Расчет мостового крана


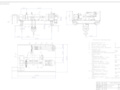
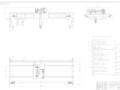
- Добавлен: 25.01.2023
- Размер: 4 MB
- Закачек: 0
Описание
Состав проекта
![]() |
![]() |
![]() |
![]() ![]() ![]() ![]() |
![]() ![]() ![]() ![]() |
![]() |
![]() ![]() ![]() |
![]() ![]() ![]() |
![]() ![]() ![]() |
![]() ![]() ![]() |
![]() ![]() ![]() |
![]() ![]() ![]() |
![]() ![]() ![]() |
![]() ![]() ![]() |
![]() ![]() ![]() |
![]() ![]() ![]() |
![]() ![]() ![]() |
Дополнительная информация
Кран мостовой (общий вид).dwg

Высота подъема груза
Группа режима работы
Продолжительность включения
передвижения тележки
Электродвигатель механизма:подъема
передвижения тележки:
Редуктор механизма:подъема
Тормоз механизма: подъема
ТЛК-О 6х31 ГОСТ7679-69
АК-РО- 6х36 ГОСТ7679-69
Тележка.dwg

передвижения тележки:
Тормоз механизма: подъема
Редуктор механизма:подъема
Электродвигатель механизма:подъема
передвижения тележки
Продолжительность включения
Группа режима работы
Высота подъема груза
Техническая характеристика
ПТМ 099.01.03.00.003
Аналетический обзор.doc
Мостовые краны предназначены для выполнения погрузочно-разгрузочных и транспортных операций в цехах промышленных предприятий на монтажных и контейнерных площадках на открытых и закрытых складах. Они перемещаются по рельсовым путям расположенным на значительной высоте от пола мало занимают полезного пространства цеха и обеспечивают обслуживание почти всей площади цеха.
Мостовой кран состоит из грузоподъемной тележки 3 включающий механизм подъема 8 грузозахватное устройство 5 механизм передвижение 9 и из моста 4 представляющего собой две сплошные (или решетчатые) формы присоединенные к концевым балкам 10 в которые вмонтированы приводные 12 и не приводные 11колеса. Механизм передвижения моста 1 имеет привод от одного или двух двигателей.
Спецификация крана.doc
Механизм передвижения моста
Кабина с аппаратурой
ПТМ 099.01.13.00.003
Тележка грузоподъемная
Устройство грузозахватное
Механизм передвижения
Аннотация.doc
Пояснительная записка состоит из 2 таблиц 7 рисунков и 33 страниц.
Основная цель курсового проекта – показать расчет механизма подъёма и передвижения отразить его качественный характер определить основные параметры и соотношения узлов и деталей мостового крана.
Ключевые слова: грузоподъёмные машины полиспаст блок крюковая подвеска траверса узел барабана маркировка динамическая грузоподъёмность редуктор колодка шкив момент инерции передаточное число установившееся движение.
1 Выбор электродвигателя и кинематический расчет привода.docx
Мостовой кран состоит из грузоподъемной тележки 3 включающий механизм подъема 9 грузозахватное устройство б механизм передвижение 10 и из моста 4 представляющего собой две сплошные (или решетчатые) формы присоединенные к концевым балкам 11 в которые вмонтированы приводные 13 и не приводные 12 колеса. Механизм передвижения моста 1 и 5 имеет привод от одного или двух двигателей.
Рассчитать механизм подъема крана общего назначения имеющего:
- грузоподъемность Q = 20 тс;
- наибольшую высоту подъема Н = 8 м;
- скорость подъема груза V = 0145 мс;
- режим работы - легкий.
Кинематическая схема механизма подъема представлена на рис. 1.
Рис.1. Кинематическая схема механизма подъема
В механизме подъема с непосредственной навивкой каната на барабан обычно применяют сдвоенный полиспаст при использовании которого обеспечивается вертикальное перемещение груза одинаковая нагрузка на подшипники барабана и на ходовые колеса тележки независимо от высоты подъема груза. Для крана грузоподъемностью 8 тс принимаем сдвоенный полиспаст (а = 2) кратностью u = 2 (приближенно кратность полиспаста можно выбирать по табл. 10).
Выбор полиспаста каната диаметра барабана и блоков
Максимальное напряжение в канате набегающем на барабан при подъеме груза определяется по формуле
где z – количество ветвей на которых висит груз
где - КПД блока с учетом жесткости каната = 0975
Канат выбираем по разрывному усилию
nk – коэффициент запаса прочности каната;
nk = 5 по [1 с.56 табл.11]
Sp = 507099 ·5 = 2535495 H
Выбираем ТЛК - 0 6х31(1 + 6 + 12 + 12) + 10с ГОСТ 7679-69 по [ приложение IV с. 456].
Расчетная площадь сечения Fk = 2336 мм2
= 1800 Н мм2 Sp = 25355 Н.
Диаметр блока и барабана по центру наматываемого каната
где е – коэффициент зависящий от режима работы и типа грузоподъемной машины[1 с.58 табл12].
Для легкого режима работы принимаем е = 20
Диаметр блока и барабана по центру канавки
Принимаем D = 260 мм по [1 с 458 приложение V].
Диаметр уравнительного блока
Блоки изготавливают из чугуна СЧ 15.
Выбор и проверочный расчет крюковой подвески
1. По номинальной грузоподъемности Q = 2 тc и режиму работы выбираем крюк однорогий тип А №15 ГОСТ 6627-74 [1 с 464 приложение VII]. Крюк изготовлен из стали 20 имеющей предел прочности QB = 420 MПa предел текучести QТ = 250 МПа предел выносливости Q-1 =120 МПа. Резьба шейки М 27 dВ = 23.85 мм t = 5 мм.
Рис.3. Крюк однорогий
Крюк рассчитывают на растяжение
МПа ≤[]=50 60 МПа (4.1)
В сечении А-А рассчитывают как кривой брус нагруженный эксцентрично приложенным усилием
где F - площадь сечения А-А
е2 – расстояние от центра тяжести сечения до внутренних волокон
k – коэффициент зависящий от кривизны и формы сечения крюка
r – расстояние от центра приложения нагрузки до центра тяжести сечения
= 95мм – диаметр зева крюка
l1 – расстояние от центра тяжести сечения до нагруженных волокон
е1=h0-е2=45-193=257мм (4.7)
Напряжение в сечении А’–А’ определяется когда стопы расположены под углом 450 к вершинам
Наибольшее растяжение внутренних волокон в сечении А’–А’
Касательное напряжение в сечении А’–А’
Сумарное напряжение в сечении А’–А’
Допускаемое напряжение
nТ – запас прочности по пределу текучести; nТ = 12 по [1 с.61]
Условие прочности соблюдается []
Высота гайки имеющей трапецеидальную резьбу должна быть не менее:
d2 – средний и минимальный диаметры мм;
p – допускаемое напряжение на смятые сталь по стали p = 300 350 МПа
(материал гайки сталь 45)
Высота гайки для метрической резьбы:
Н = 12d2=12 . 27=324 мм (4.12)
Высота гайки с учетом установки стопорной планки принимается Н = 40 мм
Наружный диаметр гайки
Dн= 18. d2=18. 27=486 мм (4.13)
Для крюка диаметром шейки d1 =30 мм выбираем упорный однорядный подшипник легкой серии 8206 по [1 с. 428 приложение IX ГОСТ 6874-75]
Расчетная нагрузка на подшипник должна быть равна или менее статической грузоподъемности
k = 12 – коэффициент безопасности [1 с. 471 приложение Х]
Qp =12 . 20000=24000 Н С0 = 47200
Траверса крюка изготовляется из стали 45 имеющей:в=610 МПа; т=450МПа -1=250МПа.
Траверсу рассчитывают на изгибе при допущении что действующие на неё силы сосредоточенные; кроме того считают что перерезывающие силы незначительно влияют на изгибающий момент. По [1 с.471приложения ХI] определяют расчетные размеры т.е. расстояние между осями крайних блоков b = 200 мм . Расчетная нагрузка на Максимальный изгибающий момент
момент сопротивления среднего сечения
Рис.4. Траверса крюка
Момент сопротивления среднего сечения траверсы
b1 – ширина траверсы назначается с учетом нагруженного диаметра D1 посадочного гнезда упорного подшипника
h – высота траверсы
Изгибающий момент в сечении Б-Б
Минимальный диаметр цапфы под подшипником
5 Выбор подшипников блоков
Эквивалентная нагрузка на подшипник
где Р1 Р2 Рn – эквивалентные нагрузки
L1 L2 Ln – номинальные долговечности
Рис.5. График загрузки для легкого режима
Для радиальных подшипников:
где Fr –радиальная нагрузка
Fа – осевая нагрузка Fа=0
XY – коэффициенты радиальных и осевых нагрузок для однорядных шарикоподшипников при
V – коэффициент вращения; при вращении наружного кольца V=12
k - коэффициент безопасности k=12
kt- температурный коэффициент kt=1
Fr2 = 0095 . Fr1=0095. 5000=475 Н
Fr3 = 005. Fr1=005.5000=250 Н
Р1 =1. 12.5000.12.1=7200 Н
Р2 =1.12.475.12.1=684 Н
Р3 = 1.12.250.12.1=360 Н
Долговечность подшипников номинальная и при каждом режиме нагрузки
где Lh ресурс подшипника Lh=1000 [1 с. 472 приложение ХII]
n – частота вращения подвижного блока крюковой подвески
L1= 04L=04. 064=0256 млн. об
L2 = L3=03L=03.064=0792 млн. об.
Динамическая грузоподъемность
C=L1αР α = 3 для шарикоподшипников
С= 0643 . 5306=1391 Н
Для данного диаметра цапфы по динамической грузоподъемности выбираем шариковый подшипник радиальный однорядный легкой серии №208 ГОСТ 8338-75 d= 40 мм. D=80 мм В=18 мм С= 2560 кгс.
Расчет узла барабана
Рис.6. Профиль канавок барабана
Принимаем барабан диаметром D=260 мм.
Расчетный диметр барабана Dб=268 мм.
