Расчет турбины Д-25В


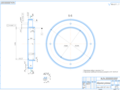
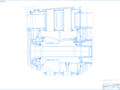
- Добавлен: 24.01.2023
- Размер: 473 KB
- Закачек: 1
- ВКонтакте
- РћРТвЂВВВВВВВВнокласснРСвЂВВВВВВВВРєРСвЂВВВВВВВВ
- Telegram
Подписаться на ежедневные обновления каталога:
Описание
Расчет турбины Д-25В
Состав проекта
![]() |
![]() |
![]() ![]() ![]() |
![]() ![]() ![]() ![]() |
![]() ![]() ![]() ![]() |
Дополнительная информация
Контент чертежей
курсовая пм.doc
Проектный расчет вала турбины .4
1Определение крутящего момента выбор материала и его основных .механических характеристи 4
2Определение наружного и внутреннего диаметров вала 4
Выбор подшипников 5
1Выбор подшипников по динамической грузоподъемности ..5
2Проверка подшипников на статическую грузоподъемность ..7
Проверочный расчет вала на усталостную прочность .8
1Построение эпюр изгибающих и крутящих моментов ..8
2Расчет амплитудных и средних значений цикла .9
3Выбор опасных сечений и определение запасов сопротивления усталости 9
4Расчет устойчивости вала при действии крутящего момента .14
5Расчет критической частоты вращения ротора турбины .. 15
Расчет на прочность соединений ..16
1Расчет на прочность шлицевого соединения .16
2Расчет на прочность штифтового соединения ..17
3Расчет на прочность группового резьбового соединения. 17
1Выбор марки масла и расчет его количества для смазки и охлаждения подшипников турбины 18.
2Описание системы смазки 22
Список использованной литературы .23
Описание узла конструкции турбины
Двигатель Д-25В представляет собой двухвальный турбовинтовой двигатель предназначенный для использования на вертолетах Ми-6 (и Ми-10). В мотоустановку вертолета входят два двигателя Д-25В и редуктор Р-7. Двигатели (правый и левый) взаимозаменяемы.
Особенностью двигателя Д-25В является наличие в нем свободной турбины для привода вала несущего винта вертолета не связанной кинематически с турбокомпрессорной частью двигателя. Наличие такого рода турбины дает возможность устанавливать на ней обороты независимо от режима работы турбокомпрессорной части двигателя.
Эта особенность имеет ряд конструктивных и эксплуатационных преимуществ а именно:
)Позволяет получать желаемое число оборотов вала несущего винта вертолета по режимам и высотам полета независимо от числа оборотов турбокомпрессорной части двигателя.
)Позволяет получать оптимальные расходы топлива при различных условиях эксплуатации двигателя.
)Обеспечивает более легкий запуск двигателя.
)Исключает необходимость иметь в силовой установке вертолета фрикционную муфту (муфту включения).
Двигатель состоит из следующих основных узлов:
- входного корпуса компрессора с коробками приводов агрегатов;
- осевого девятиступенчатого (восьмиступенчатого) компрессора с перепуском воздуха после III и IV ступеней компрессора. Перепуск воздуха осуществляется автоматически через отверстия прикрываемые лентами перепуска;
- трубчатокольцевой камеры сгорания с двенадцатью жаровыми трубами;
- одноступенчатой турбины работающей на привод компрессора;
- двухступенчатой турбины (турбина винта) работающей через редуктор на привод вала несущего винта вертолета;
- трансмиссии передающей крутящий момент от двухступенчатой турбины на редуктор;
- системы топливопитания и автоматического управления двигателем;
- системы автономного запуска со стартер-генератором;
- системы смазки и суфлирования;
- противопожарной системы двигателя;
На входном корпусе компрессора двигателя установлены верхняя и нижняя коробки приводов зубчатые колеса которых приводятся во вращение от вала ротора компрессора через центральный привод и шлицевые валики проходящие через полости верхней и нижней вертикальных стоек входного корпуса компрессора.
