ в конвертерном цехе используют технологические мостовые краны заливочные и разливочные специальные монтажные краны и краны других пролетов.
Технологическая карта монтажа конвертера показана в таб. 3.1.
Таблица 3.1 – Технологическая карта монтажа конвертера
График выполнения работ час
час. Гра-фик выполнения работ час.
технологической последовательности
Собрать опорное кольцо на стенде
Произвести укрупнительную сбоку корпуса конвертора
Установить станины и стойки конвертора
Собрать цилиндрический вертикальный редуктор
Установить корпус конвертора в опорное кольцо
Установить корпус конвертора с опорным кольцом на домкратной тележке затем установить конвертор в проектное положение
Установить верхний конус со шлемом
ЭКСПЛУАТАЦИЯ КОНВЕРТЕРА
1 Условия работы кислородного конвертера
Конвертер работает в тяжелых условиях механизм поворота и опорные узлы подвержены действию больших статических и динамических нагрузок корпус и опорное кольцо подвержены высокой и неравномерной температуре нагрева возникают большие температурные напряжения в элементах металлоконструкций привода.
2 Характер износа наиболее ответственных деталей кислородного конвертера в процессе эксплуатации
В процессе эксплуатации разливочного крана наиболее часто встречаются следующие износы:
- механический износ среднего зубчатого колеса в навесных
Ответственным элементом кислородного конвертера является футеровка которая защищает корпус конвертера от воздействия высоких температур. Стойкость футеровки составляет 600 – 1000 плавок. В процессе работы конвертера рабочий слой футеровки изнашивается в результате механического износа (удары кусков лома при завалке его в конвертер срыв настылей и др.) растворения ее в шлаке а также под действием термических напряжений.
3 Анализ мероприятий по техническому обслуживанию кислородного конвертера в целях поддержания его работоспособности
Эксплуатация конвертера должна производиться в строгом соответствии с технологическими инструкциями разработанными соответствующими проектно-технологическими организациями применительно к данной конструкции согласованными и утвержденными в установленном порядке [11].
Во время эксплуатации установить постоянное наблюдение за температурой корпуса и кольца опорного. Температура верхней части корпуса не должна превышать +350 С° нижней части +250 С° кольца опорного +250 С°.
В случаях превышения указанных температур работа на конвертере должна быть прекращена. Продолжать работу на конвертере разрешается после устранения причин ведущих к перегреву. Охлаждение конвертера должно быть естественным запрещается для ускорения охлаждения поливать перегретые участки водой.
Для предотвращения причин ведущих к общим перегревам корпуса конвертера и опорного кольца необходимо:
)не допускать нарушения технологического режима плавки приводящим к общим выбросам расплавленного шлака и скопления его на горловине и корпусе конвертера;
)установить постоянное наблюдение за состоянием футеровки конвертера. Категорически запрещается эксплуатировать конвертер при износе футеровки ведущем к оголению арматурного слоя а также при местных разрушениях рабочего слоя футеровки;
)не допускать длительных (более 5 мин.) остановок наполненных сталеразливочного ковша и шлаковой чаши под конвертером.
Состояние защитных элементов конвертера – листов защиты и вертикальных стенок между подшипниковой опорой приводом и конвертером во многом определяет работоспособность конвертера в целом. За их состоянием должно быть установлено постоянное наблюдение.
Не допускается эксплуатация конвертера в случае отрывов отдельных секций листов защиты или повреждений ведущих к попаданию выбросов шлака и прочего в кольцевой зазор между корпусом конвертера и кольцом опорным.
Вертикальные стенки между подшипниковой опорой и конвертером приводом и конвертером должны быть выполнены из толстолистового проката (толщиной 40 50 мм) либо футероваными огнеупорным кирпичом.
Не допускается попадание горячих выбросов брызг металла в зону подшипниковой опоры и привода.
Во время эксплуатации необходимо установить регулярное наблюдение за состоянием сварных швов. Во время каждой остановки конвертера на ремонт футеровка производить осмотр сварных швов внутри и снаружи кольца опорного а также швов приварки кронштейнов к корпусу конвертера. Основное внимание обращать на состояние несущих швов; в случае появления в них трещин швы должны быть обязательно отремонтированы. При появлении трещин в технологических швах необходимо установить за ним наблюдение.
Во время остановок на ремонт футеровки проверять наличие зазоров между упорами цапфовых плит и вкладышами кронштейнов корпуса конвертера. В случае увеличения зазоров более чем 4 мм на сторону установить дополнительные прокладки под вкладыши либо заменить вкладыши на новые.
После одной – двух компаний конвертера произвести подтяжку (допрессовку) навесных приводов с помощью гидрошайбы.
В начальный период эксплуатации (спустя 3 4 недели после пуска) необходимо сделать анализ проб масла из картеров редукторов. При обнаружении загрязнения масла его необходимо очистить или заменить. В дальнейшем эту операцию рекомендуется проводить I раз в 6 месяцев.
Контроль уровня масла в навесных редукторах производить один раз в сутки по мере необходимости масло следует добавлять один раз в 10 дней замену масла в муфтах и их промывку производить не реже одного раза в 6 месяцев.
В процессе эксплуатации должно быть установлено постоянное наблюдение за температурой опорного подшипника и подшипников привода наклона.
Температура подшипников не должна быть более 80° С. Уровень масла в подшипниковой опоре не должен быть выше 150 мм уровня сливных патрубков.
Периодически 1 – 2 раза в месяц рекомендуется производить несколько полных поворотов конвертера в одну сторону с целью переустановки роликов подшипниковой опоры и привода.
В процессе эксплуатации необходимо проверять правильность положения привода наклона конвертера и подшипниковой опоры относительно оси вращения конвертера в связи с возможными деформациями станин фундаментов и опорного кольца.
Отклонение плоскостей разъемов привода и подшипниковой опоры от оси вращения не должны превышать 0.5 мм на длине 1 м в направлении оси цапф и 1.0 мм на 1 м в перпендикулярном направлении при разности положения плоскостей разъемов между собой не более 2 мм.
Для обеспечения равномерного износа зубьев колеса и приводных вал шестерен специального редуктора рекомендуется во время ремонтов изменять положение зубчатого колеса по отношению к приводной цапфе кольца опорного путем поворота колеса на угол 5° 10° с последующим вводом его в зацепление с зубчатой втулкой цапфы.
Нормальная работа конвертера обеспечивается четырьмя двигателями. При выходе из строя одного из электродвигателей допускается довести плавку до конца. Длительная работа на трех электродвигателях недопустима.
При эксплуатации системы смазочной необходимо следить за нормальным поступлением масла в узлы трения а также за нормальным сливом масла в резервуар станции.
Следить чтобы в масло не попадала влага и грязь.
Контролировать химический состав масла и менять масло при его несоответствии стандарту не реже одного раза в год.
В процессе эксплуатации конвертера необходимо систематически производить технические осмотры и ремонт электрооборудования периодичность которых устанавливается в зависимости от производственных условий.
При обслуживании и ремонте электрооборудования конвертера необходимо руководствоваться технической документацией поставляемой комплектно с электрооборудованием.
Во время первых опытных плавок постоянно а во время эксплуатации не менее одного раза в смену контролировать температуру подшипников скольжения в вертлюге кислородном При повышении температуры подшипника выше 60° С необходимо установить причины повышения температуры и устранить их.
Во время эксплуатации производить пополнение смазки ВНИИП – 282 ТУ 38.101274 – 72 в подшипнике скольжения на вертлюге кислородном не менее одного раза в неделю. Разовая подача смазки около 2 см³ на каждую точку смазки.
