Современные методы восстановления деталей




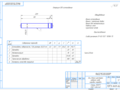
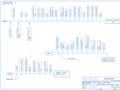
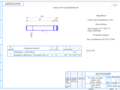
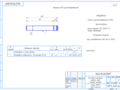
- Добавлен: 25.01.2023
- Размер: 424 KB
- Закачек: 0
Описание
Состав проекта
![]() |
![]() |
![]() ![]() ![]() ![]() |
![]() ![]() ![]() |
![]() ![]() ![]() ![]() |
![]() ![]() ![]() ![]() |
![]() ![]() ![]() ![]() |
![]() ![]() ![]() |
![]() ![]() ![]() ![]() |
![]() ![]() ![]() ![]() |
![]() ![]() ![]() |
Дополнительная информация
Операция 1 черновое А3.cdw

Центр упорный ГОСТ 18259-72.
Круг шлифовальный 600 305 63 15А50
Установить и снять деталь.
Шлифовать поверхность 1 до размера 28
Операция 090 круглошдифовальная
ПЗ.doc
2 Выбор типового технологического процесса и его краткое описание.7
3 Выбор рационального способа восстановления.8
4 Назначение методов подготовки поверхностей к восстановительным операциям и отделочных методов обработки12
5 Выбор технологических и измерительных баз схем базирования и установки.14
6. Дефекты детали и выбор способа ремонта16
7 Разработка технологического маршрута восстановления детали.17
8 Разработка технологической операции восстановления.20
8.1 Выбор оборудования и средств технологического оснащения.20
8.2 Выбор средств измерения.20
8.3 Расчет толщины слоя материала наносимого на восстанавливаемую поверхность детали.21
8.4 Определение режимов восстановления и механической обработки.22
9 Техническое нормирование.25
Разработка технологического процесса сборки (разборки) узла.30
1. Анализ конструкции узла.30
2. Сборка разъёмных соединений33
Список использованных источников.35
В процессе эксплуатации автомобилей надежность заложенная в них при производстве снижается вследствие изнашивания деталей коррозии усталости и старения материала и других вредных процессов протекающих в технике. Вредные процессы вызывают появление различных неисправностей и дефектов устранение которых становится необходимым для поддержания автомобиля в работоспособном состоянии. Отсюда возникает потребность в техническом обслуживании и ремонте.
В процессе проведения технического обслуживания и ремонта выполняются работы по устранению возникших неисправностей и замене быстроизнашивающихся деталей. Но при длительной эксплуатации наступает момент когда надежность оборудования снижается настолько что восстановление его средствами эксплутационных предприятий становится невозможным. В этом случае применяют капитальный ремонт т.к. замена деталей новыми часто менее выгодна по сравнению с восстановлением старых.
В соответствии с ГОСТ 3.1109-82 устанавливаются три вида технологических процессов:
При ремонте автомобилей на ремонтных предприятиях используются все три вида технологических процессов. Разработка того или иного вида зависит от типа предприятия. Для единичного и мелкосерийного производства разрабатываются единичные технологические процессы. Для серийного и крупносерийного производства (специализированные предприятия) групповые технологические процессы. Разработанная типовая технология является основой для разработки единичных и групповых процессов.
Использование типовых процессов облегчает решать такие задачи как выбор способа восстановления установочных (технологических баз разработки технологических маршрутов и операций) и т. д. Типизация позволяет сократить сроки разработки и освоения технологических процессов при обеспечении стабильного качества.
Данный курсовой проект включает в себя 1 лист формата А2 5 листа чертежей формата 33 листа пояснительной записки на листах формата А4 включающей 2 таблицы 6 литературных источников также технологические процессы на 7 листах формата А4.
АВТОМОБИЛЬ ВАЛ ТЕХНОЛОГИЧЕСКИЙ ПРОЦЕСС РЕМОНТ ШЛИФОВАНИЕ ОСТАЛИВАНИЕ НАПЛАВКА ВОСТАНОВЛЕНИЕ ДЕТАЛЬ.
