Изготовление тормозного шкива




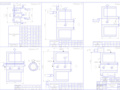
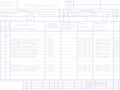
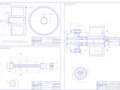
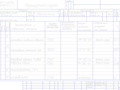
- Добавлен: 25.10.2022
- Размер: 643 KB
- Закачек: 1
Описание
Состав проекта
![]() |
![]() ![]() |
![]() ![]() |
![]() ![]() |
![]() ![]() |
![]() ![]() |
![]() |
![]() ![]() ![]() ![]() |
![]() ![]() ![]() ![]() |
![]() ![]() ![]() ![]() |
![]() ![]() ![]() ![]() |
![]() ![]() ![]() ![]() |
![]() ![]() ![]() |
![]() |
Дополнительная информация
Маршруткарта (2).dwg

растачивание посадочного отверстия
протягивание шпоночного паза
термообработка Т.В.Ч.
1 лист.dwg

Сталь 55Л ГОСТ 977-88
Термообработка поверхности торможения
закалка Т.В.Ч. на 2-3 мм. до твердости HRC 38-42
Cталь 55Л ГОСТ 977-88
колибр пробка.dwg

2 лист.dwg

Маршруткарта.dwg

черновое обтачивание
растачивание внутренней стенки
подрезка торца обода
ВОТ ЭТО КУРСАЧ1234.doc
Выбор заготовки и материала тормозного шкива5
Технические требования5
Расчет припусков на обработку тормозного шкива8
Расчет режимов резания13
Расчет технической нормы времени35
Расчет измерительного инструмента52
Описание инструмента53
Список используемой литературы54
Интенсификация производства в подъемно-транспортном машиностроении возможна лишь в направлении совершенствования форм и методов серийного производства.
Объем годового выпуска стандартизированных и нормализированных изделий возрастает и достигает таких размеров при которых оказывается целесообразным организовать их специализированное производство в отдельных цехах или даже на специализированных заводах.
Совершенствованию производственных процессов и повышению их эффективности способствует проведение работ по повышению технологичности конструкций.
Прогрессивным направлением в развитии технологии в подъемно-транспортном машиностроении является повышение качества заготовок для деталей машин повышение технического уровня производства в заготовительных цехах.
Повышение эффективности операций механической обработки связаны с разработкой высокопроизводительных схем станочных операций построенных по принципу концентрации и предусматривающих использование технологической оснастки.
В подъемно-транспортном машиностроении под руководством ВНИИПТМАШа проводится работа по стандартизации нормализации и унификации конструкций. Результатом нормализованного направления в конструировании машин являлась сложившаяся на заводах подъемно-транспортного машиностроения структура механически обрабатываемых деталей. Такая структура деталей способствует проведению работ и организации высокоэффективных производств в масштабе отрасли.
Назначение тормозного шкива
Тормозные шкивы служат для передачи момента торможения на валы механизмов. В зависимости от конкретного назначении конструкция их различна но основные элементы остаются неизменными и определяют собой технологические задачи изготовления.
Для установки на валу шкив имеет цилиндрическое или коническое посадочное отверстие со шпоночным пазом. Тормозные шкивы присоединяют к зубчатым муфтамустанавливают на валах без муфт или соединяют с пальцевыми муфтами для чего в торцевых поверхностях предусмотрены выточки и несколько отверстий расположенных по окружности.
Для процесса торможения очень важна уравновешенность шкива. Поэтому с целью устранения несбалансированных масс шкивы обрабатывают полностью т. е. даже нерабочие поверхности (внутреннюю поверхность обода наружную поверхность ступицы и переходную внутреннюю торцовую поверхность). Снизить трудоемкость обработки можно при условии резкого повышения качества литья.
