Проектирование технологических процессов восстановления деталей машин в АПК




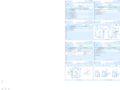
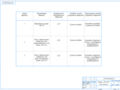
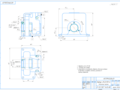
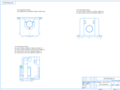
- Добавлен: 24.01.2023
- Размер: 552 KB
- Закачек: 1
Описание
Состав проекта
![]() |
![]() |
![]() ![]() ![]() ![]() |
![]() ![]() ![]() ![]() |
![]() ![]() ![]() ![]() |
![]() ![]() ![]() |
![]() ![]() ![]() ![]() |
![]() ![]() ![]() ![]() |
Дополнительная информация
Лист 2-2 (А2).cdw

Обозначение маршрутов:
Подготовка технологических баз
Лист 3 (А1).frw

выдерживая размеры 1
ОРГ-1468-01-090А Верстак - Дефект. 4 Нр 1 1 1 1 - Т
Износ резьбы М8-7Н 2-3 витка Пробка резьбовая М8-7Н ГОСТ 17763-72
Износ поверхности отверстия под шарикоподшипник 42
Нутромер индикаторный НИ 18-50-2
Износ поверхности отверстия под валик 10
Нутромер индикаторный НИ 10-18-2
ГОСТ 3.1104-84 Форма 7a
ГОСТ 3.1404-86 Форма 1
наименование оборудования
наименование операции
Обозначение документа
5 Горизонтально-фрезерный
Р83Г Горизонтально-фрезерный 13 6
М-132 Моечная машина
ОРГ-1468-01-090А Верстак 14 6
ГОСТ 3.1404-86 Форма 1a
Карта эскизов Наплавочная
Маршрутная карта Наплавочная
сб. единицы или материала
Выпрямитель сварочный
ВДГ-303 - Свар. 3 нр - 1 1 1 18
ОРГ-1468-01-090А Верстак
электрод Э-42 ГОСТ1504-82 14 5
5 Горизонтально-расточная
А181а Горизонтально-расточной 16 9
0 Радиально-сверлильная
М55 Радиально-сверлильный 16 3
А181а Горизонтально-расточной 20 6
0 Горизонтально-расточная
электрод Э-42 ГОСТ1504-82 15 3
электрод Э-42 ГОСТ1504-82 18 5
А181а Горизонтально-расточной 12 7
Приспособление специальное;
Штангенциркуль ШЦ-1-125-0
Контроль размеров исполнителем
электрод Э-42 ГОСТ1504-82;
Маршрутная карта Дефектовочная
наименование дефекта ПЗП ПЗПР ДЗП СТО
Корпус 25.22.101-А проверить размеры
Маршрутная карта Горизонтально-расточная
А181а Горизонтально-расточной 1 Ток 3 нр 1 1 1 - 1 16мин 4
Сверлить 3 отверстия под резьбу
Сверло 2310-0026 ГОСТ 28320-89;
Нарезать резьбу М8-7Н в трех отверстиях
Метчик 2621-1433 ГОСТ 3266-81;
Карта эскизовГоризонтально-расточная
Карта эскизов Дефектовочная
Лист 2-1 (А2).cdw

Установка свертного
кольца с последующим
Записка (исправления).docx
На тему: «Проектирование технологических процессов восстановления деталей машин в АПК».
Данный курсовой проект содержит графическую и расчетную часть.
В расчетной части описывается техническая характеристика детали определяется коэффициент повторяемости сочетаний дефектов изношенных поверхностей детали производится выбор рациональных способов устранения дефектов детали производится разработка технологического процесса восстановления детали производится расчет экономической эффективности восстановления детали.
Графическая часть объемом 3 листа формата А1.
Лист №1 – ремонтный чертеж детали (А2) схемы базирования детали (А2).
Лист №2 – Карта дефектов детали (А2) схема технологического маршрута восстановления детали (А2).
Лист №3 – Комплект технологической документации на восстановление детали (А1).
Техническая характеристика детали ..8
Определение коэффициентов повторяемости сочетаний
дефектов изношенных поверхностей детали 9
Выбор рациональных способов устранения дефектов детали .11
Разработка технологического процесса восстановления детали ..15
Техника безопасности работ при восстановлении детали .23
Определение экономической эффективности и целесообразности
восстановления детали .30
Список литературы 35
Эффективное использование машин и оборудования в сельском хозяйстве обеспечивается высоким уровнем их технического обслуживания и ремонта наличием необходимого числа запасных частей. Сбалансированное обеспечение запасными частями ремонтных предприятий и сферы эксплуатации машин и оборудования как показывают технико-экономические расчеты целесообразно осуществлять с учетом периодического возобновления работоспособности деталей восстановленных современными способами.
Восстановление деталей машин обеспечивает экономию высококачественного материала топлива энергетических и трудовых ресурсов а также рациональное использование природных ресурсов и охрану окружающей среды.
