Проект цеха литья чугуна в формы из ХТС мощностью 15000 тонн в год




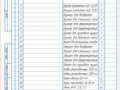
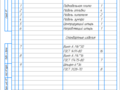
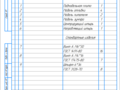
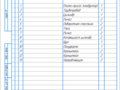
- Добавлен: 24.01.2023
- Размер: 1 MB
- Закачек: 0
Описание
Состав проекта
![]() |
![]() |
![]() |
![]() ![]() ![]() ![]() |
![]() ![]() ![]() ![]() |
![]() ![]() ![]() ![]() |
![]() ![]() ![]() ![]() |
![]() ![]() ![]() ![]() |
![]() |
![]() ![]() ![]() ![]() |
![]() |
![]() ![]() ![]() ![]() |
![]() ![]() ![]() ![]() |
![]() |
![]() |
![]() ![]() ![]() ![]() |
![]() |
![]() ![]() ![]() ![]() |
![]() ![]() ![]() ![]() |
![]() ![]() ![]() ![]() |
![]() ![]() ![]() ![]() |
![]() ![]() ![]() ![]() |
![]() |
![]() |
![]() |
![]() |
![]() ![]() ![]() ![]() |
![]() ![]() ![]() ![]() |
![]() |
![]() |
![]() ![]() ![]() ![]() |
![]() ![]() ![]() ![]() |
![]() ![]() ![]() ![]() |
![]() ![]() ![]() |
![]() |
![]() ![]() ![]() ![]() |
![]() ![]() ![]() ![]() |
![]() ![]() ![]() ![]() |
![]() ![]() ![]() ![]() |
![]() ![]() ![]() ![]() |
![]() ![]() ![]() ![]() |
![]() ![]() ![]() ![]() |
![]() ![]() ![]() ![]() |
![]() |
![]() ![]() ![]() ![]() |
![]() ![]() ![]() ![]() |
![]() ![]() ![]() ![]() |
![]() |
![]() |
![]() ![]() ![]() ![]() |
![]() |
![]() |
Дополнительная информация
Специф мод плит(7).cdw

мощностью 15000 тонн в год
модельная плита(7).cdw

мощностью 15000 тонн в год
литмод(7).cdw

мощностью 15000 тонн в год
Литейно-модельные указания на отливку
форма в сборе(7).cdw

мощностью 15000 тонн в год
Ящик стержневой(7).cdw

мощностью 15000 тонн в год
Ящик стержневой.cdw

отливки детали Муфта
Специф стер ящ.cdw

отливки детали Муфта
Специф стер ящ(7).cdw

мощностью 15000 тонн в год
Специф форма в сборе.cdw

отливки детали Муфта
Специф форма в сборе(7).cdw

мощностью 15000 тонн в год
модельная плита.cdw

отливки детали Муфта
Специф мод плит.cdw

отливки детали Муфта
форма в сборе.cdw

отливки детали Муфта
литмод.cdw

отливки детали Муфта
Литейно-модельные указания на отливку
Грузопотоки.cdw

мощностью 15000 тонн в год
-Регенерированный песок
-Очищенные отливки и литники
Разрезик.cdw

Продольный и поперечный разрезы цеха
Спец2(план).cdw

Устройство для простановки стержней
Устройство регенерации
Устройство для выбивки форм
Элеватор ковшевой ленточный
Формовочный автомат L40
Формовочный автомат L250
Транспортер ленточный
Транспортер пластинчатый
Спец1(план).cdw

мощностью 15000 тонн в год
Барабан дробеметный мод. 42322М
Бегуны катковые мод. 15101
Бункер для стального лома
Бункер для феррокремния
Бункер для ферромарганца
Бункер для чушкового чугуна
Бункер для выбитого песка
Закром для неочищенных отливок
Закром для стального лома
Закром для феррокремния
Закром для ферромарганца
Закром для чушкового чугуна
Ковш разливочный 500 кг
Ковш разливочный 200 кг
Кран мостовой Q=10 т
Стержневой автомат L5
планировочка.cdw

