Разработка инструментальной наладки и комплекта режущих инструментов




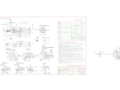
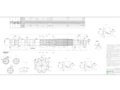
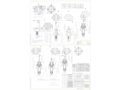

- Добавлен: 25.01.2023
- Размер: 5 MB
- Закачек: 0
Описание
Состав проекта
![]() |
![]() |
![]() ![]() ![]() |
![]() ![]() ![]() |
![]() ![]() ![]() |
![]() ![]() ![]() |
![]() ![]() ![]() |
![]() ![]() ![]() |
![]() ![]() ![]() |
![]() ![]() ![]() ![]() |
![]() ![]() ![]() ![]() |
![]() ![]() ![]() |
![]() ![]() ![]() |
![]() ![]() ![]() ![]() |
![]() ![]() ![]() |
![]() ![]() ![]() ![]() |
Дополнительная информация
Список использованной литературы.docx
Докукин Г. И. Ивлюшина И. М. Изучение конструкции сверл. Методические указания к выполнению практических работ по курсу "Резание материалов" для студентов специальности 120100 всех форм обучения. Балаково 2008 26с.
Родин П.Р. Металлорежущие инструменты Киев Высшая школа 1974.
Основной электронный каталог “SANDVIK Coromant” 2010г.
Каталог Сандвик – МКТС. Сменные пластины и инструмент. 2000.
ГОСТ 14953-80 «Зенковки конические. Технические условия».
ГОСТ 28320-89 «Сверла спиральные ступенчатые для отверстий под метрическую резьбу. Основные размеры».
ГОСТ 3266-81 «Метчики машинные и ручные».
Общий каталог MITSUBISHI 2010-2011.
Справочник технолога-машиностроителя. В 2-х т. Т.2Под ред. А.Г. Косиловой и Р.К. Мещярикова. – 4-е изд. перераб. И доп. – М.: Машиностроение 1985. 496с. ил.
Общемашиностроительные нормативы режимов резания: Справочник: В 2-х томах: Т.1А.Д. Локтев И.Ф. Гущин В.А. Батуев и др. – М.: Машиностроение 1991 – 640с.
Общий каталог фирмы EROGLU2010.
Общий каталог фирмы IMTE 2010.
Маслов А.Р. Конструкции прогрессивного инструмента и его эксплуатация. М. Издательство «ИТО» 2006 166с.:ил.
Кузнецов Ю.И. Маслов А.Р. Байков А.Н. Оснастка для станков с ЧПУ: Справочник. – 2-е изд. перераб. и доп. – М.: Машиностроение 1990. – 512 л.: ил.
Протяжки для обработки отверстий Д.К. Маргулис М.М. Тверской В.Н. Ашихмин и др. – М.: Машиностроение 1986. – 232с. ил. – (Б-ка инструментальщика).
Металлорежущие инструменты: справочник конструктора Е.Э.Фельдштейн М.А. Корниевич. – Минск: Новое знание 2009. – 1039с. : ил.
Содержание.doc
Проектирование шлицевой протяжки13
1 Анализ исходных данных13
1.1 Цели и задачи проектирования13
1.2 Протягивание шлицевых отверстий13
1.3 Геометрические элементы зуба протяжки15
1.4 Схема резания при протягивании15
1.5 Расчет протяжки17
Разработка инструментальной наладки33
1 Выбор оборудования и маршрутной технологии обработки33
2 Выбор основного инструмента 33
3 Выбор вспомогательного инструмента37
4. Расчет режимов резания40
4. Расчет наладочных размеров. Описание методов наладки
инструментов вне станка.42
Список использованной литературы49
ПРИЛОЖЕНИЕ А. Информационно-патентный поиск по
конструкциям инструментов аналогичных проектируемым и
методам их расчета50
Расчет протяжки шлицевой.docx
1 Анализ исходных данных
1.1 Цели и задачи проектирования
Целью проекта является разработка шлицевой протяжки для протягивания шлицевого отверстия детали.
Задачами проектирования являются выбор конструкции и расчет шлицевой протяжки назначение технических требований к ней определение режимов резания и эксплуатационных показателей.
1.2 Протягивание шлицевых отверстий
Шлицевые соединения представляют собой многошпоночные соединения у которых шпонки изготовлены заодно целое с валом. Их используют для передачи больших крутящих моментов и для обеспечения более высоких требований к соосности соединяемых деталей чем у шпоночных соединений. Они бывают с прямобочным эвольвентным и треугольным профилем.
В шлицевых прямобочных соединениях применяют центрирования вала и втулки: по наружному диаметру D по внутреннему диаметру d и по боковым поверхностям зубьев b. Выбор способа центрирования связан с эксплуатационными требованиями предъявляемыми к соединению и технологическими особенностями изготовления шлицевых деталей.
В обозначении шлицевого соединения указывают способ центрирования количество пазов n размеры внутреннего d и наружного D диаметров размер паза b и поля допусков.
Шлицевое отверстие в детали протягивают сложным и дорогостоящим инструментом – протяжкой.
Протяжки разделяют на внутренние (предназначенные для обработки отверстий) и наружные (для обработки незамкнутых поверхностей). Протяжки могут быть режущие и уплотняющие; последние не режут а уплотняют тонкие слои металла. Уплотняющие – выглаживающие протяжки могут увеличивать отверстия на очень малую величину. На рисунке 2.2 показаны основные типы внутренних протяжек.
Протяжки являются многозубыми металлорежущими инструментами осуществляющими снятие припуска без движения подачи за счет превышения высоты или ширины последующего зуба по отношению к высоте или ширине предыдущего. Они применяются для чистовой обработки различных по форме внутренних и наружных поверхностей деталей. Протяжки – узкоспециализированный инструмент предназначенный для обработки одной и редко нескольких деталей мало отличающихся размерами. Из-за высокой стоимости их применение эффективно в массовом и серийном производстве.
Наружные протяжки подразделяются по типу обрабатываемых поверхностей на плоские круглые и фасонные. Протяжки целесообразно изготовлять из быстрорежущих сталей. В отдельных случаях можно применять сталь ХВГ которая мало деформируется при термической обработке что важно при значительной длине протяжки.
Каждая внутренняя протяжка имеет хвостовик (для закрепления в патроне протяжного станка); шейку; переходный конус; направляющую часть (для направления протяжки в начале ее работы по предварительно обработанному отверстию); режущую часть на которой расположены зубья срезающие основной припуск; калибрующую часть на которой расположены зубья калибрующие отверстие и обеспечивающие необходимый класс шероховатости поверхности; заднюю направляющую часть служащую для удержания длинной протяжки от провисания и не допускающую перекоса заготовки в конце протягивания (в момент выхода последнего зуба). На рисунке 2.2 показана типовая конструкция круглой протяжки.
1.3Геометрические элементы зуба протяжки
Задний угол зубьев протяжки в сечении совпадающем с направлением резания выбирается независимо от материала заготовки; он должен обеспечивать хорошие условия резания уменьшение трения задней поверхности об обработанную поверхность.
У калибрующих зубьев делается цилиндрическая ленточка шириной f=005÷02мм (рис. 2.3 зуб 3). Значение заднего угла берутся в зависимости от вида операции (черновой или чистовой) и типа протяжек. Малое значение заднего угла протяжек для внутреннего протягивания объясняется тем что при большем значении угла α заточка протяжки по передней поверхности вызовет значительное изменение размеров зубьев (протяжек) в поперечном сечении. Вследствие этого же делается незначительным и задний угол на фаске у зубьев калибрующей части. Передний угол выбирается в зависимости от материала заготовки.
1.4 Схемы резания при протягивании
Конструкция рабочей части протяжки ее работоспособность размеры срезаемых слоев материала зависят от принятой схемы резания. Под схемой резания понимают картину последовательного срезания припуска режущими зубьями протяжки.
В зависимости от условий профилирования обработанной поверхности различают профильную и генераторную схемы резания. Профильная схема резания (рис.2.4 а) характеризуется тем что зубья имеют форму подобную форме окончательно обработанной поверхности но размер их постепенно увеличивается от первого к последнему режущему зубу на величину подъема зубьев Sz. Слой материала срезаемый режущим лезвием (на рисунке заштрихован) имеет дуговую форму с шириной b равной рабочей длине лезвия и толщиной a= Sz. Протягиваемый контур окончательно формируется режущими кромками последнего зуба.
