Разработка технологического процесса изготовления торцевой фрезы




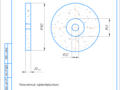
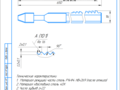

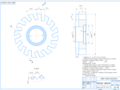
- Добавлен: 24.01.2023
- Размер: 761 KB
- Закачек: 0
Описание
Состав проекта
![]() |
![]() ![]() ![]() |
![]() ![]() ![]() |
![]() |
![]() ![]() ![]() ![]() |
![]() ![]() ![]() |
![]() ![]() ![]() ![]() |
![]() ![]() ![]() ![]() |
![]() ![]() ![]() ![]() |
![]() ![]() ![]() ![]() |
![]() ![]() ![]() ![]() |
![]() ![]() ![]() ![]() |
![]() ![]() ![]() ![]() |
![]() ![]() ![]() ![]() |
![]() ![]() ![]() ![]() |
![]() ![]() ![]() ![]() |
![]() ![]() ![]() ![]() |
![]() ![]() ![]() ![]() |
![]() |
![]() ![]() ![]() ![]() |
![]() ![]() ![]() ![]() |
![]() ![]() ![]() ![]() |
![]() ![]() ![]() ![]() |
![]() ![]() ![]() ![]() |
![]() ![]() ![]() ![]() |
![]() ![]() ![]() ![]() |
![]() ![]() ![]() |
![]() ![]() ![]() |
Дополнительная информация
тит.docx
Государственного образовательного учреждения высшего профессионального образования
«Владимирский государственный университет
имени Александра Григорьевича и Николая Григорьевича Столетовых»
по Технологии инструментального производства (наименование дисциплины)
ТемаРазработка технологического процесса изготовления “Фрезы со вставными ножами оснащенными пластинами из твердого сплава.”
СтудентМИ-108 (группа)
закл.doc
В данном курсовом проекте мы достигли:
оптимизации и интенсификации режимов резания благодаря более высокой жесткости и виброустойчивости станков возможности быстрой смены режущего инструмента.
Сокращение затрат времени на установочные перемещения холостые ходы благодаря полной автоматизации цикла
Сокращение затрат времени на установку закрепление снятие и транспортирование обрабатываемых деталей от станка к станку вследствие концентрации операций
Сокращение затрат времени на пробные проходы и наладку станка вследствие уменьшения количества инструментов и их настройки на размер вне станка.
Список использованной литературы
Ковшов А.Н. Технология машиностроения: учебник для вузов. – М.: Машиностроение 1987г.
Курсовое проектирование по технологии машиностроения:Учеб. пособие А.В.Киричек Ю.Н.Киричек. Владим. Гос. техн. Ун-т; Влидимир 1997г.
Станки с числовым программным управлениемПод ред. В.А.Лещенко. – М.:Машиностроение 1988г.
Шевляков И.М. Расширение технологических возможностей станков с ЧПУ. – К.: Техника 1989г.
Нормирование операций выполняемых на станках с ЧПУ А.В.Киричек Ю.Н.Киричек. Владим. Гос. техн. Ун-т; Влидимир 1995г
Металлорежущие станки: Учеб. пособие Л.Г. Никитина А.В. Волченков
А.Г. Лазуткин; Муром 2006г.
Справочник технолога-машиностроителя: В 2т.Под ред. А.Г.Косиловой и Р.К.Мещерякова. – М.: Машиностроение 1985.-Т1
Справочник технолога-машиностроителя: В 2т.Под ред. А.Г.Косиловой и Р.К.Мещерякова. – М.: Машиностроение 1985.-Т2
Шероховатость поверхности ГОСТ 2789-73 ГОСТ 2.309-73. – М.:ГКС
Ревин С.А. «Методические указания по проектированию технологических процессов механической обработки деталей машин» Москва 1979г
Технология конструкционных материалов. Учебник для вузов. – М.: Машиностроение 1977 г.
Технологические процессы обработки резанием. Правило оформления: Учеб. пособие А.В. Киричек Ю.Н.Киричек. м 1997г.
Справочник инструментальщика: Под. ред. В. И. Гузеев В. А. Батуев.
А.В.Сорокина «Марочник сталей и сплавов»
55 прот налад.cdw