мощностью 15000 тонн в год
Лаборатория формовочных материалов
Инженер.doc
Государственное образовательное учреждение высшего
профессионального образования
Пермский государственный технический университет
Факультет: Механико-технологический
Направление: 651400 «Машиностроительные технологии и оборудование»
Специальность: 120300 Машины и технология литейного производства
Кафедра: Технология литейного производства
канд.техн.наук доцент
ВЫПУСКНАЯ КВАЛИФИКАЦИОННАЯ РАБОТА
ДИПЛОМИРОВАННОГО СПЕЦИАЛИСТА
ПРОЕКТ ЦЕХА ЛИТЬЯ ЧУГУНА В ФОРМЫ ИЗ ХТС МОЩНОСТЬЮ 15000 ТОНН В ГОД.
Пояснительная записка (печатная и электронная версия) – 95 с.
Доклад (электронная версия) – 1 лазерный диск.
Руководитель дипломной
на выполнение выпускной квалификационной работы
Фамилия И.О. Виноградов Михаил Алексеевич
Факультет: механико-технологический. Группа: ТЛП-03.
Начало выполнения работы: 17 марта 2008 г.
Контрольные сроки просмотра работы кафедрой: еженедельно.
Контрольная проверка работы кафедрой ТЛП: 5.05.2008 г.
Предзащита квалификационной работы: 02.06.2008 г.
Защита работы на заседании ГЭК: 18.06.2008 г.
«Цех литья чугуна в формы из ХТС мощностью 15000 тонн в год».
Исходные данные к работе: чертеж и ТУ на деталь «Муфта»; материал отливки – СЧ20; способ литья – литье в разовую форму из ХТС; тип производства – крупносерийное.
Содержание пояснительной записки:
2. Строительная часть
3. Технологическая часть
4. Специальная часть
5. Безопасность жизнедеятельности
6. Экономическая часть
Перечень графического материала:
1. План цеха 1 лист А4
2. Разрез цеха 1 лист А4
3. Грузопотоки 1 лист А4
4. Литейно-модельные указания 1 лист А4
5. Подмодельная плита с моделью отливки и элементами литниковой системы 1 лист А4.
6. Стержневой ящик 1 лист А4.
7. Форма в сборе 1 лист А4.
8. Устройство для простановки стержней 4 листа А4
Рекомендуемые библиографические источники информации
1. Ковалев Ю.Г. Проект литейного цеха. ПГТУ Пермь 1993 г.
2. Ковалев Ю.Г. Скамьянова Т.Ю. Технология изготовления отливки. Пермь Перм. гос. техн. ун-т 1995. 120с.
3. Ковалев Ю.Г. Литейная технологическая оснастка: Конспект лекций. Ч 1. Основы технологической подготовки производства. Ч 2. Технологическая оснастка для изготовления песчаных набивных форм Пермь Перм. гос. техн. ун-т. 1999. 209с.
4. Ковалев Ю.Г. Литейная технологическая оснастка: Конспект лекций. Ч 3. Технологическая оснастка для специальных способов литья. Пермь Перм. гос. техн. ун-т. 1999. 182с.
5. Ковалев Ю.Г. Расчет прибылей и литниковых систем. Пермь ППИ. 1973. 60с.
6. Лукьянов В.И. Оборудование литейных цехов. Методическое пособие. Пермь Перм. гос. техн. ун-т. 2001. 48с.
7. Скамьянова Т.Ю. Формовочные и стержневые смеси. ПГТУ-Пермь 2001.
8. Шишляев В.Н. Железоуглеродистые литейные сплавы. ПГТУ-Пермь 2002. 129с.
9. Выполнение и оформление выпускной квалификационной работы бакалавра техники и технологии. Сост. М.Н. Игнатов С.А. Белова М.С. Калашникова Л.В. Ожгихина. Перм. гос. техн. ун-т Пермь. 2005. 68с.
Требования по выполнению и оформлению работы:
Расчетно-пояснительная записка и графическая часть выполняются в соответствии с методическими указаниями [5.9.].
(дата и подпись студента)
1. Производственная программа цеха и её анализ 9
2. Режимы работы цеха и фонды времени 12
3. Выбор и расчет оборудования 12
3.1. Формовочно-заливочное отделение 12
3.2. Плавильное отделение 22
3.3. Стержневое отделение 26
3.4. Смесеприготовительное отделение 30
3.5. Очистное отделение 34
4. Складское хозяйство ..36
4.1. Склад шихтовых материалов ..37
4.2. Склад формовочных материалов 38
4.3. Склад опок и модельной оснастки .38
4.4. Склад готовой продукции 38
4.5. Кладовые цеха ..39
5. Вспомогательные участки 39
5.2. Службы механика и энергетика 39
6. Транспортная система цеха. Грузопотоки ..40
7. Энергообеспечение 41
Строительная часть 44
Технологическая часть ..47
1. Анализ технических условий на отливку 47
2. Конструирование литой заготовки 47
3. Разработка литейно-модельных указаний 49
4. Расчет литниковой системы ..50
5. Проектирование модельного комплекта ..53
6. Технологический процесс изготовления отливки 54
Специальная часть ..57
1. Описание работы устройства для простановки стержней 57
2. Расчет элементов механизма .. 57
3. Схема автоматизации .59
Безопасность жизнедеятельности . 62
2. Анализ вредных и опасных факторов .. 62
2.1. Повышенная загазованность воздуха рабочей зоны 63
2.2. Повышенная температура воздуха рабочей зоны и поверхности оборудования .64
2.3. Движущиеся машины и механизмы ..65
2.4. Повышенное значение напряжения в электрической цепи .66
3. Описание методики необходимой для оценки безопасного рабочего места по условиям труда .67
4. Анализ безопасности работающего в соответствии с условиями его труда 68
5. Оценка безопасности рабочего места 70
6. Расчет сопротивления заземляющего устройства 70
Экономическая часть .74
1. Производственный план 74
1.1. Расчет эффективного годового фонда времени 74
1.2. Расчет потребного количества оборудования и транспортных средств 74
1.4. Основной капитал 76
2. Определение состава и численности работающих предприятия 76
3. Основные технико-экономические показатели предприятия 80
3.1. Основной капитал 80
3.2. Определение затрат на производство 81
3.2.1. Затраты материальные .81
3.2.2. Затраты энергетические технологического назначения 82
3.2.3. Расчет фондов заработной платы рабочих .82
3.2.4. Расходы на содержание и эксплуатацию оборудования ..85
3.2.5. Прочие постоянные статьи затрат ..88
3.3. Оборотный капитал .89
3.4. Производственный капитал 90
4. Финансовый план 90
4.1. Расчет плановой суммы прибыли .90
4.2. Расчет чистой прибыли ..91
4.3. Формирование баланса доходов и расходов 91
4.4. Расчет безубыточного объема производства продукции 92
5. Экономические и финансовые показатели бизнеса 92
Библиографический список .94
Задачей дипломного проекта является разработка литейного цеха по изготовлению отливок из серого чугуна применительно к номенклатуре отливок 000«Завод«Синергия» мощностью 15000 тонн в год в формы из ХТС .
Для расчета производственной программы проектируемого цеха были использованы технические данные цеха аналога: 20 отливок–представителей изготовляемых из серого чугуна СЧ 20.
Проектируемый цех относится к автоматизированному цеху крупносерийного производства с последовательным режимом работы. От аналога отличается введением автоматической линии сокращением операций выполняемых ручным трудом.
При проектировании были разработаны основные отделения цеха по техническим характеристикам подобрано оборудование и определено его количество.
В технологической части проекта разработан технологический процесс изготовления отливок приготовление формовочной смеси и расплава металла изготовление стержней сортировка и контроль.
В проекте описаны вредные и опасные факторы возникающие на производстве разработаны мероприятия по обеспечению безопасных условий труда в проектируемом цехе.
В строительной части описаны конструкции производственного и административно-бытового помещений.
Экономическая часть проекта содержит расчеты: численности работающих фондов заработной платы рассчитана себестоимость одной тонны готовой продукции а также приведены технико-экономические показатели проектируемого цеха.
В специальной части разработан и спроектирован механизм простановки стержней.
Литейное производство – технологический процесс получения литой заготовки путем заливки жидкого металла в литейную форму внутренняя полость которой соответствует наружному очертанию отливки.
Литье является одним из наиболее распространенных способов получения заготовок для деталей машин. Методами литья изготавливают в среднем около 65% (по массе) заготовок деталей машин а в станкостроении массовая доля доходит до 95%. Широкое распространение литейного производства объясняется большим его преимуществом по сравнению с другими способами производства. Литьём можно получить заготовки практически любой сложности с минимальными припусками на обработку. Это очень важное преимущество так как сокращение затрат на обработку резанием снижает себестоимость изделий и уменьшает расход металла.
Развитие литейного производства протекает по двум направлениям:
расширение ассортимента применяемых природных материалов постоянное совершенствование естественных и искусственных материалов изыскание новых литейных сплавов отвечающих требованиям предъявляемых к работе отливок из этих сплавов;
создание и совершенствование новых автоматизированных линий компьютизирование оборудования которое позволило бы сократить время производства отливки.
При этом большое внимание уделяется снижению материалоемкости и трудоемкости изготовления отливок экономии топливно-энергетических ресурсов применению малоотходных и безотходных технологий которые позволят уменьшить вредное воздействие на окружающую среду и повысить качество и эффективность производства.
1. Производственная программа цеха и её анализ.
Составление производственной программы цеха начинается с определения годового выпуска каждой отливки - представителя (в т) в цехе-аналоге по номенклатуре из 20 отливок-представителей. Номенклатура отливок – представителей и их характеристика приведены в таблице 1.1
Расчет программы проведен по нижеуказанным формулам [2] полученные данные сведены в таблицу 1.2.
m = (g× n) 1000 (1.1)
где gотл – номинальный вес отливки кг;
n– годовой выпуск отливок шт.
Доля выпуска отливок-представителей каждой весовой группы в общем объеме годового выпуска этих отливок в цехе-аналоге:
где: m – годовой суммарный выпуск отливок-представителей соответствующей весовой группы в цехе-аналоге т;
m – годовой суммарный выпуск отливок-представителей в цехе-аналоге т (общий итог графы 11 таблица 1.2).
Годовой выпуск отливок-представителей в каждой группе в проектируемом цехе:
где: Р – годовое производство отливок в проектируемом цехе согласно заданию т.
Условно-приведенное производство каждой отливки-представителя в проектируемом цехе т:
Номенклатура отливок – представителей и их технологическая характеристика.
Наименование детали (отливки)
Класс точности отливки
Группа технологической сложности
Количество стержней на одну отливку шт
Количество отливок-представителей на годовую программу в цехе аналоге шт.
Годовой выпуск отливок представителей в цехе-аналоге т.
Механически обработанной детали
Номинальный вес отливки
Условно-приведенный поштучный выпуск каждой отливки-представителя в проектируемом цехе шт:
2. Режимы работы цеха и фонды времени.
Режим работы литейного цеха определяется очередностью выполнения операций технологического процесса изготовления отливки. Согласно заданию в цехе предусмотрен 2-х сменный параллельный режим работы который характеризуется одновременным выполнением технологических операций на различных производственных участках и рабочих местах.
В соответствии с принятым режимом работы для каждого отделения устанавливаем действительные фонды времени работы рабочих оборудования и рабочих мест (без оборудования). [2 табл.7]
Формовочное отделение = 3935 ч.
Плавильное отделение = 3975 ч.
Стержневое отделение = 3935 ч.
Очистное отделение = 3935 ч.
3. Выбор и расчет оборудования.
3.1. Формовочно-заливочное отделение.
Проектирование литейного цеха начинаем с формовочно-заливочного отделения – центрального звена в технологической цепи изготовления отливок.
При проектировании этого отделения как впрочем и других сначала выбираю технологические процессы устанавливаются их характеристики в соответствии с которыми подбирается основное оборудование.
Производственная программа формовочного передела.
На основе производственной программы цеха составляется подетальная ведомость (табл. 1.3). В таблице отмечается тип формы: сырая или сухая. По габаритам отливок с учетом их положения при формовке размеров стержневых знаков прибылей технологических приливов и т.д. определяются основные габариты моделей. При выборе размера опок учитываются расстояния между моделями и другими элементами формы [2 таб. 9].
Брак отливок БР (от) относят к общему выпуску отливок (в вес. %) в каждой технологической группе. Штучный брак БР (шт) для каждой отливки-представителя определяется по соотношению:
где: Бр (от) принимаем равным 4%.
На количество забракованных отливок увеличивается их общее производимое количество (в весе и поштучно) и в соответствии с этим а также с учетом непосредственного брака форм БР (ф) равного 2-3 % от числа
годных форм определяется их годовое производство Nф для каждой технологической (весовой) группы.
Годовое производство форм для каждой технологической (весовой) группы определяется по формуле (см. таб. 1.3):
Nф = (гр. 6 : гр. 9) + БР(ф) (1.6)
Расчет количества основного оборудования.
В качестве основного оборудования выбираю две формовочные линии на основе формовочного пескострельных автоматов L250 и L40 (Приложение В).
Производительность всей линии определяется производительностью формовочного автомата.
Определяем расчетное количество формовочного оборудования исходя из годовой программы производства отливок и машинного цикла формовочных автоматов.
Формовочная линия №1 на базе автомата L250
Характеристика формовочного автомата L250:
Размеры опок в свету мм 1000×800
