Проектирование ТП на изготовление детали и средств технологического оснащения




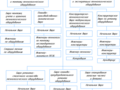
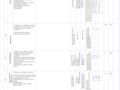
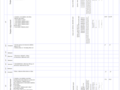
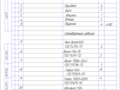
- Добавлен: 24.01.2023
- Размер: 2 MB
- Закачек: 1
Описание
Состав проекта
![]() |
![]() |
![]() ![]() ![]() |
![]() |
![]() |
![]() ![]() ![]() ![]() |
![]() ![]() ![]() ![]() |
![]() ![]() ![]() ![]() |
![]() ![]() ![]() ![]() |
![]() ![]() ![]() |
![]() |
![]() |
![]() ![]() ![]() ![]() |
![]() |
![]() ![]() ![]() ![]() |
![]() ![]() ![]() ![]() |
![]() ![]() ![]() ![]() |
![]() |
![]() |
![]() |
![]() |
![]() |
![]() ![]() ![]() ![]() |
![]() ![]() ![]() ![]() |
![]() |
![]() ![]() ![]() ![]() |
![]() ![]() ![]() ![]() |
![]() ![]() ![]() ![]() |
![]() ![]() ![]() ![]() |
![]() |
![]() |
![]() ![]() ![]() ![]() |
![]() |
![]() ![]() ![]() ![]() |
![]() ![]() ![]() ![]() |
![]() |
![]() |
![]() |
![]() |
Дополнительная информация
пояснительная записка.doc
2Характеристика материала заготовки
3Выбор метода получения заготовки
Технологическая часть
1Обоснование маршрутной технологии изготовления детали
3Выбор технологической оснастки
5Расчет режимов резания
6Обоснование и разработка технологического процесса (технологический процесс смотреть в приложении)
Конструкторская часть
1Выбор способа базирования детали
2Расчет коэффициента надежности закрепления детали
3Расчет потребных сил зажима
4Описание работы приспособления для токарно-карусельных операций
5Описание одного мерительного инструмента или контрольного приспособления
Производственная часть
1Определение потребного количества оборудования
2Определение потребного количества основных рабочих
3Определение потребного количества вспомогательных рабочих инженерно-технических работников и младшего обслуживающего персонала
Организационная часть
1Планирование размещения оборудования и рабочих мест на участке механического цеха
2Организация транспортировки изделий на участке
3Проектирование и организации рабочих мест
4Организация инструментального хозяйства
5Организация технического контроля
6Организация ремонта оборудования на участке
7Разработка мероприятий по охране труда ТБ противопожарной защите
1Определение затрат на основные материалы
2Расчёт фонда заработной платы основных и вспомогательных рабочих
3Расчёт цеховых расходов на силовую электроэнергию сжатый воздух воду
4Расчёт затрат на амортизацию оборудования
5Технико-экономические показатели участка
6Оценка технико-экономической эффективности спроектированного участка
Использованная литература
Сущностью технологии машиностроения является учение о способах и процессах промышленного производства продукции заданного качества и в требуемом количестве. Современное развитие технологии машиностроения представляет собой совокупность взаимосвязанных процессов совершенствования прежде всего методов обработки материалов технологического оборудования обрабатывающего и измерительного инструментов а также теоретических и практических основ процессов обработки. Оно стимулируется усложнением конструкции изделий повышением требований к качеству их изготовления и стремлением снизить себестоимость продукции а также частой сменой объектов производства. Использование многоинструментальных станков с ЧПУ оснащенных средствами механизации и автоматизации позволяет проектировать технологические процессы обработки деталей с укрупненными насыщенными переходами операциями уменьшить трудоемкость их изготовления и существенно сократить время технологической подготовки производства при частой смене номенклатуры выпускаемых изделий.
В современном производстве еще достаточно высока доля технологических процессов не в полной мере удовлетворяющих выше перечисленным требованиям. Поэтому внедрение прогрессивных методов размерной обработки деталей экономически обоснованное применение высокопроизводительного оборудования износостойкого комбинированного режущего инструмента механизированной оснастки и средств автоматизации производственных процессов в механических цехах современных машиностроительных заводов становится весьма актуальным.
Целью настоящего дипломного проектирования является совершенствование операционной технологии изготовления деталей "Корпус превентора кольцевого" и достижение наилучших технико-экономических показателей по сравнению с базовым вариантом заводской технологии.
Для достижения указанной цели необходимо решение целого ряда технологических задач:
Совершенствование операционного технологического процесса за счет концентрации операций с применением специального комбинированного режущего инструмента специальной оснастки и много-инструментальных станков с ЧПУ.
Оснащение металлорежущего оборудования специальными высокоточными установочными и контрольными приспособлениями.
Проведение организационно-технических мероприятий по перепланировке производственного участка предназначенного для выпуска деталей корпусов кольцевых превенторов
Для практической реализации поставленных целей и задач дипломного проектирования целесообразно на основе проведения патентно-информационного поиска выявить новые технические решения в области механической обработки деталей оснастки и металлорежущего инструмента провести их конструкторскую проработку и воспользоваться известными расчётно-аналитическими или экспериментально-статистическими методами расчета и назначения технологических режимов обработки а также провести технико-экономический анализ целесообразности организации специализированного предметного участка в составе механического цеха.
Превентор рисунок 1 состоит из следующих основных сборочных единиц и деталей: корпуса 1; крышки 2; уплотнителя 3; поршня 4; кожуха 5.
Корпус 1 представляет собой стальную деталь с центральным проходным отверстием в которую устанавливаются поршень 4 с уплотнителем 3 и кожух 5. При помощи прямоугольной резьбы корпус 1 соединяется с крышкой 2 и уплотняется прокладкой 6. Для предотвращения самоотвинчивания при проворачивании бурильного инструмента имеются стопорный винт 7. На боковой поверхности корпуса предусмотрены отверстия для подвода жидкости от станции управления и приварены четыре проушины предназначенные для подъема превентора. Фланец корпуса является присоединительным для крепления превентора к превенторному блоку противовыбросового оборудования устья скважины.
Крышка 2 представляет собой стальную деталь с центральным проходным отверстием. В канавки внутренней полости устанавливаются манжеты 8 и 9. Фланец крышки в который ввинчиваются шпильки с гайками является присоединительным для крепления на превенторе агрегатов противовыбросового оборудования скважины.
Уплотнитель 3 представляет собой массивное резиновое кольцо армированное металлическими вставками придающими уплотнителю жесткость и предохраняющими от вытекания резины в процессе эксплуатации.
Поршень 4 имеет ступенчатую форму. На поршне 4 установлен уплотнитель 3. В наружные канавки поршня устанавливаются уплотнительные манжеты 10 и 11.
Корпус 1 крышка 2 и поршень 4 образуют в превенторе две гидравлические камеры: на открывание (А) и на закрывание (Б) превентора. Герметичность камер обеспечивается уплотнительными манжетами 8910111213. Через отверстия в корпусе эти камеры соединены со станцией управления. При нагнетании масла в гидравлическую камеру Б поршень 4 движется вверх и обжимает уплотнитель 3 центральное отверстие которого сжимается обхватывает и уплотняет любую часть колонны труб оказавшуюся в зоне уплотнителя или перекрывает скважину при отсутствии в ней колонны труб при аварийной ситуации.
При нагнетании масла в гидравлическую камеру А закрытого превентора поршень 4 из верхнего положения перемещается вниз вытесняя масло в сливную линию станции управления. Уплотнитель при этом разжимается и принимает первоначальную форму.
Для работы в зимнее время превентор должен быть оснащен камерой обогрева.
Превентор является частью превенторного блока противовыбросового оборудования скважины предназначенного для герметизации устья скважины и выполнения необходимых технологических операций при бурении и капитальном ремонте нефтяных и газовых скважин с целью предупреждения открытых фонтанов и загрязнения окружающей среды а также обеспечения безопасных условий труда.
Превенторы обеспечивают расхаживание проворачивание и протаскивание бурильных труб с замковыми соединениями (с фасками по обе стороны замкового соединения под углом 18о) а также герметизацию устья скважины при закрытии уплотнителя на любой части бурильной колонны обсадных или насосно-компрессорных труб а также при отсутствии колонны труб при аварийной ситуации.
Превентор предназначен для эксплуатации в рабочих средах: нефть газ газоконденсат буровой раствор промывочная жидкость вода и их смеси с объемным содержанием СО2 до 6% (коррозионностойкое исполнение К1 по ГОСТ 13862).
При эксплуатации при температуре окружающей среды ниже 0°С превенторы должны обогреваться.
Превенторы изготовлены в климатическом исполнении У категория размещения 1 по ГОСТ 15150 для работы в умеренном макроклиматическом районе эксплуатации по ГОСТ 16350.
Основные технические характеристики превентора приведены в таблице 1
Таблица 1- Основные технические характеристики превенторов
Наименование параметра
Рабочее давление (Рр) МПа
Диаметр проходного отверстия мм
Рабочий объем гидравлической камеры превентора л:
Рабочий ход поршня мм
Давление гидроуправления (наибольшее) МПа:
Рабочая жидкость системы гидроуправления (основная)*
Наибольший диаметр труб пропускаемых с подвеской через превентор мм
Температура рабочей среды ОС
Температура окружающей среды оС:
Маркировка фланцев:***
Масло всесезонное ВМГЗ
от минус 60 до плюс 45
Продолжение таблицы 1.
Габаритные размеры мм не более:
- диаметр превентора по проушинам
- диаметр превентора по корпусу
Размер конических резьб в отверстиях для подключения к гидростанции дюймы
*Заменители основной рабочей жидкости: масла индустриальные
И-20А по ГОСТ 20799-88 масло приборное МВП по ГОСТ 1805-76.
**При эксплуатации при температуре окружающей среды ниже 0оС к превенторам подводится внешний парообогрев.
***Параметры даны по API 6А 17 редакции.
Конструктивно-технологический анализ детали
В общем случае к конструкциям деталей предъявляются следующие требования [7]:
- конструкция детали должна состоять из стандартных и унифициро-ванных конструктивных элементов и быть стандартной в целом;
- детали должны изготовляться из стандартных или унифицированных заготовок;
- размеры и поверхности детали должны иметь соответственно опти-мальные т.е. экономически и конструктивно обоснованные точность и шероховатость;
- физико-химические и механические свойства материала жесткость детали ее форма и размеры должны соответствовать требованиям техноло-гии изготовления хранения и транспортировки;
- показатели базовой поверхности детали (точность шероховатость) должны обеспечивать точность установки обработки и контроля;
- заготовки должны быть получены рациональным способом с учетом заданного объема выпуска и типа производства;
- метод изготовления должен обеспечивать возможность одновременного изготовления нескольких деталей;
- сопряжения поверхности деталей различных классов точности и шероховатости должны соответствовать применяемым методам и средствам обработки;
- конструкция детали должна обеспечивать возможность применения типовых и стандартных технологических процессов ее изготовления.
Указанные требования являются обобщением опыта проектирования и изготовления деталей а степень соответствия этим требованиям характеризует конструктивно-технологический уровень детали.
Количественно технологичность конструкции корпуса превентора кольцевого ПУГ-180х21-10-00 может быть оценена совокупностью показателей технологической рациональности и преемственности детали в число которых входят коэффициент сложности конструкции детали; коэффициент применяемости унифицированных или стандартных конструктивных элементов детали; коэффициент повторяемости конструктивных элементов детали; коэффициент точности и шероховатости поверхности детали; коэффициент обрабатываемости детали и коэффициент использования материала при механической обработке [8 9].
Коэффициент сложности конструкции детали определяется выражением в виде
где - коэффициенты определяемые как
Коэффициент зависит от количества поверхностей на исходной заготовке с которых удаляется стружка при изготовлении детали. При этом комбинированные поверхности образуемые за один рабочий ход одним инструментом учитываются в качестве одной поверхности.
Для существующей конструкции корпуса
где - количество обрабатываемых резанием и общее количество формообразующих поверхностей детали соответственно.
Подставляя численные значения требуемых показателей из чертежа детали и технологического процесса обработки детали резанием в выражения (1.3) и (1.2) находим
Коэффициент учитывает общее количество заданных на чертеже данных по обеспечению требуемых точностей формы и взаимного расположения поверхностей в пределах 005 мм.
где - количество поверхностей детали к которым предъявляются требования по точности формы и их взаимному расположению в пределах 005 мм.
Подставляя численные значения требуемых показателей из чертежа детали в выражения (1.4) и (1.2) находим
Коэффициент учитывает количество различных видов обработки резанием (технологических операторов).
Для существующей конструкции корпуса
где - количество технологических операторов;
- общее количество технологических переходов обработки резанием.
Подставляя численные значения требуемых показателей из карт технологического процесса обработки детали резанием в выражения (1.5) и (1.2) находим
Коэффициент учитывает соответствие точности и шероховатости поверхностей детали некоторым оптимальным величинам под которыми подразумеваются рекомендуемые в качестве экономичности и конструктивно обоснованные величины. Величина входящая в выражение для этого коэффициента определяется по формуле
где - количество зон на которых параметр для j-ой поверхности отстоит от оптимального сочетания.
Подставляя численные значения требуемых показателей из чертежа детали в выражения (1.6) и (1.2) находим
Согласно выражению (1.1) коэффициент сложности конструкции детали будет составлять
Коэффициент применяемости унифицированных или стандартных конструктивных элементов детали определяют по формуле
где - общее количество конструктивных элементов в детали;
- количество унифицированных конструктивных элементов;
n - количество неунифицированных элементов.
Поскольку все формообразующие поверхности корпуса можно считать унифицированными то коэффициент применяемости унифицированных или стандартных конструктивных элементов детали можно принять равным .
Коэффициент повторяемости конструктивных элементов детали рас-считывают по формуле
где - количество повторяющихся конструктивных элементов детали;
- общее количество конструктивных элементов детали.
Подставляя численные значения требуемых показателей из чертежа детали в выражение (1.8) находим
Коэффициент относительной обрабатываемости материала детали выражает относительную скорость резания соответствующую 60-минутной стойкости резцов в сравнении с эталонной сталью (сталь 45 ГОСТ 1050-84 ). Для стали 30ХМ ГОСТ 4543-71 величина этого коэффициента составляет что характеризует обрабатываемость этой стали как удовлетворительную.
Коэффициент использования материала при механической обработке определяют по соотношению
где - массы готовой детали и заготовки соответственно.
Подставляя численные значения требуемых показателей из карт технологического процесса обработки детали резанием в выражение (1.9) находим
Таким образом по рассчитанным показателям ТКИ можно сделать вывод о среднем уровне технологичности данной конкретной детали.
Необходимо отметить что корпус превентора изготавливают из заготовки получаемой штамповкой.
Обрабатываемые поверхности корпуса с точки зрения обеспечения точности и шероховатости не представляют значительных технологических трудностей однако наличие изготавливаемых фасонных канавок под уплотнения и фасонной сложносопряжённой выточки создает некоторые затруднения при окончательной обработке детали.
На технологичность конструкции детали подвергаемой обработке резанием влияют как технологические факторы (обрабатываемость материала выбор баз и размерных связей форма и размеры детали требования точности и шероховатости обрабатываемых поверхностей) так и организационные (объем выпуска и тип производства). При этом объем выпуска и тип производства определяют степень технологического оснащения механизации и автоматизации технологического процесса.
Х имический элемент
Никель (Ni) не более
Фосфор (P) не более
Таблица 2- Химический состав
Таблица 3- Механические свойства
Термообработка состояние поставки
Таблица 4- Механические свойства при повышенных температурах
Таблица 5- Механические свойства в зависимости от температуры
Таблица 6-Механические свойства в зависимости от сечения
Термообработка состояние поставки
Место вырезки образца - центр
Место вырезки образца - 12R
Место вырезки образца - 13R
Таблица 7- Температура критических точек
Таблица 8- Ударная вязкость
Состояние поставки термообработка
Закалка 880 С масло. Отпуск 350 С.
Закалка 880 С масло. Отпуск 550 С.
Таблица 9- Предел выносливости
Термообработка состояние стали
Закалка 870 С вода. Отпуск 600 С [37]
Таблица 10- Прокаливаемость
Таблица 11- Физические свойства
Температура испытания °С
Модуль нормальной упругости Е ГПа
Коэффициент теплопроводности Вт(м ·°С)
Уд. электросопротивление (p НОм · м)
Коэффициент линейного расширения (a 10-6 1°С)
Удельная теплоемкость (С Дж(кг · °С))
Таблица 12- Материалы заменители
Сортовой прокат в том числе фасонный: ГОСТ 4543-71 ГОСТ 259071 ГОСТ 2591-71 ГОСТ 2879-69 ГОСТ 10702-78. Калиброванный пруток ГОСТ 7417-75 ГОСТ 8559-75 ГОСТ 8560-78 ГОСТ 1051-73 ГОСТ 10702-78. Шлифованный пруток и серебрянка ГОСТ 14955-77. Полоса ГОСТ 103-76. Поковки и кованые заготовки ГОСТ 1133-71 ГОСТ 8479-70. Трубы ГОСТ 8731-87 ГОСТ 8732-78.
Назначение : Шестерни валы цапфы шпильки гайки и различные другие детали работающие при температуре до 450-500°С.
3Выбор метода получения заготовки.
Метод получения заготовки определяется назначением и конструкцией детали материалом техническими требованиями масштабом и серийностью выпуска. Для рационального выбора заготовки необходимо одновременно учитывать все вышеупомянутые данные. При выборе способа получения заготовки необходимо стремиться к максимальному приближению формы и размерам заготовки к параметрам основной детали и снижению трудоемкости заготовительных операций а также последующей механической обработки. Для изготовления детали «Корпус превентора» в серийном производстве применим сварную заготовку состоящую из двух поковок рисунок 2.
Верхняя часть заготовки 1 получена ковкой на молоте а нижняя часть 2 получена горячей штамповкой в открытом штампе. Сварка заготовок производится под слоем флюса после предварительной обработки под сварку фасок.
В качестве присадочного металла применяют проволоку марок Св-18ХМА Св-ЮХМ Св-ЮМХ и Св-10Х5М по ГОСТ 2246-60
Хромомолибденовую сталь лучше сваривать проволокой марки Св-18ХМА. Диаметр проволоки в зависимости от толщины металла берется по таблице 13.
Диаметр присадочной проволоки мм
Кромки металла перед сваркой должны быть зачищены до металлического блеска. При температуре окружающей среды ниже нуля должен проводиться предварительный подогрев изделия до 250—300° С. Если толщина свариваемого металла больше 16 мм то вне зависимости от температуры окружающей среды изделие предварительно подогревают до той же температуры причем она должна сохраняться во время сварки примерно постоянной.
