Двухступенчатый цилиндрический редуктор




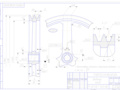
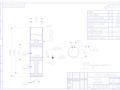
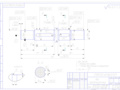
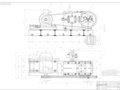
- Добавлен: 25.10.2022
- Размер: 2 MB
- Закачек: 0
Описание
Состав проекта
![]() |
![]() |
![]() ![]() ![]() ![]() |
![]() ![]() ![]() ![]() |
![]() ![]() ![]() ![]() |
![]() ![]() ![]() ![]() |
![]() ![]() ![]() ![]() |
![]() ![]() ![]() |
![]() ![]() ![]() |
![]() |
![]() ![]() |
![]() |
![]() ![]() |
![]() ![]() ![]() |
![]() |
![]() ![]() |
![]() ![]() ![]() |
![]() ![]() ![]() |
![]() |
![]() ![]() ![]() |
![]() ![]() |
![]() ![]() |
![]() ![]() ![]() |
![]() |
Дополнительная информация
Вал.dwg

РЕДУКТОР.dwg

колесо зубчатое.dwg

привод.dwg

шкив.dwg

Рекомендуемые чертежи
- 21.10.2021
Свободное скачивание на сегодня
- 06.06.2020