Технологическая подготовка производства валов насоса центробежного СДВ 2700/26,5




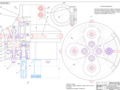
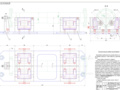
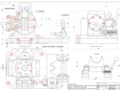
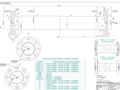
- Добавлен: 24.01.2023
- Размер: 4 MB
- Закачек: 0
Описание
Состав проекта
![]() |
![]() |
![]() |
![]() ![]() ![]() |
![]() ![]() ![]() ![]() |
![]() ![]() ![]() ![]() |
![]() ![]() ![]() ![]() |
![]() ![]() ![]() |
![]() ![]() ![]() ![]() |
![]() ![]() ![]() ![]() |
![]() ![]() ![]() ![]() |
![]() |
![]() ![]() ![]() |
![]() ![]() ![]() ![]() |
![]() ![]() ![]() ![]() |
![]() ![]() ![]() |
![]() ![]() ![]() ![]() |
![]() ![]() ![]() |
![]() ![]() ![]() |
![]() ![]() ![]() |
![]() ![]() ![]() |
![]() ![]() ![]() ![]() |
![]() ![]() ![]() |
![]() ![]() ![]() |
![]() ![]() ![]() |
![]() ![]() ![]() |
![]() ![]() ![]() ![]() |
![]() ![]() ![]() |
![]() ![]() ![]() |
![]() ![]() ![]() |
![]() ![]() ![]() |
![]() ![]() ![]() |
![]() ![]() ![]() |
![]() ![]() ![]() |
![]() ![]() ![]() |
![]() ![]() ![]() ![]() |
![]() ![]() ![]() |
![]() ![]() ![]() ![]() |
![]() ![]() ![]() |
![]() ![]() ![]() ![]() |
![]() |
![]() |
![]() |
![]() |
![]() ![]() ![]() ![]() |
![]() ![]() ![]() ![]() |
![]() ![]() ![]() ![]() |
![]() ![]() ![]() ![]() |
![]() ![]() ![]() ![]() |
Дополнительная информация
7лист_приспособление на расточной.doc
Шайба 20 65Г ГОСТ6402-70
Приспособление сверлильно-расточное поворотное
10лист_планировка участка_.dwg

Место хранения готовых деталей
Склад механического цеха
Примечание: 1) Привязка оборудования произведена по данным каталога и загруженности станков. 2) Привязка нестандартного оборудования произво- дится по месту установки.
Экспликация оборудования
Наименование и марка
Отрезной ножовочный станок 872А
Горизонтально расточной станок 2А620-1
Горизонтально- расточной станок 2651
Круглошлифовальный станок 3А153
Токарно винторезный станок 1М63БФ10
Технологическая подготовка производства валов насоса СДВ 270026
ДП.250140.22-04.31.06
3-6лист_тех.маршрут вал.dwg

Технологическая подготовка производства валов насоса СДВ 270026
механической обработки вала
Технологический маршрут механической
Резать заготовку в размер- 1.
Подрезать торец в размер-6. 5. Просверлить центровое отверстие-А12 ГОСТ 14034-74
в размеры- 7; 8; 9; 10.
Переустановить деталь. (перевернуть деталь
Фреза торцовая насадная со вставными ножами ГОСТ 1092-692. 2. Сверло центровоч- ное 2317-0005 ГОСТ 14952-69 Р6М5.
Горизон- тально расточной станок 2А620-1
Подрезать торец в размер-1. 2. Просверлить центровое отверстие- А12 ГОСТ 14034-74
в размеры- 2; 3; 4; 5.
Приспособ- ление спе- циальное (рпизмы
прижим); стол поворот- ный
Точить поверхность в соответствии с графом обработки
выдерживая размеры- 1; 2; 3; 4; 5; 6; 7; 8; 9; 10; 11; 12; 13.
Резец с механич. креплением многогран- ных твердо- сплавных пластин ГОСТ 20872-80. 2. Резец отрезной ГОСТ 18884-73. 3. Резец с механич. креплением ГОСТ 20872-80
Токарно- винторезный станок 1M63БФ101
Переустановить деталь.(перевернуть деталь
Сверлить восемь отверстий- 5
Сверло спиральное- ø30; 24 ГОСТ 10903-64. 2. Головка расточная.
Приспособ- ление сверлильно- расточное поворотное
Горизон- тально- расточной станок 2651
Сверлить восемь отверстий- 1
на диаметре- 2. 2. Расточить восемь отверстий- 3
Кругло- шлифоваль- ный станок 3А153
Круг шлифоваль- ный ГОСТ 2424-67
Шлифовать в размер-1
с подшлифовкой торца в размер-2. 2. Шлифовать в размер-3
выдерживая размеры- 4; 5.
Шлифовать в размер-6
с подшлифовкой торца в размер-7.
Контролировать размеры-1; 2; 3; 4; 5; 6; 7; 8; 9; 10; 11; 12; 13. 2. Контролировать параметры отклонения расположения формы поверхностей детали согласно чертежа детали. 3. Контролировать шероховатость поверхностей.
Плита контроль- ная.
Приспо- собление контроль- ное.
Индикато- рная голов- ка. 2.Штанген- циркуль ШЦ-1-0
- 1500 ГОСТ 166-80; 3.Штанген- циркуль ШЦ-1-0
- 350 ГОСТ 166-80. 3. Калибр. 4. Образцы шерохова- тостей.
Отрезной ножовочный станок мод. 872А
Приспособ- ление на станке
выдерживая размеры- 14; 15; 16.
9лист_головка револьверная_.dwg

Технологическая подготовка производства валов насоса СДВ 270026
ДП.250140.22-04.31.06
1лист_насос СДВ 2700.26,5.dwg
чем на три оборота. Допускается подтяжка сальника.
Технологическая подготовка производства валов насоса СДВ 270026
Технические характеристики 1. Подача
кВт 275 4. Частота вращения
обмин 740 5. Подшипник смазывается тех. чистой водой под давлением на 1кгссм больше напора насоса
лс 1 6. Содержание взвешанных частиц на смазку и охлаждение подшипников допускается не более
мгл 50 7. На промывку рабочего колеса 12лс
давлением 1кгссм больше
чем напор насоса в течении 30мин.
ДП.250140.22-04.31.06
2лист_деталь_вал.dwg

Сверление - зенкерование
Метод достижения точности размера
Анализ достижения заданной точности размеров
Требование 1. 2. обеспечивается постоянсвом базирования
Требование 3. 4. обеспечивается постоянсвом базирования
Технологическая подготовка производства валов насоса СДВ 270026
НB 230 285. 2.*Размеры для справок. 3. ±. 7. Отв. центр. А12 ГОСТ 14034-74. 4. Материал: Сталь 40Х ГОСТ 4543-71.
ДП.250140.22-04.31.06
7лист_приспособление на расточной.dwg

Приспособление предназначено для установки детали на станке
для обработки радиальных отверстий на барабане. Принцип работы заключается в следующем. Перед установкой детали в приспосо- бление
винтами поз.1 кронштейны поз.5 вместе с роликами поз.4
выводятся за опорную плоскость установочных призмы поз.6. Деталь устанавливается в приспособление
она может вращаться вокруг своей оси благодаря роликам. Деталь поворачивается в нужную позицию
после чего кронштейны с роликами опускаются и деталь фиксируется за счет своего веса. Далее сверлятся требуемые отверстия
после чего кронштейны с роликами опять приподнимаются деталь поворачивается и выставляется на требуемый угол
согласно чертежа детали и сверлится следующая пара отверстий и т.д. После сверления всех отверстий деталь снимается.
Приспособление сверлильно-расточное поворотное
Технические требования: 1. Размеры для справок. 2. Трущиеся поверхности смазать смазкой- Литол-24 ГОСТ 21150-87.
Описание принципа работы приспособления Приспособление предназначено для установки детали на станке
при обработки радиальных и осевых отверстий у крупногабаритных валов. Принцип работы заключается в следующем: Перед установкой детали в приспособление
после чего кронштейны с роликами опускаются и деталь фиксируется за счет своего веса (268кг) и осевого упора. Далее обрабатываются требуемые отверстия
после чего кронштейны с роликами опять приподнимаются
деталь поворачивается и выставляется на требуемый угол
согласно чертежа детали и обрабатываются следующие поверхности и т.д. После обработки всех требуемых поверхностей деталь снимается.
Технологическая подготовка производства валов насоса СДВ 270026
ДП.250140.22-04.31.06
8лист_наладка станка_.dwg

Технологическая подготовка производства валов насоса СДВ 270026
ДП.250140.22-04.31.06
2.1Тех.процесс сборки изделия.doc
1 Анализ соответствия технических требований и норм
точности служебному назначению изделия
Исполнительными поверхностями центробежного насоса СДВ 2700265.
являются рабочие поверхности рабочего колеса которые непосредственно выполняют служебное назначение данного узла.
Основными поверхностями центробежного насоса СДВ 2700265.
являются присоединительные поверхности всасывающего и напорного патрубка через которые осуществляется всасывание и нагнетание рабочей жидкости.
Вспомогательными поверхностями центробежного насоса СДВ 2700265.
являются опорные поверхности посредством которых становится возможно вращение рабочего колеса то есть это посадочные поверхности которые обеспечивают установку и закрепление подшипников качения.
Для выявления основных видов связей между поверхностями анализируем второй лист графической части.
Согласно сборочного чертежа на котором заданы следующие технические требования:
При консервации насоса между фланцами всасывающего и нагнетательного патрубков и дет. поз. 25 установить заглушки согласно чертежу ЗН
Инв. № 68604 при этом дет. поз. 19 20 не устанавливать.
Гидравлическое испытание на герметичность уплотнений вала проводить
водой или керосином под давлением не более: 16кгссм - для сальниковых
уплотнений; 30кгссм - для торцовых уплотнений. При испытании вал насоса должен быть провернут не менее чем на три оборота. Допускается подтяжка сальника.
Производим анализ соответствия технических требований и норм точности основными из которых являются плавность работы насоса и его герметичность при заданном давлении . Делаем вывод что при заданных проверочных условиях в технических требованиях а так же при заданных посадках на сопрягаемых узлах и деталях технические требования и нормы точности вполне соответствуют служебному назначению узла.
прилож.3.dwg

прилож.2.dwg

6Экономическая часть.doc
Исходные данные для проведения экономических расчетов представлены в таблицах 5.1 и 5.2
Таблица 5.1 – Выписка их техпроцесса механической обработки детали
Таблица 5.2 – Ведомость используемого оборудования
Площадь на 1 ст-к м2
Мощность эл.двигат. кВт
Группа ремонтной сложности мех.элек.
Годовая программа выпуска деталей 1000 штук.
Определим коэффициенты загрузки оборудования при обработке детали-вала ведомого.
Годовой эффективный фонд работы оборудования при обработке детали составляет Fэф = 100020 минут. Производим расчет коэффициентов загрузки оборудования путем отнесения времени работы станка на операции за год к эффективному фонду времени работы оборудования за год.
Подставляя значения в формулу 5.1 получаем для станка модели 872А
Кз = 2020100020 = 002;
для станка модели 1К62
Кз = 23858100020 = 024;
для станка модели 1К62Ф3
Кз = 2500100020 = 0025;
для станка модели 3А153
Кз = 14104100020 = 0141;
для станка модели 6Н82
Кз = 6060100020 = 006;
Станки с низким коэффициентом загрузки используем также для обработки детали представителя 1 (см. таблицу 5.2). Станок модели 1К62Ф3 имеет Кз = 024 поэтому для обработки деталей используем один станок данной модели.
Определим численность рабочих:
- явочное число станочников принимаем Ряв = 3 человека;
- списочное число основных рабочих Рсп = Ряв = 3 человека;
- численность наладчиков
Рсп = Рсп080042 = 3080024 = 01008 человек(5.2)
В итоге принимаем решение привлекать со стороны наладчика при этом оплата его работы будет рассчитываться в процентном отношении от заработной платы (полной) наладчика т.е. 01008%
Определим плановый годовой фонд заработной платы. Тарифный фонд зарплаты основных рабочих при повременной оплате труда определяется по формуле:
Фтар = РспFэфЧср (5.3)
гдеFэф – годовой эффективный фонд времени рабочего Fэф = 1836 часов;
Чср – часовая тарифная ставка среднего разряда;
Средний разряд определяется по формуле:
Часовая тарифная ставка I-го разряда определяется по формуле:
где МЗП – минимальная заработная плата М=5000 тг.
Средний тарифный коэффициент равен
Ктар = 115+(124-115)(38-3) = 122
Тогда часовая тарифная ставка среднего равна
Чср = Ч Ктар = 3268122 = 3986 часов (5.6)
Подставляя значения в формулу (5.1) получаем
Фтар = 318363986 = 219 54889 тг.
Тарифный фонд зарплаты наладчиков определяем
Ктар = 124+(133-124)(5-4) = 133
Чср = 3986133 = 5301 тенге
= 010085301 = 9 81049 тг.
На основе рассчитанных данных составляем таблицу 5.3.
Таблица 5.3 – Фонды оплаты
Доплаты и премии 60% тг
Среднемесячная заработная плата основных рабочих составляет:
Определим стоимость основных фондов и амортизационных отчислений.
Стоимость участка определяем по формуле
где F – площадь участка на котором обрабатывается деталь;
Суч – стоимость 1 м2 производственной площади Суч = 300 тгм2;
F = 26+29+20+27+25+30 = 157 м2 (см. таблицу 5.2);
Куч = 157300 = 47 100 тг.
Первоначальная стоимость оборудования определяется по формуле:
гдеЦi – оптовая цена оборудования i вида (см. таблицу 5.2)
= 11 – коэффициент учитывающий затраты на транспортировки и монтаж оборудования;
Коб = (310000+160000+215000+520000+320000+438000)11 = 2 159 300 тг.
Годовой объем амортизационных отчислений определяется по формуле:
гдеК – стоимость определенной группы основных фондов;
а – норма амортизационных отчислений;
Произведя расчеты заносим данные в таблицу 5.4
Группа основных фондов
Первоначальная стоимостьтг
Годовой объем аморт. отчислений тг
Остаточная стоимостьтг
Определим себестоимость продукции
Затраты на силовую электроэнергию определяются
гдеSэл – годовой расход электроэнергии;
гдеFg – годовой фонд времени работы оборудования Fg = 2040 часов;
Кс – коэффициент спроса Кс = 02;
Сni – количество станков j группы.
Qэл = 195702 (11+10+4+5+3+17) = 19 570 кВт
Сэл – цена 1 кВт Сэл = 305 тенге
Подставляя значение в формулу (5.11) получим
Sэл = 19570305 = 59 688.5 тенге
Затраты на ремонт оборудования определяются:
где Rмех и Rэл – группы ремонтной и электрической сложности оборудования
Нмех и Нэл – нормы затрат на ремонт и техобслуживание мехэлчастей оборудования; Нмех = 1000 Нэл = 800
Подставляя значение в формулу (5.13) получаем
Sрем = 1000 (10+11+13+2+18+13)+800 (73+12+55+9+15+115) = 107 240 тг
Затраты на режущий инструмент определяем по формуле
Sреж = (6800100)1957 = 93 936 тг
На основе рассчитанных данных составляем таблицы 5.5 и 5.6.
Таблица 5.5 – Смета РС и ЭО
Наименование статей затрат
Амортизация оборудования
Эксплуатация оборудования
Основная зарплата наладчика
Соц.налог 21% от п.5
Доп. зарплата наладчика
Прочие 5% от суммы всех статей
Таблица 5.6 – Цеховые расходы
Содержание здания 200% от п.1
Прочие расходы 8% от всех статей
Расчет стоимости основных материалов производим исходя из таблицы 5.7
Таблица 5.7 – Стоимость основных материалов
Наименование заготовки
Ст-ть материалов за вычетом отходов деткг
Потребность в основных материалах на годовую программу См тг
См = mз Цз N К = 35402000103 =288 400 тг(5.15)
(103 – коэффициент учитывающий транспортно-заготовительные расходы);
Потребность в основных материалах на годовую программу См кг
= mз N = 352000 = 7000 кг(5.16)
Количество возвратных отходов кг
Со = mотх N = 11952000 = 2390 кг(5.17)
Стоимость возвратных отходов тг
= Сотх Со = 6742390 = 16 1086 тг(5.18)
Стоимость материалов за вычетом отходов:
На основании всех произведенных расчетов составляем таблицу 5.8.
Таблица 5.8 – Калькуляция себестоимости годовой программы выпуска детали
Наименование статей расходов
Основные и вспомогательные материалы
Основной фонд зарплаты осн.рабочих
Соц.налог 21% от п.3
Доп.фонд зарплаты осн. рабочих
Себестоимость 1 единицы
Таблица 5.9 – Технико-экономические показатели участка мехобработки детали
I. Годовая программа выпуска
В натуральном выражении шт
Годовой действительный фонд работы оборудования
Годовой эффективный фонд работы
III. Основные производственные фонды
Количество единиц оборудования шт
Средний коэф.загрузки оборудования
Производственная площадь м2
Стоимость основных производственных фондов тг
Списочная численность раб. чел.
Средний разряд основных рабочих
Средний разряд наладчиков
Полный годовой фонд зп тг
Среднемесячная зп осн.раб. тг
Среднемесячная зп наладчиков тг
Производительность труда (выпуск продукции на одного основного рабочего в год):
Nг Рсп = 2000 3 = 66667 = 667 детчел.(5.21)
Себестоимость одной единицы продукции на заводе-изготовителе составляет 1830 тг. Следовательно себестоимость детали при внедрении на производство предлагаемого в данном дипломном проекте варианта технологической подготовки производства деталей типа «вал» снизится на 246 тг. т.к.
Сбаз – С проек = 1830 – 1584 = 246 тг(5.22)
где Сбаз – базовая себестоимость одной детали;
Спроек – проектная себестоимость одной детали.
За годовой период работы участка «суммарный экономический эффект» составит:
Эгод = Nг 245 = 2000 246 = 203000 тг. (5.23)
прилож.5.dwg