Длина каната наматываемого на одну половину барабана
Lk=HU=80.2=16 м (5.1)
Число витков нарезки на одной половине барабана
Длина нагрузки на одной половине барабана
где tн – шаг нарезки барабана [1 с. 475 приложение XIV]
Полная длина барабана
где l3 – длина участка с каждой стороны барабана используемая для закрепления каната
l3= 4.tН = 4.9=36 мм (5.5)
lГ – расстояние между правой и левой нарезкой
lГ = b-2hmintgα (5.6)
hmin – расстояние между осью барабана и осью блоков в крайнем верхнем положении
α – допустимый угол отклонения набегающей на барабан ветви каната от вертикального положения α = 4 6
b – расстояние между осями ручьев крайних блоков b = 200 мм
lГ = 200-2.375.tg4 = 147 мм
Принимаем lГ = 150 мм
lб = 2(189+36)+150=600 мм
Барабан отлит из чугуна СЧ15 с В =700 МПа
Толщина стенки барабана
к – коэффициент запаса прочности для крюковых кранов к =425 по [1 приложение XV]
Толщина стенки должна быть не менее 12 мм
= 002D+(6 10)=002. 260+(6 10)=13 мм (5.8)
Крутящий момент передаваемый барабаном
Мкр= 2Smax. Н. мм (5.9)
М и = Smax. L = 5071. 268=1359028 Н . мм (5.10)
l- расстояние до среднего торцевого диска l = 268 мм
Сложное напряжение от изгиба и кручения
где W – эквивалентный момент сопротивления поперечного сечения барабана
φ – коэффициент приведения напряжения; φ = 075
2.Расчет крепления каната к барабану
Принята конструкция крепления каната к барабану прижимной планкой имеющей трапециевидные канавки . Канат удерживается от перемещения силой трения возникающей от зажатия его между планкой и барабаном болтами (шпильками). Начиная от планки предусматривают дополнительные витки (15 2) способствующие уменьшению усилия в точке закрепления каната.
Натяжение каната перед прижимной планкой
f – коэффициент рения между канатом и барабаном f = 010 016
α – угол обхвата каната барабаном принимаем α =4
Суммарное усилие растяжения болтов
где f1 – приведенный коэффициент трения между планкой и барабаном; при угле заклинивания каната 2 =80
Суммарное напряжение в болте при затяжки креплений с учетом растягивающего и изгибающего усилий
где n – коэффициент запаса надежности крепления каната к барабана n ≥ 15 принимаем n = 18
z =2 – количество болтов
Ри – усилие изгибающие болты
Р и = Рf1=39022 . 0233=9092 Н (5.17)
d1 – внутренний диаметр болта d1 =13835 мм (М 16)
[р] – допускаемое напряжение для болта
3. Расчет оси барабана
Ось барабана изготовлена из стали 45 с пределом прочности
Размеры выбираем конструктивно:
а=180 мм lВ = 420 мм
b =120 мм lС = 600 мм
l = 900 мм lД = 186+36=222 мм
Рис.7. Схема к расчету оси барабана
RB = 2 . Smax – RA = 2. 5071-4733=5409 Н
Усилие действующее со стороны ступицы на ось
RC = 2 . Smax - RD = 375254 Н
строим эпюры изгибающих моментов и перерезывающих сил
МС = RА . а =4733. 180=851940 Нмм
МD = RB . b = 5409. 120=649080 Нмм
Диаметр оси барабана
где [] – допускаемое напряжение для стали 45 [] = 55 МПа [1 с. 478 приложение XVIII ]
Выбор подшипников оси барабана
Расчетная нагрузка на подшипник
Qp = K . RB = 5409. 12=64908 Н (6.1)
Радиальные нагрузки на подшипник при легком режиме
Fr2 =0095. Fr1 =0095. 4733 =449635Н
Fr3 = 005. Fr1 =005. 4733=23665Н
Долговечность подшипника номинальная и при каждом режиме нагрузки
L1 = 04. L=04. 1241=049632 млн.об.
L2 = L3 =03. L= 03. 1241=037224 млн.об.
Р1 = (х. v + Fr1)k6 . kt =1. 1. 4733. 12.1=56796 Н (6.3)
С = L1α . Р = 124081333 . 41858=4466 Н
С целью соблюдения унификации для опоры А подбираем подшипник №1218
Расчет мощности двигателя и выбор редуктора
При подъеме номинального груза мощность двигателя механизма подъема:
где м = 085 – КПД [1 с. 488 приложение XXXIII]
Принимаем электродвигатель переменного тока с фазным ротором типа МТF
2-6 мощность РП = 31 кВт частотой вращения п =785 мин-1 или = 822 радс с максимальным моментом МПмах = 57 Н. м моментом инерции ротора jр=000293Н. м2
Номинальный момент на валу двигателя
МН = 975 кгс. М = 385 Н.м (7.2)
Отношение максимального момента к номинальному
Передаточное число редуктора
Выбираем редуктор Ц2-250 (межосевое расстояние А =250 мм передаточное число редуктора Uр =4134).
Допускаемое величина предельного момента передаваемого редуктора
Мпред = Мред = . 973 (7.5)
где Рред – табличное значение мощности редуктора Рред =120 кВт по [1 с. 511
– кратность пускового момента = 125 [1 с.78 т. 14]
Средний момент электродвигателя в период пуска
Поскольку МПср=49665Мпред = 1522 то редуктор удовлетворяет условию перегрузки двигателя.
Фактическая частота вращения барабана
Скорость подъема груза
Статический момент на валу электродвигателя
где SПi – усилие в навиваемом на барабан канате при подъеме груза
SП1 = 5071 Н SП2 = 01·SП1 = 5071 Н SП2 = 025·SП1 = 126775 Н;
а – число ветвей наматываемых на барабан
М – КПД механизма подъема
Усилие в канате свиваемом с барабана при опускании груза
Статический момент на валу двигателя при опускании груза
Момент инерции ротора электродвигателя
Момент инерции зубчатой муфты с тормозным шкивом [1 с. 513 приложение XLVII] JМ = 0471 кг. м2
JPM = JP + JM =00293+0471=05003 кг. м2 (7.12)
коэффициент учитывающий момент инерции масс деталей вращающихся медленнее чем вал двигателя принимаем = 12
Общее передаточное число
UM = UP. U = 4134. 2 = 8268 (7.13)
Момент инерции движущихся масс механизма приведенных к валу двигателя при подъеме груза
Время пуска при подъеме и опускании груза
Коэффициент учитывающий ухудшения условий охлаждения при пуске и торможении
где 0 – коэффициент учитывающий ухудшение условий охлаждения во время пауз для выбранного двигателя 0 =085
Для мостового крана работающего в сборочном цехе машиностроительного завода средняя высота подъема груза Нс = 15[1 с. 85 таблица 17].
Суммарное время за цикл работы установившегося движения
Σtу = 8tу = 8. 1035=8276 с.
Неустановившегося движения
ΣtП = 454. 2+065. 2+1805 +096+1085+09=24895 с.
Tp =Σ tу +Σ tП = 8276+24895=107655 с. (7.19)
Время пауз за цикл работы при ПВ = 15%
tц = tp +Σ t0 =107655+61005 = 7177 с
Число включений в час
Среднеквадратический момент эквивалентный по нагреву действительному переменному моменту возникающему от заданной нагрузки электродвигателя механизма подъема в течение цикла
Эквивалентная мощность по нагреву
Условие РЭ ≤ РП; 263 335 соблюдается следовательно выбранный электродвигатель удовлетворяет условию нагрева.
Усилие в канате наматываемом на барабан при подъеме груза
К.П.Д механизма подъема
Усилие в канате свиваемом с барабана при опускании груза
Приведенный момент инерции при подъеме и опускании груза
Расчетный тормозной момент
МТ = кТ . Мст.Т (8.1)
где кТ – коэффициент запаса торможения для режима кТ =15 [1 с. 84].
Мст.Т – статический момент на валу двигателя при торможении
Выбираем двух колодочный тормоз типа ТКТ-200 с наибольшим тормозным моментом МТ = 16 Н. м.
Момент инерции движения масс механизма приведенный к валу тормоза при торможении
Время торможения при подъеме груза
Выбираем диаметр шкива D =200 мм [1 с. 85]
Сила трения между колодкой и шкивом
Сила натяжения колодки на шкив
где f – коэффициент трения f = 033 [1 с. 86 таблица 19]
Радиальный зазор между шкивом и колодкой принимаем max = 13 мм
Работа расторможения при отходе колодок
где = 09 095 – КПД рычажной системы
Выбираем по[1 с. 524 приложения LIII] электродвигатель типа МО – 300Б с рабочим моментом электромагнита МЭ =1000 кгс. см
Работа растормаживания А = 9600 Н. мм; плечо штока
перемещение штока hш = 44 мм.
Момент отвеса якоря Мя = 9200 Н. м; угол поворота α = 55
Усилие приложенное к штоку при растормаживании
Передаточное число рычажной системы
После конструктивной проработки принимаем длину меньшего плеча
l1 = 200 мм. Длина большого плеча l2 =l1. UT = 200. 105 =210 мм конструктивно принимаем l2 =300 мм.
Максимально возможный отход колодки
где UТФ – фактическое передаточное число
Высота колодки тормоза
НК = (05 08)D = (05 08).200=100 260 мм
Принимаем НК = 150 мм что соответствует углу обхвата шкива =8336’
Ширина колодки при условии что ее давление на шкив равномерно распределено по поверхности
Принимаем ВК = 100 мм.
Между двигателем и редуктором устанавливается зубчатая муфта с тормозным шкивом DТ =300 мм [1 с. 513 приложение XLVII] имеющая следующую характеристику: наибольший передаваемый крутящий момент 3200 Н. м; момент инерции JМ = 0471 Н. м2; JПМ = 0121 Н. м2 .
Крутящий момент передаваемый муфтой в период пуска двигателя при опускании номинального груза
где J'Р.М – суммарный момент ротора электродвигателя и полумуфты
J'P.М =Jр +JПМ = 00293+0121=01503 кг. М2 (9.2)
Крутящийся момент при подъеме номинального груза
Максимальный крутящий момент при двигателя
МП.П = МП max – МП1 = 451-3868=642 Н. м (9.4)
Крутящий момент от сил инерции передаваемых муфтой
где JМ – момент инерции машины;
JМ = J ПР – J'РМ = 05003 -01503=035 кг. М2 (9.6)
Крутящий момент передаваемый муфтой в период пуска
Мmas = MП1 + Ми = 3868 + 45 =4318 Н. м
Из вычисленных значений моментов выбираем момент Мmas = 432 Н. м
Определяем расчетный крутящий момент для муфты
Мрасч = к1 . Мmax (9.7)
где к1 – коэффициент учитывающий степень ответственности муфты к1 =13
[1 с. 525 приложение IV]
Мрасч = 13. 432 = 5616 Н. м
Между барабаном и редуктором устанавливается зубчатая муфта.