Генераторная схема резания (рис.2.4 б) отличается тем что главные режущие кромки зубьев протяжки mg и np по форме соответствуют окончательно обработанной поверхности или ее части. Поэтому обработанная поверхность формируется как главными так и вспомогательными режущими кромками всех режущих зубьев протяжки. Сечение материала снимаемого i-м зубом протяжки (на рис. 2.4 б заштрихован) при прямолинейной главной режущей кромке представляет собой полосу шириной b равной длине главной режущей кромки и толщиной равной подъему зубьев протяжки. Для разделения стружки лезвие протяжек профильной и генераторной схем резания имеет стружкоразделительные канавки с α1=0 и 90° (рис.2.5 а).
Для проектируемой протяжки применяем генераторную схему резания.
В зависимости от условий срезания каждого слоя припуска различают одинарную и групповую схемы резания. При одинарной схеме резания (рис. 2.5 а) каждый зуб протяжки срезает слой припуска по всему периметру обрабатываемой поверхности.
При групповой схеме резания (рис. 2.5 б) каждый слой припуска срезается не одним зубом а группой из двух-пяти зубьев. Наиболее широкое распространение получили протяжки переменного резания которые не имеют недостатков профильных и генераторных протяжек.
спроектировать протяжку для обработки шлицевого отверстия
D-8×62+022×72+006×125+006 .
Материал детали: сталь 45 (НВ=255).
Длина отверстия: Lотв.=65мм.
Диаметр отверстия до протягивания Dпред.=598+03мм.
Шлицевое отверстие D-8×62+022×72+006×125+006:
D – центрирование производится по наружному диаметру.
d=62 мм – внутренний диаметр шлицев.
D=72 мм - наружный диаметр шлицев.
b=125 мм – ширина шлицев.
В таблице 2.1 приведен химический состав материала детали.
Таблица 2.1 Химический состав стали 45
Расчет начинаем с установления схемы расположения зубьев на протяжке группы обрабатываемости и группы качества. Принимаем предварительно схему расположения зубьев ФКШ. Окончательно схему расположения зубьев будет установлена после расчета длины круглой части.
Группу обрабатываемости устанавливаем по табл. П1 приложения (стр. 203[16]). Сталь 45 с твердостью НВ255 относится к 2-й группе обрабатываемости.
Группу качества устанавливаем для каждой поверхности шлицевого отверстия отдельно по табл. П2 приложения (стр. 203 [16]). Так как центрирование производиться по наружному диаметру с D= 72+006 мм и параметром шероховатости поверхности выступов Ra25 мкм то группа качества поверхности выступов 2-я боковых сторон и поверхностей впадин вторая – 3-я.
За материал рабочей части протяжки (передний конус передняя направляющая режущая часть задняя направляющая и задний хвостовик) принимаем быстрорежущую сталь Р6АМ5 по табл. П3 приложения (стр. 203 [16]).
Таблица 2.2. Химический состав в % стали Р6М5.
Таблица 2.3- Свойства быстрорежущей стали Р6М5
после закалки с отпуском HRC3 (HRC)
диаметр отпечатка мм не менее
Сопротивление износу
Красностойкость 59HRC3 при отпуске в течение 4 ч °С
Повышенная склонность к
Таблица 2.4 - Химический состав в % материала 40Х
Конструкцию протяжки принимаем с приваренным хвостовиком материал хвостовика - сталь 40Х. Конструкцию хвостовика и размеры принимаем по ГОСТ4044-70 . Диаметр переднего хвостовика мм диаметр заднего хвостовика Dз хв.= 42с11 мм.
Силу допустимую прочностью переднего хвостовика рассчитываем по формуле где - допустимое напряжение при растяжении МПа –площадь опасного сечения хвостовика мм2. Приняв площадь опасного сечения 13854мм2 по табл. П4 (стр. 204 [16]) и рекомендуемое напряжение при растяжении = 300 МПа;
Передние и задние углы зубьев протяжки выбираем по табл. П5 приложения(стр. 207 [16]).
Передний угол черновых и переходных зубьев γ=15° чистовых и калибрующих γ=18° задний угол черновых и переходных зубьев α=3° чистовых αч=2° калибрующих αк=1°. Допуски на передние и задние углы по ГОСТ 9126-76.
Скорость резания устанавливаем по табл. П6 приложения (стр. 208 [16]) для круглой части одна из которой имеет наиболее высокую группу качества (2-ю) =6ммин. Эта скорость входит в диапазон скоростей станка.
Определяем подачу черновых зубьев по средней наработке между двумя отказами. Сначала устанавливаем наработку чистовой части при и :
Т=65 м. Для черновых зубьев при и Т=66 м на зуб на сторону.
Наработка с учетом поправочных коэффициентов составляет:
Для круглой части предназначенной для обработки поверхности 2-й группы качества: для и поверхности 2-й группы качества .
Определяем глубину стружечной канавки по формуле:
где – суммарная длина протягиваемых участков мм. Принимаем предварительно коэффициент помещаемости согласно рекомендации методики К= 3.
По табл. П19 приложения (стр. 216 [16]) принимаем ближайшую большую глубину стружечной канавки =6 мм.
Для фасочных и шлицевых зубьев:
По табл. П19 (стр. 216 [16]) принимаем ближайшую большую глубину стружечной канавки =8 мм. Глубину стружечной канавки допустимую жесткостью протяжки (диаметр сечения по дну стружечной канавки 40 мм.) определяем по формуле:
Для фасочных и круглых зубьев:
Из табл. П19 (стр.216 [16]) приложения принимаем ближайшую меньшую по отношению к расчетной глубину = 12 мм для всех частей протяжки.
Так как глубина стружечной канавки для фасочных и шлицевых зубьев принята из условия жесткости протяжки то для размещения стружки в стружечной канавке уменьшаем подачу по формуле
Вследствие округления подачи до большего значения коэффициент помещаемости уменьшается до 299.
Определяем шаг черновых зубьев и число одновременно работающих зубьев . Шаг черновых зубьев принимаем наименьшим из всех имеющихся и соответствующим данной глубине стружечной канавки Остальные элементы профиля:
Число одновременно работающих зубьев рассчитываем по формуле
Определяем максимально допустимую силу резания (max). Принимаем max наименьшей из трех сил - ст хв. и о.п.:
ст =08·=08·20000·981=156960 Н
Величину оп определяем по формуле:
где = 0785·()2 приняв =400 МПа
=0785 (5983-2·6)2=17958 Н
оп =17958 400=718341 Н.
Следовательно принимаем =ст =156960 Н
Определяем число зубьев в группе zс по формуле
где - зависимость от состояния и твердости обрабатываемого материала
Кро - зависимость от вида СОЖ
- зависимость от группы качества протягиваемой поверхности
- зависимость от способа разделения стружки. Для γ=15° и =249 Нмм (табл. П20 (стр.218 [16])) для =404 Нмм поправочные коэффициенты находим по табл. П21 приложения: =1 =1 =11 для фасочных и шлицевых зубьев так как группа качества для них 3-я; для круглых при 2-й группе качества =1. Поправочный коэффициент =1 для СОЖ принятой по табл. П18 (стр.215 [16]).
Для каждой части протяжки раздельно подставив в формулу вместо Вmax значения Вфmax Вкmax и Вшmax. Максимальную длину режущих кромок на фасочных зубьях определяем приближенно по формуле:
= 125+2·05+(62-598)=157 мм.
При Вфmax>12 и D св 50 мм допускается zс=2.
Максимальную длину режущих кромок на круглых зубья определяем по формуле:
4·628 - (125+2·05)=1083 мм.
Значение больше значения при котором допускается работа без разделения стружки; следовательно принимаем .
Максимальную длину режущих кромок на шлицевых зубьях ==1256мм.
Распределяем припуск между разными частями и зубьями протяжки. Припуск на фасочную часть определяется по формуле:
где находим по формуле а диаметр окружности проходящий через точку пересечения исходных профилей фаски и прямобочного паза по формулам
Припуск на шлицевую часть находим по формуле:
Диаметр первого шлицевого зуба находим по формуле:
Припуск на черновые шлицевые зубья определяем по формуле
где Аш.п.=024 мм Аш.ч.=008 мм
Ашо=932-(024+008)=9 мм.
