Головка штока пневматического цилиндра технологический процесс изготовления




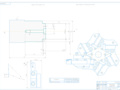
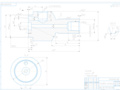
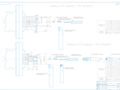
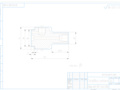
- Добавлен: 25.10.2022
- Размер: 2 MB
- Закачек: 1
Описание
Состав проекта
![]() |
![]() ![]() |
![]() ![]() |
![]() ![]() |
![]() ![]() |
![]() |
![]() ![]() |
![]() ![]() ![]() ![]() |
![]() ![]() ![]() ![]() |
![]() ![]() |
![]() ![]() |
![]() |
![]() ![]() ![]() |
![]() ![]() ![]() ![]() |
![]() ![]() |
![]() ![]() |
![]() ![]() ![]() ![]() |
Дополнительная информация
Головка штока заготовка.dwg

Головка штока.dwg

Курсовая.docx
1. Базовая информация 6
2. Руководящая информация 6
3. Справочная информация .6
ТЕХНОЛОГИЧЕСКИЙ РАЗДЕЛ ..7
1. Анализ технических требований на объект производства 7
2. Анализ технологичности конструкции детали ..8
2.1. Качественная оценка технологичности ..8
2.2. Количественная оценка технологичности .9
3. Определение типа производства ..12
4. Технико-экономическое обоснования выбора заготовки (выбор заготовки характеристика марки материалов расчет припусков) .14
4.1. Анализ способов получения заготовки и выбор оптимального 14
4.2. Описание марки материала 16
4.3. Экономическое обоснование способа получения заготовки ..16
4.4. Расчет припусков 19
5. Разработка технологического процесса 23
5.1. Cоставление маршрута обработки .23
5.2. Выбор оборудования ..27
5.3. Выбор станочного приспособления ..33
5.4. Выбор режущего инструмента 34
5.5. Выбор средств контроля ..36
6. Расчет режимов резания 37
7. Нормирование технологического процесса 40
РАЗДЕЛ БЕЗОПАСНОСТИ ЖИЗНЕДЕЯТЕЛЬНОСТИ .44
1. Анализ возможных опасных вредных факторов ЧС при работе на участке 44
2. Разработка мероприятий по снижению опасных и вредных факторов при работе на участке 46
3. Разработка мероприятий по снижениювредного воздействия техпроцесса на участке на природу ..47
СПИСОК ЛИТЕРАТУРЫ 50
Целью курсового проекта является проектирование технологического процесса изготовления детали «Головка штока». Курсовой проект обобщает все полученные знания за время освоения специальности 15.02.08 «Технология машиностроения».
Для изготовления этих деталей сегодня требуются специалисты разбирающиеся в традиционных и высоких технологиях.Эти знания дает специальность «Технология машиностроения».Она для тех кто стремится научиться что-то делать своими руками управлять современными станками и сложными машинами выполнять чертежи на компьютере точить детали на станке организовать свое дело.
В современном производстве труд технолога изменился. Распространение автоматизированного оборудования управляемого от компьютера появление систем автоматизированного проектирования и управления производством практически на всех машиностроительных предприятиях привели к тому что специалист который помогает создавать новую технику опирается на компьютерные технологии. Если раньше значительную долю в производительном времени составляли рутинные конструкторские операции работа со справочной литературой прочностные и технологические расчеты разработка чертежей и технологических карт то теперь с этой работой успешно справляются многочисленные CAD и САМ системы.
Сегодняспециальность «Технология машиностроения» актуальна как никогда и это не удивительно: производство развивается быстрыми темпами поэтому необходимы компетентные специалисты.
Специалист должен знать:
перспективы развития технологии машиностроения
методы разработки технологических процессов изготовления деталей на автоматизированном металлообрабатывающем оборудовании в том числе на станках с числовым программным управлением
нормативно-техническую документацию действующую в машиностроительной отрасли
техническое нормирование работ при обслуживании и эксплуатацииметаллообрабатывающих станков в том числе с программным управлением
методику выбора технологической оснастки
Специалист должен уметь:
пользоваться государственными стандартами
давать оценку систем управления качеством продукции на предприятиях
выполнять расчет режимов резания и норм времени норм расхода материалов;
планировать себестоимость продукции цену прибыль
пользоваться нормативной и справочной литературой при нормировании некоторых видов работ
составлять и читать чертежи несложных деталей выполнять диаграммы графики и номограммы по специальности
На сегодняшний день это одна из самых востребованных на рынке труда специальностей. Выпускники колледжа пользуются спросом на крупнейших предприятиях города на которых как правило остаются работать после прохождения производственной практики.
ИСХОДНАЯ ИНФОРМАЦИЯ ДЛЯ ПРОЕКТИРОВАНИЯ
1. Базовая информация
) базовый технологический процесс изготовления детали «Головка штока»;
) рабочие чертежи детали «Головка штока»;
) режим работы цеха - двухсменный;
) материал детали – Сталь 40Х ГОСТ 4543-2016.
) Годовая программа выпуска N-2000 шт.
2. Руководящая информация
Стандарты ЕСКД; ЕСТПП; ЕСТД.
3. Справочная информация
) вид исходной заготовки – сортовой прокат;
) имеющееся в наличии оборудование;
) нормативные данные по выбору заготовки припусков режимов резания нормированию и т.д.
) справочная литература.
ТЕХНОЛОГИЧЕСКИЙ РАЗДЕЛ
1. Анализ технических требований на объект производства
Головка штока используется для закрепления приводного гидравлического пневматического или электрического цилиндра. В зависимости от кинематики конструкции соединение может быть подвижным или неподвижным но обычно есть хотя бы один поворотный узел. Наконечник цилиндра с одной стороны имеет внутреннюю резьбу для установки на шток а с другой стороны – проушину с отверстием для крепления к опоре. Есть исполнения наконечников гидроцилиндров с цапфой вместо отверстия и с безрезьбовым корпусом для сварки.
