Разработка техпроцесса и средств технологического оснащения для изготовления детали Корпус




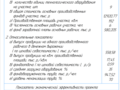
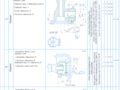
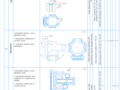
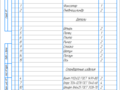
- Добавлен: 24.01.2023
- Размер: 27 MB
- Закачек: 1
Описание
Состав проекта
![]() |
![]() |
![]() |
![]() |
![]() ![]() ![]() |
![]() ![]() ![]() |
![]() ![]() ![]() |
![]() ![]() ![]() |
![]() ![]() ![]() |
![]() ![]() ![]() |
![]() ![]() ![]() |
![]() ![]() ![]() |
![]() ![]() ![]() |
![]() ![]() ![]() |
![]() ![]() ![]() |
![]() ![]() ![]() |
![]() |
![]() |
![]() |
![]() |
![]() |
![]() ![]() ![]() |
![]() ![]() ![]() ![]() |
![]() ![]() ![]() |
![]() |
![]() |
![]() |
![]() ![]() ![]() ![]() |
![]() ![]() ![]() ![]() |
![]() |
![]() |
![]() |
![]() |
![]() |
![]() |
![]() |
![]() |
![]() ![]() ![]() ![]() |
![]() |
![]() ![]() ![]() ![]() |
![]() |
![]() ![]() ![]() ![]() |
![]() |
![]() ![]() ![]() ![]() |
![]() ![]() ![]() ![]() |
![]() |
![]() ![]() ![]() ![]() |
![]() ![]() ![]() ![]() |
![]() |
![]() |
![]() ![]() ![]() ![]() |
![]() |
![]() ![]() ![]() ![]() |
![]() |
![]() ![]() ![]() ![]() |
![]() |
![]() |
![]() |
![]() |
![]() |
![]() |
![]() |
![]() |
![]() ![]() ![]() ![]() |
![]() |
![]() ![]() ![]() ![]() |
![]() |
![]() |
![]() |
![]() |
![]() |
![]() |
![]() |
![]() |
![]() |
![]() |
![]() |
![]() ![]() ![]() |
![]() |
![]() |
![]() ![]() ![]() ![]() |
![]() ![]() ![]() ![]() |
![]() ![]() ![]() ![]() |
![]() ![]() ![]() ![]() |
![]() |
![]() |
![]() |
![]() ![]() ![]() ![]() |
![]() |
![]() |
![]() |
![]() |
![]() |
![]() |
![]() ![]() ![]() |
![]() ![]() ![]() |
![]() ![]() ![]() |
![]() ![]() ![]() ![]() |
![]() ![]() ![]() ![]() |
![]() ![]() ![]() |
![]() ![]() ![]() |
![]() ![]() ![]() |
Дополнительная информация
Список литературы.doc
Дипломное проектирование по технологии машиностроения: Учеб. пособие для вузов В.В. Бабук П.А. Горезко К.П. Забродин и др. Под общ. ред. В.В. Бабука – Минск: Выш. шк. 1979. – 464 с. ил.
Алямовский А.А. SolidWorks. Компьютерное моделирование в инженерной практике. – СПб.: БХВ-Петербург 2005. – 800 с. ил.
Справочник технолога-машиностроителя. В 2-х т. Под ред. А. Г. Косиловой и Р.К. Мещерякова. – 4-е изд. переработ. и доп. Т.1 2 – М.: Машиностроение 1986. – 656 с. 496 с. ил.
Станочные приспособления: Справочник. В 2-х т. Под ред. Б.Н. Вардашкина А.А. Шатилова. Т.1 2. – М.: Машиностроение 1984. – 592 с.
Курсовое проектирование по технологии машиностроения: Учеб. пособие для вузов Под. общ. ред. А. Ф. Горбацевича. – 3-е изд. перераб. и доп. – Минск: Высшая школа 1975. – 488 с.
Маталин А.А. Технология машиностроения. – Л.: Машиностроение 1985.
Анурьев В.И. Справочник конструктора-машиностроителя. Т. 1. – М.: Машиностроение 1978. - 728 с.
Проектирование механосборочных цехов: Учебник для студентов машиностроительных специальностей вузов Под ред. А.М. Дальского – М.: Машиностроение 1990. – 352 с. ил.
Болотин Х.Л. Костромин Ф.П. Станочные приспособления – 5-е изд. переработ. и доп. – М.: Машиностроение 1973. – 344 с.
Корсаков В.С. Основы конструирования приспособлений: Учебник для вузов. – 2-е изд. переработ. и доп. – М.: Машиностроение 1983. – 277 с. ил.
Норенков И.П. Автоматизированное проектирование: Учеб. пособие. – М.: Изд-во МГТУ им. Н.Э. Баумана 2000. – 188 с.
СНиП II-4-79. Строительные нормы и правила. Нормы проектирования. Глава «Естественное и искусственное освещение». М.: Стройиздат 1980. – 48 с.
Методические указания по выполнению курсовой работы по дисциплине «Организация и менеджмент производства» для студентов специальности 120100 «Технология машиностроения» дневного обучения Сост. А.В. Ростова. – Воронеж.: ВГТУ 2003. – 33 с.
Инвестиционное проектирование: практическое руководство по экономическому обоснованию инвестиционных проектов Под ред. С.П. Шумилина. М.: «Финстатинформ» 1995. – 240 с.
Экономика машиностроительного производства Под ред. И.Э. Берзиня В.П. Калинина. – М.: Высшая школа 1988. – 304 с.
Приспособление для металлорежущих станков: справочник (под ред. А. К. Горошкина – 7-е изд. переработ.и доп. – М.: Машиностроении 1979. – 303с.
Задание.doc
ВЫСШЕГО ПРОФЕССИОНАЛЬНОГО ОБРАЗОВАНИЯ
«ВОРОНЕЖСКИЙ ГОСУДАРСТВЕННЫЙ ТЕХНИЧЕСКИЙ УНИВЕРСИТЕТ»
Факультет автоматизации и роботизации машиностроения .
Кафедра _ «Технология машиностроения» .
(фамилия имя отчество)
на выпускную квалификационную работу
План выполнения дипломного проекта дипломной работы
Название элементов проектной работы
Подпись рук. консульт.
Руководитель дипломного проекта дипломной работы
(подпись) (Фамилия имя отчество)
Дипломный проект дипломная работа закончен(а)
(подпись дипломника)
Пояснительная записка и все материалы просмотрены
(подпись) (Инициалы фамилия)
3 Безопасность и экологичность.doc
1 Расчёт общего освещения на проектируемом участке
Общее освещение на участке состоит из искусственного и естественного.
Задачей расчёта искусственного освещения является определение потребной мощности электрической осветительной установки для создания в производственном помещении заданной освещённости.
Проектируя осветительную установку необходимо решить ряд вопросов:
Выбрать тип источника света. Для освещения производственных помещений как правило применяют газоразрядные лампы; там где температура воздуха может быть менее +5 ºС и напряжение в сети переменного тока падать ниже 90 % номинального и для местного освещения следует отдавать предпочтение лампам накаливания.
Определить систему освещения. Выбирая систему освещения необходимо учитывать что эффективнее система комбинированного освещения но в гигиеническом отношении система общего освещения более совершенна так как создаёт равномерное распределение световой энергии. Используя локализованное общее освещение можно наиболее просто добиться высоких уровней освещённости на рабочих местах без значительных затрат. При выполнении зрительных работ I-IV Vа и Vб разрядов следует применять систему комбинированного освещения. Местные светильники повышают освещённость помогают создать необходимую направленность светового потока позволяют исключить отражённую блескость и в некоторых случаях выполнять работы связанные с просвечиванием материалов и деталей.
Выбрать тип светильников с учётом характеристик светораспределения ограничения прямой блескости по экономическим показателям условиям среды а также с учётом требований взрыво- и пожаробезопасности.
Распределить светильники и определить их количество. Светильники могут располагаться рядами в шахматном порядке ромбовидно. Обеспечение равномерного распределения освещённости достигается в том случае если отношение расстояния между центрами светильников L к высоте их подвеса над рабочей поверхностью НР составит для светильников: «Астра» УПД – 14; УПМ-15 – 15; НСП-07 – 14; шара молочного стекла – 20; ЛД ЛОУ – 14; ПВЛП – 15.
Определить норму освещённости на рабочем месте. Для этого необходимо установить характер выполняемой работы по наименьшему размеру объекта различения контраст объекта с фоном и фон на рабочем месте. В соответствии с выбранной системой освещения и источником света найти минимальную нормируемую освещённость. Для расчёта искусственного освещения используют в основном 3 метода.
Для расчёта общего равномерного освещения при горизонтальной рабочей поверхности основным является метод светового потока (коэффициент использования) учитывающий световой поток отражённый от потолка и стен. Световой поток лампы ФЛ (лм) при лампах накаливания или световой поток группы ламп светильника при люминесцентных лампах рассчитывают по формуле[13]
где ЕН – нормированная минимальная освещённость лк;
S – площадь освещаемого помещения м2;
z – коэффициент минимальной освещённости равный отношению EсрЕm
к – коэффициент запаса;
N – число светильников в помещении;
– коэффициент использования светового потока ламп зависящий от КПД и кривой распределения силы света светильника коэффициента отражения потолка ρп и стен ρс высоты подвеса светильников и показателя помещения i.
Значение коэффициента использования светового потока определяют по табл. Показатель помещения
I = А·ВНр·(А+В) (2.59)
где А и В – два характерных размера помещения;
Нр – высота светильников над рабочей поверхностью.
Подсчитав по приведённой выше формуле световой поток лампы ФЛ подбирают ближайшую стандартную лампу и определяют электрическую мощность всей осветительной системы. В практике допускается отклонение потока выбранной лампы от расчётного до -10 % и +20 % в противном случае выбирают другую схему расположения светильников.
Точечный метод применяют для расчёта локализованного и комбинированного освещения освещения наклонных и вертикальных плоскостей и для проверки равномерного общего освещения когда отражённым световым потоком можно пренебречь.
В основу точечного метода положено уравнение
Е = Iа·cosαr2 (2.60)
где Iа – сила света в направлении от источника на данную точку рабочей поверхности кд
r – расстояние от светильника до расчётной точки м;
α – угол между нормалью рабочей поверхности и направлением светового потока от источника.
Для практического использования вводим в формулу коэффициент запаса к и заменяем r на Нрcos откуда
Данные о распределении силы света Iа приводятся в светотехнических справочниках.
При необходимости расчёта освещённости в точке создаваемой несколькими светильниками подсчитывают освещённость от каждого из них а затем полученные значения складывают.
Метод удельной мощности является наиболее простым но и наименее точным поэтому его применяют при ориентировочных расчётах. Этот метод позволяет определить мощность каждой лампы РЛ (Вт) для создания в помещении нормируемой освещённости[13]:
где р – удельная мощность Втм2;
S – площадь помещения;
n – число ламп в осветительной установке.
Значения мощности приводят в соответствующих таблицах в зависимости от уровня освещённости площади помещения высоты подвеса и типа светильников.
Для правильной расстановки оборудования и распределения рабочих мест с различной степенью зрительного напряжения необходимо аналитически определять коэффициенты естественной освещённости в производственном помещении.
Световой поток падающий в расчётную точку производственного помещения складывается из прямого диффузного света небосвода видимого через светопроём и света отражённого от внутренних поверхностей помещения и противостоящих зданий.
При боковом освещении например КЕО определяют по формуле
Еб = (б·q+зд·R)·о·r (2.62)
где б·q+зд·R – выражение определяющее часть КЕО создаваемого светом проникающим извне;
б и зд – геометрические коэффициенты естественной освещённости в расчётных точках при боковом освещении учитывающие соответственно свет от небосвода и отражённый от противостоящего здания; их значения находят с помощью графических методов в предположении что оконные проёмы не имеют остекления и переплётов а внутренние поверхности не отражают свет;
q – коэффициент учитывающий неравномерную яркость облачного неба;
R – коэффициент определяющий относительную яркость противостоящего здания.
При расчёте учитывают общий коэффициент светопропускания о который характеризует потерю света в материале остекления в переплётах светопроёма в слое загрязнения и в солнцезащитных устройствах. Повышение КЕО за счёт отражённого света от потолка и стен помещения учитывают коэффициентом r.
Для определения геометрических коэффициента естественной освещённости следует применять графический метод А.М. Данилюка пригодный для определения КЕО при лёгкой сплошной облачности т.е. при диффузном распространении светового потока. Этот метод сводится к тому что полусферу разбивают на 10 тыс. участков равной световой активности и подсчитывают какое число участков видно из данной точки.
Все рабочие места в механических цехах должны иметь местное освещение. По способу освещения рабочих зон станки можно подразделить на три группы. К первой группе относятся токарные (универсальные винторезные револьверные) поперечно-строгальные сверлильные и зубофрезерные станки. Минимально допустимая высота установки светильника местного освещения до освещаемой поверхности изделия на станках этой группы за исключением зубофрезерных составляет 03÷04 м. Конструкция зубофрезерных станков позволяет установить светильник местного освещения на высоте не менее 05÷07 м. Нормируемый уровень освещённости на этих станках должен быть обеспечен на участке светового пятна диаметром 03÷04 м.
Ко второй группе относятся шлифовальные и полировальные станки для которых применяют светильники малой яркостью светящей поверхности. Минимально-допустимая высота установки светильника местного освещения составляет 01÷02 м.
В третью группу входят крупногабаритные станки (карусельные горизонтально-расточные продольно-фрезерные и т.п.) на которых необходимо освещать две рабочие зоны: обработки и управления.
Металлообрабатывающие станки (за исключением шлифовальных и полировальных) поставляются заводами-изготовителями со светильниками типа СГС-1 или НКС01 допускающими применение в них ламп накаливания (ЛН) мощность до 100 Вт. Типоразмер светильника и мощность источников света определяют в зависимости от требуемого уровня освещённости от светильников местного освещения и допустимой высоты установки светильника над рабочей поверхностью.
Для создания нормированной освещённости на фрезерных и сверлильных станках в зависимости от их габаритов и типа рекомендуется устанавливать светильники НКС01 либо с одной либо с двух сторон станины станка; на станках токарной группы – для обеспечения постоянной освещённости рабочей поверхности на каретке суппорта.
Рецензия, отзыв.doc
ВЫСШЕГО ПРОФЕССИОНАЛЬНОГО ОБРАЗОВАНИЯ
«ВОРОНЕЖСКИЙ ГОСУДАРСТВЕННЫЙ ТЕХНИЧЕСКИЙ УНИВЕРСИТЕТ»
Факультет автоматизации и роботизации машиностроения
Кафедра «Технология машиностроения» .
Специальность 120100 (151001) Технология машиностроения .
(фамилия имя отчество)
на выпускную квалификационную работу
Тема дипломного проекта:
Разработка технологии и технологического оснащения для изготовления корпуса.
На рецензию был представлен дипломный проект в следующем объеме:
Пояснительная записка страниц
Технологические карты листов
Общее заключение рецензента на дипломный проект:
Дипломный проект Ковешникова С.В. выполнен в полном соответствии с заданием в достаточной мере раскрывает сформулированную в задании тему и соответствует установленным требованиям к выпускным квалификационным работам.
Дипломный проект содержит графическую часть которая иллюстрирует особенности конструкции детали вид исходной заготовки основные операции разработанного технологического процесса необходимые технологические приспособления планировку производственного участка основные технико-экономические показатели. Графическая часть выполнена в соответствии с требованиями ЕСКД и ЕСТД и свидетельствует о навыках и умении дипломника в разработке конструкторско-технологической документации.
Расчётно-пояснительная записка содержит все необходимые компоненты для качественного раскрытия темы дипломного проекта: производственно-технологическую часть включающую анализ назначения и конструктивных особенностей детали определение и выбор формы организации производственного процесса анализ базового технологического процесса и постановку задач на проектирование выбор рациональной заготовки технологического оборудования маршрутного и операционного технологических процессов с базированием детали при выполнении технологических переходов расчёт припусков режимов резания техническое нормирование операций; проектно-конструкторскую часть содержащую расчёты по выбору технологической оснастки и контрольных приспособлений; организационно-экономическую часть; эксплуатационную часть а также все необходимые приложения. Все материалы изложены в соответствии с требованиями стандарта предприятия СТП ВГТУ 004-2003.
Оценка дипломного проекта:
Учитывая всё вышеизложенное считаю что дипломный проект
Ковешникова С.В. заслуживает оценки « » а сам дипломник – присвоения квалификации инженера по специальности 120100 (151001) «Технология машиностроения».
С рецензией ознакомлен дипломник С.В. Ковешников _
(подпись) (инициалы фамилия)
Допускается к защите:
на выпускную квалификационную работу (дипломный проект)
КОВЕШНИКОВА СЕРГЕЯ ВАЛЕРЬЕВИЧА
«Разработка технологии и средств технологического оснащения для изготовления корпуса»
Работа выполнена на кафедре «Технология машиностроения» ГОУ ВПО ВГТУ по документации Воронежского механического завода и носит учебно-прикладной характер с расчётом использования результатов на перспективу.
Актуальность данной разработки заключается в том что до настоящего времени на Воронежском механическом заводе не решены полностью вопросы технического и технологического обеспечения выпуска изделий типа «Корпус» в условиях серийного производства.
Выполненная C.В. Ковешниковым разработка отличается новизной в части построения маршрутного и операционного технологических процессов выбора рациональных моделей технологического оборудования метода получения исходной заготовки назначения экономически целесообразных припусков и рациональных режимов резания проектирования необходимой технологической оснастки и средств механизации технологического процесса. Работа выполнена с применением компьютерных информационных технологий систем автоматизированного проектирования содержит современные научно-технические решения конструкторско-технологических задач что свидетельствует о степени её сложности.
Считаю что дипломный проект С.В. Ковешникова выполнен в полном соответствии с заданием и в достаточной мере раскрывает сформулированную в задании тему.
При работе над расчётно-пояснительной запиской и графической частью дипломного проекта С.В. Ковешников продемонстрировал навыки и умение правильно работать с современной научно-технической и справочной литературой знание стандартов ЕСКД ЕСТД и СТП ВГТУ.
В период дипломного проектирования С.В. Ковешников зарекомендовал себя исполнительным дисциплинированным обладающим высокой трудоспособностью самостоятельно мыслящим студентом способным рационально организовать свою работу по решению конкретной научно-технической проблемы.
Материалы изложенные в расчётно-пояснительной записке свидетельствуют о достаточных знаниях С.В. Ковешникова общеобразовательных общетехнических и специальных дисциплин его умениях и навыках систематически на современном научно-техническом уровне применять свои знания к решению конкретных технических задач и подготовленности к самостоятельной инженерно-технической деятельности.
Учитывая всё вышеизложенное считаю что дипломный проект Ковешникова Сергея заслуживает оценки « » а сам дипломник – присвоения ему квалификации инженера по специальности 120100 (151001) «Технология машиностроения».
Руководитель дипломного проекта доцент В.А. Сай
Заключение.doc
Исходя из разработанного технологического процесса и объёма выпуска продукции был спроектирован участок по изготовлению корпуса. Оборудование участка позволяет вести серийный выпуск деталей. Для обеспечения полной загрузки оборудования на данных станках будет производиться выпуск подобных корпусных деталей.
Был проведён анализ базового технологического процесса производства детали и выявлена возможность повышения качества и экономической эффективности производства.
Спроектирована маршрутно-операционная технология производства детали корпус и конструкция приспособления. При этом были задействованы прогрессивные средства разработки технологического процесса обработки детали в САПР.
Был спроектирован участок механического цеха проведён расчёт относительных и абсолютных показателей спроектированного предметно-замкнутого участка. С его помощью было выявлено сокращение количества операций и переходов вследствие чего уменьшились затраты на оборудование электроэнергию амортизацию а также количества снижение себестоимости детали.
1 Проектно-конструкторская.doc
1 Назначение и краткое техническое описание детали
Корпус – деталь сложной формы но она средненагруженная и в условиях пластической деформации обладает повышенной прочностью и ударной вязкостью.
Детали авиационной техники эксплуатируются в условиях резких перепадов температур и даже в агрессивных средах. Корпус наряду с другими деталями авиационной техники не должен охрупчиваться при низких температурах и его можно использовать в условиях криогенных температур.
К деталям авиационной техники предъявляются повышенные требования по качеству прочности точности обрабатываемых поверхностей.
Корпус имеет в своей конструкции две сопрягающиеся внешние цилиндрические поверхности переходящие плавно в шаровую поверхность. На обеих цилиндрических поверхностях имеется фланец предназначенный в первом случае для крепления корпуса а во втором представляет собой рёбра жёсткости сложной округлой формы. Корпус имеет сложную по конструкции внутреннюю полость сферической формы с выступающим элементом трубчатой формы. Данная деталь имеет внешнюю технологическую резьбу М56 на шейке детали.
Деталь корпус имеет следующие габариты: 200×160×190 мм.
Материал корпуса входа – алюминиевый сплав АК6 по ГОСТ 4784-97.
Сплав системы Al – Cu – Mg – Si – Mn отличается сравнительно высокими технологическими и механическими свойствами и широко применяется в промышленности. Этот оригинальный ковочный сплав разработанный С. М. Вороновым в поисках увеличения эффекта упрочнения и уменьшения влияния перерыва между закалкой и искусственным старением.
Химический состав сплава АК6: Cu – 18÷26 %; Mg – 04÷08 %; Mn – 04÷08 %; S 01 % 03 % Zn [1].
Основные упрочняющие фазы в сплаве АК6 – и кремний. Марганец образует сложные фазы с кремнием и алюминиемили с кремнием алюминием и железом .
Сплав АК6 имеет высокие технологические свойства при обработке давлением. Сплав хорошо деформируется в горячем и холодном состоянии. Температурный интервал горячей деформации сплава АК6420÷470° С.
Сплав данной группы из-за присутствия фазы и элементарного кремния для которых характерны большие скорости выделения из твёрдого раствора и коагуляции при повышенных температурах отличаются низкой жаропрочностью (длительной прочностью и сопротивлением ползучести).
Сплав АК6 был специально разработан для изготовления штамповок.
Для данного конструктивного исполнения корпуса предъявляют следующие технические требования характеризующие различные параметры их геометрической точности.
Точность геометрической формы плоских базирующих поверхностей. Она регламентируется как прямолинейность поверхности в заданном направлении на определённой длине и как плоскостность поверхности в пределах её габаритов. Поверхности корпуса не превышают 500 мм следовательно отклонение от плоскостности и параллельности составляет 005 мм.
Точность расстояния от осей главных отверстий до базирующей плоскости составляет 003 мм. Точность расстояний между осями главных отверстий 001 мм. Соосность отверстий 001 мм.
Точность диаметральных размеров и геометрической формы отверстий. Диаметральные размеры главных отверстий выполняющих в основном роль баз под различные элементы соответствуют 8-му квалитету.
Конструкторский и технологический код детали.
Проектирование технологии изготовления отдельных деталей для станков является неэффективным. Поэтому для снижения затрат на разработку технологии управляющих программ перенастройку станка повышение его загрузки технология проектируется для группы деталей используется групповой метод обработки.
В этом случае для отбора номенклатуры деталей подлежащих обработке на станках формирования деталей в группы по конструктивно-технологическим признакам необходимо знание полного классификационного кода деталей.
В конструкторском классификаторе ЕСКД используются такие признаки классификации как форма и расположение поверхностей; соотношение длины и диаметра детали; наличие определенным образом расположенных отверстий пазов выточек и других конструктивных элементов.
По конструкторскому классификатору конструкторский код детали типа корпус складывается из:
) 730000 класс (3-ий) образуют детали сложной пространственной формы не тела вращения в том числе и корпусные;
) 731000 подкласс (1-ый) включает в себя корпусные детали без поверхностей разъёма в том числе аэрогидродинамические детали;
) 731200 группа (2-ая) составляет детали с плоской основной базой и наружной поверхностью криволинейной;
) 731260 подгруппа (6-ая) включает в себя детали с плоскими вспомогательными базами с двумя и более базовыми отверстиями;
) 731267 вид (7-ой) образуют детали с комбинированными отверстиями то есть как параллельными так перпендикулярными базовым.
Конструкторский код ВГТУ.731267.001 – деталь не тело вращения корпусная без поверхности разъема с плоской базой и несколькими базовыми отверстиями со сложнопрофильной криволинейной наружной поверхностью с комбинированными отверстиями.
Технологический код. Размерная характеристика детали обозначается 665:
- длина детали находится в пределах 180 – 250 мм (цифра 6);
- высота в пределах 180 – 250 мм (цифра 6);
- ширина в пределах 120 – 180 мм (цифра 5).
Группа материала 27: сплав алюминиевый. В нашем случае материал детали алюминиевый сплав АК6 по ГОСТ 21488-97. Вид детали по технологическому процессу – 4: обрабатываемая резанием. Код основных признаков 665274.
Код признаков определяющих вид детали – 2434Г40В: 24 – вид исходной заготовки – объёмная штамповка; 3 – код наивысшего по точности 8-го квалитета наружных поверхностей; 4 – код наивысшего 8-го квалитета точности внутренних поверхностей; Г – код отклонения плоскостности радиального биения и перпендикулярности; 4 – код степени точности на допуски и расположения поверхности (радиальное биение 002 мм); 0 – характеристика термической обработки – отсутствует; Б – весовая характеристика детали – масса находится в пределах 25÷4 кг а именно масса детали составляет 27 кг.
Конструкторско-технологический код корпуса: ВГТУ.731267.001.665274.2434Г40В.
2 Разработка твердотельной 3D модели детали
Построение твердотельной модели детали ведем в программе КОМПАС-3D V9 компании АСКОН.
Подсистема КОМПАС-3D предназначена для создания трехмерных параметрических моделей деталей с целью передачи геометрии в расчетные пакеты и в пакеты разработки управляющих программ для оборудования с ЧПУ а также расчета их геометрических и массо-центровочных характеристик.
В запущенной программе выбираем команду файл создать деталь.
В дереве модели выбираем плоскость XY. На панели «Текущее состояние» выбираем пиктограмму эскиз и в поле чертежа с помощью графических примитивов строим контур сечения детали (рисунок 2.1).
Рисунок 2.1 – Контур сечения детали
С помощью операции вращения строим твердотельную модель являющуюся
основой для дальнейшего проектирования (рисунок 2.2).
Рисунок 2.2 – Основа твердотельной модели
Строим смещенную плоскость создаем «Эскиз2» и с помощью операции выдавливания строим фланец (рисунок 2.3).
Рисунок 2.3 – Смещённая плоскость
С помощью операции выдавливания и соответствующих эскизов достраиваем диаметральную часть от первого фланца и строим нижний фланец (рисунок 2.4).
Рисунок 2.4 – Диаметральная часть и нижний фланец построение
С помощью выдавливания строим две верхние бобышки (рисунок 2.5)
Рисунок 2.5 – Построение бобышек
Далее ведем построение внутреннего контура и полостей детали (рисунок 2.6)
Рисунок 2.6 – Построение внутреннего контура и полостей детали
3 Разработка параметрической 2D модели детали
Однажды созданная параметрическая модель детали может быть быстро перестроена простым изменением значений размеров.
Выбираем в меню: Файл Создать Чертеж.
Затем выбираем меню: Вставка Вид с модели Произвольный. (Масштаб 1:1)
Рисунок 2.7 – Создание произвольного вида с модели
Выбираем необходимые нам виды (рисунок 2.8)
Рисунок 2.8 – Выбор необходимых видов
Создаем дополнительные виды разрезы выноски образмериваем чертёж проставляем шероховатости и базы.
Рисунок 2.9 – Формирование чертежа детали
4 Экономика.doc
1 Экономическое обоснование проекта участка
1.1 Определение потребности в инвестициях
Создание предметно-замкнутого участка требует некоторых затрат: на технологическую подготовку производства на закупку установку и наладку технологического энергетического подъемно-транспортного оборудования технологическую оснастку инвентарь и хозяйственные принадлежности. В затратах на здание нет необходимости так как предполагается что спроектированный участок разместится на имеющихся площадях предприятия.