В пояснительной записке рассмотрены технологические процессы восстановления оси блока шестерен заднего хода автомобиля ГАЗ-53. Также рассмотрены этапы ремонта технологии выбора оборудования и расчета основных параметров технологических процессов восстановления деталей.
Разработка и расчет технологического процесса ремонта детали
Восстанавливаемая деталь представляет собой ось блока шестерен заднего хода автомобиля ГАЗ-53 изготовленная из стали 40Х. Ось блока шестерен шестерен заднего хода предназначена для базирования на ней шестерен необходимых для осуществления движения задним ходом. Конструктивно- технологической особенностью детали является наличие паза по всей окружности на конце вала а так же ровная цилиндрическая поверхность большей его части. Основными дефектами являются износ оси и износ паза.
Условия в которых находится муфта довольно сложные:
- работа в нагруженных условиях;
- воздействие масляно-грязевых отложений;
- динамические нагрузки из-за непостоянства использования;
- работа при повышенном температурном режиме.
Количество производимых в год деталей равно 1000в соответствии с таблицей 3 [1] это мелкосерийный тип производства.
Конструкция детали соответствует технологическим требованиям ремонта содержит необходимые для ремонта и восстановления технологические базы. Имеющиеся дефекты не нарушают технологических баз и позволяют применить передовые способы ремонта относительные затраты на которые будут ниже по сравнению с изготовлением детали.
2 Выбор типового технологического процесса и его краткое описание.
Для выбора типового технологического процесса необходимо определить классификационную принадлежность восстанавливаемой детали.
По конструкции деталь относится к классу круглые стержни.
Типовой технологический процесс характеризуется единством содержания и последовательности большинства технологических операций и переходов для групп изделий с общими конструктивными признаками.
Основное техническое требование которое необходимо выполнить при восстановлении деталей круглые стержни – это обеспечение размеров восстанавливаемых поверхностей их твердости и прочности а так же соосности перпендикулярности и симметричности отверстий допустимой овальности и конусообразности. Технологический процесс восстановления деталей данного класса начинают с очистки от коррозии затем следует проверка состояния фасок и при необходимости их исправление. Затем производят правку детали и механическую обработку изношенных поверхностей под типовые способы восстановления. Выполняют сварочные и наплавочные операции с последующей нормализацией поверхностей при необходимости улучшения их обрабатываемости. Наплавочные поверхности подвергают чистовой и черновой механической обработке а затем нарезают резьбы фрезеруют шлицы шпоночные канавки. Для восстановления физико-механических свойств рабочих поверхностей деталей выполняют термическую обработку. Завершающей операцией является шлифование с последующим суперфинишированием или полированием точных поверхностей которое выполняется последним с целью предотвращения случайного повреждения окончательно обработанной поверхности.
3 Выбор рационального способа восстановления.
Восстановление паза:
Электродуговая наплавка обеспечивает восстановление детали с получением слоя достаточной толщины. Механические свойства наплавленного металла соответсвуют требуемым. Автоматической и полуавтоматической наплавкой удобно восстанавливать детали цилиндрической формы в частности валы и резьбовые поверхности.
Для защиты наплавляемого слоя от воздействия кислорода и азота воздуха применяют углекислый газ. Этим предотвращается окисление металла и обеспечивается удаление окислов. Для раскисления металла применяется специальная сварочная проволока. Наплавка производится по винтовой линии. Для предотвращения стекания металла необходимы небольшая сила тока и низкое напряжение. Чтобы предотвратить появление трещин при наплавке применяется местный подогрев детали.
Наплавка в среде углекислого газа. Достоинствами этого метода являются:
-меньший нагрев деталей;
-возможность наплавки в любом положении детали;
-более высокая производительность;
-возможность наплавки деталей небольшого диаметра (от 10мм);
-не требуется удалять шлаковую корку;
-стоимость ниже примерно на 20%.
-повышенное разбрызгивание металла;
-нужна легированная проволока;
-необходима защита сварщика от излучения дуги.
Автоматическая вибродуговая наплавка. Осуществляется вибрирующим электродом при помощи наплавочной головки в струе жидкости углекислого газа или воздуха для восстановления стальных деталей.