Деталь «Головка штока» показана на рис. 1 и представляет собой тело вращения типа вал. Имеет сквозное отверстие одно нетехнологичное отверстия под углом 5. Так же заданы две конические дюймовые резьбы.
Рисунок 1- Головка штока
2. Анализ технологичности конструкции детали
Технологичность конструкции детали – это совокупность свойств изделия определяющих её приспособляемость к достижению оптимальных затрат при производстве эксплуатации и ремонте для заданных показателей качества объема выпуска и условия выполнения работ (ГОСТ 14.205-83).
Обработка конструкций на технологичность ведется по выполненным чертежам и должна предшествовать разработке технологических процессов и представляют собой часть работ по обеспечению технологичности на этапах разработки конструкций изделия и постановке её на производство.
2.1. Качественная оценка технологичности
Проводится по чертежу путём анализа возможности обработки высокопроизводительными методами с уменьшением трудоёмкости и металлоёмкости.
Таблица 1 - Качественный анализ технологичности
Показатель технологичности
Правильная форма и размеров канавок для выхода инструмента
Возможность получения заданной точности обычными для технологии методов
Имеются глухие отверстия
Отверстия расположены под прямым углом
Свободный доступ инструмента
Наличие глубоких отверстий малого диаметра
Свойства материала детали должны удовлетворять существующей технологии изготовления хранения и транспортировки
Деталь должна изготавливаться из стандартных или унифицированных заготовок
2.2. Количественная оценка технологичности
а) Коэффициент использования материала.
где q=19 – масса детали (кг)
Q=25 – масса заготовки (кг)
Деталь технологична по коэффициенту использования т.к. значение Ким в допустимом диапазоне.
Таблица 2 - Обрабатываемые поверхности детали
Выдерживаемый размер мм
Продолжение таблицы 2
б) Коэффициент точности обрабатываемой поверхности
где Тср - средний квалитет точности
n – Количество поверхностей
Кто =092408 следовательно деталь технологична по коэффициенту точности.
в) Коэффициент шероховатости
где Шср - средняя шероховатость поверхности в Ra
n - количество поверхностей
Кш=0098024 следовательно деталь технологична по коэффициенту шероховатости.
3. Определение типа производства
Технология изготовления деталей в значительной степени зависит от типа производства. Следовательно на начальной стадии проектирования необходимо установить тип производства данной детали учитывая её массу и размер годового выпуска.
Тип производства представляет собой комплексную характеристику технических организационных и экономических особенностей производства обусловленных степенью специализации сложностью и устойчивостью изготовляемой номенклатуры изделий размером и повторяемостью выпуска продукции.
Основным показателем характеризующим тип производства является коэффициент закрепления операций который определяется как отношение числа всех различных технологических операций выполняемых или подлежащих выполнению в течение месяца к числу рабочих мест.
Таблица 3 - Величина годовой программы выпуска
Масса детали (изделия) кг
Величина годовой программы выпуска шт.
Для определения типа производства обычно пользуются соотношениями и рекомендациями позволяющими устанавливать его в зависимости от габаритных размеров массы и годового объема выпуска деталей пользуясь данными табл. 3.
Серийное производство характеризуется выпуском партиями однородной продукции в течение установленного периода времени. Серийное производство характеризуется изготовлением ограниченного ассортимента продукции. Партии (2000 шт) изделий повторяются через определенные промежутки времени. В зависимости от размера серии различают мелкосерийное среднесерийное и крупносерийное производства.
В серийном производстве удается специализировать отдельные рабочие места для выполнения подобных технологических операций. Уровень себестоимости продукции снижается за счет специализации рабочих мест широкого применения труда рабочих средней квалификации эффективного использования оборудования и производственных площадей уменьшения по сравнению с единичным производством расходов на заработную плату.
Продукцией серийного производства является стандартная продукция например машины установившегося типа выпускаемые обычно в более значительных количествах (металлорежущие станки насосы компрессоры оборудование химической и пищевой промышленности).
Отличительными чертами серийного производства являются:
- производство сериями относительно ограниченной номенклатуры повторяющейся продукции;
- относительно непродолжительная длительность производственного цикла;
- типизация технологического процесса;
- наличие специализированного оборудования и рабочих мест;
- использование в процессе производства рабочих средней квалификации;
- механизация контроля качества продукции.
Для головки штока исходя из годовой программы выпуска определяется средне-серийный тип производства.
4. Технико-экономическое обоснования выбора заготовки
4.1. Анализ способов получения заготовки и выбор оптимального
Заготовки деталей обрабатываемые на автоматизированных линиях и участках должны отвечать следующим основным требованиям:
- минимальный припуск достаточный для обеспечения заданной точности и шероховатости обрабатываемой поверхности;
- распределение припуска должно быть равномерным по поверхности заготовки и стабильным для всей партии деталей;
- постоянство физико-механических свойств по всей поверхности;
-разброс припуска не должен превосходить допустимого значения обеспечивающего эффективный зажим заготовки в заранее настроенную оснастку;
-база должна иметь относительно высокую точность формы и расположения поверхностей и обеспечивать надежное крепление детали при обработке;
-характер отвода стружки от режущих кромок инструментов должен быть свободным исключающим заклинивание и поломку инструментов особенно при обработке отверстий малого диаметра;
-отклонение от неперпендикулярности торцов заготовки к образующей не
более 05 мм для заготовок диаметром до 100 мм и не более 10 мм для
заготовок диаметром свыше 100 мм.
На выбор метода получения заготовки оказывают влияние: материал детали; её назначение и технические требования на изготовление; объём и серийность выпуска; форма поверхностей и размеры детали.
Оптимальный метод получения заготовки определяется на основании всестороннего анализа названных факторов и технико-экономического расчёта технологической себестоимости детали. Метод получения заготовки обеспечивающий технологичность изготовления из неё детали при минимальной себестоимости последней считается оптимальным.
Для данной детали можно использовать следующие методы получения заготовок: горячая объемная штамповка на молотах и прессах горячая объемная штамповка на горизонтально-ковочных машинах а также получение заготовки из проката.
