Редуктор двухступенчатый цилиндрический




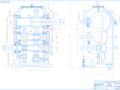

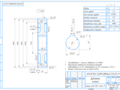
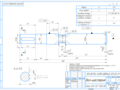
- Добавлен: 24.01.2023
- Размер: 736 KB
- Закачек: 0
Описание
Редуктор двухступенчатый цилиндрический
Состав проекта
![]() |
![]() |
![]() ![]() ![]() ![]() |
![]() ![]() ![]() |
![]() ![]() ![]() ![]() |
![]() ![]() ![]() ![]() |
![]() ![]() ![]() ![]() |
![]() ![]() ![]() |
![]() ![]() ![]() ![]() |
Дополнительная информация
Сборочный чертёж.cdw

Расчётно-пояснительная записка.doc
1. Общий КПД привода:
где 1 = 098 – КПД муфты [1c.5]
= 098 – КПД зубчатой передачи
= 099 – КПД пары подшипников
= 0982·0982·0993 = 0894
2. Требуемая мощность электродвигателя:
Nтр = N = 660894= 7374 кВт
Выбираем асинхронный электродвигатель 4А112M2У3 [1c.391]:
синхронная частота – 3000 обмин.
рабочая частота 3000(100 – 25)100 = 2925 обмин.
угловая скорость w1 = n130 = 292530 = 30615 радс
3. Передаточное число:
u = w1w3 = 303517 = 18
предположим суммарное передаточное число
принимаем по ГОСТ 2185-66 [2c.41] u1 = 45 тогда для тихоходной ступени
принимаем для тихоходной ступени u2 = 4
Отклонение 18 – 45·4010018 = 0%
4. Числа оборотов валов и угловые скорости:
n1 = nдв = 2925 обмин w1 = 292530 = 30615 радс
n2 = n1u1 = 292545 = 650 обмин w2= w1 u1 = 68 радс
n3 = n2u2 = 6504 = 1625 обмин w3= w2 u2 = 17 радс
5. Мощности передаваемые валами:
N1 = NвыхΣ = 660894 = 737 кВт
N2 = Nвхступопор = 7089·098·09915 = 684 кВт
6. Крутящие моменты:
Т1 = N1w1 = 7374·10330615 = 24086 Н·м
Т2 = N2w2 = 684310368 = 10063 Н·м
Т3 = N3w3 = 6610317 = 38823 Н·м
7. Результаты расчетов сводим в таблицу:
Расчет быстроходной ступени
1. Выбор материалов зубчатой пары:
Термообработка: колесо – закалка ТВЧ НRC = 50;
шестерня – закалка ТВЧ НRC = 50.
Допускаемые контактные напряжения:
[H] = (18HRC+150)KHL[SH]= [H]` · KHL
где [SH] – коэффициент безопасности [1 с.33]
KHL – коэффициент долговечности.
[H]`=900МПа [1 с.47 табл. 6.5]
где NH0 = 8·107 – базовое число циклов перемены напряжений [2c47];
Полное число часов работы передачи за расчетный срок службы
t = 5·300·2·7·06 = 12400 час
где 5 – срок службы в годах;
0 – число рабочих дней в году
– число смен за сутки;
– длительность смены в часах;
– коэффициент загрузки.
NP1=60·12600·2925=221·109
NP2=60·12600·650=49·108
так как NHE > NH0 то КHL = 1; КFL = 1
[H]= [H]`·KHL=900·1=900
[F] = [F]`·KFL=270·1=270
2. Межосевое расстояние:
где Ка = 430 – для косозубых колес [2c.46];
yba = 03 – коэффициент ширины колеса.
ybd = yba(u+1)2 = 03(45+1)2 = 0825
KHb = 12 – коэффициент учитывающий распределение нагрузки по ширине венца при несимметричном расположении колес
аw = 430(45+1)(10063·12452·03·9002)13 =6872 мм
принимаем согласно ГОСТ 2185-66 [2 c.52] аw =71 мм
3. Модуль зацепления:
m = (001÷002)a w = (001÷002)71= 071÷142 мм
принимаем по ГОСТ 9563-60 m = 135 мм
zΣ = 2awcosbm = 271сos10º125 = 112
где b = 10º - угол наклона зуба
z1 = zΣ(u+1) =112(45+1) = 20
z2 = zΣ - z1 = 112– 20 = 92
уточняем передаточное число
u1 = z2z1 =9220 = 46
уточняем расхождение передаточного числа
уточняем угол наклона
5. Основные размеры зубчатой пары:
делительные диаметры
d1 = mz1cosb = 125·2009859 = 2536 мм
d2 = mz2cosb = 125·9209859 = 11664 мм
проверяем межосевое расстояние
aw = (d1+d2)2 = (2536 + 11664)2 = 71 мм
da1 = d1+2m = 2536+2·125 = 2786 мм
da2 = d2+2m = 11664+2·125 = 11914 мм
df1 = d1 – 24m = 2536 – 24·125 = 2236 мм
df2 = d2– 24m = 11664 – 24·125 = 11364 мм
b2 = ybaaw = 03·71= 213 мм
b1 = b2 +(3÷5) = 213+(3÷5) = 23 мм
коэффициент ybd= b1d1 = 242536 = 0946
v = 1· d12 = 30615 · 25362 = 388 мс
принимаем 7-ую степень точности.
