Расчет и проектирование захватно-срезающего устройства валочно-трелевочной машины ЛП-58-01


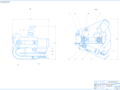
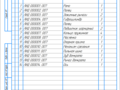
- Добавлен: 24.01.2023
- Размер: 2 MB
- Закачек: 0
Подписаться на ежедневные обновления каталога:
Описание
Расчет и проектирование захватно-срезающего устройства валочно-трелевочной машины ЛП-58-01
Состав проекта
![]() |
![]() |
![]() ![]() ![]() ![]() |
![]() ![]() ![]() ![]() |
![]() ![]() ![]() |
Дополнительная информация
Контент чертежей
ЗСУ.cdw

Спецификация.spw

РГР.doc
ФГБОУ ВПО “Сибирский государственный
технологический университет”
Лесосибирский филиал
Расчетно-графическая работа по дисциплине
“Агрегатное оборудование”
Расчет и проектирование захватно-срезающего
устройства валочно-трелевочной машины ЛП-58-01
(ЛИД 000000.007 РГР)
Задание на расчетно-графическую работу ..
Конструкционные особенности захватно-срезающих устройств валочно-трелевочных машин ..
1 Назначение и составные части захватно-срезающих устройств .
2 Конструктивные особенности захватно-срезающего устройства валочно-трелевочной машины ЛП-58-01
Проектирование и расчет захватно-срезающих устройств
1 Проектирование и расчет захватных устройств ..
1.1 Разработка компоновочно-кинематической схемы захватного устройства.
1.2 Обоснование расчетного случая нагружения захватного устройства валочно-трелевочной машины .
1.3 Определение сил действующих на захватный рычаг и расчет гидроцилиндра привода рычага .
1.4 Расчет нагрузок в опасном сечении рычага
1.5 Определение геометрических характеристик сечения рычага.
1.6 Расчет захватного рычага на прочность. ..
1.7 Расчет проушины рычага ..
1.8 Расчет опорной призмы .
1.9 Расчет шарнирных соединений ..
1.10 Проектирование рамы захватно-срезающего устройства .
2 Проектирование и расчет срезающих устройств
2.1 Определение основных параметров цепного срезающего устройства.
2.2 Компоновка срезающего аппарата на корпусе захватно-срезающего устройства . .
2.3 Определение потребной мощности гидродвигателя привода пильной цепи .
2.4 Проверка пильной цепи на прочность
2.5 Расчет гидропривода механизма надвигания пилы
3 Оценка возможности создания валочного момента натягом манипулятора ..
Библиографический список .
Задание на расчетно-графическую работу
Рассчитать и спроектировать захватно-срезающее устройство валочно-трелевочной машины ЛП-58-01 по заданным параметрам (табл. 1). Другие параметры принимаются или берутся из справочной литературы. Вычертить на листе формата А1 в масштабе проекции захватно-срезающего устройства.
Таблица 1 – Исходные данные
Марка валочно-трелевочной машины
Скорость поворота манипулятора
Порода срезаемого дерева
Диаметр срезаемого дерева в области пропила
Максимальный вылет манипулятора
Современный этап развития механизации лесозаготовок связан с применением различных рабочих органов устанавливаемых на манипуляторах. Наиболее сложными рабочими органами являются харвестерные головки объединяющие в своей конструкции захватные срезающие сучкорезно-протаскивающие механизмы и сложные гидравлические и электрические устройства.
Наряду с харвестерными головками для валки деревьев широкое применение нашли традиционные захватно-срезающие устройства (ЗСУ). Они позволяют захватывать срезать валить дерево на землю или снимать его с пня в вертикальном положении с последующим пакетированием. ЗСУ включают в себя ряд тех же устройств что и харвестерные головки. Однако их проектирование и расчет имеют специфические особенности. Основными элементами рабочих органов этого типа являются захватные рычаги приводные гидроцилиндры режущие механизмы и валочные устройства.
Знание конструктивных особенностей современных рабочих органов лесных машин и методик их расчета и проектирования являются одними из важнейших требований предъявляемых к современному инженеру лесного комплекса.
Конструкционные особенности захватно-срезающих устройств валочно-трелевочных машин
1 Назначение и составные части захватно-срезающих устройств
ЗСУ валочно-трелевочной машины (ВТМ) представляет собой сложный рабочий орган состоящий из захватного устройства (ЗУ) срезающего устройства (СУ) и устройства создающего валочный момент – валочного устройства (ВУ).
Конструкция ЗСУ позволяет при наведении его с помощью манипулятора ВТМ на дерево выполнить захват срезание валку дерева с последующим его удержанием при пакетировании в кониковое зажимное устройство.
Рассмотрим основные составные части ЗСУ.
Захватное устройство. ЗУ служит для захвата и удержания дерева при его срезании валке и пакетировании. Оно состоит из следующих основных конструктивных элементов: корпус захватный рычаг гидроцилиндр привода рычага шарниры. Основным требованием к работе ЗУ является отсутствие проскальзывания дерева относительно корпуса и захватных рычагов.
Для ЗСУ ВТМ выполняющих валку дерева на землю характерно расположение захватных рычагов в одной плоскости с корпусом выше или ниже плоскости срезания. Если технологией работы предусмотрено удержание дерева при переносе его в положении близком к вертикальному то захватные рычаги располагают на двух параллельных уровнях выше плоскости реза. Для этой же цели возможно применение более широкого ложа на корпусе при одном подвижном захватном рычаге.
Срезающее устройство. СУ предназначено для отделения ствола от корневой системы. В качестве СУ могут применяться цепные и дисковые пилы цилиндрические и дисковые фрезы ленточные пилы ножевые срезающие устройства.
Цепные пилы являются наиболее распространенными срезающими устройствами в современных ЗСУ. Они могут иметь консольную пильную шину плоскую треугольную или шину более сложной конструкции (например см. патент Швеции № 359016). Некоторые конструкции СУ имеют два пильных аппарата (а. с. № 353371). Известны комбинированные СУ имеющие пильный и ножевой срезающие органы (а. с. № 496993). Привод пильных цепей как правило гидравлический – от аксиально-поршневого или шестеренного гидромоторов. Надвигание режущего органа может быть прямолинейным криволинейным круговым и осуществляться с помощью гидропривода.
Валочное устройство. Валочное устройство (ВУ) предназначено для создания валочного момента с целью повала дерева на землю и для обеспечения беззажимного срезания дерева при использовании в качестве срезающего механизма цепных ленточных дисковых пил и фрез.
2 Конструктивные особенности захватно-срезающего устройства валочно-трелевочной машины ЛП-58-01
Устройство захватно-срезающее предназначено для зажима срезания направленного повала и укладки срезанных деревьев в коник или на землю.
Все сборочные единицы устройства смонтированы в общей раме 1 (рис. 1.1) сварной конструкции из низколегированной стали. Передняя часть рамы выполнена вогнутой по радиусу максимального дерева. В проушинах рамы при помощи пальцев 2 установлены рычаги зажимные 3 которые приводятся в действие гидроцилиндрами 4.
