Разработка группового технологического процесса обработки детали Основание




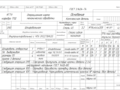
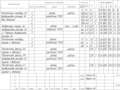
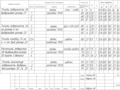
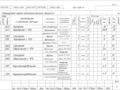
- Добавлен: 24.01.2023
- Размер: 2 MB
- Закачек: 1
Описание
Состав проекта
![]() |
![]() |
![]() |
![]() ![]() ![]() ![]() |
![]() ![]() ![]() ![]() |
![]() ![]() ![]() ![]() |
![]() ![]() ![]() ![]() |
![]() ![]() ![]() ![]() |
![]() ![]() ![]() ![]() |
![]() ![]() ![]() ![]() |
![]() ![]() ![]() ![]() |
![]() ![]() ![]() ![]() |
![]() ![]() ![]() ![]() |
![]() ![]() ![]() ![]() |
![]() |
![]() ![]() ![]() ![]() |
![]() ![]() ![]() ![]() |
![]() ![]() ![]() ![]() |
![]() ![]() ![]() ![]() |
![]() ![]() ![]() ![]() |
![]() ![]() ![]() ![]() |
![]() ![]() ![]() ![]() |
![]() ![]() ![]() ![]() |
![]() ![]() ![]() ![]() |
![]() ![]() ![]() ![]() |
![]() ![]() ![]() ![]() |
![]() ![]() ![]() ![]() |
![]() ![]() ![]() ![]() |
![]() ![]() ![]() ![]() |
![]() ![]() ![]() ![]() |
![]() ![]() ![]() ![]() |
![]() ![]() ![]() ![]() |
![]() ![]() ![]() ![]() |
![]() ![]() ![]() ![]() |
![]() |
![]() ![]() ![]() ![]() |
![]() ![]() ![]() ![]() |
![]() ![]() ![]() ![]() |
![]() ![]() ![]() ![]() |
![]() ![]() ![]() ![]() |
![]() ![]() ![]() ![]() |
![]() ![]() ![]() ![]() |
![]() ![]() ![]() ![]() |
![]() ![]() ![]() ![]() |
![]() ![]() ![]() ![]() |
![]() ![]() ![]() ![]() |
![]() ![]() ![]() ![]() |
![]() ![]() ![]() ![]() |
![]() ![]() ![]() ![]() |
![]() ![]() ![]() ![]() |
![]() ![]() ![]() ![]() |
![]() |
![]() ![]() ![]() ![]() |
![]() ![]() ![]() ![]() |
![]() ![]() ![]() ![]() |
![]() ![]() ![]() ![]() |
![]() |
![]() ![]() ![]() ![]() |
![]() |
![]() ![]() ![]() ![]() |
![]() ![]() ![]() ![]() |
![]() ![]() ![]() ![]() |
![]() ![]() ![]() ![]() |
![]() ![]() ![]() ![]() |
![]() ![]() ![]() ![]() |
![]() ![]() ![]() ![]() |
![]() ![]() ![]() ![]() |
![]() ![]() ![]() |
![]() ![]() ![]() ![]() |
Дополнительная информация
Эскиз 015.frw

Эскиз Оп. 110 - 3.frw

Операция 065.frw

Промежуточный контроль
Контролировать размеры 48
Проверить глубину паза 49.
Операция 110 - Комплексный контроль.frw

Проверить соотвествие
Операционная карта технического контроля
Комплексный контроль
Эскиз Оп. 110 - 4.frw

Эскиз ОП. 110 - 1.frw

Операция 015.frw

Промежуточный контроль
Эскиз Оп. 040.frw

Эскиз ОП. 110 -2.frw

Операция 040.frw

заусенцы и острые кромки не допускаются
Операционная карта технического контроля
Промежуточный контроль
Проверить шероховатость поверхности детали
Контролировать размеры 32
Контролировать размеры фасок Ф2
Контролировать размеры 35
Контролировать размер 4Н13
Эскиз Оп. 065.frw

Эскиз Оп. 115 - 3.frw

Эскиз Оп. 035.frw

Эскиз Оп. 115 - 4.frw

Эскиз Оп. 085.frw

Эскиз Оп. 090.frw

Эскиз Оп. 070.frw

Эскиз Оп. 080.frw

Эскиз 000.frw

Эскиз Оп. 020.frw

Эскиз Оп. 030.frw

Эскиз Оп. 025 -1.frw

Эскиз ОП. 115 -2.frw

Эскиз Оп. 045.frw

Эскиз ОП. 115 - 1.frw

Эскиз Оп. 055.frw

Эскиз Оп. 030 -1.frw

Эскиз Оп. 025 - 3.frw

Эскиз Оп. 025 -2.frw

Карта Эскизов.frw

Операция 035- 1.frw

размер 32 (все детали)
Н а и м е н о в а н и е о п е р а ц и и
Оборудование (наеменование
Инструмент (код и наименование)
Наименование и марка
мм мм мм ммоб обмин ммин мин мин
Токарный с ЧПУ 16А20Ф3
(комплексная деталь)
Операция 020-2.frw

мм мм мм ммоб обмин ммин мин мин
Операция 020-1.frw

Н а и м е н о в а н и е о п е р а ц и и
Оборудование (наеменование
Инструмент (код и наименование)
Наименование и марка
мм мм мм ммоб обмин ммин мин мин
Станок токарный 16К20
Операция 085.frw

Н а и м е н о в а н и е о п е р а ц и и
Оборудование (наеменование
Инструмент (код и наименование)
Наименование и марка
мм мм мм ммоб обмин ммин мин мин
Круглошлифовальный с ЧПУ 3У131ВМ
Операция 055.frw