тп.docx
Сталь 40Х ГОСТ 4543-71
Код наименование операции
Обозначение документа
Код наименование оборудования
Токарно-винторезый станок 16К20
Вертикально-фрезерная
Вертикально-фрезерный станок 6Т12
Горизонтально-фрезерная
Горизоньально-фрезерный станок 6Р80
ГОСТ 3.1118-82 Форма 1а
Наименование детали сб. единицы или материала
Шнутришлифовальный станок 3К227А
Специально-шлифовальный станок 32Б40
Плоскошлифовальный станок 3Г71
Горизонтально-протяжной станок 7Б55
Технический контроль
Установить закрепить заготовку снять после обработки
Приспособление патрон 3-х кулачковый
Резец подрезной Т15К6 ГОСТ18877-73 Штангенциркуль ШЦ–V–400–010 ГОСТ 166 -73
Резец расточной ГОСТ18882-73 Штангенциркуль ШЦ–V–400–010 ГОСТ 166 -73
Точить канавку 6 и фаску
Резец специальный шаблон
Контроль: исполнителю 100% мастеру и ОТК выборочно 15% от партии
Резец проходной ГОСТ18869-73 штангенциркуль ШЦ–V–400–010 ГОСТ 166 -73
Резец фасочный ГОСТ18869-73 штангенциркуль ШЦ––125–010 ГОСТ 166 -73
Приспособление зажимы упоры накладки
Фреза шпоночная 20 мм ГОСТ 9140-78 штангенциркуль ШЦ––125–010 ГОСТ 166 -73
Горизонтально-фрезерный 6Р80
Приспособление специальное
Фреза дисковая D=125 мм В=20 мм z=22 d=32 мм ГОСТ9474-73 штангенциркуль ШЦ––125–010 ГОСТ 166 -73
ГОСТ 3.1502-85 Форма 2
Наименование операции
Наименование марка материала
Наименование оборудования
Контролируемые параметры
Наименование средств ТО
Внешним осмотром проверить отсутствие заусенцев наличие фасок и скруглений
Проверить шероховатость обработанных
Образцы шероховатости ГОСТ 9378-93
Проверить размер 1 3 4 5 6 7 8 9
Штангенциркуль ШЦ–V–400–010
Калибр пробка 50H7 ГОСТ 17758-72
Внутришлифовальный станок 3К227А
Установить закрепить заготовку снять после обработки
Приспособление патрон поводковый
Шлифовать поверхность 1
Круг шлифовальный ПП 25А25GCV26R5F60 ГОСТ 17123-79 Калибр пробка 50H7 образцы шероховатости ГОСТ166-89
Круг специальный шаблон образцы шероховатости ГОСТ166-89
Приспособление станка
Протянуть поверхность 1
Протяжка специальная шаблон
Круг шлифовальный 100А25GCV26R5F60 ГОСТ 17123-79 образцы шероховатости ГОСТ 166-89
40 шлиф. пазов налад.cdw

35 внутришлиф налад.cdw

05 токар налад.cdw

10 токар налад.cdw

титульник техпроцесса.cdw

45 Плоскошлиф.cdw

60 контр налад 1.cdw

15 верт фрез налад.cdw

20 гор фрез налад.cdw

спец инструмент.cdw

Материал режущей части сталь Р14Ф4 HB=269 (после отжига)
Материал хвостовика сталь 40Х
МИВУ 151003-00.000.00 КП
Протяжка специальная
спец инструмент2.cdw

Зернистость Связка Концентрация Скорость
R4 АС6М 10080 B48 75 35
МИВУ 151003-00.000.00 КП
Круг специальный эльборовый на органической связке
R4 150х20х45х22 АС6М 10080 B48 75 35
спец инструмент3.cdw

Материал твердосплавной пластины Т15К6
Материал державки сталь 45
МИВУ 151003-00.000.00 КП
Резец специальный расточной с пластиной сложного профиля
заготовка.cdw