Припуск на круглую часть:
Припуск на черновые зубья определяем по формуле:
где (табл. П23 с.221 [16]);
(табл. П22 с.220 [16])
Находим число групп черновых зубьев остаточный припуск и распределение его. Число групп черновых зубьев определяем по формуле:
Подставив в нее соответствующие значения и принятые для каждой части; остаточный припуск находим по формуле:
Так как то остаточный припуск будет срезан переходными зубьями число которых определено ниже а число черновых групп .
Так как то о остаточный припуск будет срезан переходными зубьями число которых определено ниже а число черновых групп .
Общее число зубьев определяем по формуле:
число фасочных - по формуле:
число круглых - по формуле:
и число шлицевых - по формуле:
Число круглых черновых зубьев:
Число круглых переходных зубьев zк.п.= 2 (П23 стр.221 [16]) число круглых чистовых зубьев zк.ч.=4 число калибрующих zк.к.=4 (П22 стр.220 [16]).
Число шлицевых черновых зубьев:
Число шлицевых переходных зубьев zш.п.=4 число шлицевых чистовых зубьев (при zс.ш.ч.=1) zш.ч=2 число калибрующих зубьев zш.к.=2
Подъемы переходных зубьев круглой и шлицевой частей принимаем:
для круглых Sп1=008мм Sп2=006мм (табл. П23 с.221 [16]);
для шлицевых Sп1= 008 мм Sп2= 004 мм (табл. П23 с.221 [16]).
Подъемы чистовых зубьев круглой и шлицевой частей принимаем для круглых Szч=002 мм (два зуба) Szч= 001мм (два зуба) Szч3=002 мм и Szч4= 001 мм для шлицевых Szч= 002 мм (два зуба).
Определяем длину режущей части протяжки Lр шаги и профиль чистовых круглых и шлицевых зубьев. Вначале находим длину фасочной части по формуле:
круглой части - по формуле:
шлицевой части - по формуле:
Для круглой и шлицевой частей находим шаг чистовых зубьев по табл. П24 (стр.221 [16]) (берем средний шаг t2).
Шагу t=11мм соответствует шаг чистовых зубьев .
Остальные элементы стружечной канавки чистовых зубьев берем из табл. П19 (стр.216 [16]): h=45 мм b= 40 мм R=70 мм r=23 мм
lк=14·(9+2)+11·(4+4-1)=231 мм
lш=14·(45+4+1)+11·(2+3-1)=744 мм
Lр=196+231+744=1171 мм.
Силу протягивания на каждой части протяжки рассчитываем по формулам
Так как длина круглой части lк=231мм что более 15l то черновые переходные зубья выполняем по групповой схеме пересчитываем их число и помещаем перед фасочными зубьями (схема Ко.п.ФКч.кШ):
Длину круглой черновой и переходной а так же чистовой и калибрующей частей рассчитываем с учетом выхода шлифовального круга при шлифовании бокового профиля фасочных зубьев:
Общее число зубьев протяжки равно сумме черновых и переходных круглых фасочных чистовых и калибрующих круглых и шлицевых зубьев:
Определяем длину режущей части:
Рассчитываем силы протягивания на каждой части протяжки по формулам приняв среднюю длину режущего лезвия на фасочных зубьях
Диаметры калибрующих зубьев принимаем равными соответственно внутреннему и наружному диаметру шлицевого отверстия:
(допуски назначаем по ГОСТ 7943-78).
Для схемы Ко.п.ФКч.к.Ш принимаем диаметр впадин фасочных зубьев равным диаметру последнего переходного круглого зуба: Dв.ф.= 6224d11 диаметр впадин шлицевых зубьев Dвш= 62f9.
Число выкружек на круглых черновых и переходных зубьях и их ширину определяем по табл. П25 (стр.223[16]):
Nк= 12 ак= 80 мм и Rк= 25 мм Rв=30 мм.
Чистовые круглые зубья выполняются без выкружек.
Число выкружек шлицевых зубьев равно числу впадин Nш = 8. Ширину режущих лезвий на прорезных фасочных и шлицевых зубьях определяем по формуле:
где f – ширина фаски на шлицевом зубе f= 25 мм (табл.П32 стр. 225 [16]).
Ширина выкружек на фасочных и шлицевых зубьях при принятой ширине режущих секторов является величиной переменной: для вычисления радиуса круга это не имеет значения и поэтому ширину (мм) определяют приближенно по формуле:
Для аш= 2076 мм и D= 72 мм Rк= 25 мм Rв=30 мм.
Диаметр передней направляющей Dпн=598е8 мм. Так как то длина передней направляющей lпн=l=65 мм.
Длина переходного конуса принимаем lп=30мм (табл. 28 стр.225 [16]).
Расстояние от переднего торца протяжки до первого зуба:
L1=l1+l2+l3+l+25= 205+25+40+25=295 мм
Согласно рекомендациям (стр.57 [16])l1 принимают в зависимости от диаметра хвостовика равным 205 мм l2 и l3 в зависимости от станка l2=25 мм l3= 40 мм (для станка 7Б56).
Диаметр задней направляющей принимаем равной диаметру впадины шлицев протяжки: Dз.н.= Dв.ш.
Длину задней направляющей принимаем по рекомендациям (табл. П29 стр.225 [16]).
Так как протяжка имеет значительную длину то протяжку делаем с задним хвостовиком. Диаметр заднего хвостовика принимаем по ГОСТ 4044-70 (табл.П4 стр.205 [16]) меньшим чем диаметр переднего хвостовика Dз.хв.=40мм длину заднего берем по табл. П30( стр. 225 [16]): lз.хв=125мм.
Общую длину протяжки определяем по формуле:
L=L1+Lp+lз.н.+lз.хв. =295+1362+50+125=1832 мм.
Округляем L до 1835 мм за счет увеличения длины заднего направления: lзн= 53мм.
Общая длина протяжки не должна превышать длины допустимой жесткостью протяжки: L=(30÷40)D. LD=183572=2530. Протяжка жесткая.
Расчет комбинированного сверла1 .docx
Все большее распространение получают сверла диаметром свыше 12 мм с многогранными неперетачиваемыми твердосплавными пластинами (Рисунок 1.1). Конструкция сверла представляет собой корпус 1 с двумя прямыми или винтовыми стружечными канавками на переднем торце которого закреплены твердосплавные пластины 2 различной формы. Одна из пластин располагается у оси сверла вторая — на периферии. Сверла диаметром 20 60 мм оснащаются двумя неперетачиваемыми твердосплавными пластинами а большего диаметра — четырьмя устанавливаемыми непосредственно в корпусе сверла или в сменных кассетах. Для подачи СОЖ в зону резания в корпусе сверла предусмотрены специальные отверстия.
Снимаемый припуск делится по ширине между взаимно перекрывающимися пластинами которые располагаются в корпусе таким образом что радиальная нагрузка с обеих сторон от оси сверла сбалансирована и отпадает необходимость в предварительно засверленном отверстии или кондукторной втулке в момент
Рисунок 1.1 Сверла с неперетачиваемыми твердосплавными пластинами
Обладая высокой жесткостью и надежной системой подачи СОЖ в зону резания эти сверла позволяют вести обработку с повышенными подачами и скоростями по сравнению со спиральными сверлами из быстрорежущей стали.
Заданием на курсовое проектирование выдано сверло комбинированное с СНП с внутренним подводом СОТС для обработки ступенчатого отверстия (рис.1.2). Материал детали – конструкционная сталь по ГОСТ 4543-88.
Комбинированные сверла изготавливаются двухсторонними для лучшего использования материала. Канавки делаются или прямыми или наклонными с углом наклона = 5 8°. Угол при вершине режущей части φ = 50 60° угол наклона поперечной кромки = 50 55°. Толщина сердцевины к = (025 017)D и увеличивается по направлению к хвостовику под углом 3°. Передний угол γ= 5 6°. Заточка комбинированного сверла производится так же как и спирального. Задний угол α на периферии режущей части равен 8°.
Рисунок 1.2 Ступенчатое отверстие
Комбинированные сверла предназначены для сверления ступенчатых отверстий и для сверления отверстий и одновременного снятия фасок.
Общий вид комбинированного сверла с СНП с внутренним подводом СОТС приведен на рисунке 1.3.
Рисунок 1.3 – Комбинированное сверло с СНП и внутренним подводом СОТС.
Способы и устройства подвода СОЖ и отвода стружки.
На практике применяют два основных способа подвода СОТС и отводи стружки из зоны резаниям:
) наружный подвод СОТС и внутренний отвод стружки;
) внутренний подвод СОТС и наружный отвод стружки.
