Редуктор двухступенчатый соосный




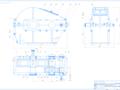
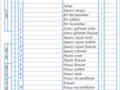
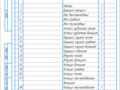
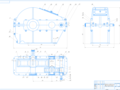
- Добавлен: 24.01.2023
- Размер: 532 KB
- Закачек: 0
Описание
Редуктор двухступенчатый соосный
Состав проекта
![]() |
![]() |
![]() ![]() ![]() ![]() |
![]() ![]() ![]() ![]() |
![]() |
![]() ![]() ![]() |
![]() ![]() ![]() ![]() |
![]() ![]() ![]() |
![]() ![]() ![]() ![]() |
![]() ![]() ![]() ![]() |
![]() |
Дополнительная информация
СБ редуктор_5.11_R03.cdw

СБ привод.cdw

сб1.doc
образования Российской Федерации
КРАСНОЯРСКИЙ ГОСУДАРСТВЕННЫЙ ТЕХНИЧЕСКИЙ УНИВЕРСИТЕТ
Кафедра «Технология Машиностроения»
Расчетно-пояснительная записка к курсовому проекту
«Технология машиностроения»
Студент: Лаврухин А.И.
Руководитель проекта: Городилов А.А.
1.Режим работы и фонды времени
2.Расчеты по программе выпуска
3.Тип и форма организации производства
Разработка технологического процесса сборки узла
1.Служебное назначение узла
2.Выявление и анализ технических условий и норм точности
3.Выбор методов достижения точности
4.Анализ технологичности узла
5.Методы и схемы контроля
6.Разработка последовательности сборки
7.Проектирование технологических операций
8.Расчет числа единиц оборудования рабочих мест и состава рабочих
Разработка технологического процесса изготовления специальной детали
1.Анализ служебного назначения и технических условий
2.Анализ технологичности
3.Методы и схемы контроля
4.Выбор экономичного варианта получения исходной заготовки
5.Обоснование выбора технологических баз и разработка последовательности изготовления
6.Определение припусков и меж переходных размеров
7.Выбор экономичного варианта технологического процесса
8.Проектирование технологических операций
8.1.Структура и содержание операции
8.3.Техническое нормирование
9.Анализ и расчет точности обработки
Снижение себестоимости изделий является наиболее актуальной задачей в условиях создавшегося экономического положения в стране. Это предопределяет разработку новых технологических процессов менее энергоёмких и материалоёмких но позволяющих получать продукцию не проигрывающую по качеству и более выгодную по себестоимости.
На снижение себестоимости продукции большое влияние оказывает последовательность и содержание технологического процесса. От последовательности технологического процесса напрямую зависит процент брака изготовляемых деталей. Из этого следует вывод о необходимости подробной проработки технологического процесса создания необходимого оборудования разработки новых инструментальных материалов и усовершенствования технологий изготовления уже известных.
В работе выполнены следующие задачи: анализ технологичности конструкции цилиндрического редуктора и корпуса; разработан технологический процесс сборки цилиндрического редуктора; выбор способа получения заготовки; расчет припусков на механическую обработку и межоперационных размеров; проектирование технологических процессов изготовления корпуса цилиндрического редуктора.
Целью данной курсовой работы является разработка технологического процесса изготовления корпуса цилиндрического редуктора.
Техническое задание.
1.Режимы работы и фонды времени.
При определении фонда времени работы оборудования и рабочих приняты следующие данные
a)Календарное время — 365 дней;
b)Количество выходных дней — 104 дня;
c)Количество предпраздничных дней сокращённых на один час — 6 дней;
d)Количество праздничных дней — 8 дней.
Отсюда следует что количество рабочих дней равно:
nР = 365 – 104 – 8 = 253 дня.
Количество рабочих дней с полной продолжительностью рабочей смены:
nP.п. = 253 – 6 = 247 дней.
Продолжительность смены — 8 часов.
Количество смен — 1.
Fном=247*8+6*7=2018 часов.
где Kr– коэффициент учитывающий потери времени при болезни простои оборудования и т. д.
Fд=2018*0.97=1957 часов.
Действительный годовой фонд времени рабочего при продолжительности отпуска 24 рабочих дня:
Fд.p.=Fд*0.88*1=1957*0.88*1=1722 часа.
2.Расчёт по программе выпуска.
Годовая программа выпуска Nг=1000 шт.
Определим месячную программу выпуска:
Nм= Nг12=100012= 83 шт.
Определим дневную программу выпуска:
Nд=Nг253=1000253 » 4 шт.
что означает 4 изделия в рабочую смену.
3.Тип и формы организации производства.