На верхней коробке приводов устанавливаются: стартер-генератор СТГ-12ТМ основной топливный насос-регулятор НР-23А (НР-23) подкачивающий топливный насос 707С центробежный регулятор ЦР-23А (ЦР-23) воздушный компрессор АК-50М датчик ДТЭ-2 счетчика оборотов и центробежный суфлер (только на двигателе 2-й серии).
На нижней коробке приводов устанавливаются: основной масляный насос МН-23В (МН-23) масляный фильтр 1ЛФС-19-18В центробежный воздухоотделитель ЦВО-23 (ЦВО-18) кран слива масла магнитная пробка и дренажный бачок.
На корпусе турбины винта устанавливается масляный насос откачки МНО-23Т приводимый во вращение от вала турбины винта через систему зубчатых колес и шлицевой валик.
Существует две модификации двигателя Д-25В. Первая серия - исходная модификация. Вторая серия двигателя отличается от первой количеством ступеней компрессора и техническими данными.
Проектный расчет вала турбины
Предварительно оцениваем средний диаметр вала из расчета только на кручение при пониженных допускаемых напряжениях разрабатываем схему вала.
1. Определение крутящего момента выбор материала и его основных механических характеристик
где Р- мощность Вт; n- число оборотов обмин.
Основные характеристики материала вала
Выбрана сталь 40ХНМА.
Предел выносливости -1= 600 МПа=6108Па;
Допускаемое напряжение на вал
где s – коэффициент запаса прочности; s=15..17. Выберем s=16.
2 Определение наружного и внутреннего диаметров полого вала
где Т- крутящий момент Нм ; a=dD= 4447=093 ; []- допускаемое напряжение Па.
По ГОСТ 6636-86 из ряда Ra 40 диаметр принимаем 100 мм..
Схема вала имеет вид:
Для нахождения расстояния между опорами необходимо рассчитать масштабный коэффициент:
где Dд - данный диаметр проточной части Dд =605мм
Dпрот -диаметр проточной части турбины измеренный на чертеже Dпрот =242 мм
где l1’ l2’- расстояния между опорами измеренные на чертеже.
Продольная (горизонтальная) реакция опоры определяется исходя из допущения что осевая нагрузка распределяется равномерно:
Fа1=Fа2=0.5Fo=0.586=4.3 кН.
Для определения вертикальных реакций опор составим уравнения изгибающих моментов относительно сечений 1 и 2:
Σ тот1= FR2 FR2= M l1= 145003859= 38 кН
Σ тот2= -FR1 FR1= -M l1= -145003859= -38 кН.
1. Подбор подшипников по динамической грузоподъемности
Подшипники подбираем по заданному ресурсу или долговечности.
Условие подбора : С потребное С паспортное
Вычислим эквивалентную динамическую нагрузку т.е. условную постоянную стационарную радиальную силу которая при приложении ее к подшипнику с вращающимся внутренним кольцом и с неподвижным наружным кольцом обеспечивает долговечность как и при действительных условиях нагружения:
где V- коэффициент вращения зависящий от того какое кольцо вращается относительно внешней нагрузки. В нашем случае вращается внутреннее кольцо следовательно ;
-температурный коэффициент для стали 40ХНМА примем ;
- коэффициент безопасности учитывающий характер нагрузки. При наличии умеренных толчков примем .
Подшипник опоры 1 (турбинный)
Предварительно примем для диаметра вала 105 мм радиально-упорный шарикоподшипник № 1176721 из особо легкой серии по ГОСТ 831-75 с диаметром внутреннего кольца d=105 мм С0=88800 Н Спаспортное=94100 Н.
Радиальная сила осевая сила
Значения различны в зависимости от отношений и.
По таблице примем для радиально- упорных шарикоподшипников следующие значения:
Вычислим эквивалентную динамическую нагрузку:
Второй этап выбора подшипника включает нахождение базовой динамической грузоподъемности Спотребное – это такая постоянная стационарная сила которую подшипник может воспринять в течение 1 млн. оборотов без проявления признаков усталости не менее чем у 90% испытываемых подшипников.
Динамическая грузоподъемность и ресурс связаны эмпирической зависимостью:
где - ресурс в млн. оборотов:
- для шариковых подшипников
коэффициент долговечности связанный с коэффициентом надежности .
