Литейный цех на выпуск 2, 5 тысяч тонн отливок в год из чугуна и стали для стекольной промышленности




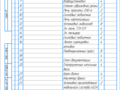



- Добавлен: 24.01.2023
- Размер: 1 MB
- Закачек: 1
Описание
Состав проекта
![]() |
![]() |
![]() ![]() ![]() |
![]() ![]() ![]() |
![]() ![]() ![]() |
![]() ![]() ![]() |
![]() ![]() ![]() ![]() |
![]() ![]() ![]() |
![]() ![]() ![]() |
![]() ![]() ![]() |
![]() ![]() ![]() |
![]() ![]() ![]() ![]() |
![]() ![]() ![]() |
![]() ![]() ![]() |
![]() ![]() ![]() ![]() |
![]() ![]() ![]() |
![]() ![]() ![]() ![]() |
![]() ![]() ![]() |
![]() ![]() ![]() ![]() |
![]() ![]() ![]() |
![]() ![]() ![]() |
![]() ![]() ![]() |
![]() ![]() ![]() ![]() |
![]() ![]() ![]() |
![]() ![]() ![]() |
Дополнительная информация
СПЕЦЧАСТЬ.doc
В настоящее время нельзя назвать область человеческой деятельности в которой бы не применялись методы моделирования. Особенно это относится к сфере управления различными процессами на основе получаемой информации. Моделирование является основным методом исследований во всех областях знаний а также научно обоснованным методом оценок характеристик сложных систем используемым для принятия решений в различных сферах инженерной деятельности. Существующие и проектируемые системы можно эффективно исследовать с помощью математических моделей (аналитических и имитационных) реализуемых на ЭВМ которые в этом случае выступают в качестве инструмента для работы экспериментатора с моделью системы [17].
Основной целью проведенного моделирования является исследование процесса заполнения полости формы жидким металлом с последующим затвердеванием.
Моделирование осуществлялось с помощью компьютерной программы LVMFlow.
Пакет программ LVMFlow - это система компьютерного моделирования тепловых и гидродинамических процессов литья. Ядром пакета являются уравнения тепломассопереноса.
Применение пакета в литейном производстве позволяет:
- снизить роль натурного эксперимента что сокращает затраты на отработку технологии литья;
- изготавливать отливки высокого качества весьма сложной конфигурации практически не требующие дополнительной обработки;
- использовать большую номенклатуру сплавов;
- повышать профессиональный уровень технолога-литейщика.
Программа учитывает:
- тепло- электронагреватели; мощность тепловыделения ТЭНов в процессе моделирования можно менять в произвольные моменты времени;
- каналы с теплоносителями; каналы с теплоносителями (газ жидкость плазма) могут использоваться как нагреватели и как холодильники;
- противопригарные покрытия;
- многократное использование формы.
Генерация сетки и начальные условия.
Последовательность работы в модуле Initial.
а) Создают разностную сетку в расчетной области на которой будут решаться уравнения тепломассопереноса. В LVMFlow элементарной ячейкой разностной сетки является куб. Поэтому для автоматической генерации сетки достаточно ввести один параметр-размер ячейки (шаг сетки) либо задать общее количество узлов сетки. Чем меньше шаг сетки тем точнее решение которое получится в процессе счета.
б) На границах расчетной области задают условия теплообмена. Задание граничных условий на границе расчетной области осуществляется выбором одного из четырех вариантов:
а) на границе расчетной области поддерживается заданная температура;
б) граница расчетной области является плоскостью симметрии;
в) за пределами границы расчетной области располагается бесконечная форма;
г) граница расчетной области является границей форма-воздух.
в) Задают начальные температуры формы и заливаемого металла. Созданную в системе геометрического моделирования конструкцию можно дополнить построением оболочки вокруг любой части отливки. Для этого достаточно указать эту часть отливки и задать толщину оболочки. Оболочка становится таким же элементом технологической оснастки как и те детали что построены в системе геометрического моделирования. В случае неоднородной технологической оснастки для каждого материала можно задать свою собственную начальную температуру.
г) Формируют параметры заливки. В LVMFlow заложена возможность моделирования двух видов заливки: гравитационное литье и литье под давлением. Задание места питания металлом (литниковой точки) производится на границе расчетной области в точке принадлежащей отливке или литниково-питающей системе. Для гравитационного литья задается напор - высота столба жидкости над сечением в котором установлена литниковая точка и коэффициент характеризующий уменьшение потока расплава вызванное трением жидкости о стенки заливочного устройства. Для литья под давлением задается либо скорость входного потока либо массовый расход расплава. При задании одного из параметров второй автоматически рассчитывается. Изменение скорости входного потока во времени можно задать изначально формированием таблицы "время-скорость" или организацией системы сенсоров. Установленные в отливку сенсоры работают следующим образом: когда фронт расплава проходит через сенсор происходит смена скорости входного потока.
д) Вводят параметры дополнительных технологических приемов. На границе металл-форма можно ввести параметры характеризующие противопригарное покрытие а также параметры учитывающие образование воздушных зазоров между металлом и формой в процессе затвердевания отливки.
е) Устанавливают датчики. Для более детального анализа пользователь может установить датчики в любом месте расчетной области (в отливке или оснастке). Показания датчиков выводятся в виде графиков временной зависимости выводимой функции (температуры скорости изменения температуры доли жидкой фазы скорости течения расплава входного потока расплава). Большинство параметров изначально установлены по умолчанию системой Системные установки. В процессе работы достаточно откорректировать параметры или не изменять их вообще. Ввод значений параметров можно производить в произвольном порядке. Из дополнительных приемов применяемых в литейной технологии в LVMFlow реализовано моделирование тепло электро нагревателей (ТЭНов) каналов с теплоносителями (газ жидкость плазма) и фильтров. Мощность тепловыделения ТЭНов в процессе моделирования можно менять в произвольные моменты времени. Каналы с теплоносителями могут использоваться как нагреватели и как холодильники. Для отработки литейной технологии предусматривающей многократное использование формы в системе LVMFlow реализовано моделирование циклического процесса.
Гидродинамический анализ заполнения формы.
В модуле Гидродинамика моделируется заполнение формы расплавом оторое рассматривается как течение идеальной несжимаемой жидкости без учета процессов теплопередачи. Течение описывается уравнениями Навье - Стокса где вязкость учитывается в виде поправки. Для изучения движения в расплаве посторонних (шлаковых) частиц в пакете предусмотрена возможность моделирования движения шарообразных частиц заданного радиуса и плотности. В пакете возможно одновременное моделирование процессов заполнения формы расплавом и его затвердевание.
В каждом отдельном модуле процессы тепломассопереноса описываются замкнутой динамической системой уравнений основанных на законах сохранения энергии импульса массы уравнений состояния многокомпонентных сплавов которые решаются на прямоугольной сетке методом конечных разностей МКР с автоматическим выбором шага интегрирования по времени. Такой подход на наш взгляд является наиболее оптимальным по сравнению например с методом конечных элементов МКЭ:
а) простая автоматическая генерация конечно-разностной сетки;
б) для достижения одной и той же точности решения конечно-разностные методы требуют значительно меньше машинной памяти и времени счета.
Конечно МКР уступает в точности аппроксимации границы но этот недостаток планируется устранить применением “метода контрольного объема”.
Динамика процесса несет в себе большое количество информации поэтому отображению результатов моделирования в пакете уделено большое внимание. Результаты моделирования такие как температура доля жидкой фазы скорость течения расплава давление в расплаве доля усадочных дефектов выводятся на каждом временном шаге. Вывод образа отливки (также как и полей функций характеризующих ее состояние) производится в виде изометрического изображения (3D) и в произвольном плоском сечении (2D) в цветовой гамме соответствующей установленной шкале. Функции вращения и масштабирования дополняют возможности просмотра. Для получения более детальной информации можно считать численное значение поля (температуры доли жидкой фазы скорости доли дефектов) в произвольной точке расчетной области.
Принимая во внимание все выше сказанное можно утверждать что LVMFlow является превосходным инструментом не только на производстве но и для образовательных целей и является важным компонентом для подготовки квалифицированного персонала для литейных производств.
Процесс моделирования осуществлялся с разными технологическими параметрами. Использовались разные способы заливки формы металлом литниковые системы и т.д.
Вариант 1. Используется боковая литниковая система с подводом металла по длине отливки прибыль расположена на отливке (расчет прибыли осуществлялся по формуле Намюра-Шкленника (18)) все поверхности выполняются в песчаной форме.
При моделировании варианта 1 были получены следующие результаты (см. рисунок 4).
В теле отливки и в прибыли имеется усадочная раковина и пористость. Максимальный объем усадочной пористости в теле отливки достигает 70 %.
По техническим требованиям усадочная пористость не должна превышать 15 %. Так как усадочная пористость превышает нормированные значения такой способ литья недопустим.
Рисунок 4 – Моделирование затвердевания отливки по варианту 1
Вариант 2. Используется боковая литниковая система с подводом металла в торцевую часть отливки питание отливки осуществляется через стояк коллекторы проливные прибыли перешейки. Результат моделирования представлен на рисунке 5.
Из рисунка 5 видно что пористость сохраняется но уже в меньшем количестве (до 25 %). Но так как значение пористости все еще превышает нормируемое этот вариант литниковой системы не подходит.
Рисунок 5 – Моделирование затвердевания отливки по варианту 2
Вариант 3. По результатам моделирования предыдущих вариантов было принято решение использовать комбинированную литниковую систему. То есть использовать вместо нижней песчаной полуформы холодильник. Он создал условия для направленной кристаллизации ускорив охлаждение отливки в нижней части и тем самым позволил устранить усадочную пористость. Результат моделирования представлен на рисунке 6.
Рисунок 6 – Моделирование затвердевания отливки по варианту варианту 3
Вывод: На основании проведенного моделирования было принято решение о изготовлении отливки “Стеклоформа” комбинированным способом. Использование этого варианта литниковой системы позволил значительно снизить усадочную пористость до допустимых значений.
ЭКОНОМИКА.doc
1 Расчёт фондов заработной платы
На основе принятых в разделе 2 решений технического характера рассчитаем необходимые финансовые вложения [3].
Фонд заработной платы определяется по формуле (49):
Ф = Чсп · Зр · 12 · К (49)
где Ф - годовой фонд заработной платы руб.;
Чсп - списочная численность рабочих чел.;
Зр - средняя зарплата руб.;
К – коэффициент (для ОПР К = 1 для ВП К = 08 для ИТР К = 12 для МОП К = 07).
Фонд заработной платы ОПР: ФОПР = 23 · 17000·12·1 = 46920 тыс. руб.
Фонд зарплаты ВП: ФВП = 16 · 15000 · 12 · 08 = 23040 тыс. руб.
Фонд зарплаты ИТР: ФИТР = 2 · 25000 · 12 · 12 = 7200 тыс. руб.
Фонд зарплаты МОП: ФМОП = 1 · 16500 · 12 · 07 = 1386 тыс. руб.
Фонд зарплаты СКП: ФСКП = 1 · 16500 · 12 · 07 = 1386 тыс. руб.
На основе полученных данных составлена ведомость фондов заработной платы за год приведённая в таблице 36.
Таблица 36 – Ведомость фондов зарплаты и среднемесячного заработка по категориямперсонала
Среднемесячная зарплата руб.
Количество рабочих чел.
Фонд заработной платы тыс. руб.
Основные производственные рабочие
Вспомогательные производственные рабочие
2 Расчет капитальных вложений производственных фондов амортизационных отчислений
В таблице 37 приведены расчетные данные по капитальным затратам и амортизационным отчислениям на здания и строительные сооружения.
Таблица 37 – Капитальные вложения и амортизационные отчисления в здание цеха чугунного литья
Наименование объекта
Сумма годовых амортизационных отчислений
Производственная площадь
Вспомогательная площадь
В таблице 38 приведены капитальные вложения в оборудование и амортизационные отчисления. Балансовая стоимость – стоимость с учётом транспортировки (К=13)
Таблица 38 – Капитальные вложения в оборудование и амортизационные отчисления
Наименование оборудования
Цена за единиц тыс. руб.
Стоимость оборудовани тыс. руб.
Балансовая стоимость тыс. руб.
Норма аморти-зации %
Плавильное отделение
Устройство подогрева шихты
Электровесовое устройство
Формовочное отделение
Продолжение таблицы 38
Отделение финишных операций
дробеметно - дробеструйной камере
Всего по цеху стоимость оборудования
К полученной стоимости оборудования нужно прибавить 60 % от стоимости этого оборудования. Из этих 60 %: 30 % для учета экологической программы 30 % на общезаводское хозяйство: 146016·16 = 233626 тыс. руб. 40 % от стоимости оборудования на оборотные средства: 146016 · 04 = 58406 тыс. руб.
Стоимость инвентаря рассчитывается как 800 руб. на человека то есть:
· 800 = 34400 руб. = 344 тыс. руб.
Тогда из таблиц 37 и 38 общие капитальные вложения будут равны 58406+233626+22464+344 = 314840 тыс. руб.
С учетом данных таблиц 37 и 38 составляется сводная ведомость капитальных затрат на строительство цеха представленная в таблице 39.
Таблица 39 – Сводная ведомость капитальных затрат на строительство литейного цеха
Общая стоимость тыс. руб.
Удельные капитальные вложения руб.т отливок
Производственная площадь м3
Вспомогательная площадь м3
Итого по строительству
Итого на оборудование с монтажом
Продолжение таблицы 39
Инструмент приспособления оснастка производственный инвентарь (500 рублей на 1т)
Хозяйственный инвентарь (400 рублей на 1 ОПР)
Общезаводское хозяйство (30 % от стоимости оборудования)
Оборотные средства (40 % от стоимости оборудования)
Экология (30 % от стоимости оборудования)
Проектные работы (10 % от стоимости оборудования)
Всего капитальных затрат
На основе полученных данных в таблицах 37 и 38 рассчитываются расходы на содержание и эксплуатацию оборудования приведённые в таблице 40.
Таблица 40 - Расходы на содержание и эксплуатацию оборудования в год тыс. руб.
амортизация оборудования
содержание оборудования (5 % от стоимости оборудования)
Энергетические расходы
Основная и дополнительная зарплата с отчислениями вспомогательных рабочих
Износ малоценных и быстроизнашивающихся инструментов и приспособлений (2000 руб. на чел.)
На основе данных из таблиц 36 37 38 и 40 составляется смета цеховых расходов за год представленная в таблице 41.
Таблица 41 - Цеховые расходы за год тыс. руб.
Содержание аппарата управления (зарплата ИТР)
Содержание зданий сооружений инвентаря (зарплата МОП + электроэнергия)
Текущий ремонт зданий сооружений и инвентаря (15 % от стоимости здания + 10 % от стоимости инвентаря)
Испытания опыты и исследования рационализация и изобретательства (500 руб. на человека)
Расходы по охране труда (400 руб. на человека)
Износ малоценного и быстроизнашивающегося инвентаря (2000 руб. На 1 производственного рабочего)
Итого цеховых расходов:
3 Расчет себестоимости
Пользуясь данными полученными в разделе 2 составим расчет [6] себестоимости одной тонны жидкого чугуна марки ЧС5. Расчёт себестоимости одной тонны жидкого чугуна приведён в таблице 42. Исходя из полученных данных из таблицы 41 и предыдущих данных произведем расчет себестоимости одной тонны отливок. Расчёт себестоимости одной тонны отливок приведён в таблице 43.
Таблица 42 - Себестоимость одной тонны жидкого чугуна марки ЧС5
Затраты за год тыс. руб.