В первом случае (рис. 1.4 а) подвод СОТС к режущим лезвиям инструмента 2 производится по наружному каналу Н имеющему вид зазора между стенками отверстия в заготовке 1 и наружной поверхностью инструмента отвод СОТС вместе со стружкой - через окно С внутрь инструмента и далее по его внутреннему каналу В.
Во втором случае (pис. 1.4б) СОТС подводится по внутреннему каналу В в инструменте 2 а отводится вместе со стружкой по наружному каналу Н.
Рисунок 1.4 – Способы подвода СОТС и отвода стружки при сверлении.
Выбираем конструкцию режущих пластин [3].
Для сверла 31мм выбираем режущие треугольные пластины производства фирмы “SANDVIK Coromant” TCMT 090204 -MF где Т- форма пластины треугольная; C- параметр указывающий на величину заднего угла α=7°; М- класс точности пластины; Т- параметр обозначающий тип фиксации пластины - односторонняя пластина с отверстием; 09- значение размера пластины – диаметр вписанной окружности - 556 мм; 02- толщина пластины 238 мм; 04- радиус при вершине 04мм MF – обозначение стружколома (рис.1.5). Марка сплава пластины – 1025.
Рисунок 1.5 – Пластина TCMT 090204 – MF
Для получения отверстия 195Н10 выбираем пластинки
LCMX 040308 T-53 где L- форма пластины прямоугольная; C- параметр указывающий на величину заднего угла α=7°; М- класс точности пластины; X- односторонняя пластина с отверстием; 04- ширина режущей кромки 4мм; 03- толщина пластины 318 мм; 08- радиус при вершине 08мм Т- параметр указывающий тип режущей кромки.
Рисунок 1.6 – Пластина LCMX 040308 T-53
Выбираем метод крепления пластин винтом с тороидальной головкой в специально подготовленных базовых поверхностях под пластины со смещением резьбового отверстия под винт (см. рис.18) [4].
Определим координаты центра отверстия под винт для установки пластины (рис.1.7).
Рисунок 1.7 – Схема для расчета координат центра отверстия под винт
где R- радиус описанной окружности: для трехгранных пластин
для пластин других форм - ;
md – размеры пластины [17];
b – вылет пластины из гнезда;
– угол при вершине пластины.
Для пластины TCMT 090204 –MF: m=794мм b=08мм =30°.
В связи с нестандартным строением пластины LCMX 040308 T-53 параметры гнезда определим геометрической прорисовкой с использованием САD – систем.
Выбираем конструкцию сверла. Выбираем сверло основываясь на уже существующие разновидности твердосплавных сверл разработанных фирмой “SANDVIK Coromant” (рис.1.10). Габаритные и конструктивные параметры выбираем по каталогу “SANDVIK Coromant”[3]. Аналог проектируемому сверлу сверло ф. “SANDVIK Coromant” – сверло комбинированное типа R416.21.
Принимаем цилиндрический хвостовик с лыской по ISO 9766 (ГОСТ 28706-90) (см. рис.1.8).
Рисунок 1.8 – Хвостовик по ГОСТ 28706-90.
Проверим перекрытие пластин.
Ширина пластины LCMX 040308 T-53 – 8мм. Суммарная ширина пластин должна быть больше радиуса обрабатываемого отверстия: 975мм 16мм - условие выполняется.
Ширина металла который необходимо снять при рассверливании отверстия 195мм до 31 мм – 575мм. Ширина пластины TCMT 090204 -MF -9мм. Условие выполняется.
Пластины в корпусе сверла расположим исходя из условий перекрытия.
Так как глубина отверстия 50мм а режущие пластины должны полностью выйти из отверстия то принимаем расстояние между вершинами пластин равным 34мм. Длину рабочей части сверла из конструктивных соображений принимаем 95мм.
Выбираем материал сверла: для корпуса – сталь 40Х по ГОСТ 4543-71 твердость 42 46 для пластины – твердый сплав Т5К10 по ГОСТ 3882-74 (аналог CU45) [4]; для винта сталь 45 по ГОСТ 1050-88 твердость 32 37 HRC.
Технические требования на сверло принимаем по ГОСТ 27724-88.
Рисунок 1.9 – Крепление пластин в сверле Coromant U для обарботки ступеньчатых отверстий под винты
Рисунок 1.10 – Сверло Coromant U для обарботки ступеньчатых отверстий под винты
Сменные неперетачиваемые пластины закреплены в специально подготовленных гнездах на переднем торце сверла и на расстоянии 34мм необходимом для сверления отверстия 31мм. Одна из пластин располагается у оси сверла другая - на периферии. Крепятся пластины при помощи винтов.
Припуск снимаемый сверлом с СНП делится по ширине между взаимно перекрывающимися пластинами которые располагаются в корпусе таким образом что радиальная нагрузка с обеих сторон от оси свела сбалансирована. При этом отпадает необходимость в предварительном засверливании отверстия или использования кондукторной втулки.
Образование стружки с формой и размерами позволяющими легко удалять ее из отверстия является первоочередным вопросом при рассмотрении любой операции сверления. Без удовлетворительной эвакуации стружки работа сверла станет невозможной вследствие забивания стружечных канавок и закупоривания сверла внутри отверстия. Большинство коротких сверл имеет две стружечных канавки для эвакуации стружки. Современное оборудование и инструмент позволяют осуществлять подвод СОЖ по внутренним каналам в сверле через которые она поступает непосредственно в зону резания уменьшая действие сил трения и вымывая стружку из отверстия. Применение современных сверл со сменными пластинами позволяет вести обработку с высокими скоростями и большими объемами образующейся стружки которая вымывается из отверстия потоками охлаждающей жидкости подающейся под определенным давлением по внутренним каналам.
Стуржкообразование зависит от типа обрабатываемого материала геометрии инструмента режимов резания схемы срезания припуска и в некоторой степени от выбранной охлаждающей жидкости. Обычно более мелкая стружка образуется при увеличении подачи иили уменьшении скорости резания (образование и эвакуация стружки см. рисунок 1.11).
Рисунок 1. 11 – Образование и эвакуация стружки подвод СОТС
Информационно-патентный поиск по конструкциям инструментов аналогичных проектируемому см. приложение А.
На рисунке 1.12 показаны схемы срезания припуска при сверлении.
Рисунок 1.12 – Схемы срезания припуска при: а) сверлении спиральным сверлом б) рассверливании в) сверлении комбинированным сверлом со сменными неперетачиваемыми пластинами.
Технические требования.
Твердость корпуса сверла – 38 45 НRCэ.
Допуск плоскостности опорной поверхности гнезда под пластину – 003мм.
Зазор между опорной поверхностью гнезда и опорной поверхностью пластины не допускается.
При сборке сверла на резьбовые соединения нанести смазку ЦИАТИМ-203 по ГОСТ 8773-73.
Смещение вершины наружной пластины образованной главными режущими кромками в сторону хвостовика относительно вершины внутренней пластины должно быть не более 02мм.
Нижние опорные поверхности пластин не должны выступать за пределы корпуса более чем на 02мм.
Момент затяжки винтов – 09Нм.
Испытание сверла на работоспособность средний и 95% - ный периоды стойкости провести на токарныо станке с ЧПУ. Испытания произвести на образцах из стали 45 по ГОСТ 1050-88. Режимы испытания по ГОСТ 27724-88.
При испытании сверла на работоспособность на режущих кромках пластин не должно быть выкрашиваний. Сверло должно быть пригодно к работе.
Смещение оси отверстия гнезда под пластину относительно оси отверстия в пластине – 15мм.
Покрытие – хим. окс. промышеленное по ГОСТ9.306-85.
Таблица к шлиц. протяжке.docx
Продолжение таблицы
Чистовые и калибрующие круглые
Расчет корригированного профиля фасочных и шлицевых прямобочных зубьев.
Для расчета корригированного бокового профиля шлицевых прямобочных зубьев из таблицы диаметров зубьев назначаем номера первого (NA=46) и последнего (NE=90) черновых зубьев на расчетном участке радиусы этих зубьев RA=3137 мм и RE=3577 мм. Для расчета используем также ширину паза b=125 мм шаг черновых зубьев t0=14 мм. Задаемся вспомогательным углом в плане: φ1=3º.