обобщенный коэффициент совместного влияния качества металла и условий эксплуатации. Его выберем для обычных условий применения из интервала (07-08):
Динамическая грузоподъемность:
Предварительно примем для диаметра вала 100 мм радиально-упорный шарикоподшипник № 176220 из легкой серии по ГОСТ 831-75 с диаметром внутреннего кольца d=100 мм С0=95500 Н Спаспортное=142000 Н.
Радиальная сила осевая сила .
2. Проверка подшипников на статическую грузоподъемность.
Определим эквивалентную статическую нагрузку для проверки подшипника по статической грузоподъемности
Тогда статическая грузоподъемность:
Условие проверки Р0≤С0 выполняется для обоих подшипников.
Недогруз первого подшипника составит (1-)·100%=(1-)·100%=035%
Недогруз второго подшипника составит (1-)·100%=(1-)·100%=24%
Диаметр внутреннего кольца подшипника составит 100 мм т.е. наружный диаметр вала будет составлять 100мм.
Проверочный расчет вала на усталостную прочность
На практике установлено что для валов основным видом разрушения является усталостное. Статическое разрушение наблюдается значительно реже. Оно происходит под действием случайных кратковременных перегрузок при нарушении правил эксплуатации. Поэтому для валов расчет на сопротивление усталости является основным. Расчет же на статическую прочность выполняют как проверочный. Приступая к расчету предположительно намечают опасные сечения вала анализируя эпюры изгибающих и крутящих моментов ступенчатую форму вала и места концентрации напряжений.
1. Построение эпюр крутящих и изгибающих моментов
Построим эпюры крутящих и изгибающих моментов учитывая найденные ранее реакции в опорах: Fа1=Fа2=0.5Fo=0.586=4.3 кН.
Fr2= M l= 14503859= 3.8 кН
Fr1= -M l= -14503859= -3.8 кН.
2. Расчет средних и амплитудных значений цикла
Напряжения будут изменяться соответственно по следующим циклам:
Для первого опасного сечения (в качестве которого примем место посадки компрессорного подшипника с натягом):
Для второго опасного сечения в качестве которого выберем участок вала с наименьшим диаметром равноудаленный от обеих опор:
Для третьего опасного сечения в качестве которого выберем место посадки турбинного подшипника:
3. Выбор опасных сечений и определение запасов сопротивления усталости
В качестве первого опасного сечения примем место посадки с натягом шарикоподшипника определим коэффициент запаса сопротивления усталости и сравним его с допускаемым.
В этом сечении действуют продольная растягивающая сила и крутящий момент.
Примем минимально допустимое значение коэффициента запаса усталости:
При совместном действии напряжений кручения и изгиба коэффициент запаса сопротивления усталости определяют по формуле:
Где - запас сопротивления усталости по изгибу
- запас сопротивления усталости по кручению.
Здесь и - амплитуды переменных составляющих циклов напряжений а и - постоянные составляющие.
Пределы выносливости для стали 40 ХНМА - стали из которой изготовлен вал:
Предел прочности для этого же материала:
и - коэффициенты корректирующие влияние постоянной составляющей цикла напряжений на сопротивление усталости. Эти величины зависят от механических характеристик материала. По ГОСТ 25.504-82 рекомендуют:
Вычислим коэффициенты концентрации напряжений в опасном расчетном сечении при изгибе и кручении соответственно:
и - эффективные коэффициенты концентрации напряжений и -коэффициенты учитывающие размеры вала (масштабный фактор) и - коэффициенты влияния качества поверхности - коэффициент учитывающий наличие поверхностного упрочнения.
Величину отношения для посадок с натягом рассчитывают по формуле:
Вычислим коэффициенты влияния качества поверхности и :
Для этой части вала в качестве механической обработки возьмем чистовое шлифование
(). Тогда при изгибе вычислим:
На данном участке вала целесообразно применить шлифовку для которой:
Подставим все эти коэффициенты в уравнение для нахождения коэффициента концентрации напряжений:
Заключение: в данном опасном сечении условие усталостной прочности выполняется.