в размер 50 выдержив.
Следующая операция 060 - Слесарная. Притупить острые кромки ( все детали )
инструмент: напильник ГОСТ 1465-80.
Н а и м е н о в а н и е о п е р а ц и и
Оборудование (наеменование
Инструмент (код и наименование)
Наименование и марка
мм мм мм ммоб обмин ммин мин мин
Вертикально-фрезерный с ЧПУ FS-400
Операция 030 - 2.frw

выдерживая размер 21
выдерживая размер 22
Точить канавку 24 на
поверхность выдержи-
Инструмент (код и наименование)
мм мм мм ммоб обмин ммин мин мин
Операция 025 -1.frw

ммоб обмин ммин мин мин
Н а и м е н о в а н и е о п е р а ц и и
Оборудование (наеменование
Инструмент (код и наименование)
Наименование и марка
Станок токарный 16А20
Операция 045.frw

Фрезеровать 6 граней
в размер 45 выдерживая
Следующая операция 050 - Слесарная. Снять заусенцы
острые кромки притупить
напильник ГОСТ 1465-80.
Н а и м е н о в а н и е о п е р а ц и и
Оборудование (наеменование
Инструмент (код и наименование)
Наименование и марка
мм мм мм ммоб обмин ммин мин мин
Вертикально-фрезерный FSS-400
(комплексная деталь)
Операция 000.frw

Следующая операция 005 - Слесарная. Притупить острые кромки (детали 2
инструмент: напильник ГОСТ 1465-80.
Следующая операция 010 - Маркирование. Маркировать штемпельной краской
№ партии. (все детали)
Н а и м е н о в а н и е о п е р а ц и и
Оборудование (наеменование
Инструмент (код и наименование)
Наименование и марка
мм мм мм ммоб обмин ммин мин мин
Станок Отрезной дисковый ВТС-50
Операция 030 - 3.frw

выдерживая размер 29
(кроме 1 - 3 детали)
Инструмент (код и наименование)
мм мм мм ммоб обмин ммин мин мин
Операция 025 -2.frw

Расточить коническую
Инструмент (код и наименование)
мм мм мм ммоб обмин ммин мин мин
Операция 035 - 2.frw

выдерживая размер 34
выдерживая размер 32
у 1 детали выдержать
выдерживая размер 42
Инструмент (код и наименование)
мм мм мм ммоб обмин ммин мин мин
Операция 090.frw

Следующая операция 095 - Слесарная. Притупить острые кромки (детали 2
инструмент: напильник ГОСТ 1465-80.
Н а и м е н о в а н и е о п е р а ц и и
Оборудование (наеменование
Инструмент (код и наименование)
Наименование и марка
мм мм мм ммоб обмин ммин мин мин
Внутришлифовальный с ЧПУ 3М227ВФ20
Следующая операция 100 - Промывка. Произвести промывку детали (все детали)
Следующая операция 105 - Маркирование. Маркировать штемпельной краской № партии. (все детали)
Операция 070.frw

Следующая операция 075 - Слесарная. Притупить острые кромки (детали 1
инструмент: напильник ГОСТ 1465-80.
Н а и м е н о в а н и е о п е р а ц и и
Оборудование (наеменование
Инструмент (код и наименование)
Наименование и марка
мм мм мм ммоб обмин ммин мин мин
Станок-сверлильный 21104Н7Ф4
Операция 080.frw

выдерживая размер 57
Н а и м е н о в а н и е о п е р а ц и и
Оборудование (наеменование
Инструмент (код и наименование)
Наименование и марка
мм мм мм ммоб обмин ммин мин мин
Станок-сверлильный 21104Н7Ф4
Операция 030 - 1.frw

Точить поверхность 25
выдерживая размер 22
Н а и м е н о в а н и е о п е р а ц и и
Оборудование (наеменование
Инструмент (код и наименование)
Наименование и марка
мм мм мм ммоб обмин ммин мин мин
Токарный с ЧПУ 16А20Ф3
(Комплексная деталь)
Маршрутка_4.frw

Маршрутная карта технологического процесса
Напильник ГОСТ 1465-80
Комплексный контроль
Маршрутка_2.frw

Маршрутная карта технологического процесса
Маршрутка_3.frw

ЧЦ 50х32х13 95Ф25ПСМ1
Стойка гибкая магнитная
НИ 50-100 Нутромер индикат-ный
Маршрутная карта технологического процесса
Напильник ГОСТ 1465-80
Маршрутка_1.frw

И СОДЕРЖЕНИЕ ОПЕРАЦИИ
Сталь 45 ГОСТ 1050-88
Фрагмент.frw

Технические условия на заготовку
Масса отходов в виде
Остаток облоя не более
Коэффициент использования
Количество деталей из
Комплексный чертёж детали.frw

Общие размеры по ГОСТ 30893.2mК
Маркировать: ОТК № парти шрифтом Н10 СТП 97-104-848-80
Заготовка: труба 114х44х205 ГОСТ 8732-78
Циклограмма ГТК.frw

Деталь 2.cdw

Маркировать: ОТК № парти Шрифт Н10 СТП 97-104-848-80
Труба 108х40х200 ГОСТ 8732-78
Деталь 3.cdw

Маркировать: ОТК № парти Шрифт Н10 СТП 97-104-848-80
Труба 108х40х200 ГОСТ 8732-78
План обработки.frw