Наиболее рациональными методами получения заготовки из вышеперечисленных для данной детали с учетом материала массы конфигурации габаритов детали и годовой программы выпуска является получение заготовки из круглого проката - используется в серийном и массовом производствах для заготовок имеющих форму тел типа “вал”. Производится со сторонами размеров от 6 до 200 миллиметров выбирается метод получения заготовок из проката так как он менее затратый не требует изготовления штампов пресс-форм и т.п.
В качестве исходной заготовки используют пруток круглого сечения. Отрезают заготовки: бруски нужной нам длины. Так прокатный стан из трех частей то напуски малы или отсутствуют. К недостаткам прокатных станов относят их высокую стоимость но подобные станы легко перенастраиваются на другие параметры т.е. имеют высокую универсальность.
Устройство прокатного стана – агрегат состоящий из трех основных частей:
передаточного механизма;
В состав рабочей машины входят одна или несколько рабочих клетей. В свою очередь каждая рабочая клеть состоит из прокатных валков вращающиеся в подшипниках расположенных на двух вертикальных стойках станины. Изменение расстояния между валками осуществляется с помощью нажимного механизма. Конечно в крупных станах также есть уравновешивающий механизм служащий для поддержки и подъема верхнего валка и прижатия подушки к торцу нажимного винта.
Устройство двухвалкового прокатного стана:
Прокатный стан приводится в движение от электродвигателя. Для передачи вращений от вала двигателя к рабочим валкам стана применяется шестеренная передача образующая так называемую шестеренную клеть. Между шестеренной клетью и электродвигателем находится редуктор состоящий в большинстве случаев из двух цилиндрических шестерен и служащий для снижения числа оборотов рабочих валков. Соединение шеек зубчатых колес с валками двигателя и стана осуществляется с помощью муфт и соединительных шпинделей с трефовым сечением. В мощных станах соединения осуществляется универсальными шпинделями с шарниром Гука. Современные прокатные станы оснащены вспомогательными механизмами с помощью которых достигается полная механизация процесса прокатки.
4.2. Описание марки материала
Марка: Сталь 40Х – (заменители45Х38ХА40ХН40ХС 40ХФ 40ХР) Таблица 4 – Химический состав стали 40Х
Химический состав в % стали 40Х
Класс: сталь конструкционная легированная.
Вид поставки: сортовой прокат: в том числе фасонный:ГОСТ 4543-2016ГОСТ 2590-2006ГОСТ 2591-2006ГОСТ 2879-2006ГОСТ 10702-78. Калиброванный прутокГОСТ 7417-75ГОСТ 8559-75ГОСТ 8560-78ГОСТ 1051-73. Шлифованный пруток и серебрянкаГОСТ 14955-77.толстыйГОСТ 1577-93ГОСТ 19903-74. ПолосаГОСТ 103-2006ГОСТ 1577-93ГОСТ 82-70. ПоковкиГОСТ 8479-70. ТрубыГОСТ 8731-74ГОСТ 8733-74ГОСТ 13663-86.
Использование в промышленности: оси валы вал-шестерни плунжеры штоки коленчатые и кулачковые валы кольца шпиндели оправки рейки губчатые венцы болты полуоси втулки и другие улучшаемые детали повышенной прочности.
Удельный вес: 7820 кгм3 ;
Термообработка: нормализация проводится при 500-600 °С закалка- 860 отпуск при 500 °C;
Твердость материала: HB 10 -1 = 217 Мпа;
Свариваемость материала: трудно свариваема.
Способы сварки: РДС ЭШС необходимы подогрев и последующая термообработка. КТС - необходима последующая термообработка;
Температура ковки °С:начала 1250 конца 800. Сечения до 350 мм охлаждаются на воздухе.
Обрабатываемость резанием:в горячекатаном состоянии при HB 163-168
Па К тв. спл=12 и К б.ст=095.
Флокеночувствительность:чувствительна.
Склонность к отпускной хрупкости: склонна.
Предел выносливости: -1=331 Мпа.
Таблица 5 – Механические свойства стали 40Х
Механические свойства стали 40Х
Состояние поставки режимы термообработки
Пруток. Закалка 860 °С масло. Отпуск 500 °С вода или масло
4.3. Экономическое обоснование способа получения заготовки
Рассмотрим выбранные методы получения заготовок для данной детали:
Сортовой горячекатаный прокат круглого профиля.
Исходные данные для расчёта стоимости заготовки:
- Цилиндрическая часть: 76 мм
Стоимость 1 тонны металла – 37 000р.
Стоимость 1 тонны отходов (стружка) – 9000р.
Таблица 6 - Сравнительная таблица показателей способов получения заготовки:
Масса заготовки Q кг
Базовая стоимость 1т заготовок Si руб.
Стоимость 1т стружки
Стоимость заготовки из проката:
где Мпр- масса заготовки из проката кг
Мд– масса детали кг;
Sпp- стоимость одной тонны проката руб.;
Для штампованной поковки:
Коэффициент использования материала:
Деталь «Головка штока» имеет форму тела типа вал и коэффициент полезного использования материала при использование проката будет больше нежели у штамповки (Ким: 069>048) и стоимость на неё выше (Sзаг : 67523руб. > 63207 руб.). Но при всём этом оборудование для получения литый заготовок стоит значительно дороже как и сами заготовки поэтому технологичное будет использовать прокат.
Принимаем способ получения заготовки методом горячей катки проката.
4.4. Расчет припусков
Межоперационный припуск определяется для самой ответственной поверхности Ra 32.
Последовательность расчета промежуточных припусков и операционных размеров при обработке наружных поверхностей:
Согласно разработанного технологического процесса записывается порядок (последовательность) обработки поверхности для которой определяется припуск.
Определяется минимальный припуск для конечной операции. Для этого:
а) записываются значения: RZ
б) Для тела вращения расчет ведется по формуле растачивания:
Где – высота микронеровностей полученная на предшествующем
технологическом переходе мкм;
– глубина дефектного слоя полученная на предшествующем переходе мкм;
– пространственные отклонения полученные на предшествующем переходе мкм;
– погрешность установки полученная на выполняемом переходе мкм.