В качестве второго опасного сечения примем сечение вала равноудаленное от опор как участок вала с наименьшим диаметром. В этом сечении действуют продольная сжимающая сила и крутящий момент.
Для этой части вала в качестве механической обработки возьмем чистовое шлифование (). Тогда при изгибе вычислим:
В качестве третьего опасного сечения выберем место посадки турбинного подшипника.
4. Расчет устойчивости вала при действии крутящего момента
Расчет на устойчивость сводится к определению критических нагрузок вызывающих потерю устойчивости. Для пояснения представим что к оболочке вала приложены внешние нагрузки под действием которых она находится в состоянии равновесия. Если при возрастании нагрузок оболочка принимает новую устойчивую форму равновесия то эти значения нагрузок называются критическими а состояние оболочки в момент предшествующий началу перехода в новую форму также называется критическим. В этот момент происходит внезапный рост прогибов и деформаций что связано с наличием зоны сжимающих напряжений.
Сравним величину крутящего момента Т=8650 Нм с критическим моментом при кручении находимым по формуле:
где h-полутолщина оболочки
R-радиус срединной поверхности
l-расстояние между опорами l=03859 м
E-модуль упругости материала Е=204·1011Па.
Условие прочности вала на устойчивость при кручении выполняется.
5. Определение критического числа оборотов ротора
Ограничимся определением критически чисел оборотов ротора без учета моментов от сил инерции дисков.
где с-жесткость вала представляющая собой силу которую нужно приложить к валу чтобы получить прогиб равный единице т- масса дисков.
Величина с зависит от размеров вала места приложения нагрузки условий размещения вала на опорах и материала из которого он сделан. Для нашего случая
где модуль упругости Е=204·1011Па для стали 40ХНМА момент инерции I расстояние между опорами l=03859м расстояние от роликоподшипника до центра тяжести дисков b= 01414м (примем вес всех дисков сосредоточенный в одной точке).
где Di-диаметр диска h - толщина диска ρ=7800 кгм3 для стали 40ХНМА.
Внешний и внутренний диаметры вала D=01 м d=0093 м тогда момент инерции
Критическое число оборотов
Вывод: имеем двухкратный запас по критической частоте вращения ротора.
Расчет на прочность соединений
1. Расчет на прочность шлицевого соединения
Выбираем шлицевое соединение с центрированием по эвольвентным профилям зубьев (центрирование по S). Задаемся наружным диаметром D=100 мм и длиной соединения l≤15D возьмем l=D=100 мм.
Диаметр делительной окружности
Номинальный наружный диаметр соединения
Смещение исходного контура рейки
Номинальные толщина зубьев вала и
ширина впадины отверстия
по делительной окружности
наружный (окружности впадин)
внутренний (окружности выступов) при плоской впадине
внутренний (окружности выступов)
Условие прочности по допускаемым напряжениям смятия:
где Т-крутящий момент z- число зубьев h и l -высота и длина поверхности контакта зубьев (для эвольвентных зубьев h= m=5 мм) dm- делительный диаметр соединения -
коэффициент учитывающий неравномерное распределение нагрузки между зубьями и вдоль зубьев =05..07 выберем =06; допускаемое напряжение смятия на боковых поверхностях для подвихных соединений [ см]=01· в=01· 1600=160 МПа
Шлицевое эвольвентное соединение смятие выдержит
2. Расчет на прочность штифтового соединения
Штифтовые соединения предназначены для точного взаимного фиксирования двух деталей иногда – для передачи небольших нагрузок. Штифты работают на срез и на смятие.
Для заданного цилиндрического штифта 10×32 по ГОСТ 3128-70: dш=10мм Dст=183.6мм.
Из условия прочности штифта на срез найдем количество штифтов z:
Из условия прочности штифта на смятие:
Принимаем число штифтов z=12
3. Расчет на прочность группового резьбового соединения
Основным видом разрушения у крепежных резьбовых соединений является срез резьбы у ходовых резьбовых соединений – износ витков. Критерий работоспособности для крепежных резьбовых соединений – это прочность по касательным напряжениям среза для ходовых – износостойкость по напряжениям смятия.