-восстановление деталей малого диаметра;
-высокая производительность для тонких слоев;
-не нужна термическая обработка;
-финишная обработка шлифованием без точения;
-небольшой нагрев деталей.
-снижение усталостной прочности;
- необходимы проволоки с большим содержанием углерода (наплавка на воздухе и в жидкости).
Сварка и наплавка под слоем флюса. Сущность процесса сварки и на плавки. Сварка (наплавка) под слоем флюса представляет собой разновидность электродуговой сварки при которой дуга горит под слоем сварочного флюса обеспечивающего защиту сварочной ванны от воздуха. Наряду с защитными функциями флюс стабилизирует горение дуги обеспечивает раскисление легирование и рафинирование расплавленного сплава сварочной ванны.
К достоинствам сварки (наплавки) под слоем флюса относится: высокая производительность процесса благодаря применению больших токов большой глубины проплавления а также почти полного отсутствия потерь металла на угар и разбрызгивание; возможность автоматизации процесса; высокое качество наплавленного металла в результате надеж ной защиты флюсом сварочной ванны; улучшение условий труда сварщика.
К недостаткам этого процесса сварки следует отнести: значителный нагрев детали; невозможность выплавки деталей диаметром менее 40мм по причине стекания расплавленных наплавляемого металла и флюса с поверхности восстанавливаемой детали; необходимость в отдельных случаях повторной термической обработки детали. При сварке под слоем флюса производительность процесса по машинному времени повышается в 6 — 12 раз по сравнению с ручной дуговой сваркой. Это достигается за счет использования больших плотностей тока в электродной проволоке.
Восстановление шейки под подшипник:
Гальванические покрытия. Сущность процесса гальванического осаждения металла на деталь заключается в получении покрытия из электролитов при прохождении через них постоянного тока. Катодом является восстанавливаемая деталь анодом – металлическая пластина. При восстановлении шеек под подшипники применяют железнение и хромирование.
Железнение – это процесс получения твердых износостойких железных покрытий из горячих хлористых электролитов. Достоинства процесса:
-высокий выход по металла по току - 85 90% (в 5-6 раз выше чем при хромировании);
-большая скорость нанесения покрытия с большой твердостью;
-простой и дешевый электролит;
-высокая прочность сцепления покрытий.
-снижается усталостная прочность деталей;
-шероховатость (бугорчитость) поверхности покрытия (из-за наличия на поверхности покрытия посторонних частиц и наличия острых кромок и углов деталей).
-высокая твердость покрытия (в 15 20 раза выше чем при ТВЧ);
-высокая износостойкость (в 3 5 раз выше чем закаленная сталь);
-низкий коэффициент трения (на 50% ниже чем у стали и чугуна);
-высокая коррозионная стойкость;
-высокая прочность сцепления с поверхностью детали.
-низкий выход металла по току;
-небольшая скорость отложения осадков;
-высокая агрессивность электролита;
-большое количество ядовитых выделений;
-толщина покрытия не более 03мм;
-плохое удержание масла гладким хромом.
Все приведенные способы удовлетворяют критерию долговечности (КД); наивысшие значения коэффициента технико–экономической эффективности имеют осталивание (КЭ=0637) и наплавка в среде углекислого газа (КЭ=0403).
4 Назначение методов подготовки поверхностей к восстановительным операциям и отделочных методов обработки
Подготовка деталей к нанесению покрытия включает следующие операции: механическую обработку поверхностей; обезжиривание в органических растворителях; монтаж детали на подвесные приспособления; изоляцию поверхностей не подлежащих осталиванию; обезжиривание деталей с последующей промывкой в воде; декапирование (анодную обработку).
Механическая обработка включает шлифование поверхностей деталей для придания им правильной геометрической формы и полирование для получения необходимой шероховатости поверхностей с использованием шлифовальных и полировальных кругов. Обезжиривание деталей предназначено для удаления с поверхностей деталей жировых загрязнений.
Деталь обезжиривают в органических растворителях: тетрахлорэтилене трихлорэтилене уайт-спирите четыреххлористом углероде и др.