При толщине металла до 5 мм сварка ведется в один слой а при большей толщине — в два и больше слоев. При двухслойной сварке первый слой накладывается на всю толщину металла а вторым слоем усиливают шов. Сварка должна проводиться без перерыва. Контроль сварочного шва по API 17 редакции А для швов работающих под давлением В базовом варианте применялась цельная поковка массой более 2400кг что не технологично и вызывает необоснованные затраты металла и материально-технических ресурсов при производстве изделия. Стоимость сварной заготовки сопоставима со стоимостью цельной поковки но сварная заготовка более технологична что приведёт к снижению себестоимости изготовления изделия Стоимость сварной заготовки состоит из стоимости материала и стоимости сварочных работ. Вес сварной заготовки составляет 1407 кг. Стоимость заготовки по данным заводов изготовителей составляет 60000 рублей. Стоимость материала 32000рт
Таблица 14- Материалы заменители
Шестерни валы цапфы шпильки гайки и различные другие детали работающие при температуре до 450-500°С.
1Обоснование маршрутной технологии изготовления детали.
Разработка технологического процесса состоит из комплекса взаимосвязанных работ предусмотренных стандартами ЕСТПП и должна выполняться в полном соответствии с требованиями ГОСТ 14.301-83 «Общие правила разработки технологических процессов и выбора технологического оснащения». При разработке маршрутной технологии придерживаются следующих основных принципов:
а) в первую очередь обрабатывают поверхности которые являются базовыми при дальнейшей обработке;
б) после этого обрабатывают поверхности с максимальным припуском для выявления дефектов заготовки;
в) необходимо соблюдать принцип концентрации операций при котором как можно больше поверхностей должно обрабатываться в одной операции;
г) необходимо соблюдать принципы совмещения и постоянства баз;
д) необходимо учитывать на каких стадиях технологического процесса целесообразно производить механическую термическую и другие виды обработки в зависимости от требований чертежа;
е) поверхности к которым предъявляются наиболее высокие требования по качественно-точностным характеристикам окончательно обрабатываются в последнюю очередь.
Разработка маршрута обработки любой детали начинается с предварительного выбора вида обработки отдельных поверхностей заготовки и определения методов достижения точности соответствующей требованиям чертежа серийности производства и технологических возможностей существующего в наличии на предприятии оборудования. После анализа этих данных приступают к составлению планов механической обработки детали. Устанавливая последовательность обработки попутно определяют количество установов и позиций заготовки на станке. С учетом особенностей конструкции заготовки; так же стремятся обработать за один установ наибольшее количество поверхностей. Вновь разработанная маршрутная технология обработки корпуса превентора представлена в комплекте карт технологического процесса.
Операционная технология для изготовления корпуса разработана с учетом места каждой операции в маршрутной технологии. К моменту проектирования каждой операции известно какие поверхности и с какой точностью обрабатываются на предшествующих операциях какие поверхности и с какой точностью нужно обрабатывать на данной операции. Проектирование операций связано с разработкой их структуры с составлением схем наладок расчетом настроенных размеров и ожидаемой точности обработки с назначением режимов обработки определением нормы времени и т. д. Номера поверхностей при составлении операционной технологии указаны на эскизах.
2Выбор оборудования.
Выбор оборудования является одной из важнейших задач при разработке технологического процесса механической обработки детали. От правильного выбора зависит производительность экономное использование площадей механизации и автоматизации ручного труда электроэнергии и в итоге себестоимость изделия.
При выборе станочного оборудования учитывается следующее: характер производства методы достижения заданной точности при обработке соответствие станка размерам детали мощность станка удобство управления и обслуживания станка габаритные размеры и стоимость станка возможность оснащения станка высокопроизводительными приспособлениями и средствами механизации и автоматизации кинематические данные станка а также наличие имеющегося оборудования.
Результаты выбора оборудования представлены в таблице 15.
Таблица 15-Выбор оборудования
Токарно-карусельная с ЧПУ
Горизонтально-сверлильная
Токарно-карусельный станок 16DS125 применяется при выполнении операций 010 015 055 060 что обусловлено возможностью обработки заготовок диаметром до 1000 мм и силовыми характеристиками станка: возможностью проведения обдирки заготовок и деталей после термической обработки. Кроме того положительным фактором обработка внутренних поверхностей за один установ за счет чего происходит сокращение вспомогательного времени на операцию.
Горизонтальный координатно-расточной станок W100A применяется при выполнении операции 075 для сверления двух отверстий и нарезки резьбы. Он значительно дешевле применявшегося ранее обрабатывающего центра с ЧПУ ИР800ПМФ4
Технические характеристики станков для выполнения операций технологического процесса изготовления корпуса приведены в таблицах
Таблица 16-Технические характеристики координатно-расточного станка СВКоZ
Наибольшая масса заготовки
Мощность привода главного движения
Таблица 17- Технические характеристики координатно-расточного станка W100А
Диаметр рабочего шпинделя мм
Конус рабочего шпинделя
Число ступеней оборотов рабочего шпинделя
Диапазон оборотов рабочего шпинделя мин-1
Число ступеней оборотов планшайбы
Диапазон оборотов планшайбы мин-1
Мощность главного двигателя кВт
Максимальный момент кручения на шпинделе
- при минимальных оборотах Н*м
- при максимальных оборотах Н*м
Перемещение рабочего шпинделя W
Диаметр планшайбы мм
Диаметр глубина центрирующего отверстия планшайбы мм
Перемещение задвижки планшайбы мм
Максимальный диаметр торцевого точения мм
Вертикальное перемещение шпиндельной головки Y мм
Мин. высота оси шпинделя над рабочим столом мм
Продольное перемещение стола Z мм
- с опорой без опоры расточных оправок мм
- только без опоры расточных оправок мм
Макс.расстояние между торцом планшайбы и подшипником опоры мм
Максимальный вес обрабатываемой детали кг
Размеры зажимной поверхности рабочего стола мм
Зажимные "T" пазы стола - размер
Диаметр глубина центрирующего отверстия заж. поверхности стола мм
Таблица 18- Технические характеристики токарно-карусельного станка 16DS125
Наибольший диаметр обрабатываемой заготовки
Наибольшая высота обрабатываемой заготовки
Наибольшее допустимое усилие резания
Диаметр планшайбы (варианты)
Пределы частоты вращения планшайбы (регулирование бесступенчатое)
Пределы частоты вращения планшайбы для фрезерования (регулирование бесступенчатое)*
Наибольший крутящий момент на планшайбе
Наибольшая длина хода портала**
Пределы рабочих подач портала**
Скорость установочных перемещений портала**
Наибольший ход поперечины (перемещение бесступенчатое)
Наибольшая длина хода суппорта
Пределы рабочих подач суппорта
Скорость установочных перемещений суппорта
Пределы частоты вращения шпинделя инструмента (регулирование бесступенчатое)*
Наибольший крутящий момент на шпинделе инструмента*
Мощность сверлильно-фрезерного привода*
Число позиций магазина токарного инструмента не менее
Число позиций магазина сверлильно-фрезерного инструмента не менее*
3Выбор технологической оснастки.
Cуществует ряд унифицированных переналаживаемых токарных планшайб многократного применения отличающихся конструкцией наружными диаметрами количеством пазов для закрепления наладок размерами и расположением центрирующих элементов.
При переходе от обработки одной детали к другой конструируется соответствующая наладка; базирующаяся на отверстие: возможны случаи базирования и крепления наладки непосредственно на планшайбу. Крепление наладки осуществляется винтами а детали – Г-образными прихватами. Прихваты передвигаются в планшайбе по Т-образным пазам. Унифицированная планшайба с наладкой обеспечивает точность обработки деталей с биением не более 004 мм.
Планшайбы диаметром 1000 мм и выше выполняются с восемью пазами. Центрирование наладок производится по центральной выточке и по переставным штырям расположенным по окружности. Штыри могут устанавливаться при обработке деталей диаметром 400 – 700 мм. Допустимое число оборотов при любом способе крепления детали не более 300 в минуту.
4Расчет промежуточных припусков допусков и размеров заготовки по укрупненным нормативам.
Припуски на механическую обработку определяем расчетно-аналитическим и опытно - статистическим методами.
Рассчитаем припуски на обработку и промежуточные предельные размеры для 427+03 по токарной операции.
Заготовка сварная состоящая из двух поковок.
Верхняя полая часть — поковка полученная методом свободной ковки припуски и допуски на поковки из углеродистой и легированной сталей при ковки на молотах устанавливают по ГОСТ 7829-70
Припуски и допуски на поковки из тех же сталей при ковки на прессах устанавливают по ГОСТ 7060-79
Нижняя часть получена штамповкой в открытом штампе припуски и допуски по ГОСТ 7505-74
Технологический маршрут обработки состоит из двух операций: чернового растачивания перед сварочной операцией и чернового и чистового растачивания после сварки.
Заготовка устанавливается в приспособлении к станку и базируется на поверхность 386 (см. КЭ технологического процесса).
Суммарное значение Rz и Т характеризующие качество кованых заготовок составляет 2000 мкм [23 табл. 11]. Для чернового и чистового растачивания величина Т и Rz численно равна: 250 мкм и 240 мкм – для чернового и 40 мкм и 40 мкм – для чистового [23 табл. 24].
Суммарное значение пространственных отклонений для заготовки данного типа определяется по формуле:
где =16 мм - величина смещения оси поверхности [1 табл 34] .
=55 мм - величина эксцентричности центрального отверстия [1 табл 33].
Суммарное значение пространственного отклонения равно:
Остаточное пространственное отклонение после чернового растачивания равно:
Погрешность установки при черновом растачивании равна:
где - погрешность базирования;
-погрешность закрепления.
Погрешность базирования в рассматриваемом случае eб=0
Погрешность закрепления заготовки eз принимаем 0 мкм [1 табл. 38]. Тогда погрешность установки при черновом растачивании будет равна:
Далее производим расчет минимальных припусков пользуясь основной формулой [1 табл. 26 ]:
Минимальный припуск под растачивание:
черновое =15.456 (мм);
Для чернового растачивания:
Рассчитываем величину расчетного максимального припуска по формуле:
Затем для перехода предшествующего конечному определяем расчетный размер путем сложения наименьшего предельного размера по чертежу и расчетного минимального припуска 2zmin.
Записываем все наибольшие и наименьшие предельные размеры по всем технологическим переходам. Определяем общий припуск z0max и z0min суммируя промежуточные припуски на обработку и делаем проверку правильности назначения припусков.
Tdз - Tdд =z0max - z0min (2.5)
226 –15456=14 – 0630;
Следовательно расчеты произведены верно.
Полученные данные заносим в таблицу.
Таблица 19- Расчет припусков и предельных размеров по технологическим переходам на обработку поверхности 427+0.3.
Размер элементарной поверхности и технологические переходы ее обработки
Предельные значения припусков
Расчетный припуск 2zimin мкм
Поверхность 427(+0.3)
Расчет режимов резания состоит в определении для заданных условий обработки глубины резания числа проходов подачи скорости резания силы резания и мощности требуемой на резание.
Рассчитаем режимы резания на операцию 015 (токарно- карусельную) которая выполняется на токарно-карусельном станке модели 16DS125. Эскиз операции представлен на рисунке 6. Операция 015 (токарно-карусельная) содержит 6 переходов содержание которых приведено в таблице 20.
Рисунок 3 - Эскиз операции 015 (токарно-карусельная)
Таблица 20 - Содержание переходов операции 01
Установить и после обработки снять деталь
Подрезать торец размера 1
Точить диаметр 2 на проход
Точить диаметр 4 выдержать размер 3
Точить диаметр 6 выдержать размер 5
Точить диаметр 7 выдержать размер 8 выполнить радиус 11
Точить диаметр 9 выдержать размер 8
Переход 1. Подрезать торец размера 1
Станок токарно-карусельный модели 16DS125 Резец К.01.4227.000-06 Т15К6 ГОСТ 21066-75; штангенциркуль ШЦ- II-1000-01 ГОСТ 166-75
Глубина резания t = 5 мм.
Скорость резания при точении ммин определяется по формуле
где - коэффициент и показатели степени выбираемые в зависимости от условий резания из справочных данных;
Т - стойкость инструмента мин;
t - глубина резания мм;
- поправочный коэффициент на скорость резания который определяют по формуле
где - коэффициент отражающий влияние качества обрабатываемого материала на скорость резания;
- коэффициент отражающий влияние состояния поверхности заготовки на скорость резания;
- коэффициент отражающий влияние материала режущей части на скорость резания;
- коэффициенты отражающие влияние параметров резца (главный угол в плане вспомогательный угол в плане радиус при вершине) на скорость резания;
Согласно справочным данным [23] эскизу операции 015 (рисунок 3) и таблице 1.12 поименованные величины составляют:
t = 5 мм; S = 10 ммоб; = 340; = 015; = 045; m = 02; Т = 60 мин; = (750)n = (750586)1 = 1218; =08; = 10; = 10 (); К=087; К=094
Подставляя численные значения в формулы (2.7) и (2.6) находим расчетное значение скорости резания
Частота вращения n1 обмин определяется по формуле
Подставляя численные значения в формулу (2.8) находим
По паспорту станка 16DS125 назначаем стандартную частоту вращения
n1ст = 45 обмин с учетом которой определяем действительное значение скорости резания
Составляющие силы резания при наружном поперечном точении рассчитывают по формуле
где - коэффициент и показатели степени выбираемые в зависимости от условий резания из справочных данных; ; ; ; ;
- поправочный коэффициент который вычисляют по уравнению
- поправочный коэффициент учитывающий влияние механических свойств обрабатываемой стали; ;
- поправочные коэффициенты учитывающие влияние геометрических параметров режущей части инструмента на составляющие силы резания; ; ; ; Кrp=093
Подставляя численные значения в формулы (2.14) и (2.13) находим
Мощность резания подсчитывают по формуле
Подставляя численные значения в формулу (2.11) получаем
Установленный режим резания должен удовлетворять условию
карусельного станка модели 16DS125 = 55 кВт.
9 кВт 55 кВт - условие выполняется.
Основное время мин рассчитывают по формуле
где для первого перехода
- величина врезания инструмента; при глубине резания t = 5 мм проходным резцом с углом в плане j = 450 = 8 мм;
- величина перебега инструмента; при t = 5 мм = 8 мм.
Подставляя численные значения в формулу (2.13) получаем
Переход 2. Точить диаметр 2 на проход
Глубина резания t = 8 мм.
Согласно справочным данным [23] эскизу операции 015 (рисунок 3) и таблице 20 поименованные величины составляют:
t = 8 мм; S = 10 ммоб; = 340; = 015; = 045; m = 02; Т = 60 мин; = (750)n = (750586)1 = 1218; =08; = 10; = 10 (); К=087; К=094
Подставляя численные значения в формулу (1.30) находим
n2ст = 42 обмин с учетом которой определяем действительное значение скорости резания
Подставляя численные значения в формулы (2.18) и (2.17) находим
Подставляя численные значения в формулу (2.19) получаем
где - мощность станка определяемая по паспорту кВт; для токарно- карусельного станка модели 16DS125 = 55 кВт.
26 кВт 55 кВт - условие выполняется.
- величина врезания инструмента; при глубине резания t = 8 мм проходным резцом с углом в плане j = 450 = 11 мм;
- величина перебега инструмента; при t = 8 мм = 8 мм.
Подставляя численные значения в формулу (2.17) получаем
Переход 3. Точить диаметр 4 выдержать размер 3
Станок токарно-карусельный модели 16DS125 Резец К.01.4227.000-06 Т15К6 ГОСТ 21066-75; штангенциркуль ШЦ-II-1000-01 ГОСТ 166-75;
t = 8 мм; S = 10 ммоб; = 340; = 015; = 045; m = 02; Т = 60 мин; = (750)n = (750586)1 = 1218; =08; = 10; = 07 (); К=1; К=094
Подставляя численные значения в формулы (2.23) и (2.22) находим расчетное значение скорости резания
Подставляя численные значения в формулу (2.24) находим
n3ст = 57 обмин с учетом которой определяем действительное значение скорости резания
Составляющие силы резания при растачивании рассчитывают по формуле
Подставляя численные значения в формулы (2.26) и (2.25) находим
Подставляя численные значения в формулу (2.26) получаем
14 кВт 55 кВт - условие выполняется.
где для третьего перехода
- величина врезания инструмента; при глубине резания t = 8 мм проходным резцом с углом в плане j = 900 = 11 мм;
Подставляя численные значения в формулу (2.29) получаем
Переход 4. Точить диаметр 6 выдержать размер 5
Станок токарно-карусельный модели 16DS125. Резец К.01.4207.000-11 Т15К6 ГОСТ 20872-75; нутромер микрометрический НМ-600ГОСТ 10-88
Подставляя численные значения в формулы (2.31) и (2.30) находим расчетное значение скорости резания
Частота вращения n4 обмин определяется по формуле
Подставляя численные значения в формулу (2.32) находим
По паспорту станка 16DS125 назначаем стандартную частоту вращения n4ст = 58 обмин с учетом которой определяем действительное значение скорости резания
Подставляя численные значения в формулы (2.34) и (2.33) находим
Подставляя численные значения в формулу (2.35) получаем
03 кВт 55 кВт - условие выполняется.
где для четвёртого перехода
Подставляя численные значения в формулу (2.37) получаем
Переход 5. Точить диаметр 7 выдержать размер 8 выполнить радиус 11
Подставляя численные значения в формулы (2.39) и (2.38) находим расчетное значение скорости резания
Частота вращения n5 обмин определяется по формуле
Подставляя численные значения в формулу (2.40) находим
n5ст = 77 обмин с учетом которой определяем действительное значение скорости резания
Подставляя численные значения в формулы (2.42) и (2.41) находим
Подставляя численные значения в формулу (2.43) получаем
09 кВт 55 кВт - условие выполняется.
где для пятого перехода
Подставляя численные значения в формулу (2.45) получаем
Переход 6. Точить диаметр 9 выдержать размер 8
Станок токарно-карусельный модели 16DS125. Резец К-01-3637-000 Т15К6 ГОСТ 20874-75; нутромер микрометрический НМ-600ГОСТ 10-88
t = 5 мм; S = 05 ммоб; = 340; = 015; = 045; m = 02; Т = 60 мин; = (750)n = (750586)1 = 1218; =08; = 10; = 07 (); К=1; К=094
Подставляя численные значения в формулы (2.46) и (2.47) находим расчетное значение скорости резания
Частота вращения n6 обмин определяется по формуле
Подставляя численные значения в формулу (2.48) находим
По паспорту станка 16DS125 назначаем стандартную частоту вращения n6ст = 175 обмин с учетом которой определяем действительное значение скорости резания
Подставляя численные значения в формулы (2.50) и (2.49) находим
Подставляя численные значения в формулу (2.51) получаем
4 кВт 55 кВт - условие выполняется.
где для шестого перехода
- величина врезания инструмента; при глубине резания t=5мм проходным резцом с углом в плане j = 900 = 5 мм;
- величина перебега инструмента; при t = 5 мм = 5 мм.
Подставляя численные значения в формулу (2.53) получаем
Суммарное основное время на выполнение операции 015 составит
= 1106+1671+4684+4379+888+365 = 13093 (мин). Вспомогательное время на операцию определяют по формуле
где - вспомогательное время на установку и снятие детали;
- вспомогательное время связанное с переходом;
- вспомогательное время на контрольные измерения.