Расход воздуха м3 ч 18
Габаритные размеры машины мм 6000*5000*3000
Количество форм на годовую программу = 142686 шт.
Действительный фонд времени для формовочного отделения = 3935 ч.
Количество форм в час = 1426863935 = 363 фч
Машинный цикл составляет 60с или 60 фч
Затем определяется коэффициент загрузки оборудования:
где: N – необходимое количество форм в час.;
N – машинный цикл форм в час шт.
Автоматическая линия оснащенная технологическим оборудованием которое обеспечивает весь процесс получения отливок – от изготовления форм до извлечения отливок из них представляет собой замкнутую цепь тележек с платформами.
Определяем скорость линии (ммин) [2]:
Где: Nф - годовое количество форм поступающее с формовочных машин конвейерной линии шт.;
– годовой действительный фонд времени формовочного оборудования ч;
Z – число форм на платформе шт.;
к – коэффициент заполнения тележек формами равный 08 - 09;
а – шаг тележки конвейера – расстояние между осями сцепления тележек м.
Длина конвейера [2]:
Lф - длина участка формовки м;
Lсб - длина участка сборки и загрузки форм м;
Lз - длина участка заливки форм м;
Lохл - длина участка охлаждения отливок м;
Lв - длина участка выбивки форм м;
Определяем длину участка формовки [2]:
Принимаем конструктивно учитывая размеры формовочного автомата
Определяем длину участка сборки [2]:
Принимаем примерно равной длине участка формовки
Определяем длину участка заливки:
где: nк – количество ковшей одновременно задействованных на заливочном участке конвейера для заливки форм шт;
к – время разливки (мин) определяем по таблице [2 табл.13]:
Для заливки форм выбираем автоматизированный заливочный ковш емкостью 500 кг.
Определяем длину участка охлаждения:
где: tохл – время охлаждения отливок в форме до ее выбивки мин; tохл= 21 ч [2 стр. 221].
Для недопущения загазованности атмосферы цеха выделяющимися из форм с охлаждающимися отливками газами участок охлаждения отливок перекрывают кожухом оснащенным принудительным нагнетателем холодного воздуха и вытяжной вентиляцией.
Определяем длину участка выбивки форм.
Длина участка выбивки сравнительно невелика и в зависимости от схем выбивки составляет 8 – 12 м.
Выбивной цикл состоит из следующих операций:
Сталкивание формы на выбивную решетку или в агрегат выдавливания «кома» с отливкой;
Отделение отливки от формовочной смеси;
Транспортировки пустых опок к месту формовки;
Транспортировка отливок в очистное отделение;
Перед попаданием «кома» с отливкой на выбивную решетку форма проходит через механизм выдавливания. Пустые опоки поступают на распаровщик и далее на участок формовки. Отливки проходя по решетке попадают на конвейер и направляются на участок обрубки. Смесь уходит в подвальное помещение на регенерацию.
При использовании конвейерных линий количество пар опок определяется по формуле:
где: Nф – годовое количество форм шт;
Фд – действительный годовой фонд времени для формовочного оборудования ч;
- принятая скорость конвейера ммин;
Коп(р) – коэффициент учитывающий резерв опок Коп(р) = 12 ÷ 13;
- коэффициент заполнения тележек конвейера формами = 085÷090;
Lк – длина конвейера м.
Формовочная линия №2 на базе автомата L40
Характеристика формовочного автомата L40:
Размеры опок в свету мм 500×400
Расход воздуха м3 ч 15
Габаритные размеры машины мм 4000*3390*2420
Количество форм на годовую программу = 334299 шт.
Количество форм в час = 3342993935 = 85 фч
Машинный цикл составляет 28с или 128 фч
Для заливки форм выбираем автоматизированный заливочный ковш емкостью 200 кг.
где: tохл – время охлаждения отливок в форме до ее выбивки мин; tохл= 05 ч [2 стр. 221].
3.2. Плавильное отделение.
Определение потребности в жидком металле и количество плавильных агрегатов.
Основой для проектирования плавильного отделения является потребность в жидком металле для выполнения производственной программы цеха. Это определяется по весовым группам отливок по маркам сплавов и цеху в целом в соответствии с весовыми характеристиками отливок (таб. 1.4). Общий расход жидкого металла превышает чистый расход на отливку т.к. металл расходуется также на литники прибыли выпора сливы и всплески.
Отношение веса готовой отливки к общему расходу металла на неё характеризует технологический выход годного (ТВГ) который определяется для каждой отливки в весовых группах.
Расход жидкого металла на каждую отливку определяется отношением:
где: gот – номинальный вес отливки кг;
ТВГ – технологический выход годного для отливки ТВГ = 70 % [6 табл.4.70].
Количество жидкого металла потребное на годовое производство каждой из отливок т:
Средняя металлоемкость определяется по формуле:
где: nф(1) nф(2) nф(
Nф – годовое количество изготовляемых форм шт.
На основании полученных результатов составляется баланс металла (таблица 1.5).
Статьи баланса металла
Литники прибыли выпоры
Возвратные потери(сплески)
Итого жидкого металла
Безвозвратные потери (угар)
Выход годного от металлозавалки
Индукционная печь промышленной частоты (ИЧТ – индукционная печь для чугуна) имеет по сравнению с другими печами ряд преимуществ:
можно получить чугун практически из любой шихты;
меньше загрязняет окружающую среду;
позволяет производить доводку жидкого чугуна как по температуре так и по химическому составу во время плавки;
достаточно высокий КПД.
Определяем часовую потребность цеха в жидком металле [3]:
где: Q – часовая производительность плавильного отделения тч;
Вг – потребное годовое количество сплава для цеха или участка тгод;
Кн – коэффициент неравномерности потребления металла Кн = 105 [3 стр. 88] ;
Фд – действительный годовой фонд времени работы печи Фд = 3975 ч [2 табл.7].
На основании расчета выбираем индукционную тигельную печь ИЧТ-2517:
емкость тигля – 25 т;
производительность – 14 тч;
продолжительность плавки – 18 ч;
Определяем количество печей на годовую программу:
где: Qж – потребное количество жидкого металла тг;
q – производительность печи тч;
Коэффициент загрузки плавильных агрегатов [2]:
где: nр – количество плавильных агрегатов по расчету шт;
nп – количество принятых плавильных агрегатов шт.
Расчет потребности в шихтовых материалах.
В балансе металла установлено необходимое общее количество шихты. Составляется сводная ведомость потребности в шихтовых материалах (таблица 1.6).
Ведомость шихтовых материалов
Чугун чушковый марки: ПЛ1 ГОСТ 805-80
Возврат собственного производства
Ферросилиций марки: ФС75 ГОСТ 1415-78
Ферромарганец марки: ФМн75 ГОСТ 4755-91
3.3 Стержневое отделение.
Стержневое отделение предназначено для изготовления стержней. Из этого отделения на сборку поступают стержни. Особенностью стержневого отделения является по существу локальный (вне зависимости от формовочного цикла) цикл производства конечного продукта – стержней. Вместе с тем работа этого отделения и выбор тех. процессов изготовления стержней зависит от характера производства литейного цеха и принятой технологии изготовления отливок из чугуна.
Выбор технологических процессов и оборудования для изготовления стержней.
Особенностью изготовления стержней из ХТС является упрочнение их кратковременной продувкой СО2. Стержни обладают высокой прочностью легко удаляются из отливок при выбивке их из форм. Их часто применяют в крупносерийном производстве чугунных отливок массой до 500 кг. Для получения стержней используются в основном металлические ящики. Стержни изготавливаются на пескодувной машине из ХТС по CO2- RESOL процессу. Упрочняются стержни продувкой СО2 в течение 30 секунд.
В стержневом отделении выполняются следующие операции:
изготовление стержней;
контроль стержней (приемка первой годной в начале каждой смены).
Набор технологических операций зависит от выбранного техпроцесса и размеров стержней. Стержневое отделение представляет собой два стержневых автомата L5. (Приложение В)
Проектирование стержневого отделения:
Составляется ведомость номенклатуры стержней (таблица 1.7)
Рассчитывается количество основного технологического оборудования.
Средний объем стержня:
где: n1 n2 ni – годовое количество изготовляемых стержней согласно производственной программе стержневого отделения шт.
Vcт(1) Vст(2) Vcт(i) – объем стержней соответствующих номеров м3.
где: Gcт – вес стержня кг;
gст – кажущаяся плотность стержня gст = 155 тм3 [2 стр. 113].
Для последующих расчетов выбираем пескодувную однопозиционную стержневую машину с продувкой СО2 модель L5.
Наибольший объем стержня 5 дм3;
Наибольший размер стержневого ящика 180355*350*400 мм;
Габаритные размеры 1800×1870×2030 мм.
Производительность 360 съемовчас;
Потребное количество стержневых машин определяется по формуле:
где: Nст – количество съемов на годовую программу шт;
Фд – действительный годовой фонд времени для стержневого оборудования Фд = 3935 ч;
Кн – коэффициент неравномерности стержневой машины Кн = 12 [2 табл. 10];
Кпр – коэффициент производительности Кпр = 08 [2 табл. 33];
gст – паспортная производительность стержневой машины съемы час.
Принимаем количество стержневых машин 2 штуки.
Определяем коэффициент загрузки оборудования для изготовления стержней:
3.4. Смесеприготовительное отделение.
Смесеприготовительное отделение создается для приготовления формовочных и стержневых смесей.
В данном проекте формы и стержни изготавливаются из единой ХТС.
Подготовка оборотных смесей.
Особенностью литейных цехов в которых применяются ХТС является постоянное повторное использование значительных количеств оборотной смеси. Образуется «круговой цикл» смесей который начинается при смесеприготовлении затем смесь проходит через выбивку форм цикл замыкается в местах складирования (в бункерах над смесителями). Так как формовочные и стержневые смеси имеют одинаковый состав они регенерируются вместе и потом распределяются по автоматам
В общем объеме формовочных смесей отработанные смеси составляют наибольшую долю. От их качества в значительной мере зависят свойства смесей. Это требует значительной подготовки отработанных смесей к повторному использованию. Главная цель подготовки отработанных (оборотных) ХТС – удаление с зерен песка пленки связующего. Такая подготовка необходима для поддержания постоянных свойств готовых смесей в которых основным компонентом является отработанная смесь и для упрощения процесса смесеприготовления.
Все операции подготовки отработанных ХТС осуществляются в машинах и механизмах непрерывного действия связанных между собой транспортными средствами (ленточными транспортерами и элеваторами); у железоотделителей и сит предусматриваются устройства для уборки металлоотходов и отсева.
В данном дипломном проекте регенерация происходит за счет выжигания пленки связующего в установке сушки песка в пневмопотоке.
Программа смесеприготовительного отделения составляется на основе номенклатуры выбранных составов смесей (таб. 1.8).
Состав и свойства формовочных и стержневых смесей
Составляющие смеси вес. %
Основные свойства смесей
Регенерированный кварцевый песок
(Полифенолятная смола ФСМ-Б)
Газопроницаемость ед.
Предел прочности МПа
Расчет количества регенерированной смеси.
Количество оборотной смеси после выбивки отливок на выбивной решетке: [2 стр.118]
где Qф.см – годовое количество формовочной смеси для производства формт
Qст.см – годовое количество стержневых смесей для производства стержней т
k1 – коэффициент учитывающий потери готовых смесей при транспортировке 004
k2 – коэффициент учитывающий долю стержневых смесей при их выбивке для ХТС=1
Возможное количество оборотных смесей для использования в формовочном цикле:
где k3 k4 k5 – коэффициенты учитывающие безвозвратные потери смесей в вентиляционной системе при транспортировке оборотных смесей и при их просеве соответственно; k3=002-004; k4=002-003; k5=003-004.
Средний выход регенерированного песка равен075-080 от общего объема оборотных смесей поступающих на регенерацию = 98897 т.
3.5. Очистное отделение.
Отделение литниково-питающих систем от отливок.
Хрупкость чугуна позволяет отделять литники и выпоры таких отливок в дробеметном барабане.
Литье после выбивки и охлаждения поступает в очистное отделение по пластинчатому конвейеру. Сначала литье попадает в дробеметный барабан непрерывного действия модели 42322М.
Характеристики дробеметного барабана модели 42322М
Наибольшая масса очищаемой отливки – 35 кг
Производительность по чугуну – 70 тч
Габаритные размеры мм – 7600*4500*7100
Из барабана отливки поступают на сортировочный стол. Далее детали укладывают в тару и отправляют на склад готовой продукции.
Вспомогательное технологическое оборудование играет существенную роль в организационно-технологическом построении обрубного процесса. К этому оборудованию следует отнести устройства обеспечивающие ритмичную и производительную работу основного технологического оборудования: загрузочно-разгрузочные механизмы транспортные устройства рабочих мест тару позволяющую осуществлять промежуточное межоперационное хранение отливок и их транспортировку от одной технологической операции к другой.
Всё оборудование должно размещаться согласно принятой последовательности технологических операций. Это обеспечивает наилучшую организацию труда и соблюдение правил техники безопасности и охраны труда.
Расчет основного технологического оборудования.
Потребное количество очистных агрегатов:
