Расчёт прямозубого цилиндрического редуктора


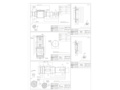
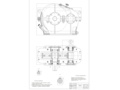
- Добавлен: 24.01.2023
- Размер: 418 KB
- Закачек: 0
Подписаться на ежедневные обновления каталога:
Описание
Расчёт прямозубого цилиндрического редуктора
Состав проекта
![]() |
![]() |
![]() ![]() ![]() ![]() |
![]() ![]() ![]() |
![]() ![]() ![]() ![]() |
Дополнительная информация
Контент чертежей
Деталировка.dwg

Коэффициент смещения
Нормальный исходный контур
Неуказанные предельные отклонения размеров по +IT142
Сталь 5 ГОСТ 4543-71
Твёрдость зубьев 260-280НВ 2. Неуказанные предельные отклонения размеров отверстия-Н14; валы- остальные +IT142
Твердость зубьев 240-260 НВ 2. Неуказанные радиусы скругления 3мм 3. Неуказанные предельные отклонения размеров отверстия - валы- остальные +IT142
Отчёт.doc
Построение планов скоростей.
Построение планов ускорений.
Определение сил инерции.
Определение мощности на кривошипе.
Кинематический расчет привода.
Расчет клиноременной передачи.
Расчет цилиндрической прямозубой передачи
Конструирование вала-шестерни и подбор подшипников.
Проверка работоспособности подшипников быстроходного вала.
Конструирование тихоходно вала.
Конструирование кованого зубчатого колеса.
Подбор подшипников качения тихоходного вала.
Подбор и проверка шпонок тихоходного вала.
Подбор и проверка шпонки быстроходного вала.
Определение количества и сорта смазки.
Конструирование корпуса редуктора
Технический уровень всех отраслей народного хозяйства в значительной мере определяется уровнем развития машиностроения. Одним из направлений решения этой задачи является совершенствование и развитие конструкций и методов расчета создаваемых машин и подготовка высококвалифицированных инженеров широкого профиля.
Проэлектирование по курсу «Деталей машин» входит в учебные планы завершающим этапом в цикле базовых общественных дисциплин. Проэлектирование по курсу «Деталей машин» - первая самостоятельная конструкторская робота.
В данной роботе произведены расчеты клиноременной передачи прямозубого цилиндрического редуктора сделан подбор шпонок подшипников качения втулочно-пальцевой муфты определены скорости и ускорения отдельных деталей привода а также силы действующие в системе.
В курсовом проекте приведены основные данные необходимые для расчета и проектирования механических приводов общемашиностроительного назначения. Рассмотрены основные компоновки привода и отдельных его узлов. Конструирование передач (ременных цепных зубчатых червячных передач винт - гайка) валов шпоночных и шлицевых соединений подбора подшипников качения муфт резьбовых соединений проектирование плит и рам.
Техническое задание. Вариант 10
Спроектировать привод поршневого насоса двойного действия
Клиноременная передача;
Одноступенчатый цилиндрический редуктор;
Упругая втулочно-пальцевая муфта;
Кривошипно-ползунный механизм;
Поршневой насос двойного действия;
Сила сопротивления жидкости при движении поршня Q=773 кН;
Частота вращения кривошипа насоса n2=159 мин-1;
Длины звеней LAB=110 мин; LB1C1=260 мм;
Масса шатуна (B1C1) m2=19 кг его центр масс S1 находится на середины длины; масса поршня со штоком и ползуном m3 =38 кг;
Момент инерции шатуна относительно его центра масс Is=007 кг м3;
Угол наклона кривошипа к горизонту для первого положення механизма α1=18;
Привод работает 1 смену за сутки;
Срок службы редуктора t =15000 часов;
Построение планов скоростей
1 Определяем абсолютную скорость B1
2 Определяем масштаб планов скоростей
где =120 мм- вектор характеризующий скорость точки В на планах скоростей;
3 Скорость точки С1 определяем по двум векторным уравнениям
4. Используя построенные планы скоростей определяем необходимую для построения планов ускорений относительную скорость С1 относительно В1.