Минимальный припуск по переходам обработки:
Где – размер предыдущего перехода обработки мм;
– размер последующего перехода обработки мм;
– припуск на обработку последующего перехода обработки мм.
За исходный размер принимается максимальный размер т.е. мм;
) Предельные размеры по технологическим переходам:
Расчетные размеры округляются до точности допуска на обработку. Минимальный размер по переходам определяется по формуле:
) Предельные припуски на обработку:
Где – минимальный и максимальный размер последующего перехода мм;
– минимальный и максимальный размер предшествующего перехода мм.
) Общие припуски на обработку:
) Проверка правильности произведенных расчетов:
Расчет выполнен правильно.
) Номинальный припуск на заготовку:
) Номинальный размер заготовки:
Размер в заготовке мм.
Таблица 7 - Результаты расчета припусков
Расчетная поверхность операции и переходы
Элементы припуска мкм
Расчетный припуск 2Zmin мкм
Расчетный размер Dp мм
Предельные размерымм
Предельные значения припуска мкм
Черновое обтачивание
Чистовое обтачивание
5. Разработка технологического процесса
5.1. Cоставление маршрута обработки
Технологический процесс - это часть производственного процесса непосредственно связанного с изменением размеров формы или свойств материала обработки заготовки выполняемую в определенной последовательности. (ГОСТ 3.1109-82)
Разработка технологического процесса состоит из комплекса взаимосвязанных работ предусмотренных стандартами ЭСТПП и должна выполняться в полном соответствии с требованиями. (ГОСТ 14.301-83).
При разработке маршрутной технологии нужно придерживаться принципов:
В первую очередь обрабатывать поверхности которые являются базовыми для последующих операций
Каждая последующая операция должна уменьшать погрешности и улучшать качество поверхностей
Необходимо соблюдать принцип концентрации операций при котором как можно больше поверхностей должно обрабатываться в одной операции
Необходимо соблюдать принципы совмещения и постоянства баз
Необходимо учитывать на каких стадиях технологического процесса целесообразно проводить механическую термическую и другие виды обработки в зависимости от требований чертежа.
Обработка поверхностей ведется в последовательности обратной степени их точности чем точнее поверхность тем позже она обрабатывается.
Таблица 8 - Технологический процесс изготовления детали “Головка штока”
Наименование и содержание операций
Эскиз и схема базирования детали
Отрезать в размер 125
Закалка 860 °С. Отпуск 500 °С.
Подрезать торец в размер 120
Точить 70 на длину 68
Точить уступы по чертежу
Центровать сверлить отверстие 8 на длину 80
Расточить отверстие 18Н10
Переустановить и закрепить
Подрезать торец окончательно в размер 118+05
Обработать наружную поверхность точить сферу R58
Точить канавку размер обеспечить инструментом
Нарезать резьбу М36х15-6g
Сверлить отверстие 8 на длину 70
Расточить отверстие под резьбу
Нарезать резьбу К12* ГОСТ 6111-52
Продолжение таблицы 8
Горизонтально-фрезерная
Фрезеровать с поворотом детали две лыски в размер 66.
Координатно-расточная
Центровать и сверлить отв. 18 выдерживая координату 33 Развернуть отв. под резьбу. Зенковать фаску 2х45
Нарезать резьбу К12* ГОСТ 6111-52 метчиком.
Произвести поворот глобусного стола на 85 вывериться по отв. 18Н10 обеспечить угол поворта 5 произвести движение координаты шпинделя на координату 19±02. Цетровать и сверлить отв. 8 на выход в резьбовое отверстие.
Запилить заусенцы притупить острые кромки.
а) шереховатость обрабатываемых поверхностей
б) отсутствие забоин заусенцев – визуально
Проверить заданные размеры по чертежу.
5.2. Выбор оборудования
При выборе оборудования необходимо учесть следующее:
Выбранный станок должен обеспечивать выполнение технических требований предъявляемых к изготовлению деталей.
Размеры рабочей зоны станка должны соответствовать габаритным размерам обрабатываемой детали.
Производительность станка должна соответствовать заданной программе выпуска деталей.
Мощность жесткость и кинематические возможности станка должны позволять вести обработку на оптимальных режимах резания с наименьшей затратой времени и с наименьшей себестоимостью.
Применение специальных агрегатных и других высокопроизводительных станков должно быть экономически обосновано: использование этих станков в крупносерийном и массовом производстве всегда целесообразно и экономически оправдывается.
При среднесерийном производстве на одном станке выполняют несколько различных операций поэтому выбранный станок должен удовлетворять техническим требованиям всех намеченных обработок. В массовом производстве каждый станок предназначен для выполнения одной операции и должен удовлетворять не только всем требованиям данной обработки но и обеспечивать заданную производительность.
Станки с ЧПУ имеют преимущество по сравнению с универсальными станками. Этими преимуществами являются: повышение точности обработки сокращение или полная ликвидация различных и слесарно-притирочных работ простота и малое время переналадки уменьшение брака по вине рабочего возможность использования менее квалифицированной рабочей силы и многие другие. Применение таких станков решает несколько социальных задач например уменьшает долю тяжелого ручного труда делает менее острой нехватку рабочей силы.
Для токарной обработки используем токарный станок с ЧПУ MASTURN 550 CNC.
Рисунок 2 - токарный станок с ЧПУ MASTURN 550 CNC.
Таблица 9- Технические характеристики станка Masturn 550 CNC.
