Редуктор цилиндрический косозубый


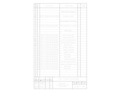
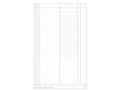
- Добавлен: 24.01.2023
- Размер: 478 KB
- Закачек: 0
Описание
Состав проекта
![]() |
![]() |
![]() ![]() ![]() |
![]() ![]() ![]() ![]() |
![]() ![]() ![]() |
![]() ![]() ![]() |
![]() ![]() ![]() |
![]() ![]() ![]() ![]() |
Дополнительная информация
вал ведомый.dwg
190÷195HB 2. Общие допуски по ГОСТ 30893.1: h14 ± 3. Неуказанные фаски 2x45° 4. Неуказанные радиусы 0
Сталь 45 ГОСТ 1050-88
ВГСТ.Т20У.19.101.00.006
Спецификация(2).dwg

Манжета 1-32x52-3 ГОСТ 8752-79
Манжета 1-25x42-3 ГОСТ 8752-79
Шпонка 8x7x25 ГОСТ 23360-78
Шпонка 12x8x28 ГОСТ 23360-78
Подшипник 36306 ГОСТ 831-75
Подшипник 36207 ГОСТ 831-75
Штифт 8x65 ГОСТ 3129-70
Винт М4x7 ГОСТ 1491-80
Болт М6x20 ГОСТ 7798-70
Болт М8x22 ГОСТ 7798-70
Болт М10x35 ГОСТ 7798-70
Шайба 4 65Г ГОСТ 6402-70
Шайба 6 65Г ГОСТ 6402-70
Шайба 8 65Г ГОСТ 6402-70
Шайба 10 65Г ГОСТ 6402-70
Гайка М8 ГОСТ 5927-70
Гайка М10 ГОСТ 5927-70
Колесо.dwg
Колесо цилиндрическое косозубое
Сталь 45 ГОСТ 1050-88
ВГСТ.Т20У.19.101.00.004
Коэффициент смещения
Твердость зубьев: 35 40 HRCэ 2. Общие допуски по ГОСТ 30893.1: h14 ± 3. Радиусы закруглений: 0
записка.doc
Выбор электродвигателя и кинематический расчет 4
Расчет цилиндрической передачи редуктора 7
Расчет цепной передачи 13
Ориентировочный расчет валов редуктора. Эскизы валов 16
Конструктивные размеры зубчатой пары редуктора 18
Размеры элементов корпуса и крышки редуктора 20
Подбор подшипников 21
Уточненный расчет ведомого вала 27
Подбор и проверочный расчет шпонок 32
Выбор посадок для зубчатых колес подшипников звездочки цепной передачи и полумуфты 34
Выбор смазки для зацепления и подшипников 35
Выбор и проверочный расчет муфты 36
С развитием промышленности более широкое применение получили редукторы представляющие собой механизмы состоящие из зубчатых и червячных передач выполняемых в виде отдельного агрегата и служащие для передачи мощности от двигателя к рабочей машине (механизму).
Основное назначение редуктора - изменение угловой скорости и соответственно изменение вращающегося момента выходного вала по сравнению с входным.
Редукторы широко применяются как в машиностроении (конвейеры подъемные механизмы) так и в строительстве (ступени приводов питателей бетонного завода) а также в пищевой промышленности и бытовой технике (различные комбайны) и так далее.
Поэтому и существуют самые разнообразные виды редукторов условно подразделяемых по признакам.
По признаку передачи подразделяют на:
В свою очередь каждая из передач может быть с различными профилями и расположением зубьев.
Так цилиндрические передачи могут быть выполнены с прямыми косыми и шевронными зубьями; конические- с косыми прямыми и винтовыми.
Передачи выполняют с эвольвентными профилями зубьев и с зацеплением Новикова. Зачастую используют и комбинированную передачу которая сочетает различные передачи: коническо-цилиндрические; червячно-цилиндрические и т.д.
