Технологический процесс сборки форсунки КАМАЗ-216




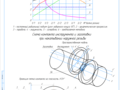
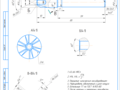
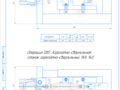
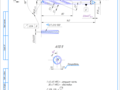
- Добавлен: 24.01.2023
- Размер: 6 MB
- Закачек: 2
Описание
Состав проекта
![]() |
![]() |
![]() ![]() ![]() |
![]() ![]() ![]() |
![]() ![]() ![]() |
![]() |
![]() ![]() ![]() ![]() |
![]() ![]() ![]() ![]() |
![]() ![]() ![]() |
![]() |
![]() ![]() |
![]() ![]() ![]() ![]() |
![]() ![]() ![]() ![]() |
![]() ![]() ![]() ![]() |
![]() ![]() ![]() ![]() |
![]() ![]() ![]() ![]() |
![]() ![]() ![]() ![]() |
![]() ![]() ![]() ![]() |
![]() ![]() ![]() ![]() |
![]() ![]() ![]() ![]() |
![]() ![]() ![]() ![]() |
![]() ![]() ![]() ![]() |
![]() ![]() ![]() |
![]() ![]() ![]() |
![]() ![]() ![]() |
![]() ![]() ![]() |
![]() ![]() ![]() |
![]() ![]() ![]() |
![]() |
![]() ![]() ![]() |
![]() ![]() ![]() |
![]() ![]() |
![]() ![]() ![]() |
![]() ![]() ![]() |
![]() ![]() ![]() |
![]() ![]() ![]() |
![]() ![]() ![]() |
![]() ![]() ![]() |
![]() ![]() ![]() |
![]() ![]() ![]() |
![]() ![]() ![]() |
![]() ![]() ![]() |
![]() ![]() ![]() |
![]() ![]() ![]() |
![]() ![]() ![]() |
Дополнительная информация
OК 1ХМА 1033.doc
Агрегатно-сверлильная
Сталь 40Х ГОСТ 1050-88
Оборудование устройство ЧПУ
Обозначение программы
Агрегатно- сверлильный
Установить и закрепить деталь в приспособлении.
86-2027 Приспособление для нарезания резьбы
Нарезать резьбу М10х125-6Н на глубину 104 min.
20-0556 Метчик М10х125-6Н
Щетка зубная ГОСТ 6388-91
Проверить рабочему размеры 12 у каждой 10й детали .
Наладчику проверить размеры 1234 и угловые размеры у первых 5ти деталей после каждой наладки и подналадки станка .
Размеры 34 и угловые размеры 8°30-1 ° 45 ° -1° проверять в ЦИЛе.
Проверку в ЦИЛе производить до изготовления контрольного приспособления .
21-9822 Пробка резьбовая М10х125-6Н
62-1814 Глубиномер резьбовой М10х125-6Н L= 104min
80-2014 Приспособление для сверления
Цековать торец 17 выдерживая размер 1 Т.Т.
51-9597 Цековка 17с ввертышем М10х127
Проверить рабочему размер 1 и Т.Т. у каждой 15й детали наладчику - у первых 5ти деталей после каждой наладки и
62-1825 Глубиномер 04+025
32-1803 Приспособление на ^ торца 17 к резьбе М10х125.
14-1812 Приспособление индикаторное к 8532-1803
Деталь образцовая на шероховатость торца подбирается технологом и контролером участка аттестуется ЦИЛ.
Установить детали в тару
070 OК UPWS.doc
Сталь 40Х ГОСТ 4543-71
Оборудование устройство ЧПУ
Обозначение программы
Установить и закрепить деталь в центрах.
94-5261 Приспособление для накатки резьбы
Накатать резьбу выдерживая размер 1 и Т.Т.
17-5087 Ролик резьбонакатной М 14х15-6g
Проверить размер 1 у каждой 20 й детали наладчику – у первых 5ти деталей после каждой наладки и
11-0060 Кольцо Сп М14х15-6g ПР
11-1060 Кольцо Сп М14х15-6g НЕ
Установить детали в тару .
Примечание : Расход деталей на наладку и подналадку станка не должен превышать 16на 1000 обработанных деталей
065 OК UPWS.doc
Сталь 40Х ГОСТ 1050-88
Оборудование устройство ЧПУ
Обозначение программы
Резьбонакатной UPWS 1625
Установить и закрепить деталь в приспособлении.
09-0210 Приспособление
32-0045 Центр задний
32-0046 Центр передний
Накатать резьбу 1 выдерживая размер 2 и Т.Т.
17-0006 Ролик накатной Сп М19х 075-6g
Рабочему проверить размер 1 2 у каждой 10-ой детали Т.Т. – у каждой 20й детали наладчику проверить размеры 1 2 и Т.Т.у
первых 5-ти деталей после каждой наладки и переналадки станка
11- 9618 Кольцо резьбовое Сп М19х075-6g ПР
11-9619 Кольцо резьбовое Сп М 19х075-6 g НЕ
11- 9617 Кольцо резьбовое для проверки биения
ПБМ 200 Прибор для проверки биения ; 8021- 0520 Центр к прибору
45-0170Калибр на соосность резьбы и 17
45- 0169 Калибр на соосность резьбы и 225
ИЧ10 кл.1 Индикатор ГОСТ 577-68
Уложить детали в тару .
Примечание : Расход деталей на наладку и подналадку оборудования при замене инструмента не должен превышать
детали на 1000 обработанных деталей .
Исследовательская ч.2.cdw

и заготовки от способа профилирования заборной части
инструмента для накатывания наружных резьб.
- постоянный радиальный подъем (угол заборного конуса 10
); 2 - арифметическая прогрессия;
- парабола; 4 - окружность; 5 - гипербола; 6 - предлагаемая методика.
Схема контакта инструмента и заготовки
при накатывании наружной резьбы
Пространственная модель
Проекция пятна контакта на плоскость XOY
Исследовательская ч.1.cdw

с одинаковыми угловыми скоростями
Двумя роликами равных диаметров
с различными угловыми скоростями
установленными в резьбонакатную
головку тангенциального типа
Роликом и сегментом с плоскосрезанной
Двумя затылованными роликами
Цилиндрическими затылованными роликами
установленными в головку
Плоскими плашками (подвижной и неподвижной)
Двумя затылованными роликами с установкой
Двумя подвижными плашками с установкой
Двумя цилиндрическими роликами
Тремя цилиндрическими роликами
с установкой заготовки в центрах
Двумя роликами с паралельными осями
Двумя роликами с наклонными осями
Тремя роликами с паралельными осями
АлтГТУ ИФФ. гр.ТМ-43
Классификация способов накатывания резьбы винтовым инструментом
Накатывание резьбы винтовым инструментом
080 OК 1ХА 140.doc
Сталь 40Х ГОСТ 1050-88
Оборудование устройство ЧПУ
Обозначение программы
Агрегатно- сверлильный
Установить и закрепить деталь в приспособлении.
80-2005 Приспособление для сверления ( доделка к приспособлению 7380-0175)
32-0179 Центр передний к приспособлению 7380-2005 ; 7051-0038 Кондукторная втулка 18 к приспособлению 7380-2005
80-2009 Приспособление для сверления
32-0180 Центр передний к приспособлению 7380-2009 7051-0103 Кондукторная втулка к приспособлению 7380-2009
32-0118 Центр с ласточкиным хвостом 7032-0178 Центр
30-0313 Оправка для выставления детали
Сверлить отверстие выдерживая размеры 1 2 и Т.Т.
00-0578 Сверло специальное 18 L = 160
Проверить рабочему размер 12 0° 1° Т.Т. у каждой 20й детали наладчику у первых 5ти деталей после каждой наладки
и подналадки станка .
62-1805 Глубиномер 85 +1
66-9962 Калибр R 6.2
33-1800 Пробка 18 +01
17-1916 Приспособление для измерения отклонения оси т.п. отверстия
05- 1926 Мера установочная к приспособлению 8517-1916
ИЧ 10кл. 1 Индикатор ГОСТ 577-68 ( 2 шт)
Установить детали в тару
Производить замену сверла после сверления 10-ти деталей .
При сверлении отверстия производить не менее 35 выводов сверла .
Расход деталей на наладку станка не должен превышать 8на 1000 обработанных деталей .
Наладка для св.гл.отв.1,8.cdw

станок агрегатно-сверлильный 1ХА 140
Операция 085: Агрегатно-сверлильная
Технологическая наладка для
сверления топливоподв.
отв. в корп. форсунки
контр.присп новое.cdw

мм оносительно резьбового
Глубиномер настраивать по мере установочной 8905-0835;
05-1063 с учетом фактического размера.
Деталь считается годной при отклонении стрелки
индикатора от 0 до 0
Приспособление контрольное для
проверки перпендикулярности
Автоматная токарная 1Б240-6к.cdw

Станок горизонтальный многошпиндельный полуавтомат модели 1Б240-6к
Агрегатно-сверлильная.cdw

Операция 050: Агрегатно-сверлильная
станок агрегатно-сверлильный 1ХМА1033
Резьбонакатка(наладка) ноая.cdw

Фрезерная приспособление новое.cdw

Размеры для справок.
Сверло d=1,8.cdw

47 HRCэ - хвостовик.
Профиль инструмента для обработки канавок по ГОСТ 4010-84
Остальные технические требования по ГОСТ 2034-80
Планировка участка.cdw

Относительные показатели
Заработная плата работающих на один рубль
изготовленной продукции
Среднемесячная заработная плата:
- основного рабочего
- вспомогательного рабочего
График загрузки оборудования
- фонтанчик для питья
Условные обозначения:
- ёмкость для эмульсии
- межоперационный склад
- транспортёр стружечный
- стол для заготовок
- подвод сжатого воздуха
- подвод электроэнергии
- ложемент для инструмента
- инструментальная тумбочка
Значения показателей
Наименование показателя
Годовой объем производства продукции
Годовой выпуск продукции
Основные технико-экономические показатели участка
Фонд оплаты труда работающих
Выпуск продукции на одного работающего в год
Трудоемкость единицы продукции
Себестоимость единицы продукции
Фреза.cdw

хвостовик - сталь 40Х ГОСТ 4543-71 32 51 HRCэ
Сварка стыковая оплавлением;
*Размеры для справок
Остальные технические требования по ГОСТ 17024-82
Зенкер конический.cdw

Маркировать обозначение и угол конуса
Остальные ТТ по ГОСТ 14953-80
После заточки и переточки произвести
старение инструмента.
Сборочное приспособление.cdw

085 OК 1ХА 140.doc
Сталь 40Х ГОСТ 1050-88
Оборудование устройство ЧПУ
Обозначение программы
Агрегатно- сверлильный
Установить и закрепить деталь в приспособлении.
80-2004 Приспособление для сверления
32-0118 Центр задний
Сверлить отверстие выдерживая размеры 1 2 и Т.Т.
51-0041 Втулка кондукторная
Проверить рабочему размер 1. у каждой 20й детали вскрытие отверстия 24 в отв. 87 у каждой детали
наладчику - у первых 5ти деталей после каждой наладки и подналадки станка .
30-0691 Пробка 24 +025
00-5098 Сверло 24 ( изношенное )
Установить детали в тару
Производить замену сверла после сверления 15-ти деталей .
При сверлении отверстия производить не менее 22 выводов сверла .
Расход деталей на наладку станка не должен превышать 5на 1000 обработанных деталей .
МК мех.обраб. форсунки 216.моя.doc
Алтайский государственный технический университет
Кафедра общей технологии машиностроения
Зав. кафедрой д.т.н. проф. Е.Ю.Татаркин
на технологический процесс мехобработки корпуса форсунки
Сталь 40Х ГОСТ 1050-88
Код наименование операции
Обозначение документа
Код наименование оборудования
0 Автоматная-токарная
Токарный автомат 1Б 240-6к
Точить заготовку из прутка со стороны конуса 60°.
Токарный автомат 1Б 240 П-6
Точить заготовку со стороны уплотнительного торца. Точить канавку под уплотнительное кольцо.
Наименование детали сб. единицы или материала
Круглошлифовальный AD15-700 ERK-45
Шлифовать поверхности 253-005 и 28-013 по профилю.
Фрезеровать лыски с двух сторон одновременно.
Фрезеровать лыску на 30 выдерживая размер 14±0135.
Фрезеровать лыску выдерживая размер 11-018.
Фрезеровать наклонную площадку под дренажное отверстие выдерживая .
5 Агрегатно-сверлильная
Агрегатно – сверлильный 1088-4513 (8 позиционный)
Цековать торец со стороны М14х15-6g. Сверлить топливоподводящее отверстие 46.
Зенкеровать отверстие 48+005 . Развернуть предварительно 49+0035. Зенкеровать конус 60°8мм.
Притупить острую кромку в конусе 60°. Развернуть окончательно 5.
Агрегатно-сверлильная
Агрегатно - сверлильный 1ХМА 1033
Обработать резьбовое отверстие М10х125 цековать торец 17.
5 Круглошлифовальная
Круглошлифовальный 3М151АН-102
Шлифовать поверхность 1298-009.
0 Круглошлифованльная
Круглошлифовальный 3М152 МВ Ф2
Шлифовать по профилю поверхности 18-0084 184-005 247-052 25-010.
Резьбонакатной UPWS 1625
Накатать резьбу М19х 075-6g.
Накатать резьбу М14х 15-6g.
Агрегатно - сверлильный 1088-4513 (8 позиционный).
Развернуть отверстие 79+0058. Сверлить два штифтовых отверстия 18+008 последовательно.
Цековать донышко 55. Сверлить канавку на торце в отверстие 75. Раскатать донышко 55.
Агрегатно - сверлильный 1ХА 140
Сверлить топливоподводящее отверстие 18.
Сверлить топливоподводящее отверстие 24.
0 Плоскошлифовальная
Плоскошлифовальный 3Е756
Шлифовать уплотнительный торец детали.
Моечная машина М630х 400
Стол контрольный С-3811; ИС-2Г-20 Источник света; ЭЖ 2.80.90 Эндоскоп
Спецификация к 1 чертежу.doc
Прокладка регулировочная
Регулировочная шайба
Кольцо уплотнительное
Заглушка распылителя
задание к проекту.doc
Федеральное агентство по образованию
Государственное образовательное учреждение высшего профессионального образования «Алтайский государственный технический университет им. И.И.Ползунова
ОБЩАЯ ТЕХНОЛОГИЯ МАШИНОСТРОЕНИЯ
НА ДИПЛОМНОЕ ПРОЕКТИРОВАНИЕ
0100 Технология маиностроения
ТМ-43 Юдович Дарье Александровне
фамилия имя отчество
Тема: Технологический процесс сборки форсунки «КАМАЗ-216» и участок
механической обработки корпуса форсунки в условиях автоматизированного
серийного производства. С исследовательской частью.
Утверждено приказом ректора от
Срок исполнения проекта
Задание приняла к исполнению
Чертеж форсунки чертеж детали годовая программа выпуска N=80000шт
действующие технологические процессы сборки форсунки и
механической обработки корпуса форсунки
Содержание разделов проекта
Наименование раздела проекта
Содержание работ по разделу
Консультант (Ф.И.О. подпись)
Расчетно-пояснительная записка
Научно-библиографический поиск
1 По научно-технической литературе просмотреть РЖ
Технология машиностроения
за последние 10 лет и научно-технические журналы
«Обработка резанием» «Вестник машиностроения»
за последние 10 лет.
2 По нормативной литературе просмотреть указатели государственных и отраслевых стандартов за последний год.
3 Патентный поиск провести за 10 лет по странам
России Украины США Франции_
Руководитель проекта доцент к.т.н. Федоров В.А.
должность ученое звание подпись фамилия имя отчество
OК 1ХМА 1033.doc
Агрегатно-сверлильная
Сталь 40Х ГОСТ 4543-71
Оборудование устройство ЧПУ
Обозначение программы
Агрегатно- сверлильный
Установить и закрепить деталь в приспособлении.
86-2027 Приспособление для нарезания резьбы
00-2812 Сверло 9 ГОСТ 4010-77
ГОСТ 3.1404-86 форма 10
Сверлить отверстие 88
01-3573 Сверло 88 ГОСТ 10903-77
01-0039 Сверло 12 ГОСТ 10903-77
51-9597 Цековка 17с ввертышем М10х127
Нарезать резьбу М10х125-6Н на глубину 104 min.
20-0556 Метчик М10х125-6Н
21-9822 Пробка резьбовая М10х125-6Н
62-1814 Глубиномер резьбовой М10х125-6Н L= 104min
Проверить рабочему ^ торца 17 к резьбе М10х125 и Т.Т. у каждой 15й детали наладчику - у первых 5ти деталей после
каждой наладки и подналадки станка.
62-1825 Глубиномер 04+025
32-1803 Приспособление на ^ торца 17 к резьбе М10х125.
14-1812 Приспособление индикаторное к 8532-1803
Деталь образцовая на шероховатость торца подбирается технологом и контролером участка аттестуется ЦИЛ.
Установить детали в тару
Содержание+лит.doc
1Определение типа производства . . 5
2 Проектирование технологического процесс сборки узла . .. ..6
2.1 Служебное назначение узла описание устройства и работы 6
2.2 Критический анализ технических требований. Обоснование метода
достижения точности по отдельным ТТ узла . 9
2.3 Методы проверки ТТ собранного узла . 15
2.4 Анализ технологичности конструкции узла . 15
2.5 Технологическая схема сборки . 16
2.6 Разработка маршрутного техпроцесса сборки с выбором
оборудования и оснастки . .. 17
2.7Нормирование технологического процесса сборки .. . ..18
2.8Организация работы участка сборки .19
3 Технологический процесс изготовления детали .. 19
3.1 Служебное назначение детали и её поверхностей характеристика
3.2 Критический анализ технических требований к детали ..22
3.3 Методы и схемы проверки ТТ .23
3.4 Анализ технологичности конструкции детали ..24
3.5 Выбор и технико-экономическое обоснование метода
получения заготовки . 24
3.6 Разработка технологического маршрута обработки с выбором
оборудования и оснастки баз и схем базирования . .27
3.7 Расчет и выбор припусков 36
3.8 Расчет и выбор режимов резания.
Техническое нормирование 44
3.9 Средства механизации и автоматизации ТП обработки 89
4 Конструирование и расчет приспособлений .90
4.1 Исходные данные .. 90
4.2 Служебное назначение приспособления и исходные данные
для проектирования 90
4.3 Схема и расчет приспособления ..91
4.4 Описание устройства и работы приспособления 95
5 Выбор и описание режущего инструмента 96
6 Планировка участка .96
Охрана труда и окружающей среды 98
1 Требования к безопасности при эксплуатации станков токарной и
сверлильной групп ..98
2 Стружка и способы защиты от травм на участке 103
3 Обезвреживание и утилизация отработанных СОЖ ..110
Организационно-экономическая часть .114
1 Организационные расчеты проектируемого участка .114
2 Технико-экономическое обоснование проекта 123
3 Расчет технико-экономических показателей проектируемого участка 138
Исследовательская часть 150
Ансеров М.А. Приспособления для металлорежущих станков. – М.: Машиностроение 1967. - 945 с.
Балашов А.В. Николаенко Н.С. Дипломное проектирование по технологии машиностроения. Графическая часть. Методические указания Алт. гос. техн. ун-т им. И.И.Ползунова. – Барнаул: Изд-во АлтГТУ 2008. – 80 с.
ГОСТ 21495-76 Базирование и базы. Термины и определения.
ГОСТ 3.1404-86 ЕСТД. Формы и правила оформления документов на технологические процессы и операции обработки резанием.
ГОСТ 7505-89 Поковки стальные штампованные. Допуски припуски и кузнечные напуски.
ГОСТ 14.205-83 (СТ СЭВ 2063-79). Технологичность конструкции изделий. Термины и определения.
Инструмент для станков с ЧПУ многоцелевых станков и ТПС И.Л.Федюшин Я.А.Музыкант А.И.Мещеряков и др. – М.: Машиностроение 1990. – 272 с.
