Расчет и проектирование вала редуктора




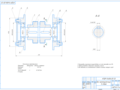
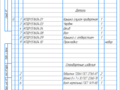
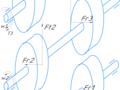
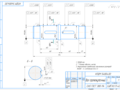
- Добавлен: 24.01.2023
- Размер: 1007 KB
- Закачек: 0
Описание
Расчет и проектирование вала редуктора
Состав проекта
![]() |
![]() ![]() ![]() |
![]() |
![]() ![]() ![]() |
![]() ![]() ![]() |
![]() ![]() ![]() |
![]() ![]() ![]() |
![]() ![]() ![]() |
![]() ![]() ![]() |
![]() ![]() ![]() |
![]() ![]() ![]() |
![]() ![]() ![]() ![]() |
![]() ![]() ![]() |
![]() ![]() ![]() |
![]() ![]() ![]() ![]() |
![]() ![]() ![]() ![]() |
![]() ![]() ![]() |
![]() ![]() ![]() ![]() |
Дополнительная информация
подшипник.frw

Винт.frw

зубчатое.frw

расчетная схема.frw

схема15.frw

манжета.frw

пространствен. схема.frw

шпонка.frw

Спецификация.spw

крышка.frw

сборка.cdw

рабочий.cdw

вал.frw

сборка-с.cdw

Рекомендуемые чертежи
- 24.01.2023
- 31.01.2023