Разработка техпроцесса и средств технологического оснащения для изготовления детали корпус




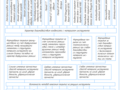
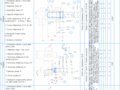
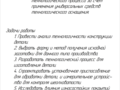
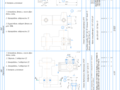
- Добавлен: 24.01.2023
- Размер: 3 MB
- Закачек: 1
Описание
Состав проекта
![]() |
![]() |
![]() ![]() ![]() ![]() |
![]() ![]() ![]() ![]() |
![]() |
![]() ![]() ![]() ![]() |
![]() ![]() ![]() ![]() |
![]() ![]() ![]() ![]() |
![]() ![]() ![]() ![]() |
![]() ![]() ![]() ![]() |
![]() ![]() ![]() |
![]() ![]() ![]() ![]() |
![]() ![]() ![]() ![]() |
![]() ![]() |
![]() ![]() ![]() ![]() |
![]() ![]() ![]() ![]() |
![]() ![]() ![]() |
![]() ![]() ![]() ![]() |
Дополнительная информация
Деталь.cdw

*Размеры указанный после покрытия.
Покрытие: Ан. Окс. хр.
от резьбообразующего инструмента.
Поверхность на длине L испытать:
на прочность воздухом при давлении 10
на герметичность воздухом при давлении 9
Разработка технологии и технологического оснащения
для изготовления корпуса клапана ракетного двигателя
Первый лист.cdw

оснащения для изготовления корпуса клапана
Цель работы: усовершенствование действующего
технологического процесса за счет
применения универсальных средств
технологического оснащения.
Провести анализ технологичности конструкции
Выбрать форму и метод получения исходной
заготовки для данного типа производства.
Разработать технологический процесс для
изготовления детали.
Спроектировать установочное приспособление
для обработки детали
и измерительное устройс-
тво для контроля шеолховатости.
Исследовать влияния износостойких покрытий
на свойства режущего инструмента и режимы
Провести технико-экономический анализ
эффективности разработанного технологи-
Карта ТП.frw

корпус воздушного клапана
Установить деталь и после обра-
Центровать торец (9)
Сверлить отверстие (4)
Точить поверхности (7)
Точить поверхности (1)
Точить поверхность (2)
Притупить острые кромки
внутр. диам. резьбы после нарезания
после нарезки резьбы
Резец подрезной ГОСТ 18871; Сверло центровочное ГОСТ 13214-67;
Сверло спиральное ГОСТ10903-77; Резец расточной ГОСТ 18883-73
ГОСТ166-73; РГ-250 ГОСТ162-73; Пробка
ГОСТ18362-73; Пробка
ГОСТ18362-73; Нутромер
ГОСТ18362-73; ШГ сп. ГОСТ7470-78; Нутромер
Сверлить отверстие (1)
Расточить отверстие (1) под
Расточить отверстие (2) угол 45
Расточить отверстие (3)
Притупить острые кромки фаской
или любой кривой R=0
Резец подрез. ГОСТ 18871-73; Сверло спирал.
Резец расточ. ГОСТ18883-73; Резец канавочный ГОСТ18879-73
ГОСТ18362-73; ШГ 250 ГОСТ7470-78;
ГОСТ18362-73; Меритель
ИЧ 10 кл.1 ГОСТ1356-79;Планка ГОСТ112-73; Вставка ГОСТ110-73
Расточить отверстие (2) под
Расточить отверстие (1)
Расточить отверстие (3) и
Расточить барабан (4)
Резец расточ. ГОСТ18883-73; Резец резьбонар. ГОСТ18885-73
Фаскомер ГОСТ1356-79; Резьбовой калибр М22
Нутромер ГОСТ 18362-73
Наименование операции
Станок ток. винторезний 1Е61М
Патрон 3-х кулачковый ГОСТ 2675-80
Угольник ГОСТ 16468-73; Наладка специальная
Карта ТП2.frw

Обработать поверхн.(3)
Повернуть деталь со столом на
; Обработать поверхн. (2)
Центровать 2 отв. (7)
Зенкеровать 2 отв. (7)
Зенкеровать 2 отв. (6)
ГОСТ 8720-69; Фреза
Сверло центровочное
ГОСТ 13214-67; Сверло спиральное
ГОСТ 12489-67; Зенке
ГОСТ166-73; РГ-250 ГОСТ162-73; Пробка
ГОСТ18362-73; Пробка
ГОСТ18362-73; Меритель l=36
ГОСТ18362-73; Меритель l=18 ГОСТ18362-73
Фрезеровать поверхность (1);
Осуществить поворот детали на
Фрезеровать поверхность (2).
Резьбовая оправка ГОСТ 162-70; Угольник ГОСТ 16468-73;
Делит. головка ГОСТ1647-73
Сверлить 8 отверстий (1) последо-
Контроль исполнения.
Сверлить 2 отверстия (2);
Зенкеровать 2 отверстия (2);
Зенкеровать 2 отверстия (1);
ГОСТ 166-73; ШГ-250 ГОСТ162-73
ГОСТ10903-77; Зенкер
Комбинированная с ЧПУ
Станок комбинированный ИР-320 ПМФ4
Наладка специальная с поворотным столом
Станок вертикально фрезерный 6Р13
Станок вертикально сверлильный 2Н125
Кондуктор ГОСТ 16751-73
Угольник с наладкой.cdw

Максимальная высота и диаметр обраба-
Технические требования:
Перед обработкой детали отбалансировать угольник
вместе с наладкой при помощи грузов массой 2 кг.
Перед обработкой проверить размер 55
При работе пользоваться защитным кожухом станка.
Разработка технологии и технологического оснащения
для изготовления корпуса клапана ракетного двигателя
Исследов. 1.cdw

Химико-термические методы
образования покрытий
Методы химического осаждения
покрытий из парогазовой фазы
осаждения (конденсации)
покрытия из пароплаз-
Электроискровое легированме
Ионное азотирование в плазме
Ионная цементация в плазме
Диффузионное насыщение из
жидкой или газовой среды
Термодиффузионное насыщение
поверхности твердого сплава
из твердой фазы (метод ДТ)
Метод GT (SANDVIC COROMANT)
Метод вакуумного титаниро-
Конденсация покрытия из плаз-
менной фазы с ионной бомбар-
дировкой (метод КИБ)
Реактивное электронно-лучевой
осаждение покрытия из пароплаз-
менной фазы в вакууме (метод СЭП)
Активированное реактивное
напыление (метод ARE)
Ионизированное реактивное
Детонационное напыление
Характер взаимодействия конденсата с материалом инструмента
Формирование покрытия преиму-
щественно за счет диффузионных
реакций между насыщающими
элементами и структурами
материала инструмента при
сильном влиянии последних на
характер диффузионных реакций
Формирование покрытия за
счет химической реакции
между элементами парога-
зовых смесей и интердиф-
фузионных реакций между
компанентами парогазовой
материала инструмента
Возможности методов нанесения покрытий на режущие инструменты
Сильное изменение прочностных
свойств материала инструмента
Среднее изменение прочностных
Слабое изменение прочностных
Инструменты из углеродис-
легированных углеро-
дистых и быстрорежущих
инструментальных сталей
с любой формой режущей
Твердосплавные пластин-
Твердрсплавные плас-
монолитно-твердосплав-
любой формой режущей
рарзмерного инстремента
ограниченной прочности)
Твердосплавные плас-
требуются перемещения
Средство активного контроля.cdw

Диапазон диаметров контролируемых отверстий
Параметр измеряемой шероховатости поверхности Ra
контроля шероховатости
цилиндрических отверстий
Разработка технологии и технологического оснащения
для изготовления корпуса клапана ракетного двигателя
ДИПЛОМ3.doc
ВОРОНЕЖСКИЙ ГОСУДАРСТВЕННЫЙ ТЕХНИЧЕСКИЙ УНИВЕРСИТЕТ
(фамилия имя отчество)
на выпускную квалификационную работу
Тема дипломного проекта: Разработка технологии и технологического оснащения для изготовления корпуса клапана ракетного двигателя
утверждена распоряжением по факультету № от « » 2011 г.
Технические условия: согласно техническому заданию режим работы участка – односменный программа выпуска корпуса – 2000 штук в год. .
Содержание (разделы графические работы расчеты и проч.) Графическая часть: 1) цели и задачи дипломного проектирования; 2) рабочий чертёж детали; 3) чертёж заготовки с твердотельной моделью; 4) чертёж приспособления для активного контроля; 5) карты технологического процесса обработки детали; 6) угольник с наладкой; 7) методы нанесения покрытий на режущий инструмент; 8) влияние износостойких покрытий на свойства режущего инструмента; 9) технико-экономические показатели спроектированного участка; 10) организационный вопрос по экономике; 11) план участка.
Расчётно-пояснительная записка: 1) производственно-технологическая часть; 2) проектно-конструкторская часть; 3) научно-исследовательская часть; 4) эксплуатационная часть; 5) организационно-экономическая часть;
План выполнения дипломного проекта дипломной работы
С « 26 » марта 2007 г. по « 1 » июня 2007 г.
Название элементов проектной работы
Подпись рук консульт.
Производственно-технологическая часть
Проектно-конструкторская часть
Научно-исследовательская часть
Эксплуатационная часть
Экономическая и организационно-управленческая часть
Комплект карт технологического процесса
Руководитель дипломного проекта дипломной работы
(подпись дата) (фамилия имя отчество)
Дипломный проект дипломная работа закончен(а)
(подпись дипломника)
Пояснительная записка и все материалы просмотрены
Оценка руководителя Кузовкин .
(подпись) (инициалы фамилия)
Допустить дипломникаСмолянов Д.А.
к защите дипломного проекта дипломной работы в Государственной аттестационной комиссии (протокол заседания кафедры №
Назначить защиту на « »2007 г.
Завидущий кафедройА.И. Болдырев .
(подпись)(инициалы фамидия)
Декан факультета В.М. Пачевский .
Пояснительная записка 106 с. 30 таблиц 32 источника 3 приложения.
КОРПУС ТЕХНОЛОГИЯ ТЕХНОЛОГИЧЕСКОЕ ОСНАЩЕНИЕ РЕЖИМЫ ОБРАБОТКИ РАСЧЕТ ПРИСПОСОБЛЕНИЯ ЭКОНОМИЧЕСКАЯ ЭФФЕКТИВНОСТЬ.
Объект исследования или разработки – технология и технологическое оснащение производства корпуса клапана ракетного двигателя
Цель работы – Разработка технологии и технологического оснащения для обработки корпуса; численное проектирование эффективной операционной технологии; численное обоснование метода изготовления заготовки; численное формирование состава переходов и операций; расчёт операционных припусков и предельных размеров; расчёт режимов обработки; техническое нормирование операций.
Полученные результаты и их новизна – в данном дипломном проекте были решены основные задачи поставленные для достижения повышения производительности труда в условиях средне серийного производства. Используя основные направления в современной технологии машиностроения был выбран метод получения заготовки что дало возможность значительно снизить трудоемкость обработки детали на металлорежущих станках а также сократить расход металла. Применение станков с числовым программным управлением приспособлений с быстродействующими зажимами позволило повысить производительность труда. Снижение трудоемкости перемещения детали между рабочими местами было учтено при разработке участка механической обработки что позволило достигнуть лучших технико-экономических показателей по сравнению с существующими на заводе.
Экономическая эффективность или значимость работы – экономический эффект от производства продукции с применением разработанного в дипломном проекте технологического процесса за расчётный период составит 21954 тысяч рублей.
Производственно-технологическая часть7
1 Анализ служебного назначения детали и условий её работы7
2 Анализ базового технологического процесса7
3 Анализ исходных данных8
4 Определение типа организации производства на участке9
5 Отработка конструкции детали на технологичность11
6 Установление вида заготовки и метода ее изготовления15
7 Выбор технологических базовых поверхностей18
8 Выбор методов и определения последовательности обработки поверхностей заготовки19
9 Расчет операционных припусков и предельных размеров22
10 Расчет режимов обработки26
11 Выбор оборудования и приспособлений34
Проектно-конструкторская часть38
1 Конструкция установочного приспособления и его расчет38
1.1 Силовой расчет38
1.2 Точностной расчет приспособления40
2 Разработка технологической планировки участка по обработке детали корпус43
2.1 Состав механического цеха43
2.2 Расчет количества основного оборудования по станкоемкости механической обработки44
2.3 Расчет количества производственных и вспомогательных рабочих46
2.4 Расчет площади складов заготовок и готовых деталей на участке цеха46
2.5 Выбор транспортного оборудования47
2.6 Системы транспортирования стружки48
2.7 Общая планировка оборудования и рабочих мест в механическом участке49
Научно-исследовательская часть51
1 Патентно-информационный поиск51
2. Влияние износостойких покрытий на свойства режущего инструмента54
2.1 Методы нанесения покрытий на режущий инструмент54
2.2 Влияние толщины покрытия на процессы резания58
Эксплуатационная часть63
1 Экология и техника безопасности63
1.1 Энергетические загрязнения окружающей среды63
1.2 Организация трудового процесса64
Экономическая и организационно-управленческая часть67
1 Экономическое обоснование принимаемых в дипломном проекте решений67
1.1 Экономическое обоснование выбора заготовки67
1.2 Экономическая оценка вариантов технологического процесса69
2 Организационно-экономическая часть дипломного проекта88
2.1. Экономическое обоснование проекта участка88
2.2 Определение потребности в инвестициях для организации проектируемого участка89
2.3 Расчет текущих затрат (плановой себестоимости продукции)92
2.4 Расчет технико-экономических показателей проектируемого участка и их анализ95
3 Расчет показателей экономической эффективности цеха (участка)97
4 Структура и состав механического цеха101
Список литературы104
Приложение А Графическая часть 108
Приложение Б Спецификации к графической части проекта 120
Приложение В Комплект карт технологического процесса 126
В процесс развития машиностроения потребовал применение более универсальных средств технологического оснащения и повышения надежности и точности обрабатываемых деталей. Разработка технологического процесса изготовления деталей занимает основные позиции в машиностроительном производстве. Применение устаревшего оборудования потребовало использование квалифицированных специалистов для достижения требуемых размеров и чистоты поверхности деталей. Требования к режущему инструменту возросли и с этой целью проводится исследования влияний покрытий.
Целью дипломного проектирования является модернизация технологического процесса и средств технологического оснащения используемых в условиях серийного производства. Для достижения указанной цели были поставлены следующие задачи:
провести анализ технологичности конструкции детали;
выбрать форму и метод получения исходной заготовки для данного типа производства;
разработать технологический процесс для изготовления детали;
спроектировать установочное приспособление для обработки детали провести точностной и силовой расчет;
провести исследование по теме "Влияние износостойких покрытий на свойства режущего инструмента и режимы обработки детали";
провести технико-экономический анализ эффективности разработанного технологического процесса.
1 Анализ служебного назначения детали и условий её работы
Корпус предназначен для размещения в нем воздушного клапана ракетного двигателя и передачи рабочей среды в зону горения топлива.
Корпус представляет собой систему внутренних цилиндрических поверхностей с возможностью совмещения его с зоной горения топлива ракетного двигателя. К штуцеру с резьбой большего диаметра подводится управляющее давление до 70 МПа для приведения сифонного механизма в действие. Данный корпус изготовлен штамповкой с последующей механической обработкой. Так как рассматриваемое изделие ответственный узел то во время штамповки не допускается появление крупнокристаллического ободка. В результате последующих обработок необходимо достигнуть шероховатости поверхности корпуса не меньше чем Ra = 63 мкм.
2 Анализ базового технологического процесса
Базовый технологический процесс сориентирован на единичный тип производства. Оборудование применяемое при обработке детали дозагружено большим количеством других деталей и предназначено для выполнения на нем большого числа операций. Станки размещены по группам и транспортирование деталей от одной операции к другим занимает много времени. Заготовка для детали производится в другом цехе на участке горячей штамповки. Большинство видов оборудования сильно изношены и для достижения заданной точности размеров приходится проводить обработку при более мягких режимах и в несколько проходов. Большинство приспособлений предназначено только для данного вида деталей что увеличивает стоимость детали во много раз из-за невозможности его применения при обработке других типов деталей.
При анализе базового технологического процесса было выявлено несколько недостатков:
применение изношенного оборудования снижающего скорость обработки и точность изготовления заданных размеров;
применение специального приспособления и невозможность его использования при обработки других деталей;
перемещение детали по операциям занимает много времени из-за группового расположения оборудования.
3 Анализ исходных данных
Приведенная в задании деталь относится к корпусным деталям узлов машин и служит базовой деталью при сборке. Материал детали – сплав алюминия АК6-ПП по ГОСТ 21488-97 содержащий :
- марганец: Mn = 04 – 1%;
- медь: Cu = 39 – 48%;
- магний: Mg = 04 – 08%;
- алюминий: Al = 909 – 947%.