Подъем заднего центра С на длине протяжки и половину угла корригированного бокового профиля зубьев и шлифовального круга к:
Для расчета подъема заднего центра С размеров для контроля бокового профиля фасочных зубьев НА и НВ назначаем номера первого NА=23 и последнего NЕ=37 фасочных зубьев и радиусы этих зубьев Rа=2992 мм и Rе=3137 мм значение угла фаски ф и корригированного угла фаски к принимаем для числа шлицев z=8: ф=47º к =45º (табл.П34 с.227 [16]).
Другие данные участвующие в расчете следующие: b=125 мм с=05 мм d=62 мм.
Расчет производим по формулам:
Шлифование бокового профиля фасочных зубьев производим профильным шлифовальным кругом с к=67º30' (табл.П34 с.227 [16]). Следовательно
Длина расчетного участка:
Корригированный угол профиля фасочных впадин на протяжке 2к=135º (табл.П34 с.227 [16]).
Для черновых зубьев: фасочных круглых и шлицевых
Для чистовых зубьев круглых и шлицевых .
Реферат.docx
Представлены результаты информационно-патентного поиска.
Графическая часть проекта состоит из рабочего чертежа инструментальной наладки рабочих чертежей спроектированных инструментов.
Титульник.doc
Белорусский национальный технический университет
Кафедра "Металлорежущие станки и инструменты
по дисциплине «Проектирование инструментальных систем. Управление качеством и сертификация»
на тему «Разработать инструментальную наладку и комплект
режущих инструментов»
Специальность 1 - 36 01 03 «Технологическое оборудование машиностроительного производства»
Специализация 1 – 36 01 03 02 «Инструментальное производство»
Исполнитель: студент
ПОЯСНИТЕЛЬНАЯ ЗАПИСКА
Разработка конструкции сверла комбинированного с СНП с внутренним подводом СОТС8
Проектирование шлицевой протяжки13
1 Анализ исходных данных13
1.1 Цели и задачи проектирования13
1.2 Протягивание шлицевых отверстий13
1.3 Геометрические элементы зуба протяжки15
1.4 Схема резания при протягивании15
1.5 Расчет протяжки17
Разработка инструментальной наладки33
1 Выбор оборудования и маршрутной технологии обработки33
2 Выбор основного инструмента 33
3 Выбор вспомогательного инструмента37
4. Расчет режимов резания40
4. Расчет наладочных размеров. Описание методов наладки
инструментов вне станка.42
Список использованной литературы49
ПРИЛОЖЕНИЕ А. Информационно-патентный поиск по
конструкциям инструментов аналогичных проектируемым и
методам их расчета50
Информационно-патентный поиск по конструкциям инструментов аналогичных проектируемым и методам их расчета.
В данном разделе произведен информационно-патентный поиск по конструкциям и методам расчета дисковых шеверов и червячных зуборезных шлицевых фрез. Собранная информация (патенты статьи обзоры каталоги) представлена далее.
Протяжка шлицевая, z=8.DWG

*Размеры для справок 2. Остальные ТТ по СТБ 1014-95.
ТП99-038001 - изображено ТП99-038001-01 - зеркальное отражение
В (4:1) остальное вид Б
Г(4:1) пластина условно не показана
Условно показано без пластин и крепежного винта
Материал корпуса сверла - 40Х по ГОСТ 4543-71. 2. Твердость корпуса сверла - 38 45HRCэ. 3. Допуск плоскостности опорной поверхности гнезда под пластину - 0
мм. 4.Зазор между опорной поверхностью гнезда и опорной поверхностью пластины не допускается. 5.Покрытие: хим. окс. промышленное по ГОСТ 9.306-85. 6.При сборке сверла на резьбовые соединения нанести смазку ЦИАТИМ-203 по ГОСТ 8773-73. 7.Смещение вершины наружной пластины
образованной главными режущими кромками в сторону хвостовика относительно вершины внутренней пластины должно быть не более 0
мм. 8.Нижние опорные поверхности пластин не должны выступать за пределы корпуса более чем на 0
мм. 9.Маркировать товарный знак предприятия-изготовителя
диаметр сверла. 10.Момент затяжки винтов поз.4 - 0
Н·м. 11.Испытание сверла на работоспособность
средний и 95%-ный периоды стойкости провести на токарном станке с ЧПУ. Испытания произвести на образцах из стали 45 по ГОСТ 1050-88. Режимы испытания по ГОСТ 27724-88. При испытании на работоспособность сверлом должно быть просверлено не менее пяти овтерстий на глубину 1
диаметра сверла. После испытания сверла на работоспособность на режущих кромках пластин не должно быть выкрашиваний. Сверло должно быть пригодно к работе. 12. Подвод СОТС через отверстия в корпусе сверла. Давление СОТС - 0
объем - 2лмин. 13.*Смещение оси отверстия гнезда под пластину относительно оси отверстия в пластине - 1
Сверло комбинированное
БНТУ.303536.675.01.00СБ
Пластина LCMX 040308-T-53
Пластина TCMT 090204-MF
Винт крепежный (специальный) M3
БНТУ.303536.675.01.01
Протяжка шлицевая - рамка.DWG

хвостовика - сталь 40Х ГОСТ 4543-71. 2. 63 66 HRC режущая часть; 61 66 HRC - направление
47 HRC - хвостовик. 3. Общие допуски по ГОСТ 30893.1-2002. 4.* Размер для справок. 5. Допуск радиального биения зубьев №38 45 и №95 98 - 0
мм. На остальной части протяжки - 0
мм. Биение зубьев допускается только одностороннее. 6. Накопленная погрешность окружного шага шлиц не более 0
6мм. 7. При шлифовании боковых поверхностей фасочных зубьев с № 23 по № 37 задний хвостовик поднять. Величина подъема - 1
мм на длине 1835мм. 8.При шлифовании боковых поверхностей шлицев с № 47 по № 89 задний хвостовик поднять. Величина подъема - 0
мм на длине 1835мм. 9. Допустимое отклонение окружного шага шлицев не более 0
мм. 10. Отклонение от параллельности боковых поверхностей зубьев относительно оси центров на длине шлицевой части не более 0
5мм. 11. Отклонение от симметричности зуба относительно оси центров в поперченом сечении не более 0
мм. 12. Маркировать обозначение
товарный знак предприятия - изготовителя
дату выпуска. 13. Остальные ТТ по ГОСТ7943-56.
Протяжка шлицевая D8-62 x72 12
Материал детали сталь 45
Длина протягиваемого овтерстия L=65мм
Усилие протягивания Pmax=156960Н
Коэффициент вмещаемости стружки К=2
3 РАЗРАБОТКА ИНСТРУМЕНТАЛЬНОЙ НАЛАДКИ - вариант №2-1.docx
1 Выбор оборудования и маршрутной технологии обработки
Исходными данными для разработки инструментальной наладки является чертеж детали (рис.3.1) и ее характеристики.
Материал детали – сталь легированная 18ХГ с НВ=1870 2410МПа.
Тип оборудования – токарный вертикальный станок с ЧПУ инверторного типа.
Выбираем токарный вертикальный станок с ЧПУ инверторного типа 1В640Ф3.
Заготовка – штамповка.
Рисунок 3.1 – Обрабатываемая деталь
Заготовку обрабатываем в следующей последовательности приведенной в таблице 3.1.
Таблица 3.1- Маршрут обработки
Точение наружной поверхности 75-016 мм с подрезкой торца и обработкой фаски 2х45°. Точение наружной поверхности 115-03
Сверление отверстия 25 на проход
Снятие фаски 2х45° в отверстии 25
Сверление отверстий под резьбу 670+026 l=25мм
Нарезание резьбы М8-7Н на длине l=20мм
Сверление отверстия 12+011 на проход
Цекование 17 на длине l=10±0075мм
2Выбор основного инструмента
Вспомогательный инструмент токарных станков должен обеспечивать крепление резцов сверл (с коническим и цилиндрическим хвостовиками) зенкеров разверток метчиков и плашек и удовлетворять следующим требованиям: быть достаточно жестким; иметь высокую точность и стабильность базирования и крепления режущего инструмента; позволять выполнять все технологические операции предусмотренные технической характеристикой станка; легко и быстро устанавливаться и сниматься; иметь межразмерную унификацию; обеспечивать настройку инструмента вне станка [15].