Колесов И.М. Основы технологии машиностроения. – М.: Высш. школа 2001. – 592 с.
Корсаков В.С. Основы конструирования приспособлений. – 2-е изд. перераб. и доп. – М.: Машиностроение 1983. – 277 с.
Кузнецов Ю.И. Конструкции приспособлений для станков с ЧПУ. – М.: Высш. шк. 1988. – 303 с.
Основы технологии машиностроенияПод ред. В.С.Корсакова. – М.: Машиностроение 1977. – 416 с.
Панов А.А. Расчет линейных размерных цепей при проектировании технологических процессов сборки: Учебное пособие Алт. гос. техн. ун-т им. И.И.Ползунова. – Барнаул : Изд-во АлтГТУ 1996. – 51 с.
Панов А.А. Хоменко В.В. Расчет припусков на механическую обработку: Методические указания для студентов машиностроительных специальностей всех форм обучения. Алт. гос. техн. ун-т им. И.И.Ползунова. – Барнаул: Изд-во АлтГТУ 2006. – 44 с.
Справочник технолога-машиностроителя: В 2-х т. Т. 1 Под ред. А.Г.Косиловой и Р.К.Мещерякова. – 4-е изд. перераб. и доп. – М.: Машиностроение 1986. – 656 с.
Справочник технолога-машиностроителя: В 2-х т. Т.2 Под ред. А.Г.Косиловой и Р.К.Мещерякова. – 4-е изд. перераб. и доп. – М.: Машиностроение 1986. – 496 с.
Безопасность труда при обработке металлов резаниемПод ред. А.Ф.Власова – М.: Машиностроение 1980. – 80 с.
Удаление пыли и стружки от режущих инструментовПод ред. А.Ф.Власова – М.: Машиностроение 1989. – 263 с.
Припуски.doc
Расчёт припуска на обработку наружного диаметра 30( ) .
Припуск на черновую обработку:
- высота микронеровностей поверхности образованная на предыдущем технологическом переходе;
- глубина дефектного слоя (обезуглероженного);
- пространственные отклонения обрабатываемой поверхности.
где И – изогнутость оси заготовки в расчетном сечении;
- кривизна проката мкммм;
- расстояние в мм от расчетного сечения до места крепления заготовки.
- погрешность установки заготовки на станке при выполняемом переходе.
где - погрешность базирования; - погрешность закрепления.
Таким образом минимально необходимый припуск на черновую обработку составляет: мкм.
Таблица 1.8 - Расчет предельных размеров для поверхности 30( ) . [13]
Наименование переходов
Припуск минимальный Zimin мкм
Припуск максимальный Zimax мкм
Допуск на припуск ITzi мкм
Наименьший предельный размер мм
Наибольший предельный размер мм
Определение предельных размеров:
Наименьший предельный размер после чернового обтачивания равен:
Действительное значение припуска минимального:
Наибольший предельный размер:
Наибольшее значение припуска на чистовое обтачивание:
Наименьший расчетный предельный размер заготовки:
Фактическое значение припуска минимального:
Наибольший предельный размер заготовки:
Задание рассчитанных размеров на операционных эскизах и чертеже
Для последнего перехода операционный размер должен соответствовать чертежному:
Номинальный размер заготовки следует назначить так чтобы при предусмотренных по ГОСТ 7505-89 отклонениях ( ) предельные размеры соответствовали расчетным. мм (1.20)
Расчёт припуска на обработку наружного диаметра .
Припуск на чистовое обтачивание.
Допуск на размер чистового обтачивания мкм мкм
Погрешность установки так как черновое и чистовое точение выполняются без переустановки.
Припуск на черновое шлифование.
Для предварительного шлифования: мкм мкм
Припуск на чистовое шлифование.
Погрешность установки так как черновое и чистовое точение выполняются без переустановки. мкм
Таблица 1.9 - Расчет предельных размеров для поверхности . [13]
Наименьший предельный размер после чистового шлифования равен:
Наибольший предельный размер после чистового шлифования равен:
Наименьший предельный размер после чернового шлифования равен:
Наибольший предельный размер после чернового шлифования равен:
Наибольшее значение припуска на черновое шлифование:
Наименьший предельный размер после чистового обтачивания равен:
Наибольший предельный размер после чистового обтачивания равен:
Максимальная величина припуска:
Допуск на припуск (проверка правильности расчетов):
Для последнего перехода (чистового шлифования) операционный размер должен соответствовать чертежному: .
Для чернового шлифования в качестве номинального принимаем размер:
Для чистового обтачивания в качестве номинального принимаем размер:
Для чернового обтачивания в качестве номинального принимаем размер:
Номинальный размер заготовки следует назначить так чтобы при предусмотренных по ГОСТ 7505-89 отклонениях ( ) предельные размеры соответствовали расчетным. [13]
Расчёт припуска на обработку торцевой поверхности .
Таблица 1.10 - Расчет предельных размеров для поверхности . [13]
Наибольшее значение припуска на чистовое шлифование:
3.8 Расчёт и выбор режимов резания. Техническое нормирование.
Операция 010 – автоматная – токарная. Станок модели 1Б240-6к.
Позиция 1.1: Точить заготовку из прутка со стороны конуса 60°. [15]
Диаметр сверления D=7.2 мм;
Длина резания L=42 мм;
Инструмент: сверло центровочное материал режущей части – Р6М5;
Технические характеристики станка:
Дополнительно.doc
Техническое нормирование.
Нормирование проводим согласно литературе [22][23]:
Операция 010 Автоматно-токарная. Станок модели 1Б240-6к:
Определение штучного времени необходимое для изготовления одной детали:
где То - основное машинное время затрачиваемое на изменение формы плотности или состояния поверхностного слоя заготовки;
Твс- вспомогательное время необходимое для выполнение основного технологического времени т.е. установка и снятие заготовки подвод отвод режущего инструмента контрольно-измерительные операции.
По рекомендациям для данного типа производства выберем следующие значения:
Тобс- время обслуживания станка затрачиваемое на уход за рабочим местом содержание его в надлежащем состоянии. Оно складывается из организационного времени затрачиваемого на уход за станком и его смазку и технического времени затрачиваемого на смену затупившегося инструмента.
По рекомендациям для крупносерийного типа производства примем:
Тотд - время на отдых. При данном типе производства время отдыха примем равным 4% от Топ.
Тп.з. - подготовительно-заключительное время.
где р - размер партии.
Операция 050 Агрегатно-сверлильная. Станок модели 1ХМА-1033:
Вспомогательное время:
Время организационного обслуживания:
Время технического обслуживания:
Подготовительно-заключительное время:
Операция 065 Резьбонакатная. Станок модели UPWS 1625:
Операция 070 Резьбонакатная. Станок модели UPWS 1625:
Операция 080 Агрегатно-сверлильная. Станок модели 1ХА 140:
Операция 085 Агрегатно-сверлильная. Станок модели 1ХА 140:
3.9 Средства механизации и автоматизации технологического
Средством механизации технологического процесса обработки корпуса форсунки является станок токарный полуавтомат 1Б240-6к. Токарный полуавтомат 1Б240-6к применяют для обработки детали со стороны резьбовой поверхности М14х15-6g. Он позволяет выполнять 5 или 6 переходов за одну операцию что приводит к значительному снижению штучного времени на изготовление детали и снижению себестоимости готовой детали. [20]
Принцип работы станка:
Станок работает по принципу последовательной обработки детали в нескольких позициях. Число позиций соответствует числу шпинделей станка. Одна из позиций является загрузочной. На полуавтомате обработанная деталь в этой позиции извлекается из зажимного патрона а вместо неё устанавливается новая заготовка. Шпиндельный барабан в котором смонтированы рабочие шпиндели несущие обрабатываемые детали из загрузочной позиции поворачивается последовательно на 16 часть оборота. Каждый поворот шпиндельного барабана соответствует переходу обрабатываемой детали в следующую позицию. Обработка ведётся на всех позициях одновременно инструментами установленными на поперечных суппортах и гранях одного общего продольного суппорта. Число граней продольного суппорта соответствует числу шпинделей станка. В загрузочной позиции полуавтомата поперечные суппорты не устанавливаются.
В качестве нулевой точки цикла принят конец рабочего хода. В этой точке нулевая риска на кулаках распредвала находится сверху а кулачок командоаппарата включает быстрое вращение распредвала. Происходит быстрый отвод суппортов в крайнее заднее положение. Затем происходит расфиксация поворот и
Обрабатываемое изделие устанавливается в зажимном приспособлении на предварительную базу. Прижим осуществляется центром к центру. Усилие центр получает от гидроцилиндра.
Обработка производится гидравлическими силовыми столами которые позволяют осуществлять регулировку величины рабочей подачи.
Все бабки установленные на силовые столы имеют устройство контроля нагрузки. При возрастании крутящего момента на сверле подается команда на дополнительный вывод его из зоны обработки. [1]
5 Выбор и описание режущего инструмента.
При крупносерийном типе производства применяется как ГОСТовский так и специальный режущий инструмент который изготовлен из современных материалов. Так например режущая часть резцов изготовлена из твёрдого сплава Т15К6 а режущие части свёрл развёрток фрезы и зенкеров изготовлены из быстрорежущей стали марки Р6М5. Данные материалы сравнительно недорогие и достаточно прочные что позволяет работать данным инструментом на высоких скоростях резания а следовательно позволяет сократить штучное время на изготовление детали. Также использование специального режущего инструмента позволяет получить более высокую точность размеров деталей и выполнение всех технических требований на изготовление предъявляемых к ним.
6 Планировка участка.
При планировке участка исходя из норм приняты следующие расстояния:
расстояние между станками не менее 09 м;
расстояние между оборудованием и колоннами не менее 08 м;
ширина магистрального проезда 4 м;
ширина транспортного проезда 2 м;
Планировка участка выполнялась по порядку технологического процесса в масштабе 1:50. Кроме основного производственного оборудования участок оснащен тарой для складирования заготовок и деталей кран-балкой. Механизирован отвод стружки с помощью скребкового конвейера. Передача заготовок от одной операции к другой осуществляется по рольгангу.
К рабочим местам в зависимости от вида выполняемой работы подводится эмульсия сжатый воздух содовый раствор. При разработке планировки учтены требования по охране труда техники безопасности и противопожарной защите. [2]
Длина участка 32 м 18 м площадь 576 м2.
Планировка показана в графической части дипломного проекта. На листе изображен график загрузки оборудования средний коэффициент загрузки учаска 74% и его технико-экономические характеристики.
Доклад.doc
Дипломный проект состоит из двух основных частей.
В первой части посвященной технологическому процессу сборки форсунки приведено служебное назначение узла и краткое описание работы произведен анализ технологичности конструкции узла и размерный анализ узла описана технологическая схема сборки изучаемого узла и выполнено технологическое нормирование трудоемкости сборки узла.
Во второй части дипломного проекта проводилось изучение технологичности конструкции детали – корпуса форсунки и технических требований к детали а также выбор метода получения заготовки. При выборе метода получения заготовки корпуса рассматривались два метода и на основе расчета себестоимости их изготовления был выбран метод изготовления заготовки из проката. На основе карты исходных данных и анализа действующего технологического процесса с учетом типа производства и специфики деталей был спроектирован технологический процесс изготовления деталей выбрано оборудование и инструмент. В одну технологическую операцию группировалась обработка поверхностей сходных по методу обработки точности шероховатости и технологическим возможностям оборудования. Оборудование выбрано характерное для крупносерийного типа производства – агрегатные и многоцелевые станки. При этом значительно сокращается парк станков и себестоимость изготавливаемых деталей.
Для спроектированных технологических процессов изготовления деталей были рассчитаны режимы резания и определена норма времени на операции. Произведен размерный анализ технологического процесса изготовления корпуса форсунки. В результате проведенной работы были рассчитаны размеры заготовки с минимально необходимыми припусками что обеспечивает минимальный расход материала; на все операции технологического процесса назначены технологические допуски и технические требования; определены минимально необходимые припуски; построены размерные схемы технологического процесса и проверена возможность обеспечения чертежных размеров и технических требований при обработки детали по данному технологическому процессу.
В части охрана труда и окружающей среды
В организационной части проекта определено число необходимого оборудования для изготовления корпуса форсунки коэффициент его загрузки и число рабочих. В экономической части рассчитаны основные технико-экономические показатели проекта которые подтверждают выгодность и рентабельность спроектированного технологического процесса.
Титульник.doc
Федеральное агентство по образованию
Государственное образовательное учреждение высшего профессионального образования «Алтайский государственный технический университет им. И.И.Ползунова
Кафедра "Общей технологии машиностроения
УДК 621.9Допустить к защите в ГАК
Технологический процесс сборки форсунки “КАМАЗ-216” и участок механической обработки корпуса форсунки в условиях автоматизированного серийного производства. С исследовательской частью.
Программа: 80 тыс. узлов в год.
тема дипломного проекта
Пояснительная записка
к дипломному проекту
обозначение документа
Дипломник группы ТМ-43Д.А.Юдович
проекта доцент к.т.н.В.А.Федоров
должность ученое звание и.о. фамилия
окружающей средыдоцент к.т.н.Д.С.Стуров
раздел проектадолжность ученое званиеподписьи.о. фамилия
Экономика организация
производствадоцент к.т.н.В.Н.Петров
НормоконтролеринженерИ.С.Буканова
Дополнительно1.doc
Агрегатно-сверлильная
Сталь 40Х ГОСТ 1050-88
Оборудование устройство ЧПУ
Обозначение программы
Агрегатно- сверлильный
Установить и закрепить деталь в приспособлении.
86-2027 Приспособление для нарезания резьбы
Нарезать резьбу М10х125-6Н на глубину 104 min.
20-0556 Метчик М10х125-6Н
Щетка зубная ГОСТ 6388-91
МК сборки форсунки 216.моя.doc
Алтайский государственный технический университет
Кафедра общей технологии машиностроения
Зав. кафедрой д.т.н. проф. Е.Ю.Татаркин
на технологический процесс сборки форсунки
конструкторского чертежа к условиям испытаний.
Все детали форсунки и каналы корпуса форсунки перед сборкой должны быть чистыми детали не должны иметь заусенцев и должны быть размагничены. Требования к степени чистоты по РД 4571-010-04. Остаточная магнитная индукция – не более 1х10-4 Тл (1 Гс). Корпус и иглу распылителя тщательно промыть профильтрованным дизельным топливом любой марки по ГОСТ 305-82.
Каждая форсунка должна быть подвергнута обкатке регулировке и контрольным испытаниям.
Испытания форсунок проводить на профильтрованном дизельном топливе ГОСТ 305-82 или на профильтрованной технологической жидкости. Вязкость топлива или технологической жидкости должна быть 4-6 мм2 с (4-6 сСт.) при температурных условиях испытаний. Температура окружающей среды при испытаниях должна быть 20+5-2 ° С.
Стенды и приборы применяемые для испытаний форсунок должны соответствовать
Опрессовочный стенд должен быть герметичным. При установке на стенд специальной заглушки время падения давления с 30 МПа (300 кгссм2) до
5 МПа (295 кгссм2) должно быть не менее 3х минут.
Проверять не реже одного раза в смену.
При сборке и транспортировке деталей и узлов особое внимание обратить на отсутствие механических повреждений фосфатированных поверхностей.
Код наименование операции
Обозначение документа
Код наименование оборудования
Входной контроль комплектующих изделий
Участковому контролеру проверить основные размеры и ТТ комплектующих деталей и узлов перечисленных в спецификации
сборочного чертежа форсунки согласно конструкторским чертежам контрольными средствами используемыми при изготовлении
этих деталей – 10% от партии.
Детали должны соответствовать требованиям к степени чистоты по РД 4571-010-04.
Особое внимание обратить на отсутствие заусенцев на всех комплектующих деталях.
Наименование детали сб. единицы или материала
Разложить комплектующие детали в соответствующие тары.
Демагнитизатор ДВК-М2
Размагнитить все комплектующие детали форсунки кроме распылителя.
Допускается остаточная магнитная индукция не более 1х 10-4 Тл (1 Гс).
Проверить величину остаточной намагниченности. Результат занести в карту статистического контроля.
Машина моечная МАГ - 3
00-3232 Ванна с бензином 7900-3233 Крышка
Промыть распылитель в бензине-растворителе Нефрас С-50170 ГОСТ 8505-80 сохраняя комплектность.
Операция выполняется только для распылителей находившихся на хранении на участке более суток и для ложного распылителя.
Для распылителей фирмы «BOSH» операцию не выполнять.
99-5386 Пневмоотсасывающий прибор.
00-3232 Ванна с дизтопливом.
Промыть распылитель в дизтопливе сохраняя комплектность.
00-1879 Ванна; 7900-2121 Ванна
Пропитать консервирующим раствором все комплектующие детали форсунки имеющие фосфатированную поверхность.
Произвести консервацию раствором на основе «Унисма» всех деталей не имеющих защитного покрытия.
Стол контрольный С-3811
Проверить все комплектующие детали форсунки и распылитель на отсутствие загрязнений подвижность иглы в корп. распылит.
ИС-2Г-20 Источник света; ЭЖ.2.80.90 Эндоскоп технический жесткий 4
Рабочему проверить отсутствие заусенцев в отв. 5+003 на выходе топливопроводящее отв. 18 – 100%
Измерение-сортировка
Сортировать корпуса форсунок на группы по диаметру отверстия под фильтр 5+003.
Стол сборочный; 7900-1355 Гидроцилиндр
Запрессовать фильтр в корпус форсунки. Проверить глубину запрессовки фильтра.
ИС-2Г-20 Источник света; ЭЖ.17.140.0 Эндоскоп 17
Рабочему проверить отсутствие заусенцев после запрессовки фильтра со стороны топливоподводящего отверстия – 100%
00-1942 Ванна с бензином.
Промыть уплотнительный торец форсунки в бензине-растворителе Нефрас-С-50170 ГОСТ 8505-80
Запрессовать два штифта в проставку.
Ванна с бензином. Шкаф обдувочный БМ-5147
Промыть проставки с запрессованными штифтами в бензине-растворителе Нефрас-С-50170 ГОСТ 8505-80.
Контролеру ОУК проверить калибром выступание штифтов и глубину запрессовки фильтра.
Собрать узел корпуса форсунки с технологической прокладкой пружиной штангой проставкой
ложным распылителем завернуть гайку распылителя вручную и затянуть ключом тарированным.
Момент затяжки 50-70 Н×м (50-70 кгс×м).
Стенд обкаточный СИ-5199
Обкатать форсунку с ложным распылителем в течение 10 минут.
Отвернуть гайку распылителя. Разобрать форсунку с ложным распылителем технологической прокладкой пружиной штангой
проставкой. Ложный распылитель передать на промывку: опер.025 030 035 данного комплекта техдокументации.
00-2488 Стенд для продувки форсунок сжатым воздухом Р = 4 Мпа
Продуть топливоподводящее отверстие узла корпуса форсунки сжатым воздухом со стороны запрессованного фильтра.
00-3232 Ванна с бензином; 7900-3233 Крышка в ванне; Шкаф обдувочный БМ-5147
Промыть комплектующие детали форсунки в бензине-растворителе Нефрас-С-50170 ГОСТ 8505-80.
Сортировать распылитель на группы по вылету хвостовика иглы.
Собрать узел корпуса форсунки со штатным распылителем согласно модификации форсунки завернуть гайку распылителя вручную.
Затянуть гайку распылителя ключом тарированным. Момент затяжки 50-70 Н×м (50-70 кгс×м).
Стенд регулировочный СП-2413
Отрегулировать форсунку на давление начала впрыска проверить герметичность гидроплотность качество распыливания
подвижность иглы распылителя. Давление начала впрыскивания топлива должно быть 240+2 МПа (240+20 кгссм2).
Обкатать форсунку с комплектным распылителем в течение 30 минут.
Рабочему проверить давление впрыска после обкатки герметичность гидроплотность качество распыливания подвижность иглы
распылителя. Давление начала впрыскивания топлива должно быть 274+08 МПа (274+8 кгссм2).
Операцию производить согласно опер. 105 данного комплекта техдокументации.