Основной целью курсового проекта является самостоятельное решение студентом инженерных задач связанных с проектированием технологических процессов восстановления изношенных деталей обоснованием рациональных способов восстановления и режимов обработки детали минимизации затрат и обеспечение конкурентоспособности ремонтного производства.
Объектом исследования в курсовом проекте является корпус 25.22.101-А.
Предметом исследования являются дефекты детали и технологический процесс их устранения.
Для достижения поставленной цели курсового проекта необходимо решить следующие задачи:
- провести анализ условий работы детали корпус 25.22.101-А выявить виды изнашивания которым подвергаются основные рабочие поверхности детали;
- определить коэффициенты повторяемости сочетаний дефектов;
- обосновать рациональные способы восстановления каждой изнашиваемой поверхности детали;
- обосновать рациональные способы восстановления детали;
- разработать технологическую документацию восстановления деталей на основе рациональных методов с выбором технологического оборудования приспособлений рабочих инструментов средств контроля;
- установить режимы обработки и нормы времени выполнения операций;
- обосновать целесообразность восстановления деталей с различными сочетаниями дефектов;
- разработать мероприятия по обеспечению техники безопасности работ по восстановлении детали.
Техническая характеристика детали
Деталь — корпус 25.22.101-А (рис. 1) представляет собой тело сложной комплексной формы. Основное назначение корпуса – размещение в его полости рабочих деталей гидропривода в требуемом пространственном положении. Материал – чугун СЧ 15 ГОСТ 1412-85.детали 34 кг.
Рисунок 1 – Эскиз корпуса 25.22.101-А
Диаметры и линейные размеры корпуса назначены из нормального ряда размеров. Неуказанная шероховатость поверхностей Ra=25 мкм.
Наиболее жесткие требования по точности предъявляются к цилиндрической внутренней поверхности 42 (Ra 125) так как эта поверхность является базовой для размещения подшипника 104. Относительно этой поверхности размещаются остальные детали привода.
Рабочие поверхности корпуса при эксплуатации испытывают повышенные механические вибрационные и ударные нагрузки.
Деталь технологична.
Следует отметить что корпус для своей обработки не требует сложного технологического оборудования. Он может быть обработан с достаточной степенью точности на оборудовании нормального класса точности «Н» и контрольно-измерительных средств по ГОСТ 2789-73
ГОСТ 8026-75 ГОСТ 577-68.
Технологическими базами заготовки служат торец и два отверстия в нем.
Определение коэффициентов повторяемости сочетаний дефектов изношенных поверхностей детали
В общем случае коэффициент повторяемости дефектов определяется по формуле
N – общее количество одноименных деталей в партии.
Вероятность того что деталь имеет i- дефект определяется из выражения
Вероятность того что деталь не имеет i- дефект определяется из выражения
Тогда вероятность появления деталей со всеми возможными дефектами определяется по формуле
Коэффициент повторяемости сочетания дефектов 12 (n-1) будет равен
Коэффициент повторяемости сочетания дефектов 12
Коэффициент повторяемости одного дефекта 1
Коэффициент повторяемости деталей не имеющих дефектов
Основные дефекты детали и их коэффициенты повторяемости:
Повреждение резьбы (А) К1=021;
Износ поверхности отверстия под подшипник (Б) К2=035;
Износ поверхности отверстия под валик (В) К3=045.
Определяем коэффициенты повторяемости сочетаний дефектов изношенной детали. При трех дефектах у детали могут встречаться следующие их сочетания:
одновременно все три дефекта – Х123;
только первый и второй дефект - Х12;
только первый и третий дефект - Х13;
только второй и третий дефект – Х23;
только первый дефект – Х1;
только второй дефект – Х2;
только третий дефект – Х3;
не имеющий ни одного дефекта - Х0;
Тогда коэффициенты повторяемости сочетаний дефектов:
33 + 0042 + 0061 + 0124 + 0075 + 0152 + 0231 + 0282 =1
Выбор рациональных способов устранения дефектов детали
Каждая изношенная поверхность может быть восстановлена несколькими способами. По рекомендациям таблицы 1 [1 стр. 7] устанавливаем возможные способы восстановления каждой поверхности по технологическому критерию.
Поверхность А – ручная наплавка (заварка отверстия) установка резьбовой спиральной вставки.
Поверхность Б – ручная наплавка установка свертного кольца с последующим зенкерованием и развертыванием.
Поверхность В – ручная наплавка установка свертного кольца с последующим зенкерованием и развертыванием.
Определяем коэффициент долговечности каждого вида обработки по формуле
где КИ – коэффициент износостойкости КВ – коэффициент выносливости КСЦ – коэффициент сцепляемости.
Коэффициент долговечности численно принимается равным значению того коэффициента который имеет минимальную величину. Численные значения коэффициентов определяем по табл. 2 [1 стр. 8] и заносим в таблицу 1.