Оп. 070 Сверлильная с ЧПУ детали 1
Станок: Сверлильный с ЧПУ 21104Н7Ф4
Оп. 085 Круглошлифовальная детали 1
Оп. 090 Внутришлифовальная детали 1
Оп. 080 Сверлильная с ЧПУ детали 2
Оп. 000 Заготовительная
Станок: Отрезной дисковый
Оп. 020 Токарная ( черновая ) детали 1
Станок: токарный - 16К20
Оп. 025 Токарная ( черновая )
Станок: токарный - 16К20
Оп. 030 Токарная с ЧПУ ( чистовая ) детали 1
Станок: токарный с ЧПУ - 16А20Ф3
Оп. 035 Токарная с ЧПУ ( чистовая ) детали 1
Станок: токарный с ЧПУ - 16А20Ф3
Станок: Вертикально-фрезерный 6Т13Ф20-1
Оп. 010 Маркирование
Оп. 105 Маркирование
Оп. 115 Консервация и упаковка готовых деталей.
Сталь 45 ГОСТ 1050-88
Деталь 1.cdw

Маркировать: ОТК № парти Шрифт Н10 СТП 97-104-848-80.
Труба 114х44х205 ГОСТ 8732-78
Эскиз Совмешеных Переходов.frw

Диаметральные размерные цепи
Сталь 45 ГОСТ 1050-88
Деталь 4.cdw

Маркировать: ОТК № парти Шрифт Н10 СТП 97-104-848-80
Труба 108х40х205 ГОСТ 8732-78
Пояснительная записка.doc
Казанский Государственный Технический Университет А. Н. Туполева
Кафедра технологии производства двигателей.
Разработка группового технологического процесса обработки детали «Основание»
РАСЧЕТНО-ПОЯСНИТЕЛЬНАЯ
Разработка плана группового технологического процесса подбор
оборудования и оснастки.
Проектирование комплексной детали.
Расчет размерных цепей
Расчет режимов резания и нормирование операций.
Расчет параметров выбор компоновки и разработка циклограммы ГТК.
Список используемой литературы.
Разработка плана группового технологического процесса.
Изучив технические требования рабочего чертежа и годовую программу выпуска был предложен следующий групповой технологический процесс обработки.
Заготовка: Труба из горячекатаной стали нормальной точности. ГОСТ 1050-88
Материал Сталь 45 ГОСТ 1050-88.
Операции 000. Заготовительная на данной операции труба режется в размер 201±05мм. Применяемое оборудование станок отрезной дисковый ВТС-50 диаметр диска-500мм.( IT17 Rz400)
Операция 005. Слесарная притупляются острые кромки.
Операция 010. Маркировка проводится маркировка деталей партии.
Операции 015. Контрольная проводится контроль размера полученного на заготовительной операции. Приспособление: Штангенциркуль угломер.
Операции 020. Токарная черновая снимается значительный припуск с внутренних поверхностей и подготавливаются базы для дальнейшей обработке ( IT14 Rz200). Применяемое оборудование станок токарный 16К20.
Приспособление: трёхкулачковый патрон.
Операции 025. Токарная черновая снимается значительный припуск с наружной поверхности и подготавливаются базы для дальнейшей обработки ( IT14 Rz200).
Применяемое оборудование станок токарный 16К20.
Дальнейшая обработка будет производится в условиях ГАП.
Операция 030. Токарная чистовая в качестве оборудования был выбран токарный станок с ЧПУ с противошпинделем 1Р72 ( IT12 Rz100). На данной операции производится получение окончательного контура детали.
Операция 035. Токарная чистовая в качестве оборудования был выбран токарный станок с ЧПУ с противошпинделем 1Р72 ( IT12 Rz100). На данной операции производится получение окончательного контура детали.
Операции 040. Контрольная проводится контроль размеров полученных на предшествующих операциях. Приспособление: Штангенциркуль Угломер нутромер линейка.
Операция 045. Фрезерная станок вертикально-фрезерный с ЧПУ FSS-400. На данной операции фрезеруется лыска фрезеруется 6 граней( IT12 Rz100).
Приспособление: пневматическое для осевой обработки.
Операция 050. Слесарная притупляются острые кромки.
Операция 055. Фрезерная на данной операции фрезеруется выборка( IT12 Rz100).
Приспособление: гидравлическое для осевой обработки. В качестве оборудования был выбран вертикально-фрезерный станок с ЧПУ 6Т13Ф20-1.
Операция 060. Слесарная притупляются острые кромки.
Операции 065. Контрольная проводится контроль размеров полученных на предшествующих операциях. Приспособление: Штангенциркуль Угломер нутромер линейка?
Операция 070. Сверлильная на данной операции сверлится 1 отверстие D= 13мм.
Приспособление: кондуктор. В качестве оборудования был выбран вертикально-сверлильный станок 2Н135.
Операция 075. Слесарная притупляются острые кромки.
Операция 080. Сверлильная на данной операции сверлится 6 отверстий D= 13мм.