0 Испытание-контроль
Стенд «Моторпал» НЦ-108
Рабочему проверить пропускную способность форсунки согласно модификации (смотреть конструкторский чертёж).
Проверить пропускную способность форсунки согласно модификации.
Проверку производить согласно опер. 120 данного комплекта техдокументации.
Форсунки отошедшие после испытаний по какому-либо параметру (давление начала впрыска качество распыливания
герметичность пропускная способность и др.) разобрать. Комплектующие детали разложить в отдельные тары и передать на
опер. 015 Размагничивание; промыть в бензине-растворителе Нефрас согласно опер. 090 Промывка; отправить на опер. 070 для
повторной сборки и подвергнуть испытаниям и контролю согласно маршрутной карте.
Примечание: Операция выполняется для 25% от партии.
Рабочему проверить момент затяжки гайки распылителя произвести подтяжку гайки – 100%. Момент затяжки 50-70 Н×м (50-70 кгс×м).
Рабочему проверить давление впрыска герметичность гидроплотность качество распыливания подвижность иглы распылителя.
Давление начала впрыскивания топлива должно быть 274+08 МПа (274+8 кгссм2).
Контролёру ОУК проверить давление впрыска герметичность качество распыливания подвижность иглы распылителя.
Рабочему проверить геометрические размеры соосность 9 корпуса распылителя относительно 25 корпуса форсунки.
00-0522 Приспособление для клеймения форсунок по окружности
Маркировать условное обозначение форсунки согласно таблице приведенной в операционной карте.
Контролёру ОУК проверить геометрические размеры соосность момент затяжки. На принятые форсунки нанести клеймо.
Установка для опрессовки азотом Р = 10 МПа
Проверить герметичность полости высокого давления у 3-х форсунок от партии.
Транспортировать форсунки на участок сборки.
Примечание: операция выполняется только для форсунок не прошедших клеймение на опер. 102.
Установка для лазерного клеймения УМЛА-600-013
Маркировать условное обозначение форсунки согласно таблице и дату изготовления (месяц год – две последние цифры)
шрифтом 3-Пр по ГОСТ 26.008-85.
Примечание: операция выполняется только для форсунок не прошедших клеймение на опер. 005.
Собрать форсунку с кольцом уплотнительным.
Законсервировать носик распылителя. Установить защитные колпачки на форсунку.
Транспортировать годную продукцию на СГД.
Исследовательская часть(17).doc
Высокие темпы развития мирового и российского машиностроения непрерывно связаны с внедрением в производство новых прогрессивных методов обработки металлов. Одним из путей развития прогрессивной технологии машиностроения является переход на обработку металлов давлением в холодном состоянии вместо обработки резанием. Применение этого метода обработки приводит к значительному повышению производительности труда повышению точности улучшению механических свойств и чистоты поверхности обрабатываемых деталей и создает предпосылки для комплексной автоматизации.
Почти все современные машины и двигатели включают в себя ответственные резьбовые и шлицевые детали условия работы которых требуют обеспечения высокой точности и повышения механических свойств резьбы и шлицев. В качестве примера можно назвать силовые шпильки и анкерные связи дизель-моторов крупные шпильки паровых газовых и гидравлических турбин шлицевые валы автомобилей и так далее которые изготавливаются в больших количествах из высоколегированных термически обработанных сталей. Образование резьбы на таких деталях резанием довольно сложно трудоемко и не обеспечивает необходимых физико-механических свойств. Поэтому более эффективной является обработка резьбы и шлицев по методу холодной пластической деформации – накатыванием.
Классификация способов накатывания резьбы
Накатывание резьбы на изделиях может осуществляться различными методами и способами широко известными и описанными в специальной технической литературе. В некоторых работах [Лапин В. В. Писаревский М.И. Самсонов В.В. Сизов Ю.И. Накатывание резьб червяков шлицев зубьев. Л.: Машиностроение 1986; Миропольский Ю.А. Луговой Э.П. Накатывание резьб и профилей. М.: Машиностроение 1976] представлены варианты классификации которые различаются между собой незначительно. В них все способы накатывания резьбы делятся натри группы (класса): накатывание плоским приводным и неприводным инструментом. Накатывание резьбы плоскими плашками осуществляется на специальных резьбонакатных станках где накатной инструмент приводится в движение извне а следовательно его также можно отнести к классу накатывания с помощью приводного инструмента. В работе Ю.Л.Фрумина «Высокопроизводительный резьбообразующий инструмент» (М.: Машиностроение 1977) такой чёткой классификации не существует но все способы накатывания сгруппированы по виду подачи: осевой .радиальной и тангенциальной. При этом способ накатывания резьбы плоскими плашками затылованными роликами и другие отнесены к тангенциальным способам. В.Г.Якухин в работе «Оптимальная технология изготовления резьб» (М.: Машиностроение 1985) способы накатывания представляет как самостоятельные: планетарный плоскими плашками роликами (с делением по подаче: радиальной тангенциальной и осевой) аксиальными головками тангенциальными и радиальными головками. Несмотря на различие классификаций многие учёные относят способ накатывания резьбы затылованными роликами к способам накатывания с тангенциальной подачей. По-другому классифицируются способы немецким исследователем Б.Ц.Фридрихом [Bethlehem Wilhelm Friderich. Kriterien zum EinordnenderGewindewalzverfahren «Drahtwelt» 1983 69 № 5]. Он предлагает классифицировать способы накатывания резьбы по применяемому оборудованию (специальному универсальному) и по степени задания фаз накатывания (жёсткой свободной).
Таким образом можно сделать вывод о том что существует несколько направлений классификации способов накатывания резьбы:
по группам инструментов;
по способу задания фаз накатывания и применяемому оборудованию.
Каждое из этих направлений по-видимому имеет право на существование. Его выбор зависит от цели и критериев положенных в основу классификации. Классификация необходима для упорядочения способов накатывания резьбы и их учёта; выявления общих закономерностей кинематики накатывания для класса (подкласса); выделения общих и частных способов (способа) и отнесения вновь появляющихся к тому или иному классу.
Известно что классификация предусматривает разложение множества объектов на подмножества по определённым признакам. Например процессы резьбообразования прежде всего классифицируют по двум принципиально отличительным признакам. Выделяют два метода образования резьбы: резанием (со снятием стружки) и пластическим деформированием (без снятия стружки - накатыванием). Классификация способов образования наружной и внутренней резьб также предусматривает различие по существенным признакам которые определяют принципиальные отличия по условиям работы инструментов и их конструкциям.
Учитывая что процесс накатывания резьбы винтовыми инструментами сопровождается осевыми перемещениями (желательными или нежелательными) целесообразно на наш взгляд выполнить классификацию по кинематическим признакам. Одним из существенных признаков является направление накатывания: продольное (вдоль оси накатываемой заготовки) и поперечное. Вторым существенным признаком определяющим особенности кинематики профилеобразования является положение диаметральной плоскости проходящей через оси инструмента и заготовки в процессе накатывания резьбы. В зависимости от способа накатывания положение диаметральной плоскости может изменяться.
Для способов накатывания показанных на рис. 1 положение диаметральной плоскости не изменяется но изменяется межосевое расстояние между инструментами. Для способов накатывания показанных на рис. 2 положение диаметральной плоскости также не изменяется но расстояние между инструментами остаётся постоянным и перпендикулярным к направлению скорости движения инструмента. А для способов показанных на рис. 3 начало и окончание процесса накатывания происходят в различных не совпадающих но изменяющих своё положение диаметральных плоскостях. Совпадение диаметральных плоскостей происходит только в момент окончания профилеобразования.
Третьим существенным признаком позволяющим отличать один способ от другого является направление движения подачи инструмента (или его элементов) относительно заготовки. По этому признаку способы накатывания можно разделить на способы накатывания с радиальным (см. рис. 1) условно-радиальным (см. рис. 2) касательным (см. рис. 3) движением подачи.
Рисунок 1. Способы накатывания резьбы с расположением осей инструмента и заготовки в одной диаметральной плоскости и изменяемым межосевым расстоянием.
Рисунок 2. Способы накатывания резьбы с расположением осей инструмента и заготовки в одной диаметральной плоскости и неизменным межцентровым расстоянием.
Рисунок 3. Способы накатывания резьбы с расположением осей инструмента и заготовки в разных диаметральных плоскостях и различным их положением в начале и в конце профилеобразования.
При условно-радиальном движении подачи встречное движение пары инструментов отсутствует. Его заменяет движение элементов инструмента определяемое конструктивным исполнением инструмента в виде заборного участка. Эти способы накатывания также относятся к способам по классификации Б.Ф.Фридмана с жёстким заданием фаз накатывания резьбы. Названные критерии справедливы при накатывании резьбы винтовым инструментом. Если же рассматривать классификацию накатывания наружной резьбы в целом то необходимо принять во внимание такой критерий как угол наклона ниток резьбы инструмента.
Рассматривая конструктивные и геометрические параметры резьбонакатных инструментов можно отметить что общими для них являются параметры резьбового профиля: угол профиля шаг резьбы высота головки и ножки радиус закругления при вершине. А принципиальным отличием следует считать наличие или отсутствие угла подъёма резьбы инструмента. По этому признаку все способы накатывания наружной резьбы делятся на два класса: с винтовой (винтовой инструмент) и кольцевой (кольцевой инструмент) нарезкой профиля инструмента. Винтовой инструмент характеризуется тем что угол подъёма со его резьбы больше нуля. У кольцевого инструмента нитки резьбового профиля параллельны опорному торцу роликов а угол подъёма со резьбы равен нулю.
Принципиальность отличия заключается и в том что соотношение углов подъёма резьбы винтового инструмента и накатываемой детали оказывает влияние на их относительные осевые перемещения а в кольцевом инструменте соотношение диаметров резьбонакатного ролика и накатываемой резьбы детали на них не влияет. Величина осевого перемещения при накатывании резьбы кольцевым инструментом может зависеть от их установки в резьбонакатном устройстве. Накатывание резьбы кольцевым инструментом (резьбонакатными роликами) происходит с осевой подачей инструмента или заготовки. Существует два способа накатывания резьбы кольцевыми резьбонакатными роликами: тремя роликами установленными в резьбонакатную головку осевого типа двумя роликами со скрещивающимися осями заготовки и инструмента. Скорость осевой подачи определяется шагом накатываемой резьбы. В соответствии с определёнными критериями все способы накатывания резьбы винтовыми инструментами можно свести к двум основным: продольному и поперечному. Продольный включает в себя способы накатывания с осевым движением подачи инструмента относительно заготовки. К способам накатывания резьбы с осевым движением подачи (с осевой подачей) следует отнести такие в которых положение осей заготовки и инструмента в начале и в конце накатывания различное но находится постоянно в двух диаметрально противоположных плоскостях. К ним относятся способы накатывания резьбы: двумя роликами с параллельными осями; двумя роликами с наклонными осями к оси заготовки.
К поперечным относятся способы накатывания с радиальным условно радиальным и касательным движением подачи. Способы накатывания резьбы с радиальным (см. рис. 1) и условно-радиальным движением подачи (см.рис. 2) объединяет то что оси инструмента и заготовки находятся в начале и в конце профилеобразования в одной диаметральной плоскости. Причём её положение в процессе накатывания теоретически и практически не изменяется.
К способам накатывания резьбы с радиальным движением подачи следует отнести накатывание:
круглым инструментом: одним двумя и тремя цилиндрическими роликами;
цилиндрическими роликами с установкой заготовки в центрах;
однороликовой державкой.
К способам накатывания резьбы сусповно-радиальным движением подачи следует отнести накатывание:
круглым инструментом: двумя или одним затылованными роликами отличающимися схемами профилирования заборных частей;
круглым инструментом на универсальных металлорежущих станках затылованными роликами установленными в резьбонакатную головку;
двумя затылованными роликами с установкой заготовки в центрах;
плоскими плашками: подвижной и неподвижной;
двумя подвижными плашками с установкой заготовки в центрах.
Накатывание резьбы с касательным движением подачи осуществляется способами при которых пара резьбонакатных роликов вращается с различными окружными скоростями:
цилиндрическим инструментом на специальных станках (двумя роликами равных диаметров двумя роликами не равных диаметров);
на универсальных металлорежущих станках двумя цилиндрическими роликами установленными в резьбонакатную головку;
роликом и сегментом (планетарный способ накатывания) на специальных станках;
Они характеризуются переменной величиной радиального внедрения профиля резьбы инструмента и неодинаковой окружной скоростью пары инструментов входящих в комплект.
Данная классификация рассматривает все способы накатывания наружной резьбы винтовым инструментом с учётом их кинематических особенностей базирующихся на четырёх существенных признаках: направлении накатывания положении диаметральной плоскости в процессе накатывания направлении движения подачи и наклоне ниток резьбы инструмента. Наглядно классификация показана на рис. 4.
Рисунок 4. Классификация способов накатывания резьбы винтовым инструментом.
Анализируя представленные способы накатывания резьбы можно сделать вывод о том что способу накатывания резьбы резьбонакатными головками тангенциального типа присуще наибольшее число отличий связанных с кинематическими особенностями способов с касательным движением подачи и ограничением осевого перемещения инструмента. Он занимает центральное место среди всех способов накатывания резьбы винтовым инструментом.
Классификация позволила чётко дифференцировать все существующие способы накатывания резьбы с учётом кинематики относительного движения инструмента и заготовки в процессе накатывания резьбы.
Особенности процесса накатывания винтовых профилей
Процесс накатывания винтовых поверхностей представляет собой одну из разновидностей процессов поперечной накатки. Рассмотрим наиболее распространенный процесс накатывания резьбы роликами при котором из цилиндрических заготовок образуются детали с винтовым профилем. Заготовку обработанную под накатывание устанавливают между двумя или тремя вращающимися в одном направлении инструментами имеющими негативный профиль по отношению к профилю готовой детали. Один из инструментов (роликов) подается в радиальном направлении. Таким образом процесс накатывания поверхностей можно рассматривать как сочетание вдавливания в заготовку профиленакатных инструментов и прокатки возникающей при вращении заготовки.
Основными особенностями происходящей при накатке пластической деформации являются:
) возможность значительных деформаций без разрушений деформируемого металла (в том числе коррозионностойких жаропрочных и других специальных сталей и сплавов);
) существенное упрочнение поверхностных слоев в процессе деформации и связанное с этим повышение нагрузочной способности накатанных деталей.
Многие эксплуатационные свойства деталей машин в значительной степени обусловливаются геометрическими характеристиками микрорельефа и физико-механическим состоянием поверхностного слоя рабочих поверхностей деталей. При накатывании вследствие скольжения на контакте образуется поверхность обладающая оптимальной шероховатостью повышенной твердостью (наклепом) однородной микроструктурой и оптимальной текстурой прилегающих к поверхности слоев материала.
Прочность накатанного винтового профиля при статических нагрузках выше прочности профиля обработанного резанием примерно на 10% при испытании на растяжении и на 20–35% при испытании витков на срез.
Для высоконагруженных резьбовых деталей местом наибольшей концентрации напряжений являются впадины профиля. Поэтому для повышения усталостной прочности необходимо стремиться к минимальному параметру шероховатости поверхности таких участков; в этом отношении накатанный профиль обладает преимуществами перед нарезанным профилем.
Изменение физико-механических свойств поверхностного слоя металла в процессе накатывания профиля оказывает еще большее влияние на усталостную прочность деталей. Образующийся наклеп поверхностного слоя и текстура металла в значительной степени повышают циклическую прочность деталей. Этому способствуют также остаточные напряжения сжатия в поверхностном слое металла.
Для сравнения прочности при симметричном усталостном изгибе нарезанных и накатанных витков были испытаны образцы Трап 36 х 6 изготовленные из стали 45 в результате испытаний получены усталостные кривые с пределами выносливости 115 Мпа у нарезанного и 377 Мпа у накатанного профиля. Таким образом предел выносливости накатанного профиля в три раза выше чем у нарезанного профиля. Прочность накатанного винтового профиля при усталостном знакопеременном растяжении также в 35 раза выше чему обработанного резанием профиля.
Еще большее повышение усталостной прочности наблюдается у деталей изготовленных из легированных сталей с высоким пределом прочности при растяжении профиль на которых накатан после термической обработки свыше 39 HRC. В этом случае усталостная прочность резьбовых соединений повышается в несколько раз. Особое значение это приобретает например при изготовлении крепежа и резьбовых соединений для авиационной промышленности. Всем понятно к каким катастрофическим последствиям может привести разрушение резьбового соединения или выход из строя детали самолета. Поэтому при изготовлении болтов винтов и т.д. для авиационной промышленности из соображений безопасности запрещено нарезание резьбы а применяется только способ накатки.
Из приведенных данных следует что накатывание винтовых поверхностей улучшает физико-механические свойства металла заготовки и в большинстве случаев устраняет необходимость последующей термообработки; кроме того для накатанных деталей вместо высоколегированных сталей можно применять более дешевые углеродистые и малоуглеродистые стали. Это тоже подтверждает целесообразность широкого применения способа накатывания вместо обработки резанием.
Оборудование для накатывания резьбы на метизах и деталях машин.
Двухроликовые профиленакатные станки. Накатывание двумя или тремя приводными цилиндрическими роликами нашло широкое применение на машиностроительных заводах при изготовлении резьбы и других профилей повышенной точности. Преимущества способа: универсальность процесса широкий диапазон диаметров накатываемой резьбы (2–200 мм) и шагов (035–16 мм) отсутствие ограничения длины накатываемой резьбы (до 2000 мм и больше) высокий предел прочности обрабатываемых заготовок – до 1500 МПа высокая точность накатанной резьбы (поле допуска 4h и выше); относительная простота конструкции оборудования.
Заготовка установленная между роликами на ножевую опору или в центрах специального устройства будет вращаться в результате действия сил трения возникающих при соприкосновении роликов с заготовкой и возрастающих по мере внедрения профиля роликов в заготовку и образования на ней профиля негативного профилю на роликах.
В настоящее время серийно изготавливаются станки с давлением накатки от 5 до 60 т. В зависимости от модификации станок может быть оборудован ЧПУ вместо электродвигателей и трансмиссий применяются серводвигатели все команды задаются с пульта управления а результаты настройки станка вводятся в память и могут быть впоследствии отображены на дисплее. Точность и надежность станков позволяют применять их для накатки всех типов резьбы (в том числе конической резьбы) червяков мелкомодульных косозубых колес ниппелей цапф а также для обкатки клапанов. Станки легко оснащаются автоматическими механизмами загрузки и выгрузки деталей что позволяет широко применить их в автоматических комплексах и линиях для изготовления массовых деталей. При использовании автоматической загрузки станок накатывает до 1200 деталей в час.
Новой разработкой является встроенная в станки система контроля качества накатанной детали. Так как станки имеют точность повторения движения подвижной бабки в пределах 001 мм то причиной брака может служить только ошибка в диаметре детали под накатку. Система контроля измеряет перемещение подвижной бабки и если деталь имеет диаметр больше или меньше заданного то соответственно изменяется и ход подвижной бабки. Сигнал поступает на пульт управления загорается красная лампочка и в зависимости от конструкции станка деталь вручную или автоматически сбрасывается в бункер брака.
Стойкость резьбонакатного инструмента
На стойкость комплекта инструмента влияет ряд факторов зависящих от характеристик обрабатываемых заготовок (марки стали механических свойств микроструктуры) накатного инструмента (конструкции марки инструментального материала механических свойств режима термической обработки) состояния накатного оборудования и условий эксплуатации (режимов накатывания и охлаждения СОЖ).
Причины выхода из строя накатного инструмента следующие: изнашивание по вершинам витков выкрашивание витков рабочей части выкрашивание торцовых фасок инструмента.
Одним из важных мероприятий уменьшающих вероятность выкрашивания торцовых кромок инструмента является нанесение фаски на резьбовую часть заготовки. В зависимости от твердости материала наносится фаска с углом 15° – 20°. В результате этого уменьшается действие осевой силы на последний виток резьбы ролика в процессе пластической деформации. Если при накатке конструкционных сталей этой операцией можно пренебречь то при накатке материалов с пределом прочности более 800 МПа без фаски происходит выкрашивание профиля спустя короткое время.