Крутящий момент передаваемый муфтой
где =098 – КПД барабана
Расчетный момент для выбора муфты
Мрасч =13868. 165.11 =2517 Н. м
По таблице [1 с. 525 приложение V] выбираем стандартную зубчатую муфту (ГОСТ 5006-55) №3 с модулем m = 3; число зубьев kz = 40; ширина зуба
b = 20 мм; толщина зуба S1 = 435 мм наибольшим моментом передаваемым муфтой 3150 Н. м
Расчет механизма передвижения
1. Выбор кинематической схемы
Механизм передвижения тележки предполагается выполнить по кинематическойсхеме показанной на рис. Для передачи крутящего момента от двигателя к приводным колёсам использован вертикальный редуктор типа ВКН. Вал двигателя соединён с быстроходным валом редуктора втулочно-пальцевой муфтой на одной половине которой установлен колодочный тормоз с электрогидротолкателем.
Рис.8. Кинематическая схема передвижения тележки
2. Расчёт сопротивления передвижению тележки.
Сопротивление передвижению тележки с номинальным грузом при установившемся режиме работы определяем по формуле:
где Q = 20000 Н – номинальный вес поднимаемого груза;
Gт – собственный вес крановой тележки;
Dк – диаметр ходового колеса тележки. Предварительно выбираем диаметр колеса пользуясь рекомендациями 1 стр.106 табл. 25:
Принимаем двухребордные колёса с цилиндрическим профилем обода по 1 стр.526-528 прил. LIX LVI (ГОСТ 3569 – 74):
В = 50 мм – ширина рабочей дорожки;
d = (025 030)Dк – диаметр цапфы:
d = (025 030)200 = 50 60 мм
Принимаем d = 50 мм;
f = 0015 – коэффициент трения в подшипниках колёс; подшипники выбираем сферические двухрядные [1 стр.106 табл. 26;
= 003 мм – коэффициент трения качения колеса по плоскому рельсу 1 стр.106 табл. 27 . Колёса изготовлены из стали 65Г (ГОСТ 1050 – 74) твердость поверхности катания НВ 320 350;
kp = 25 – коэффициент учитывающий сопротивление от трения реборд колёс о рельсы и от трения токосъёмников о троллеи 1 стр.106 табл. 28 ;
Wук – сопротивление передвижению от уклона пути
- расчётный уклон подкранового пути:
= 0001 – для путей укладываемых на металлических балках с железобетонным фундаментом;
Wв – сопротивление передвижению от действия ветровой нагрузки. При расчёте мостовых кранов работающих в закрытых помещениях принимаем Wв = 0.
3. Расчёт мощности двигателя и выбор редуктора.
Для предварительного выбора двигателя определяем сопротивление передвижению загруженной тележки в пусковой период:
Где а – среднее ускорение тележки при пуске 1 стр.108 табл. 29 :
Мощность предварительно выбираемого двигателя:
где - средняя кратность пускового момента для асинхронных двигателей с фазовым ротором:
Расчётная мощность двигателя механизма передвижения и поворота определённая с учётом инерционных нагрузок должна удовлетворять условию:
Предварительно принимаю электродвигатель закрытый 80А8 с синхронной частотой 750 мин-1
Определяем средний пусковой момент двигателя для разгона незагруженной тележки:
Чтобы получить численное значение Мп.ср следует предварительно выбрать не только двигатель но и редуктор механизма передвижения тележки затем производим расчет привода и окончательно выбираем двигатель.
Определяем частоту вращения колеса:
Расчетное передаточное число редуктора:
По каталогу 1 стр.531 прил. LXII принимаем редуктор типа ВКН-280-16-1 (с передаточным числом uр = 16 схемой сборки №1)
Фактическая частота вращения колеса:
Фактическая скорость передвижения тележки с номинальным грузом:
Минимальное время пуска двигателя незагруженной тележки:
где ап.mах – максимально допустимое ускорение незагруженной тележки.
где - сцепной вес тележки.
ксц- коэффициент запаса сцепления; принимаем ксц равным 12.
- коэффициент сцепления ведущего колеса с рельсом; для кранов работающих в закрытых помещениях = 02;
Значение коэффициента кр принято равным 1 что идет в запас при расчете аТ
Статический момент сопротивления передвижению незагруженной тележки приведённый к валу двигателя;
Момент инерции подвижных масс тележки приведенный к валу двигателя;
где Jр.м – момент инерции ротора двигателя и муфт в том числе с тормозным шкивом;
Масса тележки с крюковой подвеской
Средний пусковой момент определяем по формуле(10.7):
Для привода механизма передвижения тележки окончательно принимаем электродвигатель 100LB8:
Средний пусковой момент двигателя
Фактическое время пуска двигателя нагруженной тележки:
Фактический коэффициент запаса сцепления приводных колёс с рельсами:
Фактическое ускорение при разгоне незагруженной тележки:
Время пуска и ускорение тележки при различных поднимаемых грузах с вожу в таблицу.
4. Проверка двигателя на нагрев по эквивалентной нагрузке.
Мощность необходимая для перемещения тележки с номинальным грузом
Среднее время пуска привода тележки при перемещении грузов Q; 01Q; Q; 025Q и незагруженной
Среднее время рабочей операции передвижения тележки
где Lр – средний рабочий путь тележки 1 стр.83 табл. 17 Lр = 6 м
Отношение среднего времени пуска к среднему времени рабочей операции
По графику 1 стр.112 рис. 45(кривая Б) находим значение коэффициент
Рэ = Рн.г=095·023=0218 кВт
Эквивалентная мощность двигателя
Nэ15 = К Nэ =05218 = 0109 кВт
где К – коэффициент принимаемый в зависимости от режима работы который выбираем по 1 стр.113 табл. 30 .
Ранее выбранный двигатель удовлетворяет условию нагрева.
5. Расчёт тормозного момента и выбор тормоза.
При торможении тележки без груза допустимое максимальное ускорение при котором обеспечивается запас сцепления колёс с рельсами 12 определяем по формуле:
Время торможения тележки без груза исходя из максимально допустимого ускорения
Допускаемая величина тормозного пути 1 стр.113 табл. 31
Минимально допустимое время торможения
Время торможения тележки в общем виде находим по формуле
где Мт – тормозной момент который находим по формуле
где Мст.т – статический момент сопротивления передвижению тележки при торможении приведённый к валу двигателя
Принимаем колодочный тормоз с гидротолкателем типа ТТ – 160 с наибольшим тормозным моментом 100 Нм диаметром тормозного шкива 160 мм шириной колодки 75 мм; тип гидротолкателя ТЭГ – 16 с тяговым усилием 160 Н. Тормоз отрегулируем на необходимый тормозной момент
Результаты расчёта механизма передвижения тележки заносим в табл2.
Незагруженная тележка
Сопротивление передвижению тележки Н
Статический момент сопротивления при передвижении тележки Нм
6. Расчёт ходовых колёс
Нагрузка на одно ведущее колесо при условии их одинакового нагружения
где Qсц = 10000 Н – сила давления на ведущие колёса от поднимаемого груза.
Расчётная нагрузка на колесо
где = 08 – коэффициент учитывающий переменность нагрузки находим по 1стр.116 табл. 33 ;
k1= 11 – коэффициент учитывающий режим работы механизма;
Значения местных напряжений смятия при линейном контакте:
где b – рабочая ширина рельса; для принятого квадратного рельса 50х50
b = В 2r1=50-2·25=45 мм
r1 – радиус закругления ребра рельса;
Rk=125 мм – радиус колеса.
Выбираем колёса крановые (ГОСТ 3569 – 74) по 1 стр.526 прил. LVI изготовленные из стали 65Г с твёрдостью поверхности катания НВ 320 350 см = 850 МПа
Епр = 21105 МПа – приведенный модуль упругости для стального колеса и стального рельса.
Величина местных напряжений смятия при точечном контакте (в случае применения рельса со скруглённой головкой)
где Rmах – наибольший из двух радиусов R1 и Rк контактирующих поверхностей
R1 – радиус закругления головки рельса
m – коэффициент зависящий от отношения наименьшего радиуса к наибольшему из двух радиусов соприкасающихся поверхностей принимается по 1 стр.117 табл. 35
Полученные результаты удовлетворяют заданным условиям.
1 Выбор электродвигателя и кинематический расчет привода.doc
Мостовой кран состоит из грузоподъемной тележки 3 включающий механизм подъема 9 грузозахватное устройство б механизм передвижение 10 и из моста 4 представляющего собой две сплошные (или решетчатые) формы присоединенные к концевым балкам 11 в которые вмонтированы приводные 13 и не приводные 12 колеса. Механизм передвижения моста 1 и 5 имеет привод от одного или двух двигателей.
Рассчитать механизм подъема крана общего назначения имеющего:
- грузоподъемность Q = 40 тс;
- наибольшую высоту подъема Н = 15 м;
- скорость подъема груза V = 0116 мс;
- режим работы - тяжелый.
Кинематическая схема механизма подъема представлена на рис. 1.
Рис.1. Кинематическая схема механизма подъема
В механизме подъема с непосредственной навивкой каната на барабан обычно применяют сдвоенный полиспаст при использовании которого обеспечивается вертикальное перемещение груза одинаковая нагрузка на подшипники барабана и на ходовые колеса тележки независимо от высоты подъема груза. Для крана грузоподъемностью 4 тс принимаем сдвоенный полиспаст (а = 2) кратностью u = 2 (приближенно кратность полиспаста можно выбирать по табл. 10).
Выбор полиспаста каната диаметра барабана и блоков
Максимальное напряжение в канате набегающем на барабан при подъеме груза определяется по формуле
где z – количество ветвей на которых висит груз
где - КПД блока с учетом жесткости каната = 0975
Канат выбираем по разрывному усилию
nk – коэффициент запаса прочности каната;
nk = 5 по [1 с.56 табл.11]
Sp = 1014198 ·6 = 6085192 H
Выбираем ТЛК - 0 6х31(1 + 6 + 12 + 12) + 10с ГОСТ 7679-69 по [ приложение IV с. 456].
Расчетная площадь сечения Fk = 2336 мм2
= 1800 Н мм2 Sp = 25355 Н.
Диаметр блока и барабана по центру наматываемого каната
где е – коэффициент зависящий от режима работы и типа грузоподъемной машины[1 с.58 табл12].
Для легкого режима работы принимаем е = 20
Диаметр блока и барабана по центру канавки
Принимаем D = 260 мм по [1 с 458 приложение V].
Диаметр уравнительного блока
Блоки изготавливают из чугуна СЧ 15.