Из затрат на технологическую подготовку наиболее существенными являются: затраты на проектирование технологических процессов и затраты на проектирование приспособлений. Эти затраты рассчитываются по трудоемкости проектных работ и стоимости 1 человеко-часа работы разработчиков.
Определим затраты на технологическую подготовку производства исходя из трудоемкости проектных работ. Укрупнённо они определяются по формуле[14]:
где t - норма времени на разработку технологического процесса и конструирования оснастки;
t - норма времени на внедрение технологических процессов и оснастки;
С - стоимость одного человеко-часа р.
Стоимость 1 человеко-часа рассчитывают исходя из среднемесячной заработной платы технологов и конструкторов с учетом начислений на нее и номинального фонда времени работы в месяц.
где ЗП – среднемесячная заработная плата технологов и конструкторов с учетом всех начислений на неё р.;
Фном – номинальный фонд рабочего времени в месяц ч.
Таблица 4.1 – Перечень металлорежущих станков используемых на участке
электро-двигателя кВт
универсальный станок
Вертикально-сверлильный станок
Вертикально-фрезерный консольный станок
Горизонтально-протяжной полуавтомат
Вертикально-сверлильный станок
Капиталовложения в оборудование Ко р. рассчитываются по формуле [14]:
где Кот – капиталовложения в технологическое оборудование тыс. р;
Коэ – капиталовложения в энергетическое оборудование тыс. р;
Кпт – капиталовложения в подъемно-транспортное оборудование тыс. р;
Коу – капиталовложения в средства контроля и управления тыс. р;
Вложения в технологическое оборудование определяются по формуле [14]:
kтз – коэффициент транспортно-заготовительных расходов kтз = 005;
kс – коэффициент учитывающий затраты на строительные работы в том числе устройство фундаментов kс = 007;
kм – коэффициент учитывающий затраты на монтаж и наладку оборудования kм = 01.
Капиталовложения в технологическое оборудование по формуле (4.4)
Укрупнённо капиталовложения в энергетическое оборудование принимаем равным 5% от стоимости технологического оборудования.
Капиталовложения в подъемно-транспортное оборудование принимаем равным 10% от стоимости технологического оборудования.
Капиталовложения в средства контроля и управления технологическим процессом принимаются равными 1% от стоимости технологического оборудования.
Определяем величину капиталовложений в оборудование:
Затраты на оснастку принимаем в размере 7 % от стоимости технологического оборудования.
Вложения в инвентарь и хозяйственные принадлежности долговременного пользования примем в размере 3 % от стоимости технологического оборудования.
Результаты расчета капитальных вложений в основные производственные фонды участка представлены в таблице 4.2.
Таблица 4.2 – Результаты расчета капитальных вложений в основные производственные фонды участка
Кол-во единиц оборудования шт.
Балансовая стоимость единицы оборудования тыс. р.
Балансовая стоимость основных фондов тыс. р.
Годовые амортизационные
)Энергетическое оборудование
Продолжение таблицы 4.2
)Средства контроля и управления
)Технологическая оснастка
хозяйственные принадлежности
1.2 Организация оплаты труда на участке
Фонд зарплаты складывается из основной и дополнительной зарплаты. В основную входят тарифный фонд и различного рода доплаты большую часть которых составляет премия выплачиваемая из фонда заработной платы.
Тарифный фонд заработной платы рабочих-сдельщиков определяется по формуле [14]:
где Ризj – расценка на изделие типа j р.
di – коэффициент учитывающий многостаночность работы i = 1.
где СТЧi – часовая тарифная ставка соответствующая разряду i-ой операции р.ч.
В соответствии с данными завода для цеха выпускающего корпус:
- ставка первого разряда – = 2658 р.ч
- ставка второго разряда – = 3722 р.ч
- ставка третьего разряда – = 4254 р.ч
- ставка четвертого разряда – = 4786 р.ч
- ставка пятого разряда – = 5318 р.ч
- ставка шестого разряда – = 5848 р.ч.
Результаты расчета расценок на изготовление изделия представлены в таблице 4.3.
Таблица 4.3 – Результаты расчета расценок на изготовление изделия
Продолжение таблицы 4.3
Тарифный фонд заработной платы рабочих-повременщиков:
где ФРД – действительный годовой фонд времени работы рабочего ч;
Чп – численность рабочих-повременщиков чел.;
– часовая тарифная ставка 1-го разряда р.ч.;
– средний тарифный коэффициент рабочих-повременщиков.
Kiп – тарифный коэффициент рабочих- повременщиков i-го разряда.
Таблица 4.4 – Часовые ставки вспомогательных рабочих
Тарифный коэффициент
Часовые ставки руб.ч
Продолжение таблицы 4.4
Определяем средний тарифный коэффициент вспомогательных рабочих-повременщиков:
Составим штатное расписание для аппарата управления участком.
Таблица 4.5 – Штатное расписание аппарата управления участком
Количество на участке (факт.) чел.
Фонд заработной платы аппарата управления участком рассчитывается исходя из штатного расписания должностных окладов и премий начисленных из фонда заработной платы в соответствии с положениями о премировании принятыми на предприятии.
Результаты расчета фондов заработной платы различных категорий работников представлены в таблице 4.6.
Таблица 4.6 – Результаты расчета фондов заработной платы различных категорий работников
Вспомогательные рабочие
1.3 Расчет текущих затрат
Смета расходов на содержание и эксплуатацию оборудования включает следующие статьи: амортизация оборудования эксплуатация оборудования текущий ремонт оборудования содержание и эксплуатация транспорта износ малоценных и быстроизнашивающихся инструментов и приспособлений прочие расходы.
Расходы на амортизацию оборудования Ра = 678442 тыс. р.
Расходы на эксплуатацию оборудования включают затраты на вспомогательные материалы потребляемые в процессе эксплуатации оборудования; затраты на силовую энергию для приведения в движение производственных машин и механизмов; затраты на сжатый воздух для эксплуатации оборудования; затраты на воду для производственных нужд; основную и дополнительную заработную плату вспомогательных рабочих обслуживающих оборудование на участке с начислениями на социальные нужды.
Затраты на вспомогательные материалы принимаются в размере 5 % от стоимости технологического оборудования.
Затраты на силовую энергию определяются по формуле [14]:
где Мэ – суммарная мощность электродвигателей оборудования кВт;
kв – коэффициент загрузки оборудования по времени kв = 06;
kм–коэффициент загрузки электродвигателей по мощности kм=05;
kпс – коэффициент учитывающий потери электроэнергии в сети kпс = 104;
Цэ – цена электроэнергии р.(кВт·ч) Цэ=179 р.(кВт·ч);
– средний КПД электродвигателей оборудования = 07.
Затраты на сжатый воздух определяются по формуле [14]:
где Ссв – объем сжатого воздуха приходящийся на один станок в смену м3;
Др – число рабочих дней в году;
Nст – число станков шт.;
Цсв – цена сжатого воздуха р.м3
ЗСВ = 5·256·1·9·064 = 73728 р. 7372 тыс. р.
Затраты на воду определяют по формуле [14]:
где Св – средний расход воды на один станок м3ч;
ЗВ = 00006·256·1·8·9·3944 р. = 43617 р. = 0436 тыс. р.
Затраты на основную и дополнительную заработную плату вспомогательных рабочих обслуживающих оборудование с начислениями на социальные нужды определяются укрупнённо в размере 30 % от годового фонда заработной платы и начислений на социальные нужды всех вспомогательных рабочих:
где – коэффициент начислений на социальные нужды;
– годовой фонд заработной платы вспомогательных рабочих.
Расходы на текущий ремонт оборудования транспортных средств и технологической оснастки составляют 15 % от балансовой стоимости указанных средств.
Расходы на содержание и эксплуатацию транспортных средств принимают в размере 5% от стоимости транспортных средств.
Расходы на износ малоценных инструментов и приспособлений определяется укрупненно из расчета 50 тыс. р. на один станок в год.
Прочие расходы составляют 3% от общей суммы затрат по перечисленным выше статьям.
Смета расходов на содержание и эксплуатацию оборудования представлена в таблице 4.7.
Таблица 4.7 – Смета расходов на содержание и эксплуатацию оборудования
Амортизация оборудования.
Эксплуатация оборудования:
- затраты на вспомогательные материалы;
- затраты на силовую энергию;
- затраты на сжатый воздух;
- затраты на воду для производственных нужд;
- затраты на основную и дополнительную заработную плату вспомогательных рабочих обслуживающих оборудование с начислениями на социальные нужды.
Расходы на текущий ремонт оборудования.
Расходы на содержание и эксплуатацию транспорта.
Расходы на износ малоценных и
быстроизнашивающихся инструментов.
1.4 Расчет себестоимости продукции
В данном разделе определим себестоимость корпуса топливного клапана изготавливаемого по спроектированной технологии а также рассчитаем общие годовые затраты на производство продукции в спроектированном цехе.
Расчет себестоимости детали изготавливаемой по спроектированной технологии представлен в таблице 4.8
Таблица 4.8 – Расчет себестоимости детали
где НР – норма расхода материала на изделие НР = 55 кг; ЦМ – оптовая цена материала ЦМ = 195 ркг
Вспомогательные материалы
Кот = 8723 тыс. р.; N = 500 шт.
где Но – норма отходов на деталь кг; Но = 28 кг; Цо – цена отходов ркг; Цо = 65 р.кг.
Основная заработная плата основных производственных рабочих
Д = 04·Риз = 27628 рдеталь.
Дополнительная зп основных производственных рабочих
Начисления на социальные нужды
Рсп = 708308 тыс. р.
содержание и эксплуатацию оборудования
где – процент расходов на содержание и эксплуатацию оборудования = 162 %
где Кцр – процент цеховых расходов Кцр = 120 %.
Продолжение таблицы 4.8
изготовления детали:
Сц = Мо + МВТ – Ов+ Зо + Зд + Ос +
Общехозяйственные расходы
где Крх – коэффициент общехозяйственных расходов по данным ВМЗ Крх = 320 %.
где Кком – коэффициент коммерческих расходов Кком = 8 %.
Полная себестоимость изготовления детали
Процент расходов на содержание и эксплуатацию оборудования определяется по формуле:
где – расходы на содержание и эксплуатацию оборудования участка на год;
Ф°ор – фонд основной зарплаты основных производственных рабочих участка за изготовление партии в 500 деталей на год тыс.р.;
– коэффициент загрузки оборудования на участке.
%. Принимаем = 162 %.
Годовые текущие издержки Иг р. определяются по формуле [14]:
где Nг – годовая программа выпуска изделий шт.
2 Расчет технико-экономических показателей проектируемого участка
Относительные показатели вычисляем по формулам:
где Сцп– итоговая цеховая себестоимость изготовления партии из 500 деталей тыс. руб.; Сцп= 670296·500 =3351480 тыс. руб.
Осн.ф.– балансовая стоимость основных фондов тыс. руб.
Основные фонды используются не рационально об этом свидетельствует малый коэффициент загрузки оборудования. При расчётах следует учитывать этот факт для этого необходимо ввести поправочный коэффициент кпопр.
Дозагрузим имеющееся на участке оборудование т.е. повысим коэффициент загрузки оборудования кзо до общепринятого значения на предприятиях общего машиностроения тогда кпопр = кзофкзоо
где кзоо – коэффициент загрузки оборудования на предприятиях общего и тяжёлого машиностроения при серийном производстве (кзоо 1) примем кзоо = 08.
кзоф – средний коэффициент загрузки оборудования на участке кзоф = 035.
Данный коэффициент учитывает фактическую загрузку оборудования.
Формула 4.12 примет следующий вид
Ф = 0590 (тыс.ртыс.р).
где rосн – численность основных производственных рабочих чел
Ф = 94752 (тыс.р.чел).
Рассчитаем выпуск продукции на одного производственного рабочего:
Враб = 55858 (тыс.р.чел.).
Рассчитаем выпуск продукции на 1 м2 производственной площади [14]:
Вм2 = 1745 (тыс.р.м).
Рассчитаем уровень механизации труда при использовании спроектированного процесса по формуле [14]:
Технико-экономические показатели проектируемого участка по изготовлению корпуса представлены в таблице 4.9
Таблица 4.9 – Технико-экономические показатели проектируемого участка по изготовлению корпуса
Наименование показателей
–Абсолютные показатели
1 Годовой выпуск продукции:
- в натуральном выражении шт.;
- в стоимостном выражении тыс. р.
Продолжение таблицы 4.9
2 Количество единиц технологического оборудования на участке шт.
3 Общая стоимость основных производственных фондов участка тыс. р.
4 Производственная площадь участка м2
5 Численность основных рабочих участка чел.
6 Фонд заработной платы основных рабочих тыс. р.
–Относительные показатели
1 Выпуск продукции на одного производственного рабочего в денежном выражении тыс. р.чел.
2 Выпуск продукции на 1м2 производственной площади тыс. р.кв. м.
3 Фондоотдача тыс.ртыс.р.
4 Средняя загрузка оборудования %
5 Фондовооруженность труда тыс. р.чел.
6. Уровень механизации труда %
3 Расчет показателей экономической эффективности проекта участка
Экономический эффект от функционирования участка на котором детали изготавливаются по вновь спроектированной технологии рассчитывается на конкретный период.
Экономический эффект реализации проекта участка за расчетный период может быть определен по формуле [14]:
где РГ – неизменная по годам расчетного периода стоимостная оценка резуль-
татов производства продукции с использованием разработанного технологического процесса р.;
ЗГ – неизменные по годам расчетного периода затраты на продукцию с применением разработанного технологического процесса р.;
– норма реновации исчисленная для периода использования спроектированной технологии =01638 (период использования технологии – 5 лет)
Ен – норматив приведения разновременных результатов и затрат численно равный нормативу эффективности капитальных вложений Ен = 01.
Величина Рг определяется по формуле [14]:
n – число наименований деталей изготавливаемых на спроектированном участке по разработанным технологиям.
где Кнр – коэффициент рентабельности к себестоимости продукции Кнр = 15.
Величина Зг определяется по формуле [14]:
где И – текущие издержки производства без учета амортизации основных производственных фондов используемых при изготовлении продукции;
Лi – остаточная стоимость основных фондов на момент окончания применения разработанной технологии р.
Остаточная стоимость основных фондов на момент окончания использования разработанной технологии определяется по формуле [14]:
– норма реновации соответствующая сроку службы основных фондов
примем = 00627 что соответствует сроку службы в 10 лет.
– норма реновации соответствующая (tсл – ) = (10 – 5) = 5 =01638.
Внутренняя норма доходности проекта определяется по формуле [14]:
где К – единовременные затраты на создание участка.
Срок окупаемости капитальных вложений в проект определяется по формуле:
Таким образом а срок окупаемости капитальных вложений – Ток = 475 года – меньше срока использования разработанной технологии (5 лет) на спроектированном участке следовательно можно сделать вывод о том что разработанные в дипломном проекте инженерные решения являются экономически эффективными.
К показателям эффективности проекта также относятся снижение себестоимости изготовления детали экономия металла снижение трудоемкости изготовления детали условное высвобождение численности рабочих.
Снижение себестоимости изготовления детали определяется по формуле [14]:
где Сцб – цеховая себестоимость детали по базовому технологическому процессу р. (по данным предприятия);
Сцн – цеховая себестоимость детали по проектируемому технологическому процессу р.
Снижение трудоемкости изготовления детали определяется по формуле [14]:
где t1 – трудоемкость изготовления единицы продукции по базовому техпроцессу мин;
t2 – трудоемкость изготовления единицы продукции по спроектированному техпроцессу мин.
Условное высвобождение численности рабочих определяется по формуле:
чел. принимаем: 1 человек.
Рассчитанные показатели экономической эффективности проекта представлены в таблице 4.10.
Таблица 4.10 – Показатели экономической эффективности проекта
Интегральный экономический эффект млн. р.
Внутренняя норма доходности
Срок окупаемости капитальных вложений лет
Снижение себестоимости изготовления детали %
Снижение трудоемкости изготовления детали %
Условное высвобождение численности рабочих чел.
4 Особенности машиностроительных предприятий
Предприятие – это самостоятельный хозяйственный субъект созданный для производства продукции выполнения работ и оказания услуг с целью удовлетворения общественных потребностей и получения прибыли.
К особенностям машиностроительных предприятий в России относятся:
) многономенклатурность продукции;
) многодетальность продукции;
) длительность цикла подготовки к выпуску новой продукции;
) длительность цикла изготовления;
) широко развитые производственные связи.
Для обеспечения экономической независимости страны необходимо иметь не только собственное машиностроение но и экспортно-импортные связи. Темпы развития машиностроения должны превышать темпы развития промышленного производства.
Для машиностроения необходимо широко развивать услуги по техническому обслуживанию выпускаемой продукции гарантийный ремонт рынок запасных частей. Непременным составляющим работы машиностроительного предприятия должен быть выпуск запасных частей номенклатура и объем которых зависит от срока эксплуатации основной продукции. Запасные части будучи средством поддержания работоспособности машин выступают в качестве сопутствующих товаров а сопутствующие товары всегда дорогие.
Производственные и финансовые связи предприятия:
- связи со снабжением;
Можно отметить два подхода к формированию связей.
) Когда предприятия заключают друг с другом договоры на длительный срок — предприятия-потребители стараются помогать предприятиям-поставщикам.
) Чисто рыночные связи — когда поставщик попал в тяжелое положение потребитель ищет другого поставщика.
Производственные связи бывают прямые и косвенные. В связи с тем что предприятия взаимосвязаны в производственной сфере негативная работа одного может отрицательно сказаться на экономике другого предприятия.
Наряду с хозяйственными связями существуют финансовые связи. В подавляющем числе случаев расчет за материалы сырье производится по безналичному расчету.
Формы безналичного расчёта:
Платежное требование: применяется при расчете с иногородними покупателями – поставщик отправляет товар и предъявляет требование об оплате в свой банк (банк поставщика). Это комбинированный платежный документ объединяющий платежное поручение покупателя и платежное требование поставщика.
Платежное поручение: это документ содержащий приказ или поручения плательщика банку о списании с его счета определённой суммы на счет получателя. Преимуществом оплаты является относительно простой быстрый документооборот а также возможность для плательщика предварительно проверить качество выполняемых работ или услуг. Действительно в течение 10 дней.
Аккредитивная форма расчета: сущность заключается в том что средства получателя резервируются в банке поставщика куда они поступают по распоряжению владельца. Применяется при разовых сделках и когда нет доверия покупателю. Преимущество аккредитива в том что поставщик получает гарантию своевременного платежа покупатель – гарантию поставки и перечисления средств на счет поставщика только после выполнения последнего в условии договора. Недостаток — извлечение средств покупателя из оборота.
Расчеты с помощью чека: применяется при разовой сделке. Расчетный чек – это документ который содержит поручение чекодателя (плательщика) банку о перечислении с его расчетного счета определенной суммы на счет чекодержателя при сдаче последним чека в банк. Расчет по чеку может быть гарантирован авалистом.
Бартер т.е. натуральный обмен товарами. Неэффективная форма расчета так как проходит мимо банка.
Вексельная форма расчета. Вексель – это ценная бумага и одновременно коммерческий кредит. Простой вексель – это обязательство векселедателя уплатить по наступлению срока определенную сумму денег держателю векселя через банк. Переводной вексель – когда вексель передается первым лицом имевшим на него право другому лицу и тот обязан оплатить этот вексель.
Факторинг: осуществляется через посредническую организацию обычно тесно связанную с банком. Основная задача факторинга – ускорение расчетов. Дело в том что в условиях устоявшегося рынка широко проходят оплаты счетов от 1 до 3 месяцев. Для ускорения платежа оговариваются скидки в цене при неоплате в срок взимается штраф. Суть факторинга состоит в том что посредник немедленно оплачивает поставщику по счету клиента. За эту услугу поставщик платит посреднику определенный процент. Продавец заинтересован в скорейшем получении средств по счету так как он является покупателем других материальных средств.
В расчетах между предприятиями находящихся в разных государствах в договоре отражается вид валюты и условия оплаты.
В условиях инфляции происходит изменение цен поэтому то что стоило дешевле стоит дороже. В этом случае разумно устанавливать расчетные цены.
где Цр – цена расчетная; ЦБ – цена базовая;
Ат – цена единицы материалов в текущем году;
АБ – цена единицы материалов в базовом году;
a – удельный вес затрат материала в себестоимости продукции;
ВБ – стоимость единицы затрат труда в базовом году;
Вт – стоимость единицы затрат труда в текущем году;
b – удельный вес затрат труда в себестоимости продукции;
Построение управления основывается на выполнении определенных функций:
а) законодательная функция (применение стратегических решений);
б) исполнительная функция;
в) контрольная функция.
В своей эволюции задач управления американский экономист Ансофф рассматривает 3 эпохи развития:
) Эпоха массового производства. Главная задача — расширение масштабов производства стандартного продукта по самой низкой цене. Пути решения:
- постоянство конструкции;
- повышение эффективности производства за счет внутренних резервов;
- невмешательство государства в предпринимательскую деятельность.
) Эпоха массового сбыта. Наступает когда спрос на основные потребительские товары близок к насыщению. Основная задача — производство продукции для удовлетворения спроса т. е. переход от стандартной продукции к дифференцированной. Путь решения — продвижение моделей на рынок путем рекламы упаковки отделки организации сбыта.
- определяющие условия производства диктуются извне;
- удешевление не является самоцелью;
- главная забота — репутация фирмы.
) Постиндустриальная эпоха — эпоха наступившего благосостояния. Главная задача — обслуживание богатого потребителя через достижения научно-исследовательских конструкторских разработок.
- общество нуждается в качественной продукции;
- борьба за рынки сбыта обостряется.
Общие тенденции проблем управления:
- темпы изменения внутренней и внешней среды предприятия будут высокими;
- конкуренция будет все более безжалостной;
- понятие географической границы будет размываться;
- ускоряющиеся темпы технического прогресса приведут к возрастанию его роли в конкурентной борьбе;
- возрастет роль квалификации как условия адаптации к окружающей среде;
- роль управления сместится от контроля над людьми к возможности проявить себя.
Предприятие представляет собой систему по преобразованию ресурсов.
Особенности производственной системы:
изменчивость параметров системы и эластичность ее поведения;
способность изменять свою структуру и формировать варианты поведения в изменяющейся обстановке;
способность адаптироваться к изменяющейся обстановке;
способность к формированию цели внутри системы.
уникальность и непредсказуемость системы благодаря наличию в ней человека.
Рисунок 4.1 – Производственная система по преобразованию ресурсов
Согласно трудовой теории стоимости прибыль которую включают в цену продукции получается из того что затраченный труд больше чем та часть которая выдана рабочему в качестве заработной платы.
плата за средства производства
плата за предпринимательство
Предприятия работают ради получения прибыли. В начале 20 века экономисты Дуглас и Кларк предложили математическую модель зависимости объема производства от основных факторов производства.
где K – количество задействованного капитала;
L – количество задействованного труда;
a b - степенные показатели показывающие во сколько увеличится объем продукции Q если на 1% увеличится количество капитала или труда оставляя количество другого фактора фиксированным.
Заработная плата + A + Прибыль = Добавленная стоимость
Сегодня существует налог на добавленную стоимость (НДС)
Такая зависимость была основана на теоретической посылке что в основе цены любого фактора производства лежит так называемый предельный продукт. Коэффициент A учитывает другие кроме этих двух факторы производства.
Зависимость между K и L может быть выражена графически в виде изокванты.
Рисунок 4.2 – Зависимость объема от основных факторов производства
2 Производственно-технологическая.doc
1 Установление типа производства
Тип производства представляет собой комплексную характеристику технических организационных и экономических особенностей производства обусловленных широкой номенклатурой регулярностью стабильностью и объёмом выпуска продукции. Основным показателем характеризующим тип производства является коэффициент закрепления операции [2].
Тип производства устанавливается по участку с помощью коэффициента закрепления операций который рассчитывается как отношение количества детале-операций выполняемых на участке к числу рабочих мест
где Koni – число операций выполняемых на i-м рабочем месте.
Крм – количество рабочих мест на участке Крм = 6.
Если Кзо = 1 то тип производства массовый; 1 Кзо 10 – крупносерийный; 10 Кзо 20 – среднесерийный; 20 Кзо 40 – мелкосерийный; Кзо > 40 – единичный.
Подставив данные в формулу (2.1) получим .
Исходя из значения данный тип производства следует отнести к крупносерийному.
На основании заданной программы рассчитываем такт выпуска изделия tв а трудоемкость определяем средним штучным временем Тшт по операциям разработанного варианта маршрутного технологического процесса изготовления корпуса. Отношение этих величин называют коэффициентом серийности kс.
где tв – такт выпуска изделия миншт; Тшт – среднее штучное время мин.
Величину такта выпуска tв миншт вычисляем по формуле:
где Fд – действительный годовой фонд времени работы оборудования чсм;
N – годовая программа выпуска деталей шт.
Подставляя в формулу (2.3) значения полученных данных для расчета
Fд = 4015 чсм и N = 500получим tв = = 4818 миншт.
Для определения среднего штучного времени по операциям используем данные разработанного варианта маршрутного технологического процесса.
Расчет среднего штучного времени Тшт ср мин производим по формуле:
где Тшт n – число операций.
При определении среднего штучного времени Тшт ср по формуле (2.4) принимаем следующие исходные данные: = 78133 мин. Число операций по механической обработки на МРС n=26. Подставляя исходные данные в формулу (2.4) получим:
Тшт ср = 7813326 = 30 мин.
Подставив вычисленные по формулам (2.3) и (2.4) значения tв и Тшт ср в формулу (2.2) получим: kc = 481130 16.
Приняты следующие значения коэффициента серийности:
- для массового производства kc = 1;
- для крупносерийного производства kc = 2÷10;
- для среднесерийного производства kc = 10÷20;
- для мелкосерийного производства kc > 20.
Так как в нашем случае kc = 16 то делаем вывод что вид производства – среднесерийный.
Для данного участка установлен среднесерийный тип производства что подтверждается соответствующими расчётами. В этом случае необходимо исключить многократное перемещение деталей в процессе обработки так как это приводит к росту объёма незавершённого производства и увеличению числа пунктов промежуточного складирования что приводит к увеличению себестоимости продукции. Для крупносерийного производства наиболее эффективна будет предметная форма организации производства на участке. В этом случае всё оборудование необходимое для обработки деталей устанавливается с начала и до конца технологического процесса что обеспечивает прямоточность и уменьшение производственного цикла по длительности что в свою очередь позволяет снизить общие расходы на транспортировку деталей потребность в производственной площади на единицу оборудования а также уменьшить себестоимость продукции.
2 Анализ базового технологического процесса
На базовом предприятии технологический процесс (ТП) разработан для мелкосерийного производства.
Чертеж на деталь включает все необходимые данные и не имеет ошибок в размерных цепях.
Анализируя базовый технологический процесс механической обработки заготовки достоинством является минимизированное число операций.