Операция 085. Шлифовальная на данной операции шлифуется поверхность Dk9.1 с учётом покрытия выдерживая размер Ak9.1. В качестве оборудования был выбран кругло шлифовальный станок 3М163МФ2.
Операция 090. Шлифовальная на данной операции шлифуется поверхность Dk10.1 выдерживая размер Ak10.1. В качестве оборудования был выбран внутришлифовальный станок 3М227.
Операция 095. Слесарная притупляются острые кромки.
Операция 100. Промывочная. проводится промывка деталей.
Операция 105. Маркировочная маркируется номер партии детали.
Операция 110. Контрольная производится контроль размеров полученных на предшествующих операциях. Приспособление: Штангенциркуль Угломер линейка.
Операция 115. Консервация на данной операции производится консервация и упаковывание готовых деталей.
Выбор станков промышленных роботов и вспомогательного оборудования.
Станки с ЧПУ для каждой групповой операции выбираются по следующим критериям:
Рабочая зона станка должна соответствовать габаритным размерам деталей группы.
Технологические возможности станка должны обеспечивать:
возможность обработки всех поверхностей комплексной детали в данной групповой операции;
достижение операционных допусков и качества поверхностного слоя в зоне экономической точности;
иметь в инструментальном магазине или инструментальной головке необходимый и достаточный набор режущих и измерительных инструментов
Мощности главного привода и приводов подач станка должны быть не меньше чем требуется для осуществления процесса резания в самой высоконагруженной деталеоперации.
Стоимость станка должна соответствовать экономической выгоде от его использования.
Тип промышленного робота выбирается в зависимости от веса конфигурации и размеров подаваемых заготовок параметров станка транспортных траекторий и т.п. Для групповых технологий при равных прочих характеристиках более предпочтительны малогабаритные промышленные роботы небольшой стоимости с двумя схватами и круговой системой транспортирования. Из вспомогательного оборудования в гибких технологических комплексах получили распространение межоперационная тара и межоперационные накопители. В таре находятся ориентированные заготовки что позволяет промышленному роботу схватить и подать их на станок а после обработки в таком же ориентированном положении поместить обратно. Межоперационный накопитель служит для создания межоперационных заделов ориентированных заготовок их хранения и транспортирования от одного гибкого технологического комплекса к другому.
Группирование деталей
Классификация и группирование деталей для групповой обработки производится по признакам:
конструктивно-технологического подобия;
соответствия габаритов деталей размерам рабочей зоны станков;
общности маршрутной технологии (сходству циклов обработки);
подобию методов базирования (сходству технологической оснастки);
идентичности материалов.
Группирование деталей осуществляется в несколько этапов. На основе первичного группирования осуществляемого по конструкторскому классификатору в каждую так называемую классификационную группировки отбираются детали в соответствии с классом подклассом видом подвидом группой и подгруппой. Далее производится сортировка всех отобранных деталей в размерные группы по размерной характеристике которой является возможность детали быть вписанной:
в квадрат основных размеров (наружный диаметр длина) для тел вращения.
Затем в каждой выделенной размерной группе производится вторичное группирование по характеристикам комплектов баз. В одну группу при этом отбираются детали имеющие идентичный набор потенциальных установочных баз.
На следующем этапе в каждой группе рассматриваются имеющиеся на каждую деталь типовые варианты индивидуальных технологических процессов и отбирается деталь имеющая наибольшее количество операций выполняемых на станках разных типов (например фрезерно-центровальная токарная сверлильная фрезерная или сверлильно-фрезерная или сверлильно-фрезерно-расточная круглошлифовальная внутришлифовальная и т.д.) Найденный маршрут будем считать характерным для каждой размерной классификационной группы.
В моём случае групповой обработкой охвачена одна операция (рис.1). Детали с незаконченным циклом обработки совместно обработанные на одной групповой операции на остальных операциях входят в другие группы или изготавливаются по единичным техпроцессам.
Рис.1. Группа деталей с циклом обработки на одном типе оборудования