6. Размеры смазывающего колеса:
Межосевое расстояние aw = 55
zΣ = 2awcosbm=2·55·09859125=85
делительные диаметры:
d2 = mz2cosb = 125·6509859 = 848 мм
проверяем межосевое расстояние:
aw = (d1+d2)2 = (2536 + 848)2 = 55 мм
da2 = d2+2m = 848+2·125 = 873 мм
df2 = d2– 24m = 848 – 24·125 = 818 мм
b2 = ybaaw = 03·55= 20 мм
7. Силы действующие в зацеплении:
- окружная Ft1 = N1v = 7374·103388 = 1900 H
- радиальная Fr1 = Ft1·tgacosb = 1900·tg 20º09859 = 701 H
- осевая Fa1 = Ft1·tgb = 1900·tg 9627º = 322 H
Проверяем мощность на быстроходном валу:
N1 = vFt1 = 3881900= 7372 Вт
8.Расчетное контактное напряжение:
где ZH = 2462 – коэффициент учитывающий форму сопряженных поверхностей зубьев;
ZE = 194 МПа12 –коэффициент учитывающий механические свойства материалов [2c46];
Ze = 077- коэффициент учитывающий суммарную длину контактных линий;
Zb = 1 – коэффициент учитывающий наклон зуба;
Коэффициент осевого перекрытия
eb = b1sinbm = 24sin9627°125 = 102
Ze = (1ea)05 = (11687)05 = 077
Коэффициент торцевого перекрытия
ea = [188 – 32(1z1 + 1z2)] cosb = [188 – 32(120+192)] 09859 = 1687
KHa = 1042 – коэффициент учитывающий распределение нагрузки между зубьями; [4 с.54 табл.6.11]
KHb = 12 – коэффициент учитывающий распределение нагрузки по ширине венца;
KHv = 107 – коэффициент учитывающий динамическую нагрузку.
Н = 194·2462·077·1[1900·134· (45+1)2536·24·45]05 = 832 МПа [Н]=900МПа
Условие sH [sH] выполняется
9. Расчет при действии максимальной нагрузки:
Кпер = 15 – коэффициент перегрузки
[HPmax] = 40HRC = 40·50 = 2000 МПа
sНmax = 900·1505 = 110227 МПа [sНPmax]
Условие sНmax [sНPmax] выполняется
10. Расчетное изгибное напряжение:
F = YFSYeYbFtKFbm≤[F]
YFS – коэффициент учитывающий форму зуба;
Ye = 1 – коэффициент учитывающий перекрытие зубьев;
Yb – коэффициент учитывающий наклон зуба;
Эквивалентное число зубьев
шестерня [sF]1YF1 = 269378 = 7116 МПа
колесо [sF]2YF2 = 292361 = 8088 МПа
т.к. [sF]2YF2 > [sF]1YF1 то расчет ведем по зубьям шестерни
Yb = 1 – b·b120º = 1 –1185·9627120º = 09
KFa – коэффициент учитывающий распределение нагрузки между зубьями;
KFa = [4 + (ea - 1)(n`-5)]4ea
n` = 7 – степень точности
KFa = [4 + (1687 - 1)(7-5)]4·1687)] = 0796
KFb = 132 – коэффициент учитывающий распределение нагрузки по ширине венца; [1 c.45 табл.6.3]
KFv = 1 – коэффициент учитывающий динамическую нагрузку.
F = 1900·105·378·1·0924·125 = 226 Мпа [F]= 270МПа
Условие sF1 [sF]1 выполняется.
11. Расчет при действии максимальной нагрузки:
sFmax = sFT1maxT1 [sFPmax]
T1maxT1 = 15 – коэффициент перегрузки
[FPmax]= 17[]F = 17·270 = 459 МПа
sFmax = 226·15 =339 МПа [sFPmax]
Условие sFmax [sFPmax] выполняется.
Расчет тихоходной ступени.
принимаем сталь 40Х.
Термообработка: колесо – закалка НRC=50;
шестерня – закалка НRC=50.