Выбор и проверочный расчет крюковой подвески
1. По номинальной грузоподъемности Q = 2 тc и режиму работы выбираем крюк однорогий тип А №15 ГОСТ 6627-74 [1 с 464 приложение VII]. Крюк изготовлен из стали 20 имеющей предел прочности QB = 420 MПa предел текучести QТ = 250 МПа предел выносливости Q-1 =120 МПа. Резьба шейки М 27 dВ = 23.85 мм t = 5 мм.
Рис.3. Крюк однорогий
Крюк рассчитывают на растяжение
МПа ≤[]=50 60 МПа (4.1)
В сечении А-А рассчитывают как кривой брус нагруженный эксцентрично приложенным усилием
где F - площадь сечения А-А
е2 – расстояние от центра тяжести сечения до внутренних волокон
k – коэффициент зависящий от кривизны и формы сечения крюка
r – расстояние от центра приложения нагрузки до центра тяжести сечения
= 95мм – диаметр зева крюка
l1 – расстояние от центра тяжести сечения до нагруженных волокон
е1=h0-е2=45-193=257мм (4.7)
Напряжение в сечении А’–А’ определяется когда стопы расположены под углом 450 к вершинам
Наибольшее растяжение внутренних волокон в сечении А’–А’
Касательное напряжение в сечении А’–А’
Сумарное напряжение в сечении А’–А’
Допускаемое напряжение
nТ – запас прочности по пределу текучести; nТ = 12 по [1 с.61]
Условие прочности соблюдается []
Высота гайки имеющей трапецеидальную резьбу должна быть не менее:
d2 – средний и минимальный диаметры мм;
p – допускаемое напряжение на смятые сталь по стали p = 300 350 МПа
(материал гайки сталь 45)
Высота гайки для метрической резьбы:
Н = 12d2=12 . 27=324 мм (4.12)
Высота гайки с учетом установки стопорной планки принимается Н = 40 мм
Наружный диаметр гайки
Dн= 18. d2=18. 27=486 мм (4.13)
Для крюка диаметром шейки d1 =30 мм выбираем упорный однорядный подшипник легкой серии 8206 по [1 с. 428 приложение IX ГОСТ 6874-75]
Расчетная нагрузка на подшипник должна быть равна или менее статической грузоподъемности
k = 12 – коэффициент безопасности [1 с. 471 приложение Х]
Qp =12 . 20000=24000 Н С0 = 47200
Траверса крюка изготовляется из стали 45 имеющей:в=610 МПа; т=450МПа -1=250МПа.
Траверсу рассчитывают на изгибе при допущении что действующие на неё силы сосредоточенные; кроме того считают что перерезывающие силы незначительно влияют на изгибающий момент. По [1 с.471приложения ХI] определяют расчетные размеры т.е. расстояние между осями крайних блоков b = 200 мм . Расчетная нагрузка на Максимальный изгибающий момент
момент сопротивления среднего сечения
Рис.4. Траверса крюка
Момент сопротивления среднего сечения траверсы
b1 – ширина траверсы назначается с учетом нагруженного диаметра D1 посадочного гнезда упорного подшипника
h – высота траверсы
Изгибающий момент в сечении Б-Б
Минимальный диаметр цапфы под подшипником
5 Выбор подшипников блоков
Эквивалентная нагрузка на подшипник
где Р1 Р2 Рn – эквивалентные нагрузки
L1 L2 Ln – номинальные долговечности
Рис.5. График загрузки для легкого режима
Для радиальных подшипников:
где Fr –радиальная нагрузка
Fа – осевая нагрузка Fа=0
XY – коэффициенты радиальных и осевых нагрузок для однорядных шарикоподшипников при
V – коэффициент вращения; при вращении наружного кольца V=12
k - коэффициент безопасности k=12
kt- температурный коэффициент kt=1
Fr2 = 0095 . Fr1=0095. 5000=475 Н
Fr3 = 005. Fr1=005.5000=250 Н
Р1 =1. 12.5000.12.1=7200 Н
Р2 =1.12.475.12.1=684 Н
Р3 = 1.12.250.12.1=360 Н
Долговечность подшипников номинальная и при каждом режиме нагрузки
где Lh ресурс подшипника Lh=1000 [1 с. 472 приложение ХII]
n – частота вращения подвижного блока крюковой подвески
L1= 04L=04. 064=0256 млн. об
L2 = L3=03L=03.064=0792 млн. об.
Динамическая грузоподъемность
C=L1αР α = 3 для шарикоподшипников
С= 0643 . 5306=1391 Н
Для данного диаметра цапфы по динамической грузоподъемности выбираем шариковый подшипник радиальный однорядный легкой серии №208 ГОСТ 8338-75 d= 40 мм. D=80 мм В=18 мм С= 2560 кгс.
Расчет узла барабана
Рис.6. Профиль канавок барабана
Принимаем барабан диаметром D=260 мм.
Расчетный диметр барабана Dб=268 мм.
Длина каната наматываемого на одну половину барабана
Lk=HU=80.2=16 м (5.1)
Число витков нарезки на одной половине барабана
Длина нагрузки на одной половине барабана
где tн – шаг нарезки барабана [1 с. 475 приложение XIV]
Полная длина барабана
где l3 – длина участка с каждой стороны барабана используемая для закрепления каната
l3= 4.tН = 4.9=36 мм (5.5)
lГ – расстояние между правой и левой нарезкой
lГ = b-2hmintgα (5.6)
hmin – расстояние между осью барабана и осью блоков в крайнем верхнем положении
α – допустимый угол отклонения набегающей на барабан ветви каната от вертикального положения α = 4 6
b – расстояние между осями ручьев крайних блоков b = 200 мм
lГ = 200-2.375.tg4 = 147 мм
Принимаем lГ = 150 мм
lб = 2(189+36)+150=600 мм
Барабан отлит из чугуна СЧ15 с В =700 МПа
Толщина стенки барабана
к – коэффициент запаса прочности для крюковых кранов к =425 по [1 приложение XV]
Толщина стенки должна быть не менее 12 мм
= 002D+(6 10)=002. 260+(6 10)=13 мм (5.8)
Крутящий момент передаваемый барабаном
Мкр= 2Smax. Н. мм (5.9)
М и = Smax. L = 5071. 268=1359028 Н . мм (5.10)
l- расстояние до среднего торцевого диска l = 268 мм
Сложное напряжение от изгиба и кручения
где W – эквивалентный момент сопротивления поперечного сечения барабана
φ – коэффициент приведения напряжения; φ = 075
2.Расчет крепления каната к барабану
Принята конструкция крепления каната к барабану прижимной планкой имеющей трапециевидные канавки . Канат удерживается от перемещения силой трения возникающей от зажатия его между планкой и барабаном болтами (шпильками). Начиная от планки предусматривают дополнительные витки (15 2) способствующие уменьшению усилия в точке закрепления каната.
Натяжение каната перед прижимной планкой
f – коэффициент рения между канатом и барабаном f = 010 016
α – угол обхвата каната барабаном принимаем α =4
Суммарное усилие растяжения болтов
где f1 – приведенный коэффициент трения между планкой и барабаном; при угле заклинивания каната 2 =80
Суммарное напряжение в болте при затяжки креплений с учетом растягивающего и изгибающего усилий
где n – коэффициент запаса надежности крепления каната к барабана n ≥ 15 принимаем n = 18
z =2 – количество болтов
Ри – усилие изгибающие болты
Р и = Рf1=39022 . 0233=9092 Н (5.17)
d1 – внутренний диаметр болта d1 =13835 мм (М 16)
[р] – допускаемое напряжение для болта
3. Расчет оси барабана
Ось барабана изготовлена из стали 45 с пределом прочности
Размеры выбираем конструктивно:
а=180 мм lВ = 420 мм
b =120 мм lС = 600 мм
l = 900 мм lД = 186+36=222 мм
Рис.7. Схема к расчету оси барабана
RB = 2 . Smax – RA = 2. 5071-4733=5409 Н
Усилие действующее со стороны ступицы на ось
RC = 2 . Smax - RD = 375254 Н
строим эпюры изгибающих моментов и перерезывающих сил
МС = RА . а =4733. 180=851940 Нмм
МD = RB . b = 5409. 120=649080 Нмм
Диаметр оси барабана
где [] – допускаемое напряжение для стали 45 [] = 55 МПа [1 с. 478 приложение XVIII ]
Выбор подшипников оси барабана
Расчетная нагрузка на подшипник
Qp = K . RB = 5409. 12=64908 Н (6.1)
Радиальные нагрузки на подшипник при легком режиме
Fr2 =0095. Fr1 =0095. 4733 =449635Н
Fr3 = 005. Fr1 =005. 4733=23665Н
Долговечность подшипника номинальная и при каждом режиме нагрузки
L1 = 04. L=04. 1241=049632 млн.об.
L2 = L3 =03. L= 03. 1241=037224 млн.об.
Р1 = (х. v + Fr1)k6 . kt =1. 1. 4733. 12.1=56796 Н (6.3)
С = L1α . Р = 124081333 . 41858=4466 Н
С целью соблюдения унификации для опоры А подбираем подшипник №1218
Расчет мощности двигателя и выбор редуктора
При подъеме номинального груза мощность двигателя механизма подъема:
где м = 085 – КПД [1 с. 488 приложение XXXIII]
Принимаем электродвигатель переменного тока с фазным ротором типа МТF
2-6 мощность РП = 31 кВт частотой вращения п =785 мин-1 или = 822 радс с максимальным моментом МПмах = 57 Н. м моментом инерции ротора jр=000293Н. м2
Номинальный момент на валу двигателя
МН = 975 кгс. М = 385 Н.м (7.2)
Отношение максимального момента к номинальному
Передаточное число редуктора
Выбираем редуктор Ц2-250 (межосевое расстояние А =250 мм передаточное число редуктора Uр =4134).
Допускаемое величина предельного момента передаваемого редуктора
Мпред = Мред = . 973 (7.5)
где Рред – табличное значение мощности редуктора Рред =120 кВт по [1 с. 511
– кратность пускового момента = 125 [1 с.78 т. 14]
Средний момент электродвигателя в период пуска
Поскольку МПср=49665Мпред = 1522 то редуктор удовлетворяет условию перегрузки двигателя.