Место хранения готовых деталей
Склад механического цеха
Приложение 5- Планировка участка
Список литературы.doc
Косилова А.Г.- Справочник технолога-машиностроителя. I том. – М.: Машиностроение 1986
Косилова А.Г. – Справочник технолога-машиностроителя. II том. – М.: Машиностроение 1986
Панов А.А. Обработка металлов резанием: Справочник технолога.-М.: Машиностроение 1988
Ординарцев И.А. – Справочник инструментальщика. – Л.: Машиностроение 1987
Горбацевич А.Ф. Курсовое проектирование по технологии машиностроения
Тишин С.Д. Расчеты машиностроительного времени работы на металлорежущих станках. – М.: Машиностроение1979
Горохов В.А. Проектирование и расчет приспособлений. – М.: Издательство «Вышейшая школа» 1986
Горошкин А.К. Приспособление для металлорежущих станков: Справочник. М.: Машиностроение 1971
Горошкин А.К. Приспособление для металлорежущих станков: Справочник. – М.: Машиностроение 1979
Фещенко. Обработка металлов резанием. – М.: Машиностроение. 1982
Ансеров М.А. Приспособление для металлорежущих станков. – М.: Машиностроение 1966
Маталин А.А. Проектирование техпроцессов обработки деталей на станках с ЧПУ. – Л.: Ленинград. Отделение. Машиностроение 1977
Ансеров А.А. Металлорежущие станки. – М.: Машиностроение 1965
Шатин В.П. Справочник конструктора – инструментальщика. – М.: Машиностроение 1975
Мягков В.Д. Допуски и посадки: Справочник. – Л.: Машиностроение. Ленинградское отделение 1982
Анурьев В.И. Справочник конструктора-машиностроителя I II III том - М.: Машиностроение 1980
Афонькин А.Г. Производство заготовок в машиностроении. – Л.: Машиностроение. Ленинградское отделение 1987
Дунаев П.Ф. Конструирование делателей машин. – М.: Высшая школа 1985
Общемашиностроительные нормативы режимов резания для технического нормирования на металлорежущих станках. – М.: Машиностроение 1974
Общестроительные нормативы времени вспомогательно и подготовительно-заключительного при работе на металлорежущих станках. - М.: Машиностроение 1974
Великанов К.Н. Расчет экономической эффективности новой техники: Справочник. – М.: Машиностроение 1975
Ананьев С.Л. Технологичность конструкций. – М.: Машиностроение 1969
Чарнко Д.В. Основы проектирования механо-сборочных цехов. – М.: Машиностроение 1975
Гордиенко А.В. Трактор ДТ-75М. – Алма-Ата Издательство «Кайнар» 1974
Егоров М.Е. Технология машиностроение. – Москва. – «Высшая школа» 1976
Семенченко И.И. Проектирование металлорежущих инструментов. – М.: Машиностроение 1963
Балонкина И.И. Точность и производственный контроль в машиностроение: Справочник. – Л.: Машиностроение Ленинградское отделение 1983
«Экономика предприятия»: Курс лекций Попп Л.А.
Жасимов М.М. Учебно-методическое пособие для курсового проектирования по технологии машиностроения Павлодар 1974
Новиков М.П. Основы технологии сборки машин и механизмов. – М.: Машиностроение 1969
3.1-3.3Служебное назначение детали.Анализ..doc
1 Служебное назначение и конструктивные особенности
Валы – ответственные детали основное их назначение заключается в передаче крутящего момента между различными механизмами машин и устройств.
Вал ведомый расположен в расточках литого чугунного корпуса на подшипниках и является одним из основных его узлов. Он предназначен для передачи крутящего момента от ведущего вала на рабочее колесо.
Рассматривая конструкцию вала ведомого и его расположения в узле (см. лист 2 графической части) определим конструкторские базы (поверхности) детали:
-основными поверхностями представленного вала являются цилиндрические опорные поверхности являющиеся поверхностями посадок подшипников а также посадочные поверхности рабочего колеса и полумуфты от которой передается крутящий момент;
-исполнительными поверхностями являются поверхности шпоночных пазов передающий крутящий момент от соединительной муфты на рабочее колесо на длину вала;
-вспомогательными поверхностями являются торцы вала 3 цилиндрические поверхности и резьбовые поверхности .
Остальные поверхности не сопрягаемые с поверхностями других деталей в узле являются свободными и определяют только конструктивную форму детали.
Отсюда делаем вывод что для достижения максимальной точности при изготовлении детали основные поверхности должны будут являться основными технологическими базами при механической обработке детали и для соблюдения единства баз они также должны являться конструкторскими базами
После выявления поверхностей вала исходя из анализа взаимодействия поверхностей и служебным назначаем на деталь технические требования:
Исходя из выше приведенного анализа поверхностей и особенностей конструкции насоса и детали вала вычерчиваем рабочий чертеж вала ( см. 2 лист графической части и приложение 3 ).
2 Анализ технологичности конструкции детали
В современном машиностроении обработка снятием стружки даже в весьма развитых отраслях доходит до 30-40% от общей трудоемкости изготовления машин. Поэтому технологичность деталей подвергающихся механической обработке имеет очень важное значение особенно в связи с механизацией и автоматизацией технологических процессов.
Валы и оси – ответственные детали основное их назначение заключается в размещении на них вращающихся частей (зубчатых колес шкивов барабанов дисков кулачков рычагов и т.д.). Основное назначение валов заключается в передаче крутящего момента между различными механизмами машин и устройств.
Основными показателями качества валов и осей являются точность их геометрических форм в поперечном и продольным сечениям.
Шпоночные и шлицевые соединения валов с центрированием по внутренней поверхности более трудоемки однако они могут быть изготовлены точнее чем с центрированием по наружной поверхности вала.
Эвольвентные шлицевые соединения обладают по сравнению с прямобочным повышенной прочностью благодаря утолщению шлицев у основания. Валы с эвольвентными шлицами можно изготовлять с большой точностью.
Основной конструктивной и технологической базой валов и осей является их геометрическая ось. Исходя из эксплуатационного назначения деталей рассматриваемого класса определяются основные конструктивно-технологические требования к ним которые заключаются в следующем:
прямолинейность геометрической оси;
концентричность наружных (внутренних) поверхностей относительно геометрических осей;
точное расположение шпоночных пазов шлицев резьб как относительно осей так и по поперечным сечениям деталей.
Материалом для изготовления осей и валов обычно служат углеродистые и конструкционные стали реже чугун и другие металлы. Чтобы обеспечить качественное и экономичное изготовление валов и осей учитывая перечисленные выше общие требования к ним необходимо в процессе проектирования соблюдение следующих основных требований:
Точные валы и оси целесообразно обрабатывать в центрах при этом следует предусматривать оставление центров в готовой детали на случай переточки или перешлифовки вала при ремонте. Наличие центров упрощает контроль;
Гладкие валы и оси небольших диаметров и длин целесообразно изготавливать из чистого калиброванного проката. Для ступенчатых валов особенно большой длины применение такого проката не всегда оправдано так как получение прямолинейной геометрической оси без дополнительной обработки (рихтовки упрочняющей обработки и т.п.) технологически затруднено;
Ступенчатые валы и оси должны иметь небольшие перепады диаметров при этом на разных ступенях желательно иметь одинаковые перепады. Длины ступеней должны быть одинаковыми или кратными;
В мелкосерийном производстве для более эффективного использования гидросуппортов на операциях токарной обработки целесообразно применять групповую обработку т.е. выполнять обработку валов нескольких наименований различающихся по размерам в пределах группы на одном станке с минимальной переналадкой.
При проектировании валов и осей со шлицами следует предусматривать возможность свободного выхода режущего инструмента для чего диаметр вала прилегающий к шлицевому участку выполняют меньше внутреннего диаметра шлицев. Допустимо но нежелательно превышение наружного диаметра шлицев буртом или шейкой прилегающей к шлицевому участку более чем на 3-5 мм. Необходимо избегать отверстий пересекающих закаленную зону (особенно закаливаемую ТВЧ). Такие отверстия чаще всего являются причинами появления трещин и оплавления кромок.
Для устранения этого явления следует предусматривать фаски. Также целесообразно предусматривать фаски у торцов если они подвергаются закалке с нагревом ТВЧ. Целесообразно у торцов оставлять незакаленные участки длиной l=2 – 3 мм. Длина закаленного участка может быть выполнена с точностью по длине ±3 мм. При закалке ступенчатых валов необходимо оговаривать незакаленные пояски около торцов уступов.
В итоге проанализировав рабочий чертеж детали (см. лист 2 графической части) можно сделать вывод что при проектировании конструкции детали были максимально соблюдены все вышеперечисленные требования к технологичности детали а также необходимо и достаточно установлены технические требования (см. пункт 2.2.1) на изготовление детали с учетом ее служебного назначения.
3 Анализ технических условий на изготовление деталей
Шероховатость рабочих поверхностей не грубее Ra=25 мкм.
Неравномерность твердости на поверхностях вала не должна превышать 50% от допуска на твердость указанного на чертеже.
В собранном насосе валы должна проворачиваться легко от руки легко плавно без заеданий.
Головки маслоуказателей заливной и сливной пробки должны быть окрашены в красный цвет.
Наружные поверхности насоса должны быть окрашены (за исключением таблички предприятия изготовителя и выступающих концов валов ) атмосферной эмалью.
Предельные отклонения номинальных размеров высоты осей вращения валов относительно опорных плоскостей не должны превышать указанных величин:
Высота осей мм до 50 Св. 50 до 250 Св. 250 до 630 Св. 630 до 1000
Пред. окл. мм -04 -05 -10 -15
Конструкция вала должна исключать течь масла из корпуса и проникновение внутрь грязи и воды.
На корпусе насоса должны быть предусмотрены элементы для строповки при транспортировании и во время монтажа.
Конструкция маслоуказателя и масляных систем должна исключать возможность их повреждения при транспортировки.
3.13-3.14Разработка программЧПУ.Участок..doc
На участке обработки валов в парке станков имеется токарно-винторезный станок с ЧПУ. На каждую операцию производимую на данном станке разрабатываем графы обработки (см. лист 8 графической части) и управляющие программы
Устройством ЧПУ применяемым на станке является устройство 2Р22.
Устройство ЧПУ 2Р22 является одним из первых устройств выполненных по структуре ЭВМ. Характерными особенностями этого устройства являются расширенное количество адресов гибкий формат слова; возможность программирования постоянных циклов исключения ввода коррекций непосредственно в управляющей программе и др. Все это создало определенные возможности разработки управляющей программы непосредственно с чертежа детали.
Для выполнения разработки управляющей программы с использованием устройства 2Р22 необходимо учитывать следующее:
Разработку управляющей программы необходимо вести непосредственно с чертежа детали и разработанного графа обработки. Карту расчетных перемещений следует исключить как исходный документ. Это связано с тем что конструктивное развитие устройств ЧПУ направлено в первую очередь на упрощение самого процесса разработки управляющей программы и в частности его подготовительного этапа. В этом легко убедиться при последующем сравнительном анализе трудоемкости разработки управляющей программы с учетом оснащения токарного станка устройствами ЧПУ Н22 – 1М и 2Р22.
Возможность разработки управляющей программы непосредственно с чертежа детали определяется следующими особенностями программирования:
-гибкий формат слов: незначащие нули и знак «+» можно опускать;
-числовая информация после большинства адресов имеет прямую а не косвенную размерность или кодовое обозначение; используется разделитель (точка) целой и десятичной части числа;
-легкий переход из абсолютной системы в относительную и обратно путем изменения адресов X Z U W;
-программирование обработки фасок галтелей с помощью соответствующих адресов;
-программирование радиуса круговой траектории в качестве параметра интерполяции.
Общая структура управляющей программы мало чем отличается да и не может значительно отличаться с изменением устройства ЧПУ та как согласно условия задания – граф обработки остается неизменным. При разработке управляющей программы применительно к устройству ЧПУ 2Р22 отпадает необходимость программирования смещения нуля (первые три кадра в управляющей программе для устройства ЧПУ Н22-1М) так как непосредственная работа станка по командам управляющей программы начинается с исходной точки. Правила выбора исходной точки остаются неизменными. Отпадает также необходимость программировать выход рабочего органа в нулевую точку после обработки управляющей программы. (последние 3 кадра управляющей программы; устройство ЧПУ Н22–1М). Таким образом первые кадры управляющей программы должны содержать только необходимую технологическую информацию.
В управляющей программе не используется ввод и последующий вывод коррекций. Это связано с тем что в данном устройстве ЧПУ ввод и вывод коррекций исключен из геометрической задачи ЧПУ на стадии разработки управляющей программы и включен в задачу терминальную то есть этот вид работ осуществляется непосредственно при наладке (поднастройке) станка с панели оператора.
При программировании смены инструмента перемещение рабочего органа в исходную точку непосредственно в управляющей программе не отражается. Рабочий орган самостоятельно перемещается в исходную точку по команде Т – «Смена инструмента».
Подготовка геометрической информации к кодированию
Геометрическая задача ЧПУ исторически сформировалась первой и до сих пор находится в достаточно интенсивном развитии. Суть её заключается в отображении геометрической информации чертежа в совокупность таких формообразующих движений рабочих органов станка которые материализуют чертёж в готовом изделии. Принято различать четыре фазы решения геометрической задачи ЧПУ:
- формализация геометрического образа детали;
- кодирование (разработка УП);
- управление приводами подачи.
Под формализацией геометрического образа будем понимать представление и изучение геометрической формы детали с помощью некоторых математических методов удобных для дальнейшего использования при разработке УП.
На чертеже представлена траектория движения вершины режущего инструмента при контурном точении вала. На траектории выделены точки 0 1 2 3 в которых режущий инструмент меняет направление движения. Положение каждой из этих точек строго определено в выбранной системе координат детали. Можно сказать что построенная траектория движения вершины инструмента и вычисленные координаты точек 0 1 2 3 в достаточной мере описывают т.е. формализуют геометрическую форму детали. Здесь формализация геометрического образа детали осуществлена с помощью графического отображения формообразующих движений рабочего органа токарного станка – суппорта. С целью выработки определённых правил приданию процессу формализации геометрического образа детали определённой системности воспользуемся основными понятиями теории графов относящейся к области дискретной математики особенностью которой является геометрический подход к изучению объектов или процессов.
Основным понятием теории графов является граф который в общем случае представляет собой абстрактное математическое понятие состоящее из множества вершин V; и множества рёбер W; соединяющих какие-либо пары вершин. При этом в зависимости от физической сущности решаемой задачи вершинам и рёбрам графа приписывается различный физический смысл. Воспользуемся этими понятиями для формализации геометрического описания автоматически управляемых с применением устройства ЧПУ формообразующих движений рабочих органов станка.
При обработке отдельных элементарных поверхностей детали или при переходе от обработки одной поверхности к другой рабочие органы станка совершают движения по строго заданным законам в пространстве и времени в результате чего обеспечивается требуемое относительное положение режущего инструмента и заготовки в каждый отдельно взятый момент времени. Управляемые движения рабочих органов станка по заранее заданным законам и обеспечивают требуемую форму обрабатываемых поверхностей.
Введём понятие графа обработки который также представим в виде конечного множества вершин 0 1 2 3 и соединяющих их рёбер. За вершины графа обработки будем принимать точки в которых хотя бы один рабочий орган станка качественно (направление) или количественно (скорость) меняет движение. Рёбрами графа в общем случае будем считать кривые определяющие геометрическое место точек относительного положения вершины режущего инструмента и заготовки между двумя смежными вершинами графа в процессе обработки детали.
Граф обработки детали следует рассматривать как некоторое результирующее понятие которое в одном случае в зависимости от конструктивных особенностей станка может описывать движения одного рабочего органа. В этом случае граф обработки будет плоским (обработка на токарном станке с одним суппортом).
Маршрут является замкнутым если начальная и конечная вершины графа совпадают.
Однако только графической формализации технологической операции в виде графа обработки ещё не достаточно для того чтобы приступить к разработке УП. Необходимо качественную формализацию (граф обработки) дополнить количественной которая определяла бы положение вершин графа обработки в принятой системе координат. Такого рода количественную информацию принято представлять в виде таблицы которую называют картой расчётных перемещений. Карта расчетных перемещений на первый установ.
Относительный размер
Карта расчетных перемещений на второй установ.
Устройство ЧПУ 2Р22 является одним из первых устройств выполненных по структуре ЭВМ. Характерными особенностями этого устройства являются: расширенное количество адресов гибкий формат слова; возможность программирования постоянных циклов исключения ввода коррекций непосредственно в УП и др. Всё это создало определённые возможности разработки УП непосредственно с чертежа детали.
Управляющая программа на 1 установ:
Оборудование устройство ЧПУ
Кодирование информации содержание кадра
Управляющая программа на 2 установ:
Наиболее трудоемким и ответственным этапом наладки станка с устройством ЧПУ является настройка размерных связей которая обычно выполняется с помощью нескольких операций. Процесс настройки размерных связей усложняется ещё и тем что манипулируя клавиатурой панели оператора наладчик обычно лишен наглядности настраиваемых процессов а зачастую и недопонимает те физические процессы которые реализуются в результате выполнения отдельных операций.
Поэтому анализ размерных связей на теоретическом концептуальном уровне и в практической их реализации при наладке станка являются неотъемлемой составляющей при подготовке специалистов занимающихся непосредственно эксплуатацией станков с ЧПУ в результате чего может быть обеспечена в конечном итоге эффективность эксплуатации этого оборудования.
Размерные связи в станках с устройством ЧПУ устанавливаются между отдельными системами координат и характерными точками. В станках с ЧПУ принято различать три координатные системы.
Система координат станка (СКС) которая являются главной расчетной системой для определения начальных и текущих положений рабочих органов их предельных перемещений. Начало СКС обычно привязывают к базовым поверхностям рабочего органа станка несущего заготовку (для станков токарной группы к шпинделю). Начало СКС принимают за нуль станка.
Систему координат инструмента (СКИ) в который определяют вылеты инструментов. Начало СКИ привязывают к базовым поверхностям рабочего органа несущего инструмент. Вылеты инструментов определяют с учетом элементов инструментальной оснастки. На токарных станках сменный диск револьверной головки относится к инструментальной оснастки поэтому начало СКИ привязывают к базовым элементам шпинделя револьверной головки.
Система координат детали (СКД) которая служит для определения всех размеров деталей и на их основе координат всех точек сопряжения элементарных геометрических контуров деталей и в последующем – координат вершин графа обработки. Начало СКД привязывают к базовым поверхностям детали и принимают за нуль детали.
В добавление к нулю станка и нулю детали на станках с устройством ЧПУ различают следующие характерные точки.
Фиксированные положения подвижных рабочих органов станка которые определяются конечниками ограничения движения и располагаются часто таким образом в вершинах рабочей зоны станка.
Одну из фиксированных точек принимают за нулевое положение рабочего органа. Для рассматриваемого токарного станка 16К20Ф3 нулевое положение соответствует левому и переднему крайним положениям суппорта и каретки.
Исходную точку которая определяет положение рабочего органа в СКС перед началом его работы непосредственно по командам УП. Положение этой точки выбирается с учетом беспрепятственной загрузки разгрузки заготовки без аварийной смены режущих инструментов на токарных станках.
«Плавающий нуль» определяемый возможностями современных устройств с ЧПУ изменять (переносить) начало отсчета перемещений рабочего органа относительно нулевой точки станка.
Размерные связи между рассмотренными системами координат и характерными точками можно представить в виде технологических линейных размерных цепей в направлении соответствующих осей координат.
В реальной действительности эти размерные цепи претерпевают значительные архитектурные изменения (деформации). И дело всё в том что нулевое положение рабочего органа определяемое конечниками ограничения движения на заводе изготовителя не подвергаются точной настройки – точной аттестации в силу определённых конструктивных трудностей. Поэтому значения параметров Р1 и Р4 соответствующий наибольшему диаметру обработки и нулевому значению не будут определять положения вершины некоторого резца – эталона в координатной системе станка. В действительности параметр Р1 равный для станка 16К20Ф3400 мм определит положение некоторой точки 0 в области револьверной головки а параметр Р4=0 сместит фактически начало СКС в точку 0с. С учетом этого вылеты резца эталона будут соответствовать значениям Хи Zи=0. Остальные звенья размерных цепей за исключением Zпл. Практически не претерпевают изменений но неопределенность точки 0с усложняет процесс настройки размерных связей и в частности определения вылетов режущего каждого инструмента использованного в наладке станка.
На основе этих данных на этапе технологической подготовки производства всегда можно представить эскиз наладки где все составляющие звенья размерных цепей будут достаточно точно определены. При наличии такого документа процесс настройки размерных связей может быть сведён лишь к вводу в память устройства ЧПУ значений составляющих звеньев размерных цепей что и позволит исключить пробные проходы измерения расчеты вылетов инструмента.
14 Проектирование участка
В данном разделе необходимо спроектировать участок механической обработки деталей типа «вал» входящих в узел трактора реверс-редуктор. Обработка деталей такого типа производится на одном и том же оборудовании. Количество станков необходимых для обработки 6 штук.
Основной особенностью участков механических цехов серийного производства является то что на них изготавливают детали разных машин (узлов) в большой номенклатуре но с малыми партиями с частой переналадкой станков с одной партии на другую. При обработке вала ведомого ведущего и промежуточного также требуется небольшая переналадка оборудования при переходе с одной обрабатываемой детали на другую.
Размещение станков на участке механического цеха зависит от масштаба производства и степени его специализации. В данном случае станки размещаем по принципу технологически замкнутого участка который имеет полный набор оборудования для обработки закрепленных за ним деталей. Станки располагаем в порядке последовательности выполнения операций технологического процесса что позволяет в принципе соблюдать прямоточность движения основных деталей хотя и неминуемы некоторые возвратные движения деталей.
Определим удельную площадь на один станок.
В зависимости от размеров станков характеризуемых в частности их массой удельная площадь необходимая для размещения станков составит :
для станка модели 872А – 26 м2;
для станка модели 1К62 – 29 м2;
для станка модели 1К62Ф3 – 32 м2;
для станка модели 3А153 – 20 м2;
для станка модели 6Н82 – 27 м2;
При размещении оборудования должны быть соблюдены нормы технического проектирования регламентирующие ширину проходов и проездов (не магистральных) расстояния между станками и от стен и колонн до станков.
Расстояние между станками по фронту принимаем равным 09 м между их тыльными сторонами08 м ([22]с.194таблица 15) расстояние от стены 08 м.
Планировку рабочего места станочника производим согласно методике изложенной в [22].
Здание цеха в котором располагается участок состоит из унифицированных секций шаг колонн для средних пролетов равен 12 метров для крайних – 6 метров. Ширина пролетов равна 24 метрам. Пролеты располагаются перпендикулярно пролету сборочного цеха.
В качестве подъемно-транспортного оборудования для перемещения деталей используем подвесные кран-балки грузоподъемностью 1-3 тонны с управлением снизу. Для напольной перевозки грузов используем электрокары.
Помещения для подсобных служб типа ремонтных баз мастерских по заточке инструмента и других нужд размещаются в цехе в крайних его пролетах.
4.1-4.3Проектирование приспособлений для мех.обр..doc
Основную группу технологической оснастки составляют различные приспособления машиностроительного производства. Приспособлениями в машиностроении называют вспомогательные устройства к технологическому оборудованию используемые при выполнении операций обработки сборки и контроля.
Применение приспособлений позволяет устранить разметку заготовок перед обработкой повысить точность обработки увеличить производительность труда на операции облегчить условия труда обеспечить безопасность работы расширить технологические возможности оборудования а также организовать многостаночное обслуживание и сократить число рабочих.
Изучение закономерностей влияния приспособления на точность и производительность выполняемых операций позволит проектировать приспособления интенсифицирующие производство и повышающие его точность.
При разработке приспособлений имеются широкие возможности для проявления творческой инициативы по созданию конструкций обеспечивающих наибольшую эффективность и рентабельность производства по снижению стоимости приспособлений и сокращению сроков их изготовления. Приспособления должны быть удобными и безопасными в работе быстродействующими достаточно жесткими для обеспечения заданной точности обработки удобными для быстрой установки на станок. Это особенно важно при периодической смене приспособлений в серийном производстве простыми и дешевыми в изготовлении доступными для ремонта и замены изношенных деталей.
1 Проектирование приспособления для сверлильной операции - сверление отверстий в торце детали.
Необходимо спроектировать приспособление к вертикально- фрезерному станку модели 6Н82 для операции фрезерования трех пазов на шейках вала (см. лист 4 графической части). Остальные поверхности детали обработаны в размеры по чертежу.
Тип производства – мелкосерийный годовая программа выпуска 1000 шт.детали – 2686 кг; материал – сталь Сталь40Х ГОСТ4543-88 (НВ 230 .285). Неуказанные предельные отклонения по чертежу:
охватывающих – по Н14 охватываемых – по h14 других - .
2 Выбор элементов базирования и схемы установки
Обрабатываемая деталь – вал представляет тело вращения – ступенчатый вал. Точность размеров обрабатываемой детали зависит от правильности и точности базирования а также обеспечивается режущим инструментом и наладкой.
Из анализа чертежа детали (см. 2 лист графической части) следует что точность размеров обрабатываемой детали зависит как от правильности и точности базирования так и от наладки а также обеспечивается режущим инструментом.
Обоснование применения той или иной конструкции приспособления следует связывать с такими факторами как необходимая точность при базировании обеспечение заданной производительности станка на рассматриваемой операции которая определяется программой выпуска изделий экономическая эффективность применения.
Для расширения технологических возможностей приспособления применим разборное приспособление со сменными призмами что позволит использовать данное приспособление для обработки других подобных деталей. На чертеже графической части (см. лист 7 графической части) показано приспособление с закрепленной деталью - начерчена тонкой штрих-пунктирной линией.
Для выбора элементов базирования приспособления необходим технологический эскиз базирования детали на заданной операции который был разработан ранее. На рисунке 4.1 представлена теоретическая схема базирования на рассматриваемой операции.
Заготовка в процессе обработки должна занять и сохранить в течение всего времени обработки определенное положение относительно деталей станка и (или) приспособления. Для этого необходимо лишить заготовку шести степеней свободы. Из рисунка 4.1 видно что деталь лишена шести степеней свободы посредством базовых точек приложенных в определенных местах.
Реализуем вышеприведенную схему базирования с помощью приспособления показанного на рисунке 4.2 приспособления с установкой детали в призмах.
Так как производство единичное применение механизированного приспособления на данной операции является нецелесообразным.
Покажем как в данном приспособлении реализуются точки базирования на рисунке 4.3.
Из рисунка видно что все базы в данном приспособлении реализованы и следовательно заданная чертежом точность выполняется.
На станке приспособление крепится при помощи специальных болтов с квадратной головкой закрепляемой в пазах стола станка.
Приспособление предназначено для установки детали на станке при обработки радиальных и осевых отверстий у крупногабаритных валов.
Принцип работы заключается в следующем:
Перед установкой детали в приспособление винтами поз.1 кронштейны поз.5 вместе с роликами поз.4 выводятся за опорную плоскость установочных призмы поз.6. Деталь устанавливается в приспособление она может вращаться вокруг своей оси благодаря роликам. Деталь поворачивается в нужную позицию после чего кронштейны с роликами опускаются и деталь фиксируется за счет своего веса (268кг) и осевого упора. Далее обрабатываются требуемые отверстия после чего кронштейны с роликами опять приподнимаются деталь поворачивается и выставляется на требуемый угол согласно чертежа детали и обрабатываются следующие поверхности и т.д. После обработки всех требуемых поверхностей деталь снимается.
прилож.1.dwg