Для накатки резьбы с классом прочности 12.9 а также деталей из титановых и жаропрочных сталей на никелевой основе применяются ролики из быстрорежущих и специальных сплавов. Титановые и никелевые сплавы часто используются в авиационной промышленности и трудно поддаются деформации. Традиционно используемые ролики с накатанной резьбой не дают достаточной стойкости и при накатке некоторых жаропрочных сталей выкрашиваются спустя 100 деталей. Использование специальных твердосплавных материалов позволяет накатывать материалы с пределом прочности до 1500 МПа с достаточной стойкостью.
Использование твердосплавных роликов целесообразно также во всех областях промышленности где применяются материалы с пределом прочности более 1000 МПа. Так например при накатке резьбы М 24 х 15 болта подвески колеса грузовика с классом прочности 12.9 стойкость достигает 15 тыс. штук одним комплектом до перешлифовки.
Методика расчета резьбонакатного инструмента повышенной стойкости
Резьбонакатывание является одним из наиболее прогрессивных способов изготовления резьб. Оно обеспечивает высокую производительность и качество обработки повышение статической и в особенности усталостной прочности накатанной резьбы по сравнению с нарезанной. Однако в некоторых случаях например при обработке крупных трапецеидальных резьб резьб на заготовках из труднообрабатываемых или предварительно упрочненных материалов резьбонакатывание становится экономически невыгодным из-за низкой стойкости инструмента.
Повышение стойкости резьбонакатного инструмента является сложной задачей требующей для своего решения комплексного конструкторско-технологического подхода. Наряду с совершенствованием технологии изготовления резьбонакатного инструмента для повышения его стойкости необходимо совершенствование его конструкции.
Преждевременный выход из строя резьбонакатного инструмента в значительной степени обусловлен неравномерностью нагружения его витков. Так например при накатывании резьб резьбонакатными головками или роликами с осевой подачей традиционные методики профилирования заборной части роликов (рис. 5) не обеспечивают равномерного нагружения всех ее витков что приводит к быстрому износу или разрушению наиболее нагруженного витка.
Рисунок 5. Зависимость мгновенной площади пятна контакта инструмента и заготовки от способа профилирования заборной части инструмента для накатывания наружных резьб:
- постоянный радиальный подъем (угол заборного конуса 10°); 2 - арифметическая прогрессия; 3 - парабола; 4 - окружность; 5 - гипербола; 6- предлагаемая методика.
Так как контактные напряжения прямо пропорциональны мгновенной площади пятна контакта инструмента и заготовки (МПК) научным коллективом Тульского университета разработана оригинальная методика профилирования заборной части инструмента для накатывания наружных и внутренних резьб произвольной формы профиля (треугольных трапецеидальных круглых и т.д.) основанная на расчете МПК каждого витка через площадь ее проекции на плоскость перпендикулярную оси вращения инструмента (рис. 6).
Рисунок. 6. Схема контакта инструмента и заготовки при накатывании наружной резьбы: а - пространственная модель; б - проекция пятна контакта на плоскость Х''OY''.
Расчет МПК при накатывании резьб и профилей может так же производиться путем геометрического моделирования процесса обработки в современных 3D CAD системах среднего и высшего уровней (рис. 7).
Рисунок 7. 3D модель накатывания треугольной резьбы роликом с осевой подачей.
Рис. 8. Эквивалентные напряжения по Мизесу в заготовке при накатывании резьбы 3-хроликовой аксиальной резьбонакатной головкой.
Резьбонакатной инструмент спроектированный по разработанной методике (рис. 6) имеет стойкость в 15 2 раза больше чем традиционный.
Рисунок 9. Ролики для накатывания наружной трапецеидальной резьбы.
Данная методика может использоваться для проектирования
цилиндрических резьбонакатных роликов (для аксиальных резьбонакатных головок 2-х и 3-х роликовых станков при накатывании с осевой подачей) затылованных роликов бесстружечных метчиков и плоских плашек а так же для совершенствования технологии накатывания резьб на станках с радиальной подачей.
1 Моя Технологическая часть.doc
1 Определение типа производства.
Тип производства определяется исходя из объёма выпуска и массы изделий:
N = 80000 штгодmдет = 036 кг.
Данная программа выпуска соответствует крупносерийному типу производства.
Определим такт выпуска форсунки:
где - действительный годовой фонд времени работы оборудования в часах;
- годовая программа выпуска в штуках;
- процент отсева деталей и узлов из-за брака (0 3%);
Для механической обработки:
2 Проектирование технологического процесса сборки узла.
2.1 Служебное назначение узла описание устройства и работы.
Форсунка предназначена для распыливания жидкого топлива в камере сгорания двигателя внутреннего сгорания. Распылённые капли воздуха образуют с воздухом горючую смесь. Чтобы ускорить воспламенение и сгорание капли топлива должны быть мелкими величиной в несколько микрометров. Мелкое распыление должно осуществляться на протяжении всего цикла впрыска. Для обеспечения хорошего сгорания топливо должно быть равномерно распределено по камере сгорания что осуществляется конструктивными элементами форсунки или воздушными вихрями в камере сгорания.
В зависимости от типа и формы камеры сгорания применяются различные форсунки но все их можно разделить на открытые и закрытые. В данной работе рассматривается форсунка закрытого типа. Основной особенностью форсунок закрытого типа является наличие запорного органа – иглы.
Устройство и работа узла. Форсунка показанная на рис. 1 состоит из следующих частей: корпуса форсунки 1 пружины 5 штанги 4 передающей давление от пружины игле корпуса распылителя 22 прижимной гайки 3.
Верхняя утолщённая часть иглы служит направляющей. Направляющая точно пригнана по отверстию корпуса распылителя. Запорный конус иглы садится на коническое седло в корпусе распылителя. На носке корпуса распылителя имеются сопловые отверстия. На верхнем торце корпуса распылителя находится кольцевая канавка обеспечивающая соединение топливного канала корпуса форсунки и топливных каналов распылителя.
Распылитель форсунки имеет удлиненный корпус в конце которого находятся обычное гнездо иглы и сопловые отверстия. Игла в цилиндрическом отверстии корпуса имеет подвижную посадку с минимальным зазором.
Углы запорных конусов иглы и корпуса распылителя изготовляют разными. Угол запорного конуса иглы 60º а угол конуса корпуса 58º45'. Наличие разности углов обеспечивает линейное контактирование поверхностей а также позволяет создать надежное уплотнение даже при небольших дефектах обработки поверхностей эксцентричности между посадочным конусом и направляющей иглы и корпуса и при возникновении деформаций (тепловых монтажных).
Топливо от топливного насоса по трубопроводу высокого давления подводится в канал и по каналу поступает в распылитель. Благодаря высокому давлению создаваемому насосом игла поднимается со своего гнезда преодолевая сопротивление пружины и топливо впрыскивается в камеру сгорания.
Топливо просочившееся вдоль иглы смазывает направляющую поверхность иглы и корпуса и накапливается в полости где установлена пружина форсунки. Отвод топлива осуществляется через отверстие в колпаке форсунки. Пружина работает в среде дизельного топлива что защищает её от коррозии уменьшает вибрационные нагрузки и увеличивает долговечность. Поэтому одной из важных операций контроля является надежное уплотнение колпака форсунки.
Штанга имеет радиальный зазор в корпусе форсунки; в нижней части её есть углубление позволяющее заходить туда хвостовику иглы; верхняя часть штанги прижата к нижнему торцу пружины.
Металлические фильтры в распылителе или во впускных каналах корпусов устанавливаются тогда когда возможно загрязнение топлива окалиной трубопроводов или другими загрязнениями. Эти фильтры должны быть достаточно прочными чтобы противостоять разрушению волнами высокого давления возникающими при впрыске топлива. [14] [15]
2.2 Критический анализ технических требований. Обоснование метода достижения точности по отдельным техническим требованиям узла.
Таблица 1.1 – Анализ технических требований.
Техническое требование
Возможные неисправности при невыполнении
Все детали форсунки и каналы корпуса форсунки перед сборкой должны быть чистыми. Корпус и иглу распылителя тщательно промыть профильтрованным дизельным топливом любой марки по ГОСТ 305-82.
Засорение каналов 02 мм что приведет к нарушению работы форсунки.
Гайка распылителя поз.3 должна навёртываться на резьбу корпуса форсунки свободно от руки.
Затруднит процесс сборки резьбового соединения гайки и корпуса форсунки.
Касание диаметра А корпуса распылителя с гайкой распылителя не допускается. Минимальный зазор 005мм.
Смещение отверстий распылителя относительно днища поршня при установки форсунки на двигатель. Смещение не позволит двигателю развивать необходимую мощность.
Испытания форсунок проводить на профильтрованном дизельном топливе ГОСТ 305-82 или на профильтрованной технологической жидкости. Вязкость топлива или тех. Жидкости должна быть 3-6мм2с при температурных условиях испытаний. Температура окружающей среды при испытаниях должна быть 20 С.
Не правильная настройка форсунки.
Опрессовочный стенд должен быть герметичным. При установке на станд специальной заглушки время падения давления с 30 Мпа до 295Мпа должно быть не менее 3 минут. Проверять не реже одного раза в смену.
Не правильная настройка форсунки. Не выполнение требований техники безопасности.
Форсунка должна быть герметичной по запирающему конусу распылителя. Герметичность проверять созданием в форсунке давления топлива на 10-15 Мпа меньше номинального давления начала впрыскивания. При этом на носике распылителя допускается появление топлива не отрывающегося под действием собственной массы в течение 15 секунд.
Не выполнение техники безопасности при работе двигателя. Повышенный расход топлива.
Качество распыливания проверять на опрессовочном стенде прокачиванием топлива через форсунку отрегулированную на номинальное давление начала впрыскивания при частоте впрыскиваний 60-80 в мин.Распыленное топливо выходящее из форсунки должно быть туманообразным без сплошных струек и легко различимых местных сгущений при визуальном наблюдении.
Не выполнение проверки качества форсунки
Течь и увлажнение топливом по наружным поверхностям в местах уплотнений и соединений не допускаются. Отсутствие течи и увлажнения по наружным поверхностям в местах уплотнений и соединений полости высокого давления контролировать одновременно с проверкой герметичности по запирающему конусу распылителя. Допускается проверять герметичность форсунок по времени падения давления топлива от 20Мпа до 18Мпа. Время падения давления должно быть не менее 5 сек.
Анализ технических требований узла позволяет установить в какой мере то или иное требование обеспечивает выполнение изделием его служебного назначения а так же что произойдёт если данное требование будет нарушено.
Анализ технических требований позволил составить две размерные цепи и выявить в них соответствующие замыкающие звенья:
Зазор между хвостовиком корпуса распылителя и гайкой распылителя формируется как замыкающее звено размерной цепи А.
Несоосность малого наружного диаметра корпуса распылителя относительно посадочного диаметра корпуса форсунки формируется как замыкающее звено размерной цепи Б.
Цепи А и Б представлены на первом листе графической части проекта. [12]
Описание звеньев размерной цепи А.
- расстояние от оси поверхности малого диаметра распылителя до этой цилиндрической поверхности.
- расстояние от оси поверхности малого диаметра распылителя до оси посадочной поверхности распылителя.
- расстояние от оси посадочной поверхности распылителя до оси отверстия гайки распылителя.
- расстояние от оси отверстия гайки распылителя до оси цилиндрической поверхности малого диаметра гайки распылителя.
- расстояние от оси цилиндрической поверхности малого диаметра гайки распылителя до этой поверхности.
- расстояние от поверхности малого диаметра распылителя до поверхности малого диаметра гайки распылителя.
Таблица 2.2 – Расчет размерной цепи
Характе-ристика звена
Размер звена с отклонениями
Малый диаметр распылителя
Малый d-р распыл-ля;
Большой d-р распылителя .
Большой внутр. D-р гайки.
Большой внутр. D-р гайки;
Меньший внутр. D-р гайки.
Малый D-р распыл-ля;
Малый d-р гайки распылителя
Расчёт размерной цепи.
Номинальный размер замыкающего звена:
где - сумма номинальных размеров увеличивающих звеньев;
- сумма номинальных размеров уменьшающих звеньев;
Координата середины поля допуска замыкающего звена:
где - сумма координат середин полей допусков увеличивающих звеньев;
- сумма координат середин полей допусков уменьшающих звеньев.
Допуск замыкающего звена:
где - сумма допусков звеньев.
Верхнее и нижнее предельные отклонения замыкающего звена:
Таким образом . По техническим требованиям размер замыкающеего звена должен быть мм.
Следовательно требуемая точность может быть обеспечена методом полной взаимозаменяемости. [12]
Таблица 2.3 – Расчёт размерной цепи [12]
Значения формирующихся
Больший d-р распыл-ля.
Больший d-р распыл-ля;
Больший d-р корпуса.
Больший d-р корпуса;
Малый d-р распыл-ля.
Расчёт размерной цепи
Метод полной взаимозаменяемости
где - сумма координат середин полей допусков увеличивающих
- сумма координат середин полей допусков уменьшающих
ESБ=Б+ТБ2=> заданного значения
EIБ=Б-ТБ2= заданного значения
Полученные значения отклонения от соосности малого диаметра распылителя относительно посадочной поверхности корпуса форсунки менее требуемого значения – 015 мм. Следовательно требуемая точность замыкающего звена может быть обеспечена методом полной взаимозаменяемости. [12]
2.3 Методы проверки технических требований собранного узла.
Форсунка проверяется на работоспособность и соответствие требованиям на специальном стенде где она обкатывается в условиях приближенных к реальным.
Форсунка на стенде проверяется на: [11]
- герметичность по запирающему конусу в местах соединений областей высокого давления;
- качество распыливания;
- контроль и регулирование давления начала впрыска топлива;
- гидравлическую плотность;
2.4 Анализ технологичности конструкции узла.
К общим требованиям технологичности конструкции относятся следующие:
) Доступность мест сборки;
)Узел разбивается на отдельные сборочные единицы; сборочные едини-
цы собираются параллельно;
) Геометрические размеры и соосность обеспечивается методом полной
К не технологичным элементам относятся: [20]
) Корпус распылителя и игла распылителя соединяются методом
) Операции комплектования регулирования и контроля осуществляют-
) Отсутствуют стандартные крепёжные детали;
2.5 Технологическая схема сборки.
Изучение конструкции узла завершится разработкой технологической схемы сборки. Технологические схемы отражают структуру и последовательность процесса сборки. В данном проекте сборка узловая объектом сборки являются его составные части.
Составными частями изделия являются сборочные единицы (группы) сборочные единицы первого второго и более высоких порядков (подгруппы первого второго и т.д. порядков). На схеме сборки каждый элемент узла обозначается прямоугольником в соотношении LB=2 разделённым на три части. В верхней части прямоугольника приводят наименование детали в левой нижней части – номер по спецификации детали а в правом нижнем – количество деталей входящий в данный узел. В обозначении сборочной единицы указываем её порядок и номер базовой детали справа – количество сборочных единиц в узле. [10]
Процесс сборки изображаем на технологической схеме горизонтальной линией направленной от базовой детали к изделию. Сверху располагаем в порядке последовательности сборки условные обозначения всех непосредственно входящих в узел деталей а снизу – последовательно входящие в узел сборочные единицы.
При необходимости технологическую схему сборки снабжаем надписями поясняющими характер сборочных соединений и выполняемый при сборке контроль. Например: запрессовать смазать и др.
2.6 Разработка маршрутного техпроцесса сборки с выбором оборудования
По разработанной технологической схеме сборки установлена последовательность и содержание технологических операций и переходов выбрано оборудование инструмент приспособление и др. технологическое оснащение. Содержание операций установлено в зависимости от выбранного типа производства и такта выпуска. При крупносерийном производстве при поточной форме организации содержание операции должно быть таким чтобы её длительность была равна такту выпуска или кратна ему. Оценку длительности операций производим нормированием или использованием данных базового (заводского) типового технологического процесса. [6]
Спроектированный технологический процесс сборки узла представляем в виде заполненной маршрутной карты.
2.7 Нормирование технологического процесса сборки.
Нормирование технологического процесса сборки проводили по рекомендациям общемашиностроительных нормативов времени на выполнение сборочных работ. [22] [23]
Таблица 2.4 – Нормирование технологического процесса сборки.
Наименование операции
Взять форсунку из тары
Установить форсунку в приспособление зажимное и закрепить винтом
Отрегулировать пружину форсунки регулировочным винтом на номинальное давление начала впрыска топлива
Закрутить гайку контрящую до упора
Затянуть гайку контрящую М=3±05кг с*м
Проверить герметичность при давлении на 10-15кг см2 меньше номинального при этом на носике распылителя допускается появление топлива не отрывающегося под действием собственной массы в течение 15 сек.
Проверить герметичность форсунок по времени падения давления топлива от 20 МПа до 18 МПа. Время падения не менее 5с.
Проверить подвижность иглы распылителя. При прокачивании топлива с частотой впрысков 30-40 в мин впрыск должен сопровождаться характерным звуком.
Проверить качество распылителя при частоте впрысков 60-80 в мин. Распылённое топливо должно быть туманообразным без сплошных струек и легко различимых мест сгущений
Открепить форсунку и установить в тару
Определение штучного времени:
Тшт = Т1 + Т2 + Т3 + Т4 + Т5 + Т6 + Т7 + Т8 + Т9 + Т10 = (1.6)
= 008 +025+033+017+017+033+025+1+1+017=375 мин
2.8 Организация работы участка сборки.
Конструкция форсунки наличие открытого доступа ко всем поверхностям небольшая масса собираемого изделия но большая программа указывают на то что необходимо применить непоточную подвижную форму сборки. Данная форма сборки характеризуется тем что изделие периодически перемещяется от одного рабочего места на другое.
Сборочные операции выполняют отдельные рабочие или бригады рабочих специализирующиеся на определенных работах. Окончив выполнение всех переходов составляющих операцию рабочий перемещает собираемый объект к следующему рабочему месту. Для компенсации колебаний затрат времени на выполнение сборочных операций между смежными рабочими местами имеются межоперационные заделы собираемых объектов. Они позволяют сборщику закончившему операцию раньше сборщика работающего на предшествующей операции продолжить работу за счет задела. [21]
Рабочие места оборудованы необходимыми приспособлениями сборочным и контрольно-измерительным инструментом стеллажами для сборочных единиц и деталей.
3. Технологический процесс изготовления детали.
3.1 Служебное назначение детали и её поверхностей характеристика
Назначение корпуса форсунки – удерживать распылитель в нужном положении в камере сгорания двигателя и обеспечивать подвод топлива к нему. Корпус служит каналом для подачи топлива к распылителю также отверстие в корпусе форсунки служит направляющей штанги. Т.е. корпус форсунки определяет относительное положение деталей входящих в него.
Корпуса современных форсунок имеют уменьшенный диаметр что облегчает их установку между клапанами в головке цилиндров. Благодаря меньшей поверхности нагрева деталей форсунка меньше поглощает тепла от сгорания топлива.
В связи с тем что головки цилиндров имеют значительную высоту изготавливают форсунки с длинным корпусом. У форсунок сложностью является передача усилия от пружины на иглу: оно передаётся через удлиненную штангу.
Между штангой и корпусом форсунки – зазор для устранения бокового давления на иглу.
На основании служебного назначения детали производится классификация поверхностей. Классификация поверхностей детали по служебному назначению упрощает анализ технологичности детали и обоснование назначения технических требований. [14]
Рис 2. – Поверхности детали.
Таблица 3.1 – Классификация поверхностей корпуса форсунки.