-рама; 2- пальцы; 3- зажимные рычаги; 4- гидроцилиндр; 5 - палец;
- подшипник шарнирный; 7 - кольцо пружинное; 8 - масленка
Рисунок 1.1 - Устройство захватно-срезающее
Гидроцилиндры размещены внутри рамы и соединены с ней пальцами 5. Соосно с одним из этих пальцев в нижней части рамы при помощи болтов 1 (рисунок 1.2) установлен механизм срезания 2. В верхней части рамы над этим же пальцем установлен аксиально-поршневой гидромотор 3 привода цепи механизма срезания. Вращение от гидромотора к цепи передается при помощи шлицевого валика 4 проходящего через центральное отверстие в пальце. В средней части рамы в отверстиях верхнего и нижнего листов при помощи пальца 5 установлен гидроцилиндр 6. Шток гидроцилиндра заканчивается вилкой 7 внутри которой находится ролик 8. Осью 9 вилка и ролик соединены водилом 10. Водило вращаясь на оси 11 описывает траекторию по радиусу и выдвижение штока гидроцилиндра 6 (при подаче жидкости в поршневую полость) приводит ролик в соприкосновение с
В результате взаимодействия кулачка с роликом 8 происходит поворот ЗСУ в вертикальной плоскости и установка его в горизонтальное положение. При подаче жидкости в штоковую полость гидроцилиндра 6 шток его втягивается ролик отходит от кулачка обеспечивая свободный поворот ЗСУ вместе со срезанным деревом относительно оси соединяющей ЗСУ с подвеской.
– болт; 2 –механизм срезания; 3 – гидромотор; 4 – шлицевой валик;
– палец; 6 – гидроцилиндр; 7 – вилка; 8 – ролик; 9 – ось; 10 – водило;
– ось водило; 12 – ограждение; 13 – стойка; 14 – упор; 15 – пробка заливная
Рисунок 1.2 – Поворотное устройство ЗСУ
Для предохранения от поломок пильной шины при подводе ЗСУ к дереву в нижней части рамы установлено ограждение 12.
К верхнему листу рамы приварена стойка 13 имеющая упор 14 который служит для передачи усилия нВ дерево при его повале. Для компенсации отклонения от соосности все проушины гидроцилиндров и серьги штоков имеют шарнирные подшипники 6 (рис. 1.1) типа ШС которые закреплены от осевого перемещения с помощью пружинных колец 7. Подвод консистентной смазки производится от масленок 8 через сверления в пальцах к внутренним кольцам подшипников.
Проектирование и расчет захватно-срезающих устройств
1 Проектирование и расчет захватных устройств
1.1 Разработка компоновочно-кинематической схемы захватного устройства
Компоновочно-кинематическая схема (ККС) ЗУ разрабатывается в масштабе (ГОСТ 2.302-68) на миллиметровой бумаге. Разработка ККС является важным этапом проектирования ЗУ. На основе ККС разрабатываются чертежи устройства из схемы определяются многие данные необходимые для расчетов (плечи сил ходы штоков гидроцилиндров и другие).
Основой для разработки схемы являются значения максимального и минимального диаметров отработанных деревьев на уровне срезания. Высота оставляемого пня не должна превышать 13 диаметра расчетного дерева на высоте груди.
Если в задании на проектирование приведены значения диаметров расчетных деревьев на высоте груди то величины диаметров этих деревьев в плоскости срезания можно определить умножением диаметра дерева на уровне груди на поправочный коэффициент формы ствола (см. приложение).
Разработка схемы начинается с вычерчивания на бумаге в принятом масштабе двух окружностей соответствующих максимальному и минимальному диаметрам срезаемых деревьев.
Рисунок 2.1 - Компоновочно-кинематическая схема ЗУ
Около максимального диаметра обрабатываемого дерева в соответствии с принятой конструктивной схемой ЗСУ в тонких линиях вычерчивается корпус. Зев или ложе корпуса должен быть сконструирован таким образом чтобы при обжатии дерева любого диаметра захватным рычагом (рычагами) оно не имело возможности выскальзывания из зева в поперечной плоскости ЗУ. В основании зева для обеспечения надежного контакта дерева с корпусом обычно приваривается зубчатая гребенка (см. например конструкцию ЗСУ ЛП-17). Глубина зева корпуса для однорычажной схемы рекомендуется равной половине диаметра самого большого из обрабатываемых деревьев а для двухрычажной схемы – 13.
Далее в соответствии с конструктивной схемой (однорычажная или двухрычажная) производится компоновка захватных рычагов на корпусе. Одновременно прорабатывается конструкция рычага. Рычаги могут быть прямыми или изогнутыми в плане.
В двухрычажных схемах при расположении рычагов в одной плоскости они могут заходить один на другой за счет скошенности сечения (на виде сбоку) или входить один в прорезь другого. Поперечное сечение рычага может быть коробчатым тавровым или г-образным (например конструкции рычагов навесных харвестеров). Рычаг должен обладать достаточной жесткостью. Если рычаг выполняется изогнутым в плане то при разработке его конструкции рекомендуется обеспечить выполнение условия при котором прочностной расчет рычага можно проводить как расчет прямого бруса. Это условие имеет вид: hr ≤ 15 где h– максимальная ширина сечения рычага в плане r – радиус кривизны рычага по центрам тяжести сечений. Для выбора точки крепления захватных рычагов на корпусе ЗУ (шарнир «рычаг-корпус») необходимо выполнить по схеме следующие построения. На диаметре большого дерева построить точку 1 – точку контакта рычага со стволом. Положение этой точки характеризуется углом захвата ствола (рис. 2.1). Величина угла определяется из условия невыпадения дерева из ЗУ при падении давления в гидромагистрали. При величине коэффициента трения рычага о ствол равной 057 063 минимальное значение этого угла для однорычажных схем равно 50 60° а для двухрычажных– 20 30°.
На диаметре соответствующем наименьшему из обрабатываемых деревьев строится точка 1'. На положение этой точки влияет принятая конструкция рычага. Если захватные рычаги движутся в одной плоскости и не имеют скосов по длине рычага то они при обхвате наименьшего диаметра не должны пересекаться. В этом случае точку 1' следует поставить отстоящей от оси ЕЕ' (рис. 2.1) в сторону рычага по окружности на угол 3 5°. Габариты ЗУ при этом возрастают.