На 1 т жидкого металла
Графитизирующий коксик
Возврат производства
Продолжение таблицы 42
Итого жидкого чугуна
Зарплата производ-ственных рабочих
Дополнительная зарплата производственных рабочих (15 % от основной зарплаты)
Отчисления в общественные фонды (356 % от зарплаты производственных рабочих)
Амортизация оборудования
Расходы на содержание и эксплуатацию оборудования
Cебестоимость жидкого чугуна
Таблица 43 - Себестоимость одной тонны отливок из чугуна марки ЧС5
Годное за вычетом отходов и брака
Формовочные материалы
Основная зарплата производственных рабочих
Продолжение таблицы 43
Общезаводские расходы
Себестоимость 1 т жидкого металла составляет: 112967 руб.т.
Себестоимость 1 т отливок составляет: 229437 руб.т.
4 Расчет интегрального эффекта за весь период строительства и эксплуатации проектируемого цеха методом потока наличности
Распределение затрат на условно-постоянные (числитель) и условно переменные (знаменатель) в литейном цехе представлены в таблице 44.
Цех строится в течение двух лет. Освоение проектной мощности составит в первый год после строительства - 80 % во второй год - 100 %.
Кредит составляет 175386 тыс. рублей под 18 % годовых сроком на 4 года. Кредит получен в год предшествующий строительству.
Распределение инвестиций по годам за период строительства и эксплуатации представлено в таблице 45.
Таблица 44 - Распределение затрат на условно-постоянные и условно- переменные затраты
Распределение затрат
Фонд оплаты труда с начислениями
Амортизационные отчисления
Уровень рентабельности продукции принимается равным 40 %.
Из расчета потока наличности приведённого в таблице 45 видно что капитальные вложения с учетом платного кредита в полном объеме возвращается в 2010 году. Срок окупаемости проекта составляет 225 года с момента начала производства.
Таблица 45 - Распределение инвестиций по годам за период строительства и эксплуатации тыс.руб.
Распределение по годам
Капитальные вложения
Собственные средства
Условно-постоянные затраты (без амортизации)
Амортизационные отчисления по видам основных фондов
Текущие затраты (себестоимость
Прибыль от реализации
Прочие виды прибыли (2 % к. пункту 3 условно)
Налог на прибыль (24 %)
Уплата за банковский кредит (20 %)
Коэффициент дисконтирования
Дисконтированный кассовый остаток
Нарастающая сумма дисконтированных кассовых остатков
5 Расчет точки безубыточности
Точка безубыточности определяется по формуле (50):
где ТБ – объем производства т;
ЗС – условно-постоянные затраты на весь объём производства тыс. руб.;
Ц – цена единицы продукции тыс. руб.т;
ЗV – условно-переменные затраты на единицу продукции тыс. руб.;
С – себестоимость единицы продукции тыс. руб.т;
Р – рентабельность продукции %100;
Тогда по формуле (50) точка безубыточности равна:
График расчета точки безубыточности приведен на рисунке 3.Точке безубыточности соответствует объем производства равный 8751 тонн годных отливок в год.
Рисунок 3 - Расчёт точки безубыточности
6 Расчет рентабельности производства
Расчет рентабельности производства ведется по формуле (51):
где R - рентабельность производства %;
П - величина прибыли тыс. руб.;
ОСРН - нормируемая часть оборотных средств тыс. руб.;
ОФ - стоимость основных фондов тыс. руб.
Таким образом по формуле (51):
В таблице 46 представлены технико-экономические показатели цеха.
Таблица 46 – Сводная таблица технико-экономических показателей
Технико-экономический показатель
Масса (средняя) отливки
- производственная площадь цеха
Количество работающих
- количество производственных рабочих
Производительность труда
- на одного работающего
- на одного производственного рабочего
Капитальные вложения
Удельные капитальные вложения – новое строительство
Себестоимость жидкого чугуна
Себестоимость отливок
Рентабельность производства
Рентабельность продукции
Точка безубыточности
ТЕХНИКА ПРОИЗВОДСТВА.doc
1 Расчетная программа литейного цеха
В таблице 1 представлена спецификация отливок представителей которые предполагается выпускать в проектируемом цехе.
Спецификация отливок включает 15 наименований отливок из чугуна марок ЧС5 СЧ20 и стали марки 30ХНМЛ массой от 13кг до 1000 кг.
На основе спецификации отливок составлена производственная программа цеха представленная в таблице2.
Расчетная программа служит для дальнейших расчетов всех отделений литейного цеха входящих в состав машиностроительного литейного или металлургического заводов.
Основная цель расчетной программы состоит в том чтобы определить количество отливок каждого наименования которое должно быть изготовлено в течении года в литейном цехе [1].
В расчетную программу литейного цеха мелкосерийного и индивидуального производства вносятся отливки которые разделены на три группы по массе. Исходные данные для расчета берутся из производственной программы и спецификации отливок.
В расчете приняты технологические потери на уровне 3 %.
Таблица 1 - Спецификация отливок
Мощность проектируемого цеха 2500 тонн в год. Для дальнейшего расчета всех отделений цеха необходимо провести расчетную программу литейного цеха массового производства которая представлена в таблице 2.
Таблица 2 - Расчетная программа литейного цеха мелкосерийного производства
Технологические потери
на годовую программу
отливки с литниками
2 Расчет программы формовочного отделения
2.1 Расчет программы формовочного отделения
Для определения количества форм необходимого для изготовления 2500 тонн годных отливок составляется расчетная программа формовочного отделения представлена в таблице 3.
В соответствии с габаритными размерами отливок выбираются опоки. Как правило в литейном цехе для изготовления различных по массе и размерам отливок применяются несколько типоразмеров опок в данном случае применяется один типовой размер опоки [2].
Исходными данными для расчета формовочного отделения служат значения годового количества отливок с учетом потерь (см. таблицу 2). Технологические потери форм при формовке приняты равными 3 %. Металлоемкость формы определяется на основе известных значений массы отливок с литниками и прибылями.
Объем уплотненной формовочной смеси на форму (Vс) определяется по формуле (1):
где Vф - объем формы м3;
Vм - объем металла в форме м3;
Vст - объем стержней в форме м3.
При производстве отливки “Стеклоформы” применение стержней не предполагается поэтому Vст = 0
На основе расчетов приведенных в таблице 2 составляется расчетная программа формовочного отделения литейного цеха (см. таблицу 3).
Таблица 3 - Расчетная программа формовочного отделения
Количество отливок в форме шт.
Кол-во форм в год шт.
Кол-во форм в год с учетом потерь шт.
Наименование оборудования
Количество пленки Сэвилен м2год
Таблица 4 - Потребное количество песка
Количество песка на
Количество песка с учетом
2.2 Расчет технологического оборудования формовочного отделения
На основе определения необходимого количества форм осуществляется расчет технологического оборудования формовочного отделения по формуле (2) [3]. Результаты расчета представлены в таблице 5.
где nр - количество формовочных линий;
В - годовое количество форм с учетом потерь шт.;
Кн - коэффициент неравномерности Кн=1;
а – производительность формовочной установки формч;
ФД - действительный годовой фонд времени (при двухсменной работе ФД = 3645 ч).
Таблица 5 - Расчет количества формовочного оборудования
Потребное количество форм в год В
Производи-тельность линии а формчас
Действитель-ный годовой фонд времени Фд час
Для изготовления отливок применяются две вакуум – пленочные установки.
Основные преимущества процесса вакуумно-пленочной формовки:
- высокое качество поверхности и геометрическая точность отливок;
- значительное уменьшение поверхностных и внутренних дефектов литья;
- снижение трудоемкости финишных операций и механической обработки;
- возможность использования недорогой деревянной модельной оснастки;
- снижение расхода формовочных материалов;
- высокая экологичность процесса;
- автоматизация управления технологическим процессом.
3 Расчет плавильного отделения
3.1 Расчет программы плавильного отделения
Проектирование плавильного отделения начинается с составления расчётной программы. Исходными данными для расчёта является масса отливок на годовую программу с учётом брака. Расчётная программа плавильного отделения приведена в таблице 6.
Таблица 6 - Расчетная программа плавильного отделения
Масса на годовую программу с учетом потерь т
Всего жидкого металла т
отливок с литниками и прибылями
3.2 Расчет технологического оборудования плавильного отделения
Расчёт количества плавильных агрегатов осуществляется по формуле (3):
где n - количество плавильных агрегатов;
В - количество жидкого металла т;
Кн – коэффициент неравномерности Кн=12;
а – производительность плавильного агрегата тч;
ФД - действительный годовой фонд времени Фд=3975 ч (2-х сменный режим работы).
Тогда согласно формуле (3):
Коэффициент загрузки плавильного агрегата по формуле (4) равен:
Тогда по формуле (4) коэффициент загрузки плавильного агрегата равен:
Плавка осуществляется в индукционных тигельных печах промышленной частоты (ИЧТ) ёмкостью 25 и 05 т. Техническая характеристика электропечей и расчёт количества плавильных агрегатов представлен в таблице 7 и 8 соответственно.
Таблица 7 - Техническая характеристика электропечей
Мощность питающего трансформатора кВА
Продолжи-тельность полного
цикла плавки на твердой шихте ч
Действительная производи-тельность печи
Общая масса печи с расплавленным металлом т
Таблица 8 - Расчет количества электропечей
Наименование и тип агрегата
Потребление жидкого металла в год т
Продолжительность плавки час
Производи-тельность тчас
Действительный годовой фонд времени ч
Коэффициент загрузки
Обоснование выбора типа печи
Преимущества индукционных тигельных печей:
активное перемешивание металла;
возможность зонного перемешивания (фокусирования энергии) в печи;
малый угар легирующих элементов;
возможность плавки без "болота";
широкие технологические возможности при большом выборе емкости печи типе футеровки и рабочей частоте печи;
точная регулировка температуры расплава;
возможность плавки и выдержки металла в одном печном агрегате;
мгновенная готовность к работе;
высокая скорость плавки;
малые удельные показатели потребления электроэнергии на тонну выплавленного металла;
экологичность технологического процесса;
сохранение качества питающей сети;
При получении чугуна необходимо точно управлять химическим составом по многим элементам и прежде всего по углероду сере марганцу хрому фосфору и др. поскольку в ИЧТ плавка ведется с так называемым "холодным" шлаком практически не участвующим в химических реакциях управление химическим составом сплава по ходу плавки производится добавлением легирующих материалов и точным управлением температурой расплава. Сочетание этих возможностей позволяет реализовать технологию получения отливок в которых значительно снижены внутренние напряжения и существенно повышены прочностные характеристики.
Весьма существенным преимуществом плавки в ИЧТ по сравнению с вагранками и дуговыми печами является пониженное на 25 - 30 % содержание газа (азота водорода кислорода) в расплаве металла а также значительное уменьшение содержания неметаллических примесей. Это повышает прочность отливок и уменьшает каверны на их поверхности что позволяет снизить отходы металла при дальнейшей обработке на 20 -25 % и уменьшить металлоемкость оборудования.
Прочность и все другие свойства сплавов в конечном счете определяются их чистотой от примесей формой размером и распределением зерен т.е. структурой. При этом в понятие структуры включается как микроструктура так и макроструктура – наличие в металле газовых и усадочных раковин пористости трещин неметаллических включений и т.д. Таким образом задача повышения качества металла сводится к получению соответствующей структуры свободной от каких-либо дефектов. Измельчение зерна кристаллической структуры достигается повышением скорости зарождения центров кристаллизации которая регулируется вводом модификаторов. Эффективность действия модификаторов возрастает при максимально равномерном распределении в объеме металла и чем больше энергия извне будет внесена в расплав для перемешивания тем выше эффект модифицирования. В индукционных печах имеется возможность управления процессами электромагнитного перемешивания изменением частоты возбуждения тока в обмотках индуктора организацией пульсирующего и бегущего электромагнитного поля в ванне расплава металла и управления удельным силовым давлением а также перераспределением мощности по высоте индуктора.
Расчет шихты для сплава СЧ20
После выбора и расчета количества плавильных агрегатов проводится расчет шихты. При расчете в качестве целевой функции используется ее стоимость что позволяет выбрать оптимальный состав шихтовых материалов.
Химический состав ЧС5 приведен в таблице 9. Шихтовые материалы и их состав в массовых долях процента приведен в таблице 11. 1[1]
Таблица 9 - Химический состав сплава ЧС5 в соответствии с ГОСТ 1412-85 [4]
Массовая доля элемента %
Таблица 10 - Содержание элементов с учетом угара
В шихте с учетом угара %
Расчёт содержания элементов в шихте:
Таблица 11 - Выбор шихтовых материалов
Содержание элементов %
Графитизирующий коксик
Ферромарганец ФMn75
ПРОГРАММА РАСЧЕТА ШИХТЫ (каф. ТЛП)
Балансовые уравнения по содержанию химических элементов:
·X1+29·X2+98·X3+01·X4+35·X5+X6>29
·X1+29·X2+98·X3+01·X4+35·X5+X638
·X1+53·X2+75·X4+22·X5+2·X6>5
·X1+53·X2+75·X4+22·X5+2·X667
·X1+07·X2+03·X4+77·X51
3·X1+01·X2+001·X3+005·X4+002·X5+002·X6012
4·X1+02·X2+002·X4+007·X5+003·X603
Технологические ограничения:
Балансовое уравнение по количеству шихты:
Ш = -3 % (общий угар)
Х1 + Х2 + Х3 + Х4 + Х5+ Х6 = 103
00·X2+7000·X3+13000·X4+15000·X5+14500·X6+17000·X7=780752 рубт
Решение уравнений представлены в таблице 12:
Таблица 12 - Решение уравнений на ЭВМ
Содержание компонентов в шихте %
Анализ выполнения ограничений:
N 2 : остаток 09000 N 4 : остаток 17000 N 5 : остаток 03106
N 7 : остаток 06000 N 8 : остаток 00642 N 9 : остаток 02043
Расшифровка выполнения ограничений:
По углероду: 38-09=29
По кремнию: 67-17=50
По марганцу: 10-03106=06894
По фосфору: 03-02043=00957
По сере: 012-00642=00558
На основании расчетов сделанных при помощи ЭВМ для получения 1 тонны металла с учетом потерь необходим состав шихты приведенный в таблице 13.
Таблица 13 - Количество компонентов шихты для получения 1 тонны сплава ЧС5
компонентов шихты кг
Стальной лом 2Б ГОСТ 2787-86
Ферросилиций ФС75 ГОСТ 1415-78
Ферромарганец ФMn75 ГОСТ 4755-80
Феррохром ФХ100А ГОСТ 4757-91
Химический состав СЧ20 приведен в таблице 14. Шихтовые материалы и их состав в массовых долях процента приведен в таблице 16.
Таблица 14 - Химический состав сплава СЧ20 по ГОСТ 1412-85 [4]
Основные компоненты %
Таблица 15 - Угар элементов %
Индукционная печь промышленной частоты
Знак «-» означает пригар
Таблица 16 - Выбор шихтовых материалов
·X1+38·X2+98·X3+01·X4+35·X5>388
·X1+38·X2+98·X3+01·X4+35·X5412
·X1+21·X2+75·X4+22·X5>147
·X1+21·X2+75·X4+22·X5253
·X1+085·X2+03·X4+77·X5>088
·X1+085·X2+03·X4+77·X5125
4·X1+013·X2+002·X4+007·X502
3·X1+015·X2+001·X3+005·X4+002·X5015
Х1 + Х2 + Х3 + Х4 + Х5+ Х6+ Х7 = 103
00·X1+7000·X2+13000·X3+15000·X4+14500·X5 =755977 рубт
Решение уравнений представлены в таблице 17:
Таблица 17 - Решение уравнений на ЭВМ
N 2: остаток 0.2400 N 4: остаток 1.0600 N 6: остаток 0.3700 N 7: остаток 0.1284
По углероду: 412-024=388
По кремнию: 253-106=147
По марганцу: 125-037=088
По фосфору: 02-01284=00716
По сере: 015-00774=00726
На основании расчетов сделанных при помощи ЭВМ для получения 1 тонны металла с учетом потерь необходим состав шихты приведенный в таблице 18.
