Проектирование АТП для перевозки 1350 тысяч тонн грузов




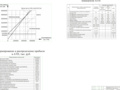
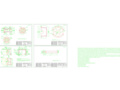
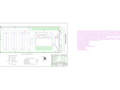
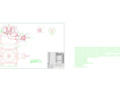
- Добавлен: 25.01.2023
- Размер: 5 MB
- Закачек: 0
Описание
Состав проекта
![]() |
![]() |
![]() ![]() ![]() |
![]() |
![]() ![]() ![]() ![]() |
![]() ![]() ![]() ![]() |
![]() ![]() ![]() ![]() |
![]() ![]() ![]() ![]() |
![]() ![]() ![]() ![]() |
![]() ![]() ![]() ![]() |
![]() ![]() ![]() ![]() |
![]() ![]() ![]() ![]() |
Дополнительная информация
Записка.doc
ФЕДЕРАЛЬНОЕ АГЕНСТВО ПО ОБРАЗОВАНИЮ
Государственное образовательное учреждение высшего
профессионального образования
МОСКОВСКИЙ ГОСУДАРСТВЕННЫЙ ОТКРЫТЫЙ УНИВЕРСИТЕТ
РАСЧЕТНО-ПОЯСНИТЕЛЬНАЯ ЗАПИСКА
К ДИПЛОМНОМУ ПРОЕКТУ
ФакультетАвтомеханический
КафедраАвтомобили и автомобильное хозяйство
Специальность190601 Автомобили и автомобильное хозяйство
ТЕМА ДИПЛОМНОГО ПРОЕКТА
Проектирование АТП для перевозки 1350 тыс. т. грузов
Консультант по безопасности и
Консультант по организационно-
Допустить дипломный проект к защите
в Государственной аттестационной комиссии
Эксплуатационная часть
2. Характеристика района перевозок
2.1. Общая характеристика района перевозок
2.2. Характеристика корреспондирующих пунктов и перевозимых грузов
2.3. Характеристика автотранспортной сети района перевозок
3. Шахматная таблица корреспонденций и схема грузопотоков
3.1. Шахматная таблица корреспонденций
3.2. Схема грузопотоков
4. Обоснование и выбор типа и модели подвижного состава
4.1. Выбор типа подвижного состава
4.2. Выбор модели подвижного состава
5 Выбор места расположения АТП
6. Построение маршрутов перевозок
7.2.Технико-эксплуатационные показатели работы подвижного состава
8. Технология и организация перевозок грузов
9 Организация работы подвижного состава и водителей на линии
10. Производственная программа АТП по эксплуатации подвижного состава
Технологическая часть
1. Технологический расчет
1.1. Исходные данные для проектирования
1.2. Расчет программ технического обслуживания и ремонта
1.3. Распределение объемов работ ТО и ТР по видам работ
1.4. Расчет объемов работ по самообслуживанию
1.5. Обоснование режима работы и принимаемых форм организации производства
1.6. Расчет численности ремонтно-обслуживающего персонала
1.7. Формирование производственной структуры технической службы АТП
1.8. Расчет линий и постов в производственных зонах и отделениях
1.9. Подбор технологического оборудования и оснастки для производственных зон и отделений
1.10. Расчет площадей производственных зон и отделений
1.11. Расчет хранимых запасов и площадей складских помещений
2. Обоснование планировочных решений
2.1. Обоснование планировочного решения производственного корпуса
2.2 Разработка генерального плана АТП
3 Организация технология работ и планировочные решения агрегатного участка
3.1 Организация работ агрегатного участка
3.2 Технология работ агрегатного участка
3.3 Обоснование планировочного решения агрегатного участка
Конструкторская часть
1 Требование к разработке
2 Технологичность конструкции пресса
3 Принцип работы пресса
4 Расчёт рабочего усилия пресса
5 Прочностной расчёт рабочих деталей пресса
6 Оценка эффективности использования разработки в
1 Описание ремонтируемого узла
2 Технология восстановления шатуна
Безопасность и экологичность проектных решений
1. Выбор и краткая характеристика объекта анализа
2. Анализ потенциальной опасности участка для персонала и корпуса
для окружающей среды
2.1. Анализ потенциально опасных и вредных
2.2. Анализ производственных воздействий производственного корпуса на окружающую среду
2.3. Анализ возможности возникновения в производственном корпусе чрезвычайных ситуаций
3. Классификация помещения и производства в производственном корпусе
4. Мероприятия и средства по обеспечению безопасности труда
4.1. Мероприятия по безопасности труда
4.2. Мероприятия по производственной санитарии
5. Мероприятия и средства защиты окружающей среды от проектируемого АТП
5.1. Очистка воздуха
5.2. Очистка производственных вод
6. Мероприятия и средства по обеспечению безопасности в чрезвычайных ситуациях
6.1. Обеспечение взрывопожаробезопасности
Организационно-экономическая часть
1. Организационный раздел
1.1. Организационно-правовая форма собственности предприятия
1.2. Организационная структура предприятия
2. Экономический раздел
2.1. Расчет стоимости основных производственных фондов
2.2. Расчёт потребности АТП в материальных затратах
2.3. Расчет численности и фонда оплаты труда по категориям работающих
2.4. Затраты на амортизацию подвижного состава
2.5. Прочие затраты
2.6. Смета эксплуатационных затрат
2.7. Калькуляция себестоимости перевозок
2.8. Расчёт потребности нормируемых оборотных средств
2.9. Расчёт финансовых показателей
2.10. Расчёт показателей использования производственных фондов
2.11. Оценка экономической эффективности инвестиций
2.12. Расчёт точки безубыточности
Список используемой литературы
Эксплуатационная часть
Исходными данными для эксплуатационной части дипломного проекта являются схема корреспонденций с указанием расстояний между пунктами процентное распределение объемов перевозок между корреспондирующими пунктами наименование грузов общий объем перевозок (сумма по всем корреспонденциям).
Рис. 1 1. Схема дорожной сети перевозок
Общий объем перевозок определен заданием на дипломное проектирование и составляет 1350000 т. грузов в год.
Таблица 1.1 Распределение объёма перевозок
Структура гру- зопотоков %
Объём перевозок тыс. т.
Навалочные и промышленные
2. Характеристика района перевозок
2.1. Общая характеристика района перевозок
В качестве географического расположения района перевозок учитывая довольно большой объем перевозок принимается город европейской части России. Перевозки осуществляются в городских и пригородных условиях. Предприятие расположено в зоне умеренного климата. Рельеф местности равнинный и слабохолмистый.
Район перевозок является экономически развитым. В нем присутствуют промышленные предприятия предприятия агропромышленного комплекса железнодорожные станции.
Грузовые потоки определяются по исходным данным и представлены в табл. 1.2.
Таблица 1.2 Грузовые потоки района перевозок
Расстояние перевозки lпг км
годовой объём перевозки Q тыс. т.
Годовой грузооборот P=Q·lпг тыс. т·км
Среднее расстояние перевозки грузов (lпг) определяется делением суммарного грузооборота (Робщ) на общий объем перевозок (Qобщ):
lпг = Робщ Qобщ = 11333251350 = 8395
2.2. Характеристика корреспондирующих пунктов и перевозимых грузов
Характеристика грузообразующих и грузопоглощающих пунктов даётся исходя из номенклатуры ввозимых и вывозимых грузов объёмов их перевозок.
гдеQp -расчётное количество груза т;
Qф- фактическое количество груза т;
γс - коэффициент статического использования грузоподъёмности единицы подвижного состава для данного груза.
В пункте В находится фабрика по переработке зерна и корма откуда вывозятся по 405 тыс. тонн крупы в пункты Е и Д а также 54 тыс. тонн комбикорма в год. В пункте А расположены склады металлического проката откуда на строительные объекты вывозятся в пункты В и Е вывозятся в год по 162 тыс. тонн и 243 тыс. тонн металлопроката. В пункте Е расположен карьер из которого выкапываются и отвозятся в пункты В С и Д уголь песок и торф. Дороги между пунктами на некоторых участках асфальто-бетонные а в большинстве щебёночные поэтому категорию дорог принимаем – II. Количество рабочих дней АТП в году принимаем 357.
Таблица 1.3 Характеристика грузов предъявленных к перевозке
Годовой объём перевозок тыс т.
Суточный объём перевозок т.
Коэффициент статического использования грузоподъёмности
Модель используемого подвижного состава
Время простоя в расчёте на одну поездку
2.3. Характеристика автотранспортной сети района перевозок
Таблица 1.4 Характеристика автомобильных дорог района перевозок
Участок автомобильных дорог
Тип дорожного покрытия
Расчётная (техническая) скорость движения подвижного состава кмч
3. Шахматная таблица корреспонденций и схема грузопотоков
Грузовые потоки в районе перевозок изучаются по шахматной таблице и схеме грузопотоков корреспондирующих пунктов
3.1. Шахматная таблица корреспонденций
Шахматная таблица грузопотоков корреспондирующих пунктов составляется по годовым объёмам перевозок.
По каждой корреспонденции в шахматной таблице указываются: наименование груза годовой объём перевозок в фактическом (Qфгод) и расчётном значениях (Qргод) отношение которых дает значение коэффициента использования грузоподъемности γс. Исходными данными для составления шахматной таблицы являются годовые объёмы перевозок грузов (таблица 1.3).
Грузообразующие пункты
Грузопоглащающие пункты
Итого по вывозу тыс. т.
Итого по ввозу тыс т
3.2. Схема грузопотоков
Схема грузопотоков корреспондирующих пунктов строится по данным шахматной таблицы и на основе схемы дорожно-транспортной сети района перевозок. Схема выполняется с соблюдением необходимых правил.
Схема грузопотоков есть графическое изображение структуры и мощности грузопотоков.
Для построения схемы грузопотоков необходимо иметь данные по:
-объёму ввоза и вывоза конкретного вида груза для каждой грузовой точки;
-коэффициенту статического использования грузоподъёмности для каждого груза;
-территориальному размещению грузовых точек и расстоянию между ними.
Масштаб необходим для построения на схеме расстояний между грузовыми пунктами дорожной сети района перевозок.
Схема грузопотоков строится следующим образом. Прежде в выбранном масштабе откладываются длины участков дорожной сети на которых осуществляются перевозки. Далее в виде стрелок откладываются грузовые потоки каждого направления с правой стороны автомобильной дороги т.е. по ходу движения подвижного состава.
Рис. 1 2. Схема грузопотоков
4. Обоснование и выбор типа и модели подвижного состава
4.1. Выбор типа подвижного состава
Подвижной состав должен соответствовать виду свойствам и характеру груза условиям эксплуатации способу производства погрузочно-разгрузочных работ.
Для навалочных грузов подбираем самосвалы а для промышленных бортовые фургоны. По способу производства погрузочно-разгрузочных работ (механизированный с помощью погрузчика) данный тип подвижного состава является приемлемым. Данные типы автомобилей соответствуют условиям эксплуатации (дорожным и климатическим) в районе перевозок.
4.2. Выбор модели подвижного состава
По каждому из типов подвижного состава с учётом величины годовых объёмов перевозок среднего расстояния перевозки дорожных и погрузочно-разгрузочных условий предварительно намечаются к эксплуатации не менее двух моделей подвижного состава.
Для определения конкретной модели подвижного состава используется метод выбора по комбинированному (обобщенному) показателю.
Метод выбора по комбинированному (обобщенному) показателю заключается в следующем. Для сравниваемых моделей устанавливается перечень наиболее значимых с точки зрения эксперта характеристик значения которых сводятся в таблицу исходных данных. В качестве характеристик примем стоимость автомобиля часовую производительность в т·км ресурс автомобиля средний межлинейный расход топлива и мощность двигателя. Производительность автомобиля подсчитывается по формуле:
Wp = (q · γ · lпг) (tпр + lпг ( · Vт)) т·кмч
где q – грузоподъемность автомобиля (т);
γ –коэффициент статического использования грузоподъемности;
– коэффициент использования пробега;
tпр – время погрузки-разгрузки ч;
Vт – техническая скорость (принимается по табл.1.4) (кмч).
Коэффициент использования пробега заранее неизвестен поэтому примем условное значение = 05.
Таблица 1.6 Исходные данные для расчёта производительности АТС (Бортовые автомобили)
Обозначение показателей
Коэффициент использования пробега
Техническая скорость кмч
Время погрузки-разгрузки час
Коэффициент использования грузоподъёмности
Среднее расстояние перевозки груза км
Производительность т кмч
Таблица 1.7 Исходные данные для расчёта производительности АТС (Самосвалы)
Таблица 1.8 Исходные данные для выбора модели АТС (Бортовые автомобили)
Производительность автомобиля т кмч
Средний межлинейный расход топлива л100 км
Мощность двигателя л.с.
Таблица 1.9 Исходные данные для выбора модели АТС (Самосвалы)
Все пять рассматриваемых характеристик имеют различные единицы измерения. Поэтому их абсолютные натуральные показатели надо представить в условных относительных единицах по единичной масштабной шкале. Для этого по каждому показателю выберется наилучшее из всех значение и принимается за единицу. Остальные значения представлены относительными величинами которые будут отображать степень ухудшения (отдаления) для данного показателя по сравнению с наилучшим.
Предварительно требуется выбрать вес или важность (значимость) каждой характеристики моделей АТС. В качестве наиболее важного критерия принимается стоимость АТС так как от ее значения будут зависеть капиталовложения в проектируемое АТП. Поэтому ей присвоено значение веса равное единице. Вторым по значимости является производительность автомобиля так как при большей производительности как правило обеспечивается более низкая себестоимость перевозок. Характеристикой которой присвоено значение веса равное трём выбран ресурс автомобиля который будет определять срок службы и обновление парка подвижного состава. Следующими по порядку значимости идут расход топлива и мощность двигателя которые косвенно определяют затраты на выполнение транспортной работы и динамические качества автомобиля.
Таблица 1.10 Результаты расчётов выбора модели АТС (Бортовые автомобили)
Стоимость тыс. руб.
Производительность автомобиля т·кмч
Средний межлинейный расход
Сумма взвешенных значений
Таблица 1.11 Результаты расчётов выбора модели АТС (Самосвалы)
Наибольшее значение суммарного показателя соответствует наилучшей модели подвижного состава. В приведенном примере это модель КАМАЗ-53215 относящиеся к типу "Бортовые автомобили"и МАЗ-5516А5-375 относящиеся к типу "Самосвалы".
5 Выбор места расположения АТП
Для заданного района перевозок производится выбор места расположения автотранспортного предприятия. Выбор обосновывается несколькими критериями.
АТП целесообразно располагать в пункте которому соответствуют:
-максимальный объём вывоза грузов;
-максимальный объём ввоза грузов;
-максимальный суммарный годовой объём ввоза и вывоза грузов;
-примерное равенство годовых объёмов ввоза и вывоза (для каждого корреспондирующего пункта рассчитывается абсолютная величина разности годовых объёмов вывоза и ввоза грузов);
-центральное расположение в районе перевозок (для каждого пункта дорожно-транспортной сети рассчитывается сумма расстояний от этого пункта до всех остальных пунктов).
Значения критериев для различных пунктов района перевозок заносятся в таблицу 1.12.
Таблица 1.12 Выбор места расположения АТП
суммарный годовой объём ввоза и вывоза
разность годовых объёмов ввоза и вывоза
центральное расположение в районе перевозок
Средний ранг каждого пункта рассчитывался как простая средняя арифметическая величина соответствующих номеров рангов.
АТП целесообразно располагать в пункте для которого получено наименьшее значение среднего ранга. В нашем случае это пункт В. Для дальнейших расчетов примем пункт В.
6. Построение маршрутов перевозок
Одной из важных задач организации работы автомобильного транспорта является маршрутизация перевозок грузов т. е. определение порядка следования автотранспортных средств (АТС) между корреспондирующими пунктами в течение рабочего дня. Составление и выбор маршрутов позволяют: максимально производительно использовать пробег подвижного состава обеспечить наибольшую загрузку транспортных средств на маршруте рационально организовывать труд водителей повышать производительность единицы подвижного состава уменьшать число АТС для перевозок постоянного количества груза снижать эксплуатационные затраты улучшать диспетчерское руководство перевозками и контроль за движением подвижного состава соблюдать установленные правила безопасности и др.
Маршруты составляют на сутки по средним или конкретным объемам перевозок в расчетных массах для группы грузов перевозимых одним типом маркой и моделью подвижного состава.
Предъявленные к перевозке грузы делятся на две группы: перевозимые автомобилями типа "Бортовые автомобили" - КАМАЗ-53215 и типа "Самосвалы" - МАЗ-5516А5-375.
Маршрутизация может проводиться различными методами: эвристическим топографическим моделирующим и другими. Наиболее распространенным простым и доступным является топографический метод маршрутизации. Этот метод основан на использовании географической карты плана города условной схемы дорожной сети района перевозок на которых указано месторасположение грузообразующих и грузопоглощающих пунктов расстояние между ними автодороги а также суточные грузопотоки в расчетных массах по всей номенклатуре грузов перевозимых одной моделью АТС.
Маршрутизация начинается с построения схемы грузопотоков по группам грузов с указанием вида груза и суточного объема перевозок. Пункт расположения АТП выделяется условным знаком "чёрный треугольник". На схеме указываются расстояния участков дорожной сети.
Первая группа грузов являются промышленные грузы:
Рис. 1.3 Схема грузопотоков для первой группы.
По карте находят ближайший от АТП грузообразующий пункт – пункт первой подачи АТС под погрузку. Он будет первым начальным для первого маршрута. По данной схеме ближайший грузообразующий пункт это пункт В. Затем выбирается любой грузопоток из данного пункта. На выбор грузопотока влияет только возможность организации маршрута с обратным груженым пробегом. Если имеется грузопоток позволяющий организовать маршрут с полным использованием пробега то есть следующий грузопоток будет идти от пункта разгрузки до пункта погрузки предыдущего то выбирают первым этот грузопоток. В нашем случае начинаем первый маршрут с пункта В.
Выбираем первый маршрут:
В первом маршруте перевозим 18908 т. комбикорма и металла.
где А Е В - пункты маршрута; 18908 - мощность маршрута т.
Рис. 1.4 Определение первого маршрута
Оставшиеся маршруты первой группы развозятся без комбинирования по схеме туда-обратно.
Рис. 1.5 Определение оставшихсямаршрутов первой группы
Следующий шаг определение маршрутов для второй группы грузов (навалочных):
Рис. 1.6 Схема грузопотоков для второй группы.
Навалочные грузы разводятся также без комбинирования ввиду невозможности совмещения более одной ездки с грузом за оборот каждый отдельно по своему маршруту.
Информация о конкретном маршруте представлена на его схеме. Эффективность работы подвижного состава по маршрутам оценивается технико-эксплуатационными показателями.
Схема маршрута содержит исходную информацию для расчёта показателей маршрута.
Для каждого из маршрутов ниже приведены: номер символьная запись маршрута мощность грузопотока на маршруте (Qм) модель и грузоподъёмность эксплуатируемого подвижного состава.
Рис. 1.7 Схема первого маршрута
Перевозка грузов осуществляется на автомобиле КАМАЗ-53215 который относится к типу "Бортовые автомобили". Грузоподъемность автомобиля 11.
Мощность грузопотока на маршруте Qм = 18908 т.
Расстояние перевозки груза ln = 106 км.
Техническая скорость на участке Vт = 37 кмч.
Перевозится Qф = 18908 т металла и 15126 т комбикорма в в сутки.
Расчетный суточный объем перевозок Qр = 18908 т.
Коэффициент статического использования грузоподъёмности γс = 09.
7.2.Технико-эксплуатационные показатели работы подвижного состава
Характеристика работы АТС на маршруте включает расчет технико-эксплуатационных показателей единицы подвижного состава и в целом по маршруту.
А. Расчет технико-эксплуатационных показателей единицы подвижного состава
Время одного оборота единицы подвижного состава по маршруту
tоб=j ( lj Vт) + i tn-pi = (54 + 52 + 66) 37 + (09 + 09) = 645 час
где tп-рi — время простоя единицы подвижного состава под погрузкой и разгрузкой за i-ю ездку час.
Количество оборотов единицы подвижного состава по маршруту за рабочий день(n).
n=Тнп tоб = 8 645 = 124
где Тнп= 8 час-принятый (планируемый) режим работы подвижного состава на маршруте час. Принимаем n = 1.
Количество ездок совершаемое единицей подвижного состава по маршруту за рабочий день (z).
где i = 2- количество ездок за один оборот единицы подвижного состава по маршруту (определено по символьной записи и схеме маршрута).
Общий пробег единицы подвижного состава за рабочий день(Lобщ)
Lобщ = L'o + Lоб · (n -1) + Lобпоб + L''o = 0 + 172 · (1 - 1) + 106+ 66 = 172 км
где L'o= 0 км - первый нулевой пробег ;
L''o= 66 км - второй нулевой пробег ;
Lоб = 172 км -пробег единицы подвижного состава за один оборот;
Lобпоб=Lоб- li =172 – 66 = 106 км - пробег единицы подвижного состава на последнем обороте движения подвижного состава по маршруту (определяется как разность между пробегом за оборот и пробегом без груза на последней ездке маршрута) км.