Выбор заготовки и материала тормозного шкива
Тормозные шкивы изготовляют преимущественно из стали 55ЛН (ГОСТ 977 -65)литьем в песчаную форму без отверстия. Вся отливка размещается в нижней опоке вниз полостью которая образуется одним кольцевым стержнем. Плоскость разъема формы совпадает с торцовой плоскостью шкива. Стальная отливка имеет массивную прибыль и ее на ряде заводов удаляют на фрезерном станке в заготовительном цехе.
Технические требования
Наружную поверхность тормозного шкива для повышения срока службы подвергают поверхностной закалке на глубину 3—5 мм до твердости HRC 38 52 и шлифуют с обеспечением шероховатости поверхности 125 мкм при обработке по 11-му квалитету. Посадочное отверстие выполняют по 7-му квалитету при чистоте поверхности 6-го класса. Должна быть соблюдена соосность наружной поверхности с посадочным отверстием (радиальное биение не более 005 мм) торцовое биение шкива не более 0.02 мм на 100 мм радиуса.
Отверстия в шкивах для соединения с зубчатыми муфтами на чистых болтах обрабатывают по 7—9-му квалитетам при высокой точности расположения; отверстия для соединения с пальцевыми муфтами обрабатывают по 11-му квалитету.
Размерный ряд тормозных шкивов определяется наружным диаметром (200 —300 —400 —500 —600 и 800 мм) а также диаметром расположения отверстий для соединения с зубчатой или пальцевой муфтами.
План обработки тормозных шкивов остается неизменным для всех типоразмеров и в любом производстве.Изменяются лишь условия выполнения операций и их трудоемкость.
В крупносерийном производстве шкивы тормозные диаметром 200—800 мм обрабатывают по следующему технологическому процессу.
Технологический маршрут включает следующие основные операции:
Операция 05Токарная —станок 1П365
Предварительная обработка с открытой стороны при установке в четырехкулачковом патроне с выверкой и закреплением и зоне дна шкива. Отрезаются остатки прибыли и подрезается торец обтачивается обод растачивается внутренняя стенка обода подрезается дно камеры и обтачивается ступица. В некоторых случаях на заводах считают целесообразным удалить прибыль в отдельной операции предшествующей точению выполняемой на вертикально-фрезерном станке.[см.лист 190205.К10.071.02.00]
Операции 10Токарная —станок 1П365
Обработка оставшегося участка обода подрезка наружного торца дна обработка отверстия и выточек. Установка в трехкулачковом патроне. Револьверная наладка уплотняется за счет одновременного выполнения переходов обтачивания обода. [см.лист 190205.К10.071.02.00]
Операция 15Токарная —станок 1П365
Окончательная обработка посадочного отверстия. Выполняется по-разному в зависимости oт его формы и размера шкива. Цилиндрическое отверстие диаметром до 40—45 мм обрабатывается протягиванием при малой трудоемкости (Тшт —2—3 мин).
Цилиндрическое отверстие большего размера окончательно обрабатываеся в составе револьверной операции путем растачивания н двухкратного развертывания.Операция требует 15— 30 миншт в зависимости от размера отверстия.
Операция 20Протяжная — станок 7Б55У
Протягивание шпоночного паза на горизонтально-протяжном станке при установке на адаптере. [см.лист 190205.К10.071.02.00]
Операция 25Токарная —станок 1П365
Окончательная обработка торцовой и наружной поверхностей обода по 4-му классу точности с припуском под последующее шлифование. Деталь устанавливается на цилиндрической оправке со шпонкой.
По выполнении операции контролируется биение торца относительно оси отверстия; допускаемое отклонение 0025 мм на радиусе 100 мм. [см.лист 190205.К10.071.02.00]
Операция 30Термическая обработка
Закалка т. в. ч. на глубину 2—3 мм твердость после отпуска HRC 38—42.Поверхностная закалка тормозного шкива диаметром 200 выполняется при следующих условиях.
Шкив устанавливается на цилиндрическую шпиндельную оправку и приводится во вращение. Индуктор располагается по образующей (с небольшим yглом) на расстоянии 15 мм от поверхности обода. Тсмператуpa закалки 900-960о С температура охлаждающей воды 15—20о С. деталь закаливается на одном обороте шкива; скорость вращения детали 6—8 ммсек. После закалки тормозные шкивы подвергаются отпуску в электропечи при температуре 480—520о С в течение 2—25 ч. Твердость контролируется в четырех местах.