Если рычаги выполнены таким образом что они имеют скосы по длине позволяющие им заходить друг на друга внахлест или вырезы то точка 1' может размещаться по окружности на угол 10 30° в противоположную сторону. Такая схема ЗУ имеет большее распространение. На рис. 2.1 точка 1' занимает некоторое среднее положение на пересечении оси ЕЕ' с линией окружности. В таком случае скосы достаточно выполнить только на концах рычагов. На правой части рис. 24 показано построение ККС для ЗУ с изогнутым рычагом работающим на обжатие дерева поршневой полостью гидроцилиндра. Работа поршневой полостью позволяет при одном и том же диаметре гидроцилиндра и давлении в гидросистеме развивать большее усилие. Габариты ЗУ в этом случае увеличиваются. Снижается и быстродействие. При соединении рычага с корпусом по наружному шарниру (точка О') а гидроцилиндра с рычагом по внутреннему (точка О) гидроцилиндр на обжатие дерева рычагом будет работать штоковой полостью. По последней схеме работает например ЗСУ машины ЛП-17. На левой части рисунка показана схема с прямым рычагом с приводным гидроцилиндром работающим на обжатие дерева штоковой полостью. По такой схеме работает шведское ЗСУ ОСА 640. Данная схема также может быть изменена на работу поршневой полостью. При разработке ККС ЗУ в каждом конкретном случае должен проводиться анализ возможных вариантов схем с оценкой по следующим критериям: развитие максимального усилия минимальные габаритные размеры ЗУ защищенность агрегатов гидросистемы от возможных повреждений (в том числе и гидроцилиндров) быстродействие. После построения на схеме точек 1 и 1' определяется место сочленения рычага с корпусом ЗУ. Линия на которой располагается шарнир «рычаг-корпус» строится следующим образом. Сначала соединяются прямой точки 1 и 1' а затем из центра отрезка 1 – 1' восстанавливается перпендикуляр который и является геометрическим местом точек возможного размещения данного шарнира (линия А – А').
После этого из картона или плотной бумаги в принятом на ККС масштабе вырезается профиль спроектированного рычага в плане и производится компоновка полученного трафарета таким образом чтобы он располагаясь как можно компактнее около диаметра наибольшего дерева обеспечивал при повороте с фиксацией его в точке шарнира О (расположенном на линии А – А') захват ствола минимального диаметра с контактом рычага со стволом в точке 1'.Если компоновка рычага устраивает проектировщика то на рычаге выбирается точка О' соответствующая месту соединения рычага с приводным гидроцилиндром (шарнир «рычаг-гидроцилиндр»). После этого на схеме вычерчивается желаемое положение приводного гидроцилиндра (линия О'С). Проектировщику необходимо стремиться более рационально и сжато использовать компоновочное пространство размещая все элементы ЗУ по возможности ближе к максимальному диаметру ствола. При этом следует учитывать потребность размещения между верхним и нижним листами корпуса в пространстве примыкающем к оси ЕЕ' других элементов конструкции ЗСУ например ВУ или вспомогательных агрегатов гидросистемы. Линия О'С строится таким образом чтобы при любом положении рычага она не пересекалась с шарниром О. После того как определено положение шарнира О «рычаг-корпус» и определена линия действия усилия гидроцилиндра О'С производится проверка работоспособности ЗУ путем поворота трафарета рычага от положения обжатия дерева минимальных размеров до полного раскрытия. Полное раскрытие рычага должно обеспечивать беспрепятственное наведение ЗУ на дерево максимальных размеров. В крайних положениях трафарет рычага обводится пунктирной линией. На этих двух положениях наносится также точка О' соответствующая положению шарнира «гидроцилиндр-рычаг». Расстояние между крайними положениями этой точки служит основой для определения потребного хода штока гидроцилиндра. Постановка задачи оптимальной компоновки захватных рычагов с корпусом формализация целевой функции и ограничений рабочий алгоритм поиска оптимальной компоновки ЗУ изложены в учебном пособии.
1.2 Обоснование расчетного случая нагружения захватного устройства валочно-трелевочной машины
Рабочий цикл ВТМ состоит из следующих элементов с процентной раскладкой по времени всего цикла:
– открытие зажимных рычагов (коника);
– поворот манипулятора в горизонтальной плоскости;
– подвод ЗСУ к дереву;
– наводка ЗСУ на дерево;
– зажим и проверка зажима дерева натягом манипулятора;
– сокращение вылета манипулятора с подтаскиванием дерева;
– поворот манипулятора с деревом в горизонтальной плоскости;
– укладка дерева в коник;
– закрытие зажимных рычагов коника из расчета на одно дерево;
– переезд машины на следующую позицию из расчета на одно дерево.
На протяжении всего времени взаимодействия ЗСУ с деревом
(5-10-й элементы технологического цикла) ЗУ должно обеспечивать надежный зажим дерева исключающий проскальзывание ствола относительно захватных рычагов и корпуса. Отсутствие проскальзывания обеспечивается необходимым усилием обжатия ствола рычагами создающими силу трения элементов ЗУ о дерево. Эта суммарная сила трения должна превышать внешние усилия способные вызвать перемещение дерева относительно захватных рычагов. Опасными с точки зрения проскальзывания дерева относительно элементов ЗУ являются 7-й 8-й и 9-й режимы работы. Надежность работы ЗУ на 7-м режиме обеспечивается предварительной проверкой качества зажима на режиме 5.Однако при работе ЗСУ типа ЛП-53 производящих захват дерева ниже плоскости реза и сталкивание ствола необходимо учитывать режим валки. Таким образом при расчете ЗУ ВТМ необходимо рассмотреть следующие три случая: валка дерева подъем дерева на комель с земли подтаскивание дерева за комель. Если ЗСУ по технологическим или лесохозяйственным требованиям должно обеспечивать перенос дерева в вертикальном положении (ЗСУ ВП-80) то в обоснование расчетного случая нагружения должны быть включены два режима: отрыв дерева от пня и поворот манипулятора с деревом в горизонтальной плоскости. Для всех отмеченных режимов (в соответствии с технологией работы ЗСУ) определяется потребное усилие прижима захватного рычага к дереву исключающее проскальзывание ствола. Режим с максимальным значением этого усилия принимается за основной расчетный случай нагружения ЗУ. Определим величину потребного усилия прижима рычага ЗУ к дереву для описанных выше режимов принимая что контакт элементов ЗУ с деревом осуществляется в трех точках (рис. 2.2).
Рисунок 2.2 - Расчетная схема взаимодействия ЗУ с деревом
Валка дерева. При повале дерева необходимо создать валочный момент относительно перемычки недопила превышающий момент сопротивления валке. Величина перемычки недопила равна 01 диаметра дерева. На величину момента сопротивления валке оказывают влияние вес дерева его размеры отклонение оси дерева от вертикали сопротивление недопиленной части ствола ветровая нагрузка. С достаточной для практики точностью момент сопротивления валке можно найти по следующему выражению (рис. 2.3):
Рисунок 2.3 - Схема сил препятствующих валке дерева
где Mв – момент сопротивления валке Н·м;
M – масса расчетного дерева М = kV = 10227 = 2754 т =2754 кг
(где V = 27 м3 – объем дерева; k – коэффициент отношения массы дерева к его объему);
g – ускорение свободного падения 981 мс2;
D – диаметр расчетного дерева на высоте груди D = D012 = 06512 = = 054 м (где D0 = 065 м – комлевой диаметр дерева);
hт – расстояние от плоскости реза до центра массы дерева hT = kH = = 03727 = 10 м (где k = 037 – коэффициент зависящий от породы дерева; H = 27 м – высота дерева);
φ – угол обратного к направлению валки наклона ствола при расчете принимается 5°;
Cz – коэффициент полной аэродинамической силы или коэффициент силы лобового сопротивления (по величине и физическому смыслу не совпадает скоэффициентом аэродинамического момента полученным В. В. Редькиным). Величина коэффициента аэродинамической силы в данном выражении определяется по эмпирической формуле:
Сх = А0 + А1 + А22 = 0944 + 0597·10-1·9 + 0134·10-2·92 = 159
где A0 A1 A2 – коэффициенты значения которых равны:
Сосна 0944 0597·10-1 0134·10-2
ρ – плотность воздуха (при t= 0°С и давлении 1013 нПа) кгм3. В расчетах ρ = 129 кгм3;
– средняя скорость ветра = 9 мс;
Sкр – мидель (площадь) кроны Sкр = 1·2·Нкр·Dкр = 067·04·54·351 = = 51 м2 (где 1 = 067 и 2 = 04 – коэффициенты формы и густоты заполнения кроны; Нкр = 02·Н = 02·27 = 54 м и Dкр = 013·Н = 013·27 = = 351 м – высота и ширина кроны);
hg = 08·Н = 08·27 = 216 м – расстояние от плоскости реза до центра приложения аэродинамических сил м.