МИВУ 151003-00.000.00
*- Размеры для справок.
Точность изготовления - класс II
степень сложности С2
стали М1 ГОСТ 7505-89
Неуказанные радиусы скруглений: наружные R=6 мм.
Штамповочные уклоны 5
Смешение половинок штампа 0
Чертеж фрезы насадной.cdw

Радиальное биение режущих кромок относительно оси отв.при
базировании на опорный торец не более: -2-ух
Торцовое биение режущих кромок относительно оси отв.при
базировании на опорный торец не более: -0
Разность расстояния от торцовых режущих кромок до торца
ступицы фрезы не более 0
Конусность по наружному диаметру на длине режущих кромок
* Размеры для справок.
Сталь 40Х ГОСТ 4543-71
МИВУ 151003-00.000.00
002-1 А2 Чертеж операционн гор фрез.cdw

Оборудование: Горизонтально-фрезерный станок 6Р80
МИВУ 151003-00.000.00
Переход 2. Фрезеровать 16 пазов 1
003-2 А2 Чертеж операционн шлифование пазов.cdw

Операция 40 Шлифовальная. Оборудование: Специально-шлифовальный станок 32Б40
Переход 2. Шлифовать отв. 1
002-1 А2 Чертеж операционн внутришлифование.cdw

Операция 35 Внутришлифовальная. Оборудование: Внутришлифовальный станок 3К227А
Переход 2. Шлифовать отв. 1
003-2 А2 Чертеж операционн горизонтально-прот.cdw

Оборудование: Горизонтально-протяжной станок 7Б55
МИВУ 151003-00.000.00
Переход 1. Протянуть пов. 1
001 А1 Чертеж операционн точение.cdw