Фактическая частота вращения барабана
Скорость подъема груза
Статический момент на валу электродвигателя
где SПi – усилие в навиваемом на барабан канате при подъеме груза
SП1 = 5071 Н SП2 = 01·SП1 = 5071 Н SП2 = 025·SП1 = 126775 Н;
а – число ветвей наматываемых на барабан
М – КПД механизма подъема
Усилие в канате свиваемом с барабана при опускании груза
Статический момент на валу двигателя при опускании груза
Момент инерции ротора электродвигателя
Момент инерции зубчатой муфты с тормозным шкивом [1 с. 513 приложение XLVII] JМ = 0471 кг. м2
JPM = JP + JM =00293+0471=05003 кг. м2 (7.12)
коэффициент учитывающий момент инерции масс деталей вращающихся медленнее чем вал двигателя принимаем = 12
Общее передаточное число
UM = UP. U = 4134. 2 = 8268 (7.13)
Момент инерции движущихся масс механизма приведенных к валу двигателя при подъеме груза
Время пуска при подъеме и опускании груза
Коэффициент учитывающий ухудшения условий охлаждения при пуске и торможении
где 0 – коэффициент учитывающий ухудшение условий охлаждения во время пауз для выбранного двигателя 0 =085
Для мостового крана работающего в сборочном цехе машиностроительного завода средняя высота подъема груза Нс = 15[1 с. 85 таблица 17].
Суммарное время за цикл работы установившегося движения
Σtу = 8tу = 8. 1035=8276 с.
Неустановившегося движения
ΣtП = 454. 2+065. 2+1805 +096+1085+09=24895 с.
Tp =Σ tу +Σ tП = 8276+24895=107655 с. (7.19)
Время пауз за цикл работы при ПВ = 15%
tц = tp +Σ t0 =107655+61005 = 7177 с
Число включений в час
Среднеквадратический момент эквивалентный по нагреву действительному переменному моменту возникающему от заданной нагрузки электродвигателя механизма подъема в течение цикла
Эквивалентная мощность по нагреву
Условие РЭ ≤ РП; 263 335 соблюдается следовательно выбранный электродвигатель удовлетворяет условию нагрева.
Усилие в канате наматываемом на барабан при подъеме груза
К.П.Д механизма подъема
Усилие в канате свиваемом с барабана при опускании груза
Приведенный момент инерции при подъеме и опускании груза
Расчетный тормозной момент
МТ = кТ . Мст.Т (8.1)
где кТ – коэффициент запаса торможения для режима кТ =15 [1 с. 84].
Мст.Т – статический момент на валу двигателя при торможении
Выбираем двух колодочный тормоз типа ТКТ-200 с наибольшим тормозным моментом МТ = 16 Н. м.
Момент инерции движения масс механизма приведенный к валу тормоза при торможении
Время торможения при подъеме груза
Выбираем диаметр шкива D =200 мм [1 с. 85]
Сила трения между колодкой и шкивом
Сила натяжения колодки на шкив
где f – коэффициент трения f = 033 [1 с. 86 таблица 19]
Радиальный зазор между шкивом и колодкой принимаем max = 13 мм
Работа расторможения при отходе колодок
где = 09 095 – КПД рычажной системы
Выбираем по[1 с. 524 приложения LIII] электродвигатель типа МО – 300Б с рабочим моментом электромагнита МЭ =1000 кгс. см
Работа растормаживания А = 9600 Н. мм; плечо штока
перемещение штока hш = 44 мм.
Момент отвеса якоря Мя = 9200 Н. м; угол поворота α = 55
Усилие приложенное к штоку при растормаживании
Передаточное число рычажной системы
После конструктивной проработки принимаем длину меньшего плеча
l1 = 200 мм. Длина большого плеча l2 =l1. UT = 200. 105 =210 мм конструктивно принимаем l2 =300 мм.
Максимально возможный отход колодки
где UТФ – фактическое передаточное число
Высота колодки тормоза
НК = (05 08)D = (05 08).200=100 260 мм
Принимаем НК = 150 мм что соответствует углу обхвата шкива =8336’
Ширина колодки при условии что ее давление на шкив равномерно распределено по поверхности
Принимаем ВК = 100 мм.
Между двигателем и редуктором устанавливается зубчатая муфта с тормозным шкивом DТ =300 мм [1 с. 513 приложение XLVII] имеющая следующую характеристику: наибольший передаваемый крутящий момент 3200 Н. м; момент инерции JМ = 0471 Н. м2; JПМ = 0121 Н. м2 .
Крутящий момент передаваемый муфтой в период пуска двигателя при опускании номинального груза
где J'Р.М – суммарный момент ротора электродвигателя и полумуфты
J'P.М =Jр +JПМ = 00293+0121=01503 кг. М2 (9.2)
Крутящийся момент при подъеме номинального груза
Максимальный крутящий момент при двигателя
МП.П = МП max – МП1 = 451-3868=642 Н. м (9.4)
Крутящий момент от сил инерции передаваемых муфтой
где JМ – момент инерции машины;
JМ = J ПР – J'РМ = 05003 -01503=035 кг. М2 (9.6)
Крутящий момент передаваемый муфтой в период пуска
Мmas = MП1 + Ми = 3868 + 45 =4318 Н. м
Из вычисленных значений моментов выбираем момент Мmas = 432 Н. м
Определяем расчетный крутящий момент для муфты
Мрасч = к1 . Мmax (9.7)
где к1 – коэффициент учитывающий степень ответственности муфты к1 =13
[1 с. 525 приложение IV]
Мрасч = 13. 432 = 5616 Н. м
Между барабаном и редуктором устанавливается зубчатая муфта.
Крутящий момент передаваемый муфтой
где =098 – КПД барабана
Расчетный момент для выбора муфты
Мрасч =13868. 165.11 =2517 Н. м
По таблице [1 с. 525 приложение V] выбираем стандартную зубчатую муфту (ГОСТ 5006-55) №3 с модулем m = 3; число зубьев kz = 40; ширина зуба
b = 20 мм; толщина зуба S1 = 435 мм наибольшим моментом передаваемым муфтой 3150 Н. м
Расчет механизма передвижения
1. Выбор кинематической схемы
Механизм передвижения тележки предполагается выполнить по кинематическойсхеме показанной на рис. Для передачи крутящего момента от двигателя к приводным колёсам использован вертикальный редуктор типа ВКН. Вал двигателя соединён с быстроходным валом редуктора втулочно-пальцевой муфтой на одной половине которой установлен колодочный тормоз с электрогидротолкателем.
Рис.8. Кинематическая схема передвижения тележки
2. Расчёт сопротивления передвижению тележки.
Сопротивление передвижению тележки с номинальным грузом при установившемся режиме работы определяем по формуле:
где Q = 20000 Н – номинальный вес поднимаемого груза;
Gт – собственный вес крановой тележки;
Dк – диаметр ходового колеса тележки. Предварительно выбираем диаметр колеса пользуясь рекомендациями [1 стр.106 табл. 25]:
Принимаем двухребордные колёса с цилиндрическим профилем обода по [1 стр.526-528 прил. LIX LVI ] (ГОСТ 3569 – 74):
В = 50 мм – ширина рабочей дорожки;
d = (025 030)Dк – диаметр цапфы:
d = (025 030)200 = 50 60 мм
Принимаем d = 50 мм;
f = 0015 – коэффициент трения в подшипниках колёс; подшипники выбираем сферические двухрядные [1 стр.106 табл. 26];
m = 003 мм – коэффициент трения качения колеса по плоскому рельсу [1 стр.106 табл. 27 ]. Колёса изготовлены из стали 65Г (ГОСТ 1050 – 74) твердость поверхности катания НВ 320 350;
kp = 25 – коэффициент учитывающий сопротивление от трения реборд колёс о рельсы и от трения токосъёмников о троллеи [1 стр.106 табл. 28 ];
Wук – сопротивление передвижению от уклона пути
a - расчётный уклон подкранового пути:
a = 0001 – для путей укладываемых на металлических балках с железобетонным фундаментом;
Wв – сопротивление передвижению от действия ветровой нагрузки. При расчёте мостовых кранов работающих в закрытых помещениях принимаем Wв = 0.
3. Расчёт мощности двигателя и выбор редуктора.
Для предварительного выбора двигателя определяем сопротивление передвижению загруженной тележки в пусковой период:
Где а – среднее ускорение тележки при пуске [1 стр.108 табл. 29 ]:
Мощность предварительно выбираемого двигателя:
где - средняя кратность пускового момента для асинхронных двигателей с фазовым ротором:
Расчётная мощность двигателя механизма передвижения и поворота определённая с учётом инерционных нагрузок должна удовлетворять условию:
Предварительно принимаю электродвигатель закрытый 80А8 с синхронной частотой 750 мин-1
Определяем средний пусковой момент двигателя для разгона незагруженной тележки:
Чтобы получить численное значение Мп.ср следует предварительно выбрать не только двигатель но и редуктор механизма передвижения тележки затем производим расчет привода и окончательно выбираем двигатель.
Определяем частоту вращения колеса:
Расчетное передаточное число редуктора:
По каталогу [1 стр.531 прил. LXII ] принимаем редуктор типа ВКН-280-16-1 (с передаточным числом uр = 16 схемой сборки №1)
Фактическая частота вращения колеса:
Фактическая скорость передвижения тележки с номинальным грузом:
Минимальное время пуска двигателя незагруженной тележки:
где ап.mах – максимально допустимое ускорение незагруженной тележки.
где - сцепной вес тележки.
ксц- коэффициент запаса сцепления; принимаем ксц равным 12.
j - коэффициент сцепления ведущего колеса с рельсом; для кранов работающих в закрытых помещениях j = 02;
Значение коэффициента кр принято равным 1 что идет в запас при расчете аТ
Статический момент сопротивления передвижению незагруженной тележки приведённый к валу двигателя;
Момент инерции подвижных масс тележки приведенный к валу двигателя;
где Jр.м – момент инерции ротора двигателя и муфт в том числе с тормозным шкивом;
Масса тележки с крюковой подвеской
Средний пусковой момент определяем по формуле(10.7):
Для привода механизма передвижения тележки окончательно принимаем электродвигатель 100LB8:
Средний пусковой момент двигателя
Фактическое время пуска двигателя нагруженной тележки:
Фактический коэффициент запаса сцепления приводных колёс с рельсами:
Фактическое ускорение при разгоне незагруженной тележки:
Время пуска и ускорение тележки при различных поднимаемых грузах с вожу в таблицу.
4. Проверка двигателя на нагрев по эквивалентной нагрузке.