где: Фд – действительный годовой фонд времени для очистного оборудования Фд =3935 ч;
Кн – коэффициент неравномерности Кн = 12;
Кпр – коэффициент производительности Кпр = 06;
gоч – паспортная производительность данного вида очистного оборудования тч;
Gотл – количество отливок в год проходящее обработку в данном виде оборудования т.
Принимаем количество очистного оборудования 2 шт.
Определяем коэффициент загрузки очистного оборудования:
Компоновка оборудования и площади обрубного отделения.
Очистное отделение обычно располагают непосредственно в литейных цехах в самостоятельных пролетах. Их желательно размещать вблизи формовочно-заливочного отделения. В связи с выделением большого количества пыли и шума обрубное отделение следует отделять от соседних отделений глухими стенами.
Площади обрубного отделения определяются в зависимости от компоновки технологического оборудования при соблюдении норм его расстановки планировки рабочих мест и установки транспортных средств.
4. Складское хозяйство.
Характерной особенностью литейного цеха является потребление большого количества различных материалов. Это требует организации развитого механизированного складского хозяйства где наряду с хранением материалов производится их подготовка к использованию.
В литейных цехах должны быть склады шихтовых и формовочных материалов опок модельной оснастки готовой продукции и др.
Исходной базой для проектирования складов служат расходы шихтовых материалов определенные в соответствии с производственной программой. При расчете площадей складов компоновке хранилищ оборудования учитываются сроки хранения материалов режим работы фонды времени организационно-технологические особенности проектируемого цеха.
4.1. Склад шихтовых материалов.
Согласно предварительно выполненным расчетам составляется ведомость количества хранимых на складе шихтовых материалов флюсов и огнеупоров (табл. 1.11).
Площадь закромов (площадок) для хранения отдельных материалов:
где: Gм – годовая потребность в материале т;
n – норма хранения материала дни [2 табл. 45];
Фн – номинальный фонд времени дни;
γм – насыпной вес материала тм³;
Н – допустимая высота хранения материала м [2 табл. 45].
Материалы должны храниться строго по маркам и сортам. Кусковые и сыпучие материалы – в бочках ящиках контейнерах мешках навалом в закромах или на площадках; огнеупоры – на площадках в укладке.
Количество хранимых на складе шихтовых материалов и огнеупоров.
Наименование материала
Потребное годовое количество
Расчетная площадь м²
Возврат литейного цеха
4.2. Склад формовочных материалов.
Согласно предварительно выполненным расчетам составляется ведомость хранимых формовочных материалов (табл. 1.12).
Ведомость хранимых материалов на складе формовочных материалов.
Потребное годовое количество т
Склад имеет участки приема и хранения материалов.
4.3. Склад опок и модельной оснастки.
Как правило основные склады опок и модельной оснастки размещают вне литейного цеха а в цехе складирование опок и модельной оснастки производится в непосредственной близости от рабочих мест на свободном месте.
4.4. Склад готовой продукции
Склад готовой продукции является конечным участком цеха и входит как правило в состав очистного отделения.
Площадь склада рассчитывается по формуле:
где: Gотл – годовое количество отливок выпускаемое цехом т;
Кп - коэффициент учитывающий проходы Кп = 13;
– коэффициент учитывающий использование полезной площади 06;
Фд –действительный годовой фонд времени ч;
t – допустимое время хранения отливок на складе (18 .24 ч);
g – удельная нагрузка на пол склада g = 075 тм².
Склады опок модельной оснастки готовой продукции оборудуются подъемными и транспортными средствами стеллажами унифицированной тарой и т.п.
В цехе предусматривается кладовая запасных частей.
Кладовые запасных частей участков механика и энергетика занимают площадь 10-20% от площади соответствующего участка. Площадь инструментальной кладовой составляет 5–8 % от суммарной площади участков механика и ремонта оснастки.
Кладовые ЛВЖ и ГЖ для цеха мощностью 15000 тгод имеют площадь 50м2. [2 стр. 142]
5. Вспомогательные участки.
В литейном цехе предусматривается лаборатория формовочных материалов располагаемую вблизи смесеприготовительного отделения и лабораторию химического анализа металлов размещаемую вблизи плавильного отделения.
Площади цеховых лабораторий м2.
Мощность цеха тыс.тгод
Лаборатория формовочных материалов м²
Лаборатория химического анализа металлов м²
5.2. Службы механика и энергетика.
Службы механика и энергетика выполняют профилактику и ремонт оборудования.
Площадь участка механика определяется исходя из номенклатуры проводимых на участке работ количества и норм расстановки механообрабатывающего и вспомогательного оборудования.
Площадь участка механика принимается из расчета норм установки оборудования: для мелких станков 5 - 9 м² средних 10 - 16 м² крупных 18 - 60 м²; площадь слесарного участка определяется из расчета 8 - 10 м² на каждого слесаря; площадь для осмотра технологического оборудования демонтированного для ремонта составляет 20% от площади участка механика. В итоге участок механика должен занимать ориентировочно площадь в цехах мощностью до 15000 тгод – 85–100 м2. [2 стр. 151]
Площадь участка энергетика для цеха мощностью до 15000 тгод равна 65-90 м2.
6. Транспортная система цеха. Грузопотоки.
Для литейных цехов характерно многократное перемещение большого количества насыпных и штучных грузов поэтому при их проектировании транспортной системе необходимо уделить большое внимание поставив цель механизировать и где возможно автоматизировать транспортные операции.
В литейных цехах используется напольный и надпольный транспорт. Рациональное применение этих видов транспорта позволяет оптимально организовать грузопотоки. Следует стремиться к созданию грузопотоков с наименьшим числом пересечений причем в узлах пересечений транспортировка груза должна вестись на разных уровнях.
Компоновку оборудования проектирование транспортных межоперационных связей и связей между отделениями нужно вести с учетом требований к грузопотокам и соответственного выбора рациональных транспортных средств.
На шихтовой склад металлическая шихта привозится жд транспортом или автотранспортом и выгружается с помощью мостового крана. Шихта после дозирования транспортируется по рельсовым путям на место подогрева шихты. После подогрева мостовым краном шихту распределяют по печам. Готовый металл разливается по ковшам движущимся по монорельсу. Свежий формовочный песок пневмотранспортом подается в бункера над смесителями которые находятся на формовочных и стержневых автоматах. Связующее поступает по трубопроводу непосредственно в смесители автоматов.
После выбивки отливок отработанная смесь по транспортеру поступает в бункер при помощи ковшевого элеватора. Из бункера оборотная смесь по питателям попадает в установку регенерации песка(выжигание связующего в пневмопотоке). Регенерированный песок пневмотранспортом доставляется в бункера над смесителями автоматов.
Отработанный песок не подлежащий регенерации пневмотранспортом доставляется в бункер находящийся за пределами помещения.
Выбитые отливки по транспортеру попадают в дробеметный барабан. После очистки по транспортеру отливки и литники попадают на сортировочный стол где отделяют готовые отливки от брака и литников.
Доставка отходов металла от сортировочных столов осуществляется с помощью электропогрузчика в бадьях. Готовые отливки упаковывают в тару и увозятся электропогрузчиком на склад готовой продукции.
Схема грузопотоков представлена на чертеже ДП 03.03.08.
7. Энергообеспечение.
Расчет потребности в энергии по видам ведется по удельным нормам расхода которые можно принять по данным цеха-аналога.
Расход электроэнергии складывается из расходов на технологические нужды Wт силовой привод Wс и освещение Wос.
Общий расход электроэнергии по цеху [2 стр. 153]:
W = Кw(Wт + Wc + Wос) (1.33)
где: Кw – коэффициент потери электроэнергии в цепи Кw = 105 - 110.
Расход электроэнергии на технологические нужды:
где: Рт – удельный расход электроэнергии на данном переделе на 1 т годных отливок при плавке чугуна в индукционных печах тигельного типа 1200 - 1400 кВтчт;
Gотл – годовой выпуск годных отливок т
Wт = 1400 15000 = 21000000 кВт
Расход электроэнергии на силовой электропривод:
Wс = Рс Фд Gотл (1.35)
где: Рс – установленная мощность оборудования на 1 т годных отливок в год Рс = 009 - 010 кВт;
Фд – действительный годовой фонд времени ч;
Wс = 01 3935 15000 = 5902500 кВт
Расход электроэнергии на освещение:
Wос = ρ Fос Фд(ос) (1.36)
где: ρ – средний расход электроэнергии за 1 час на 1 м² площади (для производственных помещений 0015 кВт; для складов и бытовых помещений 0008 кВт);
Fос - освещаемая площадь м²;
Фд(ос) – годовое количество часов осветительной нагрузки (при двухсменной работе 2300-2500 ч).
Wос = 0015 4668 2500 + 0008 2376 2500 = 1798020 кВт
W = 11 (21000000 + 5902500 + 1798020) = 31570572 кВт
Сжатый воздух необходим для работы формовочных и стержневых машин и т.д.: [2 стр. 158]
Qс.в. = 15 gс.в. Gотл (1.37)
где: gс.в. – удельный расход сжатого воздуха на 1 т годных отливок gс.в. = 900 ÷ 1100 м3;
Gотл – годовой выпуск отливок в цехе т.
Qс.в. = 15 1000 15000 = 22500000 м³
Расход воды на технологические нужды: [2 стр. 159]
где: gв – удельный расход воды 1 т годных отливок gв = 158 ÷ 210 м³.
Qв = 200 15000 = 3000000 м³
Вода для бытовых нужд = 68698 м3
В строительной части проекта выбираются и обосновываются габариты и взаимное расположение пролетов здания литейного цеха в зависимости от необходимых производственных и других площадей в первую очередь определенных расчетами технологических отделений цеха участков складов и др. с учетом норм размещения технологического и вспомогательного оборудования и его габаритов. Затем выбираются основные строительные конструкции (колонны фермы перекрытия и др.). Компоновочные решения должны отвечать требованиям безопасных и комфортных условий работы в цехе а также обеспечивать быструю эвакуацию работающих в экстренных случаях (пожар сигнал гражданской обороны и др.).
1. Общая характеристика зданий.
В практике строительства литейных цехов наиболее распространены одноэтажные здания пролетного типа из типовых строительных конструкций.
После определения состава цеха разработана его технологическая схема т.е. взаимное размещение производственных вспомогательных отделений и участков. Составление этой схемы связано с выбором взаимного расположения пролетов и их размеров. При этом учитываются особенности транспортных связей между отделениями и участками.
Здание литейного цеха спроектировано в каркасном исполнении выполнено из железобетонных и металлических элементов. Несущей частью каркаса здания являются колонны опирающиеся на фундаменты. Расстояния между колоннами 6 12м ширина пролетов составляет 18 м.
Высотой здания считается расстояние от уровня пола до низа конструкции перекрытия и составляет 18 м.
При компоновке здания и его пролетов учтены температурные колебания их размеров. В связи с этим установлены размеры типовых секций промышленных зданий разъединяемых между собой температурными швами.
Фундаменты под колонны зданий выполнены из монолитного бетона. Размеры фундаментов принимают в зависимости от действующих на них нагрузок наличия рядом с ними подвалов или фундаментов под оборудование гидрогеологических условий строительной площадки. Глубину заложения фундамента устанавливают в зависимости от свойств грунтов их промерзания и уровня грунтовых вод.
Несущие колонны предназначены для крепления самонесущих и навесных торцевых стен имеют нижнюю консоль на внешней стороне колонны для опирания фахверковых балок.
Подкрановые балки предназначены для опирания крановых рельсов.
Фермы и балки перекрытий относящиеся к плоским несущим конструкциям могут быть железобетонными или металлическими.
Плиты перекрытия кладутся на балки перекрытия или фермы на которые они опираются своими концами.
Плиты керамзитовые и из ячеистого бетона эффективны: они совмещают функции настила утеплителя и обеспечивают жесткость зданию.
Кровля обычно делается утепленной из рулонных материалов и мастик. В состав примерного покрытия входят: слой рубероида по плитам перекрытия затем слой утеплителя состоящий из пенобетона или керамзитобетона толщиной от 60 до 200 мм который стягивается цементной стяжкой толщиной 20-30 мм затем кладется до трех слоев пергамина уложенных на битумную мастику и один слой рубероида.
Гардеробные предназначены для переодевания работающих в цехе и хранения их одежды. Они оборудованы металлическими шкафами с двумя секциями. Шкафы оборудуются скамьями. Предусмотрен резерв шкафов 15%. Душевые размещаются в отдельных помещениях смежных с гардеробными.
Умывальники размещаются в отдельном помещении смежном с гардеробными. Умывальники также устанавливаются в тамбурах и туалетах. Умывальники закрепляются на стенах облицованных глазурованной плиткой. Санузлы оборудуются кабинами. Двери кабин открываются наружу. Кабины оснащаются унитазами.
Административно-конторские помещения – это совокупность комнат для размещения руководящего состава цеха технологического отдела планово-распределительного бюро бухгалтерии.
