Разработка техпроцесса мехобработки детали ось ролика




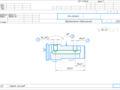
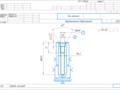
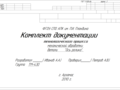
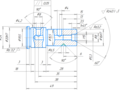
- Добавлен: 24.01.2023
- Размер: 383 KB
- Закачек: 0
Описание
Разработка т/п мехобработки детали ось ролика
Состав проекта
![]() |
![]() |
![]() |
![]() ![]() ![]() ![]() |
![]() ![]() ![]() ![]() |
![]() ![]() ![]() ![]() |
![]() ![]() ![]() |
![]() ![]() ![]() |
![]() ![]() ![]() |
![]() ![]() ![]() |
![]() ![]() |
![]() ![]() ![]() ![]() |
![]() ![]() ![]() |
![]() ![]() ![]() ![]() |
![]() ![]() ![]() ![]() |
![]() ![]() ![]() ![]() |
![]() ![]() ![]() ![]() |
Дополнительная информация
оп. 010-2.cdw

оп. 045.cdw

оп. 015.cdw

025.frw

020.frw

055.frw

1 Содержание.doc
1 Характеристика заданного типа производства
2 Технико-экономическое обоснование выбора заготовки
3 Определение коэффициента использования материала
4 Разработка маршрута обработки с выбором станочных приспособлений и оборудования
5 Разработка операционной технологии обработки детали
Выбор и обоснование технологических баз
Определение припусков и межоперационных размеров и допусков на них табличным методом
Назначение режимов резания
Нормирование технологического процесса
Список используемых источников
Развитие народного хозяйства требует непрерывного роста отечественного машиностроения как основы технического прогресса во всех отраслях промышленности.
На современном этапе развития общества значительно возросли масштабы производства ускорились темпы научно-технического прогресса. Поэтому основной проблемой стало повышение эффективности общественного производства за счет совершенствования технологии и организации производства во все более полной механизации и автоматизации производственных процессов.
Поставлена задача добиться значительного повышения труда. В качестве важного рубежа на пути к увеличению производительности труда в ближайшие годы является необходимость максимального использования резервов имеющихся на машиностроительных предприятиях.
Необходимо обеспечить снижение трудоемкости изготовления деталей и изделий сокращение потерь рабочего времени широкое применение форм научной организации труда рост структуры производства.
Важнейшие задачи машиностроителей изменение структуры производства повышение качественных характеристик машин и оборудования продолжение работ по созданию законченных систем машин позволяющих применять комплексную механизацию и автоматизацию всего технологического цикла от поступления сырья до отгрузки готовой продукции. Автоматизация и механизация призваны коренным образом преобразить рабочие места сделать труд рабочих более производительным.
В основных направлениях экономического развития указывается на внедрение систем автоматизированного проектирования развитие производства специализированного инструмента использование программных технологий.
Титул КЭ.cdw