Проведем проверку исходя из условия герметичности для винта М8 из материала 40ХН. Определим коэффициент основной нагрузки :
Податливость винта:
Податливость соединения:
l=20 мм h=108 мм Eд=200МПа Eв=200МПа Ад=0510-4 м2 Ав=0210-4 м2
Согласно условию сохранения плотности стыка силы затяжки одного винта в сечении с z винтами
Напряжения будут складываться из напряжений начальной затяжки и напряжений от внешней отрывающей стык силы:
Принимаем внешнюю силу отрывающую стык равной 04Fo=049000=3600Н. Тогда:
Принимаем число винтов необходимое для установки z=6.
1. Расчет теплового режима первого шарикоподшипника
Диаметр вала dв=0105м наружный диаметр подшипника D=0175м диаметр шарика dш=032·(D- dв)=032·(0175-0105)=00224м.
Число тел качения т=.
Число оборотов подшипника в мин .
Радиальная нагрузка на подшипник .
Осевая нагрузка на подшипник .
Максимальная температура масла на входе в подшипник
Необходимая температура подшипника
Оценка по справочным данным теплофизических параметров масла при :
)кинематическая вязкость
)удельная теплоемкость
)коэффициент температуропроводности
)критерий Прандтля .
включает в себя следующие пункты:
Определение окружной скорости сепаратора подшипника:
- диаметр окружных центров тяжести тел качения;
- угол контакта в подшипнике.
Расчет критерия Рейнольдса:
Оценка приведенной нагрузки на подшипник:
- кинематический коэффициент
- динамический коэффициент.
Определение усилия действуещего на один шарик:
Расчет критерия Эйлера:
Оценка суммарного коэффициента сопротивлений:
Определение суммарного теплового потока:
Расчет необходимой прокачки масла:
2. Расчет теплового режима второго шарикоподшипника
Диаметр вала dв=0100м наружный диаметр подшипника D=018м диаметр шарика dш=032·(D- dв)=032·(018-01)=00256м.
Расчет включает в себя следующие пункты:
2. Описание системы смазки
Малосистема необходима для смазки и охлаждения трущихся деталей двигателя а также удаления продуктов износа. Основными агрегатами системы являются:
- нагнетающие и откачивающие маслонасосы;
Рабочая жидкость маслосистемы для турбины типа Д-25В – синтетическое масло Б-3В.
Расход масла для ГТД Д-25В:
- для турбокомпрессорной части не более 10 кг на 1 час летного времени;
- для турбины винта трансмиссии не более 2.0 кг на 1 час летного времени
Список использованной литературы:
)Д.Н. Решетов. Детали машин. М.: Машиностроение 1989.
)М. Н. Иванов В. А. Финогенов. Детали Машин. М.: Высшая школа 2003.
)П. Ф. Дунаев О. П. Леликов. Конструирование узлов и деталей машин.-М.: Высшая школа 2001.
)Г. С. Писаренко А. П. Яковлев В. В. Матвеев. Справочник по сопротивлению материалов. Киев: Наукова Думка 1975.
)Р.Х. Гафаров В.С. Жернаков. Что нужно знать о сопротивлении материалов. М.: Машиностроение 2001.
)Р. Д. Бейзельман Б. В. Цыпкин Л. Я. Перель. Подшипники качения. Справочник. М.: Машиностроение 1975.
)Г. С. Скубачевский. Авиационные газотурбинные двигатели. М.: Машиностроение 1974.
)В. И. Анурьев. Справочник конструктора- машиностроителя. Тома 1;2. электронное издание.
)В. С. Левицкий. Машиностроительное черчение и автоматизация выполнения чертежей. М.: Высшая школа 2001.
)СТП УГАТУ 002-98. Уфа 1998.
Чертеж деталюшки5-1001.cdw

Неуказанные предельные отклонения размеров по ГОСТ 25670-83
Лабиринтное уплотнение
Сталь 40ХН ГОСТ 4543-71
чертежег.cdw

стороны соплового аппарата.
Рекомендуемые чертежи
- 24.01.2023
Свободное скачивание на сегодня
Обновление через: 5 часов 36 минут
Другие проекты
- 28.08.2014