3.11Расчет режимов резания.doc
Уровень режима резания находится в зависимости от типа и конструкции инструмента материала и геометрии его режущей части качества заточки правильности установки и закрепления инструмента на станке и определяет сила резания и расходуемую при резании мощность.
Назначение рационального режима резания заключается главным образом в выборе наиболее выгодного сочетания скорости резания и подачи обеспечивающих в данных условиях с учетом целесообразного использования режущих свойств инструмента и кинематических возможностей оборудования наибольшую производительность общественного труда и наименьшую стоимость операции.
Расчет режимов резания производится для наиболее труднообрабатываемой поверхности то есть той поверхности с которой снимается наибольший припуск. Этой поверхностью является поверхность диаметром 170h6. Для получения окончательного размера поверхность подвергается обработке на двух операциях:
11.1 Расчет режимов резания для операции 010
Точить размер 1703 на длину 10мм.
Глубина резания при черновой обработке равна всему припуску на обработку так как общий припуск равен 20мм разбиваем его на проходы принимаем при последнем проходе припуск t=25мм.
Подача s=0810 ммоб ([3] с.415 карта 1) для обработки стали резцом с размером державки 25х25 мм при точении детали диаметром до 100 мм с глубиной резания t=25 мм. Принимаем среднее значение подачи s=09 мм.
Скорость резания при наружном продольном точении рассчитываем по следующей формуле:
где C v x у m – постоянная для данных табличных условий показатели степени
C v = 340 х = 0.15 у = 0.45 m = 0.20 ([3]с.422 таблица 8);
Т- среднее значение стойкости инструмента Т=60 мин;
Кv – общий поправочный коэффициент на скорость резания
Кмv – коэффициент учитывающий качество обрабатываемого материала
Кмv = ([3]с.424 таблица 9) ;
Knv – коэффициент учитывающий состояние поверхности заготовки Knv =0.8 ([3]с.426 таблица 14);
Kиv - коэффициент учитывающий материал режущей части Kиv =065 ([3]с.426 таблица 15);
Кv = 1×0.8×065 = 052.
Подставляя значения в формулу 2.1 получаем:
Сила резания при наружном продольном точении рассчитываем по формуле:
где Ср x y n – постоянная для данных условий резания и показатели степени
Ср = 300 х = 1.0 у = 075 n = -015 ([2]с.429 таблица 20);
Кр – поправочный коэффициент
Кмр – поправочный коэффициент на качество материала Кмр =10;
Kjp – поправочный коэффициент на главный угол в плане j Kjp =0.89;
Кgр – поправочный коэффициент на передний угол Кgр =10;
Кrр - поправочный коэффициент на радиус при вершине r Кrр =10 ([3]с.431 таблица 24).
Подставляя значения в формулу 2.2 получаем :
Мощность резания рассчитываем по формуле:
Число оборотов шпинделя в минуту определяем по формуле
Сравнение потребляемой мощности резания с мощностью станка.
Ранее посчитанная мощность резания равна- N=112кВт. По справочнику(справочник технолога машиностроителя том2 под редакциейА.Н.Малова[3]) находим мощность токарно-винторезного станка 1К62 она равна 75квт что обеспечивает гарантированный запас мощности.
11.2 Расчет режимов резания для операции 020
Шлифовать 170h8 на длину 10мм.
Разработку режимов резания при шлифовании начинают с установления характеристики инструмента.
Выбор инструмента при абразивном и алмазном шлифовании различных конструкционных и инструментальных материалов производят по данным приведенным [3]с.331-357 таблица 170. Выбираем круг шлифовальный 300 ГОСТ 2424-67.
Окончательная характеристика абразивного или алмазного инструмента выявляется в процессе пробной эксплуатации с учетом конкретных технологических условий.
Основными элементами режима резания при шлифовании являются:
Окружная скорость рабочего круга Vк (мсек) которая для абразивных кругов обычно является максимально допускаемой прочностью круга.
Скорость вращательного или поступательного движения детали
Глубина шлифования t (мм)- слой металла снимаемый периферией или торцом круга.
Продольна подача S(мм)- перемещение шлифовального круга в направлении его оси на один оборот детали при круглом шлифовании.
Радиальная подача Sр (ммоб)- перемещение шлифовального круга в радиальном направлении.
Определяем вышеперечисленные параметры по данным приведенным в [3]с.465 таблица 69 и заносим в таблицу 3.6.
Эффективная мощность резания рассчитываем по формуле:
где d- диаметр шлифования d=60мм;
СN r СN= 13; r=075; y=07; q=02.
Подставляя значения в формулу 3.9 получаем:
1.Общая часть.doc
Насос устройство для напорного перемещения (всасывания нагнетания) главным образом жидкости в результате сообщения ей энергии (кинетической или потенциальной). Различают динамические насосы и объемные насосы. Иногда насосом называют также устройства для сжатия или разрежения газов (напр. вакуумные насосы) и для перемещения материалов (цемента и др.) потоком газа.
Объемный насос перемещает жидкость (газ в вакуумных насосах) путем периодического изменения объема рабочей камеры попеременно сообщающейся с входом и выходом насоса. Различают объемные насосы роторные поршневые диафрагменные и др.
Динамический насос насос в котором среда перемещается под силовым воздействием на нее в камере постоянно сообщающейся с входом и выходом насоса. Различают лопастные (центробежный насос) трения (струйный насос вихревой насос дисковый насос) и электромагнитные динамические насосы.
Центробежный насос динамический насос в котором жидкость перемещается под действием центробежной силы возникающей при вращении рабочего колеса с профильными лопатками. Центробежные насосы для сжатия и подачи газов называются центробежными вентиляторами и компрессорами.
В рассматриваемом случае представлен центробежный насос СДВ 2700265.
Общий вид насоса представлен на рисунке 1.1.
Материалы основных деталей: корпуса крышки рабочего колеса уплотнительных колец – чугун СЧ20; защитных втулок – сталь 30Х13; вала – сталь 40Х.
2 Определение типа производства
Ремонтно-механический цех является ремонтной базой для цехов завода. Основная задача ремонтно-механического цеха заключается в выполнении годового объема изготовления и реставрации запасных частей для всех цехов завода качественно в срок и на 100%. Поэтому каждый работник цеха должен четко знать и выполнять инструкцию соответствующую должности и профессии. Цель политики в области качества как завода так и цеха – это выполнение требований потребителей для повышения их удовлетворенности.
Возможности цеха позволяют практически полностью обеспечивать завод запасными частями полностью изготавливая их у себя. Изготовление запасных частей и агрегатов проходит полный цикл начиная с литья поковки механической обработки сборки сдачи отделу технического контроля и заканчивая отправкой на склады завода или сразу в цехи готовой продукции.
Кроме этого цех занимается реставрацией деталей узлов и агрегатов.
В случае непредвиденных ситуаций поломок оборудования остановки или аварии в цехах завода ремонтно-механический цех в кратчайший срок изготавливает требуемые детали по возможности исключая длительные простои оборудования и задержку производства.
Довольно разнообразный парк металлообрабатывающего оборудования и наличие высококвалифицированных специалистов позволяет ремонтно-механическому цеху изготавливать своими силами практически всю номенклатуру требуемых деталей. Это говорит о том что цех является надежным тылом объединения без которого невозможно обойтись.
В состав цеха входят два основных производства: литейное и механоремонтное.
Изначально материально-техническая база была спроектирована и укомплектована для массового и крупносерийного типов производств чтобы обеспечивать производственно-политические задачи того времени.
Процесс подготовки производства – это совокупность взаимосвязанных и взаимообусловленных частичных процессов создания продукции. Фазами подготовки производства являются: конструкторская технологическая и организационная подготовка производства. Чрезвычайно важным элементом организации процессов подготовки производства является определение целей организации в конкретных условиях. Этот этап имеет своей задачей определение объекта работ перечня его технико-экономических параметров срока начала и окончания работ специфических условий и требований. Все работы должны быть упорядочены во времени. Следует определить последовательность их выполнения наиболее рациональную для достижения минимума затрат времени на подготовку производства.
Важнейшим элементом работ по организации подготовки производства является обеспечение надлежащего уровня организации труда работающих и создание условий для осуществления всего комплекса работ по созданию продукции. Необходима реализация информационного материального технического и организационного обеспечения работ входящих в комплекс подготовки производства.
Тип производства оказывает главное влияние на технологию и организацию процесса сборки. Исходя из заданной производственной программы выпуска и характера подлежащих обработке деталей устанавливаем тип производства.
Особенности технологического процесса и форм организации труда зависят от объема производства одинаковых изделий за период времени. В связи с этим условно различают единичный серийный и массовый тип производства.
Согласно ГОСТ 14004-74 единичное производство характеризуется широкой номенклатурой изготавливаемых или ремонтируемых изделий с малым объемом производства.
Серийное производство характеризуется ограниченной номенклатурой изделий изготавливаемых или ремонтируемых периодически повторяющимися партиями (сериями) и сравнительно большими объемами выпуска.
Массовое производство характеризуется узкой номенклатурой и большим объемом выпуска изделий непрерывно изготавливаемых или ремонтируемых в течение продолжительного времени.
Исходя из заданной производственной программы и характера подлежащих обработке деталей устанавливаем тип производства.
Производственная программа выпуска вала массой m=321 кг составляет NB =1000Отсюда делаем вывод что тип производства серийный. В серийном производстве изделия собираются партиями повторяющимися через определенный промежуток времени.
Исходя из того что серийное производство может быть мелкосерийным среднесерийным и крупносерийным то определяем вид серийного производства. Так как количество узлов в серии N=1000то производство мелкосерийное (таблица 2[1]).
Определим режим работы и фонды времени работы оборудования и бюджета времени рабочего
Для определения количества необходимого оборудования и числа рабочих рассчитывается :
-номинальный годовой фонд времени работы оборудования ФН рассчитываем по формуле
где ФК – количество календарных дней в году ФК =365 дней;
ФП – количество праздничных дней в году ФП =8 дней;
ФВ – количество выходных дней в году ФВ =104 дня;
h – продолжительность смены h=8 часов;
Т – число часов на которое сокращается рабочая смена Т=1 час;
С – количество сокращенных рабочих дней в году С=6 дней.
Подставляя значения получаем
- действительный годовой фонд работы оборудования ФД рассчитываем по формуле
где RРЕМ – коэффициент учитывающий простои оборудования в плановом ремонте RРЕМ =0.97 – для металлорежущего оборудования;
ФД =2018*0.97=1957 часов.
-эффективный фонд времени работы оборудования ФЭФ рассчитываем по формуле
ФЭФ = ФР × RЗАГР (1.3)
где RЗАГР – средний коэффициент загрузки оборудования RЗАГР =0.80.9 принимаемый дополнительно для учета неполной загрузки оборудования при серийном и единичном производстве;
ФР – бюджет времени одного рабочего находимый из анализа фактического бюджета времени одного рабочего и возможности уменьшения потерь рабочего времени ФР =1850 часов.
ФЭФ=1850*0.8=1480 часов.
Расчет программы выпуска
Определяем программу запуска для цехов механической обработки:
где NВ – годовой объем выпуска изделий NВ =1000 шт.;
RKJ – количество деталей приходящихся на единицу изделия j типоразмера RKJ = 1 шт.;
RT – коэффициент технологических потерь учитывающий брак и другие потери RT =0.
Для сборочных цехов программа запуска принимается равной программе выпуска изделий
Так как производство является мелкосерийным то опреде6ляем величину партии т.е. количество деталей запускаемых в производство одновременно :
где N – количество деталей по годовой программе вместе с запасными частями N=1000 шт.;
Ф – число рабочих дней в году Ф=253 дня;
t – число дней на которые необходимо иметь запас деталей на промежуточном складе для бесперебойной работы сборочного цеха t=10 дней.
3.4-3.7Существующий ТП.Заготовка.doc
На данный момент существует следующий технологический процесс изготовления детали представленный в таблице 3.1.
Наименование операции
Отрезать от прутка B100 заготовку с учетом припусков на дальнейшую механическую обработку
Отрезной ножовочный станок мод. 872А
Подрезка одного торца; зацентровка центровое отверстие - В63.
Подрезка другого торца; зацентровка центровое отверстие- В63.
Обработка половины заготовки по контуру согласно чертежа.
Обработка второй половины заготовки по контуру согласно чертежа.
Токарно-винторезный станок мод. 1К62 с установленными на нем патроном трехкулачковым самоцентрирующимся
Контроль полученных на токарной операции размеров с учетом припусков под последующую шлифовку
Плита контрольная; штангенциркуль ШЦ-1-01-200 ГОСТ166-80; калибр; образцы шероховатостей
Нарезка резьбы М68х2.
Нарезка резьбы М68х15.
Токарно-винторезный станок мод. 1К62 с установленными на нем центрами с поводком
Закалка в масле с высоким отпуском НB 230 285
Печь для объемной закалки
Шлифовка посадочных шеек с одной стороны.
Шлифовка посадочных шеек с другой стороны.
Круглошлифовальный станок мод. 3А153
Фрезерование шпоночного паза.
Фрезерование стопорнго паза.
Вертикально-фрезерный станок мод. 6Н82
Зачистка заусенцев после фрезерной операции
Стол слесарный с тисками
5 Выбор заготовки. Предварительная технико-экономическая
оценка выбора заготовки по минимуму приведенных затрат
Заготовка должна гарантировать минимальную трудоемкость и себестоимость изготовления детали при заданной программе выпуска. Форма размеры и точность заготовки должны максимально приближаться к форме размерам и точности готовой детали. На выбор метода и способа получения заготовки влияют: материал детали конфигурация размеры и вес программа выпуска и др.
Заготовками для изготовления вала могут служить:
-периодический прокат;
-обжатие на ротационно-ковочных машинах;
-калиброванный прокат круглого сечения.
В условиях единичного и мелкосерийного производства для ответственных тяжело нагруженных деталей работающих в условиях переменных нагрузок а также в агрессивных средах (валы шестерни роторы и другие ответственные детали) в качестве заготовок целесообразно использовать поковки. Это такие заготовки получаемые ковкой или штамповкой поскольку в процессе деформирования создается мелкозернистая направленная волокнистая структура значительно повышающая физико-механические свойства материала ([14] с.11).
Также в условиях единичного и мелкосерийного производства для деталей представляющих собой тела вращения с относительно небольшими перепадами диаметров целесообразным является применение готового калиброванного проката круглого сечения.
В качестве примера метода получения заготовки рассмотрим штамповку и свободную ковку а также круглый прокат. Эти методы наиболее рациональны и экономически целесообразны принимая во внимание программу выпуска детали N=1000и мелкосерийность производства.
Штампованные заготовки находят широкое распространение в машиностроении в связи с их высокими механическими свойствами высокой производительностью процессов штамповки и низкой себестоимостью деталей. Часто поверхности штамповок сопрягаемые с поверхностями других деталей при сборке обрабатывают механически. В этих случаях при выборе материала детали обязательно следует учитывать не только его эксплуатационные характеристики но также пластические свойства и обрабатываемость резанием.