Для точения поверхностей 115мм 75мм подрезки торца и обработки фаски 2х45° принимаем резец SCLCR 2020K 09 фирмы Sandvik Coromant (S – система крепления – крепление пластин винтом С – форма пластины ромбическая 80° L – буква обозначающая тип державки с главным углом в плане 95° С– буква обозначающая значение заднего угла пластины - 7° R – ориентация правая 2020 – цифры обозначающие размер державки (высота × ширина мм) К – длина инструмента L=125мм 09 – цифры обозначающие размер пластины – диаметр вписанной окружности 9525мм) [3] с пластиной CСMT 09Т308 (С – форма пластины ромбическая 80° N - буква обозначающая задней угол пластины - 7° M - буква обозначающая класс допуска пластины T - буква обозначающая тип фиксации и стружколома – с отверстием отверстие цилиндрическое стружколом двухсторонний 09 - буква обозначающая размер пластины – диаметр вписанной окружности – 9525мм Т3 - буква обозначающая толщины пластины – 397мм 08 - буква обозначающая радиус при вершине пластины – 08мм).
Для сверления отверстия 25мм принимаем сверло SANDVIK R416.2 0250L25-31 с твердосплавными пластинами LCMX 040308 (L – форма пластины C – задний угол -7° M – класс допуска пластины Х – специальные характеристики резания и крепления – специальная конструкция 04 – размер пластины – длина режущей кромки 4мм 03 – толщина пластины – 318мм 08 – радиус при вершине – 08мм) (винт М25) (рис.3.2). Такое сверло позволяет вести обработку отверстия за один проход и получить точность отверстия по 9-10 квалитету точности [3].
Для зенкования фаски 2х45° принимаем зенковку коническю бысторежущую из стали Р6М5 с коническим хвостовиком 2353-0138 по ГОСТ 14953-80 D=50мм L=60мм (рис.3.3) [5].
Для сверления отверстия 675+026мм принимаем сверло спиральное комбинированное 68мм Coro Drill Delta-C R841-0675-30-A1A (SANDVIK) с цилиндрическим хвостовиком и внутренним подводом СОТС (рис.3.4). С помощью этого инструмента обрабатывается отверстие и фаска за один проход [3].
Для нарезания резьбы М8-7Н в отверстии принимаем метчик машинный 2620-1223 ГОСТ 3266-81 из стали Р6М5 (рис.3.5) [7].
Для сверления отверстия 12 принимаем сверло SANDVIK R411.5-12034D12.00 с твердосплавной вставкой (рис.3.6) что повышает производительность сверления [3].
Для обработки ступенчатого отверстия 17 l=10±0075мм принимаем фрезу AQXR174SA16S так как стандартной цековки 17 нет (AQX – тип фрезы – концевая с твердосплавными пластинами R – направление работы правое 17 – диаметр рабочей части (мм) SA – тип хвостовика – цилиндрический 16 – диаметр хвостовика S – серия хвостовика – короткая) с пластинами QOMT0830R-M2 (Q – форма пластины (специальная конструкция) O – задний угол (специальная конструкция) M – класс допуска пластины Т – способ фиксации и особенности стружколома – пластина с отверстием стружколом односторонний 08 – размер пластины (см. рис.3.8) 30 – толщина пластины – 3мм R – направление резания правое М2 – тип стружколома) [8].
Таблица 3.2 – Режущий инструмент
Резец SCLCR 1616H 09
Пластина CNMG 09Т308 (марка сплава 4215)
Сверло SANDVIK R416.2 0250L25-31
Пластина LCMX 040308 (марка сплава 1020)
Зенковка 2353-0138 по ГОСТ14953-80
Сверло комбинированное 675мм Coro Drill Delta-C R841-0675-30-A1A (SANDVIK) (марка сплава 1220)
Метчик 2620-1223 ГОСТ 3266-81
Сверло SANDVIK R411.5-12034D12.00 (марка сплава Р20)
Фреза AQXR174SA16S D=17мм
QOMT0830R-M2 (марка сплава F7010)
Рисунок 3.2 – Резец SCLCR 2020К 09
Марка сплава пластины см. табл.3.2.
Рисунок 3.3 – Сверло SANDVIK R416.2 0250L25-31
Марка сплава пластины см. табл. 3.2.
Рисунок 3.4 – Зенковка 2353-0138 ГОСТ14953-80
Рисунок 3.4 – Сверло комбинированное 675мм Coro Drill Delta-C R841-0675-30-A1A (SANDVIK)
Марка сплава – 1220.
Рисунок 3.5 – Метчик машинно-ручной 2620-1223 ГОСТ 3266-81
Рисунок 3.6 - Сверло SANDVIK R411.5-12034D12.00
Рисунок 3.7 - Фреза AQXR174SA16S
Рисунок 3.8 – Пластина QOMT0830R-M2 к фрезе AQXR174SA16S
Марка сплава – F7010.
3Выбор вспомогательного инструмента
Вспомогательный инструмент выбираем из условия базирования в отверстиях 40мм инструментального диска револьверной головки (крепление резцедержателей с системой зажима в соответствии с DIN69880).
В качестве вспомогательного инструмента при точении детали (переход №1) применяем державку B3-40×25×44 DIN69880 (рис.3.9) [12].
Рисунок 3.9 – Радиальная оправка В3-40х25х44
Для крепления сверла Сверло SANDVIK R416.2 0250L25-31 принимаем
оправку для сверл Е1-40х25х71[12].
Рисунок 3.10 – Оправка для сверл Е1-40х25х71
Для крепления зенковки принимаем держатель F1 для инструмента с конусом Морзе 3 F1 40xMK3.
Рисунок 3.11 – Держатель для инструмента с конусом Морзе 3 F1 40хMK3
Так как ступенчатое отверстие и отверстие под резьбу находятся эксцентрично оси детали то для их изготовления необходимо иметь вращательное движение инструмента. Таким образом для закрепления сверла комбинированного 2310-0025 сверла SANDVIK R411.5-12034D12.00 и фрезы AQXR174SA16S применяем приводной инструмент – аксиальный сверлильно-фрезерный держатель DA40548032 (Канада) с цангой ER32 [13].
Рисунок 3.12 – Аксиальный сверлильно-фрезерный держатель DA40548032
Рисунок 3.13 – Цанга ER32470E к держателю THC-A02-40B
Для закрепления метчика принимаем так же аксиальный сверлильно-фрезерый держатель DA40548032 с цангой ER 32. Так как в современных станках с ЧПУ появилась возможность синхронизировать вращение метчика и подачу детали при нарезании резьбы то от предохранительных головок можно отказаться что существенно снижает стоимость инструментальной наладки.
Рассмотрим конструкцию прямой головки для вращающегося инструмента с цанговым патроном (рис. 3.14) [15].
Рисунок 3.14 – Прямая головка для вращающегося инструмента с цанговым патроном
В головке могут закреплятся режущие инструменты с диаметром хвостовика до 20мм. Головка состоит из корпуса 2 и шпинделя 1 установленного в подшипниках 3-5 натяг которых обеспечивается пружинящей гайкой 8. Уплотнение подшипника 3 со стороны рабочей зоны осуществляется манжетой 9 расположенной в крышке 10. Регулирование осевого положения муфты 7 через которую передается крутящий момент производится с помощью гайки 6. Для закрепления режущих инструментов с цилиндрическим хвостовиком (фрез сверл) используются унифицированные элементы: гайка 13 цанга 12 и регулировочный винт 11 СОЖ подается в зону резания с помощью сопла 14.
4Расчет режимов резания
Расчет режимов резания при нарезании резьбы М8-7Н на l=20мм (переход №5).
Материал заготовки: сталь 18ХГ с НВ=1870 2410МПа.
Инструмент – метчик машинный.
Материал метчика – быстрорежущая сталь Р6М5.
)Подача на оборот принимается равной шагу резьбы. Для резьбы М8 стандартный шаг равен 125мм. Таким образом
)Стойкость инструмента:
– коэффициент учитывающий количество инструментов в наладке: .
Глубина резания принимается примерно равной 05 шага резьбы:
Определим длину рабочего хода:
где y и - врезание и перебег y=30мм Δ=0мм.
где по табл.49 [9] m=09 y=05.
Общий поправочный коэффициент на скорость резания:
где – коэффициент на обрабатываемый материал;
коэффициент зависящий от материала инструмента по табл.50 [9]
- коэффициент зависящий от точности резьбы по табл. 50 стр.298 [9]
где Kr – коэффициент характеризующий группу стали по обрабатываемости; Kr=07 (для хромомарганцовистой стали) (9 с.262 табл.2);
- предел прочности материала МПа;
– показатель степени.