Нормативное время на установку и снятие детали предусматривает выполнение следующих работ: установку и закрепление детали включение и выключение станка открепление и снятие детали очистку приспособления от стружки. При массе обрабатываемой заготовки более 1000кг и применении четырёхкулачкового патрона по общемашиностроительным нормативам времени [24] = 155 мин.
Вспомогательное время связанное с переходом включает в себя время на изменение числа оборотов шпинделя мин;
Вспомогательное время на контрольные измерения [9] будет складываться из времени затрачиваемого на промеры штангенциркулем =6021= 126 (мин).
Подставляя численные значения в формулу (2.54) находим
При этом величина оперативного времени будет составлять
= 13093+1739 = 14832 (мин).
Норма штучного времени определяется по формуле
где - время затрачиваемое на обслуживание рабочего места (организационное и техническое); для станков токарно-карусельной группы с диаметром стола 1500мм оно составляет = 3 % от оперативного времени ;
- время перерывов на отдых и личные надобности; в соответствии с [24] оно составляет = 8 % от оперативного времени .
Подставляя численные значения в формулу (2.55) находим
Расчет режимов резания и технического нормирования других операций технологического процесса изготовления корпуса выполняется аналогично. Результаты расчетов приведены в технологической карте.
6Обоснование и разработка технологического процесса
Базовый технологический процесс ориентированный на выпуск продукции в условиях единичного производства в основном соответствует типовому технологическому процессу. При этом частично обработку корпусов ведут на универсальном оборудовании с использованием стандартного и специального режущего и мерительного инструментов. При увеличении программы выпуска изделий базовый технологический процесс перестает удовлетворять технико-экономическим требованиям современного производства и нуждается в усовершенствовании.
Технологический процесс изготовления детали должен выполняться с наиболее полным использованием технических возможностей средств производства при наименьшей себестоимости изделий. Оптимизация технологического процесса заключается в том что в установленный промежуток времени необходимо обеспечить выпуск потребного количества изделий заданного качества при возможно минимальной себестоимости их изготовления.
Так при выполнении горизонтально-сверлильной операции 075 (в заводском технологическом процессе 130) по изготовлению двух отверстий на боковой поверхности для сокращения вспомогательного времени и весьма значительных затрат на оборудование целесообразно применить специальное установочное приспособление заменить станок марки ИР-800 на горизонтально-расточной станок марки W100A.
В разработанном на предприятии технологическом процессе (базовом ТП) применяется цельная кованная заготовка. Этот метод получения заготовки является рациональным с точки зрения простоты и при этом соблюдаются все условия прочности. Но несмотря на все это данный способ получения заготовки не является единственным.
Рациональней применить сварную полую заготовку при этом при правильном расположении сварного шва и соблюдении технологии сварки условия прочности не нарушатся.
Следует заметить что базовый ТП проектировался в расчете на использование уже имеющегося на предприятии оборудования которое имеет конкретные точностные характеристики. Режимы резания применяемые в базовом ТП не являются прогрессивными но соответствуют требованиям получения готовой детали. Поэтому в сложившихся условиях последовательность операций в базовом ТП является наиболее оптимальным способом изготовления рассматриваемого изделия.
При применении новой заготовки последовательность операций не нарушится что позволит применить тоже оборудование. При этом значительно сократится операционное время на первых двух токарно-карусельных операциях.
Базирование – это придание заготовке или изделию требуемое положение относительно выбранной системы координат.
Применительно к механической обработке на станках при базировании заготовок производится придание заготовке требуемого положения относительно элементов станка которое определяет траекторию движения подачи обрабатывающего инструмента.
Выбор технологической базы начинается с выбора технологической базы с первой операции. База на первой операции называется черновой и ее можно использовать только один раз.
Базы различаются по назначению:
Конструкторская – база используемая для определения положения детали или сборочной единицы в изделии;
Технологическая – база используемая для определения положения заготовки или изделия в процессе изготовления или ремонта.
Выбор базовых поверхностей для обработки детали является важным этапом проектирования технологического процесса.
Первой операцией механической обработки является токарная 010 на которой в качестве баз используются торец детали и поверхность вращения. Так как данные поверхности – необработанные то они могут использоваться в качестве базовых только один раз. Деталь обрабатывается с разных сторон поэтому в качестве черновой базы используется поверхность имеющая наименьший припуск.
В последующих операциях в качестве баз используются предварительно обработанные наружные внутренние и торцовые поверхности.
В токарной операции 015 в качестве базовых поверхностей выбираем обработанные цилиндрическую – 386 и торцевую поверхности. При применении станочного приспособления приложение усилия закрепления происходит в направлении перпендикулярном торцовой поверхности в результате чего обеспечивается стабильность базирования детали.
Следующей станочной операцией обработки корпуса превентора является токарно-карусельная операция 055 с ниже перечисленными базами: наружняя цилиндрическая поверхности 660 и торец детали. Усилие закрепления прикладывается к боковым поверхностям детали..
На токарно-карусельная операции 055 в качестве базовых поверхностей используются торцовая поверхность корпуса и цилиндрическая поверхность фланца 380 что дает возможность производить установку корпуса при обработке на станочном приспособлении к станку.
Для последующих операциях 065; 070; 075 вновь в качестве базовых поверхностей используются торцовая поверхность фланца корпуса и его цилиндрическая поверхность 380.
Из выше сказанного следует что для уменьшения погрешности обработки во многих операциях используются одни и те же базовые поверхности то есть соблюдается принцип постоянства баз что существенно снижает погрешность и увеличивает точность обработки. Выбранные технологические базы совместно с зажимными устройствами обеспечивают надёжное прочное крепление детали и неизменность её положения во время обработки. Принятые технологические базы и методы базирования определяют наиболее простые и надёжные конструкции приспособлений удобство установки снятия обрабатываемой детали на каждой операции.
При определении погрешности установки корпуса в четырёхкулачковом патроне на токарно-карусельной операции 010 и 055 следует учитывать что производится выверка детали по этому погрешность закрепления детали не может быть выше допустимых величин установленных в технологическом процессе
2 Расчет коэффициента надежности закрепления детали
Так как в производственных условиях могут иметь место отступления от тех условий применительно к которым рассчитывались по нормативам силы и моменты резания возможное увеличение их следует учесть путем введения коэффициента надежности (запаса) закрепления К и умножения на него сил и моментов входящих в составленные уравнения статики.
Значение коэффициента надежности К следует выбирать дифференцированно в зависимости от конкретных условий выполнения операции и способа закрепления заготовки. Его величину можно представить как произведение частных коэффициентов каждый из которых отражает влияние определенного фактора:
К=К0·К1·К2·К3·К4·К5·К6
К0 – гарантированный коэффициент запаса надежности закрепления
К1 – коэффициент учитывающий увеличение силы резания из-за случайных неровностей на заготовках
К1=12 для черновой;
К1=1 – для чистовой;
К2 – коэффициент учитывающий увеличение силы резания (при прерывистом) в следствии затупления инструмента
К3 – коэффициент учитывающий увеличение силы резания при прерывистом резании
К4 – коэффициент учитывающий непостоянство зажимного усилия;
К4=13 - для ручной;
К4=12 – для пневматического и гидравлического зажимного усилия;
К5 – коэффициент учитывающий степень удобства расположения рукояток в ручных зажимах
К5= 12 – при диапазоне угла отклонения рукоятки 900;
К5=10 – при удобном расположении и малой длине рукоятки;
К6 – учитывает неопределенность из-за неровностей места контакта заготовки с опорными элементами имеющими большую опорную поверхность (учитывается только при наличии крутящего момента стремящегося повернуть заготовку)
К6=10 – для опорного элемента имеющего ограниченную поверхность контакта с заготовкой;
К6=15 – для опорного элемента с большой площадью контакта.
К= 15·1·13·11·12·10 = 256
3 Расчет потребных сил зажима
Закрепление заготовки производится с помощью зажимных устроиств различных конструкций. Принцип действия и конструкцию зажимного устройства конструктор выбирает исходя из конкретных условий выполнения операций типа производства величин сил резания действующих на заготовку при выполнении операций конструктивных особенностей заготовки типа станка.
Силовой расчет станочных приспособлений можно разбить на следующие этапы:
Определение сил и моментов резания;
Выбор коэффициента трения f заготовки с опорными и зажымными элементами;
Составление расчетной схемы и исходного уравнения (для расчета исходного усилия Ри) для расчета исходного усилия Р3;
Расчет коэффициента надежности закрепления К;
Составление расчетной схемы и исходного уравнения для расчета исходного усилия Ри;
Расчет диаметров силовых цилиндров пневмо и гидроприводов;
Определение сил и моментов резания. Действующие на заготовку силы и моменты резания можно рассчитывать по формулам приводимых в справочниках и нормативах к определенному виду обработки.
При перемещении заготовки в кулачках вдоль оси имеем коэффициент трения f1 а при поворачивании f2.
Определим величину зажимного усилия при условии недопустимости перемещения заготовки в кулачках. Предположим что в патроне 4 кулачка.
При условии недопустимости провертывания заготовки в кулачках
Т2·r=Мкр или 4f2·Р3·r=КМкр откуда
Зз= Кx·P04f1+ Кx·МxM4f2xr
4 Описание работы приспособления для токарно-карусельных операций.
При разработке технологического процесса механической обработки заготовки необходимо правильно выбрать и спроектировать приспособления которые должны способствовать повышению производительности труда точности обработки улучшению условий труда ликвидации предварительной разметки заготовки и выверки ее при установке на станке. Применение станочных приспособлений при обработке заготовок дает ряд преимуществ:
а) повышает качество и точность обработки детали;
б) сокращает трудоемкость обработки заготовок за счет резкого уменьшения времени затрачиваемого на установку выверку и закрепление;
в) расширяет технологические возможности станков.
Для выполнения токарно-карусельных операции по обработке корпуса разработана конструкция специального установочного приспособления для токарно-карусельного станка модели 16DS125.
Основной частью приспособления является корпус 1 с базовыми посадочными местами. Корпус представляет из себя диск в который устанавливается пальцы для фиксации детали. На диск также крепятся прижимные планки с помощью которых происходит крепление детали на приспособление.
Крепление приспособления на планшайбе станка осуществляется при помощи болтов установленных в паз планшайбы и пазы основания корпуса 2.
Выставление приспособления на планшайбе осуществляется с помощью фиксатора закрепленного в центре приспособления.
Перед началом обработки деталь устанавливается на посадочные диаметры приспособления и прижимается планками 1. После обработки гайка 15 раскручивается планки 1 снимается. После чего деталь снимается а на ее место устанавливается новая.
Схема базирования и закрепления детали представлена на листе карты эскизов в технологическом процессе
5 Описание одного измерительного инструмента или контрольного приспособления
Для измерения внутренних размеров и канавки полученных в токарной операции 060 используется специальный меритель. Меритель содержит штангу 1 со сменными губками. На штанге размещена рамка 3 на которой закреплен упор 6.. Для замера размеров меритель снабжен комплектом сменных ножек-вставок 4 закрепляемых на соответствующих губках с помощью винтов 5. Значение контролируемого размера настраивается на мерителе с помощью концевых мер длины и по измерительной шкале и нониусу.
Точность измерения мерителя определяется точностью шкалы. Цена деления составляет 005(мм)
После измерения канавки губки отводятся от детали в крайнее положение деталь снимается на ее место устанавливается новая и цикл измерения повторяется.
Пределы измерения 380-1000 мм.
1 Определение потребного количества оборудования
Проектирование участка механического цеха начинают с расчета потребности в металлорежущем оборудовании. Оборудование механических цехов подразделяется на три категории: основное производственное (расчетное) дополнительное (нерасчетное) и вспомогательное. Потребности в основном оборудовании определяют по формулам приведенным в работах. Если при расчете оборудования получается дробное число то оно округляется до единицы. Расчетное количество станков по -й группе оборудования определяется на основании трудоемкости производственной программы и действительного фонда времени работы оборудования.
где – годовая программа выпуска деталей j-ого типа шт.;
- штучное время обработки детали типа j на
– коэффициент выполнения норм по
– годовой эффективный фонд времени работы одного станка
– количество наименований деталей обрабатываемых на i-й группе оборудования.
где – число рабочих дней в году;
– число рабочих смен в сутки;
– продолжительность рабочей смены ч;
– плановые потери времени на ремонт % КП = 2-8 %.
Подставляя в уравнение (4.2) исходные числовые значения согласно заданию на дипломное проектирование находим:
В соответствии с разработанным маршрутным технологическим процессом и годовой программой выпуска деталей по уравнению (4.1) определяем потребности в оборудовании по конкретным группам металлорежущих станков.
Станок токарно-карусельный модели 16DS125:
Принимаем СП = 6 станков.
Станок координатно-расточной СВКоZ с ЧПУ:
Принимаем СП = 1 станок.
Станок горизонтально-расточной W100A:
Принимаем СП = 1 станка.
Средние коэффициенты загрузки оборудования по участку в целом Кзу и по группам Кзi рассчитываются по формулам:
где m – число групп оборудования на участке.
Коэффициент загрузки оборудования по участку в целом составит:
Результаты расчетов по уравнениям (4.1) - (4.3) для основных групп необходимого станочного оборудования а также их балансовую стоимость для наглядности представляем в виде таблице 21.
Таблица 21 - Расчет потребности участка механического цеха в технологическом оборудовании
Количество оборудования шт.
Коэффициент загрузки
Станок токарно- карусельный
Станок координатно-расточной с ЧПУ
Станок горизонтально-расточной W100A
Штат механического цеха состоит из основных и вспомогательных рабочих инженерно-технических работников служащих младшего обслуживающего персонала работников технического контроля. Численность основных рабочих можно определять по формулам приведенным в работах [30 39]. Количество остальных работников цеха принимается по соответствующим установленным нормам в процентах от основных производственных рабочих.
В крупносерийном производстве численность основных рабочих для выполнения нормируемых работ определяется по формуле:
– годовой объем выпуска изделий j-ого вида шт.;
– действительный годовой фонд времени работы рабочего ч;
– коэффициент выполнения норм на i-й операции.
где - коэффициент учитывающий потери рабочего времени – неявки установленные трудовым законодательством (10-12%).
Принятое количество рабочих устанавливается путем соответствующего округления полученного значения Чор до целого.
Токари-карусельщики:
Принимаем количество основных рабочих равным 12 человека.
Токари-растоники с ЧПУ:
Округляем до целого и принимаем количество – 2 человек.
Принимаем количество рабочих – 1 человека.
Принимаем – 2 человек.
Расчет потребного количества основных рабочих оформлен в виде таблицы 22.
Таблица 22 - Расчет потребного количества основных рабочих
В таблице 23 в соответствии с рекомендациями [30 40] представлен необходимый перечень вспомогательных рабочих проектируемого участка
Таблица 23 - Ведомость вспомогательных рабочих
Определяющий показатель
Норма обслужив. на 1 раб.
Слесарь по рем. оборуд.
Слесарь по рем. оснастки
Слесарь по межрем.обсл. оборудования
Подносчики и раздатчики инструмента
Распределители работ
Уборщик произв. площ.
Кол-во ед. оборуд. в смену
Ед. оборуд. на человека
Количество основных рабочих
Процент от основных рабочих
Организационная часть
1 Планирование размещения оборудования и рабочих мест на участке механического цеха
Разработка технологической планировки проектируемого участка механического цеха осуществляется в соответствии со строительными и компоновочными планами производственных помещений цеха разрабатываемых на основании соответствующих рекомендаций руководящих материалов. При этом основным принципом используемым при планировке является прямоточность движения деталей в процессе обработки т.е. увязка планировки с технологическим процессом и установление минимальных расстояний между станками а также между станками и элементами зданий согласно нормам технологического проектирования приведенным в [38] и [39]. С учетом веса и габаритов обрабатываемых заготовок в качестве внутрицехового транспорта целесообразно использовать электрические тележки. Основной вариант технологической планировки проектируемого участка представлен на рисунке 9.
2 Организация транспортировки изделий на участке
Внутрицеховая транспортная система предназначена для своевременной доставки заготовок полуфабрикатов готовых изделий мате-
риалов и других грузов со склада на требуемый производственный участок и на склад с участков а также для транспортирования их между участками.
На основании потребности производственных участков в грузах отправляемых каждым складом для обеспечения заданной программы выпуска изделий определяют грузопотоки и наносят их на схему транспортных связей цеха. Кроме того при определении общего грузопотока следует учесть массу всех грузов предполагаемых для транспортирования.
Исходя из технологического процесса транспортирования представляющего совокупность приемов и способов выполнения транспортных работ планировки технологического оборудования и складов компоновки цеха производят расчет транспортной системы. Началом технологического процесса транспортирования к производственному участку является прием груза с приемо-сдаточной секции склада в которой он находится в подготовленном для транспортирования виде а концом — подача груза на приемо-сдаточную секцию производственного участка.
При выборе типов грузоподъемности и количества транспортных средств необходимо учитывать разделение транспортных средств на основные и вспомогательные. Основные транспортные средства проектируют централизованно и выпускают серийно а вспомогательные средства зачастую изготовляют по месту так как их типоразмеры многообразны.
3 Проектирование и организация рабочих мест