Во время эксплуатации постоянно осуществлять контроль герметичности уплотнений на подшипниках скольжения вертлюга кислородного с помощью мановакууметра присоединенного к контрольному штуцеру.
Рекомендуется не реже одного раза в 6 месяцев проводить ревизию подшипников скольжения. При этом определять состояние уплотнительных манжет и посадочных мест а также поверхностей трения.
Замену манжет 240х280 и колей 285-300-85-2 на вертлюге кислородном производить через год эксплуатации.
При срабатывании мановакууметров во время плавки свидетельствующем о “продуве” уплотнений на вертлюге кислородном необходимо определить скорость подъема давления. Если скорость подъема давления находится в пределах 0.01 – 0.1 кгсм² в мин. плавку допускается довести до конца. После чего необходимо осмотреть места уплотнений и заменить уплотнения. Если скорость подъема давления выше 0.1 кгсм² в мин. необходимо:
)прекратить продувку кислородом;
)заменить уплотнения.
4 Предложения по совершенствованию организационного и технологического характера направленного на поддержание исправного состояния кислородного конвертера
Для обеспечения равномерного износа зубъев колеса и приводных вал шестерен специального редуктора рекомендуется во время ремонтов изменять положение зубчатого колеса по отношению к приводной цапфе кольца опорного путем поворота колеса на угол 5° 10° с последующим вводом его в зацепление с зубчатой втулкой цапфы.
1 Выбор формы и метода проведения ремонтов конвертера
Ремонт конвертора производят на месте его установки. После отсоединения колпака-охладителя газов с помощью домкратной тележки отнимают днище и поворачивают корпус в горизонтальное положение и специальной машиной разрушают изношенную футеровку охлажденную до 200°-300°С а бой кирпича собирают в шлаковые ковши или думпкары [12].
Новую футеровку выкладывают начиная снизу при помощи гидравлического телескопического подъемника грузоподъемностью 5 т передвигаемого рельсовому пути сталевозной тележкой. Огнеупоры подвозят на поддонах автопогрузчиком и поднимают канатным подъемником в центр рабочей площадки. Диаметр рабочей площадки 300 мм минимальная высота над головками рельсов 4400 мм ход при подъеме 7000 мм.
По окончании выкладки футеровки к корпусу пользуясь домкратным устройством приболчивают днище поворачивают корпус в рабочее положение и обжигают футеровку коксом горящим в струе кислорода. Кокс подают машиной для завалки скрапа а раскаливают в горнах.
Проектная продолжительность смены футеровки конвертора составляет 3.5 суток. Межремонтный период равен 14-16 суток при кампании 500 плавок.
Смену корпуса конвертора а также съем конвертора в случае закозления плавки выполняют пользуясь гидравлическим устройством грузоподъемностью 1600 т установленным на специальной тележке с колеей шириной 4500 мм.
Ремонт механизма поворота конвертора и смену фурм производят с помощью мостового крана грузоподъемностью 50 или 80 т установленного в конвертерном пролете.
Ремонт конвертора производят узловым методом т.е. разбирают на узлы и требующие ремонта узлы заменяют заранее подготовленными запасными с последующей сборкой регулировкой и испытание машины. При этом методе продолжительность ремонта значительно меньше чем при других методах проведения ремонтов что очень важно так как нужно обеспечить минимальные простои оборудования.
Применяется централизованная форма проведения ремонтов она лучше всего согласуется с положениями планово0предупредительной системы ремонтов способствует повышению качества ремонтов и удлинению межремонтных периодов.
2 Разработка перспективного графика планово-предупредительных ремонтов конвертера на год
Целью планово-предупредительных работ является восстановление работоспособности машины путем рационального ухода замены и ремонта
изношенных деталей и узлов. Эти мероприятия производятся по заранее составленному плану. Планы остановок на ремонт составляются на основании многолетних опытных данных о стойкости отдельных деталей и узлов. Было установлено что наилучшая периодичность ППР 30 – 40 дней т.е. ежемесячные остановки на ремонт (таб. 5.1).
На основании данных профилактических осмотров составляется ведомость дефектов. Ведомости дефектов подвергаются тщательному изучению с целью определения количества рабочих необходимых для ремонта. На основании этих данных годового графика ППР составляется оперативный план проведения ремонта на каждый месяц который заключается в уточнении даты остановки агрегата на ремонт. (Таб. 5.2).
Годовой график составляется на основании данных о состоянии агрегата которые предоставляются главному инженеру завода начальником цеха. После этого ведется разработка годового графика капитальных и текущих ремонтов кроме этого должен учитываться финансовый план завода. Окончательный проект годового графика ремонтов подписывается начальником цеха и его помощником по оборудованию согласовывается с главным механиком завода а затем утверждается главным инженером.
Утвержденный график передается в цех за 15 дней до начала планируемого года. Ремонт привода конвертера производится одновременно с остановкой конвертера для замены футеровки или корпуса.
3 Описание методов восстановления футеровки кислородного конвертера
Для повышения срока службы футеровки конвертера применяют профилактический горячий ремонт – торкетирование которое заключается в нанесении на футеровку тонкого защитного слоя торкет-массы. Торкетирование проводят при горизонтальном положении конвертера сразу после выпуска стали когда футеровка нагрета до температуры 1300° - 1500°С.
Применяют два способа торкетирования. По первому способу торкет-массу состоящую из увлажненного огнеупорного порошка с добавкой связующего материала подают на поверхность нагретой футеровки в струе сжатого воздуха. Недостатком способа является сползание еще не затвердевшей массы с наклонных участков футеровки в результате чего торкетирование конвертора в районе цапф не эффективно.
Второй способ – факельное торкетирование – заключается в том что сухую торкет-массу состоящую из магнезитового порошка в смеси с тонкоизмельченным коксом подают на поверхность футеровки в высокотемпературном факеле. При сгорании кокса в струе кислорода частицы огнеупорного порошка разогреваются до оплавления и при их ударе о футеровку происходит приваривание. Достоинствами факельного торкетирования являются равномерность покрытия возможность работы конвертора сразу после торкетирования в то время как при торкетировании увлажненными массами требуется длительное время нагрева.
Для торкетирования конвертеров применяют машины двух типов: подвесные перемещающиеся по балкам над конвертером и напольные передвигающиеся по рабочей площадке. Напольные машины отличаются от подвесных большей гибкостью в работе возможностью качественного торкетирования труднодоступных мест на футеровке.
Огнеупорный порошок и кислород подаются к машине по гибким шлангам электроэнергия по гибким кабелям. Подвод и отвод воды для охлаждения фурмы осуществлены шлангами. Блок подачи огнеупорного порошка расположен в стороне и состоит из бункера герметичного клапанного затвора и аэрирующего устройства с которым соединен трубопровод сжатого воздуха. Аэрирующее устройство представляет собой воздухопроводящую коробку в верхней части которой закреплен лист с малыми отверстиями обтянутый тканью из стекловолокна.
Торкетирование проводят следующим образом. Фурму движением машины вводят внутрь конвертера и включают систему водоохлаждения. При поступлении сжатого воздуха в аэрирующее устройство порошок в нижней части бункера взрыхляется и транспортируется в фурму. Одновременно начинают подавать кислород. Факел пламени образуется в результате горения кокса входящего в состав торкет-порошка. С началом процесса торкетирования включают механизм вращения фурмы в результате чего на поверхность футеровки наносится кольцевой слой. Когда толщина слоя достигает 50 – 70 мм фурма смещается в осевом направлении в результате перемещения машины. При Нанесении покрытия на труднодоступные участки футеровки фурму наклоняют.