Мидель кроны и высотная координата ветра определяются по данным справочных материалов приведенных в приложении в зависимости от высоты расчетного дерева.
Формула момента сопротивления валки учитывает влияние отрицательного уклона дерева и ветровую нагрузку на него противодействующие валке. Влияние сопротивления недопиленной части
ствола на момент валки здесь не учитывается. Для получения значения потребной силы трения рычага ЗУ о ствол в данном режиме исключающей проскальзывание рычага необходимо значение момента развиваемого ВУ относительно контактной точки 3 разделить на плечи сил трения возникающие в контактных точках 1 и 2 (рис. 2.2). Эти силы направлены вдоль ствола (перпендикулярно рисунку). Значение валочного момента ВУ относительно точки 3 приближенно можно оценить по следующему выражению:
Mв3 = k·Mв = 05·40 = 20 кН·м
где Mв – значение потребного валочного момента создаваемого валочным устройством относительно перемычки недопила Н·м;
k = 05 – коэффициент для пересчета величины валочного момента относительно перемычки недопила к величине момента относительно контактной точки 3 (он характеризует примерное соотношение плеч сил в схеме). Величина этого коэффициента зависит от конструктивной схемы применяемого валочного устройства. Если валочный момент создается натягом манипулятора то значение коэффициента можно принять равным 05 07. Для устройств создающих валочный момент за счет реакций пня k = 02 05. Чем ближе валочное устройство расположено к дереву тем коэффициент K меньше. Для двухрычажной схемы плечо силы трения относительно точки 3:
Величина момента валочного устройства принимается равной моменту сопротивления валке т. к. он определен для максимальных значений входящих в него параметров. Тогда потребная сила трения одного рычага двухрычажного ЗУ равна:
По значению силы трения определяется потребное усилие прижима захватного рычага к стволу:
N1 = F1 = 20406 = 34 кН·м
где – коэффициент трения рычага о кору дерева = 06.
Величина давления дерева на корпус ЗУ в точке 3 для двухрычажной схемы равна:
N3 = 2·N1·sin = 2·34·05 = 34 кН·м.
где N1 – сила прижима рычага к стволу (считаем что N1 = N2 в силу симметрии ЗУ).
Подъем дерева за комель. При подъеме дерева за комель оно стремится выскользнуть из ЗУ вниз (рис. 2.2). В этом режиме на дерево действуют сила тяжести и сила инерции стремящиеся разжать захватные рычаги. С другой стороны на дерево действуют сила нормального давления рычага и сила трения в поперечной плоскости. Эти силы препятствуют выпадению дерева из ЗУ вниз. Значение потребной силы прижима захватных рычагов к стволу в этом режиме определяется из уравнения всех сил действующих на дерево в плоскостях захвата. Граничным условием является равенство нулю силы нормального давления в контактной точке 3 (точка опоры ствола в зеве корпуса). В этом случае условие для определения минимального потребного усилия прижима для двухрычажной схемы имеет следующий вид:
где N1– потребное усилие прижима рычага к стволу Н;
M – масса расчетного дерева кг;
g – ускорение свободного падения g = 981 мс2;
n – доля силы веса дерева приходящаяся на захватное устройство принимается n = 06;
– коэффициент трения рычага о кору дерева = 06;
W – ускорение перемещения комлевой части дерева принимается W = 05·g = 05·981 = 49 мс2.
Подтаскивание дерева за комель. В этом режиме рассматривается подтаскивание максимального расчетного дерева на подъем 15 20° (рис. 2.4) с ускорением 05·g . При этом дерево стремится вырваться из захватного устройства чему способствуют сила трения кроны о землю сила инерции и продольная составляющая сила веса дерева. Дерево в ЗУ необходимо обжать рычагами так чтобы суммарная сила трения элементов ЗУ о ствол в продольном направлении превышала силы стремящиеся вырвать дерево.
Суммарная сила стремящаяся вырвать дерево из ЗУ действующая вдоль уклона равна (рис. 2.4)
Рисунок 2.4 - Схема сил действующих на дерево при подтаскивании
где M – масса дерева кг;
n – доля силы веса дерева приходящаяся на ЗУ;
W – ускорение подтаскивания мс2;
f – коэффициент сопротивления включению кроны f = 08;
α = 160 – угол наклона местности.
В плоскости захвата на дерево действует сила Mgn (рис. 2.5).
Рисунок 2.5 - Схема сил действующих на дерево со стороны ЗУ при подтаскивании
Из уравнений проекций веса указанных сил действующих на дерево имеем (силами трения в плоскости ЗУ пренебрегаем).
Для двухрычажного ЗУ:
N3 = 2·N1·sin - Mgn = 2·21800·05 - 2754·891·06 = 66 кН
За расчетный режим нагружения принимается тот из режимов в котором потребная сила давления рычагов на ствол максимальна. Если конструкцией ЗСУ предусматривается перенос деревьев в вертикальном положении то потребное усилие прижима рычагов к стволу следует проверить по условию отрыва дерева от пня вверх и по условию невыпадения дерева из ЗУ при его перекосе в вертикальном положении с поворотом манипулятора вокруг вертикальной оси. Обычно ВТМ осуществляет перенос в вертикальном или наклонном положении более мелких деревьев (до 24 см в диаметре на уровне груди) чем расчетное. Крупные деревья валятся по обычной схеме (машины ВП-80 ТБ-1В). В этом случае в проверочные расчеты следует проставлять параметры не самого крупного (расчетного) дерева а более мелкого обусловленного технологическими требованиями. ЗСУ переносящие деревья в вертикальном положении имеют обычно разнесенную компоновку рычагов (ТБ-1В) или один подвижный рычаг и высокое ложе корпуса (ВП-80). Количество расчетных контактных точек увеличивается. Потребное усилие прижима рычагов к стволу при отрыве дерева от пня приближенно оценивается по формуле:
где M – масса дерева принимаемая при данном расчете кг;
n = 6 – количество контактных точек трения.
Усилие прижима из условия переноса вертикального дерева поворотом манипулятора равно:
где D0 – диаметр дерева в месте срезания (для данного расчетного случая) м;
L – вылет манипулятора м;
– угловая скорость поворота манипулятора с-1;
hТ – высотные координаты центра масс дерева (для данного расчетного случая) м;
b = 015 м - расстояние между разнесенными по высоте рычагами (для ЗУ типа ТБ-1В ЛП-2 ЛП-19) или расстояние от нижней кромки ЗУ до подвижного рычага (для однорычажных ЗУ типа ВП-80).