В связи с годовым выпуском устанавливаем тип производства – мелко серийный. Форма организации производства – предметная. Станки и оборудование располагаются в последовательности технологических
операций для нескольких деталей требующих одинаковый порядок обработки. Обработка деталей на станке производится партиями при этом время выполнения операций на металлорежущих станках может быть не согласованно по времени с другими операциями. Изготовленные детали хранятся в накопительных контейнерах а затем транспортируются партиями по 20 штук (что соответствует недельной программе выпуска).
Спецификация.spw

Колесо зубчатое малое
Колесо зубчатое большое
Крышка глухая средняя
Крышка глухая большая
Кольцо маслоотбойное
Крышка сквозная малая
Болт М12 х 14 ГОСТ 15589-70
Болт М8 х 18 ГОСТ 15589-70
Болт М12 х 150 ГОСТ 15589-70
Болт М12 х 45 ГОСТ 15589-70
Гайка М12 ГОСТ 15526-70
Гайка М18 ГОСТ 5929-70
Подшипник 206 ГОСТ 2893-82
Подшипник 209 ГОСТ 2893-82
Подшипник 211 ГОСТ 2893-82
Шайба 12 Н ГОСТ 6402-70
Штифт 8 х 36 ГОСТ 3129-70
Заклепка 5 х 10 ГОСТ 10299-80
Шпонка 20 х 12 х 56 ГОСТ 23360-78
Шпонка 16 х 10 х 45 ГОСТ 23360-78
Шпонка 12 х 8 х 50 ГОСТ 23360-78
Шпонка 8 х 7 х 32 ГОСТ 23360-78
Шайба 18 ГОСТ 11371-78
сб.doc
образования Российской Федерации
КРАСНОЯРСКИЙ ГОСУДАРСТВЕННЫЙ ТЕХНИЧЕСКИЙ УНИВЕРСИТЕТ
Кафедра «Технология Машиностроения»
Расчетно-пояснительная записка к курсовому проекту
«Технология машиностроения»
Студент: А.И. Лаврухин
Руководитель проекта: А.А. Городилов
Режим работы и фонды времени
Расчеты по программе выпуска
Тип и форма организации производства
Разработка технологического процесса сборки узла
Служебное назначение узла
Выявление и анализ технических условий и норм точности
Выбор методов достижения точности
Анализ технологичности узла
Методы и схемы контроля
Разработка последовательности сборки
Проектирование технологических операций
Расчет числа единиц оборудования рабочих мест и состава рабочих
Разработка технологического процесса изготовления специальной детали
Анализ служебного назначения и технических условий
Анализ технологичности
Выбор экономичного варианта получения исходной заготовки
Обоснование выбора технологических баз и разработка последовательности изготовления
Определение припусков и меж переходных размеров
7. Выбор экономичного варианта технологического процесса
8. Проектирование технологических операций
8.1Структура и содержание операции
8.3. Техническое нормирование
9. Анализ и расчет точности обработки
Расчёт и конструирование приспособления
1. Техническое задание
2. Выбор и обоснование схемы приспособления.
3. Расчет параметров силового привода.
4. Расчёт точности приспособления.
Снижение себестоимости изделий является наиболее актуальной задачей в условиях создавшегося экономического положения в стране. Это предопределяет разработку новых технологических процессов менее энергоёмких и материалоёмких но позволяющих получать продукцию не проигрывающую по качеству и более выгодную по себестоимости.
На снижение себестоимости продукции большое влияние оказывает последовательность и содержание технологического процесса. От последовательности технологического процесса напрямую зависит процент брака изготовляемых деталей. Из этого следует вывод о необходимости подробной проработки технологического процесса создания необходимого оборудования разработки новых инструментальных материалов и усовершенствования технологий изготовления уже известных.
В работе выполнены следующие задачи: анализ технологичности конструкции цилиндрического редуктора и корпуса; разработан технологический процесс сборки цилиндрического редуктора; выбор способа получения заготовки; расчет припусков на механическую обработку и межоперационных размеров; проектирование технологических процессов изготовления корпуса цилиндрического редуктора.
Целью данной курсовой работы является разработка технологического процесса изготовления корпуса цилиндрического редуктора.
Техническое задание.
Режимы работы и фонды времени.
При определении фонда времени работы оборудования и рабочих приняты следующие данные
a)Календарное время — 365 дней;
b)Количество выходных дней — 104 дня;
c)Количество предпраздничных дней сокращённых на один час — 6 дней;
d)Количество праздничных дней — 8 дней.
Отсюда следует что количество рабочих дней равно:
nР = 365 – 104 – 8 = 253 дня.
Количество рабочих дней с полной продолжительностью рабочей смены:
nP.п. = 253 – 6 = 247 дней.
Продолжительность смены — 8 часов.
Количество смен — 1.
Fном=247*8+6*7=2018 часов.
где Kr– коэффициент учитывающий потери времени при болезни простои оборудования и т. д.
Fд=2018*0.97=1957 часов.
Действительный годовой фонд времени рабочего при продолжительности отпуска 24 рабочих дня:
Fд.p.=Fд*0.88*1=1957*0.88*1=1722 часа.