-е положение (α1=18)
-е положение (α1=18+60=78)
-е положение (α1=138)
-е положение (α1=198)
-е положение (α1=258)
-е положение (α1=318)
1 Определяем ускорение точки В1
Тангенциальная составляющая ускорения точки В1 аВ1=0 так как кривошип вращается равномерно;
2 Определяем нормальную составляющую ускорения точки С1 относительно точки В1
3 Определяем масштаб планов ускорений
где =120 мм – вектор характеризующий точку В1;
4 Вычисляем длину вектора нормальной составляющей ускорения точки С1 относительно точки В1
-е положение (α1=15)
-е положение (α1=75)
-е положение (α1=135)
-е положение (α1=195)
-е положение (α1=255)
-е положение (α1=315)
5 Ускорение точки С1 определяем по двум векторным уравнениям
Нормальная составляющая ускорения точки С1 относительно точки D аС1Dn=0 так как движение прямолинейное и радиус кривизны
6. Используя построенные планы ускорений определяем ускорение центра масс:
-е положение (α1=78)
б) Поршня со штоком и ползуном
1 Определяем силу инерции шатуна В1С1
Знак “ – “ означает что сила инерции имеет противоположное направление ускорение
2 Определяем силу инерции поршня со штоком и ползуном
Раскладываем сложные движения звена В1С1 на поступательное ускорением точки В1 и вращательное вокруг этой точки. Тогда полную силу инерции получим как геометрическую сумму двух слагаемых: силы инерции Fu21' в поступательном движении и силы Fu21'' во вращательном движении то есть
Линия действия силы инерции Fi21' проходит через центр масс S1 параллельно вектору 1С1 планов ускорений и направлено в противоположную ему сторону. Сила инерции Fi21'' проходит через центр качания К1 находящийся на расстоянии от точки S1.
Линия действия силы инерции Fi21'' параллельно вектору b1s1 планов ускорений и направлено от точки b1 к точке S1.
Т1 – полная инерция;
Полная сила инерции Fi21 пройдет через точку Т1 пересечение линий действий сил инерции Fi21' и Fi21''. Параллельно вектору 1S1 планов ускорений и в противоположную ему сторону.
1 Согласно теореме Жуковского о рычаге в виде плана скоростей переносим силы Fu21 Fu31 и Q в соответствующие точки планов скоростей повернутых по часовой стрелке на 90. Для этого нарисуем еще раз план скоростей.
Определяем положение точки Е1 (e1) – на плане скоростей.
-е положение (α1=258)
-е положение (α1=318)
Fi21 на рычаге Жуковского параллельно Fi21 плану положений и направлено в ту же сторону.
2 Измеряем на размеры плеч.
h1= 30 мм; h2= 75 мм; h3= 50 мм; h4= 32 мм; h5= 20 мм; h6= 52 мм;
Р1С1=40 мм; Р2С2=106 мм; Р3С3=110 мм; Р4С4=40 мм; Р5С5=134 мм; Р6С6=62 мм;
3 Выбираем линию действия уравновешивающей силы перпендикулярную к кривошипу АВ1 и определяем уравновешивающую силу в точке В1.
4 Определяем мощность на кривошипе.
5 Определяем среднюю мощность на кривошипе.
n2кр= n2ред=159 мин.-1;
Р’дв.расч.=7.18 кВт;
Рдв.пасп..= 7.5 кВт;
Nдв.в пасп.=1455 мин.-1;
1 Определяем необходимую мощность электродвигателя по зависимости
где рем.=095 – КПД клиноременной передачи;
ред.=097 - КПД одноступенчатого цилиндрического редуктора;
муф.=099 – КПД упругой втулочно-пальцевой муфты;
2 Выбор асинхронного двигателя с короткозамкнутым ротором в закрытом обдуваемом исполнении.