Операция 05 Токарно-винторезная. Оборудование: Токарно-виторезный станок 16К20
Содержание.doc
1 Определение программы выпуска инструмента . 7
2 Определение типа производства . .8
3 Анализ технологичности детали .. 9
4 Выбор заготовки и метода её изготовления . 11
5 Разработка маршрутного технологического процесса изготовления
инструмента «Фреза» .. 12
6 Выбор методов обработки поверхностей заготовки и выбор
7 Выбор методов и средств технического контроля
качества инструмента . 16
8 Разработка технологических операций и операционного
технологического процесса
8.1 Назначение межпереходных припусков и размеров .. .17
8.2 Расчёт режимов резания норм времени . ..24
9 Разработка технического задания .. 32
Список литературы 34
Оформление технологической документации
записка ....doc
Разработка технологических процессов производства металлорежущего инструмента базируется на общих принципах и закономерностях технологии машиностроения.
Металлорежущий инструмент является одним из важнейших орудий производства. Он используется при обработке резанием всевозможных деталей на металлорежущих станках. При этом срезается часть материала заготовки в виде стружки до получения требуемой поверхности детали.
Одним из эффективных путей повышения производительности труда в машиностроении является применение новых инструментальных материалов. Например применение быстрорежущей стали вместо углеродистой инструментальной позволило увеличить скорость резания в 2 3 раза. К сталям нормальной производительности относятся Р18 Р12 Р9 Р6МЗ Р6М5 к сталям повышенной производительности – Р6М5ФЗ Р12ФЗ Р18Ф2К5 Р10Ф5К5 Р9К5 Р9К10 Р9МЧК8 Р6М5К5 и др. Высокие режущие свойства быстрорежущей стали обеспечиваются за счет легирования сильными карбидообразующими элементами: вольфрамом молибденом ванадием и некарбидообразующим кобальтом.
В настоящее время для производства режущих инструментов широко используются твердые сплавы. Они состоят из карбидов вольфрама титана тантала сцементированных небольшим количеством кобальта. Карбиды вольфрама титана и тантала обладают высокой твердостью износостойкостью. Инструменты оснащенные твердым сплавом хорошо сопротивляются истиранию сходящей стружкой и материалом заготовки и не теряют своих режущих свойств при температуре нагрева до 750-1100 °С.
В данном курсовом проекте нужно разработать оптимизированный под данный тип производства технологический процесс обработки детали «Фреза со вставными ножами оснащенными пластинами из твердого сплава».
Тщательно рассмотреть эффективность данного технологического процесса экономическую выгоду и себестоимость.
В курсовом проекте нужно достигнуть:
оптимизации и интенсификации режимов резания благодаря более высокой жесткости и виброустойчивости станков возможности быстрой смены режущего инструмента.
Сокращение затрат времени на установочные перемещения холостые ходы благодаря полной автоматизации цикла
Сокращение затрат времени на установку закрепление снятие и транспортирование обрабатываемых деталей от станка к станку вследствие концентрации операций
Сокращение затрат времени на пробные проходы и наладку станка вследствие уменьшения количества инструментов и их настройки на размер вне станка.
Технологическая часть
1Определение программы выпуска инструмента
Деталь “Торцевая фреза ” является одной из распространенных номенклатурных частей режущего инструмента. Торцовые насадные фрезы предназначены для обработки открытых плоских поверхностей стальных или чугунных деталей. Ножи фрез оснащаются пластинами из двердого сплава Т5К10 для обработки стали и ВК8 для обработки чугуна. Большое количество режущих зубьев обеспечивает плавную работу фрезы и высокую частоту обработанной поверхности.
Крепление ножей в клиновом пазу с рифлениями создает возможность компенсировать износ ножей по торцам и окружности за счет перемещения их на одно рифление от оси фрезы. После перемещения ножей фреза шлифуется затачивается режущие поверхности ножей доводится алмазом. При полном использовании ножей из заменяют новым комплектом. Корпус фрезы позволяет производить многократную замену ножей. Вреза крепится на оправках торцовыми шпонками.
Ежегодный выпуск превышает свыше миллиона единиц. Корпус фрезы изготавливается из Стали 40Х
2 Свойства Стали 40Х ГОСТ4543-71
Таблица 1.1 – Химические свойства % [9стр.154]
Таблица1.2 – Механические свойства [9]
