Редуктор конический одноступенчатый




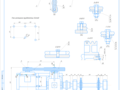
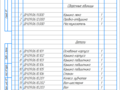
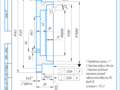
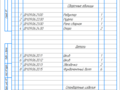
- Добавлен: 24.01.2023
- Размер: 530 KB
- Закачек: 1
Описание
Редуктор конический одноступенчатый
Состав проекта
![]() |
![]() |
![]() ![]() ![]() ![]() |
![]() ![]() ![]() |
![]() ![]() ![]() ![]() |
![]() ![]() ![]() |
![]() ![]() ![]() ![]() |
![]() ![]() ![]() ![]() |
![]() ![]() ![]() ![]() |
![]() ![]() ![]() ![]() |
Дополнительная информация
Колесо.cdw

3 лист мой.cdw

вид сверху.cdw

Спецификация на привод.spw

главный вид.cdw

Спецификация на редуктор.spw

крышка.cdw