В зависимости от числа пар звеньев в зацепление (числа ступеней) редукторы общего назначения бывают одно- и многоступенчатые.
По расположению осей валов в пространстве различают редукторы с параллельными соосными перекрещивающимися осями входного и выходного валов.
СХЕМА И КРАТКОЕ ОПИСАНИЕ ПРИВОДА
-редуктор цилиндрический
Рисунок 1- Схема привода
Движение от электродвигателя (1) передается через предохранительную муфту (2) на ведущий вал I редуктора (З) и через косозубую цилиндрическую передачу на ведомый вал II редуктора. Затем движение через цепную передачу (4) подается на вал III который является ведущим для барабана с лентой.
ВЫБОР ЭЛЕКТРОДВИГАТЕЛЯ И КИНЕМАТИЧЕСКИЙ РАСЧЕТ
1 Определяем общий коэффициент полезного действия общ:
где 1=097 – КПД закрытой цилиндрической передачи;
=093 – КПД цепной передачи;
=099 – КПД одной пары подшипников качения;
2 Определяем требуемую мощность на валу электродвигателя Pдв:
где P - мощность на валу шестерни закрытой цилиндрической передачи кВт.
3 Принимаем электродвигатель
P=3 кВт4A100S4У3=1500 мин -1
4 Определяем общее передаточное число привода и производим разбивку по ступеням с учетом рекомендаций;
где nдв - частота вращения электродвигателя мин -1;
nб - частота вращения барабана мин -1;
Принимаем U1 = 4 - передаточное число закрытой зубчатой передачи;
- передаточное число цепной передачи;
5 Определяем угловые скорости и частоты вращения на валах привода:
nI = nдв = 1500 мин -1 ; [1 c.291]
6 Определяем требуемую мощность на валах привода:
7 Определяем вращающие моменты на валах привода:
РАСЧЕТ ЦИЛИНДРИЧЕСКОЙ ПЕРЕДАЧИ
1 Выбираем материал по средним механическим характеристикам: для шестерни сталь 45 термообработка - улучшение твердость НВ=230
- для колеса сталь 45 термообработка - улучшение НВ=200 [1 с. 34 табл. 3.3]
2 Определяем допускаемое контактное напряжение:
где КHL = 1 - коэффициент долговечности
[SH] = 115 – коэффициент безопасности
Принимаем допускаемое напряжение по колесу:
3 Принимаем коэффициент ширины венца:
4 Определяем коэффициент нагрузки KH:
Не смотря на симметричное расположение колес коэффициент KH примем выше рекомендуемого так как со стороны цепной передачи действуют силы вызывающие дополнительную деформацию ведомого вала и ухудшающие контакт зубьев.
KH = 125 [1 c. 32 табл. 3.1]
5 Определяем межосевое расстояние из условия контактной выносливости активных поверхностей зубьев:
Принимаем ближайшее стандартное значение
6 Определяем нормальный модуль зацепления:
7 Принимаем предварительный угол наклона зубьев
8 Определяем числа зубьев шестерни и колеса
Принимаем Z1 = 28 тогда
9 Уточняем значение угла наклона зубьев
10 Определяем основные размеры шестерни и колеса
- делительные диаметры
- диаметры вершин зубьев
-коэффициент ширины шестерни по диаметру:
-окружная скорость колес:
При такой скорости принимаем 8-ую степень точности
11 Определяем коэффициент нагрузки
При твердости НВ350: KH = 115 [1 c. 39 табл. 3.5]
KHα = 109 [1 c. 39 табл. 3.4]
При скорости мс для косозубых колес коэффициент KH = 10 [1 c. 40 табл. 3.6]
12 Проверяем контактное напряжение
13 Определяем силы действующие в зацеплении
14 Проверяем зубья на выносливость по напряжениям изгиба
где YF - коэффициент учитывающий форму зуба и зависит от эквивалентного числа зубьев
YF1 = 380 и YF2 = 361
14.1 Определяем коэффициенты Y и KFα
14.2 Определяем коэффициент нагрузки
где KF = 107 и KF = 11[1 c. 43 табл. 3.7 3.8]
15 Определяем допускаемое напряжение
15.1 Определяем коэффициент безопасности
где [1 c. 44 табл. 3.9]
- для поковок и штамповок
16 Определяем допускаемые напряжения
17 Находим отношения
Дальнейший расчет следует вести для зубьев колеса для которого найденное отношение меньше.