Расчёт по программе выпуска.
Годовая программа выпуска Nг=1000 шт.
Определим месячную программу выпуска:
Nм= Nг12=100012= 83 шт.
Определим дневную программу выпуска:
Nд=Nг253=1000253 » 4 шт.
что означает 4 изделия в рабочую смену.
Тип и формы организации производства.
В связи с годовым выпуском устанавливаем тип производства – мелко серийный. Форма организации производства – предметная. Станки и оборудование располагаются в последовательности технологических
операций для нескольких деталей требующих одинаковый порядок обработки. Обработка деталей на станке производится партиями при этом время выполнения операций на металлорежущих станках может быть не согласованно по времени с другими операциями. Изготовленные детали хранятся в накопительных контейнерах а затем транспортируются партиями по 20 штук (что соответствует недельной программе выпуска).
1. Служебное назначение узла
Цилиндрический одноступенчатый редуктор предназначен для передачи крутящего момента в приводе транспортера.
Передаточное отношение червячного редуктора – 16083.
Максимально допустимый крутящий момент на выходном валу – 583 Нм.
Частота вращения тихоходного вала – 70 обмин.
Модуль зубьев цилиндрических колес – 3 мм.
Число зубьев шестерни – 23.
Число зубьев колеса – 106.
Вес цилиндрического редуктора – 104 кг.
Для обеспечения нормальной работы цилиндрического редуктора в картер заливается индустриальное масло И-40А ГОСТ 20790–75. Объём смазочной жидкости – 7 литров.
Крутящий момент с электродвигателя через предохранительную муфту передаётся на вал-шестерню быстроходный 3 который приводит во вращение зубчатое цилиндрическое колесо 6. Тихоходный вал приводит в действие транспортер.
2. Выявление и анализ технических условий и норм точности.
Анализируя нормы точности указанные на чертежах цилиндрического редуктора и корпуса делаем вывод что степень точности зубчатой цилиндрической передачи и нормы осевых зазоров выбраны верно.
Для обеспечения работоспособности одноступенчатого цилиндрического редуктора необходимо обеспечить осевой зазор в подшипниковых опорах в пределах 015–02 мм. Для обеспечения пятна контакта зубьев шестерни с зубьями колеса по высоте 75% по длине 35% принята норма бокового зазора в цилиндрической передаче Сmin = 05 мм данное значение может быть выбрано по рекомендациям табл. 2.41 3 т.1. Выбранная норма бокового зазора исключает возможность заклинивания цилиндрической передачи при нагреве.
Допуск на профиль зуба S = ±0025 мм соответствует нормам табл. 2.43 3 т.1 .
Допустимая ошибка окружного шага Dt = 0026 мм и накопленная ошибка окружного шага SDt = 0055 мм соответствует нормам табл. 2.44 3 т.1 .
Посадки сопрягаемых поверхностей внутренних и наружных поверхностей подшипников посадка зубчатого колеса на вал посадки шпонок выбраны верно в соответствии с рекомендациями ЕСКД СЭВ
1.Служебное назначение узла
Редуктор червячный общего назначения предназначен для уменьшения частоты вращения с одновременным увеличением крутящего момента.
Редуктор применяется при постоянной и переменной нагрузке прямой и обратной работы с остановками и без температура внешней среды от-40до+40 внешняя среда не взрывоопасная.
Технические характеристики:
Электропривод предназначен для передвижения электротележки перегрузочной
Передаточное число червячного редуктора -60
Марка электродвигателя –ФОЛС2-11-Ч
Мощность электродвигателя-06кВт
Частота вращения электродвигателя-1320обмин
Максимальный крутящий момент на выходном валу редуктора-35кгсМ
Технические требования:
При сборке обеспечить плавную без заедания работу червячной пары.
В корпус редуктора залить масло трансмиссионное автомобильное до уровня контрольного отверстия. Подшипниковые узлы заполнить смазкой ЦИАТИМ-203
Предельные отклонения размеров: +-IT142
передаточное число-60
Межосевое расстояние-125мм
2 Выявление и анализ технических условий и норм точности
Допуски для обеспечения кинематической точности плавности работы контакта зубьев и требуемого бокового зазора назначаем по ГОСТ 3675-81
Окружная скорость ведомого червяка
где D-диаметр вершин зубьев червяка равный 49
V=314*49*132060*1000=338мс
Принимаем 7 степень точности по ГОСТ 3675-56
Толщина витка Sn=5.48
Измерительная высота hм=35
Предельные отклонения осевого шага ΔвtΔнt=+_0014
Предельная накопленная погрешность осевого шага ΔвtΣΔнtΣ =+-0025
Допуск на профиль червяка f=0022
Допуск на радиальное биение витков червяка Ев= 0018
Делительный диаметр червяка d=42
3. Выбор методов достижения точности.