Монтаж деталей осуществляют на специальные подвесные приспособления которые должны обеспечить надежный контакт с восстанавливаемой деталью и токопроводящей штангой обеспечить получение равномерного открытия и беспрепятственного удаления пузырьков водорода выделяющегося при электролизе не допустить экранирование отдельных участков детали.
Изоляция мест не подлежащих осталиванию снижает расход хрома электрического тока и повышает производительность ванны. Для защиты поверхностей детали применяют наносимый в несколько слоев цапон-лак в смеси с нитроэмалью в соотношении 1:2. Для изоляции применяют также перхлорвиниловую изоляционную ленту листовую резину пластикаты которыми плотно обматывают защищаемые поверхности. Наиболее целесообразным является применение различных футляров втулок экранов из эбонита текстолита винилпласта и т.п.
Окончательное электрохимическое обезжиривание в щелочных растворах является наиболее эффективным способом очистки поверхностей деталей. При обезжиривании стальных деталей в электролите содержащем 35 40 гл каустической соды NaOH 25 30 гл кальцинированной соды 2 3 гл жидкого стекла (·2) и 15 20 гл тринатрийфосфата (·12); при температуре электролита 65 70 С плотности тока 12 16 Адм2 продолжительность процесса 5 8 мин. Детали помещают (подвешивают) на катодную штангу. В качестве анодов применяют пластины из стали или никеля. При электролизе на поверхности детали в виде пузырьков выделяется водород который механически разрушает жировую пленку ускоряя процесс омыления и эмульгирования жиров. Выделяющийся водород проникает и вовнутрь поверхностного слоя металла вызывая его хрупкость. Поэтому в конце процесса обезжиривания переходят на анодную обработку деталей в течении 1 2 мин.
Деталь также можно обезжиривать венской известью состоящей из смеси окиси кальция окиси магния с добавкой 3% кальцинированной соды или 15% каустической соды. Порошок венской извести разводят водой до пастообразного состояния и растирают вручную по поверхности детали волосяными щетками.
После обезжиривания деталь промывают в холодной затем в горячей воде с целью удаления с поверхности детали остатков щелочных растворов которые могут загрязнить гальванические ванны. Сплошная без разрывов пленка воды на обезжиренных поверхностях свидетельствует о хорошем качестве очистки. Декапирование (анодную обработку) проводят с целью снятия окисных пленок с обрабатываемых поверхностей деталей которые образуются во время обезжиривания и промывки а так же для обнажения структуры металла детали что способствует прочному сцеплению покрытия с металлом детали. Помещенные в ванну осталивания детали выдерживают без тока в течении 1 2 мин для их прогрева до температуры электролита а затем подвергают декапированию в течении 30 45 с при анодной плотности тока 25 35 Адм2.
5 Выбор технологических и измерительных баз схем базирования и установки.
При базировании детали должно выполняться основное техническое требование – геометрические оси всех обрабатываемых цилиндрических поверхностей должны лежать на одной прямой.
Установочными базами для процесса восстановления целесообразно принять базы которые использовались при изготовлении детали. Расположены они по торцам вала.
6. Дефекты детали и выбор способа ремонта
Карта технических требований на диффектацию деталей:
Деталь: ось блока шестерен заднего хода
Твердость: По всей длине HRC60-65
Обозначение по эскизу
Наименование дефектов
Способ установления дефекта и измерительные инструменты
Допустимый без ремонта
Допустимый для ремонта
Износ шейки под роликовый подшипник по диаметру
Данная деталь подлежит ремонту т. к. :
- имеет незначительные дефекты
- имеет малую протяжённость обрабатываемых поверхностей
- затраты на ремонт детали значительно ниже производства новой детали
- конструкция детали не препятствует подводу режущего и измерительного инструмента
- при восстановлении детали используются распространённые несложные и высокопроизводительные способы
7 Разработка технологического маршрута восстановления детали.
Таблица 1. - Технологический маршрут восстановления детали.
Наименование операции и перехода
Наименование оборудования
Очистка мойка и дефектация деталей.