Пробег единицы подвижного состава с грузом за рабочий день(Lг)
Lг = Lгоб · n = n · Σi lг= 106 · 1 = 106 км.
где Σi lг =106 км - пробег единицы подвижного состава с грузом за один оборот км
lг - пробег подвижного состава с грузом за i-ю поездку км.
Фактическое время нахождение единицы подвижного состава на маршруте (Тм)
Тм = tоб · (n - 1) + tnоб = 645 · (1 - 1) + 467 = 467 час
где tnоб = tоб - li Vт = 645 - 66 37 = 467 час - время последнего оборота при движении единицы подвижного состава по маршруту (определяется как разность между временем оборота единицы подвижного состава по маршруту и временем на пробег единицы подвижного состава без груза на последней ездке маршрута.) час.
В данном случае оборот состоит из пробега с грузом и холостого пробега. Пробег с грузом за последнюю ездку оборота не учитывается и остается только холостой пробег.
Время нахождения единицы подвижного состава в наряде(Тн)
Тн = t'o + Тм + t''o = 0 + 467 + 178 = 645 час где t'o и t''o - время затрачиваемое соответственно на первый и второй нулевые пробеги час
t'o = L'о Vм = 0 37 = 0 час.
t''o = L''o Vм = 66 37 = 178 час.
Время нахождения подвижного состава на линии (Тл)
Тл = Тн + tобед + tотд = 645 + 1 + 0 = 745 час.
где tобед - время обеда водителя час.
tотд - время отдыха водителя час.
Принимается перерыв на обед 1 час. Время отдыха принимается при непрерывном движении более 2-х часов. Так как время непрерывного движения автомобиля не превышает 2-х часов то время отдыха водителя равно нулю
Тр = Тн + tп-з + tм.о. = 645 + 027 + 008 = 68 час.
где tп-з — время на выполнение водителем подготовительно-заключительных работ (25мин. на каждый час Тн) час.;
tм.о. — время на проведение предрейсового медицинского осмотра водителя (до 5мин. в смену) час.
Б.В целом по маршруту определяются следующие показатели:
Количество подвижного состава потребное для эксплуатации на маршруте (Аэ)
Аэ = Qм (q · n) = 18908 (11 · 1) = 172 ед.
Коэффициент статического использования грузоподъёмности подвижного состава на маршруте в среднем за рабочий день
= Σiz Qф Σiz Qр = 170172 18908 = 09
Коэффициент динамического использования грузоподъёмности подвижного состава на маршруте в среднем за рабочий день
= Σiz Pфi Σiz Ppi = Σiz (Qф · li) Σiz (Qф · li) = 170172 · 106 18908 · 106 = 09
где Рфi и Рpi по ездкам маршрута соответственно фактический и возможный грузооборот т км.
Коэффициент использования пробега подвижного состава за рабочий день ()
= Lг Lобщ = 106 172 = 06
Средняя техническая скорость подвижного состава
на линии в течение рабочего дня
= Lобщ Тдв = Lобщ Tн - Σiz tn-pi = 172 (645 - 1 · 18) = 37 кмч.
где Тдв - время нахождения в движении единицы подвижного состава за рабочий день час.
Σiz tn-pi = n · Σi tn-pi = 1 · 18 = 18 час - суммарное время погрузки-разгрузки за сутки
= Lобщ Тн = 172 645 = 267 кмч.
Фактическая производительность единицы подвижного состава в тоннах(Wт) и тонно-километрах(Wткм) за время работы
Wт = n · q · Σi γci = 1 · 11 · 18 = 198 т.
Wт·км = n · q · Σi (γci · li) = 1 · 11 · (54 · 08 + 52 · 1) = 10472 т·км
Расчет технико-эксплуатационных показателей остальных маршрутов приведем в табличной форме. Сначала приводятся схемы маршрутов затем таблица показателей.
Рис. 1.8 Схема второго маршрута.
Рис. 1.9 Схема третьего маршрута.
Рис. 1.10 Схема четвёртого маршрута.
Рис. 1.11 Схема пятого маршрута.
Рис. 1.12 Схема шестого маршрута.
Рис. 1.13 Схема седьмого маршрута.
Рис. 1.14 Схема восьмого маршрута.
Рис. 1.15 Схема девятого маршрута.
Таблица 1.13 Технико-экономические показатели работы подвижного состава на маршрутах
Грузоподъемность qт.
Мощность грузопотока на маршруте Qмт.
Расстояние перевозки груза lег1 км.
Расстояние перевозки груза lег2км.
Холостой пробег lх1 км.
Холостой пробег lх2 км.
Техническая скорость на участке Vт1 кмч.
Техническая скорость на участке Vт2 кмч.
Фактический объем перевозок Qф1т.
Фактический объем перевозок Qф2т.
Расчетный суточный объем перевозок Qр т.
Коэффициент статического использования грузоподъёмности γс1
Коэффициент статического использования грузоподъёмности γс2
Время погрузки - разгрузки tп-р1 час.
Время погрузки - разгрузки tп-р2 час.
Принятый (планируемый) режим работы подвижного состава на маршруте Тпн час.
Количество ездок за оборот i
Первый нулевой пробег L0 км.
Второй нулевой пробег L0км.
Длина оборота Lоб км.
Пробег единицы подвижного состава на последнем обороте движения подвижного состава по маршруту Lпобоб км.
Время последнего оборота при движении единицы подвижного состава по маршруту tпоб час.
Время одного оборота единицы подвижного состава по маршруту tоб час.
Количество оборотов единицы подвижного состава по маршруту за рабочий день(n)
Принятое количество оборотов единиц подвижного состава по маршруту за рабочий день (n)
Количество ездок совершаемое единицей подвижного состава по маршруту за рабочий день (z)
Общий пробег единицы подвижного состава за рабочий деньLобщ км.
Пробег единицы подвижного состава с грузом за рабочий деньLг км.
Фактическое время нахождения единицы подвижного состава на маршрутеТм час.
Время нахождения единицы подвижного состава в нарядеТн час.
Время нахождения единицы подвижного состава на линии Тл час.
Фактическое время работы водителя Тp час.
Количество подвижного состава потребное для эксплуатации на маршрутеАэ
Коэффициент статического использования грузоподъёмности подвижного состава на маршруте в среднем за рабочий день γс
Коэффициент динамического использования грузоподъёмности подвижного состава на маршруте в среднем за рабочий день γд
Коэффициент использования пробега подвижного состава за рабочий день
Средняя техническая скорость движения подвижного состава на линии в течение рабочего дня Vт км
Средняя эксплуатационная скорость движения подвижного состава в течение рабочего дня Vэ км
Фактическая производительность единицы подвижного состава в тоннах Wт за время работы
Фактическая производительность единицы подвижного состава в тонно-километрах Wткм за время работы
8. Технология и организация перевозок грузов
Организация перевозок грузов осуществляется по централизованной форме. Централизованные перевозки грузов являются прогрессивным методом выполнения перевозочного процесса и эксплуатации подвижного состава. Они представляют собой организационную систему обеспечивающую четкое распределение обязанностей и ответственности всех участников транспортного процесса: грузоотправителей грузополучателей и автотранспортных организаций.
Технология централизованных перевозок заключаются в следующем:
перевозки грузов осуществляются одним автотранспортным предприятием на основании договоров;
заявки на перевозку груза представляются в автотранспортное предприятие грузоотправителями;
погрузка выполняется силами и средствами грузоотправителей а разгрузка — силами и средствами грузополучателей. Для работы используются погрузочно-разгрузочные механизмы;
выполнение транспортно-экспедиционных операций возлагается на автотранспортное предприятие. Грузоотправители при расчетах за перевозки груза уплачивают автотранспортному предприятию вместе со стоимостью перевозки и стоимость выполнения транспортно-экспедиционных операций;
автотранспортное предприятие вступает в договорные отношения только с грузоотправителями.
При централизованных перевозках автотранспортное предприятие выступает организатором процесса доставки груза получателям и осуществляет не только перевозку груза от отправителя до получателя но и все связанные с процессом перевозки транспортно-экспедиционные операции (прием груза и получение товарно-транспортных и других сопроводительных документов от грузоотправителей; охрана груза в пути; сдача груза грузополучателям и оформление товарно-транспортных документов) принимая на себя материальную ответственность за сохранность перевозимого груза.
Автотранспортное предприятие контролирует наличие и подготовку груза к перевозке состояние подъездных путей и обеспеченность погрузочно-разгрузочными механизмами. Проверяет своевременность прибытия автомобилей по установленному графику организует расстановку их под погрузку и разгрузку принимает меры по обеспечению загрузки автомобилей до полной их грузоподъемности и по предотвращению сверхнормативных простоев подвижного состава в пунктах погрузки и разгрузки. Поддерживает связь с диспетчерскими пунктами на погрузочных площадках грузоотправителей и контролирует выполнение оперативного плана перевозок по каждому объекту; принимает в случаях необходимости оперативные меры для переключения автомобилей с одного объекта на другой; ведет учет выполнения плана перевозок проверяет своевременность доставки груза получателям правильность оформления путевых листов и других товарно-транспортных документов.
Сводные приказы-наряды оформленные грузоотправителями составляют на пятидневку декаду а в отдельных случаях и на месяц квартал год на каждый пункт отправления отдельно. Сводные приказы-наряды подписанные ответственным лицом и заверенные печатью предоставляются на АТП не позднее чем за два дня до начала планируемого периода.
Расчеты за централизованные перевозки груза автотранспортное предприятие производит с грузоотправителями. Основанием для расчетов являются товарно-транспортные накладные. Стоимость выполненных экспедиционных операций включается отдельной строкой в счете за перевозку груза и оплачивается грузоотправителями одновременно с оплатой стоимости перевозки. При расчетах широко применяют усреднённые расстояния перевозок в систему централизованных расчетов.
9 Организация работы подвижного состава и водителей на линии
В процессе дипломного проектирования особое внимание требуют вопросы организации работы водителей на маршрутах и подвижного состава на линии.
Основным элементом позволяющим производить оперативное руководство и контроль над работой подвижного состава на линии служит график движения подвижного состава.
На графике отражаются все элементы транспортного процесса в пространственном и временном разрезе место нахождения автомобиля в конкретный момент времени.
Подготовительная работа для построения графика движения заключается в определении ряда характеристик маршрута: расстояния между точками дорожной сети(lj) скорости движения на этих участках(Vтj) времени нахождения автомобилей в наряде(Тн) и на линии(Тл) продолжительности обеда(tобед) и отдыха(tотд) водителей простоя подвижного состава под погрузочно-разгрузочными операциями по каждой ездке(tп-рi) количества автомобилей на маршруте(Аэ) интервалов движения подвижного состава (I).
Для построения графика движения выбирается маршрут с наибольшей длиной оборота. В нашем случае это маршрут № 1.
Расстояния между участками дорожной сети lВА = 54 км lАЕ = 52 км lЕВ = 66 км.
Техническая скорость на всех участках маршрута Vт = 37 кмч.
Время нахождения автомобилей в наряде Тн = 645 ч на линии Тл = 745 ч.
Время на обед tобед = 1 ч время погрузки равняется tп = 05 ч. времени разгрузки tр = 04 ч.
По расчету количество автомобилей на маршруте Аэ = 172.
Рис. 1.16 График движения подвижного состава по первому маршруту
Тл = 745 ч tоб = 645 ч Vт = 37 кмч n = 1 z = 2 tп = 05 ч tр = 04 ч Аэ = 172
10. Производственная программа АТП по эксплуатации подвижного состава
В целом по АТП рассчитываются средние технико-эксплуатационные показатели работы за рабочий день. К ним относятся:
Среднее время нахождения в наряде
= Σк (АДркгод · Тнк) Σк АДркгод = 520006 72128 = 721 час
где Тнк - время нахождения в наряде единицы подвижного состава на k м маршруте час.
АДркгод- автомобиле-дни работы k го маршрута за год автомобиле-дни:
АДркгод = Аэк · Дркгод автомобиле-дни
где Аэк - число автомобилей работающих на k-м маршруте автомобили;
Дркгод - число дней работы k-го маршрута за год дни.
Значение выражение Σк (АДркгод · Тнк) находится суммированием по всем маршрутам произведений автомобиле-дней работы в году соответствующего маршрута на время нахождения единицы подвижного состава в наряде Тн из табл. 1.13
Средняя грузоподъёмность единицы подвижного состава
= Σк (АДркгод · qнк) Σк АДркгод = 1216113 72128 = 1686 т
где qнк - номинальная грузоподъёмность единицы подвижного состава на k-м маршрутет.
Средний суточный пробег единицы подвижного
состава за рабочий день
сут = Σк (АДркгод · Lобщк) Σк АДркгод = 16424813 72128 = 22772 км
где Lобщк - общий пробег единицы подвижного состава за рабочий день на k-м маршруте км.
Средний коэффициент статического использования
с = Σк (АДркгод · Σiz Ффкi) Σк (АДркгод · Σiz Ффкi γcki)=39917114 51891672 = 077
γcki - коэффициент статического использования грузоподъёмности на i-й ездке k-го маршрута.
значение Σiz Ффкi представляет собой суточное фактическое количество груза перевезенного на k-м маршруте и находится суммированием строк Ффi из табл. 1.13. Затем полученное значение умножается на АДркгод. Значение (Σiz Ффкi γcki ) представляет собой суточное расчетное количество груза перевезенного на k-м маршруте и находится суммированием строк Ффi деленных на значение на γci соответствующей ездки из табл. 1.13
Средняя техническая скорость движения
м = Σк (АДркгод · Lобщк) Σк (АДркгод · Тдвк) = 16424813 443811 = 37 кмчас
Средняя эксплуатационная скорость движения
э = Σк (АДркгод · Lобщк) Σк (АДркгод · Тнк) = 16424813 520006 = 316 кмчас
Средний коэффициент использования
= Σк (АДркгод · Lгк) Σк (АДркгод · Lобщк) = 8063980 16424813 = 05
где Lгк - пробег единицы подвижного состава с грузом за рабочий день на k-м маршруте км.
Среднее время простоя подвижного состава
под погрузкой и разгрузкой за одну ездку
n-p = Σк (АДркгод · Σiz tn-pki) Σк (АДркгод · zk) = 7600244 10150938 = 075 час
zk - количество ездок совершаемое единицей подвижного состава по k-му маршруту за рабочий день.
Средний пробег единицы подвижного состава
е.г. = Σк (АДркгод · Σiz lе.г.ki) Σк (АДркгод · zk) = 8063980 101509 = 7944 км
Полученные средние показатели служат исходными данными для расчёта производственной программы по эксплуатации парка подвижного состава:
Пробег всего парка автомобилей за год (АLгод)
сут · Σк (АДркгод )= 16425052 км
Автомобиле-часы в наряде всего парка автомобилей за год (АЧн)
н · Σк (АДркгод )= 520045 а-ч
Исходя из режима работы каждого маршрута (количества рабочих дней в годуk-го маршрута Дркгод) и показателей транспортной работы за сутки устанавливается годовой объём перевозок (Qгодатп) и грузооборот (Ргодатп) и всего парка подвижного состава эксплуатируемого по всем маршрутам.
Qгодатп= Σк (Дркгод · Σiz Ффкi) = 1350001 т
Ргодатп= Σк (Дркгод · Σiz (Ффкi · lе.г.ki)) = 113332521 т·км
Таблица 1.14 Показатели производственной программы АТП по эксплуатации
Среднее время нахождения в наряде Тн час.
Средняя грузоподъемность подвижного состава q т.
Средний суточный пробег Lсут км.
Средний коэффициент статического использования грузоподъёмности γс
Средняя техническая скорость движения подвижного составаVт кмч.
Средняя эксплуатационная скорость движения подвижного составаVэ кмч.
Средний коэффициент использования пробега
Среднее время простоя подвижного состава под погрузкой и разгрузкой за одну ездку tп-р ч.
Средний пробег единицы подвижного состава с грузом за ездку lег км.
Количество автомобилей в эксплуатации Аэ
Пробег всего парка автомобилей за год Аlгод км.
Автомобиле-часы в наряде всего парка автомобилей за год АЧн а-ч.
Годовой объём перевозокQАТПгод т.
Годовой грузооборотРАТПгод т км.
Технологическая часть
1. Технологический расчет
1.1. Исходные данные для проектирования
Эффективность работы автомобильного транспорта базируется на надежности подвижного состава которая обеспечивается в процессе его производства эксплуатации и ремонта :
- совершенствованием конструкции и качеством изготовления;
- своевременным и качественным выполнением технического обслуживания и ремонта;
- своевременным обеспечением и использованием нормативных запасов материалов и запасных частей высокого качества и необходимой номенклатуры;
- соблюдением государственных стандартов и Правил технической эксплуатации.
Укрупнено производственная структура АТП делиться на две части:
- совокупность подвижного состава осуществляющего процесс перевозки грузов и структур организующих этот процесс;
- подразделения производящие ТО и ремонт подвижного состава.
Необходимо добиваться чтобы продолжительность нахождения подвижного состава в ТО и Р не превышала норм приведенных в Положении.
Задачей дипломного проекта является разработка предприятия обеспечивающего максимальную эффективность использования подвижного состава путем увеличения коэффициента выпуска автомобилей на линии. Это достигается следующим:
- повышение технической готовности и надежности подвижного состава;
- рациональным использованием производственных площадей и трудовых ресурсов;
- применением современного технологического оборудования и современных технологически процессов.
В соответствии с рекомендациями данными в [4] разрабатываем исходные данные и сводим их в таблицу 2.1. Нормативы даны для эталлоных условий эксплуатации (I категория условий эксплуатации умеренный климат).
Таблица 2.1 Исходные данные и условия проектирования
Показатель (условие)
Значение (характеристика) по моделям и АТП
Грузовое для перевозки грузов
Число автомобилей в наряде
Среднесуточный пробег
Категория условий эксплуатации подвижного состава
Пригородные перевозки - II
Природно-климатические условия
Режим работы предприятия
Число рабочих дней в году
Средний пробег подвижного состава с начала эксплуатации
5 от нормативного пробега КР
Время на транспортировку подвижного состава в капитальный ремонт
Продолжительность капитального ремонта
Нормативные пробеги
Нормативы трудоёмкости ТО и Р
чел·ч на одно обслуживание
2 чел·ч на одно обслуживание
Нормативы простоя в ТО и ТР
1.2. Расчет программ технического обслуживания и ремонта
А) Корректировка нормативов
Скорректируем нормативы приведенные в исходных данных к реальным условиям эксплуатации. Для этого сведем все корректировочные коэффициенты в табл. 2.2.
Таблица 2.2 Корректировка нормативов
Коректируемые нормативы
Корректировочные коэффициенты
Простой в ТО и ТР Тдо-тр дни
Обозначения в таблице 2.3:
- К1 - коэффициент корректирования нормативов в зависимости от условий эксплуатации;
- К2 - коэффициент корректирования нормативов в зависимости от модификации подвижного состава и организации работ;
– К3 - коэффициент корректирования нормативов в зависимости от природно-климатических условий;
– К4 - коэффициент корректирования нормативов удельной трудоемкости текущего ремонта в зависимости от пробега с начала эксплуатации;
– К'4 - коэффициент корректирования нормативов продолжительности простоя в ТО и Р в зависимости от пробега с начала эксплуатации;
– К5 - коэффициент корректирования нормативов технического обслуживания и текущего ремонта в зависимости от количества; обслуживаемых и ремонтируемых автомобилей на АТП и количества технологически совместимых групп подвижного состава;
Проводим корректировку нормативов по формулам:
LТО-1 = L'ТО-1 · К1 · К3 = 4000 · 09 · 1 = 3600 км
LТО-2 = L'ТО-2 · К1 · К3 = 16000 · 09 · 1 = 14400 км
Lкр = L'кр · К1 · К2 · К3 = 400000 · 09 · 1 · 1 = 360000 км
ТЕО = Т'ЕО · К2 · К5 = 05 · 1 · 095 = 047 чел·час на одно обслуживание
ТТО-1 = Т'ТО-1 · К2 · К5 = 78 · 1 · 095 = 74 чел·час на одно обслуживание
ТТО-2 = Т'ТО-2 · К2 · К5 = 312 · 1 · 095 = 296 чел·час на одно обслуживание
Ттр = Т'тр · К1 · К2 · К3 · К4 · К5 = 61 · 11 · 1 · 1 · 07 · 095 = 45 чел·час1000 км
Дто-тр = Д'то-тр · К'4 = 053 · 07 = 037 дней1000 км
LТО-1 = L'ТО-1 · К1 · К3 = 2000 · 09 · 1 = 1800 км
LТО-2 = L'ТО-2 · К1 · К3 = 10000 · 09 · 1 = 9000 км
Lкр = L'кр · К1 · К2 · К3 = 600000 · 09 · 085 · 1 = 459000 км
ТЕО = Т'ЕО · К2 · К5 = 05 · 115 · 095 = 055 чел·час на одно обслуживание
ТТО-1 = Т'ТО-1 · К2 · К5 = 78 · 115 · 095 = 85 чел·час на одно обслуживание
ТТО-2 = Т'ТО-2 · К2 · К5 = 312 · 115 · 095 = 341 чел·час на одно обслуживание
Ттр = Т'тр · К1 · К2 · К3 · К4 · К5 = 61 · 11 · 115 · 1 · 07 · 095 = 51 чел·час1000 км
Сводим полученные данные в таблицу 2.3
Корректируемые нормативы
Согласно руководству по эксплуатации
Простой в ТО и ТР Дто-тр дни
Так как ЕО проводится на поточной линии то необходимо произвести дополнительную корректировку трудоёмкости Teo с учётом механизации моечной установвок результаты занлосим в таблицу 2.4:
без учёта механизации
с учётом механизации
Б) Расчет количества технических воздействий
Согласно построению нормативов ТО и Р исходным периодом для расчета технических воздействий на автомобиль является цикл – период соответствующий пробегу автомобиля до капительного ремонта.