Таблица 18 - Количество компонентов шихты для получения 1 тонны сплава СЧ20
Расчет шихты для сплава 30ХНМЛ
Химический состав 30ХНМЛ приведен в таблице 19. Шихтовые материалы и их состав в массовых долях процента приведен в таблице 21.
Таблица 19 - Химический состав сплава 30ХНМЛ по ГОСТ 977-88 [5]
Таблица 20 - Угар элементов %
Таблица 21 - Выбор шихтовых материалов
Продолжение таблицы 21
X1+03X2+98X3+01X4+35X5+X6+05X7+001X8>029
X1+03X2+98X3+01X4+35X5+X6+05X7+001X8041
X1+03X2+75X4+22X5+2X6+5X7+003X8>022
X1+03X2+75X4+22X5+2X6+5X7+003X8044
X1+065X2+03X4+77X5>05
X1+065X2+03X4+77X5126
3X1+004X2+001X3+005X4+002X5+002X6+02X7004
4X1+004X2+002X4+007X5+003X6+01X7004
Х1+Х2+Х3+ 4+Х5+Х6+Х7+Х8= 100
00·X1+7000·X2+13000·X3+15000·X4+14500·X5 +17000·X6+16000·X7+25000·X8=747497 рубт
Решение уравнений представлены в таблице 22:
Таблица 22 - Решение уравнений на ЭВМ
N 3: превыш. 0.0544 N 2: остаток 0.1012 N 5: превыш. 0.1630
N 4: остаток 0.1656 N 6: остаток 0.5970 N 8: остаток 0.3500
N 10: остаток 0.3400 N 12: остаток 0.1100 N 13: остаток 0.0065
N 14: остаток 0.0004 N 1: превыш. 0.0188
По углероду: 029 + 002 = 031
По кремнию: 022 + 005 = 027
По марганцу: 05 + 016 = 066
По хрому: 188 - 035 = 153
По никелю: 178 - 011 = 167
По молибдену: 033 - 001 = 032
По сере: 004 - 00004 = 00396
На основании расчетов сделанных при помощи ЭВМ для получения 1 тонны металла с учетом потерь необходим состав шихты приведенный в таблице 23.
Таблица 23 - Количество компонентов шихты для получения 1 тонны сплава 30ХНМЛ
Ферромолибден ФМо50ГОСТ 4759-91
Никель НП1 ГОСТ 492-73
На основании расчета шихты составляется баланс металла приведенный в таблице 24 для определения выхода годного а также проведения в дальнейшем расчетов складов шихтовых материалов. Статьи приходной части баланса металла составляются на основе расчета оптимального состава шихты который проводится методом линейного программирования.
Таблица 24 - Статья баланса металла на годовую программу литейного цеха
Статьи прихода металла в шихтовое отделение т
Статьи расхода металлозавалки т
Покупные шихтовые материалы:
Графитизирующий коксик 11659
Возврат собственного производства:
отбракованные отливки 10200
Отправленные отливки 2500
Отбракованные отливки 102
Выход годного равен отношению кол-ва годных отливок в тоннах к металлозавалке выраженному в процентах [3].
4 Расчёт склада шихтовых материалов
Склады шихтовых материалов литейных цехов выполняют задачи принятия и разгрузки материалов хранения их. Тип плавильных печей и состав шихты предопределяет последовательность подготовки материалов для плавки.
В процессе расчета плавильного отделения определяется годовое количество шихтовых материалов необходимое для обеспечения заданного выпуска отливок. Количество поступающих на склад материалов должно превышать рассчитанные величины на величину потерь на складе. Эти потери составляют примерно 5 % для всех материалов [6].
Расчет площадей закромов и бункеров для хранения материалов производится на основе расчетной программы по формулам (5 - 9) и приведен в таблице 25:
где В1 – расход с учетом потерь т
В – расход на годовую программу т
Х – потери на складе %
где В2 – запас на складе т
К – нормы хранения сутки
где Т – запас на складе м3
Р – насыпной вес тм3
где П – потребная площадь м2
T – запас на складе м3
Z – высота хранения м
где n –норма расхода %
M – металлозавалка т
Таблица 25 - Расчётная программа склада шихтовых материалов
Наименование материала
Расход на годовую программу т
Расход с учетом потерь т
Нормы хранения сутки
Потребная площадь м2
Графитизи-рующий коксик
5 Расчёт очистного и термообрубного отделения
5.1 Выбор обоснование характеристика и расчёт технологического оборудования
Очистку отливок происходит в дробеметно - дробеструйной камере периодического действия модели ДК-10. Для зачистки отливок используются подвесной наждак.
Расчет количества очистного оборудования проводится на основе максимальной производительности формовочного отделения по формуле (10) и представлен в таблице 27:
где n - количество очистного оборудования шт;
аф - максимальная производительность формовочного отделения тч;
К - коэффициент неравномерности работы К=11;
а - производительность очистного оборудования тч.
Таблица 27 - Расчет количества очистного оборудования
Весовая группа отливок
Максимальная производительность формовочного отделения тч
Марка очистного агрегата
Производитель-ность очистного агрегата тч
Количество очистных агрегатов
5.2 Методы режимы и оборудование для термической обработки отливок
Для снятия напряжений проводится низкотемпературный отжиг (искусственное старение) отливок при температуре нагрева печи 500 – 600 ºС в течении 2 – 8 часов (в зависимости от габаритов отливки). Для устранения отбела в тонких сечениях отливок применяется графитизирующий отжиг при температуре нагрева печи 680 – 750 ºС в течение 1 – 4 часов.
Расчёт количества термического оборудования проводится исходя из норм продолжительности цикла термообработки и удельной нагрузки на площадь пода печи. Число однотипных печей определяют по формуле (11):
где Р – число печей шт;
В - масса термически обрабатываемых отливок на годовую производственную программу т;
КН - коэффициент неравномерности производства КН=11;
ФД - годовой действительный фонд времени работы печи ч;
NР - производительность печи тч;
КЗ - коэффициент загрузки оборудования.
Производительность печи рассчитывается по формуле (12):
где NР - производительность печи тч;
SП – площадь пола печи м2;
aП - удельная нагрузка на площадь пода печи тм2;
ТП - продолжительность цикла термообработки ч.
Тогда по формуле (12) производительность печи равна тч.
Количество печей по формуле (11) равен . Принята 1 печь. Коэффициент загрузки КЗ = 0551 = 055.
6 Расчёт вспомогательного и подъёмно-транспортного оборудования
6.1 Расчёт парка заливочных ковшей
Для расчёта парка заливочных ковшей можно воспользоваться следующим соотношением(13) [7]:
где К - коэффициент учитывающий число ковшей в ремонте (К = 2);
К1 - коэффициент неравномерности использования (К1 = 12);
N1 - число ковшей используемых в смену.
Число ковшей используемых в смену по формуле (14) равно:
где n - число одновременно работающих ковшей;
tсм - продолжительность смены ч;
t - продолжительность работы ковша между ремонтами ч.
Число одновременно работающих ковшей n зависит от их оборота и объёма жидкого металла и рассчитывается по формуле (15):
где Qж - годовое количество металла разливаемое из данного типа ковшей т;
tо - оборот ковша ч;
ФД - действительный годовой фонд времени работы плавильного оборудования ч;
qк - вместимость ковша т.
Следовательно по формуле (15) число одновременно работающих ковшей равно:
Расчет парка заливочных ковшей представлен в таблице 26.
Таблица 26 - Расчёт парка ковшей
Принятое количество ковшей шт
6.1.1 Ремонт футеровки раздаточных ковшей.
Ремонт раздаточных ковшей производится при разгаре футеровки более 13 ее толщины[8]
Для футеровки раздаточных ковшей применяют:
а) кирпич лещадка ШБ 11№6
б) кирпич прямой ШБ 1№5
в) масса огнеупорная массовая доля %: глина огнеупорная ДН - 3 - 40% кварцевый песок - 60% вода - 10%.
7 Описание технологического процесса в цехе
7.1 Описание технологического процесса в плавильном отделении
7.1.1 Плавка чугуна в индукционной печи
Оборудование и инструмент:
Комплекс состоит из индукционных печей емкостью 25 и 05 тонны питаемых от одного источника питания ТПЧД 3600 - 025. Управление всеми системами и механизмами комплекса осуществляется компьютерной системой управления обеспечивающей автоматическое управление процессом плавки сушки и спекания футеровки «холодный старт» и др. режимы. На жидкокристаллическом дисплее системы управления отображается мнемоническая схема комплекса суказанием состояния всех систем и механизмов комплекса режимов его работы и диагностики отображается температура расплавамощность подводимая к печи. Ведется статистический учет всех рабочих параметров комплекса.
Для выплавки чугуна используется следующее оборудование:
- индукционная печь ИЧТ - 25 с кислой футеровкой;
- стенд для подогрева ковша;
- форма для заливки проб для испытания механических свойств;
- кокиль для отливки проб для определения химического состава;
- ложка для отбора и заливки проб;
- скребок для удаления шлака;
а) 3арузка шихты в печь:
Шихтовые материалы загружаются из отдельных контейнеров с помощью весовых дозаторов и ленточного конвейера в бадью.
Бадью на тележке передвигается в печной пролет. После подогрева шихты бадью при помощи крана помещают над открытым тиглем в печи низ бадьи раскрывается и шихта загружается в печь.
б) Расплавление и доводка металла:
- На дно тигля уложить часть мелкой шихты в виде стружки или скрапа;
- Крупную часть шихты уложить у стенок тигля перпендикулярно направлению магнитных силовых линий что создает более благоприятные условия для быстрого расплавления шихты;
- Остальную часть шихты уложить так чтобы добиться максимальной плотности ее кладки в тигле для чего мелкую часть шихты расположить между крупными кусками и в средней части тигля.
Загружать тигель выше уровня индуктора не рекомендуется так как это замедляет плавку. После окончания загрузки тигель следует закрыть керамической крышкой и включить ток.
в) Контроль качества и корректировка металла по химическому составу:
- отбор пробы на химический анализ;
- скачивание шлака графитовой ложкой;
- замер температуры металла.
Корректировка чугуна по химическому составу осуществляется путем ввода соответствующего компонента шихты приведенные в таблице 28.
Таблица 28 - Корректировка химического состава чугуна
Требуемое изменение химического состава массовая доля %
Наименование вводимого компонента
На 1 т. жидкого металла кг
увеличение С на 0.1 %
увеличение Si на 0.1 %
увеличение Mn на 0.1 %
уменьшение С на 0.1 %
уменьшение Si на 0.1 %
г) Выпуск метала из печи в ковш и его доводка:
- предварительно прогреть докрасна ковш на стенде подогрева.
- подвести ковш к плавильной печи с помощью крана.
- снять напряжение с индуктора.
- измерить температуру металла в печи с помощью термопары погружения. Температура расплава должна составлять 1450 - 1470 °С.
- включить механизм поворота печи и осуществить выпуск металла из печи в ковш. Наклон тигля печи производить без рывков и толчков.
- после слива металла печь возвратить в исходное положение очистить тигель и носок печи от остатков шлака.
- с помощью крана транспортировать ковш с металлом к месту скачивания шлака.
- с помощью скребка удалить шлак с поверхности расплава из ковша в шлаковый короб.
- с помощью ложки взять пробу и отлить образец для определения механических свойств.
- с помощью крана транспортировать ковш с металлом к месту его разливки в формы.
- перед заливкой литейных форм измерить температуру расплава в ковше с помощью термопары погружения. Температура расплава должна быть не ниже 1300 - 1320 °С [1].
7.1.2 Модифицирование чугуна
Для модифицирования применяют графитизирующие модификаторы которые служат для измельчения графита и устранения отбела. В качестве основного модификатора используется ферросилиций ФС75. Но кроме ФС75 можно также применять силикокальций черный графит (если только необходимо устранить отбел без особого влияния на механические свойства чугуна) а так же модификаторы содержащие редкоземельные металлы в том числе Ce и Y которые в небольших количествах (003 - 01 %) способствуют графитизации.
Сам процесс модифицирования будет происходить в ковше. Для этого модификатор в виде кусков размером 5 - 15 мм вводится в струю чугуна при сливе из печи в ковш. Но перед использованием модификатора его нужно прокалить при температуре 300 - 400 °С. Во избежание демодифицирования продолжительность выдержки чугуна не должна быть больше живучести модификатора то есть для ФС75 и объема ковша 25 т выдержка должна быть не больше 10 минут.
В случае проявления признаков демодифицирования чугуна рекомендуется повторная обработка модификатором. Контроль качества модифицирования производится по высоте отбела клиновой пробы. Контрольные пробы отливаются через 5 - 15 мин.
В результате модифицирования повышаются не только механические свойства чугуна но и однородность структуры и свойств по сечению отливки.
7.1.3 Футеровка индукционной печи.
Состав кислой (кварцевой) огнеупорной футеровки для печи представлен в таблице 29.
Таблица 29 - Характеристика футеровки
Массовая доля составляющих %
Плотность в уплотненном состоянии
Массовая доля борной кислоты рекомендуется различной: при кислой футеровке в донной части тигля - около 10 % в верхней части - около 2 %. Технология изготовления такой футеровки включает следующие операции: подготовку смеси набивку и спекание. Подготовка смеси заключается в сушке рассеве исходных материалов на фракции дозировании и смешивании фракций. Связующее также просушивается размалывается и просеивается. Перемешивание подготовленной смеси со связующим производится непосредственно перед набивкой. Для набивки футеровки изготовляется шаблон из листовой малоуглеродистой стали (5 мм); наружный профиль шаблона соответствует профилю тигля печи; в стенках "шаблона в шахматном порядке на расстоянии 200 × 200 мм выполняются отверстия диаметром 5 - 6 мм. Набивка футеровки производится в зазоре между индуктором и шаблоном пневмотрамбовками вибраторами направленного действия или вручную слоями по 50 - 60 мм; перед засыпкой очередной порции смеси поверхность предыдущего слоя разрыхляется.
Спекание футеровки производится по определенному режиму: вначале до Т = 1300 °С за счет разогрева шаблона вихревыми токами при включении печи а затем - залитым или наплавленным жидким металлом. Длительность эксплуатации футеровки составляет обычно один - три месяца.
7.2 Описание технологического процесса в формовочном отделении
7.2.1 Вакуумный метод формовки
Процесс вакуумной формовки представлен на рисунке 1.
Нагретая пластичная пленка накладывается с помощью вакуума на снабженную вентами модель которая установлена в закрытом коробе где затем создается вакуум (а - б). Далее пленка облицованная на модель подвергается окраске.
На короб (в) для вакуума с моделью устанавливается опока. В форму (г) засыпается мелкозернистый не связанный кварцевый песок который уплотняется посредством вибрации.
После наложения покровной пленки из песка (д) отсасывается воздух и таким образом форма уплотняется. Для съема формы (е) вакуум на модели заменяется небольшим избыточным давлением.
До во время и после заливки сама форма остается под вакуумом (ж). Для отделения отливки вакуум поддерживаемый в форме убирается. Песок и отливка выпадают из опоки без какого-либо постороннего воздействия (з).
Выбивка отливок происходит на инерционной решетке с трехсторонним верхнебоковым шатровым зонтом двусторонним отсосом и подачей компенсирующего воздуха. Далее песок попадает в систему пескооборота. Сначала песок ссыпается с помощью виброжелоба в установку охлаждения песка в кипящем слое затем уже охлажденный песок перфорированным пластинчатым конвейером транспортируется в загрузочный лоток элеватора. Через разгрузочный лоток готовый к повторному использованию песок поступает в бункер установки вакуумно-пленочной формовки.
Если через слой зернистого материала продувать снизу воздух то при достижении некоторой скорости воздуха частицы материала начинают очень быстро и хаотично перемещаться образуя как бы кипящую жидкость. Это сходство не только внешнее: такой так называемый кипящий слой материала подчиняется законам гидростатики и обладает текучестью. Наличие большой поверхности контакта твердых частиц с газовой средой и интенсивное перемешивание частиц обусловливают эффективный теплообмен и массообмен между частицами и газовым потоком. Это позволяет эффективно использовать кипящий слой для охлаждения песка.