Торкетирование позволяет увеличить стойкость футеровки на 100 – 135 плавок. Средние затраты времени в сутки на торкетирование составляют 18 – 20 мин.
4 Смазка кислородного конвертера
На работоспособность и надежность деталей КПД механизмов и соответственно на расход электроэнергии при эксплуатации кислородного конвертера большое влияние оказывают выбор и режим смазки которая кроме уменьшения трения предохраняет также от коррозии попадания на взаимодействующие поверхности абразивных пылевидных частиц уплотняет зазоры отводит тепло от трущихся поверхностей.
В кислородном конвертере смазываются зубчатые передачи и зацепления подшипники узлы трения.
Из систем смазки наиболее прогрессивным является централизованная.
Трубопроводы системы смазки выполняются из стальных бесшовных труб соединенные между собой при помощи муфт и тройников. Подвод смазки к подвижным смазочным точкам осуществляется гибкими резиновыми рукавами высокого давления с металлической оплеткой. При заполнении системы смазкой вначале заполняют магистральные трубопроводы.
При эксплуатации кислородного конвертера следует строго придерживаться указания инструкций по эксплуатации. Несвоевременная смазка приводит к быстрому износу и повышенному расходу электроэнергии.
Перечень смазочных материалов используемых для кислородного конвертера приведен в таблице 5.1.
Таблица 5.1 Сведения по смазке
Централизованная жидкая
Ежесуточный контроль уровня масла в резервуаре станции и поступления к узлам трения.
Полная смена производится при несоответствии масла ГОСТу не реже одного раза в год.
Смазка жидкая заливная
Редуктор 24-80-8-53-1-2
Цилиндровое 38 ГОСТ 6411-76
Контроль и добавка еженедельно.
Полная замена через 1 год.
Индустриальное И 50-А ГОСТ 20799-75
Контроль уровня при замене футеровки конвертера.
Таблица 5.1 – Годовой график капитальных и текущих ремонтов оборудования конвертерного цеха № 2 на 2005 г.
Т – текущий ремонт час.
К – капитальный ремонт сутки.
Таблица 5.2 – Оперативный график проведения ремонтов оборудования ККЦ-2
ОРГАНИЗАЦИОННАЯ ЧАСТЬ
Задача ремонтного хозяйства на металлургическом комбинате сводится к обеспечению бесперебойной надежной и высокопроизводительной работы оборудования при минимальных затратах средств.
В состав ремонтного хозяйства входят цеха по ремонту металлургического оборудования (металлургического прокатного агломерационного) по изготовлению ремонтно-эксплуатационного металла и запасных частей (литейные кузнечные металлоконструкций механические и др.) склад запасных частей склад полуфабрикатов.
Кроме указанных выше цехов подчиненных отделу главного механика на комбинате имеются ремонтные цехи энергетического хозяйства ремонтно-строительный вальцетокарный цех и др. Они также входят в состав ремонтного хозяйства завода.
Ремонтами механического оборудования и изготовлением деталей и узлов занято более 26% общей численности промышленно-производствен-ного персонала черной металлургии.
Форма организации ремонтного хозяйства определяется тем в чьем ведении сосредоточены ремонтные средства и персонал. Поэтому принято различать децентрализованную централизованную и смешанную формы организации ремонтного хозяйства.
В настоящее время для большинства современных металлургических комбинатов характерна смешанная форма организации ремонтного хозяйства. Степень его внутризаводской централизации определяется удельным весом персонала состоящего в штатах ремонтных цехов в общей численности ремонтного персонала комбината.
На комбинате «Миттал Стил Кривой Рог» принята смешанная форма проведения ремонтов при котором текущие ремонты оборудования выполняются средствами цехов а капитальные и некоторые текущие ремонты с выполнением большим объемом работ – специализированными ремонтными цехами а также ремонтными рабочими других основных цехов. За главным механиком и его управлением сохраняется централизованное изготовление значительной части запасных деталей сменного оборудования существенно снижающее трудовые затраты на ремонты.
Условием централизованного изготовления деталей и узлов металлургических агрегатов является их постепенная унификация. При этом создается возможность организации ремонтных заводов для снабжения типовыми деталями и узлами предприятий района или области.
Большое внимание уделяется также разработке и внедрению передовой технологии специализации и кооперации в производстве ремонтно-эксплуатационного металла применению современных марок металлов и сплавов износостойких неметаллических материалов упрочняющей технологии индустриализации ремонтных работ.
Для обеспечения ухода за оборудованием выполнения мелких работ в периоды между плановыми ремонтами и для подготовки к таким ремонтам в производственных цехах предприятий существует сменный и дневной ремонтный персонал в необходимых количествах.
Полные капитальные капитальные ремонты основных производственных агрегатов комбината «Миттал Стил Кривой Рог» (доменные мартеновские печи конвертеры прокатные станы) в связи с большими объемами работ их специфичностью выполняются не только ремонтными службами самого комбината но и с привлечением специализированных ремонтных трестов и подрядных организаций (Днепродомнаремонт Укрметаллургремонт и др.).
Капитальный ремонт оборудования общего назначения (автомобилей экскаваторов и др.) а также металлорежущего и кузнечно-прессового (транспортабельного) рекомендуется проводить на районных или областных специализированных ремонтных заводах.
Задача ремонтного хозяйства цеха сводится к обеспечению бесперебойной работы оборудования при минимальных материальных и трудовых затратах.
На комбинате основные работы по производству ремонтного металла и выполнению ремонтов оборудования осуществляют цехи УГМ.
В состав УГМ входят:
- цехи производящие ремонтный металл – РМЦ 1 РМЦ 2 РМЦ 3 кузнечный цех производства изложниц ФСЛЦ ФЧЛЦ ЦМК;
- цехи выполняющие ремонты оборудования ЦРМО 1 2 3 4 5.
План производства в 2004 году по цехам УГМ выполнен в полном объеме.
В сравнении с 2003 годом вырос объем производства:
Стальное литье +49769 т.(421 %)
в т.ч.-корпусные пробки +23859 т.(+1606 %)
- мульды 3036 т.(+150 %)
- брони ГОКа 14863 т.(+410 %)
Изложницы+263869 т.(+377 %)
Поковка и штамповка+5576 т.(+173 %)
- шары+21057 т.(+4783 %)
- прочее+7783 т.(+787 %)
Снижен объем производства:
Чугунное литье-10500 т.(-67 %)
В т.ч. поддоны-40987 т.(-310 %)
Таблица 6.1 - Результаты работы цехов УГМ в 2004 году
Отклонение к 2003 г.
ЦМК: металлоконструк.
Мехообработка всего в т. ч.:
- мехообработка без поддонов;
- восстановление запчастей
Коэффициент сменности
Направленно деталей в тоннах направленного металла
Для выполнения производственной программы в цехах УГМ в 2004 году фактически работало 5608 при штате 5709 человек недоштат составил 101 человек.
Наличие производственных станочников на 01.01.2005 году 534 человека что ниже штата на 17 человек. Прирост численности производственных станочников к 2003 году +102 человека.
На выполнение плана производства мех. изделий работало 267 производственных станков.
Произведено мех. изделий 213546 тонн в т. ч.: новых изделий (запчастей) 49104 тонн что выше плана на 1374 тонн выше факта пошлого года на +778 тонн (+116 %).
Трудоемкость изготовления 1 тонны мех. изделий за (-) поддонов
н.ст.и. Против 2003 года отклонение составило – 88 и +185 н.ст.и.