Допускаемые контактные напряжения
[H] =H·limb·KHL[ SH]=(18HRC+150)KHL[SH]
где [SH] – коэффициент безопасности принимаем [SH] = 115 [1 с.33]
N - эквивалентное число циклов перемены напряжений
где - угловая скорость соответствующего вала 1с
Lh – срок службы привода
Если N>NH0 то KHL=1и KFL [3 c.55-56]
[H] = (18·50+150)1115 = 913 МПа
Допускаемые напряжения изгиба:
где 0F lim b – предел выносливости принимаем 0F lim b = 500 [4 c.45]
[SF] – коэффициент безопасности
где [SF]` = 18 – коэффициент нестабильности свойств материала
[SF]`` = 1 – коэффициент способа получения заготовки [1c.44 – 45]
[F] = 50018 = 278 МПа
yba = 0315 – коэффициент ширины колеса.
ybd = yba(u+1)2 = 0315(4+1)2 = 07875
аw = 430(4+1)(38823·124 2·0315·9002)13 =10428 мм
принимаем согласно ГОСТ 2185-66 [2 c.52] аw =100 мм
m = (001÷002)a w = (001÷002)100= 1÷2 мм
принимаем по ГОСТ 9563-60 m = 20 мм
суммарное zΣ = 2aw · cosbm = 2100·cos 10 º 2 = 9848 99
шестерни z3 = zΣ(u+1) = 9848(4+1) = 1969 20
колеса z4 = zΣ – z3 = 9848 – 1969 = 7878 79
уточняем передаточное число:
u2 = z4z3 = 7920 = 395
уточняем расхождение передаточного числа:
(4-395)395·100% = 12%
уточняем угол наклона:
d3 = mn z3cosb = 20·20cos 810961 = 40405 404 мм
d4 = mz4cosb = 20·50 cos 810961 = 159595 1596 мм
аw = 05(40405+159595) =100 мм
da3 = d3+2m = 404+2·20 = 444 мм
da4 = d4+2m = 1596+2·20 = 1636 мм
df3 = d3 – 24m = 404 – 24·20 = 356 мм
df4 = d4– 24m = 1596 – 24·20 = 1548 мм
b4 = ybaaw = 0315·100= 315 мм
b3 = b4 +(3÷5) = 315+(3÷5) = 339 мм
коэффициент ybd= b3d3 = 339404 = 0841
v = 2 · d32 = 68·4042 = 1374 мс
принимаем 7-ую степень точности
6. Размеры смазывающих пар:
d3 = mn z3cosb = 20·20cos 810961 = 40405 мм
d4 = mz4cosb = 20·50 cos 810961 = 101595 мм
d5 = mz5cosb = 20·23 cos 810961 = 46405 мм
аw = 05(46405+101595) =74 мм
da4 = d4+2m = 101595+2·20 = 105595 мм
da5 = d5+2m = 46405+2·20 = 50405 мм
df4 = d4– 24m = 101595 – 24·20 = 972 мм
df5 = d5– 24m = 46405 – 24·20 = 41405 мм
b5 = b4 +(3÷5) = 224+(3÷5) = 26 мм
Принимаем увеличенную ширину шестерни = 36 мм для упрочнения шестерни
b4 = ybaaw = 0315·71= 224 мм
Принимаем увеличенную ширину колеса = 316 мм для упрочнения колеса
b3 = b4 +(3÷5) = 224+(3÷5) = 26 мм
Принимаем увеличенную ширину шестерни = 338 мм для упрочнения шестерни.
- окружная Ft2 = 2T2d3 = 2·10063·103404 =4982 H
- радиальная Fr2 = Ft2tga =4982tg20º = 1813 H
- осевая Fa2 = Ft2·tgb = 4982·tg 810961º = 710 H
Проверяем мощность на промежуточном валу
N2= vFt2 = 49821374 = 6845 кВт
8. Расчетное контактное напряжение
где ZH = 174 – коэффициент учитывающий форму сопряженных поверхностей зубьев;
Ze - коэффициент учитывающий суммарную длину контактных линий;
Zb = 1 – коэффициент учитывающий угол наклона зуба.
ea = [188 – 32(1z3 + 1z4)] cosb = [188 – 32(120+179)]·cos 810961 = 166
eb = b1sinbm = 34sin 810961°2 = 0763
Ze = [(4 - ea)3]05 = [(4 - 166)3]05 = 0883
KHa = 102 – коэффициент учитывающий распределение нагрузки между зубьями [1];
KHb = 12 – коэффициент учитывающий распределение нагрузки по ширине венца;
KHv = 107– коэффициент учитывающий динамическую нагрузку [4 стр.40 табл. 3.6].
Н = 1·194·0883·174[4982·126(4+1)4·404·3182]05 = 736 МПа
9. Расчет при действии максимальной нагрузки
sНmax =sH ·Kпер05= 736·1505 = 901 МПа [sНPmax]
Условие sНmax [sНPmax] выполняется.