Моечные машины ОМ-4267 ОМ-961 ОМ-837 ОМ-947 или других типов.
Механическая обработка.
Круглошлифовальные станки 3Е151 3У132М 3У142.
Обезжиривание в органических растворителях.
Аппарат растворитель или ванна с органическими растворителями.
Рабочий стол шкаф с набором подвесок.
Обезжиривание венской известью или ее заменителями.
Ванна для обезжиривания волосянные щетки.
Промывка холодной проточной водой.
Ванна для проточной воды.
Обезжиривание электрохимическое.
Ванна электрохимического обезжиривания.
Промывка горячей водой.
Ванна с горячей водой.
Промывка холодной водой.
Ванна с проточной водой.
Продолжение таблицы 1. - Технологический маршрут восстановления детали.
Химическое травление.
Ванна для химического травления.
Промывка холодной проточной водой в двух ваннах.
Ванны с проточной водой.
Промывка в сборнике электролита.
Сборник электролита.
Снятие деталей с подвески.
Ванна для нейтрализации
Термическая обработка.
Сушильный шкаф или ванна с маслом.
Контроль качества покрытия.
Рабочий стол скоба рычажная СР-50 ГОСТ 11098-75.
Установка наплавочная ОЧС-1252А выпрямитель ВДУ 301.
Продолжение таблицы 2. - Технологический маршрут восстановления детали.
Токарный станок 1М63Н-3 и его типы
Круглошлифовальные станки 3М151 3У131М 3У142.
Специальный стол для контроля.
8 Разработка технологической операции восстановления.
8.1 Выбор оборудования и средств технологического оснащения.
Правку детали производим до полного исчезновения биения поверхности 2 относительно поверхности 1 (не более 002).
Т.к. восстановление детали производится в условиях мелкосерийного производства то целесообразно применение универсального оборудования и стандартных систем приспособлений. При механической обработке следует учитывать что обрабатываемый слой материала незначителен при этом требуется достаточно высокая точность (в пределах 002мм) поэтому следует применять круглошлифовальные станки 3М151У3У132М 3У142. В качестве абразивного инструмента следует пользоваться шлифовальным кругом ПП 300 150 30524А40ПС27К5 [3]. В процессе осталивания целесообразно применять ванны изготовленные из стальных листов покрытых кислотостойким материалом в качестве которых применяют: антигмитовые плитки (графит пропитанный фенол-формальдегидной смолой); эмалирование; керамические покрытия. Также применяют ванны из титана без покрытия.
8.2 Выбор средств измерения.
В условиях серийного производства основными средствами контроля размеров являются предельные калибры и шаблоны наиболее эффективным средством контроля для восстанавливаемой детали является скоба рычажная СР-50 ГОСТ 11098-75.
8.3 Расчет толщины слоя материала наносимого на восстанавливаемую поверхность детали.
При восстановлении деталей на их поверхности требуется нанести определенный слой материала. Толщину наносимого слоя hСЛ определяют с учетом размеров поступающих на восстановление и припуска на последующую механическую обработку. Толщину hСЛ определяют как разность между номинальным размером новой Нн и восстанавливаемой детали Ни с учетом припуска на последующую обработку Zпр:
где Zпр складывается из погрешности закрепления заготовки ЕZВ=01мм [3] таблица 7 толщины дефектного слоя СD=003мм [1] и минимального припуска на предварительную и окончательную обработку круглым шлифованием определяемого соответственно по формулам:
где –допуск мм на выполнение предшествующей операции его принимают равным допуску на соответствующий диаметр по посадке = 0053мм.
Из чего следует что:
8.4 Определение режимов восстановления и механической обработки.
Операция 015: Черновое шлифование. Осуществляется на станке 3М151. Тип обрабатываемого материала Сталь 25ХГМ абразивный материал 15А. Зернистость предварительная
Твердость предварительная СМ2. Связка керамзит. Припуск на механическую обработку определяется по таблице 11 [3] Глубина резанья за один проход равна половине припуска на механическую обработку.