Комнаты отдыха. Количество посадочных мест в этих помещениях равно числу работающих в наиболее многочисленной смене.
В площадь административно-бытового корпуса входят площади коридоров лестниц которые ориентировочно составляют 25% при ширине коридора 3 м от суммарной площади занятой всеми служебно-бытовыми помещениями.
Планировка и разрезы цеха представлены на чертежах ДП 03.01.08 и ДП 03.02.08.
Технологическая часть.
1. Анализ технических условий на отливку.
Отливка «Муфта» изготавливается из серого чугуна СЧ 20 имеет внутреннюю полость которая выполняется песчаным стержнем.
Химический состав и механические свойства серого чугуна ГОСТ 1412 – 85
Содержание элементов % (остальное железо)
Механические свойства
Рассмотрим влияние химических элементов на структуру и свойства чугуна.
С – в наибольшей степени способствует графитизации чугуна понижает прочность повышает пластичность улучшает литейные свойства.
Si – способствует графитизации чугуна укрупняет графитовые включения повышает механические свойства улучшает литейные свойства.
Mn – нейтрализует вредное влияние серы тормозит процесс графитизации повышает склонность к отбелу устойчивость аустенита дисперсность перлита прочность ухудшает литейные свойства.
S – сильно тормозит графитизацию способствует образованию горячих трещин понижает механические и литейные свойства.
Р – в небольшой степени способствует процессу графитизации повышает прочность твёрдость износостойкость жидкотекучесть понижает ударную вязкость и хладостойкость.
Сплав СЧ 20 обладает хорошими литейными свойствами необходимой прочностью хорошей обрабатываемостью резанием малой склонностью к образованию трещин достаточной износостойкостью.
2. Конструирование литой заготовки.
Чертёж отливки разрабатывается по чертежу детали в соответствии с требованиями ГОСТ 2.423 - 73 и включают следующие вопросы:
выбор положения отливки в форме что определяет способ формовки; плоскость разъёма формы;
назначение припусков на механическую обработку;
формовочные уклоны и галтели на отливках;
неуказанные литейные радиусы;
выбор классов точности и шероховатости.
С целью обеспечения направленного затвердевания исключающее образование усадочных раковин в отливке данную отливку располагаем в одной полуформе.
Припуски на механическую обработку отливки назначают с целью получения заданных размеров и шероховатости поверхности детали в соответствии с чертежом. Размер припусков берется в зависимости от вида сплава габаритов детали от допусков размеров отливки класса точности типа производства положения отливки в форме в соответствии с ГОСТ 26645-85. Отливка «Муфта» изготавливается из чугунного сплава СЧ-20 согласно ГОСТ 26645-85 имеет 10 класс точности и размер припуска 5 мм.
При разработке модели учитывается усадка металла отливки. Для отливки «Муфта» изготовленной из серого чугуна объёмная усадка берётся в размере 07-13 % литейная усадка 11 %.
Чтобы избежать образования трещин и снизить внутренние напряжения в местах переходов от толстых стенок к более тонким предусматривают галтели. Радиусы галтелей зависят от толщины сопрягаемых стенок для отливки «Муфта» литейные радиусы составляют 3 мм.
Отливку изготавливают по 10 классу точности поэтому величина формовочного уклона составляет 1о.
Параметры шероховатости поверхности установленные ГОСТ 2789-73 определяем исходя из способа получения отливки сплава и размеров отливки Ra 125.
3. Разработка литейно-модельных указаний.
При разработке метода заливки решают следующие вопросы:
выбор способа формовки;
выбор разъёма формы;
определение мест установки границ и количества стержней в форме;
выбор литниковой системы;
определение габаритных размеров опок метод центрирования выбор вентиляции формы;
выбор способа сборки форм при заливке.
Способ формовки определяется конфигурацией и габаритами отливки типом производства и положения отливки в форме. При данных габаритах отливки и типе производства принимаем машинную формовку по неразъемной модели. Данную отливку лучше расположить в форме вертикально при этом неразъёмная модель отливки будет располагаться в нижней полуформе. В форме будет изготовлено четыре отливки. На основании выбранного положения и количества отливок в форме определяется размер формы.
Разъём формы должен обеспечить свободный выход воздуха и газа из стержня и углублений. Выбранный разъём формы должен обеспечить наименьшее количество дефектов по перекосам а также минимальную протяжённость литейных швов по поверхности отливки и соответственно заливов.
Выбор границ количества и мест установки стержней производится в зависимости от конфигурации внутренней полости отливки и её габаритов. Для получения отливки «Муфта» достаточно одного стержня выполняющего центральное отверстие. Стержень имеет знаки с помощью которых стержень устанавливают в литейную форму и фиксируют в заданном положении. Параметры знака стержня определяют согласно ГОСТ 3212 – 92.
Выбор литниковой системы зависит от конфигурации отливки вида сплава габаритов количества и расположения отливки в форме.
Для чугунных отливок применяют сужающиеся литниковые системы которые обеспечивают спокойную заливку формы и задержание шлака.
Так как отливка невысокая для нее применима горизонтальная литниковая система с подводом металла по плоскости разъёма. Шлакоуловитель и питатели расположены в форме горизонтально. Чтобы обеспечить отделение неметаллических включений и исключить попадание шлака в отливку питатели располагаем в нижней полуформе. Такая система обеспечивает поступление расплава через питатель постепенно и без разбрызгивания.
Вентиляция формы осуществляется через каналы литниковой системы через газоотводные каналы в стержнях через форму.
Размеры опок выбирают в зависимости от размеров моделей количество их на модельной плите массы жидкого металла толщины стенки отливки конструкции и размеров литниковой системы. При выборе размеров опок исходят из максимального использования их объёма.
Для сборки формы используем штыри и гайки.
4. Расчёт литниковой системы.
Конструкция литниковой системы зависит от сплава размеров и конфигурации отливки. Для чугунных отливок применяют обычно заполненные литниковые системы обеспечивающие спокойную заливку формы и задержание шлака.
Т.к. отливка невысокая для нее применима горизонтальная литниковая система с подводом металла по плоскости разъёма. Чтобы обеспечить отделение неметаллических включений и исключить попадание шлака в отливку питатели располагаем в нижней полуформе. Такая система обеспечивает поступление расплава через питатель постепенно и без разбрызгивания.
Сначала определяем суммарное сечение питателей по формуле Озанна Диттера:
где: G – масса отливки литниковой системы и прибыли кг;
- общий коэффициент расхода литниковых систем для среднебоковой литниковой системы со средним сопротивлением формы принимаем ;
- время заливки сек;
- плотность жидкого металла для чугунного сплава СЧ 20
g – ускорение свободного падения g = 980 мс2;
Hср – среднедействующий металлостатический напор см;
По формуле А.Ф. Соболева Т.М. Дубицкого определяем время заполнения формы:
где: S1 – эмпирический коэффициент учитывающий технологические условия заполнения формы для горизонтальной литниковой системы и чугунного сплава S = 2;
- толщина стенки (средняя) мм;
G – вес отливки с литниковой системой кг;
n – количество отливок получаемых в форме шт.
Определяем скорость заливки:
где: H – высота отливки мм;
Определяем среднедействующий металлостатический напор (подвод металла в среднюю часть отливки).
Н0 – расстояние от верхнего уровня металла в чаше до горизонтальной оси питателей Н0 = 20 см;
Определение размеров элементов литниковой системы.
Принимаем соотношение площадей сечения литниковых систем:
Fпит : Fшл : Fст = 1 : 10 : 15
Число питателей = 4 тогда = см2;
Площадь шлакоуловителя: см2
Число шлакоуловителей = 2 тогда Fшл=5172=25 см2
Определяем размеры стояка.
Для обеспечения замкнутости системы и удобства формовки используем конический расширяющийся вверху круглый стояк.
Диаметр стояка внизу:
Диаметр стояка в верху:
dст.в = dст.н. + 001 · Н0
dст.в = 28 + 001 · 11 = 3 см
Определение размеров воронки осуществляется в зависимости от диаметра стояка вверху:
- верхний диаметр воронки см
В зависимости от площади поперечного сечения определяем размеры шлакоуловителя [1 таб. 34]. Так как Fшл = 25 см2 то ширина шлакоуловителя у основания bшл = 16 см ширина шлакоуловителя в верху bв.шл. = 13 см высота шлакоуловителя hшл = 16 см.
Определяем размеры питателей:
В зависимости от площади поперечного сечения определяем размеры питателя [1 таб. 34]. Так как Fпит = 12 см2 то ширина питателя внизу bпит = 22 см ширина вверху bпит в. = 25 см высота питателя hпит = 05 см.
Длина питателя берется в пределах 10 – 50 мм.
5. Проектирование модельного комплекта.
Разработка технологической оснастки производится на основании чертежа отливки с литейно-модельными указаниями.
При машинной формовки разрабатывают: подмодельные плиты низа и верха формы и стержневой ящик.
Для получения качественной отливки с заданными размерами модель должна быть больше ее на величину литейной усадки 11 %.
На нижней подмодельной плите (ДП 03.05.08) располагаются модели с питателями а на верхней подмодельной плите – верхний знак стержня с шлакоуловителем стояком и воронкой .
Подмодельные плиты изготавливают из стали 45 ГОСТ 977 – 88.
Конструкция любого стержневого ящика зависит в первую очередь от конфигурации и размеров стержня а также от способа его изготовления оборудования на котором будут стержни получать. Конструкция ящика должна обеспечить его эксплуатационную прочность и жесткость необходимую длительность пользования. В данном случае изготавливаем стержни из ХТС на пескодувной машине с последующей продувкой их СО2 непосредственно на машине. Материал стержневого ящика – сталь 45 ГОСТ 977 – 88. Размеры стержневого ящика позволяют получать два стержня за один съем.
6. Технологический процесс изготовления отливки.
Подготовка шихтовых материалов.
Металлическая шихта по рельсовому пути поступает из бункеров на место подогрева шихты . Шихта подогревается в термической печи 20 для удаления влаги при температуре 300 – 400 ºС в течении 15 минут. После подогрева металлическую шихту распределяют по печам ИЧТ-25 19 мостовым краном.
Приготовление сплава СЧ-20.
После полного расплавления всех составляющих шихты расплав перегревают до температуры 1440 – 1450 ºС скачивают шлак и отбирают пробу для определения химического состава чугуна. Готовый металл сливается в ковши 15 и 16 которые по монорельсу передвигаются к месту заливки.
Подготовка формовочных материалов.
Свежий формовочный песок просыпается сквозь решетку 21 затем пневмотранспортом доставляется в смесители которые входят в состав стержневых и формовочных автоматов 22 33 34.
Приготовление формовочной и стержневой смеси.
Приготовление формовочной и стержневой смеси осуществляется в смесителях входящих в состав формовочного и стержневого оборудования. Регенерированный песок поступает к смесителям по пневмотранспорту его освежают 30 % кварцевого песка. Связующее поступает в смесители по трубопроводам. После тщательного перемешивания всех материалов входящих в состав смесей производят отбор проб на влажность газопроницаемость и сырую прочность. Контроль свойств формовочной смеси производят два раза в смену (первый и последний замес). Готовая смесь задувается в форму.
Изготовление стержней.
Для получения стержней используют металлические ящики. Стержни изготавливают на пескодувной машине 22 модели L5. После изготовления стержни укладывают в тару и элекропогрузчиками доставляют к местам простановки стержней.
Полуформы изготавливают две формовочные машины 33 и 34 типа L40 и L250 по RESOL-CO2 процессу. На одной машине получают полуформы верха и низа.
После изготовления полуформы поступают на участок сборки. На участке сборки рабочий осматривает поверхность полученной полуформы и проставляет стержни. Полуформы низа и верха проходят через сборщик 27 и 28 и готовая форма поступает на участок заливки.
Заливка форм производится заливочными ковшами 15 и 16. Заливочные ковши движутся по монорельсам. Заливка производится заливщиком. После заливки формы ковш возвращается в исходное положение для заливки следующей формы.
Формы заполненные металлом поступают на участок охлаждения который закрыт кожухом с принудительной вентиляцией для удаления вредных испарений.
Охладившиеся отливки проходят через выбивное устройство 31 и 32 где при помощи механизма выдавливания кома смеси отливка со смесью поступает на выбивную решетку а опоки пройдя после этого через распаровщик поступают обратно на участок формовки. Разрушение кома смеси происходит на выбивной решетке после которой смесь поступает на участок регенерации смеси.
Отработанная смесь по ленточному транспортеру попадает в бункер 8 при помощи ковшевого элеватора 36. Далее по питателям смесь попадает в устройство для регенерации (выжигание связующего в пневмопотоке) 30. Регенерированный песок пневмотранспортом доставляется в бункера над смесителями.
С выбивной решетки отливки по транспортерам перемещаются к дробеметным барабанам 1 модели 42322М. В дробеметном барабане из-за хрупкости чугуна от отливки отламываются литниковые системы.