При проектировании производственных процессов и разработке плана расположения оборудования и рабочих мест на участке необходимо иметь ввиду основные положения научной организации труда и технической этики выполнение которых способствует созданию наиболее благоприятных условий для работающих и повышению производительности труда. Внешней планировкой рабочего места является размещение основного оборудования оснастки подъемно-транспортных средств приспособлений заготовок и готовых деталей.
Под рабочим местом понимается организационная зона производственной площади предназначенной для выполнения определенных работ и оснащенная необходимыми материально-техническими средствами труда оборудованием.
При любой форме организации работы для наилучшего использования оборудования и достижения наибольшей производительности труда необходимо кроме всех технических возможностей станка инструмента и приспособления предусмотреть рациональную организацию рабочего места обеспечивающего непрерывность работы станка. Для этого нужно устранить потери времени и задержки вызываемыми лишними движениями и хождением несвоевременной подачи материала неудобным расположением заготовок инструмента на рабочем месте.
Рациональная организация рабочего места предусматривает необходимую предварительную подготовку работы и рабочего места своевременное и четкое обслуживание его в процессе работы и наиболее совершенную планировку.
В механических цехах серийного производства на рабочем месте токаря хранится много различного инструмента и приспособлений. Для хранения используют инструментальную тумбочку с планшетом и приемным столиком на верхней полке которого устанавливают тару с заготовками а на нижней хранятся приспособления и необходимый инструмент. Имеется деревянная решетка под ноги рабочего. В тумбочке имеется два отделения соответственно для хранения инструмента рабочего работающего в первую и вторую смену.
4 Организация инструментального хозяйства.
Задача инструментального хозяйства - своевременное изготовление и обеспечение производства высокопроизводительными и экономичными инструментами и технологической оснасткой а также поддержание их в работоспособном состоянии в период эксплуатации.
Работа по обеспечению инструментами и технологической оснасткой выполняется подразделениями инструментального хозяйства и ведется по двум направлениям:
- инструментальное производство;
- инструментальное обслуживание.
Структура инструментального хозяйства представлена на рисунке:
Структура инструментального хозяйства
Функции инструментального хозяйства:
) разработка нормативов потребления инструмента и оснастки;
) планирование изготовления приобретения ремонта инструментов и оснастки;
) изготовление инструментов и оснастки;
) организация хранения и обслуживание цехов;
) ремонт и восстановление;
) надзор за надлежащим использованием.
Планирование и нормирование потребности в инструменте и технологической оснастке
Потребность предприятия в инструменте и технологической оснастке (далее в инструменте) складывается из расходного и оборотного фондов.
Расходный фонд - это годовая потребность в инструменте для выполнения запланированного объема и номенклатуры продукции. Расчет потребности по каждому виду инструмента ведется по утвержденным нормам расхода и годовой производственной программы.
Оборотный фонд - запас инструментов (Zоб) для обеспечения нормальной работы производства образующийся:
- из складских запасов в ЦИСе и ИРК (Zскл);
- эксплуатационного фонда на рабочих местах (Zр);
- инструментов в заточке (Zз);
- инструментов в ремонте (Zрем);
- инструментов на контроле (Zк).
Zоб = Zскл + Zр + Zз + Zрем + Zк.
Размер запасов в основном устанавливается по системе "максимум- минимум" то есть каждый вид инструментов имеет три нормы запаса:
- запас в "точке заказа" Zт.з.
Эти нормы запаса рассчитываются по формулам:
где Rдн - среднедневная потребность ИРК цехов в данном инструменте (шт);
Tп.з - периодичность пополнения запаса ( дн.);
Тс.изг и Tн.изг - время срочного и нормального изготовления партии инструментов или приобретения партии покупных инструментов (дн).
Запас точки заказа (Zт.з) отражает такую величину запаса при которой должен выдаваться заказ на изготовление или приобретение инструментов. Объем партии заказа (Zпарт) равен
Zпарт = Zmax - Zmin.
Изготовление инструментов. Если предприятие не может приобрести необходимые ему инструменты на специализированных инструментальных заводах или такое приобретение дороже собственного производства то изготовление такого инструмента осуществляет в собственных инструментальных цехах. Обычно инструментальные цехи организуются по технологическому принципу. В их состав входят отделения или участки: станочное слесарно-сборочные лекальные шлифовально-заточные заготовительные термические контрольные восстановления инструментов измерительная лаборатория кладовые и т.д.
Специализация подразделений цеха зависит от вида основной продукции предприятия и ее объемов.
Приобретение инструментов является функцией бюро покупных инструментов.
Организация инструментального обслуживания непосредственно в производственных подразделениях предприятия предполагает бесперебойное снабжение рабочих мест инструментами их правильную эксплуатацию своевременный и качественный ремонт. Рабочие места производственных цехов обслуживают ИРК в функции которых входит:
- получение из ЦИС (ЦАС) инструментов;
- организация их хранения и учета;
- выдача на рабочие места;
- организация ремонта и восстановления инструментов;
- организация контроля;
- списание пришедших в негодность инструментов.
В ЦИСе (ЦАСе) хранится основная часть запасов инструментов предприятия.
Ремонт и восстановление инструментов производится в зависимости от их особенностей и количества либо в ремонтных отделениях расположенных непосредственно в цехах основного производства либо на специализированных участках инструментальных цехов.
Заточка инструментов. Для заточки инструментов в цехах организуются заточные отделения. Заточки сложных инструментов требующих специального дорогостоящего оборудования (червячные фрезы шеверы долбяки протяжки резцовые головки для конических винтовых колес и т.д.) производят централизованно в инструментальных цехах.
Одной из важных функций является организация технического надзора за эксплуатацией инструментов:
- соблюдением правил эксплуатации;
- выполнением правил хранения;
- правильной заточкой и т.д.
5 Организация технического контроля
На всех этапах создания продукции а также при ее эксплуатации необходимым элементом управления качества является контроль. Контроль необходим не только для достоверной оценки результатов деятельности предприятий и его подразделений но и служит основным информативным источником используемым для принятия решений о необходимости и степени корректировки системы управления качеством продукции.
Сущность всякого контроля можно свести к получению информации о фактическом состоянии некоторого объекта его признаках и показателях (первичная информация); сопоставлению первичной информации с ранее установленными требованиями и нормами т. е. определения соответствия или несоответствия фактических данных ожидаемым (вторичная информация).
При контроле качества объектом контроля является перерабатываемая изготовляемая выпускаемая и эксплуатируемая продукция.
Контроль технического процесса заключается в контроле режимов характеристик параметров технологического процесса.
Контроль проектирования – это контроль конструкторской документации с целью определения соответствия разрабатываемой продукции техническому уровню и качеству.
Производственный контроль – контроль качества осуществляемый службой технического контроля при изготовлении продукции. Он заключается в контроле производственного процесса и его результатов.
Система контроля качества разрабатывается с таким расчетом чтобы регулировать все отклонения технологического процесса влияющие на качество продукции и связанные с материалами оборудованием обслуживанием и условиями производства.
Входной контроль заключается в контроле продукции поставщика поступающего к потребителю (заказчику) и предназначенной для использования при изготовлении ремонте или эксплуатации продукции.
Операционный контроль состоит в контроле продукции или процесса во время выполнения или после завершения определенной операции.
Приемочный контроль – это контроль готовой продукции по результатам которого принимается решение о ее пригодности к поставке и использованию.
Сплошной контроль – контроль при котором решение о качестве продукции принимается по результатам проверки каждой единицы продукции.
Летучий контроль является разновидностью предупредительного контроля в ходе которого контроллер или контрольный мастер БТК периодически обходит закрепленные за ним рабочие места осуществляет выборочный контроль качества изготовленных рабочими деталей проверяя при этом соблюдение технологических процессов и дисциплину.
Разрушающий контроль применяют для получения показателей качества материалов (образцов и заготовок) деталей узлов и машин в целом.
6 Организация ремонта оборудования на участке
Эффективная эксплуатация автоматизированных производств в значительной мере определяется надежностью и ремонтопригодностью оборудования а также обеспечением необходимых условий его функционирования. Для выполнения указанных функций служит система технического обслуживания.
Для обеспечения длительной и бесперебойной работы производственной системы необходимо иметь надежную систему энергообеспечения своевременно проводить работы по восстановлению работоспособности оборудования удалению стружки подачи качественных СОЖ и масел а также поддерживать требуемый микроклимат в помещениях.
Выполнение задач возлагаемых на систему технического обслуживания обеспечивается следующими подразделениями производственной системы: секцией энергопитания цеховой ремонтной базой (ЦРБ) отделением по удалению и переработке стружки участком для приготовления и раздачи СОЖ и масел отделением очистки и регенерации СОЖ вентиляционной секцией и кладовой вспомогательных материалов.
Критерии оценки качества оборудования можно подразделить на две основные группы: производственно-технологические и эксплуатационные. К первым относится себестоимость оборудования его металлоемкость и т. д. Наиболее важным эксплуатационным показателем является надежность. Остальные эксплуатационные показатели работы оборудования (производительность класс точности степень механизации и автоматизации и т. д.) без обеспечения надлежащей надежности не имеют значения.
Надежность — свойство изделия выполнять заданные функции сохраняя эксплуатационные показатели в заданных служебным назначением пределах в течение требуемых промежутков времени или наработки. Надежность оборудования определяется его работоспособностью долговечностью и ремонтопригодностью. Следует различать функциональную параметрическую и структурную надежность. Под функциональной понимают надежность срабатывания механизмов и устройств оборудования в соответствии с заданной функцией. Параметрическая надежность означает соответствие качеству обработки заготовок или сборки изделий параметрам заданным в технической документации. Структурная надежность определяется компоновочными решениями реализованными в оборудовании.
Работоспособность — состояние оборудования при котором оно может выполнять заданные функции так что параметры изготавливаемых изделий соответствуют требованиям технической документации.
Безотказность — свойство оборудования сохранять работоспособность в
течение некоторой наработки без вынужденных перерывов. Наработка — продолжительность или объем выпуска продукции с оборудования измеряемые в часах штуках циклах и т. д. Различают наработку за какой-либо период времени до первого отказа между отказами и т. д. Отказ — нарушение работоспособности оборудования. Отказами оборудования автоматического (автоматизированного) производства являются поломка деталей электрических и электронных устройств разрегулировка выход каких-либо параметров за установленные ГОСТ или ТУ пределы вследствие чего оборудование не может качественно выполнять свои функции. Порядок расположения элементов сложных технологических комплексов в зависимости от удель ного веса отказов следующий: инструменты механические узлы электроника и электрооборудование пневмо- и гидрооборудование.
Неисправность — состояние оборудования при котором оно не соответствует хотя бы одному из требований технической документации.
Долговечность — свойство оборудования сохранять работоспособность до предельного состояния с необходимыми перерывами для технического обслуживвания и ремонтов. Предельное состояние оборудования характеризуется тем что уже невозможна его дальнейшая эксплуатация либо снизилась эффективность использования ниже допустимого уровня.
Все оборудование в производственной системе должно иметь высокую ремонтопригодность — свойство оборудования заключающееся в его приспособлении к предупреждению обнаружению и устранению отказов и неисправностей путем проведения технического обслуживания и ремонтов. Ремонтопригодность количественно оценивается затратами средств и времени на устранение отказов. Затраты времени на устранение отказа включают следующие времена: на обнаружение отказа; отыскание неисправностей; подготовку запасных деталей узлов или блоков для ремонтов; ремонт; послеремонтную настройку на проверку качества ремонта и организационные потери времени. Ремонтопригодность характеризуется приспособленностью оборудования к требованиям по ликвидации повреждений.
Ремонтопригодность в значительной мере влияет на уровень затрат связанных с эксплуатацией оборудования и является одним из главных средств обеспечения его надежности и долговечности.
Система ремонтного обслуживания предусматривает совокупности взаимосвязанных средств документации ремонтного обслуживания ремонтных работ и исполнителей необходимых для поддержания и восстановления функционирования элементов входящих в производственную систему.
Служба ремонта оборудования на заводе включает: отдел главного механика (ОГМ) главного энергетика (ОГЭ); бюро числового программного управления (БЧПу); ремонтно-механический цех (РМЦ) подчиненный ОГМ; электроцех подчиненный ОГЭ; цеховые ремонтные базы (ЦРБ).
На ремонтную службу возлагают функции: надзор и уход за действующим оборудованием с целью предупреждения поломок своевременный (плановый предупредительный) ремонт оборудования оперативный (внеплановый) ремонт оборудования.
Основные направления в организации ремонта состоят: в изготовлении деталей для ремонта заранее; введении системы планово-предупредительного ремонта (ППР); использовании систем диагностики состояния систем оборудования; агрегатном узловом и блочном методе ремонта оборудования; автоматизации ремонтных работ с использованием промышленных роботов.
Система планового предупредительного ремонта (ППР) предусматривает ремонт в заранее установленные сроки что повышает срок службы оборудования и сокращает время на ремонт. Сущность ППР заключается в том что после того как оборудование проработало определенное число часов оно подвергается различным видам профилактики и плановых ремонтов периодичность и последовательность которых определяется служебным назначением оборудования его габаритными размерами конструктивными и ремонтными особенностями условиями эксплуатации. Существуют три основные системы ППР — система послесмотровых стандартных и периодических ремонтов. Первую систему используют для
оборудования работающего в условиях поточного и переменно-поточного производства вторую — для оборудования применяемого в непоточном производстве третью — для специального оборудования работающего при постоянном режиме.
Системой технического обслуживания и ремонта называют комплекс (ГОСТ 18322-85) взаимосвязанных положений и норм определяющих организацию и выполнение связанных с ними работ. Плановый ремонт оборудования выполняют через установленное нормами число часов отработанное оборудованием или по достижении установленного нормами его технического состояния.
Внеплановый (оперативный) ремонт выполняют по потребностям и к нему относят аварийный ремонт вызванный дефектами конструкции или изготовления оборудования а также дефектами и нарушениями правил технической эксплуатации.
Межремонтное обслуживание включает наблюдение за выполнением правил эксплуатации оборудования своевременное устранение мелких неисправностей и регулирование механизмов и устройств. Оно выполняется ежесуточно операторами наладчиками или дежурным персоналом во время перерывов в работе оборудования. Осмотры проводят для проверки состояния оборудования устранения мелких неисправностей и выявления объема подготовительных работ подлежащих выполнению при очередном плановом ремонте и выполняются оператором или ремонтником. Текущий ремонт — это плановый ремонт выполняемый с целью гарантированного обеспечения работоспособности оборудования в течение установленного нормативами числа часов работы до следующего ремонта и заключающийся в замене или восстановлении отдельных деталей блоков или узлов и выполнении связанных с этим разборочных сборочных и регулировочных работ. Текущий ремонт подразделяется на малый и средний.
Общая станкоемкость ремонта одной РЕ: Гст = 28 станко-ч. Приведенный расчет учитывает 10 %-ное централизованное обеспечение запасными частями в зависимости от потребности в них. При ином обеспечении вводятся коэффициенты.
Средняя ремонтная сложность механической части основного оборудования принимается равной 20 РЕ а электрической части — 15 РЕ. В общем случае средняя ремонтная сложность определяется в каждом конкретном случае следующим образом. По системе ППР берется категория ремонтной сложности по каждому виду оборудования и умножается на количество этого вида оборудования затем складывается по всем видам и делится на количество оборудования в цехе т. е. рассчитывают средневзвешенную категорию сложности.
Продолжительность межремонтного обслуживания и категории сложности ремонта для промышленных роботов рекомендуется определять в зависимости от конструктивных характеристик (массы числа деталей точности) по аналогии с межремонтным обслуживанием станков с ЧПУ пользуясь таблицей категорий сложности ремонта отдельных моделей станков. Эту продолжительность принимают равной 8—10 мес.
Для транспортных и загрузочных устройств обычно рекомендуется следующая структура ремонтного цикла: О-О-ТР-О-О-ТР-О-О-ТР-О-О-ТР-О-О-ТР-О-О-ТР-О-О-КР. Продолжительность цикла составляет 3—75 лет.
Предварительное планирование сроков ремонта и обслуживание парка оборудования участков и цехов для расчета численности ремонтников составление заявок на материалы и определение затрат на поддержание и восстановление работоспособности оборудования можно выполнять в зависимости от фактически отработанного времени. Однако вывод в капитальный ремонт отдельных станков независимо от запланированной (средней для данной группы оборудования) продолжительности цикла необходимо производить согласно их техническому состоянию.
Количество станков в ЦРБ: Nр=
где Кц — коэффициент учитывающий объем ремонтных работ выполняемый в ЦРБ (Кц09); ΣРЕ — общая ремонтоёмкость РЕ; Щ — межремонтный цикл год; Фэ — эффективный годовой фонд времени работы оборудования ч; К3 — коэффициент загрузки оборудования (К = 055 * 080); Гст — станкоемкость ремонта одной РЕ.
В укрупненных расчетах количество оборудования на станочном участке берется по нормам в зависимости от числа обслуживаемого оборудования (2—6 %). В число обслуживаемого оборудования включают все производственное оборудование цеха кроме станков в самом ЦРБ.
На слесарном участке число верстаков берется примерно равным числу станков на станочном участке ЦРБ Ориентировочный состав оборудования на слесарном участке: настольно-сверлильный станок гидравлический пресс шлифовальный переносной станок обдирочно-шлифовальный сварочный аппарат ручной пресс моечная ванна и пост газовой сварки.