С технологической точки зрения наиболее просто осуществляется штамповка без нагрева заготовки. Так осуществляют холодную высадку холодное выдавливание и другие методы. Однако в этом случае материал должен обладать высокой пластичностью. Штамповку низкопластичных материалов осуществляют с нагревом заготовки что не только вызывает удлинение технологического цикла но ведет к дополнительным трудностям связанным с предотвращением окисления или газонасыщения материала изменением его микроструктуры особенно в зонах критических деформаций.
Заготовки полученные ковкой обычно подвергаются механической обработке по всем поверхностям в отличи от штампованных заготовок которые могут иметь поверхности и элементы точность и качество поверхности которых обеспечиваются в процессе штамповки. Поэтому изготовление деталей из поковок вызывает повышенный расход металла и большой объем механической обработки. Однако затраты на специальную оснастку относительно не велики.
При выборе материала следует иметь в виду что сопротивление деформированию сталей и их пластичность обеспечивающая получение готовой детали из заданной заготовки при минимальных затратах определяется главным образом процентным содержанием углерода.
Высоколегированная и жаропрочная сталь и сплавы обладают худшей деформируемостью по сравнению с инструментальной сталью большим упрочнением при высоких температурах резко выраженной гетерогенностью структуры высоким сопротивлением деформированию низкой прочностью межкристаллических связей при высоких температурах необходимостью особых условий нагрева. Хорошей технологичностью обладают детали изготовленные из углеродистых и конструкционных легированных сталей.
С учетом всего вышесказанного можно принять заготовку – штамповку. Но по причине проведенного анализа вывод таков что производство связанное с механической обработкой металлов является на да побочным хотя и необходимым только для ремонтных целей изношенных и сломанных деталей. Ремонтное производство- это производство с огромной номенклатурой выпускаемых изделий.
Отсюда вытекает что для нашего конкретного вала который является к тому же крупногабаритным оптимальной будет заготовка из калиброванного проката круглого сечения (см. рисунок 3.2).
Технические требования на заготовку:
*Размер для справок.
**Припуск на механическую обработку.
Материал: Круг В310 ГОСТ 2590-88
6 Выбор методов обработки и оборудования
6 .1 Выбор оборудования
Выбор типа станка прежде всего определяется возможностью обеспечить выполнение технических требований предъявляемых к обработанной детали в отношении точности ее размеров формы и шероховатости поверхностей а также наименьшими затратами времени и средств на обработку. Поэтому выбранное оборудование должно обладать необходимой точностью и производительностью обработки при минимальной ее себестоимости.
На фрезерно-центровальной операции используем горизонтально-расточной станок модели 2А620-1. Деталь устанавливается на призмы расстояние между которыми регулируется движением по направляющим и сверху фиксируется прижимами. Это позволяет обрабатывать заготовки разной длины.
Обработка наружных цилиндрических поверхностей вала проточка канавок снятие внутренних и наружных фасок растачивание отверстий и подрезание торцев производится на токарно-винторезном станке с ЧПУ 1М63БФ101. Применение станков с ЧПУ взамен универсального оборудования имеет существенные преимущества такие как: сокращение сроков подготовки производства на 50-75%; сокращение общей продолжительности цикла изготовления продукции на 50-60%; экономия средств на проектирование и изготовление технологической оснастки на 30-85%; повышение производительности труда за счет сокращения вспомогательного и основного времени обработки на станке и многое другое. Целесообразность применения станка с ЧПУ 1К62Ф3 заключается в том что обработку отверстий сложной геометрической формы требующих применения нескольких последовательно работающих инструментов можно выполнить без изготовления специальной оснастки (кондукторов копиров и т.д.) которая обычно применяется на универсальных станках. Возможность обработки нескольких аналогичных деталей на одном станке без переналадки оборудования а также необходимость построения технологического процесса по принципу концентрации операций т.е. сосредоточения операций возможно большего числа однотипных видов обработки на одном рабочем месте.
Для сверлильной операции возможно использование горизонтально-расточного станка модели 2651.
Обработка вала шлифованием производится круглошлифовальном станке 3А153. Станок данного типа позволяет осуществлять одновременно обработку торцов и цилиндрических поверхностей. Операции производимые ранее на круглошлифовальном станке 3А161 выполняем на станке 3А153 без смены инструмента.
6 .2 Выбор режущего инструмента
Применение того или иного типа инструмента зависит от сложности следующих факторов: вид станка метод обработки материал обрабатываемой детали ее размера и конфигурации требуемой точности и шероховатости обработки вида производства.
Для фрезерования торцов используем фрезу 160 из твердого сплава Т5К10 по ГОСТ 24359-80 правую левую (стр.137 табл.78 [5]).
Для механической обработки вала на станке с ЧПУ используется штатный инструмент идущий в комплекте с токарным станком.
Режущий инструмент для станков с ЧПУ должен удовлетворять следующим требованиям:
-обладать стабильными режущими свойствами;
- удовлетворительно формировать и отводить стружку;
-обеспечивать заданную точность обработки;
-обеспечивать возможность наладки на размер вне станка (совместно с применяемым вспомогательным инструментом).
Указанные требования не позволяют в ряде случаев использовать на станках с ЧПУ режущий инструмент применяемый на станках общего назначения.
В комплект инструмента обычно входят следующие резцы:
-резцы проходные отогнутые правые с φ=45о для обточки и подрезки торцев деталей из сталей и чугунов ГОСТ 26611-85 пластины ГОСТ19049-80;
-резцы токарные сборные для контурного точения с режущими пластинами параллелограммной формы с φ=93÷95о которые позволяют производить обточку деталей по цилиндру и конусу обрабатывать радиусные поверхности и т.д. ГОСТ 20872-80 пластины ГОСТ19079-80;
-резцы расточные с механическим креплением твердосплавных пластин для растачивания глухих отверстий и фасок ГОСТ 26212-85 пластины ГОСТ19049-80;
-резцы для проточки наружных прямых канавок шириной от1 до 6 мм;
-резцы подрезные отогнутые с пластиной трехгранной правильной формы с φ=93о ГОСТ 26611-85 пластины ГОСТ 19043-80. ([4]с.261 таблица 8.2)
Центровые отверстия сверлим центровочным сверлом ГОСТ 14952-62 ([4]с.391таблица 10.16). Обработка отверстия до 39 мм ведется набором спиральных сверл с коническим хвостовиком 34 мм и 39 мм ГОСТ 10903-77 ([4]с.368 таблица 10.8). Дальнейшую обработку отверстия 39 до размера 46+0.62 производим растачиванием на токарно-винторезном станке с ЧПУ.
В условиях серийного и мелкосерийного производства наибольшее применение находят фрезы червячные однозаходные. Фрезерование шлицев производится червячной фрезой ГОСТ 9324-80 112 ([4]с.526 таблица 13.24). В соответствии с техническими требованиями червячные фрезы должны изготавливаться из быстрорежущей стали (ГОСТ 19265-73) с твердостью рабочей части 63-66 HRCэ.
Для чистовой обработки прямозубых и косозубых колес с наружными и внутренними зубьями в диапазоне модулей 02-80 мм предназначаются шеверы ГОСТ 8570-80.
При механической обработке вала в качестве СОЖ используется 5%-ную эмульсолу Укринол-1 Аквол-11 (стр.154табл.5.2[7]) по ТУ 38-101197-76. Подвод СОЖ осуществляем через сопловые насадки свободно подающей струей с предварительным охлаждением СОЖ.
Технологическую оснастку станка составляют приспособления вспомогательный и режущий инструмент.
Приспособления предназначены для расширения технологических возможностей станков повышения их производительности и точности при обработке заготовок и облегчения условий работы на станке. Приспособления для закрепления режущего инструмента и заготовок должны обеспечивать быструю установку надежность и правильность закрепления.
Эти устройства должны быть удобны и безопасны в работе.
Для одновременного фрезерования торцов заготовки и их центрирования применяем способ закрепления заготовки на опорных призмах ГОСТ 12195-66 на фрезерно-центровальном станке.
Для токарной обработки заготовки на токарно-винторезном станке модели 16К20Ф3 используем для установки заготовки центр передний ГОСТ 13214-79 и задний центр для поджима ГОСТ 8742-75.
Для сверления осевого отверстия применяем закрепление заготовки в разжимном цанговом патроне ГОСТ 2876-80 по предварительно обработанной поверхности.
На операции шлифования заготовку с учетом анализа вариантов базирования устанавливаем в поводковом патроне ГОСТ 18260-72 и задним центром ГОСТ 13214-79.
7 Выбор методов и средств технического контроля качества
Для обеспечения надлежащего контроля необходимо правильно выбрать средства и способы контроля. При этом нужно чтобы измерительные средства соответствовали требованиям которые предъявляются к точности обрабатываемых деталей. Предельная погрешность измерительных средств не должна превышать 1020% допуска измеряемой величины. При выборе измерительных средств необходимо также учитывать экономические показатели их себестоимости время на настройку на измерение надежность работы и т.п.
Наиболее распространенным инструментом для измерения размеров деталей после черновой и получистовой токарной обработки является штангенциркуль ШЦ-1 ГОСТ 166-86. В условиях серийного производства детали измеряют предельными скобами ГОСТ 18362-73 (цилиндрические наружные поверхности) и предельными пробками ГОСТ 14810-69 (для контроля отверстий). С их помощью оценивают два размера один из которых соответствует большему отклонению а другой меньшему. Предельные калибры дают возможность контролировать одновременно размер детали и отклонение формы поверхности ограниченной проверяемым размером.
Контроль торцов и канавок в серийном производстве осуществляют шаблонами-уступомерами линейками (где не требуется высокой точности) и штангенлубиномерами. В том случае когда контроль и измерение производятся с высокой точностью применяется контрольное приспособление оснащенное индикаторами
ГОСТ 577-68 (см. лист 10 графической части). Это универсальное приспособление позволяет контролировать торцовое биение относительно геометрической оси детали и друг относительно друга отклонение формы шейки вала – овальность и непараллельность шлицев.
Шероховатость поверхности детали оцениваем путем сравнения их с эталонами чистоты ГОСТ 9378-75 представляющие собой образцы изготовленные из стали с шероховатостью обработанных поверхностей соответствующих разным степеням шероховатости поверхности. Контроль производят сравнением проверяемых поверхностей с образцами с помощью лупы или пользуясь сравнительным микроскопом позволяющим одновременно просматривать обе поверхности – эталона и проверяемой детали. А также при помощи щуповых и оптических приборов (профилометров и профилографов).
Радиальное биение измеряем индикатором ИРБ ГОСТ 5584-75 и прибором ПБ 500М ГОСТ 9696-82.Торцовое биение проверяем индикатором ИЧ 05 кл 1 ГОСМТ 557-68.
Для контроля канавок и некоторых линейных размеров применяются различные шаблоны.
3.9Расчет припусков.doc
процессов. Расчет припусков.
Рассчитать припуски на обработку и промежуточные предельные размеры на поверхность 170 вала. На остальные обрабатываемые поверхности назначить припуски и допуски по таблицам ГОСТ 7505-85. Припуск рассчитываем при условии что заготовка- круг прокатный.заготовки 2686 кг (см 2лист графической части).
Технологический маршрут обработки поверхности 170 состоит из обтачивания предварительного и окончательного и шлифования. Операции производятся в центрах.
Расчет припусков на обработку отверстия путем составления таблицы в которую последовательно записываем технологический маршрут обработки поверхности и все значения элементов припуска. Так как обработка ведется в центрах то погрешность установки в радиальном направлении равна нулю что имеет значение для рассчитываемого размера. В этом случае эта величина исключается из расчетной формулы для расчета минимального припуска и соответствующую графу можно не включать в расчетную таблицу.
Суммарное значение пространственных отклонений для заготовки данного типа определяем по формуле:
где ρсм – величина смещения ρсм =10 ([5]с.73 таблица 34);
ρкор – величина коробления детали
ρкор =Δкор l=15102=153 мкм
Δк – удельная кривизна заготовки Δк= 15мм таблица32;
l – расстояние от обрабатываемого сечения до ближайшей опоры
ρц – коэффициент погрешности после зацентровки
Допуск на поверхности используемые в качестве базовых на фрезерно-центровальной операции рассчитываем по формуле
где Нед – допуск по недоштамповке Нед=20 (таблица 41);
Иш - допуск по износу штампов Иш =09 (таблица 41);
Ку –колебания усадки Ку =10 мкммм.
Подставляя значения в формулы получаем
Значения элементов припуска заносим в таблицу 3.5
Технологические переходы обработки
поверхности 65-003 мм
Элементы припуска мкм
Расчетный припуск 2zmin мм
Расчетный размер dp мм
Предельный размер мм
Предельные значения припусков мкм
Величина остаточного пространственного отклонения после предварительного обтачивания:
ρ 1 = 006ρ з = 006 1980 = 119 мкм;
после окончательного обтачивания:
ρ 2 = 004ρ з = 004 1980 = 79 мкм;
На основании записанных в таблице данных производим расчет минимальных значений межоперационных припусков пользуясь основной формулой:
zmini = 2 (Rz i-1+T i-1+ρ i-1) (3.4)
Минимальный припуск:
под предварительное обтачивание:
под окончательное обтачивание:
zmin3 = 2 (30+30+79) = 2139 мкм.
Графа “ Расчетный размер” (dp) заполняется начиная с конечного (чертежного) размера путем последовательного прибавления расчетного минимального припуска каждого технологического перехода.
Таким образом имея расчетный чертежный размер после последнего перехода (в данном случае шлифования 70) для остальных переходов получаем:
для окончательного обтачивания:
для предварительного обтачивания:
dpз= dp1 + 2zmin1 = 6566 + 256 = 6822 мм.
Записав в соответствующей графе расчетной таблицы значения допусков на каждый технологический переход и заготовку в графе «»Наименьший предельный размер определим их значения для каждого технологического перехода округляя расчетные размеры увеличением их значений. Округление производим до того же знака десятичной дроби с каким дан допуск на размер для каждого перехода. Наибольшие предельные размеры вычисляем прибавлением допуска к округленному наименьшему предельному размеру.
Значения допусков принимаем по таблицам в соответствии с классом точности того или иного вида обработки ([1]с.7таблица 2).
Минимальные предельные значения припусков zпр.min равны разности наибольших предельных размеров выполняемого и предшествующего переходов а максимальные значения zпр.mах – соответственно разности наименьших предельных размеров.
zпр.mах3 = 6534 – 65 = 034 = 340 мкм;
zпр.mах2 = 6606 – 6534 = 072 = 720 мкм;
zпр.mах1 = 7122 – 6606 = 516 = 5160 мкм;
Все результаты произведенных расчетов сведены в таблицу3.5.
На основании данных расчета строим схему графического расположения припусков и допусков при обработке поверхности 70 (рисунок 3.7).
Общие припуски z0min и z0max определяем суммируя промежуточные
припуски и записываем их значения внизу соответствующих граф:
z0mах = 340 + 720 + 5160 = 6220 мкм.
Общий номинальный припуск:
Нз = Иш + Ку2 = 09 + 05 = 14 мм =1400 мкм;
dз.ном = dд.ном - z0ном = 6494 – 466 = 6028 мм.
Производим проверку правильности выполненных расчетов:
з – 1= 3000 – 400 = 2600 мкм;
zпр.mах2 – zпр.mах2 = 720 – 440 = 280 мкм;
– 2 = 400 – 120 = 280 мкм;
zпр.mах1 – zпр.mах1 = 340 - 280 = 60 мкм;
– 3 = 120 – 60 = 60 мкм;
На остальные обрабатываемые поверхности вала припуски и допуски назначаем по таблицам (ГОСТ 1855 – 55).
рис.2.1.dwg