10. Расчетное изгибное напряжение
Y–коэффициент формы зуба зависящий от числа зубьев
при z1= 20 YF1 = 403
шестерня [sF]1YF1 = 270403 = 67 МПа
колесо [sF]2YF2 = 270361 = 748 МПа
Yb = 1 – b·b120º = 1 –0763·810961120º = 0948
KFb = 15 – коэффициент учитывающий распределение нагрузки по ширине венца;
KFV = 1 – коэффициент учитывающий динамическую нагрузку [4 с. 43 табл. 3.8.]
KFa = [4 + (166 - 1)(7-5)]4·166)] = 0801
F = 4982·12·403·0948·156567·2 =202 Мпа [F] =270МПа
Условие sF1 [sF] выполняется.
11. Расчет при действии максимальной нагрузки
sFmax = sFT1maxT1 sFPmax
FPmax = 17[]F = 17·270 = 459 МПа
sFmax =202·15 =303 МПа sFPmax
Условие FPmax sFPmax выполняется.
Предварительный расчет валов.
где Т – передаваемый момент;
[tк] = 15÷20 МПа – допускаемое напряжение на кручение [1c.161]
d1 = (16 · 2315·10315)13 = 20 мм
Чтобы ведущий вал редуктора можно было соединить с помощью стандартной упругой втулочно-пальцевой муфты (допускаемый момент у муфты 125 Н·м диапазон диаметров соединяемых валов 25÷28 мм) с валом электродвигателя диаметром dдв = 32 мм принимаем:
диаметр выходного конца dв1 = 32 мм;
диаметр под уплотнением dу1 = 33 мм;
диаметр под подшипником dп1 = 35 мм.
Выбираем конструкцию «Вал – Шестерня».
3. Промежуточный вал
d2 = (16·10063·10315)13 = 32 мм
диаметр под подшипником dп2 = 35 мм;
диаметр под колесом dк2 = 36 мм.
Так же выбираем конструкцию «Вал – Шестерня».
4. Конструктивные размеры колеса:
dст = (15 17)d = (15 17)36 = 54 61 мм
принимаем dст = 57 мм
lст = (12 17)d = (12 17)36 = 43 61 мм
принимаем lст = 54 мм (с последующей проверкой шпонок на смятие)
d = 4m = 4·125 = 5 мм
С = 03b = 03·24 =7 мм
d3 = (16·38823·10315)13 = 51 мм
диаметр выходного конца dв3 = 40 мм;
диаметр под уплотнением dу3 = 45 мм;
диаметр под подшипником dп2 = 50 мм.
диаметр под колесом dк2 = 52 мм.
6. Конструктивные размеры колеса:
dст = (15 17)d = (15 17)52 = 78 88 мм
принимаем dст = 80 мм
lст = (12 17)d = (12 17)52 = 62 88 мм
принимаем lст = 70 мм
d = 4m = 4·20 = 8 мм
С = 03b = 03·57 =17 мм
Первый этап компоновки редуктора
Проводим три горизонтальные осевые линии на расстоянии 100 и 71 мм – оси валов. Вычерчиваем упрощенно шестерню и колесо со ступицей. От верхнего края ступицы откладываем 5 мм и ширину шестерни тихоходной ступени. Вычерчиваем упрощенно тихоходную ступень. Очерчиваем внутреннюю стенку корпуса: принимаем зазор между торцом шестерни и ступицы и стенкой корпуса 10 мм; зазор от окружности вершин зубьев колеса до внутренней стенки корпуса 8 мм.
Предварительно намечаем радиальные шарикоподшипники лёгкой серии №207 для быстроходного роликоподшипники радиальные с короткими цилиндрическими роликами №32207А для промежуточного вала и шарикоподшипники радиально-упорные однорядные №46305 для тихоходного вала.
Принимаем для подшипников пластичный смазочный материал. Для предотвращения вытекания смазки внутрь корпуса и вымывания пластичного смазочного материала жидким маслом из зоны зацепления устанавливаем мазеудерживающие кольца.
Конструктивные элементы корпуса
Толщина стенок корпуса и крышки редуктора
Толщина верхнего фланца корпуса
S = 15d = 15·9 = 13 мм
Толщина нижнего пояса корпуса
р = 235d = 235·9 = 21 мм
принимаем болты М16 4шт.;
- крепящих крышку к корпусу у подшипников
d2 = 075dф = 075·25 = 189 мм
принимаем болты М19;
- соединяющих крышку с корпусом
d3 = 06dф = 06·25 = 15 мм
принимаем болты М15.
Проверка долговечности подшипников
1. Схема нагружения быстроходного вала.