а - Нагрев и накладывание пленки
б - Модель облицованной пленкой
г - Заполнение песком
д - Наложение покровной пленки
е - Съем готовой полуформы
Рисунок 1 – Вакуум – пленочная формовка
5.2.2 Основные рекомендации для производства отливок
Применяемый метод вакуумно-пленочной формовки (V – процесс) имеет ряд особенностей:
а) Применяемый песок.
Песок благодаря отсутствию газотворных добавок и малому давлению газов в полости формы может иметь низкую газопроницаемость. Поэтому для получения плотной формы и чистой поверхности отливки применяют смесь двух фракций песка например 1К10202 или 1К102016 по ГОСТ 2138-91. Песок должен иметь влажность не более 01 %. Для того чтобы при вибрации облегчить перетекание песка способствующее более плотной упаковке зерен зерна песка должны иметь округлую форму (хотя песок с угловатыми зернами дает при меньшей объемной плотности большую прочность на сжатие). Применение мелкозернистого песка способствует повышению чистоты поверхности литья.
б) Материал для окраски формы.
Рефракторный наполнитель - цирконовый концентрат основа - спирт.
в) Метод окраски формы.
Эффективно применение распылителя для покрытия формы; тонкий слой образуется на пленке покрывающей модель.
Окраска кистью повлечет за собой неравномерную покраску на плоской поверхности. Потребуется больше времени на покраску.
Использование воздушного распылителя в некоторых случаях может вызвать засорение сопла и загрязнение воздуха на рабочем месте. Чтобы предотвратить засорение сопла рекомендуется погрузить сопло в раствор покрытия после использования.
Сушка осуществляется посредством обдува сжатым воздухом. Однако в целях сокращения времени сушки рекомендуется подача горячего воздуха нагретого при помощи электрического или газового устройства (90 – 100 °С).
д) Применяемые разновидности пленки.
Пленка типа “Сэвилен” (сополимер этилена с винилацетатом) представляет собой высокомолекулярное соединение относящееся к полиолефинам. Получают ее методом аналогичным методу производства полиэтилена низкой плотности (высокого давления). ”Сэвилен” превосходит полиэтилен по прозрачности и эластичности при низких температурах обладает повышенной адгезией к различным материалам. Данный тип пленки используется для стороны модели. В основном применяется пленка с толщиной 113 - 100 мкм Тпл = 80 °С и
Для обратной стороны опоки рекомендуется применять полиэтиленовую пленку низкой плотности толщиной 30 мкм.
е) Опока с фильтровой трубой и системой бокового отсоса.
Опока имеет отсасывающую перфорированную трубу с сетчатым фильтром и коллектор с патрубком. Края пленки отгибают и закрепляют на стенках опоки при помощи. В опоку засыпают песок и уплотняют его при помощи вибрации затем счищают излишек песка со стороны контрлада накладывают пленку и через трубу вакуумируют форму причем атмосферное давление спрессовывает песок до твердости 90 - 95 ед. Фильтровая труба должна быть расположена таким образом чтобы отливки можно было легко снять.
Для поддержания вакуума в форме при перемещении опоки на участок сборки и заливки используется обратный клапан.
ж) Установка вакуумного отсоса.
Механизм сохранения конфигурации рабочей поверхности формы при заполнении формы металлом весьма специфичен. Пленка нагреваемая до высокой температуры на воздухе воспламеняется и если бы это произошло в полости формы то песок обрушился бы. В V-процессе благодаря созданию вакуума пленка прижимается к песку а после расплавления полимера он втягивается в форму и связывает зерна образуя оболочку. При дальнейшем нагреве испаряющийся мономер всасывается в глубь формы где он конденсируется на холодных зернах песка и выполняет роль связующего. Деструкция пленки не уменьшает вакуум до нуля хотя образовавшаяся оболочка и обладает некоторой газопроницаемостью. Непрерывное вакуумирование формы поддерживает нужную разность давлений и оболочка как вначале пленка присасывается к основной массе песка сохраняя конфигурацию рабочей полости формы.
Благодаря тому что оболочка газопроницаема имеется возможность отсасывать газ из полости заливаемой формы.
Благодаря более медленному охлаждению металла а также некоторому разрежению в полости формы улучшается ее заполняемость. Для V - процесса необходимой характеристикой вакуумного отсоса является 300 - 400 мм.рт.ст. (40 - 533 кПа)
7.3 Описание технологического процесса в отделении финишных операций
Очистка отливок производится в дробеметно - дробеструйной камере периодического действия модели ДК-10.
Удаление оставшихся после выбивки заливов швов и других неровностей на наружных и внутренних поверхностях отливок а также вырубку дефектов для заварки технологических (ложных) рёбер в отливках выполняют пневматическими рубильными молотками с зубилами (модели МР-4).
Для зачистки питателей прибылей и других мелких неровностей на наружных поверхностях чугунных отливок применяют специальные установки снабжённые абразивными корундовыми кругами. Заусенцы острые кромки и другие подобные неровности отливок удаляют на специальных вибрационных машинах и на заточных шлифовальных станках.
Основными методами исправления дефектов отливок являются декоративная заделка мелких поверхностных раковин пастами – мастиками и замазками; пропитывание специальными составами (водным раствором аммония) для устранения пористости отливок газовая или электрическая сварка.
Грунтовку применяют для предохранения отливок от коррозии при их длительном хранении или транспортировке. Окраске подвергают наружные и внутренние поверхности отливок не подлежащие обработке резанием специальной густой краской (грунтом). Перед грунтовкой отливки поверхности отливки очищают от песка и пыли в моечных установках струёй едкого натра. Отливки грунтуют в проходных окрасочных камерах на подвесных конвейерах окунанием в бак с краской. После грунтовки отливки сушат в проходной сушильной камере.
Контроль отливок осуществляется на двух этапах: после зачистки (промежуточный) и окончательный.
8 Возможные дефекты в отливках и методы их устранения
Для отливок изготовляемых по технологии вакуумно-пленочной формовки (ВПФ) характерны виды дефектов:
усадочная пористость;
Следует отметить что по данным литейных цехов зарубежных фирм общее количество видов брака по сравнению с технологией изготовления отливок в песчаных формах снижено в 2 с лишним раза. Сложность борьбы с браком в общем случае в том что один и тот же дефект может быть вызван рядом причин и одно и та же причина может повлечь за собой несколько видов дефектов. Поэтому выявление и ранжирование технологических факторов определение их оптимальных значений влияющих на качество отливок для технологии ВПФ - весьма важный вопрос.
Изучение процесса заполнения формы расплавом проведение полнофакторных экспериментов и анализ их результатов позволили сделать вывод что технологическим фактором оказывающим доминирующее влияние на образование газовых дефектов в отливках является величина разрежения в пространстве наполнителя формы. Именно от этого фактора на стадии формообразования и динамики его изменения во время заливки зависят прочность формы и как следствие качество отливок.
Виды брака (ГОСТ 19200 - 80) отливок изготовляемых ВПФ и меры его предупреждения:
а) усадочная пористость – дефект в виде мелких пор образовавшихся вследствие усадки металла во время его затвердевания при недостаточном питании отливки.
Способы предупреждения и устранения дефектов:
конструирование отливки с учетом процента усадки сплава;
простановка прибылей в массивных частях отливки;
ЛС должна обеспечивать питание отливки в процессе ее охлаждения;
б) рыхлота – дефект в виде скопления мелких усадочных раковин.
те же что и для усадочной пористости.
в) розностенностъ – дефект в виде увеличения или уменьшения толщины стенок отливки вследствие смещения деформации или всплытия стержня.
тщательная сборка форм.
г) заливы – дефект в виде металлического прилива или выступа возникающего вследствие проникновения жидкого металла в зазоры по разъему формы стержней или по стержневым знакам.
Способы предупреждения и устранения:
пленка перед нанесением на модель должна быть разогрето до температуры термопласта чтобы исключить места неплотного ее прилегания в углах модели и образование галтелей;
зазоры в знаковых частях между формой и стержнем в условиях ВПФ должны быть сведены к минимуму;
перед заливкой возможна установка груза на верхнюю полуформу.
д) газовая пористость – дефект в виде мелких пор образовавшихся в отливке в результате выделения газов из металла при его затвердевании.
Способы предупреждения и устранения:
дегазация расплава перед его заливкой в форму;
снижение температуры заливки расплава на 15 – 20 °С;
выбор минимально допустимой величины разрежения в форме при ее заливке.
е) газовая шероховатость – дефект в виде сферообразных углублений на поверхности отливки возникающих вследствие роста газовых раковин на поверхности раздела "металл – форма".
выбор минимального разрежения в форме при ее заливке;
не допускать порывов пленки оформляющей полость формы;
ЛС должно обеспечивать спокойное заполнение расплавом полости формы;
наколы в пленке в торцах знаковых частей формы для удаления газов из стержня его естественным вакуумированием.
ж) газовые раковины – дефект в виде полости образованной выделившимися из металла или внедрившимися в металл газами.
Способы предупреждения и устранении:
з) пригар – дефект в виде трудноотделяемого специфического споя на поверхности отливки образовавшегося вследствие физического и химического взаимодействия формовочного материала с металлом и его оксидами.
нанесение противопригарного покрытия на пленку со стороны формовочного материла;
Для исправления несквозных дефектов средних и больших размеров на не обрабатываемых нерабочих местах отливок использоваться такой вид заделки дефектов как - холодная сварка. Этот вид сварки выполняют без нагрева с предварительной тщательной подготовкой и разделкой пораженного места отливки.
В отливках из любых сплавов наиболее часто встречаются газовые дефекты. При этом если в реальных производственных условиях большинство технологических факторов можно зафиксировать на заранее заданных уровнях то разрежение в форме может изменяться случайным образом. Причинами могут служить: случайные капли расплава попавшие на пленку контрлада при заливке формы порывы пленки в рабочей полости формы и ряд других способствующих разгерметизации формы.
Поэтому наряду с правильным подбором перечисленных технологических факторов и правильно сконструированной ЛС крайне важно в конструкции машины для ВПФ иметь систему слежения и автоматического регулирования разрежения в вакуумируемой форме на протяжении всего цикла изготовления отливки что позволит свести к минимуму вероятность появления брака по газовым включениям и пригару.
9 Система управления качеством продукции
Для осуществления системы качества продукции в проектируемом литейном цехе осуществляется контроль не только за качеством выпускаемой продукции но и за всеми технологическими процессами и за всеми видами материалов которые используются в производстве.
За качеством следит отдел технического контроля (ОТК). За качество также отвечает главный инженер.
За контроль качества в цехе отвечают:
- мастер смены участка;
Методы контроля за технологическими процессами в различных отделениях цеха представлены в таблице 30.
Таблица 30 - Управление качеством продукции
- кокс литейный КЛ-1;
Жидкий металл: ЧС5 и СЧ20
Осуществляется путем проведения химического анализа в лаборатории предприятия для сравнения с сертификатом завода поставщика. Если будут отклонения то должен быть выполнен повторный контрольный анализ удвоенного количества проб. Среднеарифметический результат повторного анализа будет являться окончательным.
Осуществляется путем проведения химического анализа в экспресс лаборатории цеха для контроля технического процесса плавки металла. При этом контролируется химический состав сплава его температура и так же берется проба на отбел.
Продолжение таблицы 30
Концентрация углерода и серы проверяется кулонометрическим способом или титрованием.
Все остальные элементы – при помощи спектрального анализа.
Измерение углеродного эквивалента происходит путем снятия термограммы и при помощи электрического пирометра.
Проба на отбел проверяется при помощи клиновой пробы.
Раствор едкого натра;
При поступлении на склад песок должен пройти химический анализ в лаборатории предприятия.
При подготовке песка контроль качества должен выполняться в соответствии с технологическим процессом: влажность газопроницаемость газотворность осыпаемость. Контроль осуществляется в экспресс лаборатории цеха на соответствующем оборудовании. Так же частичный визуальный контроль может быть осуществлен рабочим на своем рабочем месте. При поступлении компонентов для ЖСС должны проверятся необходимые документы подтверждающие качество продукции.
При поступлении на склад пленка должна пройти контроль на соответствие ТУ 6-05-1636-97
Основной метод контроля – визуальный и осуществляется самим рабочим-обрубщиком. Рабочий так же может воспользоваться измерительными средствами и приборами для осуществлении контроля в соответствии с заданными геометрическими параметрами.
Каждая отливка должна быть проверена на соответствие геометрических размеров.
Также отливки должны быть проверены методами неразрушающего контроля – радиографической и ультразвуковой дефектоскопией для выявления внутренних дефектов. Если был выявлен дефект то отливка должна отправиться на участок заделки дефектов.
И если там не удается устранить дефект то такую отливку отправляют на переплав.
Отливка представитель должна пройти контрольно–сдаточные испытания.
9.1 Организация и метод контроля отливок
Отливки в проектируемом цехе контролируются по следующим видам контроля:
а) Контроль размерной точности отливки
Отливка проверяется на соответствие геометрическим размерам указанных в чертеже. Контроль выполняется на размерной плите линейкой рейсмусом шаблоном и другими инструментами. Таким образом в цехе определяется коробление перекос подутость и разностенность.
Проверяется каждая первая партия отливок после смены модельного комплекта.
б) Контроль внешнего вида отливки
Контроль внешнего вида отливки выполняют визуально на соответствие отливок техническим условиям путём сравнения с эталоном.
в) Контроль качества поверхности и выявления дефектов
Внутренние дефекты отливок в проектируемом цехе выявляются методами радиографической и ультразвуковой дефектоскопии. Дефекты отливок (шлаковые включения газовые и усадочные раковины рыхлоты поры и трещины) в меньшей степени поглощают (ослабляют) интенсивность лучей чем сам металл поэтому на специальной плёнке (которая применяется в данном методе) такие дефекты появляются в виде тёмных пятен. Радиографические методы позволяют определить глубину залегания дефекта и его размеры.
Поверхностные дефекты отливок в виде трещин пор и раковин пригара и ужимин выявляются различными методами. Видимые дефекты обнаруживают при визуальном осмотре. Невидимые поверхностные дефекты определяются с помощью люминесцентной магнитной и цветовой дефектоскопии.
Шероховатость поверхности определяется по специальным образцам и контролируется с помощью эталонов и специальных приборов – профилографов и профилометров.
г) Контроль механических свойств
Прочность отливок определяется по специальным отливкам-образцам приливам отливок и вырезанием из отливок образцов. Твердость определяется на отливке а в некоторых случаях на образцах вырезанных из отливок. По специальным отливкам-образцам так же определяются временное сопротивление относительное удлинение и т.д.
На прочность проверяются образцы из каждой партии отливок; на твердость – каждая крупная отливка а средние и мелкие выборочно.
д) Контроль микроструктуры
Микроструктура проверяется по стандартным образцам-приливам и по вырезанным из отливок образцам. Из образцов изготавливаются шлифы по которым в лаборатории металлографии определяется микроструктура.
Контролю подвергаются все ответственные отливки; отливки общего назначения проверяются выборочно.
е) Контроль химического состава
Отлитые образцы или стружка отливки подвергаются в лаборатории химическому или другому специальному анализу.
Проверяется каждая партия отливок.
ж) Испытание на гидропроницаемость
Испытания проводятся на специальных стендах. В испытываемую полость наливается вода или керосин до требуемого уровня. Места течи определяются визуально. Отливки работающие под давлением испытывают после механической обработки. Проверяется каждую отливку если того требуют технические условия.
з) Контроль на соответствие отливки технологическим требованиям
Проверяется точность некоторых геометрических размеров наличие специальных транспортировочных скоб (для крупных и средних отливок) а также технологических приливов и т.п. Контролируется покрытие отливок специальными грунтовками их жаростойкость и другие параметры.