Операция 35Шлифовальная –обработка наружной поверхности по 7-му классу чистоты с обеспечением соосности с посадочным отверстием. Деталь устанавливается на центровой оправке. [см.лист 190205.К10.071.02.00]
Расчет припусков на обработку тормозного шкива
Рассчитаем припуски на обработку и промежуточные предельные размеры на поверхность диаметр -200h7.
Номинальный размер диаметр 200-0.04 мм.
На остальные обрабатываемые поверхности назначить припуски и допуски по таблицам ГОСТ 1855-55.
Заготовка - стальная фасонная отливка по ГОСТ 2009-55 шестому классу точности
Масса заготовки - 13 кг
Технологический маршрут обработки поверхности диаметр 200h7 состоит из обтачивания лезвийным инструментом: чернового и чистового и шлифования абразивным кругом. Обработка производится на токарно-револьверном станке 1П365 и круглошлифовальном станке ЗТ160 при закреплении на центровой оправке.
Технологический маршрут обработки записуем в расчетную таблицу 1.1 там же записываем соответствующие заготовке и каждому технологическому переходу значения элементов припуска.
Таблица 1.1 Припуски и предельные размеры по технологическим переходам на обработку поверхности
Технологические переходы обработки поверхности
Элементы припуска мкм
Расчетный припуск 2Zmin
Припуском на обработку называют слой металла который удаляется с поверхности обработки резанием.
Припуск на черновую обработку поверхности:
Rz-1 – высота шероховатостеймкм;
– остаточное пространство отклонения;
–погрешность закрепления;
Для отливки I класса с габаритным размером не более 1250 [1 с. 63].
Суммарное значение пространственных отклонений
мкм – удельная кривизна заготовки;
Тогда пространственное отклонение
б г – допуски поверхности для литой заготовки 2 класса точности 14 квалитета
Допуск на поверхности используемые в качестве базовых – находим по соответствующему квалитету для диаметра 200h7 [2табл. 21 с.395]. Номер квалитета определяем по табл. 31 [6 с. 150 ]
Заготовка - 1000 мкм
черновое - 12 квалитет - 630 мкм
чистовое - 10 квалитет -160 мкм
шлифование - 7 квалитет - 40 мкм
Остаточное предварительное отклонение:
-после чернового обтачивания:
и – коэффициент уточнения формы
у- погрешность установки
б –погрешность базирования
з –погрешность закрепления
з=120мкм (литьезакрепление в четырехкулачковом патроне)
з=100мкм (чисто обработаннаяустановка в зажимное приспособление с пневматическим зажимом)
Минимальный припуск:
-под черновое обтачивание
-под чистовое обтачивание
Графу «расчетный размер Dr» заполняем начиная с конечного (чертежного) размера путем последовательного прибавления расчетного минимального припуска каждого технологического перехода (для 200h7 допуск 0 -40 мкм) расчетный размер - находим по предельному отклонению h7:
В графе «наименьший предельный размер» получчается по расчетным размерам :
Наибольшие предельные размеры вычисляем прибавление допуска к наименьшему предельному размеру:
Предельные значения припусков определяем как разность наименьших предельных размеров предшествующего и выполняемого переходов:
Аналогично определяем предельные значения припусков
Общие припуски и рассчитываем суммируя промежуточные припуски:
Проверка правильности:
На оснований данных расчета строим схему графического расположения припусков и допусков по обработке поверхности обода тормозного шкива 200h7
На остальные обрабатываемые поверхности припуски и допуски выбираем по таблицам (ГОСТ 1855-55) и записываем их значения в табл. 1.2
Таблица 1.2 Припуски и допуски на обрабатываемые поверхности
Расчет режимов резания
Станок - токарно-револьверный 1П 365 [2 табл. 4.4 с. 159]
- диаметр обрабатываемой заготовки (максимальный) - 500 мм
- длина заготовки (максимальная) - 200 мм
- обороты обмин - 344866136 188274385 530 7771080 1500;
- подачи ммоб - 09; 012; 017; 025; 035; 05; 07; 1; 135.