Рабочий диаметр над станиной
Рабочий диаметр над поперечным суппортом
Межцентровое расстояние
Передний конец шпинделя (DIN55027)
HEIDENHAIN MANUAL plus 4110
Автоматическая двухступенчатая коробка передач
Продолжение таблицы 9
Диапазон оборотов шпинделя
Макс. крутящий момент на шпинделе: на 1-й ступени
Макс. крутящий момент на шпинделе: на 2-ой ступени
Инструментальная головка
Конус полости в пиноли - MORSE
Длина x ширина x высота
Для горизонтально-фрезерной операции выбираем станок консольно-фрезерный с ЧПУ FGS 63 NCP
Рисунок 3 Горизонтально-фрезерный станок с ЧПУ FGS 63 NCP
Таблица 10 - Технические характеристики станка FGS 63
Длина рабочего стола
Ширина рабочего стола
Кол-во Т-образных пазов
Ширина паза расстояние между пазами
Макс. нагрузка на стол
Диапазон частот вращения шпинделя
Пределы регулирования скорости
Мощность главного двигателя S1S6
Макс. момент на шпинделе
Диапазон рабочих подач (продольная поперечная)
Диапазон рабочих подач (вертикальная)
Ускоренное перемещение (продольное поперечное)
Ускоренное перемещение (вертикальное)
Макс. усилие подачи по осям X Y Z
Суммарная электрическая мощность
Габариты станка (ширина х глубина х высота)
Для координатно-расточной операции выбираем станок 2В440А
Рисунок 4 Координатно-расточной станок 2В440А
Таблица 11 - Технические данные станка 2B440A
Наименование параметра
Основные параметры станка
Класс точности (НПВАС)
Рабочая поверхность стола мм
Наибольший диаметр сверления в стали 45 мм
Наибольший диаметр расточки в стали 45 мм
Наименьшее и наибольшее расстояние от торца шпинделя до стола мм
Расстояние от оси шпинделя до стойки (вылет шпинделя) мм
Частота вращения шпинделя (бс регулирование) обмин
Пределы рабочих подач гильзы шпинделя на один оборот шпинделя ммоб
Наибольшее вертикальное перемещение шпинделя (ход) (ручное механическое) мм
Наибольшее вертикальное перемещение шпиндельной бабки (установочное от руки) мм
Породолжение таблицы 11
Внутренний конус шпинделя (внутренний конус) специальный
Наибольший конус закрепляемого инструмента
Закрепление шпиндельной коробки на направляющих
Наибольшее перемещение стола (продольное поперечное) мм
Число Т- образных пазов на столе
Величина ускоренного перемещения стола и салазок мммин
Пределы рабочих подач стола и салазок при фрезеровании мммин
Наибольшая масса обрабатываемого изделия кг
Цена деления растровой сетки установки координат мм
Точность установки координат мм
Точность расстояний между осями отверстий растачиваемых на станке мм
Точность растачиваемого диаметра (постоянство диаметра) мм
Количество электродвигателей на станке
Электродвигатель привода главного движения кВт
Электродвигатель привода перемещения стола кВт
Электродвигатель привода перемещения салазок кВт
Электронасос охлаждающей жидкости
Габариты станка включая ход стола и салазок мм
5.3. Выбор станочного приспособления
Важность технологической оснастки определяется тем что она повышает производительность труда и создает предпосылки для механизации и автоматизации производства.
Повышение производительности труда при применении технологической оснастки обеспечивается следующим:
– сокращением вспомогательного времени на установку и закрепление заготовки;
– интенсификацией режимов резания за счет увеличения жесткости и виброустойчивости системы СПИЗ;
– сокращением пригоночно-слесарных работ при сборке изделия;
– расширением многостаночного обслуживания;
– устранением разметки заготовок перед обработкой;
– повышением точности изготовления и т.д.
Установку заготовки выполняют осуществляя плотный контакт базовых поверхностей с установочными элементами приспособления жестко закрепленными в его корпусе. Это обеспечивается приложением к заготовке соответствующих сил закрепления. Для полной ориентации заготовки число и положение опор должно быть таким чтобы при соблюдении условия неотрывности баз от опор заготовка не могла сдвигаться и поворачиваться относительно координатных осей. При выполнении условия неотрывности заготовка лишается всех степеней свободы.
Число опор (точек) на которые устанавливается заготовка не должно быть больше шести (правило шести точек). Для обеспечения устойчивого положения заготовки в приспособлении расстояние между опорами следует выбрать возможно большим; при установке заготовки на опоры не должен возникать опрокидывающий момент. С увеличением расстояния между опорами уменьшается влияние погрешностей формы базовых поверхностей на положение заготовки в приспособлении. Основные опоры жестко связаны с корпусом приспособления.
Наиболее действенным способом уменьшения деформаций заготовки под воздействием усилий закрепления является направление усилий если возможно на опору. Это избавляет заготовку от воздействия изгибающих моментов.
При этом необходимо помнить о некоторых путях уменьшения возможных деформаций: например не стоит прилагать большее усилие чем необходимо для надежной фиксации заготовки.
Используемые приспособления:
)Трёхкулачковый самоцентрирующийся патрон ГОСТ 2675-80
)Поворотный глобусный стол ГОСТ 16163-90
)Тиски ГОСТ 16518-96
5.4. Выбор режущего инструмента
При разработке технологического процесса механической обработки заготовки выбор режущего инструмента его конструкции и размеров в значительной мере предопределяется методами обработки свойствами обрабатываемого материала требуемой точностью обработки и качества обрабатываемой поверхности заготовки.
При выборе режущего инструмента необходимо стремиться принимать стандартный инструмент но когда целесообразно следует применять специальный комбинированный фасонный инструмент позволяющий совмещать обработку нескольких поверхностей.
Правильный выбор режущей части инструмента имеет большое значение для повышения производительности и снижения себестоимости обработки. Для обработки стали рекомендуется применять инструмент режущая часть которого изготовлена из титановольфрамовых твердых сплавов (Т5К10 Т14К8 Т15К6Т Т30К4) быстрорежущих инструментальных сталей (Р18Ф1 Р9М6 Р9Ф4 Р14Ф4) вольфрамовых твердых сплавов (ВК2 ВКЗМ ВК4 ВК8) и др. Для обработки чугуна цветных металлов и неметаллических материалов используют инструмент из вольфрамовых твердых сплавов. Выбор материала для режущего инструмента зависит от формы и размеров инструмента материала обрабатываемой заготовки режимов резания и типа производства.
Режущий инструмент необходимо выбирать по соответствующим стандартам и справочной литературе в зависимости oт методов обработки деталей.