Разработка комплексной детали
При построении групповых технологических процессов за основу берется комплексная деталь.
Для комплексной детали разрабатывается маршрутная технология групповые операции и групповая оснастка.
Конструирование комплексной детали осуществляется методом наложения который заключается в следующем. Просматривая чертежи деталей группы технолог из ряда подобных деталей выбирает одну наиболее характерную. Затем рассматриваются детали отличающиеся от первой наличием других обрабатываемых поверхностей. Эти новые поверхности наносятся на чертеж исходной детали. Таким образом компонуется условная комплексная деталь содержащая все элементы деталей группы.
Расчет размерных цепей.
РАСЧЕТ РАЗМЕРНЫХ ЦЕПЕЙ ДЛЯ ДЕТАЛИ №1.
Длинновые размерные цепи.
АК41=200-0460мм ТА31 =046мм
Z=025 мм. (согласно 1. стр.19 таблица 3)
ZК41= Z+TA31=025+046=071 мм.
А31= Аk41+ ZК41=200+071=20071 мм.
Округляем до предпочтительного окончания технологических межоперационных размеров (согласно 1. стр. 93. таблица 1)
А31=2008-0460мм. ТА21 =046мм.
Z=03 мм. (согласно 1. стр.19 таблица 3)
Z31= Z+TA21=03+046=076 мм.
А21= А31+ Z31=2008+076=20156 мм.
А21=2018-0460мм. ТА11 =046мм.
Z=055 мм. (согласно 1. стр.19 таблица 3)
Z21= Z+TA11=055+046=101 мм.
А11= А21+ Z21=2018+101=20282 мм.
А11=203-1150мм. ТАН =115 мм.
Z=085 мм. (согласно 1. стр.19 таблица 3)
Z11= Z+TA11=085+115=2 мм.
АН= А11+ Z11=203+2=205 мм.
АК10.1=10±0090мм. ТА35=009 мм.
Z=013 мм. (согласно 1. стр.19 таблица 3)
ZК101= Z+TA35=013+009=022 мм.
А35= АК101+ ZК101=10+0220=1022 мм.
АК9.1=15±0021мм. ТА42 =0042мм.
ZК91= Z+TA42=013+0042=0172 мм.
А42= АК91+ ZК91=15+015=1517 мм.
АК36=55 ±03 мм. А31=2008-0460 мм. А21=2018-0460 мм.
Z=05 мм. (согласно 1. стр.19 таблица 3)
ZК36= Z+TA13 =05+03=08 мм.
А13= А21+ АК36 – А31 – ZК36 =2018+55 -2008-08=552 мм.
А42=152 ±0021 мм. А31=2008-0460 мм. АК41=200-0460 мм.
Z42= Z+TA22 =05+0042=0542 мм.
А22= А31+ А42 - АК41 - Z42 =2008+152 -0542-200=15458 мм.
Диаметральные размерные цепи.
DК10.1=80+0046мм. ТD33 =0046мм.
ZК101=2Z+TD3.3=05+0046=0546 мм.
D3.3= DК101- ZК101=80-0546=79454 мм.
DК9.1=70+0046мм. ТD4.1 =0046 мм.
ZК91=2Z+TD4.1=05+0046=0546 мм.
D4.1= DК91+ ZК91=70+0546=70546 мм.
D4.1=705 +0074 мм. ТD2.2 =0074 мм.
Z=09 мм. (согласно 1. стр.19 таблица 3)
Z2.2=2Z+TD2.2=09+0074=0974 мм.
D2.2= D4.1- 2Z2.2=70-0974=69026 мм.
D3.3=795 +0074мм. ТD3.2 =0074 мм.
Z3.3=2Z+TD32=09+074=0974 мм.
D3.2= D33- 2Z3.3=795-0974=7841 мм.
D32=784 +019мм. ТD13 =019 мм.
Z=17 мм. (согласно 1. стр.19 таблица 3)
Z3.2=2Z+TD13=17+019=189 мм.
D13= D32- 2Z3.2=784-189=7656 мм.
DK2.3=47 +016мм. ТD1.2 =016 мм.
Z=08 мм. (согласно 1. стр.19 таблица 3)
ZK2.3=2Z+TD12=08+016=096 мм.
D12= DK2.3- 2ZK2.3=47-096=4604 мм.
DК21=108 +0350 мм. ТDH.1 =035 мм.
z=2 мм. (согласно 1. стр.19 таблица 3)
ZК2.1=2Z+TDН.1=2+035=235 мм.
DH1= D2.1+ 2Z2.1=108+235=11035 мм.
D12=461 +025мм. ТDH.2 =025 мм.
Z=2 мм. (согласно 1. стр.19 таблица 3)
Z1.2=2Z+TDН.2=2+025=262 мм.
DH.2= D1.2- 2Z1.2=461-225=4385 мм.
РАСЧЕТ РАЗМЕРНЫХ ЦЕПЕЙ ДЛЯ ДЕТАЛИ №2.
Линейные размерные цепи.
АК41=195-046мм. ТА31 =046 мм.
Z41= Z+TA31=025+046=071 мм.
А31= Аk41+ Z41=195+071=19571 мм.
А31=1958 -0460 мм. ТА21 =046мм.
А21= А31+ Z31=1958+076=19656 мм.
А21=1968 -046мм. ТА21 =046мм.
А11= А21+ z21=1968+101=19781 мм.
А11=1978 -1150 мм. ТА11 =115 мм.
Z11= Z+TAН1=085+115=2 мм.
АН1= А11+ Z11=1978+2=1998 мм.
АК10.1=8±009мм. ТА35=009 мм.
А35= АК101+ ZК101=8+022=822 мм.
АК9.1=12±0021 мм. ТА41 =0042 мм.
ZК91= Z+TA41=013+0042=0172 мм.
А42= АК91+ ZК91=12+015=1217 мм.
АК36=50 ±03 мм. А31=1958-046 мм. А21=1968-046 мм.
Z=05мм (согласно 1. стр.19 таблица 3)
А13= А21+ АК36 – А31 – ZК36 =1968+50-1958-08=502 мм.
А42=122 ±0021 мм. А31=1958 -046 мм. АК41=195-046 мм.
ТА22 =0042 мм. А22=?
А22= А31+ А42 - АК41 - Z42 =1958+122 -0542-195=12458 мм.
DК10.1=75+0046мм. ТD33 =0046 мм.
D3.3= DК101- ZК101=75-0546=74454 мм.
DК9.1=65+0046мм. ТD4.1 =0046 мм.
D4.1= DК91+ ZК91=65+0546=65546 мм.
D4.1=655 +0074мм. ТD2.2 =0074мм.
Z2.2=2Z+TD4.1=09+0074=0974 мм.
D2.2= D4.1- 2Z2.2=655-0974=64474 мм.
D3.3=745 +0074мм. ТD3.2 =0074мм.
Z3.3=2Z+TD32=09+0074=0974 мм.
D3.2= D33- 2Z3.3=745-0974=7341 мм.
D32=734 +019 мм. ТD13 =019 мм.
D13= D32- 2Z3.2=734-189=7156 мм.
DK2.3=42 +016 мм. ТD1.2 =016 мм.
Z = 08 мм. (согласно 1. стр.19 таблица 3)
ZK2.3 = 2Z+TD12 = 08+016 = 096 мм.