Инструмент - резец проходной прямой по МН 582-64 с пластинками из твердого сплава Т5К10 [3 табл. 6 с.287) резец упорный отогнутый по МН 577-64 с пластинками из твердого сплава Т5К10 [3 табл. 3 с.283] резец подрезной отогнутый по МН 592-64 с пластинками из твердого сплава Т5К10 [3 табл.4 с.284].
Переход №1- подрезка торца ступицы
D = 74 мм; d = 34 мм
Припуск на обработку: 3 мм
Глубина резания: t = 3 мм
-величина врезаниямм
-величина перебегамм
Назначаем подачу суппорта на оборот детали S0 = 06 ммоб [3 табл. 8А-1 с.539] по паспорту станка принимаем ближайшее стандартное значение: S0 = 05 ммоб
Период стойкости инструмента:
Где λ=lрез l рх=20215=093 >07 следовательно λ=1
Vрез=Vтабл *К5*К6*К7=83*1*09*13=9711 ммин
Vтабл - табличное значение скорости резания Vтабл= 83 ммин при t = 3 мм s = 05 ммоб [3табл. 8А-5с.540]
К5 - поправочный коэффициент на материал К5 = 1 [3 табл. 8А-7с.541]
К6 - поправочный коэффициент в зависимости от периода стойкости режущего инструмента
К6 = 09 [3 табл. 8А-7 с.541]
К7 - поправочный коэффициент в зависимости от вида обработки К7 = 13 так как Dнаим Dнаиб 04 [3 табл. 8А-7 с.542]
Частота вращения шпинделя:
Согласно паспортным данным станка принимаем частоту вращения шпинделя
Фактическая скорость резания :
Nтабл - условная расчетная мощность Nтабл = 59 кВт при t=3 мм s = 05 ммоб [3 табл. 8А-8 с.542]
К8-поправочный коэффициент на мощность резания К8 = 075 [3 табл. 8А-9с.542]
Переход №2- черновое обтачивание обода
Диаметр обработки:D = 2034 мм;
Припуск на обработку: 24 мм
Глубина резания: t = 12 мм
Где λ=lрез l рх=5353=1>07 следовательно λ=1
Vрез=Vтабл *К5*К6*К7=120*1*09*1=108 ммин
Vтабл - табличное значение скорости резания Vтабл= 120 ммин при t = 12 мм s = 05 ммоб [3табл. 8А-5с.540]
К6 - поправочный коэффициент в зависимости от периода стойкости режущего инструмента К6 = 09 [3 табл. 8А-7 с.541]
К7 - поправочный коэффициент в зависимости от вида обработкиК7 = 1 так как Dнаим Dнаиб> 07 [3 табл. 8А-7 с.542]
Nтабл - условная расчетная мощность Nтабл = 25кВт при t=12 мм
s =05ммоб [3 табл. 8А-8 с.542]
Переход №3- растачивание внутренней стенки обода
Диаметр обработки:D = 176 мм;
Припуск на обработку: 2 мм
Глубина резания: t = 2 мм
Где λ=lрез l рх=8080=1 >07 следовательно λ=1
Vрез=Vтабл *К5*К6*К7=90*1*09*1=81 ммин
Vтабл - табличное значение скорости резания Vтабл= 90 ммин при
t = 2 мм s = 05 ммоб [3табл. 8А-5с.540]
К7 - поправочный коэффициент в зависимости от вида обработкиК7 = 1 так как D>75мм [3 табл. 8А-7 с.542]
Nтабл - условная расчетная мощность Nтабл = 4 кВт при t=2 мм
Переход №4- обтачивание ступицы
Диаметр обработки:D = 74 мм;
Где λ=lрез l рх=9292=1 >07 следовательно λ=1
Переход №5- подрезка торца обода
Диаметр обработки:D = 20057 мм;d=180 мм
