Участок групповой обработки корпусных деталей горного оборудования





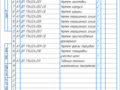
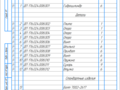
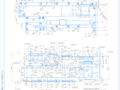
- Добавлен: 24.01.2023
- Размер: 1 MB
- Закачек: 0
Описание
Состав проекта
![]() |
![]() |
![]() ![]() ![]() |
![]() ![]() ![]() |
![]() ![]() ![]() |
![]() |
![]() ![]() ![]() ![]() |
![]() ![]() ![]() ![]() |
![]() ![]() ![]() ![]() |
![]() ![]() ![]() ![]() |
![]() ![]() ![]() ![]() |
![]() ![]() ![]() ![]() |
![]() ![]() ![]() ![]() |
![]() ![]() ![]() ![]() |
![]() ![]() ![]() ![]() |
![]() ![]() ![]() ![]() |
![]() ![]() ![]() ![]() |
![]() ![]() ![]() ![]() |
![]() ![]() ![]() ![]() |
![]() |
![]() ![]() ![]() ![]() |
![]() ![]() ![]() ![]() |
![]() ![]() ![]() ![]() |
![]() ![]() ![]() ![]() |
![]() |
![]() ![]() ![]() ![]() |
![]() ![]() ![]() ![]() |
![]() |
![]() ![]() ![]() |
![]() |
![]() ![]() ![]() |
![]() ![]() ![]() |
![]() ![]() ![]() |
![]() ![]() ![]() |
![]() ![]() ![]() |
![]() ![]() ![]() |
![]() ![]() ![]() |
![]() ![]() ![]() |
![]() |
![]() ![]() ![]() |
![]() ![]() ![]() |
![]() |
![]() ![]() ![]() |
![]() ![]() ![]() |
![]() ![]() ![]() |
![]() ![]() ![]() |
![]() ![]() ![]() |
![]() |
![]() ![]() ![]() |
![]() ![]() ![]() |
![]() ![]() ![]() |
Дополнительная информация
Фреза торцовая ДП 176.024.009.cdw

Заготовка корпуса (Лист 2) ДП 176.024.001.cdw

Эскиз на операцию 50 - ДП 176.024.007.cdw

Экономика ДП 176.024.011.cdw

Заготовка корпуса (Лист 1) ДП 176.024.001.cdw

Спецификация приспособления 2 ДП 176.024.008.000.cdw

Эскиз на операцию 15 - ДП 176.024.006.cdw

Спецификация приспособления ДП 176.024.008.000.cdw

ДП 176.024.002.000 СБ - корпус (Лист 2).cdw

Эскиз на операцию 05 - ДП 176.024.004.cdw

Приспособление фрезерное ДП 176.024.008.000 СБ.cdw

Спецификация корпуса ДП 176.024.002.000.cdw

Планировка участка цеха ДП 176.024.010.cdw

Эскиз на операцию 10 - ДП 176.024.005.cdw

ДП 176.024.002.000 СБ - корпус (Лист 1).cdw

Спецификация крышки ДП 176.024.003.000.cdw

ДП 176.024.003.000 СБ - крышка.cdw

Для приспособы.cdw

Ведомость.cdw

Рекомендуемые чертежи
- 14.06.2022
- 29.07.2014