Данный сплав алюминия является деформируемым сплавом. Применяется для горячей штамповки различных деталей после закалки и искусственного старения. Равнопрочен дуралюмину но имеет более высокий предел текучести Т = 300 МПа и предел прочности ВР = 410 МПа и более пластичен при горячем и холодном деформировании. В сплаве АК6-ПП кремний является обязательным компонентом обеспечивающим высокий эффект упрочнения при искусственном старении. Сплав АК6-ПП рекомендуют для тяжелонагруженных штампованных деталей а также для деталей сложной формы и средней прочности.
Заданная деталь характеризуется простой конфигурацией и образована простыми геометрическими поверхностями которые могут быть использованы в качестве установочных баз при первой механической обработке. Основная масса размеров выполнена по квалитетам H14 и h14 и имеет шероховатость Ra=40 мкм.
Остальные требования к поверхностям по точности и шероховатости могут быть удовлетворены использованием методов чистового растачивания и фрезерования.
4 Определение типа организации производства на участке
Тип производства во многом предопределяет формы организации производственного процесса и в соответствии с ГОСТ 3.1108-74 характеризуется коэффициентом закрепления операций [10]
где - число операций выполняемое на
- количество рабочих мест на участке.
Тип производства зависит от двух факторов а именно: заданной программы выпуска и трудоемкости изготовления изделия.
На основании заданной программы рассчитывается такт выпуска изделия миншт по формуле
где - действительное годовое число часов работы одного станка;
N – годовая программа выпуска деталей шт.
Подставляя численные значения в формулу (1.2) находим
= 60 × 1930 2000 = 579 (миншт).
Трудоемкость изготовления детали определяется средним штучным временем (Tшт.ср.) по операциям действующего на производстве технологического процесса. Формула для расчета среднего штучного времени имеет следующий вид
где - суммарная трудоемкость изготовления детали;
n - число технологических операций.
Подставляя численные значения в формулу (1.3) находим
Тшт.ср. = 37726 36 = 1048 (мин.).
Отношение величины такта выпуска к среднему значению штучного времени называют коэффициентом серийности т.е.
Kc = (Тшт.ср.). (1.4)
Подставляя численные значения в формулу (1.4) находим
Для крупносерийного производства значение коэффициента серийности находится в диапазоне Кс = 1 - 10 из чего следует что процесс изготовления корпуса при программе выпуска N = 2000 штгод соответствует крупносерийному типу производства.
Для крупносерийного производства величину партии деталей определяют по уравнению
где N - количество деталей по годовой программе вместе с запасными частями шт;
t - число дней на которое необходимо иметь запас деталей на складе; согласно рекомендациям принимаем t = 2 дня;
Ф - число рабочих дней в году; для определения размера партии деталей принимаем Ф = 240 дней.
Подставляя численные значения в формулу (1.5) находим
n = 2000 × 2 240 = 17 (шт).
5 Отработка конструкции детали на технологичность
В общем случае к конструкциям деталей предъявляются следующие требования :
- конструкция детали должна состоять из стандартных и унифицированных конструктивных элементов и быть стандартной в целом;
- детали должны изготовляться из стандартных или унифицированных заготовок;
- размеры и поверхности детали должны иметь соответственно оптимальные т.е. экономически и конструктивно обоснованные точность и шероховатость;
- физико-химические и механические свойства материала жесткость детали ее форма и размеры должны соответствовать требованиям технологии изготовления хранения и транспортировки;
- показатели базовой поверхности детали (точность шероховатость) должны обеспечивать точность установки обработки и контроля;
- заготовки должны быть получены рациональным способом с учетом заданного объема выпуска и типа производства;
- метод изготовления должен обеспечивать возможность одновременного изготовления нескольких деталей;
- сопряжения поверхности деталей различных классов точности и шероховатости должны соответствовать применяемым методам и средствам обработки;
- конструкция детали должна обеспечивать возможность применения типовых и стандартных технологических процессов ее изготовления.
Указанные требования являются обобщением опыта проектирования и изготовления деталей а степень соответствия этим требованиям характеризует конструктивно-технологический уровень детали.
Количественно технологичность конструкции корпуса может быть оценена совокупностью показателей технологической рациональности и преемственности детали. В число этих показателей входят: коэффициент сложности конструкции детали; коэффициент применяемости унифицированных или стандартных конструктивных элементов детали; коэффициент повторяемости конструктивных элементов детали; коэффициент точности и шероховатости поверхности детали; коэффициент обрабатываемости детали и коэффициент использования материала при механической обработке .
Коэффициент сложности конструкции детали определяется выражением в виде
где - коэффициенты определяемые как
Коэффициент зависит от количества поверхностей на исходной заготовке с которых удаляется стружка при изготовлении детали. При этом комбинированные поверхности образуемые за один рабочий ход одним инструментом учитываются в качестве одной поверхности.
Для существующей конструкции корпуса
где - количество обрабатываемых резанием и общее количество формообразующих поверхностей детали соответственно.
Подставляя численные значения требуемых показателей из чертежа детали и технологического процесса обработки детали резанием в выражения (1.8) и (1.7) находим
Коэффициент учитывает общее количество заданных на чертеже данных по обеспечению требуемых точностей формы и взаимного расположения поверхностей в пределах 005 мм.
где - количество поверхностей детали к которым предъявляются требования по точности формы и их взаимному расположению в пределах 005 мм.
Подставляя численные значения требуемых показателей из чертежа детали в выражения (1.9) и (1.7) находим
Ар=2278=028 и Кр=100-028=072.
Коэффициент учитывает количество различных видов обработки резанием (технологических операторов).
Для существующей конструкции корпуса воздушного клапана
где - количество технологических операторов;
- общее количество технологических переходов обработки резанием.
Подставляя численные значения требуемых показателей из карт технологического процесса обработки детали резанием в выражения (1.10) и (1.7) находим
Коэффициент учитывает соответствие точности и шероховатости поверхностей детали некоторым оптимальным величинам под которыми подразумеваются рекомендуемые в качестве экономичности и конструктивно обоснованные величины. Величина входящая в выражение для этого коэффициента определяется по формуле
где - количество зон на которых параметр для j-ой поверхности отстоит от оптимального сочетания.
Подставляя численные значения требуемых показателей из чертежа детали в выражения (1.11) и (1.7) находим
Согласно выражению (1.6) коэффициент сложности конструкции детали будет составлять
Ксл=025(042+072+087+03)=05775.
Коэффициент применяемости унифицированных или стандартных конструктивных элементов детали определяют по формуле
где - общее количество конструктивных элементов в детали;
- количество унифицированных конструктивных элементов;
n - количество неунифицированных элементов.
Поскольку все формообразующие поверхности корпуса можно считать унифицированными то коэффициент применяемости унифицированных или стандартных конструктивных элементов детали можно принять равным .
Коэффициент повторяемости конструктивных элементов детали рассчитывают по формуле
где - количество повторяющихся конструктивных элементов детали;
- общее количество конструктивных элементов детали.
Подставляя численные значения требуемых показателей из чертежа детали выражение (1.13) находим
Коэффициент относительной обрабатываемости материала детали выражает относительную скорость резания соответствующую 60-минутной стойкости резцов в сравнении с эталонной сталью (сталь 45 ГОСТ 1050-84 ). Для сплава алюминия АК-6-ПП по ГОСТ 21488-97 величина этого коэффициента составляет что характеризует обрабатываемость этого сплава как удовлетворительную.
Коэффициент использования материала при механической обработке определяют по соотношению
где - массы готовой детали и заготовки соответственно.
Подставляя численные значения требуемых показателей из карт технологического процесса обработки детали резанием в выражение (1.14) находим
Необходимо отметить что корпус изготавливают из штампованной заготовки. Некоторые поверхности корпуса благодаря этому методу не подвергаются обработке резанием.
Обрабатываемые поверхности корпуса с точки зрения обеспечения точности и шероховатости не представляют значительных технологических трудностей.
Таким образом по рассчитанным показателям ТКИ можно сделать вывод о среднем уровне технологичности данной конкретной детали.
6 Установление вида заготовки и метода ее изготовления
При выборе способа получения заготовки необходимо стремиться к максимальному приближению формы и размеров заготовки к параметрам готовой детали и снижению трудоемкости последующей механической обработки. При этом тот или иной способ получения заготовки предопределяется назначением и конструкцией детали материалом техническими требованиями масштабом и серийностью выпуска а также экономичностью ее изготовления. Анализ рабочего чертежа показывает что значительное число наружных поверхностей детали не подвергается механической обработке резанием и может быть сформировано уже на стадии изготовления заготовки.
Заготовка корпуса может получаться не только в результате применения различных технологических процессов (литья ковки штамповки и др.) но и несколькими различными вариантами одного и того же технологического метода. При выборе конкретного метода получения заготовки определяющими являются обеспечение заданной чертежом детали точности и чистоты поверхности не подвергаемой дальнейшей механической обработке и экономичность ее изготовления .
С учетом обеспечения требуемых чертежом показателей точности и шероховатости необрабатываемых поверхностей детали заготовка корпуса может быть получена методом горячей объемной штамповки в закрытых разъемных штампах. Однако для реализации этого процесса с учетом массы штампуемой заготовки необходимо использование кузнечно-прессового оборудования и штамповой оснастки.
В условиях крупносерийного производства наиболее рациональным способом получения заготовки корпуса представляется литье.
Литье по выплавляемым моделям обеспечивает заготовке 12-14 квалитеты точности и чистоту поверхности в пределах 10-40 мкм. При этом существенно снижаются припуски на механическую обработку за счет снижения коробления и размера смещения стержня а также уменьшения толщины дефектного слоя и величины шероховатости.
Стоимость заготовок получаемых методами литья и штамповки в соответствии с рекомендациями можно определять по формуле
Кт Кс Кв Км Кп - коэффициенты зависящие от класса точности группы сложности массы марки материала и объема производства заготовок;
Q - масса заготовки кг;
q - масса готовой детали кг;
Sотх - цена 1тонны отходов руб.
Данные необходимые для расчета стоимости заготовок полученных литьем по выплавляемым моделям представлены в таблице 1.1.
Таблица 1.1 – Расчетные показатели литья
В соответствии с формулой (1.15) стоимость заготовок получаемых литьем по выплавляемым моделям будет составлять
Данные необходимые для расчета стоимости заготовок полученных штамповкой представлены в таблице 1.2.
Таблица 1.2 – Расчетные показатели штамповки
В соответствии с формулой (1.15) стоимость заготовок получаемых штамповкой будет составлять
Метод горячей штамповки на горизонтально-ковочной машине (ГКМ) обладает целым рядом достоинств:
возможность штамповки в закрытых штампах (безоблойных) и во многих случаях без штамповочных уклонов;
возможность получения поковок высокой точности и качества;
высокое качество получаемых поковок что объясняется благоприятным расположением волокон и осевой ликвации относительно действующих усилий при работе детали;
высокая производительность (400-900 поковок в час) и возможность полной автоматизации технологического процесса штамповки.
Из результатов проведенных расчетов и уточнения метода следует что наиболее рациональным способом получения заготовки для корпуса является штамповка на ГКМ обеспечивающая меньшую технологическую себестоимость детали и более высокий коэффициент использования материала.
7 Выбор технологических базовых поверхностей
Маршрутную технологию разрабатывают выбирая технологические базы и схемы базирования для всего технологического процесса. Выбирают две системы баз – основные базы и черные базы используемые для базирования при обработке основных баз.
Всю механическую обработку распределяют по операциям и таким образом выявляют последовательность выполнения операций и их число; для каждой операции выбирают оборудование и определяют конструктивную схему приспособления. В поточном производстве на данной стадии проектирования продолжительность выполнения операций соразмеряют с ранее рассчитанным тактом выпуска .
На первых двух операциях при базировании по черным базам обрабатывают основные технологические базы. Затем выполняют операции формообразования детали до стадии чистовой обработки (точность 7-9-го квалитета). Далее осуществляют операции местной обработки на ранее обработанных поверхностях (нарезают резьбу сверлят отверстия растачивают канавки и т. д.). Затем выполняют отделочную обработку основных наиболее ответственных поверхностей (точность 7-го квалитета). При необходимости за этим следует дополнительная обработка самых ответственных поверхностей с точностью 6-7-го квалитета и параметром шероховатости Ra=0.32 мкм и менее.
8 Выбор методов и определения последовательности обработки поверхностей заготовки
Разработка технологического процесса состоит из комплекса взаимосвязанных работ предусмотренных стандартами ЕСТПП и должна выполняться в полном соответствии с требованиями ГОСТ 14.301-83 «Общие правила разработки технологических процессов и выбора технологического оснащения» . При разработке маршрутной технологии придерживаются следующих основных принципов:
а) в первую очередь обрабатывают поверхности которые являются базовыми при дальнейшей обработке;
б) после этого обрабатывают поверхности с максимальным припуском для выявления дефектов заготовки;
в) необходимо соблюдать принцип концентрации операций при котором как можно больше поверхностей должно обрабатываться в одной операции;
г) необходимо соблюдать принципы совмещения и постоянства баз;
д) необходимо учитывать на каких стадиях технологического процесса целесообразно производить механическую термическую и другие виды обработки в зависимости от требований чертежа;
е) поверхности к которым предъявляются наиболее высокие требования по качественно-точностным характеристикам окончательно обрабатываются в последнюю очередь.
Разработка маршрута обработки любой детали начинается с предварительного выбора вида обработки отдельных поверхностей заготовки и определения методов достижения точности соответствующей требованиям чертежа серийности производства и технологических возможностей существующего в наличии на предприятии оборудования. После анализа этих данных приступают к составлению планов механической обработки детали. С учетом особенностей конструкции заготовки так же стремятся обработать за один станов наибольшее количество поверхностей. Вновь разработанная маршрутная технология обработки корпуса воздушного клапана представлена в комплекте карт технологического процесса.
Операционная технология для изготовления корпуса разработана с учетом места каждой операции в маршрутной технологии. К моменту проектирования каждой операции известно какие поверхности и с какой точностью обрабатываются на предшествующих операциях какие поверхности и с какой точностью нужно обрабатывать на данной операции. Проектирование операций связано с разработкой их структуры с составлением схем наладок расчетом настроенных размеров и ожидаемой точности обработки с назначением режимов обработки определением нормы времени и т. д. Номера поверхностей при составлении операционной технологии указаны на эскизах.
Таблица 1.3 - Последовательность обработки заготовки
Наименование операции
Комбинированная с ЧПУ
Испытания на прочность
Испытания пневматические
Испытания на разрушение
9 Расчет операционных припусков и предельных размеров
Всякая заготовка предназначенная для дальнейшей механической обработки изготавливается с припусками необходимыми для обеспечения заданных чертежом размеров детали и шероховатости ее поверхности.
Чрезмерные припуски вызывают излишние затраты на изготовление детали и тем самым увеличивает ее себестоимость. Снятие излишних припусков увеличивает трудоемкость обработки. С другой стороны слишком малые припуски не дают возможность выполнить необходимую механическую обработку с желаемой точностью и чистотой.
Величины припусков на механическую обработку зависят от ряда факторов к числу которых относятся:
а) материал заготовки;
б) конфигурация и размеры заготовки;
в) вид заготовки и способ ее изготовления;
г) требования в отношении механической обработки;
д) технические условия в отношении качества и класса шероховатости поверхности и точности размеров детали.
Устанавливаем маршрут обработки внутренней цилиндрической поверхности 30+0033 мм:
сверление отверстия;
Вся указанная обработка выполняется с установкой заготовки в трех- кулачковый патрон и резьбовую оправку.
Заносим маршрут обработки в графу 1 таблицы 1.4. Данные для заполнения граф 2 3 7 взяты из нормативно-статистических таблиц.
Расчет минимальных припусков на диаметральные размеры для каждого перехода произведем по формуле:
zmin = 2(Rz + h +Δ) (1.16).
Таблица 1.4 - Припуски на обработку и предельные размеры по технологическим переходам отверстия 30+0033
Маршрут обработки поверхности
Элементы припуска мкм
Допуск на выполняемые размеры мкм
Принятые размеры заготовки по переходам мм
Предельный припуск мкм
минимального диаметра мм
сверление 2zmin = 2(65 + 80 + 280) = 850 мкм
зенкерование 2zmin = 2(32 + 28 + 15) = 150 мкм
развертывание 2zmin = 2(5 + 10) = 30 мкм
Расчетные значения припусков заносим в графу 5 таблицы 1.4.
Расчет наименьших расчетных размеров по технологическим переходам производим складывая значения наименьших предельных размеров соответствующих предшествующему технологическому переходу с величиной припуска на выполняемый переход:
00 - 0150 = 2985 мм.
Наименьшие расчетные размеры заносим в графу 9 таблицы 1.4.