Мощность необходимая для перемещения тележки с номинальным грузом
Среднее время пуска привода тележки при перемещении грузов Q; 01Q; Q; 025Q и незагруженной
Среднее время рабочей операции передвижения тележки
где Lр – средний рабочий путь тележки [1 стр.83 табл. 17 ] Lр = 6 м
Отношение среднего времени пуска к среднему времени рабочей операции
По графику [1 стр.112 рис. 45(кривая Б) ] находим значение коэффициент
Рэ = g ×Рн.г=095·023=0218 кВт
Эквивалентная мощность двигателя
Nэ15 = К× Nэ =05×218 = 0109 кВт
где К – коэффициент принимаемый в зависимости от режима работы который выбираем по [1 стр.113 табл. 30 ].
Ранее выбранный двигатель удовлетворяет условию нагрева.
5. Расчёт тормозного момента и выбор тормоза.
При торможении тележки без груза допустимое максимальное ускорение при котором обеспечивается запас сцепления колёс с рельсами 12 определяем по формуле:
Время торможения тележки без груза исходя из максимально допустимого ускорения
Допускаемая величина тормозного пути [1 стр.113 табл. 31 ]
Минимально допустимое время торможения
Время торможения тележки в общем виде находим по формуле
где Мт – тормозной момент который находим по формуле
где Мст.т – статический момент сопротивления передвижению тележки при торможении приведённый к валу двигателя
Принимаем колодочный тормоз с гидротолкателем типа ТТ – 160 с наибольшим тормозным моментом 100 Н×м диаметром тормозного шкива 160 мм шириной колодки 75 мм; тип гидротолкателя ТЭГ – 16 с тяговым усилием 160 Н. Тормоз отрегулируем на необходимый тормозной момент
Результаты расчёта механизма передвижения тележки заносим в табл2.
Незагруженная тележка
Сопротивление передвижению тележки Н
Статический момент сопротивления при передвижении тележки Нм
6. Расчёт ходовых колёс
Нагрузка на одно ведущее колесо при условии их одинакового нагружения
где Qсц = 10000 Н – сила давления на ведущие колёса от поднимаемого груза.
Расчётная нагрузка на колесо
где g = 08 – коэффициент учитывающий переменность нагрузки находим по [1стр.116 табл. 33 ];
k1= 11 – коэффициент учитывающий режим работы механизма;
Значения местных напряжений смятия при линейном контакте:
где b – рабочая ширина рельса; для принятого квадратного рельса 50х50
b = В - 2r1=50-2·25=45 мм
r1 – радиус закругления ребра рельса;
Rk=125 мм – радиус колеса.
Выбираем колёса крановые (ГОСТ 3569 – 74) по [1 стр.526 прил. LVI ] изготовленные из стали 65Г с твёрдостью поверхности катания НВ 320 350 [s]см = 850 МПа
Епр = 21×105 МПа – приведенный модуль упругости для стального колеса и стального рельса.
Величина местных напряжений смятия при точечном контакте (в случае применения рельса со скруглённой головкой)
где Rmах – наибольший из двух радиусов R1 и Rк контактирующих поверхностей
R1 – радиус закругления головки рельса
m – коэффициент зависящий от отношения наименьшего радиуса к наибольшему из двух радиусов соприкасающихся поверхностей принимается по [1 стр.117 табл. 35 ]
Полученные результаты удовлетворяют заданным условиям.
Мостовой кран(частичный расчет).doc
Кинематическая схема механизма подъема представлена на рис. 1.
Рис.1. Кинематическая схема механизма подъема
В механизме подъема с непосредственной навивкой каната на барабан обычно применяют сдвоенный полиспаст при использовании которого обеспечивается вертикальное перемещение груза одинаковая нагрузка на подшипники барабана и на ходовые колеса тележки независимо от высоты подъема груза. Для крана грузоподъемностью 4 тс принимаем сдвоенный полиспаст (а = 2) кратностью u = 2 (приближенно кратность полиспаста можно выбирать по табл. 10).
Выбор полиспаста каната диаметра барабана и блоков
Максимальное напряжение в канате набегающем на барабан при подъеме груза определяется по формуле
где z – количество ветвей на которых висит груз
где - КПД блока с учетом жесткости каната = 0975
Канат выбираем по разрывному усилию
nk – коэффициент запаса прочности каната;
nk = 6 по [1 с.56 табл.11]
Sp = 10141.98 ·6 = 6085192 H
Выбираем АК-РО 6х36(1 + 7 + 77 + 14) + 10с ГОСТ 7668-69 по [ приложение IV с. 456].
Расчетная площадь сечения Fk = 3882 мм2
Расчетный вес 383.5 Н
= 1700 Н мм2 Sp = 60851 Н.
Диаметр блока и барабана по центру наматываемого каната
где е – коэффициент зависящий от режима работы и типа грузоподъемной машины[1 с.58 табл12].
Для тяжелого режима работы принимаем е = 30
DБЛ = 30 ·9.7=291 мм
Диаметр блока и барабана по центру канавки
Принимаем D = 335 мм по [1 с 458 приложение V].
Диаметр уравнительного блока
Блоки изготавливают из чугуна СЧ 15.
Выбор и проверочный расчет крюковой подвески
1. По номинальной грузоподъемности Q = 4 тc и режиму работы выбираем крюк однорогий тип А №13 ГОСТ 6627-74 [1 с 464 приложение VII]. Крюк изготовлен из стали 20 имеющей предел прочности QB = 420 MПa предел текучести QТ = 250 МПа предел выносливости Q-1 =120 МПа. Резьба шейки М 42 dВ = 37.129 мм t = 4.5 мм.
Рис.3. Крюк однорогий
Крюк рассчитывают на растяжение
МПа ≤[]=50 60 МПа (1.8)
В сечении А-А рассчитывают как кривой брус нагруженный эксцентрично приложенным усилием
где F - площадь сечения А-А
Принимаем b=20 b2=48
е2 – расстояние от центра тяжести сечения до внутренних волокон
k – коэффициент зависящий от кривизны и формы сечения крюка
r – расстояние от центра приложения нагрузки до центра тяжести сечения
= 95мм – диаметр зева крюка
l1 – расстояние от центра тяжести сечения до нагруженных волокон
е1=h0-е2=75-3235=4273мм (1.14)
Напряжение в сечении А’–А’ определяется когда стопы расположены под углом 450 к вершинам
Наибольшее растяжение внутренних волокон в сечении А’–А’
Касательное напряжение в сечении А’–А’
Сумарное напряжение в сечении А’–А’
Допускаемое напряжение
nТ – запас прочности по пределу текучести; nТ = 175 по [1 с.61]
Условие прочности соблюдается []
Высота гайки имеющей трапецеидальную резьбу должна быть не менее:
d2 – средний и минимальный диаметры мм;
p – допускаемое напряжение на смятые сталь по стали p = 300 350 МПа
(материал гайки сталь 45)
Высота гайки для метрической резьбы:
Н = 12d2=12 . 42=504 мм (1.19)
Высота гайки с учетом установки стопорной планки принимается Н = 55 мм
Наружный диаметр гайки
Dн= 18. d2=18. 42=756 мм (1.20)
4. Упорный подшипник
Для крюка диаметром шейки d1 =45 мм выбираем упорный однорядный подшипник легкой серии 8209 по [1 с. 468 приложение IX ГОСТ 6874-75]
Расчетная нагрузка на подшипник должна быть равна или менее статической грузоподъемности
k = 12 – коэффициент безопасности [1 с. 471 приложение Х]
Qp =12 . 40000=48000 Н С0 = 90500
Траверса крюка изготовляется из стали 45 имеющей:в=610 МПа; т=450МПа -1=250МПа.
Траверсу рассчитывают на изгибе при допущении что действующие на неё силы сосредоточенные; кроме того считают что перерезывающие силы незначительно влияют на изгибающий момент. По [1 с.471приложения ХI] определяют расчетные размеры т.е. расстояние между осями крайних блоков b = 200 мм . Расчетная нагрузка на траверсу =48000 Н . Расчетная нагрузка на Максимальный изгибающий момент
момент сопротивления среднего сечения
Рис.4. Траверса крюка
Момент сопротивления среднего сечения траверсы
b1 – ширина траверсы назначается с учетом нагруженного диаметра D1 посадочного гнезда упорного подшипника
h – высота траверсы
Изгибающий момент в сечении Б-Б
Минимальный диаметр цапфы под подшипником
6 Выбор подшипников блоков
Эквивалентная нагрузка на подшипник
где Р1 Р2 Рn – эквивалентные нагрузки
L1 L2 Ln – номинальные долговечности
Рис.5. График загрузки для тяжелый режима
Для радиальных подшипников:
где Fr –радиальная нагрузка
Fа – осевая нагрузка Fа=0
XY – коэффициенты радиальных и осевых нагрузок для однорядных шарикоподшипников при
V – коэффициент вращения; при вращении наружного кольца V=12
k - коэффициент безопасности k=12
kt- температурный коэффициент kt=1
Fr2 = 075 . Fr1=075. 10000=7500 Н
Fr3 = 0195. Fr1=0195.10000=1950 Н
Fr4 = 005. Fr1=005.10000=500 Н
Р1 =1. 12.10000.12.1=14400 Н
Р2 =1.12.7500. 12.1=10800 Н
Р3 = 1.12.1950.12.1=2808 Н
Р4 = 1.12.500.12.1=720 Н
Долговечность подшипников номинальная и при каждом режиме нагрузки
где Lh ресурс подшипника Lh=1000 [1 с. 472 приложение ХII]
n – частота вращения подвижного блока крюковой подвески
L1= L3 =02L=02. 063=0126 млн. об
L2 =06L2=06.063=0378 млн. об.
L3 =07L3=07.063=0.441 млн. об.
Динамическая грузоподъемность
C=L1αР α = 3 для шарикоподшипников
Для данного диаметра цапфы по динамической грузоподъемности выбираем шариковый подшипник радиальный однорядный средней серии №304 ГОСТ 8338-75 d= 20 мм. D=52 мм В=15 мм С= 12500 кгс.
7 Расчет узла барабана
Рис.6. Профиль канавок барабана
Принимаем барабан диаметром D=335 мм.
Расчетный диметр барабана Dб=344.7 мм.