Методы обработки в технологическом процессе приняты правильно. Станки при обработке данных деталей типа «Корпус» ориентированы для обработки при мелкосерийном производстве.
Технологический процесс изготовления обеспечивает высокую долговечность и надёжность корпуса. Но в тоже время базовый технологический процесс имеет целый ряд недостатков. Среди которых следует отметить следующие:
- Технологический процесс (ТП) разработан в виде маршрутной карты нет подробной разбивки технологического процесса на отдельные операции.
- Малая степень автоматизации.
- В нём нет ссылок на специальную оснастку или специальный инструмент.
- Базовая технология плохо представляет особенности эксплуатации данной детали.
- Универсальные станки.
При разработке нового технологического процесса механической обработки необходимо учитывать положительные и отрицательные стороны действующего технологического процесса на изготавливаемую деталь.
При анализе базового технологического процесса необходимо обратить внимание на уровень механизации и автоматизации всех производственных процессов изготовления деталей а также оборудование.
Вывод: проектируемый ТП будет выгодно отличаться от базового. Разработанный технологический процесс должен быть эффективным и технологичным по сравнению с заводским т.к. сократится время на токарные операции за счёт станков с ЧПУ сократится количество слесарных операций вследствие чего уменьшатся затраты на оборудование электроэнергию амортизацию площади сократится количество рабочих мест и увеличатся затраты на заработную плату.
3 Выбор типа заготовки и предварительное назначение припусков
Технико-экономическое обоснование выбора заготовки для обрабатываемой детали производят по нескольким направлениям: металлоемкости трудоемкости и себестоимости учитывая при этом конкретные производственные условия. Технико-экономическое обоснование ведется по двум или нескольким выбранным вариантам. При экономической оценке определяют металлоемкость себестоимость или трудоемкость каждого выбранного варианта изготовления заготовки а затем их сопоставляют [4].
Современное состояние технологии машиностроения предоставляет большие возможности для рационального выбора вида исходной заготовки и способа её получения. Чем больше объем выпуска деталей тем важнее выбрать заготовку форма и размеры которой приближаются к форме и размерам готовой детали. Такая направленность современной технологии позволяет снизить до минимума количество черновых операций добиться высокой эффективности производства и экономичного расхода металла. Правильный выбор заготовки существенно влияет на технико-экономические показатели технологического процесса изготовления детали.
Из нескольких методов изготовления заготовки выбирают наиболее экономичный при равной экономичности – наиболее производительный в ряде случаев – тот который обеспечивает наименьшее время подготовки производства. Программа выпуска заготовок характеризующаяся количеством изготавливаемых заготовок в течение года является важным фактором при выборе способа производства заготовок.
Окончательный выбор метода изготовления заготовки осуществляется с учетом суммарных затрат на изготовление заготовок и последующую их механическую обработку.
Сравним два наиболее рациональных способа изготовления заготовки корпуса – литьё в кокиль и штамповку на прессе.
Главным при выборе заготовки является обеспечение заданного качества готовой детали при ее минимальной себестоимости. Способ получения заготовки должен быть наиболее экономичными при заданном объеме выпуска деталей.
Расчет отдельных составляющих себестоимости. Стоимость основных материалов (заготовок) с учетом утилизации отходов определяют по формуле:
Мо = Ц3АГ – qотх·Цотх (2.5)
где Ц3АГ – цена заготовки руб.шт.;
qOTX – масса отходов на одну деталь кгшт.;
ЦОТХ – цена отходов руб.кг.
Цены материалов заготовок и отходов определяют по прейскурантам оптовых цен. Зная цены на материалы можно вычислить цену заготовки:
Ц3АГ = qм··Цм··кт-з (2.6)
где Цм – действующая оптовая цена единицы массы материала (рубкг)
qM – норма расхода материала на одну деталь кгшт.;
кт-з – коэффициент транспортно-заготовительных расходов при приобретении материалов; кт-з = 104 - 108 [2].
Оптовые цены на заготовки (рубкг) рассчитывают по формуле:
Цi = α – ·ln(m) (2.7)
где m – масса заготовки кг;
α – эмпирические коэффициенты.
Стоимость вспомогательных материалов Мвс определяют по заводским нормам расхода.
класс точности 3 группа серийности 4 группа сложности 3 [4]
Ц3АГ = 55 кгшт · 195 рубкг · 105 1125 руб;
Мо = 1125 – 28·65 945 руб.
Оценим методы изготовления по критериям: производительность металлоёмкость трудоёмкость и стоимость (таблица 2.1)
Таблица 2.1 – Обоснование выбора метода получения заготовки
Показатели метода изготовления
Метод получения заготовки
Заготовки при литье в кокиль имеют больший допуск чем при горячей объёмной штамповке. Отливка имеет литниковую систему выпары приливы и т.д. в то время как штамповка практически не имеет отходов (они появляются при штамповке в открытых штампах) кроме штампованных уклонов.
Отсюда следует вывод что:
а) отходов будет больше при литье;
б) затраты на механическую обработку будут выше при литье.
Металлоёмкость выше при штамповке так как в данном случае при штамповке заложен больший общий припуск на механическую обработку. При литье же есть возможность формирования внутренней полсти введением стержневой системы. Трудоёмкость последующей механической обработки будем считать меньшей для литья. Трудоёмкость же изготовления заготовки примем большей для литья. Для данного типа производства себестоимость выше при литье а это самый главный критерий выбора метода изготовления заготовки.
Единовременные затраты на изготовление оснастки для штамповки и литья а так же стоимость оборудования используемого в процессе изготовления заготовки корпуса в расчет не принимаются.
Наиболее рациональным способом изготовления заготовки «Корпус» является штамповка.
4 Выбор технологических базовых поверхностей и оценка точности
Процесс базирования заготовки заключается в её ориентации и последующем жёстком закреплении в координатной системе станка или приспособления в требуемом положении необходимом для выполнения операции обработки или сборки.
Выбор технологических баз и последовательности обработки поверхностей заготовки является наиболее ответственным этапом разработки технологического процесса. Правильность принятия решения на этом этапе технологического проектирования во многом определяет достижение требуемой точности детали в процессе ее изготовления.
Для повышения точности обработки детали необходимо учитывать принцип совмещения баз т.е. конструкторская технологическая и измерительная базы должны совпадать. Если базы выбраны правильно то требуемая точность изготовления детали будет обеспечена. Выбранная база вполне соответствует общепринятым принципам постоянства и совмещения баз [7].
В зависимости от числа идеальных опорных точек с которыми база находится в контакте или в зависимости от числа отнимаемых степеней свободы различают установочную базу находящуюся в контакте с тремя опорными точками; направляющую базу находящуюся в контакте с двумя опорными точками; упорную базу имеющую контакт с одной опорной точкой.
Каждая из перечисленных баз определяет положение заготовки относительно одной из плоскостей системы координат в направлении перпендикулярном к этой базе т.е. в направлении одной из координатных осей. Очевидно что для полной ориентировки заготовки в приспособлении необходимо использовать комплект из всех трёх баз [7].
Также при выборе баз необходимо учитывать дополнительные условия: удобство установки и снятия заготовки надежность закрепления заготовки в выбранных местах приложения сил зажима возможность подвода режущих инструментов с разных сторон заготовки и др. Для установки заготовки на первой операции используют необработанные поверхности так называемые черновые базы.
У деталей не подвергающихся полной обработке за технологические базы для операций черновой обработки рекомендуется принимать поверхности которые вообще не обрабатываются. Это обеспечит наименьшее смещение обработанных поверхностей относительно необработанных [7].
На первой операции в качестве базы используем необработанную поверхность заготовки. Закрепляем деталь в трёхкулачковом патроне. Затем используем в качестве баз торцы и обработанные на первой операции поверхности.
При выборе баз для чистовой обработки следует иметь в виду что наибольшая точность обработки достигается при условии использования на всех операциях механической обработки одних и тех же базовых поверхностей т. е. при соблюдении принципа единства баз. Для базирования используем внутренние цилиндрические поверхности отверстия обработанные торцы внешние обработанные диаметральные поверхности.
В токарных операциях опорной базой у корпуса служит наружная цилиндрическая поверхность которая непосредственно соприкасается с установочной поверхностью кулачков 3-х кулачкового патрона.
Опорными поверхностями для корпуса являются:
- центральное отверстие;
- наружные цилиндрические поверхности в том числе и резьбовая.
Настроечными базами по отношению к которым ориентируются другие обрабатываемые поверхности на корпусе являются:
- торец от которого формируется высота и все линейные размеры корпуса;
- наружные цилиндрические поверхности к которой привязаны диаметральные размеры корпуса;
- поверхности отверстий.
Поверочными базами по которым происходит выверка положения детали на станке или установка режущего инструмента являются поверхности:
- наружные и внутренние цилиндрические поверхности;
Выбранные технологические базы должны совместно с зажимными устройствами обеспечивать надежное прочное крепление детали и неизменность ее положения во время обработки.
Исходной заготовкой данной корпусной детали служит штамповка из алюминиевого сплава. При механической обработке данной заготовки применяют:
- базирование по плоскости и двум установочным отверстиям; при этом заготовка одним отверстием устанавливается на цилиндрический палец а другим – на ромбический (заготовка лишается шести степеней свободы);
- базирование по трём базовым поверхностям (и в этом случае заготовка лишается шести степеней свободы).
Оба способа базирования широко применяются в серийном производстве.
Первый способ базирования удобен простотой установки не требующей создания в приспособлениях специальных устройств для поджима обрабатываемой заготовки к направляющим и упорным базовым плиткам. Его недостатком является износ пальцев (особенно при их малом диаметре – порядка 10 мм). Это требует проведения хромирования пальцев.
Критерием точности базирования является погрешность положения.
Погрешность положения заготовки возникает в результате погрешностей изготовления СП погрешностей установки и фиксации СП на станке и износа опор.
Погрешность изготовления приспособлениязависит в основном от точности изготовления деталей СП. Соблюдение точности изготовления опор и других стандартных изделий СП является ответственной работой поэтому допуски ответственных размеров как стандартных так и нестандартных деталей СП обычно составляют 10 – 30 % допуска на соответствующий обрабатываемый размер заготовки. Как правило мм [8]. Соответственно примем .
Составляющая возникает в результате перемещений и перекосов корпуса приспособления на столе. В серийном производстве когда имеет место многократная периодическая смена СП на станках превращается в некомпенсируемую случайную величину изменяющуюся в определённых пределах. На величину влияют износ и возможные повреждения поверхностей сопряжения в процессе регулярной смены СП. При соблюдении рациональных условий смены СП и при правильном выборе зазоров в сопряжениях величину можно принять снизив её до 001÷002 мм. Соответственно примем
Составляющая характеризует изменение положения базирующих поверхностей опор в результате их износа в процессе эксплуатации СП. Интенсивность износа опор зависит от их конструкции и размеров материала и массы заготовки состояния баз а также условий установки заготовки в СП и снятия после обработки. Число установок вызывающих износ опоры на 1 мкм называют износостойкостью опор. Таким образом примем .
Погрешность положения определим по формуле:
Подставив в формулу (2.8) значения погрешностей изготовления установки и положения корпуса в процессе обработки получим:
5 Разработка технологического процесса обработки детали в САПР ТП
5.1 Использование информационных технологий и технических средств при разработке технологического процесса
В основу работы САПР ТП «КОМПАС–АВТОПРОЕКТ» положен принцип заимствования ранее принятых технологических решений. В процессе эксплуатации системы накапливаются типовые групповые единичные технологии унифицированные операции планы обработки конструктивных элементов и поверхностей. При формировании технологического процесса пользователю предоставляется доступ к архивам и библиотекам хранящим накопленные решения [12].
Разработка технологических процессов осуществляется в следующих режимах:
- проектирование на основе технологического процесса-аналога (автоматический выбор соответствующего ТП из базы данных с последующей его доработкой в диалоговом режиме);
- формирование ТП из отдельных блоков хранящихся в библиотеке типовых технологических операций и переходов;
- объединение отдельных операций архивных технологий;
- автоматическая доработка типовой технологии на основе данных переданных с параметризированного чертежа КОМПАС–ГРАФИК (чертежно-конструктор-ского редактора);
- разработка ТП в режиме прямого документирования в диалоговом режиме с помощью специальных процедур к справочным базам данных.
В системе реализована процедура позволяющая проектировать сквозные технологии включающие одновременно операции механообработки штамповки термообработки сборки сварки и т.д.
В комплект разрабатываемой документации входят: титульный лист карта эскизов маршрутная маршрутно-операционная операционная карты ТП ведомость оснастки материалов и другие документы в соответствии с ГОСТ. В базовую поставку системы включены более 60 видов технологических карт. Они выполнены в среде MS Excel. Распечатывать их можно как в горизонтальном так и вертикальном исполнении. При необходимости пользователь может разрабатывать новые карты а также вносить изменения в существующие образцы. Эскизы и графическая часть технологических карт выполняются в среде КОМПАС–ГРАФИК и вставляются в листы MS Excel как OLE – объекты [12].
Для разработки документов произвольной формы используется специальный генератор отчетов также формирующий технологические карты в среде MS Excel.
Технологические процессы разработанные в КОМПАС–АВТОПРОЕКТ помещаются в архив системы в сжатом виде. Оглавление такого архива доступно для ручного просмотра и корректировки. Автоматический поиск ТП в архиве производится либо по коду геометрической формы детали либо по отдельным характеристикам: тип детали принадлежность к изделию вид заготовки габаритные размеры и т.д. По заданным критериям поиска система находит несколько ТП оставляя окончательный выбор за технологом.
Оглавлением архива разработанных технологических процессов служит база данных конструкторско-технологических спецификаций (КТС) включающих в себя уровни изделий узлов и деталей. Система обеспечивает свободное перемещение от одного уровня к другому позволяя при этом просматривать и редактировать состав изделий узлов и деталей. Каждый уровень имеет подчиненную таблицу «Документы» записи которой содержат ссылки на документы созданные в различных приложениях: графические текстовые файлы архивные технологи и т.д.
Выбор ТП осуществляется процедурой разархивации которая извлекает технологический процесс из архива и помещает его в рабочее поле КОМПАС–АВТОПРОЕКТ доступное для внесения изменений. Информация о текущем технологическом процессе распределяется по уровням: деталь – операция – переход.
Пользователю предоставлена возможность перемещаться по уровням отслеживать состав переходов по каждой технологической операции осуществлять необходимую корректировку. При этом технологический процесс находящийся в архиве не меняется. Модифицированная технология может быть помещена обратно в архив под прежним или новым именем.
Процедуры обработки КТС позволяют производить выборку деталей по принадлежности к изделиям сборочным единицам цехам изготовления и т.д. На их основе формируются сводные нормы заявки на материал комплектующие карты и другие технологические документы.
В системе реализованы процедуры позволяющие глобально корректировать любую информацию в архиве технологических процессов (например замена устаревших ГОСТов технологической оснастки) рассчитывать суммарную трудоемкость изготовления деталей и сборочных единиц определять материалоемкость и себестоимость изделия в целом.
Система обеспечивает удобную организацию баз данных и быстрый доступ к требуемой информации. Она обладает хорошо организованным диалоговым интерфейсом обеспечивающим легкое и наглядное перемещение по всем базам данных. Приемы работы с базами данных идентичны что упрощает их сопровождение. Программа поддерживает диалоговый доступ к сведениям об оборудовании инструментах материалах и т.д. В любой момент эти данные могут быть выведены на экран скорректированы или пополнены. В информационном пространстве КОМПАС–АВТОПРЕКТ можно создавать новые информационные массивы корректировать состав и размерность их полей. Взаимодействие между таблицами данных в КОМПАС–АВТОПРОЕКТ построено на динамически формируемых SQL-запросах. Операторы SQL генерируются либо автоматически либо по шаблону заданному пользователем. В базовую поставку системы входит около 3000 реляционных таблиц различной структуры и подчиненности.
Работа с базами данных организована в архитектуре клиент-сервер что исключает дублирование и обеспечивает защиту информации. В качестве SQL – серверов в КОМПАС–АВТОПРОЕКТ могут быть использованы InterBase MS SQL Oracle. Данные могут располагаться как на локальной станции так и на выделенном сервере. Имеющиеся у пользователя информационные массивы легко включаются в состав баз данных системы КОМПАС–АВТОПРЕКТ.
Одним из основных преимуществ КОМПАС–АВТОПРОЕКТ является возможность модернизации системы без участия разработчика самими пользователями. Корректируются состав и структура всех баз данных настраиваются формы технологических документов подключаются новые программные модули.
Гибкость программного и информационного обеспечения позволяет быстро адаптировать систему к любым производственным условиям. Инструментальные средства системы позволяют разрабатывать на ее основе пользовательские приложения.
САПР ТП КОМПАС–АВТОПРОЕКТ состоит из ядра и окружения прикладных задач [12]. Основные функциональные режимы системы делятся на две группы: функции подсистемы проектирования и функции подсистемы управления базами данных (СУБД).
Функции подсистемы проектирования:
- автоматизированное проектирование технологических процессов;
- интеграция с КОМПАС–ГРАФИК и КОМПАС–МЕНЕДЖЕР;
- материальное и трудовое нормирование;
- автоматическое формирование комплекта технологической документации (горизонтальное и вертикальное исполнение);
- каталогизация разработанных ТП в архиве технологий;
- возможность глобального анализа архивных технологий с передачей результатов в автоматизированную систему управления производством;
- возможность разработки сквозного ТП и подключения новых технологических переделов;
- оперативный просмотр графики: чертежей деталей инструментов эскизов операций и т.д.;
- возможность настройки образцов технологических документов;
- архивация текущего комплекта технологических документов в архиве карт;
- ведение конструкторско-технологических спецификаций;
- автоматический поиск технологий по коду или текстовому описанию детали в базе данных конструкторско-технололгических спецификаций;
- автоматизированное формирование кода детали в соответствии с ЕСКД и ТКД;
- архивация текущего состава спецификаций в архиве изделий;
- расчетные процедуры.
- организация иерархическо-реляционной связи информационных массивов;
- возможность структурной модификации любой базы данных;
- возможность подключения новых информационных массивов;
- возможность подключения к любому табличному полю справочного массива;
- многостраничный режим доступа одновременно к нескольким базам данных;
- отображения данных: таблица – слайд таблица – дерево таблица – комментарий;
- процедура поиска по критериям в любой базе данных;
- экспорт данных из любой базы данных в текстовый документ или в формат файлов E
- блокировка несанкционированного доступа к защищенной базе данных;
- возможность установки различных степеней защиты данных от изменений;
- копирование удаление вставка записей по одной или блоками;
- сортировка замена просмотр распечатка содержимого любых данных;
- возможность настройки содержимого блоков основного меню системы;
- возможность подключения к системе новых программ;
- встроенный генератор отчетов;
- настройка параметров системы с помощью файла конфигурации (*.ini).
Функциональные возможности САПР ТП КОМПАС–АВТОПРОЕКТ довольно широки и позволяют решить широкий спектр технологических задач машиностроительных предприятий.
САПР КОМПАС–АВТОПРОЕКТ позволяет повысить производительность труда технолога сократить сроки и трудоемкость технологической подготовки производства. В состав данного интегрированного программного комплекса входят подсистемы проектирования технологий: механообработки штамповки сборки сварки термообработки покрытий гальваники.
Принципы проектирования технологических процессов в КОМПАС–АВТО-ПРОЕКТ универсальны и основаны на использовании часто повторяемых технологических решений хранящихся на различных уровнях иерархии: архивы групповых и типовых технологий библиотеки операций и переходов. С этой точки зрения САПР технологических процессов – это прежде всего система управления базами данных (СУБД). От того как реализованы функции обработки данных от их логических взаимосвязей зависят остальные показатели системы.
Базовая поставка системы КОМПАС–АВТОПРОЕКТ включает более 1000 информационных массивов общим объемом 30 МБ. Количество подключаемых новых баз данных (БД) не ограничено а на структуру имеющихся БД не наложено никаких ограничений. Общая схема разработки ТП выглядит как процесс слияния различных технологических компонентов типовых решений НСИ в некоторую центральную область (текущую технологию) способную принимать информацию из различных источников.
В САПР КОМПАС–АВТОПРОЕКТ реализован механизм позволяющий отобразить структуру изделия (детали) взаимосвязи между оборудованием технологической оснасткой и методами обработки. Модель технологического процесса в САПР ТП занимает центральное место. В КОМПАС–АВТОПРОЕКТ – это трехуровневая цепочка связанных реляционных таблиц записи которых имеют различную логическую структуру. Такая модель является универсальной и настраиваемой. Она позволяет создавать технологии различных переделов и включать в них любые средства технологического оснащения в том числе и принципиально новые.
Вся информация о текущем технологическом процессе распределена по уровням «Деталь» - «Операция» - «Переход». Пользователю предоставлена возможность перемещаться по уровням отслеживать состав переходов каждой технологической операции вносить необходимые изменения на любом из уровней. Особенностью этой модели является наглядная форма представления информации. Записи таблицы «Переходы» содержащие тексты переходов режущие инструменты приспособления режимы резания и др. выводятся на экран одним списком. Такая возможность достигается тем что физические записи данного уровня имеют различную логическую структуру. Этот же механизм позволяет проектировать технологии включающие одновременно операции механообработки штамповки термообработки покрытий и т.д. Подключение нового технологического передела производится самим пользователем.
Одним из основных преимуществ КОМПАС–АВТОПРОЕКТ является возможность модернизации системы без участия разработчика. Корректируется состав и структура всех баз данных настраиваются формы технологических документов подключаются новые программные модули. Гибкость программного и информационного обеспечения позволяет быстро адаптировать систему к любым производственным условиям.
5.2 Разработка технологического процесса изготовления корпуса средствами САПР КОМПАС-Автопроект 9.3
Разработка технологического процесса начинается с загрузки в рабочее поле системы режима «Технология» из раздела «Базы данных».
Перед началом разработки нового технологического процесса необходимо очистить поле текущей технологии (рисунок 2.1) произведя двойной щелчок на пиктограмме «Очистка технологии». Затем следует установить курсор на нужной записи и нажатием клавиши F12> запустить требуемый режим. Во всех таблицах текущей технологии будут удалены все записи.
Рисунок 2.1 – Режим очистки содержимого таблиц текущей технологии
Ввод данных начинается с таблицы «Деталь». Процесс ввода и редактирования полей записи на всех уровнях идентичен. Для загрузки формы просмотра и корректировки полей необходимо нажать на инструментальной панели кнопку «Редактирование записи» или клавишу F4>. Данная форма имеет следующую структуру: слева располагаются имена полей справа— их значения.
Данные можно вводить с клавиатуры установив курсор в заполняемом поле или копировать из справочной базы данных (БД). Признаком привязки такой БД к определенному полю записи является пиктограмма «Книга» справа от поля ввода данных. Справочные БД могут быть подключены к любому полю. Например в таблице «Деталь» к соответствующим полям подключены БД по материалам заготовкам наименованиям деталей и т.д.
Чтобы скопировать данные из БД следует подвести курсор к пиктограмме «Книга» щелчком левой кнопки мыши запустить справочную БД выбрать нужную строку произвести двойной щелчок мышью или нажать клавишу F12>. Система вернется в форму редактирования и скопирует информацию в нужные поля.
После того как введены все данные о детали необходимо выйти из формы редактирования нажав кнопку «Выход» или комбинацию клавиш Alt>+ F4>. На уровне Деталь должна появиться запись с данными о детали. Необходимую корректировку можно произвести не входя в режим редактирования F4>. Для этого нужно выделить курсором требуемое поле и начать ввод с клавиатуры непосредственно в ячейке таблицы. Отмена ввода— нажатие клавиши Esc>. Если к полю привязан справочный массив данных то в таблице с правой стороны появляется кнопка с пиктограммой «Многоточие».
Переход на уровень Операции осуществляется нажатием кнопки «Переход на следующую таблицу» на инструментальной панели или клавиши F12>. При начальном вводе таблица Операции не содержит записей. Необходимо зарезервировать нужное количество строк клавишей Insert>. Затем последовательно в каждую строку ввести информацию об одной технологической операции. Порядок следования операций в технологическом маршруте задается порядком расположения строк в таблице. Режим корректировки полей F4> осуществляет загрузку формы редактирования (рисунок 2.2) аналогичной использующейся на уровне Деталь.
Рисунок 2.2 – Структура записи таблицы «Операции»
Информация в поля таблицы расположенной на уровне Операции может вводиться как с клавиатуры так с помощью справочных баз данных.
После того как введены сведения об операциях можно вводить данные о переходах. Для этого следует установить курсор на нужную операцию и нажать клавишу F12>. Система перейдет к следующему объекту и в рабочее поле системы будет загружена таблица Переходы.
Поскольку таблицы Операции и Переходы связаны уникальным ключевым полем ID (генерируемым автоматически при каждом вводе новой операции) то каждая строка объекта Операции будет иметь подчиненный список записей в таблице Переходы. При первоначальном вводе она не содержит записей. Нужно зарезервировать необходимое количество пустых записей клавишей Insert> и войти в режим редактирования первой строки нажав клавишу F4>.
Справочная таблица Тип перехода содержащая список наименований доступных баз данных представлена на рисунке 2.3.
Рисунок 2.3 – Справочные базы данных таблицы «Переходы»