Наименование поверхности
Служебное назначение поверхности
Фаска наружная 1.6х45°
Наружная резьба М14х15-6g
Вспомогательная конструкторская
Служит для установки накидной гайки трубопровода высокого давления
Фаска наружная 4х45°
Наружная поверхность
Свободная поверхность
Служит для крепления форсунки в головке блока цилиндров двигателя
Торцовая поверхность
Наружная цилиндрическая поверхность 30 мм
Торцевая поверхность
Основная конструкторская база
Служит для обеспечения правильного положения детали в двигателе
Наружная цилиндрическая поверхность 24 мм
Свободная пове рхность
Служит для облегчения сборки
Наружная цилиндрическая поверхность 25 мм
Наружная цилиндрическая поверхность 247 мм
Фаска наружная 6х30°
Наружная цилиндрическая поверхность 18 мм
Наружная резьба М19х075-6g
Вспомогательная конструкторская база
Служит для закрепления гайки на корпус форсунки
Топливоподводящее отверстие 2 мм
Исполнительная поверхность
Служит для подачи топлива
Служит для создания герметичного контакта с фильтром
Служит для направления пружины
Служит для размещения пружины
Служит для размещения тарелки штанги
Топливоподводящее отверстие 25 мм
Наружняя цилиндрическая поверхность 28 мм
Служит для размещения иглы
Служит для размещения колпачка защитного
Кольцевая канавка 19 мм.
Фаска наружная 1х45°
Наружная радиусная поверхность детали R2
Внутренная радиусная поверхность детали R1
Вспомогательная конструкт-ая база
Служит для установки колпачка
При этом некоторые поверхности выполняют определённое технологическое назначение: канавки – для выхода инструмента фаски – для облегчения сборки.
Характеристика материала детали.
Деталь – корпус изготавливается из конструкционной легированной
стали 40Х ГОСТ 1050 – 88.
Химический состав %: углерод С – 0.36 0.44
кремний Si – 0.17 0.37
марганец Mn – 0.5 0.8
Остальное – железо Fe.
Механические свойства: предел прочности
относительное удлинение 17 %
твёрдость кованой заготовки 187 207 НВ.
Технологические свойства.
Сталь 40Х трудносвариваемая склонна к отпускной хрупкости. [14]
3.2 Критический анализ технических требований к детали.
Исходя из служебного назначения корпуса форсунки к нему предъявляются технические требования:
Таблица 1.8 – Анализ технических требований на деталь. [8]
ТТ размеры (допустимые предельные отклонения) шероховатость
Возможные неисправности в работе узла при невыполнении ТТ
7..207НВ кроме поверхности торца для размещения штанги
Твёрдость на поверхности торца для размещения штанги проверять на участке 13 16 мм
Допускается прокалка двух витков резьбы.
Неравномерность припусков при механической обработке.
На поверхности П допускается след от инструмента.
Покрытие: Хим. Фос. пасс. кроме поверхностей: торца для размещения штанги и отверстия для размещения иглы
Отсутсвие плотного прилегания торца для размещения штанги к его отверстию.
3.3 Методы и схемы проверки ТТ.
Для проверки технического требования (допустимая погрешность измерений 002 мм вариация показаний не более 0006мм) используется контрольное приспособление.
Порядок работы: Глубиномер настраивать по мере установочной 8905-0835; 8905-1063 с учетом фактического размера. Деталь считается годной при отклонении стрелки индикатора от 0 до 03 мм. [1]
Рис 3. – Приспособление контрольное для проверки перпендикулярности
отверстия М10x125 относительно поверхности 17мм.
3.4 Анализ технологичности конструкции детали.
Корпус форсунки - деталь сложной несимметричной формы; для её обработки требуется специальное: оборудование приспособления режущий инструмент. Деталь достаточно прочная и жёсткая (отношение длины к диаметру меньше 8). Некоторые поверхности трудно доступны для обработки.
В конструкции детали присутствуют глубокие отверстия. Одно из отверстий малого диаметра для изготовления которого требуется специальное оборудование и режущий инструмент.
В конструкции предусмотрены технологические канавки простой формы для выхода инструмента.
Точность наивысшая до 7 квалитета Изготовление детали требует доводочных операций на поверхности - 15 (Ra = 0080) что однако необходимо согласно служебному назначению. Глубокое отверстие 25 мм необходимо исходя из служебного назначения хотя имеет технологические трудности при изготовлении так как необходим специальный режущий инструмент – сверло ружейное.
В её конструкции присутствует достаточное число сложных для обработки поверхностей доступ инструмента к обрабатываемым поверхностям затруднён а требования по точности и шероховатости поверхностей являются жесткими но необходимыми согласно служебному назначению.
Оценка технологичности выполнена по ГОСТ 14.205 – 83 (СТ СЭВ 2063–79) – технологичность конструкции изделий. В результате анализа конструкции детали – корпуса были выявлены технологичные и нетехнологичные элементы которые оказывают значительное влияние на себестоимость изделия трудоёмкость его изготовления. В целом деталь – корпус является технологичной. [15]
3.5 Выбор и технико-экономическое обоснование метода получения
В действующем технологическом процессе деталь – корпус изготавливается с помощью заготовки из круглого проката что целесообразно для крупносерийного производства.заготовки Мз.п. = 07031 кг. Для анализа рассмотрим также метод получения заготовки штамповкой на горизонтально-ковочных машинах (ГКМ). Сравним эти методы по технико – экономическим показателям. Коэффициенты для расчётов выберем по методическим указаниям. [5]
получение заготовки из круглого проката;
штамповка на горизонтально-ковочных машинах (ГКМ).
Сравним себестоимость получения заготовки этими способами.
Себестоимость заготовки изготовленной из проката:
Себестоимость заготовки полученной штамповкой на ГКМ:
где - базовая стоимость 1 тонны заготовок руб;
- базовая стоимость одной тонны отходов;
- коэффициенты зависящие от класса точности группы
сложности массы марки материала и объема производства заготовок;
Сотх – базовая стоимость 1 тонны отходов
Себестоимость заготовки изготовленной на ГКМ:
Себестоимость механической обработки:
где - стоимость снятия 1 кг стружки;
Себестоимость механической обработки заготовки изготовленной из проката:
Себестоимость механической обработки заготовки изготовленной на ГКМ:
Себестоимость изготовления детали:
Себестоимость изготовления детали из заготовки изготовленной из проката:
Себестоимость изготовления детали из заготовки изготовленной на ГКМ
Экономический эффект:
Технико – экономические расчёты подтверждают что получение заготовки из проката значительно эффективней чем изготовление детали на ГКМ следовательно способ получения заготовки – из проката.
Рис. Заготовка из проката.
3.6 Разработка технологического маршрута обработки с выбором
оборудования и оснастки баз и схем базирования. [3]
Таблица. Технологический маршрут с выбором оборудования и оснастки.
Модель станка инструменты содержание опер.
Горизонтальный многошпиндельный полуавтомат токарный модели
Б 240-6к резец проходной сверло центровочное.
Точить заготовку из прутка со стороны конуса 60°.
Токарный полуавтомат 1Б 240П-6 сверло центровочное 30 резец проходной Т5К10 резец подрезной Т5К10 сверло 75.
Точить поверхность центровать выдерживая размеры 12 и подрезать торец выдерживая размер 57мм. Точить канавку под уплотнительное кольцо.
Круглошлифовальный AD15-700 ERK-45 круг шлифовальный. Шлифовать поверхности 253-005 и
Фрезерная ДФ96 приспособление для фрезерования фреза 35. Фрезеровать лыски с двух сторон одновременно.
Фрезерный 6М13П приспособление для фрезерования резец Т5К10. Фрезеровать лыску на 30 выдерживая размер 14±0135
Фрезерный 6М13П приспособление для фрезерования фреза 68 резец Т5К10. Фрезеровать лыску выдерживая размер 11-018.
Фрезерный 6М13П приспособление для фрезерования фреза оправка для фрезы. Фрезеровать наклонную площадку под дренажное отверстие выдерживая
Агрегатно-сверлильный
Приспособление для зенкования; цанга 75; цековка 135; Цанга 46; Сверло 46; Зенкер – развертка 48; Цанга 6; Развертка 4915; Цанга 75; Зенковка коническая 60°; втулка; Развертка 501-0007.
Цековать торец со стороны М14х15-6g; Сверлить топливопроводящее отверстие 46; зенкеровать отверстие 48+005; развернуть предварительно 49+0035; Зенкеровать конус 60°8мм; Притупить острую кромку в конусе 60°; развернуть окончательно 5.
Агрегатно-сверлильный 1ХМА 1033 приспособление для сверления Метчик М10х125-6Н Цековка 17 с ввертышем М10х125 Цанга 12. Обработать резьбовое отверстие М10х125 цековать торец 17.
Круглошлифовальный 3М151АН-102 центр передний центр задний круг шлифовальный. Шлифовать поверхность 1298-009.
Круглошлифовальный 3М152 МВФ2 Центр передний Центр задний КМ4 круг шлифовальный. Шлифовать по профилю поверхности 18-0084184-005 247-052 25-010.
Резьбонакатной UPWS 1625 Ролик накатной
Сп 19х 075-6g. Накатать резьбу Сп 19х 075-6g.
М14х15-6g. Накатать резьбу М14х 15-6g.
Приспособление для развертывания; цанга 8; развертка 793; втулка 12; цанга 18; сверло 18; цековка 55; втулка 75; сверло канавочное 75; втулка 55; развальцовка 55.
Развернуть отверстие 793+0058; сверлить два штифтовых отверстия 18+008 последовательно; цековать донышко 55; сверлить канавку на торце в отверстие 75; раскатать донышко 55.
Агрегатно-сверлильный 1ХА140 Цанга 18 Сверло специальное 18. Сверлить топливоподводящее отверстие 18.
Агрегатно-сверлильный 1ХА140 Цанга 24 Сверло специальное 24. Сверлить дренажное отверстие 24.
Плоскошлифовальный 3Е756 Кассета для шлифования Втулка ремонтная М19х075-7Н. Шлифовать уплотнительный торец детали.
Выбираем 3 основных схемы базирования для проетируемого ТП они показанны на эскизах в операциях: 010 025 080.
3.7 Расчет и выбор припусков.
Расчёт припуска на обработку наружного диаметра 30(-035) h14.
Припуск на черновую обработку:
- высота микронеровностей поверхности образованная на предыдущем технологическом переходе;
- глубина дефектного слоя (обезуглероженного);
- пространственные отклонения обрабатываемой поверхности.
где И – изогнутость оси заготовки в расчетном сечении;
- кривизна проката мкммм;
- расстояние в мм от расчетного сечения до места крепления заготовки.
- погрешность установки заготовки на станке при выполняемом переходе.
где - погрешность базирования; - погрешность закрепления.
Таким образом минимально необходимый припуск на черновую обработку составляет: мкм.
Таблица. Расчет предельных размеров для поверхности 30(-035) h14. [13]
Наименование переходов
Припуск минимальный Zimin мкм
Припуск максимальный Zimax мкм
Допуск на припуск ITzi мкм
Наименьший предельный размер мм
Наибольший предельный размер мм
Определение предельных размеров:
Наименьший предельный размер после чернового обтачивания равен:
Действительное значение припуска минимального:
Наибольший предельный размер:
Наибольшее значение припуска на чистовое обтачивание:
Наименьший расчетный предельный размер заготовки:
Фактическое значение припуска минимального:
Наибольший предельный размер заготовки:
Задание рассчитанных размеров на операционных эскизах и чертеже
Для последнего перехода операционный размер должен соответствовать чертежному:
Номинальный размер заготовки следует назначить так чтобы при предусмотренных по ГОСТ 7505-89 отклонениях () предельные размеры соответствовали расчетным. мм (1.20)
Расчёт припуска на обработку наружного диаметра h12.
Припуск на чистовое обтачивание.
Допуск на размер чистового обтачивания
Погрешность установки так как черновое и чистовое точение выполняются без переустановки.
Припуск на черновое шлифование.
Для предварительного шлифования:
Припуск на чистовое шлифование.
Погрешность установки так как черновое и чистовое точение выполняются без переустановки.
Таблица. Расчет предельных размеров для поверхности h14. [13]
Наименьший предельный размер после чистового шлифования равен:
Наибольший предельный размер после чистового шлифования равен:
Наименьший предельный размер после чернового шлифования равен:
Наибольший предельный размер после чернового шлифования равен:
Наибольшее значение припуска на черновое шлифование:
Наименьший предельный размер после чистового обтачивания равен:
Наибольший предельный размер после чистового обтачивания равен:
Максимальная величина припуска:
Допуск на припуск (проверка правильности расчетов):
Для последнего перехода (чистового шлифования) операционный размер должен соответствовать чертежному: .
Для чернового шлифования в качестве номинального принимаем размер:
Для чистового обтачивания в качестве номинального принимаем размер:
Для чернового обтачивания в качестве номинального принимаем размер:
Номинальный размер заготовки следует назначить так чтобы при предусмотренных по ГОСТ 7505-89 отклонениях () предельные размеры соответствовали расчетным. [13]
Расчёт припуска на обработку торцевой поверхности h14.
Наибольшее значение припуска на чистовое шлифование:
3.8 Расчёт и выбор режимов резания. Техническое нормирование.
Операция 010 – автоматная – токарная. Станок модели 1Б240-6к.
Позиция 1.1: Точить заготовку из прутка со стороны конуса 60°. [15]
Диаметр сверления D=7.2 мм;
Длина резания L=42 мм;
Инструмент: сверло центровочное материал режущей части – Р6М5;
Технические характеристики станка:
Диапазон частот вращения шпинделя: n = 80 ÷ 1120 мин-1;
Подача шпинделя 0056 – 25 ммоб.
Мощность привода главного движения: 15 кВт.
Расчёт для сверления.
Глубина сверления: мм (1.22)
Подача: выбираем максимально допустимую по прочности сверла подачу.
Принятое значение S = 0.3 ммоб.
где - коэффициент и показатели в формуле скорости резания при сверлении;
- диаметр сверла (мм);
- стойкость инструмента (мин);
- общий поправочный коэффициент учитывающий фактические условия резания.
- коэффициент на обрабатываемый материал;
- коэффициент на инструментальный материал;
- коэффициент учитывающий глубину сверления.
где и НВ – фактические параметры характеризующие обрабатываемый материал;
- коэффициент характеризующий группу стали по обрабатываемости и показатель степени .
; = 1.0; = 10; ; q = 0.4; y = 0.5; m = 0.2; Т=50 мин.
Частота вращения шпинделя:
где d – наибольший диаметр обрабатываемой поверхности.
обмин. Принимаем с учётом частот вращения шпинделя станка 140 обмин.
Фактическая скорость резания: ммин. (1.27)
Крутящий момент и осевая сила:
- коэффициент учитывающий фактические условия обработки.
– показатель степени.
Основное машинное время.
- основное машинное время затрачиваемое на изменение формы плотности или состояния поверхностного слоя заготовки.
где - длина обрабатываемой поверхности;
n – частота вращения инструмента;
Позиция 1.2: Точить заготовку из прутка со стороны конуса 60°. [15]
Диаметр резания D=30-035 мм
Длина резания L=603 мм;
Инструмент: проходной резец материал режущей части – Р6М5;
Диапазон частот вращения шпинделя: n = 80 ÷ 1120 обмин;
Подача: выбираем максимально допустимую по прочности резца подачу.
Скорость резания: (1.33)
где - коэффициент и показатели в формуле скорости резания при точении;
t - глубина резания (мм);
- коэффициент учитывающий состояние поверхности.
; = 1.0; = 085; ; х = 0.15; y = 0.35; m = 0.2; Т=60 мин.
Фактическая скорость резания: ммин.
Тангенциальная и осевая составляющие силы резания:
; y = 0.75; ; y = 0.5.
Позиция 1.3: Точить заготовку из прутка со стороны конуса 60°. [15]
Длина резания L= 14мм;
Инструмент: подрезной резец материал режущей части – Р6М5;
Принятое значение S = 0.5 ммоб.
; = 1.0; = 085; ; y = 0.35; m = 0.2; х=015; Т=60 мин.
Тангенциальная и радиальную составляющие силы резания:
Позиция 4.1: Зенковать заготовку из прутка со стороны конуса 60°. [15]
Диаметр зенкования D=7.5 мм;
Длина зенкования L= 25мм;
Инструмент: зенкер материал режущей части – Р6М5;
Расчёт для зенкования.
Глубина зенкования: мм
Подача: выбираем максимально допустимую по прочности зенкера подачу.
где - коэффициент и показатели в формуле скорости резания при зенковки;
- диаметр зенкера (мм);
- коэффициент учитывающий глубину зенковки.
Позиция 4.2: Точить заготовку из прутка со стороны конуса 60°. [15]
Диаметр резания D=15мм
Длина резания L=13 мм;
; = 1.0; = 085; ; q = 0.4; y = 0.5; m = 0.2; Т=60 мин.
Позиция 4.3: Точить заготовку из прутка со стороны конуса 60°. [15]
Диаметр резания D=25 мм
Длина резания L= 55мм;
Инструмент: резец материал режущей части – Р6М5;
Принятое значение S = 0.05 ммоб.
Тангенциальная и радиальная составляющие силы резания:
Позиция 5: Точить заготовку из прутка со стороны конуса 60°. [15]
Диаметр резания D=137мм
Длина резания L=6 мм;
Мощность привода главного движения: 15 КВт.
Принятое значение S = 0.035 ммоб.
Позиция 6: Точить заготовку из прутка со стороны конуса 60°. [15]
Длина резания L= 182мм;
Инструмент: отрезной резец материал режущей части – Р6М5;
Принятое значение S = 0.1 ммоб.
Сумма мощностей на всех операциях не должна превышать мощность привода главного движения: .
Операция 050 – агрегатно - сверлильная. Станок мод. 1ХМА-1033.
Позиция 2. Обработать резьбовое отверстие М10х125 цековать торец 17. [15]
Инструмент: центровка материал режущей части – Р6М5;
Обрабатываемый материал сталь 40Х (НВ 230; )
Диапазон частот вращения шпинделя: n = 50 ÷ 1250 обмин;
Мощность привода главного движения: 185 кВт.
Расчёт для зацентровки.
Глубина центрования: мм
Подача: выбираем максимально допустимую по прочности центровки подачу.
Принятое значение S = 0.15 ммоб.
- диаметр центровки (мм);
- коэффициент учитывающий глубину центрования.
обмин. Принимаем с учётом частот вращения шпинделя станка 500 обмин.
Позиция 3. Обработать резьбовое отверстие М10х125 цековать торец 17. [15]
Инструмент: сверло материал режущей части – Р6М5;
Глубина сверления: мм
Позиция 4. Обработать резьбовое отверстие М10х125 цековать торец 17. [15]
Позиция 5. Обработать резьбовое отверстие М10х125 цековать торец 17. [15]
Инструмент: цековка материал режущей части – Р6М5;
Глубина цекования: мм
Подача: выбираем максимально допустимую по прочности цековки подачу.
Принятое значение S = 0.08 ммоб.
где - коэффициент и показатели в формуле скорости резания при цековании;
- диаметр цековки (мм);
- коэффициент учитывающий глубину цекования.
обмин. Принимаем с учётом частот вращения шпинделя станка 250 обмин.
Позиция 6. Обработать резьбовое отверстие М10х125 цековать торец 17. [15]
Инструмент: ролик резьбонакатной материал режущей части – Р6М5;
Расчёт для нарезания резьбы.
Глубина нарезания: мм
Подача: выбираем максимально допустимую по прочности ролика подачу.
Принятое значение S = 1.25 ммоб.
где - коэффициент и показатели в формуле скорости резания при нарезании;
- диаметр ролика резьбонакатного (мм);
- коэффициент учитывающий глубину нарезания.
обмин. Принимаем с учётом частот вращения шпинделя станка 100 обмин.
Операция 065 – резьбонакатная. Станок мод. UPWS 1625.
Накатать резьбу М19х075-6g. [15]
Инструмент: Ролик накатной М19х 075-6g;
Диапазон частот вращения шпинделя: n = 20 ÷ 90 обмин;
Мощность привода главного движения: 51 кВт.
Расчёт для резьбонакатки.
Принятое значение S = 008 ммоб.
Шаг резьбы : Р = 008
- коэффициент учитывающий качество обрабатываемого материала;
- коэффициент учитывающий материал режущей части инструмента;
- коэффициент учитывающий способ нарезания резьбы.
; = 1.0; = 10; ; y = 0.30; m = 0.11; х = 070; Т=80 мин.