Затем определяем наибольшие предельные размеры по переходам:
00 + 0033 = 30033 мм
Результаты расчетов заносим в графу 8 таблицы 1.4.
Расчет фактических максимальных и минимальных припусков по переходам:
Максимальные припуски:
Минимальные припуски:
850 + 2900 = 850 мкм
Результаты расчетов заносим в графы 10 и 11 таблицы 1.4.
Zоmin = 730 + 93 = 823 мкм.
Произведем проверку правильности расчетов:
Zоma 1000 - 823 = 210 - 33 = 177 мкм.
Устанавливаем маршрут обработки внутренней цилиндрической поверхности 20+0021 мм:
Таблица 1.5 - Припуски на обработку и предельные размеры по технологическим переходам отверстия 20+0021
Расчетные значения припусков заносим в графу 5 таблицы 1.5.
Наименьшие расчетные размеры заносим в графу 9 таблицы 1.5.
Результаты расчетов заносим в графу 8 таблицы 1.5.
Результаты расчетов заносим в графы 10 и 11 таблицы 1.6.
10 Расчет режимов обработки
Расчет режимов резания состоит в определении для заданных условий обработки глубины резания числа проходов подачи скорости резания силы резания и мощности требуемой на резание.
Рассчитаем режимы резания на обработку отверстия 30+0033 которое обрабатывается в три перехода:
сверление-станок 1Е61М приспособление 3-х кулачковый патрон;
зенкерование-станок MDW-5F приспособление резьбовая оправка;
развертывание-станок MDW-5F приспособление резьбовая оправка.
Переход 1. Сверлить отверстие.
Станок токарно-винторезный модели 1Е61М. Приспособление - патрон 3-х кулачковый ГОСТ 24351-80.
Глубина резания t = 05×D = 05×29 = 145 мм.
Подача S = 096 ммоб выбираем из .
Скорость резания при сверлении мммин определяется по формуле
где - коэффициент и показатели степени выбираемые в зависимости от условий резания из справочных данных;
Т - стойкость инструмента мин;
t - глубина резания мм;
- поправочный коэффициент влияющий на скорость резания который определяют по формуле
- коэффициент отражающий влияние качества обрабатываемого материала на скорость резания;
- коэффициент отражающий влияние состояния поверхности заготовки на скорость резания;
- коэффициент отражающий влияние материала режущей части на скорость резания;
Согласно справочным данным :
t = 145 мм; S = 096 ммоб; = 407; = 025; = 040; m = 0125; Т = 75 мин; = 12; = 10; = 10.
Подставляя численные значения в формулы (1.18) и (1.17) находим расчетное значение скорости резания
Крутящий момент и осевая сила вычисляются по формулам:
= 0005; = 20; = 08; = 10 и = 98; = 10; = 07; = 10.
Тогда подставляя значения коэффициентов в уравнения (1.19) и (1.20) получаем
Частота вращения n обмин определяется по формуле
Подставляя численные значения в формулу (1.21) находим
По паспорту станка 1Е61М назначаем стандартную частоту вращения
nст = 750 обмин с учетом которой определяем действительное значение скорости резания
Мощность резания подсчитывают по формуле
Подставляя численные значения в формулу (1.22) получаем
Установленный режим резания должен удовлетворять условию
где - мощность станка определяемая по паспорту кВт; для токарно-винторезного станка модели 1Е61М = 96 кВт.
3 кВт 96 кВт - условие выполняется.
Основное время мин рассчитывают по формуле
где для первого перехода
- величина врезания инструмента; = 145 мм;
- величина перебега инструмента; = 0 мм.
Подставляя численные значения в формулу (1.24) получаем
Переход 2. Зенкеровать отверстие.
Станок токарный с ЧПУ модели MDW-5F. Приспособление – оправка резьбовая ГОСТ 16211-70.
Глубина резания t = 05×(D-d) = 0425 мм.
Подача S = 12 ммоб выбираем из .
Скорость резания при зенкеровании мммин определяется по формуле
t = 0425 мм; S = 12 ммоб; = 279; = 02; = 04; m = 0125; Т = 40 мин; = 12; = 10; = 10.
Подставляя численные значения в формулы (1.26) и (1.25) находим расчетное значение скорости резания
= 017; = 085; = 07; = 10 и = 38; = 10; = 04; = 10.
Тогда подставляя значения коэффициентов в уравнения ( 1.27) и ( 1.28) получаем
Подставляя численные значения в формулу (1.29) находим
По паспорту станка MDW-5F назначаем стандартную частоту вращения
nст = 450 обмин с учетом которой определяем действительное значение скорости резания
Подставляя численные значения в формулу (1.30) получаем
где - мощность станка определяемая по паспорту кВт; для токарного станка c ЧПУ модели MDW-5F = 18 кВт.
кВт 18 кВт - условие выполняется.
- величина врезания инструмента; = 0425 мм;
Подставляя численные значения в формулу (1.32) получаем
Переход 3. Развертывание отверстия.
Глубина резания t = 05×(D-d) = 0075 мм.
Подача S = 31 ммоб выбираем из .
Скорость резания при развертывании мммин определяется по формуле
t = 0075 мм; S = 31 ммоб; = 232; = 02; = 05; m = 03; Т = 75 мин; = 12; = 10; = 10.
Подставляя численные значения в формулы (1.33) и (1.34) находим расчетное значение скорости резания
Крутящий момент вычисляется по формуле:
= 40; = 01; = 075; Z= 12.
Тогда подставляя значения коэффициентов в уравнение (1.35) получаем
Подставляя численные значения в формулу (1.36) находим
nст = 550 обмин с учетом которой определяем действительное значение скорости резания
Подставляя численные значения в формулу (1.37) получаем
9 кВт 18 кВт - условие выполняется.
- величина врезания инструмента; = 0075 мм;
Подставляя численные значения в формулу (1.39) получаем
Суммарное основное время на выполнение отверстия 30+0033 составит
= 0125 + 014 + 005 = 0315 (мин)
11 Выбор оборудования и приспособлений
Для изготовления корпуса воздушного клапана ракетного двигателя на заводе были применены такие виды оборудования как токарно-винторезные станки верстак печь вертикально-сверлильный станок токарно-револьверный и вертикально-фрезерный станок.
Токарные станки предназначены для обработки наружных внутренних цилиндрических конических фасонных и торцевых поверхностей заготовок а также для нарезания резьбы. При наличии специальных приспособлений на них можно шлифовать фрезеровать полировать и т.д.
Токарные станки составляют значительную долю станочного парка и включают девять типов станков: автоматы и полуавтоматы одношпиндельные и многошпиндельные револьверные сверлильно-отрезные карусельные токарные и лобовые многорезцовые специализированные для фасонных изделий разные токарные.
Токарные станки в свою очередь подразделяются на универсальные и специализированные; универсальные станки делят на токарно-винторезные и токарные последние не имеют ходового винта для нарезания резьбы резцом.
Основным параметром токарного станка являются наибольший диаметр обрабатываемой заготовки над станиной и наибольше расстояние между центрами (или наибольшая длина обрабатываемой заготовки).
Сверлильные станки предназначены для сверления рассверливания зенкерования развертывания отверстий нарезания резьбы цекования зенкерования и т.д. Основными параметрами сверлильных станков являются: условный наибольший диаметр получаемого отверстия в стальных деталях размер конуса шпинделя вылет и наибольший ход шпинделя и др.
Сверлильные станки подразделяют на настольно-сверлильные вертикально-сверлильные многошпиндельные с постоянным расположением шпинделей и с переставными шпинделями горизонтально-сверлильные для глубокого сверления. Настольные станки выпускают для сверления отверстий диаметром 3 6 12 16 мм; вертикально-сверлильные и радиально-сверлильные - для сверления отверстий диаметром 18 25 35 50 и 75 мм. В сверлильных станках главным движением являются вращение шпинделя с инструментом а движением подачи - вертикальное перемещение шпинделя.
Вертикально-фрезерный станок 6Р13 предназначен для обработки заготовок сложного профиля из стали чугуна труднообрабатываемых сталей и цветных металлов в условиях единичного и серийного производства. В качестве инструмента применяют концевые торцевые угловые сферические и фасонные фрезы сверла зенкеры. Класс точности станка Н.
Техническая характеристика станка: размеры рабочей поверхности стола (длина×ширина) 1600×400 мм; число частот вращения шпинделя – 18; пределы частот вращения шпинделя 40 – 2000 мин-1; пределы рабочих подач (бесступенчатое регулирование) стола и ползуна 10 – 2000 мммин; скорость быстрого перемещения стола и ползуна 4800 мммин; габаритные размеры станка 3200×2465×2670 мм.
Базой станка является станина имеющая жесткую конструкцию за счет развитого основания и большого числа ребер. По вертикальным направляющим корпуса станины движется консоль (установочное перемещение). По горизонтальным (прямоугольного профиля) направляющим консоли перемещается в поперечном направлении механизм стол-салазки (подача по оси Y’) а по направляющим салазок в продольном направлении – стол (подача по оси X’). В корпусе консоли смонтированы приводы поперечной и вертикальной подачи а в корпусе салазок – привод продольной подачи. Главное движение фреза получает от коробки скоростей. В шпиндельной головке установлен привод вертикальных перемещений ползуна по оси Z.
Таблица 1.6 - Оборудование для обработки корпуса 19Д9
Наименование оборудования
Таблица 1.7 – Приспособления для обработки корпуса воздушного клапана
Патрон 3-х кулачковый
Угольник; Наладка специальная
Наладка спец. с поворотным столом
Резьбовая оправка; Угольник
Резьбовая оправка; Делительная головка
1 Конструкция установочного приспособления и его расчет
Приспособлением используемым для закрепления заготовки в процессе обработки является угольник с наладкой. Уголь представляет собой легко переналаживаемой приспособление которое может применяться и для обработки деталей похожей конфигурации. Наладка применяется только для деталей схожей конфигурации и относится к специальным приспособлениям. Наладка на угольнике крепится на установочных поверхностях при помощи болтового соединения. Угольник оснащен специальными противовесами в виде грузов в 2 килограмма. Деталь базируется в наладке при помощи пальца и двух центрирующих винтов которые выставляют деталь точно по оси обработки. Закрепляется деталь при помощи прижимной планки в виде коромысла. После установки детали в наладке происходит балансировка приспособления для проверки точности параметров биения и отклонения осей. Наладка с деталью базируется по установочным поверхностям угольника и центрируется за счет пальца.Приспособление показано в графической части к сборочному чертежу прилагается комплект карт спецификации.
Для закрепления заготовки в наладке используется коромысло один конец которого закреплен жестко а другой прижимается при помощи болтового соединения. Для силового расчета проверяется среднее сечение коромысла на изгиб. Считаем что сечение коромысла прямоугольник материал из которого оно изготовлено - сталь 40Х. Схема действия сил в коромысле показана на рисунке 2.1.
Рисунок 2.1 – Схема действия сил
Сечение коромысла должно удовлетворять следующее условие:
Найдем напряжение в нужном нам сечении и сравним его со значением допускаемого напряжения при изгибе для стали 40Х.
Напряжение при изгибе для сечения в виде прямоугольника выглядит так
где Wx-момент сопротивления сечения при изгибе
Mx- момент инерции сечения при изгибе.
Момент инерции для прямоугольного сечения равен
где Р- сила действующая на заготовку со стороны инструмента;
l- плечо действия силы.
Сила действующая на заготовку равна максимальной осевой силе со стороны режущего инструмента Ро = 2762 Н.
Момент сопротивления при изгибе для прямоугольного сечения равен
Напряжение при изгибе равно
Допустимое напряжение при изгибе для стали 40Х =210 (МПа)
Неравенство удовлетворяется значит сечение выдержит максимальное напряжение.
1.2 Точностной расчет приспособления
Определим погрешность установки корпуса в наладке.
Погрешность установки детали в приспособлении находят по уравнению
где eб – погрешность базирования заготовки в приспособлении мкм;
eз – погрешность закрепления заготовки мкм.
Погрешность базирования есть отклонение фактически достигнутого положения заготовки при базирование от требуемого; определяется как предельное поле рассеяния расстояния между технологической и измерительной базами в направлении выдерживаемого размера. Величина б зависит от принятой схемы базирования и точности выполнения баз заготовок. Выбираем схему базирования внутренней цилиндрической поверхностью на жесткий цилиндрический палец (оправку) с гарантированным зазором при растачивании внутреннего отверстия на определенную глубину.
Расчетная формула для определения погрешности базирования будет выглядеть так
где - допуск на размер детали;
- допуск на размер приспособления;
- гарантированный зазор принимаем его равным 5 мкм.
Уточнив значения допусков по чертежу детали и чертежу приспособления подставляем их в (2.5) и находим значение погрешности
Погрешность закрепления- это разность между наибольшей и наименьшей величинами проекций смещения измерительной базы на направление выполняемого размера в результате приложения к заготовке силы закрепления. На погрешность закрепления наибольшее влияние оказывают следующие факторы: непостоянство силы закрепления неоднородность шероховатости и волнистости базы заготовок износ опор.
Расчетная формула для определения погрешности закрепления будет выглядеть так
где - угол между направлением выдерживаемого размера и направлением наибольшего перемежения;
- суммарная погрешность закрепления из-за непостоянства силы закрепления неоднородности шероховатости базы заготовок и неоднородности волнистости базы заготовок;
- из-за износа опорной поверхности установочного элемента принимает его равным 0.
Погрешность закрепления из-за непостоянства силы закрепления вычисляется по формуле
где - наибольшая высота неровностей профиля 225 мкм;
- безразмерный параметр опорной кривой 22;
Q- сила действующая по нормали на опору 1600 Н ;
А- номинальная площадь опоры мм²;
- безразмерный коэффициент стеснения характеризующий степень упрочнения поверхностных слоев 524;
- предел текучести материала заготовки 408 МПа;
- коэффициент характеризующий условия контакта базы заготовки с опорой
- коэффициенты показывающие параметры качества плоских баз
- упругая постоянная материалов контактирующих заготовок и опоры
где - соответственно модули упругости и коэффициенты Пуассона материала опоры и заготовки;
Подставляя все значения в формулу (2.7) получаем
Погрешность закрепления из-за неоднородности шероховатости базы заготовок вычисляется по формуле
подставляя значения получаем
Погрешность закрепления из-за неоднородности волнистости базы заготовок вычисляется по формуле
Подставляя значения получившихся погрешностей в уравнение (2.7) получаем
Подставляя значение в выражение ( ) получаем
Подставляем все вычисленные значения в (2.6) находим погрешность установки
2 Разработка технологической планировки участка по обработке детали корпус
2.1 Состав механического цеха
В состав механического цеха входят производственные отделения участки линии вспомогательные и административно-бытовые службы
Производственные подразделения механического цеха предназначены для размещения оборудования и рабочих мест согласно технологическим процессам обработки деталей или по однотипности выполняемых операций
Состав их зависит от типа и организации производства. Механические цехи завода серийного и единичного производств специализируются на выпуске определенных деталей связанных общностью массы и габаритов или технологических процессов обработки. В таких цехах обработка деталей производится на подетально-групповых участках.
В условиях крупносерийного и массового поточного производств в цехах изготовляются все детали определенной сборочной единицы или машины. В составе таких цехов имеются механические и сборочные отделения детали с поточных станочных линий поступают непосредственно на узловую сборку.
Вспомогательные службы механического цеха включают:
инструментальное хозяйство в состав которого входят
инструментально-раздаточная кладовая (ИРК) кладовая приспособлений оснастки и абразивов заточное отделение мастерская по ремонту приспособлений;
ремонтное хозяйство - цеховая ремонтная база (РБ) кладовая запасных частей;
складское хозяйство — склады и кладовые металла и заготовок загрузочные площадки склады межоперационного хранения деталей готовых деталей а также кладовые вспомогательных материалов;
эмульсионное хозяйство — помещения для приготовления различных охлаждающих жидкостей и системы их раздачи на рабочие места;
склады масел и система раздачи масел на рабочие места и возврата их на регенерацию;
цеховая система сбора и транспортировки стружки с отделением переработки стружки;
цеховой контроль с постами промежуточного окончательного контроля и контрольным отделением.
В небольших цехах эмульсионное и масляное хозяйства входят в состав ремонтного.
В зависимости от принятой схемы организации производства и мощности цеха некоторые отделения вспомогательных служб могут быть объединены или исключены из состава цеха за счет кооперации вспомогательного хозяйства с другими цехами
Если несколько цехов располагаются в одном корпусе вспомогательные службы входят в состав наиболее крупного цеха и обслуживают весь корпус или организуется самостоятельное общекорпусное вспомогательное отделение.
2.2 Расчет количества основного оборудования по станкоемкости механической обработки
Потребное количество станков данного типа для непоточного производства определяется по формуле:
где Тшт = Тоij Ni (2.2)
n – число разных деталей обрабатываемых на станках данного типа;
m – число операций обработки детали на станках данного типоразмера;
Fд – эффективный фонд времени работы станка.