Технологические свойства:
свариваемость – трудносвариваемая;
флокеночувствительность - чувствительна
2 Определение типа производства
В последнее время на предприятиях экономические составляющие являются его главными характеристиками. Экономические составляющие предприятия зависят от множества причин но одной из причин следует отметить правильный выбор типа производства. От правильности этого выбора зависит: составление технологического процесса выбор оборудования и т.д.
Предварительно тип производства определяется по известному годовому объёму выпуска и массе детали (табл. 2).
Окончательное определение типа производства осуществляется после разработки технологического процесса и расчёта количества рабочих мест по ГОСТ 3.1121-84 коэффициентом закрепления операций
где О – число различных операций выполняемых в течение планового периода
Р – число различных мест выполняющих различные операции.
Значение применяют для планового периода равного одному месяцу.
Таблица 3 - Ориентировочное определение типа производства по годовому объёму выпуска и массе детали
Объём выпуска детали в год (шт.) при типе производства
Из таблицы 2 видно что при массе детали 16 кг и условии среднесерийного производства годовой объём выпуска находится в пределах 200 10000 деталей в год. Принимаем ориентировочно 1000 дет.год.
Серийное производство характеризуется ограниченной номенклатурой изделий изготовляемых или ремонтируемых периодически повторяющимися партиями и сравнительно большим объемом выпуска.
Серийное производство является основным типом современного машиностроительного производства и предприятиями этого типа выпускается 75-80% всей продукции машиностроительного производства.
Следовательно из вышесказанного следует что принимаем тип производства: серийное.
3 Анализ технологичности детали
Анализ технологичности конструкции детали и корректировка её чертежа проводится с целью увязки конструкторских и технологических требований предъявляемых к детали при заданном объеме выпуска а также с целью приведения чертежа детали в соответствие с требованиями ЕСКД. Все предложения по изменению конструкции детали должны быть систематизированы обоснованы и могут быть внесены в конструкцию детали.
Технологическая характеристика детали определяется: коэффициентом точности - Ктч коэффициентом шероховатости –Кш коэффициентом унификации - Ку коэффициентом использования материала Ким.
Коэффициент точности обработки определяется по формуле:
Ктч = 1 – 1ITср (1.4)
где ITср – средний квалитет точности обработки изделия.
Средний квалитет точности обработки изделия определяется по формуле:
ITср = S (ITi ni) nS (1.5)
nS - общее количество принятых во внимание размеров детали.
Коэффициент шероховатости поверхности определяется по формуле:
Кш = 1 -1 Raср (1.6)
где Raср – среднее числовое значение параметра шероховатости поверхности по Ra для всех обрабатываемых поверхностей.
Среднее числовое значение параметра шероховатости поверхности определяется по формуле:
Raср = S (Rai mi) mS (1.7)
mS – общее количество принятых во внимание поверхностей.
Таблица 1.3 - Технологическая характеристика детали «фреза»
Шероховатость Ra мкм
Значение полученных коэффициентов близко к единице что свидетельствует о технологичности данной детали. Это значит что деталь при обработке на станке можно изготовить в пределах допуска с требуемой шероховатостью.
4 Выбор заготовки метода её изготовления.
Одно из основных направлений современной технологии машиностроения – совершенствование заготовительных процессов с целью снижения припусков на механическую обработку.
Определение массы заготовки и массы отходов кг
( ρ=00078 кгсм3 [2] mд=16кг)
mотх= 197 – 16=37 кг
mотх= 26.8 – 16=10.8 кг
Определение Ким=mдНрасх
При выборе заготовки первоначально решается вопрос об основных способах изготовления заготовки. Предпочтительным должен быть тот метод который обеспечивает наименьшую технологическую себестоимость изготовления детали и более высокий коэффициент использования материала что должно обосновываться технико-экономическим анализом двух близких по своим технологическим параметрам способов получения заготовок с учётом затрат на механическую обработку.
5 Разработка маршрутного технологического процесса изготовления инструмента.
Разработка технологического процесса включает комплекс взаимосвязанных работ (ГОСТ 14301-82):