Консольная сила от муфты
Fм = 100Т105 = 100·240905 = 491 Н
Силы действующие в зацеплении:
Рис. 7.1. – Расчетная схема быстроходного вала
Горизонтальная плоскость. Сумма моментов сил и реакций опор относительно опоры А
mA = 43Ft1 – 166BX + 97Fм = 0
Отсюда находим реакцию опоры В в плоскости XOZ
BX =(43Ft1 + 97Fм)166 = (43·1900 + 97·491)166 = 779 H
Сумма моментов сил и реакций опор относительно опоры В
mВ = 263Fм – 123Ft1 – 166АX = 0
Реакция опоры А в плоскости XOZ
AX =(263Fм –123Ft1)166= (491·263 – 123·1900)166 = – 630 H
AX + Ft1 – BX – FМ = – 630 + 1900 – 779 – 491 = 0 H
Изгибающие моменты в плоскости XOZ
MX1 =123BX = 123·779= 958 Н·м
MX2 =97Fм = 97·491= 476 Н·м
Вертикальная плоскость. Сумма моментов сил и реакций опор относительно опоры А
mA = 43Fr1+ Fa1d12 – 166BY = 0
Отсюда находим реакцию опоры В в плоскости YOZ
BY =(43Fr1 + Fa1d12)166= (43·701+322·25362)166 = 206 H
mВ = 166АY + Fa1d12 – 123Fr1 = 0
Реакция опоры А в плоскости YOZ
AY =(123Fr1 – Fa1d12)166= (123·701 – 322·25362)166 = 495 H.
AY – Fr1 + BY = 495 – 701 + 206 = 0 H
Изгибающие моменты в плоскости YOZ
MY1 = 43Fм = 43·495 = 21 Н·м
MY2 = 123BY = 123·206 = 25 Н·м
Суммарные реакции опор
А = (АХ2 + АY2)05 = ((-630)2 + 4952)05 = 801 H
B= (BХ2 + BY2)05 = (7792 + 2062)05 = 806 H
2. Эквивалентная нагрузка
P = (XVFr + YFa)KбКТ
где Х = 1 – коэффициент радиальной нагрузки;
V = 1 – вращается внутреннее кольцо;
Fr = В – радиальная нагрузка;
Y – коэффициент осевой нагрузки;
Fa – осевая нагрузка;
Kб = 15 – коэффициент безопасности;
КТ = 1 – температурный коэффициент.
Проверяем наиболее нагруженный подшипник В
Отношение FaВ = 322800 = 04025 > e : следовательно Х = 056; Y = 199
Р = (056·1·701+199·322)15·1 = 1550 Н
3. Расчетная долговечность подшипника
где р = 3 – для шариковых подшипников
Lh = (10660·2925)(191001550)3 =10661 час
больше минимальной долговечности подшипников 10000 час (ГОСТ 16162-85) а так же примерно равно ресурсу работы редуктора t = 12600 час.
4. Схема нагружения промежуточного вала.
Ft1 = 1900 H; Ft2 = 4982 H;
Fr1 = 701 H; Fr2 = 1813 H;
Fa1 = 322 H; Fa2 = 710 H.
Рис. 7.2 – Расчетная схема промежуточного вала
Горизонтальная плоскость. Сумма моментов сил и реакций опор относительно опоры С
mС = 43Ft1 + 106Ft2 – 1665DX = 0
Отсюда находим реакцию опоры D в плоскости XOZ
DX = (43Ft1 + 106Ft2)1665 = (43·1900 + 106·4982)1665 = 3662 H
Сумма моментов сил и реакций опор относительно опоры D
mD = 1235Ft1 + 605Ft2 – 1665CX = 0
Реакция опоры C в плоскости XOZ
CX = (1235Ft1 + 605Ft2)1665 = (1235·1900+605·4982)1665 = 3220 H
CX – Ft1 – Ft2 + DX = 3220 – 1900 – 4982 + 3662 = 0 H
MX1 = 43CX = 43·3220 = 138460 Н·мм = 1385 Н·м
MX2 = 605DX = 605·3662 = 221551 Н·мм = 2215 Н·м
Вертикальная плоскость. Сумма моментов сил и реакций опор относительно опоры C
mC = 106Fr2 – 43Fr1 – 1665DY + Fa1d12 – Fa2d22 = 0
Отсюда находим реакцию опоры D в плоскости YOZ
DY = (106Fr2 – 43Fr1 + Fa1d12 – Fa2d2)1665 =
= (106·1813 – 43·701+322·116642 – 710·4042)1665 = 1000 H
mD = 605Fr2 – 1235Fr1 + 1665CY – Fa1d12 + Fa2d22 = 0
Реакция опоры C в плоскости YOZ
CY = (1235Fr1 + Fa1d12 – Fa2d22 – 605Fr2)1665 =
= (1235·701 + 322·116642 – 710·4042 – 605·1813)1665 = –112 H
CY – Fr1 – DY + Fr2 = –112 – 701 – 1000 + 1813 = 0 H
MY1 = 43CY = 43·(–112) = – 4816 Н·мм = – 48 Н·м
MY2 = 605DY = 605·1000 = 60500 Н·мм = 605 Н·м
MY3 = 1235DY – 63Fr2= 1235·1000 – 63·1813 = 9281 Н·мм = 9 Н·м
C = (CX + CY)05= (32202 + (-112)2)05 = 3222H
D = (DX + DY)05= (36622 + 10002)05 = 3796 H
5. Эквивалентная нагрузка
Fr = D – радиальная нагрузка;
Проверяем наиболее нагруженный подшипник D
Отношение FaD = 2463796 = 0064 e : следовательно Х = 10; Y = 0
Р = (100·1·3796 + 0)15·1 = 5694 Н
6. Расчетная долговечность подшипника
Lh = (10660·650)(484005694)3 = 15748 час
больше минимальной долговечности подшипников 10000 час (ГОСТ 16162-85) а так же больше ресурса работы редуктора t = 12600 час.