Так как условию КД > 08 удовлетворяют все выбранные способы восстановления деталей то выбор оптимального проводим по технико-экономическому показателю численно равному отношению себестоимости восстановления к коэффициенту долговечности для этих способов. Окончательно выбирается способ который обеспечивает минимальное значение этого отношения:
где СВ – себестоимость восстановления соответствующей поверхности.
При обосновании способов восстановления поверхностей значение себестоимости восстановления определяется по формуле
где Су – удельная себестоимость восстановления рубдм2; S – площадь восстанавливаемой поверхности дм2.
Значения Су принимаем по рекомендациям табл. 3 [1 стр. 9] с учетом коэффициента инфляции равного 10.
Площадь восстанавливаемой поверхности определяем при помощи программных средств редактора «Компас».
Принятые значения сводим в таблицу 1.
Таблица 1 – Технико-экономическая характеристика способов восстановления поверхностей корпуса
Способ восс-тановления
Повреждение резьбы (А)
Резьбовая спиральная вставка
Износ поверхности отверстия под подшипник (Б)
Установка свертного кольца
Износ поверхности отверстия под валик (В)
Из таблицы 1 видно что оптимальными способами восстановления изношенных поверхностей являются следующие
для поверхности А – ручная наплавка (заварка отверстия);
для поверхности Б – ручная наплавка;
для поверхности В – ручная наплавка (заварка отверстия).
Для окончательного решения вопроса о способах восстановления изношенных поверхностей детали в целом произведем перебор различных сочетаний способов. Затем определяем минимальное значение отношения себестоимости восстановления детали оптимальным для каждой изнашиваемой поверхности способом и коэффициенту долговечности
где СВДJ – себестоимость восстановления изношенных поверхностей детали J-м сочетанием способов руб.; Сy S КДВJ – коэффициент долговечности детали восстановленной J-м сочетанием способов; n – количество изнашиваемых поверхностей.
где К КДij - коэффициент повторяемости i-й поверхности восстановленной р-м способом.
Рассмотрим применение трех вариантов сочетаний способов восстановления корпуса в целом:
I вариант – резьбовая спиральная вставка для поверхности А ручная наплавка для поверхности Б и установка свертного кольца для
II вариант – ручная наплавка для поверхности А и установка свертных колец для поверхностей Б и В.
III вариант – – ручная наплавка для поверхностей А Б В.
Определим значение коэффициентов долговечности восстановленной детали по каждому варианту
Определяем отношение себестоимости восстановления детали к коэффициенту долговечности для каждого варианта
Для наглядности сведем произведенные расчеты в таблицу 2.
Как следует из расчетов наиболее целесообразным является третий вариант - ручная наплавка для поверхностей А Б В.
Таблица 2 – Технико-экономические показатели восстановления изношенных поверхностей корпуса
Сочетание способов восстановления
Коэффи-циент долговеч-ности
Себестои-мость восстанов-ления
Отношение себестои-мости восстановления к коэффициенту долго-вечности руб.
резьбовая спиральная вставка для поверхнос-ти А ручная наплавка для поверхности Б и установка свертного кольца для поверх-ности В
ручная наплавка для поверхности А и уста-новка свертных колец для поверхностей Б и В
ручная наплавка для поверхностей А Б В
Разработка технологического процесса восстановления детали
1 Назначение и обеспечение требуемой точности формы и шероховатости поверхности
По рекомендации табл. 1 [3 стр. 294] для посадочной поверхности под подшипник принимаем квалитет 7 для поверхности под валик H9 для резьбы квалитет 7Н.
По рекомендации табл. 2 [3 стр. 296] для посадочной поверхности под подшипник принимаем шероховатость Ra 125 мкм для валика и резьбовой поверхности Ra 63 мкм.
2 Выбор и использование технологических баз
По рекомендации табл. 4 [3 стр. 306] принимаем следующие схемы базирования:
) при предварительной обработке базового торца и правке базовых отверстий в торце - схема базирования по наружной поверхности в тисках;
) при заплавке и мехобработке дефектов А Б В – схема базирования плоскостью торца и двумя отверстиями в торце на два пальца.
3 Выбор оборудования и оснастки для восстановления детали
Процесс очистки детали
Так как разрабатываемый процесс – серийный то для операции очистки деталей принимаем моечную машину мод. М-132 и емкость для заготовок моющее средство препарат АМ-15.
Процесс дефектации производим на верстаке ОРГ-1468-01-090А.
Процесс механической обработки.
Корпус – деталь сложной комплексной формы однако обрабатываемые поверхности – поверхности вращения поэтому большая часть механической обработки – сверлильная и расточная. Деталь имеет форму которой трудно придать вращение вокруг обрабатываемой оси. Так как обрабатываются детали различных размеров с разной степенью точности обработки то принимаем агрегатный трехшпиндельный горизонтально-расточной станок 2А614-1. Станок позволяет производить растачивание деталей широкого диапазона диаметров и длин.