Где λ=lрез l рх=102851178=087 >07 следовательно λ=1
Vрез=Vтабл *К5*К6*К7=83*1*09*1=747 ммин
Vтабл - табличное значение скорости резания Vтабл= 83 ммин при
t = 3 мм s = 05 ммоб [3табл. 8А-5с.540]
Nтабл - условная расчетная мощность Nтабл = 59 кВт при t=3 мм
Переход №6- подрезка дна камеры
Диаметр обработки:D = 180 мм; d=70 мм
Где λ=lрез l рх=5555=1 >07 следовательно λ=1
Vрез=Vтабл *К5*К6*К7=83*1*09*12=8964 ммин
К7 - поправочный коэффициент в зависимости от вида обработкиК7 = 1 так как Dнаим Dнаиб>05 - 07 [3 табл. 8А-7 с.542]
Операция 10-токарная
Инструмент - резец проходной прямой по МН 582-64 с пластинками из твердого сплава Т5К10 [3 табл. 6 с.287] резец упорный отогнутый по МН 577-64 с пластинками из твердого сплава Т5К10 [3 табл. 3 с.283] резец подрезной отогнутый по МН 592-64 с пластинками из твердого сплава Т5К10 [3 табл.4 с.284].
D = 2034 мм; d = 34 мм
Где λ=lрез l рх=84528602=098 >07 следовательно λ=1
Где λ=lрез l рх=4040=1>07 следовательно λ=1
Операция 15-токарная
Инструмент - резец проходной прямой по МН 582-64 с пластинками из твердого сплава Т5К10 [3 табл. 6 с.287].
Растачивание посадочного отверстия
D = 40 мм; d = 34 мм
Припуск на обработку: 3025 мм
Глубина резания: t = 3025 мм
Где λ=lрез l рх=110113=097 >07 следовательно λ=1
Vрез=Vтабл *К5*К6*К7=90*1*09*085=6885 ммин
Vтабл - табличное значение скорости резания Vтабл= 90 ммин при t = 3025 мм
s = 05 ммоб [3табл. 8А-5с.540]
К7 - поправочный коэффициент в зависимости от вида обработки К7 = 085 так как D 75мм [3 табл. 8А-7 с.542]
Nтабл - условная расчетная мощность Nтабл = 59 кВт при t=3025 мм
s = 05 ммоб [3 табл. 8А-8 с.542]
К8-поправочный коэффициент на мощность резания К8 = 075
Операция 20 - протяжная
Станок - горизонтально-протяжный 7Б55У [2 табл. 4.40 с.194]
- скорость протягивания - 15 115 ммин
- скорость обратного хода - 25 ммин
Инструмент - протяжка шпоночная по ГОСТ 26479-85 шаг ротяжки t = 12 мм подача на зуб Sо = 003 [4 с.194]
Протягивание шпоночного паза 33*12*110
Длина рабочего хода:
-величина перебега инструмента в направлении главного движения мм
Zc- число зубьев в секции протяжки при генераторной схеме резания Zc=1
Z1- наибольшее число одновременно режущих зубьев
В-периметр резания одного зуба
Принимаем скорость резания для протяжек из быстрорежущей стали
Р6М5 - Vp = 10 ммин –Rа = 32 63 мкм [4 табл.52 с.299]
Р-сила резания на 1мм Р=136 Нмм [4табл.54с300]
Скорость рабочего ходадопускаемая мощность станка :
Следовательно станок соответствует требуемым параметрам.
Операция 25-токарная
Инструмент - резец проходной прямой по МН 582-64 с пластинками из твердого сплава Т5К10 [3 табл. 6 с.287] резец подрезной отогнутый по МН 592-64 с пластинками из твердого сплава Т5К10 [3 табл.4 с.284].