1.3 Определение сил действующих на захватный рычаг и расчет гидроцилиндра привода рычага
После определения максимальной потребной силы нормального давления рычага на ствол необходимо оценить другие силы характеризующие нагруженность рычага при его взаимодействии с деревом. В плоскости перпендикулярной плоскости рычага в контактной точке 1 на него действует сила F равная
F = N = 06113 = 678 кН
где – коэффициент трения рычага о ствол дерева ( = 06).
В плоскости движения рычага он нагружен силой N действующей со стороны дерева в точке 1. Кроме этой силы в точке 1 возникает сила трения рычага о ствол действующая в плоскости движения рычага T . Величина этой силы составляет некоторую часть от силы нормального давления и определяется из условия что линия равнодействующей сил N и T проходит через точки 1 и 3.
Рисунок 2.6 - Система сил действующих на захватный рычаг
Проводя на компоновочной схеме прямую через точки 1 и 3 и измерив величину угла λ (рис. 2.6) получим:
T = Ntgλ = 116059 = 667 кН
Таким образом на рычаг в точке 1 действуют три взаимоперпендикулярные силы T F N. Потребное усилие прижима рычага к дереву создается гидроцилиндром. Усилие развиваемое гидроцилиндром также определяет напряженное состояние рычага. Для определения потребного усилия гидроцилиндра составим уравнение равновесия рычага относительно шарнира «рычаг-корпус» (точка О на рис. 2.6). Тогда для приведенной на рисунке схемы получим:
NhN - ThT - PгцhP =0
где hN = 047 м hT = 0205 м hP = 0115 м – плечи сил определяемые из компоновочной схемы. Отсюда потребное усилие гидроцилиндра равно:
По усилию PГЦ производится расчет диаметра гидро-цилиндра привода рычага.
При работе гидроцилиндра на зажим дерева поршневой полостью его диаметр равен:
где PГЦ – усилие гидроцилиндра Н;
P0 =28 – давление в гидроприводе МПа.
При работе гидроцилиндра штоковой полостью
где φ – коэффициент характеризующий отношение значений поршневой и штоковой полостей гидроцилиндра (по ГОСТ 6540-68). Для гидроцилиндров приведенных в приложении значение коэффициента φ равно 16. Потребный ход штока гидроцилиндра определяется из компоновочно-кинематической схемы. По величине диаметра и хода штока выбирается стан-дартный гидроцилиндр (с округлением в большую сторону). После этого определяется точное усилие развиваемое гидроцилиндром.
Для поршневой полости:
где d = 004 м – диаметр штока.
Затем корректируется значение сил нагружающих рычаг. Определение реакции в шарнире «О» («рычаг-корпус») проводится геометрически путем параллельного переноса сил N T PГЦ в центр шарнира «О» с изображением их на схеме в определенном масштабе сил и суммированием. Суммарная сила переводится через масштаб в реальную величину. Направление реакции Rш противоположно направлению полученной суммарной силы давления на шарнир.
При проектировании рычага было принято что высота его сечения в плоскости движения должна быть больше радиуса кривизны в 5 раз. В этом случае для расчета рычага на прочность можно применить классические методы курса сопротивления материалов для расчета прямого бруса. Сначала определяется положение опасного сечения. Опасное сечение проходит через точку А (рис. 2.7) – точку пересечения линии действия силы Rш с линией соединяющей центры тяжести сечений (для схемы работающей поршневой полостью) при присоединении гидроцилиндра к наружному шарниру рычага. Если гидроцилиндр соединен с внутренним шарниром рычага и работает на обжим ствола штоковой полостью то точка А – это точка пересечения линии действия усилия с линией центра масс сечений PГЦ. Рассматривая рычаг как балку определим нагрузки в сечении I-I:
– изгибающий момент в плоскости движения рычага
My = NlN - TlT = 113044 – 667013 = 4105 кНм.
– изгибающий момент в плоскости перпендикулярной плоскости движения рычага
My = Flp = 678045 = 3051 кНм.
где lN = 044 м lp = 045 м и lT = 013 м - плечи сил определяемые из компоновочной схемы.
Рисунок 2.7 - Определение нагрузок в сечении захватного рычага
Mкр= rF = 01678 = 0678 кНм.
где r = 01 м – расстояние от точки прижима рычага к стволу до касательной к окружности рычага проходящей через точку А.
– нормальная нагрузка
R = N sin + T cos = 11305 + 667085 = 1132 кН
где =300 - угол определяющийся из ККС.
– касательные нагрузки
1.5 Определение геометрических характеристик сечения рычага
Для определения напряжений в опасном сечении необходимо рассчитать его геометрические характеристики:
– момент инерции Iy относительно оси У;
– площадь сечения S;
– момент инерции при кручении Iкр;
– статический момент наружной стенки Sсту (для коробчатого сварного соединения) необходимый для расчета сварных швов относительно оси У.
Определение геометрических характеристик проводится по известным формулам курса «Сопротивление материалов». Так для коробчатого тонкостенного сечения показанного на рисунке 2.7 при выполнении условия H15 где – толщина стенки справедливы следующие формулы.
Момент инерции относительно оси Х:
Момент инерции относительно оси У:
S = 2(B+H) - 42 = 2001(009+016) - 40012 = 00046 м2
где B = 009 м Н = 016 м и = 001 м – размеры сечения рычага.
Момент инерции при кручении
где h = H2 = 016-2001 = 014 м; b = B2 = 009 - 2001 = 007 м.
Момент сопротивления при кручении в данном случае
Wкр = 2bh = 2001009016 = 000029 м3.
Статический момент наружной стенки относительно оси У
Sсту = (B - 2)(H2 – 2) = (009 - 2001)001(0162 – 0012) = = 0070010075 = 0000053 м3.
Геометрические характеристики других сложных сечений приведены в справочниках.
1.6 Расчет захватного рычага на прочность
Для рычага показанного на рисунке 2.7 максимальные нормальные растягивающие напряжения возникают в точке Е. Величина нормального напряжения в этой точке определяется по формуле:
Максимальное касательное напряжение обусловленное кручением для данного сечения (точки М и L) равно
В этих точках (L и М) возникают также касательные напряжения от нагрузок Qx и Qy определяемые по формуле Журавского:
где Q – поперечная сила;
Sст – статический момент отсеченной части;
I – момент инерции относительно соответствующей оси (при определении
l – ширина сечения в рассматриваемом слое.