Для механической обработки базовых отверстий необходимо обеспечить выполнение операции сверления одиночных отверстий. Принимаем радиально-сверлильный станок 2М55. Станок позволяет производить обработку отверстий в стали диаметром до 35 мм в крупногабаритных деталях.
Процесс ручной наплавки.
Для ручной заварки отверстий необходимо зафиксировать деталь в горизонтальном положении. Используем специальное приспособление. Для проведения процесса необходима следующая оснастка: выпрямитель сварочный ВДГ-303 Медножелезные электроды ОЗЧ-2 изготовленные из медного стержня с фтористо-калиевым покрытием в которое добавляют 50% железного порошка. Применяют также флюсы ФНЧ-1 ФСЧ-2.
4 Определение припусков на механическую обработку
По рекомендации табл. 4 [3 стр. 306] принимаем следующие припуски:
) на диаметр на обработку посадочных отверстий под подшипник и валик:
- зенкерование – 225 мм;
- развертывание – 025 мм;
Общий припуск на обработку – 25 мм.
5 Режимы механической обработки восстанавливаемых деталей
Механическая обработка восстанавливаемых деталей характеризуется некоторыми особенностями. Например высокая твердость неравномерность распределения припуска на обработку неоднородность свойств обрабатываемой поверхности. Поэтому при обработке принимаем режущий инструмент с пластинами из твердого сплава.
Режимы механической обработки назначаем табличным методом.
Сверловка отверстие под резьбу диаметром 75 мм глубиной
S=01 ммзуб; V=25 ммин; n=1250 обмин
Нарезка резьбу М8-7Н на длину 10 мм Ra 63 мкм.
По рекомендациям табл. 25 [3 стр. 344] принимаем: h=t=10мм; S=15 мм; V=1ммин; n=40 обмин.
Сверловка отверстие под валик диаметром 9 мм глубиной
S=01 ммзуб; V=25 ммин; n=700 обмин
Зенкерование отверстия под валик диаметром 10 мм на длину
мм Ra 63 мкм. По рекомендациям табл. 25 [3 стр. 344] принимаем:
h=t=075 мм; S=01 мм; V=25ммин; n=630 обмин.
Расточка отверстия под подшипник диаметром 40 мм глубиной
h=t=1мм; S=01 ммзуб; V=25 ммин; n=400 обмин.
Зенкерование отверстия под подшипник диаметром 415 мм на длину 18 мм Ra 63 мкм. По рекомендациям табл. 25 [3 стр. 344] принимаем:
h=t=075 мм; S=01 мм; V=25ммин; n=355 обмин.
Развернуть отверстие под подшипник выдерживая размеры
ø42мм Ra = 125 мкм L=18 мм:
h=t=025 мм; S=01 мм; V=25ммин; n=355 обмин.
Основные параметры режимов наплавки определяем по следующим формулам:
скорость наплавки мч
скорость подачи проволоки мч
смещение электрода мм
где – коэффициент наплавки гАч (при наплавке постоянным током обратной полярности = 11 14);
h - толщина наплавленного слоя мм;
- плотность электродной проволоки гсм3 ( = 785 );
dПР - диаметр электродной проволоки мм;
d - диаметр отверстия мм.
6 Определение норм времени выполнения операций
Норма времени выполнения операций в общем случае слагается из следующих затрат:
где ТОСН – основное время на обработку мин; ТВСП - вспомогательное время на обработку мин; ТДОП – дополнительное время мин; ТПЗ – подготовительно-заключительное время мин; n – количество обрабатываемых деталей в партииПринимаем n = 20 шт.
В технологических картах проставляют штучное время ТШТ и подготовительно-заключительное время ТПЗ
Определяем основное время на обработку на различных операциях.
При сверлении зенкеровании развертывании
где L – глубина обработки мм; S – подача на один оборот инструмента ммоб; n – частота вращения инструмента обмин.
Сверление отверстия диаметром 75 мм глубиной 14 мм:
Нарезание резьбы М10-7Н:
Сверление отверстия диаметром 9 мм глубиной 7 мм:
Зенкерование отверстия диаметром 10 мм глубиной 7 мм:
Расточить отверстие диаметром 40 мм глубиной 18 мм:
Зенкерование отверстия диаметром 415 мм глубиной 18 мм:
Развертывание отверстия диаметром 42 мм глубиной 18 мм:
где L - длина наплавляемой поверхности с учетом захода и выхода электрода мм;
– скорость наплавки мч;
Заплавка резьбового отверстия
Наплавка поверхности под подшипник
Заплавка отверстия под валик
Дополнительное время определяется по формуле
Вспомогательное время ТВСП в зависимости от применяемой технологической оснастки принимаем в пределах от 2 до 12 мин.