Если технологические особенности детали не ограничивают применения высоких скоростей резания то следует применять высокопроизводительные конструкции режущего инструмента оснащенного твердым сплавом так как практика показала что это экономически выгодней чем применение быстрорежущих инструментов. Особенно это распространяется на резцы (кроме фасонных малой ширины автоматных) фрезы зенкеры конструкции которых оснащены твердым сплавом хорошо обработаны.
Выбранный режущий инструмент для детали «Головка штока»:
)Пила ленточная М51 34х11х34х3920 Россмарк Сталь
)Державка PSSNRL 2525-M12 Korr SNMG 120408-VM
)Сверно центровочное HSS Co 381-315 GUHRING
)Державка SCLCR2020K12 Пластина CCMT120408-RP4 WPP30S WALTER
)Державка SER 2020 K16 Пластина 16ER 150 ISO IC908 ISCAR
)Державка PCHR 20-24 Пластина PENTA 24N100J006 IC1008 ISCAR
)Сверло корпусное DCN 080-064-12A-80 Головка сверлильная FCP 081 IC908 ISCAR
)Сверло 2301-0050 15 ГОСТ 10903-77
)Державка PICCO 16-6-7 Резец PICCO R 050.6-42C IC908 ISCAR
) Сверно центровочное HSS 381-1 GUHRING
) Фреза 90 PPM 4125R Korloy
) Сверло 2317-0004 ГОСТ 14952-75;
) Сверло 2301-0062 1825 ГОСТ 10903-77
) Развёртка 2373-0035 К12” ГОСТ 6226-71
) Зенковка 2353-0137 ГОСТ 14953-80
) Метчик 2680-0008 К12” ГОСТ 6227-80
5.5. Выбор средств контроля
Факторы приводящие к браку деталей делятся на две группы. К первой группе относится изнашивание базовых элементов приспособлений и элементов станков которое влияет на точность геометрической формы и взаимного расположения обработанных поверхностей. Это изнашивание протекает сравнительно медленно и поэтому нет необходимости осуществлять контроль этих параметров чаще чем один раз в неделю что делает нецелесообразным автоматизацию контроля.
Ко второй группе относится размерное изнашивание режущих инструментов а также случайные факторы (погрешности базирования детали колебание твердости и жесткости детали и т. п.). Это изнашивание протекает сравнительно быстро и для предотвращения возможного брака на автоматизированных линиях и участках организуют контроль:
-фактического размера обработанной поверхности непосредственно на станке т. е. в процессе обработки;
-статистический контроль качества обрабатываемых деталей; лимита стойкости инструмента; за работой нового инструмента.
Автоматизированный контроль размеров обрабатываемой детали непосредственно на станке является наиболее эффективным поскольку позволяет предупредить выход за пределы допуска размеров первой же детали. При действии случайных факторов предупреждается повторение брака на последующих деталях.
Недостатком контроля на станке является некоторое снижение производительности оборудования за счет увеличения вспомогательного времени что может составить существенную величину при большом числе контролируемых размеров.
Используемые средства контроля:
)Штангенциркуль ШЩ-II-125-01 ГОСТ 166-89
)Штангенциркуль ШЩ-I-200-01 ГОСТ 166-89
)Шаблон 45 8371-0082 МН 1419-61
)Штангенциркуль MarCal 16EWR-200-001
)Шаблон 1х45 ОБ 8317-0142 СТП401-К3711-87
)Кольцо М36х15 6g 8211-0127 ГОСТ 17763-72
)Калибр-пробка 8 Н14 8133-0918 ГОСТ 14810-69
)Калибр-пробка К12 ОБ8255-0005 СТП 401-К251-87
6. Расчет режимов резания
Операция 015 сверлильная с ЧПУ.
Сверление 8 на глубину 80мм.
Движение подачи поступательное скорость резания – вращение инструмента.
Где t – глубина резания;
D – диаметр инструмента.
Рассчитываем глубину резания:
Скорость резания (ммин)
Где V – скорость резания ммин;
D – диаметр инструмента мм;
m q y – показатели степеней;
Т – стойкость резца мин;
– общий поправочный коэффициент на скорость резания учитывающий фактические условия резания.
Где: – коэффициент на обрабатываемый материал;
– коэффициент на инструментальный материал;
– коэффициент учитывающий глубину сверления.
Где: – коэффициент характеризующий группу стали по обрабатываемости;
– фактические параметры характеризующие обрабатываемый материал для которого рассчитывается скорость резания;
– показатель степени.
Из справочника технолога – машиностроителя находим что:
; ; ; ; ; у = 070; q = 04; m = 02; Т = 25 мин; S = 018 ммоб.
Рассчитываем скорость резания:
Определяем частоту вращения инструмента:
Крутящий момент (Н·м):
q y – показатели степеней.
Рассчитываем крутящий момент:
; q = 2; y = 08; D = 8 мм; S= 018 ммоб; ; n = 075;
; q = 1; y = 07; D = 8 мм; S = 018 ммоб; ; n = 075;
Рассчитываем осевую силу резания:
Мощность резания (кВт)
Где – крутящий момент Нм;
n – частота вращения шпинделя обмин;
D – диаметр инструмента мм.
Рассчитаем мощность резания:
Поскольку выполняется условие то обработка на данном станке возможна.
Операция 015 расточная с ЧПУ растачивание отверстия 8 до 18Н10 на глубину 7мм.
Инструмент: державка SCLCR2020K12 Пластина CCMT120408-RP4 WPP30S WALTER
;; ; ;;; у=020; m=02.
Для внутренней обработки принимаем скорость резания равную скорости резания для наружной обработки с введением поправочного коэффициента 09.
Определяем частоту вращения детали:
Рассчитываем силу резания (Н):
Определяем значения постоянной и показателей степени:
Cpz=300; х=10; y=075; n= - 015;
Определяем значения поправочных коэффициентов:
Поправочные коэффициенты учитывающие геометрию резца:
- учитывается только для резцов из быстрорежущей стали;
Находим мощность резания:
Где – окружная сила Нм;
V – скорость резания ммин.
