Разработка штампа совмещенного действия




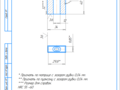

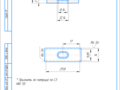
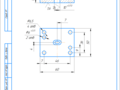
- Добавлен: 25.01.2023
- Размер: 2 MB
- Закачек: 0
Описание
Состав проекта
![]() |
![]() |
![]() |
![]() ![]() ![]() ![]() |
![]() ![]() ![]() ![]() |
![]() ![]() ![]() ![]() |
![]() |
![]() ![]() ![]() ![]() |
![]() |
![]() |
![]() |
![]() ![]() ![]() ![]() |
![]() ![]() ![]() ![]() |
![]() |
![]() |
![]() ![]() ![]() ![]() |
![]() |
![]() ![]() ![]() |
![]() |
![]() |
![]() |
![]() |
![]() |
![]() |
![]() ![]() ![]() ![]() |
Дополнительная информация
ПУАНСОНОДЕРЖАТЕЛЬ.cdw

МАТРИЦА.cdw

ШТАМП СОВМ ДЕИСТ.cdw

СЪЕМНИК.cdw

Вытал.cdw

ПУАНСОНОМАТРИЦА.cdw

** Пригнать по пуансону с зазором рубки 0
*** Размер для справок.
расположение.cdw

Записка.docx
КУРСОВАЯ РАБОТА ПО ДИСЦИПЛИНЕ:
«Технология производства элементов РЭС»
на тему:«Разработка штампа совмещенного действия»
Материалы для штампов деталей 7
Расчеты для операций вырубки8
Список использованной литературы11
Для изготовления данной детали из листового материала выбран штамп совмещённого действия который позволяет штамповать за один рабочий ход и совмещать две различные операции: вырубку детали по наружному контуру и пробивку отверстия.
Проведён расчет для операции вырубки детали при холодной штамповке рассчитаны исполнительные размеры пуансона и матриц.
Холодная штамповка является одним из наиболее прогрессивных технологических методов производства; она имеет ряд преимуществ перед другими видами обработки металлов как в техническом так и в экономическом отношении.
В техническом отношении холодная штамповка позволяет:
) получать детали весьма сложных форм изготовление которых другими методами обработки или невозможно или затруднительно;
) создавать прочные и жёсткие но лёгкие по массе конструкции деталей при небольшом расходе материала;
) получать взаимозаменяемые детали с достаточно высокой точностью размеров преимущественно без последующей механической обработки.
В экономическом отношении холодная штамповка обладает следующими преимуществами:
)экономным расходованием материала и сравнительно небольшими отходами;
)весьма высокой производительностью оборудования с применением механизации и автоматизации производственных процессов;
)массовым выпуском и низкой стоимостью
изготавливаемых изделий.
Холодная листовая штамповка объединяет большое количество разнообразных операций которые могут быть систематизированы по технологическим признакам.
По характеру деформаций холодная листовая штамповка рассчитана на две основные группы: деформация с разрешением материала и пластические деформации. Первая группа объединяет деформации которые приводят к местному разъединению материала путём среза и отделение одной его части от другой. Группа пластических деформаций холодной местной штамповки включает операции по изменению формы гнутых и полых листовых деталей.
Имеется четыре основных вида деформаций холодной листовой штамповки: резка-отделение одной части материала от другой по замкнутому или незамкнутому контуру;
) гибка-превращение плоской заготовки в изогнутую деталь;
) вырубка-превращение плоской заготовки в новую деталь любой формы или дальнейшее изменение её размеров;
) формовка-изменение формы детали или заготовки путём местных деформаций различного характера.
Холодная штамповка широко применяется в машиностроительной приборостроительной и других отраслях промышленности. Наибольшее распространение холодная штамповка получила в крупносерийном и массовом производстве где большие масштабы выпуска позволяют применять технически более совершенные хотя и более сложные и дорогие штампы.
Основным прогрессивным конструктивным показателем характеризующем эффективность применение холодной листовой штамповки является снижение массы при увеличении прочности и жёсткости штампованных из листа деталей по сравнению с литыми кованными или обработанными из листового проката.
Основным прогрессивным технологическим фактором дальнейшего развития холодной листовой штамповки является стремление получить полностью законченную деталь не требующую дальнейшей обработки резанием.
Прогрессивность тех или иных технологических методов неразрывно связана с единством и конкретными условиями данного производства а следовательно является не столько технологическим сколько организационно-техническим понятием.