Приблизительно эти напряжения можно принять равными:
Тогда суммарные касательные напряжения с учетом кручения и касательной силы в точках М и L равны:
Σм = кр + м = 234106 + 107103 = 35 МПа;
ΣL = кр + L = 234106 + 73106 = 964 МПа;
Обычно второе слагаемое этих формул мало и им можно пренебречь при расчете приведенных напряжений. В точках M M' L L' середин боковых стенок возникают нормальные напряжения
С точки зрения оценки нормальных напряжений наиболее опасными являются точки L и M' (рис. 2.7) где растягивающие напряжения суммируются. Оценим приведенные напряжения в точках L и M' по 4-й теории прочности:
Таким образом рассматриваемое коробчатое тонкостенное сечение проверяется на прочность в трех точках: А (по величине максимального нормального напряжения) L и M' (по величине приведенного нормального напряжения). Расчет сварного шва наружной стенки проводится по формуле:
где hш = 0005– катет сварного шва;
[ш] – допустимое напряжение на срез сварного шва.
Допустимое напряжение [ш] для шва в зависимости от типа электродов составляет обычно 06[] – допускаемого напряжения на растяжение материала рычага. [ш] = 06110 = 66 МПа.
1.7 Расчет проушины рычага
Если захватный рычаг имеет проушину для соединения его с приводным гидроцилиндром (например рычаг ОСА 640) то необходимо провести расчет проушины на прочность (рис. 2.8). В сечении II-II действует изгибающий момент
Миз = РГЦl = 3434005 = 172 кНм
где PГЦ – усилие развиваемое гидроцилиндром при обжатии расчетного дерева Н;
l = 005 м – высота проушины м.
Потребный момент сопротивления сечения
где [] – допускаемое напряжение на растяжение материала рычага.
По полученной величине момента сопротивления определяются момент инерции и размеры сечения (толщина листа стенок равна толщине листа стенок захватного рычага).
Рисунок 2.8 - Схема проушины рычага
Например для коробчатого сечения проушины (рис. 2.8):
Момент инерции этого сечения относительно оси У:
где B = 01 м Н = 018 м и = 002 м – размеры сечения проушины.
Принимая размер B равным высоте самого захватного рычага подбирается потребная ширина основания проушины H .
Сечение I-I (рис. 2.8) проверяется на срез:
где S – площадь сечения I-I без боковых шайб.
Допустимое напряжение на смятие [см] принимается равным 175 [] = 175110 = 1925 МПа.
1.8 Расчет опорной призмы
Если в конструкции ЗСУ предусмотрена опорная призма улучшающая условия работы валочного устройства (см. ЗСУ машин ЛП-17 ЛП-49) то производится ее расчет на прочность. Обычно опорная призма имеет корытное (рис. 2.9) тавровое или коробчатое сечение свариваемое из стальных листов. Сверху к вертикальным листам приварена стальная пластина имеющая зубчатую гребенку или заостренную кромку. При валке дерева эта пластина упирается в ствол воспринимая силу
R = Mвa = 40027 = 14815 кН
где Мв – валочный момент Н·м;
а = 027 – расстояние между верхним листом (ножом) призмы и захватными рычагами м.
Для принятой марки стали по известному допускаемому напряжению и силе R рассчитывается необходимый момент сопротивления:
где [] – допускаемое напряжение материала.
Рисунок 2.9 - Схема опорной призмы ЗСУ
По величине момента сопротивления определяются размеры сечения и толщина листов. Для данного сечения производится расчет сварных швов по формуле:
где ш – касательное напряжение в сварных швах;
Sст – статический момент наружной стенки относительно центральной оси У;
Iy – момент инерции сечения относительно оси У;
hш – катет сварного шва откуда
Сварные швы верхнего листа соединяющие его со стойками призмы рассчитываются на срез (рис. 2.9) по следующей формуле:
Отсюда можно определить потребный катет сварного шва:
1.9 Расчет шарнирных соединений
Основными шарнирными соединениями захватного устройства являются шарниры (рис. 2.10 а) «рычаг-корпус» 1 «рычаг-гидроцилиндр» 2 и «гидроцилиндр-корпус» 3.
Рисунок 2.10 - Схема к расчету шарнирных соединений
Шарнирные соединения «рычаг-гидроцилиндр» и «гидроцилиндр-корпус» имеют однотипную конструкцию. Принципиальная расчетная схема такого шарнира показана на рисунке 2.10 б. На палец шарнира действует нормальная к его оси сила PГЦ. Минимально допустимый диаметр пальца по условию изгиба определяется по формуле:
где [] = 480 МПа – допускаемое напряжение для материала пальца; l = 01 м b = 005 м а = 005 м – размеры соединения (рис. 2.10 б). Полученное значение диаметра пальца для данного сопряжения проверяется на срез по формуле:
где [] = 130 МПа – допускаемое напряжение на срез для пальца.
Реальный диаметр пальца в конструкции ЗУ принимается большим или равным рассчитанному с округлением до стандартного размера. Давление пальца на втулку шарнира определяется по формуле:
где c – ширина втулки; [ρ] = 60 МПа – допускаемое удельное давление на втулку.
Для стальных втулок [ρ] = 50 60 МПа для бронзовых [ρ] = 15 30 МПа. Наружный диаметр втулки D рекомендуется принимать равным 12d. Принципиальная схема шарнирного соединения «рычаг-корпус» показана на рисунке 2.10 в. Для расчета диаметра пальца этого шарнира и размеров втулки необходимо определить силы действующие на палец P1 и P2 (рис. 2.10 в). В местах контакта пальца с верхней и нижней втулками на него действуют усилия A1 и A2 равные по величине:
A1 = A2 = Мh = 32005 = 64 кН
где h = 005 – расстояние между центрами втулок; M – момент силы F приложенной в точке контакта рычага со стволом и направленной вдоль ствола перпендикулярно рычагу относительно точки центра шарнира:
M = FhN = 678047 = 32 кНм.
где hN – плечо силы F (рис. 2.10 а) определяемое из компоновочно-кинематической схемы. Кроме сил A1 и A2 в контактных точках пальца со втулками действует сила R2.
Сила R определяется геометрически с использованием компоновочной схемы. Для этого на схеме принимается масштаб сил. Все силы действующие на рычаг в плоскости его движения PГЦ TN путем параллельного переноса приводятся в центр шарнира и складываются графически по правилу сложения сил. Суммарная сила измеряется на схеме и через принятый масштаб переводится в размерность силы. Таким образом в центре верхней втулки будет действовать суммарная сила:
P1 = R2 – A1 = 3682 – 64 = -456 кН
а в центре нижней втулки:
P2 = R2 + A2 = 3682 + 64 = 824 кН
Расчетная схема пальца показана на рис. 2.10 в. Исходя из этой схемы минимальный диаметр пальца равен:
где Mиз – максимальный изгибающий момент.
где a = 0025 м b = 0025 м h = 0.05 м – размеры сопряжения (рис. 2.10 в).
Полученное значение диаметра проверяется на срез
где [] = 130 МПа– допускаемое напряжение на срез.
Допускаемое давление во втулках проверяется по условию:
где c – ширина втулки.
Если потребная ширина втулки окажется сопоставимой по величине с размером h то втулка выполняется сплошной неразрезной.
1.10 Проектирование рамы захватно-срезающего устройства
Рама ЗСУ должна обладать достаточной жесткостью и прочностью. Толщина стальных листов для конструкции рамы берется не меньше чем толщина листов захватных рычагов. Конструкция рамы обычно сварная. При ее разработке следует пользоваться рекомендациями изложенными в справочниках и результатами анализа существующих конструктивных аналогов. Следует учитывать возможность компоновки на раме ЗУ срезающего и валочного устройств узла сочленения ЗСУ с манипулятором и гидроагрегатов.