Длина каната наматываемого на одну половину барабана
Lk=HU=15.2=30 м (1.33)
Число витков нарезки на одной половине барабана
Длина нагрузки на одной половине барабана
где tн – шаг нарезки барабана [1 с. 475 приложение XIV]
Полная длина барабана
где l3 – длина участка с каждой стороны барабана используемая для закрепления каната
l3= 4.tН = 4.11=44 мм (1.37)
lГ – расстояние между правой и левой нарезкой
lГ = b-2hmintgα (1.38)
hmin – расстояние между осью барабана и осью блоков в крайнем верхнем положении
α – допустимый угол отклонения набегающей на барабан ветви каната от вертикального положения α = 4 6
b – расстояние между осями ручьев крайних блоков b = 200 мм
lГ = 200-2.650.tg4 = 109 мм
Принимаем lГ = 110 мм
lб = 2(319+44)+110=836 мм
Барабан отлит из чугуна СЧ15 с В =700 МПа
Толщина стенки барабана
к – коэффициент запаса прочности для крюковых кранов к =425 по [1 приложение XV]
Толщина стенки должна быть не менее 12 мм
= 002D+(6 10)=002. 335+(6 10)=14.7 мм (1.40)
Крутящий момент передаваемый барабаном
Мкр= 2Smax. Н. мм (1.41)
М и = Smax. L = 10142. 363=3681546 Н . мм (1.42)
l- расстояние до среднего торцевого диска l = 363 мм
Сложное напряжение от изгиба и кручения
где W – эквивалентный момент сопротивления поперечного сечения барабана
φ – коэффициент приведения напряжения; φ = 075
8 Расчет крепления каната к барабану
Принята конструкция крепления каната к барабану прижимной планкой имеющей трапециевидные канавки . Канат удерживается от перемещения силой трения возникающей от зажатия его между планкой и барабаном болтами (шпильками). Начиная от планки предусматривают дополнительные витки (15 2) способствующие уменьшению усилия в точке закрепления каната.
Натяжение каната перед прижимной планкой
f – коэффициент рения между канатом и барабаном f = 010 016
α – угол обхвата каната барабаном принимаем α =4
Суммарное усилие растяжения болтов
где f1 – приведенный коэффициент трения между планкой и барабаном; при угле заклинивания каната 2 =80
Суммарное напряжение в болте при затяжки креплений с учетом растягивающего и изгибающего усилий
где n – коэффициент запаса надежности крепления каната к барабана n ≥ 15 принимаем n = 18
z =2 – количество болтов
Ри – усилие изгибающие болты
Р и = Рf1=2263.9 . 0233=5274 Н (1.49)
d1 – внутренний диаметр болта d1 =13835 мм (М 16)
[р] – допускаемое напряжение для болта
9 Расчет оси барабана
Ось барабана изготовлена из стали 45 с пределом прочности
Размеры выбираем конструктивно:
а=150 мм lВ = 538 мм
b =120 мм lС = 836 мм
l = 1106 мм lД = 418 мм
Рис.7. Схема к расчету оси барабана
RB = 2 . Smax – RA = 2. 10141.98-19866.88=10417.08 Н
Усилие действующее со стороны ступицы на ось
RC = 2 . Smax - RD = 10141.98 Н
строим эпюры изгибающих моментов и перерезывающих сил
МС = RА . а =9866.88. 150=1480032 Нмм
МD = RB . b = 10417.08. 120=1250049.6Нмм
Диаметр оси барабана
где [] – допускаемое напряжение для стали 45 [] = 55 МПа [1 с. 478 приложение XVIII ]
10 Выбор подшипников оси барабана
Расчетная нагрузка на подшипник
Qp = K . RB = 10417.08. 12=12500.5 Н (1.61)
Радиальные нагрузки на подшипник при тяжелом режиме
Fr2 = 075 . Fr1=075. 9866.88=740016 Н
Fr3 = 0195. Fr1=0195.9866.88=1924.04 Н
Fr4 = 005. Fr1=005.9866=4933 Н
Долговечность подшипника номинальная и при каждом режиме нагрузки
L1= L3 =02L=02. 1095=0219 млн. об
L2 =06L2=06.1095=0657 млн. об.
L3 =07L3=07.1095=0.766 млн. об.
Р1 = (х. v + Fr1)k6 . kt =1. 1. 9866.88. 12.1=1184145 Н (1.63)
С = L1α . Р = 109513 . 91092=9360.61 Н
11 Расчет мощности электродвигателя и выбор редуктора
При подъеме номинального груза мощность двигателя механизма подъема:
где м = 085 – КПД [1 с. 488 приложение XXXIII]
Принимаем электродвигатель переменного тока с фазным ротором типа МТF
1-6 мощность РП = 9 кВт частотой вращения п =960 мин-1 или = 10048 радс с максимальным моментом МПмах = 320 Н. м моментом инерции ротора
Номинальный момент на валу двигателя
МН = 975 кгс. М = 91.4 Н.м (1.66)
Отношение максимального момента к номинальному
Передаточное число редуктора
Выбираем редуктор Ц2-350 (межосевое расстояние А =350 мм передаточное число редуктора Uр =5094).
Допускаемое величина предельного момента передаваемого редуктора
Мпред = Мред = . 973 (1.69)
где Рред – табличное значение мощности редуктора Рред =9 кВт по [1 с. 510
– кратность пускового момента = 20 [1 с.78 т. 14]
Средний момент электродвигателя в период пуска
Поскольку МПср=21937Мпред = 2231 то редуктор удовлетворяет условию перегрузки двигателя.
Фактическая частота вращения барабана
Скорость подъема груза
Статический момент на валу электродвигателя
где SПi – усилие в навиваемом на барабан канате при подъеме груза
SП1 = 10141.98 Н SП2 = 05·SП1 = 507099 Н SП2 = 075·SП1 = 760648 Н;
а – число ветвей наматываемых на барабан
М – КПД механизма подъема
Усилие в канате свиваемом с барабана при опускании груза
Статический момент на валу двигателя при опускании груза
Момент инерции ротора электродвигателя
Момент инерции зубчатой муфты с тормозным шкивом [1 с. 513 приложение XLVII] JМ = 00763 кг.м.с2
JPM = JP + JM =00229+00763=00992 кг.м.с2 (1.76)
коэффициент учитывающий момент инерции масс деталей вращающихся медленнее чем вал двигателя принимаем = 12
Общее передаточное число
UM = UP. U = 5094. 2 = 10188 (1.77)
Момент инерции движущихся масс механизма приведенных к валу двигателя при подъеме груза
Время пуска при подъеме и опускании груза
Коэффициент учитывающий ухудшения условий охлаждения при пуске и торможении
где 0 – коэффициент учитывающий ухудшение условий охлаждения во время пауз для выбранного двигателя 0 =07
Для мостового крана работающего в сборочном цехе машиностроительного завода средняя высота подъема груза Нс = 15[1 с. 85 таблица 17].
Суммарное время за цикл работы установившегося движения
Σtу = 8tу = 8. 227=1816 с.
Неустановившегося движения
ΣtП = 094. 2+017. 2+0348 +0275+0194+0.175=321 с.
Tp =Σ tу +Σ tП = 1816+321=2137 с. (1.83)
Время пауз за цикл работы при ПВ = 40%
tц = tp +Σ t0 =2137+3205 = 5342 с
Число включений в час
Среднеквадратический момент эквивалентный по нагреву действительному переменному моменту возникающему от заданной нагрузки электродвигателя механизма подъема в течение цикла
Эквивалентная мощность по нагреву
Условие РЭ ≤ РП; 717 738 соблюдается следовательно выбранный электродвигатель удовлетворяет условию нагрева.
Усилие в канате наматываемом на барабан при подъеме груза
К.П.Д механизма подъема
Усилие в канате свиваемом с барабана при опускании груза
Приведенный момент инерции при подъеме и опускании груза
Расчетный тормозной момент
МТ = кТ . Мст.Т (1.87)
где кТ – коэффициент запаса торможения для режима кТ =15 [1 с. 84].
Мст.Т – статический момент на валу двигателя при торможении
Выбираем двух колодочный тормоз типа ТКТ-200 с наибольшим тормозным моментом МТ = 160 Н. м.
Момент инерции движения масс механизма приведенный к валу тормоза при торможении
Время торможения при подъеме груза
Выбираем диаметр шкива D =200 мм [1 с. 85]
Сила трения между колодкой и шкивом
Сила натяжения колодки на шкив
где f – коэффициент трения f = 033 [1 с. 86 таблица 19]
Радиальный зазор между шкивом и колодкой принимаем max = 13 мм
Работа расторможения при отходе колодок
где = 09 095 – КПД рычажной системы
Выбираем по[1 с. 524 приложения LIII] электродвигатель типа МО – 300Б с рабочим моментом электромагнита МЭ =1000 кгс. см
Работа растормаживания А = 9600 Н. мм; плечо штока
Максимальное перемещение штока hш = 44 мм.
Момент отвеса якоря Мя = 9200 Н. м; угол поворота α = 55
Усилие приложенное к штоку при растормаживании
Передаточное число рычажной системы
После конструктивной проработки принимаем длину меньшего плеча
l1 = 200 мм. Длина большого плеча l2 =l1. UT = 200. 1 =200 мм конструктивно принимаем l2 =300 мм.
Максимально возможный отход колодки
где UТФ – фактическое передаточное число
Высота колодки тормоза
НК = (05 08)D = (05 08).200=100 160 мм
Принимаем НК = 160 мм что соответствует углу обхвата шкива =8336’
Ширина колодки при условии что ее давление на шкив равномерно распределено по поверхности
Принимаем ВК = 100 мм.
Между двигателем и редуктором устанавливается зубчатая муфта с тормозным шкивом DТ =200 мм [1 с. 513 приложение XLVII] имеющая следующую характеристику: наибольший передаваемый крутящий момент 70 кгс. м; момент инерции JМ = 000763 кгс м.с2.
Крутящий момент передаваемый муфтой в период пуска двигателя при опускании номинального груза
где J'Р.М – суммарный момент ротора электродвигателя и полумуфты
J'P.М =Jр +JПМ = 00229+00121=0035 кг. М2 (1.99)
Крутящийся момент при подъеме номинального груза
Максимальный крутящий момент при двигателя
МП.П = МП max – МП1 = 32-7846=2415 кгс. м (1.101)
Крутящий момент от сил инерции передаваемых муфтой
где JМ – момент инерции машины;
JМ = J ПР – J'РМ = 0132 -0035=0097 кгс м с. 2 (1.103)
Крутящий момент передаваемый муфтой в период пуска
Мmas = MП1 + Ми = 7846 + 1774 =2558 Н. м
Определяем расчетный крутящий момент для муфты
Мрасч = к1 . Мmax (1.104)
где к1 – коэффициент учитывающий степень ответственности муфты к1 =13
[1 с. 525 приложение IV]
Мрасч = 13. 2558 = 3325 кгс. м
Между барабаном и редуктором устанавливается зубчатая муфта.