Дополнительное время на обработку для каждой операции:
Штучное время на обработку
Подготовительно-заключительное время ТПЗ принимаем равным 15 20 мин на партию деталей.
Норма времени выполнения операции
7 Разработка маршрутов восстановления
При формировании технологических маршрутов восстановления руководствуемся следующими положениями:
- сочетание дефектов по каждому маршруту должно быть устойчивым;
- число маршрутов должно быть минимальным;
- в составе маршрута должно быть минимальное количество несуществующих дефектов;
- маршруты должны обеспечивать экономическую целесообразность их реализации.
Учтя эти требования разрабатываем три маршрута восстановления:
I – детали с сочетанием дефектов ХВ и ХБВ. Этот маршрут объединяет 355% деталей;
II – детали с сочетанием дефектов ХБ и ХАБ. Этот маршрут объединяет 194% деталей;
III – детали с сочетанием дефектов ХА и ХАВ. Этот маршрут объединяет 136% деталей.
Детали имеющие все возможные дефекты включаем в число неремонтопригодных из-за большой трудоемкости и высокой себестоимости их восстановления.
Рисунок 2 - Маршруты восстановления
Техника безопасности работ при восстановлении детали
1 Улучшение условий труда.
Производительность труда рабочих в значительной степени зависит от условий труда: микроклимата освещенности загазованности помещения шума и т. д. Все перечисленные факторы микроклимата должны соответствовать требованиям СНиП.
Микроклимат производственных помещений зависит от температуры и относительной влажности. Загрязненность воздуха в зависимости от условий производства может быть вызвана наличием токсичных (ядовитых) газов паров пыли и др. К токсичным веществам относятся: хлор пары бензина и бензола углекислый газ и др. Их содержание в воздухе определяют с помощью универсального газоанализатора (УГ).
Нетоксичными веществами являются абразивная пыль угольная алюминиевая и другие вещества содержание которых определяют пропуская через фильтр определенный объем исследуемого воздуха. При анализе воздуха отбирают не менее двух проб на уровне дыхания человека.
Освещенность помещений изменяют люксометром с пределами измерения 1—50 000 лк. Естественная освещенность характеризуется коэффициентом освещенности Ксм или отношением световой поверхности окон к площади пола.
Шум и вибрация появляются при работе динамически неуравновешенных агрегатов и инструмента (компрессоров наждачных и точил кузнечных молотов обрабатывающих станков пневматического инструмента и т. д.).
Единицей измерения уровня (силы) шума принят децибел (дб) а частота шума (вибрации) измеряется в герцах (Гц). Уровень шума в производстве измеряют шумомерами типа Ш-ЗМ АШ-2М ИНШ-2.
При чрезмерных шумах устанавливают звукоизоляцию кожухи кабины отражающие экраны глушители и другие устройства.
Амплитуду колебаний при вибрациях измеряют с помощью электрических виброметров типа АИН-4. Ориентировочные замеры вибраций выполняют механическими вибрографами (приборами Гейгера и Вр-1). Вибрации снижаются при использовании амортизаторов смазочных материалов и реактивных гасителей пульсации.
При создании ремонтных предприятий и организации работ на них необходимо учитывать факторы снижающие и предупреждающие травматизм. При разработке технологических процессов и расстановке оборудования не должны допускаться встречные потоки и возвратные движения людей и грузов. Возле рабочих мест необходимо предусматривать площадки для деталей и материалов.
Полы должны иметь ровную нескользкую поверхность без выбоин и порогов. В помещениях с холодными полами например цементными на рабочих местах под ноги укладывают деревянные решетки или настилы.
Для предупреждения поражения электрическим током все оборудование должно быть заземлено. Состояние заземления проверяют не реже одного раза в квартал. Электроустановки электрооборудование и проводку разрешается ремонтировать только после отключения их от сети.
Подъемно-транспортное оборудование с механическим приводом обязательно регистрируется в инспекции Гостехнадзора которая проводит его техническое освидетельствование.
Подъемные устройства с ручным приводом цепи и канаты проходят освидетельствование комиссией под руководством главного инженера ремонтного предприятия. Техническая проверка содержит осмотр оборудования поднятие груза масса которого превышает на 10 % грузоподъемностью подъемного устройства по паспорту на высоту 100 мм и выдержку в поднятом положении 10 мин. Цепи канаты и чалочные устройства испытывают под двойным грузом. Результаты испытания заносятся в спецжурнал а на кранах и других подъемных устройствах четко наносят краской предельную грузоподъемность и срок последующего освидетельствования. К управлению кранами допускают лиц имеющих специальные удостоверения на право работы на грузоподъемных средствах.
2 Техника безопасности при сварочно-наплавочных работах.
К наплавочным работам допускаются лица не моложе 18 лет прошедшие медицинское освидетельствование и специальное обучение имеющие удостоверение на право выполнения указанных работ и группу по электробезопасности не ниже второй.