7. Схема нагружения тихоходного вала.
Fм = 125Т305 = 125·388205 = 2463 Н
Рис. 7.3. – Расчетная схема тихоходного вала
Горизонтальная плоскость. Сумма моментов сил и реакций опор относительно опоры Е
mЕ = 106Ft2 + 1665Fх – 2745Fм = 0
Отсюда находим реакцию опоры F в плоскости XOZ
FX = (2745Fм – 106Ft2)1665 = (2745·2463 – 106·4982)1665 = 889 H
Сумма моментов сил и реакций опор относительно опоры F
mF = 605Ft2 – 1665Fх + 108Fм = 0
Реакция опоры E в плоскости XOZ
EX = (605Ft2 + 108Fм)1665 = (605·4985 + 108·2463)1665 = 3409 H
EX – Fx – Ft2 + FM = 3409 – 889 – 4982 + 2463 = 0 H
MX1 = 108FM = 108·2463 = 266004 Н·мм = 266 Н·м
MX2 = 106EX = 106·3409 = 361354 Н·мм = 3614 Н·м
Вертикальная плоскость. Сумма моментов сил и реакций опор относительно опоры E
mE= 106Fr2– 1665FY = 0
Отсюда находим реакцию опоры F и Е в плоскости YOZ
FY =106Fr21665= 106·18131665 = 1154 H
mF = 605Fr2 – 1665FY = 0
EY = 605Fr21665 = 605·18131665 = 659 Н
ЕY – Fr2 + FY = 659 – 1813 + 1154 = 0 H
MY1 = 106EY = 106·659 = 69854 Н·мм = 699 Н·м
E =(EX2 + EY2)05= (34092 + 6592)05 = 3472 H
F =( FX2 + FY2)05= (8892 + 11542)05 = 1457 H
8. Эквивалентная нагрузка
где Х = 1 – коэффициент радиальной нагрузки при отсутствии осевой нагрузки;
Fr = Е – радиальная нагрузка;
Y = 0 – коэффициент осевой нагрузки;
Kб = 15 – коэффициент безопасности;
FrC0= 009 отсюда e = 023
Проверяем наиболее нагруженный подшипник Е
FaE = 02 e : X = 1 Y=0
Р = (1·1·3427+0)15·1 = 5140 Н
9. Расчетная долговечность подшипника
Lh = (10660·1625)(351005140)3 = 32660 час
больше минимальной долговечности подшипников зубчатых
редукторов 10000 час (ГОСТ 16162-85) а так же больше ресурса работы редуктора t = 12600 час.
Проверка прочности шпоночных соединенний.
1. Выбираем шпонки призматические по ГОСТ 23360-78.
Материал шпонок – сталь 40Х улучшенная.
Находим напряжение смятия и среза шпонок:
ср = 2Тdlb [cp] = 06[cм] = 60 МПа
где h – высота шпонки;
2. Быстроходный вал. Шпонка на выходном конце вала 10×8×45
см = 2·2409·10331(8-5)(45-10) = 148 МПа
ср = 2·2409·10331·45·10 =35 МПа
3. Промежуточный вал. Шпонка под колесом 10×8×35
см = 2·1006·10336(8-5)(35-10) = 745 МПа
ср = 2·1006·10336·35·10 = 16 МПа
4. Тихоходный вал. Шпонка под колесом 16×10×37
см = 2·3882·10352(10-6)(60-16) = 85 МПа
ср = 2·3882·10352·60·16 = 155 МПа
5. Тихоходный вал. Шпонка на выходном конце вала 20×12×70
см = 2·3882·10344(12-75)(70-20) = 784 МПа
ср = 2·3882·10340·70·20 = 139 МПа.9. Уточненный расчет валов
1. Быстроходный вал.
Рассмотрим сечение А-А проходящее под опорой А. Концентрация напряжений обусловлена подшипником посаженным с гарантированным натягом.