После этого отливки попадают на участок сортировки.
Детали поступают на сортировочные столы 23 где по внешнему виду разделяют годные детали от брака а так же литников. Если деталь годная то ставят клеймо и отправляют на склад готовой продукции при помощи электропогрузчика.
1. Описание работы устройства для простановки стержней.
Устройство предназначено для автоматической простановки стержней в полуформу. При этом выполняются следующие операции: простановка стержней (вручную) в гнезда кондуктора 1; включение вакуумного насоса на конце трубопровода 2 (стержни присасываются к гнездам кондуктора 1) и цилиндра 8 (звенья рычажно-шарнирной системы поворачиваются в результате чего кондуктор 1 устанавливается гнездами вниз – над полуформой низа 10 на небольшой высоте); опускание цилиндра 3 (кондуктор 1 ложится на полуформу 10 стержни входят в углубления полуформы 10); вакуумный насос выключается в результате стержни остаются в полуформе 10; производится отвод кондуктора 1 в исходное положение.
Схема устройства приведена на чертеже ДП.03.08.08.
2. Расчет элементов механизма.
Расчет цилиндра подъема.
В данном случае центр тяжести поднимаемых частей не находится на линии действия поднимающей силы в результате возникает эксцентричная нагрузка принимаемая роликами опирающимися на направляющую.
Определение расчетного усилия находим из уравнения моментов реакций опор
Где G – вес поднимаемых частей. Принимаем G = 500 кг.
lг – расстояние между центром тяжести поднимаемых частей и линией действия сил. Принимаем lг = 028 м.
lв – расстояние между роликами. Принимаем lв = 02 м.
Определяем расчетное усилие:
Где f1 – коэффициент трения в опорах роликов. Принимаем f1 = 005
d0 = 001 м – диаметр оси ролика.
dр = 005 м – диаметр ролика.
к – коэффициент трения качения. Принимаем к = 005.
Согласно ГОСТу диаметр цилиндра примем 110 мм. Диаметр штока примем равным 50 мм следовательно
Расчет диаметров цилиндра:
что обеспечивает требуемое усилие.
Расчет цилиндра поворота:
Центр тяжести поворачиваемых масс совпадает с осью поворота момент сил сопротивления возникающих при движении определяется моментом сил трения в опорах:
G – поворачиваемые массы G = 400 кг;
f1 - коэффициент трения в опорах f1 = 02;
dв – диаметр шейки вала; dв = 10 мм.
Мтр = 02 400 ( 10 2) = 40 кгсм
γ - угол поворота (примем 40 град);
R – расстояние от центра тяжести поворачиваемых масс до оси поворота R = 76см .
М = 76 400 cos 40 + 40 = 23288+40=23328 кгсм
Расчетное усилие определяют по формуле:
Ррасч = М ( l*2) = 23328 27 = 4322=432 кг
Расчетный диаметр гидроцилиндра получаем следующий
Согласно ГОСТу ближайший диаметр равен 70 мм. Диаметр штока примем равным 30 мм следовательно
3. Схема автоматизации.
При включении рубильника QS1 подается электроэнергия к трансформатору TV1 питающего управляющую ветвь схемы управления. Для предохранения оборудования от высоких напряжений в цепь включен плавкий предохранитель FU1. Силовая ветвь схемы управления включается рубильником QS2 она также содержит плавкий предохранитель FU2 и трансформатор TV2. При нажатии кнопки SB1 срабатывает реле напряжения KV1 замыкая контакты KV1.1 и KV1.2 которые подводят питание к цепи управления схемы управления. Загорается сигнальная лампа HL1 сигнализирующая о включении цепи управления. Отключение цепи управления производится нажатием кнопки SB2 при этом отключается реле напряжения KV1 размыкая тем самым контакты KV1.1 и KV1.2 погасает сигнальная лампа HL1.
При нахождении ключа Р-А в положении А цепь работает в автоматическом режиме. При нажатии кнопки SB3 (пуск) срабатывает реле напряжения KV2 которое замыкает контакты KV2.1 KV2.2 KV2.3. Одновременно срабатывает реле времени KT1 которое отсчитывает время операции. Подается питание на электромагнит YA1. Включается вакуум и происходит захват стержня после того как операция завершена срабатывает размыкающий контакт KT1.1. Питание реле KV2 заканчивается оно отключается тем самым размыкая контакты KV2.1 KV2.2 KV2.3. Разрывается цепь питания электромагнита YA1 и вакуум выключается.
При срабатывании размыкающего контакта KT1.1. подается кратковременный импульс на замыкающий контакт KT1.2. срабатывает реле напряжения KV3 которое замыкает контакты KV3.1 KV3.2 KV3.3. Подается питание на электромагнит YA2.Начинается поворот после того как операция поворота завершена срабатывает размыкающий контакт SQ1.1. Питание реле KV3 заканчивается оно отключается тем самым размыкая контакты KV3.1 KV3.2 KV3.3. Разрывается цепь питания электромагнита YA2 и поворот заканчивается.
При срабатывании размыкающего контакта SQ1.1. подается кратковременный импульс на замыкающий контакт SQ1.2. срабатывает реле напряжения KV4 которое замыкает контакты KV4.1 KV4.2 KV4.3. Подается питание на электромагнит YA3.Начинается простановка стержня после того как эта операция завершена срабатывает размыкающий контакт SQ2.1. Питание реле KV4 заканчивается оно отключается тем самым размыкая контакты KV4.1 KV4.2 KV4.3. Разрывается цепь питания электромагнита YA3 и простановка стержня заканчивается.
При срабатывании размыкающего контакта SQ2.1. подается кратковременный импульс на замыкающий контакт SQ2.2. срабатывает реле напряжения KV5 которое замыкает контакты KV5.1 KV5.2 KV5.3. Одновременно срабатывает реле времени KT2. Подается питание на электромагнит YA4. Срабатывает размыкающий контакт KT2.1. Питание реле KV5 заканчивается оно отключается тем самым размыкая контакты KV5.1 KV5.2 KV5.3. Разрывается цепь питания электромагнита YA4 вакуум выключается.
При срабатывании размыкающего контакта KT2.1. подается кратковременный импульс на замыкающий контакт KT2.2. срабатывает реле напряжения KV6 которое замыкает контакты KV6.1 KV6.2 KV6.3. Подается питание на электромагнит YA5.Начинается подъем гидроцилиндра после того как эта операция завершена срабатывает размыкающий контакт SQ3.1. Питание реле KV6 заканчивается оно отключается тем самым размыкая контакты KV6.1 KV6.2 KV6.3. Разрывается цепь питания электромагнита YA5 и подъем заканчивается.
При срабатывании размыкающего контакт SQ3.1. подается кратковременный импульс на замыкающий контакт SQ3.2. срабатывает реле напряжения KV7 которое замыкает контакты KV7.1 KV7.2 KV7.3. Подается питание на электромагнит YA6.Начинается поворот гидроцилиндра после того как эта операция завершена срабатывает размыкающий контакт SQ4.1. Питание реле KV7 заканчивается оно отключается тем самым размыкая контакты KV7.1 KV7.2 KV7.3. Разрывается цепь питания электромагнита YA6 и поворот заканчивается.
При нахождении ключа Р-А в положении Р (ручное управление) включение и выключение каждой операции производится отдельно. Допустим запуск операций в произвольном порядке для отладки оборудования. Запуск операций производится кнопками SB4 SB6 SB8 SB10 SB12 SB14. Отключение соответственно SB5 SB7 SB9 SB11 SB13 SB15. Механизм работы цепей управления операциями приведен выше.
Безопасность жизнедеятельности.
Человеческая практика дает основание для утверждения что любая деятельность потенциально опасна. Ни в одном виде деятельности невозможно достичь абсолютной безопасности.
Необходимость разработки мероприятий по безопасности жизнедеятельности на предприятии предусматривается статьей 11 "Основ законодательства Российской Федерации об охране труда" согласно которой проектирование строительство и реконструкция производственных объектов разработка и выпуск средств производства внедрение технологий в том числе приобретенных за рубежом использование средств коллективной и индивидуальной защиты не отвечающих требованиям по охране труда не допускаются. Кроме того в Трудовом Кодексе РФ прописано что каждый имеет право на труд безопасный для жизни и здоровья работающего
Безопасность жизнедеятельности выявляет и изучает производственные опасности и профессиональные вредности а также обеспечивает нормальные (комфортные) условия деятельности людей. Улучшение условий труда и повышение его безопасности приводят к снижению производственного травматизма уменьшению случаев профессиональных заболеваний инвалидности что не только сохраняет здоровье работников но и снижает затраты на оплату льгот и компенсаций за работу в неблагоприятных условиях труда.
Проектируемый цех отличается от аналога введением автоматической линии сокращением операций выполняемых ручным трудом.
2. Анализ вредных и опасных производственных факторов на участке плавильного отделения которые воздействуют на рабочего.
Технологический процесс плавки чугуна в индукционных печах включает следующие операции: загрузку шихты нагрев и расплавление металла при температуре 1260°С перегрев науглероживание и доведение химического состава до заданного а также его выдержка. Готовый расплав переливают в миксер. Заливку форм производят ковшом емкостью 500 т. который по монорельсу подходит к миксеру и заполняется металлом.
На участке плавильного отделения имеются следующие вредные и опасные производственные факторы:
2.1. Повышенная загазованность воздуха рабочей зоны.
Вредные вещества в воздушной среде образуются от раскаленных форм расплавленного металла пыли осевшей на оборудовании. Газы также образуются при выделении легкоплавких и легко испаряемых элементов в процессе плавки заливки.
Опасность этих выделений в том что при длительном воздействии на организм они могут привести к отравлениям к хроническим изменениям в организме проявляемым в повреждениях внутренних органов кровеносной системы нервной системы; могут иметь канцерогенное действие оказывать удушающее и раздражающее воздействие на дыхательные пути: отдышка воспалительные реакции отеки.
Согласно ГОСТ 12.1.005-88ССБТ и СНиП 2.04.05-91 должны соблюдаться мероприятия по обеспечению рабочих коллективными и индивидуальными средствами защиты:
На пультах и постах управления технологическими процессами при выполнении работ операторского типа связанных с нервно-эмоциональным напряжением физической нагрузкой должны соблюдаться оптимальные величины температуры воздуха 22-24°С его относительной влажности 60-40% и скорости движения (не более 01 мс).
Интенсивность теплового облучения работающих от нагретых поверхностей технологического оборудования осветительных приборов инсоляции на постоянных и непостоянных рабочих местах не должна превышать 35 Втм2 при облучении 50% поверхности тела и более 70 Втм2 - при величине облучаемой поверхности от 25 до 50% и 100 Втм2 - при облучении не более 25% поверхности тела.
Содержание вредных веществ в воздухе рабочей зоны не должно превышать допустимых концентраций (ПДК).
2.2. Повышенная температура воздуха рабочей зоны и поверхности оборудования.
Возникает от нагретых частей оборудования а также при перемещении заливочного ковша от печи к заливаемой форме.
На организм человека влияние фактора повышенной температуры рабочей зоны заключается в снижении работоспособности ослаблении сопротивляемости организма - к повышению заболеваемости к тепловому истощению или удару. Повышенная температура поверхности оборудования может привести к ожогам различной степени тяжести.
Согласно ГОСТ 12.3.38-86 ССБТ и СНиП 2.04.05-91 рабочие плавильного участка должны иметь коллективные средства защиты:
Лица работающие на оборудовании с повышенной температурой поверхности должны подвергаться медицинскому осмотру.
К работе на оборудовании с повышенной температурой поверхности допускаются лица прошедшие соответствующее обучение инструктаж и проверку знаний требований безопасности в соответствии с ГОСТ 12.0.004-79.
Для удаления избытков тепла применяется механическая вентиляция.
Источники повышенного тепловыделения подвергают дополнительной теплоизоляции. При этом температура наружной поверхности не должна превышать +45 ºС.
Согласно ГОСТ 12.3.011-80 ССБТ индивидуальные средства защиты:
Рабочие должны быть обеспечены средствами индивидуальной защиты: сапоги рукавицы суконные брюки и куртка.
Рабочие получившие средства индивидуальной защиты должны быть проинструктированы о порядке пользования и ухода за ними.
На плавильном участке должны быть предусмотрены средства для оказания первой медицинской помощи и условия соблюдения личной гигиены.
2.3. Движущиеся машины и механизмы (груз поднятый на высоту).
Т. к. плавильный участок расположен в центральном пролете цеха то особую опасность представляют мостовые краны которые передвигаются с грузами над центральным пролетом.
Движущийся транспорт может привести к травмам различной степени тяжести: ушибы вывихи переломы а также к летальному исходу.
Согласно ГОСТ 12.3.020-80 ССБТ рабочие плавильного участка должны иметь коллективные средства защиты:
Порядок и виды обучения организация инструктажа работающих согласно ГОСТ 12.0.004-90.
К управлению транспортными средствами погрузочно-разгрузочных работ допускаются лица не моложе 18 лет прошедшие обучение по специальной программе и имеющие удостоверение на право выполнения соответствующего вида работ.
Программы для обучения работающих занятых перемещением грузов на предприятиях должны составляться с учетом требований стандартов безопасности труда "Правил устройства и безопасной эксплуатации грузоподъемных кранов" утвержденных Госгортехнадзором РФ и других нормативно-технических документов.
