Редуктор конический одноступенчатый 2





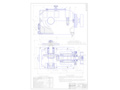
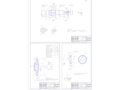
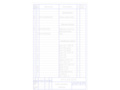
- Добавлен: 25.10.2022
- Размер: 4 MB
- Закачек: 2
Описание
Состав проекта
![]() |
![]() ![]() ![]() ![]() |
![]() ![]() ![]() |
![]() ![]() ![]() |
![]() ![]() ![]() |
![]() ![]() ![]() ![]() |
![]() |
![]() ![]() |
![]() ![]() ![]() |
![]() |
![]() ![]() ![]() |
![]() |
![]() ![]() |
![]() |
![]() ![]() |
![]() ![]() ![]() ![]() |
![]() ![]() ![]() ![]() |
![]() ![]() ![]() |
![]() ![]() ![]() ![]() |
![]() |
![]() ![]() |
![]() ![]() ![]() |
![]() ![]() ![]() |
![]() ![]() |
Дополнительная информация
Спецификация. Привод..dwg

Компановка.dwg

Привод.dwg

СБ.dwg

Редуктор 160-3,15.dwg