18 Проверяем прочность зуба колеса
F = 91 МПа ≤ [F] = 206 МПа
Условие прочности выполнено
РАСЧЕТ ЦЕПНОЙ ПЕРЕДАЧИ
1 Выбираем вращающий момент на ведущей звездочке
2 Определяем число зубьев
- на ведущей звездочке: [1 c. 148]
-на ведомой звездочке:
3 Определяем расчетный коэффициент нагрузки
где - динамический коэффициент
kа = 1; kн = 125; kр = 125; kсм = 14; kп = 1.
4 Определяем шаг однорядной цепи
4.1 Принимаем по таблице 7.15 цепь ПР-1905-318
t=1905 мм; Q=318; q=19 кгм; AОП=1058 мм2.
5 Определяем скорость цепи
6 Определяем окружное усилие цепи
7 Проверяем давление в шарнире
8 Уточняем допускаемое давление
МПа [1 c. 150 табл. 7.18]
Условие p≤[p] выполнено
9 Определяем усилие в цепи:
kf=1 – при вертикальном расположении цепи
aц=(30÷50)t=(30÷50)*1905=762мм=0762м [1 c. 148]
- от центробежных сил
10 Определяем расчетную нагрузку на валы
11 Проверяем коэффициент запаса прочности цепи
Нормативный коэффициент [s] по табл. 7.19
Условие s≥[s] выполнено.
12 Определяем основные размеры ведущей звездочки
где d1=1191мм – диаметр ролика цепи (см. табл. 7.15)
13 Определяем основные размеры ступицы звездочки
14 Определяем толщину диска звездочки
где - расстояние между пластинами внутреннего звена (см. табл. 7.15)
Аналогично определяем размеры ведомой звездочки.
ПРЕДВАРИТЕЛЬНЫЙ РАСЧЕТ ВАЛОВ РЕДУКТОРА
1 Принимаем материал для ведущего вала Сталь 45 термообработка – улучшение
в=780 МПа т=440 МПа [к]=15 МПа
2 Определяем диаметр выходного конца d1
3 d1=22 мм - диаметр вала под муфту;
d2=25 мм - диаметр вала под уплотнение;
d3=30 мм - диаметр вала под подшипник;
d4=32 мм - диаметр вала под буртик;
d5=385 мм – диаметр вершин зубьев шестерни;
Рисунок 2 - Эскиз ведущего вала
4 Принимаем материал для ведомого вала Сталь 45 термообработка - нормализация в=570 МПа т=290 МПа [к]=16 МПа
5 Определяем диаметр выходного конца d2
3 d1=28 мм - диаметр вала под звездочку;
d2=32 мм - диаметр вала под уплотнение;
d3=35 мм - диаметр вала под подшипник;
d4=40 мм - диаметр вала под колесо;
d5=45 мм - диаметр вала под буртик;
Рисунок 2 - Эскиз ведомого вала
КОНСТРУКТИВНЫЕ ОСОБЕННОСТИ ШЕСТЕРНИ И КОЛЕСА
1 Шестерню выполняем за одно целое с валом.
Ее размеры: d1=36 мм; dа1=385 мм; b1=41 мм.
2 Размеры кованного колеса:
d2=144 мм; dа2=1465 мм; b2=36 мм.