Согласно ГОСТ 12.3.020-80 ССБТ индивидуальные средства защиты:
Работающие должны быть обеспечены средствами индивидуальной защиты с учетом воздействующих на них опасных и вредных производственных факторов в соответствии с отраслевыми нормами.
Все средства индивидуальной защиты применяемые работающими при работах связанных с внутризаводским перемещением грузов должны подвергаться периодическим контрольным осмотрам и испытаниям в порядке и в сроки установленные нормативно-технической документацией на эти средства.
Работающие участвующие в выполнении погрузочно-разгрузочных работ грузоподъемными механизмами должны носить защитные каски по ГОСТ 12.4.091-80 и ГОСТ 12.4.128-83.
2.4. Повышенное значение напряжения в электрической цепи замыкание которой может произойти через тело человека.
На плавильном участке имеются токопроводящие полы пыль химические вещества которые при длительном воздействии могут разрушить изоляцию проводов.
Поражение человека электрическим током может привести к ожогам электрическим ударам электроофтальмии металлизации кожи к прекращению работы сердца и остановке дыхания.
Согласно ГОСТ 12.1.019-79 ССБТ рабочие плавильного участка должны иметь коллективные средства защиты: защитное заземление зануление выравнивание потенциала система защитных проводов защитное отключение изоляция нетоковедущих частей электрическое разделение сети малое напряжениеконтроль изоляции компенсация токов замыкания на землю.
Согласно ГОСТ 12.1.019-79 ССБТ рабочие плавильного участка должны иметь индивидуальные средства защиты: защитные оболочки защитные ограждения (временные или стационарные) безопасное расположение токоведущих частей изоляция токоведущих частей (рабочая дополнительная усиленная двойная) изоляция рабочего места малое напряжение защитное отключение предупредительная сигнализация блокировка знаки безопасности.
3. Описание методики необходимой для оценки безопасного рабочего места по условиям труда.
Оценка безопасности рабочего места проводится по следующей методике:
Оцениваются все источники опасности: параметры источников опасности соответственно j – мощность; ρ – приведенное расстояние; – время воздействия.
Записываются все допустимые значения параметров источников:
повышенная температура поверхности оборудования: jд = 50°С ρд = 05 м tд = 8 ч.
опасность поражения электрическим током при замыкании на корпус: jд = 001А ρд = 03 см д = 01 сек.
груз поднятый на высоту: jд = 50 кг ρд = 4 м tд = 8 ч.
повышенная запыленность воздуха: jд = 4 мгм3 rд = 05 м tд = 8 ч;
Измеряются действующие фактические значения источников опасности: на предприятии создается комиссия которая производит замеры различными приборами.
Вычисляются показатели безопасности каждого источника опасности: .
Если показатель безопасности b если bi 0 то источник еще опаснее и необходимо предусмотреть дополнительные меры безопасности.
Вычисляется показатель безопасности каждого рабочего места: показатель безопасности рабочего места при воздействии на него нескольких источников опасности определяется по формуле:
где М – количество источников опасности на рабочем месте.
4. Анализ безопасности работающего в соответствии с условиями его труда.
Рабочее место 1. Участок плавильного отделения.
На данном рабочем месте действуют следующие источники опасности:
Повышенная температура поверхности оборудования.
Опасность поражения электрическим током при замыкании на корпус;
Груз поднятый на высоту;
Повышенная запыленность воздуха.
На участке имеются следующие средства защиты:
для удаления избытков тепла применяется механическая вентиляция;
источники повышенного тепловыделения подвергают дополнительной теплоизоляции;
рабочие плавильного участка имеют средства индивидуальной защиты: сапоги рукавицы суконные брюки и куртка;
Данные средства защиты соответствуют ГОСТ 12.3.38-86ССБТ и СНиП 2.04.05-91. При выполнении действующих инструкций b1 > 0.
- Проводится периодический контроль состояния электрооборудования и изоляции.
- Электроустановки имеют блокировки которые исключают включение оборудования при открытых его частях которые находятся под напряжением.
- Электрооборудование имеет сигнализацию о его включении.
Данные средства защиты соответствуют ГОСТ 12.1.019-79 ССБТ и при выполнении существующих инструкций значительно снижают вероятность повреждения работающего электричеством. В результате b2 > 0.
Подъем и перемещение грузов кран-балкой может осуществлять только специально обученный рабочий.
Перед подъемом необходимо удостовериться в исправности стропов.
При подъеме грузов запрещается нахождение посторонних людей в радиусе 2 м.
При начале движения кран-балки загорается световое табло.
Данные средства защиты соответствуют ГОСТ 12.3.020-80ССБТ. При соблюдении инструкции b3 > 0.
т.к. b4 0 источник опасен.
Существует приточно-вытяжная вентиляция которая обеспечивает содержание вредных веществ меньше ПДК.
Токсичные вещества хранят в отдельных помещениях в герметичной таре.
На участке установлены промышленные кондиционеры.
Данные средства защиты соответствуют ГОСТ 12.1.005-88 ССБТ и СНиП 2.04.05.-91. При соблюдении инструкции b4 > 0.
5. Оценка безопасности рабочего места.
Безопасность рабочего места при выполнении всех указанных выше мероприятий:
при соблюдении всех предписанных выше мероприятий безопасность рабочего места обеспечена.
6. Расчёт сопротивления заземляющего устройства.
Защитное заземление выполняется в соответствии с ГОСТ 12.1.030-81.
Для расчета выбираем электроиндукционную печь - с линейным напряжением 380 В источника трехфазного тока следовательно сопротивление заземляющего устройства должно быть не более 4 Ом.
Выбираем форму и геометрические размеры заземлителя:
заземлитель вертикальный в виде стальных стержней схема которого представлена на рис. 5.1.
Рис. 5.1 Схема стержневого заземителя.
t0 – расстояние от веха до заземлителя 08 м;
d – диаметр стержневого заземлителя 001 м;
Определяем сопротивление одиночного заземлителя по формуле:
где: – расчетное удельное сопротивление грунта с учетом климатического коэффициента находится по формуле:
где: – удельное сопротивление грунта (супесок)
– климатический коэффициент значения которого равно 145.
Определяем потребное число заземлителей без учета их взаимного экранирования:
где: n – потребное число заземлителей без учета экранирования;
– коэффициент использования заземлителей учитывающий их взаимное экранирование зависящий от размеров и расположения заземлителей;
R – сопротивление заземлителя;
– требуемое сопротивление искусственного заземлителя
Выбираем расстояние между заземлителями L из отношения С = LзL для углубленных стационарных заземлителей С = 1.
Получаем: Lз = С L = 1 5 = 5 м. (5.4)
Выбираем коэффициент использования заземлителей при числе стержней n = 50 и при принятом отношении С = 1; =04
Определяем необходимое количество заземлителей с учетом их взаимного экранирования:
nэ = 10104(4 04) = 63 шт
Определяем расчетное сопротивление при принятом числе заземлителей nэ.п. = 63 шт:
Rрасч = R( nэ.п. ) (5.6)
Rрасч = 10104 (63 04) = 4 Ом
Определяем длину соединительной полосы при расположении заземлителей по контуру
Lс.п. = 105 Lз nэ.п. (5.7)
Lс.п. = 105× 5× 63 = 33075 м
Определяем сопротивление растеканию тока в соединительной полосе:
Определяем коэффициент использования n для соединительной полосы при nэ.п. = 63 и принятом отношении С = 1. Значение этого коэффициента табличные n = 02.
Определяем расчетное сопротивление соединительной полосы с учетом взаимного экранирования:
Rрасч.n = R( nэ.п. n) (5.8)
где: nэ.п. – число параллельно уложенных полос.
Rрасч.n = 10104 (63 02) = 8 Ом
Определяем общее расчетное сопротивление в заземлителях и соединительной полосе:
Rо.расч. Ru оставляем принятое количество заземлителей.
Выявив вредные и опасные производственные факторы применяем средства защиты коллективные и индивидуальные при использовании которых источник опасности уменьшается до допустимых норм b1 > 0.
Обеспечение нормальных (комфортных) условий деятельности людей улучшение условий труда и повышение его безопасности приводят к снижению производственного травматизма уменьшению случаев профессиональных заболеваний инвалидности что не только сохраняет здоровье работников но и снижает затраты на оплату льгот и компенсаций за работу в неблагоприятных условиях труда. Что полностью соответствует требованиям Трудового Кодекса.
Экономическая часть.
1. Производственный план.
1.1. Расчет эффективного годового фонда времени
работы оборудования.
Эффективный годовой фонд времени работы оборудования определяется по формуле:
где: Fк – календарный фонд времени работы единицы оборудования дни;
Fп – время перерывов в работе (число праздничных и выходных дней в году) дни;
S - продолжительность смены ч;
q - количество смен;
Kр коэффициент учитывающий плановые простои оборудования обусловленные выполнением ремонтных работ и особенностями технологии производства при работе в две смены принимаем Кр= 095.
1.2. Расчет потребного количества оборудования и транспортных средств.
Все необходимое технологическое и силовое оборудование а также подъемно-транспортное оборудование рассчитано в технологической части дипломного проекта. Все данные сведены в таблицу 6.1.
Ведомость технологического оборудования.
Наименование оборудования
Количество ед. оборуд.
Категория ремонтосложности
Первоначальная стоимость тыс. руб.
Отчисления в ремонтный фонд
Амортизационные отчисления
Стержневая машина L5
Дробеметный барабан 42322М
Формовочный автомат L40
Формовочный автомат L250
Устройство для простановки стержней
Установка регенерации
Фрезеровальный станок
Итого по оборудованию:
Итого по транспорту:
Общая производственная площадь определяется как сумма площадей под участки производства продукции вспомогательные отделения и склады бытовые и конторские помещения.
Sп = Sпу + Sвс + Sбк (6.2)
где: Sп - общая производственная площадь;
Sпу - площадь под производственные участки;
Sвс – площадь под вспомогательные отделения и склады;
Sбк - площадь бытовых и конторских помещений.
Sп = 3588 + 1080 + 1188 = 5856 м2
1.4. Основной капитал.
ОК = Спл + Соб + Сдэ (6.3)
где: Спл – стоимость площадей;
Соб – стоимость оборудования и транспортных средств тыс. руб.;
Сдэ – стоимость других элементов основного капитала тыс. руб.
где: Цпп – цена 1 м2 площади 20 тыс. руб.;
Sп – общая производственная площадь.
Спл = Цпл Sп = 20 4668 = 93360 тыс.руб;
ОК =93360 + 161670 + 4774 = 259804 тыс.руб;
2. Определение состава и численности работающих предприятия.
Численность работающих цеха планируется по каждой категории отдельно:
основные производственные рабочие;
вспомогательные рабочие;
руководители (менеджеры);
служащие (СКП) и младший обслуживающий персонал (МОП).
Численность основных производственных рабочих берется исходя из норм обслуживания основного технологического оборудования при двухсменном графике работы.
Для определения численности рабочих (основных и вспомогательных) предварительно рассчитаем эффективный фонд рабочего времени. Определение фонда времени работы одного среднесписочного работника приведено в таблице 6.2.
Расчет фонда времени рабочего
Состав фонда времени рабочего
% к номинальному фонду
Календарный фонд времени
Выходные и праздничные дни
Номинальный фонд времени
Целодневные невыходы на работу
б) дополнительный отпуск
г) выполнение гос. и общ. обязан.
Явочный фонд рабочего времени
Потери внутри рабочего времени
Эфф. фонд времени рабочего
Средняя продолжительность раб. дня
Расчет списочной численности основных рабочих занятых на работах производится по количеству рабочих мест и нормам обслуживания. Все расчеты сводятся в таблицу 6.3.
Расчет списочной численности основных рабочих по нормам при многостаночном обслуживании:
где: С – количество однотипного оборудования шт.;
S – число смен в сутках;
Nо – норма обслуживания одним рабочим оборудования или рабочих мест (число единиц оборудования обслуживаемых одним рабочим);
Кпер – коэффициент перевода явочного числа рабочих в списочное
здесь Фн и Фэ – номинальный и эффективный фонды времени.
Численность основных рабочих по рабочим местам и нормам обслуживания.
Число рабочих в смену
Списочная численность рабочих
Численность рабочих по ремонту оборудования определяется по формуле:
где: Rе – количество единиц ремонтной сложности оборудования предприятия рем.ед.;
Nо – норматив межремонтного обслуживания одним рабочим в смену рем.ед.
Кпер – коэффициент перевода явочного числа рабочих в списочное.
Расчет численности вспомогательных рабочих выполненный по профессиям сводится в таблицу 6.4.
Расчет численности вспомогательных рабочих
Измеритель нормы обслуживания
Норма обсл. на одного вспомогат. рабочего
Кол-во расчетных единиц
Коэффициент пересчета
Списочная численность вспомогательных рабочих
Слесари по ППР и межрем. обслуж
Кол-во ед. ремонтной сложности
Наладчик автоматической линии
Станочники по ремонту
Наладчики прочего оборудования
Количество прочего оборудования
Численность основных раб.
Станочники отделения
Транспортные рабочие
Кладовщики раздатчики инструмента
Уборщики производственных помещений
Расчет численности специалистов управленцев и МОП.
зам. начальника цеха