Расчет количества технических воздействий на автомобиль за цикл
Капитальный ремонт Nкр = 1
ТО-2: NТО-2 = Lкр Lto-2 - Nкр = 360000 14400 - 1 = 24
ТО-1: NТО-1 = Lкр Lto-1 - (Nкр + NТО-2) = 360000 3600 - (1 + 24) = 75
ЕО: NЕО = Lкр Lcc = 360000 22634 = 1591
ТО-2: NТО-2 = Lкр Lto-2 - Nкр = 459000 9000 - 1 = 50
ТО-1: NТО-1 = Lкр Lto-1 - (Nкр + NТО-2) = 459000 1800 - (1 + 50) = 204
ЕО: NЕО = Lкр Lcc = 459000 22846 = 2009
где Lкр LТО-2 LТО-1 Lсс - пробег до КР ТО-2 ТО-1 и среднесуточный пробег в км соответственно скорректированный для конкретных условий.
Расчет количества воздействий за год
Для перехода от цикла к году необходимо определить пробег за год и коэффициент перехода.
Количество дней эксплуатации за цикл:
ДЭЦ.борт. = Lкр Lcc = 360000 22634 = 1591
ДЭЦ.самос. = Lкр Lcc = 459000 22846 = 2009
Количество дней простоя в ТО и ТР за цикл:
ДРЦ.АВТ.борт. = ДКР + ДКР.тр + ДТО-ТР · Lкр 1000 = 22 + 2 + 037 · 360000 1000 = 157
ДРЦ.АВТ.самос. = ДКР + ДКР.тр + ДТО-ТР · Lкр 1000 = 22 + 2 + 037 · 459000 1000 = 194
где ДКР ДКР.тр ДТО-ТР – простой в капитальном ремонте время транспортировки в капитальный ремонт удельный простой в ТО и ТР на 1000 км пробега дни соответственно.
Определим коэффициент технической готовности за цикл по формуле:
αт.борт. = ДЭЦ.борт. (ДЭЦ.борт. + ДРЦ.АВТ.борт.) = 1591 (1591 + 157) = 091
αт.самос. = ДЭЦ.самос. (ДЭЦ.самос. + ДРЦ.АВТ.самос.) = 2009 (2009 + 194) = 091
Определим списочное число автомобилей:
Ас = Аэ αт.борт.= 705 091 = 77 ед.
Ас = Аэ αт.самос.= 1316 091 = 145 ед.
Пробег за год составит:
бортовой: Lг.борт. = Дрг · αт.борт. · Lcc = 357 · 091 · 22634 = 73531 км
самосвал: Lг.самос. = Дрг · αт.самос. · Lcc = 357 · 091 · 22846 = 74220 км
где Дрг = 357 – количество дней работы подвижного состава в году.
Коэффициент перехода от цикла к году:
г.борт. = Lг.борт. Lц = 73531 360000 = 0204
г.самос. = Lг.самос. Lц = 74220 459000 = 0162
где Lц – пробег за цикл ( равен Lкр).
С учетом коэффициента перехода количество технических воздействий в год на единицу (автомобиль) равно:
Nгкр = Nкр · г.борт. = 1 · 0204 = 0204 ед.
NгТО-2 = NTO-2 · г.борт. = 24 · 0204 = 49 ед.
NгТО-1 = NTO-1 · г.борт. = 75 · 0204 = 153 ед.
NгЕО = NЕО · г.борт. = 1591 · 0204 = 3246 ед.
Nгкр = Nкр · г.самос. = 1 · 0162 = 0162 ед.
NгТО-2 = NTO-2 · г.самос. = 50 · 0162 = 81 ед.
NгТО-1 = NTO-1 · г.самос. = 204 · 0162 = 33 ед.
NгЕО = NЕО · г.самос. = 2009 · 0162 = 3255 ед.
Общая программа технических воздействий на весь парк данной группы подвижного состава:
Σ Nгкр = Nгкр · Аборт. = 0204 · 77 = 16 ед.
Σ NгТО-2 = NгТО-2 · Аборт. = 49 · 77 = 377 ед.
Σ NгТО-1 = NгТО-1 · Аборт. = 153 · 77 = 1178 ед.
Σ NгЕО = NгЕО · Аборт. = 3246 · 77 = 24994 ед.
Σ Nгкр = Nгкр · Асамос. = 0162 · 145 = 23 ед.
Σ NгТО-2 = NгТО-2 · Асамос. = 81 · 145 = 1175 ед.
Σ NгТО-1 = NгТО-1 · Асамос. = 330 · 145 = 4785 ед.
Σ NгЕО = NгЕО · Асамос. = 3255 · 145 = 47198 ед.
где Аборт. = 77Асамос. = 145- среднесписочное число подвижного состава данной группы
Число диагностических воздействий за год определим по формулам:
Σ NгД1 = 11 · Σ NгТО-1 + Σ NгТО-2 = 11 · 1178 + 377 = 1673 ед.
Σ NгД2 = 12 · Σ NгТО-2 = 12 · 377 = 452 ед.
Σ NгД1 = 11 · Σ NгТО-1 + Σ NгТО-2 = 11 · 4785 + 1175 = 6439 ед.
Σ NгД2 = 12 · Σ NгТО-2 = 12 · 1175 = 1410 ед.
Расчет количества технических воздействий за сутки
Суточная программа по каждому виду обслуживаний определяется для того чтобы можно было спланировать производство на сутки и по сменам.
Количество обслуживаний в сутки определим по формуле
NiC = Σ Nгi ДРГi где ДРГi = 357 дней - количество дней в году выполнения данного вида обслуживания.
NсТО-2 = Σ NгТО-2 ДРГ = 377 357 = 11 ед.
NсТО-1 = Σ NгТО-1 ДРГ = 1178 357 = 33 ед.
NсЕО = Σ NгЕО ДРГ = 24994 357 = 70 ед.
NсД1 = Σ NгД1 ДРГ = 1673 357 = 47 ед.
NсД2 = Σ NгД2 ДРГ = 452 357 = 13 ед.
NсТО-2 = Σ NгТО-2 ДРГ = 1175 357 = 33 ед.
NсТО-1 = Σ NгТО-1 ДРГ = 4785 357 = 134 ед.
NсЕО = Σ NгЕО ДРГ = 47198 357 = 1322 ед.
NсД1 = Σ NгД1 ДРГ = 6439 357 = 18 ед.
NсД2 = Σ NгД2 ДРГ = 1410 357 = 39 ед.
Таблица 2.5 Варианты переменных циклов суточной программы
Принятая программа по дням цикла
Расчет объемов работ технических воздействий
Расчет объемов работ по ТО и ТР за год
Годовые объемы работ по ТО и ТР определим по формулам:
TгЕО = Σ NгЕО · TЕО = 24994 · 014 = 3499 чел·ч
TгТО-1 = Σ NгТО-1 · TТО-1 = 1178 · 74 = 8717 чел·ч
TгТО-2 = Σ NгТО-2 · TТО-2 = 377 · 296 = 11159 чел·ч
TгТР = (Lг.борт.· Aборт.· ТТР) 1000 = (73531 · 77 · 45) 1000 = 25478 чел·ч
TгЕО = Σ NгЕО · TЕО = 47198 · 018 = 8496 чел·ч
TгТО-1 = Σ NгТО-1 · TТО-1 = 4785 · 85 = 40673 чел·ч
TгТО-2 = Σ NгТО-2 · TТО-2 = 1175 · 341 = 40068 чел·ч
TгТР = (Lг.самос.· Aсамос.· ТТР) 1000 = (74220 · 145 · 51) 1000 = 54886 чел·ч
Трудоемкость диагностических работ определим при распределении работ ТО и ТР по видам работ как составную часть работ по ТО и ТР.
1.3. Распределение объемов работ ТО и ТР по видам работ
Объем ТО и Р распределяется между различными подразделениями по технологическим и организационным признакам. ТО и ТР выполняются на постах и производственных участках. К постовым относятся работы по ТО и ТР выполняемые непосредственно на автомобиле (моечные уборочные смазочные крепежные диагностические и др.). К участковым работам относятся работы по проверке и ремонту узлов и агрегатов снятых с автомобиля и выполняемых на участках (агрегатном слесарно-механическом электротехническом и т.д.).
Работы по ЕО ТО-1и ТО-2 выполняются в самостоятельных зонах а работы по ТР выполняемые на отдельных универсальных постах производят в общей зоне.
Таблица 2.6 Распределение годовой трудоёмкости ТО-1 и ТО-2 по видам работ
Контрольно-диагностические
Крепежно-регулировочные
Смазочно-заправочные
По обслуживанию системы питания
Таблица 2.7 Распределение годовой трудоёмкости по ТР по видам работ
Работы выполняемые в зоне ТР:
Крепёжно-регулировочные
Разборочно-сборочные
Работы выполняемые участками и отделениями:
Слесарно-механические
Ремонт приборов системы питания
Весь годовой объём работ вносим в таблицу 2.8. Контрольно-диагностические работы из ТО-1 и ТО-2 выносим в отдельные посты Д-1 и Д-2 (соответственно). Контрольно-диагностические работы из текущего ремонта распределяем между Д-1 и Д-2 по 50% на каждый пост.
Таблица 2.8 Годовые объёмы работ ТО и ТР
Для последующего расчёта количества постов и численности рабочих объёмы ряда работ текущего ремонта разделяем на постовые и участковые. При этом для расчёта количества постов учитываются только объёмы постовых работ а для расчёта количества рабочих суммарные объёмы.
Таблица 2.9 Распределение объёмов работ ТР на постовые и участковые
1.4. Расчет объемов работ по самообслуживанию
Работы по самообслуживанию обеспечивают содержание зданий сооружений оборудования и оснастки предприятия в исправном состоянии. Они выполняются подразделениями главного механика энергетика строительно-ремонтными группами.
Объем работ самообслуживания определяется в процентном отношении от суммарной годовой трудоемкости работ по техническому обслуживанию и ремонту подвижного состава выполняемых на территории предприятия по формуле
Тсам = (ТгЕО + ТгТО-1 + ТгТО-2 + Тгтр) · КС 100 = [(3499 + 8496) + (8717 + 40673) + (11159 + 40068) + (25478 + 54886)] · 10 100 = 19298 чел·ч
где Кс = 10 -доля работ по самообслуживанию от суммарной годовой трудоемкости работ по ТО и ТР подвижного состава [7].
Распределение работ по самообслуживанию по видам работ приведено в таблице 2.10.
Для организации работ по самообслуживанию на предприятии создается отдел главного механика (ОГМ).
Таблица 2.10 Распределение работ по самообслуживанию
Ремонтно-строительные и деревообделочные
1.5. Обоснование режима работы и принимаемых форм организации производства
Режим работы производства ТО и ТР т.е. количество смен их продолжительность и распределение по сменам объемов каждого вида работ определяет параметры проектируемой производственно-технической базы (количество постов и рабочих мест площади зон и отделений и т.д.).
Чем больше смен и чем равномернее распределены по ним объемы работ ТО и ремонта тем меньше требуется производственных мощностей и капитальных вложений на строительство АТП.
Режим выполнения обслуживания и ремонта зависит от следующих факторов:
- режима работы подвижного состава на линии (количества рабочих дней в году и продолжительности работы на линии);
- требования ежедневного обслуживания (мойки уборки и пр.) зависящих от видов перевозок и климатических условий;
- наличия производственных мощностей и ограничения по их развитию;
- возможности привлечения рабочих к работе в вечернее и ночное время.
Чем больше суточное время работы подвижного состава тем меньше остается времени у технической службы АТП для выполнения ЕО ТО и ТР без потерь линейного времени. Исходя из этого рекомендуется организовывать работы [4]:
ЕО ТО-1 - в межлинейное время (во время отстоя подвижного состава т.е во вторую смену);
ТО-2 - в первую смену или с минимальными целодневными простоями автомобилей;
Д-2 - в первую или в первую и вторую смены;
ТР - максимальное количество мелких заявок между возвратом и выездом автомобилей на линию с организацией для этой цели дополнительной (второй и третьей) смены производства после окончания работы автомобилей.
Участки электротехнический топливной аппаратуры и другие выполняющие работы непосредственно на автомобиле должны работать во все организованные смены ТР.
Работы по восстановлению оборотного фонда агрегатов узлов приборов и деталей - в первую смену производства. Для сокращения потребного количества рабочих мест может организовываться вторая смена;
Работы самообслуживания - во все производственные смены.
Учитывая вышесказанное принимаем:
ЕО – работа в две смены.
ТО-1 – работа в три смены.
ТО-2 – работа в три смены.
Д-1 – работа во вторую смену.
Д-2 – работа в первую смену.
ТР - работа в две смены.
Служба ОГМ – работа в две смены.
Участки – работа в 2 смены.
По рекомендациям [3] поточный метод ТО целесообразен если сменная программа составляет по ТО-1 не менее 12 15 а по ТО-2 не менее 5 6 обслуживаний. В нашем случае ТО-1 и ТО-2 проводим на универсальных постах. ЕО выполняем на отдельной поточной линии.
1.6. Расчет численности ремонтно-обслуживающего персонала
Технологически необходимое количество рабочих т.е. непосредственно обеспечивающее выполнение годового объема работ ТО и ремонта в общем или отдельно по каждому виду работ рассчитывается по формуле:
где Тг - годовой объем работ чел·ч ( по зоне или отделению);
Фт - годовой фонд времени рабочего места или технологически необходимого рабочего ч.
Штатное количество производственных рабочих т.е. принимаемое предприятием с учетом потерь рабочих дней на отпуска болезни и по другим причинам определяется по формуле:
где Фш – годовой фонд времени штатного рабочего ч.
Распределение рабочих по сменам проводим в соответствии с ранее принятыми рекомендациями. Результаты расчетов сводим в таблицу 2.11.
Таблица 2.11 Расчет численности рабочих
ТР (Крепёжно-регулировочные разборочно-сборочные)
Работы самообслуживания выполняемые ОГМ
1.7. Формирование производственной структуры технической службы АТП
В этом разделе определим производственную структуру АТП.
Производственная структура отражает перечень производственных подразделений технической службы АТП их численность внутреннюю структуру (количество звеньев бригад) и взаимосвязи обуславливаемые технологическими и территориальными факторами.
По итогам расчёта ремонтных рабочих принимаем следующие организационные решения:
Объединяем шиноремонтный и шиномонтажный участки в шиноремонтный участок.
Объединяем сварочный и арматурно-кузовной участки в сварочно-кузовной участок.
Объединяем медницкий и кузнечно-рессорный в кузнечный участок.
Объединяем столярный и обойный участок в столярный участок.
1.8. Расчет линий и постов в производственных зонах и отделениях
А) Расчет поточных линий
Поточная линия непрерывного действия для ЕО
Такт линии непрерывного действия (ЕО) определяется исходя из следующих соображений:
- на линиях ЕО на специализированных постах выполняются различные виды работ (уборочные моечные обтирочные и др.) с равным уровнем механизации;
- равномерность работы линии может быть обеспечена при равенстве тактов всех постов;
- определяющим фактором такта поста может являться пропускная способность моечной установки (Ny - авт.ч.);
- такты других постов регулируются количеством рабочих.
Такт линии ЕО из условия пропускной способности мойки:
ео = 60 Nу = 60 15 = 4 мин.
Потребная скорость конвейера:
Vк = (Lа + а) ео =(9 + 2) 4 = 28 ммин
где Lа = 9 м - длина автомобиля
а = 2 м - принятый интервал между автомобилями стоящими на постах линии
RЕО = (ТЕОобсл. · 60) NEOc = (7 · 60) 2022 = 21 мин
где ТЕОобсл. = 7 ч.- продолжительность работы линии ЕО за смену
NEOc = (700 + 1322) = 2022 - суточная программа воздействий ЕО ед.
Расчётное количество линий ЕО:
mЕО = ео RЕО = 4 21 = 19
Принимаем mЕО = 1 общая продолжительность работы линии 134 ч. в сутки;
Количество постов на линии ЕО принимаем ХЕО = 3 в соответствии с рекомендациями [7].
пост – уборочные работы;
пост – моечные работы;
пост – обтирочные смазочные и дозаправочные работы
Количество рабочих занятых на посту уборки:
Рубор. = tубор. · 60 ео = 006 · 60 4 = 09 чел.
tубор. - трудоёмкость уборочных работ;
Б) Расчет количества постов ТО ТР и диагностики
RТО-1 = (ТТО-1 · 60) NТО-1c = (7 · 60) 167 = 25 мин
где ТТО-1 = 7 ч- продолжительность работы поста ТО-1 за смену
NТО-1c = (33+134) = 167 - ед суточная программа воздействий ТО-1
то-1 = (tто-1 · 60) Рп + tпс = (812 · 60) 25 + 2 = 197 мин
Рп - количество рабочих одновременно работающих на посту (25 чел);
tто-1 - трудоёмкость технического воздействия на посту ТО-1 (812 чел·ч);
tпс - время затрачиваемое на постановку вывешивание на подъёмнике и съезд автомобиля с поста (принимаем 2 мин.);
XТО-1 = то-1 (RТО-1 · ) = 197 (25 · 09) = 88; принимаем 3 поста при трёхсменной работе ТО-1.
- коэффициент использования рабочего времени поста (09);
RТО-2 = (ТТО-2 · 60) NТО-2c = (7 · 60) 44 = 95 мин
где ТТО-2 = 7 ч.- продолжительность работы поста ТО-2 за смену
NТО-2c = (11+33) = 44 - ед. суточная программа воздействий ТО-2
то-2 = (tто-2 · 60) Рп + tпс = (3254 · 60) 25 + 2 = 783 мин
XТО-2 = то-2 (RТО-2 · ) = 783 (95 · 09) = 92 принимаем 3 поста при трёхсменной работе ТО-2.
RД-1 = (ТД-1 · 60) NД-1c = (7 · 60) 227 = 19 мин
где ТД-1 = 7 ч.- продолжительность работы поста Д-1 за смену
NД-1c = (47+180) = 227 - ед. суточная программа воздействий Д-1
д-1 = (tд-1 · 60) Рп + tпс = (075 · 60) 25 + 2 = 20 мин
XД-1 = д-1 (RД-1 · ) = 20 (19 · 09) = 12.
RД-2 = (ТД-2 · 60) NД-2c = (7 · 60) 52 = 81 мин
где ТД-2 = 7 ч.- продолжительность работы поста Д-2 за смену
NД-2c = (13+39) = 52 - ед. суточная программа воздействий Д-2
д-2 = (tд-2 · 60) Рп + tпс = (219 · 60) 25 + 2 = 55 мин
XД-2 = д-2 (RД-2 · ) = 55 (81 · 09) = 08;
Выводы: так как работы Д-1 и Д-2 выполняются в разные смены то для них выбираем один общий пост на участке диагностики с режимом работы: Д-1 во вторую смену Д-2 в первую.
Зона ТР (без учёта контрольно-диагностических работ)
Количество постов для проведения работ определим по формуле:
Xп = (Тгп · φ · Кmax ) (ДРГ · Тсм · Рп · п)
где Тгп - годовая трудоемкость контрольных крепежных регулировочных
разборочно-сборочных работ выполняемых на постах чел.-ч
ДРГ = 357 - принятое количество дней работы в году постов ТР;
ТСМ = 712 ч - продолжительность рабочей смены ч.;
РП = 1 15 - среднее количество рабочих одновременно работающих на посту чел. Принимается согласно рекомендациям [2];
= 12 15 – коэффициент учитывающий возможность неравномерного поступления автомобилей в зону ТР в течение смены. Зависит в основном от уровня совершенства планирования и управления производством [7];
п = 085 09 - коэффициент использования рабочего времени поста за смену;
Кmax - коэффициент отражающий долю работ выполняемых в наиболее загруженную смену. Односменная работа Кmax =10. Двухсменная работа при равномерном распределении объемов Кmax = 05. Трехсменная работа при равномерном распределении объемов Кmax = 033. При неравномерном распределении объемов работ по сменам Кmax = 035 ÷ 09 (устанавливается исходя из конкретных условий АТП и должно соответствовать распределению рабочих в табл. 2.11).
Количество универсальных постов для проведения работ по ТР.
ХТР = (ТгТР · φ · Кma принимаем 4 поста;
Зона участковых работ ТР
В этой зоне машино-место требуется для малярных кузовных работ и т.д в зависимости от производственной структуры технической службы конкретного АТП. Для расчётов учитываем трудоёмкость (Т чел·час) только постовых работ проводимых на рассчитываемом участке из таблицы 2.9.