D12= DK2.3- 2ZK2.3=42-096=4104 мм.
DК21=103 +035 мм. ТDH.1 =035 мм.
DH1= D2.1+ 2z2.1=103+235=10535 мм.
D12=411+062 мм. ТDH.2 =062 мм.
Z1.2=2Z+TDН.2=2+062=262 мм.
DH.2= D1.2- 2Z1.2=411-262=3848 мм.
РАСЧЕТ РАЗМЕРНЫХ ЦЕПЕЙ ДЛЯ ДЕТАЛИ №3.
АК41=185-046 мм. ТА31 =046 мм.
А31= Аk41+ Z41=185+071=18571 мм.
А31=1858 -046 мм. ТА21 =046 мм.
Z31= Z+TA21=03+046=076 мм
А21= А31+ Z31=1858+076=18656 мм.
А21=1868 -046 мм. ТА11 =046 мм.
Z=055мм. (согласно 1. стр.19 таблица 3)
А11= А21+ Z21=1868+101=18782мм.
А11=188-115 мм. ТАН =115 мм.
Z=085мм. (согласно 1. стр.19 таблица 3)
Z11= Z+TAН=085+115=2 мм.
АН1= А11+ Z11=188+2=200мм.
АК9.1=25±0021мм. ТА42 =0042 мм.
Z=013мм. (согласно 1. стр.19 таблица 3)
ZК91= z+TA42=013+0042=0172 мм.
А42= АК91+ ZК91=25+015=2517мм.
А42=252 ±0021 мм. А31=1858 -046 мм. АК41=185-046 мм.
z=05мм. (согласно 1. стр.19 таблица 3)
z42= z+TA22 =05+0042=0542 мм.
А22= А31+ А42 - АК41 - z42 =1858+252 -0542-185=25458 мм.
DК9.1=67+0046 мм. ТD4.1 =0046 мм.
Z=05мм. (согласно 1. стр.19 таблица 3)
D4.1= DК91+ ZК91=67+0546=67546 мм.
D4.1=675 +0074 мм. ТD2.2 =0074 мм.
D2.2= D4.1- 2Z2.2=675-0974=66474 мм.
DK2.3=43 +016 мм. ТD1.2 =016 мм.
Z=08мм. (согласно 1. стр.19 таблица 3)
Z2.3=2Z+TD12=08+016=096 мм.
D12= DK2.3- 2Z2.3=43-096=4204 мм.
DК21=104 +035 мм. ТDH.1 =035 мм.
DH.1= D2.1+ 2Z2.1=104+235=10635 мм.
D12=421 +062 мм. ТDH.2 =074 мм.
Z1.2=2Z+TDН.2=2+074=274 мм.
DH.2= D1.2- 2Z1.2=421-274=3936 мм.
РАСЧЕТ РАЗМЕРНЫХ ЦЕПЕЙ ДЛЯ ДЕТАЛИ №4.
АК41=193-046 мм. ТА31 =046 мм.
Z41= z+TA31=025+046=071 мм.
А31= Аk41+ Z41=193+071=19371мм.
А31=1938 -046 мм. ТА21 =046 мм.
А21= А31+ Z31=1938+076=19456мм.
А21=1948 -046 мм. ТА11 =046 мм.
А11= А21+ Z21=1948+101=19581 мм.
А11=196 -115 мм. ТАН =115 мм.
АН= А11+ Z11=196+2=198 мм.
АК10.1=6±009 мм. ТА35=009 мм.
А35= АК101+ ZК101=6+022=622 мм.
АК36=48 ±03 мм. А31=1938-046 мм. А21=1948-046 мм.
ZК36= Z+TA13=05+03=08 мм.
А13= А21+ АК36 – А31 – ZК36 =1948+48 -1938-08=482 мм.
DК10.1=78+0046мм. ТD33 =0046 мм.
D3.3= DК101- ZК101=78-0546=77454 мм.
D3.3=775+0074 мм. ТD3.2 =0074 мм.
Z3.3=2Z+TD33=09+0074=0974 мм.
D3.2= D33- 2Z3.3=775-0974=7641 мм.
D32=764+019 мм. ТD13 =019 мм.
Z3.2=2Z+TD31=17+019=189 мм.
D13= D32- 2Z3.2=764-1890=7456 мм.
DK2.3=44 +016 мм. ТD1.2 =016 мм.
Z=08мм (согласно 1. стр.19 таблица 3)
D12= DK2.3- 2ZK2.3 =44-096=4304 мм.
DК21=106+035 мм. ТDH.1 =035 мм.
ZК2.1=2z+TDН.1=2+035=235 мм.
DH1= D2.1+ 2Z2.1=106+235=10835 мм.
D12=431 +062 мм. ТDH.2 =062 мм.
Z1.2=2Z+TD1.2=2+062=262 мм.
DH.2= D1.2- 2Z1.2=431-262=4048 мм.
Расчет режимов резания для детали №1 на операции 020
Глубина резания: t = 3мм
Выбираем подачу: Sт = 033ммоб
Находим поправочные коэффициенты для подачи:
k1=1; k2=1; k3=08; k4=085; k5=1; k6=107
k = 1×1×08×085×1×107 = 072
Рассчитываем скорректированную подачу: S = Sт×k = 033×072 = 024ммоб
Находим стойкость инструмента: Т = 30мин
Выбираем скорость резания: Vт = 214ммин
k1=1; k2=1; k3=092; k4=12; k5=1; k6=1; k7=1; k8=1; k9=1; k10=1
k = 1×1×092×12×1×1×1×1×1×1 = 11
Рассчитываем скорректированную скорость: V = Vт×k = 214×11 = 236ммин
Рассчитываем частоту вращения: n = 1000×236(314×110.8) = 680 1мин
Рассчитываем основное время: То = (5+10+5)(024×680) = 012 мин
Рассчитываем вспомогательное время: Tв = 0124 = 003мин
Рассчитываем усилие резания: PZ = 300×3×024×089 = 240 кг
Рассчитываем мощность резания: N = (240×236)(60×102) = 92 кВт
Глубина резания: t = 18мм
Выбираем скорость резания: Vт = 100ммин
Рассчитываем скорректированную скорость: V = Vт×k = 190×11 = 110ммин
Рассчитываем частоту вращения: n = 1000×110(314×585) = 575 1мин
Рассчитываем основное время: То = (5+230+5)(024×575) = 175 мин
Рассчитываем вспомогательное время: Tв=164=044 мин
Рассчитываем усилие резания: PZ = 300×18×024×089 = 115 кг
Рассчитываем мощность резания: N = (115×110)(60×585) = 36 кВт
Расчет режимов резания для детали №1 на операции 025
Глубина резания: t=285мм
Выбираем подачу: Sт=033ммоб
k=1×1×08×085×1×107=072
Рассчитываем скорректированную подачу: S=Sт×k=033×072=024ммоб
Находим стойкость инструмента: Т=30мин
Выбираем скорость резания: Vт=214ммин
k=1×1×092×12×1×1×1×1×1×1=11
Рассчитываем скорректированную скорость: V=Vт×k=214×11=236ммин
Рассчитываем частоту вращения: n=1000×236(314×110.8)=680 1мин
Рассчитываем основное время: То=(5+10+5)(024×680)=012 мин
Рассчитываем вспомогательное время: Tв=0124=003мин