На основании расчетов составляется сводная ведомость состава работающих (таблица 6.6) с указанием численности работающих среднего разряда рабочих.
Сводная ведомость общего состава работающих.
3. Основные технико-экономические показатели предприятия.
К числу важнейших технико-экономических показателей относятся: основной капитал себестоимость продукции оборотный капитал сводные технико-экономические показатели и показатели финансового состояния предприятия.
3.1. Основной капитал.
Стоимость технологической оснастки определяется укрупнено в размере до 10 % от первоначальной стоимости технологического оборудования.
Стоимость производственного и хозяйственного инвентаря принимается в размере 15 - 20 % от первоначальной стоимости технологического оборудования.
Наименование основных фондов представлено в таблице 6.7.
Наименование основных фондов
Транспортные средства
3.2. Определение затрат на производство.
3.2.1. Затраты материальные.
Затраты на основные материалы и вспомогательные материалы технологического назначения определяются исходя из норм расхода данных видов материалов на изделие цены весовой единицы материала с учетом данных о количестве и стоимости возможных отходов. Данные о материальных затратах представлены в таблице 6.8. и в таблице 6.9.
Расчет затрат на основные материалы технологического назначения
Цена за 1 тонну тыс. руб
Расчет затрат на вспомогательные материалы технологического назначения.
Стоимость материала тыс. руб
Приведенная программа т
Стоимость годовой программы тыс. руб.
3.2.2. Затраты энергетические технологического назначения.
Затраты энергетические технологического назначения
Наименование вида энергии
Цена за ед. измер. (руб.)
Расход на годовую прогр.
Стоимость энергии на годов. прогр.(тыс.руб.)
Технологическая энергия
3.2.3. Расчет фондов заработной платы рабочих.
Тарифный фонд заработной платы рабочих-повременщиков
Зпр.п. = Счас Фэф Рвсп
где: Счас – часовая тарифная ставка рабочих-повременщиков данной профессии разряда рубч;
Фэф – эффективный фонд времени одного рабочего ч;
Рвсп – списочная численность рабочих-повременщиков данной профессии и разряда.
Годовой фонд заработной платы рассчитывается путем суммирования дневного фонда и доплат до годового фонда. К доплатам до годового фонда относятся: оплата отпусков оплата за время выполнения гос. и общественных обязанностей и т. д. Результаты расчёта фонда зарплаты сводятся в табл. 6.11.
Расчет фонда заработной платы производственных рабочих
Вспомогательные рабочие
часовые тарифные ставки
Эффективный фонд времени
Фонд прямой зп рабочих
ИТОГО тарифный фонд зп
Доплаты до основного фонда
ИТОГО основной фонд зп
Доплаты до годового фонда
ИТОГО годовой фонд зп
Всего годовой фонд зп
Среднегодовая зп одного рабочего
Среднемесячая зп одного рабочего
Заработная плата специалистам управленцам и МОП.
Кдоп - коэффициент доплат;
Крк - районный коэффициент;
Ксоц - отчисления на социальные нужды;
Общая годовая зп руб
Годовой фонд зп руб.
Зам. начальника цеха
Средняя месячная зп ИТР
Отчисления во внебюджетные фонды 26%
Всего годовой зп с отчислениями
Распределение фонда заработной платы и отчислений
на социальные нужды по статьям калькуляции
Категория работающих
Сумма отчисл. на соц. нужды (26%) т.р
Сумма фонда зп и суммы отчисл.на соц. нужды т.р.
Зароботная плата (основная и дополнительная) основных производственных рабочих
Расходы на содержание и эксплуатацию оборудования. В том числе:
а) содержание оборудования
дежурный персонал наладчики смазчики электронщики и др.
б) ремонт оборудования и технологической оснастки
Слесари станочники занятые ремонтом оборудования и технолог. оснастки
в) внутрицеховое перемещение грузов
транспортные рабочие
г) износ малоценных и быстроизнашивающихся инструментов
слесари станочники РЕМПРИ
контролеры ОТК распорядители работ кладовщики и т.д.
а) на содержание прочего персонала
вспомогательные рабочие ученики МОП
б) на содержание зданий сооружений инветаря
уборщики производственных помещений
3.2.4. Расходы на содержание и эксплуатацию оборудования.
Затраты энергетические силового назначения
Затраты на силовую электроэнергию
где: Nу – суммарная мощность электродвигателей технологического оборудования предприятия кВт;
Км – средний коэффициент загрузки электродвигателей по мощности Км = 08;
Кз - средний коэффициент загрузки электродвигателей по мощности Кз= 06;
Код – коэффициент одновременной работы электродвигателей Код = 08;
Kw – коэффициент потерь электроэнергии в сети Kw = 106;
Fэ – эффективный фонд времени работы единицы оборудования ч;
– средний коэффициент полезного действия электродвигателей = 08;
Сэл – стоимость 1кВтч электроэнергии руб.
Затраты на сжатый воздух:
где: Qчас – среднечасовой расход сжатого воздуха для всех воздухоприемников (100 м3);
Fэф – эффективный фонд времени работы оборудования ч;
Кз – средний коэффициент загрузки оборудования по времени (07);
Свозд – стоимость 1000 м3 сжатого воздуха (700) руб.
Все сведенья по содержание и эксплуатацию оборудования сведены в таблицу 12.14.
Смета расходов на содержание и эксплуатацию оборудования
Амортизация на полное восстановление оборудования и транспортных средств оснастки
Амортизационные отчисления на полное восстановление по действующим нормам от первоначальной стоимости основного оборудования оснастки а также производственный и хозяйственный инвентарь
Эксплуатация оборудования (кроме расходов на ремонт)
Затраты на вспомогательные эксплуатационные материалы (смазочные обтирочные материалы эмульсии материалы для промывки деталей и т.д.)
Стоимость электроэнергии и сжатого воздуха
Зарплата (основная и дополнительная) вспомогательных рабочих обслуживающих оборудование (наладчиков смазчиков электронщиков электриков слесарей и др.) с отчислениями на социальные нужды
Затраты на ремонт оборудования дорогостоящей оснастки (отчисления в ремонтный фонд)
Отчисления в ремонтный фонд и заработная плата рабочих занятых ремонтом оборудования и дорогостоящей оснастки
Внутрицеховое перемещение груза
Заработная плата (основная и дополнительная) с отчислениями на социальные нужды транспортных рабочих
Затраты на эксплуатации транспорта (стоимость смазочных обтирочных материалов горючего и т.д.)
Износ малоценных и быстроизнашивающихся инструментов и приспособлений
Расходы по восстановлению и ремонту (заработная плата рабочих занятых восстановлением стоимость мат. услуг других цехов и т.д.)
Заработная плата (основная и дополнительная) и отчисления на соц. нужды контролеров ОТК распределителей работ кладовщиков и т.д. исключая уборщиков помещений
Всего расходов по содержанию и эксплуатации оборудования
3.2.5. Прочие постоянные статьи затрат.
Общепроизводственные расходы:
-содержание производственных помещений;
-заработная плата обслуживающих рабочих специалистов основная и дополнительная с отчислениями;
-расходы на сервисное обслуживание.
Общехозяйственные расходы:
-заработная плата управляющих премии;
-командировочные расходы оплата услуг связи бухгалтерских и юридических услуг арендные платежи; и др.
Т.О. общепроизводственные расходы связаны с обслуживанием и управлением производства. Их определяем в размере 500 % от основной ЗП основных производственных рабочих.
Сумма общехозяйственных расходов принимается в размере 300-400 % от основной ЗП основных производственных рабочих а сумму внепроизводственных расходов – 2 % от себестоимости товарной продукции.
Себестоимость всего объема определятся:
С = Зпер х N + Зпост
Себестоимость единицы продукции:
где: Зпер – переменные затраты на единицу продукции т.руб.;
Зпост – постоянные затраты на весь объем т.руб.;
N – годовая программа выпуска шт.
Калькуляция себестоимости продукции.
Годовая приведенная программа предприятия 1566773 шт.
Наименование статей затрат
Основные материалы без возвратных отходов
Вспомогательные материалы технологического назначения
Итого прямых мат. затрат
Затраты на технологическую энергию
Заработная плата основных производственных рабочих
Отчисления на соц. нужды
Итого сумма переменных затрат (п.1 ÷ п.5)
Расходы на содержание и эксплуатацию оборудования
Общепроизводственные расходы
Общехозяйственные расходы
Производственная себестоимость
Внепроизводственные расходы
Итого сумма постоянных затрат (п.6÷9)
Полная себестоимость
3.3. Оборотный капитал (оборотные средства).
где Ос.м. – затраты на материалы;
Тпл – величина планируемого периода (год) в днях;
Нм – норматив запаса материала в днях определяется из условий поставки материала ( Нм = 4);
С – себестоимость годового объема продукции;
Ннзп – норматив на незавершенное производство в днях определяется на основе длительности производственного цикла (Ннзп = 1);
Нг.п. – норматив запаса готовой продукции в днях определяется из условий сбыта продукции (Нг.п. = 10).
3.4.Производственный капитал.
Пк = О.К. + Об.К. = 2783961 + 21394 = 299790 т.р.
4.1. Расчет плановой суммы прибыли.
Цед = СебелРен + НДСед
где: Цед – цена единицы продукции;
Себед – себестоимость единицы продукции;
Рен – коэффициент рентабельности (Рен = 025);
Цед = 036 + 036 * 025 + 00145 = 04645 т.р.
Пналогообл = Пбал - Ним
В = ЦедN = 04645 * 1566773 = 727766 т.р.
Пбал =В -(С+НДСv)= 727766 – (564584 + 22709) = 140473 т.р.
Расчет плановой суммы балансовой и чистой прибыли.
НДС (расчетная ставка 18%)
Полная себестоимость т.р.
Прибыль от реализации продукции т.р.
Балансовая прибыль т.р.
Платежи в бюджет (налоги) т.р.
4.2. Расчёт чистой прибыли.
Рассчитываются налоги с балансовой прибыли и налог на прибыль. Из балансовой прибыли вычитаются налоги.
Пчист = Пбал. – (Ним. + Нприб.) = 140473 – (62398 + 32216) = 1020172 т.р.
4.3. Формирование баланса доходов и расходов.
Баланс доходов и расходов
Доход и поступления средств
Расход и отчисления средств
Амортизационные отчисл.
Отчисления в ремон. фонд
4.4. Расчет безубыточного объема производства продукции.
Безубыточный объем производства продукции (деталей):
где Зпост – постоянные затраты определенные на объем производства;
Зпер – переменные затраты на единицу продукции.
Выручка т.руб. Выручка от реализации
Точка безубыточности
Рис.12.1. График достижения безубыточности
5. Экономические и финансовые показатели бизнеса.
Рентабельность производственного капитала
Рентабельность продукции
Маржа чистой прибыли
Пбал – балансовая прибыль тыс.руб.;
Пч – чистая прибыль тыс.руб.;
С – себестоимость годового выпуска продукции тыс.руб.;
В – выручка тыс.руб.
Финансовый результат может быть оценен положительно т.к. Кчп = 14 % что выше 4.7%.
Экономические показатели бизнеса
Наименование показателей
Значения показателей
Годовая приведенная программа
Кол-во едениц технол. обор.
Выработка на одного работающего
Стоимость основного капитала
Себестоимость ед. продукции
Прибыль от реализации
Выручка от реализации
рентабельность продукции
маржа чистой прибыли
рентабельность произв. капитала
Библиографический список.
Могилев В. К. Лев О. И. Справочник литейщика. М.: Машиностроение 1988. – 272 с.
Ковалев Ю. Г. Проектирование литейных цехов: Методическое пособие по выполнению курсового проекта для студентов. Перм. гос. техн. ун-т. – Пермь 1993.
Миляев А. Ф. Проектирование новых и реконструкция действующих литейных цехов: Учебное пособие. – Магнитогорск: МГТУ им. Г. И. Носова 2001. – 410 с.
Шуляк В. С. Проектирование литейных цехов: Учебное пособие. – М.: МГИУ 2004. – 92 с.
Кнорре Б. В. Основы проектирования литейных цехов и заводов: Учебник. – М.: Машиностроение 1979. – 376 с.
Логинов И. З. Проектирование литейных цехов. Минск «Вышэйш. школа» 1975. 320 с.
Шишляев В. Н. Железоуглеродистые литейные сплавы: Учебное пособие Перм. гос. техн. ун-т. – Пермь 2002. – 161 с.
Ковалев Ю. Г. Литейная технологическая оснастка: Конспект лекций. Ч. 1. Основы технологической подготовки производства. Ч. 2.
Технологическая оснастка для изготовления песчаных набивных форм Перм. гос. техн. ун-т. – Пермь 1999. 209 с.
Ковалев Ю. Г. Расчёт прибылей и литниковых систем. Учебное пособие. Пермский ун-т 1978 78 с.
Трухов А. П. Технология литейного производства: Литьё в песчаные формы: Учебник для студ. высш. учеб. заведений. – М.: Издательский центр «Академия» 2005. – 528 с.
Чуркин Б.С. Гофман Э.Б. «Технология литейного производства» Екатеринбург: Урал. гос. проф.-пед. ун-та 2000 г.
Лукьянов В. И. Поточные и автоматические линии: Атлас; Перм. гос. техн. ун-т. Пермь 1997. 124 с.
Сафронов В. Я. Справочник по литейному оборудованию. М.: Машиностроение 1985. – 320 с.
Михнюк Т. Ф. Безопасность жизнедеятельности. Мн.: Дизайн ПРО 2004. – 240 с.
Шубина Н. Н. Разработка бизнес-плана предприятия металлургического профиля. Мет. указания к курсовой работе и дипломному проекту для студентов; Перм. гос. техн. ун-т. – Пермь 2001 43 с.
(Альбом спецификаций)
(Пескострельные автоматы LAEMPE.
Техническое описание)
видАгот(7).cdw

СПЕЦ общий.cdw

Плита-присос (кондуктор)
Общий(7).cdw

мощностью 15000 тонн в год
Устройство для простановки стержней
видБ(7).cdw

видБ.cdw

видАгот.cdw

Цилиндр подъема(7).cdw

мощностью 15000 тонн в год
СПЕЦ Цилиндр(7).cdw

мощностью 15000 тонн в год
Общий.cdw

СПЕЦ Цилиндр.cdw

Цилиндр подъема.cdw

СПЕЦ общий(7).cdw

мощностью 15000 тонн в год
Плита-присос (кондуктор)
Рекомендуемые чертежи
- 25.01.2023
- 24.01.2023
- 13.05.2023
- 24.01.2023