Титульный.doc
Павлодарский государственный университет им. С. Торайгырова
Кафедра Технологии машиностроения
ПОЯСНИТЕЛЬНАЯ ЗАПИСКА
ДП.250140.22-04.31.06
Тема: Технологическая подготовка производства валов
насоса центробежного СДВ 2700265
Должность учёная степень
Фамилия инициалы подпись
Старший преподаватель_ _
Старший преподаватель__
3.8Выбор баз.ТП.doc
Точность детали во многом определяется выбором технологических баз при механической обработке. При проектировании технологического процесса изготовления той или иной детали в каждом конкретном случае при выборе баз необходимо учитывать ее конструктивные особенности (конфигурацию размеры жесткость и т.п.). При этом желательно осуществлять принципы постоянства баз и совмещения баз. Кроме того следует различать выбор технологических баз для обработки большинства операций технологического процесса. В первую очередь необходимо выбирать базы для обработки большинства поверхностей детали а затем базы для первой и первых операций.
Основными параметрами точности непосредственно зависящими от порядка базирования и базирующих поверхностей являются размеры и характеристики определяющие точность относительного положения обрабатываемых поверхностей. Это радиальное биение относительно общей оси поверхностей 170h6 180h8 170h8 допускается:
а) поверхности 170 h6 не более 003 мм;
б) поверхности 180 h8 не более 003 мм;
в) поверхности 170 h8 не более 003 мм;
Диаметральные размеры отверстий непосредственно не зависят от базирования.
Назначим технологические базы на основные операции технологического процесса и выберем предварительно оборудование.
Заготовительная операция. Предварительно выбираем отрезной ножовочный станок модели 872А. Схема базирования представлена на
Центровальная операция. Предварительно горизонтально-расточной станок модели 2А620-1. Схема базирования представлена на
Токарная операция. Предварительно выбираем токарно-винторезный станок с ЧПУ 1М63БФ101. Схема базирования представлена на
рисунке 3.5. Данная схема реализуется при использовании центров с поводком.
Шлифовальная операция. Предварительно выбираем круглошлифовальный станок модели 3А153. Схема базирования представлена на
рисунке 3.6. Данная схема реализуется при использовании центров с поводком.
Сверлильная операция. Предварительно выбираем горизонтально-расточной станок модели 2651. Схема базирования представлена на рисунке 3.7. Данная схема реализуется при использовании специального приспособления с призмами (разработку произведем в 4 пункте пояснительной записки).
Согласно выше проведенному выбору технологических баз и предварительному выбору оборудования разработаем несколько вариантов технологических процессов изготовления детали вала (см. таблицу 3.2-3.4).
Наименование операции
Отрезать от прутка B100 заготовку с учетом припусков на дальнейшую механическую обработку
Отрезной ножовочный станок мод. 872А
Подрезка одного торца; зацентровка центровое отверстие - В63.
Подрезка другого торца; зацентровка центровое отверстие- В63.
Обработка половины заготовки по контуру согласно чертежа.
Обработка второй половины заготовки по контуру согласно чертежа.
Токарно-винторезный станок мод. 1К62 с установленным на нем патроном трехкулачковым самоцентрирующимся
Контроль полученных на токарной операции размеров с учетом припусков под последующую шлифовку
Плита контрольная; штангенциркуль ШЦ-1-01-200 ГОСТ166-80; калибр; образцы шероховатостей
Нарезка резьбы М68х2.
Нарезка резьбы М68х15.
Токарно-винторезный станок мод. 1К62 с установленными на нем центрами с поводком
Закалка в масле с высоким отпуском НB 230 285
Печь для объемной закалки
Шлифовка посадочных шеек с одной стороны.
Шлифовка посадочных шеек с другой стороны.
Круглошлифовальный станок мод. 3А153
Фрезерование шпоночного паза.
Фрезерование стопорнго паза.
Вертикально-фрезерный станок мод. 6Н82
Зачистка заусенцев после фрезерной операции
Стол слесарный с тисками
Фрезерно-центровальная
Фрезеровка заготовки одновременно с двух сторон.
Зацентровка центровых отверстий- В63 с двух сторон.
Фрезерно-центровальный станок модели 2Г942
Токарно-винторезный станок мод. 1К62 с установленными на нем патроном трехкулачковым самоцентрирующимся
Нарезка резьбы М45х15.
Обработка второй половины заготовки по контуру согласно чертежа..
Токарно-винторезный станок с ЧПУ мод. 1К62Ф3 с установленными на нем центрами с поводком
Шлифовка посадочных шеек с подшлифовкой торца с одной стороны.
Шлифовка посадочных шеек с подшлифовкой торца с другой стороны.
Контроль полученных размеров шероховатостей параметры отклонения расположения формы поверхностей детали согласно чертежа детали.
Плита контрольная; штангенциркуль ШЦ-1-01-200 ГОСТ166-80; калибр; образцы шероховатостей; индикаторная головка.
Проанализировав приведенные технологические процессы делаем вывод что наиболее оптимальным является третий вариант технологического процесса.
Так как он содержит наименьшее число операций и в качестве оборудования в нем используются станки с ЧПУ.
Заключение.doc
В результате произведения экономических расчетов можно сделать вывод что предлагаемая в данном проекте технологическая подготовка производства деталей мелкосерийного производства (1000 штук в год) более выгодна по сравнению с базовым вариантом.
Преимущества разработанного варианта заключаются в следующем: уменьшение используемого парка станков для обработки деталей основную долю которого составляет универсальное оборудование сокращение числа основных рабочих уменьшение производственной площади участка мехобработки себестоимость детали понижается на 10%.
Предлагаю внедрить разработанный проект на производство.
3.10РазработкаТП.doc
процессов. Расчет припусков.
Тех. процесс распечатать на формате А4.
2.2Расчет размерной цепи.doc
помощью теории размерных цепей
Разработке или проведению анализа соответствия технических требований и норм точности служебному назначению машины могут способствовать теоретические исследования физической сущности явлений способствующих работе машины (узла); эксперименты на опытных образцах макетах или даже первых экземплярах машины; изучение опыта эксплуатации машин аналогичных подготовленной к изготовлению; суждения логического характера на основании опыта.
Выбору метода достижения требуемой точности машины (узла) обычно предшествует изучение рабочих чертежей. В результате изучения рабочих чертежей выявляются состав связь и взаимодействие всех сборочных единиц и деталей составляющих машину (узел).
Приступая к выбору метода достижения требуемой точности машины (узла) прежде всего необходимо сформулировать задачи которые требуется решить в процессе достижения ее точности. Эти задачи вытекают из требований к точности машины и каждая из них касается обеспечения точности одного из параметров размерной связи. Требуемая точность машины (узла) в процессе ее сборки достигается через технологические размерные цепи.
Для обеспечения заданной производительности насоса и во избежание задевания втулок на валу и в корпусе (без заклинивания) при работе между ними необходимо обеспечить после сборки наличие гарантированного оптимального зазора между торцами ротора и внутренней поверхности корпуса. Принимаем этот зазор равным АD= 4t06 мм и строим линейную размерную цепь “А” в которой АD является замыкающим (исходным) звеном цепи (1 лист графической части а также рисунок 2.1).
Размерная цепь “А” состоит из следующих составляющих ее звеньев:
А2- зазор между торцами ротора и корпуса (показан условно так как он вынесен в замыкающее звено и А2 =0) ;
А3- толщина левой накладки;
А4- расстояние между внутренним и наружным торцами корпуса;
А5- толщина прокладки;
А6- расстояние между торцами стакана;
А7- толщина правой накладки;
АD- вышеуказанный зазор – замыкающее звено.
Звенья А1А6 А7 - уменьшающие так как имеет одинаковое с замыкающим звеном направление стрелки по контуру цепи и наоборот звенья А4 А5 - увеличивающие.
Руководствуясь формулой: АD= где: (2.1)
n- количество увеличивающих звеньев (n =2);
m- общее количество звеньев цепи включая замыкающее (m=7 без звена А2=0);
Назначаем номиналы звеньям заносим в таблицу 2.1 и делаем проверочный расчет по вышеприведенной формуле 2.1:
АD= 4=А4+ А5-( А1+ А2+ А3+ А6+ А7)=392+2-(252+20+20+98)=394-390=4мм.
Найденное значение номинала соответствует принятому следовательно номиналы звеньев найдены правильно.
Находим все значения АD.
Верхнее и нижние предельные отклонения:
ЕSАD= +06мм; ЕIАD= -06мм
Допуск: ТАD= ЕSАD- ЕIАD=06-(-06)=12мм.
Координата середины поля допуска:
Ввиду мелкосерийности производства дальнейший расчет размерной цепи производим методом полной взаимозаменяемости. В этом случае величина среднего допуска на составляющие звенья находится по формуле:
- допуск замыкающего звена;
m- общее количество звеньев цепи включая замыкающее ;
Руководствуясь найденными назначаем экономически целесообразные допуски на все звенья кроме звена А6К которое принимаем в качестве корректирующего звена. Полученные данные заносим в таблицу (2.1).
Таблица 2.1- Допуски звеньев размерной цепи
Верх. и ниж. пред.откл.
Допуск на корректирующее звено находим из формулы :
Подставляем в формулу численные значения из таблицы:
Отсюда получаем: мм.
Полученные данные заносим в таблицу.
Руководствуясь формулой: ;
назначаем предельные отклонения для каждого звена кроме А6К и заносим в таблицу.
Руководствуясь формулой:
Находим координаты середин полей допусков всех звеньев (кроме звена А6К) и заносим в таблицу 2.1.
У всех остальных звеньев (кроме А1К )координаты середины полей допусков равны нулю так как у них предельные отклонения симметричны (равны).
Координату середины поля допуска корректирующего звена ЕСА1 находим из формулы :
Подставляем численные значения и получаем :
Находим верхнее и нижнее предельные отклонения корректирующего звена :
Заносим все полученные данные в таблицу 2.1 и делаем проверочный расчет по формулам :
Подставляем в формулу значения из таблицы :
Вывод: Полученные значения предельных отклонений замыкающего звена равны заданным в начале расчета следовательно значения всех составляющих звеньев найдены правильно.
Наносим размерную цепь на чертеж узла (графическая часть- лист1).
5Охрана труда.doc
1 Закон «Об охране здоровья граждан в РК»
Работодатель обязан:
)обеспечить безопасные условия труда;
)осуществлять контроль за состоянием безопасности и охраны труда;
)информировать работников о возможных вредных производственных факторах на территории организации и рабочих мест;
)принимать меры по предотвращению любых рисков на рабочих местах и в технологических процессах путем проведения профилактики замены производственного оборудования и технологических процессов на более безопасные;
)проводить обучение и подготовку работников по безопасности и охране труда в соответствии с требованиями правил и нормативов в том числе при внедрении нового оборудования и новых технологических процессов;
)разрабатывать мероприятия по безопасности и охране труда и выделять средства на проведение их в организации;
)обеспечивать работника за счет собственных средств спецодеждой спецобувью и средствами индивидуальной защиты от воздействия вредных и (или) опасных производственных факторов в установленные сроки их носки и осуществлять контроль за применением по назначению индивидуальных и коллективных средств защиты спецодежды;
)проводить инструктажи обеспечивать работников соответствующими инструктивными документами (инструкциями правилами методическими указаниями) по безопасному ведению производственного процесса и работ;
)проходить проверку знаний по вопросам безопасности и охраны труда и организовывать проверку знаний руководителей и специалистов ответственных за обеспечение безопасности и охраны труда в организациях в соответствие с правилами утвержденным уполномоченным органом;
)проводить за счет собственных средств обязательные предварительные периодические (в течение трудовой деятельности) медицинские осмотры и предсменное медицинское освидетельствование работников в случаях предусмотренных законодательством Республики Казахстан а также при переводе на другую работу с изменением условий труда либо при проявлении признаков профессионального заболевания;
)создавать работникам за счет собственных средств необходимые санитарно-гигиенические условия обеспечивать средствами профилактической обработки моющими и дезинфицирующими средствами медицинской аптечкой молоком лечебно-профилактическим питанием не ниже норм устанавливаемых уполномоченным органом а также ремонт спецодежды и обуви;
)беспрепятственно допускать должностных лиц уполномоченного органа и его территориальных подразделений представителей работников общественных инспекторов по охране труда для проведения проверок состояния безопасности условий и охраны труда в организациях и соблюдения законодательства Республики Казахстан о безопасности и охране труда а также для расследования несчастных случаев на производстве и профессиональных заболевания;
)предоставлять уполномоченному органу и его территориальным подразделениям представителям работников необходимую информацию о состоянии безопасности условий и охраны труда в организациях;
)принимать исполнять предписания государственных инспекторов труда;
)осуществлять регистрацию учет и анализ несчастных случаев и профессиональных заболеваний на производстве;
)проводить с участием представителей работников периодическую не реже чем один раз в пять лет аттестацию производственных объектов по состоянию условий труда а также обязательную аттестацию после реконструкции модернизации установления новой техники или технологии в соответствии с правилами утвержденными уполномоченным органам;
)в соответствии с законодательством Республики Казахстан возмещать вред причиненный жизни и здоровью работника;
)обеспечивать расследование несчастных случаев на производстве в порядке установленном законодательством Республики Казахстан;
)проводить в соответствие с действующими нормами и правилами безопасности и охраны труда все основные фонды находящиеся в эксплуатации;
)страховать ответственность за нанесение вреда здоровью и жизни работника при исполнении им трудовых обязанностей;
)обеспечивать гигиеническое обучение (санитарный минимум знаний по вопросам профилактики общих и профессиональных заболеваний) рабочих и специалистов занятых во вредных и опасных условиях труда;
)принимать неотложные меры по предотвращению развития аварийной ситуации и воздействия травмирующих факторов на других лиц;
)сохранять до начала расследования несчастного случая на производстве обстановку какой она была на момент происшествия если это не угрожает жизни и здоровью других лиц и не ведет к состоянию аварийной ситуации а в случае невозможности ее сохранения зафиксировать сложившуюся обстановку (составить схемы в том числе использовать фото- видеосъемки);
)сообщать в течение суток в соответствующие государственные органы о групповом несчастном случае на производстве (два человека и более) тяжелом несчастном случае либо несчастном случае со смертельным исходом.
)Сообщать о случаях острого отравления в соответствующее территориальное подразделение уполномоченного органа в области санитарно-эпидемиологического благополучия населения.
Индивидуальным трудовым либо коллективным договором с учетов специфики деятельности организации и видов работ наличия источников повышенной опасности могут быть предусмотрены дополнительные обязанности работодателя.
2 Порядок расследования несчастных случаев
О каждом несчастном случае пострадавший или очевидец обязан незамедлительно сообщить работодателю или организатору работы.
Работодатель или организатор работы обязан:
)организовать первую медицинскую помощь пострадавшему и его доставку в организацию здравоохранения;
)сохранить до начала расследования обстановку на месте несчастного случая т.е. сохранить состояние оборудования и механизмов а также орудия труда такими какими они были в момент происшествия (если это не угрожает жизни и здоровью работников а нарушение непрерывности производственного процесса не приведет к аварии) и произвести фотографирование места несчастного случая.
Ответственные должностные лица организаций здравоохранения должны информировать работодателей о каждом случае первичного обращения с травмой или иным повреждением здоровья работников на производстве а также случаях острого профессионального заболевания (отравлений) – органы государственной санитарно-эпидемиологической службы уполномоченного органа по делам здравоохранения (далее - Госсанэпидслужба).
Работодатель о несчастном случае на производстве или ином повреждении работников немедленно сообщает:
)территориальным подразделениям уполномоченного государственного органа по труду (далее – территориальное подразделение);
)представителям работников организации (профсоюзы);
)страховой организации при наличии соответствующего договора со страховой организацией;
)местным органам Госсанэпидслужбы о случаях профессионального заболевания или отравления;
В случаях профессионального или острого профессионального заболевания (отравления) в расследовании комиссии принимают участие представители органа Госсанэпидслужбы или Центра профессиональной патологии. Отдельное расследование случаев острого профессионального заболевания (отравления) производиться представителями органа Госсанэпидслужбы или Центра профессиональнойпатологии в течение двадцати четырех часов а хронического профессионального заболевания – в течение семи дней с момента получения сообщения.
В работе комиссии в праве принимать участие представитель страховой организации имеющей соответствующие договорные отношения с работодателем или пострадавшим.
Расследование несчастного случая происшедшего с работником направленным в другую организацию для выполнения производственного задания (служебных или договорных обязанностей) в том числе с лицами проходящими производственную практику обучающимися в общеобразовательных профессиональных школах и высших учебных заведениях проводится комиссией создаваемой руководителем организации на чьей территории произошло происшествие с участием полномочных представителей пострадавшего.
Расследование несчастного случая происшедшего с работником организации расположенной и ведущей работы на территории другой организации проводится его работодателем с участием ответственного представителя организации на территории которой произошел несчастный случай.
Расследование несчастных случаев происшедших в результате аварии транспортных средств проводится на основании материалов расследований органов транспортной инспекции.
Органы транспортной инспекции в пятидневный срок со дня транспортного происшествия по требованию председателя комиссии по расследованию несчастных случаев обязаны представить ему копии необходимых документов.
Несчастные случаи о которых не было своевременно сообщено работодателю или организатору работ либо в результате которых нетрудоспособность наступила не сразу (независимо от срока давности) расследуются по заявлению пострадавшего его полномочного представителя или по предписанию государственного инспектора ( далее – инспектор) труда в течение десяти дней со дня регистрации заявления получения предписания.
Расследование несчастного случая проводятся комиссией создаваемой в течение двадцати четырех часов руководителем организации с момента его наступления в составе: председателя – руководителя организации (производственной службы) или его заместителя членов – руководителя службы охраны труда организации представителя уполномоченного органа работников или доверенного лица потерпевшего (по согласованию).
Специальному расследованию подлежат:
)несчастные случаи с тяжелым или со смертельным исходом;
)групповые несчастные случаи происшедшие одновременно с двумя и более работниками независимо от степени тяжести травм пострадавших;
)групповые случаи острого профессионального заболевания (отравления).
Специальное расследование несчастного случая в зависимости от тяжести и последствий проводится в течение десяти дней комиссией создаваемой территориальным уполномоченным государственным органом по труду в составе: председателя – государственного инспектора труда членов – работодателя представителя уполномоченного органа работников или доверенного лица потерпевшего. Расследование групповых несчастных случаев при которых погибло два человека проводится комиссией которую возглавляет главный инспектор труда области городов Астаны и Алматы.
Расследование групповых несчастных случаев при которых погибло три-пять человек проводится комиссией создаваемой уполномоченным государственным органом по труду а при гибели более пяти человек – Правительством республики Казахстан.
Для решения вопросов требующих экспертного заключения председатель комиссии по специальному расследованию создает экспертные подкомиссии из числа специалистов организаций ученных и контрольно-надзорных органов.
Дальнейший поиск пострадавшего (пострадавших) без вести пропавшего (пропавших во время взрыва аварий разрушений и других случаев) на объектах организации определяется комиссией по специальному расследованию на основании заключения руководителя аварийно-спасательного подразделения и специалистов-экспертов за исключением случаев предусмотренных законодательством.
Категорически запрещается без согласия председателя комиссии по специальному расследованию проведение опроса свидетелей очевидцев а также параллельных расследований данного несчастного случая кем-либо или иной комиссией в дни работы официально назначенной комиссии.
3 Техника безопасности при работе с ручным
электрифицированным инструментом
Ручной электрифицированный инструмент (далее для краткости “электроинструмент”) должен соответствовать требованиям ГОСТ 12.2.013-87 “ССБТ. Машины ручные электрические. Общие требования по безопасности и методы испытаний”.
К работе с электроинструментом класса 1 в помещениях с повышенной опасностью поражения электрическим током и вне помещений допускается персонал имеющий группу по электробезопасности не ниже 2 а к работе с электроинструментом 2 и 3 класса – 1 группу по электробезопасности. Лица допущенные к работе с электроинструментом должны предварительно пройти обучение и проверку знаний инструкции по охране труда и иметь запись в квалификационном удостоверении и допуске к выполнению работ с применением электроинструмента.