Поскольку выполняется условие то обработка на станке Masturn 550CNC возможна.
Операция 020 Горизонтально-фрезерная. Фрезерование двух лысок в размер 66. Подачу назначем на зуб Sz=01мм
По справочнику технолога-машиностроителя находим:
2; q=02; y=04; u=02; p=0; m=02.
T=180 Т=156 t=1; B=48 D=125 z=8
Сила резания определяется по формуле:
; t=1; y=075; u=11; q=13; w=02 B=48 z=8 n=756 D=125
Крутящий момент Hм:
Мощность резания (эффективная) кВт:
Поскольку выполняется условие то обработка на станке возможна.
Таблица 12 - Таблица режимов резания
и содержания операции
7. Нормирование технологического процесса
Под технически обоснованной нормой времени понимается время необходимое для выполнения заданного объема работы (операции) при определенных организационно-технических условиях.
Норма штучного времени – это норма времени на выполнение объема работы равной единице нормирования на выполнение технологической операции.
Технические нормы времени в условиях массового и серийного производств устанавливаются расчетно-аналитическим методом.
В серийном производстве определяется норма штучно-калькуляционного времени Тш-к:
в массовом производстве определяется норма штучного времени Тшт:
Тшт = to + tв + tоб + tот (23)
гдеТп-з – подготовительно-заключительное время на партию деталей мин.;
n – количество деталей в настроечной партии шт.;
to – основное время мин.;
tв – вспомогательное время мин.
Вспомогательное время состоит из затрат времени на отдельные приемы:
tв = tу.с + tз.о + tуп + tиз (24)
tу.с – время на установку и снятие детали мин.;
tз.о – время на закрепление и открепление детали мин.;
tуп – время на приемы управления мин.;
tиз – время на измерение детали мин.;
tоб – время на обслуживание рабочего места мин.
Время на обслуживание рабочего места tоб в массовом и серийном производстве слагается из времени на организационное обслуживание tорг и времени на техническое обслуживание tтех рабочего места:
tоб = tтех + tорг; (25)
tот – время перерывов на отдых и личные надобности мин.
Нормирование операции осуществляется в соответствии с выбранными методами обработки.
В курсовом проекте привести аналитический расчет основного времени to только для одной операции. Для всех остальных операций основное время можно установить по нормативным справочникам или по базовому технологическому процессу.
Основное (технологическое) время to определяется расчетом по всем переходам обработки с учетом совмещения переходов (для станочных работ) по формуле
S – подача инструмента ммоб
В общем случае расчетная длина обрабатываемой поверхности
l = lo +lвр + lп + lсх (27)
lсх – длина перебега (схода) инструмента мм.
Длину lвр lп lсх определяют по нормативам (lп = lсх 1 2 мм). Значение lвр можно определить расчетным путем по схеме обработки.
Вспомогательное время устанавливается по нормативам для каждого перехода [17 18].
Сумму основного и вспомогательного времени называют оперативным временем:
Таблица 13 - Таблица норм времени
Номер и наименование операции
РАЗДЕЛ БЕЗОПАСНОСТИ ЖИЗНЕДЕЯТЕЛЬНОСТИ
1. Анализ возможных опасных вредных факторов ЧС при работе на участке
Анализ проектируемого участка механического цеха показывает что в рабочей зоне присутствуют опасные и вредные факторы по ГОСТ 12.0.003-76
. Физические опасные вредные факторы.
Движущиеся машины и механизмы (электрокары);
Незащищенные подвижные элементы производственного оборудования (столы металлорежущих станков);
Острые кромки на поверхностях деталей;
Повышенное значение напряжения в электрической цепи замыкание которого возможно через тело человека;
Осколки инструментов деталей стружка обрабатываемого материала;
Повышенная температура обрабатываемых поверхностей детали и режущего инструмента;
Повышенный уровень вибрации вызванный работой производственного оборудования;
Повышенное давление в гидросистемах станков;
. Вредные производственные факторы химического происхождения:
Элементы и пыль материалов обрабатываемых деталей;
СОЖ (смазочно- охлаждающая жидкость);
Отработанное машинное масло пары которого присутствуют в воздухе а также пары бензина керосина которые используется для протирания инструмента деталей.
Предельно - допустимые концентрации (ПДК) в воздухе рабочей зоны согласно ГОСТ 12.1.005-88.
Таблица 14 – Предельно-допустимые концентрации
Наименование вещества
Агрегатное состояние
В соответствии с вышеизложенным на проектируемом участке предусмотрены следующие мероприятия:
Материалы конструкции производственного оборудования и помещений не оказывают вредного влияния на организм человека;
Конструкция оборудования исключает возможность самопроизвольного смещения падения или выбрасывания предметов при обработке деталей;
Движущие части оборудования ограничены и исключают возможность прикасания к ним работающих;
Трубопроводы гидросистем электрические кабели защищены и расположены так чтобы не было случайного повреждения;
Конструкция применяемых оградительных устройств выполнена по ГОСТ 12.4.125-83;
Для обеспечения оптимальных условий микроклимата в соответствии с ГОСТом 12.1.005-88 участок оборудован приточно-вытяжной вентиляцией.
Механический цех в котором располагается проектируемый участок расположен в поясе светового климата. Для обеспечения требуемой освещенности по СНиП 11 – 4 – 95 для участка предусматривается естественное и комбинированное освещение. Наименьший объект различения 05-1 мм. Разряд длительных работ – 6.
Для обеспечения требуемой освещенности применяются газообразные лампы высокого давления:
а) для общего освещения - металлогенные мощностью до 2000 Вт;
б) для местного освещения - натривые мощностью 100 Вт.
С целью снижения шума и вибраций на участке предусмотрены шумопоглатители виброустойчивые фундаменты и резиновые подкладки под днище тары.
С целью электробезопастности и защитой от статического электричества все металлические части оборудования защищены.
Для защиты от молнии на здание имеется специальная конструкция громоотвода.
Для обеспечения пожарной защиты на участке имеется пожарный щит
огнетушители (3 на 500 м2).