Коэффициент загрузки оборудования
Результаты расчетов сводятся в таблицу 2.1.
Таблица 2.1 - Расчет количества станков
Ср = (9638*2000)60*1930
Ср = (10796*2000)60*1930
Ср = (2347*2000)60*1930
Ср = (1358*2000)60*1930
Ср = (1469*2000)60*1930
Итого: станков 7 Кзаг цех.=0576
2.3 Расчет количества производственных и вспомогательных рабочих
По количеству станков число рабочих-станочников определяется:
R= S*Fд*КзагFг*Кмг (2.4)
где S- количество станков данного вида принятых в проекте;
Fд – действительный годовой фонд времени работы оборудования;
Кзаг - коэффициент загрузки оборудования;
Fг - действительный годовой фонд времени рабочего ч;
Кмг – коэффициент многостаночности.
Расчеты рабочих–станочников для каждого вида оборудования сведены в таблице 2.2.
Таблица 2.2 - Расчеты рабочих–станочников
Итого: рабочих-станочников 7
2.4 Расчет площади складов заготовок и готовых деталей на участке цеха
Основной задачей цеховых складов является обеспечение нормального хода производства. В комплекс цеховых складов входят склады участков заготовок и готовых деталей.
Запас заготовок и материалов в цеховом складе должен быть невелик так как назначением его является только регулярное обеспечение цеха (участка) материалами и заготовками для бесперебойной работы станков.
При расчете площади складов заготовок исходят из необходимости запаса и грузонапряженности пола:
где P – площадь складов заготовок м²; Q – масса заготовок обрабатываемых в цехе в течение года т; Т – запас заготовок дни; f – среднее число рабочих дней в году (f=253); qp - средняя грузонапряженность склада тм²; kp – коэффициент использования площади склада представляющий отношение полезной площади склада к его общей площади и учитывающий проходы и проезды (kp = 04-05).
где mз- масса одной заготовки; n – программа выпуска деталей в год.
Площадь склада готовой продукции определяется также как и общая площадь под заготовки и материалы.
Расчет площади складов заготовок и готовых деталей на участке цеха сведены в таблице 2.3.
Таблица 2.3 - Расчет площади складов заготовок и готовых деталей
2.5 Выбор транспортного оборудования
Заводской транспорт делится на три вида: внешний межцеховой и внутрицеховой.
Внешний транспорт используется для связи завода с ближайшими магистралями промышленными и хозяйственными предприятиями.
Межцеховой транспорт представляют электро- и автокары автомобили мотоциклы с тележками автотягачи с прицепами и др.
Цеховой транспорт обслуживает станки места сборки цеховые и складские помещения. Применяются ручные тележки электро- и автокары монорельсовые дороги поворотные и консольные краны кран-балки. Мостовые краны конвейеры разных типов рольганги желоба склизы скаты подъемники электрические и пневматические и т.д.
Выбор транспорта зависит от характера изготовляемой продукции ее массы и размера вида и формы организации производства типа и размеров здания.
В каждом конкретном случае нужно выбирать такой вид транспорта который наиболее рационально и экономично обслуживал бы производственный процесс.
В нашем случае выбирается напольно-тележечный транспорт. Количество тележек- 1.
2.6 Системы транспортирования стружки
Основным условием механизации и автоматизации процесса и транспортирования стружки является размещение станочных линий на участке для обработки деталей из однородных материалов.
Выбор цеховой системы транспортирования стружки зависит от количества. Сорта материала и вида стружки а также компоновки и планировки оборудования.
Различают три способа транспортирования стружки:
) автоматизированный. С применением средств непрерывного транспорта с помощью линейных и магистральных транспортеров;
) комбинированный с использованием только магистральных или линейных транспортеров: при удалении стружки от станков в тару вручную и при транспортировании тары к магистральному транспортеру или от линейного транспортера в отделение переработки стружки средствами малой механизации или напольным транспортом;
) механизированный. С применением ручного труда и транспортных средств общего назначения: от станков вручную стружка перегружается в тару а затем мостовыми кранами кран-балками электроталями на монорельсе самоходными тележками автопогрузчиками или другими средствами транспортируется в отделение переработки стружки.
В зависимости от среднечасового выхода стружки и площади участка рекомендуется применять:
механизированную систему транспортирования при выходе стружки 200-300 кгч на площади 1000-2000 м2. Для отдельных участков площадью 300-500 м2 при таком выходе стружки рационально применять линейные транспортеры расположенные вдоль технологических линий в конце которых размещены бункеры с контейнерами для сбора стружки;
комбинированную систему транспортирования при выходе стружки 300-700 - кгч на площади 2000-3000 м2;
автоматизированную систему транспортирования при выходе стружки более 800 кгч с участка площадью 3000 м и более.
2.7 Общая планировка оборудования и рабочих мест в механическом участке
Состав производственных отделений и участков механического цеха определяется характером изготавливаемых изделий технологическим процессом объемом и организацией производства.
В серийном производстве механический цех разбивается на участки (или пролеты) по размерам деталей (участок (пролет) крупных деталей участок (пролет средних деталей участок (пролет) мелких деталей) или по характеру и типу деталей (участок валов участок зубчатых колес и т.д.)
Определение размера площади участка (цеха) определяется на основании планировки путем разработки плана расположения оборудования рабочих мест конвейерных и других устройств складочных мест заготовок и готовых деталей проездов проходов и пр. На основании планировки уточняются принятые ширина длина и число пролетов здания участка (цеха).
Пролетом называется часть здания ограниченная в продольном направлении двумя параллельными рядами колонн. Ширину пролета принимаем 18 м.
Расстояние между осями колонн в продольном направлении называется шагом колонн. Принимаем 12 м.
Длина пролета определяется (считая по его продольной оси) суммой размеров последовательно расположенных производственных и вспомогательных отделений проходов и других участков цеха.
Установив необходимую ширину пролета их длину количество колонн определяют размер потребной площади производственного (станочного) участка цеха. Показателем характеризующим использование производственной площади механического цеха (участка) является удельная площадь т.е. площадь приходящаяся в среднем на один станок (вместе с проходами). Она получается путем деления общей площади занятой станками с проходами на число станков расположенных на ней. Средняя величина удельной площади составляет для малых станков 10-12 м2 средних - 15-25 м2 крупных - 30-45 м2.
Особенно важное значение для повышения производительности труда имеет рациональная планировка и организация рабочего места при которой устраняются потери времени на лишнее хождение лишние движения и т. д.
При размещении станков необходимо стремиться к достижению прямоточности производства. При расстановке станков руководствуются нормальными размерами промежутков (разрывов) между станками в продольном и поперечном направлениях и размерами расстояний от стен и колонн. Эти размеры должны гарантировать удобство выполнения работ на станках безопасность рабочих свободу движения людей и транспортных средств с грузом и т.д. При планировке оборудования всегда нужно стремиться получить короткую технологическую линию чтобы детали не совершали длинный путь.
1 Патентно-информационный поиск
Авторское свидетельство СССР № 938010 кл. G 01 B 1130 1990.
Устройство для контроля качества поверхности цилиндрических отверстий по авторскому свидетельству № 938010 отличающееся тем что с целью повышения точности и надежности контроля отражающая поверхность аксикона выполнена в виде тороида.
Изобретение относится к контрольно-измерительным устройствам используемых для контроля дефектов поверхности цилиндрических отверстий деталей различного типа.
По основному авторскому свидетельству № 938010 известно устройство для контроля качества поверхности цилиндрических отверстий содержащее последовательно расположенные на одной оптической оси лазер фокусирующую линзу аксикон световод выполненный в виде кольцевых секций выходные торцы которых скошены а каждый выходной торец соединен с соответствующим приемником излучения.
Однако для известного устройства характерны недостаточная точность контроля особенно при контроле дефектов поверхностей с ярко выраженными следами режущего инструмента а также неудовлетворительная надежность выявления дефектов.
Целью изобретения является повышение точности и надежности контроля.
Указанная цель достигается тем что в устройстве для контроля качества поверхности цилиндрических отверстий отражающая поверхность аксикона выполнена в виде тороида.
В графической части изображена схема устройства для контроля дефектов цилиндрических отверстий.
Устройство содержит лазер 1 фокусирующую линзу 2 фокус которой расположен на поверхности контролируемой детали или заготовки 3 аксикон 4 с отражающей поверхностью выполненной в виде тороида световод 5 кольцевого сечения с секциями 6.1-6.n приемники 7.1-7.n излучения.
Устройство работает следующим образом.
Луч лазера 1 фокусируется фокусирующей линзой 2 на контролируемую поверхность детали 3. На пути фокусирующего потока расположен аксикон 4 на тороидальной отражающей поверхности которого происходит формирование светового потока в виде кольца и дополнительная фокусировка на контролируемую поверхность детали 3. Рассеянное на дефекте излучение воспринимается волоконно-оптическим световодом 5 причем каждая из его секций 6.1-6.n воспринимает рассеянное излучение от соответствующего ей участка поверхности.
Наличие скошенных торцов световодных секций 6.1-6.n позволяет воспринимать излучение рассеянной дефектами в большем телесном угле. Выходной торец каждой из секций связан с приемником 7.1-7.n излучения что позволяет определить местоположение дефекта поверхности. Сканирование всей поверхности сфокусированным по периметру световым кольцом обеспечивается при относительном поступательном перемещение устройства и контролируемой детали 3.
Устройство обладает большей точностью и надежностью в связи с тем что при формирование кольцевого пучка зондирующего излучения на тороидальной отражающей поверхности аксикона происходит его дополнительная фокусировка. В результате пучок на поверхности фокусируется в линию малой ширины и большей концентрации энергии что приводит к увеличению контраста между освещенным участком поверхности цилиндрического отверстия и фоном и тем самым к повышению точности и надежности контроля.
Авторское свидетельство СССР №389396 кл. G 01b 734 1983.
Изобретение относится к области измерительной технике и может быть использовано для контроля шероховатости поверхности деталей.
Известен способ контроля шероховатости поверхности детали заключающийся в том что электрод емкостного датчика накладывают на исследуемую поверхность являющуюся вторым электродом датчиком и прикладывают напряжение. О шероховатости поверхности судят по изменению емкости между электродом и исследуемой поверхностью.
Недостатком известного способа является его небольшая чувствительность из-за влияния паразитной емкости между электродом и исследуемой поверхностью.
Предлагаемый способ отличается тем что для повышения чувствительности к электроду датчику прикладывают усилие отрыва в направлении нормали к поверхности измеряют его и по нему судят о шероховатости.
Устройство содержит электрод расположенный под ним полупроводящий слой поверхность которого обращенная к исследуемой поверхности обработанная по классу чистоты 12. Электрод и исследуемая поверхность подсоединены к источнику напряжения U.
Контроль шероховатости поверхности заключается в следующем. Между электродом и исследуемой поверхностью создают постоянное электрическое поле. Величина электростатической силы притяжения между ними обратно пропорциональна квадрату эффективной толщины воздушного зазора которая определяется высотой микронеровностей. К электроду прикладывают усилие отрыва с помощью электромеханического преобразователя в направлении нормали к исследуемой поверхности замеряют это усилие и по заранее снятой номограмме определяют класс чистоты поверхности.
Авторское свидетельство № 557264 кл. G 01 B 1130 1987.
Изобретение относится к контрольно-измерительной технике в частности к измерительным и индикаторным приборам позволяющим определять класс шероховатости и судить о качестве обработки поверхности.
Данное предложение может быть использовано в машиностроении и приборостроении в том числе оптическом для исследования шероховатости поверхности сквозных каналов кругового сечения в частности сверленых каналов в металлических и диэлектрических деталях с диаметром отверстия три и более миллиметра.
Известно устройство для контроля шероховатости поверхности объекта представляющее собой двойной микроскоп Линника и содержащее осветительный тубус со щелью и воспринимающий тубус в выходном зрачке объектива которого располагается диафрагма со щелью.
Это устройство позволяет измерять среднюю высоту микронеровностей лишь на малом участке исследуемой поверхности что приводит к трудоемкости контроля. Кроме того известное устройство не позволяет выполнять неразрушающий контроль внутренней поверхности узкого цилиндрического канала.
Наиболее близким к изобретению по своей технической сущности и решаемой задачи является устройство для контроля шероховатости поверхности объекта содержащее осветитель состоящий из последовательно расположенных источника света коллиматора и выходной головки в виде поворотной призмы и светоприемник состоящий из последовательно расположенных входной головки в виде поворотной призмы фокусирующей системы светофильтра и регистрирующего блока.
Недостатком указанного устройства является то что оно может быть использовано для контроля шероховатости плоской поверхности объекта и неприменимо для контроля поверхности сквозных цилиндрических отверстий объекта.
Предлагаемое устройство отличается от известного тем что с целью контроля поверхности сквозных цилиндрических отверстий объекта выходная головка осветителя и входная головка светоприемника выполнены в виде зеркально расположенных аксиально-симметричных двух пар состоящих каждая из оптического клина и диафрагмы.
В качестве устройства для активного контроля было выбрано первое устройство для контроля шероховатости цилиндрических поверхностей которое удовлетворяет всем требованиям для достижения нужного нам результата.
2. Влияние износостойких покрытий на свойства режущего инструмента
2.1 Методы нанесения покрытий на режущий инструмент
Применение традиционных методов повышения режущих свойств инструментов за счет сложного легирования инструментальных материалов в настоящее время в большей степени ограничено из-за дефицитности ряда элементов. В связи с этим актуальной задачей является создание принципиально новых инструментальных материалов так называемых композиционных которые обладают повышенной поверхностной износостойкостью и относительно высокой прочностью а также вязкостью.
Промышленное использование режущих инструментов с износостойкими покрытиями позволяет решать целый комплекс важнейших задач. К таким задачам можно отнести:
значительное повышение стойкости и надежности металлорежущего инструмента;
увеличение производительности процессов обработки деталей резанием;
сокращение удельного расхода дорогостоящих инструментальных материалов и дефицитных элементов (вольфрам молибден тантал кобальт) для их изготовления;
расширение эффективной области использование твердых сплавов и сокращение номенклатуры применяемых сплавов стандартных марок;
увеличение качества поверхностного слоя и точности размеров обработанных деталей;
улучшение обрабатываемости сложнолегированных сталей и сплавов;
повышение режущей способности инструментов изготовленных из низколегированных материалов.
Существует большое число методов получения покрытий на рабочих поверхностях режущих инструментов. С учетом специфики протекания процессов формирования покрытий существующие методы можно разделить на три основные группы. К первой группе относятся методы при которых формирование покрытий осуществляется преимущественно за счет диффузионных реакций между насыщаемыми элементами и структурами инструментального материала. Во вторую группу входят методы формирования покрытий по комплексному механизму. Покрытие образуется за счет реакции между парогазовыми смесями состоящими из соединения металлоносителя носителя второго компонента служащего как газом-транспортером так и восстановителем. При этом одновременно в процессе формирования покрытия большой вклад вносят субструктура поверхности материала инструмента и интердиффузионные реакции между конденсатом и материалом инструмента. К третьей группе можно отнести методы формирования покрытий за счет химических и плазмохимических реакций потока частиц одновременно в объемах пространства непосредственно примыкающего к насыщаемым поверхностям инструментального материала.
Каждый из технологических методов нанесения покрытий на режущие инструменты обладает своими преимуществами и недостатками. Классификация методов нанесения покрытий на режущие инструменты по характеру формирования покрытий приведены в приложении .
К методам первой группы относятся химико-термические методы образования покрытий (ХТМ) основанные на твердофазовом жидкостном и газофазовом насыщении поверхностей инструмента. Методы ХТМ позволяют получить покрытия толщиной 10-40 мкм что дает возможность увеличить стойкость различных типов инструментов из быстрорежущих и углеродистых сталей в 15-2 раза.
Среди методов ХТМ наибольшим преимуществом обладает ионное азотирование инструментов из быстрорежущих сталей. Эффективность инструментов с ионным азотированием поверхностных слоев значительно снижается при глубине азотированного слоя более 25-30 мкм и твердости слоя около НВ 750-780 и выше из-за хрупкого разрушения режущей части инструмента.
Метод ХТМ позволяет лишь ограниченно увеличить поверхностные свойства быстрорежущих сталей за счет варьирования технологическими параметрами процесса поэтому эффективность этого метода относительно невысока.
Ко второй группе методов по классификации показанной в приложении относятся методы химического осаждения покрытий из парогазовой фазы (метод ХОП) получивший в мировой практике наименование CVD (Chemical vapor deposition).
Метод ХОП получил широкое распространение для нанесения покрытий на основе карбидов нитридов карбонитридов титана а также окисла алюминия на многогранные неперетачиваемые твердосплавные пластинки. В нашей стране разработан метод нанесения карбидотитановых покрытий на неперетачиваемые твердосплавные пластинки получивший наименование ГТ.