Рассчитаем размерные цепи А и g0 для цепи выберем А-метод регулирования для цепи g-метод неполной взаимозаменяемости.
Изобразим эскиз узла(рис.3.3.1.)и составим схему размерных цепей(рис.3.3.2.) для каждой цепи составим таблицу расчетов(Табл.3.3.1.)
Для цепи А задачей является нахождение компенсаторас помощью метода регулирования для цепи g задачей является задача выдержать угол между осями вращения червяка и червячного колеса в 90 градусов.
Рис.3.3.1.Эскиз узла.
Рис.3.3.2. Схема размерной цепи
Рассмотрим размерную цепь γ.
Примем радиальное биение всех подшипников 0025мм тогда
γ1=-+0013100ммммм; х1=0025100мммм
где 100-расстояние между подшипниками вала червячного колеса
γ4=-+0013190мммм; х1=0025190
где 190-расстояние между подшипниками вала червяка.
Для приведения допускаемых отклонений к одной базовой длине которую примем 200 мм необходимо вычислить передаточное отношение для всех составляющих звеньев.
Допуск и предельные отклонения на размер звена γ3 определяется из следующего уравнения
Примем К3=12 Кхi=0.6 тогда
Полученные значения сводим в таблицу 3.3.1.
Рассмотрим размерную цепь А.
Проверим правильность номинальных значений составляющих звеньев:
Пусть Кi=12 в формуле погрешности замыкающего звена
Примем точность метода компенсации 004мм
Величина компенсации погрешности замыкающего звена
Определим погрешность координаты середины поля допуска замыкающего звена.
Величина компенсации координаты середины рассеяния погрешности замыкающего звена
Предельные значения величины необходимой компенсации погрешности замыкающего звена.
Чтобы исключить Δнк0 изменим координату середины поля допуска звена А5на величину Δнк
Новые предельные отклонения размера А5
Толщину одной прокладки принимаем равной
Тогда число прокладок будет
Звено размерной цепи
Угол между осями вращения червяка и чер.колеса
смещение и поворот оси вала червячного колеса
вследствии радиального биения подшипников
откл.от прямого угла между осями отв.в корпусе
смещение и поворот оси червяка вследствии
радиального биения подшипников
Расстояние между прокладками крышек
Расстояние между торцами крышки и подшипника
Монтажная высота подшипника
Расстояние между втулками
4.Анализ технологичности.
Определим соответствие качественной оценки конструкции редуктора согласно рекомендациям (12) ГОСТ 1883-73”Технологичность конструкций” ГОСТ14202-73 ГОСТ14204-73.
Сборочный чертеж расчленяется на рациональное число составных частей предусматривается возможность сборки обособлено подузлов редуктора-это является одним из основных условий технологичности изделия. Конструкцией редуктора предусмотрена возможность применения стандартных и унифицированных сборочных единиц без применения сложной технологической оснастки. Примером могут быть подшипники элементы резьбовых соединений шпоночных соединений и т.д.
Виды используемых соединений их конструктивные особенности и место расположения отвечают требованиям механизации.
Учтена возможность механизации и автоматизации сборочных работ т.е. например у ступенчатого вала обеспечен удобный подвод механизированного инструмента для напрессовки подшипников.
Конструкцией сборочного узла предусмотрена базовая составная часть-корпус являющаяся основной для размещения остальных составляющих частей.
Базовая составная часть является удобной для правильной установки на рабочем месте в приспособлении и т.д. Конструкцией предусмотрено использовать конструктивных сборочных баз в качестве технологических и измерительных.
Конструкцией предусмотрена регулировка червячного зацепления при установке вала.
Точность расположения составных частей обуславливается точностью их изготовления.
Регулируемые компенсаторы имеют простую конструкцию свободный доступ для рабочего и контролируемого инструмента при сборке.
Вывод конструкция редуктора технологична.
5.Методы и схемы контроля.
Все основные методы контроля осуществляются в процессе изготовления деталей (сборочных единиц) и в процессе сборки редуктора.
У редуктора в сборке контролируют осевые люфты валов:
входного-005 010мм выходного -008 015мм и провести испытание под нагрузкой для выявления отсутствия повышенного шума подтекания
масла чрезмерного нагрева подшипников и масла.
В процессе сборки для обеспечения нормальной работы червячной передачи необходимы в первую очередь: правильное расположение и форма суммарного пятна контакта червячной передачи.
Правильность суммарного пятна контакта червячной передачи проверяем по краске на контрольно-обкатных станках после вращения собираемой передачи под нагрузкой(Рис.3.5.1.). Относительные размеры суммарного пятна контакта определяются в процентах. Для редуктора имеющего 8 ст. точности краска должна перекрывать поверхность зуба червячного колеса не менее чем на 50% по длине и высоте. Норма плавности работы червячного колеса ±0022мм проверяем шагомером; погрешность профиля зубьев колеса 0018мм производим на специальных приборах (ГОСТ 3675-81).