)Частота вращения шпинделя:
Принимаем n=600 мин-1.
где по табл.51 [9]; g=14; y=15; .
Расчет режимов резания при сверлении отверстий.
Материал заготовки: сталь 18ХГ НВ=1870 2410МПа. Инструмент – сверло SANDVIK R416.2 0250L25-31. Материал режущей части сверла – твердый сплав.
Расчет режимов резания при сверлении отверсти 25мм.
Глубина отверстия L=58мм.
Расчет производим при помощи электронного ресурса удаленного доступа размещенного на сайте [10]. Результаты расчета приведены в таблице 3.3.
Таблица 3.3 – Режимы резания при сверлении отверстия 25мм
Расчет режимов резания при сверлении 12мм. Сверло SANDVIK R411.5-12034D12.00. Глубина отверстия L=25мм.
Расчет производим при помощи электронного ресурса удаленного доступа размещенного на сайте [10].
Результаты расчета приведены в табл.3.4.
Таблица 3.4 – Режимы резания при сверлении отверстия 12мм
Остальные режимы резания выбираем по таблицам приведенным в нормативах [11].
Полученные результаты расчетов режимов резания сводим в таблицу 3.5.
Таблица 3.5 – Режимы резания
Наименование операции
Зенкование фаски 2×45°
Сверление отверстия под резьбу 670+026 l=25мм
Нарезание резьбы М8-7Н l=20мм
Сверление отверстия 12+011
Фрезерование отверстия 17мм l=10±0075мм
5Расчет наладочных размеров. Описание методов наладки инструментов вне станка [14]
Предварительная настройка инструмента вне станка обеспечивает значительное сокращение его простоев благодаря совмещению подготовительно-заключительного времени затрачиваемого на переналадку станка и вспомогательного времени затрачиваемого на замену и поднастройку инструмента с временем работы станка. Предварительная настройка инструмента проводится независимо от конкретной программы. Для этого регламентируются координатные размеры вершин режущей кромки инструмента. Приборы для предварительной настройки инструмента к станкам с ЧПУ по сравнению со специальными приспособлениями для настройки инструментов на агрегатных станках и станках-автоматах должны обладать большей универсальностью и гибкостью т.е. возможностью быстрой переналадки для настройки различных инструментов.
Станки с ЧПУ являются высокоточными автоматизированными станками. Основной предпосылкой обеспечивающей достижимую точность обработки на этих станках является точность предварительной настройки инструмента. Следовательно приборы для предварительной настройки инструмента должны обеспечивать высокую точность настройки инструментов на размер по одной или нескольким координатам. С этой целью базирующие элементы приспособлений должны строго соответствовать базирующим элементам станков предназначенным для установки вспомогательного инструмента.
Зарубежные производители предлагают широкий выбор приборов для размерной настройки инструмента отличающихся степенью автоматизации от самых простых типа «Toolset 350» (рис.3.15) фирмы «Innotool» (Австрия) до приборов очень сложных и насыщенных автоматикой.
Рисунок 3.15 – Установка для размерной настройки инструмента вне станка ”Toolset 350”
Так фирма KELCH (Швейцария) предлагает серию приборов KALIMAT (рис.3.16):
a) «KALIMAT-a» с наибольшей степенью автоматизации;
б) «KALIMAT-e» экономичного класса;
в) «KALIMAT-c» компактный прибор.
Рисунок 3.16 - Установка для размерной настройки инструмента вне станка фирмы KELCH
Фирма «ГАЛИКА» (г. Москва) - представитель швейцарских фирм в России поставляет приборы фирмы «ZOLLER» моделей «smile 500» (рис.3.17) «venturion 400500» (рис.3.18) и ряд других.
Эти приборы имеют шпиндели повышенной точности с радиальным биением менее 2 мкм при повторяемости положения инструментов в шпинделе в пределах 1 мкм. Приборы имеют пневматический зажим салазок для обеих осей электронную тонкую настройку кнопку управления одной рукой сенсорную клавиатуру для проведения операций зажима и разжима инструмента. Телевизионная камера с самофокусирующимся объективом и программным обеспечением для измерений и настройки любых инструментов автоматически распознает формы режущих кромок и показывает режущую кромку на цветном мониторе 17" с 35-кратным увеличением.
Рисунок 3.17 - Установка для размерной настройки инструмента вне станка zoller - smile 500
Рисунок 3.18 - Установка для размерной настройки инструмента вне станка venturion 400500
По заказу в комплект прибора может быть включен принтер для распечатки результатов измерений.
Автоматизированная настройка инструмента непосредственно на станке путем измерения отклонения размеров инструмента с учетом погрешностей его установки позволяет передать в систему ЧПУ требуемые коррекции положения инструмента. При этом отпадает необходимость в точной предварительной настройке инструмента на приборах поскольку предварительная настройка необходима лишь в пределах нескольких миллиметров.
Для автоматического измерения инструмента непосредственно на станках применяют измерительные щупы-датчики касания (с дискретным сигналом). Датчики могут быть установлены на корпус передней бабки токарного станка (рис. 3.19 а) выполнены выдвижными перемещаемыми в рабочую позицию на точных направлениях (рис. 3.19 б и в) либо откидными установленными на откидном рычаге (рис 3.19 г).
После поворота револьверной головки перед началом обработки режущая кромка каждого резца по программе подводится к щупу датчика для автоматического измерения в зоне обработки. Щуп посредством кабеля через интерфейс соединен с УЧПУ
станка. В момент касания режущей кромки инструмента с щупом возникает электрический сигнал воспринимаемый УЧПУ. Перед началом работы станка измерительный щуп калибруется в автоматическом цикле посредством эталонного инструмента для определения действительного расстояния между точкой отсчета станка и щупом. При настройке инструмента щуп прямоугольной формы фиксирует фактическое положение режущей кромки инструмента которое сопоставляется в УЧПУ с заданным в программе после чего рассчитывается необходимая коррекция позиционирования режущей кромки инструмента. Повторное измерение инструмента позволяет вносить коррекцию его положения.
Рисунок 3.19 – Схемы установки датчиков касания на токарных станках
Для автоматической настройки инструмента на токарных станках может быть использован метод АТС (Automatic Toll Calculation) - метод автоматического расчета установочных размеров инструмента. При применении этого метода инструменты в револьверной головке токарного станка могут быть установлены произвольно.
С помощью электронного маховика инструменты револьверной головки последовательно устанавливаются под перекрестием расположенной в зоне работы инструментов оптической системы которая находится в заданной точке координатной системы станка (рис. 3.20). Координаты перекрестия оптической системы в качестве параметра станка хранятся в памяти системы управления что позволяет автоматически рассчитывать установочные размеры инструментов. Эти размеры передаются в систему управления для коррекции программы при определении траектории режущих кромок. Этот метод обеспечивает точность позиционирования 002 мм по диаметру.
Рисунок 3.20. Схема автоматической настройки инс трумента на токарных станках с ЧПУ
Для автоматической настройки инструмента на многооперационных станках измерительное устройство устанавливают на столе станка вне рабочей зоны. Перед началом обработки стол станка и шпиндельная бабка по программе выводятся в положение при котором соответствующий режущий инструмент доводится до касания с щупом датчика измерительного устройства выдающим сигнал указывающий положение вершины режущей кромки относительно начала отсчета. Разность между фактическим положением режущей кромки и заданным положением определяет величину необходимой коррекции. Оценка полученной информации с помощью микропроцессора обеспечивает формирование корректирующего сигнала. Схема контроля положения режущей кромки сверла показана на рис. 3.21 а.
На рис. 3.21 б показана схема измерения длины сверла посредством щупа 2 пневматической головки 3 на рис. 3.21 в - схема измерения длины вылета режущей кромки расточного резца посредством щупов 3 и 2 пневматических головок 4. Щупы под давлением сжатого воздуха выдвинуты. При контактировании инструмента с щупом головки создаются два точно повторяемых электрических сигнала соответствующих допуску ±1 мкм.
Рисунок 3.21 – Схемы установки датчиков касания на многооперационных станках
Измерение координат режущего инструмента с помощью лазера основано на том что луч совмещенный с осью проходящей через центр фотоэлемента сфокусирован в общей точке пересечения; линза концентрирует на фотодетекторе луч отраженный от детали. Фотоэлемент определяет положение фокальной точки в трех положениях: перед режущей кромкой за ней или непосредственно на ее вершине. Далее излучатель перемещается таким образом чтобы фокальная точка совместилась с вершиной режущей кромки. Оптический прибор выполненный на основе лазера может обеспечивать контроль геометрических параметров инструмента его износ и выход из строя непосредственно в процессе обработки. Данные измерения используются для управления положением инструмента с помощью обратной связи. В приборах используют модулированные лазерные источники малой мощности на основе гелийнеоновой смеси.