Отличительной особенность покрытий полученных методам ХОП является формирование переходной зоны между покрытием и твердым сплавом обычно называемой h-фазой. Формирование переходной зоны связано с интердиффузионными реакциями между насыщающим тугоплавким металлом из парогазовой смеси и компонентами твердого сплава.
Методы второй группы обычно реализуются при температурах около 1000-1100°С что исключает их использование для нанесения покрытий на инструменты из быстрорежущей стали подвергнутые полной термической обработке. Используя методы второй группы можно получить покрытие на основе карбидов нитридов и карбонитридов металлов 4-6 групп Периодической системы элементов использование которых позволяет повысить стойкость твердосплавных пластин в 3-10 раз в широкой области применения.
К третьей группе методов могут бить отнесены методы физического осаждения покрытия (методы ФОП) получившие название в мировой практике PVD (Phisical vapor deposition). При этом процессе ФОП обычно включает вакуумное испарение тугоплавкого металла - образователя соединения покрытия его частичную или полную ионизацию подачу реакционного газа химические и плазмохимические реакции конденсацию покрытия на рабочих поверхностях режущего инструмента.
Среди методов ФОП наибольшее распространение получил метод конденсации покрытий из плазменной фазы в вакууме с ионной бомбардировкой поверхностей инструмента (метод КИБ).
Применение вакуумно-плазменных методов значительно расширяет технологические возможности инструментов с покрытиями. Эти методы позволяют более эффективно управлять процессами получения покрытий с заданными свойствами а также предупреждать образование геометрических кристаллохимических и физико-механических дефектов на поверхностных слоях инструментального материала.
Наиболее характерной особенностью покрытий получаемых вакуумно-плазменным методом является отсутствие переходной зоны между покрытием и инструментальным материалом [4].
2.2 Влияние толщины покрытия на процессы резания
Одним из важнейших параметров покрытия оказывающим сильное влияние на работоспособность режущего инструмента является его толщина [4].
Толщина покрытия является параметром подлежащим оптимизации в каждом конкретном случае.
Ниже приведены данные оценки оптимальной толщины покрытия на твердосплавных и быстрорежущих инструментах в различных условиях резания. С учетом сильной склонности покрытия к хрупкому разрушению по мере роста толщины критерием оценки оптимальности служили среднее значение стойкости Тср полученной при 10-15 дублях испытаний и коэффициент ее вариации .
Влияние толщины покрытия TiC ГТ на стойкость твердосплавных пластинок ВК6 ТТ10К8Б Т5К10 при продольном точении стали 45 и чугуна СЧ 32 показано на рисунке 3.1.
Для операций прерывистого резания (фрезерования зубодолбления строгания и т.д.) экстремальный характер зависимости стойкости от толщины покрытия проявляется в значительно большей степени чем для непрерывного резания причем оптимальное значение толщины покрытия сдвигается в область меньших значений что показано на рисунке 3.2.
-точение стали 45 (НВ180) пластинками Т5К10;
- точение серого чугуна СЧ 32 (НВ200) пластинками ВК6;
- точение стали 45 (НВ180) пластинками ТТ10К8Б;
- точение стали 45(НВ180) пластинками ВК6;
при t=10 мм S=015 ммоб V=150 ммин.
Рисунок 3.1 - Влияние толщины покрытия TiC ГТ на стойкость твердосплавных пластинок
Данные представленные на рисунке 3.1 и 3.2 демонстрируют насколько сильно зависит коэффициент повышения стойкости от величины скорости резания и подачи при разных толщинах покрытий.
Коэффициент повышения стойкости пластинок с покрытием определяли как отношение средней стойкости инструмента с покрытием к средней стойкости инструмента без покрытия.
В частности эффективность толстых покрытий (9-14 мкм) в значительно большей степени проявляется с ростом скорости резания что показано на рисунке 3.3.
Рисунок 3.2 -Влияние толщины покрытия на стойкость твердосплавных пластинок при симметричном фрезеровании стали 40Х (НВ 220) с В=140 мм; t=20 мм; s=032 ммзуб; v=170 ммин; z=1
Рисунок 3.3 -Влияние скорости резания на коэффициент повышения стойкости твердосплавных пластинок ТТ10К8Б с различными толщинами покрытий T t=10 мм.
Эффективность любого покрытия заметно снижается по мере роста подачи однако такое снижение меньше для более тонких покрытий что показано на рисунке 3.4.
Рисунок 3.4 - Влияние подачи на коэффициент повышения стойкости твердосплавных пластинок ТТ10К8Б с различными толщинами покрытий T t=10 мм.
1 Экология и техника безопасности
1.1 Энергетические загрязнения окружающей среды
Техногенная деятельность является источником энергетических воздействий на биосферу. К ним относятся тепловое электромагнитное световое ионизирующее акустическое излучения механические колебания (вибрации).
Энергия избыточной теплоты выделяется многими энергетическими и технологическими установками и распространяются в окружающую среду с теплоносителями (нагретые газы пар вода растворы расплавы и др.) и тепловым излучением от нагретых поверхностей. Тепловые загрязнения носят как правило локальный характер. Газовые выбросы в атмосферу при неблагоприятных метеорологических условиях могут способствовать повышению температур в зоне их распространения выпадению осадков и др. Нагретые сточные воды повышают температуру в водных объектах изменяя их естественный тепловой режим и протекание биохимических процессов.
В условиях производств действие тепловых излучений и выбросов сказывается прежде всего на рабочих местах что может привести к поражениям работающих в результате ожогов и перегрева.
Источником электромагнитных излечений являются мощные электрические машины и установки линии электропередач технические комплексы радио и телевидения и др. Воздействие таких излучений на живые организмы приводит к нарушениям в тонких клеточных и молекулярных биологических структурах вызывающим серьезные физиологические и психические расстройства.
Развитие промышленности транспорта формирование мегаполисов и связанное этими процессами шумовое загрязнение влияют на среду обитания и жизнедеятельность людей. У человека повышается утомляемость снижается умственная активность возникают стрессы физические и нервные заболевания. Наибольшему воздействию шума человек подвергается на производстве и в крупных мегаполисах.
Источником светового излучения негативно влияющего на окружающую среду являются промышленные установки и аппаратура. Это прежде всего лазеры высокотемпературные излучатели источники УФ-излучений. Их воздействие на человека зависит не только от мощности излучения но и от его спектральных характеристик. Наиболее типичным проявлением светового излучения является поверхностное поражение тканей живых организмов ожоги сетчатки глаз.
Радиационное загрязнение вызывается действием ионизирующих излучений. При воздействии - и -частиц на ткани живых организмов они проникают вглубь на 01-03 мм чем наносят повреждение клеткам вблизи места проникновения. Фотоны -излучения имеют длину пробега в воздухе от метров до километров и поэтому свободно проходят через мягкие ткани организмов вызывая глубинные и обширные поражения.
Одним из энергетических загрязнений получивших особое распространение в техносфере являются вибрации возникающие при работе промышленных установок транспортных средств двигателей и др. У человека вибрации могут вызывать как легкие психические и физиологические расстройства так и серьезные поражения такие как деформация и отрыв органов при резонансе тяжелые профессиональные заболевания при длительном контакте с источником механических колебаний. Вибрации являются причиной многих аварий и катастроф связанных с разрушением технических устройств зданий сооружений и др.
1.2 Организация трудового процесса
Правильное расположение и компоновка рабочего места обеспечение удобной позы и свободы трудовых движений использование оборудования отвечающего требованиям эргономики и инженерной психологии обеспечивают наиболее эффективный трудовой процесс уменьшают утомляемость и предотвращают опасность возникновения профессиональных заболеваний.
Оптимальная поза человека в процессе трудовой деятельности обеспечивает высокую работоспособность и производительность труда. Неправильное расположение тела на рабочем месте приводит к быстрому возникновению статической усталости снижению качества и скорости выполняемой работы а также снижению реакции на опасность. Нормальной рабочей позой следует считать такую при которой работнику не требуется наклоняться вперед больше чем на 10 15 º; наклоны назад и в сторону нежелательны; основное требование к рабочей позе - прямая осанка.
Выбор рабочей позы зависимости от мышечных усилий во время работы точности и скорости движений а также от характера выполняемой работы. При усилиях не более 50 Н можно выполнять работу сидя. При усилиях 50 100 Н работа может выполняться с одинаковым физиологическим эффектом как стоя так и сидя. При усилиях более 100 Н желательно работать стоя.
Работа стоя целесообразнее при необходимости постоянных передвижений связанных с настройкой и наладкой оборудования. Она создает максимальные возможности для обзора и свободных движений. Однако при работе стоя повышается нагрузка на мышцы нижних конечностей повышается напряжение мышц в связи с высоким расположением центра тяжести и увеличиваются энергозатраты на 6 10% по сравнению с позой сидя.
Работа в позе сидя более рациональна и менее утомительна так как уменьшается высота центра тяжести над площадью опоры повышается устойчивость тела снижается напряжение мышц уменьшается нагрузка на сердечно-сосудистую систему. В положении сидя обеспечивается возможность выполнять работу требующую точность движения. Однако и в этом случае могут возникать застойные явления в органах таза затруднение работы органом кровообращения и дыхания.
Смена позы приводит к перераспределению нагрузки на группы мышц улучшению условий кровообращения ограничивает монотонность. Поэтому где это совместимо с технологией и условиями производства необходимо предусматривать выполнение работы как стоя так и сидя с тем чтобы рабочие по своему усмотрению могли изменять положение тела.
При организации производственного процесса следует учитывать антропометрические и психофизиологические особенности человека его возможности в отношении величины усилий темпа и ритма выполняемых операций а также анатомо-физиологические различия между мужчинами и женщинами.
Размерные соотношения на рабочем месте при работе стоя строятся с учетом того что рост мужчин и женщин в среднем отличается на 111 см длина вытянутой в сторону руки- на 62 см длина вытянутой вперед руки- на 57 см длина ноги- на 66 см высота глаз над уровнем пола- на 101 см. на рабочем месте в позе сидя различия в размерных соотношениях у мужчин и женщин выражаются в том что в среднем длина тела мужчин на 98 см и высота глаз над сиденьем- на 44 см больше чем у женщин.
На формирование рабочей позы в положении сидя влияет высота рабочей поверхности определяемая расстоянием от пола до горизонтальной поверхности на которой совершаются трудовые движения. Высоту рабочей поверхности устанавливают в зависимости от характера тяжести и точности работ. Оптимальная рабочая поза при работе сидя обеспечивается также конструкцией стула: размерами формой площадью и наклоном сиденья регулировкой по высоте. Основные требования к размерам и конструкции рабочего стула в зависимости от вида выполняемых работ приведены в ГОСТ 12.2.032-78 и ГОСТ 21889-76.
1 Экономическое обоснование принимаемых в дипломном проекте решений
Современная техника и технологии позволяют одно и то же изделие изготовить различными методами. Задача технолога выбрать не только технологически совершенный но и экономически целесообразный вариант.
Экономическое обоснование принимаемых в дипломном проекте решений должно производиться при выборе заготовки варианта технологического процесса оснастки и при проектировании организационно-технических мероприятий. Причем расчеты экономической эффективности рассматриваемых вариантов технологий изготовления изделий и выбор оптимального из них предшествуют непосредственному проектированию и служат основанием для определения целесообразности дальнейших проектных разработок.
1.1 Экономическое обоснование выбора заготовки
При выборе заготовки для вновь проектируемого технологического процесса возможны следующие варианты:
Метод получения заготовки принимается аналогичным по
существующему на данном производстве.
Метод изменяется однако это обстоятельство не вызывает
изменений в технологическом процессе механической обработки.
Метод изменяется что влечет за собой существенное изменение технологического процесса механической обработки детали.
В первом случае достаточно ограничиться ссылкой на справочную литературу где для данных условий рекомендован этот вариант как оптимальный. Так как стоимость заготовки не изменяется она не учитывается - при определении технологической себестоимости или принимается по базовому варианту.
Во втором случае предпочтение следует отдать заготовке характеризующейся лучшим использованием металла и с более низкой стоимостью.
В третьем случае вопрос в целесообразности определенного вида заготовки может быть решен лишь после расчета технологической себестоимости детали по сравниваемым вариантам. Предпочтение следует отдать той заготовке которая обеспечивает меньшую технологическую себестоимость детали. Если же сопоставляемые варианты оказываются равноценными предпочтение следует отдавать варианту заготовки с более высоким коэффициентом использование материала.
Расчет стоимости заготовки может быть произведен укрупненным методом по следующей методике.
Для первого варианта изготовления заготовки – горячая объемная штамповка на ГКМ- стоимость заготовки будет определяться по формуле:
где Q1 – масса заготовки кг;
S – цена одного килограмма материала заготовки равная 153 рублям;
q1 – масса готовой детали кг;
– цена одной тонны отходов равная 15.3 рублям.
Таким образом для первого варианта изготовления заготовки ее стоимость будет составлять М1 = 1047×154 – (1047 – 044)×1541000 =1612 рублей.
Для второго варианта- литье по выплавляемым моделям:
где - базовая стоимость одной тонны заготовок рублей;
- коэффициенты зависящие от класса точности группы сложности массы марки материала и объема производства заготовок.
Тогда стоимость заготовки будет равна – М2 = (153 ×19 ×105× 078 × ×089 ×127×1) – (19 – 044)×1541000 = 269 рублей.
Исходя из сравнения стоимости изготовления заготовок по двум различным методам (М1 и М2) можно сделать вывод что первый способ является более эффективным.
1.2 Экономическая оценка вариантов технологического процесса
Прежде чем принять решение о методах и последовательности обработки отдельных поверхностей детали и составить технологический маршрут ее изготовления необходимо произвести расчеты экономической эффективности по каждому варианту и выбрать наиболее рациональный из них. Сравнение вариантов технологических процессов производится по техническим (натуральным) и стоимостным показателям.
К техническим показателям относятся: трудоемкость технологических процессов технологическая оснащенность количество применяемого оборудования удельные нормы расхода сырья материалов технологического топлива энергии и прочее. Стоимостные показатели (технологическая себестоимость приведенные затраты) позволяют выбрать вариант технологии осуществляемый с наименьшими затратами.
Расчеты путем сопоставления приведенных затрат ведут в тех случаях когда при выпуске одной и той же продукции сравниваемые варианты связаны со значительными капитальными затратами (приобретение нового оборудования дорогостоящего приспособления средств автоматизации и т.п.). Во всех остальных случаях можно ограничиться суммой затрат входящих в технологическую себестоимость то есть суммой тех затрат которые изменяются в сравниваемых вариантах.
Расчет технологической себестоимости ведется укрупнено причем учитываются те статьи расходов на которые оказывают влияние особенности технологического процесса:
где Мо - стоимость основных материалов или стоимость заготовки рублей (М0 принимается в расчет в том случае если изменение метода получения заготовки влечет за собой существенное изменение технологического процесса механической обработки);
Мвт - затраты на вспомогательные материалы для технологических целей рублей (электролит вода и пр.). К числу вспомогательных материалов технологического назначения не следует относить материалы необходимые для эксплуатации оборудования - смазочные обтирочные эмульсии и т. п.;
ЗЭ - затраты на энергию для технологических целей (нагрев плавка на создание вакуума и т.п.) рублей;
о и Зд - основная и дополнительная заработная плата производственных рабочих при выполнении технологических операций рублей;
Ос-начисления на заработную плату на социальные нужды рублей;
Исп - затраты на возмещение износа инструментов и приспособления целевого назначения рублей;
РСЭО – расходы на содержание и эксплуатацию оборудования рублей;
Рпл - расходы на использование площади рублей.
Затраты на основные материалы – см. пункт 1.
Для изготовления детали типа Корпус воздушного клапана вспомогательных материалов не требуется не по первому варианту изготовления не по второму.
Затраты на энергию для технологических целей определяются по формуле:
где - установленная мощность оборудования для обработки детали кВт;
- машинное время на операцию на данном типе оборудования часов;
- коэффициент использования оборудования по мощности (его можно принять в интервале 05-07);
- стоимость одного кВт-ч электроэнергии (данные предприятия) 1469 рублей за кВтч.
Таблица 5.1 – Данные для расчета затрат на энергию для технологических нужд (Вариант 1)
Штучное время Тшт мин.
Для операции 010 (Токарная) затраты на энергию определяются как
ЗЭ1 = 12×1395×06×1469 = 1476 рубля.
Для операции 015 (Токарная с ЧПУ) затраты на энергию равны
ЗЭ2 = 15×3222 ×06×1469 = 426 рубля.
Для операции 020 (Токарная с ЧПУ) затраты на энергию равны
ЗЭ3 = 15×1477 ×06×1469 = 1953 рубля.
Для операции 025 (Токарная) затраты на энергию равны
ЗЭ4 = 12×1112×06×1469 = 1176 рубля.