Это означает что величина которую мы приняли не подходит следовательно выбираем ближайшее большее значение.
По каталогу выбираем трехфазный асинхронный электродвигатель с короткозамкнутым ротором в закрытом обдуваемом исполнении. Принимаем тип электродвигателя 4А132S4У3 мощностью Рдв.пасп=7.5кВт с частотой вращения nдв.=1455 мин.-1;
Кинематический расчет двигателя.
1 Определяем общее передаточное число привода насоса
2 Принимаем передаточное число клиноременной передачи
3 Определяем передаточное число редуктора
Выбираем сечение ремня по расчетной мощности Рдв.'расч.=7.18 кВт;
и частоте вращения nдв=1455 мин.-1 .
2 Выбираем расчетный диаметр меньшего шкива. Выбираем d1=180 мм.
3 Определяем расчетный диаметр большего шкива
Принимаем d2=355 мм ;
4 Уточняем частоту вращения большего шкива
где =002- относительное скольжение ремня.
Расчет цилиндрической прямозубой передачи.
Рассчитать цилиндрическую прямозубую передачу одноступенчатого редуктора (рис. 1) если с тихоходного вала снимается мощность P2ред.= Pкрср=589 кВт при частоте вращения n2ред = n2кр=159 мин-1. Частота вращения быстроходного вала n1ред= n2рем=72291мин-1. Кратковременные перегрузки -до 200% номинального момента. Срок службы редуктора t= 15000 ч.
1.В качестве материала для шестерни и зубчатого колеса легированную сталь 40Х (поковка). Назначаем для них термообработку-улучшение (закалка с высоким отпуском). Принимаем твердость после термообработки для шестерни НВ1=280 для колеса НВ 2 =250.
2 Определяем допускаемое контактное напряжение по формуле
При термической обработке—улучшении
Коэффициент долговечности
Где NHO- базовое число циклов перемены напряжений соответствующее длительному пределу выносливости и определяемое по зависимости NHO=30 НВ24 NHE - эквалентное число циклов перемены напряжений.
Так как и то а то более слабым оказывается колесо по нему и будем вести расчет.
Шероховатость поверхностей зубьев при чистовом фрезеровании соответствует 6-му классу поэтому ZR=095. Для зубчатых колес с однородной структурой материала SH= 11.
3 Определяем межосевое расстояние из условия контактной выносливости зубьев:
Где u'- предварительное значение передаточного числа определяемое по зависимости
T2 — крутящий момент на колесе;
KH- коэффициент учитывающий неравномерное распределение нагрузки по ширине зубчатого венца принимаем коэффициент ширины по начальному диаметру шестерни а=b2dш1=1 тогда по рис. П. 1 кривая 6 KH = 105; KH-предварительное значение коэффициента учитывающего динамическую нагрузку в зацеплении принимаем К'Н=11; а- коэффициент ширины по межосевому расстоянию:
Округляя до ближайшего значения кратного 5мм принимаем aw=155 мм.
4 Модуль зубчатого зацепления в редукторах принимаем m=(001 002)*aw=17 34мм. Согласно ГОСТ 9563-60* назначаем m = 15 мм (см. табл. П.1).
5 Определяем ширину зубчатого венца колеса:
Согласно ГОСТ 6636-69* принимаем b2= 56 мм (см. табл. П. 2).
6. Определяем суммарное число зубьев:
округляя до ближайшего меньшего целого принимаем =155.
7. Определяем угол зацепления рад:
8 Определяем коэффициент суммы смещения:
Принимаем коэффициент смещения у шестерни х1=0205; у колеса – х2=0.