Лазерная система мод. NC4 фирмы Renishaw (Великобритания) для настройки инструмента благодаря использованию сверхкомпактных излучателей и приемников (диаметр 30 мм высота 35 мм) позволяет выполнять скоростную бесконтактную настройку инструмента и определять его выход из строя практически на любых станках.
Система NC4 обеспечивает высокую повторяемость настройки инструмента при расстоянии между излучающим и приемным блоками системы до 5 м (рис. 3.22). В зависимости от этого расстояния возможно измерение режущих кромок малогабаритного инструмента диаметром до 02 мм а также определение поломки инструмента с размером вплоть до 005 мм
Система NC4 имеет класс защиты IPX8 что позволяет использовать ее в самых неблагоприятных производственных условиях. Для обеспечения защиты от попадания стружки графита и СОЖ (в том числе и в процессе выполнения измерений) используется постоянный обдув сжатым воздухом. Даже в случае перебоя в подаче воздуха герметизирующее устройство предотвращает попадание грязи внутрь системы.
Независимо от расстояния между излучающим и приемным блоками в них устанавливаются источник и приемник излучения одних и тех же типов. Перенастройка на другое расстояние между блоками осуществляется путем замены одной и той же детали в источнике и приемнике излучения.
Настройка системы достаточно проста так как нет необходимости в определении фокальной точки лазерного пучка.
Полностью совместимая с комплексом программ Renishaw позволяющих осуществлять всесторонний контроль инструмента система NC4 имеет очень короткое время отклика системы (10 мкс) что существенно важно для точного измерения быстро вращающегося инструмента (до 10 000 мин!).
Renishaw выпускает несколько модификаций системы NC4 с расстоянием между излучающим и приемным блоками от 40 до 450 мм а также раздельные системы расстояние между блоками которых может достигать 5 м.
Рисунок 3.22 – Лазерная система NC4
Траектории движения инструмента
Правильный выбор траекторий движения режущих инструментов позволяет сократить машинное время обработки и количество инструментов в наладке.
Токарную операцию обычно начинают с черновой обработки которая содержит несколько прямолинейных черновых проходов выполняемых вдоль оси детали перпендикулярно или под углом к ней с постоянной по возможности глубиной резания. После каждого прохода инструмент отводится в исходное положение (рис.3.23).
Рисунок 3.23 – Отвод резца перпендикулярно к оси детали (а) под углом к ней (б) и параллельно профилю (в)
Если деталь имеет несколько ступеней то припуск условно делится на зоны (перпендикулярно к оси детали) и уровни. В результате образуется определенное число элементарных участков каждый из которых можно обозначить двумя цифрами: первая – номер уровня вторая – номер зоны. Варианты удаления припуска при черновой обработке приведены на рис. 3.24 [9].
В данном курсовом проекте рассматривается обработка на токарном станке с ЧПУ инверторного типа. В нашем случае инструмент неподвижен а все траекторные движения осуществляет шпиндельная бабка с зажатой в патроне деталью.
Рассмотрим траекторию движения детали на токарной операции. В нашем случае целесообразно организовать программу обработки детали по схеме 1 (рис.3.24 а) так как при данной схеме обработки и высоких скоростях резания которые может обеспечить система ЧПУ станка получится наиболее оптимальный по времени вариант съема припуска. На рис. 3.25 показана схема срезания припуска детали «Крышка» заданной в курсовом проекте.
Рисунок 3.24 – Последовательность удаления припуска по уровням и зонам:
а – 1-1 1-2 1-3 2-1 2-2 3-1; б – 1-1 1-2 2-1 3-1 2-2 1-3; в – 1-1 2-1 3-1 1-2 2-2 1-3
Рисунок 3.25 – Схема срезания припуска детали «Крышка».
Сверло комбинированное.DWG

*Размеры для справок 2. Остальные ТТ по СТБ 1014-95.
ТП99-038001 - изображено ТП99-038001-01 - зеркальное отражение
В (4:1) остальное вид Б
Г(4:1) пластина условно не показана
Условно показано без пластин и крепежного винта
Материал корпуса сверла - 40Х по ГОСТ 4543-71. 2. Твердость корпуса сверла - 38 45HRCэ. 3. Допуск плоскостности опорной поверхности гнезда под пластину - 0
мм. 4.Зазор между опорной поверхностью гнезда и опорной поверхностью пластины не допускается. 5.Покрытие: хим. окс. промышленное по ГОСТ 9.306-85. 6.При сборке сверла на резьбовые соединения нанести смазку ЦИАТИМ-203 по ГОСТ 8773-73. 7.Смещение вершины наружной пластины
образованной главными режущими кромками в сторону хвостовика относительно вершины внутренней пластины должно быть не более 0
мм. 8.Нижние опорные поверхности пластин не должны выступать за пределы корпуса более чем на 0
мм. 9.Маркировать товарный знак предприятия-изготовителя
диаметр сверла. 10.Момент затяжки винтов поз.4 - 0
Н·м. 11.Испытание сверла на работоспособность
средний и 95%-ный периоды стойкости провести на токарном станке с ЧПУ. Испытания произвести на образцах из стали 45 по ГОСТ 1050-88. Режимы испытания по ГОСТ 27724-88. При испытании на работоспособность сверлом должно быть просверлено не менее пяти овтерстий на глубину 1
диаметра сверла. После испытания сверла на работоспособность на режущих кромках пластин не должно быть выкрашиваний. Сверло должно быть пригодно к работе. 12. Подвод СОТС через отверстия в корпусе сверла. Давление СОТС - 0
объем - 2лмин. 13.*Смещение оси отверстия гнезда под пластину относительно оси отверстия в пластине - 1
Сверло комбинированное
БНТУ.303536.675.01.00СБ
Пластина LCMX 040308-T-53
Пластина TCMT 090204-MF
Винт крепежный (специальный) M3
БНТУ.303536.675.01.01
Введение.docx
Развитие машиностроения тесно связано с совершенствованием конструкций технологических машин металлорежущих станков и в частности режущего инструмента.
От качества надёжности и работоспособности режущих инструментов применяемых в машиностроении в значительной степени зависит качество и точность детали её шероховатость производительность и эффективность процесса обработки в особенности в наше время при использовании инструмента в автоматизированном производстве в условиях гибких производственных систем.
Данный курсовой проект включает в себя разделы по разработке инструментальной наладки детали расчёты режимов резания выбора режущего инструмента проектирование режущего инструмента.
Графическая часть проекта состоит из рабочего чертежа инструментальной наладки рабочих чертежей спроектированных инструментов.
Наладка инструментальная.dwg

Sandvik R416.2 0250L25-31
E1-40x25x71 (DIN 69880)
F1 40 x MK3 (DIN 69880)
Delta-C R841-0675-30-A1A
Sandvik R411.5 12034D12.00
B3-40x25x44 (DIN69880)
Электромеханическая револьверная головка с инструментальным диском SM-BR20 D1B 12 360 4030 ф. "DUPLOMATIС
Таблица режимов резания
Наладка инструментальная
БНТУ.303536.675.000 НИ
Пластина CNMG 09T308
Пластина LCMX 040308
Пластина QOMT 0830R-M2
МР-7 ОСТ 38.01445-88
ХГ (НВ=1870 2410МПа)
Вспомогательный инструмент
Радиальная оправка В3-40х25х44
Резец проходной упорный SCLCR 1616H 09
GNMG 09T308 (марка сплава 4215)
Оправка для сверл Е1-40х25х71
Сверло Sandvik R416.2 0250L25-31
LCMX 040308 (марка сплава 1020)
Зенковка 2353-0138 ГОСТ 14953-80
Аксиальный сверлильно-фрезерный держатель DA40548032
Сверло комбинированное Coro Drill Delta-C R841-0675-30-A1A (Sandvik)
Метчик 2620-1223 ГОСТ 3266-81
Сверло Sandvik R411.5 - 12034D12.00
Твервдосплавная пластина марки Р20
Фреза AQXR 174SA 16S (mitsubishi)
Пластина QOMT 0830R-M2 (марка сплава F7010)