Опорные детали передачи: подшипники стаканы не должны иметь смещения и перекосов осей.
Оси основных отверстий в корпусе должны лежать в одной плоскости пересекаться в одной определенной точке под требуемым углом. Это требование обеспечивает нормальное зацепление червячной передачи но осуществляется и контролируется в процессе изготовления корпусной детали.
Рис.3.5.1.Суммарное пятно контакта
6. Разработка последовательности сборки.
Последовательность сборки изобразим в виде технологической схемы см.(рис3.6.1.).
7. Проектирование технологических операций
Используя технологическую схему сборки редуктора проведем нормирование сборочных переходов. Нормативы времени сборки редуктора принимаем по ( 4 стр. 12-48). Полученные данные сводим в таблицу 3.6.1.
Установить червяк в приспособление
Распокавать подшипник
Напрессовать подшипник
Открепить и снять червяк в сборе
Уложить червяк в тару
Установить вал в приспособление
Промыть червячное колесо
Продуть червячное колесо
Напрессовать червячное колесо
Установить вал с другой стороны
Открепить и снять вал в сборе
Протереть посадочные поверхности
Установить корпус в приспособление
Напрессовать в корпус червяк в сборе
Проверить легкость вращения
Напрессовать манжету
Установить прокладку
Установить крышку в сборе
Надеть шайбы на болты
Ввернуть предварительно болты
Ввернуть окончательно болты
Напрессовать вал в сборе
Открепить и снять редуктор в сборе
Уложить редуктор в тару
Итого на сборку редуктора
Определим штучное время по формуле (из 4) для каждой из характерной операции указанной в технологической схеме сборки.
где =0- время технического обслуживания
=2 6%-время организационного обслуживания
γ=4 6%-время перерывов на отдых
Для операции сборка редуктора
8. Расчет числа единиц оборудования оборудованья рабочих мест и состава работающих.
Число единиц оборудования определим по (4стр.79)
где Тшт- трудоемкость сборки одного изделия
N- годовая программа выпуска
Фд- действительный годовой фонд времени оборудования
Принимаем число единиц оборудования- 1.
Число рабочих мест для узловой и общей сборки определим по
где Фд- действительный годовой фонд времени рабочих
П- средняя плотность работы
Принимаем число рабочих –1 на одну операцию сборки редуктора.
9. Планировка участка сборки.
Планировку участка сборки произведем в соответствии с выбранной организацией производства.
Рис.3.9.1. Планировка участка сборки.
-испытательный стенд
- путь перемещения изделия
Разработка технологического процесса изготовления специальной детали.
1. Анализ служебного назначения и технических условий.
Корпус редуктора является базовой деталью на которую монтируют отдельные сборочные единицы и детали такие как вал и червяк обеспечивая требуемую точность относительного расположения между собой.
Корпусная деталь должна иметь требуемую точность обладать необходимой жесткостью и виброустойчивостью что обеспечивает требуемое относительное положение соединяемых деталей и узлов правильность работы передачи и отсутствие вибраций.
Корпус редуктора должен обеспечивать точность относительного положения червяка и червячного колеса.
Базирование валов осуществляется по главным отверстиям. Поверхности главных отверстий корпуса совместно с поверхностями торцов образуют комплекты вспомогательных баз корпуса.
Технические требования можно определить по:
Точность относительного положения вспомогательных конструкторских баз
- требования определяющие точность положения осей основных отверстий относительно торцов отсутствуют
Точность относительного положения вспомогательных конструкционных баз отсутствуют
Точность основных отверстий :
-диаметральных размеров
Отверстий под опоры червяка
-отверстий под опоры вала червячного колеса
-геометрической формы не заданы
-Параметры шероховатости
Точность геометрической формы и качества плоских поверхностей
Параметры шероховатости:
Плоскость основании
Торцы основных отверстий
Неуказанные предельные отклонения размеров:
2. Анализ технологичности.
Оценка уровня технологичности устанавливает на сколько полно учтены технологические требования и отвечает ли изделие требованиям рациональной организации производства.
Конструкция должна удовлетворять два основных условия:
-выполнение служебного назначения
-обеспечить возможность применения высокопроизводительных методов обработки детали
Материал для корпуса редуктора Ст.3 обладает невысокой стоимостью. Способ изготовления –сварка.
При этом надо обратить особое внимание на обеспечение перпендикулярности оси отверстия f 100 к оси отверстия f 52.
Корпусная деталь имеет удобную технологическую базу- основание позволяющее использовать не только в процессе обработки но и в процессе контроля как измерительную.
Снижению трудоемкости способствует наличие отверстий в противоположных сторонах корпуса. Это позволяет использовать высокопроизводительное оборудование для расточки отверстий без переустановки корпуса одновременно с двух сторон.