Как было отмечено в разделе 1.1 в качестве срезающего механизма на ЗСУ ВТМ могут применяться цепные дисковые и ленточные пилы фрезы ножевые срезающие устройства. Наибольшее распространение получили цепные пилы с гидравлическим приводом механизма вращения и подачи.
2.1 Определение основных параметров цепного срезающего устройства
Цепные срезающие устройства состоят из пильной цепи направляющей шины ведущей (приводной) звездочки приводного двигателя механизма надвигания пилы. Основным элементом цепного режущего устройства является пильная цепь важнейший проектный параметр которой – шаг цепи. В основном на отечественных машинах для сплошных рубок леса применяются пильные аппараты с цепями ПЦУ-20 и ПЦУ-30. При разработке ЗСУ для рубок ухода или для обработки мелкого леса можно применять цепи ПЦУ-10 ПЦУ-15. Краткая характеристика некоторых пильных цепей дана в табл. 1.
Таблица 2.1 - Характеристика пильных цепей
Масса 1 метра цепи кг
Шаг по режущим зубьям мм
Диаметр отверстий мм:
Высота звеньев в опасном сечении мм
Число звеньев цепи в блоке шт.
Продолжение таблицы 2.1
Номинальная длина выпускаемой промышленностью собранной цепи м
Наименьшая разрывная сила кН
Ориентировочное значение подачи
Рекомендуемая скорость резания мс
После выбора цепи определяются другие параметры СУ. Диаметр звездочки приводящей цепь в движение определяется по формуле:
где Δ = 003 м – шаг цепи; z = 10 – число зубьев или впадин на ободе звездочки. Для валочно-трелевочных машин z = 8 11. Для малогабаритных ЗСУ с цепями ПЦУ-10 и ПЦУ-15 z = 6-7. Длина пильной шины зависит от величины максимального диаметра расчетного дерева в плоскости срезания и равна:
L0 = 15D0 = 15065 = 0975 = 12 м
где D0 – диаметр ствола в плоскости срезания.
Окончательная длина пильной шины уточняется по компоновочной схеме. Толщина пильной шины равна толщине цепи или меньше ее на 1 мм. Формы пильной шины могут быть разнообразными: прямая с уширением в середине каплевидная прямая с более узкой консольной частью. Конструкция и размеры пильных шин лесных машин рассмотрены в книге. Основным требованием к форме пильной шины ВТМ и компоновке пилы является получение перемычки недопила расположенной в направлении валки. Постановка задачи оптимального проектирования формы профиля пильной шины и положения оси ведущей звездочки относительно корпуса ЗСУ приведена в пособии. В курсовом проекте проработку формы профиля шины и ее положения можно провести методом подбора лучшего варианта на компоновочной схеме ЗСУ. Если шина выполнена прямой с утолщением в середине то ее ширина по краям этого утолщения равна:
где Dзв – диаметр ведущей звездочки м;
mц = 23 – масса 1 метра цепи кг;
S0 = 175 – начальное натяжение цепи Н.
Начальное натяжение цепи принимается для пил ПЦУ-20 и ПЦУ-30 равным 150 200 Н а для других пил 80 100 Н. Длина пильной цепи одетой на шину должна быть кратной величине n Δ где Δ – шаг цепи n– число звеньев в блоке (табл. 2.1).
2.2 Компоновка срезающего аппарата на корпусе захватно-срезающего устройства
Проработка компоновки срезающего аппарата на корпусе ЗСУ производится с использованием ККС ЗУ. В принятом для схемы масштабе вырезается из плотной бумаги трафарет пильной шины. Ось ведущей звездочки пилы фиксируется точкой в определенном конструкцией ЗСУ месте. Если положение оси ведущей звездочки пильной цепи не регламентировано положением шарниров захватного рычага то ее координаты относительно контактной точки 3 можно принять равными (рис. 2.11):
yз = D04 = 0654 = 0163 м
где D0 – диаметр расчетного дерева в месте среза.
где R0– расстояние от центра пропила до оси вращения пилы (ось ведущей звездочки):
Поворотом пильной шины вокруг этой оси осуществляется проверка возможности перерезания дерева данной пилой и определяется положение перемычки недопила. Перемычка недопила должна располагаться в направлении валки. В ходе компоновки СУ может рассматриваться несколько возможных вариантов размещения ведущей звездочки пильной цепи относительно корпуса ЗУ. Форма и размеры пильной шины также окончательно уточняются при компоновке СУ.
Рисунок 2.11 - Компоновка пильной шины
После определения места крепления пилы на ЗУ из компоновочной схемы определяется потребный угол поворота пильной шины необходимый для перерезания дерева. При проработке компоновочной схемы рассматривается также вопрос размещения механизма надвигания пилы на дерево.
2.3 Определение потребной мощности гидродвигателя привода пильной цепи
Площадь сечения ствола по месту реза равна:
где D0 – диаметр дерева в месте среза. Производительность чистого пиления:
Пчп = Ft = 03312 = 0028 м2с
где t = 12 c – регламентированное время на срезание ствола.
Скорость надвигания пилы на дерево определяется по формуле:
где аз – коэффициент зависящий от степени заострения зубьев (при заточке 1 раз в смену – 14; при заточке через смену – 17).
Тогда угловая скорость поворота пильной шины равна:
= UR0 = 0039078 = 005 c-1?
где R0 – расстояние от центра пропила до оси вращения м.
Согласно известным кинематическим соотношениям возникающим при пилении потребная скорость движения пильной цепи должна удовлетворять условию:
где D0– диаметр дерева в месте срезания; nз– коэффициент зависящий от формы зуба и степени заполнения впадин зубьев (nз = 01 02); Δз = 012 м – шаг зубьев (расстояние между одноименными зубьями цепи).
Исходя из этого соотношения можно принять:
Значение скорости движения пильной цепи (скорости резания) должно находиться в рекомендуемых пределах (табл. 1). Тяговое усилие на пильной цепи определяется по формуле:
T = P(1 + a0) = 839(1 + 0902) = 839118 = 990 Н
где P – усилие резания на цепи;
– коэффициент трения цепи о пильную шину ( = 015 025);
a0 – коэффициент зависящий от степени затупления зубьев пильной цепи (a0= 08 10).
Усилие резания рассчитывается по следующей формуле:
P = kbH(U)106 = 14620024065(0039106) 106 = 839 Н
где k – удельная работа резания при пилении мДжм3;
b – ширина пропила м;
H – высота пропила (H = D0) м.
Величина удельной работы резания в свою очередь равна:
k = k'aпазawaт = 116114091 = 1462 МДжм2
где k' = 116 МДжм2 – удельная работа резания при распиловке воздушно-сухой сосны зависящая от подачи на зуб (табл. 2.2);
aп – породный коэффициент (сосна ель – 1; осина – 085; береза – 125);
аз– коэффициент зависящий от степени заострения зубьев (при заточке 1 раз в смену –14; при заточке через смену – 17);
aw – коэффициент учитывающий влажность древесины (aw = 09 для свежесрубленной древесины);
aт – температурный коэффициент (лето – 1 зима 13 15).