Материал вала сталь 40Х закалённая: sВ = 930 МПа [4c.34]
Пределы выносливости материала вала:
-при изгибе s-1 » 043×sВ = 043×930 = 400 МПа;
-при кручении t-1 » 058×s-1 = 058×400 = 232 МПа.
Суммарный изгибающий момент: Mи = Мх = 476 Н×м
момент сопротивления сечения изгиба:
W = d332 = ·35332 = 42·103 мм3
момент сопротивления кручению:
Wр = 2W = 2·42·103 = 84·103 мм3
Амплитуда нормальных напряжений:
v = MиW = 476·10342·103 = 113 МПа.
Амплитуда и среднее напряжение цикла касательных напряжений при кручении:
tv = tm = T12Wp = 2409·1032·84·103 = 14 МПа.
Коэффициенты: ke =38; kt et = 27; yt = 01 [4c.166]
Коэффициент запаса усталостной прочности по нормальным напряжениям:
s = -1(kve ) = 40038·113 = 93
Коэффициент запаса прочности по касательным напряжениям:
st = t-1(kttvet + yt tm) = 232(27·14 + 01·14) = 59
Общий коэффициент запаса прочности:
s = sst(s2 + st2)05 = 93·59(932 +592)05 = 92 > [s] = 2 [2c162]
Расчет на статическую прочность:
МПа [] = 9302 = 465 МПа
2.Промежуточный вал.
Рассмотрим сечение В-В. Концентрация напряжений обусловлена наличием шпоночной канавки.
Суммарный изгибающий момент:
= (21882 + 6582)12 = 228 Н×м
где t1 и b – параметры шпоночного паза
WНЕТТО = p×36332 – [16×6×(36-6)2](2×36)=338×103 мм3
Момент сопротивления кручению:
WК_НЕТТО = p×36316 – [16×6×(36-6)2](2×36)=796×103 мм3
sV = МИWнетто = 228×103338×103 = 675 МПа
Амплитуда и среднее напряжение цикла касательных напряжений:
tV = tm = Т22×Wк нетто = 1006×1032×796×103 = 63 МПа
ks = 17 [1c. 165];es = 086 [1с. 166];
Коэффициент запаса прочности по нормальным напряжениям:
= 400(17×675086) = 3
= 232(265×63075 + 01×63) = 101
= 3×101(32 +1012)12 = 29 > [s] = 20
МПа [] = 9302 = 465 МПа.
Опасное сечение Д-Д проходит под колесом. Концентрация напряжений обусловлена наличием шпоночной канавки.
Материал вала сталь 40Х закалённая: sВ = 930 МПа.
Пределы выносливости:
Суммарный изгибающий момент:
= (35672 + 6892)12 = 363 Н×м
Момент сопротивления изгибу:
= p×52332 – [16×6×(52-6)2](2×52)=119×103 мм3
sV = МИ Wнетто = 363×103119×103 =31 МПа
tV = tm = Т3 (2×Wк нетто) = 3882×1032×257×103 = 76 МПа
ks = 17 [1c. 165]; es = 086 [1с. 166];
= 400(17×31086) = 65
= 232(265×76075 + 01×76) = 84
= 6584(652 + 842)12 = 51 > [s] = 20 [1c. 162]
Рассмотрим сечение Е-Е проходящее через опору F
Осевой момент сопротивления:
W = d332 = 50332 =123103 мм3
Полярный момент сопротивления:
Wp = 2W = 2123103 = 246103 мм3
v = MиW =266103123103 =216 МПа; m = 0
v = m = max2 = T32Wp = 38821032246103 = 79 МПа
s = -1(k)v = 40038216 = 49
s = -1[(k)v + m] = 232(2779+0179) = 105
s = sst(s2 + st2)05 = 49·105(492 +1052)05 = 44 > [s] = 20
Расчет и проверка муфт.
Для передачи вращающего момента с вала электродвигателя на ведущий вал редуктора выбираем муфту упругую втулочно-пальцевую МУВП по ГОСТ 21424-75 с допускаемым передаваемым моментом [T] = 125 Н·м.
Расчетный вращающий момент передаваемый муфтой:
Тр = kТ1 = 15·2409 = 361 Н·м [T]=125Н·м
Условие Тр [T] выполняется.
Посадки назначаем согласно рекомендациям [1c.263]
Посадка зубчатых колес на вал Н7р6;
Посадка полумуфт на вал Н7
Посадка внутренних колец подшипника на валы
Посадка наружных колец подшипника в корпус Н7.
1. Смазка зубчатого зацепления осуществляется путем окунания зубчатых колес в масляную ванну.
Объем масляной ванны:
V = (0508)N = (05 08)75 » 4 л
Рекомендуемое значение вязкости масла:
среднее значение n = 31·10-6 м2с
По этой величине выбираем масло индустриальное И-30А
2. Смазка подшипниковых узлов пластичная - смазочным материалом УТ-1.