2. Разработка мероприятий по снижению опасных и вредных факторов при работе на участке
Техника безопасности при работе на металлорежущих станках.
В целях предупреждения производственного травматизма и профессиональных заболеваний рабочие и служащие должны знать и строго соблюдать правила техники безопасности. Они заключаются в следующем:
Перед началом работы:
Рабочий должен быть ознакомлен с техникой безопасности для работы на данном оборудовании.
Перед началом работы рабочий должен привести в порядок рабочую одежду.
Проверить наличие заземляющих устройств.
Проверить на холостом ходу работу станка.
Не работать на неисправном или не имеющем защитного ограждения станке.
При работе на станке:
Работать на станке только в специальной одежде.
Запрещается удалять стружку голыми руками сдувать необходимо пользоваться щёткой.
Не разрешается работать на станке в рукавицах или перчатках.
Надёжно и жёстко закрепить обрабатываемую деталь на станке.
Работать только исправным инструментом и приспособлением.
Масса и габаритные размеры обрабатываемой детали должны соответствовать паспортным данным станка.
Следует выполнять ту работу которую поручил мастер.
Не отрывать товарища от работы и т.п.
После окончания работы:
Рабочий должен выключить станок и электродвигатель.
Привести в порядок рабочее место: убрать со станка стружку инструмент приспособление очистить станок от грязи.
Инструмент положить в отведённое для него место.
Обо всех неисправностях доложить мастеру.
3. Разработка мероприятий по снижению вредного воздействия техпроцесса на участке на природу
Влияние участка на окружающую среду определяется производственными отходами поступающими в атмосферу гидросферу и литосферу. К ним относятся:
)Отработанное машинное масло;
)Использованная ветошь;
)Канализационные воды.
Механическая обработка всегда сопровождается выделением пыли паров масел и эмульсий бензина и керосина которые через вентиляционную систему могут выбрасываться в атмосферу поэтому в вентиляционную систему ставят фильтры (тканевые волокнистые зернистые) а также туманоуловители типа УПП. Кроме этого энергетическое загрязнение окружающей среды за счёт шума и вибраций. Кроме обычных звукоизолирующих звукопоглощающих материалов для максимального ослабления влияния производства на окружающую среду принимают метод «зонирования» (отделения производственных помещений от жилой застройки зелёной зоной длинной не менее 50 м где высаживают газоустойчивые породы деревьев и кустарников).
Для защиты гидросферы отработанная СОЖ используется в качестве компонента для приготовления эмульсии. Хозяйственно - бытовые канализационные воды поступают на очистные сооружения где проходят физическую и биологическую очистку проходят через фильтры и отстойники.
Для защиты литосферы на участке происходит сбор отходов которые затем сортируют металлические отходы прессуют и отправляют в переплавку ветошь складируют вне территории цеха мусор вывозиться на специальный полигон для захоронения отработанные масла собираются в специальную ёмкость и вывозятся для утилизации.
В результате выполнения курсового проекта по ПМ.01 МДК.01.01 «Разработка технологических процессов изготовления деталей машин» был разработан технологический процесс механической обработки детали «Головка штока» который включает в себя: операции токарной с ЧПУ фрезерной обработки с ЧПУ и координатно-расточную. На наиболее точную поверхность осуществлен расчет межоперационных припусков в результате выполненного расчета спроектирована заготовка для данной детали. На часть операций механической обработки определены режимы резания путем аналитического расчета а на остальные – назначены по общим машиностроительным нормативам. Приведено технологическое нормирование операции механической обработки.
В приложении курсового проекта представлен комплект технологической документации который включает в себя:
) комплект технологической документации (технологический процесс механической обработки детали «Головка штока»);
) графическая часть (чертеж детали и технологической наладки).
Иванов А.С. Давыденко П.А. Шамов Н.П. Курсовое проектирование по технологии машиностроения: Учебное пособие - М.: ИЦ РИОР: НИЦ ИНФРА-М 2014. - 276 с.
Иванов И. С. Технология машиностроения: производство типовых деталей машин. - М.: НИЦ ИНФРА-М 2014. - 224 с.
Ильянков А. И. В. Ю. Новиков Технология машиностроения: Практикум и курсовое проектирование: Учебное пособие. - М.: ИЦ "Академия" 2012. - 432 с.
Кане М.М. и др. Технология машиностроения. Курсовое проектирование - Минск: Высш. шк. 2013. - 311 с.
Новиков В. Ю. Технология машиностроения. Учебник в 2 ч. - М: Академия 2012.- 352 с.
Харламов Г.А. Припуски на механическую обработку: справочник. – М.: Машиностроение 2013г. – 256 с.
ГОСТ 3.1102-81 Единая система технологической документации. Стадии разработки и виды документов.
ГОСТ 3.1118-82 Единая система технологической документации. Формы и правила оформления маршрутных карт.
ГОСТ 3.1128-93 Единая система технологической документации. Общие правила выполнения графических технологических документов.
ГОСТ 3.1129-93 Единая система технологической документации. Общие правила записи технологической информации в технологических документах на технологические процессы и операции.
ГОСТ 21495-76. Базирование и базы в машиностроении
Карта наладки111.dwg

Державка PSSNRL 2525-М12 Korrloy
Пластина SNMG 120408-VM
Сверло корпусное DCN 080-064-12A-80 ISCAR
Головка сверлильная FCP 081 IC908 ISCAR
Державка PICCO 16-6-7 ISCAR
Метчик 2680-0008 К12" ГОСТ 6226-71
Зенковка 2353-0137 ГОСТ 14953-80
Державка SER 2020 K16 ISCAR
Токарный станок с ЧПУ
Карта наладки на токарную операцию с ЧПУ
Операция 015 Токарная с ЧПУ. Установ 1
Операция 015 Токарная с ЧПУ. Установ 2
Карта наладки.dwg

Станок: токарный с ЧПУ модели Masturn 550 CNC
PSSNRL 2525-M12 Korr SNMG -VM
Рекомендуемые чертежи
- 24.01.2023