Рассчитываем усилие резания: PZ=300×285×024×089=183 кг
Рассчитываем мощность резания: N=(183×236)(60×102)=70 кВт
Глубина резания: t=22мм
Выбираем скорость резания: Vт=150ммин
Рассчитываем скорректированную скорость: V=Vт×k=150×11=165ммин
Рассчитываем частоту вращения: n=1000×165(314×1078)=480 1мин
Рассчитываем основное время: То=(5+210+5)(024×480)=19 мин
Рассчитываем вспомогательное время: Tв=194=047 мин
Рассчитываем усилие резания: PZ=300×3×024×089=192 кг
Рассчитываем мощность резания: N=(192×165)(60×102)=52 кВт.
Расчет режимов резания для детали №1 на операции 025
Глубина резания: t=25мм
Выбираем подачу: Sт=023ммоб
Рассчитываем скорректированную подачу: S=Sт×k=023×072=016ммоб
Рассчитываем частоту вращения: n=1000×165(314×62)=850мин
Рассчитываем основное время: То=(5+5+5)(016×850)=011 мин
Рассчитываем вспомогательное время: Tв=01 мин
Рассчитываем усилие резания: PZ=300×5×016×089=214 кг
Рассчитываем мощность резания: N=(214*165)(60*585)=95 кВт
Расчет режимов резания для детали №1 на операции 030
Глубина резания: t=15мм
Выбираем скорость резания: Vт=300ммин
Рассчитываем скорректированную скорость: V=Vт×k=300×11=330ммин
Рассчитываем частоту вращения: n=1000×330(314×107)=980 1мин
Рассчитываем основное время: То=(5+10+5)(024×980)=012 мин
Рассчитываем усилие резания: PZ=300×15×016×089=64 кг
Рассчитываем мощность резания: N=(64×330)(60×107)=32 кВт.
Глубина резания: t=1мм
Рассчитываем частоту вращения: n=1000×165(314×80)=650 1мин
Рассчитываем основное время: То=(5+175+5)(016×650)=178 мин
Рассчитываем вспомогательное время: Tв=045 мин
Рассчитываем усилие резания: PZ=300×1×016×089=425 кг
Рассчитываем мощность резания: N=(425×165)(60×175)=1 кВт.
Расчет режимов резания для детали №1 на операции 035
Глубина резания: t=13мм
Рассчитываем основное время: То=(5+10+5)(024×980)=05 мин
Рассчитываем усилие резания: PZ=300×13×016×089=555 кг
Рассчитываем мощность резания: N=(555×330)(60×107)=285 кВт
Глубина резания: t=1 мм
Рассчитываем частоту вращения: n=1000×330(314×106)=980 1мин
Рассчитываем основное время: То=(5+190+5)(016×980)=13 мин
Рассчитываем вспомогательное время: Tв=04 мин
Рассчитываем мощность резания: N=(425×330)(60×106)=32 кВт
Расчет режимов резания для детали №1 на операции 045
Глубина резания: t=3мм
Выбираем подачу: Sт=011ммзуб
k1=1; k2=1; k3=13; k4=1
Рассчитываем скорректированную подачу: S=Sт×k=011×13=014ммоб
Выбираем скорость резания: Vт=20ммин
k1=14; k2=1; k3=1; k4=1
Рассчитываем скорректированную скорость: V=Vт×k=15×14=32ммин
Рассчитываем частоту вращения: n=1000×21(314×100)=83 1мин
Рассчитываем основное время: То=(5+10+5)(011×67)=23 мин
Рассчитываем вспомогательное время: Tв=684=07 мин
Рассчитываем усилие резания: PZ=218×599×019×15×10199=212 кг
Рассчитываем крутящий момент: М=(1755×100)(10×1000)=175 кгм
Рассчитываем мощность резания: N=(1755×21)6120=06 кВт
Расчет режимов резания для детали №1 на операции 055
Выбираем скорость резания: Vт=15ммин
Рассчитываем скорректированную скорость: V=Vт×k=15×14=21ммин
Рассчитываем частоту вращения: n=1000×21(314×100)=67 1мин
Рассчитываем основное время: То=(5+10+5)(011×67)=68 мин
Рассчитываем вспомогательное время: Tв=684=17 мин
Расчет режимов резания для детали №1 на операции 070
Глубина резания: t=6мм
Выбираем подачу: Sт=025ммзуб
k1=1; k2=1; k3=1; k4=1; k5-09
Рассчитываем скорректированную подачу: S=Sт×k=025×09=022ммоб
Выбираем скорость резания: Vт=12ммин
k1=1; k2=1; k3=1; k4=1; k5=1; k6=1; k7=1
Рассчитываем скорректированную скорость: V=Vт×k=12×1=12ммин
Рассчитываем частоту вращения: n=1000×12(314×10)=380мин
Рассчитываем основное время: То =(5+35)(022×380)=048 мин
Рассчитываем вспомогательное время: Tв=0484=012 мин
Рассчитываем осевое усилие резания: PZ=143×10×022×09=283 кг
Рассчитываем крутящий момент: М=0041×144×022×09=117 кгм
Рассчитываем мощность резания: N=(117*316)075=059 кВт.
Расчет режимов резания для операции 085
Глубина резания: t=035мм
Выбираем скорость вращения детали: Vд=40 ммин
Рассчитываем частоту вращения детали:
nд=1000×40(314×109)= 120 1мин
Выбираем скорость вращения круга: Vк=35 мс
Рассчитываем частоту вращения круга:
nк=60×1000×35(314×200)=3300 1мин
Рассчитываем продольную подачу:
Находим поправочные коэффициенты для продольной подачи:
k1=1; k2=1; k3=1; k4=1; k5=06; k6=075; k7=13;
k=1×1×1×1×06×075×13=058
Рассчитываем скорректированную продольную подачу:
Sпр=Sт пр×k=1×058=058ммоб
Выбираем поперечную подачу:
Находим поправочные коэффициенты для поперечной подачи:
k1=1; k2=08; k3=07; k4=08; k5=1; k6=1; k7=1;
k=1×08×07×08×1×1×1=045
Рассчитываем скорректированную поперечную подачу:
Sпп=Snт пп×k=0006×045=00027 ммдв.ход
Рассчитываем основное время:
То=(5+50+5) ×08×15(058×117)=107 мин
Рассчитываем вспомогательное время:
Рассчитываем мощность резания:
N=13×1600×068×055×253=2 кВт.
РАСЧЕТ ПАРМЕТРОВ КОМПОНОВКА И РАЗРАБОТКА
Расчет параметров ГТК
) Расчет количества станков
Принимаем что количество станков на каждой операции равно:
Отсюда определим программу выпуска всех деталей по самой загруженной операции (025)
- эффективный годовой фонд работы станка.
Примем 1 станок (оп. 030).
Коэффициент загрузки оборудования.
Примем 1 станка (оп.035).
Примем 1 станок (оп.045).
Примем 1 станок (оп. 055).
Примем 1 станок (оп. 070).
Примем 1 станок (оп. 080).
Расчет потребного количества промышленных роботов.
Определим минимальное штучное время выполнения операции на каждом станке:
Если штучное время выполнения какой - либо детале операции хотя бы одной детали группы на данном станке будет меньше 3 минут то количество роботов R принимается равным количеству станков Сп.
При tшт >3 минут рекомендуется многостаночное обслуживание одним роботом ряда станков. В этом случае:
где СR -число станков обслуживаемых одним роботом рекомендуемые [12 стр.142] значения которого приведены в таблице:
Технологические параметры ГТК
Минимальное штучное время
Для станков С1 С2С3 можно применить многостаночное обслуживание (один робот на три станка) так как у них tmin>3мин
Выбор компоновки и разработка циклограммы работы ГТК
Выбираем Кольцевую компоновку ГТК.
Выбор промышленного робота.
Вспомогательные (подъемно-транспортные) роботы выполняют действия типа взять- принести-положить. Их применяют при обслуживании основного технологического оборудования для автоматизации вспомогательных операций установки снятия заготовок деталей инструмента оснастки.
По работе [7] выбираем ПР исходя из веса заготовки mз=6 кг.
грузоподъемность: 15 кг.
число степеней подвижности: 4
привод: пневматический
система управления цикловая: цикловая
число программируемых координат: 4
способ программирования перемещения: по упорам
объем памяти (число команд): 2
погрешность позиционирования: ±03 мм.
Набольший вылет руки: 1100 мм.
габариты мм. H L M: 1035 500 720.
Примем для робота следующие интервалы времени:
- взять деталь из тары (накопителя станка) – 3 сек
- перенести к таре (накопителю станку) – 6 сек
- поставить в тару (накопитель станок) – 3 сек
Определим время цикла обработки для каждой детали:
- время обработки на станках
- время работы робота
tст=1118+6+3+69+7=3416мин.
tр=(3+6+3)*5+6=66=11мин.
кзс = tст tц =341352=096
кзр = tр tц =11352=003
tст=1118+6+112+69+7+83=506мин.
кзс = tст tц =506516=097
кзр = tр tц =1516=002
tст=259+6+112+69+7+83=42мин.
tр=(3+6+3)*5=60с=1 мин.
кзс = tст tц =4243=098
кзс = tст tц =143=002
tц=2526+278+298=8286 мин.
tст=1118+43+112+69+7+89=495мин.
кзс = tст tц =495505=098
кзс = tст tц =1505=002
tц=352+516+43+505=1803 мин.
Список используемой литературы
Дунин Н. А. Основы проектирования технологических процессов производства деталей машин. Учебное пособие.Изд-во Казан. Гос. Техн. Ун-та. Казань1998. 132с.
Баранчиков В. И. Прогрессивные режущие инструменты и режимы резания металлов: Справочник. М. Машиностроение 1990. 400 с.
Справочник технолога-машиностроителя. В 2 т. Под ред. Косиловой А. Г. и Мещерякова Р. К. М. : Машиностроение 1986 Т. 2 496 с.
А.К. Горошкин «Приспособления для металлорежущих станков» Справочник. М «Машиностроение» 1979.
Г.М. Ганевский И.И. Гольдин «Допуски посадки и технические измерения в машиностроении» М «Высшая школа» 1993.
В.Ю. Зыков Е.М. Коровин «Расчет режимов резания конструкционных материалов» методические указания Казань КГТУ 2002.
Я.М. Радкевич В.А. Тимерязев А.Г. Схирладзе М.С. Островский «Расчет припусков и межоперационных размеров в машиностроении» М «ВЫСШАЯ ШКОЛА » 2004г.
Титул.frw

кафедра технологии производства двигателей
ТЕХНОЛОГИЧЕСКИЙ ПРОЦЕСС
Руководитель проекта: Лабутин А.Ю.
Студент гр. 22574 Талапин Е.Ю.
МЕХАНИЧЕСКОЙ ОБРАБОТКИ ДЕТАЛИ "ОСНОВАНИЕ"
Рекомендуемые чертежи
- 24.01.2023
- 24.01.2023
- 28.05.2016
Свободное скачивание на сегодня
- 23.02.2023