Пред сборкой внутреннюю полость редуктора тщательно очищают и покрывают маслостойкой краской. Сборку производят в соответствии со сборочным чертежом редуктора начиная с узлов валов.
На ведущий вал насаживают смазывающие колёса манжеты мазеудерживающие кольца и шарикоподшипники предварительно нагретые в масле до 80 – 100 ºС и надевают закладную крышку подшипника с манжетным уплотнением.
В промежуточный вал закладывают шпонку и напрессовывают зубчатое колесо до упора в буртик вала; затем надевают распорную втулку мазеудерживающие кольца и устанавливают предварительно нагретые подшипники.
В тихоходный вал также закладывают шпонку и напрессовывают зубчатое колесо до упора в буртик вала; затем надевают распорную втулку мазеудерживающие кольца манжету и устанавливают предварительно нагретые подшипники.
Собранные валы укладывают в основание корпуса редуктора вставляют закладные крышки подшипников в подшипниковые камеры закладывают пластичную смазку и устанавливают крышку корпуса: центровка которой осуществляется с помощью двух конических штифтов; затягивают винты крепящие крышку к корпусу.
Затем устанавливают дополнительные оси для смазывающих колёс на оси напрессовывают распорные втулки на которые устанавливают смазочные колёса.
Далее вворачивают пробку маслоспускного отверстия устанавливают маслоуказатель заливают в корпус масло и закрывают смотровое отверстие крышкой.
Собранный редуктор обкатывают и подвергают испытанию на стенде по программе устанавливаемой техническими условиями.
Список использованной литературы
Расчет и проектирование деталей машин: Учебное пособие для вузов. Под ред. Г.Б. Столбина и К.П. Жукова. – М.: Высш. шк. 1978. – 247 с.
Шейнблит А.Е. Курсовое проектирование деталей машин. – М.: Высш. шк. 1991.–432 с.
Курсовое проектировании деталей машин. С.А. Чернавский К.Н. Боков И.Б. Чернин и др. – М.: Машиностроение 1988. – 416 с.
Кинематический расчет с.1
Расчет быстроходной ступени с.3
Расчет тихоходной ступени с.10
Предварительный расчет валов .с.17
Первый этап компоновки редуктора .с.19
Конструктивные элементы корпуса ..с.20
Проверка долговечности подшипников с.21
Проверка прочности шпоночных соединений .с.30
Уточненный расчет валов с.31
Расчет и проверка муфт с.37
Смазка редуктора с.37
Сборка редуктора .с.38
Список использованной литературы .. ..с.39
вал -шестерня.cdw

Центровые отверстия форма Н по ГОСТ14034-74.
Смещение шпоночных пазов относительно оси вала не более 0.08мм.
Неуказанные рабиусы R2
Сталь 40Х ГОСТ 1050-88
КП-ИГЭУ-ТиПМ-0894023-01-11
Спецификация.spw

Кольцо мазеудерживающее
Шестерня (Вал-шестерня)
Шестерня (Вал - шестерня)
-6g х 60.58.35Х.16 ГОСТ 7808-70
-6H.12.40Х.16 ГОСТ 5915-70
Шайба 8 Л 65Г029 ГОСТ 6402-70
Шайба 6 Л 65Г029 ГОСТ 6402-70
Мaнжета 1.1-50 х 8- 1 ГОСТ 8752-79
Мaнжета 1.1-65 х 8- 1 ГОСТ 8752-79
Подшипник №46305 ГОСТ 831-75
Подшипник №207 ГОСТ 8338-75
Подшипник №32207А ГОСТ 8328-75
Шпонка 10 х 8 х 35 ГОСТ 23360-78
Шпонка 10 х 8 х 45 ГОСТ 23360-78
Шпонка 16 х 10 х 70 ГОСТ 23360-78
Шпонка 20 х 12 х 70 ГОСТ 23360-78
Вставка корпусная.cdw

Формовочные уклоны по ГОСТ 3212-57.
Литье должно быть плотным - раковины и рытвины
Покрытие механически необработанных поверхностей:
внутрених - нитроэмаль.
Неуказанные предельные отклонения размеров диаметров Н14
КП-ИГЭУ-ТиПМ-0894023-01-11
допуски и посадки.doc
Условное обозначение полей
Подшипник-корпус 90Н7l0
Подшипник-корпус 72Н7l0
Подшипник-корпус 62Н7l0
колесо.cdw

Неуказанные предельные отклонения размеров:
Перекос шпоночного паза не более 0
Сталь 40Х ГОСТ 4543-71
КП-ИГЭУ-ТиПМ-0894023-01-11
Направление линии зуба
Нормальный исходный контур
Коэффициент смещения
Рекомендуемые чертежи
- 21.10.2021