Комплект документации
технологического процесса
механической обработки
детали "Ось ролика".
ГОСТ 3.1105-84 форма 2
1 Тех процесс.doc
1 Характеристика заданного типа производства
Согласно ГОСТ 31108-74 тип производства характеризуется коэффициентом закрепления операций т.е. отношению числа различных операций выполняемых в течение месяца к числу рабочих мест. Если это отношение равно единицы то производство массовое от 2 до 10- крупно-серийное а от 10 до 20- среднесерийное.
где О- планируемое число операций;
Р- планируемое число рабочих мест.
Следовательно производство - крупносерийное. Оно характеризуется узкой номенклатурой выпускаемых изделий при большой программе выпуска. При этом оборудование приспособления режущий и мерительный инструмент используется в основном специальные. Квалификация рабочих и стоимость продукции средняя.
Годовая программа выпуска деталей
где N1- годовая программа выпуска изделий шт.;
m- количество деталей в изделии шт;
a- процент запасных частей % ;
b- процент технологической убыли %.
Партия деталей для одновременного запуска определяется упрощенным способом:
где -число рабочих дней хранения деталей на складе;
F=253- число рабочих дней в году.
2 Технико-экономическое обоснование выбора заготовки
Выбрать заготовку – значить установить способ ее получения рассчитать размеры назначить припуски на обработку каждой поверхности и указать допуски на неточность изготовления.
На выбор способа получения заготовок влияют следующие факторы:
– технологическая характеристика материала его свойства определяющие возможность применения литья пластической деформации порошковой металлургии сварки;
– конструктивная форма поверхностей и размеры детали ее масса;
– наличие технологического оборудования;
– социальные условия т.е. безопасность работы экологические факторы;
– суммарная себестоимость изготовления заготовки изготовления из нее детали сборки транспортировки и эксплуатации изделия.
Выбор способа получения заготовки её формы проводим на основе требований чертежа и типа производства.
Заготовки из проката применяют в тех случаях когда конфигурация детали соответствует форме какого-либо сортового (круглого шестигранного квадратного прямоугольного) горячекатаных бесшовных труб различных толщин и диаметров а также профильный прокат (угловая сталь швеллеры и др.) Учитывая все условия для детали «ось ролика» принимаем способ получения заготовки из проката круглого сечения. Материал – сталь 40Х ГОСТ 4543-71. Используя таблицу 1. выбираем сортовой горячекатаный прокат обычной точности по ГОСТ 2590-88.
Таблица 1. Виды и области применения проката
Сортовой горячекатаный
-А – высокой точности;
-Б – повышенной точности;
-В – обычной точности
Гладкие и ступенчатые валы с небольшим перепадом диаметров ступеней; стаканы диаметром до 50 мм; втулки с наружным диаметром до 25 мм
По ГОСТ 2590-88 выбираем диаметр прутка при отношении Ld4 диаметр прутка заготовки d=27 мм. Длину заготовки условно принимаем равной 50±2 мм.
Для определения массы заготовки определим объём заготовки по формуле
где - диаметр заготовки м;
- длина заготовки м.
Используя справочные данные определяем плотность сталь 40Х ρ=78 кгм3 затем определяем массу заготовки умножая плотность на объём.
Определяем стоимость заготовки детали в ценах действующего производства 2009 года.
где Мз - масса заготовки кг;
Мд - масса детали кг;
Цз - цена 1 кг металла рубкг;
Цо - цена отходов рубкг;
Кт - коэффициент класса точности заготовки;
Кс - коэффициент сложности заготовки;
Кв - коэффициент массы;
Км - коэффициент марки детали;
Кп - коэффициент серийности.
Определим стоимость годовой программы заготовок
3 Определение коэффициента использования материала
Выбор заготовки можно достаточно достоверно оценить по коэффициенту использования материала. При этом учитываются следующие рекомендации: в массовом производстве КИМ ≥ 085; в серийном производстве КИМ≥ 05 – 06
Коэффициент использования материала определяется по формуле
где - масса заготовки кг;
Полученный результат удовлетворяет условию КИМ =077≥ 05 – 06 следовательно метод получения заготовки выбран правильно.
4 Разработка маршрута обработки с выбором станочных приспособлений и оборудования