Выделить курсором нужную БД и двойным щелчком поместить ее в рабочее поле системы. Из загруженного справочника выбирать информацию последовательно нажимая клавишу F12>. При достижении последнего уровня все необходимые данные будут скопированы и система вернется в форму редактирования записи таблицы Переходы. В зависимости от вида выбранной информации на форме «Редактирование записи» меняются наименования полей. Так например если были выбраны данные о режущем инструменте (рисунок 2.4) поле «Переход» изменит свое название на «Режущий инструмент». Данный механизм реализуется с помощью специальных режимов управления логической структурой данных F3>.
Рисунок 2.4 – Выбор режущего инструмента из справочника КОМПАС-Автопроект
В поле дублирующей технологии могут помещаться как реальные ТП связанные с базой данных КТС так и типовые ТП доступ к которым осуществляется из режима «Архив типовых технологий» в КОМПАС-АВТОПРОЕКТ-Технология.
Технологический процесс может быть разработан на основе библиотеки типовых операций. Последовательность действий реализующих данный режим будет
рассмотрена для проектирования фрезерной операции ТП «Корпус».
Рисунок 2.5 – Формирование переходов фрезерования плоскости
Подсистема «Сквозной ТП» позволяет сформировать технологию состоящую из операций и переходов. В режиме текущей технологии на уровне «Операции» при обращении к справочнику в отличие от других подсистем диалог начинается с выбора вида операции. После выбора требуемого и нажатии клавиши F12> загружается соответствующая база данных. Из базы данных выбирается всё необходимое и таким образом формируется технологический переход и весь ТП в целом.
Для просмотра созданной технологии используется «Дерево технологий».
Чтобы представить данные о техпроцессе в виде дерева необходимо произвести двойной щелчок мыши на пиктограмме с изображением дерева в области «Процедуры» режима «Технология функции». Стартует приложение treetex.exe на форму которого выводятся два технологических процесса. Реализован механизм копирования и перемещения данных между этими ТП. Технологические операции копируются из одной технологии в другую вместе с подчиненными таблицами.
Структура дерева включает четыре уровня:
- разделы: «Переходы» «Эскизы» «Карты» «Контроль» «Комментарии»;
- содержимое разделов.
Когда технологический процесс в поле текущей технологии сформирован и отредактирован можно переходить к разработке комплекта документации. Для этого необходимо щелкнуть мышью на пиктограмме с изображением карт в области Процедуры. Стартует программа формирования комплекта технологической документации. Результатом данной процедуры является комплект документов технологического процесса обработки резанием представленный приложением к выпускной квалификационной работе.
6 Выбор моделей оборудования
Выбор оборудования производят по главному параметру в наибольшей степени выявляющему его функциональное значение и технические возможности. Физическая величина характеризующая главный параметр устанавливает взаимосвязь оборудования с размером изготавливаемого изделия [4].
При выборе вариантов оборудования учитывают минимальный объем приведенных затрат на выполнение технологического процесса при максимальном сокращении периода окупаемости затрат на механизацию и автоматизацию. Годовая потребность в оборудовании определяется из годового объема работ устанавливаемого статистическим анализом затрат средств и времени на изготовление изделий.
При выборе оборудования в условиях действующего производства приходится ориентироваться на имеющееся в цехе оборудование и обязательно учитывать степень фактической загрузки отдельных его групп. Во многих случаях технологическая операция осуществление которой предусматривалось на загруженном в цехе оборудовании может быть произведена без ущерба для качества и производительности обработки. Подобные изменения первоначально намеченных способов обработки должны подкрепляться экономическими расчётами их производственной целесообразности. Проектирование технологического процесса рассчитанного на приобретение специального оборудования в условиях действующего серийного производства являются исключением и требует проведения предварительного экономического обоснования.
Таблица 2.2 – Станки применяемые по ТП
Наименование оборудования
Токарный станок с ЧПУ
Фрезерный широко-универсальный станок
Вертикально-сверлильный станок
Вертикально-фрезер-ный консольный станок
Фрезерный широко- универсальный станок
Горизонтально-протяжной полуавтомат
Номинальная тяговая сила
Вертикально-сверлильный станок
Производительность оборудования определяют на основании анализа времени изготовления изделия заданного качества. Годовые приведенные затраты на использование оборудования определяются размерами затрат на его эксплуатацию и изготовление.
7 Выбор конструкции и расчёт станочного приспособления для автоматизированного оборудования
При выполнении работы по выбору конструкции и расчёту приспособления следует руководствоваться многими критериями среди которых наиболее важными являются: экономическая эффективность; надёжность и точность; производительность [6].
По конструкции силовой части целесообразно применение пневматического поршневого привода. В этом приводе давление сжатого воздуха преобразуется в силу действующую вдоль оси штока связывающего привод с зажимным механизмом приспособления [8].
Пневматические приводы приспособлений отличаются быстротой действия относительной простотой конструкции лёгкостью и простотой управления надёжностью и стабильностью в работе. По быстроте действия пневмоприводы значительно превосходят не только ручные но и многие механизированные приводы. К преимуществам пневмопривода следует отнести то что его работоспособность не зависит от колебаний температуры окружающей среды. Большое преимущество состоит также в том что пневмоприводы обеспечивают непрерывное действие зажимной силы вследствие чего эта сила может быть значительно меньше чем при ручном приводе. Это обстоятельство весьма существенно при обработке деталей склонных к деформациям при зажиме.
Рычажно-шарнирные механизмы обычно применяются в качестве усилителей приводов. По конструкции они делятся на однорычажные двухрычажные одностороннего действия двухрычажные двухстороннего действия (самоцентрирующие). Свойством самоторможения не обладают [8].
7.1 Описание приспособления
Приспособление служит для фрезерования плоскостей детали типа корпус.
Обрабатываемая деталь базируется по цилиндрическому отверстию диаметром 70 мм торцом выступа в четырёх точках и боковой стороне.
Установка корпуса производится на четыре опоры 7 и палец 5 а правильная ориентация для фрезеровки обеспечивается посредством подвижного фиксатора 1. Перемещение фиксатора размещённого на стойке выполняется с помощью винтовой пары.
Закрепление корпуса осуществляется лапками двух рычагов 8. При запуске пневматического цилиндра ползун 14 начинает своё перемещение в горизонтальном направлении увлекая за собой ползун и передавая усилие шатуну 11 переносит его на рычаг который непосредственно осуществляет зажим заготовки для фрезерования горизонтальной поверхности.
Все зажимные и установочные элементы приспособления смонтированы на плите 6. Приспособление устанавливается на столе фрезерного станка в пазы по двум фиксаторам 12 соединённым с плитой посредством винтов 13. Крепление приспособления на стол станка осуществляется болтами.
Руководствуясь конструкцией приспособления силовые элементы которого представляют собой рычажно-шарнирный механизм где усилие передаётся от ползуна к шатуну а в последствии и рычагу убедились в преимуществе данной конструкции.
Использование пневмоприводов двухстороннего действия позволяет сократить расход воздуха на 30-40 %. Поршневой привод крепится на столе станка. Шток пневмопривода связывается соответствующим образом с зажимным устройством приспособления.
Рычажное зажимное устройство имеет ряд преимуществ [8]: простая конструкция; значительный выигрыш в силе и в перемещениях; постоянство силы закрепления которая не зависит от размеров заготовки; возможность закрепить заготовку в труднодоступном месте; технологичность; удобство в эксплуатации; надёжность.
Простота конструкции является достоинством приспособления. Однако необходимость использования двух зажимных устройств и одного подвижного фиксатора требует значительного количества времени на переустановку обрабатываемых деталей. Конструкция разработана для серийного производства.
7.2 Силовой расчёт приспособления
Проведём силовой расчёт рычажного механизма руководствуясь конструкцией приспособления силовые элементы которого испытывающие нагружение представляют собой усложнённый шарнирно-рычажный механизм с ползуном где усилие передаётся от ползуна к шатуну а в последствии и рычагу [10].
Силу закрепления определим из условия равновесия силовых факторов действующих на заготовку.
Исходя из условия надёжности закрепления обрабатываемой детали необходимо чтобы соблюдалось следующее условие: РЗАК > PZ.
Рисунок 2.6 – Программа расчета режимов резания при фрезеровании корпуса
Главная составляющая силы резания при фрезеровании PZ – окружная сила.
Согласно расчета PZ = 2143 кгс = 2100 Н.
Величина конструктивных элементов следующая: h = 50 мм l = 10 мм а = 35 мм в = 45 мм высота рычага n = 21мм.
Сила зажима рассчитывается исходя из конструктивных соображений.
Расчётная схема силы зажима и схема взаимодействия сил резания и зажима представлены на рисунке 2.7
а) расчётная схема силы зажима
б) схема взаимодействия сил резания и зажима: RA - реакция опор А (на действующие нагрузки); РВ - вес детали; F –сила трения; РЗ – сила закрепления; Р1Р2 –вертикальная и горизонтальная составляющая сил резания.
Рисунок 2.7 – Схемы
При данной конструкции приспособления усилие передаваемое от пневмоцилиндра равно горизонтальной составляющей силы реакции опоры так как ползун в механизме совмещён со штоком пневмоцилиндра.
Произведём расчёт усилия зажима:
По рисунку видно что
Вертикальная составляющая силы имеет вид Rdy = Rdx sin откуда Rdx = = Rdy sin и Rdy = Rdxhl = 7455010 = 3725Н и переносится в точку С как усилие действующее на рычаг. Т.о. Pc = 3725 Н.
Произведём суммирование моментов относительно точки А соблюдая правило знаков. Результат будет выглядеть следующим образом:
Проведя анализ полученных величин пришёл к выводу что максимальное нагружение испытывает точка В т. к.:
RDy = PC = 3725 H – вертикальная составляющая приведённого выше фактора;
RB = 85143 Н – реакция опоры в точке В максимальная нагрузка;
RА = PЗ = 47893 Н – реакция опоры в (А) что соответствует усилию зажима.
Определяем диаметр пневмоцилиндра[8].
Подставив в формулу (2.12) числовые значения получим
Принимаем нормализованный цилиндр диаметром Dц = 40 мм. Остальные размеры пневмоцилиндра принимаем по ГОСТ 15608-81.
Так как рычаг имеет форму конструкции переменную по длине но симметричную относительно оси то усилие непосредственно действующее на деталь т. е. усилие зажима складывается из двух равных по величине. Таким образом зажим осуществляется по двум точкам.
Следовательно номинальное усилие RА2 = PЗ2 = 478932 = 239465 Н.
Усилие зажима в одной из двух точек касания с закрепляемой деталью лапки рычага сила необходимая для закрепления заготовки рассчитывается с учётом трения [17].
где - коэффициент учитывающий потери от трения на осях прихватов.
Для определения коэффициента трения воспользуемся табличными данными. Для рычагов (прихватов) с данным конструктивным исполнением при l1l = ba = = 4535 = 128.
Учитывая что q = 119 Н получим усилие необходимое для закрепления обрабатываемой заготовки отличное от номинального на величину потери на трение и другие. Проведём расчёт зажимного усилия для одной лапки прихвата.
Рассчитаем усилие Q развиваемое пневматическим цилиндром:
где Н – сила трения поршня с манжетным уплотнением;
p – давление воздуха; ; Н.
Усилие зажима (сила закрепления заготовки) рассчитывается по формуле
– коэффициент учитывающий потери от трения на осях прихватов;
Q – усилие развиваемое пневматическим цилиндром Н.
Определяем реакцию в опоре R = Q + P = 765 + 875 = 1640 Н
Диаметр d опоры из условия прочности на смятие и ширина B рычага связаны соотношением (2.16)
Принимаем диаметр штифта= 10мм.
7.3 Точностной расчёт станочного приспособления
Погрешность установки есть отклонение фактически достигнутого положе- ния заготовки при установке в СП от требуемого.возникает вследствие несовмещения измерительных и технологических баз неоднородности качества поверхностей заготовок неточности изготовления и износа опор СП нестабильности сил закрепления (сокращение погрешности от данного фактора получено в результате усовершенствования приспособления и замены механического узла зажимного механизма на пневматический привод) и др[5].
вычисляют по погрешностям: базирования закрепления и положения.
содержит как случайные составляющие погрешности объединяемые в основную так и закономерно изменяющуюся систематическую погрешность связанную с измерением формы поверхности контакта установочного элемента в результате его износа.
включает закономерно изменяющуюся систематическую погрешность определяемую прогрессирующим изнашиванием установочных элементов а также постоянные систематические погрешности определяемые погрешностями изготовления и сборки опор СП и определяемые погрешностями установки и фиксации СП на станке[5].
В общем случае . (2.17)
Если постоянные систематические погрешности можно полностью уст- ранить соответствующей настройкой станка то
Если погрешности и зависящие от износа установочных элементов можно регулярно компенсировать поднастройкой инструмента то
При укрупнённых расчётах на точность обработки погрешность соответствующему последнему случаю можно определить по таблицам.
При установке заготовок с выверкой соответствующая погрешность установки возникает из-за неточности выверки по разметочным рискам или непосредственно по поверхностям заготовки. Погрешностьвключает также и погрешность закрепления . При укрупнённых расчётах на точность обработки погрешность установки с выверкой можно определить по таблицам.
Нахождение всех составляющих в формуле (2.17) произведено далее по тексту. Подставив все найденные ниже числа в формулу (2.17) получим:
Погрешность базирования есть отклонение фактически достигнутого положения заготовки при базировании от требуемого; определяется как предельное поле рассеяния расстояний между технологической и измерительной базами в направлении выдерживаемого размера. Приближённо можно оценить разностью между наибольшим и наименьшим значениями указанного расстояния. Величина зависит от принятой схемы базирования и точности выполнения баз заготовок (включая отклонения размера формы и взаимного расположения баз). Значения определяют соответствующими геометрическими расчётами или анализом размерных цепей что в некоторых случаях обеспечивает более простое решение задачи.
В общем случае погрешность базирования следует определять исходя из пространственной схемы расположения заготовки. Однако для упрощения расчётов
обычно ограничиваются рассмотрением смещений только в одной плоскости.
Погрешность базирования = 0 если:
) совмещены технологическая и измерительная базы к чему всегда следует стремиться при проектировании СП;
) размер получен мерным инструментом;
) направление выдерживаемого размера перпендикулярно направлению размера характеризующего расстояние между технологической и измерительной базами.
Проведём расчёт погрешности базирования [5]. При L = 78 мм что приблизительно равно табличному значению 80 мм
Если учесть что выдерживаемый размер соответствует размеру обработки а
базирование осуществляется по плоской поверхности при фрезеровании выступа то а поле допуска по H14.
Подбор поля допуска осуществлён по СТП 2.К04-050-84 для интервала размеров 65÷80 мм.
Погрешность закрепления – это разность между наибольшей и наименьшей величинами проекций смещения измерительной базы на направление выполняемого размера в результате приложения к заготовке силы закрепления. В основном возникает в связи с изменением контактных перемещений в стыке "заготовка – опоры приспособления“.
Деформациями жёстких заготовок и корпуса приспособления под действием сил закрепления обычно пренебрегают.
На погрешность закрепления наибольшее влияние оказывают следующие факторы: непостоянство силы закрепления неоднородности шероховатости и волнистости базы заготовок износ опор. Формулы для расчёта погрешности закрепления как функции наиболее значимых факторов приведены далее.
Суммарная погрешность закрепления рассчитывается по формуле[5]
Проведём расчёт каждой составляющей данного выражения.
) Погрешность из-за непостоянства силовых факторов закрепления
) Погрешность из-за неоднородности шероховатости базы заготовки
) Погрешности из-за неоднородности волнистости базы заготовки
) Погрешность из-за износа опорной поверхности установочного элемента для опор с плоской головкой по ГОСТ 13440-68 и ГОСТ 4743-68 принимаем равной 0.
Q – сила действующая по нормали на опору Н;
индексы з и о означают что рассматриваемые параметры относятся к заготовке и к опоре соответственно;
– упругая постоянная материалов контактирующих заготовки и опоры
где – модули упругости опоры и заготовки ГПа;
– коэффициенты Пуассона материала опоры и заготовки;
НВ – твёрдость материала заготовки по Бринеллю;
– безразмерный коэффициент стеснения характеризующий степень упрочнения поверхностных слоёв обработанных без заготовки;
– предел текучести материала заготовки МПа;
А – номинальная площадь опоры ;
где d1 – наружный диаметр мм;
d2 – внутренний диаметр мм;
u – линейный износ опоры мм;
и – безразмерные параметры опорной кривой = 01 и = 04 [4];
W и RB соответственно высота и длина волны поверхности мкм
(указанные параметры характерны для волнистости поверхности).
Безразмерный приведённый параметр кривой опорной поверхности характеризующий условия контакта базы заготовки с опорой
Произведём расчёт параметров необходимых для расчёта погрешности закрепления:
) По формуле (2.23) подставив соответствующие значения получим
) По формуле (2.24) подставив соответствующие значения получим
) По формуле (2.25) подставив соответствующие значения получим
Рассчитаем погрешность закрепления:
) Погрешность из–за непостоянства силы факторов закрепления
) Погрешность из-за неоднородной шероховатости базы заготовки
) Погрешности из-за неоднородности волнистости базы заготовки
Суммарная погрешность закрепления рассчитаем по формуле
Если учесть что при применении опоры с плоской головкой погрешность из-за износа опорной поверхности установочного элемента равна нулю то и .
Погрешность изготовления приспособлениязависит в основном от точности изготовления деталей СП. Соблюдение точности изготовления опор и других стандартных изделий СП является ответственной работой поэтому допуски ответственных размеров как стандартных так и нестандартных деталей СП обычно составляют 10 – 30 % допуска на соответствующий обрабатываемый размер заготовки. Как правило мм. Соответственно примем
Составляющая возникает в результате перемещений и перекосов корпуса приспособления на столе. В массовом производстве при однократном неизменном закреплении СП на станке эту величину доводят до определённого минимума выверкой и считают постоянной в течении эксплуатации данного СП. При определённых условиях составляющая может быть устранена соответствующей настройкой данного станка. В серийном производстве когда имеет место многократная периодическая смена СП на станках превращается в некомпенсируемую случайную величину изменяющуюся в определённых пределах.
На величину влияют износ и возможные повреждения поверхностей сопряжения в процессе регулярной смены СП. При соблюдении рациональных условий смены СП и при правильном выборе зазоров в сопряжениях величину можно принять снизив её до 001÷002 мм. Соответственно примем
Составляющая характеризует изменение положения базирующих поверхностей опор в результате их износа в процессе эксплуатации СП. Интенсивность из- носа опор зависит от их конструкции и размеров материала и массы заготовки состояния баз а также условий установки заготовки в СП и снятия после обработки. Число установок вызывающих износ опоры на 1 мкм называют износостойкостью опор С. Величину С рассчитывают в порядке указанном ниже.
При известной величине Сф можно определить погрешность обработки связанную с износом опор при заданном числе установок N или оценить допустимое по износу число установок и следовательно найти периодичность замены опор СП. В этом случае необходимо предварительно рассчитать допустимый износ опор uДОП. Износостойкость можно определить также и по зависимости.
Произведём расчёт погрешности от изменения положения базирующих поверхностей опор в результате их износа в процессе эксплуатации СП:
Рассчитаем износостойкость опор[5]:
где – коэффициенты приведённые в таблице для опорных пластин причём m = 6832 m1 = 4287 m2 = 293750.
– критерии износостойкости с учётом материала заготовки и опор и нагружения опор соответственно.
определяется по таблице и в соответствии с этим равен 097 при учете того что материал заготовки алюминиевый сплав а материал опор сталь У10А.
Таким образом проведя подборку по таблице критериев износостойкости пришли к выводу что номинальное значение 097.
определяется по следующей формуле:
где Q – усилие от зажимного механизма;
F – номинальная площадь касания опоры с базой заготовки;
HV – твёрдость рабочих поверхностей опор по шкале Виккерса.
Таким образом получаем что Q = 2200 H F = 1000 HV = 700.
Подставив данные выражения в формулу (2.28) получим
Подставив все данные и расчеты данного пункта в формулу (2.26) мы получим .
Определим поправочные коэффициенты:
где – коэффициент учитывающий время неподвижного контакта заготовки с опорами;
– коэффициент учитывающий влияние длины L пути скольжения заготовки по опорам СП в момент базирования;
– коэффициент учитывающий условия обработки.
где – машинное время обработки.
Остальные значения табличные и соответственно .
Таким образом К = 17775 × 1 × 112 = 199.
Фактическая износостойкость Сф = СК = 1763199 = 885 уст.мкм. (2.31)
Нормальный износ u = 5000885 = 565 мкм.
8 Расчёт и проектирование режущего инструмента
Произведём расчёт и конструирование протяжки для обработки отверстия диаметром 25 мм в размер 26H13 и длиной LИ = 125 ± IT162 × (± 095) в заготовке корпуса входа из алюминиевого сплава АК6 с В = 360 МПа ( 36 кгсмм²).
Отверстие протягивают после тонкого растачивания на горизонтально протяжном станке 7Б56. Патрон быстросменный автоматический по ГОСТ 16885-71.
Припуск на диаметр под протягивание
где D – исходный диаметр отверстия перед протягиванием;
D0 – получаемый после протягивания диаметр отверстия.
А = 26 - 25 = 1 мм.
Припуск под протягивание отверстий и значения допусков предварительного диаметра могут быть определены по таблицам. Т.о. припуск под протягивание предварительно обработанных растачиванием поверхностей А = 10 мм для отверстия диаметром 25 мм в размер 26H13 и длиной L = 125 ± IT162 × (± 095).
Подъём на зуб на сторону SZ выбираем по нормативам режимов резания для протягивания. Принимаем SZ = 005 мм.
Между режущими и калибрующими зубьями делают несколько (два – четы- ре) зачищающих зубьев с постоянно убывающим подъёмом на зуб. Для нашего при- мера принимаем zЗ = 3 и распределяем подъём на зуб следующим образом: 12 SZ 0025 мм; 13 SZ 0017 мм; 16 SZ 0008 мм.
Профиль размеры зуба и стружечных канавок между зубьями выбирают в зависимости от площади слоя металла снимаемого одним режущим зубом протяжки. Необходимо чтобы площадь сечения стружечной канавки между зубьями отвечала условию[4]
где – коэффициент заполнения канавки (выбираем по таблице);
– площадь сечении канавки мм²;
– площадь сечения среза металла снимаемого одним зубом:
где – длина обрабатываемого отверстия;
– подъём на зуб на сторону мм.
Из формулы (2.33) находим .
Пользуясь таблицей для большего ближайшего значения при криволинейной форме стружечной канавки зуба принимаем: шаг протяжки t = 12 мм; глубина канавки h = 5 мм; длина задней поверхности b = 4 мм; радиус закругления канавки r = 25 мм.
Шаг калибрующих зубьев tК принимаем равным 06 – 08 мм шага режущих зубьев. Для данного примера принимаем tК = 07·t = 0712 = 84 мм.
Для получения лучшего качества обработанной поверхности шаг режущих зубьев протяжки делают переменным: от t + (02 1 мм) до t – (02 1 мм). Принимаем изменение шага ± 03 мм. Тогда из двух смежных шагов один равен 12 + 03 = 123 мм; а второй 12 – 03 = 117 мм. Фаска f на калибрующих зубьях плавно увеличивается от первого зуба к последнему с 02 до 06 мм.
Геометрические элементы лезвия режущих и калибрующих зубьев выбираем по источникам γ = 20º; α = 3º. Число стружкоразделительных канавок находится в пределах 6÷8. Переднее отклонение передних углов всех зубьев ±2º задних углов режущих зубьев ±30 задних углов калибрующих зубьев ±15.
Максимальное число одновременно работающих зубьев
Определим размеры режущих зубьев. Диаметр первого зуба принимаем равным диаметру передней направляющей части: DЗ = D – А = 26 – 1 = 25 мм. Диаметр каждого последующего зуба увеличивается на 2SZ. На последних трёх зачищающих зубьях предшествующих калибрующим зубьям подъём на зуб постепенно уменьшается.
Диаметр калибрующих зубьев DK = Dma – изменение диаметра отверстия после протягивания (при увеличении диаметра отверстия – со знаком «–» а при уменьшении – со знаком «+»); определяется для каждого материала и толщины стенок протягиваемой заготовки опытным путём. В большинстве случаев при протягивании заготовок из стали увеличение диаметра отверстия составляет 0005 – 001 мм; при протягивании алюминиевого сплава АК6 уменьшение достигает 001 мм. При обработке отверстий с большими полями допусков (11÷17-й квалитеты) диаметр калибрующих зубьев DK = Dmax – (001 0015) мм.
Предельные отклонения диаметров режущих зубьев не должны превышать 001 мм а калибрующих зубьев 0005мм.
Число режущих зубьев подсчитываем по формуле и затем уточняем по таблице размеров зубьев:
где А – припуск на протягивание;
А = D – DЗ = 26 – 25 = 1 мм;
Число калибрующих зубьев зависит от типа протяжки. В данном конкрет- ном случае принимаем Zк = 6.
Длину протяжки от торца хвостовика до первого зуба принимают в зависимости от размеров патрона толщины опорной плиты приспособления для закрепления заготовки зазора между ними длины заготовки других элементов:
где – длина входа хвостовика в патрон зависящая от конструкции патрона (принимаем мм);
– зазор между патроном и стенкой опорной плиты станка равный 5 20 мм (принимаем мм);
– толщина стенки опорной плиты протяжного станка (принимаем мм);
– высота выступающей части планшайбы (принимаем мм);
– длина направляющей (с учётом зазора ) мм.
Длину хвостовика надо проверить графически во время вычерчивания рабочего чертежа протяжки. Затем длину следует проверить с учётом длины протягиваемой заготовки . Таким образом принимаем мм.
Выбираем конструктивные размеры хвостовой части протяжки. По ГОСТ 4044-80 принимаем хвостовик типа 3 с предохранением от вращения с наклонной опорной поверхностью: ; ; ;
с = 05 мм; мм; мм; мм; мм; мм; мм;
; диаметр передней направляющей принимаем равным диаметру предварительного отверстия заготовки с предельным отклонением по е8:
; длину переходного конуса конструктивно принимаем мм; длину передней направляющей до первого зуба – мм. Таким образом полная длина хвостовика мм.
Диаметр задней направляющей протяжки должен быть равен диаметру протянутого отверстия с предельным отклонением f7.
Определяем общую длину протяжки:
– длина режущих зубьев;
– длина зачищающих зубьев;
– длина калибрующих зубьев;
– длина задней направляющей (принимаем в зависимости от диаметра задней направляющей DИ) равна наименьшему диаметру протянутого отверстия DИ = = Dmin выполненного с полем допуска f7 т.е. мм.
Общая длина протяжки
Если общая длина протяжки превышает наибольшую длину хода станка то делают комплект протяжек. Общее число режущих зубьев делят на принятое число рабочих ходов. Диаметр первого режущего зуба протяжки данного прохода принимают равным диаметру калибрующих зубьев протяжки предыдущего прохода.
Максимально допустимая главная составляющая силы резания
Поправочные коэффициенты на изменённые условия резания: (для γ = = 15º); (при применении смазочно-охлаждающей жидкости); (для зубьев протяжки со стружкоразделтельными канавками); тогда сила резания
Полученная сила не превышает тяговую силу станка приведённую в его паспортных данных следовательно обработка возможна.