Сварочно-кузовной участок:
ХТРкузов. = (Тгкузов · φ · Кma
ХТРмал. = (Тгмал · φ · Кma
В) Расчет постов ожидания ЕО ТО и ТР
Посты ожидания предназначены для повышения эффективности использования рабочих постов за счет сокращения времени поиска автомобилей на территории АТП и их перегона а также обеспечения возможности начать работы сразу после постановки автомобиля на пост особенно в зимнее время. Количество постов ожидания принимается из рекомендаций [2]:
Исходя из этих рекомендаций принимаем:
- на линии ЕО 50% часовой пропускной способности – принимаем 7 постов (6 постов в зоне ожидания возле въезда на улице и 1 пост подпора на линии ЕО);
- для ТО-1 ТО-2 – 50% сменной программы: ((33 + 134) 3 + (11+33) 3) · 05 = 35; принимаем 4 поста ожидания;
- для постов ТР 20% от количества рабочих постов – 4 · 02 = 08; принимаем 1 пост ожидания.
1.9. Подбор технологического оборудования и оснастки для производственных зон и отделений
Подбор технологического оборудования для постов и технологических зон проведен по имеющимся источникам [8 910].
Таблица 2.12 Состав технологического оборудования
Наименование оборудования
Установка для мойки автомобилей
Воздухо-раздаточная колонка
Конвейер для передвижения автомобилей на линии ЕО
Машина подметально-пылесосная
Передвижная маслораздаточная колонка
Шкаф для приборов и инструмента
Комплект инструментов для ТО и ТР электрооборудования автомобилей
Стеллаж для запасных частей
Тележка инструментальная
Линейка для проверки схождения колёс
Комплект инструментов автомеханика
Шкаф для приборов технической документации и инструмента
Установка для промывания системы смазки
Подставка для рабочих в осмотровой канаве
Бак с моторным маслом
Установка для мойки фильтров
Комплект приборов и инструментов для ТО аккумуляторов
Стол - тележка смазчика
Установка для слива масла
Прибор для проверки шкворневых соединений
Установка смазочно-заправочная
Бак с тормозной жидкостью
Бак с трансмиссионным маслом
Колонка воздухораздаточная для накачки шин
Гайковерт для стремянок рессор
Прибор для проверки карданных валов
Тележка для снятия колес
Установка для проверки рулевого управления
Линейка для проверки сходимости колес автомобиля
Стеллаж для деталей приспособлений
Ключ динамометрический
Комплект инструментов
Тележка для снятия и установки рессор
Приспособление для снятия и установки КПП
Солидолонагнетатель смазочный
Тележка для снятия и установки колес
Тележка с набором инструмента для ремонта автомобилей
Тележка для перевозки агрегатов и узлов
Тележка для перевозки двигателей
Подставка под колеса
Домкрат гаражный гидравлический
Прибор для проверки переднего моста
Шкаф для приборов и приспособлений
Приспособление для выпрессовки шкворней
Съемник универсальный
Маслораздаточный бак для гипоидного масла
Емкость для слива трансмиссионных масел
Емкость для слива охлаждающей жидкости
Емкость для слива моторн масел
Комплект диагностический
Комплект приборов для проверки тормозов
Прибор для проверки и регулировки света фар
Стенд для проверки тормозов грузовых автомобилей
Ларь для обтирочных материалов
Стенд для разборки и сборки КПП
Пpecc гидравлический
Стеллаж для деталей
Ванна для мойки деталей
Стенд для разборки сборки и регулировки сцеплений
Стенд для разборки сборки и регулировки рулевых механизмов
Стенд для испытаний заднего моста
Стенд для ремонта двигателя и КПП
Устройство для притирки клапанов
Стенд для приработки и испытания двигателей
Стенд для приработки и испытания КПП
Слесарно-механический участок
Станок токарно-винторезный
Станок вертокально-фрезерный
Стеллаж для инструментов
Аккумуляторный участок
Комплект приспособлений и инструмента для ремонта АКБ
Стенд для проверки аккумуляторных батарей
Пробник аккумуляторный
Шкаф для зарядки АКБ
Бак для дистиллированной воды
Ванна для электролита
Тележка для транспортировки АКБ
Комплект оборудования для ТО АКБ
Электротехнический участок
Контрольно-испытательный стенд для проверки электрооборудования
Прибор для проверки якорей
Пуско-зарядное устройство
Шкаф для инструмента
Комплект инструмента для ремонта
Подставка под оборудование
Стенд для проверки генераторов стартеров и реле-регуляторов
Участок ремонта топливной аппаратуры
Контрольно-испытательный стенд
Прибор для проверки топливной системы
Стенд для регулировки топливных агрегатов
Стенд для очистки и испытания форсунок
Шиноремонтный участок
Мульда для ремонта сквозных повреждений
Станок для шероховки
Домкрат гидравлический
Ванна для проверки герметичности
Верстак для ремонта камер
Стенд для монтажа и демонтажа шин
Стенд для балансировки колес
Воздухораздаточная колонка
Стеллаж для хранения шин и колес
Компрессор воздушный поршневой
Сварочно-кузовной участок
Набор приспособлений и инструментов
Шкаф инструментальный
Инструмент и приспособление для правки
Пневматическое зубило ручное
Трансформатор сварочный
Преобразователь для ручной электродуговой сварки
Стол для сварочных работ
Генератор ацетиленовый
Тележка для газовых баллонов
Редуктор кислородный
Р=15МПа Пропуск 60м3ч
Редуктор ацетиленовый
Горелка сварочная для ручной ацетиленокислородной сварки
Шкаф для хранения баллонов с отсосом воздуха
Стенд для работ по ремонту радиаторов
Стелаж для радиаторов бензобаков
Верстак для медницких работ с тумбой
Ванна для проверки радиаторов и топливных баков
Стенд для разборки и сборки рессор и рихтовки рессорных листов
Стеллаж для рессорных листов
Стенд для проверки и ремонта радиаторов автомобиля
Установка для прочистки радиаторов
Шкаф вытяжной для распайки радиаторов
Установка для промывки и продувки топливных баков автомобилей
Стеллаж для топливных баков и радиаторов
Верстак для ремонта топливных баков
Точильно-шлифовальный станок
Пресс-ножницы комбинированные
Верстак для жестяницких работ
Набор инструмента для правки кузовов автомобилей
Электроножницы ручные
Приспособление для навивки пружин
Станок для заточки столярного инструмента
Рубанок электрический
Установка для окраски
Сушилка инфракрасного излучения
Стеллаж для покрасочных материалов
Прибор для полировки кабин
Обдирочно-шлифовальный станок
Электротехническое отделение
Шкаф для инструментов
Верстак универсальный
Комплект электротехнических приборов
Механическое отделение
Ремонтно-строительное и деревообрабатывающее отделение
Станок деревообрабатывающий
1.10. Расчет площадей производственных зон и отделений
А) Поточная линия ЕО
Для зоны ЕО размещенной на поточной линии применяется аналитический метод расчета площадей по формуле:
FEO = Lф · Нф = 540 · 8 = 432 м2
где LФ - фактическая длина линии м;
НФ - фактическая ширина линии м.
Фактическая длина линии по формуле
Lф = Lа · ХП + а · (ХП - 1) + 2 · (La + 2 · a) = 9 · 3 + 15 ·(3 - 1) + 2 · (9 + 2 · 15)= 540 м
где La = 9 м - длина автомобиля обслуживаемого на линии;
XП = 3 - рабоч. пост. на линии;
а = 15 м - нормативная величина расстояния между автомобилями стоящими на линии и от крайнего автомобиля до ворот линии;
Ширина линии определяется исходя из установленных нормативов [3] расстояния от боковой стороны автомобиля до стенки с учетом расстановки оборудования в нашем случае все будет определятся шириной мойки:
Нф = В + 2b = 5 + 2 · 15 = 8 м2
где В = 5 м- ширина мойки м:
b = 15 м - нормативная величина прохода между стеной и мойкой.
FТО-1ТО-2 = fa · XП · КП = 225 · 10 · 5 = 1125 м2;
где fa - площадь занимаемая автомобилем (225 м2);
XП - суммарное число постов в зоне ТО: рабочих и ожидания;
КП - коэффициент плотности расстановки постов (5);
В) Зона диагностики
FД-1 = (fa · XП + Fоб) · Кп = (225 · 1 + 118) · 5 = 172 м2
XП - количество постов зоны Д-1 (2 пост);
Fоб - площадь занятая оборудованием (115 м2);
Кп - коэффициент плотности расстановки оборудования (5);
FТР = fa · XП · КП = 225 · 5 · 5 = 563 м2
Д) Производственные участки
Fкузов = (fa · Xп + Fоб) · Кп = (225 · 1 + 89) · 4 = 126 м2
Fмал = (fa · Xп + Fоб) · Кп = (225 · 1 + 7) · 4 = 118 м2
Fагр = Fоб · Кп= 308 · 4 = 123 м2
Fслес = Fоб · Кп= 83 · 4 = 33 м2
Fак = Fоб · Кп= 51 · 35 = 18 м2
Fэлек = Fоб · Кп= 71 · 35 = 25 м2
Fуч = Fоб · Кп= 51 · 4 = 20 м2
Fшин = Fоб · Кп= 124 · 4 = 50 м2
Fкузн = Fоб · Кп= 216 · 45 = 97 м2
Fжес = Fоб · Кп= 59 · 45 = 27 м2
Fуч = Fоб · Кп= 57 · 4 = 23 м2
Fогм = Fоб · Кп= 131 · 35 = 46 м2
Результат расчётов сводим в таблицу 2.13
Наименование зоны отделения
Площадь занимаемая оборудованием м2
1.11. Расчет хранимых запасов и площадей складских помещений
А) Склад смазочных материалов
Суточный расход топлива на линейную работу подвижного состава определим по формуле
Gл = (Аи · аи · Lсс) · q 100 = (222 · 091 · 22772) · 25 100 = 11501 л
где Аи =222 - списочное количество автомобилей;
Lсс = 22772 км - среднесуточный пробег км;
q = 25 л100 км - линейный расход топлива по нормам.
аи = 091 - коэффициент использования парка.
Суммарный суточный расход топлива определим по формуле
Gсут = (Gл + Gт) · = (11501 + 11501 · 001) · 103 = 11964 л
где Gл – суточный расход топлива на линейную работу автомобилей л.;
Gт - суточный расход топлива на внутригаражное маневрирование и технологические надобности (составляет менее 1% от Gл) л.;
= 103 - коэффициент учитывающий принятые в АТП повышение или снижение нормы расхода топлива.
Запас смазочных материалов определим по удельным нормам расхода смазок на каждые 100 л планируемого расхода автомобильного топлива и продолжительности хранения материалов на складе АТП по формуле
Зм = 001 · Gсут · qн · Дз = 001 · 11964 · 32 · 15 = 5743 л - моторное масло
Зт = 001 · Gсут · qн · Дз = 001 · 11964 · 04 · 15 = 718 л - трансмиссионное масло
Зс = 001 · Gсут · qн · Дз = 001 · 11964 · 01 · 15 = 179 л - специальное масло
Зп = 001 · Gсут · qн · Дз = 001 · 11964 · 03 · 15 = 538 л - пластичная смазка
Объём отработанных масел - 15% от расхода свежих масел.
Qм = 015 · 5743 = 861 л - моторное масло
Qт = 015 · 718 = 108 л - трансмиссионное масло
Qс = 015 · 179 = 27 л - специальное масло
Qп = 015 · 538 = 81 л - пластичная смазка
Подбираем стандартные бочки для масел и смазок.
Моторное масло: V – 5 емк – 12 м3 Площадь Fм = 39 м2
Трансмиссионное масло: V – 1 емк – 12 м3 Площадь Fм = 078 м2
Специальное масло: V – 2 емк – 01 м3 Площадь Fм = 034 м2
Пластичные смазки: V – 1 емк – 06 м3 Площадь Fм = 05 м2
Моторное масло: V – 4 емк – 023 м3 Площадь Fм = 108 м2
Трансмиссионное масло: V – 6 емк – 002 м3 Площадь Fм = 036 м2
Специальное масло: V – 1 емк – 005 м3 Площадь Fм = 01 м2
Пластичные смазки: V – 1 емк – 01 м3 Площадь Fм = 017 м2
Оборудование: насос для перекачки масел – Fн = 022 м2
насосная установка – Fн = 17 м2.
Площадь склада смазочных материалов
Fсм = (Fоб + Fм) · Кп = (022 + 17 + 017 + 01 + 036 + 108 + 05 + 034 + 078 + 39) · 25 = 23 м2
Площадь склада резины определяем исходя из того что покрышки хранятся на стеллажах в два яруса в положении стоя вплотную одна к другой. Запас покрышек рассчитываем по формуле
Зрез = (Аи · аи · Lcc · Xк · Дз) (Lгн + Lгп) = (222 · 091 · 22772 · 10 · 15) (45000 + 24000) = 100
где Хк = 10 - количество шин используемых на автомобиле (без запасной);
Lгн = 45000 км- гарантийная норма пробега новой покрышки без ремонта;
Lгп = 24000 км- гарантийная норма пробега шин после первого наложения нового протектора;
ДЗ - число дней запаса (15 дней).
Длину стеллажей определим из выражения
Lст = Зрез П = 100 6 = 167 м
где П = 6 - количество покрышек размещающихся на одном погонном метре стеллажа с учетом ярусности
Площадь занимаемая стеллажами с покрышками
FОБ.п = Lст · bст = 167 · 11 = 18 м2
Площадь занимаемая камерами на вешалах определяется исходя из значений П = 15 20 при двухъярусном хранении и ширине равной 06 диаметра камеры.
FОБ.к = (Зрез · 06 15) · bст = 100 · 11 · 0615 = 4 м2
Площадь склада резины
Fрез = (Fоб.п + Fоб.к) · Кп = (4 + 18) · 25 = 55 м2
В) Склад запасных частей агрегатов и материалов
Размер запаса склада запчастей определяем по формуле:
Мзч = (Аи · ат · Lcc · a · Ма · Дз) (1000 · 100) = (222 · 091 · 22772 · 2 · 11000 · 20) (10000 · 100) = 20242 кг
где Ма = 11000 кг - масса автомобиля.
а = 2% - средний процент расхода запчастей на 10000 км пробега [4];
ДЗ - число дней запаса (20 дней).
Площадь под запчасти:
Fзч = Мзч mCзч = 20242 600 = 337 м2
где mс - допускаемая нагрузка на 1 м2 площади стеллажа (600 кг)
Площадь склада под запчасти: Fск.зч = Fзч · Кп = 337 · 25 = 84м2
Размер запаса склада металлов (ДЗ = 10 дней)
Мм = (Аи · ат · Lcc · a · Ма · Дз) (1000 · 100) = (222 · 091 · 22772 · 1 · 11000 · 10) (10000 · 100) = 5060 кг
Площадь под металлы:
Fм = Мм mCм = 5060 650 = 78 м2
Площадь склада под металлы: Fск.м = Fм · Кп = 78 · 25 = 20м2
Склад лакокрасочных изделий и химикатов
Размер запаса склада лакокрасочных изделий (ДЗ = 10 дней)
Млк = (Аи · ат · Lcc · a · Ма · Дз) (1000 · 100) = (222 · 091 · 22772 · 02 · 11000 · 10) (10000 · 100) = 1012 кг
Площадь лакокрасочные покрытия:
Fлк = Млк mCлк = 1012 250 = 40 м2
Площадь склада под лакокрасочные покрытия: Fск.лк = Fлк · Кп = 40 · 25 = 10м2
Склад прочих материалов
Размер запаса склада прочих материалов (ДЗ = 10 дней)
Мпр = (Аи · ат · Lcc · a · Ма · Дз) (1000 · 100) = (222 · 091 · 22772 · 02 · 11000 · 10) (10000 · 100) = 1012 кг
Площадь под прочие материалы:
Fпр = Мпр mCпр = 1012 250 = 40 м2
Площадь склада под прочие материалы: Fск.пр = Fпр · Кп = 40 · 25 = 10м2
Размер запаса склада агрегатов определяется по количеству и массе оборотных агрегатов на каждые 100 однотипных автомобилей [23].
Мдв = (Кдв · qдв · Аи) 100 = (4 · 1188 · 222) 100 = 10549 кг
где Кдв = 4 – число оборотных двигателей на 100 автомобилей;
qдв = 1188 кг – вес двигателя.
Мк.п. = (Кк.п. · qк.п. · Аи) . 100 = (4 · 250 · 222) 100 = 2220 кг
Передний мост автомобиля
Мп.м. = (Кп.м. · qп.м. · Аи) 100 = (4 · 500 · 222) 100 = 4440 кг
Задний мост автомобиля
Мз.м. = (Кз.м. · qз.м. · Аи) 100 = (4 · 500 · 222) 100 = 4440 кг
Мрул = (Крул · qрул · Аи) 100 = (4 · 63 · 222) 100 = 559 кг
Площадь под агрегаты:
Fаг = Маг mаг = (10549 + 2220 + 4440 + 4440 + 559) 500 = 44 м2
Площадь склада под агрегаты:
Fск.аг = Fаг · Кп = 44 · 25 = 110 м2
Площадь складов промежуточного хранения принимаем 20% от общей площади складов. Расчёты сводим в таблицу 2.14.
Таблица 2.14 Площадь складов
Расчётная площадь м2
Склад смазочных материалов
Склад промежуточного хранения
Г) Зона хранения (стоянки) подвижного состава
Fx = fa · Аи · Кп = 225 · 222 · 3 = 14985 м2
fa - площадь занимаемая автотранспортным средством м2;
Аи - списочное число автомобилей;
Кп - коэффициент плотности расстановки автомобиле-мест хранения (25 - 30);
2. Обоснование планировочных решений
2.1. Обоснование планировочного решения производственного корпуса
Размеры производственного корпуса определяется длиной поточной линии ЕО. При этом по габаритным требованиям оборудования линии ЕО (габарит моечной установки) ширина пролета где размещается линия ЕО принимается равной 6 м. Исходя из этого определяем длину и ширину корпуса (78 м х 42 м). Высота корпуса - 7 м. Производственный корпус спроектирован из сборных модульных конструкций
Учитывая что корпус одноэтажный принимаем основной шаг колонн – 6 м и 6 м. В центральной части корпуса в зоне работ ТО и ТР создаем сквозной проезд 6 м для обеспечения проезда автомобилей.
Из-за большого количества автомобилей АТП зону ЕО выносим в отдельный корпус чтобы автомобили с линии ЕО не мешали въезду и выезду автомобилям на зону ТО и ТР.
Зоны ТО и ТР располагаются в центральной части корпуса и имеют непосредственное сообщение друг с другом. Размещение постов ТО и ТР исключает возможность встречных и пересекающихся потоков. Это удобно и безопасно.
Производственные помещения располагаются по периметру основной производственной зоны.
Агрегатный участок размещаем смежно со складом агрегатов это позволяет сократить затраты на транспортировку агрегатов и узлов при их ремонте после снятия с автомобиля также возле агрегатного участка располагаем сварочно-кузовной слесарно-механический жестяницкий и кузнечный участки. Такая компановка позволяет обеспечить их единым подъёмным краном. Сварочно-кузовной участок размещаем в отдельном помещении изолируя его от остальных помещений несгораемыми стенками учитывая его повышенную пожароопасность. Для возможности в зоне ТР использовать подъёмный кран для снятия агрегатов с автомобилей два поста ТР находятся под отдельным подъёмным краном.
Производственные помещения располагаются по периметру что позволяет их обеспечить естественным освещением.
2.2 Разработка генерального плана АТП
Генеральный план предприятия – это план отведенного под застройку земельного участка территории ориентированный в отношении проездов общего пользования и соседних владений с указанием в нем зданий и сооружений по их габаритному очертанию площадки для безгаражного хранения подвижного состава основных и вспомогательных проездов и путей движения подвижного состава по территории.
Генеральные планы разрабатываются в соответствии со СНиП II-89-80 "Генеральные планы промышленных предприятий" и другими нормативными документами.
Определим площади основных зданий и сооружений размещаемых на территории АТП:
Производственный корпус
Административно-бытовой корпус
Fад.-быт. = а-б · N · К1 · К2 · К3 · К4 = 87 · 222 · 114 · 103 · 094 · 1 = 2132 м2
где а-б = 87 м2авт. – удельная норма площади административно-бытовых зданий [12] табл.5;
N = 222 авт. – списочный состав автомобилей;
К1 = 114 – коэффициент учитывающий количество подвижного состава [12] табл.7;
К2 = 103 – коэффициент учитывающий тип подвижного состава [12] табл. 8;
К3 = 094 – коэффициент учитывающий среднесуточный пробег;
К4 = 1 – коэффициент учитывающий категорию эксплуатации.
На стадии технико-экономического обоснования потребную площадь участка предприятия можно определить по формуле
Fуч = (Fпр + Fад.-быт. + Fх.) Kз = (14985 + 3276 + 2132) 05 = 40786 м2
где Кз = 05 – коэффициент плотности застройки территории.