Определяем тангенциальную силу резанья по формуле:
где -коэффициент. Для закаленной стали принимается равным 22для незакаленной 21принимаем ; - окружная скорость заготовки ммин; -скорость продольной подачи стола принимаем при В-ширина шлифовального круга мм :
Определяем мощность необходимую для шлифования:
где -коэффициент берется из таблицы 35 [3] .
Что удовлетворяет условию:
Определяем машинное время по формуле:
где - Припуск на механическую обработку определяется по таблице 11 [3]; -частота вращения обрабатываемой детали мин-1определяют по формуле:
Подставим известные данные в формулу:
Операция 055: Осталивание выполняется в электролите со следующим составом 300-350 гл 1-3 гл . В качестве анодов применяют стержни и пластины из малоуглеродистой стали Ст. 08 Ст. 10.
Для определения режимов техпроцесса необходимо рассчитывать время процесса электролиза:
где Адм2 - катодная плотность тока; мм - толщина покрытия; гсм3 - удельный вес осажденного металла; г(Ач) - электрохимический эквивалент; %- выход по току [5].
Операция 080: Чистовое шлифование. Осуществляется на станке 3М151. Тип обрабатываемого материала Сталь 25ХГМ абразивный материал 15А. Зернистость окончательная 40. Твердость окончательная СМ1. Связка керамзит. Глубина резанья за один проход . Окружная скорость заготовки ммин. Скорость вращения круга мс. Припуск на механическую обработку определяется по таблице 11 [3]
где -коэффициент. Для закаленной стали принимается равным 22для незакаленной 21принимаем ; - окружная скорость заготовки ммин; -скорость продольной подачи стола ммоб.
9 Техническое нормирование.
Техническая норма штучно-калькуляционного времени мин в серийном ремонтном производстве включает в себя следующие элементы затрат:
-основное (технологическое) время to необходимое для целенаправленного воздействия на объект производства;
-вспомогательное время tв затрачиваемое на установку и снятие изделия технологический переход и контрольные измерения;
-время организационного и технического обслуживания рабочего места tобс;
-время на отдых и личные надобности работающего tог;
-подготовительно-заключительное время работы tпз которое определяется для партии деталей n:
tшк =to+tв+tобс+tог+tпзn. (1.9)
Черновое шлифование.
Основное технологическое время было рассчитано по формуле (1.6): to1 = 00105мин;
Вспомогательное время tв = 02мин [3];
Время на отдых и личные надобности работающего tог составляет 7% от оперативного времени (оперативное время tоп = (to+ tв) [3]:
Подготовительно-заключительное время работы
tпз = 154мин [3] для партии из 1000шт.
tпз =миншт.; т.к. работа не требует длительных приемов то время организационного и технического обслуживания рабочего места tобс можно не учитывать.
Штучно-калькуляционное время по формуле (1.9):
Чистовое шлифование.
Основное технологическое время было расчитано по формуле (1.6): to2 = 00228мин;
Вспомогательное время tв = 04мин [3];
Время на отдых и личные надобности работающего tог составляет 7% от оперативного времени;
подготовительно-заключительное время работы
Штучно-калькуляционное время по формуле (1.9): tшк2=мин.
Процесс нанесения гальванического покрытия.
Основное технологическое время было рассчитано по формуле (1.7):
Вспомогательное время tв складывается из времени на загрузку деталей в ванну выгрузку их промывку вручную и времени на монтаж деталей на подвеску и демонтаж их.
tв = 022 + 5 = 522 мин [5].
Время на отдых и личные надобности работающего tог составляет 7% от оперативного времени (оперативное время
Подготовительно-заключительное время работы tпз складывается из времени на выдержку деталей в ваннах при выполнении дополнительных операций сушку деталей и подготовку поверхностей. Время выполнения операций сведено в таблицу 2.
Таблица 2. – Подготовительно-заключительные работы.
Наименование операции
Время на выполнение мин.
Очистка мойка и дефектация.
Электролитическое обезжиривание на катоде.
Электролитическое обезжиривание на аноде.
Прогревание в ванне хромирования перед покрытием.
Загрузка деталей в сушильный шкаф и выгрузка.
Время на протирку деталей ветошью.