Дуговая сварка. Правильное и рациональное размещение рабочего места сварщика имеет большое значение в повышении безопасности сварочных работ производительности труда и качества сварки. В целях защиты сварщиков подсобных и вспомогательных рабочих от лучистой энергии горящих поблизости сварочных дуг в постоянных местах сварки для каждого сварщика устраивают отдельные кабины площадью [(2x2)-(2x3)] м (не считая площади занятой оборудованием) и высотой 18—2 м. Для улучшения вентиляции стены кабины не доводят до пола на 15—20 см. Материалом стен кабин может служить тонкое железо фанера брезент покрытые огнестойким составом или другие огнестойкие материалы. Дверной проем как правило закрывается брезентовым занавесом на кольцах. Стены окрашивают в светлые матовые тона.
При ручной дуговой сварке в кабине сварщика устанавливают сварочный стол или кондуктор настенную полку для мелкого инструмента и приспособлений стул со спинкой и другое оборудование. Кабина оборудуется местной вентиляцией.
Для предохранения глаз и лица сварщика от вредного воздействия дуги необходимо использовать щитки или маски со специальными светофильтрами в зависимости от силы сварочного тока: Э-1 при силе тока до 75 А Э-2 при 75—200 А Э-3 — 200—400 А а также ЭС-100 ЭС-300
В целях исключения попадания под напряжение при замене электродов сварщик обязан пользоваться сухими брезентовыми рукавицами которые одновременно защищают его руки от расплавленного металла и лучистой энергии дуги.
Большое значение для безопасности сварщика имеет проверка правильности проведения проводов к сварочным постам и оборудованию.
Прокладка проводов к сварочным машинам по полу или земле а также другим способом при котором изоляция проводов не защищена и провод доступен для прикосновения не разрешается. Ток от сварочных агрегатов к месту сварки передается гибкими изолированными проводами чаще всего марки ПРГД.
Перед началом работ электросварщик обязан надеть специальную одежду — брезентовый костюм ботинки и головной убор.
Сварочную дугу при вибродуговой наплавке и сварке закрывают специальными устройствами в которых должно быть предусмотрено смотровое окно со светофильтром нужной плотности.
Газовая сварка. При выполнении газовой сварки соблюдаются те же правила безопасности что и при дуговой. Однако при газовой сварке необходимо следить чтобы в радиусе 5 м от рабочего места отсутствовали горючие материалы.
В местах хранения и вскрытия барабанов с карбидом кальция запрещено курить и применять инструмент дающий при ударе искры. Барабаны с карбидом хранят в сухих прохладных помещениях. Вскрытие барабана разрешается только латунным ножом.
Ацетилен при соприкосновении с медью образует взрывчатые вещества поэтому применять медные инструменты при вскрытии карбида и медные припои при ремонте ацетиленовой аппаратуры нельзя. Ацетиленовые генераторы располагают на расстоянии не менее 10 м от открытого огня.
Баллоны с газами хранят и транспортируют только с навинченными на их горловины предохранительными колпаками и заглушками на боковых штуцерах вентилей. При транспортировании баллонов не допускаются толчки и удары. Переносить баллоны на руках запрещается. К месту сварочных работ баллоны доставляют на специальных тележках или носилках.
Баллоны с газом устанавливают в помещении не ближе чем на 1 м от радиаторов отопления и не ближе чем на 10 м — от горелок и других источников тепла с открытым огнем.
Запрещено хранить баллоны с кислородом в одном помещении с баллонами горючего газа с барабанами карбида кальция лаками маслами и красками.
При обнаружении на баллоне или вентиле следов жира или масла баллон немедленно возвращают на склад. Соседство масла и кислорода может привести к взрыву.
В целях безопасности в обращении кислородные баллоны окрашивают в синий цвет ацетиленовые — в белый а баллоны с пропанбутановыми смесями — в красный.
3 Техника безопасности при станочно-слесарных работах.
Постоянно работающие металлообрабатывающие станки должны быть установлены на прочных фундаментах или общем основании пола тщательно выверены и закреплены. Все станки (постоянные или переносные) обслуживаются только закрепленными за ними лицами. Выключение станка обязательно при смене инструмента установке закреплении и снятии заготовки ремонте чистке смазке и уборке станка.
Станки работа на которых приводит к образованию осколков стружки или искры оборудуют удобными в эксплуатации предохранительными устройствами с достаточно прочным стеклом или другим прозрачным материалом для наблюдения за процессом обработки. Если по техническим условиям предохранительные щитки поставить невозможно то на станках работают в защитных очках.
Металлообрабатывающие станки и другое оборудование устанавливают в помещениях таким образом чтобы они не загромождали главные проходы и двери. Расстояние между отдельными станками должно быть не менее 08 м этого достаточно для прохода рабочих при обслуживании и ремонте станков.