При разработке генерального плана необходимо учесть следующее:
- ширина проезжей части наружных проездов должна быть не менее 3 м. при одностороннем и не менее 6 м при двустороннем движении;
- исходя из противопожарных требований ко всем зданиям предприятия должен обеспечен подъезд пожарных автомобилей с двух сторон;
- должно быть предусмотрено два выезда с территории;
- минимальное расстояние от края дороги до ограждения территории и открытых площадок не менее 15 м;
- минимальное расстояние от края дороги до наружной стены здания не менее 3 м.
3. Организация технология работ и планировочные решения агрегатного участка
3.1. Организация работ агрегатного участка
В дипломном проекте подробно разрабатывается планировочное решение агрегатного участка. Участок предназначен для ремонта агрегатов автомобиля и замены в них неподлежащих ремонту деталей а также для станочной обработки деталей подлежащих ремонту. На участке производится разборка и сборка агрегатов автомобиля мойка и дефектация агрегатов ремонт агрегатов и их испытания после ремонта.
В виду малой численности ремонтных рабочих на участке работу на агрегатно-механическом участке рациональнее организовать во вторую смену для совместного взаимодействия с работой зоны ТР.
Непосредственное управление технологическим процессом агрегатного участка осуществляется сменным мастером и начальником участка. Они подчиняются начальнику производства.
Материально-техническое обеспечение участка обеспечивается материально-техническим отделом АТП через склады предприятия по заявкам агрегатного участка.
Планирование работы агрегатного участка производится по общим плана планового отдела предприятия. На основании этого плана и поступающих заявок составляются месячные и суточные планы работы агрегатного участка.
После определения объема работ суточный план распределяется по сменам и заявка передается сменному мастеру. По этой заявке проводится запланированные работы в отделении и на участках ТР. Факт проведения работ фиксируется в листке учета работ на основании которых составляются наряды на выполненные работы. Расходные материалы учитываются в материальных накладных.
3.2. Технология работ агрегатного участка
После установки автомобиля на пост ТР мастер смены исходя из отметки в листке учета дает задание рабочим. Если ремонт возможен непосредсвенно на автомобиле то он проводится на посту. Если же ремонт требует разборки агрегата или узла тогда агрегат или узел снимается с автомобиля и отправляется на соответствующий участок. Основные узлы такие как двигатель коробка передач раздаточная коробка передач задний и средний мосты ремонтируются и проверяются именно на агрегатном участке. В целях снижения времени простоя автомобиля в ремонте существует оборотный фонд и новые запасные части. Механик по ремонту в зависимости от неисправности заранее или после разборки делает заявку на склад для получения запасных частей (новых или из оборотного фонда). Мастер смены получает необходимые запасные части по заявке и контролирует правильность сборки и установки их на соответствующий агрегат а при необходимости и правильность регулировки замененных деталей узлов или агрегатов. В случаях когда возможен быстрый ремонт или восстановление детали узла или агрегата то их устанавливают обратно на свое место.
3.3. Обоснование планировочного решения агрегатного участка
В агрегатном участке располагается оборудование для ремонта агрегатов и испытательное оборудование (стенды для ремонта и приработки двигателей КПП). Также находятся стенды предназначеные для проведения обкаточных и приемо-сдаточных работ заднего моста и турбокомпрессоров после их ремонта. Зона проведения обкаточных работ отделена шумозащитной стенкой. В этой зоне используется система отсоса выхлопных газов.
Конструкторская часть
В агрегатно-слесарном участке производится множество связанные со сборкой и разборкой различных механизмов и автомобильных узлов при их ремонте. Приходиться сталкиваться с соединениями и съёмами различных сопряжённых по жёсткой посадке деталями. При такой посадке требующей значительного усилия уже непригодны подручные средства как молоток или зубила. Поэтому возникает необходимость в разработке соответствующей оснастки которая облегчить труд ремонтному рабочему и повысит его производительность. В качестве приспособления разработаем небольшой по габаритам гидравлический пресс с помощью которого можно спрессовывать и разъединять жёстко сопряжённые детали. Данное приспособления подойдёт и для снятия подшипников выпрессовок и впрессовок тугих и переходных посадок между отверстиями и валами и т.д.
Рис. 3.1 Гидропресс в сборе.
- корпус 2 - гайка 3 - шток 4 - поршень 5 - винт сливного отверстия 6 - стенка 7 - труба 8 - корпус 9 - поршень 10 - пружина 11 - шток 12 - втулка 13 - основание 14 – втулка.
Пресс состоит из двух гидроцилиндров нагнетательного который подаёт масло и рабочего который непосредственно поднимает рабочую нагрузку. Поршень 4 надевается на резьбовой шток 3 и закручивается гайкой. Шток в сборе устанавливается в корпус 1 прикручивается внутренняя втулка гайка 2 и прижимается сверху крышкой на винтах. Аналогично собирается и рабочий цилиндр за исключением что в него вставляется ещё и пружина 10. Корпуса цилиндра и поршни выполнены из легированной стали 30ХГСА гайка 2 и шток 3 из стали 20Х2НЧА. Данная стали хорошо поддаётся термообработке которую выполняют для повышения прочности данных деталей что увеличивает срок службы. После сборки цилиндры соединяются сварной трубой посредством 8 винтов М4 состоящей из гнутой прокатной трубы внутренним диаметром 25 мм и толщиной 3 мм выполненной из алюминиевого сплава Д16 и приваренных к ней фланцев также из Д16. После сварки в данной трубе фрезеруются посадочные плоскости и сверлятся отверстия во фланцах. После сборки всей гидромагистрали в неё заливается масло через сливное отверстие и заворачивается винт 5. Затем вся магистраль вставляется между двумя разъёмными симметричными стенками 6 которые заранее были обработаны в сборе. Стенки скрепляются на два калиброванных болта для точной сборки и четыре болта М5 по ГОСТ 7805-70. Каждый цилиндр привёртывается к стянутым стенкам шестью винтами М5. Затем привёртывается шесть винтами М5 основание 13. Вся эта собранная конструкция крепится на установочную поверхность четырьмя болтами М10.
По своему конструктиву конструкция проста в сборке и разборке технологична и не требует квалифицированных подгоночных операций.
Ремонтный рабочий рожковым или накидным ключом на 19 мм закручивая гайку 2 которая проворачивается на одном месте и перемещает шток 3 который является винтом вместе с поршнем 4 вглубь цилиндра создаёт давление на масло. Поршень 9 совместно со штоком 11 под давлением перемещается вверх тем самым шток 11 давит на запрессованную деталь. Раскручивая гайку 2 поршень 4 перемещается к выходу из корпуса цилиндра 1 масла перетекает обратно в полость нагнетательного цилиндра давление падает и поршень 9 под действием пружины 10 опускается вниз. Для более плавного вытекания масла из полости рабочего цилиндра соответственно и опускания штока 11 в корпус цилиндра 8 вварена втулка 14 с уменьшенным внутренним диаметром. Втулка имеет внутренний конус для более плавного втекания масла в полость рабочего цилиндра и более препятственного вытекания из этой полости при падении давления. Для хорошей герметизации магистрали во фланцевых соединениях трубы 7 и корпусов цилиндров устанавливаются резиновые прокладки 14. Шток 11 на выходе имеет резьбу М18 она предназначена для привёртывания различных насадок под каждую конкретную выпрессовываемую или впрессовываемую деталь. Также с помощью насадок можно увеличивать длину штока 11. Основание 13 предназначено для закрепления на нём неподвижной детали при выпрессовке. Основание также можно менять на другое разработанное под какую-нибудь индивидуальную деталь что делает всё приспособление универсальным.
В данном прессе нагнетательный цилиндр можно расположить горизонтально относительно рабочего так как давление от веса масла в рабочем цилиндре ничтожно мало по сравнению с рабочим давлением поэтому давлением от веса масла тоже пренебрегаем.
Крутящий момент на гайке 2 (рис. 3.1) равен:
Мкр = Qнаг · dшт2 · tg( + ρ) + Мтр ;
Qнаг - усилие штока поршня нагнетательного цилиндра
dшт - диаметр резьбы штока (12 мм)
- угол подъёма винтовой линии штока (3°30’)
ρ – угол трения резьбы (6°10’)
Мкр подбираем для усиленного нажатия на стандартный рожковый или накидной ключ среднестатистического ремонтного рабочего (40 Нм = 40000 Нмм);
Мтр - момент трения винтовой пары;
Мтр = 13f · Qнаг · (d3пор - d3шт) (d3пор - d3шт);
f – коэффициент трения в резьбе (0.12);
dпор – диаметр поршня нагнетательного цилиндра (25 мм);
Мкр = Qнаг · dшт2 · tg( + ρ) + 13f · Qнаг · (d3пор - d3шт) (d3пор - d3шт)
Из данной формулы находим усилие:
Qнаг = 40000 [122 · tg(9°40’) + 13 · 0.12 · (253 – 123) (252 – 122)] = 972 Н;
Площадь нагнетательного цилиндра:
Fнаг = d2наг 4 = 3.14 · 252 4 = 490.6 мм2;
Давление масла во всей магистрали:
P = Q Fнаг = 972 490.6 = 0.2 кгсмм2 (20 атм);
По справочным данным автомобилестроения одни из усиленных посадок в узлах – это посадки внешних или внутренних колец подшипников в различных узлах в 3÷33 кН. Под данное усилие в 33 кН и будем проектировать рабочий цилиндр.
Площадь рабочего цилиндра:
Fраб = Qраб P = 330 0.2 = 1620 мм2;
Диаметр поршня рабочего цилиндра:
dраб = (4 Fраб)12 = 452 из стандартного ряда принимаем 45 мм;
Площадь рабочего цилиндра в 3.3 раза больше площади нагнетательного значит рабочих ход его будет в 3.3 раза короче и будет составлять:
hраб = hнаг 3.3 = 50 3.3 = 15 мм;
Шток нагнетательного цилиндра
сж = Q Fшт = 972 113 = 09 кгсмм2;
Fшт – площадь штока при диаметре резьбы М12;
Стержень сделан из стали 20Х2НЧА предел текучести данной стали т = 60 кгсмм2 так как сж т условие прочности на сжатие выполняется.
Критическая сила устойчивости:
Е – модуль упругости (для данной стали 2 · 104 кгсмм2);
J – момент инерции сечения (d264 = 1017 мм2);
Ркр= 4 · 3.142 · 2 · 104 · 1017 712 = 397826 кгс
так как Q Ркр условие устойчивости выполняется.
Резьбовая часть болта М12 с пределом текучести т = 60 кгсмм2 может выдержать усилие сжатия по справочнику инженера-конструктора 180 кг (т.к. 180 > 972) условие прочности резьбы выполняется.
H = z · t = 9 · 1.75 = 15.75 мм принимаем 16 мм
z - количество витков резьбы;
t – шаг резьбы (для М12 – 1.75 мм);
Удельное давление на виток:
q = Q [4 · (d2вер - d2вп) · zраб];
dвер - диаметр вершин витков;
dвп - диаметр впадин витков;
zраб – число рабочих витков (принимаем 5);
q = 972 [3.14 4 · (122 – 10.12) · 5] = 06 кгсмм2;
Гайка сделана из стали 20Х2НЧА так как q т условие прочности на резьбовую часть гайки выполняется.
Расчёт прочности на растяжение винтов которые крепят планку вместе с гайкой:
рас = Q (Fвин · n) = 972 (7 · 6) = 2.3 кгсмм2;
Fвин – площадь винта при резьбе М3 (7 мм2);
n – количество винтов (6 шт.);
Винты выполнены из прочной легированной стали 40ХНМА предел текучести данной стали т = 80 кгсмм2 так как рас т условие прочности на растяжение выполняется.
Сварочная труба соединяет два гидроцилиндра и является наиболее слабым элементом в магистрале которая подвергается нормальным напряжениям n на разрыв так как тонкостенна и выполнена из алюминиевого сплава Д16.
n = P · r [2 · (r2 – r1)];
P – давление в магистрале (0.2 кгсмм2);
r – средний радиус трубы;
n = 02 · 1338 [2 · (1425 – 125)] = 08 кгсмм2;
Предел текучести для сплава Д16 равен 38 кгсмм2 поэтому условие прочности на разрыв (n т) выполняется с коэффициентом запаса 1.5.
После этого расчёт на разрыв корпусов гидроцилиндров можно не проводить так как толщина стенок у них в 3 раза больше и предел текучести стали из которых они выполнены в 2.5 раза больше.
Шток рабочего цилиндра
сж = Q Fшт = 330 314 = 1 кгсмм2;
Fшт – площадь штока при диаметре 20 мм;
Стержень сделан из стали 20Х2НЧА предел текучести данной стали т = 85 кгсмм2 так как сж т условие прочности на сжатие выполняется.
6 Оценка эффективности использования разработки в эксплуатации
Гидропресс технологически необходим для сборочно-разборочных работ. Его также можно использовать в хозяйственных нуждах АТП где необходима повышенная сила.
Достоинства данного устройства:
- простота конструкции;
- достаточная дешевизна изготовления;
- большие усилия при небольших габаритах;
- плавный ход поршня;
- приспособление полностью локально не требует дополнительных насосных станций и трубопроводов.
Технология ремонта шатуна.
Шатуны относятся к классу «некруглые стержни» и изготавливаются из стали 40Р НВ 217 248; крышки из стали 40. Шатуны и их крышки не должны разукомплектовываться для предотвращения этого их клеймят. Шатунные болты должны затягиваться динамометрическим ключом .
Основные дефекты шатунов показаны на рис. 1.
Рис. 4.1. Основные дефекты шатуна двигателя:
— изгиб или скручивание; 2 — износ отверстия в нижней головке; 3 — износ отверстия под втулку в верхней головке; 4 — износ отверстия во втулке верхней головки; 5 — уменьшение расстояния между осями верхней и нижней головок
При наличии трещин любого характера и расположения а также погнутости и скрученности не поддающихся правке шатуны подлежат выбраковке. Проверка шатунов на погнутость и скрученность производится на известном приборе ГАРО или на приспособлении показанном на рис.1 Погнутость шатуна в плоскости оси коленчатого вала при которой получается односторонний износ стенок цилиндров и износ шеек коленчатого вала и подшипников проверяется индикаторами 1 а скрученность — индикатором 2 Установка индикаторов на ноль производится по эталонному (новому заводскому) шатуну при этом каждый индикатор 1 ставится на ноль после того как противоположный конец пальца ляжет на нож. При контроле проверяемого шатуна со вставленным пальцем разность отклонений индикаторов 1 и 2 от нуля не должна превышать допускаемых техническими условиями величин погнутости и скрученности (005 мм).
Шатуны с погнутостью или скрученностью более допустимой техническими условиями подвергаются правке. Правка погнутых шатунов производится при помощи специального рычага с зевом для захвата шатуна на винтовых или гидравлических прессах. Правка скрученных шатунов производится при помощи специального рычага или специальной струбцинки захваты которой закрепляются винтами с разных сторон таврового сечения шатуна.
Изношенные втулки верхней головки шатуна развертываются под увеличенный против номинального размер пальца или выпрессовываются и заменяются новыми. Втулки изготовляются из бронзы: оловянистой Бр. ОЦС4-4-25 или кремнемарганцовистой Бр. КСМцЗ-1. Химическ состав бронзы (в %): кремнемарганцовистой —S Мп 08—1.9; РЬ 25—35; Си — остальное; оловянистой —Sn 35—5; Zп 3—5; Си 15—3 РЬ — остальное.
Шатуны и крышки с поврежденными торцами разъема наиболее целесообразно восстанавливать шлифованием торцов «как чисто». В случае же значительных повреждений торцов разъема крышки или шатуна вместо шлифования производится фрезерование торцов.
Рис. 4.2. Приспособление для фрезерования плоскости разъема крышек шатунов.
После шлифования (фрезерования) производится сборка шатуна и обработка нижней головки под номинальный размер.
Для обработки плоскости разъема шатунов и крышек применяются приспособления различных конструкций. Так для фрезерования торцов разъема крышки можно использовать приспособление показанное рис.2. За установочные базы приняты отверстия под болты и поверхность гнезда под вкладыши. Крышка устанавливается на два плавающих стержня 1 которые под действием пружины 2 прижимают крышку до упора пальца 3. Закрепление крышки производится двумя планками 4 при зажиме гайки 5.
На рис.4.3 показано приспособление для фрезерования торцов разъема нижней головки шатуна. Шатун устанавливается отверстием верхней головки (без втулок) на палец 3 вставляемый во втулку 2. Отверстиями головки под болты шатун надевается на пальцы 4 и торцом головки опирается на ползун 1. Закрепление шатуна в приспособлении производится при помощи планки 5.
Рис.4 . Приспособление для растачивания отверстия нижней головки шатуна в сборе: 1 5 — пальцы; 2 — опорная втулка; 3 — диск; 4 — кожух; 6 — вилка; 7 — опора.
Целесообразно применение пневмогидравлического приспособления для фрезерование торцов разъема шатуна и крышек. Обработку отверстия нижней головки шатуна можно осуществить гонким растачиванием на станках 2710 2711 а за неимением их — на токарных на режиме близком к тонкому растачиванию в приспособлении показанном на рис.3.. Отверстием верхней головки шатун устанавливается на палец 5 центрируется при помощи пальца 1 и закрепляется вилкой 6 после чего обрабатывается. Однако раздельная обработка нижней и верхней головок шатуна часто не дает желаемых результатов из-за нарушения параллельности их осей и межцентрового расстояния между ними. Поэтому обработку отверстий верхней головки утратившей первоначальный размер после перепрессовки втулки и нижней головки желательно вести тонким растачиванием с одной установки. Для этой цели служит двух-шпиндельное приспособление конструкции УкрдортрансНИИ показанное на рис.4.. Приспособление содержит две расточные головки вращающиеся от шпинделя токарного станка 1616 на котором приспособление монтируется. Число оборотов при расточке верхней головки 1880 в минуту (310 обсек) и нижней головки — 720 (12 обсек). Закрепление шатунов производится в приспособлении установленном на направляющей продольного суппорта станка. Головки шатуна центрируются на приспособлении при помощи направляющих втулок и пробок-калибров: ромбической — нижняя головка и цилиндрической — верхняя. Стержень шатуна и верхняя головка закрепляются роликами плавающих тисков а нижняя головка — прижимной планкой с диафрагменным пневмоприводом.
Контроль межцентрового расстояния осей головок и их параллельности производится индикаторным приспособлением рис.5. Шатун устанавливается при помощи большой скалки 3 пропущенной через стойки 2. Малая скалка 3 вставляется в обработанное отверстие верхней головки. Посадочные диаметры скалок — конусные что обеспечивает большую плотность посадки отверстий шатуна. Шатун проверяется в верхнем положении как показано на рис. При этом малая скалка 3 соприкасаясь с упорами коромысла 4 упирается в штифты (один из них 6 виден на рис.) индикаторов. Индикаторы 1 показывают скрученность шатуна индикатор 2— расстояние между осями отверстий и индикатор 3 — непараллельность осей отверстий.
Разумеется что указанное приспособление с успехом может быть использовано и для контроля шатуна на погнутость. При погнутости шатун подвергается правке специальным ключом без снятия с приспособления. Настройка приспособления производится по эталонному шатуну. Оси отверстий головок должны лежать в одной плоскости допустимое отклонение не более 005 мм. Непараллельность осей отверстий допускается не более 003 мм; овальность и конусность отверстия нижней головки — не более 001 мм.
Рис. 4.4 Шатун: 1 – верхняя головка; 2 – нижняя головка; 3 – отверстие для выхода масла; 4 – бронзовая втулка; 5 – вкладыши.
После ремонта шатуны промывают для удаления абразивных частиц продувают сжатым воздухом и при необходимости прочищают отверстия через которые подается масло на поверхности гильз цилиндров.
После ремонта шатуны должны отвечать следующим техническим требованиям:
- не цилиндричность отверстия нижней головки должна быть не более 0080 мм;
- шероховатость должна соответствовать Ка = 050 мкм;
- не цилиндричность отверстия верхней головки 0040 мм и шероховатость Rа = 125 мкм.
Безопасность и экологичность проектных решений
1. Выбор и краткая характеристика объекта анализа
Объектом анализа с точки зрения безопасности и производственной санитарии является агрегатный участок. На участке и приле6гающей к нему зоне ТР производятся почти все виды работ по ремонту и регулировке автомобиля.
Объектом анализа с точки зрения экологичности и возникновения чрезвычайных ситуаций является помещение производственного корпуса в котором находится указанная зона. Производственный корпус расположен в одноэтажном здании высотой 6 м. площадью 1620 м2 (54 × 30). В корпусе работают 18 человек.
для окружающей среды
2.1. Анализ потенциально опасных и вредных
Производственных факторов
В зоне ТР имеются следующие опасные и вредные производственные факторы классифицированные по ГОСТ 12.0.003-74*.
движущиеся машины и механизмы
подвижные части оборудования
повышенная запыленность и загазованность воздуха рабочей зоны
повышенная или пониженная температура воздуха рабочей зоны
повышенная или пониженная влажность воздуха рабочей зоны
повышенная подвижность воздуха рабочей зоны
недостаток естественного света
недостаток освещенности рабочей зоны
повышенный уровень шума
повышенный уровень вибрации
повышенное значение напряжения в электрической цепи замыкание которой может произойти через тело человека.