При этом виде получения заготовок точность формы шероховатость не обработанных поверхностей достигается Rz 20.
Вывод корпус редуктора технологичен.
3.Методы и схемы контроля.
Контроль корпусных деталей производится при выполнении наиболее ответственных операции технологического процесса и после обработки.
Контроль выполняем с помощью универсальных измерительных средств.
Точность размеров относительных поворотов и геометрической формы плоских поверхностей и отверстий контролируем с помощью линеек угольников индикаторов.
При контроле учитываем что допускается погрешность контролируемого параметра не должна превышать 10-20% его поля допуска.
Контроль отклонения от перпендикулярности торцевой плоскости к оси отверстия ф100 проверяем с помощью индикаторов установленных на вала. Отклонение определим по показаниям индикаторов 12.
Рис.4.3.1. Контроль перпендикулярности торцевой плоскости к оси отверстия.
Проверку межосевого расстояния червяка и колеса 125±0055 проводим с помощью оправки 1 и оправки 2. Вставляем оправку 1 на место червяка а оправку 2 в отверстие ф100 устанавливаем между ними измерительное устройство с помощью которого контролируем расстояние между ними.
Рис.4.3.2. Контроль межосевого расстояния.
4. Выбор экономического варианта получения исходной заготовки.
Исходя из того что у нас единичное производство и сварной корпус редуктора экономически нецелесообразно принимать способ получения заготовки литьем т.к. это требует дополнительных затрат на изготовление и формирование форм для литья предназначенных для серийного производства. Приходим к выводу что необходимо применить способ получения заготовки сваркой. Сварка ручная электродуговая. Марка электрода УОНИИ 1355 ГОСТ 9466-75.
5.Обоснование выбора технологических баз и разработка последовательности изготовления.
В качестве технологической базы выбираем поверхность которая связана размерами с наибольшим числом других поверхностей. Далее базируя по этой поверхности растачиваем отверстие f 52 растачиваем фаску фрезеруем отверстия ф90 ф115 обрабатывая при этом торец. Фрезеруем отверстие ф130 и торец одновременно фрезеруем отверстие ф90 с другой стороны. Разворачиваем заготовку на столе на 90 градусов и растачиваем отверстие ф100 и фаски с двух сторон. Фрезеруем отверстие растачиваем отв. Ф225 растачиваем фаску фрезеруем торец.
Определяем число необходимых переходов.
Для определения числа переходов необходимо определить уточнения для каждой операции:
Растачивание отверстия f 52
Величина уточнения и количество переходов регламентируется значением шероховатости.
Необходимо 2 перехода – черновое и чистовое растачивание.
Растачивание фаску(1*45) одновременно с двух сторон
Черновое растачивание
Фрезеруем фасонной фрезой ф90ф115 и торец с двух сторон
Фрезеруем ф130и торец одновременно
-черновая -чистовая
количество переходов 2черновое и чистовое фрезерование
При обработке отверстий под резьбу необходимая точность обработки достигается за один переход и шероховатость за два: черновое и чистовое растачивание.
Таким же образом определяем переходы и для отверстий ф100 ф225
Рисунок 4.5-Эскиз наладки на расточной операции
А – разность оси отверстия в заготовке и оси борштанги
– погрешность звена определяется схемой базирования на первой операции когда обрабатывается технологическая база.
– погрешность звена определяется точностью обработки на расточном станке.
6. Определение припусков и межоперационных размеров.
Расчет выполним исходя из (5.стр.175-193)
Рассчитаем припуски на обработку и промежуточные предельные размеры для отверстия корпуса ф52Н7. Расчет припусков сведем в таблицу 4.6.1.в которой последовательно записываем технологический маршрут обработки отверстия состоящий из двух переходов: чернового и чистового . Для отверстия ведем расчет по формуле :
Находим по справочнику (Т1стр.180) значения Rz:
для чернового растачивания Rz=40мкм
для чистового растачивания Rz=20мкм.
Суммарное значение пространственных отклонений для заготовки данного типа:
Коробление отверстия rкор следует учитывать как в диаметральном так и в осевом его сечении следовательно:
где D-удельная кривизна заготовки
d и l- диаметр и длина обрабатываемого отверстия.
Произведем расчет минимальных значений припусков используя основную формулу:
В графе Предельный размер наибольшие значения получается по расчетным размерам округленным до точности допуска соответствующего перехода. Наименьшие предельные размеры определяются из наибольших предельных размеров вычитанием допусков соответствующих переходов.
Минимальные предельные значения припусков равны разности наибольших предельных размеров выполняемого и предшествующего переходов а максимальные значения соответственно разности наименьших предельных размеров.
Результаты расчетов сводим в таблицу 4.6.1.
Таблица 4.6.1.-Расчетная карта.
Аналогично делаем расчет для отверстия ф130Н7 и сводим в таблицу 4.6.2.
Таблица 4.6.2.-Расчетная карта.