Основанием для контроля является чертеж литой детали. Проверяется каждая крупная отливка а средние и мелкие отливки выборочно.
Отливки взвешиваются после проверки их на геометрическую точность.
10 Складское хозяйство цеха
10.1 Хранение и транспортирование оснастки
Модели и опоки следует хранить в специально оборудованном общезаводском складе модельной оснастки.
Подача комплектов оснастки в промежуточные склады модельной оснастки должна производиться вилочными электропогрузчиками и электрокарами в унифицированной таре на поддонах электрокарами с прицепами.
Промежуточные склады модельной оснастки необходимо оборудовать подъемными средствами (электропогрузчиками штабелерами) стеллажами этажерками позволяющими хранить на прокладках модели опоки модельные плиты с моделями в несколько ярусов высотой 15 – 20 м что определяется возможностями штабелируемого механизма [2].
Для хранения крупных опок и другой литейной оснастки следует предусматривать открытые или крытые эстакады. Склады опок должны размещаться в непосредственной близости к формовочным участкам.
10.2. Хранение и транспортировка отливок и возврата
Готовые отливки хранятся на общезаводском складе отливок. Межоперационные склады отливок предусмотрим с применением унифицированной оборотной тары которая обеспечивает многоярусную укладку электропогрузчиком а при больших объемах складов – организацию механизированных и автоматизированных складов с использованием штабелеров.
Возврат собственного производства (литники и бракованные отливки) после резки доставляется в шихтовое отделение электропогрузчиком в контейнерах для последующего переплава.
11 Расчет численности персонала цеха
При планировании штата работающих персонал цеха подразделяют на следующие категории: рабочие и их ученики младший обслуживающий персонал (МОП) инженерно-технические работники (ИТР) служащие - счетно-конторский персонал (СКП).
Расчету количества основных и вспомогательных рабочих должно предшествовать составление годового фонда времени их работы.
Важнейшим в данном разделе является расчет так называемого расстановочного (явочного) штата основных производственных рабочих под которым понимается количество рабочих которые должны быть заняты работой во всех сменах [3].
Расстановочный штат производственных рабочих рассчитывается в соответствии с принятыми в проекте нормами обслуживания машин и агрегатов их количеством и запроектированной сменностью работы либо по нормам на выполнение отдельных операций.
В случае использования норм обслуживания явочное число рабочих Р определяется по формуле (16):
где f – норма обслуживания одного агрегата чел.смена;
О – количество агрегатов находящихся в работе шт.;
С – число смен в сутки.
Согласно формуле (16) определяем явочное число производственных рабочих для:
а)Плавильного отделения:
Рпл = 3 · 1 · 1 = 2 чел.
б)Формовочного отделения:
Рфор = 2 · 4 · 1 = 8 чел.
в)Шихтовое отделения:
Рш = 2 · 1 · 1 = 2 чел.
г)Отделения финишных операций:
Рфин = 7 · 1 · 1 = 7 чел.
Р = Рпл + Рфор + Рш + Рфин = 2 + 8 + 2 + 7 = 19 чел.
На основании установленного явочного количества производственных рабочих рассчитывается их списочный состав по формуле (17):
где Рсп – количества производственных рабочих чел.;
Р – явочное число рабочих чел.;
d – коэффициент показывающий отношение действительного фонда времени рабочего к номинальному d = 083 ÷ 090
Тогда согласно формуле (17) рассчитаем количество производственных рабочих:
Рпр = 19083 = 23 чел.
Количество вспомогательных рабочих для работы в цехе 70 % от основных производственных рабочих ИТР – 7 – 9 % СКП – 06 – 10 % МОП – 15 – 2 %. Используя эти соотношения составляется ведомость списочного состава всего персонала (таблица 31).
Таблица 31 - Ведомость списочного состава персонала
Основные производственные рабочие
Вспомогательные рабочие
Итого списочный состав всех рабочих за две смены
12 Система управления
Схема управления цехом схема управления и принятия управленческих решений представлена в таблице 32 и приложении А.
Таблица 32 - Схема управления и принятия управленческих решений
Лицо принимающее решение или функциональное звено
Развитие предприятия (новое строительство
реконструкция и т.д.).
– административная: 50 %
– коммерческая: 35 %
Собрание акционеров;
Научно-технический совет предприятия.
Техническое развитие производства (реконструкция и модернизация без строительства основных вспомогательных и обслуживающих хозяйств).
административная: 40 %
Оперативное управление производством (организация работы на конкретном рабочем месте выдача и учет выполнения задания выдача инструмента вопросы связанные с отклонением от производственного процесса).
административная: 15 %
Коммерческие и финансовые директора.
Плановое диспетчерское бюро;
Бюро технического контроля.
13 Схема грузопотоков
На основе технологических программ отделений можно составить схему грузопотоков в год в проектируемом цехе.
На склад шихтовых материалов из базисного склада по подъездным железнодорожным путям в контейнерах поступают чугун литейный и лом стальной а ферросплавы в специальных мешках. Из отделения финишных операций транспортируется возврат собственного производства (литники и неисправимый брак отливок). Шихта из контейнеров при помощи крана загружается в суточные бункера а оттуда с помощью весовых дозаторов и ленточного конвейера подается в специальные тележки. И уже эти тележки расположенные на высоте загрузки печи передвигаются в плавильное отделение и загружают тигель шихтой.
Формовочные материалы (кварцевый песок и пленка) поступают на склад формовочных материалов железнодорожным или автомобильным транспортом. На складе песок разгружается в контейнер для хранения а пленка на специальную площадку. На складе производится подготовка свежего песка которая заключается в сушке. Для сушки песка применяется горизонтальная барабанная печь и установка для сушки и охлаждения песка в кипящем слое.
Со склада формовочных материалов свежий песок подается к бункерам установки вакуумно-пленочной формовки. После формовки полуформы доставляются на участок сборки и заливки форм.
Жидкий металл из плавильного отделения при помощи мостового передается на заливочный плац. Заливка происходит из литейного ковша конического типа.
После заливки и охлаждения отливки поступают на выбивку.
Выбивка отливок происходит на инерционной решетке. Далее песок попадает в систему пескооборота. Сначала песок ссыпается с помощью воброжелоба в установку охлаждения песка в кипящем слое затем уже охлажденный песок перфорированным пластинчатым конвейером транспортируется в загрузочный лоток элеватора. Через разгрузочный лоток готовый к повторному использованию песок поступает в бункер установки вакуумно-пленочной формовки.
С участка выбивки отливки поступают на участок обрубки зачистки и финишных операций. Годные изделия направляются на наждачную заточку отливки с исправимыми дефектами на заделку а отливки с неисправимыми дефектами отправляют на переплавку.
Годные отливки поступают на склад готовой продукции.
Схема грузопотоков приведена в приложении Б.
Технология изготовления отливки
1 Анализ конструкции отливаемой детали и оценка её технологичности
Данная деталь имеет достаточно простую конструкцию. Она имеет вид полуцилиндра с внутренней видом в форме бутылки. Габаритные размеры детали – R761×275. Толщина стенок цилиндрической части отливки 40 мм.детали 15 кг.
Разработка модельно-литейных указаний показана на чертеже 1 подмодельная плита показана на чертеже 2 форма в сборе показа на чертеже 3.
2 Обоснование и выбор способа изготовления отливки
Данную отливку целесообразно изготавливать литьем в вакуум-пленочные песчаные формы. Выбор данного способа литья обусловлен в первую очередь требованиями к шероховатости поверхности детали (Rz40 за исключением нескольких поверхностей с Rz25 которые подвергаются механической обработке) конфигурацией отливки материалом из которого изготавливается отливка а также типом производства (мелкосерийное).
Литье в вакуум–пленочные песчаные формы обеспечивает простоту изготовления форм относительно небольшие капитальные вложения не требует дорогостоящих материалов и высококвалифицированных кадров позволяет получать отливки данных габаритов и конфигурации. Уплотнение формовочной смеси производится за счет вакуумирования.
3 Определение поверхности разъёма модели и формы
Разъём модели и формы показан на чертеже отрезком заканчивающейся знаком –х над которым стоит буквенное обозначение разъёма – Ф. Направление разъёма показано сплошной основной линией ограниченной стрелками перпендикулярной разъёма. Плоскость разъёма выбрана так чтобы обеспечивалось свободное извлечение модели без поломок формы. Положение отливки в форме при заливке обозначено буквами В (верх) и Н (низ). Буквы стоят у стрелок показывающих направление разъёма формы.
4 Назначение припусков на механическую обработку и точность размеров и массы отливки
Припуском на механическую обработку называется слой металла (на сторону) который предназначен для снятия в процессе механической обработки. Припуск соответствует серединам полей допусков детали и отливки. Припуски на механическую обработку определяются согласно ГОСТ 26645-85 [9]:
При выборе технологичности процесса литья выбирается литье в вакуум – пленочные песчаные формы.
При выборе типа сплава выбираются значения относящиеся к термообрабатываемым чугунным и цветным тугоплавким сплавам. При этом выбираются меньшие значения относящиеся к отливкам небольшой сложности.
а) Класс размерной точности отливки
Наибольший габаритный размер отливки – 2754 мм
Тип сплава – термообрабатываемый чугунный сплав
Технологический процесс литья – литье в вакуум – пленочные песчаные формы
Класс точности размеров – 10
б) Допуск размера отливки - выбирается в зависимости от класса точности отливки и номинального размера.
Номинальный размер 2754 мм
Величина допуска – 40 мм
в) Степень точности поверхности отливки - берется в зависимости от технологического процесса литья типа сплава и наибольшего габаритного размера отливки.
Наибольший габаритный размер отливки - 132 мм
Отливка простая изготавливаемая в условиях мелкосерийного производства
Степень точности поверхности отливки – 11
г) Ряд припусков на механическую обработку отливки – выбирается по степени точности поверхности отливки.
Степень точности поверхности – 11
д) Степень коробления элементов отливки - выбирается по элементу отливки с наибольшей степенью коробления. То есть отношение наименьшего размера элемента отливки к наибольшему должно быть минимальным.
Сложность отливки - простая
Степень коробления отливки – 6
е) Допуск формы и расположения элементов отливки - выбирается по степени коробления и номинальному размеру нормируемого участка.
Номинальный размер нормируемого участка – 2754 мм
Степень коробления элементов отливки - 6
Допуск формы и расположения элементов отливки – 10 мм
ж) Окончательный вид механической обработки с учетом погрешностей формы и расположения поверхности отливки
Чистовая механическая обработка
з) Точность обработки и припуски отливок.
Выбираем неавтоматизированное оборудование при высоком уровне точности обработки при средней точности станков.
и) Общий допуск элементов отливки - выбирается в зависимости от допуска размера от поверхности до базы и от допуска формы и расположения поверхности. (Для поверхностей симметричных или образованных телом вращения берется половинный допуск).
Допуск размера от поверхности до базы – 40 мм
Допуск формы и расположения поверхности – 10 мм
Общий допуск – 40 мм (не более)
к) Общий припуск на сторону - определяется по общему допуску элемента поверхности виду окончательной механической обработки и ряду припуска на механическую обработку.
Общий допуск элемента поверхности – 40 мм
Окончательная механическая обработка – чистовая
Общий припуск на сторону – 48 мм (не более)
л) Класс точности массы отливки - выбирается исходя из технологического процесса литья номинальной массы отливки и типа сплава.
Номинальная масса отливки – 150 кг
Класс точности массы отливки – 9
м) Допуск массы отливки и припуски на обработку
Класс точности массы – 9
Допуск массы отливки – 8 %.отливки с учётом припусков 162 кг
н) Минимальный литейный припуск на сторону
Ряд припуска отливки – 6
Минимальный литейный припуск – 06 мм (не более)
о) Допуск смещения отливки по плоскости разъёма – выбирается по классу размерной точности отливки и номинальному размеру наиболее тонкой из стенок отливки выходящих на разъём или пересекающих его.
Класс размерной точности – 10
Номинальный размер – 40 мм
Допуск смещения – 22 мм
Точность отливки: 10 – 6 – 11 – 9 См. 22 ГОСТ 26645-85
Масса 15-008-0-162 ГОСТ 26645-85
5 Выбор усадки сплава
Величина линейной (свободной) усадки серого чугуна ЧС5 соответствует 05 - 12 %. Коэффициент объёмной усадки () в жидком и твёрдо-жидком состояниях для чугуна ЧС5 принимается равным 2 % [10].
6 Назначение формовочных уклонов и галтелей
На вертикальных стенках моделей предусматривают специальные уклоны для того чтобы модель можно было свободно удалить из формы без каких-либо повреждений формы.
Формовочные уклоны на обрабатываемых поверхностях отливки выполняют сверх припуска на механическую обработку. Уклоны устанавливаются по ГОСТ 3212-80 [11]. Следовательно для Н = 761 уклон равен 25' или 075 мм.
Для получения плавных переходов от одной поверхности отливки к другой предусматриваются галтели.
7 Выбор и расчет прибыли холодильника и литниковой системы
По формуле (18) Намюра-Шкленника рассчитаем объем прибыли:
где m – безразмерный коэффициент зависящий от расстояния между прибылью и местом подвода металла;
– объёмная усадка сплава %100;
– безразмерный коэффициент конфигурации прибыли;
y – безразмерный коэффициент учитывающий относительную продолжительность затвердевания теплового узла и прибыли в зависимости от их конфигурации;
z – безразмерный коэффициент характеризующий тепловое состояние прибыли и теплового узла;
Vф – объём формы или той её части для которой рассчитывается прибыль см3
Rэ.т.у. – эффективная приведённая толщина теплового узла отливки.
Для расстояния между прибылью и питателем литниковой системы равного >2 толщины стенки отливки m = 10.
Для наиболее часто применяемой прибыли с соотношением высоты и диаметра значение x = 108.
Эффективная приведенная толщина теплового узла отливки определяется по соотношению (19): (19)
где Vэ.т.у. – объём теплового узла см3;
Sэ.т.у. – площадь поверхности на которой осуществляется теплоотвод см2.
Тогда из соотношения (19) эффективная приведенная толщина теплового узла отливки равна:
Выбираем коэффициент объемной усадки. Так как отливка изготавливается из высокопрочного чугуна то коэффициент объемной усадки равен: b = 004.
Примем y = 162 для цилиндрической прибыли.
Коэффициент Z = 1 для песчаной формы.
Следовательно по формуле (18) объем прибыли равен:
Vпр.= 10 × 108 × 2373 × (1 + 004)3 × 162 × 1+3 × 004×364 = 266357 см3.
Из полученных данных находим высоту и диаметр прибыли:
Расчет перешейка производится по формуле (20):
где a b и c – размеры перешейка мм;
n – коэффициент теплообмена;
R' – приведенная толщина прибыли см
Значит размеры перешейка будут:
a=30мм; b=30мм; c=30мм.
8 Выбор и расчёт элементов литниковой системы
Для питания отливки выбираем среднебоковую горизонтальную литниковую систему как наиболее удобную для формовки и позволяющую получить максимальную плотность отливки. В форме расположено 2 отливки.
Выбираем литниковую систему расширяющегося типа как обеспечивающую спокойную заливку и соответственно более высокое качество отливок. В такой системе самым узким местом будет поперечное сечение стояка.
Таким образом шлакоуловители и литниковые ходы расположены сбоку отливки в горизонтальной полости формы что удобно в отношении формовки.
Все расчеты элементов литниковой системы ведутся от площади самого узкого сечения. Площадь самого узкого сечения находится по формуле (21) [12]:
где М – масса одной отливки равная 162 кг (с учётом припусков);
N – число отливок в форме равное 2 шт;
– продолжительность заполнения формы металлом;
ρ – плотность жидкого металла ρ=6950 кгм3;
– коэффициент расхода литниковой системы =06 – так как сопротивление системы малое используется 1 поворот и горизонтальная среднебоковая литниковая система;
НР – расчётный статический напор металла.