Выполнено договоров в объеме 3757 тонн на сумму 834243 тыс. грн. В полном объеме выполнено 68 частично 52 договора.
2 Характеристика ремонтного хозяйства конвертерного цеха
В конвертерном цехе имеются ремонтные бригады которые закреплены за определенными участками оборудования. Закрепление осуществляется исходя из однотипности сложности металлургического оборудования и его территориального положения:
- бригада по ремонту напольного оборудования;
- бригада по ремонту кранов;
- бригада по ремонту автосмазки и гидравлики;
- бригада по ремонту вентиляционных устройств и кондиционеров;
- бригада по ремонту и сборке подшипниковых опор;
Ремонтное хозяйство цеха обеспечивает эксплуатацию уход и ремонт оборудования. В связи с круглосуточной работой цеха ремонтная служба подразделяется на дежурный и дневной ремонтный персонал.
Дневной ремонтный персонал занимается изготовлением запасных частей деталей сборочных единиц а также участвует в профилактических осмотрах оборудования.
Дежурный сменный персонал обеспечивает надзор и уход за оборудованием в течение смены и устраняет все поломки и неисправности.
Дежурный персонал распределяется таким образом что за каждым дежурным слесарем закрепляется определенная номенклатура оборудования за исправное состояние которого он несет личную ответственность на протяжении всей смены.
Вся работа в смене планируется и выполняется под руководством бригадира сменных слесарей.
Общее руководство механослужбой осуществляет заместитель начальника цеха по механическому оборудованию и механик цеха.
Во время проведения капитальных ремонтов цеховой ремонтный персонал закрепляется за бригадами специализированных цехов и организаций что позволит вести строгий контроль над проведением ремонта и оперативно решать проблемы возникающие в процессе ремонта.
3 Планирование ремонтов оборудования
Чтобы поддержать постоянную работоспособность оборудования за ним организуют системный уход и ремонт.
К мероприятиям обеспечивающим сохранность и долговечность машин относятся: межремонтное обслуживание – текущие ремонты и осмотры плановые ремонты.
Межремонтное обслуживание включает смазку и чистку механизмов затяжку клиньев болтов и другие мероприятия не связанные с заменой деталей.
Для небольших предупредительных ремонтов используют время технологических пауз то есть время когда машиной закончен очередной цикл и до следующего цикла временно не работает.
Такой ремонт включает:
а) поджатие гаек болтов и шпилек у подшипников всех механизмов;
б) осмотр и мелкий ремонт линий централизованной смазки;
в) проверка состояний швов сварных несущих металлоконструкций;
г) проверка состояния зубчатых и пальцевых муфт.
Для поддержания оборудования в работоспособном состоянии на металлургических предприятиях принята система ППР которая предотвращает нарастание износа оборудования внеплановые ремонты и аварии.
Состояние графиков ППР на год производится в начале предшествующего года работниками управления главного механика совместно с механиками цехов. Годовой план-график ремонтов увязывается с планом основного производства.
Годовой график составляется отдельно для каждого цеха. В нем предусматривают текущий и капитальный ремонты основного цехового оборудования.
Месячные графики ППР для каждого цеха составляют механики цехов. В них планируют сроки остановки агрегатов на ремонт и пуска их после проверки. Текущий ремонт оборудования является основным видом ремонта в системе ППР и характеризует выполнение работ по замене отдельных быстроизнашивающихся деталей и узлов выверкой отдельных узлов ревизией.
Текущий ремонт Т1. Производится бригадой по ремонту оборудования конверторного цеха (при необходимости привлекают ремонтный персонал ЦРМО №4).
Работы которые выполняют во время ремонта:
) очистка оборудования от пыли и грязи отработанной смазки;
) наружный осмотр и простукивание с целью выявления дефектов отдельных узлов;
) вскрытие окон люков для осмотра;
) регулировка зазоров в узлах оборудования;
) регулировка тормозов;
) проверка исправности тупиков;
) проверка подтяжка или замена уплотнений разъемов соединений;
) мелкий ремонт трубопроводов системы смазки;
) различные виды испытаний.
Текущий ремонт Т2. Предусматривает выполнение работ в объеме ремонта Т1 и дополнительно:
) частичная разборка узлов машин замена поврежденных и предельно изношенных узлов и деталей;
) центровка и балансировка быстровращающихся узлов;
) шлифовка или замена тормозных шкивов;
) ревизия подшипников качения с заменой поврежденных и предельно изношенных;
) замена деталей и узлов которые не смогут доработать до следующего ремонта Т1 или капитального ремонта;
) ремонт или замена аппаратуры системы смазки.
Периоды между текущими ремонтами машин устанавливают исходя из проверенных практикой сроков службы изнашиваемых узлов и деталей а периоды между капитальными ремонтами – исходя из срока службы крупных базовых деталей и узлов и соображений модернизации.
Капитальные ремонты машин и агрегатов ведут с привлечением цехов управление главного механика. Ремонты выполняемые во время капитальных ремонтов:
) полная разборка всех механизмов и узлов оборудования их очистка и промывка;
) уточнение ведомости дефектов с включением в него ранее неучтенных ремонтных работ;
) реставрация или ремонт замена изношенных механизмов металлоконструкций узлов деталей;
) работа по модернизации оборудования;
) сборка механизмов проведение необходимых испытаний агрегатов;
) замена пришедшего в негодность комплектующего оборудования;
) реставрация или замена ограждений экранов и переходов.
4 Организация выполнения ремонтных работ
Ремонту сталеплавильных агрегатов машин предшествует техническая и материальная подготовка. Цель материальной подготовки ремонта – заблаговременное приобретение и доставка на место ремонта материалов покупных изделий заготовок и запасных частей. Заявки на эти материалы и изделия составляют на основании норм и уточненной годовой программы работы ремонтного предприятия или годовых графиков ремонта разработанных предприятием эксплуатирующим машины.
Важнейшим условием рациональной организации выполнения ремонтных работ является тщательная подготовка к ремонту.
Подготовка к ремонту начинается с составления ведомости дефектов которые являются исходными для расчетов потребности в деталях материалах рабочей силе транспортных средствах и т.д. Затем цеховой ремонтной службой определяется возможность покрытия этой потребности средствами своего цеха. На изготовление и доставку остальных деталей и узлов составляются заявки-заказы и подаются в УГМ. В УГМ поступившие заказы подвергаются обработке: проверяется необходимость заказов определяется технологический маршрут заказов нормирование работ по выполнению заказа. На основании календарных планов графиков ремонтов определяется потребность в рабочих днях для выполнения текущего ремонта.
Таким образом на основе заявок и графика ППР УГМ составляет задание и другим ремонтным цехам на изготовление деталей узлов.
Вторым этапом подготовки к ремонту является своевременное изготовление и доставка необходимых для ремонта деталей узлов приспособлений. После выполнения двух первых этапов подготовки ремонта производится разработка технологии ремонта которая заключается в составлении сетевого графика ремонта. Эти графики составляются руководителем цеха производящего ремонт. При разработке технологии ремонта учитываются и внедряются все факторы сокращающие время работы. В разработанном графике технологии ремонта учитываются также необходимые меры техники безопасности.
В практике ремонтного хозяйства конвертерного цеха широкое применение получили методы поузловой замены деталей рассредоточения ремонтов. Особенно широко применяются эти методы при ремонте кранового оборудования и приводов во время ремонтов.
Большое влияние на увеличение межремонтного времени имеет контроль качества ремонта. Также эффективным средством является внедрение гарантийных ремонтов.