3 Определяем диаметры ступицы
dст=16*dк2=16*40=64 мм
4 Определяем длину ступицы
lст=(12÷15)dк2=(12÷15)*40=48÷60 мм
5 Определяем толщину обода
=(25÷4)mn=(25÷4)*125=3125÷5 мм
6 Определяем толщину диска
C=03*b2=03*36=108 мм
Рисунок 4 - Колесо зубчатое
КОНСТРУКТИВНЫЕ РАЗМЕРЫ КОРПУСА РЕДУКТОРА
1 Определяем толщину стенок крышки
=0025a+1=0025*90+1=325 мм;
=002а+1=002*90+1=28 мм;
2 Определяем толщину фланцев поясов корпуса и крышки
2.1 Верхнего пояса корпуса и крышки
2.2 Нижнего пояса корпуса
3 Определяем диаметры болтов
3.1 Фундаментальных болтов
d1=(003÷0036)a+12=(003÷0036)*90+12=147÷1524 мм;
принимаем болты с резьбой M12
3.2 Крепящих крышку к корпусу у подшипников
d2=(07÷075)d1=(07÷075)*12=84÷9 мм;
принимаем болты с резьбой M10
3.3 Соединяющих крышку с корпусом
d3=(05÷06)d1=(05÷06)*12=6÷72 мм;
принимаем болты с резьбой M8
1 Принимаем для ведущего вала подшипников средней серии табл. П6 [1]
Принимаем подшипники радиально-упорные однорядные по ГОСТ 831-75.
Тип подшипников 36306.
Основные параметры:
D=62 мм; B=17 мм; C=216 кН; C0=159кН.
2 Проводим расчет опорных реакций и изгибающих моментов
2.1 Горизонтальная плоскость
Так как окружная сила F действует на одинаковом расстоянии от опор то опорные реакции будут равны:
2.2 Вертикальная плоскость
3 Находим моменты для построения эпюр
3.1 Горизонтальная плоскость
МСлев=НА*415=5255*415=2180825 Н*мм
МСпр=НВ*415=5255*415=2180825 Н*мм
3.2 Вертикальная плоскость
МСлев=-VА*415=-142*415=-5893 H*мм
МСлев=-VА*415-m=-142*415-4536=-10429 Н*мм
МСпр=-VВ*415=-252*415=-10458 H*мм
4 Проверяем подшипники на долговечность
4.1 Определяем суммарные реакции опор FV
4.2 Определяем эквивалентную нагрузку FЭ
где -радиальная нагрузка Н
-коэффициент учитывающий вращение колес
- коэффициент безопасности[1 c. 214 табл. 9.19]
- температурный коэффициент[1 c. 214 табл. 9.20]
Отношение [1 c. 212 табл. 9.18]
Отношение X=045; Y=181
4.3 Определяем расчетную долговечность
Горизонтальная плоскость
Вертикальная плоскость
Рисунок 5 – Эпюры ведущего вала
1 Принимаем для ведомого вала подшипников легкой серии табл. П6 [1]
Тип подшипников 36207.
D=72 мм; B=17 мм; C=308 кН; C0=178кН.