На машиностроительном предприятии помимо директора и главного инженера ответственных за создание безопасных условий труда имеется служба по технике безопасности и производственной санитарии.
Для предупреждения производственного травматизма на каждом предприятии должны быть разработаны утверждены и изучены всем производственным персоналом правила техники безопасности производственной санитарии и пожарной безопасности.
Администрация предприятий обязана обеспечить своевременное и качественное проведение инструктажа и обучение работающих безопасным приемам и методам работы.
Все работники поступающие на работу проходят вводный инструктаж по технике безопасности и производственной санитарии который является первым этапом обучения технике безопасности. Вторым этапом обучения является инструктаж на рабочем месте с целью усвоения рабочим безопасных приемов труда непосредственно по специальности и на том рабочем месте где он должен работать. Проводит этот инструктаж мастер цеха или механик цеха.
При выполнении работ по специальностям повышенной опасности проводятся повторные инструктажи через определенные промежутки времени (один раз в 3 месяца) а также при каждом случае нарушения правил техники безопасности.
В данном технологическом процессе существуют следующие вредные и опасные факторы: механические характеризующиеся кинетической и потенциальной энергией и механическим влиянием на человека; электрические – электрический ток; химические – наличие вредных примесей в воздухе; психо-физические: утомление стресс.
Наиболее существенное влияние на организм человека оказывают следующие вредные факторы: шум вибрация микроклимат и электрический ток.
Работа механообрабатывающего цеха сопровождается шумом возникающим при токарной фрезерной сверлильной обработках детали. Шум – это всякий нежелательный неприятный для восприятия человека звук.
Шум неблагоприятно воздействует на организм человека. Он вызывает психические и физиологические нарушения усиливает утомляемость рабочего снижает работоспособность и создает предпосылки для общих профессиональных заболеваний и производственного травматизма. Известно что ряд таких серьезных заболеваний как гипертонические и язвенные болезни неврозы с перенапряжением нервной системы из-за увеличения уровней шума до 70 децибел и выше.
Методы и средства борьбы с шумом принято подразделять на: методы снижения шума на пути распространения его от источника; методы снижения шума в источнике; средства индивидуальной защиты. Так как в механообрабатывающих цехах шум как правило имеет механическое происхождение то основным методом борьбы с ним является совершенствование технологических процессов и оборудования. Но в производстве есть оборудование которое нельзя заменить и нельзя исключить его применение. Им отводятся специальные помещения со звукопоглощающими перегородками. Основным нормативным документом устанавливающим требования к относительно акустическим методам борьбы с шумом является СНиП – 12-17 «Защита от шума» содержащее требования к проектированию средств шумопоглушения строительно-акустическими и архитектурными планированными методами. К средствам индивидуальной защиты относятся вкладыши наушники.
На проектируемом участке механической обработки корпуса превентора установлены станки. При работе задача рабочего сводится к установке закреплению и снятию детали со станка. Это значительно снижает процент травматизма но не исключает его. К числу характерных опасностей и вредностей могут быть отнесены вращающиеся элементы токарно-карусельных сверлильных и фрезерных станков. При обслуживании этих видов станков может произойти захват одежды рабочего волос руки.
При работе на токарно-карусельном станке опасность представляет отлетающая стружка. Причиной несчастного случая может стать неправильный выбор режимов резания нарушение технологического процесса.
К числу производственных факторов отрицательно влияющих на условия и производительность труда на участке относятся неблагоприятные метеоусловия неудовлетворительная освещенность рабочих мест шум опасность поражения электрическим током использование охлаждающей жидкости которая может вызвать разного рода поражения и заболевания кожи. Травматизм в цехе повышается также из-за наличия транспортных средств для перевозки деталей заготовок мостового крана.
По пожарной безопасности проектируемый участок можно отнести к категории Д – не пожароопасный так как обрабатываются негорючие материалы в холодном состоянии.
Эксплуатация большинства машин связана с применением электрической энергии. Электрический ток проходя через организм человека оказывает термическое электрическое и биологическое действие вызывая местные и общие электротравмы. Поражающие действия электрического тока зависят от следующих факторов: значение и длительность протекания тока через тело человека рода тока индивидуальных свойств человека. Человек начинает ощущать ток при значении 06 – 15 мА.
Согласно ГОСТ 12.2.006-83 «ССБТ. Электробезопасность. Допустимые токи» существуют предельно допустимые нормы напряжения прикосновения и тока проходящих через человека с частотой 50 Гц
Вопросам электробезопасности нужно уделить большое внимание.
Электробезопасность – система организационных и технологических мероприятий и средств обеспечивающих защиту людей от вредного и опасного воздействия электрического тока.
Основными мерами защиты от электрического тока являются:
Обеспечение недоступности токоведущих частей находящихся под напряжением от случайного прикосновения. Это обеспечивается рядом способов:
) изоляцией токоведущих частей размещение их на недоступной высоте ограждение;
) электрическое разделение сети с помощью специальных трансформаторов;
) защитное заземление и зануление;
) организация безопасной эксплуатации электроустановок.
Применяются также средства индивидуальной защиты.
По ТУ 38-105504-72 к ним относятся резиновые диэлектрические перчатки диэлектрические галоши коврики и изолирующие подставки.
Экономическая часть.
1.Определение затрат на основные материалы.
Марка материла: Сталь 30 ХМ.
Масса заготовки: = 1407 кг.
Цена материла заготовки: 45 руб.кг.
Масса заготовки на программу:
Стоимость материала на программу:
Расходы транспортно – заготовительные.
Принимаем: Рт-з = 7% от стоимости материала.
Масса готовой детали: = 576 кг.
Масса отходов на деталь:
Масса отходов на программу:
где: - коэффициент потери отходов = 095.
Цена отходов: 12 руб.кг.
Стоимость отходов на программу:
Стоимость материалов с учетом транспортно – заготовительных расходов:
Ведомость затрат на основные материалы
Наименование материала
Масса материала на программу кг.
Цена материала Руб.кг.
Стоимость материала на программу руб.
Транспортно-заготовительные расходы руб.
Затраты на материалы за вычетом отходов и с учетом Рт-з
Масса отходов на деталь кг.
Масса отходов на программу кг.
Цена отходов руб.кг.
Стоимость отходов на программу
2Расчет фонда заработной платы основных и вспомогательных рабочих.
Для оплаты ОПР принимаем сдельно – премиальную форму оплаты труда. Фонд заработной платы ОПР определяется по формуле:
где: - средняя тарифная ставка на участке
- коэффициент доплаты = 12
- премиальный коэффициент = 18
Среднемесячная заработная плата ОПР составит:
Для оплаты труда ВПР принимаем повременно – премиальную форму оплаты труда.
Численность руководящих работников служащих и специалистов рассчитывается укрупнено по методу относительной численности т.е. в процентном отношении от общего числа ОПР и ВПР. Руководящие работники – 10 – 12% и служащие – 4 – 6%.
3. Расчет цеховых расходов на силовую электроэнергию сжатый воздух воду.
Затраты на силовую электроэнергию:
где: - стоимость 1 кВтч. электроэнергии = 194 (руб.)
- годовой расход электроэнергии
где: - установочная мощность всех станков = 682 кВт.
- эффективный годовой фонд производственного времени оборудования = 3984 часа.
- средний коэффициент загрузки оборудования = 063.
- коэффициент одновременной работы оборудования = 06.
- коэффициент потерь в электрической сети = 095.
- КПД электродвигателя = 085.
Затраты на сжатый воздух.
где: - стоимость одного кубического метра сжатого воздуха
- годовой расход сжатого воздуха.
Затраты на воду для производственных нужд.
где: - стоимость 1 водопроводной воды на станок = 2928 (руб.)
- годовой расход воды на один станок = 25 ()
- число смен работы оборудования.
4 Расчет затрат на амортизацию оборудования
Смета расходов на содержание и эксплуатацию оборудования включает следующие статьи: амортизация оборудования эксплуатация оборудования расходы по содержанию и эксплуатации транспорта износ малоценных и быстроизнашивающихся инструментов и приспособлений прочие расходы.
Расходы на эксплуатацию оборудования включают в себя: затраты на вспомогательные материалы потребляемые в процессе эксплуатации оборудования; затраты на силовую энергию потребляемую для привидения в движение производственных машин; затраты на сжатый воздух для эксплуатации оборудование; затраты на воду для производственных нужд; затраты на основную плату вспомогательных рабочих обслуживающих оборудование.
Амортизация оборудования применяется в долях стоимости основных фондов для металлорежущих станков работающих абразивным инструментом 12 % не абразивным инструментом 122 %.
Затраты на текущий ремонт и обслуживание оборудования применяют в размере 7 % от их первоначальной стоимости.
Затраты на износ малоценного инструмента и инвентаря 2000 руб. на один станок.
затраты на вспомогательные материалы определяем ориентировочно по укрупненному нормативу в размере 1000 рублей на один станок.
Затраты на основную и дополнительную заработную плату ОПР ВПР с отчислениями на социальное страхование – 385 %.
Затраты на охрану труда и обеспечение техники безопасности составляют 500 рублей в год на рабочего.
(17+3)500 = 10000 (руб.)
Прочие расходы (отопление освещение хозяйственные нужды) составляют 5 % от суммы затрат по всем статьям.
Таблица – 26. Составление сметы затрат на участок.
Наименование статьи расходов
Расходы на содержание и эксплуатацию оборудования:
Затраты на силовую электроэнергию.
Амортизация оборудования транспортных средств и дорогостоящей оснастки.
Затраты на текущий ремонт и обслуживание оборудования.
Затраты на износ и содержание малоценного инструмента и инвентаря.
Затраты на вспомогательные материалы.
Общецеховые расходы:
Основная и дополнительная зарплата ОПР и ВПР с отчислениями на социальное страхование.
Затраты на охрану труда.
5 Технико – экономические показатели участка
Затраты на основные материалы.
Основная заработная плата ОПР на деталь.
Таблица – 27. Расчет сдельных расценок на деталь
Дополнительная заработная плата ОПР на деталь составляет 20 % от основной заработной платы.
Отчисления на социальные страхования составляют 385 %от суммы основной и дополнительной заработной платы.
Цеховые накладные расходы принимаем 500 % основной заработной платы ОПР.
Определяем цеховую себестоимость единицы продукции.
Таблица – 28 Калькуляция цеховой себестоимости на деталь.
Наименование статей затрат
Затраты на материалы.
Дополнительная заработная плата ОПР на деталь.
Отчисления на социальное страхование.
Цеховые накладные расходы.
Цеховая себестоимость единицы продукции.
6 Технико-экономические показатели
Таблица – 29 Технико-экономические показатели
Наименование показателей
Коэффициент использования металла.
Трудоемкость механической обработки.
Количество установленного оборудования на участке.
Средний коэффициент загрузки.
Численность рабочих на участке в том числе:
Руководящих работников и специалистов
Производительность 1 ОПР.
Средняя заработная плата 1 ОПР.
Себестоимость единицы продукции.
7 Расчет показателей экономической эффективности проекта
Экономический эффект от функционирования участка на котором детали изготавливаются по вновь спроектированной технологии рассчитывается на конкретный период. Исходя из темпов обновления промышленной продукции в состав которой входит изготавливаемая деталь принимаем этот период равным одному году.
Экономический эффект реализации проекта участка за расчетный период может быть определен по формуле:
где - неизменная по годам расчетного периода стоимостная оценка результатов производства продукции с использованием разработанного технологического процесса р;
- неизменные по годам расчетного периода затраты на продукцию с применением разработанного технологического процесса р;
- норма реновации исчисленная для периода использования проектируемой технологии; [42];
- норматив приведения разновременных результатов и затрат численно равный нормативу эффективности капитальных вложений .
Величина определяется по формуле
где - оптовая цена детали производимой на спроектированном участке р;
- коэффициент рентабельности к себестоимости продукции; ;
- годовая программа выпуска деталей шт.
где - текущие издержки производства (себестоимость годового выпуска продукции с использованием разработанного технологического процесса) без учета амортизации основных производственных фондов используемых при изготовлении продукции р;
- среднегодовая стоимость основных производственных фондов используемых при производстве продукции на спроектированном участке;
- ликвидационное сальдо основных фондов либо их остаточная стоимость на момент окончания применения разработанной технологии р. Ликвидационное сальдо основных фондов принимают в размере 5 % от их первоначальной стоимости. Остаточная стоимость основных фондов на момент окончания использования разработанной технологии определяется по формуле
где - первоначальная (балансовая) стоимость основных фондов р;
- норма реновации соответствующая сроку службы основных фондов = 00315 (15 лет) [42];
- норма реновации соответствующая = 00357.
Внутренняя норма доходности (внутренний коэффициент эффективности) проекта определяется по формуле
где – единовременные затраты на создание участка р.
Срок окупаемости капитальных вложений в проект определяется по формуле
Таким образом а срок окупаемости примерно равен сроку использования разработанной технологии.
Следовательно можно сделать вывод о том что разработанные инженерные решения являются экономическими эффективными.
Анализ приведенных материалов дипломного проекта показывает что основная цель дипломного проектирования - адаптация базового технологического процесса изготовления корпуса превентора кольцевого ПУГ 180х21-10-00 для условий крупносерийного производства - в целом достигнута. При этом были решены следующие задачи:
- на основе визуализации и компьютерного проектирования минимизированы припуски на механообрабатываемые поверхности заготовоки получаемой ковкой и штамповкой с последующей сваркой (экономия металла составила 980 кг на одну заготовку увеличение КИМ с 10% до 40%);
- взамен дорогостоящего обрабатывающего центроа использованы универсальные металлорежущие станки обеспечивающие на всех операциях прогрессивные режимы резания (сокращение трудоемкости механической обработки составило 214168 %);
- взамен универсально-сборочных приспособлений рассчитана и спроектирована высокоточная специализированная технологическая оснастка применяемая на токарно-карусельных и сверлильных станках;
- исходя из заданной программы выпуска изделий и сменности работы производственного участка разработана его технологическая планировка учитывающая построение маршрутного и операционного технологических процессов;
- дана технико-экономическая оценка принятым в процессе дипломного проектирования техническим решениям (годовая экономическая эффективность разработанного проекта составила более 15063 млн. р. срок окупаемости капитальных вложений – 21 года снижение себестоимости - до 202 %);
- проанализированы воздействия негативных факторов промышленного производства на экологию окружающей среды и работников участка.
Вместе с тем в дипломном проекте не нашли отражения такие вопросы как расчеты технологических размерных цепей и оценка точности получаемых межоперационных размеров применение средств механизации и автоматизации технологических процессов и некоторые другие.
Cписок использованной литературы:
Сорокин В.Г. «Марочник сталей и сплавов» М.: Машиностроение 1989г.
Панов А.А. «Обработка металлов резанием».
Горбацевич А.Ф. «Курсовое проектирование по технологии машиностроения» Минск Высшая школа 1975 г.
Справочник технолога том 1 и 2 под редакцией Косилова А.А. Москва машиностроение 1986 г.
«Общемашиностроительные нормативы времени» М. Машиностроение 1989 г.
«Общемашиностроителные нормативы времени режимов резания для технического нормирования работ на металлорежущих станках». Москва машиностроение 1967 г.
Сахаров С.Н. «Металлорежущие инструменты» Москва машиностроение 1989 г.
Нефедов Н.Е. «Сборник задач примеров по резанию металлов и режущего инструмента» Москва машиностроение 1977 г.
Методические указания по расчету приспособлений».
Ансеров М.А. «Приспособления для металлорежущих станков» М.: Машиностроение 1975 г.
Бабук В.В. «Дипломное проектирование по технологии машиностроения» Минск высшая школа 1975 г.
Балобанов А.Н. «Краткий справочник технолога – машиностроения» М.: «Издательство станков» 1982 г.
Добрыднев И.С. «Курсовое проектирование по предмету технология машиностроения» Москва машиностроение 1985 г.
Маталин А.А. «Технология машиностроения» М.: Машиностроение 1985 г.
Егоров М.Е. «Основы проектирования машиностроительных заводов».
Добрыднев И.С. Курсовое проектирование по предмету «Технология машиностроения»: Учебн. пособие. - М.: Машиностроение 1985 г.
Титов Н.Д. Технология литейного производства.- М.: Машиностроение 1968 г.
Брюханов А.Н. Ковка и объемная штамповка: Учеб. пособие. - М.: Машиностроение 1975 г.
Методические указания к выполнению индивидуальной работы по дисциплине: «Организационно-технологическая подготовка производства» для студентов всех форм обучения по специальности 12.01.00 - «Технология машиностроения» (в электронном виде на магнитном носителе) Часть 1. Раздел «Технологичность конструкции изделий. Обработка резанием». Сост.: Бородкин В.В. Болдырев А.И. Бочаров В.Б. Кириллов О.Н. Чечета И.А. Воронеж: ВГТУ 1999 г.
Проектирование технологических процессов механической обработки деталей: Методические указания для выполнения курсовой работы по дисциплине «Технология машиностроения» В.Н. Самохвалов. - Самара: СамИИТ 2000 г.
Технология машиностроения (специальная часть). Б.Л. Беспалов Л.А. Глейзер И.М. Колесов и др.- М.: Машиностроение 1973 г.
Ковшов А.Н. Технология машиностроения: Учеб. для студ. машиностроительных специальн. вузов.- М.: Машиностроение 1987 г.
Общемашиностроительные нормативы времени вспомогательного на обслуживание рабочего места и подготовительно-заключительного для технического нормирования. Серийное производство. - М.: Машиностроение 1974 г.
Попилов Л.Я. Электрофизическая и электрохимическая обработка материалов. - М.: Машиностроение 1969 г.
Охрана труда в машиностроении: Учебник для машиностроительных вузов Под общей ред. Е.Я. Юдина С.В. Белова. – 2-е изд. перераб. и доп. – М.: Машиностроение 1983 г.
«Охрана окружающей среды» Под ред. С.В. Белова. – М.: Высш. шк. 1991 г.
Станочные приспособления: Справочник. Т. 1 Под ред. Б.Н. Вардашкина А.А. Шатилова. - М.: Машиностроение 1984 г.
Норенков И.П. Автоматизированное проектирование: Учеб. пособие. - М.: Изд-во МГТУ им. Н.Э. Баумана 2000 г.
Худобин Л.В. Гурьянихин В.Ф. Берзин В.Р. Расчет и проектирование специальных средств технологического оснащения в курсовых и дипломных проектах: Учеб. пособие. - Ульяновск: УлГТУ 1997 г.
ИНФОРМАЦИОННЫЙ ЛИСТ 1.frw