Для операции 030 (Токарная) затраты на энергию равны
ЗЭ5 = 12×1646×06×1469 = 1741 рубля.
Для операции 035 (Токарная с ЧПУ) затраты на энергию равны
ЗЭ6 = 15×908 ×06×1469 = 1201 рубля.
Для операции 040 (Комбинированная с ЧПУ)
ЗЭ7 = 17× 2347 ×06 × ×1469 = 3517 рублей.
Для операции 045 (Фрезерная) затраты на энергию равны
ЗЭ8 = 11×347×06×1469 = 337 рублей.
Для операции 050 (Токарная с ЧПУ) затраты на энергию равны
ЗЭ9 = 15×1611 ×06×1469 = 213 рублей.
Для операции 055 (Фрезерная) затраты на энергию равны
ЗЭ10 = 11×392×06×1469 = 38 рублей.
Для операции 060 (Фрезерная) затраты на энергию равны
ЗЭ11 = 11×592×06×1469 = 574 рублей.
Для операции 075 (Токарная с ЧПУ) затраты на энергию равны
ЗЭ12 = 15×908 ×06×1469 = 120 рублей.
Для операции 80 (Сверлильная)
ЗЭ13 = 12× 632 ×06× ×1469 = 669 рублей.
Для операции 85 (Сверлильная)
ЗЭ14 = 12× 837 ×06× ×1469 = 885 рублей.
Для операции 100 (Токарная с ЧПУ) затраты на энергию равны
ЗЭ15 = 15×267 ×06×1469 = 353 рубля.
Для операции 130 (Токарная) затраты на энергию равны
ЗЭ16 = 12×1175×06×1469 = 1243 рубля.
Для операции 140 (Токарная) затраты на энергию равны
ЗЭ17 = 12×1255×06×1469 = 1327 рубля.
Для операции 145 (Токарная) затраты на энергию равны
ЗЭ18 = 12×1255×06×1469 = 1327 рубля.
Результаты расчета затрат на энергию для технологических целей суммируем ЗЭ = 1476 +426 + 1953 + 1741 + 1201 + 3517 + 337 + 213 + 38 +
+ 574 + 120 + 669 + 885 + 353 + 1243 + 1327 + 1327 = 2775 рублей.
По аналогичной методике рассчитываются затраты на энергию для второго варианта изготовления детали Корпус воздушного клапана.
Таблица 5.2 – Данные для расчета затрат на энергию для технологических нужд (Вариант 2)
Результаты расчета затрат на энергию для технологических целей (Вариант 2) ЗЭ = 29547 рублей.
Затраты на основную заработную плату производственных рабочих выполняющих технологические операции определяются по формуле:
где - расценка на операцию рублей;
Д - доплаты до часового фонда (премии из фонда заработной платы) которые можно принять в размере 30-40% от величины основной заработной платы.
где - часовая тарифная ставка соответствующая разряду работ на операции р.ч;
- трудоемкость операции минут.
Дополнительная заработная плата основных производственных рабочих определяется по формуле:
где - процент дополнительной заработной платы равный 235.
Начисления на социальные нужды рассчитываются по формуле:
где - процент начислений на зарплату на социальные нужды равный 26.
Таким образом использую исходные данные представленные в таблице 5.3 рассчитаем основную и дополнительную заработную плату для основных рабочих.
Таблица 5.3 – Исходные данные для расчета фонда заработной платы основных рабочих
Стоимость минуты коп
Часовые ставки рублей
Тогда для Токарной операции (010) ЗО1 = [2096×(319560)] = 112 рубля. Дополнительная заработная плата составляет Зд1 =112×0235 = 263 рублей. Отчисления на социальные нужды Ос1 = (112+263)×026 = 36 рублей.
По аналогии производится расчет для других операций и результаты сводятся в таблицу 5.4.
Таблица 5.4 – Результаты определения основной дополнительной заработной платы отчислений на социальные нужды по операциям для первого варианта изготовления детали
Основная заработная плата рублей
Дополнительная заработная плата рублей
По аналогии рассчитываются затраты на основную дополнительную заработную плату для производственных рабочих а также отчисления на социальные нужды для изготовления детали по второму варианту (таблица 5.5).
Таблица 5.5 – Результаты расчета фондов основной и дополнительной заработной платы для второго варианта изготовления детали Корпус воздушного клапана
Затраты на возмещение износа инструментов и приспособлений целевого назначения определяются по формуле:
где N - число видов инструментов и приспособлений целевого назначения применяемых при выполнении операции;
На - годовая норма амортизационных отчислений На = 02.
Стоимость приспособлений для первого и второго варианта изготовления изделия приведены в таблице 5.6.
Таблица 5.6 – Стоимость приспособлений
Стоимость приспособления тыс. рублей
Таким образом затраты на возмещение износа приспособлений целевого назначения определяются как: Исп1 = (40000×02)2 = 4000 рублей; Исп2 = 3000 рублей; Исп3 = 5000 рублей; Исп4 = 4000 рубля; Исп5 = 3000 рублей.
Аналогично рассчитываются затраты на возмещение износа приспособлений целевого назначения результаты расчетов по двум методам изготовления изделия сводятся в таблицу 5.7.
Таблица 5.7 – Затраты на возмещения износа приспособлений
Первый и второй вариант
Затраты на износ приспособления рублей
Расходы на содержание и эксплуатацию оборудованы определяются по формуле:
Рсэо = Рэ + Ра + Рр + Рпр
где Рэ - затраты на силовую энергию потребляемую для приведения в движение станков р.шт.;
Ра - расходы на амортизацию оборудования ршт.;
Рр - затраты на ремонт оборудования р.шт.;
Рпр - прочие затраты принимаются в размере 5% от вышеперечисленных затрат р.шт.
где - установленная мощность электродвигателя станка на котором выполняется операция кВт;.
- коэффициент загрузки электродвигателя по мощности равный 05-08;
- коэффициент учитывающий потери электроэнергии в сети равный 104- 108;
- средний коэффициент полезного действия электродвигателей для металлорежущих станков он равен 065.
Тогда расходы на силовую энергию потребляемую для приведения в движение станков определяются: Рэ1 = (12×156×07×106×1469) 065 = 314 рублей; Рэ2 = 15×184×07×106×1469 065 = 463 рубля.
Результаты расчетов приводятся в таблице 5.8.
Таблица 5.8 – Расходы на силовую энергию потребляемую для приведения в движение станков для двух вариантов изготовления детали
Номер и наименование операции
Применяемое оборудование
Затраты на силовую энергию рублей
0 Комбинированная с ЧПУ
Расходы на амортизацию оборудования определяются по формуле:
где - балансовая стоимость оборудования на котором выполняется операция р.ед.;
- норма амортизационных отчислений выраженная в процентах;
- норма штучного времени на выполнение операции минут;
- действительный эффективный фонд времени оборудования за год часов;
- коэффициент использования оборудования (его можно принять равным 085);
- коэффициент выполнения норм (его можно принять равным 1).
Таблица 5.9 –Исходные данные для расчета затрат на амортизацию оборудования
Первый и второй варианты изготовления детали
Стоимость единицы оборудования млн. руб.
Определяется величина расходов на амортизацию оборудования для станка модели 1Е61М: Ра1 = 1450000×65×9638(100×60×1930×085×1) = =922 рублей; для станка модели МDW-5F: Ра2 = 5000000×65×10796 (100×60 × 1930 × 085×1) = 3565 рублей. Значения затрат на амортизацию для других видов оборудования представлены в таблице 5.10.
Таблица 5.10 – Результаты расчетов расходов на амортизацию оборудования
Первый вариант изготовления детали
Величина расходов на амортизацию рублей
Затраты на ремонт оборудования (Рр) определяются по формуле:
где Кр - коэффициент затрат на текущий ремонт оборудования равный 0015.
Затраты на текущий ремонт оборудования для двух вариантов технологического процесса сводятся в таблицу 5.11.
Таблица 5.11 – Затраты на текущий ремонт оборудования
Величина расходов на текущий ремонт оборудования рублей
Расходы на использование площади помещения цеха (участка) определяется по формуле:
где - площадь занимаемая станком;
- коэффициент учитывающий дополнительную площадь (его можно принять равным 20%);
- средние расходы на содержание 1м помещения (можно принять в размере 80 тыс. рублей в год на 1м2).
Таблица 5.12 – Габаритные размеры и площади станков применяемых при изготовлении детали Корпус воздушного клапана
Габаритные размеры (длина × ширина) мм
Затраты на использование площади помещения участка сводятся в таблицу 5.13.
Таблица 5.13 – Затраты на использование площади помещения участка
Величина расходов на использование площади помещения участка рублей
Результаты расчетов технологической себестоимости обработки детали на отличающихся операциях вариантов технологических процессов оформляется в виде таблицы 5.14.
Таблица 5.14 - Сравнение вариантов технологического маршрута по технологической себестоимости
Наименование позиции
Стоимость заготовки рублей
Балансовая стоимость оборудования млн. рублей
Площадь занимаемая станками м2
Вспомогательные материалы на технологические нужды
Технологическая себестоимость вариантов рублей
Таким образом оптимальным является первый вариант технологического процесса изготовления детали.
2 Организационно-экономическая часть дипломного проекта
2.1. Экономическое обоснование проекта цеха (участка)
Целесообразность разработки и внедрения проекта цеха (участка) может быть оценена с помощью следующих характеристик:
-экономический эффект функционирования цеха (участка) за расчетный период (этот же показатель называют также интегральным экономическим эффектом или чистым дисконтированным доходом за расчетный период);
-внутренняя норма доходности (внутренний коэффициент эффективности) проекта;
-срок окупаемости или период возврата единовременных затрат;
-определение выручки от реализации продукции и критического объема производства.
Экономическое обоснование проекта цеха иди участка выполняется в следующей последовательности:
а) определяется потребность в инвестициях для организации проектируемого участка;
б) определяются текущие затраты связанные с функционированием цеха (участка);
в) формируется сводная таблица технико-экономических показателей проектируемого цеха (участка) и проводится их анализ;
г) рассчитывается экономическая эффективность проектируемого цеха (участка).
д) определяется точка безубыточности.
По данным анализа технико-экономических показателей оценкам экономической эффективности проекта цеха (участка) и предел безопасности объема выпуска (точки безубыточности) формулируются выводы и делается заключение о целесообразности и эффективности проектных решений.
2.2 Определение потребности в инвестициях для организации проектируемого участка
Создание проектируемого цеха (участка) требует определенных единовременных затрат (инвестиций) которые связаны во-первых с проведением технологической подготовки производства во-вторых с закупкой установкой и наладкой технологического подъемно-транспортного оборудования. Кроме того необходимо учесть затраты на технологическую оснастку инвентарь и хозяйственные принадлежности а также стоимость здания в котором расположен участок.
Из затрат на технологическую подготовку наиболее существенными являются: затраты на проектирование технологических процессов и затраты на проектирование приспособлений. Эти затраты рассчитываются по трудоемкости проектируемых работ и стоимости 1 человека-часа работы разработчиков.
Стоимость одного человека-часа С1ч-ч = Зср т Фн где Зср т – среднемесячная заработная плата технологов и конструкторов; Фн – номинальный фонд времени работы в месяц. Тогда С1ч-ч = 5000176 = 284 руб. Определим затраты на проектирование технологических процессов:
Зпр т п = С1ч-ч × Нпр + С1ч-ч × Нвн
где Нпр Нвн – нормы времени на проверку конструкции деталей на технологичность (разработку маршрутного и операционного технологических процессов нормирование технологического процесса) и на внедрение технологического процесса соответственно.
Таким образом Зпр т п = 284 * 286 + 284 * 29 = 163584 руб.
Аналогично рассчитаем затраты на проектирование приспособлений.
Зпр пр = С1ч-ч * (Нн и к пр + Нр и вс ин) = 284* (328 + 432) = 10542 руб.
Капиталовложения в оборудование рассчитываются по формуле:
Ко = Кто + Кэо + Кпт + Кку
где Кто Кэо Кпт Кку – капиталовложения соответственно в технологическое оборудование энергетическое оборудование подъемно-транспортное оборудование в средства контроля управления тыс. рублей.
Вложения в технологическое оборудование определяется как
kтз – коэффициент транспортно-заготовительных расходов равный 005-1 соответственно для тяжелого и легкого оборудования;
kc – коэффициент учитывающий затраты на строительные работы в том числе устройство фундаментов (kc = 007-008);
kмн – коэффициент учитывающий затраты на монтаж и наладку оборудования kмн = 01-015 от оптовой цены оборудования.
Таким образом Кто = 1450×(1+1+007+01) + 5000×(1+1+007+01) + 3500×(1+1+007+01) + 850×(1+008+007+01) + 350×(1+008+007+01) = =230915 тыс. рублей.
Укрупнено капиталовложения в энергетическое оборудование принимают равными 5-20% от стоимости технологического оборудования а подъемно-транспортное оборудование – 10-15% от Кто.
Соответственно Кэо = 230915 × 10100 = 230915 тыс. рублей.
Капиталовложения в средства контроля и управления технологическим процессом рассчитываются (если эти средства не входят в состав технологического оборудования) пропорционально затратам на технологическое оборудование исходя из конкретных условий производства (не более 3% стоимости) т. е. Кку = 230915 × 2100 = 46183 тыс. рублей.
При укрупненных расчетах затраты на оснастку можно принять в размере 7-10% от Кто (Косн = 230915 × 7100 = 16164 тыс. рублей) вложения в инвентарь и хозяйственные принадлежности долговременного использования – в размере 3-5% от стоимости технологического оборудования (Зин = 230915 × ×3100 = 6927 тыс. рублей).
Капитальные вложения в здание определяются по формуле:
где - стоимость 1 м2 здания 546 рублей;
- площадь участка (цеха) определяется исходя из его планировки.
Результаты расчета капиталовложений в основные производственные фонды участка занесем в таблицу 5.15.
Таблица 5.15 – Сводная ведомость капитальных вложений
Виды основных фондов
Количество ед. оборудования
Балансовая стоимость оборудования тыс. рублей
Балансовая стоимость основных фондов тыс. рублей
Годовая сумма амортизационных отчислений тыс. рублей
Технологич. оборудование:
Энергетическое оборудование
Подъемно-транспортное оборудование
Средства контроля и управления
Технологическая оснастка
Инвентарь и хозяйственные принадлежности
Капитальные вложения в здание
2.3 Расчет текущих затрат (плановой себестоимости продукции)
Начинать расчеты текущих затрат целесообразно с составления сметы общепроизводственных расходов. Общепроизводственные расходы делятся на две группы:
группа А - расходы на содержание и эксплуатацию оборудования (РСЭО);
группа Б - цеховые расходы.
Необходимо провести расчеты обеих групп расходов. При составлении сметы необходимо учитывать коэффициент загрузки оборудования по участку.
Расчет себестоимости детали изготавливаемой по проектируемой технологии следует оформить в виде таблицы 16.
Необходимо составить смету на РСЭО участка включающие следующие статьи:
Амортизация оборудования – определяется на основе балансовой стоимости оборудования участка и норм отчислений рассчитанных в таблице 15.
Эксплуатация оборудования.
Данная статья включает:
- затраты на вспомогательные материалы потребляемые в процессе эксплуатации оборудования – в укрупненных расчетах их сумма может быть принята в размере 5% от стоимости технологического оборудования (они составляют 229055 тыс. рублей);
- затраты на силовую энергию потребляемую для приведения в движение производственных машин и механизмов рассчитанную ранее и равную 2775 рублей;
- затраты на сжатый воздух для эксплуатации оборудования определяемые как произведение годового расхода сжатого воздуха (из расчета 5 м3 на 1 станок в смену) на цену 1 м3 сжатого воздуха (по ценам предприятия) - Зс в = 342 рублей;
- затраты на воду для производственных нужд (при отсутствии точных данных можно принять средний расход воды на один металлорежущий станок 06 литра в час цену воды принять по данным предприятия) – Зв = 2088 рублей;
- основную и дополнительную заработную плату вспомогательных рабочих обслуживающих оборудование (наладчиков слесарей и др.) с начислениями на социальные нужды определяется по штатному расписанию вспомогательных рабочих или укрупнено в размере 30% от основной и дополнительной зарплаты.
Текущий ремонт оборудования транспортных средств и дорогостоящего инструмента.
Расходы по содержанию и эксплуатации транспорта.
Износ малоценных и быстро изнашиваемых инструментов и приспособлений.
Затраты по статье определяются укрупнено из расчета 50 тыс. руб. на один станок в год.
Прочие расходы – составляют примерно 3% от общей стоимости суммы затрат по перечисленным выше статьям.
Результаты расчетов расходов на РСЭО участка Рсэо = 429385 рублей.
Таблица 5.16 –Калькуляция себестоимости детали
где НР – норма расхода материала на изделие кг;
УМ – оптовая цена материала рубкг.