5 Расчет годового фонда заработной платы ремонтных рабочих участка
Бригада состоит из четырех человек. График работы – пятидневная рабочая неделя. Определим число часов одного рабочего в год:
Календарное количество дней366
Число часов работы одного работающего в год:
Средняя часовая тарифная ставка рабочих составляет:
Слесарь ремонтник6 разряд- 387 грнчас
Слесарь ремонтник5 разряд- 332 грнчас
Слесарь ремонтник4 разряд- 289 грнчас
Слесарь ремонтник3 разряд- 257 грнчас
Сумма заработной платы (6 разряда) при почасовой оплате по тарифу составляет:
Сумма премии за выполнение работ будет:
Основная заработная плата:
Оплата отпуска определяется следующим образом:
где 252 – число рабочих дней;
– число отпускных дней.
Общий годовой фонд заработной платы рабочего 6 разряда составит:
Оплата труда рабочих остальных квалификаций рассчитываются аналогично.
В данном дипломном проекте предлагается произвести модернизацию подшипниковой опоры кислородного конвертера. До предлагаемой модернизации подшипниковая опора имела более сложную конструкцию что приводило к снижению работоспособности и надежности конструкции имело место проскальзывание роликов линейных подшипников.
1 Анализ затрат на текущий ремонт и содержание основных средств
Для того чтобы определить затраты на производство стали составляется калькуляция себестоимости 1 тонны стали в которой последовательно производится расчет затрат на:
а) стоимость материалов деталей и запасных частей необходимых для проведения ремонтов;
б) энергетические затраты: электроэнергия вода пар топливо сжатый воздух (относятся к содержанию основных средств);
в) основная и дополнительная заработная плата занятых ремонтами и содержанием оборудования с начислениями;
г) стоимость услуг других цехов и организаций принимающих участие в ремонтах.
Стоимость инвентаря и инструментов не числящегося в основных средствах в эту статью не входит.
В таблице 7.1 приведены затраты по отчетной калькуляции 1 тонны стали за 2001 год.
Стоимость послеосмотровых ремонтов выполняемых силами ремонтной службы цеха в калькуляции себестоимости стали показывают по стоимости основных расходов (материалы и зарплата) без включений накладных расходов.
Если текущий ремонт выполняется ремонтными цехами то в калькуляции себестоимости стали включается себестоимость выполняемых работ без калькуляции. Плановые ремонты составляют после оформления ведомости дефектов а отчетные – после проведения ремонтов.
В калькуляцию стоимости стали включают данные отчетных калькуляций себестоимости ремонта. Если на проведение ремонта не составлены ведомости дефектов то разрабатывают ориентировочные сметы затрат применительно к отдельным пунктам статьи затрат: «текущий ремонт и содержание основных средств» [13].
Как видно из приведенных данных в структуре затраты по статье «содержание основных средств» удельный вес занимают затраты на материалы (2962%) торкетмассу (2251%) и огнеупоры (2995%). В затратах на ремонты 6962% составляют затраты на огнеупоры. Значительный удельный вес по этой статье занимают услуги других цехов (1904%).
Таблица 7.1 – Состав и структура затрат
Структура в процентном соотношении
) Содержание основных средств
г) масса факельного торкетирования
д) масса набивки ковшей
в) услуги подрядчиков
Эти показатели характеризуют качество ремонта ремонтной службы цеха и используются при разработке мероприятий по снижению затрат на ремонт.
2 Экономическая эффективность от внедрения проекта
В результате усовершенствования конструкции подшипниковой опоры конвертера уменьшится время его простоев. Увеличится производительность кроме того в результате усовершенствования конструктивных элементов трех конвертеров увеличится период между капитальными ремонтами.
Экономический эффект от увеличения межремонтного периода достигается в результате годовой экономии на ремонтах Эг. и условно постоянных расходов Эу [14].
Годовая экономия затрат на ремонтах достигается в результате уменьшения числа ремонтов (Nк) можно выразить как отношение календарного фонда времени работы конвертера к длительности периода между капитальными ремонтами М и продолжительностью одного капитального ремонта Т уменьшения числа капитальных ремонтов равно разности между числом ремонтов до и после межремонтного периода:
где Мс=365 – длительность периода между капитальными ремонтами до модернизации суток;
Мн=430 – длительность периода между капитальными ремонтами после модернизации суток;
Тс=2 и Тн=2 продолжительность капитального ремонта до и после модернизации соответственно суток.
Затраты на капитальные ремонты Зк – снижаются пропорционально уменьшению числа ремонтов в год:
где Зк=22500 – затраты на капитальный ремонт грн.
Однако при определении числа текущих ремонтов в расчете на год необходимо исходить из того что во время капитального ремонта выполняется весь объем работ по текущему ремонту. Следовательно число текущих ремонтов в расчете на год сократится на единицу и будет равно:
где mн=40 и mc=30 – продолжительность периода между текущими ремонтами после модернизации и до нее соответственно суток;
tн=tc=1 – продолжительность текущего ремонта после модернизации и до нее соответственно (осталась без изменений) суток.
Уменьшение числа текущих ремонтов равно:
Затраты на текущие ремонты Зт – снижаются пропорционально уменьшению числа ремонтов в год:
При увеличении периодов между капитальными и текущими ремонтами годовая экономия затрат на ремонтах Эг будет равна:
Годовую экономию условно постоянных расходов Эу определяем по формуле:
гдеВо=1008778 – годовой объем стали одного конвертера тонн;
Ну=1884 – условно постоянные расходы грнт;
Кп – коэффициент прироста выпуска продукции.
Определим коэффициент прироста выпуска продукции:
где Рс=Рн=2764 – среднесуточная производительность до и после модернизации соответственно (осталась без изменений) тонн.
Тогда экономия условно постоянных расходов будет равна:
Общий экономический эффект будет равен:
Таблица 7.1 - Стоимость ремонтов до модернизации
Текущий рем. конвертера
Текущий рем. в целом по цеху
Таблица 7.2 - Стоимость ремонтов после модернизации
Таблица 7.3 – Эффективность проектных решений
Наименование показателя
Время работы сутокгод
Производительность тсутки
Годовая производительность т
Высвободившийся в результате модернизации конвертера экономические ресурсы возможно направить на дальнейшее улучшение эксплуатационно-технических характеристик оборудования улучшение медико-социальных условий труда.
Охрана труда – это система мероприятий обеспечивающих безопасные для здоровья и жизни трудящихся условия выполнения работы. Охрана труда включает в себя законодательные мероприятия технику безопасности и производственную санитарию.
В сталеплавильном производстве достаточно многочисленны и многообразны опасные и вредные производственные факторы.
Охрана жизни и здоровья трудящихся гарантируется Конституцией Украины Законом Украины об «Охране труда» и другими законодательными документами.
КЗОТ Украины во главе 11 «Охраны труда» требует чтобы при проектировании производственных объектов разработке новых технологий и средств производства средств коллективной и индивидуальной защиты работающих учитывались требования по охране труда ст. 154 чтобы на всех предприятиях учреждениях и организациях создавались безопасные и не вредные условия труда на работах связанных с пребыванием в условиях ненормальной температуры в сырости. Работающим бесплатно выдается спецодежда предохранительные приспособления моющие средства а также средства индивидуальной защиты (ст. 163).
Строительные нормы и правила (СниП) определяют требования к зданиям и помещениям производственных предприятий и их освещению вентиляции отоплению благоустройству территории [15].