Необходимо ограждать: ременные и зубчатые передачи; все выступающие движущиеся части станков находящиеся на высоте до 2 м от пола; обрабатываемые движущиеся предметы выходящие за габариты станка.
Стружку со станка нельзя убирать руками для этого используют щётки и крючки.
Высоту укладки изделий в штабеля определяют исходя из устойчивости штабеля и удобства пользования. Максимальная высота штабелей — 15 м.
Все эксплуатируемое оборудование должно находиться в полной исправности. За его состоянием осуществляется постоянный контроль со стороны технического руководства.
При приемке из ремонта в акте необходимо оговорить наличие на станке всех оградительных устройств и их исправность. Работа на неисправных станках и с неисправными ограждениями запрещается.
Станочники должны работать в хорошо застегнутой одежде без развевающихся рукавов поясов и лент. Волосы особенно у женщин должны быть закрыты головным убором (фуражкой косынкой беретом сеткой и др.).
При обработке пруткового материала на револьверных станках и токарных автоматах выступающие за шпиндель части прутков ограждаются. Зачистка деталей наждачным полотном зажимаемым руками запрещается.
Правку шлифовальных кругов осуществляют алмазами алмазно-металлическими карандашами или алмазозаменителями (металлическими звездочками кругами бруски из карбида кремния или диски). Правка кругов зубилом или каким-либо другим слесарным инструментом недопустима. Запрещается также при обработке деталей шлифовальными кругами применять рычаги для увеличения давления на круг. При установке на шпинделе шлифовального станка двух кругов их диаметры не должны отличаться более чем на 10 %. Для работы можно использовать только испытанные на прочность круги.
Ленточные пилы для распилования металла ограждают по всей длине ленты прочными полосами или бугелями.
Верстки из металла и дерева для слесарных работ должны иметь жесткую и прочную конструкцию и быть достаточно массивными чтобы не качаться и не вибрировать при работе на них. Верхнюю крышку верстака делают из хорошо пригнанных досок толщиной 40—50 мм которые обивают листовым железом. Ширина двухсторонних верстаков 12—15 м. В середине верстака предусматривают сетку высотой 08 м для предохранения рабочих от ранения отлетающими при рубке кусочками металла. Ширина односторонних верстаков 06—08 м. С точки зрения безопасности предпочтительнее одноместные верстаки но для экономии площади ремонтные производства часто оборудуют многоместными верстаками. Высота верстаков должна быть такой чтобы губки тисков находились на уровне локтя работающего.
Стеллажи для хранения деталей должны иметь небольшой уклон полок внутрь и быть удобными по высоте для укладки деталей.
Рабочее место слесаря под ногами оборудуют решетчатым настилом с расстоянием между планками 25—30 мм.
Определение экономической эффективности и целесообразности восстановления детали
Экономическая эффективность от восстановления изношенных деталей определяется по формуле
где ЭВ – экономическая эффективность от восстановления деталей руб.; ЦН ЦВ – цена новой и восстановленной детали руб.; РН РВ – ресурсы новой и восстановленной детали ч; - остаточная стоимость после эксплуатации новой и восстановленной деталей руб.
Таким образом экономически эффективно восстанавливать детали для которых ЭВ>0. Примем что а отношение РВРН представим как коэффициент долговечности КД восстановленной детали. Тогда соотношение цен новой и восстановленной детали должно удовлетворять выражению
Максимальная цена для потребителя определяется по выражению
Минимальная цена для производителя определяется по формуле
где СЗ – заводская себестоимость восстановления детали руб.; П – планируемая балансовая прибыль руб.
В зависимости от числа дефектов и их сочетаний заводская себестоимость восстановления будет различной.
В общем случае заводская себестоимость определяется по выражению:
где СВср – средняя себестоимость восстановления деталей одного наименования имеющих различное сочетание дефектов руб.; ДП – стоимость дополнительных работ (очистка дефектация) руб.; СФ – затраты на приобретение ремонтного фонда руб.
Средняя себестоимость восстановления деталей одного наименования определяется по формуле
где - себестоимость восстановления деталей с 1-м 2-м j-м сочетанием дефектов; х1 х2 хj – коэффициенты повторяемости деталей
с 1-м 2-м j-м сочетанием дефектов.
Значение ДП принимаем равным 01 от себестоимости устранения всех дефектов
Изношенные детали поступающие от поставщиков ремонтного фонда учитывают при исчислении себестоимости восстановления деталей по договорной цене. При этом на практике стоимость изношенной детали равна 01 от цены новой детали
Прибыль определяется из выражения
где НПР – норма прибыли в процентах. Принимаем 20%.
Определяем экономическую целесообразность и эффективность восстановления корпуса 25.22.101-А.
Цена нового корпуса на рынке – ЦН = 884 руб.
Исходя из коэффициента долговечности восстановленного корпуса
КД = 08 его максимальная цена может быть установлена не более
Себестоимость восстановления отдельных поверхностей:
поверхность А – 84 руб.;
поверхность Б – 322 руб.;
поверхность В – 42 руб.