Проверяем конструкцию протяжки на прочность.
Рассчитаем конструкцию на разрыв во впадине первого зуба
где F – площадь опасного сечения во впадине первого зуба определяем по формуле
– напряжение в опасном сечении (если площадь опасного сечения хвостовика Fx F то расчёт надо вести по Fx)
Напряжение в опасном сечении не должно превышать допустимого напряжения.
Приведём аналогичный расчёт для сечения хвостовика (D1=18 мм):
Полученное напряжение также допустимо для хвостовика из легированной стали 40Х.
Рассчитаем хвостовик на смятие
F1 – опорная площадь замка;
Допустимое напряжение при смятии не должно превышать 600 МПа что выполняется. Для данных условий работы режущих часть протяжки изготовляют из стали Р18 а хвостовик – из стали 40Х.
Предельные отклонения на основные элементы протяжки и другие технические требования выбираем по ГОСТ 9126-76.
Центровые отверстия выполняются по ГОСТ 14034-74.
Выполняем рабочий чертёж протяжки с указанием основных технических требований.
Нестандартная сборная протяжка для внутреннего протягивания с выглаживающими твердосплавными элементами: 1 – хвостовик; 2 – режущая часть; 3 – калибрующая часть с боковыми зубьями; 4 – выглаживающая часть содержащая твердосплавные выглаживающие элементы; 5 – клин; 6 – крепёжный винт.
Данная протяжка предназначена для обработки отверстий. Имеет повышенную в 2 – 25 раза работоспособность по сравнению со стандартными протяжками.
9 Разработка алгоритма компьютерного управления автоматизированными операциями обработки детали
9.1 Обоснование программно-информационной модели и программных средств (КОМПАС АВТОПРОЕКТ) для функционального проектирования технологической подготовки производства
Первыми двумя целями автоматизации функционального проектирования технологической подготовки производства являются следующие [12]:
- сокращение трудоемкости технологической подготовки производства и как следствие сокращение числа технологов;
- сокращение сроков технологической подготовки производства.
Третьей целью автоматизации функционального проектирования технологической подготовки производства является повышение качества разрабатываемых технологических процессов.
С автоматизацией проектирования при технологической подготовке производства объекта связаны три основные задачи:
- проектирование технологических процессов (КОМПАС-АВТОПРОЕКТ);
- проектирование технологической оснастки (КОМПАС-3D);
- проектирование управляющих технологических программ для оборудования с ЧПУ (ГеММа-3D).
Принцип накопления технологических знаний реализованный во многих современных системах автоматизированного проектирования технологических процессов (САПР ТП) позволяет разрабатывать качественные технологические процессы. Знания опытных технологов накапливаемые в САПР ТП сами технологические процессы разработанные ими которые могут быть взяты за основу при разработке новых технологических процессов позволяют повысить общий уровень технологической подготовки производства.
При ручном проектировании технолог сравнивает в уме ряд вариантов разрабатываемого технологического процесса (состав и содержание операций варианты станков инструментов и т.д.) и интуитивно выбирает лучшие на его взгляд решения. Подробного экономического обоснования не производится за неимением времени. Применение ЭВМ на базе соответствующих математических моделей позволяет находить оптимальные технологические решения.
Кроме этого с применением САПР практически исключаются «человеческие» ошибки. Если компьютер работает на основе качественного программного обеспечения технически исправен то при вводе одинаковых входных данных любое количество раз выдаются правильные результаты.
9.2 Проектирование операционной технологии с разработкой управляющих программ для станков с программным управлением в САПР ТП
Управляющая программа к токарной операции 090 станок 16А20 (NC210):
N085 G2 X 120.765 Z-0.3 R0.6 F.1
N100 G2 X1181 Z-3.3 R0.3
G95 – по умолчанию (G80 G29 G90 G71 G17 G97).
G – быстрое позиционирование;
G1 – линейная интерполяция;
G2 – интерполяций круговая по часовой стрелке;
G79 – программирование относительно нуля станка;
M01 – условная остановка программы;
M3 – вращение шпинделя по часовой стрелке;
M4 – вращение шпинделя против часовой стрелки;
M5 – остановка вращения шпинделя;
M6 – замена инструмента;
M8 – включение основного охлаждения;
М9 – выключение охлаждения;
М30 – конец программ и возврат к первому кадру.
G95 – скорость подачи осей в ммоб;
G80 – отмена постоянных циклов;
G29 – позиционирование от точки к точке;
G90 – абсолютное программирование;
G71 – программирование в миллиметрах;
G17 – выбирает плоскость интерполяции определённую конфигурируемыми осями 1 и 2;
G97 – скорость вращения шпинделя в оборотах мм.
10 Технологическое проектирование участка механического цеха
10.1 Расчёт количества технологического оборудования
Расчетное количество станков Срi по i-ой группе оборудования определяется по формуле[9]:
где t – штучное время обработки детали на
Nj – годовая программа выпуска деталей шт;
F– годовой эффективный фонд времени работы станка
n – количество наименований деталей обрабатываемых на i-ой группе оборудования.
Годовой эффективный фонд времени определяется по формуле:
где D – число рабочих дней в году;
m– число смен в сутки;
t– продолжительность рабочей смены ч;
kп – плановые потери времени на ремонт %
По формуле находим годовой эффективный фонд рабочего времени работы одного станка первой группы:
Fэ = 251 · 1· 8 · (1 – ) = 19076 ч.
)Расчетное количество токарно-винторезных станков 1К62:
Принимаем количество токарно-винторезных станков 1К62 С = 3
Средний коэффициент загрузки оборудования определяем по формуле:
где C- принятое количество станков шт.
Подставив полученные данные в формулу (2.50) получим:
) Расчетное количество универсально-фрезерных станков СФ 676:
Принимаем количество универсально-фрезерных станков СФ 676 с учётом условной дозагрузки С = 1
Средний коэффициент загрузки оборудования равен:
) Расчетное количество вертикально-сверлильных станков 2Н118:
Принимаем количество вертикально-сверлильных станков 2Н118 с учётом условной дозагрузки С=1
) Расчетное количество вертикально-фрезерных консольных станков 6Р11:
Принимаем количество вертикально-фрезерных консольных станков 6Р11 с учётом условной дозагрузки С = 1
Средний коэффициент загрузки оборудования равен:
) Расчетное количество фрезерных широкоуниверсальных станков 6М12П:
Принимаем количество фрезерных широкоуниверсальных станков 6М12П с учётом условной дозагрузки С = 1
) Расчетное количество вертикально-сверлильных станков СС49:
Принимаем количество вертикально-сверлильных станков СС49 с учётом условной дозагрузки С = 1
) Расчетное количество горизонтально-протяжных полуавтоматов 7Б56:
Принимаем количество горизонтально-протяжных полуавтоматов 7Б56 с учётом условной дозагрузки С = 1
Средний коэффициент загрузки оборудования по участку в целом K определяется по формуле: K = (2.51)
где m - число групп оборудования на участке.
Подставив значения в формулу получим коэффициент загрузки оборудования
10.2 Расчёт численности персонала
В серийном производстве численность основных рабочих для выполнения нормируемых работ определяется по формуле[9]:
где t – трудоемкость
N – годовой объем выпуска изделий шт.;
ФРД – действительный годовой фонд времени работы рабочего ч;
Квн – коэффициент выполнения норм на i-ой операции.
Действительный годовой фонд времени работы рабочего определим по формуле: ФРД = D·t· (2.53)
где α – коэффициент учитывающий потери рабочего времени. Подставив данные в формулу получим:
) Определим число токарей:
Принимаем число токарей пятого разряда: 3 человека.
) Определим число фрезеровщиков (станки мод. 676; 6Р11; 6М12П):
Принимаем число фрезеровщиков: 1 человек.
) Определим число сверловщиков (станки мод. 2Н118; СС49):
Принимаем число сверловщиков: 1 человек.
) Определим число рабочих на протяжных полуавтоматах 7Б56:
Принимаем число рабочих на протяжном полуавтомате 7Б56: 1 человек.
Принятое количество основных рабочих устанавливается путем соответствующего округления полученного значения до целого при этом допускается перегрузка не более 20 %.
Таблица 2.3 – Расчет потребного количества основных рабочих
Общая трудоемкость работ выполненных за год нормо-час
Определение численности вспомогательных рабочих производится по нормам обслуживания. На основании этих норм составляется ведомость.
Таблица 2.4 – Ведомость вспомогательных рабочих
Кол-во ед. оборуд. в смену
Слесари по рем. оснастки
Кол-во основных рабочих
Водители электрокар и
Количество тонн груза в
Слесари по межремонтному обслуживанию оборуд.
Распределители работ
% от числа основных раб.
Уборщики производственных площадей
Убираемая площадь м2
При расчете численности ИТР следует пользоваться следующими примерными нормативами. В подчинении мастера должно быть 20÷25 рабочих; старший мастер назначается для руководства не менее чем для двух мастеров (участка или сменными). Т.о. на 6 основных рабочих принимаем 025 ставки мастера и 0125 – старшего мастера.
10.3 Определение производственной площади участка
Производственная площадь участка занимаемая непосредственно оборудованием и рабочими местами определяется исходя из удельной площади приходящейся на один станок и числа основных станков.
Удельная площадь на один мелкий станок – 10÷12 средний – 15÷25 крупный – 30÷45 м2. Хотя эта классификация является довольно условной.
К мелким относятся станки с габаритами до 1800×800 мм средним – до 4000×2000 мм к крупным – до 8000×4000 мм.
Из 8 станков образующих участок механической обработки корпусов 6 станков средних размеров и 2 – мелких (по табл. 2.2).
Производственная площадь участка Sпр рассчитывается исходя из удельных норм площади на один металлорежущий станок[9].
где Sуд – средняя величина удельной площади на один станок м2
К – количество станков.
Sпр = 7·20 + 2·10 = 160 м2
С учетом проездов проходов стеллажей и конвейера по уборке стружки площадь станков и вспомогательного оборудования составит 192 м2.
10.4 Выбор системы складирования
В серийном производстве цеховой склад заготовок и полуфабрикатов размещают в начале пролётов в соответствии с обрабатываемыми деталями. Хранение штучных грузов (отливок поковок деталей и т.д.) должно производиться в унифицированной таре которая позволяет использовать механизированные погрузочно-разгрузочные транспортирующие устройства и многоярусное хранение в штабелях или на стеллажах. Запас материалов и заготовок в цеховом складе должен быть невелик так как назначением его является только обеспечивать регулярное снабжением цеха (участка) материалами. При расчете площади складов заготовок исходят из необходимости запаса и грузонапряженности пола[9]:
где Р – площадь складов заготовок м2;
Q – масса заготовок обрабатываемых в цехе в течение года т;
Т – запас заготовок дни;
f – среднее число рабочих дней в году;
q – средняя грузонапряженность склада тм2;
кр – коэффициент использования площади склада представляющий отношение полезной площади склада к его общей площади и учитывающий проходы и проезды (кр = 04÷05). Q = 500×55 = 2750 кг = 275 т.
P = 275×10253×25×04 01 м².
Склад готовых деталей предназначен для хранения деталей перед отправкой на сборку. Склад готовых деталей и комплектовочный склад размещают в конце пролетов механического цеха на пути следования деталей на сборку. Грузонапряженность площади пола складов принимается меньшей чем в цеховом складе заготовок так как готовые детали хранятся как правило на стеллажах или специальных подставках столах и таре. Допускаемую грузонапряженность следует принимать равной: при удельном весе материалов более 1÷4 т на 1 м2 для мелких и средних деталей и 15 т на 1 м2 для крупных; при удельном весе материалов до 4 т – соответственно 04 и 06 на 1 м2. Q = 500×27= 1350 т.
P = 135×10253×25×04 005 м².
Содержание.doc
Проектно-конструкторская часть
1 Назначение и краткое техническое описание детали
2 Разработка твердотельной 3D модели детали
3 Разработка параметрической 2D модели объекта для проектирования технологичной конструкции детали
Производственно-технологическая часть
1 Установление типа производства
2 Анализ базового технологического процесса
3 Выбор типа заготовки
4 Выбор технологических базовых поверхностей и оценка точности базирования
5 Разработка технологического процесса обработки детали в САПР ТП
5.1 Использование информационных технологий и технических средств при разработке технологического процесса
5.2 Разработка технологического процесса изготовления корпуса средствами САПР КОМПАС-Автопроект 9.3
6 Выбор моделей оборудования
7 Выбор конструкции и расчёт станочного приспособления для автоматизированного оборудования
7.1 Описание приспособления
7.2 Силовой расчёт приспособления
7.3 Точностной расчёт станочного приспособления
8 Проектирование и расчёт режущего инструмента
9 Разработка алгоритма компьютерного управления автоматизированными операциями обработки детали
9.1 Обоснование программно-информационной модели и программных средств (КОМПАС АВТОПРОЕКТ и др.) для функционального проектирования технологической подготовки производства
9.2 Проектирование операционной технологии с разработкой управляющих программ для станков с программным управлением в САПР ТП
10 Технологическое проектирование участка механического цеха
10.1 Расчёт количества технологического оборудования
10.2 Расчёт численности персонала
10.3 Определение производственной площади участка
10.4 Выбор системы складирования
Безопасность и экологичность
1 Расчёт общего освещения на проектируемом участке
Экономическая и организационно-управленческая часть
1 Экономическое обоснование проекта участка
1.1 Определение потребности в инвестициях
1.2 Организация оплаты труда на участке
1.3 Расчет текущих затрат
1.4 Расчет себестоимости продукции
2 Расчет технико-экономических показателей проектируемого участка
3 Расчет показателей экономической эффективности проекта участка
4 Особенности машиностроительных предприятий
Приложение А. Графическая часть проекта
Твердотельная 3D модель детали
Результаты расчёта САЕ
Результаты разработки ТП средствами САПР КОМПАС-Автопроект 9.3
Станочное приспособление
Результаты расчёта технологических размерных цепей
Планировка участка с автоматизированным оборудованием
Показатели экономической эффективности проектных решений
Приложение Б. Спецификации к графической части проекта
Приложение В. Комплект документов технологического процесса обработки резанием
Реферат, задание.doc
ВЫСШЕГО ПРОФЕССИОНАЛЬНОГО ОБРАЗОВАНИЯ
«ВОРОНЕЖСКИЙ ГОСУДАРСТВЕННЫЙ ТЕХНИЧЕСКИЙ УНИВЕРСИТЕТ»
(фамилия имя отчество)
на выпускную квалификационную работу
Тема дипломного проекта: Разработка технологии и средств технологического оснащения для изготовления корпуса .
утверждена распоряжением по факультету № от « » 2008 г.
Технические условия: согласно техническому заданию режим работы участка – односменный программа выпуска корпуса – 500 штук в год . .
Содержание (разделы графические работы расчеты и проч.)
Графическая часть: 1) чертёж заготовки; 2) рабочий чертёж детали; 3) твердотельная модель; 4) чертёж приспособления; 56) технологические наладки обработки детали; 7) режущий инструмент; 8) технико-экономические показатели спроектированного участка; 9) план участка; 10) результаты расчёта САЕ; 11) результаты расчёта технологических размерных цепей.
Расчётно-пояснительная записка: 1) проектно-конструкторская часть; 2) производственно-технологическая часть; 3) экология и техника безопасности; 4) экономическая и организационно-управленческая часть.
План выполнения дипломного проекта
с « » 2008 г. по « » 2008г.
Название элементов проектной работы
Подпись руководителя консультанта
Проектно-конструкторская часть
Производственно-технологическая часть
Экология и техника безопасности
Экономическая и организационно-управленческая часть
Комплект документов технологического процесса
Руководитель дипломного проекта
(подпись) (Фамилия имя отчество)
Дипломный проект закончен
(подпись дипломника)
Пояснительная записка и все материалы просмотрены
(подпись) (Инициалы фамилия)
Пояснительная записка: 20 таблиц 17 источников 3 приложения.
КОРПУС ТЕХНОЛОГИЯ ТЕХНОЛОГИЧЕСКОЕ ОСНАЩЕНИЕ РЕЖИМЫ ОБРАБОТКИ РАСЧЕТ ПРИСПОСОБЛЕНИЯ ЭКОНОМИЧЕСКАЯ ЭФФЕКТИВНОСТЬ РАЗМЕРНАЯ ЦЕПЬ ПЛАНИРОВКА УЧАСТКА.
Объект исследования или разработки – деталь типа «Корпус»
Цель работы – разработка технологии изготовления корпуса; проектирование эффективной операционной технологии с использованием САПР; численное обоснование метода изготовления заготовки; формирование состава переходов и операций; расчёт станочного приспособления; расчёт технологических размерных цепей; проектирование производственного участка; расчёт экономических показателей участка.
Полученные результаты и их новизна – в данном дипломном проекте были решены основные задачи поставленные для достижения повышения производительности труда в условиях среднесерийного производства. Используя основные направления в современной технологии машиностроения был выбран наиболее рациональный метод получения заготовки что дало возможность значительно снизить трудоемкость обработки детали на металлорежущих станках а также сократить расход металла. Применение станков с числовым программным управлением приспособлений с быстродействующими зажимами позволило повысить производительность труда. Снижение трудоемкости перемещения детали между рабочими местами было учтено при разработке участка механической обработки что позволило достигнуть лучших технико-экономических показателей по сравнению с существующими на заводе.
Экономическая эффективность или значимость работы – экономический эффект от производства продукции с применением разработанного в дипломном проекте технологического процесса за расчётный период составит 401118 тысяч рублей.
Введение.doc
Для достижения высоких эксплуатационных и технико-экономических характеристик изделий необходимо совершенствовать технологию.
Целью выпускной квалификационной работы является разработка технологии и средств технологического оснащения программными средствами КОМПАС-3D КОМПАС-АВТОПРОЕКТ.
На первом этапе производится разработка моделей: параметрической и твердотельной средствами КОМПАС-3D .
На втором этапе устанавливается тип производства анализируется базовый и разрабатывается новый технологический процесс. На данном этапе средствами КОМПАС-АВТОПРОЕКТ осуществляется выбор: технологических баз моделей оборудования метода получения заготовки; подбор режущего инструмента. Выбор конструкции и расчёт станочного приспособления.
На третьем этапе проектируется участок механического цеха проводится расчёт: относительных и абсолютных показателей спроектированного предметно-замкнутого участка в том числе и экономической эффективности проекта.
речь.doc
Целью дипломной работы является: Повысить качество и технико-экономические показатели технологического процесса изготовления корпуса.
В процессе работы над проектом были выполнены следующие задачи:
- расчет силовых и деформационных параметров корпуса в процессе его изготовления с использованием САЕ.
- выбор и обоснование метода изготовления заготовки
- разработка технологии изготовления корпуса в САПР ТП
- разработка средств технологического оснащения
- планировка участка механического цеха для изготовления корпуса
- расчет техника - экономических показателей спроектированного участка.
Корпус – деталь сложной формы но она средненагруженная и в условиях пластической деформации обладает повышенной прочностью и ударной вязкостью.
Детали авиационной техники эксплуатируются в условиях резких перепадов температур и даже в агрессивных средах. Корпус наряду с другими деталями авиационной техники не должен охрупчиваться при низких температурах и его можно использовать в условиях криогенных температур.
Корпус имеет в своей конструкции две сопрягающиеся внешние цилиндрические поверхности переходящие плавно в шаровую поверхность. На обеих цилиндрических поверхностях имеется фланец предназначенный в первом случае для крепления корпуса а во втором представляет собой рёбра жёсткости сложной округлой формы. Корпус имеет сложную по конструкции внутреннюю полость сферической формы с выступающим элементом трубчатой формы.
Материал корпуса входа – алюминиевый сплав АК6 по ГОСТ 4784-97.
Также была выполнена разработка твердотельной ЗD модели детали в программе КОМПАС-ЗD V9 компании АСКОН
Трехмерная параметрическая модель детали создается с целью передачи геометрии в расчетные пакеты и в пакеты разработки управляющих программ для оборудования с ЧПУ а также расчета их геометрических и массо-центровочных характеристик. На основе ЗD модели создаются параметрические 2D модели и формируется рабочий чертеж детали.
В программе СОSМОSХрrеss был сделан расчет силовых и деформационных нагрузок для данной детали. При расчетах учитывались свойства материала детали и нагрузки действующие на нее во время эксплуатации.
Результаты расчетов представлены на рисунке.
В производственно-технологической части сделан выбор оборудования и разработан технологический процесс изготовления детали корпус. Определён тип производства серийный.
Технико-экономическое обоснование выбора заготовки для обрабатываемой детали производят по нескольким направлениям: металлоемкости трудоемкости и себестоимости учитывая при этом конкретные производственные условия. Технико-экономическое обоснование ведется по двум или нескольким выбранным вариантам.
В процессе разработки было произведено сравнение двух наиболее рациональных способов изготовления заготовки корпуса – литьё в кокиль и штамповку на прессе.
Заготовки при литье в кокиль имеют больший допуск чем при горячей объёмной штамповке. Отливка имеет литниковую систему выпары приливы и т.д. в то время как штамповка практически не имеет отходов (они появляются при штамповке в открытых штампах) кроме штампованных уклонов.
Отсюда следует вывод что:
а) отходов будет больше при литье;
б) затраты на механическую обработку будут выше при литье.
Наиболее рациональным способом изготовления заготовки «Корпус» является штамповка.
Разработка технологического процесса обработки детали проведена в САПР ТП «КОМПАС-АВТОПРОЕКТ». Эта система автоматизированного проектирования позволяет решать задачи ведения конструкторско-технологических спецификаций изделий организации хранения разработанных технологий нормирования расхода материалов регистрации документов анализа архивных технологий автоматической замены информации в архивах а также часть реализует функции проектирования технологических процессов различных видов производств систематизирует нормативно-справочную информацию ведет технологические расчеты формирует комплекты документации.
Основные операции выполненные в этой программе при разработке технологического процесса детали «корпус» представлены на слайдах 7-8.
Выбор оборудования осуществлен при помощи базы данных «Станки» из САПР КОМПАС-Автопроект 9.3.
Произведён расчёт технологической размерной цепи методом максимума-минимума с помощью прикладной библиотекой системы КОМПАС
Метод учитывает только предельные отклонения звеньев размеров цепи и самые неблагоприятные их сочетания обеспечивает заданную точность сборки без подгонки деталей то есть полную взаимозаменяемость.
Приспособление служит для фрезерования плоскости операции №90.
Обрабатываемая деталь базируется по цилиндрическому отверстию диаметром 70 мм торцом выступа в четырёх точках и боковой стороне.
Установка корпуса производится на четыре опоры 7 и палец 5 а правильная ориентация для фрезеровки обеспечивается посредством подвижного фиксатора 1. Перемещение фиксатора размещённого на стойке выполняется с помощью винтовой пары.
Закрепление корпуса осуществляется лапками двух рычагов 8. При запуске пневматического цилиндра ползун 14 начинает своё перемещение в горизонтальном направлении увлекая за собой ползун и передавая усилие шатуну 11 переносит его на рычаг который непосредственно осуществляет зажим заготовки для фрезерования горизонтальной поверхности.
Все зажимные и установочные элементы приспособления смонтированы на плите 6. Приспособление устанавливается на столе фрезерного станка в пазы по двум фиксаторам 12 соединённым с плитой посредством винтов 13. Крепление приспособления на стол станка осуществляется болтами.
Использование пневмоприводов двухстороннего действия позволяет сократить расход воздуха на 30-40 %. Поршневой привод крепится на столе станка. Шток пневмопривода связывается соответствующим образом с зажимным устройством приспособления.
Рычажное зажимное устройство имеет ряд преимуществ: простая конструкция; значительный выигрыш в силе и в перемещениях; постоянство силы закрепления которая не зависит от размеров заготовки; возможность закрепить заготовку в труднодоступном месте; технологичность; удобство в эксплуатации; надёжность.
Конструкция разработана для серийного производства.
Пневматические приводы приспособлений отличаются быстротой действия относительной простотой конструкции лёгкостью и простотой управления надёжностью и стабильностью в работе. По быстроте действия пневмоприводы значительно превосходят не только ручные но и многие механизированные приводы. К преимуществам пневмопривода следует отнести то что его работоспособность не зависит от колебаний температуры окружающей среды.
Нестандартная сборная протяжка для внутреннего протягивания с выглаживающими твердосплавными элементами: 1 – хвостовик; 2 – режущая часть; 3 – калибрующая часть с боковыми зубьями; 4 – выглаживающая часть содержащая твердосплавные выглаживающие элементы; 5 – клин; 6 – крепёжный винт.
Режущих часть протяжки изготовляют из стали Р18 а хвостовик – из стали 40Х.
Данная протяжка предназначена для обработки отверстий. Имеет повышенную работоспособность по сравнению со стандартными протяжками.
Перепланировка механического участка была выполнена на основании программы выпуска в зависимости от выбранного типа производства.
При планировании участка механического цеха металлорежущие станки были расположены так чтобы была обеспечена прямоточность и последовательность прохождения материалов заготовок и изделий по стадиям обработки. При планировке оборудования на участке были соблюдены нормы расстояний между оборудованием и элементами здания ширина проходов и проездов. Помимо этого в цехе предусмотрены площадки для складирования и хранения заготовок.
Были рассчитаны технико-экономические показатели участка по изготовлению детали «корпус». Экономический эффект от функционирования участка на котором детали изготавливаются по вновь спроектированной технологии рассчитывается на конкретный период. Исходя из темпов обновления промышленной продукции в состав которой входит изготавливаемая деталь принимаем этот период равным десяти годам. В результате расчетов получены следующие экономические показатели: снижение себестоимости изготовления детали 93% снижение трудоёмкости изготовления детали 98%
Доклад закончен спасибо за внимание.
Не следует основывать проектные решения исключительно на данных представленных в этом отчете. Используйте эту информацию совместно с экспериментальными данными и практическим опытом. Испытания в условиях эксплуатации обязательны для утверждения окончательного проекта. COSMOSXpress помогает уменьшить время продвижения на рынок путем снижения но не упразднения испытаний в условиях эксплуатации.
Протяжка режущих зубьев-12 калибрующих-6.
Термическая 65 Анодномеханическая.
Анодно-механическая обработка основана на снятии слоя образующегося в электролите на поверхности металлической детали включенной в качестве анода
Рис. 1. Анодно-механическая обработка
В качестве электролита применяется раствор жидкого стекла или глины. С помощью анодно-механической обработки можно получить поверхность чистотой от 2 до 9 классов чистоты. При использовании абразивных брусков в качестве инструмента снимающего пленку анодного растворения можно получить поверхность чистотой до 10-го класса. Качество поверхности зависит главным образом от напряжения тока и скорости перемещения инструмента относительно поверхности детали. Анодно-механическую обработку можно применять в ремонтных предприятиях для обработки закаленных деталей деталей наплавленных чугуном и твердыми сплавами. С помощью анодно-механической обработки можно выполнять резку металлов заточку инструментов обдирку шлифовку и доводку деталей.
3D.cdw
оснащения для изготовления корпуса
Твердотельная модель
Корпус.cdw