Производственно-технологические методы прогрессивные в мелкосерийном производстве в большинстве случаев оказываются непрогрессивными и нецелесообразными в крупносерийном и массовом производстве и наоборот.
Этим объясняются различия производственных методов и путей развития холодной штамповки в массовом и мелкосерийном производстве.
В крупносерийном производстве холодная штамповка характеризуется:1) применением сложных совмещено-комбинированных штампов; 2)применением последовательной многопозиционной штамповки в ленте; 3) механизацией и автоматизацией процессов штамповки; 4) совершенствованием и развитием методов дающих повышенную точность и производительность и заменяющих обработку металлов резанием (зачистка в штампах холодное выравнивание)
В мелкосерийном и единичном производстве холодная листовая штамповка характеризуется использованием универсальных и дешёвых упрощённых штампов а также применением новых технологических методов (штамповка резиной штамповка взрывом и др.)
При изготовлении деталей РЭС из всех процессов формообразования преимущественно используют методы холодной листовой и объёмной штамповки. Причём листовой холодной штамповкой изготавливают до 85% деталей конструктивной базы РЭС (детали корпусов кожухи и др.) и широкая номенклатура деталей входящих в модули и узлы элементной схемотехнической базы (выводы корпуса и крышки микросхем и микросборок детали магнитопровода панели разъёмов и др.).
Материалы для штампов деталей.
Рабочие детали штампов (пуансона и матрицы) подвергаются ударной нагрузке с сильной концентрацией напряжений на рабочих кромках или на рабочей поверхности. Поэтому к материалу пуансона и матриц предъявляется требование высокой или повышенной твёрдости и износоустойчивость при достаточной вязкости.
В таблице приведены марки материалов применяемых для пуансонов и матриц.
Стали применяемые для изготовления рабочих частей штампов холодной штамповки делятся на следующие группы:
) Углеродистые стали небольшой прокаливаемости: У8А У10А У8 У10.
) Легированные сталиповышенной прокаливаемости: 9Х 9ХС 9ХФ ХВГ 9ХВГ.
) Высокохромистые стали высокой прокаливаемости высокой износоустойчивости малодеформируемые при закале:Х12 Х12Ф Х12М.
Легированные стали повышенной вязкости: 4ХС 6ХС 4ХСВ2С %ХВ2С 5ХВГ.
Расчёты для операции вырубки.
Определение ширины полосы В.
L – Размер вырубаемой детали по чертежу: L= 30 мм;
m – наименьший размер боковой перемычки: m= 12 мм;
Δn – односторонний допуск на ширину полосы Δn=08 мм;
В = 30+2*12-08 = 31.2 мм;
Определение коэффициента использования материала.
n – количество деталей в полосе заготовки;
h = 10+12 = 11.2 мм;
Кол-во полос np= 1420B = 142031.2 = 45;
f – площадь вырубаемой детали в мм2;
f = f1+f2-fотв = 30*10-(4*4+*4) = 271 мм2;
M – количество деталей на листе;
F – Площадь листа (1420х710);
M = n*np = 63*45 = 2835;
F = 1420*710 = 1008200 мм2
Коэффициент использования материала оценивает рациональность раскроя или раскладки деталей в листе. Обычно раскрой материала может быть с перемычками по всему контуру вырубаемой детали с отходами по краям и торцам полосы без отходов;
KМ = 2835*2711008200 = 076;
Определение усилий при вырубке.
L - периметр вырубаемой детали;
S - толщина материала 0.5 мм;
Tср - предел прочности среза Tср = 50кгмм2;
L = 30+30+10+10=80 мм;
Рв = 125*80*0.5*50 = 2500 кг*мм = Pобщ;
Расчет исполнительных размеров на матрицу и пуансон.
Для наружного контура:
Рм и Рn - размеры матрицы и пуансона Рн - номинальный размер;
Δ - допуск заданный по чертежу детали
Zmin - минимальный двухсторонний зазор между Пуассоном и матрицей.
Zmin = 0085*S = 0085*0.5 = 0.0425 мм.
Рn°(10) = 10+075*(-0.15) = 9.8875мм
Рn°(30)= 30+075*(-0.21) = 29.8425мм
Рм°(10) = 9.8875-0.0425= 985+004 мм;
Рм°(30) = 30-0.0425 = 29.8+005 мм;
*Пуансон пригнать по матрице с зазором рубки 004 мм;
Рn°(8) = 8+075*015 = 409 мм;
Рм°(42) =4.09-0.0425= 405-003* мм;
*Матрицу пригнать по пуансону с зазором рубки 009 мм;
Список использованной литературы.
)Чепахин Г.А. - Методические указания к выполнению курсового проекта по курсу: «Формообразование деталей РЭС из конструкционных материалов» Казань 2003г.
)Романовский В.Н. – Справочник по холодной штамповке М.: Машгиз 1962г.
)Конспект лекций по дисциплине – «Технология РЭС»
ПУАНСОН.cdw
