Проектирование и исследование механизмов поперечно-строгального станка с качающейся кулисой вариант 3Б




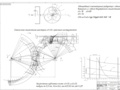
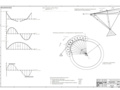
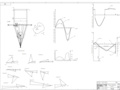
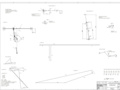
- Добавлен: 25.10.2022
- Размер: 7 MB
- Закачек: 0
Описание
Состав проекта
![]() |
![]() |
![]() ![]() ![]() ![]() |
![]() ![]() |
![]() |
![]() ![]() |
![]() ![]() ![]() ![]() |
![]() |
![]() |
![]() |
![]() |
![]() |
![]() |
![]() |
![]() |
![]() |
![]() |
![]() |
![]() |
![]() ![]() ![]() ![]() |
![]() ![]() |
![]() |
![]() |
![]() ![]() |
![]() ![]() ![]() ![]() |
![]() ![]() ![]() |
Дополнительная информация
Лист 3.dwg

Проектирование зубчатой
Теория механизмов и машин
МГТУ им. Н.Э.Баумана
Зона технологического заострения
Станочное зацепоение шестерни z1=12 с реечным инструментом
Зацепление зубчатых колес z1=12 и z2=23
внешним и с одним внутренним зацеплением U=8
Однорядный планетарный редуктор с одним
Лист 2.dwg

F30+F34+F21+G3+ФS3=0
-Fcl+M50+F50lS5-G5lS5=0
Fc +F43+F50+G5+ФS5x =0
Шавалеев(чертеж)-Лист2..docx
Loa=0.09 м Lcd=0.66 м Lcs
ф43 ф45 ф21 ф30 ф23 ф10 М
F43 F45 F21 F30 F23 F10 F50 М
Полученные данные (Силы Н
aA2 = aA + aAпостАк(
aA2 = aC + aA3Cn(DC) + aA3C
ad3 = aA3 (lCB lCA)
aS3 = aA3 (lCS3 lCA)
Лист 1.dwg

Лист 4.dwg

кулачкового механизма
Межосевое расстояние 0
Радиус начальной шайбы конструктивного профиля 0
Радиус начальной шайбы центрового профиля 0
. Наименование параметра Значение
Построение центрового и конструктивного профилей кулачка
шайбы кулачка по углу давления
Определение радиуса начальной окружности
Результаты проектирования кулачка
конструктивный и центровой профили
-кулачокж; 2-толкатель
РПЗ.docx
«Московский государственный технический университет имени Н.Э. Баумана»
(МГТУ им. Н.Э. Баумана)
ФАКУЛЬТЕТ «РОБОТОЕХНИКА И КОМПЛЕКСНАЯ АВТОМТИЗАЦИЯ»
КАФЕДРА«ПОДЪЕМНО-ТРАНСПОРТНЫЕ СИСТЕМЫ»
РАСЧЕТНО-ПОЯСНИТЕЛЬНАЯ ЗАПИСКА К КУРСОВОМУ ПРОЕКТУ
ПРОЕКТИРОВАНИЕ И ИССЛЕДОВАНИЕ МЕХАНИЗМОВ ПОПЕРЕЧНО-СТРОГАЛЬНОГО СТАНКА С КАЧАЮЩЕЙСЯ КУЛИСОЙ
Руководитель курсового проекта канд. техн. наук доцент
Исполнитель курсового проекта студент группы
Краткое описание работы механизмов поперечно-строгального станка с качающейся кулисой
Поперчно-строгальный станок предназначен для строгания поверхностей. Станок имеет следущие основные узлы: станина 1 ползун 2 с резцовой головкой 3 стол 4 (рис. 3-1).
Привод состоит из зубчатой передачи z4 z5 планетарного редуктора 6 и электродвигателя 7 (рис. 3-2 а).
Рис. 3-1. Общий вид поперчно-строгального станка с качающейся кулисой
Рис. 3-2. а) Схема кривошипно-кулисного и кулачкового механизмов
б) Диаграмма сил сопротивления
Резание металла осуществляется резцом закрепленным в резцовой головке при его возвратно-поступательном движении в горизонтальном направлении.