Крутящий момент передаваемый муфтой
где =098 – КПД барабана
Расчетный момент для выбора муфты
Мрасч =3565. 155.12 =66309 Н. м
По таблице [1 с. 525 приложение V] выбираем стандартную зубчатую муфту (ГОСТ 5006-55) №5 с модулем m = 3; число зубьев kz = 56; ширина зуба
b = 25 мм; толщина зуба S1 = 435 мм наибольшим моментом передаваемым муфтой 800 кгс. м
Расчет механизма передвижения
1 Выбор кинематической схемы
Механизм передвижения тележки предполагается выполнить по кинематическойсхеме показанной на рис. Для передачи крутящего момента от двигателя к приводным колёсам использован вертикальный редуктор типа ВКН. Вал двигателя соединён с быстроходным валом редуктора втулочно-пальцевой муфтой на одной половине которой установлен колодочный тормоз с электрогидротолкателем.
Рис.8. Кинематическая схема передвижения тележки
2 Расчёт сопротивления передвижению тележки.
Сопротивление передвижению тележки с номинальным грузом при установившемся режиме работы определяем по формуле:
где Q =4000 кгс – номинальный вес поднимаемого груза;
Gт – собственный вес крановой тележки;
Dк – диаметр ходового колеса тележки. Предварительно выбираем диаметр колеса пользуясь рекомендациями [1 стр.106 табл. 25]:
Принимаем двухребордные колёса с цилиндрическим профилем обода по [1 стр.526-528 прил. LIX LVI ] (ГОСТ 3569 – 74):
В = 50 мм – ширина рабочей дорожки;
d = (025 030)Dк – диаметр цапфы:
d = (025 030)200 = 50 60 мм
Принимаем d = 60 мм;
f = 0015 – коэффициент трения в подшипниках колёс; подшипники выбираем сферические двухрядные [1 стр.106 табл. 26];
m = 003 мм – коэффициент трения качения колеса по плоскому рельсу [1 стр.106 табл. 27 ]. Колёса изготовлены из стали 65Г (ГОСТ 1050 – 74) твердость поверхности катания НВ 320 350;
kp = 25 – коэффициент учитывающий сопротивление от трения реборд колёс о рельсы и от трения токосъёмников о троллеи [1 стр.106 табл. 28 ];
Wук – сопротивление передвижению от уклона пути
a - расчётный уклон подкранового пути:
a = 0001 – для путей укладываемых на металлических балках с железобетонным фундаментом;
Wв – сопротивление передвижению от действия ветровой нагрузки. При расчёте мостовых кранов работающих в закрытых помещениях принимаем Wв = 0.
3 Расчёт мощности двигателя и выбор редуктора.
Для предварительного выбора двигателя определяем сопротивление передвижению загруженной тележки в пусковой период:
Где а – среднее ускорение тележки при пуске [1 стр.108 табл. 29 ]:
Мощность предварительно выбираемого двигателя:
где - средняя кратность пускового момента для асинхронных двигателей с фазовым ротором:
Расчётная мощность двигателя механизма передвижения и поворота определённая с учётом инерционных нагрузок должна удовлетворять условию:
Предварительно по каталогу принимаю электродвигатель с фазовым ротором типа МТF 011-6
Определяем средний пусковой момент двигателя для разгона незагруженной тележки:
Чтобы получить численное значение Мп.ср следует предварительно выбрать не только двигатель но и редуктор механизма передвижения тележки затем производим расчет привода и окончательно выбираем двигатель.
Определяем частоту вращения колеса:
Расчетное передаточное число редуктора:
По каталогу [1 стр.531 прил. LXII ] принимаем редуктор типа ВКН-280-16-2 (с передаточным числом uр = 16 схемой сборки №2)
Фактическая частота вращения колеса:
Фактическая скорость передвижения тележки с номинальным грузом:
Минимальное время пуска двигателя незагруженной тележки:
где ап.mах – максимально допустимое ускорение незагруженной тележки.
где - сцепной вес тележки.
ксц- коэффициент запаса сцепления; принимаем ксц равным 12.
j - коэффициент сцепления ведущего колеса с рельсом; для кранов работающих в закрытых помещениях j = 02;
Значение коэффициента кр принято равным 1 что идет в запас при расчете аТ
Статический момент сопротивления передвижению незагруженной тележки приведённый к валу двигателя;
Момент инерции подвижных масс тележки приведенный к валу двигателя;
где Jр.м – момент инерции ротора двигателя и муфт в том числе с тормозным шкивом;
Масса тележки с крюковой подвеской
Средний пусковой момент определяем по формуле(10.7):
Для привода механизма передвижения тележки окончательно принимаем электродвигатель MTF 012-6:
Средний пусковой момент двигателя
Фактическое время пуска двигателя нагруженной тележки:
Фактический коэффициент запаса сцепления приводных колёс с рельсами:
Фактическое ускорение при разгоне незагруженной тележки:
Время пуска и ускорение тележки при различных поднимаемых грузах с вожу в таблицу.
4. Проверка двигателя на нагрев по эквивалентной нагрузке.
Мощность необходимая для перемещения тележки с номинальным грузом
Среднее время пуска привода тележки при перемещении грузов Q; 05Q; Q; 075Q и незагруженной
Среднее время рабочей операции передвижения тележки
где Lр – средний рабочий путь тележки [1 стр.83 табл. 17 ] Lр = 6 м
Отношение среднего времени пуска к среднему времени рабочей операции
По графику [1 стр.112 рис. 45(кривая Б) ] находим значение коэффициент
Рэ = g ×Рн.г=1.1·067=073 кВт
Эквивалентная мощность двигателя
Nэ15 = К× Nэ = = 073 кВт
где К – коэффициент принимаемый в зависимости от режима работы который выбираем по [1 стр.113 табл. 30 ].
Ранее выбранный двигатель удовлетворяет условию нагрева.
5. Расчёт тормозного момента и выбор тормоза.
При торможении тележки без груза допустимое максимальное ускорение при котором обеспечивается запас сцепления колёс с рельсами 12 определяем по формуле:
Время торможения тележки без груза исходя из максимально допустимого ускорения
Допускаемая величина тормозного пути [1 стр.113 табл. 31 ]
Минимально допустимое время торможения
Время торможения тележки в общем виде находим по формуле
где Мт – тормозной момент который находим по формуле
где Мст.т – статический момент сопротивления передвижению тележки при торможении приведённый к валу двигателя
Принимаем колодочный тормоз с гидротолкателем типа ТТ – 200 с наибольшим тормозным моментом 200 Н×м диаметром тормозного шкива 200 мм шириной колодки 95 мм; тип гидротолкателя ТЭГ – 25 с тяговым усилием 250 Н. Тормоз отрегулируем на необходимый тормозной момент
Результаты расчёта механизма передвижения тележки заносим в табл2.
Незагруженная тележка
Сопротивление передвижению тележки
Статический момент сопротивления при передвижении тележки
6. Расчёт ходовых колёс
Нагрузка на одно ведущее колесо при условии их одинакового нагружения
где Qсц = 2000 кгс – сила давления на ведущие колёса от поднимаемого груза.
Расчётная нагрузка на колесо
где g = 08 – коэффициент учитывающий переменность нагрузки находим по [1стр.116 табл. 33 ];
k1= 12 – коэффициент учитывающий режим работы механизма;
Значения местных напряжений смятия при линейном контакте:
где b – рабочая ширина рельса; для принятого квадратного рельса 50х50
b = В - 2r1=50-2·25=45 мм
r1 – радиус закругления ребра рельса
Rk=125 мм – радиус колеса.
Выбираем колёса крановые (ГОСТ 3569 – 74) по [1 стр.526 прил. LVI ] изготовленные из стали 65Г с твёрдостью поверхности катания НВ 320 350 [s]см = 850 МПа
Епр = 21×105 МПа – приведенный модуль упругости для стального колеса и стального рельса.
Величина местных напряжений смятия при точечном контакте (в случае применения рельса со скруглённой головкой)
где Rmах – наибольший из двух радиусов R1 и Rк контактирующих поверхностей
R1 – радиус закругления головки рельса
m – коэффициент зависящий от отношения наименьшего радиуса к наибольшему из двух радиусов соприкасающихся поверхностей принимается по [1 стр.117 табл. 35 ]
Полученные результаты удовлетворяют заданным условиям.
Титульный лист.doc
Восточноукраинский национальный университет
по дисциплине «Подъемно-транспортные механизмы и машины»
тема: Расчет мостового крана
Содержание.doc
1 Выбор полиспаста каната диаметра барабана и блока 6 .
2 Выбор и проверочный расчет крюковой подвески 8
4 Упорный подшипник 10
5 Траверса крюка 10
6 Выбор подшипников блоков 12 112
7 Расчет узла барабана 14 ..
8 Расчет крепления каната к барабану 15
9 Расчет оси барабана 17
10 Выбор подшипников оси барабана 19
11 Расчет мощности электродвигателя и выбор редуктора 19
12 Расчет тормоза 24
13 Выбор муфты 26 ..
Расчет механизма передвижения 28 ..
1 Выбор кинематической схемы 28
2 Расчет сопротивления передвижению тележки 28
3 Расчет мощности двигателя и выбор редуктора 29
4 Проверка двигателя на нагрев по эквивалентной нагрузке 33
5 Расчет тормозного момента и выбор тормоза 33 ..
6 Расчет ходовых колёс 35 ..
Список использованной 37
Литература.doc
Иванченко Ф.К. и др. Расчеты грузоподъемных и транспортирующих машин. - Киев издательское объединение «Вища школа» Головное издательство 1978.- 576 с.
Марон А.С. Кузьмин В.Ю. Справочник по расчетам подъемно-транспортных механизмов. – М.: Машиностроение 1981г.
Введение.doc
Мостовой кран состоит из: грузоподъёмной тележки включающей в себя механизм подъёма и грузозахватное устройство и из моста представляющего собой две сплошные (или решетчатые) формы присоединённые к концевым балкам в которые вмонтированы приводные и не приводные колёса. Механизм передвижения моста имеет привод от одного или двух двигателей.
Курсовой проект выполняется по следующим исходным данным:
- грузоподъемность Q = 6.3 тс;
- длина пролета L = 20 м;
- наибольшая высота подъема Н = 20 м;
- скорость подъема груза V = 0165 мс;
- режим работы - средний
По исходным данным необходимо провести расчет механизма подъёма а именно подобрать канат диаметр барабана и блока крюковую подвеску выполнить выбор и расчет электродвигателя и редуктора расчет муфты и тормоза а также провести расчет механизма передвижения по аналогичной схеме.