9 Определяем коэффициент уравнительного смещения:
10 Определяем число зубьев шестерни:
11 Определяем число зубьев колеса:
12 Уточняем передаточное число редуктора:
13 Определяем начальный диаметр шестерни:
14 Определяем окружную скорость зубчатых колес:
По ГОСТ 1643-81 принимаем 8-ю степень точности которая рекомендуется для прямозубых цилиндрических колес при окружности скорости до 6 мс.
15 Уточняем коэффициент учитывающий динамическую нагрузку в
зацеплении где HV - удельная окружная динамическая сила определяемая по формуле Н- коэффициент учитывающий влияние вида зубьев при твердости Н≤НВ 350 и прямых зубьев Н=0006 (см. табл. П. 3); g0- коэффициент учитывающий влияние разности шагов зацепление зубьев шестерни и колеса (по табл. П. 4 g0 = 56); таким образом
- окружная сила в зацеплении определяемая по зависимости
16 проверяем контактное напряжение в полюсе зацепления:
Недогрузка что меньше 5%.
17 Выполняем расчет на контактную прочность при действии максимальной нагрузки. Расчетное напряжение создаваемое наибольшей нагрузкой ;
По условию кратковременные перегрузки до 200% поэтому Т2maxT2=2.
Допускаемое предельное напряжение для зубьев колес подвергнутых улучшению где - предел текучести материала при растяжении. Для колеса как более мягкого =490 МПа поэтому
что больше =690198 МПа;
18 Определяем допускаемое напряжение на выносливость зубьев при изгибе: где - предел выносливости зубьев при изгибе соответствующий базовому числу циклов перемены напряжений ; - коэффициент долговечности; - коэффициент безопасности.
При термической обработке – улучшении =18;
Коэффициент долговечности где - базовое число циклов перемены напряжений принимаемое ; - эквивалентное число циклов перемены напряжений. Для колеса что больше Поэтому и для шестерни следовательно KFL1=KFL2=1. Коэффициент безопасности при 99% вероятности неразрушения принимают SF=175. Таким образом допускаемые напряжения:
19 Определяем коэффициенты учитывающие формы зубьев:
a)Для шестерни Z1=28 при коэффициенте смещения Х1=0205 по ( рис.1.2.23); F1=363 ;
b)Для колеса F2=356 так как Z2=127>80.
20 Сравнительная оценка прочности зубьев:
Ширина шестерни принята b1=b2+4=67+4=71 мм;
Так как 563305 Нмм483867 Нмм то слабее зубья колеса .
21 Определяем расчетное напряжение в зубьях колеса:
Где- коэффициент учитывающий неравномерное распределение нагрузки по ширине венца при твердости H≤НВ350 d=1 по рис. П.2кривая 6 =11; -коэффициент учитывающий динамическую нагрузку возникающая в зацеплении определяется по зависимости
-удельная окружная динамическая сила определяемая по зависимости
-коэффициент учитывающий влияние вида зубьев при прямых зубьях =0016 (см.табл.П.3.).
Расчетное напряжения в зубьях колеса что меньше =2571 МПа.
22 Выполняем расчет на прочность при изгибе максимальной нагрузкой для предотвращения остаточной деформации и излома зубьев. Наибольшее расчетное напряжение в зубьях колеса не должно превышать допускаемое равное Fl Fl SFM2-коэффициент безопасности равный при 99% вероятности неразрушения 175. Таким образом FPma
23 Геометрические размеры шестерни при X1=0205:
Диаметр делительной окружности d1=2*30=60 мм;
Диаметр вершин зубьев dα1=d1+2* m=60+2*2=64 мм;
Диаметр впадин зубьев df1=d1-2* m= 60-2*2=56 мм;
Ширина зубчастого венца b1=64 мм;
Геометрические размеры колеса X2=0:
Диаметр делительной окружности d2=m* z2=2*120=240 мм;
Диаметр вершин зубьев dα2=m*(z2+2)=2*(120+2)=244 мм;
Диаметр впадин зубьев df2= m*(z2-25)= 2*(140-25)=236мм;
Ширина зубчастого венца b2=60 мм;
Межосевое расстояние (для контроля)
Конструирование вала – шестерни и подбор подшипников
Данные роликоподшипника конического легкой широкой серии
Условное обозначение
1 Обычно шестерню выполняют как одно целое с валом это проще и дешевле чем насадная шестерня. По техническому заданию на курсовой проект [8] на конце вала—шестерни сидит большой шкив клиноременной передачи. Его ширина полученная из расчета клиноременной передачи В = 105 мм. Так же получена сила давления ремней на шкив и вал F = 25 кН. Силой веса шкива пренебрегаем полагая диаметр вала под подшипником dn1=35 мм и ориентируясь на роликоподшипник конической легкой широкой серии выписываем его данные из табл. П.5. в табл. 1.