оснащения для изготовления корпуса
Неуказанные радиусы 3 5 мм.
Фаски на резьбовых отверстиях 1
Неуказанные предельные отклонения размеров отверстий - по
Допускаемое притупление кромки пересечения поверхности дна и
сферы R5 max мм. с обеспечением плавногосопряжения.
Острые кромки притупить
* Размеры для справок.
3D5.cdw
оснащения для изготовления детали "Корпус
Твердотельная модель
ЛИСТ1.cdw

проходной прямой ГОСТ 18869-73; расточной резец ГОСТ 18882-73.
Зенкер насадной ГОСТ 2255-71; Резец расточной
ГОСТ 18882-73; Проходной резец ГОСТ 18869-73.
А.Установить деталь и после
выдерживая размер (3).
Точить поверхность (1).
Расточить поверхность (2).
Зенкеровать поверхность (2).
Расточить поверхность (3)
выдерживая конус (1) и поверхность (2).
Притупить острые кромки R0
Расточить поверхность (6).
Расточить поверхность (4).
Расточить поверхность (5).
Расточить поверхность (1).
Точить поверхность (3)
Нутромер индикаторный НИ 868-82;
Штангенциркуль ШЩ-I-250-0
Резец подрезной отогнутый ГОСТ 18871-73; Резец расточной
ГОСТ 18882-73; Проходной резец с пластинкой Р18 ГОСТ 18869-73.
Технологический процесс изготовления корпуса
Станок токарно-винторезный 1К62
Патрон трехкулачковый; наладка; угольник
* Размер для справок
ЛИСТ2.cdw