Химические опасные и вредные факторы имеющиеся на участке представлены в таблице 5.1.
Химические опасные и вредные производственные факторы в воздухе рабочей зоны
Нормирование по ГОСТ 12.1.005-88 ГН 2.2.5.1313-03 и ГН 2.2.5.1314-03
Особенность действия
2.2. Анализ производственных воздействий производственного корпуса на окружающую среду
Химические загрязняющие вещества которые могут попадать из корпуса в атмосферный воздух населенной местности приведены в таблице 5.2.
Таблица 5.2 Вещества загрязняющие атмосферный воздух
Загрязняющие вещества
Нормирование по ГН 2.6.1338-03 и
Алюминий и его соединения
Масло минера-е нефтяное
Химические вещества загрязняющие сточные производственные воды приведены в таблице 5.3 где даны их нормируемые параметры для воды водных объектов хозяйственно-питьевого и культурно-бытового водопользования.
Таблица 5.3 Вещества загрязняющие сточные воды
Нормирование по ГН 2.1.5.1315-03 и
Масло минеральное нефтяное
Корпус может загрязнять окружающую среду энергетически: теплом шумом вибрационными колебаниями и электромагнитным излучением.
2.3. Анализ возможности возникновения в производственном корпусе чрезвычайных ситуаций
В здание где находится рассматриваемая зона возможно попадание молнии. Вероятность этого события невелика но тем не менее требуется организация молниезащиты.
Из возможных чрезвычайных ситуаций техногенного характера следует указать взрыв или пожар. В таблице 4.4 указаны вещества имеющиеся в корпусе которые могут представлять опасность во взрывопожарном отношении и даны характеристики по ГОСТ 12.1.004-91.
Таблица 4.4 Взрывопожарные вещества в производственном корпусе
Вещества и технические продукты
Горючесть воспламеняемость
На основании приведенных в таблице характеристик можно сделать вывод о возможности возникновения в производственном корпусе взрыва или пожара.
3. Классификация помещения и производства в производственном корпусе
По взрывопожарной и пожарной опасности помещение корпуса следует отнести в соответствии с НПБ 105-03 к категории А – взрывопожароопасные т.к. в нем имеются горючие газы и легковоспламеняющиеся жидкости с температурой вспышки менее 28оС.
Степень огнестойкости здания по СНиП 31-03-2001 не менее III т.к. площадь корпуса 1620 м2 здание одноэтажное высотой 7м.
По окружающей среде помещения цеха по ПУЭ относится к сухим нормальным помещениям.
С точки зрения опасности поражения человека помещение цеха по ПУЭ относится к особо опасным помещениям т.к. одновременно имеются два признака повышенной опасности:
возможность одновременного прикосновения человека к заземленным металлоконструкциям с одной стороны и к металлическим корпусам электроустановок с другой стороны
токопроводящие полы (железобетонные).
В помещении цеха имеются по ПУЭ взрывоопасная зона В-I и пожароопасная зона П-I т.к. присутствуют горючие газы (ГГ) и горючие жидкости (ГЖ).
Группа производственных процессов по санитарной характеристике по СНиП 2.09.04.-87* - 1б т.к. происходит загрязнение тела и спецодежды работающих веществами 3 и 4-го классов опасности (масло бензин керосин и др.).
По СанПиН 2.2.12.1.1.1200-03 санитарный класс АТП - III и санитарно-защитная зона 300м т.к. предприятие по обслуживанию грузовых автомобилей.
4. Мероприятия и средства по обеспечению безопасности труда
4.1. Мероприятия по безопасности труда
4.1.1. Защита от механических травм.
Механические травмы при перемещении по участку
Скользкие поверхности пола
Покрытие пола рифленой плиткой или материалом с большим трением
Механические травмы при попадании рук или ног в подвижные части производственного оборудования
Несоблюдение правил техники безопасности
Закрытие подвижных частей кожухами и установления ограждений
Травмирование инструментом
Применение СИЗ от механических воздействий
4.1.2. Электробезопасность.
В цехе 3-х фазная 4-х проводная электрическая сеть с глухо заземленной нейтралью TN-C напряжением 380220В и мощность 1200кВА.
Электроснабжение осуществляется по кабельным линиям под полом (в люках) или по воздуху не ниже 35м над проходами и 6м над проездами. Проводка изолирована и для защиты от механических повреждений уложена в металлорукава. Электроаппаратура смонтирована в специальных электрошкафах с защитными дверьми которые снабжены знаком безопасности. Рубильник защищен кожухами. Для защиты работающих от поражения электрическим током при косвенном прикосновении предусмотрено защитное автоматическое отключение питания от сверхтоков (ПУЭ гл.17) с применением автоматических выключателей А3100.
При выполнении ремонтных работ предусмотрены СИЗ электрические штанги перчатки боты и коврики.
4.2. Мероприятия по производственной санитарии
4.2.1. Обеспечение параметров микроклимата.
Микроклимат производственных помещений определяется температурой воздуха рабочей зоны относительной влажностью и скоростью движения воздуха в рабочей зоне.
Так как рассматриваемый цех относится к помещениям без избытка явного тепла (менее 232Втм3) то проектом рекомендуется обеспечить оптимальные параметры микроклимата. Работы выполняемые на участке относятся к работам средней тяжести IIб (связаны с ходьбой и переносом тяжестей до 10кг энергозатраты 233-290Вт). Оптимальные нормы микроклимата для этой категории для двух периодов года – холодного и теплого в соответствии с ГОСТ 12.1.005-88 приведены в таблице 5.5.
Таблица 5.5 Оптимальные нормы микроклимата
Категория работы по тяжести
Относительная влажность
Скорость движения воздуха мс
Обеспечение указанных параметров микроклимата производится в соответствии со СНиП 41-01-2005 «Вентиляция отопление и кондиционирование».
Отопление воздушное вентиляция приточно-вытяжная у въездных ворот тепловые завесы.
4.2.2. Производственное освещение.
Рабочие места в производственных помещениях должны быть обеспечены освещенностью в соответствии со СНиП 23-05-95.
Для участка диагностики проектом рекомендуется естественное и искусственное освещение. Исходя из характера зрительной работы – считывание показаний с приборов и экранов – относим ее к III разряду (минимальный объект различения 015÷03мм) подразряд В (фон средний контраст средний). Рекомендуемая система искусственного освещения – комбинированная состоящая из общего и местного. Естественное освещение – боковое.
Нормы по СНиП 23-05-95 представлены в таблице 5.6.
Таблица 5.6 Нормы освещенности на рабочих местах зоны ТР
Наименьший размер объек
Указание норм обеспечиваются общим освещением (лампы ЛБ-80 в светильниках) и местным освещением в осмотровой канаве (лампы МОД 36).
Расчет общего искусственного освещения корпуса
Расчет выполняем используя метод коэффициента использования светового потока.
Требуемая освещенность от системы общего освещения – Е = 200лк.
Длина помещения – 54 м.
Ширина помещения – 30 м.
Высота помещения – 7 м.
Высота от потолка до освещаемой рабочей поверхности – 08м.
Светильник ЛСП-01 с лампами Лб-80 имеющими световой поток – 5220лм.
Коэффициент отражения от стен - ρс = 30%.
Коэффициент отражения от потолка - ρп = 50%.
Коэффициент минимальной освещенности – ZН =110 (для люминесцентных ламп).
Выбираем коэффициент запаса исходя из выполняемой работы и запыленность помещения по СНиП 23-05-95 – Кз =16.
Определяем расчетную высоту подвеса светильников над освещаемой поверхностью:
Определяем расстояние между светильниками из условия равномерности освещения:
L = l × h = 15 × 62 = 93
Определяем минимальное количество светильников:
Определяем индекс помещения:
По индексу помещения с учетом коэффициентов отражения и и типа светильника находим по таблице [2 с.128] коэффициент использования светового потока = 062.
Тогда по формуле метода коэффициента использования светового потока находим световой одного светильника:
Этот метод слишком велик и требует в одном светильнике около 26 ламп типа ЛБ-80 что невозможно.
Поэтому корректируем число светильников ограничив число ламп в светильнике двумя.
Тогда число светильников ЛСП-01 с двумя лампами ЛБ-80 будет равно:
Потребляемая искусственным освещением мощность составит:
Р = 80 × 80Вт = 64 кВт.
4.2.3. Защита от шума и вибрации.
Допустимые уровни звукового давления и уровня звука не должны превышать значений указанных в ГОСТ 12.1.003-83* и приведены в таблице 4.7.
Таблица 4.7 Допустимые уровни звука и звукового давления
Средние геометрические частоты октавных полос Гц
Уровень звука и эквивалент дБА
Постоянные рабочие места и рабочие зоны
Уровень звукового давления дБ
Допустимые уровни вибраций категории 3а возникающие на рабочем месте не должны превышать значений указанных в ГОСТ 12.1.012-90 и приведены в таблице 5.8.
Таблица 5.8 Допустимые уровни вибрации
Предельные значения виброскорости мс ×10-2
Предельные значения виброускорения мс2
Логарифмический уровень виброскорости дБ
Логарифмический уровень виброускорения дБ
В качестве акустических средств защиты от шума рекомендуется применять средства звукоизоляции (звукоизолирующие ограждения зданий и помещений звукоизолирующие кожухи и кабины акустические экраны выгородки); средства звукопоглощения (звукопоглощающие облицовки объемные поглотители звука); глушители звука (адсорбционные реактивные комбинированные).
Для защиты от вибрации рекомендуется применять средства виброизоляции (виброизолирующие опоры упругие прокладки конструкционные разрывы) средства демпфирования (линейные и нелинейные).
5. Мероприятия и средства защиты окружающей среды от проектируемого АТП
5.1. Очистка воздуха
Воздух выбрасываемый из системы вытяжной общеобменной вентиляции проходит сначала очистку от взвешенных частиц в циклоне ЦН-15 а затем рукавных фильтрах.
5.2. Очистка производственных вод
Для очистки производственных сточных вод от взвешенных частиц и нефтепродуктов проектом рекомендуются отстойники осветлители и нефтеловушки.
Очищенная вода пускается по замкнутому циклу.
Расчет центробежного циклона для очистки воздуха
Цель расчета - определить эффективность предварительной очистки воздуха выбрасываемого центробежным циклоном из вентиляционной системы.
Расход очищаемого воздуха Q = 50м3с.
Динамическая вязкость воздуха m = 1837 × 10-6 Па×с
Плотность воздуха ..рг = 129тм3.
Плотность материала частиц пыли С = 01гм3.
Средний размер частиц пыли .d =38мкм.
Оптимальная скорость воздуха в сечении циклона = 35мс.
Требуемая эффективность очистки = 095.
Поправочный коэффициент на запыленность воздуха К2 = 095 (табл.).
Поправочный коэффициент на диаметр циклона .. К1 = 1 (табл.).
Коэффициент гидравлического сопротивления одиночного циклона диаметром 05 м К500 = 155 (табличное).
Коэффициент учитывающий потери давления связанные с компоновкой циклона в группу К3 = 35 (для одиночного циклона К3 = 0).
Принимаем количество циклонов n кратным двум в зависимости от расчетной скорости воздуха в установке (т = 2 4 6 8).
Алгоритм расчета циклона:
Требуемая площадь сечения циклона равна:
S = Q = 50 35 = 143м2
Рассчитываем диаметр циклона по формуле:
Полученное расчетное значение Dц округляем до диаметра стандартного циклона Dц= 05м (табл.).
Находим действительную скорость воздуха в данном стандартном циклоне:
Определяем отклонение действительной скорости от оптимальной:
Δ = 100 × [(V – V Vc)] = [(35 - 32) 35] × 100 = 91%.
Полученное отклонение не превышает 15%. Поэтому диаметр циклона выбран правильно.
Коэффициент гидравлического сопротивления одиночного циклона:
= К1 × К2 × К500 + К3 = 1 × 087 × 155 + 35 = 169.
Гидравлическое сопротивление циклона:
Δр = × рг -V2 2 = 169 × 129 × 101 2 = 1106Па.
Рассчитываем значение параметра d50 при рабочих условиях (после определения табличных параметров и характеризующих эффективность циклона):
Определяем численное значение параметра c по формуле:
Находим табличное значение функции Лапласа Ф(c). Оно соответствует полному коэффициенту очистки газа = 0992 (требуемый коэффициент очистки по условиям задания равен = 095).
6. Мероприятия и средства по обеспечению безопасности в чрезвычайных ситуациях
6.1. Обеспечение взрывопожаробезопасности
Система пожарной защиты
Обеспечение пожарной безопасности осуществлено в соответствии с ППБ 01-03.
В соответствии с этим документом проектом рекомендуется оснастить цех автоматической пожарной сигнализацией (датчики КИ-1) иметь следующие первичные средства пожаротушения:
иметь спринклерную систему пожаротушения.
Для обеспечения молниезащиты АТП выбираем тип зоны и категорию устройств молниезащиты которые помещаем в таблицу 4.10.
Таблица 5.10 Тип зоны и категории устройств молниезащиты
Производственные помещения которые по ПУЭ относятся к классам П-I П-II и П-IIа
В местностях со среднегрозовой деятельностью 20 часов в год
Для зданий и сооружений I и II степени огнестойкости при 01N2 и для III IV и V степеней огнестойкости при 002N2 - зoнa Б; при N>2 - зона А
Здания и сооружения III категории молниезащиты защищены от прямых попаданий молнии и заноса высоких потенциалов через наземные металлические коммуникации. Для молниезащиты здания выбираем двойной стержневой молниеотвод высотой - 30м.
Организационно-экономическая часть
1. Организационный раздел
1.1. Организационно-правовая форма собственности предприятия
Принимаем организационную форму предприятия на первом этапе его развития – акционерное общество закрытого типа (частные инвестиции). Предварительная оценка рынка показывает что потребность в таком предприятия есть. Потому форма предприятия в виде закрытого акционерного общества позволяет на первом этапе развития предприятия более гибко и быстро принимать различные организационные решения так как основные решения принимает небольшое количество людей.
В дальнейшем если работа предприятия будет успешной и оно будет расширяться то его можно преобразовать в акционерное общество открытого типа и получить таким образом дополнительное финансирование на развитие предприятия выпустив акции предприятия в свободную продажу.
1.2. Организационная структура предприятия
Организационная структура предприятия принимается упрощенная. Она приведена на рис. 6.1.Расчет штатного расписания АТП проводим методом укрупненного нормирования. Численность руководителей специалистов и служащих принимаем в размере 8 11% от общей численности рабочих. Численность вспомогательных рабочих принимаем в размере 10 25% от численности ремонтных рабочих. Штатное расписание предприятия дано в таблице 6.4.
Перечень должностных обязанностей руководителей сновных структур АТП
Планирование и организация бухгалтерского учета.
Контроль за состоянием расчетов с предприятиями организациями учреждениями и лицами а также сохранность денежных средств и товарно-материальных ценностей.
Контроль за рациональным и экономным использованием материальных трудовых и финансовых ресурсов организации.
Формирование в соответствии с действующем законодательством и нормативно-правовыми актами о бухгалтерском учете учетной политики исходя из структуры и особенностей деятельности организации.
Проведение инвентаризации денежных средств товарно-материальных ценностей расчетов с организациями.
Проведение совместно со структурными подразделениями организации экономического анализа хозяйственно-финансовой деятельности по данным бухгалтерского учета в целях выявления внутрихозяйственных резервов предупреждение потерь и непроизводственных расходов.
Составление баланса и оперативных сводных отчетов о доходах и расходах средств об использовании бюджета другой бухгалтерской и статистической отчетности представление их в установленном порядке в соответствующие органы.
Руководство всем производственным процессом обеспечения подвижного состава комплексом работ по ТО и ТР.
Корректировка технической документации получаемой предприятием со стороны применительно к конкретным условиям.
Разработка технических условий на проектирование изготовление и поставку стендов собственной разработки.
Рассмотрение и принятие решений по техническим вопросам возникающим в процессе ремонта автомобилей выдача разрешений на изменение чертежей.
Планирование производственного процесса ЕО и ТО и ТР.
Организация бесперебойного обеспечения АТП запчастями и технологическим оборудованием.
Начальник ремонтного производства:
Руководство производственным процессом работ по ЕО и ТО и ТР.
Начальник производственно-технического отдела:
Разрабатывает планы по внедрению новой техники и технологий.
Разрабатывает и проводит мероприятия по охране труда и технике безопасности.
Осуществляет работы по составлению технических нормативов и технической документации.
Осуществляет содержание в технически исправном состоянии зданий сооружений энергосилового и санитарно-технического хозяйства.
Обслуживание и ремонт технологического оборудования производства
Обеспечивает бесперебойное материально-техническое снабжение АТП.
Организует правильную работу складского хозяйства.
Осуществляет контроль качества работ на производстве.
Осуществляет контроль качества услуг АТП.
Осуществляет контроль состояния подвижного состава и технологического оборудования.
Зам. Гендиректора по эксплуатации:
Организует и руководит всей работой подвижного состава на линии.
Организует планирование работ подвижного состава
Начальник отдела эксплуатации:
Обеспечивает организацию работ подвижного состава и планирование грузовых перевозок
Руководитель группы организации перевозок
Обеспечивает организацию работ подвижного состава на линии непосредственно руководит перевозками грузов.
Выпускает автомобили на линию контролирует выездную документацию распределяет грузовые потоки.
Руководитель группы анализа перевозов:
Организует анализ состояния грузовых перевозок и разрабатывает планы повышения их эффективности.
Организует и контролирует мероприятия по безопасности движения подвижного состава.
Зам. Гендиректора по экономике:
Организует работу по разработке финансово-экономических планов предприятия. Анализирует экономические показатели предприятия и разрабатывает планы по их улучшению.
Начальник планово-экономического отдела:
Разрабатывает экономические планы развития предприятия контролирует текущее состояние финансово-экономической деятельности
Начальник отдела труда и заработной платы:
Организует работу по начислению и контролю заработной платы работников предприятия
Начальник отдела кадров:
Организует работу отдела кадров ведет учет всего работающего персонала предприятия
Начальник административно-хозяйственного отдела:
Решает социальные и хозяйственные вопросы на предприятии.
Руководит всеми вспомогательными службами в части хозяйственного обслуживания подразделений предприятия.
2. Экономический раздел
Таблица 6.1 Исходные технико-эксплуатационные показатели использования автотранспортных средств АТП
Списочное количество автомобилей Асп
2.1. Расчет стоимости основных производственных фондов
Расчет стоимости основных производственных фондов АТП производится последующим группам: здания и сооружения; дорогостоящие инвентарь и приспособления; оборудование и рабочие машины; автотранспортные средства.
Стоимость зданий и сооружений
Стоимость зданий и сооружений определяется по формуле:
где Цз – общая стоимость здания руб м3;
цз – стоимость одного м3 здания руб м3;
Vз – объем здания м3;
Стоимость открытой стоянки и затраты на благоустройство незастроенной территории определяется по формуле:
где цс – стоимость одного м2 открытой стоянки или благоустройства территории рубм2;
Sо – площадь открытой стоянки или благоустройства территории м2.
Затраты на проектно–изыскательские работы (привязка к местности) принимаем в размере 15% от стоимости зданий и сооружений.
Стоимость дорогостоящего инструмента и приспособлений следует принимаем в размере 24% от стоимости зданий и сооружений.
Стоимость оборудования и рабочих машин определяется в размере 2030% для грузовых от стоимости зданий и сооружений.
Для средних условий эксплуатации стоимость грузового АТС составляет 6070 от стоимости всех основных фондов производственного назначения.
Балансовая стоимость Цаб парка АТС рассчитывается на основании среднесписочного количества АТС их оптовой цены и добавленной стоимости на доставку и приобретение по формуле:
где Ца – оптовая цена данной модели АТС руб.;
Кт – коэффициент учитывающий затраты на доставку и постановку на учет АТС (Кт=106108);
Кн - коэффициент учитывающий налог на приобретение АТС (Кн=11).
Определим балансовую стоимость АТС.
Цаб борт. = Ца · Кт · Кн · Nавт = 2000000 · 105 · 11 · 77 = 177870 тыс. руб.
Цаб самос. = Ца · Кт · Кн · Nавт = 2200000 · 105 · 11 · 145 = 368445 тыс. руб.
Результаты расчета стоимости основных фондов (ОФ) приведены в таблице 6.2.
Балансовая стоимость основных фондов создается за счет капитальных вложений. Источником финансирования капитальных вложений являются собственный капитал включая амортизационные отчисления бюджетные ассигнования и банковский кредит.
Таблица 6.2 Стоимость основных фондов АТП
Виды основных фондов
Общая площадь здания м2
Удельная стоимость рубм3 или рубм2
Балансовая стоимость единицы ОФ тыс. руб.