Потребная мощность двигателя привода пильной цепи:
где n – полный КПД устройств передающих энергию от двигателя к пильной цепи.
где ц = 065 072 – КПД пильной цепи; p = 08 09 – КПД редуктора (если он предусмотрен конструкцией). Потребная частота вращения ведущей звездочки:
Рассчитанное значение мощности может быть проверено по условию износа шарниров цепи и условию прочности цепи по методике либо должен быть проведен проверочный расчет пильной цепи . По величине потребной мощности и числу оборотов подбирается гидродвигатель привода пильной цепи.
Таблица 2.2 - Значение удельной работы резания
Удельная работа резания МДжм3 при подаче на зуб Uz мм
Подача на зуб рассчитывается по формуле:
Uz = ΔU = 0120039106 = 044 м.
Полное натяжение пильной цепи при набегании ее на ведущую звездочку:
S = S0 + Pц + Т = 175 + 990 + 25843 = 142 кН
где S0 = 175 – монтажное натяжение Н;
Т – тяговое усилие на цепи Н;
Pц – натяжение от действия центробежной силы Н.
Pц = mц = 23106 = 25843 Н
где mц – масса одного метра цепи кг; – скорость цепи мс.
По величине ведется расчет звеньев цепи на прочность на разрыв и расчет заклепок цепи на срез и смятие [23]. Расчетная схема приведена на рисунке 2.12.
где [S] = 48 кН.– наименьшая разрывная сила цепи приводимая в табл. 2.1.
Рисунок 2.12 - Расчетная схема пильной цепи
Касательные напряжения в заклепках цепи:
где d1 = 00083 м – диаметр отверстия под заклепку в боковом звене цепи (рис. 2.12);
где 1 = 0003 м – толщина бокового звена;
Удельное давление в шарнирах цепи:
где d3 = 0012 - диаметр диаметр отверстия под заклепку в среднем звене;
= 0006 м – толщина среднего звена;
Наибольшее распространение получили механизмы надвигания с гидроцилиндром шестерней-рейкой с гидроприводом. Конструкция этих механизмов описана в книгах. По величине потребного усилия надвигания пилы на дерево рассчитанного для середины пропила
Pн = Pа0 = 83909 = 7551 Н
где Р – усилие резания Н;
а0– коэффициент зависящий от степени затупления зубьев пильной цепи (08 10); через уравнение моментов относительно оси поворота пильной шины (плечи сил определяются из компоновочно-кинематической схемы) определяется потребное усилие на штоке гидроцилиндра привода механизма надвигания пилы. При расчете гидропривода должны быть выполнены два условия:
) по величине потребного усилия на штоке гидроцилиндра механизма надвигания пилы определяется диаметр этого гидроцилиндра:
где hн = 06 – плечо силы надвигания относительно оси поворота пильной шины м;
hц = 02 – плечо силы развиваемой приводным гидроцилиндром механизма надвигания пилы относительно той же оси м;
p0 = 073 – давление в гидросистеме МПа;
) для обеспечения требуемой производительности пиления объемная подача насоса привода механизма надвигания должна быть равна (м3):
– КПД гидросистемы (08 085);
t – регламентированное время срезания с. Если не удается подобрать насос с требуемой объемной подачей то необходимо провести корректировку ККС для получения других величин диаметра хода штока гидроцилиндра и отношения плеч.
3 Оценка возможности создания валочного момента натягом манипулятора
В случае создания валочного момента натягом манипулятора в техническом задании на проектирование указывается грузоподъемность манипулятора. Оценка возможности создания валочного момента манипулятором проводится после предварительной компоновки ЗСУ когда становится ясным способ сочленения манипулятора с этим рабочим органом. Из компоновочной схемы определяется расстояние от перемычки недопила (точка поворота дерева при валке) до линии действия усилия создаваемого манипулятором. Произведение этого расстояния на величину грузоподъемности манипулятора сравнивается с потребным валочным моментом. Если рассчитанная величина окажется большей или равной величине потребного валочного момента то в конструкцию ЗСУ не требуется вводить дополнительно ВУ (если оно не предусмотрено заданием на проектирование). В том случае если рассчитанный момент окажется меньше потребного следует в конструкции ЗСУ предусмотреть ВУ с создаваемым моментом равным разнице потребного и расчетного.
При выполнении расчетно-графической работы «Расчет и проектирование захватно-срезающего устройства валочно-трелевочной машины ЛП-58-01» были рассчитаны и приняты размеры рычагов гидроцилиндров и других деталей захватно-срезающего устройства.
Для этого потребовалось разработать компоновочно-кинематическую схему захватно-срезающего устройства рассчитать силы воздействующие деревом на рычаги захватно-срезающего устройства нагрузки в опасном сечении рычага геометрические характеристики сечения рычага произвести расчет на прочность захватного рычага рассчитать проушину рычага опорную призму и шарнирные соединения спроектировать и рассчитать срезающее устройство.
По полученным данным на листе формата А1 в масштабе было построено захватно-срезающее устройство с указанием размеров его составных детелей.
Библиографический список
Беловзоров Л. Н. Цепные режущие устройства лесозаготовительных машин Л. Н. Беловзоров и др. М.: Лесная пром-сть 1982. 136 с.
Можаев Д. В. Механизация лесозаготовок за рубежом Д. В. Можаев С. Н. Илюшкин. М.: Лесная пром-сть 1988. 296 с.
Кушляев В. Ф. Конструктивные особенности и применение захватно-срезающих устройств В. Ф. Кушляев и др. Л. 1981. 62 с.
Кушляев В. Ф. Лесозаготовительные машины манипуляторного типа В. Ф. Кушляев. М.: Лесная пром-сть 1981. 248 с.
Аболь П. И. Валочно-трелевочная машина ЛП-49 П. И. Аболь и др. М.: Лесная пром-сть 1988. 168 с.
Федоров Ю. М. Валочно-трелевочная машина ЛП-17 Ю. М. Федоров и др. М.: Лесная пром-сть 1984. 240 с.
Аболь П. И. Перспективы машинизации лесосечных работ. Обзорная информация П. И. Аболь Р. А. Люманов. М. 1989. 48 с.
Кусакин Н. Ф. Валочно-трелевочные машины манипуляторного типа. Обзорная информация Н. Ф. Кусакин. М. 1981. 44 с.
Виноградов Г. К. Лесосечные работы Г. К. Виноградов. М.: Лесная пром-сть 1981. 272 с.
Баринов К. Н. Проектирование лесопромышленного оборудования: Учеб. пособие К. Н. Баринов В. А. Александров. Л.: Изд-во ЛГУ 1988. 240 с.
Александров В. А. Конструирование и расчет машин и
оборудования для лесосечных работ и нижних складов В. А. Александров Н. Р. Шоль. Ухта: Издательско-полиграфическое управление УГТУ 2000. 243 с.
Рекомендуемые чертежи
- 24.01.2023
Свободное скачивание на сегодня
Обновление через: 10 часов 33 минуты