Припуск на обработку: 0434 мм
Глубина резания: t = 0217 мм
Где λ=lрез l рх=9596=098 >07 следовательно λ=1
Vрез=Vтабл *К5*К6*К7=135*1*09*1=1215 ммин
Vтабл - табличное значение скорости резания Vтабл= 135 ммин при t = 0217 мм
s = 025 ммоб [3табл. 8А-5с.540]
К7 - поправочный коэффициент в зависимости от вида обработки К7 = 1 так как Dнаим Dнаиб> 07 [3 табл. 8А-7 с.542]
Nтабл - условная расчетная мощность Nтабл = 03 кВт при t=0217 мм
s = 025 ммоб [3 табл. 8А-8 с.542]
Переход №2- подрезка торца
D = 20014 мм; d = 40 мм
Припуск на обработку: 1 мм
Глубина резания: t = 1 мм
Назначаем подачу суппорта на оборот детали S0 = 04 ммоб [3 табл. 8А-1 с.539] по паспорту станка принимаем ближайшее стандартное значение:
Где λ=lрез l рх=80078107=098 >07 следовательно λ=1
Vрез=Vтабл *К5*К6*К7=127*1*09*13=1486 ммин
Vтабл - табличное значение скорости резания Vтабл= 127 ммин при t = 1 мм
s = 035 ммоб [3табл. 8А-5с.540]
Nтабл - условная расчетная мощность Nтабл = 15 кВт при t=1 мм s = 035 ммоб [3 табл. 8А-8 с.542]
Операция 35 - шлифовальная
Станок - круглошлифовальный ЗТ160 [2 табл. 4.16 с.173]
- частота вращения привода обмин - 5578 110156220 310440620
- подача - 01 3 мммин
Инструмент - шлифовальный круг прямого профиля общего назначения DB = 40030 ГОСТ 2424-67 [4 табл. 170 с.253]. Шлифовальный материал.
- диаметр обработки - 20014 мм
- глубина резания - 0089 мм
Stx- подача на глубину за двойной ход стола Stx=00035 ммход
CN-коэффициент при определении мощности СN=034 [4табл.56с303]
xyrq-показатели степени [4табл.56с303]
-коэффициент на основаное время на выхаживание и доводку шлифования к=14
Расчет технической нормы времени
Норма штучного времени мин
Тшт = Топ + Тоб + Тот = 0471 +001+0028 = 051 мин
Топ - оперативное время мин
Топ = Т0 + Тв = 011 + 0361 = 0471 мин
Т0 - основное время мин
Тв - вспомогательное время мин
Тв = Тус+Тзо+Туп+Тиз=02+0071+005 + 004=0361мин
Тус-время на установку и снятие детали
Тус=02 мин [2 табл. 5.6 с.199]
Тзо -время на закрепление и раскрепление детали
Тзо = 0071 мин [2 табл. 5.7 c.201]
Туп -время на приёмы управления мин
Туп=t1 + t2 = 001 + 004 = 005 мин
t1 - время на включение станка кнопкой
t1= 001 мин [2 табл. 5.8 с.202]
t2 - время на подвод резца
t2 = 004 мин [2 табл. 5.8 с.202]
Тиз -время на измерение детали
Тиз - 004 мин [6 табл. 5.12 с.207]
Тоб -время на обслуживание мин
Тоб=Ттех + Торг =00029 + 0008 = 001 мин
Ттех - время на техническое обслуживание мин
Ттех = Т0 *tcмТ=011*1350 = 00029 мин
tcм –время на смену инструмента
tcм=13 мин [2табл 5.17с209]
Т-стойкость инструментамин
Торг –время на организационное обслуживаниемин
Торг=0017*Топ =0017*0471=0008 мин
Тот –время на отдыхмин
Тот =006*Топ =006*0471=0028 мин