изготовления корпусапревентора кольцевого ПУГ-180х21-10-00
А Установить и после обработки снять деталь
Подрезать торец размера 2.
Точить диаметр 3 на размер 4
. Точить диаметр 6 на размер 7
Точить диаметр 1 на размер 9
Точить диаметр 13 выдержать размеры 12
выполнить радиусы 14 и 15 обеспечивается программой.
Расточить отверстие 17.
А Установить и после обработки снять деталь.
Подрезать торец размера 1;
Точить диаметр 2 на проход;
. Точить диаметр 4 выдержать размер 3;
Точить диаметр 6 выдержать размер 5;.
Точить диаметр 7 выдержать размер 8
выполнить радиус 11;
Точить диаметр 9 выдержать размер 8.
К.01.4227.000-06 Т15К6 ГОСТ 21066-75
К.01.4207.000.10 Т15К6 ГОСТ 20872-75
К.01.4204.000-12 Т15К6 ГОСТ 20874-75
Штангенциркуль ШЦ- I-250-0
ГОСТ 166-75;Штангенциркуль ШЦ- II-1000-0
ГОСТ 166-75;Штангенглубиномер ШГ-1000-0
ГОСТ 166-75;Штангенглубиномер
ГОСТ 162-75;Штангенциркуль ШЦ- II-630-0
Штангенглубиномер ШГ-250-0
ГОСТ 162-75; Штангенциркуль ШЦ-II-250-0
угломер оптический ОУ ГОСТ 11197-7;шаблоны радиусные 6060-3340; 6060-4303;6060-4305;
Выполнять по технологии заготовительного
приспособление Р6310-01989-00-000-00СБ
Резец К.01.4227.000-06 Т15К6 ГОСТ 21066-75
Резец К.01.4207.000-11 Т15К6 ГОСТ 20872-75
Резец К-01-3637-000 Т15К6 ГОСТ 20872-75
Резец К.01.4204.000-12 Т15К6 ГОСТ 20874-75
Штангенциркуль ШЦ- II-1000-0
Штангенглубиномер ШГ-630-0
ГОСТ 162-75;нутромер микрометрический НМ-600 ГОСТ 10-88;
Зачистить заусенцы после механической обработки
Разметить деталь поз. 1 под приварку детали поз.2
Выполнить подогрев и сварку
по технологии сварочного цеха
Термообработать сборочную единицу по
технологии термического цеха
А. Выставить деталь биение поверхности 6 не более 0
Точить поверхность 1; выдержать размер 10;
допуск перпендикулярности 8 обеспечивается обработкой
Точить диаметр 3; выдержать размер 9; радиус 7
обеспечивается программой
Точить канавку Д; допуск биения 5 обеспечивается
обработкой за один установ.
Расточить диаметр 11.
Резец К.01.4227.000-06 Т15К6 ГОСТ 21066-75;
Резец К.01.4207.000-10 Т15К6 ГОСТ 20872-75;
Резец 6163-1879-05 Т15К6; резец 6161-05062-01 Т15К6;
Штангенциркуль ШЦ-II-300-0
ГОСТ 166-75;штангенглубиномер ШГ-160-0
Штангенциркуль ШЦ- II-630-0
ГОСТ 166-75; штангенциркуль ШЦ-I-125-0
нутромер микрометрический НМ-600 ГОСТ 10-88;фаскомер 6027-3150;фаскомер 6027-3154;
Калибр 6084-10651-12; меритель 6002-03147;
глубиномер 6027-2269; шаблон 6035-02994;микрометр МК 300-400 ГОСТ 6507-90
Станок мод. 120DS160
Удалить с поверхности детали выплески от сварки.
структура.cdw