Мощность привода главного движения 51 кВт достаточна.
Операция 070 – резьбонакатная. Станок мод. UPWS 1625.
Накатать резьбу М14х15-6g. [15]
Инструмент: Ролик накатной М14х15-6g;
обмин. Принимаем с учётом частот вращения шпинделя станка 400 обмин.
Операция 080 – агрегатно – сверлильная. Станок модели 1ХА 140.
Сверлить топливоподводящее отверстие 18. [15]
Диаметр сверления D=18 мм;
Длина резания L=80 мм;
Инструмент: сверло специальное материал режущей части – Р6М5;
Обрабатываемый материал сталь 40Х (НВ 230; ).
Диапазон частот вращения шпинделя: n = 50 ÷ 1500 мин-1;
Принятое значение S = 015 ммоб.
обмин. Принимаем с учётом частот вращения шпинделя станка 1330 обмин.
Мощность привода главного движения 185 кВт достаточна.
Операция 085 – агрегатно – сверлильная. Станок модели 1ХА 140.
Сверлить топливоподводящее отверстие 24. [15]
Диаметр сверления D=24 мм;
Длина резания L=43 мм;
обмин. Принимаем с учётом частот вращения шпинделя станка 1120 обмин.
3.9 Средства механизации и автоматизации технологического процесса
Средством механизации технологического процесса обработки корпуса форсунки является станок токарный полуавтомат 1Б240-6к. Токарный полуавтомат 1Б240-6к применяют для обработки детали со стороны резьбовой поверхности М14х15-6g. Он позволяет выполнять 5 или 6 переходов за одну операцию что приводит к значительному снижению штучного времени на изготовление детали и снижению себестоимости готовой детали. [20]
Принцип работы станка:
Станок работает по принципу последовательной обработки детали в нескольких позициях. Число позиций соответствует числу шпинделей станка. Одна из позиций является загрузочной. На полуавтомате обработанная деталь в этой позиции извлекается из зажимного патрона а вместо неё устанавливается новая заготовка. Шпиндельный барабан в котором смонтированы рабочие шпиндели несущие обрабатываемые детали из загрузочной позиции поворачивается последовательно на 16 часть оборота. Каждый поворот шпиндельного барабана соответствует переходу обрабатываемой детали в следующую позицию. Обработка ведётся на всех позициях одновременно инструментами установленными на поперечных суппортах и гранях одного общего продольного суппорта. Число граней продольного суппорта соответствует числу шпинделей станка. В загрузочной позиции полуавтомата поперечные суппорты не устанавливаются.
В качестве нулевой точки цикла принят конец рабочего хода. В этой точке нулевая риска на кулаках распредвала находится сверху а кулачок командоаппарата включает быстрое вращение распредвала. Происходит быстрый отвод суппортов в крайнее заднее положение. Затем происходит расфиксация поворот и фиксация шпиндельного барабана. Начинается быстрый подвод суппортов в положение начала обработки.
В загрузочной позиции шпиндель автоматически останавливается. Загрузка заготовками и разгрузка готовых деталей производится вручную. Разжим и зажим патрона производится рукояткой. Этой же рукояткой производится включение вращения шпинделей. Если не произошёл зажим заготовки и включение вращения шпинделя поворот шпиндельного барабана в следующую позицию не произойдёт и по окончании рабочего хода отключается подача. [8]
4. Конструирование и расчет приспособлений.
4.1 Исходные данные.
Чертеж заготовки и программа выпуска
Операционная карта на данную операцию
Технические характеристики станка
Справочные данные по проектированию оснастки.
4.2 Служебное назначение приспособления и исходные данные
Исходя из крупносерийного типа производства а также конфигурации детали на фрезерной операции 040 применяется специальное станочное зажимное приспособление с гидроприводом. Данное приспособление обеспечивает надежность закрепления точность установки и минимальную погрешность базирования а гидропривод позволяет сократить вспомогательное время на закрепление детали.
Зажимное приспособление состоит из гидропривода установочных и зажимных элементов а также стандартных изделий. [1]
Технические характеристики станка 6М13П:
Наибольшее перемещение:Стола продольное – 1900
Гильз шпинделей – 1900
Наибольший крутящий момент на шпинделе – 200 Нм;
Скорость быстрого перемещения суппорта – 4 ммин;
Наибольшее перемещение по осям X Y Z – 630х360х560 мм;
Пределы частот вращения шпинделя – 10..1600 обмин;
Мощность главного привода – 30 кВт;
Режущий инструмент – фреза.
4.3 Схема и расчет приспособления.
Расчет режима резания для операции 040 – фрезерная.
Станок модели 6М13П.
Позиция 1: Фрезеровать наклонную площадку под дренажное отверстие выдерживая 45° 25° и 8°30'. [15]
Диаметр фрезы D=20мм;
Длина фрезерования L=1807 мм;
Инструмент: фреза материал режущей части – Р6М5;
Диапазон частот вращения шпинделя: n = 10 ÷ 1600 обмин;
Подача шпинделя 3 – 3000 мммин.
Мощность привода главного движения: 30 кВт.
Расчёт для фрезерования.
Глубина фрезерования: мм
Принятое значение S = 51 мммин.
где - коэффициент и показатели в формуле скорости резания при фрезеровании;
- диаметр фрезы (мм);
- коэффициент учитывающий состояние поверхности заготовки.
; = 1.0; = 085; ; q = 0.45; х=03; y = 0.2; m = 0.33; u=01; p=01; Т=100 мин.
обмин. Принимаем с учётом частот вращения шпинделя станка 360 обмин.
Мощность резания (эффективная):
Мощность привода главного движения 30 КВт достаточна.
Расчет сил на приспособлении:
Находим крутящий момент Мкр
Находим силу закрепления Рз
где f – коэффициент трения;
где К – коэффициент запаса.
Рассчитываем диаметр поршня:
Выбираем диаметр цилиндра и штока D = 25мм d = 12мм. [10] [15]
Расчеты выполнены верно поэтому принимаем диаметр цилиндра и
штока D = 25мм d = 12мм.
4.4 Описание устройства и работы приспособления для агрегатного станка
на операции сверления топливоподводящих отверстий.
Устройство и принцип работы: [9]
Обрабатываемое изделие устанавливается в зажимном приспособлении на предварительную базу. Прижим осуществляется центром к центру. Усилие центр получает от гидроцилиндра.
Обработка производится гидравлическими силовыми столами которые позволяют осуществлять регулировку величины рабочей подачи.
Все бабки установленные на силовые столы имеют устройство контроля нагрузки. При возрастании крутящего момента на сверле подается команда на дополнительный вывод его из зоны обработки. [1]
5 Планировка участка.
При планировке участка исходя из норм приняты следующие расстояния:
расстояние между станками не менее 09 м;
расстояние между оборудованием и колоннами не менее 08 м;
ширина магистрального проезда 4 м;
ширина транспортного проезда 2 м;
Планировка участка выполнялась по порядку технологического процесса в масштабе 1:50. Кроме основного производственного оборудования участок оснащен тарой для складирования заготовок и деталей кран-балкой. Механизирован отвод стружки с помощью скребкового конвейера. Передача заготовок от одной операции к другой осуществляется по рольгангу.
К рабочим местам в зависимости от вида выполняемой работы подводится эмульсия сжатый воздух содовый раствор. При разработке планировки учтены требования по охране труда техники безопасности и противопожарной защите. [2]
Длина участка 3860 м 2140 м площадь 82604 м2.
Планировка показана в графической части дипломного проекта. На листе изображен график загрузки оборудования средний коэффициент загрузки учаска 74% и его технико-экономические характеристики.
В настоящее время основными направлениями развития машиностроения являются комплексная автоматизация технологических процессов и использование экономичных способов получения заготовок деталей машин что позволяет сократить участие человека в процессе изготовления и следовательно повысить качество продукции а также сократить расходы связанные с низким коэффициентом использования металла и временными затратами на механическую обработку.
Необходимо уделять повышенное внимание разработке более производительных технологий повышению качества контроля обеспечению точности формы и размеров при изготовлении форсунки и ее корпуса; необходимо совершенствовать конструкции режущего инструмента технологической оснастки организацию производства и охрану труда.
Однако к сожалению далеко не на всех предприятиях имеется необходимое для этого оборудование. В настоящее время АЗПИ переходит на стандарт качества «Evro 4» и внедряет систему управления качеством в соответствии с международным стандартом ISO 9000.
В данной работе на основе данных полученных на производственной практике будет рассмотрен технологический процесс сборки форсунки и разработан технологический процесс механической обработки корпуса форсунки. Действующий технологический процесс осуществляется на агрегатных станках заготовка получается из проката.
Годовой объём выпуска форсунки а следовательно и корпуса форсунки составляет 80000 штук в год что соответствует крупносерийному типу производства.
Технологическая часть ..
1Определение типа производства . .
2 Проектирование технологического процесс сборки узла . .. ..
2.1 Служебное назначение узла описание устройства и работы
2.2 Критический анализ технических требований. Обоснование метода
достижения точности по отдельным ТТ узла .
2.3 Методы проверки ТТ собранного узла .
2.4 Анализ технологичности конструкции узла .
2.5 Технологическая схема сборки .
2.6 Разработка маршрутного техпроцесса сборки с выбором
оборудования и оснастки . ..
2.7Нормирование технологического процесса сборки .. .
2.8Организация работы участка сборки ..
3 Технологический процесс изготовления детали ..
3.2 Критический анализ технических требований к детали
3.3 Методы и схемы проверки ТТ
3.4 Анализ технологичности конструкции детали .
3.5 Выбор и технико-экономическое обоснование метода
получения заготовки .
оборудования и оснастки баз и схем базирования .
3.7 Расчет и выбор припусков ..
3.8 Расчет и выбор режимов резания.
Техническое нормирование ..
3.9 Средства механизации и автоматизации ТП обработки ..
4 Конструирование и расчет приспособлений
4.1 Исходные данные
4.3 Схема и расчет приспособления .
4.4 Описание устройства и работы приспособления .
5 Планировка участка
Охрана труда и окружающей среды
1 Требования к безопасности при эксплуатации станков токарной и
2 Стружка и способы защиты от травм на участке
3 Обезвреживание и утилизация отработанных СОЖ ..
Организационно-экономическая часть ..
1 Организационные расчеты проектируемого участка ..
2 Технико-экономическое обоснование проекта
3 Расчет технико-экономических показателей проектируемого участка
Исследовательская часть
Ансеров М.А. Приспособления для металлорежущих станков. – М.: Машиностроение 1967. - 945 с.
Балашов А.В. Николаенко Н.С. Дипломное проектирование по технологии машиностроения. Графическая часть. Методические указания Алт. гос. техн. ун-т им. И.И.Ползунова. – Барнаул: Изд-во АлтГТУ 2008. – 80 с.
ГОСТ 21495-76 Базирование и базы. Термины и определения.
ГОСТ 3.1404-86 ЕСТД. Формы и правила оформления документов на технологические процессы и операции обработки резанием.
ГОСТ 7505-89 Поковки стальные штампованные. Допуски припуски и кузнечные напуски.
ГОСТ 14.205-83 (СТ СЭВ 2063-79). Технологичность конструкции изделий. Термины и определения.
Инструмент для станков с ЧПУ многоцелевых станков и ТПС И.Л.Федюшин Я.А.Музыкант А.И.Мещеряков и др. – М.: Машиностроение 1990. – 272 с.
Колесов И.М. Основы технологии машиностроения. – М.: Высш. школа 2001. – 592 с.
Корсаков В.С. Основы конструирования приспособлений. – 2-е изд. перераб. и доп. – М.: Машиностроение 1983. – 277 с.
Кузнецов Ю.И. Конструкции приспособлений для станков с ЧПУ. – М.: Высш. шк. 1988. – 303 с.
Основы технологии машиностроенияПод ред. В.С.Корсакова. – М.: Машиностроение 1977. – 416 с.
Панов А.А. Расчет линейных размерных цепей при проектировании технологических процессов сборки: Учебное пособие Алт. гос. техн. ун-т им. И.И.Ползунова. – Барнаул : Изд-во АлтГТУ 1996. – 51 с.
Панов А.А. Хоменко В.В. Расчет припусков на механическую обработку: Методические указания для студентов машиностроительных специальностей всех форм обучения. Алт. гос. техн. ун-т им. И.И.Ползунова. – Барнаул: Изд-во АлтГТУ 2006. – 44 с.
Справочник технолога-машиностроителя: В 2-х т. Т. 1 Под ред. А.Г.Косиловой и Р.К.Мещерякова. – 4-е изд. перераб. и доп. – М.: Машиностроение 1986. – 656 с.
Справочник технолога-машиностроителя: В 2-х т. Т.2 Под ред. А.Г.Косиловой и Р.К.Мещерякова. – 4-е изд. перераб. и доп. – М.: Машиностроение 1986. – 496 с.
Безопасность труда при обработке металлов резаниемПод ред. А.Ф.Власова – М.: Машиностроение 1980. – 80 с.
Удаление пыли и стружки от режущих инструментовПод ред. А.Ф.Власова – М.: Машиностроение 1989. – 263 с.
Обезвреживание и утилизация отработанных СОЖПод ред. Е.Г.Бердичевский – М.: Машиностроение 1986. – 254 с.
Петров В.Н. Сухорукова О.Б. Методические указания к выполнению экономической части дипломных проектов: Методические указания для студентов специальности «Технология машиностроения» всех форм обучения. Алт. гос. техн. ун-т им. И.И.Ползунова. – Барнаул: Изд-во АлтГТУ 2009. – 50 с.
Анурьев В.И. Справочник конструктора-машиностроителя: В 3т. Т.1 – 8-е изд.
перераб. и доп. Под ред. И.И. Жестковой. – М.: Машиностроение 2001. –
Панов А.А. Лабецкий В.М. Неверов В.И. Методические указания к диплом
ному проектированию для студентов специальности 120100 «Технология ма
шиностроения» дневной и вечерней форм обучения: Методические указания
для студентов машиностроительных специальностей всех форм обучения.
Алт. гос. техн. ун-т им. И.И.Ползунова. – Барнаул: Изд-во АлтГТУ 2000. – 32с.
Общемашиностроительные нормативы времени и режимов резания для нор
мирования работ выполняемых на универсальных и многоцелевых станках с
числовым программным управлением. Часть1. Нормативы времени. Ред. С.Ю.
Романова Изд. Экономика 1990г. 210 с.
Общемашиностроительные нормативы времени и режимов резания для норми
рования работ выполняемых на универсальных и многоцелевых станках с чи
словым программным управлением. Часть2. Нормативы режимов резания.
Ред. С.Ю. Романова Изд. Экономика 1990г. 480 с.
В ходе дипломного проектирования была произведена следующая работа: спроектирован технологический процесс механической обработки форсунки и описан технологический процесс сборки форсунки. Также были произведены организационно-экономические расчеты и в исследовательской части произведен анализ способов накатывания резьбы.
При рассмотрении технологического процесса сборки узла была рассчитана размерная цепь на зазор между хвостовиком корпуса распылителя и гайкой распылителя а также несоосность малого наружного диаметра корпуса распылителя относительно посадочного диаметра корпуса форсунки. Для сборки узла была принята узловая форма сборки и определена норма времени на операции.
При проектировании технологического процесса механической обработки корпуса была оценена технологичность детали и дан анализ технических требований предъявляемых к ней для проверки перпендикулярности отверстия М10x125 относительно поверхности 17мм спроектировано приспособление. Это приспособление отличается универсальностью за счет использования унифицированных деталей и узлов. При выборе метода получения заготовки корпуса рассматривались два метода и на основе расчета себестоимости их изготовления был выбран метод изготовления заготовки из проката.
На основе карты исходных данных и анализа действующего технологического процесса с учетом типа производства и специфики деталей был спроектирован технологический процесс изготовления деталей выбрано оборудование и инструмент. В одну технологическую операцию группировалась обработка поверхностей сходных по методу обработки точности шероховатости и технологическим возможностям оборудования. На первой операции технологического процесса обрабатываются поверхности служащие в дальнейшем технологическими базами для последующей обработки. Оборудование выбрано характерное для
крупносерийного типа производства – агрегатные многоцелевые станки и универсальное оборудование. При этом значительно сокращается парк станков и себестоимость изготавливаемых деталей.
Для спроектированных технологических процессов изготовления деталей были рассчитаны режимы резания и определена норма времени на операции. Произведен размерный анализ технологического процесса изготовления корпуса форсунки. В результате проведенной работы были рассчитаны размеры заготовки с минимально необходимыми припусками что обеспечивает минимальный расход материала; на все операции технологического процесса назначены технологические допуски и технические требования; определены минимально необходимые припуски; построены размерные схемы технологического процесса и проверена возможность обеспечения чертежных размеров и технических требований при обработки детали по данному технологическому процессу.
В организационной части проекта определено число необходимого оборудования для изготовления корпуса коэффициент его загрузки и число рабочих. В экономической части рассчитаны основные технико-экономические показатели проекта которые подтверждают выгодность и рентабельность спроектированного технологического процесса.
Спецификация к фрезер.приспособлению.doc
Поршень гидроцилиндра
Корпус гидроцилиндра
3 Моя экономика.doc
1 Организационные расчеты проектируемого участка
1.1 Годовая производственная программа.
Форсунка «Камаз-216» производится Алтайским заводом прецизионных изделий (АЗПИ). Основная продукция - распылители и форсунки для автомобильных и тракторных дизельных двигателей. Большая часть изделий выпускаются крупными партиями. Основной тип производства - крупносерийный.
Таблица 3.1 – Годовая производственная программа.
изделия (сборочной ед.)
Заготовка для детали
1.1.1 Технологический маршрут механической обработки детали.
Таблица 3.2 – Технологический маршрут обработки корпуса форсунки.
времени на операцию мин
Токарный полуавтомат
Агрегатно-сверлильная
Агрегатно-сверлильный
Круглошлифовальный 3М151АН-102
Резьбонакатной UPWS 1625
Плоскошлифовальный 3Е756
1.1.2 Уточнение типа производства:
Расчетное количество рабочих мест при обработке данной детали:
Коэффициент массовости:
Коэффициент закрепления операций: (3.3) Учитывая полученные значения коэффициента массовости и коэффициента закрепления операции делаем вывод что у нас крупносерийное производство.[19]
1.2. Выбор формы организации производства на участке.
Таблица 3.3 – Форма организации участка обработки корпуса форсунки..
Однопредметная линия: прерывно-поточная с межоперац-ми заделами
1.3 Определение общего количества рабочих мест на участке.
Таблица 3.4 – Расчет количества рабочих мест на участке.