Вспомогательные материалы для технологических целей
где НО – норма отходов на изделие кг;
ЦО – цена отходов рубкг.
ОВ = 067× 153 = 1025
Основная заработная плата основных производственных рабочих
Дополнительная заработная плата основных производственных рабочих
ЗД = 1144×0235 = 269
Начисления на социальные нужды
ОСОЦ = (ЗО + ЗД) * КСОЦ 100
ОСОЦ = (1144 + + 269) × 026= = 367
Износ специальных инструментов и приспособлений
где - ставка погашения стоимости специальной оснастки =
= 2165(2 × 174 ×24) = 0026
Расходы на содержание и эксплуатацию оборудования
ОПР включает в себя расходы на подготовку и освоение производства износ специальных элементов и приспособлений расход на содержание и эксплуатацию оборудования и цеховые расходы
По данным завода ОПР = 2165* 461100 = 998
Цеховая себестоимость детали
СЦ = МО - ОВ + ЗО + ЗД + ОСОЦ + Исп + Рсэо +
+ ОПР = 2295 – 1025 + 1144 + 269 + 367 + 45 + 429385 + 998 = 569275
Общехозяйственные расходы
Рх = ЗО × Крх где Крх – коэффициент общехозяйственных расходов.
Рх = 1144 × 100100 = 1144
Производственная себестоимость
Спр = 569275 + 1144 = 580715
Коммерческие расходы
Рк = Спр × Кк где Кк – коэффициент коммерческих расходов равный 08%.
Рк = 580715×0008 = 465
Полная себестоимость детали
Сп = 580715 + 465 = 58537
Годовые текущие издержки участка определяются по формуле:
где - годовая программа выпуска равная 2000 штукам.
Таким образом годовые текущие издержки участка равны Иг = 58537 × 2000 = 11707400 рублей.
2.4 Расчет технико-экономических показателей проектируемого (участка) и их анализ
Производится расчет основных технико-экономических показателей результаты заносятся в таблицу 5.17.
Таблица 5.17 – Технико-экономические показатели проектируемого цеха (участка) по изготовлению детали «Корпус воздушного клапана»
Наименование показателя
Абсолютные показатели
1 Годовой выпуск продукции:
в натуральном выражении штук; стоимостном выражении тыс. рублей
2 Количество единиц технологического оборудования цеха (участка)
3 Общая стоимость основных производственных фондов участка тыс. рублей
б) технологическое оборудование
4 Общая площадь участка м2
5 Численность основных производственных рабочих цеха (участка) чел
6 Фонд заработной платы основных рабочих тыс. рублей
Относительные показатели
1 Выпуск продукции на одного производственного рабочего в денежном выражении (по цеховой себестоимости) тыс. рублейчел
2 Выпуск продукции на м2 производственной площади тыс. рублей м2
3 Фондоотдача (по цеховой себестоимости) рр
4 Средняя загрузка оборудования %
5 Фондовооруженность труда млн. рублейчел
6 Уровень механизации труда %
Показатель фондоотдача рассчитывается как отношение годового выпуска продукции (по цеховой себестоимости) к общей стоимости основных производственных фондов цеха (участка).
Средняя загрузка оборудования определяется отношением количества оборудования цеха (участка) к принятому количеству.
Фондовооруженность труда определяется как отношение общей стоимости основных производственных фондов цеха (участка) к численности основных производственных рабочих.
Уровень механизации труда при использовании проектируемой технологии рассчитывается как отношение машинного времени на изготовление детали на норму штучного времени.
По результатам проведенных расчетов основных технико-экономических показателей таких как: фондовооруженность фондоотдача уровень механизации и другие – проект является эффективным но низкое значение коэффициента загрузки оборудования говорит о возможности производства на данном участке подобных деталей то есть дозагрузки оборудования. Также существует (благодаря применяемому в основном универсальному оборудованию) возможность переналадки производства.
3 Расчет показателей экономической эффективности цеха (участка)
Экономический эффект от функционирования цеха (участка) на котором детали изготавливаются по разработанной технологии рассчитывается на определенный период. В качестве начального года расчетного периода принимается год начала финансирования работ по проектированию технологии и созданию цеха (участка). Конечный год расчетного периода может определяться плановыми сроками обновления продукции и технологии ее изготовления.
Экономический эффект реализации проекта цеха (участка) за расчетный период может быть определен по формуле:
где - неизменная по годам расчетного периода стоимостная оценка результатов производства продукции с использованием разработанного технологического процесса рублей;
- неизменные по годам расчетного периода затраты на изделие с применением разработанного технологического процесса рублей;
- норма реновации исчисленная для периода использования спроектированной технологии равная 01638;
- норматив приведения разновременных результатов и
затрат численно равный нормативу эффективности капитальных
- единовременные затраты на реализацию разработанной технологии не увеличивающие стоимости основных фондов и не относимые на себестоимость продукции (например затраты на НИР затраты на освоение новых технологических процессов и т.д.) рублей.
Величина определяется по формуле:
где - оптовая цена i-го вида производимой на спроектированном участке рублей = ( - коэффициент рентабельности к полной себестоимости продукции составляющий 20-50 %)
- годовая программа выпуска деталей
n – число наименований деталей изготавливаемых на спроектированном участке по технологиям.
Итогом расчета стоимостной оценке результатов производства продукции с использованием разработанных технологических процессов является =906250 рублей.
Так как основные фонды привлекаются для производства продукции по новой технологии лишь на небольшую часть своего годового фонда рабочего времени то есть на участке производятся различные виды деталей в том числе и по другим технологиям не разрабатываемым в дипломном проекте то допустимо использование следующего приближенного метода расчета :
где Иг – текущие издержки производства (себестоимость годового выпуска продукции) включая затраты на амортизацию основных фондов рублей;
Фоi – остаточная стоимость основных фондов i-го вида определяемая по формуле:
где - годовая норма амортизационных отчислений для основных фондов i-го вида %.
Таким образом при Фо =1621600 рублей неизменные по годам расчетного периода затраты на изделие с применением разработанного технологического процесса = 1642395 + 01×1621600 = 3263995 рублей а экономический эффект составляет 21953786 рублей.
Внутренняя норма доходности (внутренний коэффициент эффективности) проекта определяется по формуле:
где К – единовременные затраты на создание участка (см. п. 5.2.2).
Рассчитывается внутренний экономический эффект: е = (906250 – 3263995) 17440000 × 00135= 0246.
Так как коэффициент загрузки оборудования производства деталей по спроектированной технологии меньше 08 то следует учесть это обстоятельство при расчете инвестиций в основные фонды умножив их стоимость на данный коэффициент.
Срок окупаемости капитальных вложений в проект определяется по формуле:
Срок окупаемости для данного проекта = 1 0246 = 4.
По результатам расчетов е и Ток делается вывод об эффективности проекта. Так как Эт > 0 е > = 015 а срок окупаемости капитальных вложений меньше срока использования разработанной технологии на спроектированном участке то разработанные в дипломном проекте инженерные решения можно считать экономически эффективными.
К показателям эффективности проекта также относятся:
Снижение себестоимости изготовления детали выраженные процентах:
где - цеховая себестоимость детали по базовому и проектируемому техпроцессам рублей.
=100× 1969458337 = 236 %;
где М1 М2 - расход материала на изделие в базовом и проектируемом вариантах производства кг.
= (24 – 147)×2000 = 1860 кг;
Снижение трудоемкости изготовления детали:
где - трудоемкость изготовления единицы продукции по базовому и спроектированному техпроцессам минут.
= (625×100259) – 100 = 141%;
Условное высвобождение численности рабочих чел:
где - эффективный фонд времени рабочего за год часов.
= (625 – 259)×24182272×1×60 = 01 человек.
Рассчитанные показатели экономической эффективности проекта сводятся в таблицу 5.18.
Таблица 5.18 – Показатели экономической эффективности проекта
Наименование показателей
Интегральный экономический эффект млн.р
Внутренний коэффициент эффективности
Срок окупаемости лет
Снижение себестоимости изготовления детали %
Экономия материала кг
Снижение трудоемкости изготовления детали %
Условное высвобождение численности рабочих чел
4 Структура и состав механического цеха
Инструментальное хозяйство занимает ведущее место в системе технического обслуживания производства. Современный технический и организационный уровень машиностроения определяется высокой оснащенностью его моделями штампами пресс-формами приспособлениями режущим мерительным и вспомогательными инструментами и приборами объединяемыми в общий комплекс технологической оснастки. Крупные производственные объединения (предприятия) используют сотню тысяч различных наименований инструментов и другой технологической оснастки. От степени ее совершенства своевременности обеспечения ею рабочих мест и размеров затрат на инструмент непосредственно зависят важнейшие показатели работы предприятия: производительность труда качество и себестоимость продукции ритмичность производства.
При выполнении дипломного проекта были решены следующие задачи:
- проведен анализ технологичности конструкции детали и сделан вывод о невысокой технологичности;
- выбрана форма и метод получения исходной заготовки для данного типа производства;
- разработан технологический процесс для изготовления детали;
- взамен специальных дорогостоящих приспособлений рассчитана и спроектирована высокоточная универсально-сборочная оснастка применяемая на токарных фрезерных и сверлильных станках;
- спроектировано устройство для контроля шероховатости цилиндрических отверстий;
- проведено исследование влияния износостойких покрытий на свойства режущего инструмента и режимы обработки детали а также методов нанесения этих покрытий;
- проведен технико-экономический анализ эффективности разработанного технологического процесса.
- взамен дорогостоящего оборудования использованы универсальные металлорежущие станки обеспечивающие на всех операциях совместно с твердосплавным инструментом прогрессивные режимы резания;
Проделанная работа гарантирует высокое качество и надежность деталей.
Маталин А.А. Технология машиностроения: Учеб. для студ. машиностроительных специальн. вузов.- Л.: Машиностроение 1985. - 496 с.
Ковшов А.Н. Технология машиностроения: Учеб. для студ. машиностроительных специальн. вузов.- М.: Машиностроение 1987. - 320 с.
Технология машиностроения (специальная часть). Б.Л. Беспалов Л.А. Глейзер И.М. Колесов и др.- М.: Машиностроение 1973.- 448 с.
Верещак А.С.Третьяков И.П. Режущие инструменты с износостойкими покрытиями. - М.: Машиностроение1986. – 192 с. ил.
Приданцев М.В. Давыдова Л.Н. Тамарина И.А. Конструкционные стали (справочник). - М.: Металлургия 1980. - 288 с.
Федотиков А.П. Краткий справочник технолога-машиностроителя. М.: ГНТИ Оборонгиз 1960. - 403 с.
Проектирование технологических процессов механической обработки деталей: Методические указания для выполнения курсовой работы по дисциплине «Технология машиностроения» В.Н. Самохвалов. - Самара: СамИИТ 2000. - 29 с.
Методические указания к выполнению индивидуальной работы по дисциплине: «Организационно-технологическая подготовка производства» для студентов всех форм обучения по специальности 120100 - «Технология машиностроения» (в электронном виде на магнитном носителе) Часть 1. Раздел «Технологичность конструкции изделий. Обработка резанием». Сост.: Бородкин В.В. Болдырев А.И. Бочаров В.Б. Кириллов О.Н. Чечета И.А. Воронеж: ВГТУ 1999. - 33 с. (№ 229-99).
Технологичность конструкции изделия: Справочник Ю. Д. Амиров Т. К. Алферова П. Н. Волков и др.; Под общ. ред. Ю. Д. Амирова. - 2-е изд. перераб. и доп. - М.: Машиностроение 1990. - 768 с.
ЕСТПП. ГОСТ 14.004-83. Термины и определения основных понятий. - М.: ГК СССР по стандартам 1984. - 8 с.
Курсовое проектирование по технологии машиностроения: Учеб. пособие Л.В. Худобин В.Ф. Гурьянихин В.Р. Берзин. - М.: Машиностроение 1989. - 288 с.
Курсовое проектирование по технологии машиностроения: Учеб. пособие для вузов Под. общ. ред. А. Ф. Горбацевича. -3-е изд. перераб. и доп. - Минск: Высшая школа 1975. - 488 с.
Методические указания к выполнению курсового проекта по дисциплине «Технология изготовления штампованных литых и сварных заготовок» для студентов всех форм обучения специальности 120100 «Технология машиностроения» Воронеж. гос. техн. ун-т; Сост.: И. А. Чечета; В. А. Сай В. В. Бородкин. - Воронеж 1999. - 34 с.
Брюханов А.Н. Ковка и объемная штамповка: Учеб. пособие. - М.: Машиностроение 1975. - 408 с.
Согришин Ю.П. Гришин Л.Г. Воробьев В.М. Штамповка на высокоскоростных молотах. - М.: Машиностроение 1978. - 167 с.
Методические указания к проведению индивидуальной работы по курсу «Технология изготовления штампованных литых и сварных заготовок» для студентов всех форм обучения по специальности 120100 «Технология машиностроения» Воронеж. политехн. ин-т; В.В. Бородкин И.А. Чечета В.А. Сай. Воронеж 1992 28 с. (№ 58-92).
Титов Н.Д. Технология литейного производства.- М.: Машиностроение 1968. - 388 с.
Справочник технолога-машиностроителя. Том 1. Под ред. А.Г. Косиловой и Р.К. Мещерякова. - М.: Машиностроение 1972. - 694 с.
Анурьев В.И. Справочник конструктора-машиностроителя. Т. 1. - М.: Машиностроение 1978. - 728 с.
Обработка металлов резанием: Справочник технолога А.А. Панов В.В. Аникин Н.Г. Бойм и др. - М.: Машиностроение 1988. - 736 с.
ЕСТПП. ГОСТ 14.301-83. Общие правила разработки технологических процессов и выбора технологического оснащения. - М.: ГК СССР по стандартам 1984. - 6 с.
Добрыднев И.С. Курсовое проектирование по предмету «Технология машиностроения»: Учебн. пособие. - М.: Машиностроение 1985. - 184 с.
Справочник технолога-машиностроителя. Том 2.Под ред. А.Н. Малова. - М.: Машиностроение 1972. - 568 с.
Общемашиностроительные нормативы времени вспомогательного на обслуживание рабочего места и подготовительно-заключительного для технического нормирования. Серийное производство. - М.: Машиностроение 1974. - 328 с.
Общемашиностроительные нормативы режимов резания для технического нормирования работ на металлорежущих станках. Ч.1. Токарные карусельные токарно-револьверные алмазно-расточные сверлильные строгальные долбежные и фрезерные станки. - М.: Машиностроение 1967. - 279 с.
Режимы резания металлов. Справочник: Под ред. Ю.В. Барановского. - М.: Машиностроение 1972. - 598 с.
Станочные приспособления: Справочник. Т. 1 Под ред. Б.Н. Вардашкина А.А. Шатилова. - М.: Машиностроение 1984. - 592 с.
Станочные приспособления: Справочник. Т. 2 Под ред. Б.Н. Вардашкина В.В. Данилевского. - М.: Машиностроение 1984. - 656 с.
Худобин Л.В. Гурьянихин В.Ф. Берзин В.Р. Расчет и проектирование специальных средств технологического оснащения в курсовых и дипломных проектах: Учеб. пособие. - Ульяновск: УлГТУ 1997. - 64 с.
Егоров М.Е. Основы проектирования машиностроительных заводов. – 6-е изд. перераб. и доп. Учебник для машиностроительных вузов. М.: Высш. шк. 1969. – 480 с.
Проектирование машиностроительного производства: Учеб. пособие В.Б. Бочаров А.И. Болдырев К.В. Бородкин. - Воронеж: ВГТУ 2002. - 176 с.
Норенков И.П. Автоматизированное проектирование: Учеб. пособие. - М.: Изд-во МГТУ им. Н.Э. Баумана 2000. - 188 с.
Спецификации к графической части проекта
Эконом. 2.cdw

по изготовлению детали «Корпус воздушного клапана»
Планир. уч.cdw

для изготовления корпуса клапана ракетного двигателя
Деталь 3Д.m3d

Заготовка А1.cdw

Неуказанные радиусы закруглений 2 мм.
Допускаемое смещение штампов 0
Остающийся заусенец 0
Разработка технологии и технологического оснащения
для изготовления корпуса клапана ракетного двигателя
Исследов. 2.cdw

твердосплавных пластинок при точении:
-точение стали 45 (НВ180) пластинками Т5К10;
- точение серого чугуна СЧ 32 (НВ200) пластинками ВК6;
- точение стали 45 (НВ180) пластинками ТТ10К8Б;
- точение стали 45(НВ180) пластинками ВК6;
Рисунок 2-Влияние толщины покрытия на стойкость твердосплавных
пластинок при симметричном фрезеровании стали 40Х (НВ 220) с
ммзуб; v=170 ммин; z=1
Рисунок 3-Влияние скорости резания на коэффициент повышения стой-
кости твердосплавных пластинок ТТ10К8Б с различными толщинами
покрытий TiC ГТ при точении стали 45 (НВ 180) с s=0
мм. Толщина покрытия:
Рисунок 4-Влияние подачи на коэффициент повышения стойкости
твердосплавных пластинок ТТ10К8Б с различными толщинами
Толщина покрытия TiC ГТ
Влияние износостойких покрытий на свойства режущего инструмента
ТП на диплом.doc
технологического процесса
Сплав алюм. АК-6 ПП ГОСТ 21488-97
Код наименование операции
Обозначение документа
Код наименование оборудования
Хранить и транспортировать деталь в таре
2 А Заготовительная .20140.00005.