Для движения ползуна с резцовой головкой используется шестизонный кривошипно-кулисный механизм с качающейся кулисой состоящий из кривошипа 1 камня 2 кулисы 3 ползунов 4и5. Диаграмма сил сопротивлению движению ползуна 5 показана на рис. 3-2б.Ход ползуна H выбирается в зависимости от длины lД обрабатываемой поверхности с учетом перебегов lП в начале и конце рабочего хода. Длина хода ползуна может изменяться при накладке станка для обработки конкретных деталей. Средняя скорость резания (скорость поступательного движения при рабочем ходе) выбирается в зависимости от условий обработки.
Во время перебегов в конце холостого и в начале рабочего ходов осуществляется перемещение стола на величину подачи с помощью ходового винта. Поворот винта производится посредством храпового механизма состоящего из колеса 10 рычага 11 с собачкой тяги 9 и качающегося толкателя 8 рис.. 3—2 а).
Рис.3-3. Законы изменения ускорений толкателя кулачкового механизма:
Поворот толкателя 8 осуществляется от дискового кулачка который выполнен в виде паза в теле зубчатого колеса z5. Регулирование подачи стола производится путем изменения длины рычага LN что позволяет изменять количество зубьев захватываемых собачкой и следовательно обеспечивает поворот ходового винта на требуемый угол. При проектировании кулачкового механизма необходимо обеспечить заданный закон движения толкателя (рис. 3-3) и осуществить подачу резца во время заднего перебега (в конце холостого и в начале рабочего ходов) в соответствии с циклограммой приведенной на рис. 3—4.
Рис.3-4. Циклограмма работы механизмов строгального станка.
Наименование параметра
Максимальная длина хода ползуна
Длина перебега резца в долях от хода Н
Число оборотов кривошипа
Число оборотов электродвигателя
Коэффициент изменения скорости ползуна
Межосевое расстояние между опорами кривошипа и кулисы
Сила трения между ползуном и направляющими
Момент инерции кулисы относительно оси проходящей через ее центр тяжести
Отношение расстояния от точки С до центра тяжести кулисы к длине кулисы
Координата центра тяжести ползуна
Коэффициент неравномерности вращения кривошипа
Маховой момент ротора электродвигателя
Маховой момент зубчатых механизмов приведенный к валу электродвигателя
Угловая координата для силового расчета (рис. 3-2а)
Максимальный подъем толкателя
Максимально допустимый угол давления толкателя
Соотношение между величинами ускорений толкателя (рис. 3-3)
Число зубьев колеса 4
Число зубьев колеса 5
Модуль зубчатых колес 4.5
Число сателлитов в планетарном редукторе
Параметры исходного контура реечного инструмента
Расчет длин звеньев механизма
Угловой ход кулисы:
Длина кривошипа ОА:
Определение передаточных функций
Кинематические передаточные функции определяем методом планов скоростей. Для этого строим для всех положений механизма планы скоростей в произвольном масштабе.
Для нахождения функции аналогов скоростей будем использовать формулу:
Пусть расстояние pa на всех планах аналогов скоростей будет равно 50 мм тогда масштаб каждого плана: v=pVaVa.
v=58мм011 = 527.27 ммм.
Результаты расчетов сводим в таблицу:
Приведение масс и моментов инерции.
Т=Jпр(φ)*22 где Jпр(φ) = J1пр + J2пр(φ) .
В данной формуле J1пр = const – момент инерции первой группы звеньев а
J2пр = var – момент инерции второй группы звеньев.
Формула приведения для i звена данного механизма:
Jiпр = miV2qsi + Jsi2gi
Найдем приведенный момент инерции первой группы звеньев:
J1пр = J1пр + Jротпр + Jредукпр + Jмаховпр
Приведенный момент инерции второй группы звеньев:
Найдем аналог угловой скорости точки D:
Занесем полученный результаты в таблицу для 14 положений механизма.
Значения момента инерции второй группы звеньев в 12 положениях.
Определение приведенного момента.
Mcпр=Fc*Vqd*cos(Vqd)
Значение приведенных моментов.
Определение работы кинетической энергии.
Т2=I2пр *w122 где w122=const
Силовой расчет механизма
Силовой расчет механизма проводится в положении 2 угловая координата
кривошипа в данном положении φ = 60°.