Необходимое количество оборудования для каждой группы станков рассчитываем по формуле:
Qрасч. = Пгод × Тшт. Фд.об ×60 где (3.4)
П год.– годовая программа выпуска деталей шт.;
Тшт. – норма штучного времени на операцию мин.;
Фд.об. – действительный годовой фонд времени оборудования;
0 Qоб.р = 80 000 × 113 1950 × 60 = 078; Qоб = 1; Кз = 078 1 = 078
5 Qоб.р = 80 000 × 1219 1950 × 60 = 084; Qоб. = 1; Кз = 084 1 = 084
0 Qоб.р = 80 000 × 1398 1950 × 60 = 096; Qоб. = 1; Кз = 096 1 = 096
5 Qоб.р = 80 000 × 1156 1950 × 60 = 068; Qоб. = 1; Кз = 068 1 = 068
0 Qоб.р = 80 000 × 041 1950 × 60 = 028; Qоб. = 1; Кз = 028 1 = 028
5 Qоб.р = 80 000 × 041 1950 × 60 = 028; Qоб. = 1; Кз = 028 1 = 028
0 Qоб.р = 80 000 × 098 1950 × 60 = 067; Qоб. = 1; Кз = 067 1 = 067
(030035040 Qоб.р = 80 000 × (041+041+098) 1950 × 60 = 123; Qоб. = 2;
5 Qоб.р = 80 000 × 065 1950 × 60 = 044; Qоб. = 1; Кз = 044 1 = 044
5 Qоб.р = 80 000 × 055 1950 × 60 = 038; Qоб. = 1; Кз = 038 1 = 038
0 Qоб.р = 80 000 × 0814 1950 × 60 = 056; Qоб. = 1; Кз = 056 1 = 056
5 Qоб.р = 80 000 × 0413 1950 × 60 = 028; Qоб. = 1; Кз = 028 1 = 028
0 Qоб.р = 80 000 × 100 1950 × 60 = 068; Qоб. = 1; Кз = 068 1 = 068
(055060 Qоб.р = 80 000 × (0413+100) 1950 × 60 = 097; Qоб. = 1;
5 Qоб.р = 80 000 × 0439 1950 × 60 = 030; Qоб. = 1; Кз = 030 1 = 030
0 Qоб.р = 80 000 × 0404 1950 × 60 = 028; Qоб. = 1; Кз = 028 1 = 028
(065070 Qоб.р = 80 000 × (0439+0404) 1950 × 60 = 058; Qоб. = 1;
0 Qоб.р = 80 000 × 145 1950 × 60 = 099; Qоб. = 1; Кз = 099 1 = 099
5 Qоб.р = 80 000 × 075 1950 × 60 = 051; Qоб. = 1; Кз = 051 1 = 051
0 Qоб.р = 80 000 × 096 1950 × 60 = 066; Qоб. = 1; Кз = 066 1 = 066
Находим средний коэффициент загрузки: Кз.ср. = SQоб.р SQоб. (3.5)
Кз.ср. = (078 + 084 + 096 + 068 + 123 + 082 + 056 + 097 + 058 + 099 + 051+ 066) 13 = 074
График загрузки оборудования по типоразмерам:
1.4 Определение численности производственных рабочих.
1.4.1. Численность основных рабочих.
Расчетная численность основных рабочих: (3.6)
1.4.2. Численность вспомогательных рабочих.
1.4.2.1 Численность наладчиков оборудования.
Таблица 3.5 – Расчет численности наладчиков.
В данном разделе определяется численность рабочих исходя из количества установленных рабочих мест коэффициента их загрузки действующих норм обслуживания и режима работы по формуле:
Рр = (Qоб ×Кз об. ×nсм) Нобс (3.7)
где РР – расчетная численность;
Qоб – принятое количество оборудования;
Кз об. – коэффициент загрузки оборудования; nсм – число рабочих смен;
Нобс – норма многостаночного обслуживания для основных рабочих или норма обслуживания станков на одного наладчика в смену. [19]
1.4.2.2. Численность рабочих по инструментальному обслуживанию.
Так как численность рабочих по инструментальному обслуживанию составляет 16-20% от принятой численности основных рабочих участка (10 человек) то будем считать что инструментальное обслуживание будет осуществлять 2 человека.
1.4.2.3. Численность рабочих по текущему ремонту оборудования.
Таблица 3.6 – Расчет численности рабочих по текущему ремонту оборудования.
ность единицы оборудования
Объем ремонтных работ
Расчетная численность рабоч
Таблица 3.7 – Расчет численности рабочих по межремонтному
обслуживанию оборудования.
Расчет рабочих по ремонту механической части оборудования:
Расчет рабочих по ремонту электрической части оборудования:
Принимаем одного слесаря по межремонтному и текущему обслуживанию оборудования и три электрика по межремонтному и текущему обслуживанию.
Численность контролеров для крупносерийного производства определяется из соотношения: один контролер на 20-25 основных рабочих в смену. Принимаем одного контролера.
1.4.3. Определение общей численности производственных рабочих
Таблица 3.8 – Состав производственных рабочих участка. [19]
Оператор агрегатного станка
Всего основных рабочих:
Вспомогательные рабочие:
Слесарь по межремонтному текущему обслуживанию оборудования
Электрик по межремонтному текущему обслуживанию оборудования
Рабочие по инструментальному обслуживанию
Всего вспомогательных рабочих:
Итого производственных рабочих:
2 Технико-экономическое обоснование проекта.
2.1. Экономическое обоснование выбора заготовки.
Деталь изготавливается из проката:
где Зм – затраты на материал за вычетом возвратных отходов руб.
Нм – норма расхода материала на деталь кг.
Цм – цена за 1 кг. материала руб.
Мд – масса детали по чертежу кг.
Цотх – заготовительная цена за 1 кг отходовруб.
2.2. Обоснование выбора варианта технологического процесса по
экономической эффективности.
2.2.1. Расчет технологической себестоимости обработки деталей по
сравниваемым вариантам.
Таблица 3.9 – Сопоставимые варианты обработки детали корпуса форсунка
Действующий техпроцесс
Проектируемый техпроцесс
Норма времени на операц мин.
2.2.2 Основная заработная плата основных рабочих.
Таблица 3.10 – Расчет затрат на заработную плату (действующий вариант).
вая тариф. ставка руб
вые затраты на зар. плату
Итого: основная заработная плата основных рабочих
Дополнительная заработная плата
Единый социальный налог на заработную плату
Таблица 3.11– Расчет затрат на заработную плату (проектируемый вариант).
Затраты на основную заработную плату основных рабочих:
2.2.3 Дополнительная заработная плата основных рабочих:
Для действующего варианта: руб
Для проектируемого варианта: руб
2.2.4 Единый социальный налог на заработную плату основных рабочих:
2.2.5 Затраты на амортизацию оборудования:
где Сб.об. – балансовая стоимость единицы данного оборудования руб.
Таблица 3.12 – Расчет затрат на амортизацию оборудования
(действующий вариант).
Наим. и модель оборуд.
Балансов. ст-ть ед.об руб
Срок полезного испол-я оборуд. год
Годовые затраты на амортиз. руб
Настольно-сверлильный НС 12М
Агрегатно-сверлильный 1ХМА 1032
Настольно-сверлильный НС 12A
Таблица 3.13 – Расчет затрат на амортизацию оборудования
(проектируемый вариант).
Агрегатно-сверлильный 1088-4513
2.2.6 Затраты на силовую электроэнергию.
Затраты на силовую электроэнергию определяются:
Таблица 3.14 – Расчет затрат на электроэнергию (действующий вариант).
Годовой фонд врем. обор. час
Цена одного кВт-ч. руб
Год. затр.на электро- энергию руб.
Таблица 3.15 – Расчет затрат на электроэнергию (проектируемый вариант).
вой фонд врем. обор. час
Цена одногокВт-ч. руб
Год. затр. на электр энер-
2.2.7 Затраты на межремонтное обслуживание оборудования.
Затраты на межремонтное обслуживание оборудования определяются по формуле: руб (3.17)
Таблица 3.16 – Расчет затрат на межремонтное обслуживание оборудования
Категор. слож-ти ремонта ед.
Нормативы затрат руб
Коэф-т класса точнос.
Коэф-т заг-ки обору-
вые затр. на межрем. обслуж. оборуд. руб.
Таблица 3.17 – Расчет затрат на межремонтное обслуживание оборудования
2.2.8 Затраты на текущий ремонт оборудования.
Таблица 3.18 – Расчет затрат на текущий ремонт оборудования
Таблица 3.19 – Расчет затрат на текущий ремонт оборудования
2.2.9 Затраты на приспособление.
Затраты на приспособление рассчитываются по формуле:
Таблица 3.20 – Расчет затрат на приспособление (действующий вариант).
Расч. цена присп. руб
Годов. затраты на присп руб
Приспособление для сверления (зенкерования развертывания)
Расчет затрат на приспособление (проектируемый вариант):
Стоимость приспособлений включена в стоимость оборудования.
2.2.10 Затраты на режущий инструмент.
Годовые затраты по цельному режущему инструменту определяются по формуле:
Таблица 3.21 – Расчет затрат на режущие инструменты (действующий вариант).
Год. прог. выпуска дета-
Зенковк. конич. 60°.
Таблица 3.22 – Расчет затрат на режущие инструменты (проектируемый вариант).
2.2.11 Амортизация производственной площади.
Годовые затраты на амортизацию производственной площади занимаемой оборудованием определяется по формуле:
где Тзд. - срок полезного использования производственного здания ( 50 лет) год.;
Сб.пл. - балансовая стоимость производственной площади занимаемой оборудованием руб. определяется по формуле:
Сб.пл=SплQобЦплКд.пл.Кзан.об. руб. (3.22)
где Sпл – производственная площадь занимаемая оборудованием кв.м.;
Qоб – количество установленного оборудования данного типа на операции;
Цпл – цена кв.м. производственной площади руб.;
Кд.пл. – коэффициент учитывающий дополнительную производственную
Кзан.об. – коэффициент занятости оборудования.
Таблица 3.23 – Расчет амортизации производственной площади
(действующий вариант)
Площадь занимаем. ед.оборуд. кв.м
Цена одного кв.м. площади руб
Год. затр.на амортиз. площади
Таблица 3.24 – Расчет амортизации производственной площади
(проектируемый вариант)
2.2.12 Технологическая себестоимость обработки деталей
по сравниваемым вариантам.
Таблица 3.25 – Технологическая себестоимость годового выпуска.
Результат сравнения:
Основная заработная плата основных рабочих
Дополнительная заработная плата основных рабочих
Амортизация оборудования
Силовая электроэнергия
Межремонтное обслуживание оборудования
Текущий ремонт оборудования
Амортизация производств-ой площади
2.3 Расчет капитальных вложений по сравниваемым вариантам.
2.3.1 Определение капитальных вложений воборудование.
Величина капитальных вложений определяется по тем операциям которые различаются затратами на оборудование и производственную площадь.
Определение капитальных вложений в оборудование производится по формуле: (3.23)
Таблица 3.26 – Расчет капитальных вложений в оборудование
Капитальные вложения в оборудование
Таблица 3.27 – Расчет капитальных вложений в оборудование
Капитальные вложения в оборудование руб
2.3.2 Определение капитальных вложений в производственную
Капитальные вложения в производственную площадь:
Таблица 3.28 – Расчет капитальных вложений в производственную площадь
мая ед. оборудов. кв.м
Цена одного кв.м. площади
затраты в площадь руб
Таблица 3.29 – Расчет капитальных вложений в производственную площадь
Таблица 3.30 – Капитальные вложения по сравниваемым вариантам. [19]
Направления капитал.вложений
Производственная площадь
2.4 Расчет годового экономического эффекта и срока окупаемости
дополнительных капитальных вложений.
2.4.1 Годовая экономия от снижения себестоимости деталей.
где Сдейств Спроект – технологическая себестоимость годового выпуска деталей по действующему и проектируемому варианту руб. Определяется как сумма затрат на заготовку и обработку деталей.
2.4.2 Срок окупаемости дополнительных капитальных вложений.
Проектируемый вариант техпроцесса предусматривает приобретение новых основных средств. В этом случае срок окупаемости дополнительных капитальных вложений в годах определяется следующим образом:
где Кдоп – дополнительные капитальные вложения руб.
Дополнительные капитальные вложения определяем как стоимость нового с учетом реализации оборудования действующего варианта:
где Кпроект – капитальные вложения в проектном варианте;
Кдм – затраты на демонтаж оборудования действующего варианта руб. Принимаются в размере 5-7 процентов от его стоимости;
где Сост – остаточная стоимость высвобождаемого оборудования. Принимается в размере 20-30% от его стоимости.
Внедрение предлагаемого варианта технологического процесса изготовления корпуса форсунки считается целесообразным т.к. годовой экономический эффект положительный а срок окупаемости дополнительных капитальных затрат 071 года что не превышает пяти лет. [19]
3 Расчет технико-экономических показателей
проектируемого участка.
3.1. Годовой фонд оплаты труда и ЕСН..
Основная заработная плата рабочих за год рассчитывается по формуле:
где Р - принятая численность рабочих (табл. 3.8).
Фд.р – действительный годовой фонд времени рабочего равный 1820 часов.
Значения остальных показателей приведены ранее.
Таблица 3.31 – Расчет годового ФОТ и ЕСН.
Слесарь по межремонтному текущему обслужив-ию оборудова-ия
Электрик по межремонтному текущему обслужив-ию оборудова-ия
Рабочие по инструмента-
льному обслужива-нию
3.2. Стоимость производственной площади участка.
Таблица 3.32 – Расчет стоимости производственной площади участка.
Площадь занимаемая ед. оборудов. кв.м
Год. затр.на амортиз. площадируб.
3.3. Балансовая стоимость оборудования.
Таблица 3.33 – Расчет балансовой стоимости оборудования.
3.4. Cмета расходов на содержание и эксплуатацию
производственного оборудования.
3.4.1 Содержание рабочих мест (оборудования).
Затраты на вспомогательные материалы (02 – 03 % от балансовой стоимости оборудования при односменном режиме) составляют: 0003*3925295 = 11776 руб.
Заработная плата вспомогательных рабочих по наладке с отчислениями на социальные нужды составляют: 487350 руб.
Заработная плата вспомогательных рабочих по межремонтному обслуживанию с отчислениями на социальные нужды составляют: 324900 руб.
Затраты на силовую электроэнергию:
Таблица 3.34 – Расчет годовых затарт на силовую электроэнергию.
на электро-энерг руб.
3.4.2 Ремонт производственного оборудования.
Годовые затраты на ремонт оборудования укрупненно принимаются 2-3% от его балансовой стоимости составляют: 003*3925295 = 117759 руб.
3.4.3 Содержание и эксплуатация внутрицехового транспорта.
Годовые затраты по внутрицеховому перемещению грузов:
где Зтр – годовые затраты на услуги внутрицехового транспорта руб.;
Qтр – количество транспортных средств. Принимается 1 транспортное средство на участок в смену;
Цтр – стоимость одного часа работы транспортного средства. Принимается 120 руб.
Фд.тр – действительный годовой фонд времени транспортного средства. Фд.тр.=1800 час при односменном режиме.
3.4.4 Амортизация производственного оборудования.
Амортизация производственного оборудования составляет: 337781 руб.
3.4.5 Износ малоценного и быстроизнашивающегося инструмента.
Принимаются в размере 5-7% от балансовой стоимости оборудования составляет: 007*39252295 = 274771 руб.
Таблица 3.35 – Смета годовых расходов на содержание и
эксплуатацию оборудования. [19]
Годовые затраты руб.
Содержание рабочих мест (оборудования)
Содержание и эксплуатация внутрицехового транспорта
Износ малоценного инструмента
Процент расходов на содержание и эксплуатацию оборудования к основной заработной плате основных рабочих составляет:
(1980081 1547146) * 100 % = 128 %
3.5. Калькуляция себестоимости детали.
3.5.1 Затраты на основные материалы за вычетом возвратных отходов.
3.5.2 Основная заработная плата основных рабочих на деталь.
где Тдет - трудоемкость детали мин.;
Счас.ср.- средняя часовая тарифная ставка рабочего руб.
3.5.3 Дополнительная заработная плата основных рабочих на деталь.
Дополнительная заработная плата составляет 8-10% от основной заработной платы основных рабочих и составляет: 182 руб.
3.5.4 ЕСН на зароботную плату основных рабочих:
ЕСН составляет 26% от суммы основной и дополнительной заработной платы
что составляет: 473 руб.
3.5.5 Содержание и эксплуатация оборудования.
Расходы по данной статье калькуляции определяются:
3.5.6 Цеховые расходы на деталь.
Цеховые расходы на деталь определяются аналогично предыдущей статье. Процент цеховых расходов к основной заработной плате основных рабочих принимается по данным предприятия. Ориентировочно от 80 до120 %. что составляет 08 * 182 = 1456
3.5.7 Общезаводские расходы на деталь.
3.5.8 Внепроизводственные (коммерческие) расходы.
Внепроизводственные (коммерческие) расходы определяются в % к заводской себестоимости детали по данным предприятия (3-5%) составляет: 90 руб.
3.5.9 Полная себестоимость детали.
Таблица 3.36 – Полная себестоимость детали. [19]
Затраты на деталь руб
Основные материалы (за вычетом отходов)
Содержание и эксплуатация оборудования
Цеховая себестоимость:
Общезаводские расходы
Производственная себестоимость детали
Внепроизводственные расходы
Полная себестоимость детали:
3.5.10 Расчет отпускной цены детали.
При расчете отпускной цены следует учесть прибыль от реализации в размере 16-20% от полной себестоимости детали составляет: 12209 * 116 = 14162 руб.
3.6. Построение точки безубыточного производства.
Постоянные расходы за год = годовые затраты на производство и реализацию продукции – переменные расходы на годовую программу выпуска = 9767200 – 4416800 = 5350400 руб.
Годовые затраты на производство и реализацию продукции = полная себестоимость ед.продукции * годовую программу выпуска = 12209 * 80000 = 9767200 руб.
Переменные расходы за год = переменные затраты на деталь * годовую программу = (3046+ 182 + 182 + 473) * 80000 = 4416800 руб.
Выручка от реализации = Годовая программа выпуска * отпускную цену ед.продукции =
= 80000 * 14162 = 11329600 руб.
График взаимосвязи показателей объема производства затрат и прибыли:
3.7 Основные показатели производственного участка. [19]
Таблица 3.37 – Основные показатели проекта.
Наименование показателя
Годовая программа выпуска деталей
Годовой объем производства продукц.
Основные производственные фонды участка
Численность производ-х рабочих:
Годовой фонд оплаты труда производст-х рабочих:
Средний коэфф-т загрузки оборудования участка год.программы
Трудоемкость единицы продукции
Выпуск продукции на один рубль основных производ-х фондов:
Заработная плата производст.рабочих на один рубль продукции:
Выпуск продукции на одного произв-го рабочего за год
Среднемесячная заработная плата:
Полная себестоимость единицы продукции
Отпускная цена единицы продукции
Годовой экономический эффект:
Дополнительные капитальные вложения
Срок окупаемости дополнительных капитальных вложений
2 Мое БЖД.doc
На участке механической обработки с точки зрения охраны труда факторами риска следует считать:
)Травмоопасность станочного оборудования;
)Отходы производства (стружка лом СОЖ);
)Санитарно – гигиенические и бытовые условия труда работников.
Для создания безопасных и безвредных условий труда в проекте рассматриваются вопросы:
1 Требования к безопасности при эксплуатации станков
токарной и сверлильной групп.
К станкам токарной группы относятся автоматы и полуавтоматы токарные одношпиндельные и многошпиндельные; станки токарно-револьверные; резьбонакатные; токарно-затыловочные; токарно-карусельные; токарно-винторезные; токарные специальные и специализированные. [16]
Обработка различных материалов на станках токарной группы является самым распространенным способом получения точных размеров и форм деталей машин и приборов типа тел вращения. Изучение производственного травматизма показывает что среди большего числа станков токарной группы различного конструктивного оформления и назначения наибольшего внимания с точки зрения техники безопасности требуют токарно-винторезные токарно-револьверные и другие универсальные станки.
При работе на токарных станках часто отмечаются случаи ранения различных частей тела станочника ленточной сливной стружкой образующейся при обработке вязких металлов (сталей) при современных режимах резания. Наиболее эффективным средством предупреждения порезов ленточной стружкой является изменение её формы в процессе резания путем завивания в винтовую
спираль или дробления на отдельные элементы. Это осуществляется приданием передней грани резца криволинейной формы (рис. 2.1 а и б) а также устройством на передней грани резца постоянных или регулируемых порогов (рис. 2.1 в и г).
Рис. 2.1 Устройства для дробления и завивания стружки.
Наиболее рационально для работы на универсальных станках и автоматическом оборудовании использовать сборные резцы оснащенные многогранными неперетачиваемыми пластинками с мелкоразмерными лунками формируемыми при прессовании пластинок. При использовании средств дробления стружки в процессе резания элементы стружки разлетаясь на значительное расстояние представляют определённую опасность для травмирования глаз. Поэтому использование средств защиты является обязательным. [16]
Для защиты работающих от травм отлетающей стружкой станки снабжают ограждениями зоны резания со смотровыми окнами (рис. 2.2).
Рис. 2.2 Ограждение зоны резания токарного станка.
Безопасность приспособлений для закрепления обрабатываемой детали требует большого внимания токаря. Он должен знать что применять поводковые приспособления с выступающими элементами на их наружных поверхностях опасно а использовать открытые поводковые хомутики запрещено в связи с опасностью ушиба рук выступающими их частями и захвата одежды иногда с тяжелыми травматическими последствиями. На рис. 2.3 приведены примеры безопасных поводковых приспособлений.