Требования по пожарной профилактике предприятий определены Законом Украины «О пожарной безопасности».
Правила устройств электроустановок (ПУЭ) усиленно регламентирует все вопросы сооружения и приемки в эксплуатацию различных электростанций подстанций сетей проводок электрооборудования по использования электроэнергии.
В настоящем проекте рассмотрены основные вредности и опасности имеющие место в конвертерном цехе № 2 предложены мероприятия по их устранению описаны средства индивидуальной защиты трудящихся пожарная профилактика с расчетом общего количества первичных средств пожаротушения.
1 Характеристика строительной площадки
При проектировании промышленных предприятий учитываются требования технологии транспорта экономии а также условия обеспечивающие безопасный труд. Площадка предприятия должна быть хорошо освещенной ровной с некоторым уклоном обеспечивающим отток ливневых и сточных вод. По отношению к жилому району располагаются с подветренной стороны а цеха с вредными выделениями располагаются с подветренной стороны по отношению к другим цехам отвалы и свалки располагаются с подветренной стороны по отношению к предприятию. Между предприятиями и жилыми районами предусматривается защитная зона ширина которой регулируется в зависимости от санитарной потребности производства. Санитарно-защитная зона и территория предприятия определяется лиственными породами деревьев.
Строительная площадка цеха удовлетворяет санитарным требованиям в отношении солнечного освещения естественного проветривания и отвода сточных и поверхностных вод.
1.1 Бытовые и вспомогательные помещения ККЦ-2
В состав бытовых и вспомогательных помещений входят: гардеробные умывальные душевые уборные курительные комнаты для приема пищи обогревания рабочих.
Гардеробные предназначены для хранения личной одежды и спецодежды.
Умывальные размещены в отдельном помещении смежным с гардеробным. Число кранов для умывальных назначены из расчета один кран на двадцать человек.
Душевые размещены в смежных с гардеробными помещениях. Число душевых сеток определено из расчета одна сетка на три человека.
Помещения для хранения одежды объединены с душевыми и гардеробными в так называемый умывальный блок.
Уборные размещены в здании цеха на небольшом расстоянии от рабочих мест (не более 75 метров) и на территории цеха на расстоянии около 150 метров. Пол в туалетах умывальных душевых водонепромокаемый с уклоном в сточную яму. Стены покрыты влагоустойчивым материалом на высоту 15 метров.
Для раздачи питьевой воды установлены фонтанчики а также автоматы с газированной подсоленной водой.
В цехе предусмотрены столовые буфет комната для раздачи пищи. Пункты питания рассчитаны из расчета одного посадочного места на четыре человека.
На территории цеха имеется здравпункт.
2 Основные вредные и опасные факторы производственного процесса в кислородно-конвертерном цехе № 2
Условия труда в цехе характеризуются наличием вредных факторов таких как: запыленность загазованность теплоизлучение шум вибрации резкое контрастное освещение.
В цехе основные и вспомогательные технологические операции сопровождаются выделением значительного количества пыли; как показали исследования в основном из окислов железа с примесью других веществ; окиси кремния марганца и в отдельных случаях – легирующих элементов.
В воздушном пространстве цеха содержится графитная пыль источником которой является открытые чугуновозные ковши перевозящие чугун из миксерного отделения в конвертерное. Содержание различных элементов в пыли не всегда постоянно по химическому составу и зависит от вида технологической операции проводимой технологическим персоналом.
Размер частиц пыли в цехе колеблется в широких пределах. Крупные фракции быстро оседают а мелкие длительное время находятся в воздухе. Состав пыли в воздухе отличается по химическому составу в связи с выплавкой различных марок стали.
Пыль преимущественно фиброгенного действия металлическая с содержанием Mn до 3% - нормативное значение ПДК.
Фактическая величина равна 62 млгм³.
Вредные химические вещества мгм³:
I класс опасности – фактическая величина 02838.
II класс опасности – нормативное значение ПДК = 05; фактическое менее 1.
IV класс опасности – нормативное значение ПДК = 20; фактическая 60.
Другим фактором характеризующим санитарно-гигиенические условия труда является загазованность. Наличие различных газов в атмосфере цеха обусловлено нарушением технологического режима неисправностью и несовершенством оборудования. Одним из основных источников выделения вредных газов является конвертер.
Состав газа в атмосфере конвертерного отделения зависит от типа выплавляющейся марки стали и характеризуется следующими компонентами: углекислый газ CO2 окись углерода CO двуокись серы SO2 окись азота NO. Дым выбрасываемый трубой состоит из 10 – 12 % CO2 12 – 13 % O2 75 – 78 % N2.
В процессе выплавки стали выделяется большое количества тепла излучаемое расплавленным жидким металлом. Так в производственном помещении конвертерного отделения тепловые нагрузки в среднем составляют 70 – 80 ккалм²ч и более а на учаcтке рабочих зон конвертеров удельная тепловая нагрузка равна 250 ккалм²ч и более. Наличие многочисленных источников теплового излучения требует соблюдения специальных мер по создании на этих участках нормальных санитарно-гигиенических условий.
Некоторые технологические операции сталеплавильного производства сопровождается образованию шумов низкой и высокой частоты. Громкими шумами уровень которых превышает допустимые санитарно-гигиенические нормы сопровождается продувка стали в конвертере работа вибропитателей конвертерного тракта.
Существенное значение имеют метеорологические условия в цехе. Метеоусловия определяются температурой влажностью и подвижностью воздуха. Температура на горячих участках значительно превышает температуру наружного воздуха. Наличие участков с высокой и низкой влажностью воздуха отрицательно влияет на самочувствие человека.
Эксплуатация электромашин требует обязательного применения средств и мер защиты от поражения электрическим током.
Безопасен переменный ток (50 – 60 Гц) силой 15 мА и постоянный ток до 25 мА. Эти значения и определяют порог не отпускающего тока. Порог не превышает 15 мА. Ток силой 100 мА – смертельный.
Производственные помещения по признаку электроопасности с учетом состояния изоляции проводов и возможности перехода напряжения на нетоковедущие части подразделяются на три категории.
Конвертерный цех в этом отношении относится к особоопасным. В нем используется много электрооборудования. Производственные помещения характеризуются повышенной температурой воздуха значительным содержанием в нем электропроводящей пыли (плавильной шлаковой графитной). Полы обладаю токопроводящими свойствами имеется постоянная опасность одновременного соприкосновения человека с металлоконструкциями и частями электроустановок.
3 Мероприятия по уменьшению вредных и опасных факторов в кислородно-конвертерном цехе № 2
Борьба с пылью в конвертерном цехе ведется во многих направлениях. Разработаны средства подавления пыли в местах ее образования отсева от сыпучих материалов мелких фракций и пыли снижения потерь материалов при транспортировке хранении на складах на погрузке и выгрузке герметизации перевалочных углов.
Обеспыливание газов производится сухим мокрым электростатическим комбинированными способами. Сухим способом очищаются аспирационные выбросы в пылеосадительных камерах и циклонах. Действие этих аппаратов основано на принципе осаждения частиц пыли (120 мм и более) под действием сил тяжести центробежных и инерционных сил.
Из пылесборников (бункеров) осадочных камер и циклонов пыль периодически выгружают и вывозят. Для транспортировки используют грузовые машины с закрытым кузовом типа цементовоза.
Сухую очистку газов и аспирационных выбросов производят также с помощью фильтров. Применяют пылеочистные фильтры трех видов: хлопчатобумажные пористые или насыпные из гравия или мелкого кокса и сетчатые.