2 Определяем расстояние от середины шкива до точки приложения реакции (рис.2.)
где Δ — зазор между плоскостью торца шкива и головкой болта крепящего крышку подшипника принимаем Δ= 10 мм; h — сумма высоты головки болта и толщины пружинной шайбы принимаем болты М8 тогда h = 8 мм;
— толщина крышки подшипника под болты М8 рекомендуют 1= 10 мм;
р — глубина захода крышки в гнездо подшипника принимаем р = 10 мм;
α — расстояние между торцом подшипника и точкой приложения реакции
определяется по зависимости
3 Определяем изгибающий момент в точке приложения реакции:
4 Определяем крутящий момент на валу—шестерне:
где — КПД редуктора при 8—й степени точности зубчатых колес принимают = 097.
5. По четвертой теории прочности определяем момент эквивалентный:
6 Проверяем напряжение изгиба :
что меньше допускаемое для стали 40Х улучшенной при знакопеременном симметричном изгибе -1up=70 MПа.
7 Определяем диаметр вала на входе (под шкивом):
dвх1=dn1(6 8)=35-7=28 мм что соответствует ГОСТ 6636-69*(см.табл.П.2.).
8 Определяем длину входного конца вала:
9 Диаметр буртика принимают в зависимости от размера фаски на внутреннем конце подшипника. У подшипника 7507 фаска 2х45 по этому d1 = dn1+8=35+8=43 мм;
10 Ширину канавки х на выход шлифовального круга и глубину для валов d≤50 мм принимают х =3 мм =025 мм.
1 Для определения нагрузки на более нагруженный подшипник у шкива необходимо определить расстояние l1 между точками приложения реакций. Для уменьшения реакций подшипники располагаем как можно дальше друг от друга. Ширину внутренней полоски редуктора согласно [ 12] принимаем b=b2+2 где — толщина стенки основания корпуса редуктора принимаем = 8 мм тогда b=67+2*8=83 мм. Длина гнезда под подшипники согласно [12] принята L = 45 мм тогда ширина корпуса по гнездам под подшипники ВК=b + 2L = 83+2*45=173 мм. Теперь определяем расстояние между точками приложения реакций:
l1= BK- 2а -2p=173-2*185-2*10=116 мм 116 мм.
2 Определяем силы действующие в зацеплении зубчатых колес. Так как редуктор горизонтальный окружная сила Ft= 3973 кН будет действовать в вертикальной плоскости. Радиальная составляющая Fr будет действовать в горизонтальной плоскости где действует сила давления ремней на шкив и вал F = 25 кН. Радиальная составляющая определяется по зависимости
Fr= Ft* tgα=3973*036322=1443 кН.