Электроинструмент питающий от сети должен быть снабжен несъемным гибким кабелем (шнуром) со штепсельной вилкой. Несъемный гибкий кабель электроинструмента класса 1 должен иметь жилу соединяющую заземляющий зажим электроинструмента с заземляющим контактом штепсельной вилки. Кабель в месте ввода в электроинструмент должен быть защищен от истираний и перегибов эластичной трубкой из изоляционного материала. Трубка должна быть закреплена в корпусных деталях электроинструмента и выступать из них на длину не менее пяти диаметров кабеля. Закрепление трубки на кабеле вне инструмента запрещается.
Для присоединения однофазного электроинструмента шланговый кабель должен иметь три жилы: две - для питания одну - для заземления. Для присоединения трехфазного инструмента применяется четырехжильный кабель одна жила которого служит для заземления. Эти требования относятся только к электроинструменту с заземляющим корпусом.
Доступные для прикосновения детали электроинструмента класса 1 которые могут оказаться под напряжением изоляции должны быть соединены с заземляющими зажимом. Электроинструмент классов 2 и 3 не заземляется.
Заземление корпуса электроинструмента должно осуществляться с помощью специальной жилы питающего кабеля которая не должна одновременно служить проводником рабочего тока. Использовать для этой цели нулевой рабочий привод запрещается.
Штепсельная вилка должна иметь соответствующее число рабочих и один заземляющий контакт. Конструкция вилки должна обеспечивать опережающее замыкание заземляющего контакта при включении и более позднее размыкание его при отключении.
Конструкция штепсельных вилок электроинструмента класса 3 должна исключать сочленение их с розетками на напряжение свыше 42 В.
При каждой выдаче электроинструмента должны быть проверены:
-комплектность и надежность крепления деталей;
-исправность кабеля и штепсельной вилки целостность изоляционных деталей корпуса рукоятки и крышек щеткодержателей наличие защитных кожухов и их исправность (внешним осмотром);
-четкость работы выключателя;
-работа на холостом ходу.
У электроинструмента класса 1 кроме того должна быть проверена исправность цепи заземления между его корпусом и заземляющим контактом штепсельной вилки и должны быть выданы средства индивидуальной защиты )электрические перчатки галоши ковры) или разделительный трансформатор или преобразователь с раздельными обмотками или защитно-отключающее устройство.
Электроинструмент не соответствующий хотя бы одному из перечисленных требований или с просроченной датой периодической проверки выдавать для работы запрещается.
Перед началом работы необходимо проверить:
-соответствие напряжения и частоты тока в электрической сети напряжению и частоте тока электродвигателя электроинструмента указанным на табличке;
-надежность закрепления рабочего исполнительного инструмента: сверл абразивных кругов дисковых пил ключей – насадок и др.
При работе с электроинструментом класса 1 применение средств индивидуальной защиты (диэлектрических перчаток галош ковров и т.д.) обязательно за исключением следующих случаев:
-только один электроинструмент получает питание от разделительного трансформатора;
-электроинструмент получает питание от автономной двигатель – генераторной установки или от преобразователя частоты с разделительными обмотками;
-электроинструмент получает питание через защитно–отключающее устройство;
В помещениях без повышенной опасности поражения работающих электрическим током необходимо применение диэлектрических перчаток а в помещениях с токопроводящими полами – также и диэлектрических галош или ковров.
Электроинструментом класса 2 и 3 разрешается работать без применения индивидуальных средств защиты в помещениях без повышенной опасности поражения работающих электрическим током.
В сосудах аппаратах и других металлических сооружениях с ограниченной возможностью перемещения и выхода из них разрешается работать электроинструментом класса 1 и 2 при условии что только один инструмент получает питание от автономной двигатель – генераторной установки разделительного трансформатора или преобразователя частоты с разделительными обмотками а также электроинструментом класса 3. При этом источник питания (трансформатор преобразователь и т.д.) должен находиться вне сосуда а его вторичная цепь не должна заземляться.
Подключать электроинструмент напряжением до 42В в электрической сети общего пользования через автотрансформатор резистор или потенциометр запрещается.
Вносить внутрь топок и барабанов котлов конденсаторов турбин баков трансформаторов и других емкостей трансформатор или преобразователь частоты к которому присоединен электроинструмент запрещается.
При работах в подземных сооружениях а также при земляных работах трансформатор должен находиться вне этих сооружений.
Подключение вспомогательного оборудования к сети его проверку а также устранение неисправностей должен производить специально подготовленный персонал имеющий группу по электробезопасности не ниже 3.
Кабель электроинструмента должен быть защищен от случайного повреждения и соприкосновения его с горячими сырыми и масляными поверхностями.
Натягивать перекручивать и перегибать кабель ставить на него груз а также допускать пересечение его с тросами кабелями и рукавами электросварки запрещается.
Устанавливать рабочую часть электроинструмента в патрон и изымать ее из патрона а также регулировать инструмент следует после отключения его от сети штепсельной вилкой и полной остановки.
Лицам работающим с электроинструментом разбирать и ремонтировать самим инструмент кабель штепсельные соединения и другие части запрещается.
Работать электроинструментом с приставных лестниц запрещается.
Удалять стружку или опилки руками во время работы инструмента запрещается. Стружку следует удалять после полной остановки электроинструмента специальными крючками или щетками.
При работе электродрелью предметы подлежащие сверлению необходимо надежно закреплять. Касаться руками вращающегося режущего инструмента запрещается.
При сверлении электродрелью с применением рычага для нажима необходимо следить чтобы конец рычага не опирался на поверхность с которой возможно его соскальзывание.
Применяемые для работы рычаги должны быть инвентарными и храниться в инструментальной. Использовать в качестве рычагов случайные предметы запрещается.
Обрабатывать электроинструментом обледеневшие и мокрые детали запрещается.
Работать электроинструментом не защищенным от воздействия капель или брызг не имеющим отличительных знаков (капля в треугольнике или две капли) в условиях воздействия капель и брызг а также на открытых площадках во время снегопада или дождя запрещается.
Работать таким электроинструментом разрешается вне помещений только в сухую погоду а при дожде или снегопаде – под навесом на сухой земле или настиле.
Оставлять без надзора электроинструмент присоединенный к сети а также передавать его лицам не имеющим права с ним работать запрещается.
При внезапной остановке электроинструмента он должен быть отключен выключателем. При переносе электроинструмента с одного рабочего места на другое а также при перерыве в работе и ее окончании электроинструмент должен быть отсоединен от сети штепсельной вилкой.
Если во время работы обнаружится неисправность электроинструмента или работающий с ними почувствует хотя бы слабое действие тока работа должна быть немедленно прекращена и неисправный инструмент сдан для проверки и ремонта.
Запрещается работать электроинструментом у которого истек срок периодической проверки а также при возникновении хотя бы одного из следующих неисправностей:
- повреждение штепсельного соединения кабеля и его защитной трубки;
-повреждение крышки щеткодержателя;
-нечеткая работа выключателя;
-искрение щеток на коллекторе сопровождающееся появлением кругового огня на его поверхности;
-вытекание смазки из редуктора или вентиляционных каналов;
-появление дыма или запаха характерного для горящей изоляции;
-появление повышенного шума стука вибрации;
-поломка или появление трещин в корпусной детали рукоятке защитной ограждении;
-повреждение рабочей части инструмента;
-исчезновение электрической связи между металлическими частями корпуса и нулевым защитным штырем питательной вилки;
Электроинструмент и вспомогательное оборудование к нему должны подвергаться периодической проверке не реже 1 раза в 6 месяцев.
Хранить электроинструмент и вспомогательное оборудование к нему следует в сухом помещении оборудованном специальными стеллажами полками ящиками обеспечивающими его сохранность. Кроме того должны выполняться требования к условиям хранения указанные в паспорте электроинструмента.
Запрещается складировать электроинструмент без упаковки в два ряда и более.
При транспортировке электроинструмента в пределах предприятия должны быть приняты меры предосторожности исключающие его повреждение. Запрещается перевозить электроинструмент вместе с металлическими деталями и изделиями.
4 Требования пожарной безопасности
технологического оборудования
Технологическое оборудование при нормальных режимах работы должно быть пожаробезопасным а на случай опасных неисправностей и аварий необходимо предусматривать защитные меры ограничивающие масштаб и последствия пожара.
На каждом объекте на основании действующих строительных норм и правил а также по специальным перечням утвержденным соответствующими министерствами и ведомствами; должна быть определена категория взрывопожароопасности производственных цехов отдельных помещений установок и складов.
С обслуживающим персоналом предприятий должны быть изучены характеристики пожарной опасности применяемых или производимых (получаемых) веществ и материалов. Применять в производственных процессах и хранить вещества и материалы с неизученными параметрами по пожарной и взрывной опасности запрещается.
Технологическое оборудование аппараты и трубопроводы в которых обращаются вещества выделяющие взрыво – пожароопасные пары газы и пыли как правило должны быть герметичными.
Запрещается выполнять производственные операции на оборудовании установках и станках с неисправностями могущими привести к загораниям и пожарам а также при отключении контрольно – измерительных приборов по которым определяются заданные режимы температуры давления концентрации горючих газов паров и другие технологические параметры.
Работа технологического оборудования и его нагрузка должна соответствовать требованиям паспортных данных и технологического регламента.
Температура поверхностей оборудования во время работы не должна превышать температуру окружающего воздуха более чем на 45 градусов Цельсия.
Технологическое и транспортирующее оборудование должно проходить текущий и капитальный ремонт в соответствии с техническими условиями и в сроки определенные графиком.
Ремонтные работы на оборудовании набивка и подтягивание сальников на работающих насосах и компрессорах а также уплотнение фланцев на аппаратах и трубопроводах без снижения давления в системе запрещаются.
Горячие поверхности трубопроводов в помещениях в которых они вызывают опасность воспламенения материалов или взрыва газов паров жидкостей или пыли должны изолироваться негорючими материалами для снижения температуры поверхности до безопасной величины.
Технологические линии машины и аппараты осуществляющие первичную переработку волокнистых материалов твердых горючих веществ в раздробленном виде должны иметь приспособления для улавливания посторонних предметов.
Помещения в которых расположены пожаро–взрывоопасные производства следует оборудовать автоматическими средствами пожаротушения и пожарной сигнализации согласно перечням утвержденным в установленном порядке соответствующими министерствами и ведомствами.
Для контроля за состоянием воздушной среды в производственных помещениях в которых применяются производятся или хранятся вещества и материалы способные образовать взрывоопасные концентрации газов и паров должны устанавливаться автоматические газоанализаторы.
При отсутствие серийно выпускаемых газоанализаторов должен осуществляться периодический лабораторный анализ воздушной среды.
В пожароопасных цехах и на оборудовании представляющем опасность взрыва или воспламенения в соответствии с требованиями ГОСТ 15548-70 “Цвета сигнальные и знаки безопасности для промышленных предприятий” должны быть вывешены знаки запрещающие пользование открытым огнем а также знаки предупреждающие об осторожности при наличии воспламеняющихся и взрывчатых веществ.
Администрация предприятия (цеха) обязана ознакомить всех работающих со знанием таких знаков.
5 Расчет искусственного освещения помещения.
- рабочая поверхность находится на расстояние hp=125 м;
-размер объектов различия 01 мм;
-подразряд работ – 6;
-площадь помещения АхВ-50 м2;
-высота помещения Н=30м.
h = H –hp-hэ=30-125-05=125
где hp – высота рабочей поверхности над полом;
hэ – расстояние от потолка (свес);
Н – высота помещения.
Определяем оптимальное расстояние между светильниками при многорядном расположении:
L = 15*h = 15*125 = 1875 м
Так как светильник имеет к поперечным плоскости кривую света распределения типа Д для которого l = 14 размещаем светильники в 4 ряда.
Находим индекс площади помещения
¦ = А*Вh*(А+В) = 5*10125*(5+10) = 2667
По таблице находим h = 044.
Определяем потребный поток ламп уже не в светильнике (число светильников пока неизвестно) а в каждом из рядов:
Ф=Еж*Кz*S*Z h*h = 300*13*50*11 30*044 = 16250
где Е = 300 (лк) – определяется по размеру к подразряду работ;
Кz = 13 –коэффициент запаса;
h = 044 –коэффициент использования светового потока;
Z = 11 – коэффициент неравномерного освещения.
Если в светильнике установить по 2 лампы 40 Вт с потоком 3000 лм то потребное число светильников:
n = 16250 6000 =27 штук округляем 3
При длине одного светильника 124 м их общая длина составит:
Таким образом светильники необходимо расположить равномерно по центру помещения в ряд это будет наиболее благоприятно.
Аннотация(рус,англ).doc
«Технологическая подготовка производства валов
насоса центробежного СДВ 2700265»
- с. в том числе -ил. 10 листов формата А1 графической части.
Павлодарский государственный университет им. С. Торайгырова 2006 г.
В дипломном проекте представлен анализ технических условий и технологический процесс сборки насоса центробежного СДВ 2700265.
Разработан рабочий маршрутно-операционный технологический процесс механической обработки валов насоса центробежного СДВ 2700265. Приведен анализ служебного назначения и технологических условий конструкция вала ведомого отработана на технологичность обоснован выбор заготовки. Выполнены расчеты припусков и режимов резания а также нормирование технологического процесса. Разработано: механизированное приспособление для установки детали при сверлении отверстий на горизонтально-расточном станке модели 2651.
Решен комплекс вопросов организации и экономики производства: определены оптимальные для заданных условий формы организации сборки и механической обработки; выполнены соответствующие расчеты и составлена смета цеховых расходов и плановая калькуляция себестоимости вала ведомого и всего центробежного насоса СДВ 2700265 а также таблица технико-экономических показателей проекта.
В соответствии с заданием выполнены разработки по безопасности жизнедеятельности охране труда и окружающей среды.
The degree project of the student
The name of institute
First name middle initial last name.
Technological preparation of manufacture of shaft
The pump centrifugal СДВ 2700265
- With. including silt. 10 sheets of a format А1 of a graphic part.
The Pavlodar state university by him(it). With. Торайгырова 2006.
In the degree project the analysis of specifications and technological process of assembly of the pump centrifugal СДВ 2700265 is submitted.
The working маршрутно-operational technological process of machining of shaft of the pump centrifugal СДВ 2700265 is developed. The analysis of service purpose(appointment) and technological conditions is given the design of the shaft conducted is fulfilled on adaptability to manufacture the choice of preparation is proved. The accounts припусков and modes of cutting and also нормирование of technological process are executed. Is developed: the mechanized adaptation for installation of a detail at drilling apertures on horizontal - расточном the machine tool of model 2651.
The comple the appropriate accounts are executed and the estimate of the shop charges and scheduled accounting of the cost price of the shaft of conducted and all centrifugal pump СДВ 2700265 and also table of technical and economic parameters of the project is made.
According to the task the development on safety of ability to live protection of work and environment are executed.
3.12Нормирование.doc
Расчет норм времени производится также как и расчет режимов резания для самой труднообрабатываемой поверхности.
Техническое обоснование норм времени определяем аналитическим расчетным методом.
Механической обработке деталь подвергается на трех операциях:
12.1 Нормирование операции 010.
Норма времени состоит их штучного времени Тшт и подготовительно-заключительного – Тн.з.
Штучное время применительно к механической обработке детали представляет собой затрату времени необходимую на выполнение одной операции из общего технологического процесса обработки:
В общем случае Тшт определяется:
Тшт = То+Твсп+Тобсл+Тотд (3.14)
где То – основное технологическое время;
Твсп – вспомогательное время;
Тобсл – время на обслуживание рабочего места;
Тотд – время на отдых.
Время затрачиваемое на одну деталь с учетом подготовительно-заключительного времени и называемое штучно-калькуляционным временем Тшт.к
где Тп.з. – подготовительно-заключительное время на партию деталей Тп.з. = 3 мин;
n – величина партии деталей n = 79(см.п.1.3 РПЗ).
Для мелкосерийного производства техническая норма устанавливается путем применения норм на типовые технологические процессы или операции.
Формула основного времени То имеет следующее выражение:
где Lp – расчетная длина обработки в направлении подачи;
([4] с.118 таблица 4);
n – число оборотов шпинделя в минуту n = 58869 обмин;
s – подача за один оборот или на один двойной ход S = 09 ммоб;
i – число переходов i = 1
Вспомогательное время Тв расходуется рабочим на действия обеспечивающие выполнение основной работы. Вместе с основным (технологическим) временем оно составляет оперативное время. При расчете нормы штучного времени учитывается только часть вспомогательного времени не перекрываемая машинным временем.
При определении нормы вспомогательного времени суммируют следующие элементы:
- время на установку и снятие детали (если оно не перекрывается машинным временем при работе на многопозиционных станках);
- время на приемы управления станком. Сюда входит время затрачиваемое на пуск и остановку станка включение и выключение подачи изменение числа оборотов шпинделя или величины подачи поворот и перемещение частей стана и приспособлений смену инструмента в быстросменном патроне смену быстро сменных кондукторных втулок и другие приемы непосредственно обеспечивающие выполнение обработки;
- время на измерение деталей (если оно не может быть перекрыто машинным временем). Это время зависит от ряда факторов: измеряемого размера (его величины) и применяемого инструмента способа достижения размера (мерным путем настройкой системы СПИД на размер или пробными промерами) и наконец от точности измерения.
Твсп. = tуст. + tпер. + tизм.(3.17)
где tуст. – время на установку закрепление снятие детали tуст. = 086 мин. ([3] с.18 карта 5);
tпер. – время на приемы управления станков tпер. = 085 мин. ([3] с.91 Приложение 3 лист 1);
tизм. – время на контрольные измерения обработанной поверхности tизм. = 021 мин.
Твсп. = 086 + 085 + 021 = 192 мин.
Оперативное время рассчитывается по формуле
Топ = То+Твсп = 031 + 192 = 223 мин.(3.18)
Время на обслуживание рабочего места Тобсл состоит из двух частей:
) времени на техническое обслуживание рабочего места Ттех которое затрачивается на смену затупившегося режущего инструмента или правку шлифовального круга на регулировку и подналадку станка во время работы и на уборку стружки на рабочем месте во время работы.
Эта часть времени обслуживания рабочего места зависит от типа станка и характера выполняемой работы.
) времени на организационное обслуживание рабочего места Торг которое требуется для раскладки инструмента в начале смены и уборки его в конце смены осмотра и опробования оборудования получения инструктажа в течение рабочего дня смазки чистки станка в течение смены и уборки рабочего места в конце смены. Это время зависит от типа оборудования и условий работы и задается в процентах от оперативного времени.
Время перерывов на отдых и личные надобности Тотд зависит от веса обрабатываемой детали процента машинного времени величины оперативного времени характера подачи (ручная или механическая) и определяется в процентах от оперативного времени как в массовом так и в серийном производстве
Подготовительно-заключительное время Тп.з. нормируется на партию деталей и часть его приходящаяся на одну деталь включается в норму штучно-калькуляционного времени (только при серийном и единичном производстве).
В состав подготовительно-заключительного времени входит ознакомление с работой настройка оборудования на выполнение данной работы и на требуемые режимы резания пробная обработка деталей получение на рабочем месте заданий заготовок инструмента приспособлений сдача продукции и (иногда) доставка на рабочее место инструмента и приспособлений и сдача их в кладовую после окончания работы. Подготовительно-заключительное время задается по нормативам в минутах и зависит от характера и объема подготовительных работ.
Тп.з. = 7 мин. ([3] с.14 карта 1).
Штучное время рассчитываем по формуле 3.14:
Штучно-калькуляционное время находим по формуле 3.15:
12.2 Нормирование операции 020.
Формула основного времени То для шлифовальной операции имеет следующее выражение:
n – число оборотов шпинделя в минуту n = 151 обмин;
s – подача за один оборот или на один двойной ход S = 198 ммоб;
Вспомогательное время рассчитывается по формуле 3.17:
Твсп. = tуст. + tпер. + tизм.
где tуст. – время на установку закрепление снятие детали tуст. = 086 мин. ([3] с.79 карта 2);
tпер. – время на приемы управления станков tпер. = 063 мин.;
tизм. – время на контрольные измерения обработанной поверхности tизм. = 035 мин.
Твсп. = 086 + 063 + 035 = 184 мин.
Оперативное время рассчитывается по формуле 3.18:
Топ = То+Твсп = 039 + 184= 223 мин.
Время на обслуживание рабочего места Тобсл рассчитывается по
Время перерывов на отдых и личные надобности Тотд рассчитывается по формуле 3.20:
Подготовительно-заключительное время Тп.з.
Тп.з. = 12 мин. ([3] с.78 карта 1).
3.10РазработкаТП.dwg