Технологический маршрут обработки заготовки устанавливает последовательность выполнения технологических операций.
На этапе разработки маршрута технологического процесса решаются следующие задачи:
– намечается общий план обработки детали;
– предварительно выбираются средства технологического оснащения;
– намечается содержание операций.
На основе типового технологического процесса изготовления деталей класса тел вращения и с учетом конструктивных особенностей и технических требований к рассматриваемой детали ось ролика маршрут технологического процесса следующий:
Таблица 2 Технологический маршрут механической обработки с выбором станочных приспособлений и оборудования.
5 Токарная автоматная
Токарный прутковый полуавтомат с ЧПУ 1365
Трехкулачковый самоцентрирующийся патрон с механизированным приводом зажима - патрон 7100–0005 ГОСТ 2675–80.
0 Токарно-винторезная с ЧПУ
Токарно-винторезный станок с ЧПУ 16Б16Т1
Трехкулачковый самоцентрирующийся патрон - патрон 7100–0009 ГОСТ 2675–80. Кулачки 7019-8539 центр жесткий упорный ГОСТ 2576–79.
62-8900 собственного изготовления головка револьверная 7760-8807.
Приспособление кондукторное
Продолжение таблицы 2
Трехкулачковый самоцентрирующийся патрон - патрон 7100–0005 ГОСТ 2675–80. Кулачки собственного изготовления
центр жесткий упорный ГОСТ 2576–79.
5 Разработка операционной технологии обработки детали
При проектировании технологических операций решается комплекс вопросов
– уточняется содержание операции (предварительно намеченное в маршруте обработки);
– определяются последовательность и содержание переходов;
– окончательно выбираются средства технологического оснащения;
– устанавливаются режимы резания;
– определяются нормы времени;
– определяются настроечные размеры;
– разрабатываются операционные эскизы;
– определяется разряд и квалификация работы.
Операционный технологический процесс механической обработки детали «Ось ролика» разрабатывается с учётом требований ГОСТ 14.301-83 «Общие правила разработки технологических процессов и выбора средств технологического оснащения» и состоит из следующих операций и вспомогательных переходов:
Технологические операции.
5 Токарная автоматная (Подготовка основных технологических баз и предварительная обработка поверхностей)
Габаритные размеры детали 24 0 49.– 018 кг.
Исходя из габаритов детали ее массы и точности выполнения токарной операции (9 квалитет) выбираем токарный прутковый полуавтомат с ЧПУ 1365 с устройством автоматической подачи прутков.
Выбор средств технологического оснащения.
Приспособления для установки и закрепления прутка.
Исходя из присоединительных размеров станка мод. 1365 установка и закрепление заготовки осуществляется в трехкулачковом самоцентрирующем патроне ( 160) с механизированным приводом зажима – патрон 7100–0005 ГОСТ 2675–80 выбираем исходя из назначения и присоединительных размеров станка приспособлений и вспомогательной оснастки. Так в револьверной головке поперечного суппорта станка мод. 1365 при помощи съёмных кассет может закрепляется до восьми режущих инструментов.
Режущий инструмент.
Резец подрезной отогнутый с пластинкой из твердого сплава – резец 2112–0035 ВК8 ГОСТ 18880–73; резец проходной упорный с пластинкой из твердого сплава – резец 2103–0007 ВК8 ГОСТ 18880–73; резец отрезной с пластинкой из твердого сплава – резец 2100–0009 ВК8 ГОСТ 18879–73; сверло центровочное А63 ГОСТ 14952–75; сверло спиральное с цилиндрическим хвостовиком 4 ГОСТ 10903–77.
Средства технического контроля.
Штангенциркуль ШЦ – I – 125 – 01 ГОСТ 166–89.
Содержание операции.
Прутки загружаются в устройство подачи обрабатываемый пруток закрепляется в трехкулачковом патроне с гидроприводом зажима на длину 65 мм от торца кулачков. подача прутка автоматизирована.
Подрезать торец прутка. 2. Точить заготовку до диаметра 25 мм на длину 52 мм. 3. Точить 18 на длину 28. 4.Сверлить отверстие А63 ГОСТ 14034–74. 5. Сверлить отверстие 4 на глубину 25 мм. 6. Отрезать заготовку в размер 52±1 мм.
0 Токарно-винторезная с ЧПУ (Чистовая обработка поверхностей)
Станок. Токарно-винторезный станок с ЧПУ 16Б16Т1.
Установка и закрепление заготовки осуществляется в трехкулачковом самоцентрирующимся патроне с поджатием жестким центром при установе Б установленном в задней бабке.
Средства технологического оснащения.