Время на зачистку покрываемых поверхностей.
Время на изоляцию не покрываемых поверхностей.
Время на обезжиривание деталей венской известью.
Время на промывку деталей горячей и холодной водой.
Время на нейтрализацию.
Всего времени на подготовительно-заключительные работы.
Время организационного и технического обслуживания рабочего места tобс составляет 7% от оперативного времени [5]:
Штучно – калькуляционное время по формуле (1.8):
Штучно – калькуляционное время на выполнение всего процесса:
tшк=tшк1+tшк2+tшк3=мин.
Разработка технологического процесса сборки (разборки) узла.
1. Анализ конструкции узла.
УСТРОЙСТВО ГЕНЕРАТОРА ПОСТОЯННОГО ТОКА
В двухполюсном генераторе постоянного тока имеются: корпус 1 с крышками 22 и 18; электромагниты с полюсами 3 и обмотками 2 возбуждения; вращающийся якорь.
Корпус 1 генератора изготовлен из мягкой стали и имеет цилиндрическую форму.
С обеих сторон к корпусу присоединены две чугунные крышки 22 и 18 стягиваемые сквозными длинными болтами 17. В крышках на шарикоподшипниках 16 и 25 установлен вал 4 с якорем. Подшипник 25 со стороны привода закрыт с обеих сторон крышками с сальниками 21. Для смазки этого подшипника на крышке корпуса установлена масленка 26. Подшипник со стороны коллектора имеет сальник 14 с внутренней стороны а снаружи закрыт глухой крышкой 15 установленной на прокладке. Смазку закладывают в подшипник при сборке. При необходимости для закладывания смазки снимают крышку.
Подшипники с обеих сторон якоря закреплены на валу гайками.
На валу укреплен сердечник 5. Сердечник цилиндрической формы установлен между полюсами с небольшим зазором он служит для усиления магнитного потока между полюсами.
К коллектору прижаты при помощи пружин токосъемные щетки 13 и 20. Щетки спрессованы из угольного порошка и установлены в щеткодержателях 19 закрепленных на внутренней части крышки со стороны коллектора.
В двухполюсных генераторах имеются две щетки одна щетка 13 — минусовая — через щеткодержатель соединена с массой а другая щетка 20 — плюсовая — установлена в щеткодержателе изолированном от массы и соединена с изолированной клеммой 7 на корпусе генератора. Эта клемма имеет метку Я (якорь).
В случае регулирования работы генератора трехэлементным реле-регулятором один конец обмотки 2 возбуждения намотанной на оба полюса последовательно соединяется с массой винтом 8 а другой присоединен ко второй изолированной клемме 6 корпуса имеющей метку Ш (шунт). В корпусе генератора завернут винт с меткой М к которому присоединяется провод от клеммы М (масса) реле-регулятора.
В корпусе генератора против щеток сделаны окна для их осмотра. Окна закрыты защитной лентой 11; концы ленты стянуты винтом 12. На наружном конце вала якоря с противоположной стороны от коллектора закреплен на шпонке гайкой с шайбой приводной шкив 24 (литой или штампованный).
Генератор работает следующим образом. При вращении якоря 3 в магнитном поле создаваемом электромагнитами 2 витки обмотки якоря с большой скоростью пересекают магнитные силовые линии поля и в обмотках индуктируется Э.Д.С. а при замыкании цепи генератора по обмоткам проходит ток. Так как все витки обмотки соединены между собой последовательно через пластины коллектора 4 то общее напряжение генератора получается значительно больше напряжения каждого витка.Электрический ток вырабатываемый генератором от его щеток поступает во внешнюю сеть к потребителям. Кроме того ток проходит в обмотки возбуждения электромагнитов 2 подключенных к главным щеткам параллельно. К обмотке возбуждения ток поступает от плюсовой щетки через приборы регулирования и через массу и минусовую щетку 5 возвращается к коллектору. Проходя по обмоткам возбуждения ток намагничивает полюсы создавая между ними сильное магнитное поле в котором вращается якорь с обмотками.
