Разработка зажимного приспособления




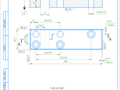
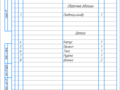
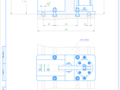
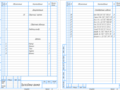
- Добавлен: 25.01.2023
- Размер: 484 KB
- Закачек: 0
Описание
Состав проекта
![]() |
![]() |
![]() ![]() ![]() ![]() |
![]() ![]() ![]() ![]() |
![]() ![]() ![]() |
![]() ![]() ![]() ![]() |
![]() ![]() ![]() ![]() |
![]() ![]() ![]() ![]() |
![]() |
![]() ![]() ![]() ![]() |
Дополнительная информация
Разм_ан.cdw

Зажимное_приспособление.cdw

Корпус.cdw

Приспособление_зажимное.spw

Спецификация.frw

Разм_ан2.cdw