МДлев=НА*415=5255*415=2180825 Н*мм
МВлев=НА*83-Ft*415=5255*83-1051*415=0
МДлев=VА*415=340*415=14110 H*мм
МДлев=VА*415+m=340*415+18144=32254 Н*мм
МВлев=VА*83+m+Fr*415=340*83+18144+394*415=62715 Н*мм
МBпр=Fц*655=957*655=626835 Н*мм
- коэффициент безопасности [1 c. 214 табл. 9.19]
Горизонтальная плоскость
Рисунок 5 – Эпюры ведомый вала
УТОЧНЕННЫЙ РАСЧЕТ ВЕДОМОГО ВАЛА РЕДУКТОРА
Рисунок 7- Эскиз ведомого вала редуктора
1 Материал вала - сталь 45 нормализация
2 Определяем предел выносливости
3.1 Диаметр вала в этом сечении 40мм
3.2 Концентрация напряжений обусловлена наличием шпоночной канавки:
; [1 c. 165 табл. 8.5]
масштабные факторы ; [1 c. 166 табл. 8.8]
3.3 Крутящий момент Н*мм
3.4 Определяем изгибающий момент в горизонтальной плоскости
3.5 Определяем изгибающий момент в вертикальной плоскости
3.6 Определяем суммарный изгибающий момент в сечении А-А
3.7 Определяем момент сопротивления кручению
[1 c. 165 табл. 8.5]
3.8 Определяем момент сопротивления изгибу
3.9 Определяем амплитуду и среднее напряжение цикла касательных напряжений
3.10 Определяем амплитуду нормальных напряжений изгиба
МПа; среднее напряжение
3.11 Определяем коэффициент запаса прочности по нормальным напряжениям
[1 c. 162 форм. 8.18]
3.12 Определяем коэффициент запаса прочности по касательным напряжениям
[1 c. 164 форм. 8.19]
3.13 Результирующий коэффициент запаса прочности для сечения А-А
[1 c. 162 форм. 8.17]
4 Рассмотрим сечение Б-Б
4.1 Концентрация напряжений обусловлена посадкой подшипника с гарантированным натягом:
и [1 c. 166 табл. 8.7]
4.2 Изгибающий момент в этом сечении
4.3 Осевой момент сопротивления
4.4 Определяем амплитуду нормальных напряжений
4.5 Полярный момент сопротивления
4.6 Амплитуда и среднее значение цикла касательных напряжений
4.7 Коэффициент запаса прочности по нормальным напряжениям
4.8 Коэффициент запаса прочности по касательным напряжениям
4.9 Результирующий коэффициент запаса прочности для сечения Б-Б
5 Рассмотрим сечение В-В
5.1 Концентрация напряжений обусловлена наличием шпоночной канавки
и [1 c. 165 табл. 8.5]
и [1 c. 166 табл. 8.8]
5.2 Момент сопротивления изгиба
5.3 Момент сопротивления кручению
5.4 Амплитуда и среднее значение напряжений цикла касательных напряжений
6.5 Результирующий коэффициент запаса прочности в сечении В-В
Таблица 1 – Коэффициенты запаса прочности
Коэффициент запаса S
ПРОВЕРКА ПРОЧНОСТИ ШПОНОЧНЫХ СОЕДИНЕНИЙ
1 Материал шпонки Сталь 45 нормализованная
2 Напряжение смятия и условие прочности
[1 c. 170 форм. 8.22]
2.1 Допускаемое напряжение смятия при стальной ступице:
2.2 Шпонка на выходном конце ведущего вала
d=22 мм; b*h=6*6 мм; t1=35 мм; l=20 мм
Момент на ведущем валу T1=1892*103 Н*мм
2.3 Шпонка на выходном конце ведомого вала
d=28 мм; b*h=8*7 мм; t1=40 мм; l=25 мм
момент на ведомом валу T2=7266*103 Н*мм
2.4 Шпонка под колесом
d=40 мм; b*h=12*8 мм; t1=50 мм; l=28 мм
Прочность шпоночных соединений выдерживается
Рисунок 8 – Эскиз шпонки
ВЫБОР ПОСАДОК ДЛЯ ЗУБЧАТЫХ КОЛЕС ЦЕПНОЙ ПЕРЕДАЧИ
1 Посадки назначаем основным деталям редуктора по ГОСТ 2.5347-82
1.1 Посадки зубчатого колеса на вал [1 c. 263 табл. 10.13]
1.2 Посадки муфты на вал или [1 c. 263 табл. 10.13]
1.3 Посадки звездочки цепной передачи или [1 c. 263 табл. 10.13]
1.4 Внутренние кольца подшипников на валы:
отклонение вала k6 [1 c. 263 табл. 10.13]
1.5 Наружные кольца подшипников в корпусе:
Отклонение отверстия H7 [1 c. 263 табл. 10.13]
ВЫБОР СМАЗКИ ДЛЯ ЗАЦЕПЛЕНИЯ
1 Смазка зубчатого зацепления производиться окунанием зубчатого колеса в масло заливаемое в корпус до погружения колеса примерно на 10мм.