Тшт = Топ + Тоб + Тот = 065 +0026+0039 = 0715 мин
Топ = Т0 + Тв = 056 + 009 = 065 мин
Тв =Туп+Тиз=005 + 004=009мин
Тоб=Ттех + Торг =0015 + 0011 = 0026 мин
Ттех = Т0 *tcмТ=056*1350 = 0015 мин
Торг=0017*Топ =0017*065=0011 мин
Тот =006*Топ =006*065=0039 мин
Тшт = Топ + Тоб + Тот = 094 +0038+006 = 1038 мин
Топ = Т0 + Тв = 085 + 009 = 094 мин
Тоб=Ттех + Торг =0022 + 0016 = 0038 мин
Ттех = Т0 *tcмТ=085*1350 = 0022 мин
Торг=0017*Топ =0017*094=0016 мин
Тот =006*Топ =006*094=006 мин
Тшт = Топ + Тоб + Тот = 056 +0021+00095 = 059 мин
Топ = Т0 + Тв = 047 + 009 = 056 мин
Тоб=Ттех + Торг =0012 + 00095 = 0021 мин
Ттех = Т0 *tcмТ=047*1350 = 0012 мин
Торг=0017*Топ =0017*056=00095 мин
Тот =006*Топ =006*056=0033 мин
Тшт = Топ + Тоб + Тот = 024 +0008+0014 = 0262 мин
Топ = Т0 + Тв = 015 + 009 = 024 мин
Тоб=Ттех + Торг =00039 + 00041= 0008мин
Ттех = Т0 *tcмТ=015*1350 = 00039 мин
Торг=0017*Топ =0017*024=00041 мин
Тот =006*Топ =006*024=0014 мин
Тшт = Топ + Тоб + Тот = 068 +0027+0027 = 0747 мин
Топ = Т0 + Тв = 059 + 009 = 068 мин
Тоб=Ттех + Торг =0015 + 00012= 0027мин
Ттех = Т0 *tcмТ=059*1350 = 0015 мин
Торг=0017*Топ =0017*068=0012 мин
Тот =006*Топ =006*068=004 мин
Тшт = Топ + Тоб + Тот = 1281 +0046+0077 = 1404 мин
Топ = Т0 + Тв = 092 + 0361 = 1281 мин
Ттех = Т0 *tcмТ=092*1350 = 0024 мин
Торг=0017*Топ =0017*1281=0022 мин
Тот =006*Топ =006*1281=0077 мин
Тшт = Топ + Тоб + Тот = 052 +00188+0031 = 056 мин
Топ = Т0 + Тв = 043 + 009 = 052 мин
Тоб=Ттех + Торг =0011 + 00088= 00188мин
Ттех = Т0 *tcмТ=043*1350 = 0011 мин
Торг=0017*Топ =0017*052=00088 мин
Тот =006*Топ =006*052=0031 мин
Тшт = Топ + Тоб + Тот = 051 +0019+0031 = 056 мин
Топ = Т0 + Тв = 042 + 009 = 051 мин
Тв = Туп+Тиз=005 + 004=009мин
Тоб=Ттех + Торг =0011 + 00086= 0019мин
Ттех = Т0 *tcмТ=042*1350 = 0011 мин
Торг=0017*Топ =0017*051=00086 мин
Тот =006*Топ =006*051=0031 мин
Тшт = Топ + Тоб + Тот = 050 +000854+003 = 053 мин
Топ = Т0 + Тв = 0021 + 0484 = 050 мин
Тв = Тус+Тзо+Туп+Тиз=0119+0135+005 + 018=0484мин
Тус=0119 мин [2 табл. 5.6 с.199]
Тзо = 0135 мин [2 табл. 5.7 c.201]
Тиз - 018 мин [6 табл. 5.12 с.207]
Тоб=Ттех + Торг =000004 + 00085= 000854мин
Ттех = Т0 *tcмТ=0021*0150 = 000004 мин
tcм=01 мин [2табл 5.17с209]
Торг=0017*Топ =0017*050=0085 мин
Тот =006*Топ =006*050=0030 мин
Тшт = Топ + Тоб + Тот = 18 +003+001 = 184 мин
Топ = Т0 + Тв = 14 + 04 = 18 мин
Тв = Тус+Тзо+Туп+Тиз=019+07+005 + 009=04мин
Тус=019 мин [2 табл. 5.6 с.199]
Тзо = 07 мин [2 табл. 5.7 c.201]
Тиз - 009 мин [6 табл. 5.12 с.207]
Тоб=Ттех + Торг =0027 + 0024= 0051мин
Ттех = Т0 *tcмТ=14*1350 = 0036 мин
Торг=0017*Топ =0017*18=003 мин
Тот =006*Топ =006*18=001 мин
Тшт = Топ + Тоб + Тот = 098 +0039+006 = 1079 мин
Топ = Т0 + Тв = 084 + 014 = 098 мин
Тв = Туп+Тиз=005 + 009=0014мин