3 Определяем реакцию на подшипник у шкива (как более нагруженный) в горизонтальной плоскости из условия
4 Реакция на тот же подшипник в вертикальной плоскости
5 Полная реакция на подшипник
Определяем эквивалентную динамическую нагрузку:
где Х и У — коэффициенты соответственно радиальной и осевой нагрузок зависящее от конструкции подшипника и соотношения между осевой Fα1 и
радиальной Fr1 нагрузкой при Fα1 (V* Fr1)≤е X=1 и Y=0; е- коэффициент зависящий от угла контакта подшипника; Y — коэффициент вращения учитывающий какое кольцо вращается при вращении внутреннего кольца (в нашем случае) Y = 1 К – коэффициент безопасности учитывающий характер нагрузки для зубчатых редукторов принимают К=13; КТ — температурный коэффициент при t≤100С КТ=1. Для рассчитываемого подшипника Fα1=0 так как осевая составляющая от радиальной нагрузки более нагруженного подшипника будет больше осевой составляющей менее нагруженного подшипника.
7 Определяем срок службы подшипника:
Принимаем пoдшипник 7507. Второй подшипник нагружен слабее но для уменьшения номенклатуры пoдшипника ставим одинаковые подшипники.
Конструирование тихоходного вала.
1 Определяем диаметр вала под колесом dв = (03 035) принимаем d'в = 032*d= 032*180=576 мм. Согласно ГОСТ 6636-69* принимаем dв =56 мм (см. табл. П.2).
2 Определяем диаметр вала под подшипниками:
dn2 = dB-(1 5) =56-1=55 мм;
3 Определяем диаметр вала на входе:
dвх2 = dn2-(6 8) =55-7=48 мм что согласуется с табл. П.2.
4 Определяем длину входного конца вала:
5 Определяем диаметр буртика:
d2= dв+8=56+8=64 мм.
6 Определяем длину вала под ступицей:
l=lC-2=67-2=65 мм где длина ступицы lC= 67 мм.
7 Определяем длину направляющей части вала где посадка с зазором для диаметра dвх=48 мм (см.табл.П.7). Из технологических соображений на одном валу шпоночные канавки выполняют одинаковой ширины.
8 Ширину проточки х и глубину y принимаем х=3 мм y=025 мм (для валов 10≤d≤ 50 мм).
1 Определяем внутренний диаметр обода:
2 Определяем диаметр ступицы:
3 Определяем длину ступицы:
LС'=(1 12)*55=55 66. Принимаем LС= b2=67 мм.
4 Определяем толщину диска:
C'=03 b2=03*67=201 мм. Принимаем C=20 мм.
5 В диске выполняем четыре отверстия d0=40 мм для удобства крепления при обработке и транспортировке.
1 Ориентируясь на подшипник шариковый радиальный однородный особо легкой серии вписываем его данные из табл.П.6.
Данные подшипника шарикового особо легкой серии
Грузоподъемность кгс
2 Определяем силу нормального зуба на зуб:
Fn=Ftcosα= 39730 93909=4231 кН.
3 Так как зубчатое колесо расположено симметрично относительно опор радиальная нагрузка на подшипник
Fr2= Fn2=42312=2115 кН.
4 Эквивалентная динамическая нагрузка:
P2= Fr2 *K=2115*13=2749 кН.
5 Определяем срок службы подшипника:
1. По входному диаметру вала dвх1=28 мм согласно ГОСТ 23360-78 (см.табл.П.7) принимаем призматическую шпонку сечением b*h=8*7 мм.
2. Длину шпонки принимают меньше входной длины вала на 6 10 мм из ряда указанного в примечании к табл.П.7. Так как lвх1= 56 мм длину шпонки принимаем l=50 мм. Ставим шпонку с закругленными концами.
3 Проверяем напряжение смятия между шпонкой и чугунным шкивом:
СМ1= что меньше СМР= 80 мПа
СМ2= что меньше СМР= 80 мПа
Подбор и проверка шпонки тихоходного вала.
1. По входному диаметру вала dвх2=47 мм согласно ГОСТ 23360-78 (см.табл.П.7) принимаем призматическую шпонку сечением b*h=14*9 мм.
СМ= что меньше СМР= 80 мПа.
Определения количества и сорта смазки.