Продолжительность времени затвердевания формы исчисляется от начала выхода металла из питателей и до подхода его к потолку рабочей полости формы. Для устранения дефектов которые могут появиться в отливках в виде недоливов неслитин ужимин и засоров возникающих в результате длительного теплового воздействия расплава на стенки формы необходимо более быстрое заполнение формы.
Продолжительность заполнения формы металлом определяется по формуле (22) (формула Соболева - Дубицкого):
где - продолжительность заполнения формы с;
– преобладающая толщина стенки отливки мм;
S - коэффициент зависящий от рода сплава тип литейной формы конструкцию литниковой системы;
М - масса отливки кг.
Таким образом продолжительность заполнения формы металлом по формуле (22) равно:
Расчётный статический напор металла рассчитывается по формуле (23):
где Нр – расчётный статический напор м;
Нст – высота стояка м;
p – высота от оси питателей до верха отливки;
Н1 – расстояние от формы до уровня металла в поворотном ковше м.
По формуле (23) для опоки с высотой 150 мм расчётный статический напор равен:
Таким образом по формуле (21):
Диаметр стояка рассчитывается по формуле (24):
где Fуз - площадь поперечного сечения узкого места см2.
Тогда диаметр стояка по формуле (24) равен:
Так как в производстве используются стандартные стояки выбираем минимальный диаметр стояка 3 см и получаем площадь узкого сечения FУЗ=71 10-6 м2.
Поперечное сечение шлакоуловителя и питателей рассчитаем согласно следующим соотношениям. Для чугуна соотношение площадей поперечных сечений стояка шлакоуловителя и питателей расширяющейся литниковой системы составляет: Fст : ΣFшл : ΣFпит = 1 : 12 : 15.
Отсюда Fшл = 71·12=85 см2; ΣFпит = 71·15 = 107 см2
Круг в сечении – наиболее распространенная форма стояков. В производстве для удобства формовки стояк имеет обратный конус.
Диаметр стояка внизу определяется по формуле (25):
Высота стояка принимается равной высоте полуформы см
Наиболее часто применяют шлакоуловитель постоянного сечения в виде трапеции площадь которого определяют по принятому соотношению площадей. Их определяет после расчета его площади поперечного сечения.
Ширина шлакоуловителя у основания определяется по формуле (26):
Тогда ширина нижнего основания шлакоуловителя по формуле (26) равно:
Ширина шлакоуловителя вверху определяется по формуле (27):
Следовательно по формуле (27):
Высота шлакоуловителя определяется по формуле (28):
Высота шлакоуловителя по формуле (28) равна:
Толщина питателя определяется по формуле (29):
dпит. = 075bотл (29)
Толщина питателя равна по формуле (29) равна:
dпит. = 075×40 = 3 10-2 м
Суммарная ширина питателей рассчитывают из равенства (30)
Тогда из равенства (30) ширина питателей равна:
Следовательно ширина одного питателя равна:
где k = 4– число питателей.
Длина питателей рассчитывается по формуле (31):
Из формулы (31) видно что длина питателей равна:
lпит. = 065 364=237 10-2 м
Размеры литниковой чаши определяют по формуле (32):
где Vмет – объем металла заливаемого в форму м3.
Из формулы (32) размер литниковой чаши равен:
9 Расчет времени выдержки отливки в форме
Время выдержки отливки в форме рассчитывается по формуле (33) которая включает в себя время для снятия перегрева время кристаллизации сплава и время необходимое для охлаждения отливки до температуры выбивки:
где tвыд – время выдержки отливки в форме с;
tпер – время для снятия перегрева с;
tкр – время кристаллизации с;
tохл – время охлаждения до температуры выбивки с.
Время для снятия перегрева рассчитывается по формуле (34):
где S0 – преобладающая толщина стенки отливки м;
ρж – плотность жидкого металла кгм3;
Cж – теплоемкость жидкого металла Дж(кг К);
bф – коэффициент аккумуляции теплоты формой (Вт с12)(м2 К);
bж - коэффициент аккумуляции теплоты жидким металлом (Вт с12)(м2 К);
Tзал – температура заливки металла К;
Tнф – начальная температура формы К;
Tкр – температура кристаллизации сплава К.
Тогда по формуле (34):
Время кристаллизации отливки рассчитывается по формуле (35):
где ρт-ж – плотность металла в твердо жидком состоянии кгм3;
Cэф – эффективная теплоемкость кристаллизующего металла Дж(кг К);
bт-ж – коэффициент аккумуляции теплоты металла в твердо - жидком состоянии
Tс – температура солидус К.
Эффективная теплоемкость кристаллизующего металла вычисляется по формуле (36):
где Cт-ж – теплоемкость металла в твердо жидком состоянии Дж(кг К);
L – удельная теплота затвердевания данного сплава Дж(кг К).
Тогда по формуле (36) эффективная теплоемкость кристаллизующего металла равна:
Из равенства (35) время кристаллизации отливки равно:
Время охлаждения отливки до температуры выбивки рассчитывается по формуле (37):
где ρт – плотность металла в твердом состоянии кгм3;
Cт - теплоемкость металла в твердом состоянии Дж(кг К);
bт - коэффициент аккумуляции теплоты металла в твердом состоянии (Вт с12)(м2 К);
Tвыб - температура выбивки К.
Из формулы (37) время охлаждения отливки до температуры выбивки равно:
Подставляя найденные значения в формулу (33) получаем:
Время выдержки отливки до выбивки составляет 3032 секунд или 505 минут.
[1] Далее состав сплавов приводится в масс. долях %. Слова “массовая доля” опущены
Грузопотоки.dwg

Склад готовой продукции
Участок грунтовки отливок
Участок обрубки литья
Плавильное отделение
Приложение Б Схема грузопотоков
- формовочные материалы
Масштаб: 1 мм = 25 т
СОДЕРЖАНИЕ.doc
Техника и организация производства12
1 Расчётная программа литейного цеха12
2 Расчёт формовочного отделения15
2.1 Расчет программы формовочного отделения15
2.2 Расчёт технологического оборудования формовочного отделения16
2.3 Расчёт основных параметров литейных линий16
3 Расчёт плавильного отделения17
3.1 Расчёт программы плавильного отделения17
3.2 Расчет технологического оборудования плавильного отделения17
4 Расчёт склада шихтовых материалов30
5 Расчёт очистного и термообрубного отделения31
5.1 Выбор обоснование характеристика и расчёт технологического оборудования31
5.2 Методы режимы и оборудование для термической обработки отливок32
6 Расчёт вспомогательного и подъёмно-транспортного оборудования33
6.1 Расчёт парка ковшей33
6.1.1 Ремонт футеровки раздаточных ковшей34
7 Описание технологического процесса в цехе34
7.1 Описание технологического процесса в плавильном отделении34
7.1.1 Плавка чугуна в индукционной печи34
7.1.2 Модифицирование чугуна36
7.1.3 Футеровка индукционной печи37
7.2 Описание технологического процесса в формовочном отделении38
7.2.1 Вакуумный метод формовки38
7.2.2 Основные рекомендации для производства отливок40
7.3 Описание технологического процесса в отделении финишных операций41
8 Возможные дефекты в отливках и методы их устранения42
9 Система управления качеством продукции45
9.1 Организация и метод контроля отливок47
10 Складское хозяйство цеха48
10.1 Хранение и транспортирование оснастки48
10.2 Хранение и транспортировка отливок и возврата49
11 Расчёт численности персонала цеха49
12 Система управления51
13 Схема грузопотоков51
Технология изготовления отливки53
1 Анализ конструкции отливаемой детали и оценка её технологичности53
2 Обоснование и выбор способа изготовления отливки53
3 Определение поверхности разъёма модели и формы53
4 Назначение припусков на механическую обработку и точность размеров и массы отливки53
5 Выбор усадки сплава.56
6 Назначение формовочных уклонов и галтелей56
7 Установление границ стержней и стержневых знаков56
8 Выбор и расчёт элементов литниковой системы57
9 Расчёт времени выдержки отливки в форме61
1 Меры по обеспылеванию рабочей зоны64
Безопасность жизнедеятельности67
1 Объемно-планировочные и другие характеристики проектируемого цеха67
2 Отопление и вентиляция67
4 Анализ опасных и вредных факторов71
5 Меры защиты от опасных и вредных факторов72
5.1 Меры защиты от тепловых излучений72
5.2 Меры защиты от пылегазовых выделений74
5.3 Меры защиты от шума и вибрации74
5.4 Предотвращение пожаров и взрывов75
5.5 Защита от поражения электрическим током77
5.6 Расчет бортовых отсосов77
6 Оценка возможности возникновения черезвычайной ситуации78
Экономика и управление производством80
1 Расчёт фондов заработной платы80
2 Расчет капитальных вложений производственных фондов
амортизационных отчислений81
3 Расчет себестоимости84
4. Расчет интегрального эффекта за весь период строительства и эксплуатации проектируемого цеха методом потока наличности86
5 Расчет точки безубыточности88
6 Расчет рентабельности производства89
Разработка оптимального варианта литья отливки “Стеклоформа” на основе компьютерного моделирования90
Список использованных источников98
Приложение А Схема управления цехом99
Приложение Б Схема грузопотоков100
СПИСОК ИСПОЛЬЗОВАННЫХ ИСТОЧНИКОВ.doc
Справочник по чугунному литью. Под ред. д-ра техн. наук Н. Г. Гиршовича. – Л.: Машиностроение 1978
Общесоюзные нормы технологического проектирования предприятий машиностроения приборостроения и металлообработки. Литейные цехи и склады шихтовых и формовочных материалов. – М.: МИНАВТОПРОМ 1984
Соловьёв В.П. Гладышев С.А. Воронцов В.И. Проектирование новых и реконструкция действующих литейных цехов. Учебное пособие. - М.: МИСиС 2002;
ГОСТ 1412-85 Чугун с пластинчатым графитом для отливок. Марки. – М.: Издательство стандартов 1985
ГОСТ 977-88 Стали конструкционные. Марки. – М.: Издательство стандартов 1988
Благов Б.Н. Сиваева Е.К. Соловьев В.П. Оборудование и проектирование литейных цехов. Расчет технико-экономических показателей проектируемого цеха. – М.: МИСиС 1979
Соловьёв В.П. Герасимов С.П. Проектирование итейных цехов. Учебное пособие. - М.: МИСиС 1989
Муравьев В.А. Охрана труда и окружающей среды. Безопасность жизнедеятельности. – М.: МИСиС 1995
ГОСТ 26645-85 Отливки из металлов и сплавов. Допуски размеров массы и припуски на механическую обработку – Переизд. Янв. 1990 с изм. 1- М.: Издательство стандартов 1994
Шкленник Я.И. Технологические основы литейного производства. М: МИСиС. 1977
ГОСТ 3212-80 Комплекты модельные. Уклоны формовочные. Основные размеры. - М.: Издательство стандартов 1982
Бауман Б.В. Балашова Н.П. Технологические основы литейного производства. Учебное пособие. - М.: Учёба 2003
Колтыгин А.В. Экологические проблемы литейного производства. Учебное пособие. - М.: Учёба 2003
Стрижко Л.С. Безопасность жизнедеятельности в металлургии. - М.: Металлургия 1996
Мастрюков Б.С. Безопасность жизнедеятельности. Учебное пособие. – М.: Учёба 2003
Нормативные показатели удельных выбросов вредных веществ в атмосферу от основных видов технологического оборудования предприятий отрасли. – Харьков: 1987.
ОБОСНОВАНИЕ ПРОЕКТА СТРОИТЕЛЬСТВА ЛИТЕЙНОГО ЦЕХА.doc
На данный момент времени состояние отрасли в частности литейной оценивается как не самое благоприятное. Это связано не только с экономической ситуацией по стране но и с тем что почти всё литейное оборудование на заводах последний раз обновлялось в 70-80 - х годах. Это привело к тому что производительности литейных цехов не хватает чтобы обеспечить необходимый объём выпуска продукции.
Сегодня многие литейные заводы закрываются сдают свои цеха под склады другим фирмам из-за нехватки финансовых средств и высокой себестоимости продукции. Чтобы остановить этот процесс нужно выпускать такое литьё себестоимость которого будет ниже существующей тогда и прибыль предприятия возрастёт. Для этого нужно модернизировать оборудование снизить количество рабочих и увеличить количество автоматического оборудования то есть механизировать как можно больше процессов. В связи с этим производительность предприятия в целом должна возрасти себестоимость упасть а прибыль вырасти.
На заводах стекольной промышленности для производства изделий из стекла использовались формы изготовленные в странах бывшего СССР. В связи с закрытием литейных цехов производивших эти формы руководством завода было принято решение о строительстве собственного литейного цеха.
Номенклатуру предприятия составляют отливки из чугуна марок ЧС5 СЧ20 и стали марки 30ХНМЛ массой от 13кг до 1000 кг. Технологические потери отливок составляют 30 %. Цех состоит из шихтового двора плавильного формовочно - заливочного термообрубного вспомогательных отделений и бытовых помещений.
Основными исходными данными для проектирования являются данные предоставленные руководством завода “Стекломаш”. Это номенклатура отливок и производственная программа литейного цеха.
На основе номенклатуры отливок составляется производственная программа цеха.
Расчётная программа служит для дальнейших расчётов всех отделений литейного цеха.
Основная цель расчётной программы состоит в том чтобы определить количество отливок каждого наименования которое должно быть изготовлено в течении года в литейном цехе.
Мощность проектируемого цеха 2500 тонн годных отливок в год. На основе анализа номенклатуры выпускаемых отливок определяются группы отливок по массе.
Способ изготовления отливок и соответственно тип плавильного оборудования зависят от марки сплава годового выпуска отливок массы отливок характера производства. После выбора технологического оборудования проводится расчёт необходимого их количества.
Затем переходят к графической части проекта. Выбирается ширина пролётов тип колонн наносится сетка колонн. После этого располагается технологическое оборудование.
В проекте предусматривается строительство одноэтажного производственного здания. Все основные технологические процессы проходят на первом этаже. Использование современного автоматизированного оборудования позволяет использовать минимальный штат рабочих и производить качественную продукцию.
План литейного цеха.dwg

Склад готовой продукции
Участок грунтовки отливок
Участок формовки литниковой чаши
Экспресс- лаборатория
Кладовая и ремонт инструмента
Участок обрубки литья
Склад компонентов ЖСС
Отзыв руководителя Грибков.doc
Студент Грибков О.В. выполнил дипломный проект на тему «Литейный цех на выпуск 2500 тонн в год отливок из чугуна и стали для стекольной промышленности». Тема проекта сформулирована по заявке производственной фирмы «ОАО Стекломаш» планируемой номенклатуре будущего завода.
В дипломном проекте студ. Грибков О.В. рассчитал программу литейного цеха и его подразделений обосновал выбор прогрессивных технологических процессов изготовления отливок на основе плавок в индукционных печах и вакуумно-пленочной формовки рассчитал количество технологического оборудования выполнил проект его объемно-планировочного размещения на имеющихся производственных помещениях а также определил условия безубыточной работы проектируемого цеха.
В специальной части дипломного проекта студ. Грибков О.В. рассмотрел различные технологические варианты изготовления типовой отливки стеклоформы и по данным компьютерного моделирования процессов заполнения и затвердевания чугунной стеклоформы определил оптимальный вариант их изготовления в комбинированных песчано-кокильных формах.
В период дипломирования студ. Грибков О.В. проявил себя активным работоспособным и инициативным.
В процессе выполнения дипломного проекта студ. Грибков О.В. показал умение работать с технической литературой различными компьютерными программами имитирующими процесс литья а также позволяющими выполнять проектно-графические работы.
В целом студ. Грибков О.В. уверенно справился с полученным заданием выполнил дипломный проект на заказанную тему в объеме предъявляемых к ней требований и заслуживает присвоения квалификации инженера по специальности «Литейное производство черных и цветных металлов». Работу студ. Грибкова О.В. над дипломным проектом оцениваю на «отлично» и рекомендую его для поступления в аспирантуру.