Трехкулачковый самоцентрирующийся патрон - патрон 7100–0009 ГОСТ 2675–80. Кулачки 7019-8539. Центр жесткий упорный ГОСТ 2576–79.
Резец проходной отогнутый правый (φ=60о) с пластинкой из твердого сплава – резец 2102 –0005 Т15К6 ГОСТ 18877–73; резец проходной отогнутый левый (φ=60о) с пластинкой из твердого сплава – резец 2102 –0006 Т15К6 ГОСТ 18877–73; резец канавочный специальный b=3 мм (собственного изготовления); резец отогнутый (φ=45о) с пластинкой из твердого сплава – резец 2114–0035 ВК8 ГОСТ 18880–73.
Установ А. 1. Точить 165 и торец выдерживая размер 28. 2. Точить канавку 155 шириной 3 мм 3. Снять фаску 1045°.
Установ Б. 1. Точить 245 напроход. 2. Точить уступ с 245 до 205 выдерживая размер 3. Точить канавку 195 шириной 3 мм. 4. Точить фаску 1 0 45о.
Операционные эскизы.
5 Вертикально-сверлильная. (Зенкерование отверстия и нарезание резьбы М5).
Станок. Вертикально-сверлильный 2Н118.
Установка и закрепление заготовки осуществляется в специальном приспособлении.
Приспособление 7362-8900 собственного изготовления головка револьверная 7760-8807.
Сверло-зенкер комбинированный с коническим хвостовиком – сверло-зенкер собственного изготовления; метчик машинно-ручной для нарезания метрической резьбы –метчик М5008 ГОСТ 3266–81.
Штангенциркуль ШЦ – I – 125 – 01 ГОСТ 166–89; калибр-пробка резьбовая двухсторонняя М5008
Рассверлить отверстие 4 до 42 под резьбу и одновременно зенкеровать выдерживая размеры 35 38 8 и угол 60° . 2. Нарезать резьбу М 5 на глубину 13 мм.
0 Вертикально-сверлильная. (Сверление 2 отверстий на цилиндрических поверхностях).
Вертикально-сверлильный 2Н118.
Средства технологического оснащения.
Приспособление кондукторное 7362-8806 патрон 7160-8807.
Сверло спиральное с цилиндрическим хвостовиком – сверло 2301–0400 ГОСТ 10903–77; зенковка коническая с углом при вершите 90о с цилиндрическим хвостовиком – зенковка 8 ГОСТ 14953–80.
Штангенциркуль ШЦ – I – 125 – 01 ГОСТ 166–89; калибр-пробка гладкая двухсторонняя 4 мм.
Установ А. 1. Сверлить отверстие 42 до пересечения с отв. 4.2 выдерживая размер 35. 2. Зенковать отверстие 8 угол 90°. 3. Сверлить отверстие 4 до пересечения с отв. 4.2 выдерживая размер 15 мм.
Установ Б. Повернуть деталь на 180°. Засверлить отверстие 65 выдерживая угол 90°и размер 16 мм.
5 Слесарная (Зачистка заусенцев и снятие острых кромок).
0 Промывочная (Очистка от загрязнений горячим содовым раствором).
5 Контрольная (Промежуточный контроль – выборочно из партии).
0 Термическая (Закалка).
5 Круглошлифовальная (Подготовка поверхностей под нарезание шлицев)
Круглошлифовальный станок 3В151А
Установка и закрепление заготовки осуществляется в трёхкулачковом самоцентрирующемся патроне с поджимом упорным центром с выверкой по индикатору.
Трехкулачковый самоцентрирующийся патрон - патрон 7100–0005 ГОСТ 2675–80. Кулачки собственного изготовления центр жесткий упорный ГОСТ 2576–79.
Круг шлифовальный ПП 500 х 63 х 32; 15А40С27К ГОСТ 2424–83.
Средства технического контроля
Микрометр гладкий МК 50 – 75 ГОСТ 6507–90; МК 75 – 100 ГОСТ 6507–90. Образцы шероховатости.
Шлифовать 16Н7 2. Шлифовать 20Н7.
Оборудование. Стол контролера. Плита поверочная 400 х 400 ГОСТ 10905–86. Стойка С-II ГОСТ 10197–70. Штатив с магнитным основанием – ШМ – IIВ. Центра ПБ – 500М ТУ 2-034-543 – 81.
Скоба рычажная СР 50–75 ГОСТ 11098–75; СР 75–100 ГОСТ 11098–75.
Индикаторный нутромер НИ - 100М ГОСТ 868–82.
Штангенциркуль ШЦ – II – 400 – 005; штангенциркуль ШЦ – II – 200 – 005; штангенциркуль ШЦ – I – 125 – 01 ГОСТ 166–99.
Индикатор часового типа ИЧ 10 ГОСТ 577–68.Индикатор многооборотный 2МИГП ГОСТ 9696–82.
Нормалемер БВ – 5045 ГОСТ 5368–81.
Образцы шероховатости
Контролировать размеры: 165Н7 20Н7 8195; 155-02 42 отв. М5; линейные размеры: 49 28 38 3513 16; 18 3 5.
Шероховатость поверхности Ra= 32; Rz=40.
Выбор и обоснование технологических баз
При разработке технологических операций необходимо особое внимание уделить выбору баз для обеспечения заданной точности обработки детали и выполнения требований чертежа.
При выборе баз необходимо применять поверхности не подлежащие обработке а если деталь имеет несколько необработанных поверхностей то за базу надо принимать ту из них которая имеет наименьшее смещение относительно своей оси или быть с наименьшими припусками на обработку.