Тоб=Ттех + Торг =0022 + 0017= 0039мин
Ттех = Т0 *tcмТ=084*1350 = 0022 мин
Торг=0017*Топ =0017*098=0017 мин
Тот =006*Топ =006*098=006 мин
Тшт = Топ + Тоб + Тот = 17 +0089+0102 = 189 мин
Топ = Т0 + Тв = 12 + 05 = 17 мин
Тв = Тус+Тзо+Туп+Тиз=019+0135+005 + 013=05мин
Тиз - 013 мин [6 табл. 5.12 с.207]
Тоб=Ттех + Торг =006 + 0029= 0089мин
Ттех = Т0 *tcмТ=12*2350 = 006 мин
Торг=0017*Топ =0017*17=0029 мин
Тот =006*Топ =006*17=0102 мин
Расчет измерительного инструмента
Для контроля посадочного отверстия тормозного шкива используется калибр-пробка проходная и непроходная.
если оба калибра проходной и непроходной не проходят то деталь испорчена но брак может быть исправлен продолжением обработки.
если проходной проходит а непроходной не проходит - деталь годная.
если проходят оба калибра имеет место неисправимый брак.
- наибольший размер - 40+0039 = 40039 мм
- наименьший размер - 40+0= 40 мм
Согласно СТ СЭВ 157-75 для 8-го квалитета: z = 0006 мм Н = 0004 мм
Проходной max и min:
Dmin - наименьший размер отверстия мм
Z - отклонение середины поля допуска на изготовление проходного калибра для отверстия относительно наименьшего размера Z = 0006 мм
Н - допуск на изготовление калибров Н = 0004 мм
Непроходной max и min :
Описание инструмента
Окончательная обработка торцовой и наружной поверхностей по 4-му классу точности с припуском под последующее шлифование. Деталь устанавливается на конусной оправке со шпонкой. На чертеже представлена быстрозажимная оправка. Она устанавливается в шпиндель токарного станка конусным хвостовиком корпуса 3 и закрепляется кроме того с помощью фланца 2. На конце штока имеются кольцевая радиусная канавка и две лыски. В полости корпуса размещается шток 1 пневмоцилиндра. Посадив обрабатываемую деталь на поверхность корпуса с конусностью 1:10 надеваем на конец штока в зоне лысок спецвтулку 5 с вставленным в ней штифтом 4. При повороте втулки штифт вводится в зону радиусной канавки и соединяет втулку со штоком а после рабочею хода штока влево шкив оказывается закрепленным на оправке.
По выполнении операции контролируется биение торнца относительно оси отверстия; допускаемое отклонение 0025 мм на радиусе 100мм.
Список используемой литературы
А.Ф. Горбацевич. Курсовое проектирование по технологии машиностроения.Мн. 1983.-256 стр.
В.И. Анурьев. Справочник конструктора машиностроителя. Том 1 М 1980.-728 стр.
Обработка металлов резанием. Справочник технолога. Под ред. Монахова Г.А. М. 1974.-598 стр.
Справочник технолога - машиностроителя. Под ред. Косиловой А.Е. М. 1985.-687 стр.
Технология производства ПТМ. Косилова А.Е. и др. М. Машиностроение 1972. -376 стр.
Рекомендуемые чертежи
- 30.05.2022
Свободное скачивание на сегодня
- 24.01.2023