Стоимость дополнительных работ
Стоимость изношенной детали СФ = 884 руб.
По формуле (27) определяем значение заводской себестоимости восстановления корпуса с различными сочетаниями дефектов а по формуле (26) – соответствующую расчетную цену восстановленной детали. Результаты расчетов сведем в таблицу 3.
Таблица 3 – Технико-экономические показатели восстановления корпуса с различными сочетаниями дефектов
повторяе-мости со-четания дефектов
Заводская себестои- мость вос-становле-ния СЗ руб.
Расчетная цена восс-тановлен-ной детали
Только поверхность А
Только поверхность Б
Только поверхность В
Сочетание поверхностей А и Б
Сочетание поверхностей А и В
Сочетание поверхностей Б и В
Сочетание поверхностей АБВ
Сравнив максимально возможную для потребителя цену 707 руб. и минимально допустимые цены на восстановленные детали для предприятия делаем вывод что экономически целесообразно восстановление деталей с любым сочетанием дефектов.
Средняя заводская себестоимость восстановления корпуса составляет
Минимально возможная цена восстановленной корпуса может быть установлена на уровне
Таким образом если ремонтное предприятие будет восстанавливать корпуса то цена их реализации может колебаться от 1398 руб. до 707 руб.
В курсовом проекте разработан технологический процесс восстановления изношенной детали «Корпус 25.22.101-А».
В процессе проектирования были решены следующие задачи:
- проведен анализ условий работы детали «Корпус 25.22.101-А» выявивший что основные виды изнашивания которым подвергаются рабочие поверхности детали это износ резьбы износ поверхности под подшипник износ посадочной поверхности под валик.
- определены коэффициенты повторяемости различных сочетаний дефектов;
- обоснованы рациональные способы восстановления каждой изнашиваемой поверхности детали: для поверхности А – ручная наплавка (заварка отверстия); для поверхности Б - ручная наплавка; для поверхности В – ручная наплавка (заварка отверстия). – Обосновать!
- разработан комплект технологической документации восстановления корпуса на основе рациональных методов с выбором технологического оборудования приспособлений рабочих инструментов и средств контроля;
- установлены режимы обработки и нормы времени выполнения операций;
- обоснована целесообразность восстановления деталей с различными сочетаниями дефектов. Определено что если ремонтное предприятие будет восстанавливать корпуса то цена их реализации может колебаться от 1398 руб. до 707 руб. что обеспечит прибыль более 30%.
Надежность и ремонт машин В.В. Курчаткин Н.Ф. Тельнов К.А. Ачкасов и др.; Под ред. В.В. Курчаткина. - М.: Колос 2000.-776с.
Ремонт машин Под ред. Н.Ф. Тельнова. - М.: Агропромиздат 1992.-560с.
Молодык Н.В. Зенкин АС. Восстановление деталей машин. Справочник. - М: Машиностроение 1989.-480с.
Варнаков В.В. и др. Технический сервис машин сельскохозяйственного назначения В.В. Варнаков В.В. Стрельцов В.Н. Попов В.Ф. Карпенков. - М: Колос 2000.-256с.
Карагодин В.И. Митрохин Н.Н. Ремонт автомобилей и двигателей. - М.: Мастерство; Высш. школа 2001.-496с.
Голубев И.Г. Спицын И.А. Ремонт сельскохозяйственных машин в условиях мастерских сельских товаропроизводителей. - М.: ФГНУ «Росинформагротех» 2001.-88с.
Батищев А.Н. Чижикова Т.В. Голубев И.Г. Спицын И.А. Юдин В.М. Монтаж эксплуатация и ремонт технологического оборудования перерабатывающих отраслей АПК Справочник. - М.: Информагротех 1997.-288с.
Новиков B.C. Очковский Н.А. Тельнов Н.Ф. Ачкасов К.А. Проектирование технологических процессов восстановления изношенных деталей. Методические рекомендации к курсовому и дипломному проектированию. - М.: МГАУ 1998.-50С.
Методическое пособие к расчету технологической карты на восстановление деталей машин Власов П.А. Степанов В.А. Спицын И.А. Галкин A.M. Гурьев И.В. - Пенза 1990 -68с.
Лист 1-1 (А2).cdw

*Размеры для справок.
Допускается не устранять дефекты
не выходит за пределы значений
Лист 1-2 (А2).cdw

при предварительной обработке базовых поверхностей
при ручной заварке отверстия под валик (дефект В)
при горизонтально-расточной обработке (дефект В)
при ручной заварке резьбового отверстия (дефект А)
при ручной наплавке отверстия под подшипник (дефект Б)
при горизонтально-расточной обработке (дефект А)
при горизонтально-расточной обработке (дефект Б)
Рекомендуемые чертежи
- 30.04.2023