Протяжка нестандартного профиля для
внутреннего протягивания
А.Установить деталь и после
Сверлить 8 отв. согласно эскизу.
Зенкеровать 8 отв. согласно
Развернуть 8 отв. согласно
Фрезеровать поверхность П
Зачистить заусенцы после
Установить протяжку через
отверстие (1) и закрепить её в
Протянуть поверхность (1)
Станок вертикально-сверлильный 2Н118
Нутромер индикаторный НИ 868-82; штангенциркуль ШЦ-I-250-0
Станок вертикально-фрезерный 6В11
Приспособление зажимное шарнирно-рычажное
Фреза торцовая насадная ГОСТ 9304-69
Штангенциркуль ШЩ-I-250-0
Станок горизонтально-протяжной 7Б56
Установочное приспособление; оправка
* Размеры выполнить инструментом
Информационный лист Автопроект.cdw

Выбор режущего инструмента
из справочника КОМПАС-Автопроект
Справочные базы данных
Формирование перехода
Спецификация.spw

технологического оснащения для изготовления корпуса
Станок ток.-винт. 1К62
Станок токарный NC210
Станок вертик.-сверл. 49Н
Станок вертик.-фрез. 6М12П
Полуавтомат гориз.-протяж. 7Б56
Контейнер для стружки
Станок фрезерный 676
Станок вертик.-сверл. 2Н118
Станок вертик.-фрез. 6В11
План участка.cdw