Внешние силы действующие на звенья механизма:
Из первого листа для положения 2 механизма: угловая скорость 1 =638
Угловое ускорение Ем1dm dt звена динамической модели равное угловому
ускорению Е1 начального звена механизма (обобщенному угловому ускорению)определяется из уравнения движения в дифференциальной форме:
Jпр + 2 2 (dJпр dφ) = Mпр
полученного из уравнения Лагранжа 2-го рода и подсчитывается по формуле
= Мпр Jпр (2 * dJпр) Jпрdφ
Производную dJпрсумм dφ нашли графически используя соотношение
dJпр dφ = d(yJ J) d(xφ φ ) = φ dyJ J dyφ = (φ J) * tg
где - угол между касательной проведенной к кривой Jпрсумм(φ) в исследуемом положении и положительным направлением оси абсцисс. Таким образом угловое
ускорение звена 1 в положении 2 имеет значение: 1 = 1115
Построение плана ускорений механизма
Для нахождения ускорений центров масс звеньев и угловых ускорений звеньев необходимо построить план ускорений механизма.
Определяем ускорение точки А второго звена: a20 = a20 + a20n. Нормальное
a20n = 12 lao = 685 мс2
Нормальное ускорение Тангенциальное ускорение:
Полное ускорение точки А:
aA= sqrt((a20)2 + (a20n )2) = 685 мс2
Ускорение точки A третьего звена:
aA2 = aA + aAпостАк(DC) + аАпостАr(DC)
aA2 = aC + aA3Cn(DC) + aA3C(DC)
Ускорение Кориолиса для точки A третьего звена относительно второго звена:
aAпостА k = 2 3 Vаа2 = 262 мс2
Ускорение точки A3 найдено из плана ускорений: aA3 = 277 мс2
Методом пропорции найдены ускорения точек S3 D:
ad3 = aA3 (lCB lCA) = 5714 мс2
aS3 = aA3 (lCS3 lCA) = 2857 мс2
Определены угловые ускорения звеньев:
Определение сил инерции главных моментов сил инерции
Силы инерции определяются по формуле Фi=-mai откуда получено
Для определения главных моментов сил инерции воспользовались формулой
Для звеньев механизма получено
MФ1 = JIпр 1 = 385*115 = 44 Нм
Определение реакций в кинематических парах
Расчетные схемы для всех звеньев механизма а также планы сил изображены на графическом листе 2. Для нахождения неизвестных силовых факторов воспользовались принципом Даламбера.
Сумма всех сил звеньев 4-5:
Графическим способом определены величины F43=2601Н=F45
Сумма всех сил звеньев 2-3 :
Графическим способом определены величины F30=2440Н F23=F21=5040Н
Записана векторная сумма всех сил действующих на звено 1 и построен план сил:
Fk1 = 0 Откуда F12=F10=5040Н
Сумма всех моментов относительно точки O:
Проектирование эвольвентной зубчатой передачи
Число зубьев: Z1 =14 Z2=20;
Угол главного профиля: .
Угол наклона зубьев: =0º
Коэффициент радиального зазора .
Коэффициент высоты зуба: .
Геометрические параметры:
Угол профиля: t = arctg(tgαcos) = α.
Шаг: pt = pcos = p . (pt = Пmt)
Модуль зацепления зубьев: mt = mcos = m.
Коэффициент высоты головки зуба: hat = ha* cos = ha*.
Коэффициент радиального зазора: ct = c* * cos = c*.
Радиусы делительных окружностей колес: r12 = mt*z122 .
Радиусы основных окружностей: rb12 = mt*z122 * cost.
Суммарное смещение: xΣ = x1 + x2
Суммарное количество зубьев: zΣ = z1 + z2
Угол зацепления передачи: invtw = invt + 2xtgt z
Межосевые расстояния для положительной зубчатой передачи:
tw =rw1 + rw2 = (z1+z2)*cosα2cosw
Делительные диаметры шестерни и колеса: d1 = z1 * m ; d2 = z2 * m
Радиусы основных окружностей: rb1b2 = mt*z12*cosαt2
Начальные радиусы шестерни и колеса: rw1w2 = mz12cost2*cosrw
Коэффициенты воспринимаемого смещения: y = Z1+Z22(costcostw-1).
Коэффициент уравнительного смещения: Δy = xΣ y .