Руководитель дипломного проекта
ст.пр. каф. ТЛП Орехова А.И.
БЕЗОПАСНОСТЬ ЖИЗНЕДЕЯТЕЛЬНОСТИ.doc
В проектируемом литейном цехе используется различное технологическое оборудование и материалы поэтому необходим анализ условий труда и принятие ряда мер по безопасности жизнедеятельности трудящихся для предотвращения несчастных случаев на производстве и улучшения условий труда.
1 Объемно-планировочные и другие характеристики проектируемого цеха
Проектируемый цех состоит из двух продольных пролетов. Все оборудование в цехе размещено с учетом требований безопасности. Ширина всего цеха составляет 48 м длина равна 60м высота цеха 12 м. Площадь цеха равна 2880 м2. Объем цеха равен 34560 м3. Расстояние между колонн 6 м.
Численный персонал цеха составляет 43 человек. Тогда на одного работающего приходиться 288043 = 670 м2 и 3456043 = 8037 м3
Все подвижные механизмы оборудования защищены ограждениями. В центральной части цеха предусматриваются проезды шириной 3 м.
2 Отопление и вентиляция
Работа выполняемая в цехе относится к средней тяжести физических работ (категория 2а). Энергетические затраты рабочих составляют порядка 700 кДжч. Работы выполняемые в цехе связаны с постоянными перемещениями или выполняются сидя но не требуют перемещения тяжестей [14].
Так как в проектируемом цехе в основном находятся материалы в горячем раскаленном и в расплавленном состоянии а так же твердые вещества то в соответствии со СНиП 2-90-81 помещение по взрывобезопасности относится к категории Г.
Исходя из категорий выполняемых в цехе работ в соответствии с требованиями санитарных норм в таблице 33 приведены параметры воздушной среды для рабочей зоны.
Для создания заданных климатических условий в цехе применяем общеобменную вентиляцию.
Для этого рассчитаем количество воздуха подаваемого или удаляемого из помещения проектируемого литейного цеха по формуле (38) [15].
Таблица 33 - Параметры воздушной среды для рабочей зоны
Категория работ по тяжести
Относительная влажность %
Скорость движения воздуха мс
холодный период года
где L – количество воздуха м3ч;
K – коэффициент ед.;
V – объем помещения цеха м3.
Коэффициент К – принимается равным 6.
Тогда согласно формуле (38) количество воздуха будет равно:
L = 6 · 34560 = 207360 м3ч; L = 576 м3с
Произведем расчет мощности вентилятора по формуле (39):
где P – мощность вентилятора кВт;
Н – сопротивление воздушного потока при движении по воздуховоду ед.;
Сопротивление воздушного потока рассчитывается по формуле (40):
где Н – сопротивление воздушного потока при движении по воздуховоду ед.;
L – количество воздуха м3с.
По формуле (40) сопротивление будет равно:
H = 12 5762; Н = 39813 ед.
Тогда согласно формуле (39) мощность вентилятора будет равна:
Система отопления цеха подключена к заводской теплосети. Отопление цеха осуществляется в холодное время года в теплое время года – перекрывается подвод горячей воды к батареям отопления.
Для проветривания отделений цеха применяется аэрация. Воздух поступает через проемы в наружных стенах а удаление производится через аэрационные фонари.
Для работ выполняемых в цехе по СНиП 23-05-95 принят VII разряд зрительных работ.
С учетом принятого разряда зрительных работ нормированное значение освещенности равно 200 лк. В цехе используется совмещенное освещение – естественное и искусственное. Естественное освещение осуществляется через оконные проемы. Литейный цех расположен в III поясе светового климата поэтому коэффициент естественного освещения равен 41.
Искусственное освещение осуществляется с помощью дуговых ртутных ламп (ДРЛ) расположенных на фермах здания.
К искусственному освещению литейного цеха предъявляются следующие требования:
- достаточная освещенность рабочего места;
- высокое качество освещения (хороший спектральный состав близкий к естественному освещению и отсутствие ярких частей в поле зрения отсутствие колебаний);
- экономичность всей системы освещения;
- удобство в обслуживании;
- электро- и пожаробезопасность;
Исходя из этих требований проведем расчет искусственного освещения. Расчет будем проводить по коэффициенту использования светового потока.
Расчетная формула (41) для подсчета необходимого количества ламп:
где N – число светильников шт.;
– коэффициент использования светового потока ед.;
Ф – световой поток лм;
z – коэффициент пульсации зависит от напряжения в сети ед.;
E – освещенность на рабочем месте лк;
S – площадь помещения м2;
k – коэффициент запаса ед.;
Коэффициент использования светового потока () определяется по индексу производственного помещения по формуле (42):
– высота подвеса светильника м.
Тогда по формуле (42):
Тогда для i = 369 выбираем = 066 ед.
Так как были выбраны для проектируемого цеха лампы ДРЛ то приведем их технические характеристики:
– световой поток 22000 лм;
– продолжительность горения ламп состовляет: 1000 часов.
Тогда по формуле (41) число светильников будет равно:
Суммарная мощность осветительной установки рассчитывается по формуле (43):
где Р – мощность осветительной установки Вт;
– мощность одной лампы Вт;
N – число светильников шт.
Тогда согласно формуле (43) мощность осветительной установки будет равна:
P = 400 143 = 57200 Вт = 572 кВт.
Напряжение в осветительной сети принято равным 220 В ремонтного освещения – 42 В.
Кроме рабочего освещения предусмотрим аварийное освещение для которого используются отдельные светильники из общего количества по линии основных проходов.
4 Анализ опасных и вредных факторов
Анализ опасных и вредных факторов приведен в таблице 34.
Таблица 34 - Анализ опасных и вредных факторов в цехе
опасных и вредных факторов
Выгрузка из вагонов и самосвалов материалов в приемные ямы
повышенная запыленность
повышенный уровень шума
Пересыпка сыпучего материала
ленточные транспортеры
повышенная запыленность (SiO2)
Подготовка материалов
сита дробилки сушила
повышенная запыленность (SiO2) повышенный уровень инфракрасных излучений
Изготовление литейных форм
Вакуум-пленочные устройства
Навеска загрузка шихты
Электровесовая тележка загрузочная бадья
повышенная запыленность (FeO) повышенный уровень шума
Плавка чугуна слив металла заливка формы
индукционная тигельная печь
повышенное уровень инфракрасного излучения выделение пыли и газов (FeO СО NOх) повышенный уровень шума повышенный уровень электромагнитных излучений f=50 Гц
Продолжение таблицы 34
Сушка и подогрев ковшей
повышенное тепловыделение
инерционная решетка дробеметный барабан зачистной станок
повышенная запыленность
повышенный уровень шума.
На основании проведенного анализа и определения опасных и вредных производственных факторов можно сделать вывод что условия труда являются неблагоприятными и необходимо принять технические решения обеспечивающие защиту от опасных и вредных производственных факторов.
5 Меры защиты от опасных и вредных факторов
5.1 Меры защиты от тепловых излучений
Для защиты от тепловых потоков печей применяют водоохлаждаемые теплоотводящие экраны а также общеобменную вентиляцию. Экраны располагаются между печным агрегатом и рабочими местами с целью локализации теплового источников излучения.
Общеобменная вентиляция в плавильном отделении обеспечивается естественным притоком воздуха. Приток воздуха направляется к рабочим местам в виде воздушных душей.
Для защиты от тепловых излучений предусмотрена автоматизация производства – это непрерывная разливка с помощью литейной машины дозирование металла из плавильной печи в раздаточную печь посредством магнитодинамического дозатора оснащенные электроприводом. Все описанные мероприятия позволяют значительно увеличить дистанцию между оператором и источником тепловых излучений.
Для индивидуальной защиты предусматривается спецодежда: куртка и брюки из грубошерстного сукна специальная обувь стойкая против повышенной температуры с подошвой хромового дубления брезентовые рукавицы с внутренней стороны из грубой кожи. Для защиты лица используются щитки из органического стекла. Для восстановления водно-солевого баланса организма рабочих предусматривается обеспечение подсоленной газированной водой из расчета 4– 5 л на человека в смену.
При разработке мер защиты от тепловых излучений следует исходить из фактических величин интенсивности тепловых облучений на рабочих местах.
Для защиты от тепловых потоков металлургических печей применяют водоохлаждаемые теплоотводящие экраны. Так как водоохлаждаемые экраны располагаются на некотором расстоянии от стенки печи то тепло передаваемое излучением воспринимается водой полностью а конвективная составляющая незначительна ввиду того что горячий воздух в прослойке уносится вверх (конвекцией пренебрегаем).
Тепловой поток переданный излучением с 1м2 поверхности горячей стенки воде определяется по формуле (44):
где Ф - тепловой поток Втм2;
eпр - приведённая степень черноты;
С0 - коэффициент излучения абсолютно чёрного тела равный 567 Вт(м2×К2);
Тс - температура стенки печи К;
Тэ - температура стенки водоохлаждаемого экрана К.
Приведённая степень черноты определяется по формуле (45):
где eс и eэ - степень черноты соответственно горячей стенки и стального листа экрана.
Тогда по формуле (44) и (45) получаем:
Ф=076×567× = 9918 Втм2
Расход воды определяется по формуле (46):
G = F × Ф с×(tув - tпв ) (46)
где G - расход воды на охлаждение кгс;
F - площадь экрана м2;
с - теплоёмкость воды равная 418 × 103Дж(кг × К);
tув - температура уходящей воды (не более 35 0С);
tпв - температура поступающей воды 0С.
Тогда для экрана площадью F= 225 м2 по формуле (46):
G = 225 · 9918418×103 × (30 - 10) = 0026 кгс = 961 кгч.
5.2 Меры защиты от пылегазовых выделений
Общеобменная вентиляция в плавильном отделении обеспечивается вытяжкой через шахты на крыше. Приток воздуха направляется к рабочим местам в виде воздушных душей. Количество
приточного воздуха компенсирует вытяжку общеобменной и местной вентиляции.
Для исключения попадания в атмосферу газа и пыли предусматривается отсос газов в момент загрузки шихты в индукционную печь.
Для удаления загрязненного воздуха над местом где переливается металл из печей в раздаточные ковши предусмотрен вытяжной зонт.
Вредные газы удаляются через систему местной вытяжной вентиляции.
Для очистки отходящих газов от пыли проектируется система пылеулавливания с использованием циклонов.
При охлаждении форм также выделяются газы. Но так как охлаждение происходит на автоматической линии под кожухом то в местах входа и выхода форм из под кожуха проектируется местная вытяжная вентиляция [16].
Процесс извлечения отливок из форм сопровождается выделением пыли. Что бы локализовать эти выделения так же применяется местная вентиляция.
На участке обрубки заточки и финишных операций все вредные выделения будут удаляться через систему местной вентиляции. Каждое рабочее место должно быть изолировано в отдельные камеры.
5.3 Меры защиты от шума и вибрации
Уровни звуковой мощности оборудования в проектируемом литейном цехе приведены в таблице 35.
Таблица 35 - Уровни звукового давления оборудования в литейном цехе дБ
Уровни звукового давления в частотах октавных
Допустимые уровни звукового давления на рабочих местах
В приведенной таблице допустимые уровни звукового давления на рабочих местах для работ операторов связанных с наблюдением за агрегатами и управлением ими за пультами без речевой связи.
Для снижения уровня шума каждое шумное оборудование (например формовочная машина и т.д.) изолировано. Звукоизоляция источников шума достигается путем установки звукоизолирующих преград в виде стен перегородок кожухов кабин экранов. Уменьшается механический шум при совершенствовании технологического оборудования (амортизация ударов выбивной решетки). Рациональным путем снижения шума является использование оборудования в которых удары отсутствуют.
Предусматривается использование средств индивидуальной защиты для рабочих работающих в отделениях с повышенным шумом (отделение обрубки и зачистки шихтовое отделение при разгрузке и взвешивании шихты формовочное отделение плавильное отделение) – беруши наушники.
Так же для рабочих работающих в этих отделениях предусмотрены организационные мероприятия: сокращение времени пребывания людей в условиях с повышенным шумом лечебно-профилактические мероприятия и т.д.
5.4 Предотвращение пожаров и взрывов
Проектируемый цех относится к пожароопасному производству категории Г поэтому в потенциальных источниках взрыва устанавливаются посты и краны водоснабжения.
Посты комплектуются пожарным инструментом ящиками с песком ручными химическими огнетушителями. Расход воды в соответствии со СНиП II-31-74 и исходя из категории производства на наружное пожаротушение принимается не менее 20 лс.
В проектируемом цехе имеются источники взрыва и пожаров такие как баллоны сжатого газа аппараты работающие под давлением расплавленный металл и сети питающие природным газом плавильную печь и горелку конвейера. Для предотвращения возникновения чрезвычайных ситуаций связанных со взрывом предусматривается разработка и реализация норм и правил врывопожаробезопасности обучение персонала организация порядка хранения веществ предотвращение образования взрывоопасной среды локализация взрывов.
Предотвращения образования взрывоопасной среды при попадания воды на работающее оборудование (заливочные ковши миксер и т.д.) которое связано с расплавленным металлом обеспечивается герметизацией оборудование и контролем за техническими и технологическими процессами. Также ведется непрерывный контроль за состоянием шихтовых и формовочных материалов (песков глин и пр.) во избежание контакта воды с расплавленным металлом. Сами же рабочие которые работают с оборудованием которое может привести к пожару и взрыву должны иметь соответствующий опыт работы. Если должны работать рабочие не имеющие необходимый стаж работы с таким оборудованием то они обязательно должны быть тщательно проинструктированы мастером.
Автоматические средства пожаротушения и пожарной сигнализации на пожаровзрывоопасных участках (плавильное отделение стержневое отделение и т.д.) предполагается оснастить автоматическими установками пожаротушения и автоматической сигнализацией.
На участках цеха в качестве средств извещения о пожаре будем применять электрическую кнопочную пожарную сигнализацию или телефоны внутренней связи.
На участках где применяется оборудование с силовыми гидроприводами использующими индустриальные масла в качестве рабочей жидкости проектируются стационарные установки пожаротушения и огнетушители пожарные краны и другие установки. Типы стационарных установок и средства пожаротушения (вода пена газ или порошок) должны определяться исходя из требований технического процесса защищаемого производства.
В местах протечек масла из гидросистем оборудования должна предусматриваться установка периодически опорожняемых поддонов.
В закрытых помещениях следует устанавливать газосигнализаторы на метан регистрирующие его концентрацию в воздухе помещения до 20 % от нижнего предела воспламенения.
В местах предназначенных для хранения молотого графита необходимо предусматривать локальные автоматические установки газового тушения. Емкости для хранения молотого угля транспортные устройства и помещения для его хранения приготовления и использования должны отвечать требованиям действующих правил техники безопасности и производственной санитарии в литейном производстве.
5.5 Защита от поражения электрическим током
В проектируемом литейном цехе электрический ток используется почти во всех установках агрегатах машинах и в освещении. Уровень напряжения соответствует 380220 В.
Основная причина поражения электрическим током – неосторожность работы с оборудованием и не соблюдение правил работы с оборудованием находящимся под напряжением. Поражение током может быть через оголенные провода металлический корпус оборудования металлический пол и т.д.
Для защиты рабочих от поражения током используются следующие меры защиты:
– изоляция токоведущих частей;
– защитное заземление корпусов оборудования;
– недоступное расположение частей оборудования находящихся под напряжением;
– проведение ремонтных работ при отключенном напряжении;
– сигнализация о подаче напряжения на оборудование;
– использование индивидуальных средств защиты (прорезиненных перчаток защищенного от поражения током инструмента и т.д.).
Заземляются стойки с приборами управления корпуса электроустановок и трансформаторов. Тип заземления – стержневой трубчатый расположение вертикальных заземлителей – по контуру.