по изготовлению нестандартного
и монтажу технологического
и эксплуатации технологического
смазочного хозяйства
технологического оборудования
и ремонтному хозяйству
по смазке оборудования
и ремонтному хозяйству
Инспектор по станкам
Слесарь-комплектовщик
Структура управления ремонтным хозяйством
машиностроительного завода
Отдел главного механика
ИНФОРМАЦИОННЫЙ ЛИСТ 2.frw

Точить торец размера 17;выдержать размер 6; угол 11
обеспечивается программой
допуск перпендикулярности 7
обеспечить установкой детали в приспособлении
Точить диаметр 5 на глубину 19
обеспечить установкой детали в приспособлении.
. Точить диаметр 1 на глубину 3.
выдержать размер 18 и размер 19.
радиусы 34 обеспечиваются
допуск биения обеспечивается обработкой
за один установ; выдержать размеры 10 и 8
Точить диаметр 20 выдержать размер 9
обеспечивается программой.
Точить диаметр 21 на глубину 23
сопряжения выполняются программой;
Точить диаметр 22 на глубину 25
выполняется программой.
Установить и после обработки снять деталь
А.Выставить деталь в ось шпинделя станка
по поверхности Е. Допустимое биение
Сверлить двенадцать отверстий 1
равнорасположенных на диаметре 2
Резец К.01.4227.000-06 Т15К6 ГОСТ 21066-75;резец К.01.4283.000-01 Т30К4 ГОСТ20872-75
Резец К.01.4207.000.10 Т15К6 ГОСТ 20874-75; Резец 2130-0323 Т16К6 ГОСТ18884-73;
Резец К.01.4283.000 Т30К4 ГОСТ20872-75; резец 6163-1879-05; Резец в оправку 6162-04792 Т15К6.
Штангенциркуль ШЦ- I-250-0
ГОСТ 166-75;Штангенглубиномер ШГ-1000-0
Штангенглубиномер ШГ-630-0
ГОСТ 162-75;Штангенциркуль ШЦ- II-630-0
ГОСТ 166-75;планка 6072-0495;
Штангенглубиномер ШГ-400-0
ГОСТ 162-75; Штангенциркуль ШЦ-II-250-0
ГОСТ 166-75; нутромер микрометрический НМ-600ГОСТ 10-88;
угломер оптический ОУ ГОСТ 11197-7; штангенглубиномер ШГ-160-0
ГОСТ 162-75;штангенциркуль специальный 6027-4284;
губки сменные 6080-0780-01; штангенциркуль ШЦ-II-250-0
ГОСТ 166-75;шаблон радиусный 6060-2796;
Штангенциркуль специальный 6027-04599; губки сменные 6080-027755-00; Калибр пазовый 6060-06149-00Пр; калибр пазовый 6060-06149-01НЕ 9
приспособление Р6310-01990-00-000-00СБ
Оправка 6210-1066-02
Станок мод. СКР СВКоZ 1400х2240
ЧПУ SINUMERIK 840Di
Часы индикаторные ИЧ-10 ГОСТ 577-88 ;
штангенциркуль ШЦ-II-400-0
калибр пробка 6022-07845
Станок мод. СКР СВКоZ
Р6310-01990-00-000-00СБ
А. Установить и после обработки снять деталь
А. Выставить деталь в ось шпинделя станка
по поверхности 1 допустимое биение
Фрезеровать 75% первого витка прямоугольной
резьбы по высоте профиля
контроль по цифровой
индикации и визуально.
Сверлить пять отверстий 4 на глубину 2 вид Г
контроль по цифровой
Фреза 2223-0047 ГОСТ 17026-71;
штангенциркуль ШЦ-I-125-0
калибр пробка 202.8133-1074-6Н СТП 202.59.77
Станок Горизонтально-
Штангенциркуль ШЦ-I-125-0
калибр пробка 6052-1033-02;Коническая калибр пробка 6052-00665;
Сверло 6103-1296-01;Зенкер 6111-04798-05;
Зенкер 6116-01276-02;Зенкер 6116-01220-01;
Комплект метчиков К 1
Сверлить два отверстия 1 выдержать размеры
и 3 контроль по оптическим линейкам станка
Зенкеровать диаметр 5 на глубину 4
Зенкеровать диаметр 5 на глубину 4 коническим
Зенкеровать фаску 7;
Нарезать резьбу 8 на станке с поджатием
. Зачистить заусенцы и притупить острые
нарезать резьбу в пяти отверстиях М12-6Н
Разработка технологии и технологического оснащения для
изготовления корпуса кольцевого превентора
Станок мод. 120DS160
ПРЕВЕНТОР ЛИСТ-1 с моделью.cdw