Рис. 2.3 Примеры безопасных поводковых приспособлений.
Важным условием безопасной обработки деталей в центрах является рациональное устройство задней бабки и надежное её крепление к станине станка. Ходовые винты и валики представляют опасность захвата рабочей одежды так как они находятся в оперативной зоне токаря. Для предупреждения этого необходимо обращать внимание на состояние и соблюдать правила ношения спецодежды исключающие захват её ходовыми винтами и валиками. Также главным мероприятием является ограждение ходовых винтов и валиков.
Порезы рук острыми кромками резца могут иметь место при спешке и неправильных приемах поворота резцовой головки. Кроме того режущая твердосплавная пластина может разрушиться и нанести травму при нарушении установленных режимов резания и правил выключения станка. Основным мероприятием по безопасности в данном случае является строгое соблюдение инструкции в отношении приемов работы.
Пусковые и переключающие устройства токарных станков должны отвечать общим требованиям предъявляемым к этим устройствам прежде всего это сблокированные рукоятки включения шпинделя. Эти рукоятки должны всегда иметь надежную фиксацию в заданных положениях и если она ослабла то необходимо немедленно восстановить её надёжность.
Проверка всей заземляющей сети специалистами проводится периодически в соответствии с правилами Госэнергонадзора. Также станочник должен следить за тем чтобы заземляющая шина всегда была присоединена к станку в предусмотренном для этого месте.
При обработке пруткового материала на токарно-винторезных токарно-револьверных станках и токарных автоматах возникает опасность травмирования людей случайно находящихся в зоне быстровращающегося прутка. Возможны случаи травмирования концом прутка образующего при большом вылете конус вращения. Несчастные случаи могут произойти вследствие захвата одежды или волос при приближении к вращающемуся прутку. При обработке пруткового материала пруток должен быть огражден а режимы резания должны исключать изгиб конца прутка во время его вращения. У токарных автоматов ограждением прутков служат направляющие трубы которые не полностью защищают прутки так как этому мешает механизм подачи (рис. 2.4).
Рис. 2.4 Ограждение прутков в зоне механизма подач.
При вращении обрабатываемых прутков в направляющих трубах удары прутков о их внутренние стенки вызывают сильный шум который утомляет рабочего вредно отражается на органах слуха понижает производительность труда и приводит к травмам. Токарно-револьверные станки и автоматы обрабатывающие прутковый материал следует снабжать глушителями шума. Шум при обработке на этих станках глушится спиральной пружиной которая помещается внутри направляющих труб.
К станкам сверлильной группы относятся вертикально-сверлильные радиально-сверлильные специальные и агрегатно-сверлильные. [16]
При работе на сверлильных станках наибольшую опасность для рабочих представляют вращающиеся части станка – шпиндель патрон сверло. Несчастные случаи возможны при недостаточно надежном креплении обрабатываемой детали на столе станка а также инструмента и при поломке сверла в связи с нарушением правил эксплуатации станка или несоблюдением режимов резания при глубоком сверлении. При сверлении на большую глубину вязких металлов спиральными сверлами стружка из-под сверла выходит двумя длинными спиралями которые вращаются вместе со сверлом и могут нанести ранения работающему на станке.
При сверлении сталей спиральными сверлами целесообразно применять средства дробления стальной стружки. Дробление может осуществляться сверлами со стружкодробящими канавками или прерывистой подачей сверла.
Рис. 2.5 Вариант использования щелевого пневматического пылестружкоприемника.
На рис. 2.5 приведен возможный вариант использования щелевого пневматиче-
ского пылестружкоприемника для многошпиндельных сверлильных станков.
При организации работы на сверлильных станках и в процессе её выполнения необходимо иметь в виду то что патрон для закрепления сверла не должен иметь на наружных поверхностях выступающих частей. Механизм крепления сверла должен обеспечивать надежный зажим прочное центрирование и быструю смену инструмента. При сверлении отверстий в деталях малого размера следует пользоваться ручными зажимами; удерживать деталь непосредственно в руках опасно. Уборку станка от стружки следует производить только предназначенной для этого щеткой.
При работе на сверлильных станках необходимо строго соблюдать правила ношения личной одежды и спецодежды. К работе на сверлильных станках не должны допускаться станочники без головного убора в неряшливо надетой одежде и без защитных очков. [16]
2 Стружка и способы защиты от травм на участке.
Одной из причин несчастных случаев связанных с воздействием стружки обрабатываемого материала на организм станочников является незнание последствий этого воздействия а в некоторых случаях пренебрежение опасностью неоправданный риск работы без средств защиты.
Сливная стружка образуется главным образом при точении вязких металлов (сталей) и представляет серьезную опасность нанесения травм в виде порезов рук и ног токарей и уборщиков стружки. Чем выше скорость резания тем больше вероятность травмирования такой стружкой станочников. Статистика показывает что в последние годы число травм сливной стружкой на машиностроительных предприятиях в целом снижается это можно объяснить тем что на многих предприятиях в процессе резания внедряются средства дробления сливной стружки. Однако суммарно такая стружка наносит еще ущерб здоровью многих станочников и уборщиков а также экономический ущерб обусловленный оплатой пострадавшим дней нетрудоспособности и дефицитом рабочих кадров. Следует учитывать также потери металла в связи с плохой транспортабельностью сливной стружки ее окислением потерями при транспортировке необходимостью ее дробления на специальных дробилках и обезжиривания перед переплавкой. [17]
Проблема устойчивого изменения формы сливной стружки в процессе точения сталей и организованного её отвода из зоны резания уже давно находится в поле зрения отечественных и зарубежных станкостроителей. Не найдено еще универсального способа устойчивого дробления сливной стружки в процессе резания. Из всего многообразия решений приходится выбирать наиболее приемлемое к данным конкретным условиям.
Все известные средства управления стружкой делятся на две группы: устройства отводящие сливную стружку без изменения её формы и устройства изменяющие форму стружки в процессе резания на более безопасную и транспортабельную. Организованный отвод сливной стружки без изменения её формы достигается соответствующей компоновкой узлов станка обеспечивающей сход стружки на заднюю сторону станка в специальный стружкосборник. В связи с большой упругостью сливная стружка часто находит выход в сторону рабочего места и требуется дополнительное управление ею посредством ручных инструментов. Кроме того в связи с большим объемом занимаемым сливной спутанной стружкой приходится часто освобождать от нее стружкосборник.
Эффективнее показали себя в практике заводов средства управления сливной стружкой второй группы связанные с изменением формы стружки в процессе точения.
Рис. 2.6 Классификация средств управления сливной стружкой.
Как видно из рис. 2.6 средства изменения формы сливной стружки делятся на две большие подгруппы: средства завивания стружки в винтовую спираль и средства дробления стружки на отдельные элементы. [17]
Принцип дробления и завивания сливной стружки канавками состоит в следующем: сливная стружка движущаяся по передней поверхности резца попадая в канавку как бы повторяет ее форму и отклоняемая канавкой завивается в кольцо. Если кольцо не встречает какого-либо препятствия свободному движению то стружка завивается в непрерывную спираль. При упоре завитка стружки в препятствие она дробится на отдельные элементы.
На рис. 2.7 показан профиль проходного резца со стружкозавивающейся канавкой.
Рис. 2.7 Средство изменения формы сливной стружки в процессе точения.
В данном случае стружкозавивающая канавка глубиной 01 – 015 мм выполнена электроискровым способом. При обработке сталей 35 45 40Х и 20Х такой профиль канавки устойчиво завивает ленточную стружку при подаче
Наиболее рациональным для работы на универсальных и автоматическом оборудовании использовать сборные резцы оснащенные многогранными неперетачиваемыми пластинами с мелкоразмерными лунками формируемыми при прессовании пластинок. При этом рассматриваются два основных типа мелкоразмерных лунок: замкнутая не доходящая до вспомогательной режущей кромки на 02 – 03 мм; сквозная лунка выходящая на вспомогательную режущую кромку.
Для устойчивого завивания или дробления сливной стружки мелкоразмерными лунками необходимо чтобы стружка попала в лунку и обтекая её получила соответствующее направление и форму. Основными параметрами обеспечивающими дробление или завивание стружки являются ширина фаски у главной режущей кромки резца длина лунки величина скругления лунки в сечении перпендикулярном главной режущей кромке глубина лунки. [17]
Формирование мелкоразмерных лунок на многогранных неперетачиваемых пластинках в процессе их прессования является весьма экономичным решением проблемы изменения формы сливной стружки в процессе точения сталей. Стремление получить устойчивое дробление сливной стружки независимо от режимов резания а также желание получить заранее известную стабильную форму дробленной стружки знать направление полета потока раздробленных стружек в целях их улавливания в зоне образования привели к возникновению новых идей и направлений в решении этой проблемы.
При дискретном резании на автоматах с кулачковым приводом дробление стружки осуществляется соответствующим профилированием кулачков. Необходимо учитывать что широкое внедрение на многих предприятиях средств дробления сливной стружки в процессе точения вязких материалов способствует значительному сокращению числа травм в виде порезов рук и ног станочников и уборщиков стружки.
Рис. 2.8 Классификация средств защиты от травм отлетающей стружкой
обрабатываемого материала.
Из средств индивидуальной защиты глаз наиболее широкое применение при обработке различных материалов на станках нашли защитные очки а из средств коллективной защиты – ограждения зоны резания с ручным управлением.
Для защиты глаз от стружки обрабатываемого материала при резании применяют очки открытого типа очки с боковой защитой и в меньшей степени очки закрытого типа полумаски и индивидуальные щитки (рис. 2.9).
Рис. 2.9 Средства индивидуальной защиты глаз.
Наиболее надежны в рассматриваемых условиях очки с боковой защитой и очки закрытого типа. Однако при работе в защитных очках особенно в очках с боковой защитой и очках закрытого типа заметно осложняется наблюдение через смотровые стекла за точными и тонкими рабочими операциями. Во-первых защитные очки сужают поле зрения что очень заметно при работе в очках с боковой защитой и в очках закрытого типа. Во-вторых внутренняя поверхность стекол очков быстро запотевает вследствие значительного перепада температур подочкового пространства и окружающей среды.
К устройствам отражающим элементную стружку относятся различные экраны укрепляемые на резце резцедержателе корпусе фрезерного станка
Рис. 2.10 Примеры устройств отражающих элементную стружку:
а – отражатель-щетка на резце; б – отражатель-сетка на вертикально-фрезерном станке;
в – экран-отражатель.
Эти устройства имели небольшое практическое применение на отдельных рабочих местах станочников в период развития скоростного резания металлов. Предупреждая разлетание стружки в направлении лица оператора они в какой-то мере являлись средством защиты. Однако чрезмерная индивидуальность и примитивность не позволяют рекомендовать их для практического применения в период научно-технического прогресса в станкостроении.
Ограждение зоны резания станков осуществляемые с целью защиты станочников от травмирования отлетающей стружкой и уменьшения степени рассеивания стружки по станку и рабочему месту. Применяются такие ограждения на токарных и фрезерных станках – универсальных и специального назначения.
Таблица 2.1 Разложение на элементы операции
«Открыть ограждение зоны резания»
Как видно из таблицы для того чтобы открыть ограждение рабочий должен совершить шесть различных движений. Суммарное время потребное на ручное управление ограждением зоны резания в смену может быть определено из следующей зависимости:
где n – число обработанных в смену деталей
а – количество установок резцедержателя необходимых для обработки одной детали.
Из формулы видно что чем больше количество обрабатываемых деталей в смену и чем больше число установок резцедержателя необходимых для обработки одной детали тем больше будет затрачено времени на управление ограждением зоны резания.
Основными причинами неиспользования во многих случаях станочниками ограждений зоны резания при обработке хрупких материалов являются быстрое загрязнение смотрового окна пылью обрабатываемого материала и значительное время потребное на ручное управление ограждением зоны резания.
Наряду с задачами защиты глаз очками от летящих частиц защиты станочников от травмирования отлетающей стружкой с помощью ограждений зоны резания в условиях высокой запыленности особенно при выполнении работ требующих точного зрительного контроля необходимо решать и проблему обеспыливания воздуха. [17]
3 Обезвреживание и утилизация отработанных СОЖ.
Основной целью процесса обезвреживания эмульсий является получение технически чистых оборотных и сточных вод. Кроме того при обезвреживании может попутно осуществляться сбор маслянной фазы в целях её последующей регенерации или утилизации. Чаще всего обезвреживание эмульсий проводят при её разделении на составляющие фазы различными способами (табл.1) или комбинациями этих способов.
Таблица 2.2 Способы разделения фаз эмульсий.
Седиментационный способ основан на разложении эмульсий отстаиванием в процессе которого построение масла и крупные частицы эмульсола всплывают на поверхность. Применяются для предварительного извлечения ловушечных масел. [18]
Механический способ основан на разделении фаз эмульсий в центробежных силовых полях при этом фактор разделения должен быть не меньше 7260. Для повышения производительности разрушения эмульсию необходимо подкислять реагентами что усложняет технологию.
Реагентный способ заключается в разрушении структуры эмульсий химическими продуктами (деэмульгаторами). В качестве деэмульгаторов используют растворы кислот и неорганические соли. Недостатки реагентных способов разрушения эмульсий: кислая реакция очищенной воды (рН = 1..2) при введении в эмульсию кислот и необходимость в её щелочной нейтрализации.
Коагуляционный способ основан на применении специальных веществ (коагулянтов) обеспечивающих перевод частиц масла и других коллоидных примесей в осадок. Коагулянты гидролизуются в воде с образованием хлопьевидных рыхлых структур обладающих высокими адсорбционными свойствами. Расход коагулянтов составляет 30 – 200 на 1 м3 эмульсии и зависит от её исходной щелочности и концентрации. После обработки коагулянтами водная фаза может иметь повышенную кислотноть которую устраняют последующей нейтрализацией.
Флотационный способ пригоден для выделения масел из слабоконцентрированных эмульсий. Обычная воздушная флотация малоэффективна поэтому в эмульсию необходимо вводить реагенты-коагуляторы. Неорганические реагенты существенно интенсифицируют флотируемость масла и перевод его в пенный слой однако маслянная фаза при этом сильно загрязняется и становится непригодной для дальнейшей утилизации.
Электрохимический способ заключается в электролизе эмульсии с применением стальных или алюминиевых анодов. Переходящие в раствор ионы железа или алюминия превращаются в гидроокиси сорбирующие своей поверхностью частички масла. Пузырьки водорода выделяющиеся при электролизе воды ускоряют разделение фаз эмульсий. При введении в эмульсию незначительного количества реагентов процесс протекает более интенсивно. Преимущество способа – универсальность простота обслуживания установок возможность автоматизации образование плотного малозагрязненного осадка.
Сорбционный способ предназначен для очистки маслоэмульсионных сточных вод. Очистка проводится в процессе фильтрации эмульсионного стока через зернистую загрузку обладающую высокими сорбционными и фильтрующими свойствами. В качестве сорбентов часто используют активированные угли гидрофильные глины силикагели алюмогели и др. Преимущество способа – попутная утилизация маслянной фазы эмульсии которая оседая в порах углей значительно увеличивает их топливную калорийность. [18]
Мембранный способ основан на разделении эмульсий путем их продавливания через полупроницаемые мембраны пропускающие воду и задерживающие растворенные и эмульгированные часицы. Известны три метода мембранного разделения – ультрафильтрация обратный осмос и микрофильтрация. Мембраны изготовляют из ацетатцеллюлозы и других полимерных материалов. Преимуществами мембранного разделения эмульсий являются компактность и низкая стоимость установок высокая производительность и малая энергоемкость высокое качество разделения фаз.
Термический способ позволяет разделить эмульсию на практически чистую воду и сгущенный маслянный остаток пригодный для утилизации. Недостаток способа – высокая энергоемкость и возможность разрушения маслянной фазы при нагревании.
В промышленных установках обычно испоьзуют несколько способов обезвреживания эмульсий. Типовая схема установки разделения фаз эмульсий седиментационным механическим реагентным и коагуляционным способами показана на рис. 2.11.
Рис 2.11 Технологическая схеиа обезвреживания эмульсий:
А – отработанная эмульсия; Б – серная кислота; В – масло; Г – сжатый воздух;
Д – на коагуляцию; Е – сток очищенной воды в канализацию.
Таблица 2.3 Утилизация отработанных СОЖ на предприятии.
Основным способом обезвреживания маслянных СОЖ не подлежащих регенерации и утилизации является их сжигание в топках заводских котлов или на автономных установках. Широко распространен простой и эффективный турбобарботажный способ сжигания масел особенности способа: горение происходит в узкой кольцевой или треугольной камере любого диаметра; газификацию отходов проводят в тонком слое что улучшает условия его прогрева вскипания газификации и перемешивания. [18]
Утилизация отработанных СОЖ не подлежащих регенерации является важнейшим этапом малоотходной и безотходной технологии машиностроительного производства. Утилизация может осуществляеться как на предприятиии – потребителе СОЖ (табл. 2.3) так и путем передачи отработанных жидкостей другим организациям (табл. 2.4).
Таблица 2.4 Утилизация отработанных СОЖ вне предпрития.
OК 1Б240-6к.doc
Сталь 40Х ГОСТ 1050-88
Приспособление код и наименование
10-5384-02 Цанга подающая 30 для 1Б240-6
10-5385-02 Цанга зажимная 30 для 1Б240-6
40А-30 Цанга зажимная для 1А240-6
ТПН 240-32 Цанга подающая для 1А240-6
Сменные шестерни скоростей
Сменные шестерни подач
Номер и содержание перехода
Точить поверхность 27 центровать и подрезать торец
выдерживая размер 13±02
25-5013 Державка П 2101-5016 Резец проходной;
71-5002 Стойка неподвижная; 6153-5010 Державка;
17-5017 Сверло центровочное 30; 6105-0054 Втулка переходная.
00-0407 Державка; 2136-0334 Резец
ШЦ 0-125-01 Штангенциркуль ГОСТ 166-89
Точить поверхность 25 центровать конус 60°.
71-5013 Державка; П 2101-5016 Резец проходной;
17-0221 Сверло центровочное 25; 6571-5002 Стойка неподвижная;
53-5010 Державка; 6105-2065 Втулка переходная 30 125
Точить поверхности 20 точить фасонную поверхность
выдерживая размеры 287-033 275-033 491±031
25-5013 Державка; П 2101-5016 Резец проходной;
30-5022 Державка; 2155-0569 Резец фасонный;
13-1765 Скоба 287-033; 8113-1986 Скоба 275-033
Точить поверхность 15 зенковать конус 60°
точить канавку 90° под отрезной резец выдерживая размер 1197.
53-0370 Зенковка 60°; 6571-5002 Стойка неподвижная;
53-5010 Державка; 6105-2064 Втулка переходная 30 75
00-0407 Державка; 2155-0334 Резец; 8162-7588 Глубиномер 75+0360°;
Точить фасонную поверхность
выдерживая размеры 137-03 13±02 21-02
30-5022 Державка; 2155-0945 Резец фасонный;
13-9774 Скоба 137-03;8153-2771 Колибр для контроля фаски 21-02х45º
Отрезать деталь выдерживая размер 1188-03 1х45º
подать пруток до упора.
00-0407 Державка; 6043-5043 Державка;
02-1762 Скоба 1188-03; П 2131-0801 Резец отрезной
Проверить рабочему размеры 123456789 у каждой 20-й детали
наладчику – у первых 6-ти деталей после каждой наладки и подналадки.
13-1765 Скоба 287-033; 8113-9774 Скоба 137-03;
13-1986 Скоба 275-033; 8371-7112 Шаблон 60°;
62-7588 Глубиномер 75+03; 8153-0646 Шаблон 13±02;
02-1762 Скоба 1188-03;
14-1910 Контрольное приспособление на размер 491±031;
05-1821 Мера установочная на размер 491
Рекомендуемые чертежи
- 24.01.2023
- 24.05.2015
- 24.04.2014