- выбор технологических баз;
- определение последовательности и содержания операций;
- определение и выбор средств технологического оснащения;
- назначение и расчет режимов резания;
- выбор средств механизации и автоматизации элементов технологического процесса.
Базовый тех процесс на массовом производстве:
0 Токарная программная
Таблица 5 – Маршрут изготовления детали “Торцевая фреза”.
Наименование операции
Вертикально-фрезерная
Горизонтально-фрезерная
6 Выбор методов обработки поверхностей заготовки и выбор оборудования.
Для достижения мелкосерийного выпуска деталей целесообразно применить универсальные станки. Эти станки позволяют достигнуть оптимальных технических и экономических показателей. В данном технологическом процессе я предлагаю использовать токарно-винторезный станок модели 16К20 горизонтально-фрезерный станок 6Р80 вертикально - фрезерный станок 6Т12 внутришлифовальный станок 3К227А станок плоскошлифовальный универсальный 3Г71. Они имеют следующие технические характеристики приведенных в таблицах 678910.
Таблица 6 – Техническая характеристика станка 16К20.
Наибольший диаметр обрабатываемой детали над станиной мм
Наибольший диаметр обрабатываемой детали над суппортом мм
Расстояние между центрами мм
Наибольший диаметр обрабатываемого прутка мм
Частота вращения шпинделя обмин
Мощность электродвигателя главного движения кВт
Таблица 7 - Техническая характеристика станка 6Р80
Наименование размера
Размеры рабочей поверхности стола мм
Число скоростей шпинделя
Частота вращения шпинделя ммоб
Внутренний конус шпинделя мм
Наибольший угол поворота шпиндельной головки град.
Перемещение гильзы со шпинделем мм
Мощность главного привода кВт
Таблица 8 - Техническая характеристика станка 6Т12
Скорость вертикального движения подачи стола мммин.
Скорость продольного и поперечного движения подачи стола мммин
Таблица 10 - Техническая характеристика станка 3К227А
Наибольший диаметр мм
Диаметр шлифуемых отверстий мм
Наибольший ход стола мм
Наибольший угол поворота бабки мм
Частота вращения обмин
Таблица 10 - Техническая характеристика станка 3Г71
Длина (диаметр) рабочей поверхности стола мм
Размеры шлифовального круга мм
7 Выбор методов и средств технического контроля качества инструмента
Для контролирования инструмента применяются различные технологии:
Калибр пробка 50Н7 ГОСТ 24853-81.
Калибр пробка 65Н9 ГОСТ 24853-81.
ШЦ-I — штангенциркуль с двусторонним расположением губок для измерения наружных и внутренних размеров и с линейкой для измерения глубин.
ШЦ-III — с односторонним расположением губок для измерения наружных и внутренних размеров.
8. Разработка технологических операций и операционного технологического процесса.
8.1 Назначение межпереходных припусков и размеров.
Рассчитаем припуск на диаметр детали «Фреза». Шероховатость обработанной поверхности Ra=063 мкм. Материал детали – Сталь 40Х ГОСТ 4543-71.
Для обеспечения заданной степени точности и шероховатости необходимо предусмотреть следующую последовательность обработки поверхности:
Точение черновое точение чистовое шлифование.
Двусторонний минимальный припуск на обработку внутренних поверхностей определяется по формуле:
RZi-1 – высота неровностей профиля на предшествующем переходе мкм
i – погрешность установки заготовки на выполненном переходе
ΔΣi-1 - суммарное отклонение расположения поверхности мкм
ΔΣкi-1 - суммарное отклонение оси детали от прямолинейности (кривизна) мкм
Δui-1 – погрешность центрирования заготовки мкм
Tdi-1 – допуск на диаметральный размер базы используемой при центрировании мкм.
В качестве заготовки используется поковка Rz+h=500 мкм.
Суммарное отклонение расположения поверхности включает перекос отверстия п коробление к погрешность расположения отверстия относительно технологических баз ртб.
к=1·D=1·280=280 мкм;
Остаточное отклонение расположения заготовки (кривизна) после обработки определяется по формуле:
где Ку – коэффициент уточнения
Величина коэффициента уточнения после точение чернового – 006
точения получистового -005 точения чистового – 004 [4]. Следовательно остаточная кривизна после:
точения черновое - ΔΣ1=566·006=34(мкм)
точения чистовое - ΔΣ2=34·005=17 (мкм)
шлифование- ΔΣ2=17·004=007 (мкм)
При закреплении заготовки в 3-х кулачковом самоцентрирующимся патроне =200 [8].