Закручивание зубчатой передачи при окружной скорости V[12 15] мс обычно смазывают окунанием в жидкую масляную ванну. Рекомендуемые значения смазки приведены в таблице
Окружная скорость V мс
При окружной скорости колеса V=292 мс принимаем смазку редуктора И-100А. Количество жидкой смазки выбирают из расчета 037-07 л на 1 кВт передаваемой мощности количество смазки определяется так же сечением внутренней полости корпуса редуктора и глубиной масляной ванны желательно предусмотреть расстояние между наибольшим колесом и днищем корпуса (не менее от 5 до 10 см) что дает возможность осаждается продуктом износа.
Конструкция корпуса редуктора.
Толщина стенки корпуса редуктора.
=0025*α+1=00225*180+1=505 мм;
Толщина стенки крышки редуктора
=002*α+1=002*180+1=46 мм;
Толщина верхнего фланга корпуса.
S1=(15 175)*=8*175=14 мм;
Толщина нижнего Франца корпуса.
Толщина Франца крышки редуктора.
Толщина ребер корпуса.
С1=(08 1)*=8*1=8 мм;
Ширина минимального зазора между колесом и корпусом.
Артоболевский И.И. «Теория механизмов и машин». – М.: Наука 1975. – 366 с.
ГОСТ 1284.1-80. «Ремни приводные клиновые нормальных сечений. Технические условия». – М.: Изд-во стандартов 1980
ГОСТ 1284.2-80 «Ремни приводные клиновые нормальных сечений. Технические условия». – М.: Изд-во стандартов 1980.
. ГОСТ 1284.3-80 «Ремни приводные клиновые нормальных сечений. Технические условия». – М.: Изд-во стандартов 1980.
Гузенков П.Г. «Детали машин».- М.: Высш.шк. 1982.-351с
Дунаев П.Ф. «Конструирование узлов и деталей машин».- М.: Высш.шк. 1978.-351с.
Зиновьев Вл.А. «Теория механизмов и машин». – М.: Высш.шк. 1963.-257с.
Методические указания к выполнению контрольных робот по курсу «Теория механизмов и машин и детали машин» Сост. В.А. Максимович.- Киев: КПИ 1982.- 24с.
Перель Л.Я. «Подшипники качения»: Справочник.- М.: Машиностроения 1983.- 543с.
Устименко В.Л. Киркач Н.Ф. Баласанян Р.А. «Основы проектирования деталей машин». – Харьков
Цехновыч Л.И. Петриченко И.П. «Атлас конструкций редукторов».-Киев: Выща шк. 1979.-127 с.
Чернавський С.А. Ицкович Г.М. Кисилев В.А. и др. «Проектирование механических передач: Учебно-справочное пособое по курсувому проектированию механических передач».- М.: Машиностроение 1976.–608 с.
Методические указание к выполнению курсового проекта по курсу «Теория механизмов и машин и детали машин» Сост. В.А. Максимович Г.В.Герасимов. – Киев: КПИ 1984. – 31с.
МНСТЕРСТВО ОСВТИ НАУКИ УКРАНИ
НАЦОНАЛЬНИЙ ТЕХНЧНИЙ УНВЕРСИТЕТ УКРАНИ
Пояснювальна записка
до курсового проекту з курсу
«Проектування приводу поршневого насосу подвійної дії»
Допущено до захисту студент 2-го курсу
Захищено з оцінкою залікова книжка
Курсовий проект з курсу
сборка.dwg

Технические требования
Редуктор Сборочный чертеж
Техническая характеристика Мощность на тихоходном валу N= Крутящий момент на тихоходном валу Т= Частота вращения быстроходного вала n= Передаточное число u=
Зазоры в зацеплении и пятно контакта по степени точности 8-В ГОСТ 1643-81 2. Редуктор обкатать без нагрузки втечение двух часов. 3. Сборку
окраску и консервацию редуктора производить по заводским техническим условиям.
Рекомендуемые чертежи
Свободное скачивание на сегодня
Обновление через: 1 час 2 минуты