Отрезной ножовочный станок мод. 872А
Приспособ- ление спе- циальное (рпизмы
прижим); стол поворот- ный
Подрезать торец в размер-1. 2. Просверлить центровое отверстие- А12 ГОСТ 14034-74
в размеры- 2; 3; 4; 5.
Горизон- тально расточной станок 2А620-1
Фреза торцовая насадная со вставными ножами ГОСТ 1092-692. 2. Сверло центровоч- ное 2317-0005 ГОСТ 14952-69 Р6М5.
Переустановить деталь. (перевернуть деталь
Подрезать торец в размер-6. 5. Просверлить центровое отверстие-А12 ГОСТ 14034-74
в размеры- 7; 8; 9; 10.
Резать заготовку в размер- 1.
10 Разработка технологических операций и операционных технологических процессов. Выбор оборудования.
Точить поверхность в соответствии с графом обработки
выдерживая размеры- 14; 15; 16.
Переустановить деталь.(перевернуть деталь
Токарно- винторезный станок 1M63БФ101
Резец с механич. креплением многогран- ных твердо- сплавных пластин ГОСТ 20872-80. 2. Резец отрезной ГОСТ 18884-73. 3. Резец с механич. креплением ГОСТ 20872-80
выдерживая размеры- 1; 2; 3; 4; 5; 6; 7; 8; 9; 10; 11; 12; 13.
Шлифовать в размер-1
с подшлифовкой торца в размер-2. 2. Шлифовать в размер-3
выдерживая размеры- 4; 5.
Круг шлифоваль- ный ГОСТ 2424-67
Кругло- шлифоваль- ный станок 3А153
Сверлить восемь отверстий- 1
на диаметре- 2. 2. Расточить восемь отверстий- 3
Горизон- тально- расточной станок 2651
Приспособ- ление сверлильно- расточное поворотное
Сверло спиральное- ø30; 24 ГОСТ 10903-64. 2. Головка расточная.
Сверлить восемь отверстий- 5
Индикато- рная голов- ка. 2.Штанген- циркуль ШЦ-1-0
- 1500 ГОСТ 166-80; 3.Штанген- циркуль ШЦ-1-0
- 350 ГОСТ 166-80. 3. Калибр. 4. Образцы шерохова- тостей.
Приспо- собление контроль- ное.
Плита контроль- ная.
Контролировать размеры-1; 2; 3; 4; 5; 6; 7; 8; 9; 10; 11; 12; 13. 2. Контролировать параметры отклонения расположения формы поверхностей детали согласно чертежа детали. 3. Контролировать шероховатость поверхностей.
Шлифовать в размер-6
с подшлифовкой торца в размер-7.
Содержание.doc
2Определение типа производства
Технологический процесс сборки изделия
1Анализ соответствия технических требований и норм точности служебному назначению изделия
2Выбор методов достижения требуемой точности изделия с помощью теории размерных цепей
Технологические процессы изготовления деталей
1Служебное назначение и конструктивные особенности деталей
2Анализ технологичности конструкции деталей
3Анализ технических условий на изготовление деталей
4Анализ существующих технологических процессов изготовления деталей
5Выбор заготовки. Предварительная технико-экономическая оценка выбора заготовки по минимуму приведенных затрат
6Выбор методов обработки и оборудования
7Выбор методов и средств технического контроля качества деталей
8Выбор технологических баз. Предварительная разработка маршрутных технологических процессов изготовления деталей. Предварительный выбор оборудования
9Размерный анализ различных вариантов технологических процессов. Расчет припусков.
10Разработка технологических операций и операционных технологических процессов. Выбор оборудования
11Расчет режимов резания
12Нормирование операций технологического процесса
13Разработка управляющих программ для станков с ЧПУ
14Проектирование участка
Конструкторская часть
1Проектирование приспособлений для операций механической обработки
2Выбор элементов базирования и схемы установки
3Силовой расчет приспособлений
1Закон «Об охране здоровья граждан в РК»
2Порядок расследования несчастных случаев
3Техника безопасности при работе с ручным электрофицированым инструментом
4Требования пожарной безопасности технологического оборудования
5Расчет искусственного освещения помещения
Список использованных источников
прилож.4.dwg