Параметры характеризующие точность и качество поверхности заготовки после механической обработки необходимые для расчета припусков приведены в таблице 6 [8].
Таблица 1.5 – Данные для расчета припуска
Исходя из вышеизложенного определим расчетную величину минимального припуска: на точение черновое:
на точение чистовое:
Таблица 1.6 – Расчет припусков на обработку и предельных размеров по технологическим переходам
Элементарная поверхность детали и тех. маршрут ее обработки
Элементы припуска мкм
Расчетный припуск Zmш мкм
Допуск на изготовление Td мкм
Принятые (округленные) размеры по переходам мм
Полученные предельные припуски мкм
Проверка расчета: Tdз-Tdд=2Zomax-2Zomin
Tdз – допуск на изготовление заготовки;
Tdд – допуск на изготовление детали.
00-25=3386-2361=750=750=0.
Рассчитаем припуск на диаметр детали «Фреза». Шероховатость обработанной поверхности Ra=32 мкм. Материал детали – Сталь 40Х ГОСТ 4543-71.
Точение черновое точение чистовое.
точения чистового -005 [4]. Следовательно остаточная кривизна после:
Таблица 1.8 – Расчет припусков на обработку и предельных размеров по технологическим переходам
8.2 Расчёт режимов резания
Режимы обработки назначаются на все технологические операции по общемашиностроительным нормативам времени и режимов резания для соответствующего вида обработки и типа производства. Режимы резания рассчитываются на ЭВМ или определяются расчётно – аналитическим методом. В пояснительной записке дипломного проекта приводится пример подробного расчёта режимов резания. Расчёт расчетное – аналитическим методом ниже в данном разделе. Пример расчёта режимов резания расчетно – аналитическим методом: расчет производится по методике изложенной.
Расчет режимов резания при операции «токарно-винторезная»
Элементы режимов резания устанавливаются в следующем порядке:
- глубина резания t: при черновой обработке принимается наибольшая из возможных глубина резания равная большей части припуска на обработку; при чистовой обработке - в зависимости от требуемой точности размеров и требований к шероховатости поверхности;
- подача s: при черновой обработке выбирают максимально возможную подачу исходя из жесткости и прочности технологической системы мощности привода станка прочности инструмента; при чистовой обработке – в зависимости от требуемой точности размеров и шероховатости поверхности. Выбранная подача согласовывается с паспортными данными станка;
- скорость резания V рассчитывается по эмпирическим формулам;
- частота вращения шпинделя n определяется исходя из рассчитанной скорости резания и корректируется по паспортным данным станка;
- определяется фактическое значение скорости резания с использованием скорректированного значения частоты вращения шпинделя;
- определяются силы резания мощность резания крутящий момент на шпинделе станка. Мощность резания не должна превышать мощность привода станка.
Расчет режимов резания на операцию 005 “Токарно-винторезная”. Оборудование – станок токарно-винторезный 16К20.
Точить торец выдерживая размер 45 мм.
Расточить отверстие 50 мм
Расточить отверстие 65 мм
Точить канавку 25 мм
Переход 1. Точить торец выдерживая размер 45 мм.
Глубина резания 2.5 мм
Инструмент резец подрезной с механическим креплением трехгранной пластины Р18.
Скорость резания при точении определяется по формуле:
T – стойкость инструмента мин;
t – глубина резания мм s – подача ммоб.
где Cv=467; y=05; m=033; q=045; u=01; p=01;
Частота вращения шпинделя определяется по формуле
где D – диаметр заготовки мм
По паспорту станка принимаем 315 мин-1. Тогда фактическая скорость резания составит
Фактическая скорость:
где СР – постоянная;
КР – поправочный коэффициент.
СР = 300; х = 1; у = 075; n = - 015; [21]
КР = КМР×КjР×КgР×КlР×
КМР – поправочный коэффициент учитывающий влияние качества обрабатываемого материала на силовые зависимости
КjР – коэффициент учитывающий влияние главного угла в плане КjР = 0.89
КgР – коэффициент учитывающий влияние угла резца КgР = 1.1
КlР - коэффициент учитывающий влияние угла резца КlР = 1
КР = 0.846×0.89×1.1×1 = 0.83
Pz = 10×300×25×396075×040075×83 = 568Н.
Операция 035 Внутришлифовальная
Переход №2. Шлифовать поверхность 50 мм
Припуск на обработку составляет t = 005 мм
Определяю скорость шлифовального круга
Определяю скорость вращения заготовки
Принимаю uз = 25 ммин
Определяю частоту вращения шпинделя соответствующую принятой скорости резания
Принимаю n = 145 обмин