Выполняется по тех. процессу кузнечного цеха
1 005 0190 Слесарная .20140.00005.
Верстак .60188. 0340
1 010 4110 Токарная .20140.00005.
Е61М ст. ток.-винт. .60146. 0164
Наименование детали СЕ или материала
1 015 4110 Токарная с ЧПУ .20140.00005.
MDW-5F ст. ток.-винт. .60146.
1 020 4110 Токарная с ЧПУ .20140.00005.
MDW-5F ст. ток.-винт. .60146.
1 025 4110 Токарная .20140.00005.
Е61М ст. ток.-винт. .60146.
1 030 4110 Токарная .20140.00005.
1 035 4110 Токарная с ЧПУ .20140.00005.
1 040 4103 Комбинированная с ЧПУ .2014000005.
ИР-320 ст. комбинированный .60146.
1 045 4260 Фрезерная .20140.00005.
Р13 вертик.-фрез. .60141.
1 050 4110 Токарная с ЧПУ .20140.00005.
MDW-5F ст. ток.-винт. .60140.
1 055 4260 Фрезерная .20140.00005.
1 060 4260 Фрезерная .20140.00005.
1 065 0190 Слесарная .20140.00005.
1 070 Электроэрозионная .20140.00005.
Электроэрозионная установка .60184.
1 075 4110 Токарная с ЧПУ .20140.00005
1 080 4120 Сверлильная .20140.00005.
Н125 вертик.-сверлильн. .60146.
1 085 4120 Сверлильная .20140.00005.
1 090 0190 Слесарная .20140.00005.
Настольное сверло .60188.
1 095 0190 Слесарная .20140.00005.
1 100 4110 Токарная с ЧПУ .20140.00005.
1 105 0190 Слесарная .20140.00005.
1 110 0131 Промывочная .20140.00005.
1 115 0191 Слесарно-сдаточная .20140.00005.
1 120 Контроль твердости
1 130 4110 Токарная .20140.00005.
Е61М ст. ток.-винт. .60146. 0164
1 135 0190 Слесарная .20140.00005.
1 140 4110 Токарная .20140.00005.
1 145 4110 Токарная .20140.00005.
1 150 0131 Промывочная .20140.00005.
1 155 Испытание на прочность и герметичность
1 160 Испытание на разрушение
1 165 0191 Слесарно-сдаточная .20140.00005.
1 175 5161 Анодирование
1 185 Комплектовка .20140.00005.
1 190 0190 Слесарная .20140.00005.
1 195 0131 Промывка в бензине .20140.00005.
1 200 0190 Слесарная .20140.00005.
1 205 0131 Промывка в бензине .20140.00005.
Наименование операции
Оборудование устройство ЧПУ
Обозначение программы
А. Установить деталь и после обработки снять
Расточить перед началом обработки сырые кулачки
Рез.ВК8-3-R05 ГОСТ18871-73; ШЦ--250-005 ГОСТ166-73; РГ-250 ГОСТ162-73
Центровать торец (9)
Сверло центровочное ø10 ГОСТ 13214-67
Сверлить отверстие (4)
Сверло ø25 ГОСТ 10903-77; Пробка ø25 ГОСТ18362-73
Точить поверхн. (7) (5)- под резьбу ø2843 на длину l=19±04
Резец расточной ГОСТ18883-73; Пробка ø2843 ГОСТ18362-73; ШГ 250 ГОСТ7470-78
Точить поверхн. (1) (3) (6) (10)
Резец расточной ГОСТ 18883-73; Нутромер ø307 ГОСТ18362-73; ШГ сп. ГОСТ7470-78
Резец расточной ГОСТ18883-73; Нутромер ø30 ГОСТ18362-73; ШГ 250 ГОСТ7470-78
Притупить острые кромки (01 04) мм
Оправка резьбовая ГОСТ 16211-70
Сверло ø18 ГОСТ10903-77; Пробка ø18 ГОСТ18362-73
Расточить (3)- окончательно
Резец расточной ВК8-3-R05 ГОСТ18883-73; ШГ 250 ГОСТ7470-78; МК 125-150 ГОСТ6507-73
Точить поверхн. (6) (5) (2)- окончательно; (4) выдержав размер под резьбу ø2043 ;(9)- окончательно
Резец расточной ГОСТ18883-73; Пробка ø2043 ГОСТ18362-73; Пробка ø26 ГОСТ18362-73; Пробка ø222 ГОСТ18362-73
Расточить поверхн. (7) (8)- окончательно
Резец расточной ГОСТ18883-73; Меритель ( Шаблон ( Нутромер ø35 ГОСТ18362-73
Расточить поверхн. (4)- окончательно
Резец расточной ГОСТ18883-73; Пробка ø20376 ГОСТ18362-73
Точить поверхн. (10) (11)- окончательно
Резец канавочный ГОСТ18879-73; Меритель ø24±02 ГОСТ18362-73; ИЧ 10 кл.1 ГОСТ1356-79; Планка ГОСТ112-73; Вставка ГОСТ110-73
Притупить острые кромки по программе (01 04) мм в перех. 2 3 4.
Контроль исполнения
Проверить перед началом обработки биение посадочных поверхностей оправки (не более 003 мм)
Штатив ШМ-Н8 ГОСТ162-73; ИЧ -10 кл.1 ГОСТ18362-73
Расточить (7) (6) (5) (3) (2)- окончательно; (4)- под резьбу ø3143
Резец расточной ВК8-3-R05 ГОСТ18883-73; ШГ 250 ГОСТ7470-78; ; Пробка ø37 ГОСТ18362-73; Пробка ø332 ГОСТ18362-73;
Пробка ø3143 ГОСТ18362-73; Нутромер ø315 ГОСТ18362-73
Точить поверхн. (1)- окончательно
Резец расточной ГОСТ18883-73; Пробка ø28 ГОСТ18362-73 ШГ 250 ГОСТ7470-78
Расточить поверхн. (8) (9) (10) (11)- окончательно
Резец расточной ГОСТ18883-73; Нутромер ø333 ГОСТ18362-73; ШГспец. (l=21±04) ГОСТ7470-78
Резец расточной ГОСТ18883-73; Пробка ø31376 ГОСТ18362-73
Точить поверхн. (12) (13)- окончательно
Резец канавочный ГОСТ18879-73; Меритель ø35±02 ГОСТ18362-73; ИЧ 10 кл.1 ГОСТ1356-79; Планка ГОСТ112-73; Вставка ГОСТ110-73
Угольник ГОСТ 16468-73; Наладка специальная
Подрезать торец Т2 как чисто
Резец подрезной отогнутый ГОСТ 18871-73
Сверлить отверстие (1)
Сверло спиральное ø12 ГОСТ10903-77; Пробка ø12 ГОСТ18362-73
Расточить отверстие (1) под резьбу на ø1443
Резец расточной ГОСТ18883-73; Пробка ø1443 ГОСТ18362-73; Пробка ø162 ГОСТ18362-73; ШГ 250 ГОСТ7470-78
Расточить отверстие (2) угол 45º
Расточить отверстие (3)
Резец расточной ГОСТ18883-73; Пробка ø20 ГОСТ18362-73
Резец расточной ГОСТ18883-73; Резец резьбонарезной ГОСТ 18885-73
Резец канавочный ГОСТ18879-73; Меритель ø18±02 ГОСТ18362-73; ИЧ 10 кл.1 ГОСТ1356-79; Планка ГОСТ112-73; Вставка ГОСТ110-73
Притупить острые кромки фаской или любой кривой R 03мм.
Сверло спиральное ø17 ГОСТ10903-77; Пробка ø17 ГОСТ18362-73
Расточить отверстие (2) под резьбу на ø2043
Резец расточной ГОСТ18883-73; Пробка ø2043 ГОСТ18362-73
Расточить отверстие (1)
Резец расточной ГОСТ18883-73; Пробка ø18 ГОСТ18362-73
Расточить отверстие (3) и фаску 1×45º
Резец расточной ГОСТ18883-73; Пробка ø30 ГОСТ18362-73; Фаскомер ГОСТ 1356-79
Резец резьбонарезной ГОСТ 18885-73; Резьбовой калибр М22×15-6Н ГОСТ 1452-73
Расточить барабан (4)
Резец расточной ГОСТ18883-73; ; ШГ 250 ГОСТ7470-78; Нутромер ГОСТ 18362-73
Расточить (5)- окончательно
Резец расточной ВК8-3-R05 ГОСТ18883-73; ШЦ-250-005 ГОСТ166-73; ШГ 250 ГОСТ 162-73
Сверлить отверстие (2)-предварительно
Сверло ø12 ГОСТ10903-77; ШЦ -250-005 ГОСТ166-73
Расточить поверхн. (4) (3) (1)- окончательно; (2)-под резьбу ø1443
Резец расточ. ГОСТ18883-73; Пробка ø20 ГОСТ18362-73; Пробка ø162 ГОСТ18362-73 ; ШГ-250 ГОСТ162-733;
Пробка ø1443 ГОСТ18362-7
Расточить поверхн. (2)- окончательно
Резец расточной ГОСТ18883-73; Пробка ø14376 ГОСТ18362-73
Точить поверхн. (6) (7)- окончательно
Резец канавочный ГОСТ18879-73; Меритель ø18±02 ГОСТ18362-73; ИЧ 10 кл.1 ГОСТ1356-79; Планка ГОСТ112-73; Вставка ГОСТ110-73
Притупить острые кромки по программе (01 04) мм в перех. 2 4.
Комбинированная с ЧПУ
Наладка специальная с поворотным столом
Выставить перед началом обработки приспособление по посадочным поверхностям с точностью до 003 мм
ИЧ -10 кл.1 ГОСТ18362-73
Обработать поверхн.(3) (5)
Фреза пальцевая ø40 ГОСТ 8720-69; ШЦ-250-005 ГОСТ166-73; ШГ 250 ГОСТ 162-73
Повернуть деталь со столом на угол 180º; Обработать поверхн. (2) (1) (4)
Фреза ø40 ГОСТ8720-69; ШЦ -250-005 ГОСТ166-73; ШГ 250 ГОСТ 162-73; Меритель l=36±04 ГОСТ 18362-73
Центровать 2 отв. (7)
Сверло центровочное ø315 ГОСТ 13214-67
Сверло спиральное ø42 ГОСТ10903-77; ШГ 250 ГОСТ 162-73
Зенкеровать 2 отв. (7)
Зенке ø505 ГОСТ 12489-67; Пробка ø505 ГОСТ18362-73; Меритель l=18 ГОСТ18362-73
Зенкеровать 2 отв. (6)
Зенке ø7 ГОСТ 12489-67; Пробка ø7 ГОСТ18362-73; ШЦ -125-01 ГОСТ166-73
Контроль исполнения БТК.
Резьбовая оправка ГОСТ162-70; Угольник ГОСТ 16468-73
Фрезеровать 2 бабышки
Фреза пальцевая ø40 ГОСТ 8720-69; Меритель 36±04 ГОСТ 18362-73
Обработать поверхн.: (3) (4) (11) (Т) (7)- предварительно
Обработать поверхн.: (5) (8) (Т) (Т1) (Т2) (2) - окончательно
Резец расточной отогнутый ГОСТ 18871-73; Нутромер ø37 ГОСТ 18362-73; Глубиномер инд. ГОСТ 7470-78; Скоба ø24 ГОСТ 18362-73
Набор мерителей 1 кл. 3 ГОСТ 18362-73 ( l=18±02).
Расточить поверхн. (7) (6))- окончательно; (4)-под резьбу ø3443 ; (11) (3)- окончательно.
Резец расточ. ГОСТ18883-73; Пробка ø3443 ГОСТ18362-73; Пробка ø3401 ГОСТ18362-73 ; ШГ-250 ГОСТ162-733;
Пробка ø28 ГОСТ18362-73
Расточить поверхн. (1)- окончательно
Резец расточной ГОСТ18883-73; Пробка ø20 ГОСТ18362-73; Меритель ( l= 52±02) ГОСТ 18362-73
Точить поверхн. (10)- окончательно
Резец расточной ГОСТ18883-73; ШГ-250 ГОСТ162-733; Нутромер ø35 ГОСТ 18362-73; Шаблон (l=15±02) ГОСТ 18362-73
Расточить поверхн.: (9) (12) (13) (14)- окончательно
Резец расточной ГОСТ18883-73; Нутромер ø363 ГОСТ 18362-73; Меритель ( l= 4±02) ГОСТ 18362-73
Нарезать резьбу (4)-окончательно
Резец резьбонарезной ГОСТ18885-73; ; Пробка ø34376 ГОСТ18362-73
Притупить острые кромки по программе (01 04) мм в перех. 3 4 5 6 7.
Резьбовая оправка ГОСТ162-70; Угольник ГОСТ 16468-73; Делительная головка ГОСТ 1647-73
Фрезеровать поверхн. (1)
Фреза пальцевая ø50 ГОСТ 8720-69; ШЦ-250-005 ГОСТ166-73
Осуществить поворот детали на угол 180º; Фрезеровать поверхн. (2)
Фреза пальцевая ø40 ГОСТ 8720-69; ШЦ-250-005 ГОСТ166-73
Обработать поверхн.: (5)- окончательно
Резец подрезной ВК8-3-R05 ГОСТ18883-73; ШЦ-250-005 ГОСТ166-73; ШГ 250 ГОСТ 162-73
Сверлитьотверстие (2)- предварительно
Сверло спиральное ø12 ГОСТ10903-77; ШЦ-250-005 ГОСТ 166-73
Расточить поверхн. (4) (3) (1)- окончательно; (2)-под резьбу ø1443
Резец расточ. ГОСТ18883-73; Пробка ø1443 ГОСТ18362-73; Пробка ø162 ГОСТ18362-73 ; ШГ-250 ГОСТ162-733;
Пробка ø20 ГОСТ18362-73
Точить поверхн. (6) (7)- окончательно
Кондуктор ГОСТ 16751-73
Сверло спиральное ø42 ГОСТ 8720-69
Зенкеровать 2 отв. (2)
Зенкер ø505 ГОСТ 12489-67; ШЦ-250-005 ГОСТ166-73; Пробка ø505 ГОСТ18362-73
Зенкеровать 2 отв. (1)
Зенкер ø7 ГОСТ 12489-67; ШГ-250 ГОСТ162-733 ; Пробка ø7 ГОСТ18362-73
Контроль исполнения.
Сверлить 8 отв. (1) последовательно
Сверло спиральное ø10 ГОСТ 8720-69; ШЦ-250-005 ГОСТ166-73; Пробка ø10 ГОСТ18362-73
Оправка цех. ГОСТ 16211-70
Проверить перед началом обработки биение посадочных поверхностей оправки (не более 002 мм)
Обработать поверхн.: (4) (5) (Т)-предварительно; (1)-окончательно
Точить поверхн. (Т) (2)-окончательно
Резец расточ. ГОСТ18883-73; Пробка ø20 ГОСТ18362-73; Меритель l=845±03 ГОСТ18362-73
Расточить поверхн. (Т2) (5) (7) (Т1) (3)- окончательно
Резец расточ. отогнутый ГОСТ18883-73; Меритель ø24 ГОСТ 18362-73 ; Меритель Шаблон l=68±02 ГОСТ 18362-73
Нутромер ø37 ГОСТ18362-73
Зенкеровать поверхн. (4)- окончательно
Зенкер ГОСТ12489-71;
Развернуть поверхность (4) окончательно
Равертка ГОСТ11172-70; Пробка ø30Н8 ГОСТ18362-73;
Притупить острые кромки по программе (01 04) мм в перех. 3 4 5.
Резьбовая оправка ГОСТ 16211-70
Резец канавочний отогнутый ГОСТ 18871-73; Шаблон Глубиномер Нутромер ГОСТ 18362-73
Точить уплотнительный элемент (А)
Резец спец. ГОСТ 18883-73; Меритель Глубиномер l=85±02 ГОСТ 7470-78
Резец спец. ГОСТ 18883-73; Меритель Глубиномер l=30±02 ГОСТ 7470-78
Эконом. 1.cdw

Зам. начальника цеха
Структура механического цеха
Рекомендуемые чертежи
- 24.01.2023
- 24.01.2023
- 24.01.2023