Механические свойства от плавки :
для поперечного направления волокон.
4 255 HB- 100% -гр.6 -ОСТ 92-1311-77.
Электроды тип Э50А ГОСТ 9467-75.
Сварные соединения по 202.25290.00002.
Уровень качества PSL2 для швов не радотающих под давлением.
После сварки провести отпуск. 3
Неуказанная шероховатость обрабатываемых поверхностей
* Размеры обеспечиваются инструментом.
** Размеры для справок.
Срезать 75% первого витка прямоугольной резьбы по высоте
Контроль поверхности И магнитный..
Покрыпие : Хим. Окс. прм.
Маркировать : 7 116" - 3000-R 45.
Маркировать : "Открыто ".
Маркировать : "Закрыто ".
Маркировать действительное значение твердости.
Маркировать ударным способом клеймами "U"-образным профилем
шрифтом 5 - Пр.3 ГОСТ 26.020-80.
Контроль качества по техническим условиям API 6A.
Уровень качества PSL2.
Разработка технологии и средств технологического оснащения
для изготовления корпуса превентора кольцевого ПУГ-180х21-10-00
Содержание.doc
2Характеристика материала заготовки
3Выбор метода получения заготовки
Технологическая часть
1Обоснование маршрутной технологии изготовления детали
3Выбор технологической оснастки
4Расчет промежуточных припусков допусков и размеров заготовки по укрупненным нормативам
5Расчет режимов резания
6Обоснование и разработка технологического процесса (технологический процесс смотреть в приложении)
Конструкторская часть
1Выбор способа базирования детали
2Расчет коэффициента надежности закрепления детали
3Расчет потребных сил зажима
4Описание работы приспособления для токарно-карусельных операций
5Описание одного мерительного инструмента или контрольного приспособления
Производственная часть
1Определение потребного количества оборудования
2Определение потребного количества основных рабочих
3Определение потребного количества вспомогательных рабочих инженерно-технических работников и младшего обслуживающего персонала
Организационная часть
1Планирование размещения оборудования и рабочих мест на участке механического цеха
2Организация транспортировки изделий на участке
3Проектирование и организации рабочих мест
4Организация инструментального хозяйства
5Организация технического контроля
6Организация ремонта оборудования на участке
7Разработка мероприятий по охране труда ТБ противопожарной защите
1Определение затрат на основные материалы
2Расчёт фонда заработной платы основных и вспомогательных рабочих
3Расчёт цеховых расходов на силовую электроэнергию сжатый воздух воду
4Расчёт затрат на амортизацию оборудования
5Технико-экономические показатели участка
6Технико-экономические показатели
7Расчет показателей экономической эффективности проекта
Использованная литература
спецификация приспособления лист 2.cdw

ПРЕВЕНТОР ЛИСТ-1.cdw

Механические свойства от плавки :
для поперечного направления волокон.
4 255 HB- 100% -гр.6 -ОСТ 92-1311-77.
Электроды тип Э50А ГОСТ 9467-75.
Сварные соединения по 202.25290.00002.
Уровень качества PSL2 для швов не радотающих под давлением.
После сварки провести отпуск. 3
Неуказанная шероховатость обрабатываемых поверхностей
* Размеры обеспечиваются инструментом.
** Размеры для справок.
Срезать 75% первого витка прямоугольной резьбы по высоте
Контроль поверхности И магнитный..
Покрыпие : Хим. Окс. прм.
Маркировать : 7 116" - 3000-R 45.
Маркировать : "Открыто ".
Маркировать : "Закрыто ".
Маркировать действительное значение твердости.
Маркировать ударным способом клеймами "U"-образным профилем
шрифтом 5 - Пр.3 ГОСТ 26.020-80.
Контроль качества по техническим условиям API 6A.
Уровень качества PSL2.
ЧЕРТЕЖ ШТАНГЕЛЯ С ГУБКАМИ.cdw

Отклонение от перпендикулярности плоскости А от Б не более 0
Отклонение от параллельности плоскостей Б между собой не более 0
Поверхности А лежат в одной плоскости в пределах 0
Остальные ТУ по ГОСТ 166-73.
Цементировать глубиной 0
Размер L=120 должен быть одинаков на обеих губках
обработать одновременно.
при ремонте должен быть равен целому числу десятых долей миллиметра и замаркировать
Острые кромки притупить R 0
Маркировать чертежный номер
Планировка цеха.frw

для механической обработки детали
Пути и мостовой кран
грузоподъемностью 5 тс
установленные на пролетах производственного
условно не показаны.
ПРЕВЕНТОР ЛИСТ2.cdw

ЧЕРТЕЖ ШТАНГЕЛЯ.cdw

Отклонение от перпендикулярности плоскости А от Б не более 0
Отклонение от параллельности плоскостей Б между собой не более 0
Поверхности А лежат в одной плоскости в пределах 0
Остальные ТУ по ГОСТ 166-73.
ПРЕВЕНТОР с заготовкой.cdw

Механические свойства от плавки :
для поперечного направления волокон.
4 255 HB- 100% -гр.6 -ОСТ 92-1311-77.
* Размеры для справок.
Специф на планировку цеха.frw

ПРИСПОСОБЛЕНИЕ для установки.cdw

контроль и эксплуатация по СТП 202.20.3204-77
Спецификация приспособления лист 1.frw

Специф. на штангенциркуль.frw

ПРЕВЕНТОР ЛИСТ-1 с заготовкой.cdw

Механические свойства от плавки :
для поперечного направления волокон.
4 255 HB- 100% -гр.6 -ОСТ 92-1311-77.
Электроды тип Э50А ГОСТ 9467-75.
Сварные соединения по 202.25290.00002.
Уровень качества PSL2 для швов не радотающих под давлением.
После сварки провести отпуск. 3
Неуказанная шероховатость обрабатываемых поверхностей
* Размеры обеспечиваются инструментом.
** Размеры для справок.
Срезать 75% первого витка прямоугольной резьбы по высоте
Контроль поверхности И магнитный..
Покрыпие : Хим. Окс. прм.
Маркировать : 7 116" - 3000-R 45.
Маркировать : "Открыто ".
Маркировать : "Закрыто ".
Маркировать действительное значение твердости.
Маркировать ударным способом клеймами "U"-образным профилем
шрифтом 5 - Пр.3 ГОСТ 26.020-80.
Контроль качества по техническим условиям API 6A.
Уровень качества PSL2.
чертеж губок.cdw

Размер L=120 должен быть одинаков на обеих губках
обработать одновременно.
при ремонте должен быть равен целому числу десятых долей миллиметра и замаркировать
Острые кромки притупить R 0
Маркировать чертежный номер
Рекомендуемые чертежи
- 24.01.2023
- 24.01.2023
- 24.01.2023
- 24.01.2023