Найденное значение n = 145 обмин может быть установлено на станке имеющем бесступенчатое регулирование частоты вращения шпинделя в пределах 63–400 обмин.
Определяю поперечную подачу круга
S = 001 ÷ 0025 мм [8]
Принимаю S = 0015 мм
Определяю мощность затрачиваемую на резание [8]
где CN – постоянная в формуле
r y q z – показатели степеней
uз – скорость вращения заготовки
d – обрабатываемый диаметр
b – ширина шлифования
Операция 20 Горизонтально-фрезерная.
Расчет режимов резания на фрезерование паза глубиной 30±1мм
Шириной 20 длиной L=27 мм. режущий инструмент – фреза дисковая 125мм ширина 20мм материал режущей части Т15К6 число зубьев z=22.
Глубина резания t = 14 мм. Рекомендуемая подача зуб Sz = 002 ммзуб.[9].
Скорость резания рассчитывается при обработке заготовки по формуле:
Значение периода стойкости Т коэффициента СV и показателей степеней [9] равны СV =690 x = 03 y = 04 m = 035 q=02 u=01 p=0 T=180
Коэффициент КV в формуле находится по формуле:
где Kмv - поправочный коэффициент учитывающий качество обрабатываемого материала;
Knv – поправочный коэффициент учитывающий состояние поверхности заготовки;
Kиv – поправочный коэффициент учитывающий материал инструмента;
Kмv =114[9] Для поверхности заготовки без корки Knv = 10 [9] Kиv =10[9]
Частота вращения шпинделя:
Скорректируем определенную исходя из рассчитанной скорости резания по
паспорту станка частоту вращения шпинделя n = 200 (мин-1).
Следовательно фактическая скорость резания равна:
Главная составляющая силы резания при фрезеровании– окружная сила определяется по формуле:
Значения коэффициента Ср и показателей степени [5]:
Ср = 261 x = 09 y = 08 u=11 q=11w=01 KMP=096[5].
Следовательно сила резания будет равна:
Крутящий момент определяется по формуле:
Мкр=621*2002*100=621(Н·м)
Мощность резания рассчитывают по формуле:
8.3 Расчёт нормы штучного времени
Расчёт нормы штучного времени и подготовительно – заключительного времени. Производится на следующую операцию.
8.3.1 Определение штучно-калькуляционного времени на операцию «Токарно-винторезная»
На данной операции производиться точение поверхностей на станке 16К20 .
Переход 2: Точить торец выдерживая размер 45 мм.
Основное технологическое время определяется:
L = L0 + L1 + L2 (37)
где L – длина резания мм;
L0 – длина обрабатываемой поверхности мм;
L2 – величина врезания и перебега инструмента мм;
L3 – дополнительная длина на взятие пробной стружки мм;
n – частота вращения шпинделя ммоб;
Sмин – минутная подача мммин;
S – подача на один оборот шпинделя ммоб;
Вспомогательное время на установку закрепление и снятие детали ТВСП = 45 мин.
Вспомогательное время на переход (включение и отключение подачи подвод инструмента к детали и т.д.) ТВСП = 01 мин
ТОП = ТОСН + ТВСП = 1.3 + 45 + 01 = 5.9 (мин)
Время на отдых составляет ТОТД = 9% на обслуживание рабочего места ТОБС = 3% о оперативного времени [3. Карта 72. С 150]
ТОБС + ТОТД = 5.9×(009+003) = 082 (мин) (38)
ТШТ = ТОП + ТОБС + ТОТД = 5.9 + 082 = 76 (мин) (40)
Подготовительно заключительное время на партию деталей: ТП.З. = 165 мин.
Штучно-калькуляционное время определяется:
где ПЗ = партия запуска деталей.
где N – годовой выпуск деталей шт;
Sn – число запусков в год.
ТШТ.К = 76 + 165 250 = 77 (мин)
8.3.2 Определение штучно-калькуляционного времени на операцию «Внутришлифовальная»
ТОП = ТОСН + ТВСП = 8 + 45 = 125 (мин)
ТОБС + ТОТД = 125×(009+003) = 15 (мин)
ТШТ = ТОП + ТОБС + ТОТД = 125 + 15 = 14 (мин)
ТШТ.К = 14 + 165 250 = 141 (мин)
8.3.4 Определение штучно-калькуляционного времени на операцию «Горизонтально-фрезерная»
ТОП = ТОСН + ТВСП = 11 + 45 = 155 (мин)
ТОБС + ТОТД = 155×(009+003) = 19 (мин)
ТШТ = ТОП + ТОБС + ТОТД = 155 + 19 = 174 (мин)
ТШТ.К = 174 + 165 250 = 175 (мин)
9 Разработка технологического задания на проектирование специального режущего инструмента.
Для изготовления фрезы необходимы следующие специальные инструменты:
- резец специальный расточной с пластиной сложного профиля из твердого сплава Т15К6 сечение державки 40х32 мм L=140 мм φ=90°;
- протяжка специальная L=550 мм 18х30 мм
материал: сталь быстрорежущая Р14Ф4 HB 269 (после отжига)
- круг шлифовальный специальный эльборовый на органической связке D=150 мм ширина 20мм
R4 150х20х45х22 АС6М 10080 B48 75 35
Рекомендуемые чертежи
- 24.01.2023
- 24.01.2023
Свободное скачивание на сегодня
Другие проекты
- 29.08.2014