Что бы предотвратить все негативные последствия от поражения током в проектируемом цехе все люди работающие с электрическими приборами агрегатами и т.д. должны знать технику безопасности по данному оборудованию и работать только с токоизоляционным инструментом.
Таким образом все принятые меры в полном объеме обеспечивают безопасность жизнедеятельности трудящихся.
5.6 Расчет бортовых отсосов
Бортовые отсосы располагаются по длине литейной формы для удаления выделившихся газов в процессе заливки и частиц SiO2.
Количество воздуха (м3ч) удаляемого бортовыми отсосами без передувки с щелью всасывания в горизонтальной или вертикальной плоскости следует определять по формуле (47) [15]:
где BL – размеры опоки в свету м;
H- расстояние от зеркала расплава до края формы м;
kΔt- коэффициент учитывающий разность температур раствора и воздуха в помещении;
kt-коэффициент учитывающий токсичность и интенсивность выделения вредных веществ;
k1-коэффициент учитывающий тип отсоса;
k2-коэффициент учитывающий воздушные перемешивания раствора;
k3-коэффициент учитывающий укрытие зеркала раствора поплавками;
k4-коэффициент учитывающий укрытие зеркала раствора пенным слоем.
Тогда по формуле (47) объем удаляемого воздуха состовляет:
Далее выбирается вентилятор с учетом необходимого напора и производительности.
Потребная мощность (кВт) на валу электродвигателя рассчитывается по формуле (48):
где V- производительность м3ч;
в- КПД вентилятора;
6 Оценка возможности возникновения чрезвычайных ситуаций
Вероятность и последствия воздействия на человека и среду его обитания опасных и вредных факторов как природного так и техногенного происхождения резко повышается при возникновении чрезвычайных ситуаций. Вопрос о возможности возникновения чрезвычайной ситуации на данном предприятии может быть рассмотрен в двух аспектах. Во-первых предприятие и его персонал может быть объектом воздействия внешних факторов возникших в результате стихийных бедствий или по другим причинам. Последствия поражения в этом случае возрастает при наличие на объекте пожаровзрывоопасных токсичных радиоактивных материалов аппаратов и емкостей со сжиженным или сжатым газом и другого опасного оборудования (агрегаты с расплавленным металлом). Во-вторых виновником происшествий может оказаться сам персонал работающий на предприятии при несоблюдении правил пожаровзрывобезопасности и инструкций по технике безопасности.
Метод расчета вероятности возникновения пожара или взрыва в пожаровзрывоопасном объекте приведен в ГОСТ 12.1.004 - 91. Согласно этому стандарту уровень предотвращения воздействий опасных пожара на людей должен быть 0999999 а допустимый уровень воздействия опасных факторов превышающих предельно допустимые значения 10-6 на каждого человека в год. При этом учитывается вероятность возникновения взрыва во всех помещениях здания при инициирование его как в самом помещении так и в любом из расположенных в нем технологических аппаратов. В свою очередь эта вероятность связана с возможностью образования в объеме помещения или в любом объекте горючей среды то есть одновременным наличием горючего и окислителя и возможность появления источника зажигания
Вывод: Все принятые меры по защите от тепловых и электромагнитных излучений от поражения электрическим током а также мероприятия по предотвращению пожаров и взрывов в полном объеме обеспечивают безопасность жизни и здоровья трудящихся.
Разрез литейного цеха.dwg

Водоизоляционный ковёр
Подстилающий слой (бетон)
ВВЕДЕНИЕ.doc
В общей структуре машиностроительных заводов литейное производство как правило является убыточным так как полностью зависит от ценовой политики на рынке на сырьевые материалы топливо электроэнергию транспорт. В настоящее время структура себестоимости отливок такова: энергозатраты и затраты на топливо составляют 50 – 60 % затраты на исходные материалы (пески глины краски смолы шихтовые материалы и ферросплавы) – 30 – 38 % заработная плата составляет 8 - 17 %. Кроме того в связи с изменением социальной ориентации населения проблема привлечения квалифицированных трудовых ресурсов становится все более острой. Для решения всех вышеуказанных проблем строительство новых литейных цехов и реконструкция существующих должны вестись по мировым стандартам с учетом тенденций развития литейного производства. При проектировании литейных цехов необходимо предусматривать оптимальные мощности для интенсивного использования оборудования. С целью ликвидации тяжелого и вредного ручного труда освобождения рабочих от монотонных работ следует предусматривать применение промышленных роботов и манипуляторов в том числе для механизации и автоматизации отдельных операций литья. Для обеспечения высокой производительности труда следует предусматривать прогрессивные освоенные технологические процессы и высокопроизводительное автоматическое и комплексно-механизированное оборудование автоматические системы управления технологическими процессами прогрессивную организацию производства.
Кроме этого при проектировании необходимо учитывать действующие нормативные документы в строительстве правила техники безопасности и производственной санитарии пожаро- и взрывобезопасности санитарные нормы и правила технологических процессов санитарно-технические требования к оборудованию а также другие нормы инструкции и правила по проектированию.
Подмодельная плита.dwg

Отливка.DWG

Точность отливки 10-6-11-9 См. 2
ГОСТ 26645-85 Неуказанные литейные радиусы 3 мм Усадка сплава 2
ЗАКЛЮЧЕНИЕ.doc
На основе анализа номенклатуры отливок рассчитаны производственные программы всех отделений проектируемого цеха. На основе этих программ выбрано необходимое технологическое оборудования требуемой мощности. Так же произведен расчет численности персонала цеха (43чел.) и приведена схема управления проектируемым цехом.
Для контроля качества продукции предложена система контроля исходных материалов по всем переделам. Эта система позволяет проконтролировать качество изготовляемых отливок от контроля качества исходных материалов до контроля качества уже готовой отливки.
В разделе экономики производства произведен расчет фондов заработной платы (средняя зарплата производственного рабочего составляет 17000 руб. в месяц). Также подсчитаны необходимые капитальные вложения (375386 тыс. руб.) производственные фонды и амортизационные отчисления. Проведен расчет себестоимости 1 т жидкого чугуна (112967 руб.) и себестоимости 1 т отливок (229437 руб.). По итогам расчета строительства и эксплуатации проектируемого цеха методом потока наличности срок окупаемости составляет 225 года с момента начала производства и 4 года с момента начала строительства цеха.
В специальной части дипломного проекта выполнено компьютерное моделирование процесса заполнения и затвердевания отливки и на основе полученных результатов выбран наиболее оптимальный вариант получения отливки в комбинированной форме.
В разделе экология проведен меры по обеспылеванию рабочей зоны.
Рассмотрены вопросы безопасности и жизнедеятельности проведен анализ всех переделов и предложены средства защиты по охране окружающей среды и труда рабочих.
По результатам исследования моделирования отливки предложен ее способ изготовления.
Спецификация плана.spw
Установка вибрационная
Станок абразивной резки
Пневморычажный пресс
Платформенные напольные
Установка приготовления
модельного состава 652А
модельного состава 651
Нагревательная станция
Малый плавильный бак
Автомат изготовления
Полуавтомат изготовления
Стол для пайки моделей
Стол для сборки блоков
Роботизированный комплекс
Автомат приготовления
Линия обжига и заливки
Установка для приготовления
Рампа для сушки ковшей
Эл. таль на монорельсе
ЭКОЛОГИЯ.doc
Одним из простых и эффективных способов очистки промышленных газов от взвешенных частиц является мокрый способ получивший в последние годы значительное распространение в отечественной промышленности и за рубежом.
Аппараты мокрой очистки газов отличаются высокой эффективностью улавливания взвешенных частиц и небольшой стоимостью по сравнению с аппаратами сухой очистки.
Некоторые типы аппаратов мокрой очистки (турбулентные газопромыватели) могут быть применены для очистки газов от частиц размером до 01 мкм.
Аппараты мокрой очистки газов по степени очистки могут не только успешно конкурировать с такими высокоэффективными пылеуловителями как рукавные фильтры но и использоваться в тех случаях когда рукавные фильтры не могут быть применены вследствие высокой температуры повышенной влажности или взрывоопасности очищаемых газов.
В аппаратах мокрой очистки газов одновременно со взвешенными частицами можно улавливать парообразные и газообразные компоненты. К недостаткам мокрой очистки следует отнести: необходимость обработки образующихся сточных вод повышенный брызгоунос и необходимость защиты аппаратов от коррозии при обработке агрессивных сред. Несмотря на эти недостатки мокрые газоочистные аппараты с успехом применяют в химической промышленности.
Аппараты мокрой очистки часто используют в газоочистных системах для одновременного охлаждения и увлажнения газов. В этом случае газоочистные аппараты служат еще и теплообменниками смешения где охлажденный газовый поток непосредственно контактирует с охлаждающей жидкостью.
Среди аппаратов для очистки газов от пыли мокрые пылеуловители отличаются наибольшим многообразием что обусловливается силами воздействующими на газо-жидкостные потоки. При этом жидкая фаза находится в аппарате в виде пленки струи капель пены или различных сочетаний.
По принципу работы аппараты мокрой очистки газов делятся на следующие группы: полые и насадочные барботажные и пенные аппараты ударно-инерционного типа центробежного типа динамические и турбулентные промыватели.
Мокрые газоочистные аппараты ударно-инерционного типа работают по принципу инерционного осаждения частиц во время преодоления очищаемыми газами препятствия или при резком изменении направления движения газового потока над поверхностью жидкости.
Мокрый ударно-инерционный пылеуловитель представляет собой вертикальную колонну в нижней части которой находится слой жидкости. Запыленные газы со скоростью 20 мс2 направляются сверху вниз на поверхность жидкости. При резком изменении направления движения газового потока (на 180°) взвешенные частицы содержащиеся в газах проникают в воду и осаждаются в ней а очищенные газы натравляются в выходной газопровод. Пылеуловители этого типа удовлетворительно работают в случае хорошо смачивающейся пыли с размером частиц более 20 мкм. Шлам из аппарата удаляется периодически или непрерывно через гидрозатвор. Для удаления уплотненного осадка со дна применяют смывные сопла.
Ротоклон типа N является типичным представителем газопромывателей ударно-инерционного действия (рисунок 2) В аппарате установлены один или несколько изогнутых щелевых каналов нижняя часть которых затоплена жидкостью. Газовый поток ударяясь о поверхность жидкости захватывает часть жидкости и заставляет ее двигаться вдоль нижней направляющей канала. Затем жидкость отбрасывается к верхней направляющей и при выходе из щели падает в виде сплошной водяной завесы. Для предотвращения уноса капель газы после канала проходят через систему каплеотбойных устройств. Скорость газов в канале обычно не превышает 15 мс2.
– устройство для подвода газов;
– направляющие лопатки;
– устройство для вывода газов.
Рисунок 2 - Ротоклон
Среди мокрых пылеуловителей ударного действия можно выделить еще два наиболее распространенных в промышленности аппарата: статический пылеуловитель ПВМ типа ротоклон и скруббер ударного действия (скруббер Дойля).
Все из перечисленных агрегатов удовлетворяют требованиям. Но по факторам и габаритам производительности и гибкости в использовании наиболее подходящим является аппарат типа ротоклон. Поэтому в данном проекте для обеспылевания используется Ротоклон марки “Урал” производительность которого 15-20 тыс. м3ч [13].
Вывод: Система обеспылевания отсасывающих газов обеспечивает достаточно хорошую отчистку воздуха.
Форма в сборе.dwg

Задание на проект.doc
ГОСУДАРСТВЕННОЕ ОБРАЗОВАТЕЛЬНОЕ УЧРЕЖДЕНИЕ ВЫСШЕГО
ПРОФЕССИОНАЛЬНОГО ОБРАЗОВАНИЯ
(ТЕХНОЛОГИЧЕСКИЙ УНИВЕРСИТЕТ)
Факультет МТРиЭ «УТВЕРЖДАЮ»
Кафедра ТЛП Зав. кафедрой Белов В.Д.
Тема дипломного проекта Литейный цех на выпуск 25 тысяч тонн отливок в год из чугуна и стали
для стекольной промышленности
Исходные данные (в том числе проектная и технологическая документация и основная литература)
Номенклатура завода “Стекломаш”
“Проектирование новых и реконструкция действующих литейных цехов” В.П. Соловьёв С.А. Гладышев В.И. Воронцов
“Основы проектирования литейных цехов и заводов” Б.В. Кнорре
Перечень подлежащих разработке вопросов:
1.По обоснованию строительства (или реконструкции) объекта проектирования
Размещение цеха в производственном здании фирмы “Стекломаш”
2.По технике производства Технология производства стеклоформ
Производственная программа литейного цеха и его отделений выбор и расчёт основного и вспомогательного
технологического оборудования объёмно-плановые решения
3.В специальной части проекта Разработка оптимального варианта литья отливки ”Стеклоформа”
на основе компьютерного моделирования
4.По экономике и управлению производством 1.Расчет капитальных вложений в строительство
(реконструкцию модернизацию) с учетом инвестиций в общезаводское хозяйство экологические мероприятия
Расчет себестоимости жидкого металла и годного литья. 3.Оценка экономической эффективности инвестиций (капитальных вложений) с использованием метода денежных потоков.
Итоговая таблица оценки эффективности проектных решений.
Согласовано:Консультант по экономике и управлению производством
5.По безопасности жизнедеятельности
Анализ условий труда в проектируемом цехе
Санитарно-гигиеническая характеристика цеха
Разработка мероприятий по обеспечению безопасных условий труда
Согласовано:Консультант по безопасности жизнедеятельности
6.По охране окружающей среды
Разработка комплекса мер по обеспылеванию рабочей зоны
Согласовано:Консультант по охране окружающей среды
Использование ЭВМ Расчет оптимального состава шихты для выплавки чугуна для стеклоформ
Перечень графического и иллюстрированного материала (с указанием обязательных чертежей)
План и разрез литейного цеха – 2-3 листа
Технология изготовления типовой отливки – 2-3 листа
Спецчасть – 3-4 листа
Срок сдачи проекта руководителю 15 мая 2006 года
Консультанты по проекту (с указанием относящихся к ним разделов)
экономика и управление производством – проф. С.А. Гладышев
охрана труда – проф. В.А. Муравьёв
охрана окружающей среды – доц. А.В. Колтыгин
метрология и стандартизация – Т.А. Базлова
Дата выдачи задания 17 февраля 2006 года
Руководитель проекта ст. пр. Орехова А.И.
Задание принял к исполнению студент О.В. Грибков
АННОТАЦИЯ.doc
В проекте предусматривается установка современного высокопроизводительного оборудования обеспечивающего необходимые экономические и экологические характеристики литейного цеха. Также в проекте представлена технология изготовления отливки “стеклоформа”. Выполнено компьютерное моделирование процесса заполнения и затвердевания отливки.
В разделе экономика производства приводится расчёт капитальных вложений амортизационных отчислений себестоимости продукции экономической эффективности проекта точки безубыточности.
Дипломная записка изложена на 100 страницах содержит 46 таблиц 51 формулу 6 рисунков 5 приложений и список использованных источников литературы состоящий из 17 наименований.
The purpose of the given degree project is development of foundry shop on release of 2500 tons suitable castings per one year from cast iron of marks ЧС5 СЧ20 and from steel of mark 30ХНМЛ for the glass industry.
In the project installation of the modern high-efficiency equipment providing necessary economic and ecological characteristics of foundry shop is provided. Also in the project the manufacturing techniques of casting “a glass - form” are submitted. Computer modelling process of filling and hardening of casting is executed.
In section the economy of manufacture is resulted calculation of capital investments depreciation charges cost prices of production economic efficiency of the project a point of break-even.
The degree note is stated on 99 pages contains 46 tables 51 formulas 6 figure 5 appendices and the list of the used sources of the literature consisting of 17 names.
Рекомендуемые чертежи
- 24.01.2023
- 25.01.2023
- 24.01.2023
- 13.05.2023
- 01.07.2014
Свободное скачивание на сегодня
Другие проекты
- 09.07.2014