8. Проектирование технологических операций.
Уточним намеченные ранее структуру и содержание операций технологическое оснащение. Назначим режимы резания и выполним техническое нормирование.
8.1. Структура и содержание операций.
005-Расточная станок 2м615 горизонтально-расточной
Расточить 2 отверстия ф52 с двух сторон на длину 40
Растачиваем фаску с двух сторон
Черновая и чистовая обработка
Инструмент –резец ГОСТ18883-73
010-Фрезерная станок 2м615 горизонтально-расточной
Фрезеруем 2отверстия ф90с двух сторонф115 и торец одновременно
Фрезеруем отверстие ф130 и торец одновременно
015-Расточная станок 2м615 горизонтально-расточной
Расточить отверстие ф100 на длину 30
Фрезеруем фасонной фрезой
020-Расточная станок 2м615 горизонтально-расточной
Растачиваем отверстие ф225
Инструмент –резец ГОСТ 18883-73
Фрезеруем торец с двух сторон
Инструмент –торцевая фреза
025-Сверление станок 2М55
Сверлить 12 отверстий М10-7Н
Инструмент- сверло ГОСТ 6647-68-9-ВК8
Инструмент –метчик ГОСТ3266-71
8.2. Режимы резания.
Рассчитаем режимы резания для чернового фрезерования торца отверстия.
Ширина фрезерования В=275
Глубина резанья t=15
Подачу на один зуб фрезы выбираем по таблицам ( с.283) Sz=0.25
Число зубьев фрезы z=18
Найдем скорость резанья:
для наших условий обработки:
Период стойкости режущей части инструмента:
Тогда численно получим:
Частота вращения шпинделя тогда составит:
Усилие возникающее в процессе обработки определим по формуле:
по условиям обработки
Подставив в формулу получим:
Мощность потребляемая на резание в этом случае составит:
Составим таблицу режимов резания
Таблица 4.8.2.1.-Режимы резания
Наименование перехода
Расточить 2 отверстия
Фрезеруем 2 отверстия
Расточить отверстие
8.3. Техническое нормирование.
Назначим технические нормы времени для операции 025.
Операция –сверление отверстия.
Найдем норму штучного времени по зависимости:
tшт. оп.= t0 + tв+ tобс.+ tотд
t0 – основное время автоматической работы станка по программе мин;
tв- вспомогательное время мин;
tобс.- время на организацию и техническое обслуживание рабочего места мин;
tотд – время на личные потребности отдых мин.
Определим время цикла автоматической работы станка при растачивании поверхности:
где n-число оборотов шпинделя
L-длина рабочего хода
L=10мм; S=0.1мм n=2242обмин
Определив все составляющие основного времени найдем его :
Поскольку в операции обрабатывается 12 отверстий то и основное время увеличивается в 12 раз т.е.
Определяем вспомогательное время по формуле :
tвсп. = Туст. + Тв.оп.. +Тиз.
Т уст. =011 мин; - время на установку и снятие детали
Тв.оп. =0052мин; - на операцию
Тиз = 014 мин. - на контрольные измерения
Тогда вспомогательное время по формуле (4.29):
tв = 011 + 0052 + 014 = 0302мин.
Время на организационное и техническое обслуживание рабочего места отдых и личные потребности зависят от типа и характеристики станка принимаем (tобс.+ tотд) 9% от оперативного времени (t0 + tв):
(tобс.+ tотд) = 009×(048 + 0302) =007мин.
Норму штучного времени на операцию находим по формуле:
tшт. оп.= 048 + 0302 + 007 = 0852 мин.
9 Анализ и расчет точности обработки
Анализ технологических решений:
Таблица 4.5-Анализ технологического решения.
Наименование перехода (операция)
Требование к точности изготовления
Методы достижения точности
б) шероховатость Rz40
Фрезерование черновое.
Режимы чистовой обработки: S=02 ммзуб;
Режущий инструмент – торцевая фреза с пластинами из твердого сплава.
Суммарная погрешность обработки:
- погрешность установки заготовок в приспособление;
-погрешность возникающая в результате упругих деформаций системы;
- погрешность наладки технологической системы на размер;
- погрешность измерения;
- погрешность обработки возникающая в следствии геометрических неточностей;
-погрешность обработки вызванная температурными деформациями;
Определим погрешность установки:
=0046мм-погрешность базирования
=012мм-погрешность закрепления
=0288мм-погрешность приспособления
Погрешность обработки определим по формуле
W-податливость системы
Погрешность обработки вызванная температурными деформациями определим по формуле:
Так как d (039204) то принятая схема базирования обеспечивает заданную точность обработки.
Расчет и конструирование специального приспособления
1. Техническое задание.
Необходимо спроектировать приспособление:
)для фрезерования торца отверстия в корпусе редуктора
)для горизонтально- расточного станка 2М615. Размеры станка 9001000
)инструмент торцевая фреза ГОСТ 24359-80 D=200 z=12 со вставными ножами оснащенными пластинами из твердого сплава.