Введение.doc
Изначально материально-техническая база ремонтно-механических цехов была спроектирована и укомплектована для массового и крупносерийного типов производств чтобы обеспечивать производственно-политические задачи того времени.
На данный момент вся технология производства деталей требует серьезного и экономически взвешенного пересмотра так как мелкосерийный тип производства имеющий место в настоящее время на предприятии не даст необходимого экономического эффекта. Если его осуществить на оборудовании предназначенном для массового выпуска продукции поэтому в своем дипломном проекте я хочу наглядно продемонстрировать механизм себестоимости детали (типа «вал») путем анализа и улучшения производственных показателей при проектировании технологической подготовки производства.
рис.1.1.dwg

7лист_головка 4-шпиндельная.dwg

Технические характеристики: 1. Минимальный диаметр расположения отверстий под сверление- 93мм. 2. Максимальный диаметр расположения отверстий под сверление- 350мм. 3. Максимальный диаметр обрабатываемых отверстий- до 22мм. 4. Погрешность позиционирования- не более ±0
Голвка четырехшпиндельная универсальная
Технологическая подготовка производства корпусных деталей насоса центробежного нефтяного
нефтяной НК560335-70
3лист_схема сборки_олжас.dwg

насоса центробежного
5лист_технологический эскиз мех.обработки на 010 операции.dwg

5мм. 2. Торцовое биение фланца переднего конца шпинделя вместе с присоблением и валом не более- 0
5мм. 3.*Для справок.
Технические характеристики: 1. Подача станка должна состовлять- 100мммин. 2. Обороты шпинделя- 300обмин.
Технологическая подготовка производства валов насоса центробежного НК-650 в условиях ТОО "Кастинг
Технологический эскиз мех.
обработки на 010 операции
9лист_стенд сборки и контроля насоса_олжас.dwg

Технологическая подготовка производства валов насоса центробежного НК-650 в условиях ТОО "Кастинг
*Размеры для справок. 2. ±. 3. Подшипниковый узел заполнить смазкой- Литол 24 ГОСТ 21150-87.
8лист_приспособление запресовки подшипников.dwg

запрессовки подшипников
Технологическая подготовка производства валов насоса центробежного НК-650 в условиях ТОО "Кастинг
Размеры для справок. 2. Отклонение от перпендикулярности оси опоры поз.15 относителино поверхности Г не более 0
мм на длине 300мм. 3. Отоклонение от соосности осей упоров поз.3 и поз.16 относительно оси поверхности Д не более 0
Рекомендуемые чертежи
- 24.04.2014
- 24.04.2014
- 25.01.2023
- 24.01.2023
- 31.05.2024
- 28.08.2014