При выборе баз необходимо принимать те на которые дан размер на чертеже определяющий положение обрабатываемой поверхности.
Базы должны обеспечивать отсутствие недоступных деформаций детали а также простоту конструкции станочного приспособления с удобной установкой закреплением и снятием обрабатываемой детали.
Базовые поверхности на операции механической обработки детали ось ролика указаны в таблице 2.1.
Таблица 3 Базовые поверхности
Цилиндрическая поверхность прутка
Установ А: Подрезанный торец заготовки 25 мм.
Установ Б: Подрезанный торец заготовки 165Н11 мм.
Подрезанный торец заготовки 205 мм 165Н11 мм .
Подрезанный торец заготовки 205 Н11мм 165Н11 мм .
Продолжение таблицы 3
Отверстие 8060° головка 24 торец.
Определение припусков и межоперационных размеров и допусков на них табличным методом.
При определении припусков по табличному (опытно-статистическому) методу общий и операционные припуски берутся по таблицам справочных данных составленных на основании обобщения и систематизации производственных наблюдений ряда предприятий.
Припуски устанавливаются на номинальные размеры деталей указанных на чертеже На основании результатов определения припусков для рассчитываемых поверхностей вращения одного линейного размера и отверстия под резьбу определяются межоперационные размеры и допуски на них. Полученные данные указаны в таблице 4.
Таблица 4 Припусков операционные размеры и допуски при обработке оси ролика длиной 49 мм
Маршрут обработки поверхности
Экономическая точность
Операционный размер мм
Припуск на диаметр мм
Обработка поверхности оси ролика из стали 40Х - 16 Н7
Заготовка – сортовой горячекатаный прокат обычной точности по ГОСТ 2590-88.
Обработка за три прохода.
Припуск на один проход
Продолжение таблицы 4
Обработка поверхности оси ролика из стали 40Х - 20 Н7
Точение получистовое
Подрезка торцев оси из стали 40Х в размер 49Н10
Сверление отверстия 42Н7 под резьбу М5008
Сверление получистовое
Назначение режимов резания
Режимы резания – совокупность глубины резания (t) подачи (S) и скорости резания (V).
Режимы резания (обработки) определяют: точность обработки качество обработанной поверхности производительность и себестоимость обработки условия работы оборудования и рабочих.
Факторами влияющими на выбор режима резания являются:
– материал форма жесткость и прочность обрабатываемой заготовки;
– вид режущего инструмента материал его режущей кромки жесткость и прочность;
– способ закрепления заготовки на станке;
– мощность главного привода станка.
В порядке возрастания влияния на стойкость инструмента составляющие режимов резания располагаются в следующей последовательности: t S V и назначаются согласно существующей методике по справочным материалам и литературе].
Выбранный по справочникам режим резания корректируется по паспортным данным станка проверяется по мощности и должен удовлетворять условию:
где N – мощность потребная на резание кВт;
Nэ – эффективная мощность станка кВт (определяется по паспорту станка).
Если выбранный режим резания не отвечает указанным условиям необходимо величину скорости резания понизить соответственно величине допускаемой мощностью станка. Режимы резания на операции механической обработки детали «ось ролика» указаны в таблице 5.
При точении и растачивании определяют силу резания Pz. Н; при сверлении зенкеровании круглом шлифовании определяют крутящий момент МКР Н.
Для назначения режимов резания используем справочные данные [3]. Режимы резания на операции механической обработки детали «ось ролика» указаны в таблице 5 составленную в редакторе Ms Excel.
Таблица 5 Свободная таблица режимов резания
Нормирование технологического процесса
После определения содержания операций выбора оборудования инструментов назначения режимов резания определяются нормы времени в следующей последовательности.
На основании рассчитанных режимов работы оборудования по каждому переходу (обрабатываемой поверхности) вычисляется основное (технологическое) время обработки (табл. 53 – 64 [10]).