Мокрое обеспыливание газов осуществляют в скрубберах – промывателях различной конструкции действующих по принципу противотока воды и загрязненного воздуха.
Электростатическое обеспыливание позволяет выполнить тонкую очистку газов и аспирационного воздуха. Электрофильтр работает на постоянном токе высокого напряжения (60 – 100 кВт).
Для того чтобы защитить в конвертерном цехе людей от тепловых воздействий рабочие места удалены из зон интенсивного инфракрасного тепла сооружены технические устройства для уменьшения теплорадиации и применяют средства индивидуальной защиты работающих. В этом направлении совершенствуется и технология. Освоена например бесстопорная разливка стали с шиберным затвором.
Отдалить человека от зоны облучения позволяет механизация и автоматизация производственных процессов создание дистанционного управления агрегатами применения телевидения для наблюдения за ходом работ. В частности из опасной зоны выведены пульты управления конвертером и сталевозной тележкой.
Широко применяются установки искусственного микроклимата – кондиционеры которые монтируют в дистрибуторных диспетчерских конторских и других рабочих помещениях в комнатах кратковременного отдыха.
Необходимым условием высокопроизводительного и безопасного труда является рациональное освещение рабочих помещений и территорий цеха. Здорового человека в его деятельности ориентируют в первую очередь глаза.
С учетом воздействий окружающей среды применяют светильники в защитном исполнении уплотненные пылезащитные влагонепроницаемые переносные с защищающей сеткой и другие.
Световые поверхности светильников регулярно (не реже раз в год) очищают от грязи пыли и копоти. Несоблюдение этого требования приводит к снижению видимости на рабочих местах и к перерасходу электроэнергии на освещение цеха. Установку замену светильников замену перегоревших ламп производит электрик при включенном напряжении. Перегоревшие люминесцентные лампы содержащие ртуть хранят в отдельном помещении и вывозят для уничтожения в положенном месте. Стены колоны и фундаменты агрегатов часто белят для улучшения их отражающей способности.
Для устранения вредной вибрации на обслуживающий персонал в конструкции проектированного конвертера предусмотрены резиновые компенсаторы – демпферы колебания.
Опасные места проемы зоны работы механического оборудования ограничены. Все вращающие и движущие части механизмов имеют кожухи.
Токоведущие части конвертера заключены в кожухи. Токопроводящие части кабели защищены металлическими трубами или гибким рукавом [16].
3.1 Расчет искусственного освещения в цехе
Площадь цеха 192х24 м²; высота ферменных стояков над полом 21м; расположены стояки через каждые 12 м по длине цеха (рис. 8.1). Нормативная освещенность в плоскости пола Еп = 60 лк; минимально допустимая высота подвеса светильников 43 м; максимально допустимая высота подвеса определяется высотой цеха с учетом крепления светильника и не должна быть более 20 м; коэффициент неравномерности освещения z = 098; коэффициент запаса k = 15. Мощность лампы 1500 Вт для сети напряжением 220 В. Коэффициент использования осветительной установки =05.
Наиболее выгодное отношение расстояния между лампами к высоте их над рабочей поверхностью для светильников данного типа равно 09. При максимальной высоте подвеса 20 м наиболее выгодное для этой высоты расстояние между светильниками будет:
Определяем площадь S освещаемую одним светильником:
где Fл – световой поток одной лампы мощностью 1500 Вт.
При условии равенства расстояния между светильниками по длине и ширине цеха достигается максимальная равномерность освещения. Это расстояние определяется из найденной площади освещаемой одним светильником:
Учитывая размеры и строительные особенности цеха устанавливаем размещение светильников по длине помещения цеха устанавливаем размещение светильников по длине через каждые 12 метров и по ширине – через 12 метров. Расстояние от боковых стен до светильников будет 6 метров от торцовых стен тоже 6 метров.
Выбранные расстояния между светильниками определяют их число: по ширине 2в ряд по длине цеха 16в ряд т.е. всего 32 светильника. Схема размещения и подвески светильников приведена на рисунке 8.1.
Общая мощность осветительной установки цеха составит:
Удельная мощность приходящаяся на 1 м² освещаемой площади равна:
Рисунок 8.1 Схема размещения светильников в конвертерном цехе
4 Средства индивидуальной защиты
Исходя из основных производственных вредностей и опасностей в конвертерном отделении рабочие обеспечиваются средствами индивидуальной защиты.
Для защиты органов дыхания от вредных веществ в виде газов паров пыли применяются фильтрующие приборы – распираторы.
Для защиты тела применяется специальная одежда – комбинезон брюки куртка из хлопчатобумажной ткани и шинельного сукна. Спецодежда соответствует стандартам. Периодичность выдачи спецодежды показана в таблице 8.1.
Для защиты ног от механических повреждений используют как индивидуальное средство защиты обувь – ботинки сапоги.
Для работы с грузовыми приспособлениями а также для выполнения производственных заданий для защиты рук предусмотрено применение рукавиц из суровой хлопчатобумажной ткани.
Для защиты головы от механических повреждений применяют каски (текстолитовые полиэтиленовые винилопластовые) с амортизаторами.
Таблица 8.1 Периодичность выдачи специальной одежды в ККЦ-2
5 Пожарная безопасность в конвертерном цехе № 2
Все производственные и вспомогательные здания сооружения и составы сталеплавильных цехов должны отвечать межгосударственному стандарту ГОСТ 12.1.004-91 "Пожарная безопасность. Общие требования" Правилам пожарной безопасности для предприятий черной металлургии (ППБО-136-86) и быть обеспечены первичными средствами пожаротушения.
По степени пожароопасности производство конвертерного цеха относится к категории «Г» - пожароопасное.
Наиболее вероятными очагами возникновения пожара являются токоведущие кабеля посты дистанционного управления кабины электроустановок смазочные материалы и склад смазочных материалов. Во избежания возникновения пожара хранение и складирование воспламеняющихся материалов производится в специально отведенных местах.
Все помещения где нет постоянного обслуживания оборудованы пожарной сигнализацией. Помимо этого в производственных помещениях оборудованы пожарные пункты окрашенные в красный цвет с надписью «Пожарный пункт».
Пожарные щиты устанавливаются из расчета один щит на площадь 500м. В комплект щита входит: три огнетушителя ящик с песком (объемом не менее 01 м) покрывало из несгорающего теплоизолирующего материала размером 2м х 2м три крюка три лопаты два топора.
Здание цеха обеспечивается огнетушителями из расчета один огнетушитель на площадь цеха не менее 200 м а также баком с водой (объемом не менее 02 м) ведром (объемом не менее 0008 м) ящиком с песком. На каждый пожароопасный агрегат - два огнетушителя. Расстояние от возможного очага пожара до места расположения огнетушителя не должно превышать 20 метров - для административно-бытовых помещений; 40 метров - для помещений категории Г; 70 метров - для помещений категории Д. Применены огнетушители типов ОВП ОВИ ОУ.
Производственное и вспомогательное здания предлагается оборудовать устройством для молниезащиты.
Здание цеха оснащено пожарной сигнализацией с выводом информации на центральный пульт ГПУ.
В случае возникновения пожара происходит эвакуация людей согласно плана эвакуации.
ОХРАНА ОКРУЖАЮЩЕЙ СРЕДЫ
Выбросы промышленных предприятий энергетических систем транспорта в атмосферу водоемы и недра достигли таких размеров что в ряде районов земного шара уровни загрязнения значительно превышает допустимые санитарные нормы. Это приводит особенно среди городского населения к увеличению количества людей заболевающих хроническим бронхитом астмой ишемией раком.