)схема базирования по призме и плоскости
2. Выбор и обоснование схемы базирования
Принимаем решение: на приспособление для обеспечения быстродействия зажима заготовки устанавливаем круглый стандартный эксцентрик простой и надежный в эксплуатации. Зажим осуществляется вручную рукояткой эксцентрика. Ручной привод приспособления принимаем в следствии единичного производства.
На основании принятой схемы базирования разрабатываем конструкцию и размеры установочного элемента.
С учетом направления сил резания выбираем зажимное устройство в виде Г -образного прихвата и разрабатываем общую схему приспособления.
Рисунок 5.1 – Схема приспособления.
Приспособление состоит из:
3 Расчет параметров силового привода.
Расчет силы зажима производим исходя из уравнений равновесия обрабатываемой заготовки под действием приложенных к ней внешних сил.
Рисунок 5.2 – схема действия сил
Зажимной механизм предотвращает перемещение заготовки относительно призмы. Силу закрепления Р определим из условия равновесия силовых факторов действующих на заготовку. Для расчета принята схема действия сил на рисунке 5.2.
- коэффициент запаса
-коэффициент трения
Найдем диаметр шпильки
Найдем осевую силу Q для Г –образного прихвата
Для достижения необходимой осевой силы Q с помощью затягивающей гайки необходимый момент составит:
-средний диаметр резьбы
-угол наклона резьбы
4 Расчет точности приспособления.
Рассчитаем точность приспособления по формуле:
=03мм-допуск выполняемый при обработке размера заготовки.
=1-12-коэффициент учитывающий отклонение рассеяния значений составляющих величин от закона нормального распределения.
=08-085-коэффициент учитывающий уменьшение предельного значения погрешности базирования при работе на настроенных станках
=06-08-коэффициент учитывающий долю погрешности обработки в суммарной погрешности вызываемой факторами не зависящими от приспособления.
=46мкм-погрешность базирования
=120мкм-погрешность закрепления
=129мкм-погрешность установки
=60мкм-погрешность положения заготовки возникающая в результате изнашивания элементов приспособления
=54мкм-погрешность измерения
=250мкм-экономическая точность обработки
Список используемой литературы:
Проектирование машиностроительных заводов и цехов. Справочник в 6- ти томах. Том 4. Под редакцией З.И.Соловья –М.: Машиностроение.1974.
Авраменко В.Е.Технология машиностроения. Методические указания к проектированию технологических процессов сборки в курсовых и дипломных проектах. КГТУ -Красноярск 1995.
Гусев А.А. Ковальчук Е.Р. Колесов И.М. и др. Технология машиностроения. – М.: 1986.
ТМС.Метод.указания по курсовому и дипломному пректированию
Справочник технолога машиностроителя.В2-х томах под ред. Косиловой и Мещерякова 1985г.
Ансеров М.А. Приспособления для металлорежущих станков. –Л: Машинострое 1975
Горошкин А.К. Приспособления для металлорежущих станков. –Справочник – М: 1979.
Основы технологии машиностроения. Под редакцией В. С. Корсакова. Изд.3-е.-М.:
Косилова А.Г.Мещеряков Р.К. Точность обработки заготовки и припуски в машиностроении. –М.:Машиностроение.1976.
ГороховВ.А.Проектирование и расчет приспособлений ВШ1986г.
Режимы резания металлов справочник под ред.БарановскогоМ1972
Технологичность конструкций машин.М:Машиностроение1987-337
Проектирование механосборочных цехов Г.Н.Мельников
М- .Машиностроение 1990
СБ редуктор.cdw

Спецификация_5.11R03.spw

Колесо зубчатое малое
Колесо зубчатое большое
Крышка глухая средняя
Крышка глухая большая
Кольцо маслоотбойное
Крышка сквозная малая
Болт М12 х 14 ГОСТ 15589-70
Болт М8 х 18 ГОСТ 15589-70
Болт М12 х 150 ГОСТ 15589-70
Болт М12 х 45 ГОСТ 15589-70
Гайка М12 ГОСТ 15526-70
Гайка М18 ГОСТ 5929-70
Подшипник 206 ГОСТ 2893-82
Подшипник 209 ГОСТ 2893-82
Подшипник 211 ГОСТ 2893-82
Шайба 12 Н ГОСТ 6402-70
Штифт 8 х 36 ГОСТ 3129-70
Заклепка 5 х 10 ГОСТ 10299-80
Шпонка 20 х 12 х 56 ГОСТ 23360-78
Шпонка 16 х 10 х 45 ГОСТ 23360-78
Шпонка 12 х 8 х 50 ГОСТ 23360-78
Шпонка 8 х 7 х 32 ГОСТ 23360-78
Шайба 18 ГОСТ 11371-78