технологического оснащения для изготовления корпуса
Технико-экономические показатели участка.cdw

по изготовлению корпуса
Наименование показателя Величина
Абсолютные показатели:
а) годовой выпуск продукции
- в натуральном выражении
- в стоимостном выражении
б) количество единиц технологического оборудования
в) общая стоимость основных производственных
г) Производственная площадь участка
д) Численность основных рабочих участка
е) фонд заработной платы основных рабочих
Относительные показатели:
а) Выпуск продукции на одного производственного
рабочего в денежном выражении
( по цеховой себестоимости )
б) выпуск продукции на кв.м. производственной
в) фондоотдача ( по цеховой себестоимости )
г) средняя загрузка оборудования
д) фондовооружённость труда
е) уровень механизации труда
Показатели экономической эффективности проекта
а) интегральный экономический эффект
б) внутренняя норма доходности ( внутренний
коэффициент эффективности )
в) срок окупаемости капитальных вложений
г) снижение себестоимости изготовления детали
д) снижение трудоёмкости изготовления детали
е) условное высвобождение численности рабочих
Заготовка.cdw

оснащения для изготовления корпуса
Неуказанные радиусы 3 5 мм.
Допускаемое смещение штампов - 0
Допускаемый остаток от облоя - 0
Допускаемое притупление кромки пересечения поверхности дна и
сферы радиусом менее 5 мм с обеспечением плавного сопряжения.
Требования к штамповке по ОСТ 190073 - 85.
Наличие крупнокристаллического ободка не допускается.
* Размеры для справок.
Спецификация.spw

оснащения для изготовления корпуса
Протяжка.cdw

сталь Р18 или другой марки по ГОСТ 19265-73.
Обрабатываемый материал: алюминий и его сплавы.
Протяжка должна удовлетворять техническим требованиям
Твердость: режущей и задней направляющей части 63 66 HRC
передней направляющей части 61 66 HRC
хвостовой части 43 51 HRC
Материал хвостовой части - сталь 40Х по ГОСТ 4543-71.
Разработка технологии и средств технологического
оснащения для изготовления корпуса
Профиль выглаживающей части
Профиль режущей части
Тема.cdw

оснащения для изготовления корпуса
Цель: Повысить качество и технико-экономические
показатели технологического процесса изготовления корпуса.
- расчет силовых и деформационных параметров корпуса в
процессе его изготовления с использованием
- выбор и обоснование метода изготовления заготовки;
- разработка технологии изготовления корпуса в САПР ТП;
- разработка средств технологического оснащения;
- планировка участка механического цеха для изготовления
- расчет технико - экономических показателей
спроектированного участка.
Спецификация.spw

Разработка технологии и средств технологического
оснащения для изготовления корпуса
Винт М12х32 ГОСТ 1491-80
Опора 7034-0278 ГОСТ 13440-68
Штифт 8n6х25 ГОСТ 3128-70
Шпонка 7031-0607 ГОСТ 14737-69
Винт М6х25 ГОСТ 1491-80
Болт М8х12 ГОСТ 7805-70
Фрезерное приспособление.cdw

Давление воздуха в пневмосети
Технические требования.
Трущиеся поверхности смазать смазкой ЦИАТИМ.
Неперпендикулярность направляющих поверхностей не более 0
Цилиндр пневмопривода перед работой проверить на герметичность.
* Размеры для справок.
Разработка технологии и средств технологического
оснащения для изготовления корпуса
для установа корпуса
Информационный лист CAE.cdw

детали в процессе ее изготовления с использованием CAE
Эпюра 1 - Статическое узловое напряжение
Эпюра 2 - Статическое перемещение
Эпюра 3 - Деформированная форма
Эпюра 4 - Проверка проектирования
Результаты расчета технологических размерных цепей.cdw

Формирование размерной цепи
3D.cdw
оснащения для изготовления корпуса
Твердотельная модель
Корпус.cdw

оснащения для изготовления корпуса
Неуказанные радиусы 3 5 мм.
Фаски на резьбовых отверстиях 1
Неуказанные предельные отклонения размеров отверстий - по
Допускаемое притупление кромки пересечения поверхности дна и
сферы R5 max мм. с обеспечением плавногосопряжения.
Острые кромки притупить
* Размеры для справок.
Заготовка.cdw

оснащения для изготовления корпуса
Неуказанные радиусы 3 5 мм.
Допускаемое смещение штампов - 0
Допускаемый остаток от облоя - 0
Допускаемое притупление кромки пересечения поверхности дна и
сферы радиусом менее 5 мм с обеспечением плавного сопряжения.
Требования к штамповке по ОСТ 190073 - 85.
Наличие крупнокристаллического ободка не допускается.
* Размеры для справок.
Протяжка.cdw

сталь Р18 или другой марки по ГОСТ 19265-73.
Обрабатываемый материал: алюминий и его сплавы.
Протяжка должна удовлетворять техническим требованиям
Твердость: режущей и задней направляющей части 63 66 HRC
передней направляющей части 61 66 HRC
хвостовой части 43 51 HRC
Материал хвостовой части - сталь 40Х по ГОСТ 4543-71.
Разработка технологии и средств технологического
оснащения для изготовления корпуса
Профиль выглаживающей части
Профиль режущей части
План участка.cdw

технологического оснащения для изготовления корпуса
Фрезерное приспособление.cdw

Давление воздуха в пневмосети
Технические требования.
Трущиеся поверхности смазать смазкой ЦИАТИМ.
Неперпендикулярность направляющих поверхностей не более 0
Цилиндр пневмопривода перед работой проверить на герметичность.
* Размеры для справок.
Разработка технологии и средств технологического
оснащения для изготовления корпуса
для установа корпуса
125.frw

070.frw

090.frw

195.frw

085.frw

075.frw

105.frw

Документ Microsoft Word.doc
Графическая часть проекта
Комплект документов технологического процесса обработки резанием
Рекомендуемые чертежи
- 24.01.2023
- 24.01.2023
- 24.01.2023