Рациональное решение экологических проблем возможно лишь при оптимальном взаимодействии природы и общества обеспечивающем с одной стороны дальнейшее развитие общества с другой - сохранение и поддержание восстановительных сил в природе что достижимо лишь при проведении широкого комплекса практических мероприятий и научных исследований по охране окружающей среды. Необходимость охраны окружающей среды отражена в Основном Законе нашего государства. В Конституции Украины записано что в интересах настоящего и будущих поколений в Украине принимаются необходимые меры для охраны и научно-обоснованного рационального использования земли и ее недр водных ресурсов растительного и животного мира для сохранения в чистоте воздуха и воды обеспечения воспроизводства природных богатств и улучшения окружающей человека среды.
Однако в промышленности нерешенными проблемами пока остаются эффективность очистки технологических и вентиляционных сбросов от газовых паровых и пылевых примесей. Современная технология охраны окружающей среды еще не базируется на широком применении безотходных производств. До настоящего времени все еще применяется способ снижения концентраций примесей путем их рассеивания в атмосфере.
Предприятия черной металлургии являются одним их основных источников загрязнения воздушного бассейна. На их долю приходится около 20 - 30% общих загрязнений атмосферы промышленностью.
За 2004 год на строительстве природоохранных объектов комбината освоено 245 млн. гривен из которых за счет льготных средств – 115 млн. гривен.
Льготные средства были использованы комбинатом на строительство наиболее капиталоемких экологических объектов:
строительство аспирационной установки миксерных отделений № 1 № 2 конверторного цеха что позволит уменьшить выбросы пыли в атмосферу на 896 тонн в год (по проекту);
аспирация пылеприемных бункеров огнеупорно-известкового цеха что позволит повысить эффективность сбора пыли уловленной газоочистками вращающихся печей ВП № 1-5;
строительство ливневого коллектора конверторного цеха;
реконструкция хвостового хранилища в районе села Миролюбова. Введение в эксплуатации этого объекта в 2006 году что даст возможность уменьшить загрязнение земель отходами обогащения.
января 2005 года был подписан приказ № 3 «О состоянии экологии и дополнительных мер по улучшению природоохранной работы на комбинате в 2005 году». Включенные в него мероприятия охватывают весь комбинат в целом и направлены на снижение наносимого им ущерба природе улучшение условий труда и производственного быта трудящихся комбината а также на благоустройство комбината. Еженедельно проводятся комиссионно-выездные совещания.
В 2004 году комбинат занял первое место среди промышленных предприятий города по содержанию зеленых ограждений.
С целью улучшения благоустройства и озеленения территории комбината на 2005 год следующие мероприятия:
программа ландшафтной реконструкции участков на территории комбината;
мероприятия по благоустройству цехов территории коксохимического металлургического производства и шахтоуправления;
график агротехнических работ по уходу за зелеными насаждениями;
план-график посадки зеленых насаждений на территории комбината;
график ремонта автомобильных дорог и пешеходных тротуаров;
график капитальных и текущих ремонтов бытовых помещений столовых здравпунктов комбината «Миттал Стил Кривой Рог».
Установлен каждый четверг недели днем благоустройства организованы работы по благоустройству и озеленению территории в течении рабочего дня.
Запланированы работы по озеленению закрепленной территории: полос газонов дикорастущих трав обрез и побелка деревьев кустарников вести работы по уходу за цветочными клумбами.
Точных расчетов конечного эффекта от выполнения данных программ пока не существует но очевидно что экология Кривого Рога при этом значительно улучшится.
Продление экономического эксперимента будет способствовать успешной реализации налагаемых комбинатом «Миттал Стил Кривой Рог» природоохранных мероприятий.
В ККЦ – 2 при эксплуатации конвертеров возникают следующие неполадки. Практика эксплуатации конвертеров показала что температура корпуса достигает 300°С. Термические напряжения возникающие в средней части корпуса вызывают значительную несоосность и перекосы осей до 1-2° которые приводят к быстрому разрушению цилиндрических роликовых подшипников. Конвертер работает в тяжелых условиях механизм поворота и опорные узлы подвержены действию больших статических и динамических нагрузок корпус и опорное кольцо подвержены высокой и неравномерной температуре нагрева возникают большие температурные напряжения в элементах металлоконструкций привода. Также отмечена недостаточная надежность плавающей подшипниковой опоры конвертера из-за проскальзывания роликов линейных подшипников сложности конструкции и неудобству обслуживания. Не достаточная надежность работы навесных редукторов из-за частой поломки средних зубчатых колес вследствие больших нагрузок. Большие остаточные напряжения возникающие в процессе сварки опорного кольца что ведет к снижению надежности и долговечности.
Данным проектом предлагается изменить конструкцию подшипниковой опоры конвертера которая позволит устранить проскальзывание роликов линейного подшипника повысит простоту эксплуатации подшипниковой опоры а также предотвратит поворот конвертера вокруг вертикальной оси.
Ожидаемый экономический эффект при внедрении данных технологических новшеств составит:
- в результате экономии на ремонтах 15630 грн.;
- в результате экономии условно постоянных расходов 1330376 грн.;
- общий экономический эффект 148668 грн.
Как показывают расчеты представленные в дипломной работе внедрения увеличивают надежность и долговечность оборудования. Расчеты также показали что напряжения в роликах подшипниковой опоры и в сепараторах значительно меньше допустимых напряжений. Из этого можно сделать вывод что эти детали можно выполнить из более дешевых материалов. Повышают эффективность работы цеха за счет снижения времени технологических простоев. В тоже время внедрения проекта не требует значительных капитальных затрат и ввода в действие нового технологического оборудования.
Иванченко Ф.К. Павленко Б.А. Механическое оборудование сталеплавильных цехов. Изд. «Металлургия» 1979.
Целиков А.И. Полухина П.И. Гребенник В.Н. Машины и агрегаты металлургических заводов. 2-ое изд. перераб. и доп. – М.: Металлургия 1988. 432 с.
Баптизманский В.И. Охотский В.Б. Конвертерные процессы производства стали. Теория технология конструкции агрегатов. – Киев; Донецк: Высшая школа. 1984. – 343 с.
Авторское свидетельство №1541275 Кл. С 21 С542 550.
Авторское свидетельство №1560563 Кл. С 21 С542.
Авторское свидетельство №1696491 Кл. С 21 С550.
Анурьев В.И. Справочник конструктора-машиностроителя: В 3 т. Т. 1.– 5-е изд. перераб. и доп. – М.: Машиностроение. 1979. – 728 с.
Якушев А.М. Проектирование сталеплавильных и доменных цехов. – М.: Металлургия 1984. – 216 с.
Касаткин М.Н. Ремонт и монтаж металлургического оборудования. – М.: Металлургия 1970.
Инструкция по эксплуатации кислородного конвертера вместимостью 160 т.
Прыткин Д.П. Надежность ремонт и монтаж металлургического оборудования: Учебник для вузов. М.: Металлургия 1985. 368 с.
Зайцев Х.П. Хоменко М.А. Экономика ремонтного хозяйства металлургических заводов. Техника 1974.
Брюханенко Б.А. Иванов И.Н. Макаров Н.В. Технико-экономические расчеты по организации и планированию предприятий черной металлургии. – М.: Металлургия 1974.
Санитарные нормы СН-245-71 СниП IIМ3СниП II.М2-72 СниП II.М5-70.
Перельман С.Г. Зайков А.С. Вовк И.Н. Безопасность труда в конвертерном цехе. Высшая школа 1977.