Трансформаторная станция
Центральный тепловой пункт
Благоустройство незастроенной территории
Привязка к местности (15% от суммы пп1-6)
Итого по зданиям и сооружениям (пп1-8)
Дорогостоящие инструменты приспособления и инвентарь (24% от п9)
Оборудование и рабочие машины (30% от п9)
Всего ОФ без АТС (п9+п10+п11)
Автотранспортные средства
2.2. Расчёт потребности АТП в материальных затратах
Расчет материальных затрат на выполнение прогнозируемого объема перевозок проводится в натуральном и стоимостном выражении по следующим группам: автомобильное топливо смазочные материалы керосин для технологических нужд обтирочные материалы прочие эксплуатационные материалы ремонтные материалы и запасные части восстановление износа и ремонт шин. Расчет ведем за год.
Объемный расход автомобильного топлива для АТС работа которых учитывается в тонно-километрах определим по формуле:
Gл = 001 · (Нл + Hткм · q · ·) · Kз · Kд · Kг · Lобщ = 001 · (25 + 13 · 1686 · 077 · 05 ) · 1042 · 085 · 1005 · 16425052 = 4888835 л
где Нл = 25 л100км – норма расхода топлива на пробег;
Нткм = 1.3 л100 км – норма расхода топлива на транспортную работу;
q = 1686 т – грузоподъемность автомобиля;
К3 = 1.042 – коэффициент учитывающий расход топлива в зимний период (три зимних месяца);
Kд = 0.85 - коэффициент учитывающий дорожные условия (для внегородских дорог с усовершенствованным покрытием;
Кг = 1.005 – коэффициент учитывающий расход топлива на внутри гаражные нужды;
Lобщ = 16425052 км – общий пробег всех АТС;
= 077 - средний коэффициент статического использования грузоподъёмности;
= 05 - средний коэффициент использования пробега;
Расход смазочных материалов по каждому виду (моторное масло трансмиссионное масло консистентная смазка) определяется по формуле:
где Ксм – норма расхода смазочных материалов в литрах от расхода топлива для масел или в килограммах от расхода топлива для консистентной смазки (приложение 2 табл. 12).
Моторные масла: Gм.м. = 4888835 · 005 = 244442 л
Трансмиссионные масла: Gт.м. = 4888835 · 0005 = 24444 л
Пластичные смазки: Gп.с. = 4888835 · 0003 = 14667 кг
Специальные масла:Gс.м. = 4888835 · 001 = 48888 кг.
Расход технического керосина Gк принимается в размере 0.5% от весового расхода топлива:
Gк = 0005 · Gл · т = 4888835 · 0005 · 0825 = 20166 кг
где т = 0825 кгл - плотность топлива.
Расход обтирочных материалов Gоб определяется по нормам Ноб расхода на одну единицу АТС в год: грузовые автомобили – 36 кгед.
Gоб = Асс · Ноб = 222 · 36 = 7992 кг
Затраты на прочие эксплуатационные материалы (электролит дистиллированную воду антифриз тормозную жидкость) можно принять в размере 10% от суммы затрат по всем видам масел и техническому керосину.
Затраты на ремонтные материалы (Зрм) и запасные части (3зч) необходимые для проведения технических обслуживаний и текущих ремонтов в денежном выражении определяются на основании норм затрат в руб. на 1000 км пробега и общего пробега парка по формуле:
- ремонтные материалы
Зрм = 0001 · Нрм · Lобщ = 0001 · 150 · 16425052 = 2463758 руб.
где Нрм = 150 руб.1000 км - норма затрат на ремонтные материалы (приложение 1 табл. 14);
Зз.ч. = 0001 · Нзч · Lобщ = 0001 · 134 · 16425052 = 2200957 руб.
Затраты на восстановление и ремонт шин определяются на основании нормативов на 1000 км пробега и норм пробега шин по типам автомобилей.
Расчет затрат на восстановление и ремонт шин проводится по формуле:
ш = 0001 · Цш · nк· Нш · Lобщ = 0001 · 8000 · 10 · 089 100 · 16425052 = 11694637 руб.
где Цш = 8000 руб. – стоимость одного комплекта шин (покрышка камера ободная лента);
nк = 10 – число колес на автомобиле без учета запасного колеса шт;
Нш = 089% - норма отчислений на восстановление и ремонт одного комплекта шин на 1000 км пробега для соответствующего размера шин и условий эксплуатации (приложение 1 табл. 15).
Результаты расчёта потребности в материальных затратах приведены в таблице 6.3
Таблица 6.3 Потребность АТП в материальных затратах
Цена за единицу руб.
Всего затраты тыс. руб.
Автомобильное топливо л
Трансмиссионное масло л
Консистентная смазка кг
Технический керосин л
Обтирочные материалы кг
Всего масел и других эксплуатационных материалов (сумма пп 2-8)
Всего ремонтные материалы и запчасти
Восстановление и ремонт шин
2.3. Расчет численности и фонда оплаты труда по категориям работающих
А) Расчет фонда оплаты труда водителей
Среднесписочная численность водителей
Среднесписочная численность водителей определяется по формуле:
Nв = (АЧр + 0.2 · АЧТО-2 + АЧр · tп.з.) (Фг.в. · Кw) = (520045 + 02 · 48108 + 520045 · 0042) (1755 · 11) = 286 чел.
где АЧр = 520045 ч - автомобиле часы работы на линии (рассчитаны в эксплуатационной части проекта);
АЧТО-2 – объем времени участия водителей в ТО может быть принят равным 10-20% от трудоемкости ТО-2;
tп.з. – подготовительно – заключительное время водителей принимается 0.042 час на 1 час работы водителей;
Фг.в. = 1755 ч – годовой фонд рабочего времени водителя;
Кw = 1.1 – коэффициент роста производительности труда.
Расчет основной заработной платы водителей
Сдельная расценка за 1 т перевозимого груза и за 1 т·км транспортной работы определяется по формулам:
Sт = (Счас · tпр) (60 · q) = (140 · 41) (60 · 1686 ) = 57 рубт;
Sткм = (Счас · (tдв + tпр) · Кзп) (60 · V · q · н) = (140 · (60+41) · 125) (60 · 38 · 1686 · 045) = 10 рубт·км;
где Счас = 140 руб. – часовая тарифная ставка водителя третьего класса данной группы автомобилей руб.;
tпр = 41 мин. – норма времени простоя автомобиля под погрузкой и разгрузкой на ездку;
tдв = 60 мин. – норма времени движения автомобиля на 1 ч работы;
q = 1686 т. - грузоподъемность автомобиля;
Кзп = 125 - коэффициент учитывающий изменение сдельных расценок от класса перевозимого груза (принимается для 2-го класса);
н = 048 – нормативный коэффициент использования пробега;
V = 38 кмч - норма пробега автомобилей для соответствующей категории дорог "II".
Sт – сдельная расценка за 1 тонну перевезенного груза руб.;
Рткм = 38 (113332521) должно быть т·км – транспортная работа;
Sткм – сдельная расценка за 1 т·км транспортной работы.
Основная заработная плата водителей работающих по сдельным расценкам за перевезенные тонны и выполненные тонно-километры определяется по формуле:
ОЗП = Qт · Sт + Рткм · Sткм = 1350001 · 57 + 113332521 · 10 = 121028 тыс. руб.
где Qт = 1350001 т – объем перевоза груза;
Расчет доплат водителям
Водителям работающим на грузовых и легковых автомобилях выплачивается ежемесячная надбавка от часовой тарифной ставки водителя 3 класса в следующих размерах: водителям второго класса – 10% водителям первого класса – 25%.
Принимаем что на АТП работает:
- водителей первого класса – 10% 29 чел.;
- водителей второго класса – 20% 57 чел.
Надбавку за классность рассчитывают за отработанное время исходя из месячной тарифной ставки водителя 3 класса.
Нкл = Счас · Фмв · nм · (dкл2 · Nв2 + dкл1 · Nв1) = 140 · 1755 · 11 · (01 · 57 + 025 · 29) = 35000 тыс. руб
где nм = 11 - число месяцев работы водителя в планируемом периоде;
Nв2 Nв1 - численность водителей соответственно второго и первого классов;
dкл2 dкл1 - надбавка за классность водителям соответственно второго и первого классов;
Доплата бригадирам за руководство бригадой:
Дбр= 001 · Счас · Фгв · nбр · dбр = 001 · 140 · 1755 · 14 · 10 = 344 тыс. руб.
где nбр - количество бригад водителей; nбр = Nв nв = 286 20 = 14;
nв - количество водителей в бригаде;
dбр = 10% - доплата бригадирам за руководство бригадой.
Доплата за работу в сверхурочное время принимаем 5 ÷ 7% от основной заработной платы.
Дсв.у. = 005 · ОЗП = 005 · 121028 = 6051 тыс. руб.
Премии водителям за качественное выполнение работ принимает 40% от фонда основной заработной платы.
Дпр. = 04 · ОЗП = 04 · 121028 = 48411 тыс. руб.
Дополнительная заработная плата - 106% от фонда основной заработной платы.
Ддоп. = 0106 · ОЗП = 0106 · 121028 = 12829 тыс. руб.
Расчет отчислений на социальные нужды
Отчисления на социальные нужды для частного предприятия составляют 395% от суммы основной и дополнительной оплаты труда.
Осоц = 0395 · (ОЗП + Ддоп) = 0395 · (121028 + 12829) = 52874 тыс. руб.
Фонд оплаты труда водителей.
ФОТв = ОЗП + Нкл + Дбр + Дсв.у + Дпр +Ддоп = 121028 + 35000 + 344 + 6051 + 48411 + 12829 = 223663 тыс. руб.
Среднемесячная заработная плата одного водителя.
Зср.м. = ФОТв (12 · Nв) = 223663 (12 · 286) = 652тыс. руб.
Б) Расчёт фонда оплаты труда ремонтных рабочих
Численность ремонтных рабочих - Npp = 122 чел.
Расчёт заработной платы ремонтных рабочих
Основная заработная плата ремонтных рабочих включает: заработную плату рассчитанную по тарифам за отработанное время и различные виды доплат – за руководство бригадой сверхурочные работы работы в ночное время и др.
Заработная плата по тарифу производится по формуле:
ПРР = Счас · Т = 200 · 212275 = 42455 тыс. руб.
где Счас = 200 рубч – часовая тарифная ставка соответствующая условиям труда;
Т = 212275 чел·ч- трудоемкость работ выполняемых в соответствующих условиях труда чел·ч.
Общую величину доплат ремонтным рабочим по укрупненному расчёту целесообразно принимать в размере 810% от основной заработной платы по тарифу.
Добщ.доп = 01 · 3ПРР = 01 · 42455 = 4246 тыс. руб.
Премирование за выполнения задания по обеспечению выпуска автомобилей на линию – в размере до 30 % тарифной ставки.
Дпр = 03 · 3ПРР = 03 · 42455 = 12737 тыс. руб.
Основная заработная плата ремонтных рабочих.
ОЗПрр = 3ПРР + Добщ.доп + Дпр = 42455 + 4246 + 12737 = 59438 тыс. руб.
Дополнительную заработную плату принимаем в размере 11% от основной заработной платы ремонтных рабочих.
Ддоп = 011 · ОЗПрр = 011 · 59438 = 6538 тыс. руб.
Отчисления на социальные нужды
Осоц = 0395 · (ОЗПрр + Ддоп) = 0395 · (59438 + 6538) = 26061 тыс. руб.
Фонд оплаты труда ремонтных рабочих
ФОТрр = ОЗПрр + Ддоп = 59438 + 6538 = 65976 тыс. руб.
Среднемесячная заработная плата одного ремонтного рабочего
Зср.рр = ФОТрр (12 · Npp) = 65976 (12 · 122) = 45 тыс. руб.
В) Расчёт фонда оплаты труда вспомогательных рабочих
Численность вспомогательных рабочих принимаем в размере 2025% от численности ремонтных рабочих.
Nвр = 025 · Nрр = 122 · 025 = 31 чел.
Пвр = Счас · Т · Nвр = 150 · 1840 · 31 = 8556 тыс. руб.
где Т = 1840 ч – годовой фонд рабочего времени вспомогательного рабочего.
Доплаты за работу в ночное время за работу в праздничные дни а также премии могут быть приняты в размере 20% от заработной платы по тарифам.
Добщ.доп = 02 · 3Пвр = 02 · 8556 = 1711 тыс. руб.
ОЗПвр = 3Пвр + Добщ.доп = 8556 + 1711 = 10267 тыс. руб.
Дополнительная заработная плата принята в размере 106% от заработной платы по тарифам.
Дд = 0106 · О3Пвр = 0106 · 10267 = 1088 тыс. руб.
Отчисления на социальные нужды
Осоц = 0395 · (ОЗПвр + Дд) = 0395 · (10267 + 1088) = 4485 тыс. руб.
Фонд оплаты труда вспомогательных рабочих
ФОТвр = ОЗПвр + Дд = 10267 + 1088 = 11355 тыс. руб.
Среднемесячная заработная плата одного вспомогательного рабочего
Зср.вр = ФОТвр (12 · Nвр) = 11355 (12 · 31) = 305 тыс. руб.
Г) Расчёт фонда оплаты труда ИТР
Численность ИТР принимаем 15% от числа водителей. В указанный процент не входят работники сторожевой службы и пожарной охраны а также производственно-линейный персонал.
Nитр = 286 · 015 = 43 чел.
Таблица 6.4 Штатный список ИТР АТП
Структурные подрапзделения
наименование должности
Генеральный директор АТП
Зам гендиректора по экономике
Зам гендиректора по эксплуатации
Планово-экономический отдел
Отдел труда и заработной платы
Руководитель группы по организации перевозок
Производственно-технический отдел
Диспетчер производства
Производственно-линейный персонал
Отдел технического контроля
Отдел материального-технического снабжения
Младший обслуживающий персонал и пожарная охрана (ПСО)
Прочие рабочие (ПВР)
Инструментальщик кладовщик
Доплаты за работу в ночное время за работу в праздничные дни могут быть приняты в размере 20% от заработной платы.
Добщ.доп = 02 · 3Питр = 02 · 17124 = 3425 тыс. руб.
Основная заработная плата ИТР
ОЗПитр = 3Питр + Добщ.доп = 17124 + 3425 = 20549 тыс. руб.
Дополнительная заработная плата принята в размере 106% от заработной платы.
Дд = 0106 · О3Питр = 0106 · 20549 = 2178 тыс. руб.
Премирование по результатам хозяйственной деятельности – в размере до 40 % тарифной ставки.
Дпр = 04 · 3Питр = 04 · 17124 = 6850 тыс. руб.
Осоц = 0395 · (ОЗПитр + Дд) = 0395 · (20549 + 2178) = 8977 тыс. руб.
Фонд оплаты труда ИТР
ФОТитр = ОЗПитр + Дд + Дпр = 20549 + 2178 + 6850 = 29577 тыс. руб.
Среднемесячная заработная плата одного ИТРовца
Зср.итр = ФОТитр (12 · Nитр) = 29577 (12 · 52) = 47 тыс. руб.
Расчет фонда оплаты труда дан в таблице 6.5.
Таблица 6.5 Потребность в персонале и фонд оплаты труда
Категории работающих
Ср. мес. зп тыс. руб.
Отчисления на социальные нужды тыс. руб.
ФОТ с отчислениями на социальные нужды тыс. руб.
Вспомогательные рабочие
Руководители специалисты и служащие (ИТР)
2.4. Затраты на амортизацию подвижного состава
Затраты на амортизацию определяются исходя из балансовой стоимости и норм амортизационных отчислений с учетом срока службы по формуле:
Зам.борт. = (Сатс · На.сл · Асс) 100 = (23100 · 15 · 77) 100 = 26681 тыс. руб.
Зам.самос. = (Сатс · На.сл · Асс) 100 = (25410 · 15 · 145) 100 = 55267 тыс. руб.
Сатс - балансовая стоимость одного АТС руб.;
На.сл - норма амортизационных отчислений в зависимости от амортизационного срока службы АТС %;
Асс - среднесписочное количество АТС;
Норму амортизационных отчислений применительно к конкретным условиям эксплуатации определим для автомобилей с учетом амортизационного срока На.сл по формуле:
Нам.сл.борт. = (100 · (Сатс - Со)) (Сатс · Тсл) = (100 · (23100 - 231)) (23100 · 6) = 15 %
Нам.сл.самос. = (100 · (Сатс - Со)) (Сатс · Тсл) = (100 · (25410 - 2541)) (25410 · 6) = 15 %
где Со – остаточная стоимость одного АТС (можно принять 10% от Сатс) руб.;
Тсл – амортизационный (нормативный) срок службы одного АТС (можно принять 6 лет);
Нормы амортизационных отчислений по стационарным основным фондам (здания сооружения оборудование и т.п.) принимаем в размере 38%.
Затраты на амортизацию зданий и сооружений:
Зам.зд. = (Сзд · На.зд) 100 = (350933 · 5) 100 = 17547 тыс. руб.
где Сзд - балансовая стоимость зданий и сооружений.
Затраты на амортизацию технологического оборудования:
Зоб. = (Соб · На.зд) 100 = (112299 · 5) 100 = 5615 тыс. руб.
где Соб - балансовая стоимость технологического оборудования.
Результаты расчёта затрат на амортизацию по основным фондам представлены в таблице 6.6
Таблица 6.6 Затраты на амортизацию основных фондов
Балансовая стоимость ОФ тыс. руб.
Стоимость отчислений тыс. руб.
Здания сооружения производственного назначения
Технологическое оборудование
По укрупненному расчету величина прочих затрат должна составлять 57% общей величины сметы эксплуатационных затрат.
2.6. Смета эксплуатационных затрат
Расчет эксплуатационных затрат сводим в таблицу 6.7.
Таблица 6.7 Смета эксплуатационных затрат
Сумма затрат тыс. руб.
Структура затрат % к итогу
Автомобильное топливо
Восстановление и ремонт автомобильных шин
Амортизация ОПФ всех видов
2.7. Калькуляция себестоимости перевозок
Калькуляция себестоимости перевозок представляет собой расчет величины эксплуатационных затрат приходящихся на единицу транспортной работы.
При калькуляции себестоимости предусматривают статью затрат "Накладные расходы" которые не зависят от размеров движения (транспортной работы) и по производственному назначению относятся к постоянным затратам. Накладные расходы определяют как сумму прочих затрат фонда оплаты труда с отчислениями на социальные нужды вспомогательных рабочих руководителей специалистов и служащих амортизации основных фондов без АТС.
Для средних условий эксплуатации величина накладных расходов может составить 1520% от общей величины эксплуатационных затрат АТП.
Себестоимость перевозок по каждой статье определяют путем деления суммы эксплуатационных затрат ΣSэк соответствующей статьи за определенный период времени на выполненную транспортную работу
Себестоимость калькулируют по грузовым перевозкам на 10 т·км при применении тарифа за выполненные т·км.
Определим накладные расходы:
Нр = 57503 + 54394 + 23162 = 135059 тыс. руб.
Калькуляция себестоимости перевозок приведена в таблице 6.8
Таблица 6.8 Калькуляция себестоимости перевозок
Всего по АТП тыс. руб.
Себестоимость руб.10 т·км
Структкра затрат % к итогу
Фонд оплаты труда водителей с отчислением на социальные нужды
Смазочные и эксплуатационные материалы
Техническое обслуживание и ремонт АТС
2.8. Расчёт потребности нормируемых оборотных средств
Исходными данными для определения оборотных средств являются смета эксплуатационных затрат и установленные нормы запаса в днях по каждой группе материальных ценностей входящих в состав оборотных средств.
В соответствии с Положение о бухгалтерском учете и отчетности в Российской Федерации в составе средств в обороте (малоценные быстроизнашивающиеся предметы) учитываются предметы срок службы которых меньше года независимо от стоимости а также стоимостью на дату приобретения не более пятидесятикратного установленного законом минимального размера месячной оплаты труда за единицу без ограничения срока их службы.
Сумма потребных нормируемых оборотных средств Фн. об определяется по формуле:
Фн.об = (Si · Hi) Дк
Дк = 357 дней - число календарных дней расчетного периода.
К эксплуатационным материалам относятся: смазочные и обтирочные материалы технический керосин и др. Фонд оборотных агрегатов можно определить из расчета 7075% от норматива оборотных средств по статье “Запасные части”. Прочие нормируемые оборотные средства (топливо для хозяйственных нужд материалы лесоматериалы краски тормозная жидкость малоценный и быстро изнашивающийся инвентарь и инструменты спецодежда и т.п.) можно принять в размере 5% от их общей суммы.
Результаты расчета потребности нормируемых оборотных средств приведены в таблице 6.9.
Таблица 6.9 Потребность в нормируемых оборотных средствах
Наименование оборотных средств
Норматив оборотных средств тыс. руб.
По схеме затрат расходов
Эксплуатационные материалы
Фонд оборотных агрегатов
Прочие нормируемые средства
Всего нормируемые оборотные средства Фн.об
2.9. Расчёт финансовых показателей
Экономическая целесообразность хозяйственной деятельности предприятия определяется абсолютными и относительными показателями. Различают две основные группы показателей экономического эффекта и экономической эффективности.
Экономический эффект – показатель характеризующий общий результат хозяйственной деятельности предприятия. В АТП в качестве основного показателя безубыточности предприятия является прибыль. Однако по этому показателю взятому изолированно нельзя сделать обоснованный вывод по использованию вложенного капитала и ресурсов. Поэтому используют показатели экономической эффективности деятельности предприятия.
