Разработка управляющей программы для изготовления детали Пуансон




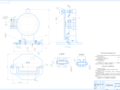
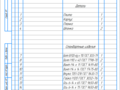
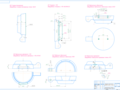
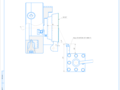
- Добавлен: 25.01.2023
- Размер: 2 MB
- Закачек: 0
Описание
Разработка управляющей программы для изготовления детали Пуансон
Состав проекта
![]() |
![]() ![]() ![]() ![]() |
![]() ![]() ![]() ![]() |
![]() ![]() ![]() ![]() |
![]() ![]() ![]() |
![]() ![]() ![]() ![]() |
![]() ![]() ![]() |
![]() ![]() ![]() |
![]() ![]() ![]() ![]() |
![]() ![]() ![]() ![]() |
Дополнительная информация
_Д_ТП проектный_.cdw

_Д_Кондуктор_.cdw

_Д_отливка_.cdw

_Д_Наладки 3 шт_.cdw

_Д_пуансон_.cdw

СП_Кондуктор.spw

Рекомендуемые чертежи
- 25.01.2023
- 24.01.2023
- 24.01.2023