По содержанию каждого перехода (обрабатываемой поверхности) устанавливается необходимый комплекс приемов вспомогательной работы и определяется вспомогательное время путем суммирования его элементов (табл. 67 – 71 88[11]). Вспомогательное время на установку и снятие детали учитывается для каждой технологической операции один раз. Как правило это время учитывается в первом технологическом переходе (обрабатываемой поверхности).
По каждой технологической операции определяется оперативное время обработки детали по формуле
В зависимости от точности детали и средства измерения по табл. 88[10] устанавливается вспомогательное время на контрольные измерения.
По нормативам в зависимости от операций и оборудования устанавливается время на обслуживание рабочего места отдых и естественные надобности по табл.89[10].
Определяется штучное время на технологическую операцию по формуле:
где - основное (машинное)время мин;
-вспомогательное время мин;
-время на организационное обслуживание в % от ;
- время на отдых и личные надобности рабочего в % от ;
- время перерывов обусловленных технологией в % от ;
- время на техобслуживание рабочего места в % от ;
-оперативное время мин.
По табл. 90[11] определяется подготовительно-заключительное время обработки партии деталей .
Определяется норма времени в виде штучно-калькуляционного времени по формуле
где - штучное время мин;
- подготовительно-заключительное время мин*;
-число деталей в партии шт.
*Примечание: Подготовительно-заключительное время зависит от сложности задания наладки оборудования и не зависит от размера партии деталей.
Полученные справочные данные сводятся в таблицу 6 составленную в редакторе Ms Excel для расчёта.
Таблица 6 Сводная ведомость норм времени на операции механической обработки детали ось ролика.
Основное (машинное) время мин
Вспомогательное время мин
Установка и снятие детали
Связанное с переходом
Изменение числа оборотов
Контрольные измерения
Подрезать торец прутка
Сверлить отверстие А63 ГОСТ 14034 - 74
Сверлить отверстие 4
Продолжение таблицы 6
Отрезать заготовку в размер 52
Оперативное время мин
Подготовит.-заключит. времяпартию дет. мин
Штучно-калькуляционное время мин
Точить уступ с 245 до 205
5 Вертикально-сверлильная
Рассверлить отверстие 4 до 42 и одновременно зенкеровать на глубину 35 мм.
0 Вертикально-сверлильная
Сверлить отверстие 42
Зенковать отверстие 8.
Засверлить отверстие 65
Окончание таблицы 6.
5 Круглошлифовальная
Общая трудоёмкость изготовления детали час
Курсовой проект по предмету «Технология машиностроения» выполнен в полном объеме. На основании исходных данных спроектирован технологический процесс изготовления детали «ось ролика».
Проект разработан на основе современных достижений в области машиностроения и теории резания с возможностью использования инструментов изготовленных из современных инструментальных материалов и сплавов. Расчёты и оформление проводились с применением средств вычислительной техники. В спроектированном техпроцессе предложены: применение высокопроизводительного оборудования оснастка и приспособления с механизированными приводами зажимных элементов гарантирующих постоянство усилия зажима детали высокопроизводительные и объективные методы контроля.
Курсовой проект выполнен на основе объективных справочных данных.
Список используемых источников
Ананьев С.Л. Технологичность конструкции М.: Машиностроение 1969 г. 420 с.
Ансеров М.А. Приспособления для металлорежущих станков М.: Машиностроение 1968 г. 652 с.
Барановский Ю.В. Режимы резания металлов М.: Машиностроение 1972 г. 408 с.
Горбацевич А.Ф. Курсовое проектирование по технологии машиностроения Минск: Высшая школа 1983 г.288 с.
Данилевский В.В. Справочник техника машиностроения М.: Высшая школа 1984 г. 416 с.
Добрыдиев М.С. Курсовое проектирование по предмету "Технология машиностроения" М.: Машиностроение 1995 г. 480 с.
ЕСДП СЭВ в машиностроении и приборостроении М.: Издательство стандартов 1987 г. 30 с.
Панов А.А. Обработка металлов резанием М.: Машиностроение 1972 г. 408 с.
Рубинштейн С.А. Основы учения о резании металлов и режущий инструмент М.: Машиностроение 1988 г.528 с.
Стародубцева В.С. Сборник задач по техническому нормированию в машиностроении М.: Машиностроение 1974 г.458 с.
Справочник технолога в 2-х томах. Т2. под ред. Дальского А.М. Косиловой А.Г. и др. М.: Машиностроения 2001. 943 с.
оп. 010.cdw

оп. 020-2.cdw

оп. 005.cdw

оп. 020.cdw

Рекомендуемые чертежи
- 24.01.2023
- 24.01.2023