Исполнительные размеры зубчатых колес
Радиусы вершин зубьев шестерни и колеса: ra12 =mt(Z122+ hta* + x12 - Δy).
Радиусы впадин шестерни и колеса: rf12 =mt(Z122- hta* + x12 – ct*).
Высота зубьев колес: h = h1 = h2 = mt(2hta* + ct* - Δy).
Толщины зубьев шестерни и колеса по дугам делительных окружностей:
S12 = mt(П2 + 2x12tgt).
Углы профиля зуба в точке на окружности вершин: a12 = arccos(rb12ra12)
Толщины зубьев по дугам окружностей вершин:
sa12 = mtcostcosa12*[П2+2x12tgt-z12(inva12- invt)]
Качественные показатели
Коэффициент торцового перекрытия: = Z12Пtga1-tgtw+Z22П(tga2-tgtw)
Коэффициенты удельного скольжения: λ1’’ = Z2tga2-tgtwz1+z2tgtw-z2tga2(1+Z1Z2).
λ2’’ = Z1tga1-tgtwz1+z2tgtw-z1tga1(1+Z1Z2).
Коэффициент удельного давления:
p = mtu21+12awsintwu21= 2(z1+z2)z1z2tgtwcost
Для станочного зацепления
Толщина зуба (ширина впадины): е0t = S0t = Пmt2.
Радиус скругления: ρft =ct*mt1-sint
Шаг по хорде делительной окружности шестерни: p1 = mtz1sin(180°z1).
Шаг по хорде делительной окружности колеса: p2 = mtz2sin(180°z2).
Коэффициент смещения первого колеса выбирается исходя из трех условий:
) Отсутствие подреза:
) Отсутствие заострения:
) Обеспечение плавности:
Проектирование планетарного зубчатого механизма с цилиндрическими колесами.
Цель: рассчитать планетарный редуктор обеспечивающий заданное передаточное отношение и имеющий наименьший размер.
Числом сателлитов в планетарном редукторе к=3.
Передаточное отношение редуктора явно не задано поэтому мы его рассчитываем:
передаточное отношение редуктора
Вычисление чисел зубьев колес редуктора:
Проверяем условие сборки:
где N – целое число.
При любом значении P N будет целым.
Проверяем условие соседства:
866>0.77 - условие соседства выполняется.
Определим графически передаточное отношение:
U1h=w1wh=tg1tgh=AA`AA``=8
Вывод: спроектирован планетарный редуктор обеспечивающий передаточное отношение что подтверждают аналитический и графический расчет с допустимым отклонением между ними так же выполняются условия сборки и соседства.
Проектирование кулачкового механизма поперечной подачи стола
Цель: спроектировать кулачковый механизм минимальных размеров обеспечивающий заданный закон движения толкателя.
Построение кинематических диаграмм методом графического интегрирования
Строим график кинематической передаточной функции ускорения. По оси абсцисс откладываем рабочий угол раб. Вычисляем масштаб по оси :
Методом графического интегрирования строим график кинематической передаточной функции скорости толкателя VqB(1).
Аналогично строим график зависимости перемещения толкателя от угла поворота кулачка SB(1) графическим интегрированием диаграммы VqB(1).
Вычисляем масштабы по осям координат построенных графиков:
Определение основных размеров кулачкового механизма
Основные размеры механизма определяем с помощью фазового портрета который строим в полярной системе координат с полюсом в точке С в масштабе: . Для получения кулачкового механизма наименьших размеров необходимо определить минимальный радиус кулачка ro.
На первом этапе от полюса С в направлении откладываем отрезок равный длине толкателя в масштабе S. Для построения фазового портрета по оси S откладываем перемещение толкателя от начала координат. Значения снимаем с графика зависимости перемещения толкателя от угла поворота кулачка . От полученных точек откладываем отрезки кинематических передаточных функций перпендикулярно линии перемещения толкателя.
Построение профиля кулачка
Для построения профиля кулачка применяем метод обращения движения: всем звеньям механизма условно сообщаем угловую скорость равную -1. При этом кулачок остается неподвижным а остальные звенья вращаются с угловой скоростью равной по величине но противоположной по направлению угловой скорости кулачка.
Рекомендуемые чертежи
- 05.10.2019
- 24.01.2023