Закрепочный полуавтомат с МПУ




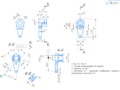


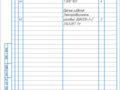
- Добавлен: 24.01.2023
- Размер: 10 MB
- Закачек: 0
Описание
Закрепочный полуавтомат с МПУ
Состав проекта
![]() |
![]() |
![]() |
![]() |
![]() |
![]() ![]() ![]() ![]() |
![]() ![]() ![]() ![]() |
![]() ![]() ![]() ![]() |
![]() ![]() ![]() ![]() |
![]() ![]() ![]() ![]() |
![]() |
![]() ![]() ![]() ![]() |
![]() ![]() ![]() ![]() |
![]() ![]() ![]() ![]() |
![]() ![]() ![]() ![]() |
![]() ![]() ![]() ![]() |
![]() ![]() ![]() ![]() |
![]() |
![]() |
![]() ![]() ![]() ![]() |
![]() ![]() ![]() ![]() |
![]() ![]() |
![]() ![]() ![]() ![]() |
![]() ![]() |
![]() |
![]() ![]() ![]() ![]() |
![]() ![]() |
![]() ![]() ![]() |
![]() |
![]() ![]() ![]() |
![]() ![]() ![]() |
![]() ![]() ![]() |
![]() ![]() ![]() |
![]() ![]() ![]() |
![]() ![]() ![]() |
![]() ![]() ![]() |
![]() ![]() ![]() |
![]() ![]() ![]() |
![]() ![]() ![]() |
![]() ![]() ![]() |
![]() ![]() ![]() |
Дополнительная информация
2-Рейка.cdw

1-коромысло.cdw

3-Колесо.cdw

4-Крышка.cdw

5-Тяга.cdw

Пластина.cdw

Каретка.cdw

Шестерня 61.cdw

Рычаг.cdw

Кольцо.cdw

Квадратный вал.cdw

Сборочный чертеж 1 лист.cdw

Спецификация 2.cdw

Спецификация 3.cdw

Спецификация к сборке.cdw