В момент пуска двигателя когда в обмотках возбуждения тока еще нет ток в генераторе создается в результате наличия магнитного поля создаваемого вследствие действия остаточного магнетизма полюсов и корпуса.
Требуется составить схему сборки генератора Г-130Г. Данное изделие следует подразделить на подгруппы .В качестве базовой детали можно взять корпус генератора в сборе. Первой подгруппой является крышка со стороны коллектора в сборе; в которую входят: крышка со стороны коллектора и подшипник. Второй подгруппой является крышка со стороны привода в сборе; в которую входят: крышка со стороны привода подшипник кольца установочные болт гайка шайба.
В корпус в сборе вставляем якорь ставим установочное и уплотнительное кольца затем ставим крышки стягиваем шпильками устанавливаем щетки в сборе обтягиваем окна защитной лентой регулируем подшипники регулировочной гайкой закрываем этот узел крышкой затем запрессовываем шпонку шкив затягиваем гайку.
Большое значение для качества сборки имеет чистота деталей. Поэтому перед сборкой все детали необходимо обдуть сжатым воздухом тщательно протереть и смазать сопрягаемые поверхности.
2. Сборка разъёмных соединений
Сила предварительной затяжки
-модуль упругости стали
- площадь сечения стержня болта
k = 075 – l =075 – 0016 = 0734
P = 150 H – внешняя сила
= 75 мм -средний диаметр резьбы
S = 125 мм – шаг резьбы
= 016 – коэффициент трения в резьбе
= 016 – коэффициент трения на торце гайки
= 1215 мм – диаметр опорной поверхности
Изменение длины болта
Список использованных источников.
Курсовое проектирование по восстановлению деталей. Улашкин А.П. Тузов Н.С. ХГТУ 2000. – 140 с.
Дажин В.Г. Таблицы по расчету режимов обработки деталей. Методический материал к курсовому проектированию. ХГТУ 1988. – 63с.
Методика и основные данные для технического нормирования гальванических работ при восстановлении деталей. ХГТУ 1988. – 46с.
Ремонт автомобилей Л. В. Дехтеринский К. ". Акмаев В. П. Апсин и др.; Под ред. Л. В. Дехтеринского. – М. Транспорт 1992. – 295 с.
Справочник технолога авторемонтного производства. под. ред Г.А. Малышева – М. 1977. – 431 с.
Справочник технолога-машиностроителя: В 2 т. Под ред. А. Г. Косиловой и Р. К. Мещерякова. – М. Высшая школа 1986. –645с.
Операция 2 осталивние А3.cdw

Термическая обработка
Контроль качества покрытия
Ванна с проточной водой.
Ванна для нейтрализации.
Скоба рычажная СР-50 ГОСТ 11098-75
Операция 055 осталивание
Чертеж 1.cdw

Неуказанные предельные отклонения размеров
Неуказанные отклонения допусков формы и
расположения поверхностей по ГОСТ 25069-81
Сборка генератора.cdw

щеткодержателя 2 шт.
держатель внутренний
Титул.doc
Государственное образовательное учреждение высшего профессионального образования
Современные методы восстановления деталей
Расчетно-пояснительная записка к курсовому проекту
Операция 3 чистовое А3.cdw

Центр упорный ГОСТ 18259-72.
Круг шлифовальный 600 305 63 15А40
Установить и снять деталь.
Шлифовать поверхность 1 до размера 30 мм
Операция 090 круглошдифовальная
Чертеж 2.cdw

Реферат.doc
АВТОМОБИЛЬ ВАЛ ТЕХНОЛОГИЧЕСКИЙ ПРОЦЕСС РЕМОНТ ШЛИФОВАНИЕ ОСТАЛИВАНИЕ НАПЛАВКА ВОССТАНОВЛЕНИЕ ДЕТАЛЬ.
В пояснительной записке рассмотрены технологические процессы восстановления оси блока шестерен заднего хода. Также рассмотрены этапы ремонта технологии выбора оборудования и расчета основных параметров технологических процессов восстановления деталей.
Рекомендуемые чертежи
- 24.10.2015
- 24.01.2023
- 25.01.2023
- 04.03.2024