2Объем масляной ванны определяем из расчета 025 дм3 на 1кВт передаваемой мощности.
3 По [1 c. 253 табл. 10.8] устанавливаем вязкость масла 28*10-6 м2с
4 По [1 c. 253 табл. 10.10] принимаем масло индустриальное И-30А по
5 В виду большой окружной скорости зубчатых колес пластичная смазка не применяется так как подшипники смазываются за счет разбрызгивания масла зубчатыми колесами.
ВЫБОР И ПРОВЕРОЧНЫЙ РАСЧЕТ МУФТЫ
Рисунок 9 – Эскиз муфты упругой втулочно-пальцевой
1 Материал пальцев – сталь 45 нормализованная; втулки из специальной резины Нмм2
2 Проверяем втулки на смятие
[1 c. 287 форм. 12.6]
- диаметр окружности на которой расположены оси пальцев;
Прочность втулки обеспечена
3 Проверяем пальцы на изгиб
[1 c. 288 форм. 12.7]
1 Перед сборкой внутреннюю полость корпуса редуктора тщательно счищают и покрывают маслостойкой краской.
2 Сборку производят в соответствии с чертежом общего вида редуктора начиная с узлов валов.
2.1 На ведущий вал насаживают радиальные однорядные шарикоподшипники предварительно нагреваемые в масле до 80-100°С.
2.2 В ведомый вал закладывают шпонку и напрессовывают зубчатое цилиндрическое колесо до упора в бурт вала и устанавливают шарикоподшипник предварительно нагретый в масле.
3 Собранные валы укладывают в основание корпуса редуктора и надевают крышку корпуса покрывая предварительно поверхность стыка крышки и корпуса спиртовым лаком. Для центровки устанавливают крышку на корпус с помощью двух штифтов; затягивают болты крепящих крышку к корпусу.
4 После этого на ведомый вал надевают распорное кольцо ставят крышки подшипников с комплектом металлических прокладок регулируют тепловой зазор.
5 Перед постановкой сквозных крышек в проточки закладывают резиновую армированную манжету. Проверяют проворачиванием валов отсутствие заклинивания подшипников и закрепляют крышку винтами.
6 Затем ввертывают пробку маслоспускаемого отверстия с прокладкой и жезловый масло указатель.
7 Заливают в корпус масло и закрывают смотровое отверстие крышкой с прокладкой; закрепляют крышку болтами.
8 Собранный редуктор обкатывают и подвергают испытанию на стенде по программе» устанавливаемой техническими условиями.
Федоренко В.А. Жомин А.И. Справочник по машиностроительному черчению Л: Машиностроение 1983
Козловский II.В. Виноградов A.M. Основы стандартизации допуски посадки и технические измерения М: Машиностроение 1982
Спецификация(1).dwg

ВГСТ.Т20У.19.101.00.000
ВГСТ.Т20У.19.101.00.000СБ
ВГСТ.Т20У.19.101.00.001
Маслоуказатель жезловый
Колесо цилиндрическое
Вал-шестерня ведущий
Крышка смотрового окна
ВГСТ.Т20У.19.101.00.002
ВГСТ.Т20У.19.101.00.003
ВГСТ.Т20У.19.101.00.004
ВГСТ.Т20У.19.101.00.005
ВГСТ.Т20У.19.101.00.006
ВГСТ.Т20У.19.101.00.007
ВГСТ.Т20У.19.101.00.008
ВГСТ.Т20У.19.101.00.009
ВГСТ.Т20У.19.101.00.010
ВГСТ.Т20У.19.101.00.011
ВГСТ.Т20У.19.101.00.012
ВГСТ.Т20У.19.101.00.013
ВГСТ.Т20У.19.101.00.014
ВГСТ.Т20У.19.101.00.015
ВГСТ.Т20У.19.101.00.016