Экономическая эффективность – относительный показатель который соизмеряет полученный эффект с затратами и ресурсами при достижении этого эффекта.
В АТП в качестве основных относительных показателей характеризующих уровень экономической эффективности хозяйственной деятельности предприятия являются рентабельность общая (основных фондов и нормируемых оборотных средств) рентабельность производственных затрат и другие показатели. Расчет ведем за год.
Прибыль Пб от реализации работ и услуг определяется как разница между суммой всех доходов и поступлений и суммой всех затрат понесённых предприятием за период деятельности с начала года.
Прибыль (балансовая) определяется из выражения:
Пб = Д - Зэкс = 1140352 - 877194 = 263158 тыс. руб.
где Д - общая сумма доходов за грузовые перевозки;
Зэкс – эксплуатационные затраты.
Доход предприятия определим по укрупненной формуле:
Д = Зэкс· КР = 877194 · 13 = 1140352 тыс. руб.
где КР – коэффициент учитывающий рентабельную работу АТП для средних условий эксплуатации по грузовым перевозкам КР = 13
Эксплуатационные затраты определим по формуле:
Зэкс = 01 · Сусл · Р = 01 · 774 · 113332521 = 877194 тыс. руб.
где Сусл = 774 руб. (10 т·км) – себестоимость грузоперевозок;
Р = 113332521 т·км – произведенная работа за год.
Прибыль остающуюся в распоряжении предприятия (Пост) можно рассчитывать из выражения:
Пост = Пб - Нпр - Ним - Ндор - Ндр = 263158 - 63158 - 20474 - 22807 - 3947 = 152772 тыс. руб.
где Нпр – налог на прибыль (24% от Пб) руб.;
Нпр = 024 · 263158 = 63158 тыс. руб.
Ним – налог на имущество (2% от стоимости основных и нормируемых оборотных фондов) руб.;
Ним = 002 · (1009547 + 14135) = 20474 тыс. руб.
Ндор - налог на пользователей автомобильных дорог (2% от доходов за перевозки) руб.;
Ндор = 002 · 1140352 = 22807 тыс. руб.
Ндр – другие виды налогов относимые на прибыль платежи кредиторам и собственникам предприятия (15% от Пб) руб.
Ндр = 0015 · 263158 = 3947 тыс. руб.
Фонд технического перевооружения и реконструкций (60% от Пост) тыс. руб.
ФТР = 152772 · 06 = 91663 тыс. руб.
Фонд социального развития (25% от Пост) тыс. руб.
ФСР = 152772 · 025 = 38193 тыс. руб.
Фонд материального стимулирования (10% от Пост) тыс. руб.
ФМС = 152772 · 01 = 15277 тыс. руб.
Резервный фонд (5% от Пост) тыс. руб.
РФ = 152772 · 005 = 7639 тыс. руб.
Рентабельность общая Rобщ по балансовой прибыли показывает сколько денежных единиц прибыли получено предприятием с единицы стоимости активов (основных фондов и нормируемых оборотных средств).
Rобщ = Пб (Фосн + Фн.об) · 100% = 263158 (1009547 + 14135) · 100 = 26 %
Рентабельность перевозок Rпер по балансовой прибыли показывает насколько эффективно предприятие ведет производственную деятельность по перевозкам (по выпуску продукции) и рассчитывается по формуле:
Rпер = Пб Зэкс · 100% = 263158 877194 · 100 = 30 %
Рентабельность по чистой (остающейся на предприятии) прибыли:
Rпер.чист = Пост Зэкс · 100% = 152772 877194 · 100 = 17 %
Показатель производительности труда в натуральном (Wн) и стоимостном выражении (Wс) определяется как объем транспортной работы или объем валового дохода на одного работающего:
- в натуральном выражении:
Wн = Р Nраб = 113332521 491 = 230820 т·кмчел.
- в стоимостном выражении:
Wс = Д Nраб = 1140352 491 = 2323 тыс.руб.чел.
2.10. Расчёт показателей использования производственных фондов
Эффективность производства оценивается также и другими показателями характеризующими использование производственных фондов.
Фондоотдача Коф показывает размер дохода на один рубль основных фондов:
Коф = Д Фосн = 1140352 1009547 = 113
Период окупаемости инвестиций Ток в проектируемое предприятие:
Ток = (Фосн + Фн.об) Пост = (1009547 + 14135) 152772 = 67 лет
2.11. Оценка экономической эффективности инвестиций.
Оценку варианта эффективности инвестиций рекомендуется проводить по показателю чистый дисконтированный доход (ЧДД). Вспомогательными показателями могут быть период окупаемости инвестиций индекс доходности и другие показатели отражающие интересы участников или специфику проекта.
ЧДД определяется как алгебраическая сумма текущих эффектов за весь расчетный период приведенных к базисному (начальному) шагу.
При равномерных инвестициях:
ЧДД = - [Kt (1+R)t] + [(Пч + Зам) (1+R)t] + Kл(1+R)t тыс. руб.
Где: t – номер шага расчета (год);
R – норма дисконта (0.15);
Kt – размер инвестиций t-го периода (Фосн + Фн.об);
Пч – чистая прибыль;
Зам – амортизационные затраты;
Кл – ликвидные капиталовложения за весь период расчета рекомендуется прибыль Кл = 01 · К;
ЧДД = - 1023682(1+015) + (152772+105110)(1+015)1 + (152772+105110)(1+015)2 + (152772+105110)(1+015)3 + (152772+105110)(1+015)4 + (152772+105110)(1+015)5 + 01·1023682(1 + 015)6 = 18560 тыс. руб.
ЧДД инвестиционного проекта положителен проект является эффективным
( при данной норме дисконта) и может рассматриваться вопрос о его принятии.
2.12. Расчёт точки безубыточности
При оценке всех затрат инвестиционного проекта (в дипломе это создание АТП) их можно условно разделить на две составляющие :
- постоянные затраты (новые капвложения – это основные фонды табл.6.3.) они не изменяются в течение реализации проекта;
- переменные затраты зависящие от количества проданных услуг (в нашем случае грузоперевозки).
При методике расчета затрат в соответствии с [14] переменные затраты соответствуют себестоимости грузоперевозок (табл.6.8.).
Точкой безубыточности инвестиционного проекта называют количество проданных товаров услуг и т.д. после которого проект полностью окупается (включая все новые капвложения) и инвестор начинает получать чистую прибыль. Эту точку можно определить графически построив графики доходов и расходов в зависимости от количества проданных услуг и аналитически по формуле. При графическом определении точку безубыточности получают как точку пересечения графика доходов и расходов. Аналитически точку безубыточности определим по формуле:
Ркр = (Зпост · 10) (Цусл - Сусл) = (1023682000 · 10) (1004 - 774) = 445079130 т·км
где Ркр – величина транспортной работы в т·км при которой проект полностью окупается;
Зпост = 1023682000 руб. – затраты постоянные (балансовая стоимость всех основных фондов + оборотные фонды);
Цусл = 1004 руб. (10т·км) – цена единицы услуги т.е. десяти т·км при рентабельности продажи 30%;
Сусл = 774 руб (10т·км) – себестоимость единицы услуги т. е. десяти т·км.
График безубыточности проекта показан на рис. 6.1
Рис. 6.1 График безубыточности.
Результаты экономических расчетов сводим в таблицу 6.10.
Таблица 6.10 Технико-экономические показатели АТП
Наименование технико-экономических показателей АТП
Значение показателей
КАМАЗ-53215 (бортовой)
МАЗ-5516А5-375 (самосвал)
Среднесписочное количество подвижного состава АТП
Коэффициент технической готовности
Коэффициент использования парка
Годовой объем перевозок
Среднесуточный пробег одного автомобиля
Годовой пробег одного автомобиля
Производительность труда водителей
Себестоимость перевозок
Стоимость основных производственных фондов
Стоимость нормируемых производственных средств
Срок окупаемости инвестиций
Общая рентабельность
Рентабельность перевозок
Таблица 6.11 Формирование и распределение прибыли в АТП тыс. руб.
Наименование показателей
Материальные затраты
Техническое обслуживание и ремонт автомобилей
Фонд оплаты труда персонала АТП
Амортизация основных фондов
Баланс (валовая прибыль)
Прибыль остающаяся в распоряжении предприятия
Платежи по кредитам и % по долгосрочным кредитам
Фонд развития производства
Фонд социального развития
Фонд материального поощрения
В дипломном проекте разработан проект АТП для перевозки 1350 тыс. тонн грузов для заданного района грузоперевозок. Дипломный проект состоит из нескольких частей связанных друг с другом
В эксплуатационной части проведен анализ грузопотоков разработаны грузовые маршруты перевозок определена потребность предприятия в подвижном составе . Здесь же с помощью специальной методики выбран оптимальные тип и моделей подвижного состава (КАМАЗ-53215 и МАЗ 5516А5) определены основные технические показатели предприятия.
В технологической части определены объем и виды технического обслуживания и текущего ремонта подвижного состава рассчитано количество ремонтных рабочих. Кроме этого здесь же разработан производственный корпус АТП подобрано технологическое оборудование для ремонта подвижного состава разработан генеральный план предприятия и подробно рассмотрена компоновка агрегатного участка.
В конструкторской части в дипломном проекте разработано гидравлическое приспособление для выпрессовки и впрессовки деталей малых и средних габаритов проведен расчет на прочность элементов приспособления пояснена рентабельность внедрения гидроприспособления в производство.
В ремонтно-технологической части дипломного проекта подробно рассмотрен текущий ремонт шатуна автомобиля КАМАЗ 53215 разработан технологический маршрут ремонта шатуна определены и проанализированы его возможные дефекты в результате эксплуатации.
В разделе " Безопасность и экологичность проектных решений" проведен анализ вредных и опасных производственных факторов возникающих на агрегатном участке и экологичной безопасности АТП разработаны мероприятия обеспечивающие нормы труда и экологичность. В этом разделе проведены расчеты освещенности рабочих мест и загазованности рабочей зоны выхлопными газами.
В экономической части дипломного проекта разработана организационно-структурная схема предприятия определены потребные капвложения и себестоимость перевозки грузов. В этом разделе показано что окупаемость проекта наступает через 67 лет при цене единицы услуги 1004 руб.(10т*км). В экономическом разделе определены основные технико-экономические показатели АТП.
Список используемой литературы
Проектирование предприятий автомобильного транспорта (Организация и планирование перевозок). Бачурин А. А. Бугримов В. А. Под редакцией Лукашиной Н. В. Цатуряна Э. О. М.: Издательство МГОУ 2007.
Напольский Г.М. Технологическое проектирование автотранспортных предприятий и станций технического обслуживания: Учебник для вузов. – М.: Транспорт 1993. – 271 с.
Положение о техническом обслуживании и ремонте подвижного состава автомобильного транспорта.М-во автом. трансп. РСФСР. – М.: Транспорт 1986. – 72 с.
Тарасов В.В. Проектирование предприятий автомобильного транспорта. Уч. пособие и задания по курсовому проектированию. МГОУ 2007.
Автомобили МАЗ-5336 -6303: Руководство по эксплуатации техническому обслуживанию и ремонту каталог запасных частей А.Кузнецов. – М.: Издательский дом Третий Рим 2007. – 216 с.
Техническая эксплуатация автомобилей: Учебник для вузов Под ред. Г.В. Крамаренко.- М.: Транспорт 1983.-488 с.
Проектирование авторемонтных предприятий. Справочник инженера-механика. Верещак Ф.П. Абелевич Л.А. Транспорт 1973. – 328 с.
Афанасьев Л.Л. и др. Гаражи и станции технического обслуживания автомобилей. (Альбом чертежей). – М.: Транспорт 1980. – 216 с.
Сарбаев В.И. и др. Механизация производственных процессов технического обслуживания и ремонта автомобилей: Учебное пособие. – М.: МГИУ 2006 – 284 с.
Техническая эксплуатация автомобилей: Учебник для вузов Под ред. Кузнецова Е.С. - М.: Транспорт 1991 – 413 с.
Бейлин В.И. Быховский М.Л. Проектирование предприятий автомобильного транспорта (Объемно-планировочные решения).Методические указания по дипломному проектированию М.: МГОУ. 2002.
Иванов М.Н. Детали машин. Учебник для студентов втузов. –М.: высшая школа. 1998.
Мариниченко А.В. Безопасность жизнедеятельности: Учебное пособие. М. "Дашков и К" 2007.
Проектирование предприятий автомобильного транспорта (Организационно–экономическая часть дипломного проекта). Методические указания по экономике. МГОУ М. 2001.
лист№2 (генплан).dwg

недели. Стоимость всего дипломного проекта 30000 руб.
без предоплат и с полной гарантией. По окончанию выполнения мы созвониваемся
встречаемся я передаю Вам распечатку диплома и диск
а Вы мне оплату. В данную стоимость входит бесплатное консультирование по диплому в течении всего дипломного семестра (ответы по электронной почте на все интересующие Вас вопросы) и посредствам програмного обеспечения оперативная корректировка нужного раздела
что делает нашу с Вами работу удобной и гибкой. Если Вам не нужен диплом полностью
а нужна одна или несколько частей
или если хотите поэтапно заказывать диплом
Проезд общего пользования
Генеральный план АТП
Центральный тепловой пункт
Трансформаторная станция
Открытая автостоянка
Контрольно-технический пункт
Административный корпус
Производственный корпус
Условные обозначения
- ограждение участка
- направление движения
Общая площадь участка - 39 621 м Площадь застройки - 22639 м Площадь озеления - 7924 м Плотности застройки - 58 % Коэффициент озеленения - 0
Коэффициент использования территории - 0
Стоянка для личного транспорта
Проектирование АТП для перевозки
50000 тыс. тонн грузов
лист№4 (агрегатный участок).dwg

Ванна для мойки деталей
Стенд для испытания компрессора
Ларь для обтирочных материалов
регулировки рулевых механизмов
Стенд для испытания заднего моста
Стенд для ремонта двигателя
Стенд для ремонта КПП
Условные обозначения
- розетка штепсельная трехфазная
- потребитель электроэнергии
- розетка штепсельная однофазная
- подвод сжатого воздуха
- подвод холодной воды с отводом в канализацию
- подвод горячей воды с отводом в канализацию
Проектирование АТП для перевозки
50000 тыс. тонн грузов
лист№3 (производственный корпус).dwg

Условные обозначения
- гидравлический подъемник
- направление движения автомобилей
Сварочно-кузовной участок
Электро-аккумуляторный участок
Шиноремонтный участок
Склад смазочных материалов
Склад лакокрасочных изделий и
Склад прочих материалов
Склад промежуточного хранения
Слесарно-механический участок
Проектирование АТП на 180 автомобилей "ЗИЛ-5301В2" для производственных грузов
Выполнение дипломных проектов по теме "Проектирование АТП". Срок выполение одного диплома 1-1
недели. Стоимость всего дипломного проекта 30000 руб.
без предоплат и с полной гарантией. По окончанию выполнения мы созвониваемся
встречаемся я передаю Вам распечатку диплома и диск
а Вы мне оплату. В данную стоимость входит бесплатное консультирование по диплому в течении всего дипломного семестра (ответы по электронной почте на все интересующие Вас вопросы) и посредствам програмного обеспечения оперативная корректировка нужного раздела
что делает нашу с Вами работу удобной и гибкой. Если Вам не нужен диплом полностью
а нужна одна или несколько частей
или если хотите поэтапно заказывать диплом
Аккумуляторный участок
- канавный подъёмник
Компрессорная и электрощитовая
Условные обозначения:
- подземный переход в административный корпус
Электротехнический участок
Участок ремонта топливной аппаратуры
Склад лакокрасочых покрытий
Проектирование АТП для перевозки
50000 тыс. тонн грузов
лист№1 (эксплуатационная часть).dwg

недели. Стоимость всего дипломного проекта 30000 руб.
без предоплат и с полной гарантией. По окончанию выполнения мы созвониваемся
встречаемся я передаю Вам распечатку диплома и диск
а Вы мне оплату. В данную стоимость входит бесплатное консультирование по диплому в течении всего дипломного семестра (ответы по электронной почте на все интересующие Вас вопросы) и посредствам програмного обеспечения оперативная корректировка нужного раздела
что делает нашу с Вами работу удобной и гибкой. Если Вам не нужен диплом полностью
а нужна одна или несколько частей
или если хотите поэтапно заказывать диплом
Схема грузопотоков перевозок и технико-эксплуатационные показатели работы подвижного состава на маршрутах и по АТП
Шахматная таблица корреспонденций
Показатели производственной программы АТП по эксплуатации
- Движение без груза
График движения подвижного состава по маршруту
Проектирование АТП для перевозки
50000 тыс. тонн грузов
лист№8 (экономическая часть).dwg

График безубыточности
Формирование и распределение прибыли в АТП
Технико-экономические показатели АТП График безубыточности Формирование и распределение прибыли в АТП
Проектирование АТП для перевозки
50000 тыс. тонн грузов
лист№6 (деталировка).dwg

Н 300 Максимальная сила давления
кН 90 Ход поршня домкрата
Проектирование АТП для перевозки
Выполнение дипломных проектов по теме "Проектирование АТП". Срок выполение одного диплома 1-1
недели. Стоимость всего дипломного проекта 30000 руб.
без предоплат и с полной гарантией. По окончанию выполнения мы созвониваемся
встречаемся я передаю Вам распечатку диплома и диск
а Вы мне оплату. В данную стоимость входит бесплатное консультирование по диплому в течении всего дипломного семестра (ответы по электронной почте на все интересующие Вас вопросы) и посредствам програмного обеспечения оперативная корректировка нужного раздела
что делает нашу с Вами работу удобной и гибкой. Если Вам не нужен диплом полностью
а нужна одна или несколько частей
или если хотите поэтапно заказывать диплом
Сталь 30ХГСА ГОСТ 4543-70
кроме поверхности А 2. Остальные ТТ по ОСТ4 ГО.070.014
Сталь 45 ГОСТ 1050-88
Покрытие: Ц12хр 2. Остальные ТТ по ОСТ4 ГО.070.014
Размеры в квадратных скобках выполнять совместно с ответной стенкой 2. Покрытие: Ц12хр
зеленовато-жёлтая - наружняя поверхность кроме отверстий и поверхности Б. Всё покрытие выполнить после сборки
штифтовки и совместной обработки стенок 3. Остальные ТТ по ОСТ4 ГО.070.014
Сталь 20Х2НЧА ГОСТ 4543-71
Твёрдость 57 63 HRC 2. Остальные ТТ по ОСТ4 ГО.070.014
Пресс гидравли- ческий винтовой
Проектирование АТП для перевозки
50000 тыс. тонн грузов
лист№7 (ремонт шатуна).dwg

недели. Стоимость всего дипломного проекта 30000 руб.
без предоплат и с полной гарантией. По окончанию выполнения мы созвониваемся
встречаемся я передаю Вам распечатку диплома и диск
а Вы мне оплату. В данную стоимость входит бесплатное консультирование по диплому в течении всего дипломного семестра (ответы по электронной почте на все интересующие Вас вопросы) и посредствам програмного обеспечения оперативная корректировка нужного раздела
что делает нашу с Вами работу удобной и гибкой. Если Вам не нужен диплом полностью
а нужна одна или несколько частей
или если хотите поэтапно заказывать диплом
Технологический эскиз
Технологический эскиз шатуна двигателя
Наименование дефекта
Изгиб или скручивание
Износ отверстия в нижней головке
Износ отверстия под втулку в верхней головке
Износ отверстия во втулке верхней головки
Уменьшение расстояния между осями верхней и
Растачивание на двушпиндельном
Растачивание под ремонтный размер
Приспособление для проверки
шатуна на погнутость и
Шлифование торцев и обработка
нижней головки под номинальный
Проектирование АТП для перевозки
лист№5 (пресс гидравлический).dwg

Н 300 Максимальная сила давления
кН 90 Ход поршня домкрата
Проектирование АТП для перевозки
Выполнение дипломных проектов по теме "Проектирование АТП". Срок выполение одного диплома 1-1
недели. Стоимость всего дипломного проекта 30000 руб.
без предоплат и с полной гарантией. По окончанию выполнения мы созвониваемся
встречаемся я передаю Вам распечатку диплома и диск
а Вы мне оплату. В данную стоимость входит бесплатное консультирование по диплому в течении всего дипломного семестра (ответы по электронной почте на все интересующие Вас вопросы) и посредствам програмного обеспечения оперативная корректировка нужного раздела
что делает нашу с Вами работу удобной и гибкой. Если Вам не нужен диплом полностью
а нужна одна или несколько частей
или если хотите поэтапно заказывать диплом
Пресс гидравли- ческий винтовой
гидравлический Максимальная сила давления
кН 3 Ход поршня домкрата
Винт сливного отверстия
Гайка М5-6Н ГОСТ 5927
Болт М5х18 ГОСТ 7805-72
Винт М4х10 ГОСТ 17475-80
Винт М3х20 ГОСТ 17475-80
Техническая характеристика:
Проектирование АТП для перевозки
50000 тыс. тонн грузов
Рекомендуемые чертежи
- 25.01.2023
- 04.11.2022
- 24.04.2018
- 24.01.2023